[0001] This invention relates to a moist packaged towelette and to a method of making the
same.
[0002] Moist packaged towelettes are generally made by coating a sheet of nonwoven fabric,
usually absorbent paper, with a binder and storing the coated fabric in contact with
an aqueous solution in a container. The aqueous solution typically contains alcohol
and, for example, a perfume or deodorant. The binder increases the structural integrity
of the nonwoven fabric and prevents it disintegrating in the aqueous solution. (For
the avoidance of doubt the term "nonwoven fabric" as used herein includes fabrics
comprising carded or randomly orientated or cross-laid fibres. The fibres may comprise,
for example, natural or regenerated cellulose, other synthetic or proteinaceous fibres
of biodegrade materials, or mixtures of these).
[0003] Various binders have been proposed but all which are known to us have the disadvantage
that the coated fabric maintains a high structural integrity even after prolonged
exposure to water. This can result in blocked drains.
[0004] One known binder for nonwoven fabrics which are not intended to be exposed to moisture
is polyvinyl alcohol. Whilst nonwoven fabrics provided with this binder have excellent
structural integrity in the dry they disintegrate rapidly when immersed in water.
[0005] We have discovered that a nonwoven fabric provided with a binder comprising polyvinyl
alcohol will retain a high structural integrity in contact with an aqueous solution
provided that the aqueous solution contains a sufficient concentration of a compound
to prevent the polyvinyl alcohol dissolving in the aqueous solution. When the solution
is diluted the polyvinyl alcohol dissolves thereby weakening the structural integrity
of the towelette.
[0006] Accordingly, the present invention provides a moist packaged towelette comprising
a sheet of nonwoven fabric provided with a binder and maintained in contact with an
aqueous solution in a container characterized in that said binder is polyvinyl alcohol
and said aqueous solution contains a compound which is present in said solution at
a sufficient concentration to prevent said polyvinyl alcohol dissolving in said aqueous
solution but which, when diluted in excess water, permits said polyvinyl alcohol to
dissolve in said excess water thereby reducing the structural integrity of said towelette.
[0007] Compounds which will prevent polyvinyl alcohol dissolving in aqueous solutions are
well known and examples are listed in "Polyvinyl Alcohol", 1973; Finch C.A., John
Wiley & Sons Ltd., Table 2.3 at page 40. Substantially all of these compounds (which
comprise boric acid and water soluble'salts) will, when dissolved in excess water,
permit the polyvinyl alcohol to dissolve thereby reducing the structural integrity
of the nonwoven fabric. It is, of course, a simple procedure to check if a particular
compound is suitable.
[0008] Of the available compounds boric acid is presently preferred and preferably comprises
at least 1% (by weight) of the aqueous solution with 3% to 5% (by weight) being preferred
and 4% to 5% (by weight) being more preferred.
[0009] One of the problems associated with using a water soluble salt as the compound is
that the required concentration in the aqueous solution is so high that, in many cases,
the salt crystalizes on the skin when the towelette is used. We strongly recommend
that the salts which are used should be those which need be present to no more than
40% (by weight) of the aqueous solution and, more preferably, to no more than 20%
(by weight) of the aqueous solution.
[0010] If a salt is to be used then we recommend sodium sulphate at a concentration of between
3% and 20% (by weight) of the aqueous solution and more preferably between 7% and
20% (by weight) of the aqueous solution.
[0011] Polyvinyl alcohol is generally produced by the hydrolysis of polyvinyl acetate. Pure
polyvinyl alcohol (i.e. 100% hydrolysed polyvinyl acetate) is relatively insoluble
in water at room temperature when compared with 80% to 99% hydrolysed polyvinyl acetate.
Accordingly, the binder preferably comprises a mixture of polyvinyl alcohol and polyvinyl
acetate. If desired the polyvinyl alcohol may comprise as little as 1% (by weight)
of such a mixture although it preferably comprises between 80% and 95% thereof.
[0012] Mixtures (emulsions) comprising vinyl acetate-ethylene copolymers and polyvinyl alcohol
may also be used as a binder. In such a case the polyvinyl alcohol preferably comprises
from 1% to 10% (by weight) of the binder and probably acts as a protective colloid.
If desired the binder may also contain polyvinyl acetate and preferably between 5
and 25% .(by weight) thereof. One particularly preferred range of binders comprises
(by weight) 1 to 10% of 80 - 90% hydrolysed polyvinyl acetate and the balance vinyl
acetate-ethylene copolymers. Preferably the vinyl acetate-ethylene copolymers contain
(by weight) not more than 45% vinyl acetate and not more than 60% ethylene.
[0013] In all the above cases the weight of the binder is preferably between 5% and 50%
of the weight of the untreated nonwoven fabric.
[0014] The present invention also provides a method for making a moist packaged towelette
which method comprises the step of wetting a sheet of nonwoven fabric provided with
a binder by bringing said sheet into contact with an aqueous solution characterized
in that said binder comprises polyvinyl alcohol and said aqueous solution contains
a sufficient concentration of a compound which prevents the polyvinyl alcohol dissolving
in the aqueous solution but which, when dissolved in excess water, allows the polyvinyl
alcohol to dissolve in the water thereby reducing the structural integrity of the
towelette.
[0015] The present invention also provides a method for making a moist packaged towelette
which method comprises taking a sheet of nonwoven fabric which has been provided with
a binder and packaging said sheet of treated material in contact with an aqueous solution
in a container characterized in that said binder comprises polyvinyl alcohol and said
aqueous solution contains a sufficient concentration of a compound which prevents
the binder from dissolving in the aqueous solution but which, when dissolved in excess
water, allows the binder to dissolve in the water thereby reducing the structural
integrity of the towelette.
[0016] Preferably said compound is boric acid and advantageously said aqueous solution comprises
at least 1% (by weight) of said compound with 3% to 5% (by weight) being preferred
and 4% to 5% (by weight) being more preferred.
[0017] The container should preferably be impermeable to all the components of the aqueous
solution. However, for economic reasons a container need only be sufficiently impermeable
to the components of the aqueous solution for a limited period of time, for example,
the anticipated time delay between manufacture and use. The container itself may be
in the form of a sachet for accommodating a single towelette or a bag or box for accomodating
a plurality of towelettes. In the latter cases the bags or boxes are preferably resealable
tj2 minimise evaporation of the aqueous solutions.
[0018] The binder may conveniently be applied to the nonwoven fabric by making an aqueous
solution (or emulsion) of the binder and applying it to the fabric by, for example,
a roller or a spray gun. Alternatively, the nonwoven fabric may simply be dipped in
the aqueous solution (or emulsion).
[0019] Once treated the nonwoven fabric is preferably dried, and is then cut and, if desired,
folded. The nonwoven fabric may then either be wetted by the aqueous solution and
inserted in a container or inserted in a container and wetted. It should be understood
that it is not essential to dry the nonwoven fabric after the application of the binder
although drying is preferred for ease of handling.
[0020] For a better understanding of the invention reference will now be made to the following
non-limiting examples.
EXAMPLE 1
[0021] A sheet of 24 pound (25 x 38 inch - 500
'ream) (10.9 Kg - 27.7 96.5 cm) high groundwood, unsized paper was immersed in water
for two minutes. The wet sheet was found to have a tensile strength of approximately
0.59 pounds (0.27 Kg).
EXAMPLE 2
[0022] A sheet of the same paper used in Example 1 was impregnated with a solution of VINOL
(Trade Mark) 205 polyvinyl alcohol (PVOH) to the extent of 4 pounds (1.80 Kg) dry
add-on and dried in a 120°C forced air oven. After immersion in water for two minutes
the wet sheet was found to have a tensile strength of 0.59 pounds (0.27 Kg), i.e.
approximately equal to the wet sheet in Example 1. (VINOL 205 is 87% to 89% hydrolysed
polyvinyl acetate of low viscosity (4-6 cps) marketed by Applicants).
EXAMPLE 3
[0023] Two sheets of paper were prepared and dried as in Example 2. However, instead of
immersion in water both sheets were immersed in an aqueous solution containing 5%
(by weight) boric acid at room temperature.
[0024] After immersion for two minutes one wet sheet was tested and found to have a tensile
strength of 1.6 pounds (0.73 Kg), i.e. nearly 3 times the tensile strength in Example
1 and 2.
[0025] The other wet sheet was then immersed in a large quantity of water for a further
two minutes and when tested was found to have a wet tensile strength of less than
0.8 pounds (0.365 Kg).
EXAMPLE 4
[0026] A sheet of paper was prepared and dried as in Example 2. The sheet was then immersed
in an aqueous solution containing 5% (by weight) boric acid at room temperature for
1 year. On removal from the solution there was no detectable reduction in tensile
strength as measured by finger pull.
EXAMPLE 5
[0027] In order to determine the probable shelf life of the packaged towelette films of
15 ml. (0.038 cm) wet thickness were separately cast from VINOL 205 and VINOL 540
PVOH and dried at .room temperature. Strips of the films of 1 x 6 inches (2.54 x 15.24
cm) were then immersed in an aqueous solution containing 5% (by weight) boric acid
at various temperatures. The probable shelf life of the packaged towelette at various
temperatures is indicated in Table 1.
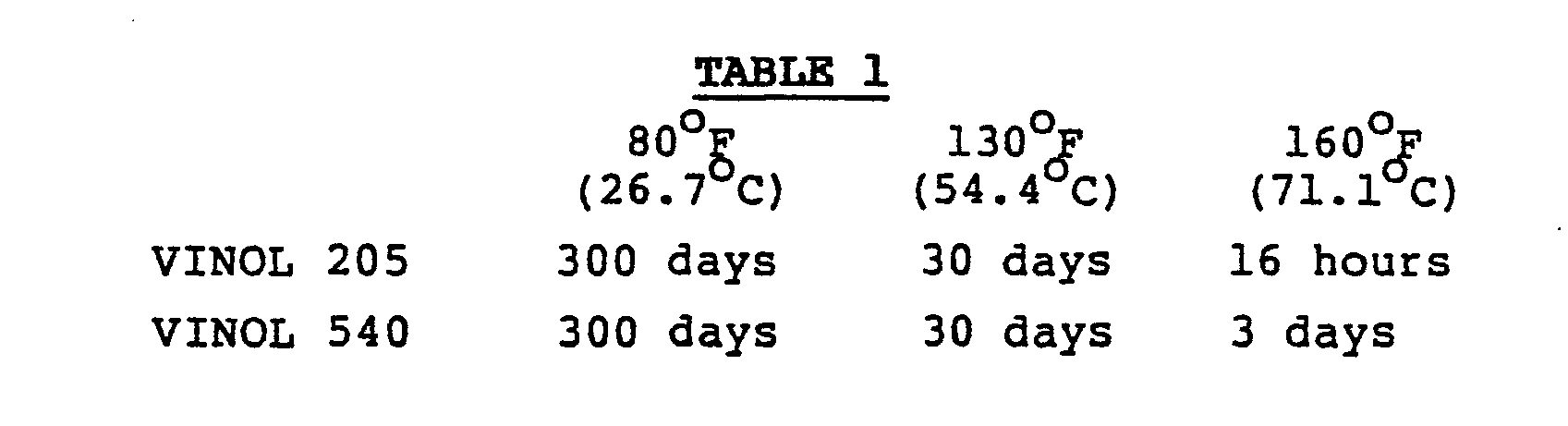
[0028] In contrast all the films dissolved within 5 minutes when immersed in ordinary water.
(VINOL 540 is 87% to 89% hydrolysed polyvinyl acetate of high viscosity (40 - 50 cps)
marketed by Applicants). 80% hydrolysed PVOH is commonly known to have reverse solubility,
i.e. is insoluble in water above 20°C but is soluble at room temperature. For this
reason towelettes should advantageously be coated with this material for use in high
temperature atmospheres.
EXAMPLE 6
[0029] A high groundwood stock paper substrate (24 pound/3300 ft. 2 = 10.9 Kg/307 sq. meters)
was treated with a 15% aqueous solution of VINOL 205 PVOH applied with a No. 10 Mayer
rod separately to each side of the paper and dried at 250°F ( 120°C) for 30 seconds.
The coated first side was dried before applying the coat- . ing to the other side.
[0030] The dried paper was then immersed for two minutes in a 5% boric acid solution and
its wet tensile strength determined by Instron (C) and compound with that of the base
stock (A) and the coated sheet without boric acid (B). The results are reported in
Table 2 below. The resolubility was demonstrated by further immersion of the boric
acid treated sheet in plain water for two minutes (D).
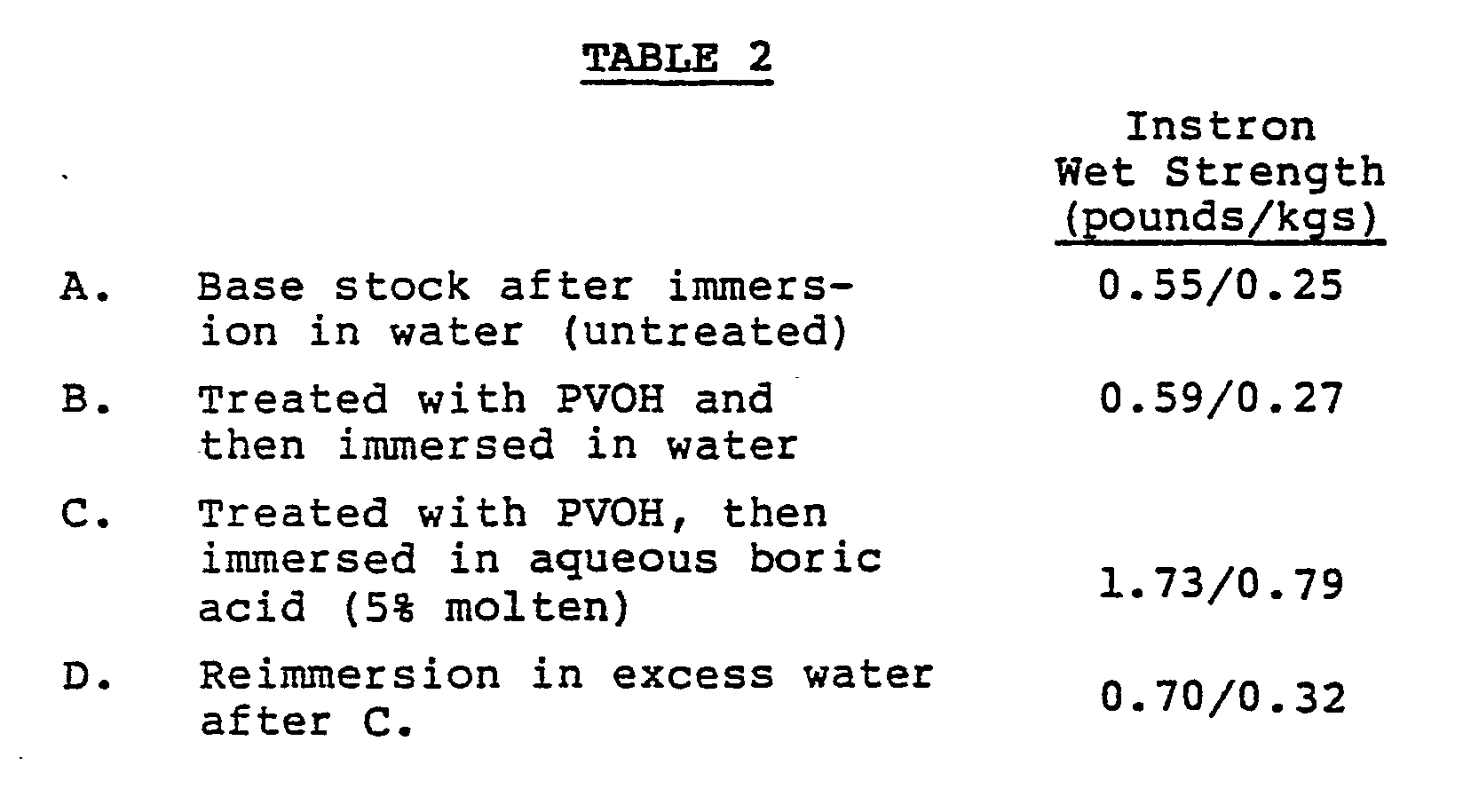
EXAMPLE 7
[0031] Further studies were carried out to determine the effect of boric acid concentration
on the wet tensile strength of PVOH in pregnated papers. These studies were made on
paper sheets of a 42 pound/3300 sq. ft. stock (19 kg/307 sq. meters) each respectively
immersed in boric acid solution of successively increasing concentrations. It was
found that the wet tensile strength increased almost linearly with concentration from
0.72 pounds (~ .33 kg) at zero boric acid to 1.41 pounds (
~ 0.64 kg) at 5% boric acid.
EXAMPLE 8
[0032] Papers treated with other grades of polyvinyl alcohol were tested to determine the
effect of boric acid in inhibiting disintegration. These included commercial grades
identified as:
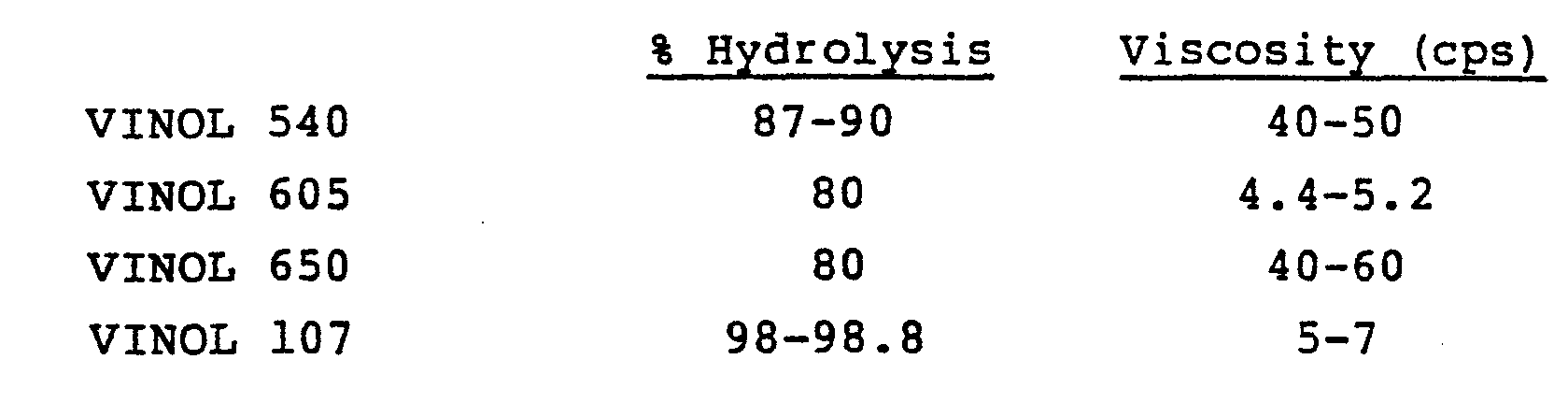
[0033] Each of these VINOL compositions were applied to a 24 lb./3300 ft.
2 (10.9 Kg/307 sq. meters) base stock and dried at 250°F (120°C) for 30-90 seconds,
as required. The amount of PVOH add-on varied due to viscosity differences so that
the measured wet tensile values are not directly relatable between the grades.
[0034] All of these PVOH treated sheets exhibited wet tensile improvement with 5% boric
acid immersion versus water immersion and all showed resolubility in plain water after
short immersion in boric acid solution, as shown in Table 3.
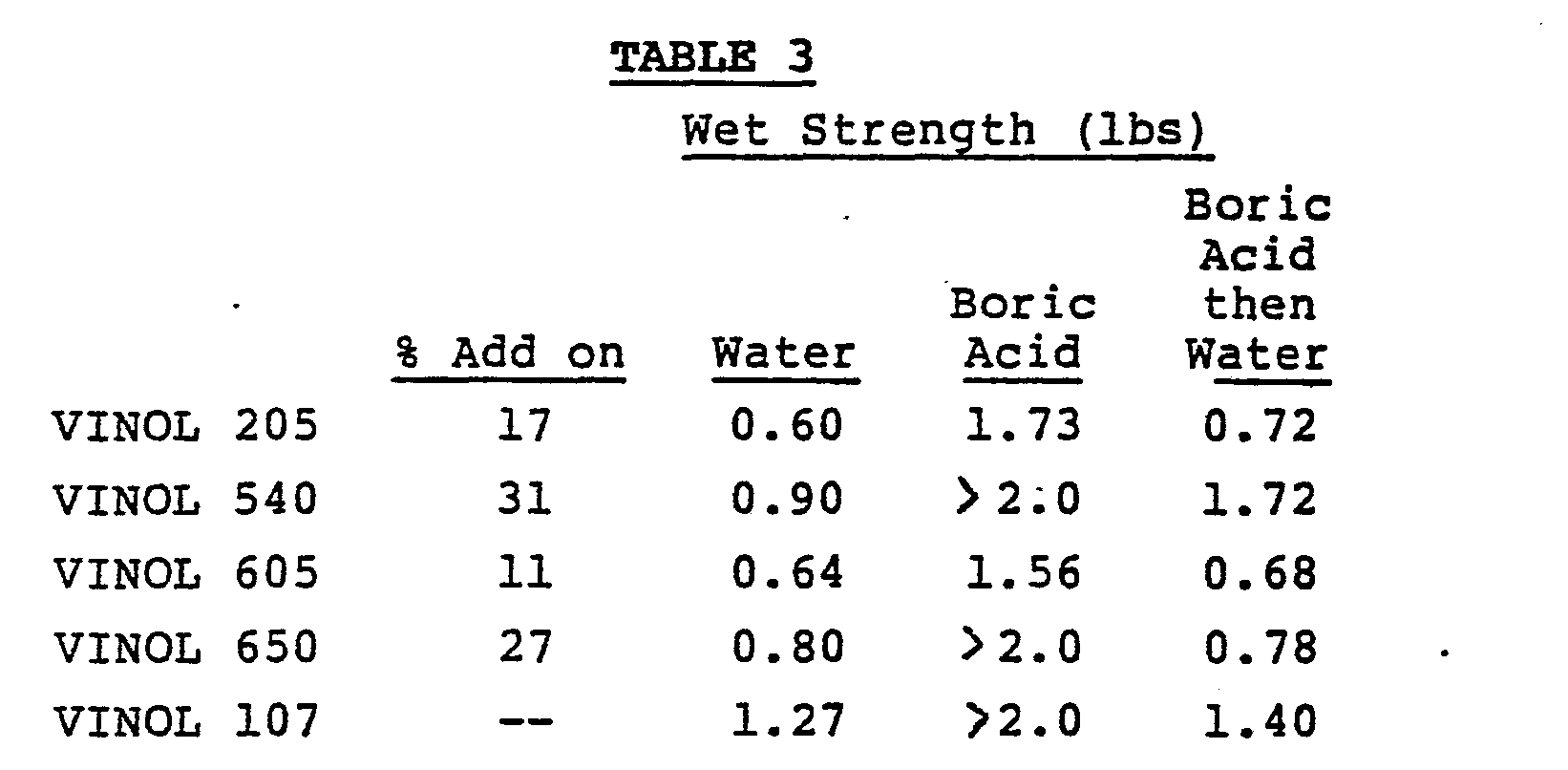
EXAMPLE 9
[0035] The water soluble salts listed in Table 4 below are believed to be suitable substitutes
in place of boric acid, (which is also listed for comparison) at concentrations of
up to 20% (by weight) in the articles of this invention. Table 4 shows the minimum
concentration causing precipitation of the compound dissolved in a 5% solution of
polyvinyl alcohol (98-99% hydrolysed, degree of polymerization 1700-1800).
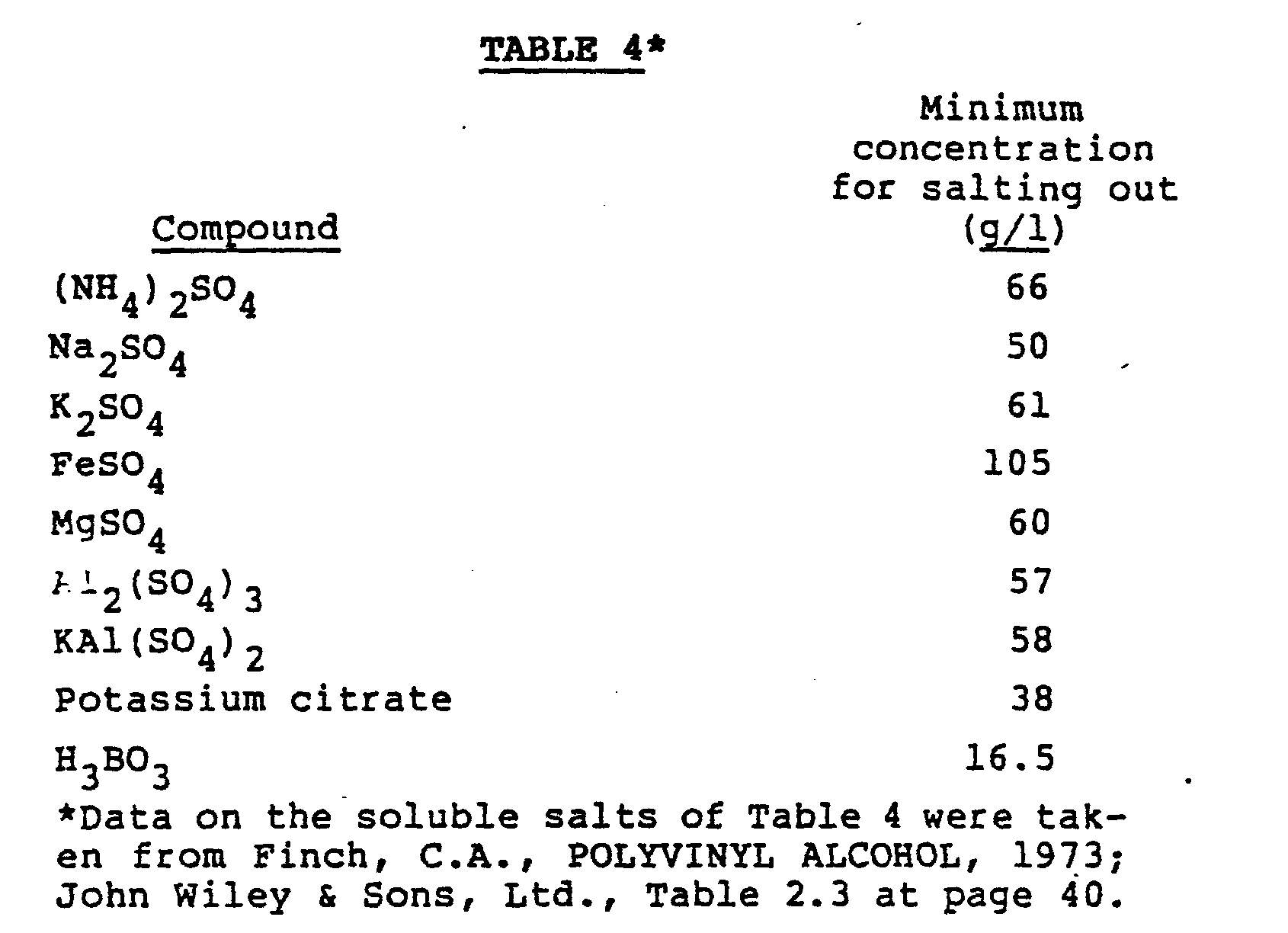
EXAMPLE 10
[0036] Cast films of VINOL 205 PVOH (1" x 6" = 2.5 x 15.24 cm) were separately tested to
determine solubility respectively in boric acid solutions and in sodium sulphate solutions
at different concentrations. The results are reported in Table 5.
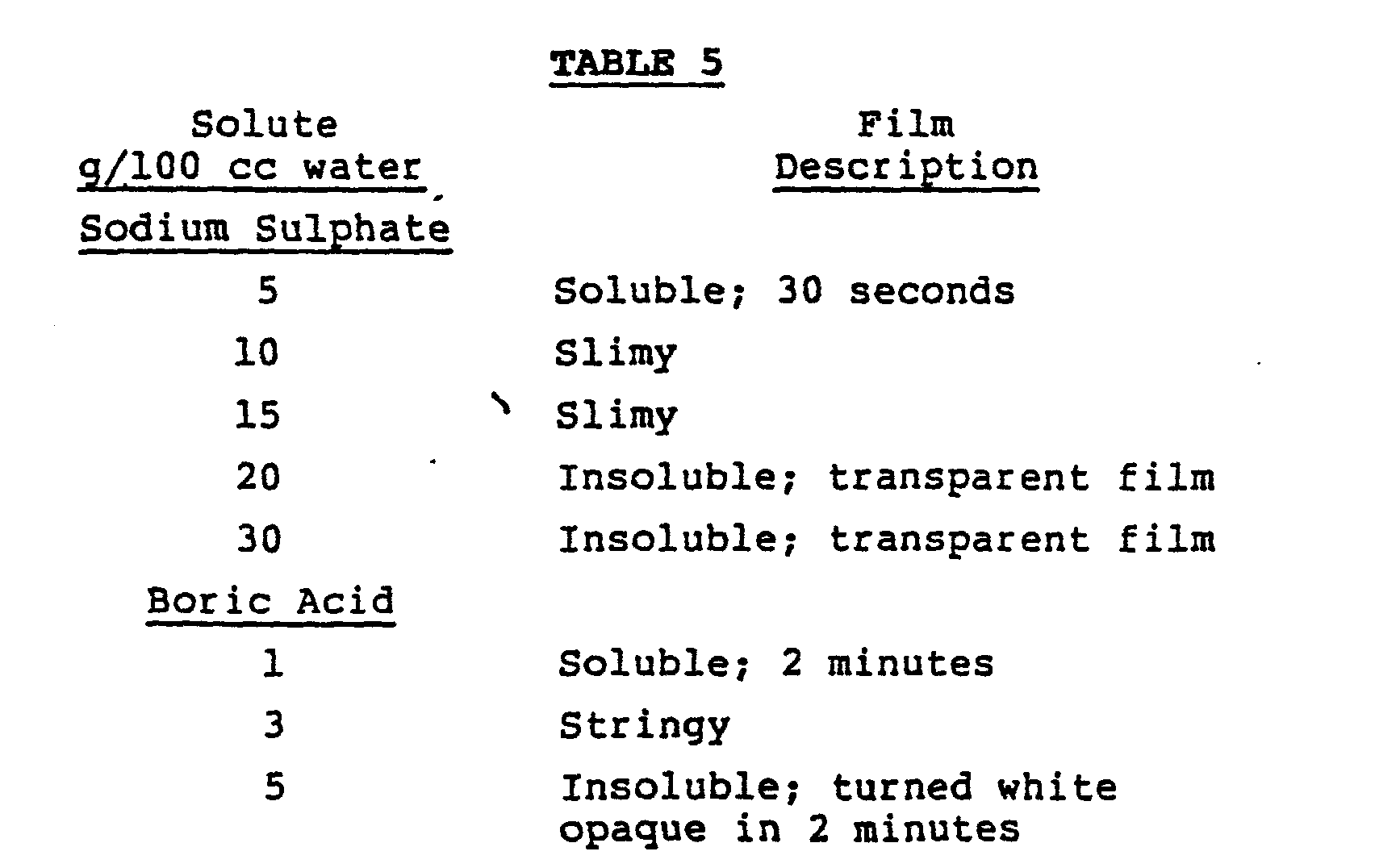
[0037] From the foregoing tests it appears that while the soluble salts listed in Table
4 above, such as sodium sulphate, can be employed to retard solubilization of polyvinyl
alcohol films, greater concentrations i.e. about 7% to about 20%, are required than
when using boric acid.
[0038] As projected from the data set forth in Tables 4 and 5, potassium citrate appears
to be even more efficient than sodium sulphate.
[0039] The specific behaviour of boric acid in retaining solubilization of PVOH film is
not attributable to the pH of the boric acid solution. Whereas a VINOL 205 film was
insoluble in 5% boric acid solution, such film was readily dissolved respectively,
in 5% aqueous solution of citric and phosphoric acid and a 0.7% solution of fumaric
acid.
EXAMPLE 11
[0040] A 60% vinyl acetate-40% ethylene copolymer emulsion containing 4% PVOH (75% VINOL
205 and 25% VINOL 523) (by weight) of the copolymer, and containing a total of 52%
solids was cast to form a film of 15 mil wet thickness and air dried. While the film
retained its definition when immersed in water, it exhibited practically no wet tensile
strength as evidenced by the fact that it could not suspend its own weight.
[0041] When immersed in a 5% boric acid solution, the film exhibited surprisingly good wet
tensile strength and was highly elastic. However, this film removed from the boric
acid solution was redispersed in plain water in less than two minutes.
[0042] The treated film in contact with boric acid solution retained wet tensile strength
for more than 30 days at 130°F (54.4°C). At 160°F (71.1°C) the film retained wet tensile
strength for 3 days indicating excellent film stability and shelf life at the elevated
temperature that may be experienced under storage conditions.
EXAMPLE 12
[0043] The same emulsion as employed in Example 11 was diluted and applied to a paper substrate.
[0044] The emulsion was diluted with water to a 25% total solids content and applied to
both sides of a 42 pound/3300 square foot (19 Kg/307 mg/square meters) paper substrate,
and the treated paper dried at 120°C in a forced air oven. The pick-up was 3.5 pounds
(1.59 Kg) dry emulsion.
[0045] A sample of the dried emulsion treated paper, as determined by conventional Instron
test, showed a wet tensile strength after immersion in water, of 1.08 pounds (0.49
Kg) as compound to the untreated stock which showed a wet tensile of 0.72 pounds (0.33
Kg).
[0046] A duplicate sample of the dried emulsion treated paper immersed in 5% boric acid
solution for 2 minutes when tested by Instron exhibited a tensile of 1.41 pounds (0.64
Kg). When reimmersed in plain water for 2 minutes, the paper returned to about its
initial wet strength, 1.09 pounds (0.49 Kg).
[0047] Another duplicate sample of the dried emulsion treated paper was immersed in 5% boric
acid solution for 30 minutes maintained about the same tensile strength as that previously
shown for the boric acid treatment while the water value on reimmersion decreased
to 0.91 pounds (0.41 Kg).
[0048] It should be noted that the paper in the foregoing example had a relatively low dried
emulsion add-on. At higher add-on levels or lower basis weight substrate greater relative
increase in tensile strength may be realized.
EXAMPLE 13
[0049] While in Example 10 and 11 boric acid is employed as the agent for increasing the
wet strength of the nonwoven fiber sheet during storage and use, certain soluble salts
known to react with polyvinyl alcohol to effect precipitation or gelling thereof,
may be employed. These are less preferred than boric acid, however, since larger concentrations
of these are required for the desired purpose. Examples of such salts are set out
in Table 4 hereinbefore.
EXAMPLE 14
[0050] Cast films of the same emulsion as employed in Example 11 (1" x 6" = 2.5 x 15.24
cm) were separately tested to determine solubility respectively in boric acid solutions
and in sodium sulphate solutions at different concentrations. The results are reported
in Table 2.

[0051] From the foregoing results, it appears that while the soluble salts, such as sodium
sulphate, can be employed to retard solubilization of polyvinyl acetate films, somewhat
greater concentrations, i.e. about 3% to about 20%, are required than when using boric
acid.
1. A moist packaged towelette comprising a sheet of nonwoven fabric provided with
a binder and maintained in contact with an aqueous solution in a container characterized
in that said binder is polyvinyl alcohol and said aqueous solution contains a compound
which is present in said solution at a sufficient concentration to prevent said polyvinyl
alcohol dissolving in said aqueous solution but which, when diluted in excess water,
permits said polyvinyl alcohol to dissolve in said excess water thereby reducing the
structural integrity of said towelette.
2. A moist packaged towelette according to Claim 1, characterized in that said compound
is boric acid.
3. A moist packaged towelette according to Claim 2, characterized in that said boric
acid comprises at least 1% (by weight) of said aqueous solution.
4. A moist packaged towelette according to Claim 3, characterized in that said boric
acid comprises 3% to 4% (by weight) of said aqueous solution.
5. A moist packaged towelette according to Claim 4, characterized in that said boric
acid solution comprises 4% to 5% (by weight) of said aqueous solution.
6. A moist packaged towelette according to any preceding Claim, characterized in that
said compound comprises a water soluble salt and said aqueous solution contains from
3% to 20% (by weight) of said salt.
7. A moist packaged towelette according to Claim 6, characterized in that said salt
is sodium sulphate.
8. A moist packaged towelette according to any preceding Claim, characterized in that
said binder comprises polyvinyl acetate.
9. A moist packaged towelette according to Claim 8, characterized in that said binder
comprises between 80% and 99% (by weight) polyvinyl alcohol.
10. A moist packaged towelette according to Claim 8, characterized in that said binder
comprises vinyl acetate-ethylene copolymer.
11. A moist packaged towelette according to Claim 10, characterized in that said vinyl
- acetate-ethylene copolymers comprises from 10% to 40% (by weight) vinyl acetate.
12. A moist packaged towelette according to Claim 10 or 11 when appended to Claim
8, characterized in that said binder comprises from 1% to 10% (by weight) polyvinyl
alcohol.
13. A method for making a moist packaged towelette which method comprises the step
of wetting a sheet of nonwoven fabric provided with a binder by bringing said sheet
into contact with an aqueous solution characterized in that said binder comprises
polyvinyl alcohol and said aqueous solution contains a sufficient concentration of
a compound which prevents the polyvinyl alcohol dissolving in the aqueous solution
but which, when dissolved in excess water, allows the polyvinyl alcohol to dissolve
in the water thereby reducing the structural integrity of the towelette.
14. A method for making a moist packaged towelette which method comprises taking a
sheet of nonwoven fabric which has been provided with a binder, and packaging said
sheets of treated material in contact with an aqueous solution in a container characterized
in that said binder comprises polyvinyl alcohol and said aqueous solution contains
a sufficient concentration of a compound which prevents the binder from dissolving
in the aqueous solution but which, when dissolved in excess water, allows the binder
to dissolve in the water thereby reducing the structural integrity of the towelette.
15. A method according to Claim 13 or 14, characterized in that said compound is boric
acid.