[0001] Die Erfindung betrifft ein Verfahren zur Umsetzung von Mono-, Di- und Triglyceriden
der allgemeinen Formel

worin R
1, R
2 und R
3, die gleich oder verschieden sein können, aliphatische Kohlenwasserstoffreste mit
3 bis 23 Kohlenstoffatomen bedeuten, wobei diese Reste gegebenenfalls mit einer OH-Gruppe
substituiert sein können, oder von Gemischen solcher Glyceride in flüssiger Phase
mit Ammoniak unter Gewinnung von Fettsäurenitrilen der Formel R
1 (R2, R
3)-CN und von Glycerin mittels Hindurchleiten von gasförmigem Ammoniak, gegebenenfalls
unter Zumischung von Inertgas, bei erhöhten Temperaturen und in Gegenwart von Katalysatoren.
[0002] Fettsäurenitrile, die wichtige Zwischenprodukte zur Herstellung von Aminen darstellen,
werden nach technischen Verfahren bevorzugt aus den entsprechenden Fettsäuren und
Ammoniak in Gegenwart geeigneter Katalysatoren hergestellt. Diese seit langem bekannte
Synthese kann sowohl in der flüssigen Phase in einem Temperaturbereich von 250 bis
350 °C als auch in der Gasphase in einem Temperaturbereich von 320 bis 380 °C durchgeführt
werden. Geeignete Katalysatoren für die Reaktion in der flüssigen Phase sind z. B.
Zinkoxid oder Manganacetat, für die Gasphase beispielsweise Aluminiumoxid oder Bleicherde.
Zusammenfassende Angaben über solche Verfahren finden sich in "Methoden der Organischen
Chemie" (Houben-Weyl), Band 8, Seite 330 ff., Georg Thieme Verlag, Stuttgart, 1952,
sowie in "Fatty Acids and their Industrial Applications", Marcel Dekker, New York,
1968, Seite 909 ff. Ein Verfahren zur Herstellung von Fettsäurenitrilen durch Umsetzung
von Fettsäuren mit Ammoniak in flüssiger Phase in Gegenwart von Zink- oder Calciumsalzen
von Fettsäuren beschreibt die US-PS 2 589 232. Ein weiteres Verfahren, bei dem Titansäureester
kurzkettiger aliphatischer Alkohole als Katalysatoren eingesetzt und neben Fettsäuren
auch die Fettsäureester kurzkettiger Alkohole als Ausgangsprodukte verwendet werden
können, ist beschrieben in der US-PS 2 993 926. Sollen für die genannten Verfahren
natürliche Fette oder Öle eingesetzt werden, so bedingt dies zunächst die Gewinnung
der freien Fettsäure oder der kurzkettigen Fettsäureester in einer gesonderten Stufe.
[0003] Es ist ferner bekannt, natürliche Fette oder auch Fettsäureester einwertiger Alkohole
durch Umsetzung mit Ammoniak zu den entsprechenden Fettsäureamiden umzusetzen. Geeignete
Katalysatoren hierfür sind beispielsweise Metalloxide oder Calciumnitrat (vgl. japanische
Patentbekanntmachungen 70-35524 und 71-21846 sowie japanische Patentanmeldung 71-6614).
Aus den Fettsäureamiden kann dann in bekannter Weise durch Dehydratisierung in einer
zweiten Stufe das Fettsäurenitril gewonnen werden.
[0004] Aus der japanischen Patentbekanntmachung 72-26921 ist ein Verfahren bekannt, in dem
natürliche Fette durch Umsetzung mit aliphatischen Aminen in Fettsäureamide überführt
werden können, wobei das entstehende Glycerin durch die Gegenwart von Borsäure als
Glycerinborsäureester aus dem Gleichgewicht entfernt wird.
[0005] Unter wirtschaftlichen Gesichtspunkten wäre ein Verfahren erstrebenswert, bei dem
natürliche Fette oder öle, das heißt native Triglyceride, die geringe Mengen von Mono-
und Diglyceriden enthalten können, ohne Isolierung der Fettsäureamidstufe bzw. ohne
den Umweg über die freie Fettsäure oder den kurzkettigen Fettsäureester direkt in
die entsprechenden Fettsäurenitrile überführt werden können.
[0006] Derartige Versuche sind bereits gemacht worden. In den britischen Patentschriften
416 631 und 451 594 wird ein Verfahren zur Umsetzung von Hydroxyfettsäuren bzw. Fettsäuren,
erhalten aus natürlichen Fetten, mit Ammoniak zu Fettsäurenitrilen in der Gasphase
bei Temperaturen von 300 bis 450 °C in Gegenwart von oxidischen Dehydratisierungs-Katalysatoren,
insbesondere in Gegenwart von Aluminiumoxid, beschrieben. Dort finden sich auch Hinweise,
daß Glyceride direkt einsetzbar sind, obwohl diese unter den angegebenen Bedingungen
nicht verdampfbar sind. Im Beispiel 3 der GB-PS 416 631 und in den Beispielen 7 und
14 der GB-PS 451 594 werden solche Umsetzungen von Castoröl, Palmkernfett und Cocosöl
mit Ammoniak bei Temperaturen von 350 bis 400 °C in Gegenwart von Bauxit gezeigt.
Es fehlt hier jedoch jeglicher Hinweis auf den Verbleib des Glycerins. Nacharbeitungen
haben ergeben, daß das Glycerin unter den Bedingungen dieses Verfahrens durch thermische
Spaltung völlig zersetzt wird.
[0007] Dies führt nicht nur zum Verlust eines wertvollen Rohstoffs, sondern bewirkt auch
eine entscheidende Verschlechterung der Qualität der als Produkte erhaltenen Fettsäurenitrile,
die sich insbesondere in Farbe und Geruch manifestiert. Da Fettsäurenitrile Zwischenprodukte
darstellen und für die Weiterverarbeitung hohe Reinheitsgrade gefordert werden, macht
dies aufwendige Reinigungsoperationen zur Beseitigung der Zersetzungsprodukte erforderlich,
wodurch das genannte Verfahren völlig unwirtschaftlich wird.
[0008] Somit bestand die Aufgabe, ein einstufiges Verfahren zu entwickeln, nach dem es möglich
ist, aus Glyceriden in wirtschaftlich vertretbaren Reaktionszeiten neben dem Fettsäurenitril
auch das Glycerin in hoher Ausbeute zu gewinnen.
[0009] Die Aufgabe wird im Sinne der Erfindung gelöst durch ein Verfahren zur Umsetzung
von Mono-, Di- und Triglyceriden der allgemeinen Formel
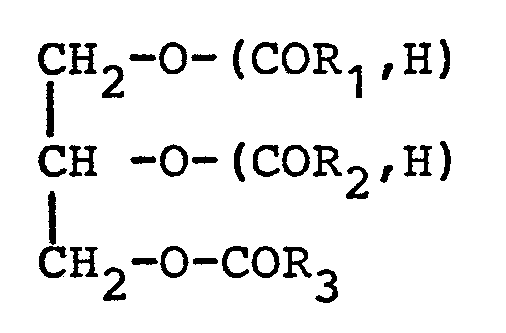
worin R
1, R
2 und R3, die gleich oder verschieden sein können, gesättigte oder ein- oder mehrfach
ungesättigte Kohlenwasserstoffreste mit 3 bis 23 Kohlenstoffatomen bedeuten, wobei
diese Reste gegebenenfalls mit einer OH-Gruppe substituiert sein können, oder Gemischen
solcher Glyceride in flüssiger Phase mit Ammoniak unter Gewinnung von Fettsäurenitrilen
der Formel R
l(R
2, R
3)-CN und von Glycerin mittels Hindurchleiten von gasförmigem Ammoniak, gegebenenfalls
unter Zumischung von Inertgas, bei erhöhten Temperaturen und in Gegenwart von Katalysatoren,
das dadurch gekennzeichnet ist, daß das Glycerid mit einem Ammoniakstrom von mindestens
200 l/kg Glycerid und Stunde, bei Temperaturen von 220 bis 300 °C, in Gegenwart von
Blei-, Zink-,
[0010] Cadmium-, Zinn-, Titan-, Zirkon=, Chrom-, Antimon-, Mangan-, Eisen-,Nickel- oder
Kobaltsalzen von Carbonsäuren oder Sulfonsäuren als Katalysatoren in innigen Kontakt
gebracht und das ausgetragene Produktgemisch einer Phasentrennung in eine Fettsäurenitrilphase
und eine Glycerin/Wasser-Phase unterworfen wird.
[0011] Ausgangsstoffe für das erfindungsgemäße Verfahren sind Mono-, Di- und Triglyceride
der allgemeinen Formel
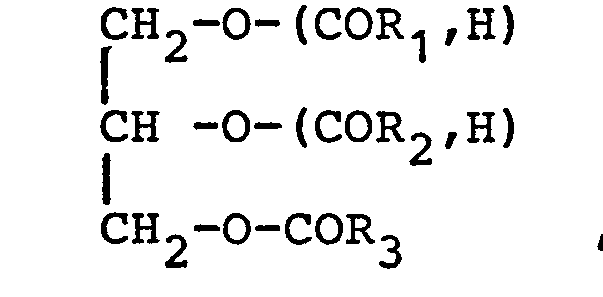
das heißt in dieser Formel können ein oder zwei Fettsäurereste durch H ersetzt sein.
Die Fettsäurereste R
1CO-, R
2CO-und R
3CO- leiten sich ab von Fettsäuren mit 3 bis 23 Kohlenstoffatomen. Die aliphatischen
Kohlenwasserstoffreste R
1' R
2 und R
3 können geradkettig oder auch ein- oder mehrfach verzweigt sein. Sie können gesättigte
Ketten darstellen oder auch eine oder mehrere Mehrfachbindungen, vorzugsweise Doppelbindungen,
aufweisen. Gegebenenfalls können diese Reste mit einer OH-Gruppe substituiert sein.
Bevorzugte Ausgangsstoffe für das erfindungsgemäße Verfahren sind vor allem die natürlichen
Fette, die Gemische aus überwiegend Triglyceriden und kleinen Anteilen aus Diglyceriden
und Monoglyceriden darstellen, wobei auch diese meist wiederum Gemische darstellen
und verschiedenartige Fettsäurereste im obengenannten Bereich, insbesondere solche
mit 8 und mehr C-Atomen, enthalten. Beispielsweise seien genannt pflanzliche Fette
wie Olivenöl, Cocosfett, Palmkernfett, Babussu- öl, Palmöl, Erdnußöl, Rüböl, Rizinusöl,
Sesamöl, Cottonöl, Sonnenblumenöl, Sojaöl, Hanföl, Mohnöl, Avocadoöl, Baumwollsaatöl,
Weizenkeimöl, Maiskeimöl, Kürbiskernöl, Traubenkernöl, Kakaobutter oder Pflanzentalge,
ferner tierische Fette wie Rindertalg, Schweinefett, Knochenfett, Hammeltalg,
[0012] Japantalg,, Walöl und andere Fischöle sowie Lebertran. Ebenso eingesetzt werden können
aber auch einheitliche Tri-, Di- und Monoglyceride, sei es, daß diese aus natürlichen
Fetten isoliert oder auf synthetischem Wege gewonnen wurden. Hier seien beispielsweise
genannt: Tributyrin, Tricapronin, Tricaprylin, Tricaprinin, Trilaurin, Trimyristin,
Tripalmitin, Tristearin, Triolein, Trielaidin, Trilinoliin, Trilinolenin, Monopalmitin,
Monostearin, Monoolein, Monocaprinin, Monolaurin, Monomyristin oder gemischte Glyceride
wie beispielsweise Palmitodistearin, Distearoolein, Dipalmitoolein oder Myristopalmitostearin.
[0013] Entscheidend für das Gelingen des einstufigen Verfahrens, das heißt die Gewinnung
von Fettsäurenitril oder einem Gemisch von Fettsäurenitrilen in hoher Reinheit und
hoher Ausbeute sowie die Gewinnung von Glycerin in hoher Ausbeute, sind vor allem
drei Verfahrensparameter, nämlich die Wahl der richtigen Temperatur bzw. die richtige
Temperaturführung, die rasche Entfernung des gebildeten Glycerins aus der Reaktionszone
sowie die Auswahl des richtigen Katalysators.
[0014] Die rasche Entfernung des Glycerins aus der Reaktionszone bedingt, daß eine bestimmte
Mindestmenge an Ammoniak durch das Reaktionsgemisch hindurchgeleitet wird. Diese beträgt
mindestens 200 1 pro kg Glycerid und Stunde, vorzugsweise mindestens 400 1 pro kg
Glycerid und Stunde. Nach oben besteht keine kritische Grenze bezüglich des durchzuleitenden
Ammoniakstroms, die mengenmäßige Obergrenze wird allenfalls durch wirtschaftliche
Überlegungen bestimmt und liegt aus diesen Gründen bei etwa 1000 l, vorzugsweise bei
etwa 800 1 Ammoniak pro kg Glycerid und Stunde. Der hindurchgeleiteten Gasmenge kann
dabei mit Vorteil bis zu 30 %, vorzugsweise bis zu 15 %, bezogen auf die durchgesetzte
Menge an Ammoniak, an Inertgas, beispielsweise Stickstoff, hinzugefügt werden.
[0015] Weiterhin ist es von entscheidender Bedeutung, daß die Reaktionstemperatur während
des gesamten Reaktionsverlaufs im Bereich zwischen 220 und 300 °C, vorzugsweise 230
bis 290 °C, gehalten wird. Vorzugsweise läßt man die Temperatur vom Beginn bis zum
Ende des Prozesses ansteigen. Dies kann sowohl kontinuierlich als auch stufenweise,
insbesondere in Form eines Temperaturprogramms geschehen. Ein bevorzugtes Temperaturprogramm
ist, daß die Reaktion zunächst im Temperaturbereich von etwa 220 bis 240 °C so lange
abläuft, bis etwa 30 bis 70 % der theoretisch zu erwartenden Glycerinmenge aus dem
Reaktionsgefäß ausgetragen sind, daß man die Temperatur dann im Verlauf von etwa einer
halben bis 5 Stunden stufenweise oder kontinuierlich erhöht, bis ein Temperaturbereich
von etwa 270 bis 300 °C erreicht ist, und die Reaktion dann in diesem Temperaturbereich
zu Ende führt. Das Ende der Reaktion ist daran erkennbar, daß keine flüssige Phase
mehr in die Vorlage übergeht.
[0016] Schließlich ist die Auswahl der Katalysatoren von wesentlicher Bedeutung für das
erfindungsgemäße Verfahren. Als Katalysatoren können eingesetzt werden die Blei-,
Zink-, Cadmium-, Zinn-, Titan-, Zirkon-, Chrom-, Antimon-, Mangan-, Eisen-, Nickel-
oder Kobaltsalze von organischen Carbon-oder Sulfonsäuren. Die genannten Katalysatoren
können auch in Form von Gemischen Anwendung finden. Die organischen Carbon- und Sulfonsäuren,von
denen sich die Anionen der genannten Salze ableiten, gehören insbesondere folgenden
Gruppen an:
[0017] Offenkettige Carbonsäuren mit gerader oder verzweigter Kette, wobei diese Kette gesättigt
ist oder auch eine oder mehrere Doppelbindungen enthalten kann und 4 bis 23, vorzugsweise
8 bis 23 Kohlenstoffatome besitzt,
[0018] Alkylarylcarbonsäuren vorzugsweise Alkylbenzolcarbonsäuren und Alkylnaphthalincarbonsäuren,
die einen oder mehrere Alkylreste mit je 1 bis 23, vorzugsweise 1 bis 12 Kohlenstoffatome
tragen,
[0019] Alkylsulfonsäuren und Alkyldisulfonsäuren mit geradkettigen oder verzweigten Alkylresten
mit 4 bis 24, vorzugsweise 8 bis 24 Kohlenstoffatomen, wobei diese Alkylreste gegebenenfalls
mit OH-Gruppen, vorzugsweise mit einer OH-Gruppe substituiert sein können und wobei
ferner in der Alkylkette die Wasserstoffatome teilweise oder vorzugsweise völlig durch
Fluor ersetzt sein können, sowie Alkylarylsulfonsäuren, insbesondere Alkylbenzolsulfonsäuren
und Alkylnaphthalinsulfonsäuren (wobei hierunter jeweils die Mono-, Di- und Trisulfonsäuren
verstanden werden), mit einem oder mehreren geradkettigen oder verzweigten Alkylresten
mit je 1 bis 24 Kohlenstoffatomen, wobei die genannten Alkylketten auch mit zwei,
vorzugsweise mit einer Carboxylgruppe substituiert sein können.
[0020] Von diesen, als Katalysatoren im Rahmen des erfindungsgemäßen Verfahrens einsetzbaren
Salzen sind besonders bevorzugt hinsichtlich des Kations die Blei-, Cadmium-, Eisen-,
Kobalt- und insbesondere die Zinksalze. Hinsichtlich des Anions sind besonders bevorzugt
die obengenannten Gruppen von Sulfonsäuren, insbesondere jedoch daraus wieder die
Alkylarylsulfonsäuren der letztgenannten Gruppe. Beispielsweise seien genannt:
n-Dodecylsulfonsäure, n-Octadecylsulfonsäure, Isobutylnaphthalinsulfonsäure, n-Butylnaphthalinsulfonsäure,
Isopropylnaphthalinsulfonsäure, Cetylbenzolsulfonsäure, Octadecylbenzolsulfonsäure,
Tetrapropylenbenzolsulfonsäure und Triisobutylbenzolsulfonsäure.
[0021] Die als Katalysatoren im erfindungsgemäßen Verfahren eingesetzten Salze sind durch
Umsetzung der freien Säuren mit den entsprechenden Metalloxiden nach bekannten Verfahren
zugänglich. Die freien Sulfonsäuren können erhalten werden aus den bekannten Sulfonierungsprozessen
oder aus den entsprechenden Alkalisulfonaten, beispielsweise über Ionenaustauscher.
[0022] Die genannten Katalysatoren können in Form ihrer genannten Salze direkt zugesetzt
werden. Es kann aber auch das entsprechende Metalloxid und die entsprechende Carbon-
oder Sulfonsäure einzeln dem Reaktionsgemisch zugesetzt werden, wobei sich der Katalysator
während der Reaktion in situ bildet. Die genannten Katalysatoren werden im erfindungsgemäßen
Verfahren in Mengen von 0,5 bis 75 Gew.-%, bei diskontinuierlicher Fahrweise vorzugsweise
von 1 bis 25 Gew.-% und insbesondere von 1 bis 10 Gew.-%, bei kontinuierlicher Fahrweise
in Mengen von vorzugsweise 5 bis 75 Gew.-%, insbesondere von 10 bis 30 Gew.-%, jeweils
bezogen auf das eingesetzte Glycerid,zugegeben.
[0023] Zur Durchführung des erfindungsgemäßen Verfahrens wird das jeweilige Glycerid oder
Glyceridgemisch in einem geeigneten Reaktionsgefäß, beispielsweise einem Rührkessel,
zusammen mit dem oben beschriebenen Katalysator vorgelegt. Es kann die Gesamtmenge
an Katalysator vorgelegt werden oder auch eine Teilmenge, wobei der restliche Teil
dann während der Reaktion portionsweise oder kontinuierlich nachgeschleust wird. Das
Reaktionsgefäß ist mit einer Gaseinleitungsvorrichtung, die die Messung des Gasstromes
gestattet, versehen, ferner mit einer Temperaturmeßeinrichtung, einer Heizeinrichtung
und gegebenenfalls mit einem Rührer. Das Reaktionsgefäß ist verbunden mit einer Kondensationsvorrichtung,
die aus einer oder vorzugsweise aus mehreren, auf Temperaturen von etwa 60 ° bis 120
°C beheizten Kondensationsvorlagen besteht. Nach dem Aufheizen des Reaktionsgefäßes,
das gegebenenfalls unter Stickstoffspülung erfolgt, wird nach Erreichung der Anfangstemperatur
der Ammoniakstrom eingestellt. Das in die Kondensationsvorrichtung austretende Produktgemisch
besteht in der Anfangsphase aus höheren Anteilen von Rohglycerin. Der Anteil an Fettsäurenitril
nimmt im Laufe der Reaktion mehr und mehr zu, so daß im letzten Teil im wesentlichen
reines Fettsäurenitril ausgetragen wird, während die Austragung des Rohglycerins bereits
vorher beendet ist. Der Ammoniakstrom (dem Inertgas zugefügt sein kann, wie oben beschrieben)
sorgt ferner für eine rasche Austragung des Reaktionswassers während der gesamten
Reaktionsdauer. Der austretende Gasstrom wird zweckmäßigerweise, nach Abtrennung des
mitgeführten Wassers und gegebenenfalls unter Zuführung von frischem Ammoniak, in
die Reaktion zurückgeführt. In der Kondensationsvorrichtung sammelt sich das ausgetragene
Produktgemisch, wobei eine Vortrennung dieses Gemisches in eine Fettsäurenitrilphase
und in eine Rohglycerin/Wasser-Phase erfolgt. Die abschließende Phasentrennung wird
zweckmäßigerweise nach Ablassen der Kondensationsvorrichtung und Überführung in einen
Separator, beispielsweise in einen Dampfabscheider, bei etwa 60 bis 100 °C vorgenommen.
Restliches Glycerin wird mittels Wasser aus der Fettsäurenitrilphase ausgewaschen.
Das aus der wäßrigen Phase (beispielsweise durch Destillation) isolierte Rohglycerin
kann nach bekannten Verfahren (vergleiche Ullmann Encyklopädie der Technischen Chemie,
1956, Band 7, Seiten 523 bis 524), beispielsweise durch Destillation, gereinigt werden.
[0024] Nach dem erfindungsgemäßen Verfahren gelingt es, Fettsäurenitrile und Glycerin in
ausgezeichneten Ausbeuten herzustellen. Diese Ausbeuten liegen bei mindestens 93 %
und erreichen 96 % und mehr Fettsäurenitril sowie bis zu 95 % Rohglycerin (jeweils
bezogen auf die theoretische Ausbeute auf Basis des eingesetzten Glycerids). Das erhaltene
Fettsäurenitril enthält höchstens bis zu 2 Gew.-% an freien Fettsäuren und bis zu
10 Gew.-%, meistens aber weniger als 6 Gew.-% Fettsäureamide als Nebenprodukte.
[0025] Diese im ausgetragenen Produktgemisch enthaltenen Fettsäuren und Fettsäureamide werden
zweckmäßigerweise ebenfalls noch in Fettsäurenitrile überführt, indem sie nach oder
gegebenenfalls vor der Phasentrennung einer Nachreaktion in Gegenwart von Ammoniak
und in Gegenwart der oben definierten Katalysatoren unterworfen werden.
[0026] DieserNachreaktion können entweder die aus dem ausgetragenen Fettsäurenitril abgetrennten
freien Fettsäuren und Fettsäureamide, gegebenenfalls zusammen mit noch nicht ausgetragenem
Rohnitril, unterworfen werden, oder es wird die gesamte Fettsäurenitrilphase nachbehandelt.
Dies kann insbesondere nach folgenden Ausführungsformen der Nachreaktion geschehen:
[0027] Nach einer bevorzugten Methode wird zwischen den Reaktor und die Kondensationsvorrichtung
eine Fraktionierkolonne zwischengeschaltet. Diese Fraktionierkolonne, die eine Spiegelglaskolonne
oder ein gut isoliertes Rohr, gefüllt beispielsweise mit Raschigringen, sein kann,
trennt die während der Reaktion intermediär gebildeten Fettsäureamide und freien Fettsäuren
ab und führt sie in das Reaktionsgefäß zurück, während das restliche ausgetragene
Produktgemisch in die Vorlage gelangt und dort unter Kondensation gesammelt wird wie
oben beschrieben.
[0028] Unter Zwischenschaltung dieses Fraktioniersystems kann das erfindungsgemäße Verfahren
in besonders einfacher Weise vollkontinuierlich gestaltet werden. Dazu wird das Glycerid,
wie oben beschrieben, zusammen mit den früher genannten Anteilen an Katalysator im
Reaktionsgefäß vorgelegt oder wahlweise zu einem inerten, nicht flüchtigem Lösungsmittel,
wie beispielsweise Paraffinöl, zudosiert. Die zugeführte Ammoniakmenge soll auch hier
mindestens 200 l/kg Glycerid und Stunde betragen und liegt normalerweise bei höheren
Durchsätzen als sie oben für die diskontinuierliche Verfahrensweise angegeben wurden.
[0029] Die Verfahrenstemperaturen sollen vorteilhafterweise im Temperaturbereich von 220
bis 270 °C, insbesondere im Temperaturbereich von 230 bis 250 °C gehalten werden.
Während der Reaktion wird dann das Glycerid kontinuierlich nachgespeist. Glycerid
und Katalysator können auch im Gemisch kontinuierlich zugeführt werden. Über das Fraktioniersystem
erfolgt der stetige Austrag von Fettsäurenitril, Glycerin und
Was- ser, während Fettsäureamid und freieFettsäure kontinuierlich in den Prozeß zurückgeführt
werden.
[0030] Nach einer weiteren Variante der Nachbehandlung wird die Reaktion zunächst bis zur
im wesentlichen vollständigen Austragung des Rohglycerins geführt (was bei der Phasentrennung
daran erkennbar ist, daß die Rohglycerin-Phase nicht mehr zunimmt), sodann wird die
aus der Phasentrennung erhaltene Fettsäurenitrilphase zu dem noch nicht ausgetragenen
Anteil an Fettsäurenitril zurück in den Reaktor gegeben, wobei im Reaktor die Temperatur
auf einen Bereich von 200 ° bis 320 °C eingestellt und der Ammoniakstrom auf eine
Menge von 5 bis 150 l/kg Fettsäurenitril und Stunde, vorzugsweise auf 15 bis 100 l/kg,
reduziert wird. Sofern im ersten Teil der Reaktion bereits genügend Katalysator eingesetzt
worden ist (Katalysatormengen, die an der oberen Grenze der oben angeführten Mengenbereiche
liegen), erübrigt sich die neuerliche Zugabe an Katalysator. Andernfalls ist eine
entsprechende Menge an Katalysator nachzuführen. Bei diesen Reaktionsbedingungen geht
die vollständige Umwandlung von Fettsäureamiden und Fettsäuren in Fettsäurenitrile
vor sich, die an der Bildung von Reaktionswasser verfolgt werden kann. Dieses Wasser
wird mit dem überschüssigen Ammoniak ausgetragen, wobei der Ammoniakstrom, gegebenenfalls
unter Zugabe von frischem Ammoniak und nach Befreiung von Wasser, wieder in den Prozeß
zurückgeführt werden kann. Nach Beendigung der Umsetzung wird das im Reaktor befindliche
Fettsäurenitril zur Abtrennung des Katalysators zweckmäßigerweise noch einer Destillation
unterworfen.
[0031] Nach einer weiteren Methode kann aber auch das gesamte Fettsäurenitril aus der Reaktion
ausgetragen, der Phasentrennung unterworfen und dann in einen zweiten Reaktor (Nachreaktor)
eingebracht werden, wobei die oben angegebenen Katalysatoren in den genannten Mengen
zuzusetzen sind. Die Nachbehandlung erfolgt dann unter den gleichen Bedingungen, wie
sie vorstehend bei der Rückführung einer Teilmenge in das erste Reaktionsgefäß genannt
wurden. Auch hier ist nach Beendigung der Nachbehandlung das Fettsäurenitril destillativ
aufzuarbeiten.
[0032] Diese Methode der Nachbehandlung kann auch so abgewandelt werden, daß die gesamte
Fettsäurenitrilphase kontinuierlich, beispielsweise durch einen Rohrreaktor,unter
den angegebenen Bedingungen geführt wird.
[0033] Schließlich kann die gewonnene Fettsäurenitrilphase auch im gasförmigen Zustand gemeinsam
mit Ammoniak in einer Menge von 200 bis 800 l/kg Fettsäurenitril und Stunde, vorzugsweise
300 bis 600 l/kg, und bei einer Temperatur von 280 bis 400 °C, vorzugsweise bei 300
bis 380 °C, kontinuierlich über ein Festbett von Dehydratisierungskatalysatoren geleitet
werden. Geeignete Dehydratisierungskatalysatoren sind beispielsweise Aluminiumoxid
in Form von Bauxit oder Hydrargilit, Thoriumoxid, Zirkonoxid, Aluminiumphosphat, Silicagel,
aktive Bleicherden und dergleichen oder Mischungen davon.
[0034] Nach dem erfindungsgemäßen Verfahren ist es also überraschenderweise möglich, nicht
nur Fettsäurenitrile in ausgezeichneten Ausbeuten und guter Reinheit zu gewinnen,
sondern es kann auch Glycerin in hohen Ausbeuten gewonnen werden. Mit den geschilderten
Nachbehandlungsmethoden kann die Reinheit des gewonnenen Fettsäurenitrils weiter erhöht
werden, so daß es weniger als 2 Gew.-%, in den meisten Fällen weniger als 0,1 Gew.-%
Fettsäureamid und weniger als 1,5 Gew.-%, in den meisten Fällen weniger als 0,1 Gew.-%
freie Fettsäuren enthält und auch sonst von Nebenprodukten völlig frei ist.
[0035] Fettsäurenitrile sind wichtige chemische Zwischenprodukte, die insbesondere zu primären
Aminen und quaternären Ammonjumsalzen weiterverarbeitet werden, welche wiederum insbesondere
als Textilhilfsmittel,Flotationshilfsmittel und als kationenaktive oberflächenaktive
Substanzen in vielen technischen Prozessen verwendet werden können. Glycerin ist eine
wichtige chemische Verbindung, die beispielsweise für die Herstellung von Sprengstoffen,
als Zusatz zu Wärme-und Kraftübertragungsflüssigkeiten, als feuchtigkeitserhaltender
Zusatz zu Hautcremes, Zahnpasten, Seifen, Tabak und ähnlichem, als Textilfhilfsmittel,
als Lösungsmittel und auf vielen anderen Gebieten, die dem Fachmann bekannt sind,
verwendet werden kann.
[0036] Das erfindungsgemäße Verfahren wird durch folgende Beispiele erläutert:
Beispiel 1
[0037] Die Reaktion wurde durchgeführt in einem beheizbaren Reaktor von 800 cm
3 Inhalt, versehen mit Gaseinleitungsvorrichtung, Rührer, Innenthermometer sowie einer
Fraktionierkolonne in Form eines mit Raschigringen gefüllten Glasrohres (Länge 20
cm, Durchmesser 1,5 cm) und eines aus drei hintereinander geschalteten Vorlagen bestehenden
Vorlagensystems, in dem die flüchtigen Reaktionsprodukte kondensiert werden. In dieser
Apparatur wurden 495 g Talg (Verseifungszahl 190, Säurezahl 7,6) zusammen mit 5 g
Zink-Dodecylbenzolsulfonat als Katalysator eingebracht. Während des Aufheizens wurde
die Apparatur mit Stickstoff gespült. Anschließend wurde der Stickstoff durch Ammoniakgas
ersetzt, wobei 600 1 NH
3/kg Talg h im Kreis geführt wurden. Dabei wurde während der Reaktion laufend frisches
Ammoniakgas nachgeführt. Im Reaktor ergab sich folgender Temperaturverlauf:
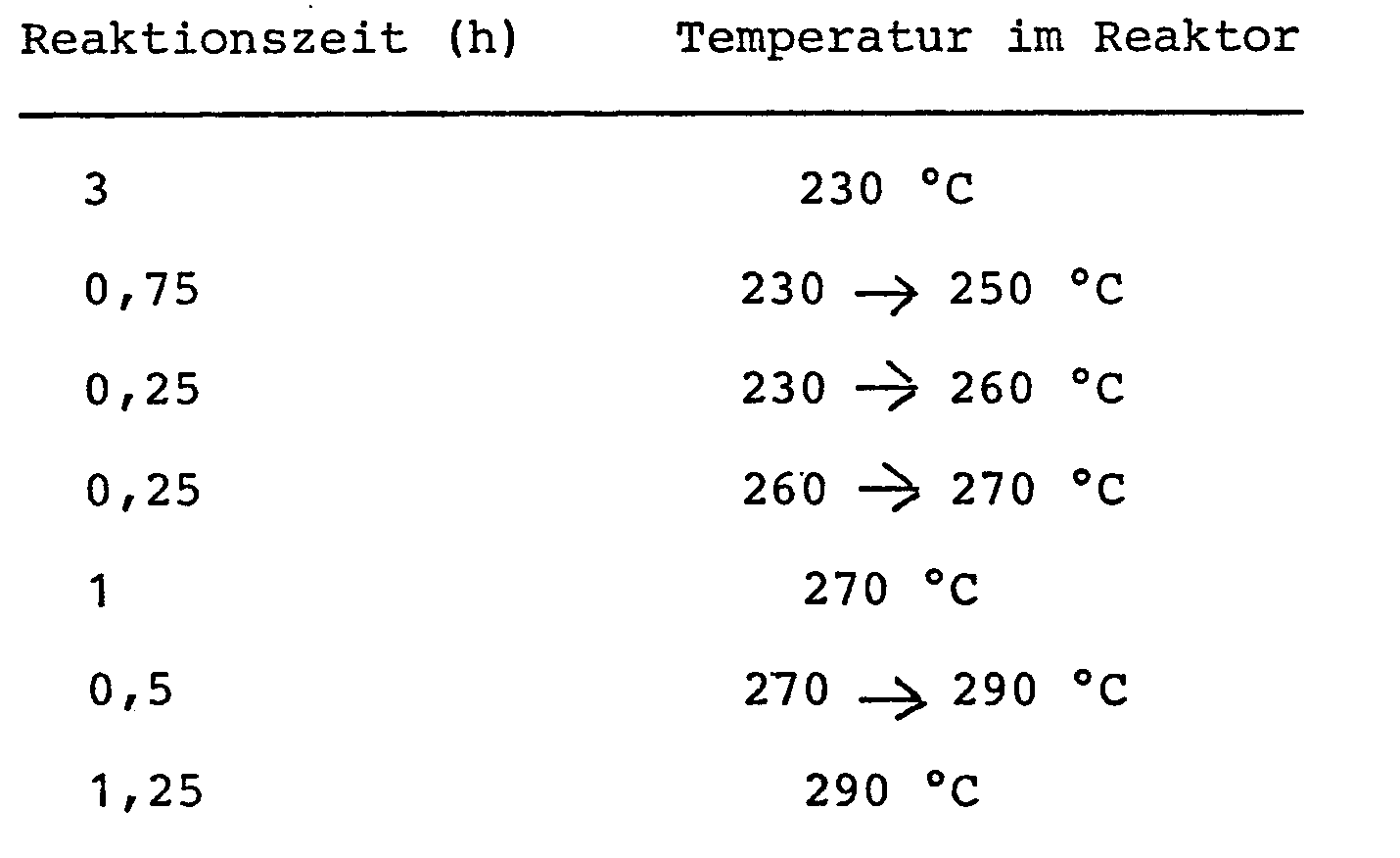
Nach einer Gesamtreaktionszeit Von 7 Stunden war die Umsetzung von Talg mit Ammoniak
beendet. Dabei wurden gebildetes Talgfettnitril und Glycerin in zwei hintereinander
geschalteten Vorlagen aufgefangen. In einer weiteren nachgeschalteten Vorlage wurde
das ammoniakalische Reaktionswasser kondensiert.
[0038] Das während der Reaktion in den beiden ersten Vorlagen gesammelte Glycerin und Talgfettnitril,
das in zwei Phasen anfällt, wurde getrennt und das Talgfettnitril mit Wasser nachgewaschen.
So erhaltenes Talgfettnitril wurde mit 93,6 % Ausbeute (413,7 g), bezogen auf Theorie,
bei 1,8 Gew.-% Amidgehalt sowie 1,5 Gew.-% Talgfettsäure und Reinglycerin nach Aufarbeitung
mit 80,2 % (39,6 g) Ausbeute isoliert. (Hier und im folgenden sind die Ausbeutenwerte
stets auf Theorie bezogen zu verstehen.)
Beispiel 2
[0039] In der in Beispiel 1 beschriebenen Apparatur wurden 495 g Rindertalg (Verseifungszahl
190, Säurezahl 1,6) zusammen mit 10 g Zink-Dodecylbenzolsulfonat vorgelegt, und es
wurde beginnend bei 230 °C, eine Menge von 600 1 NH
3/kg Talg h durch das Fett geleitet. Folgender Temperaturverlauf im Reaktor wurde eingehalten:

Die Gesamtreaktionszeit betrug 7;5 Stunden. Die in die Vorlagen ausgetragenen Reaktionsprodukte
wurden mittels Wasser ausgewaschen und aufgearbeitet. Talgfettnitril wurde in einer
Ausbeute von 92,3 % (408 g) mit einem Amidgehalt von 0,7 Gew.-% sowie einem Fettsäuregehalt
von 0,5 Gew.-% und Rohglycerin mit einer Ausbeute von 87,7 % (44,7 g) erhalten. Das
isolierte Rohglycerin enthielt nach der OH-Zahl von 1694 81,2 % Glycerin,bezogen auf
eingesetzten Talg.
Beispiel 3
[0040] In der in Beispiel 1 beschriebenen Apparatur wurden 445 g technischer Talg ("bleachable
tallow") (Verseifungszahl 186, Säurezahl 12,6) und 9 g Zink-Dodecylbenzolsulfonat
vorgelegt und unter den Reaktionsbedingungen von Beispiel 2 mit Ammoniak umgesetzt.
Die während der Reaktion innerhalb von 7,5 Stunden ausgetragenen Reaktionsprodukte
wurden vereinigt und mit Wasser Glycerin ausgewaschen. Talgfettnitril konnte nach
Abtrennung der wäßrigen Phase mit 93,0 % Ausbeute (370,4 g, Amidgehalt 0,5 Gew.-%
und Fettsäuregehalt von 0,3 Gew.-%) isoliert werden. Aus der wäßrigen Phase wurde
Rohglycerin mit 97,5 % Ausbeute (38,5 g) gewonnen. Die Ausbeute an Reinglycerin betrug
laut OH-Zahl von 1683 84,0 %, bezogen auf eingesetzten Talg.
Beispiel 4
[0041] In die in Beispiel 1 beschriebene Apparatur, die hier mit einer 70 cm-Spiegelglaskolonne
mit Raschigringen zur Fraktionierung ausgerüstet war, wurden 488 g Speisetalg (Verseifungszahl
190, Säurezahl 2,4) und 5 g Zink-Toluolsulfonat gegeben. Während des Aufheizens wurde
ein schwacher Stickstoffstrom durch den Reaktor geleitet. Bei 190 °C erfolgte die
Umstellung auf 600 1 NH
3/kg Fett h. Die Umsetzung wurde 3 Stunden bei 230 °C durchgeführt. Anschließend wurde
innerhalb einer halben Stunde von 230 °C auf 270 °C hochgeheizt und für weitere 3,25
Stunden die Temperatur bei 270°Cgehalten. Nach insgesamt 6,75 Stunden waren dann alle
flüchtigen Reaktionsprodukte aus dem Reaktor über die Kolonne augetragen.. Das im
Vorlagensystem gesammelte Glycerin/Talgfettnitril-Gemisch wurde anschließend mit Wasser
behandelt. Nach Aufarbeitung beider Phasen konnte Talgfettnitril mit einer Ausbeute
von 93,2 % (406 g, 1,7 % Amidgehalt, 0,5 Gew.-% Fettsäuregehalt) und Reinglycerin
mit einer Ausbeute von 80,1 % (40,1 g) erhalten werden.
[0042] In der gleichen Apparatur und unter den gleichen Versuchsbedingungen wurde Speisetalg
auch in Gegenwart weiterer Katalysatoren umgesetzt. Die Versuchsergebnisse sind nachfolgend
tabellarisch angegeben:
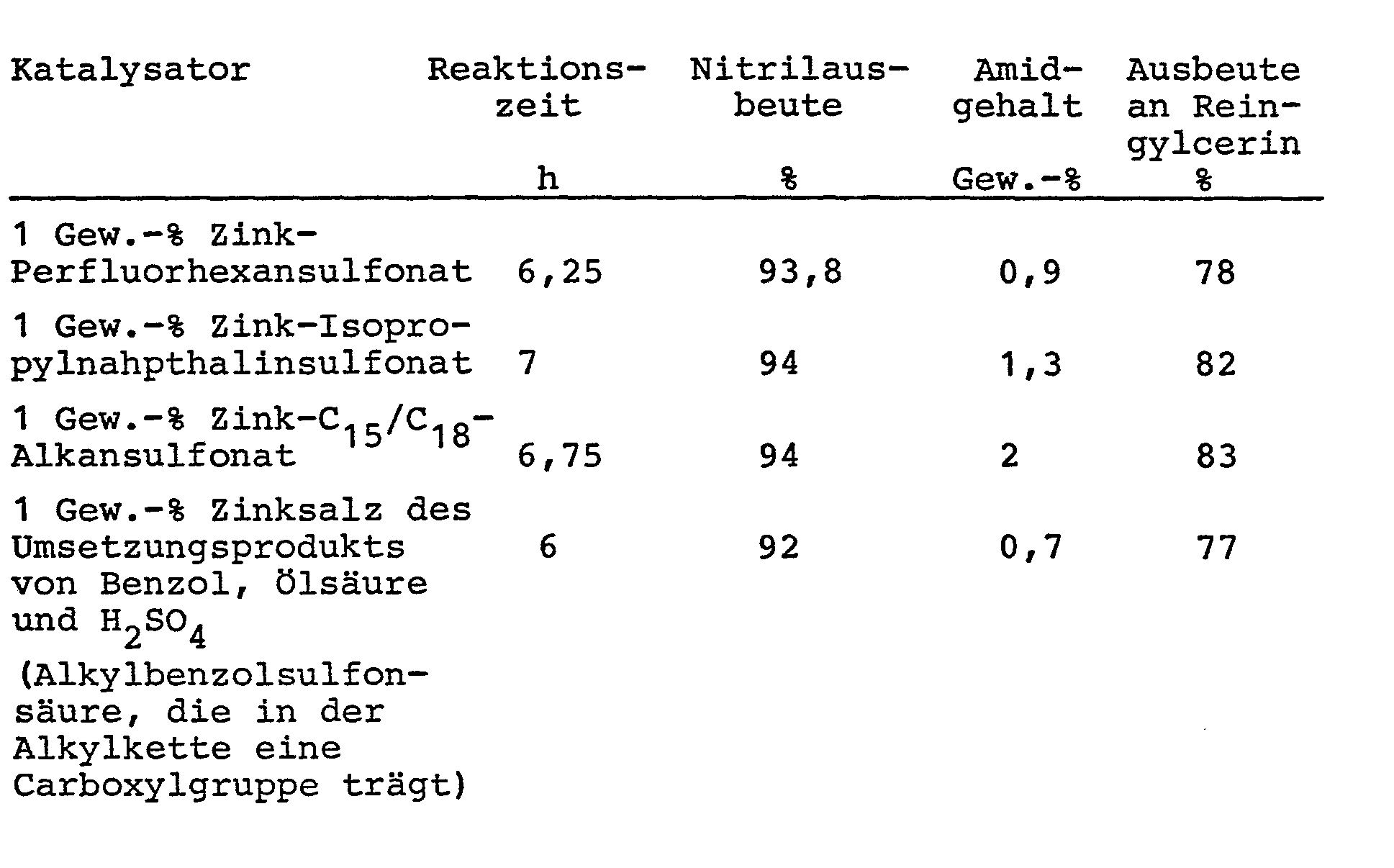
Beispiel 5
[0043] In der in Beispiel 4 beschriebenen Apparatur wurden 436 g Sonnenblumenöl (Verseifungszahl
189, Säurezahl 0,8) und 9 g Zink-Dodecylbenzolsulfonat als Katalysator unter den in
Beispiel 4 angegebenen Bedingungen (6,75 Stunden Reaktionszeit) mit Ammoniakgas (690
l/kg Fett h) umgesetzt. Nach Aufarbeiten wurden 94,6 % Fettnitril (Amidgehalt 0,5
Gew.-%, Fettsäuregehalt 0,35 Gew.-%) und 91,2 % Rohglycerin (40,9 g) bzw. laut OH-Zahl
von 1717 85,6 % Reinglycerin, bezogen auf eingesetztes öl, erhalten.
Beispiel 6
[0044] Die Herstellung von Fettsäurenitril und Glycerin direkt aus Glyceridin ist auch mittels
kontinuierlicher Fahrweise möglich. In einem beheizbaren, zylindrischen 750 ml Glasgefäß
wurden 192 g Speisetalg zusammen mit 7,5 g Zink-Dodecylbenzolsulfonat vorgelegt. Der
Reaktor war mit Rührer, Innenthermometer, beheiztem Tropftrichter und einer mit Raschigringen
gefüllten 70 cm-Spiegelglaskolonne versehen. 600 1 Ammoniak/kg Fett . h wurden mittels
Fritte bei 230 °C von unten her in den Reaktor geleitet. Unter diesen Bedingungen
wurden 1009 g Speisetalg vermischt mit 1 Gew.-% Zink-Dodecylbenzolsulfonat innerhalb
von 36 Stunden zudosiert (27 - 29 g Talg/h). Die kontinuierlich über die Kolonne ausgetragenen
flüchtigen Reaktionsprodukte wurden im Vorlagensystem kondensiert. Das anfallende
Talgfettnitril wurde mittels Wasser von Glycerin befreit. Talgfettnitril konnte mit
96,1 % Ausbeute (1033 g; 1,4 Gew.-% Amidgehalt) isoliert werden. Aus dem Wasser wurde
Rohglycerin mit 95,5 % Ausbeute (115,4 g) isoliert.
Beispiel 7
[0045] In der in Beispiel 4 beschriebenen Apparatur wurden 486 g Speisetalg (Verseifungszahl
190, Säurezahl 1,6) und 5 g Zink-Dodecylbenzolsulfonat vorgelegt. Bei ca. 270 °C wurden
konstant 500 1 NH
3/kg Fett . h durch das Reaktionsgut geleitet. Die Reaktionszeit betrug 6,5 Stunden.
Die in die Vorlagen ausgetragenen Reaktionsprodukte wurden mittels Wasser gewaschen
und aufgearbeitet. Talgfettnitril wurde in einer Ausbeute von 93,7 % (406 g) mit einem
Amidgehalt von 2,2 Gew.-% sowie einem Fettsäuregehalt von 0,4 Gew.-% und Reinglycerin
mit einer Ausbeute von 73,45 % (36,8 g), bezogen auf eingesetzten Talg, erhalten.
Beispiel 8
[0046] In die in Beispiel 4 beschriebene Apparatur wurden 486 g Talg (Verseifungszahl 187,5,
Säurezahl 11,1) und 4,25 g Zinksalz der Talgfettsäure gegeben. Während des Aufheizens
wurden 30 1 N
2/h durch den Reaktor geleitet und bei 190 °C auf 600 1 NH
3/kg Fett h umgestellt. Nach 13 Stunden war die Reaktion beendet. Dabei wurde die Reaktionstemperatur
zunächst 3 Stunden bei 230 °C und nach Aufheizen 9,5 Stunden bei 270 °C gehalten.
Die in den Vorlagen gesammelten, aus dem Reaktor ausgetragenen Talgfolgeprodukte wurden
mit Wasser gewaschen. Talgfettnitril wurde mit 84,6 %iger Ausbeute (367,8 g) und Reinglycerin
mit 60,4 %iger Ausbeute (28,3 g), bezogen auf eingesetzten Talg, isoliert.
Beispiel 9
[0047] In der in Beispiel 1 beschriebenen Apparatur und mit dem in Beispiel 4 angegebenen
Fraktioniersystem wurden 445 g Rindertalg (Verseifungszahl 186, Säurezahl 0,8) zusammen
mit 9 g Eisen-Dodecylbenzolsulfonat als Katalysator vorgelegt. Beginnend bei 230 °C
wurden 600 1 NH
3/kg Fett h durch den Talg geleitet. Die Reaktionstemperatur wurde innerhalb von 7,25
Stunden auf 290 °C gesteigert. Nach Ende der Reaktion und Aufarbeitung resultierten
364,1 g Talgfettnitril (91,4 % Ausbeute) mit einem Amidgehalt von 2,9 Gew.-% sowie
einem Fettsäuregehalt von 0,4 Gew.-% und 30,2 g Reinglycerin (67,0 % Ausbeute), bezogen
auf eingesetzten Talg.
Beispiel 10
[0048] In die in Beispiel 1 beschriebene Apparatur wurden 445 g Rindertalg (Verseifungszahl
190, Säurezahl 0,2) und 9 g Blei-Dodecylbenzolsulfonat gegeben und dann 600 1 NH
3/kg Fett. h, beginnend bei 230 °C Reaktionstemperatur, durchgeleitet. Die Reaktionstemperatur
wurde innerhalb von 7,25 Stunden kontinuierlich auf 290 °C gesteigert. Nach Ende der
Reaktion und Aufarbeitung resultierten 350,5 g (88,2 %Ausbeute) Nitril mit einem Amidgehalt
von 2,7 Gew.-% sowie einem Fettsäuregehalt von 0,35 Gew.-% und 36,5 g Reinglycerin
(78,9 % Ausbeute).
Beispiel 11
[0049] In der in Beispiel 1 beschriebenen Apparatur wurden 445 g Sojaöl (Verseifungszahl
203,2) zusammen mit 9 g Zink-Dodecylbenzolsulfonat vorgelegt. Beginnend bei 230 °C
wurden 600 1 NH
3/kg Fett . h durch das öl geleitet. Innerhalb von 7,25 Stunden wurde die Reaktionstemperatur
auf 290 °C gesteigert. Nach Ende der Reaktion und Aufarbeitung wurden 363,3 g Sojanitril
(92,2 % Ausbeute) mit einem Amidgehalt von 0,7 Gew.-% sowie einem Fettsäuregehalt
von 0,7 Gew.-% und 36,0 g Reinglycerin (Ausbeute 72,8 %, bezogen auf eingesetztes
öl) erhalten.
Beispiel 12
[0050] In der in Beispiel 1 beschriebenen Apparatur wurden 445 g Rindertalg (Verseifungszahl
192, Säurezahl 0,25) und 9 g Cadmium-Dodecylbenzolsulfonat vorgelegt. Beginnend bei
230°C wurden 600 1 NH
3/kg Fett . h durch das Fett geleitet. Innerhalb von 6,5 Stunden wurde die Reaktionstemperatur
auf 290°C gesteigert. Nach Ende der Reaktion und Aufarbeitung wurden 373,6 g Talgfettnitril
(94,2 % Ausbeute) mit einem Amidgehalt von 2 Gew.-% sowie einem Fettsäuregehalt von
0,7 Gew-% und 75,2 % Ausbeute an Reinglycerin (35,1 g) erhalten.
Beispiel 13
[0051] In der in Beispiel 1 beschriebenen Apparatur wurden 445 g Rindertalg (Verseifungszahl
192) und 9 g Kobalt-Dodecylbenzolsulfonat vorgelegt. Beginnend bei 230 °C wurden 600
1 NH
3/kg Fett h durch das Fett geleitet. Innerhalb von 7,25 Stunden wurde die Reaktionstemperatur
auf 290 °C gesteigert. Nach Ende der Reaktion und Aufarbeitung resultierten 373 g
(94 % Ausbeute) Talgnitril mit einem Amidgehalt von 4,9 Gew.-% sowie einem Fettsäuregehalt
von 0,8 Gew.-% und eine Rohglycerinausbeute von 86,4 % (40,3 g).
Beispiel 14
[0052] In der in Beispiel 1 beschriebenen Apparatur, die jedoch anstelle einer Fraktioniereinheit
mit einem direkten Übergangsstück vom Reaktor zum Vorlagensystem ausgerüstet war,
wurden 486 g Speisetalg, (Verseifungszahl 187, Säurezahl 0,8) zusammen mit 1 Gew.-%
Zink-Dodecylbenzolsulfonat, bezogen auf Talg, vorgelegt. Während der Umsetzung wurden
600 1 NH
3/kg Fett - h durch das Reaktionsgut geleitet. Es wurde dabei die Temperatur 3 Stunden
bei 230 °C und nach Aufheizen (0,5 Stunden) 1,25 Stunden bei 270 °C gehalten. Nach
insgesamt 4,75 Stunden war die Reaktion beendet. Die bei 230 °C und 270 °C in die
Vorlagen ausgetragenen Reaktionsprodukte wurden jeweils getrennt gesammelt und aufgearbeitet.
Das bei 230 °C isolierte Fettsäurenitril besaß einen Amidgehalt von 20 Gew.-%. Bei
270 °C wurde ein Amidgehalt von etwa 9 Gew.-% beobachtet. Der Amidgehalt im gesamten
Fettsäurenitril war 10 Gew.-%.
Beispiel 15
[0053] In der in Beispiel 1 beschriebenen Apparatur, die jedoch anstelle einer Fraktioniereinheit
mit einem direkten Übergangsstück vom Reaktor zum Vorlagensystem ausgerüstet war,
wurden 500 g Talg (Verseifungszahl 189, Säurezahl 0,9) zusammen mit 2 Gew.-% Zink-Dodecylbenzolsulfonat,
bezogen auf Talg, vorgelegt. Während der Umsetzung wurden 600 1 NH
3/kg Fett h durch das Reaktionsgut geleitet. Es wurde dabei die Temperatur 3 Stunden
bei 230 °C gehalten und danach um 10 °C und nach je einer halben Stunde um weitere
10 °C erhöht. Bei 280 °C war die Reaktion beendet. Die Reaktionszeit betrug 5,25 Stunden.
Das gesamte Kondensat wurde mittels Wasser bei 80 °C in Fettsäurenitril und Glycerin/Wasser
aufgetrennt. Das isolierte Fettsäurenitril besaß einen Amidgehalt von 5,3 Gew.-% und
einen Fettsäuregehalt von 0,5 Gew.-%. Die Nitrilausbeute betrug 95,2 %. Nach Aufarbeiten
konnte Reinglycerin mit einer Ausbeute von 91,4 % gewonnen werden.
Beispiel 16
[0054] In einem beheizbaren Reaktor, der mit einem Gaseinleitungsrohr, einem Rührer und
einem Innenthermometer ausgerüstet ist und dem ein Vorlagesystem (Kondensationssystem
aus einer oder mehreren Vorlagen, Behältern) angegliedert ist, wurden 500 g technischer
Talg (Verseifungszahl 191,4, Säurezahl 1,5) zusammen mit 2 Gew.-% Zink-Dodecylbenzolsulfonat,
bezogen auf Talg, vorgelegt. Nun wurde auf 230 °C erhitzt und 600 1 Ammoniak pro kg
Fett h durch das Reaktionsgut geleitet. Die Temperatur wurde 3 Stunden bei 230 °C
gehalten und anschließend kontinuierlich innerhalb von 1,5 Stunden auf 260 °C erhöht.
Nach insgesamt 4,5 Stunden war der Austrag an Glycerin beendet und zusätzlich etwa
die Hälfte an Roh-Fettsäurenitril ausgetragen. An dieser Stelle der Umsetzung wurde
der Ammoniakdurchsatz auf 60 l/kg Reaktionsgut . h reduziert und die Reaktionstemperatur
gleichzeitig auf 290 °C gesteigert. Während des Aufheizens wurde die Wasserwäsche
desglycerinhaltigen Rohnitrils durchgeführt, das dann, von Glycerin befreit, in den
290 °C heißen Reaktor zurückgeführt wurde. Nach einer Reaktionszeit von insgesamt
6,5 Stunden (Nachreaktion 2 Stunden) wurde das Talgfettnitril abgelassen und durch
Destillation vom Katalysator befreit. Es wurden 417 g (93,2 % Ausbeute) Talgfettnitril
mit einem Amidgehalt unter 0,05 Gew.-% sowie einer Säurezahl von 0,1 und (laut OH-Zahl)
42,9 g Reinglycerin (82,7 % Ausbeute) erhalten.
Beispiel 17
[0055] In der in Beispiel 1 beschriebenen Apparatur wurden 500 g technischer Talg (Verseifungszahl
191,4, Säurezahl 1,5) zusammen mit 2 Gew.-% Zink-Dodecylbenzolsulfonat, bezogen auf
Talg, vorgelegt. Während der Umsetzung wurden 600 1 Ammoniak pro kg Fett und Stunde
durch das Reaktionsgut geleitet, wobei die Temperatur 3 Stunden bei 230 °C gehalten
und anschließend kontinuierlich innerhalb von 2,25 Stunden bis auf 280 °C erhöht wurde.
Die Gesamtreaktionszeit betrug 5,25 Stunden. Während der Umsetzung wurde darauf geachtet,
daß das Temperaturgefälle zwischen Sumpf und Übergang möglichst gering war. Das erhaltene
Kondensat wurde in Roh-Fettsäurenitril und Glycerin mittels Wasserwäsche aufgetrennt.
[0056] Die isolierten 432,8 g Roh-Fettsäurenitril (Amidgehalt 6,1 Gew.-%) wurden in einem
Reaktor, versehen mit Gaseinleitungsrohr, Rührwerk, Innenthermometer und Kondensationssystem,
vorgelegt und 2 Gew.-% Zink-Dodecylbenzolsulfonat dazugegeben. Durch das Reaktionsgemisch
wurden 60 1 Ammoniak pro kg Reaktionsgut . h bei 290 °C durchgeleitet. Gebildetes
Reaktionswasser wurde dabei ausgetragen. Die Reaktionszeit betrug 1 Stunde. Nach Destillation
des Reaktorinhalts lagen 415 g Talgfettnitril (93,1 % Ausbeute) mit einem Amidgehalt
unter 0,05 Gew.-% und einer Säurezahl von 0,1 vor. Reinglycerin (laut OH-Zahl) wurde
47,3 g (91,2 % Ausbeute) erhalten.
Vergleichsbeispiel (analog GB-PS 451,594)
[0057] Durch ein mit 800 cm
3 gekörntem Alumiumoxid gefülltes Glasrohr wurden von unten bei 320 bis 360 °C gemeinsam
300 1 NH
3/1 Katalysator h und 50 g Rindertalg pro Stunde durchgesetzt. Insgesamt wurden 1342
g Rindertalg zudosiert. Die flüchtigen Reaktionsprodukte, die oben aus dem Reaktor
austraten, wurden in einem Vorlagensystem aufgefangen und nach ihrer Vereinigung mit
Wasser gewaschen. Es wurden 1191 g rohes Talgfettnitril (Ausbeute 99 %) erhalten,
jedoch von schlechter Qualität (schwarz gefärbt und stechender Geruch). Glycerin konnte
nicht nachgewiesen werden.Theoretisch waren 140 g Glycerin zu erwarten.