[0001] THIS INVENTION relates to a composition suitable for use in cleaning and to a method
of cleaning printing inks from apparatus and from personnel.
[0002] At present, undiluted organic solvents are used as cleaning fluids for removing printing
inks from surfaces. The solvents are selected according to the character of the particular
ink or inks to be removed. Solvents which are used include aromatic hydrocarbons,
aliphatic alcohols, ketones and ethers, paraffins and halogenated hydrocarbons. Various
disadvantages arise from the use of these solvents for the purpose mentioned. These
disadvantages include the inflammability and toxicity of the solvents, particularly
of their vapours, the volatility of the solvents, the effect of the solvents on the
skin of persons using them, the insolubility of many of the solvents in water and
the ability of the solvents to attack apparatus used in printing processes, for example
to soften adhesive which secures a blanket on a roller. Solvents with high volatility
generally have good ink-penetrating and dissolving ability but they evaporate rapidly
and redeposit the dissolved ink. When the solvents come into contact with the skin,
they tend to dry the skin and to cause dermatitis. Solvents which are readily soluble
in water can be washed from the hands or from apparatus by means of water, but many
of the solvents used have a character such that it is necessary, once the ink has
been dissolved in the solvent, to wash the solution away with further quantities of
the solvent, either by rinsing the surface to be cleaned in the solvent or by wiping
the surface with a cloth soaked in the solvent. These procedures are fairly expensive
since there must be used considerably more solvent than is necessary merely to dissolve
the ink which is to be removed. Furthermore, these procedures exaggerate the other
disadvantages which have been mentioned herein.
[0003] It will be understood that not all solvents have all of the disadvantages hereinbefore
mentioned and that different solvents suffer from these disadvantages to differing
degrees. Nevertheless, the solvents which are used at the present time for removing
printing inks are not entirely satisfactory and it is an object of the present invention
to provide a cleaning composition which is more satisfactory than those now in use.
[0004] According to a first aspect of the invention, there is provided a cleaning composition
comprising in admixture an organic solvent which is not completely miscible with water
and a surfactant capable of forming an emulsion of the solvent in water.
[0005] A cleaning composition in accordance with the invention may also contain water and
it is envisaged that in many circumstances a composition containing water will be
used. The composition may be supplied as an aqueous composition or as a substantially
non-aqueous composition. In either case, the composition may be diluted with water
prior to use.
[0006] Water can be used to wash away from a surface to be cleaned a composition according
to the invention which has been applied to the surface, together with any ink dissolved,
emulsified or suspended in the composition. A composition according to the invention
is less detrimental to the skin of a user than are the solvents used heretofore.
[0007] The composition preferably includes a second organic solvent. The second solvent
is preferably at least partially miscible with water.
[0008] The first organic solvent may be immiscible with water and in compositions intended
for cleaning dried inks from surfaces, the first solvent is immiscible with water.
[0009] The composition may be such that neither the first solvent nor the second solvent
is completely miscible with water.
[0010] Preferably, the kauri-butanol number of one of the solvents exceeds the kauri-butanol
number of the other of the solvents by at least twenty units. The difference between
the kauri-butanol numbers may be at least 60 units
[0011] The kauri-butanol number of a solvent is an indication of the ability of that solvent
to dissolve materials used in printing inks. The procedure for determining the kauri-butanol
number of a solvent is described in standard test method 1133 published by the American
Society for Testing and Materials.
[0012] The power of the composition as a solvent for printing inks can be determined by
measuring the time required to remove a 25 mm square of the ink from a metal surface
by rubbing the square of ink with a cloth impregnated with the composition and comparing
this with the time required to remove a substantially identical ink square by means
of a cloth impregnated with toluene. In order for consistent results to be achieved
it is necessary for each square to be subjected to rubbing under substantially the
same conditions but we have found that with a little practice a person can achieve
consistent results rubbing the ink squares with the cloth by hand. It is also necessary
for each ink square to have a similar character. For convenience, we have used ink
squares which can be removed by rubbing with a cloth impregnated with toluene in 7
seconds.
[0013] The procedure we have used to determine the power of a composition as a solvent is
as follows. Two 25 mm squares of printing ink are deposited on a clean steel plate.
The ink is permitted to dry for a period such that rubbing for about 7 seconds with
a cloth impregnated with toluene will be necessary to remove one of the squares. One
of the squares is then rubbed with a cloth impregnated with toluene and the time required
to remove the square, T(tol) is noted. The other square is rubbed with a cloth impregnated
with the composition and the time required to remove the square T(comp) is noted.
The time which would be required for removing the ink square by means of the composition
if the ink square could be removed in 7 seconds by toluene is calculated from the
following expression:-

all time being in seconds.
[0014] We have found that if the corrected time required for undiluted solvents having known
kauri-butanol numbers is used to plot a graph of loge of the kauri-butanol number
against time in seconds, there is produced a straight line according to the equation
:-

where N is the kauri-butanol number and t is the time in seconds required for removal
of a 25 mm.square of printing ink from a surface by rubbing with a cloth impregnated
with the solvent and which square can just be removed in 7 seconds by rubbing with
a cloth impregnated with toluene.
[0015] To calculate the power P of a composition as a solvent for printing ink we use the
expression :-

where t is the time in seconds required for removal of a 25 mm square of printing
ink from a surface by rubbing with a cloth impregnated with the composition and which
square can just be removed in 7 seconds by rubbing with- a cloth impregnated with
toluene.
[0016] We have found that the power of examples of compositions in accordance with the invention
having two organic solvents exceeds the weighted average of the respective powers
of composition each comprising a single solvent and which could be mixed to form the
composition comprising two solvents. By weighted average of the powers we mean :-
P
1. R +
P2 R + 1 where P
1 is the power of the first single solvent composition P
2 is the power of the second single solvent composition and R is the ratio weight of
first single solvent composition weight of second single solvent composition
[0017] The proportion by weight of the solvent with the lower kauri-butanol number preferably
exceeds the proportion by weight of the solvent with the higher kauri-butanol number.
The ratio of the respective proportions of solvents may be in the range 2:1 to 5:1.
[0018] The first solvent may be selected from the group comprising halogenated, especially
chlorinated, hydrocarbons and ketones. The second solvent may be selected from the
group comprising ethers and aromatic hydrocarbons. The preferred ethers are those
containing hydroxyl groups, particularly mono-ethers of glycols.
[0019] Alternatively, the first solvent may be selected from the group comprising ethers
and aromatic hydrocarbons, the second solvent being a mixture of aliphatic hydrocarbons.
[0020] There is also provided according to the invention a method of removing printing ink
from a surface wherein there is applied to the surface a composition according to
the first aspect which is subsequently removed by rinsing with water or wiping with
a medium impregnated with water.
[0021] The constitution of a number of examples of compositions in accordance with the invention
is given in Table I and various parameters of each of these compositions are given
in Table II. For convenience, the organic solvents of the compositions identified
in Table I are designated by the letters S to Z as follows:-
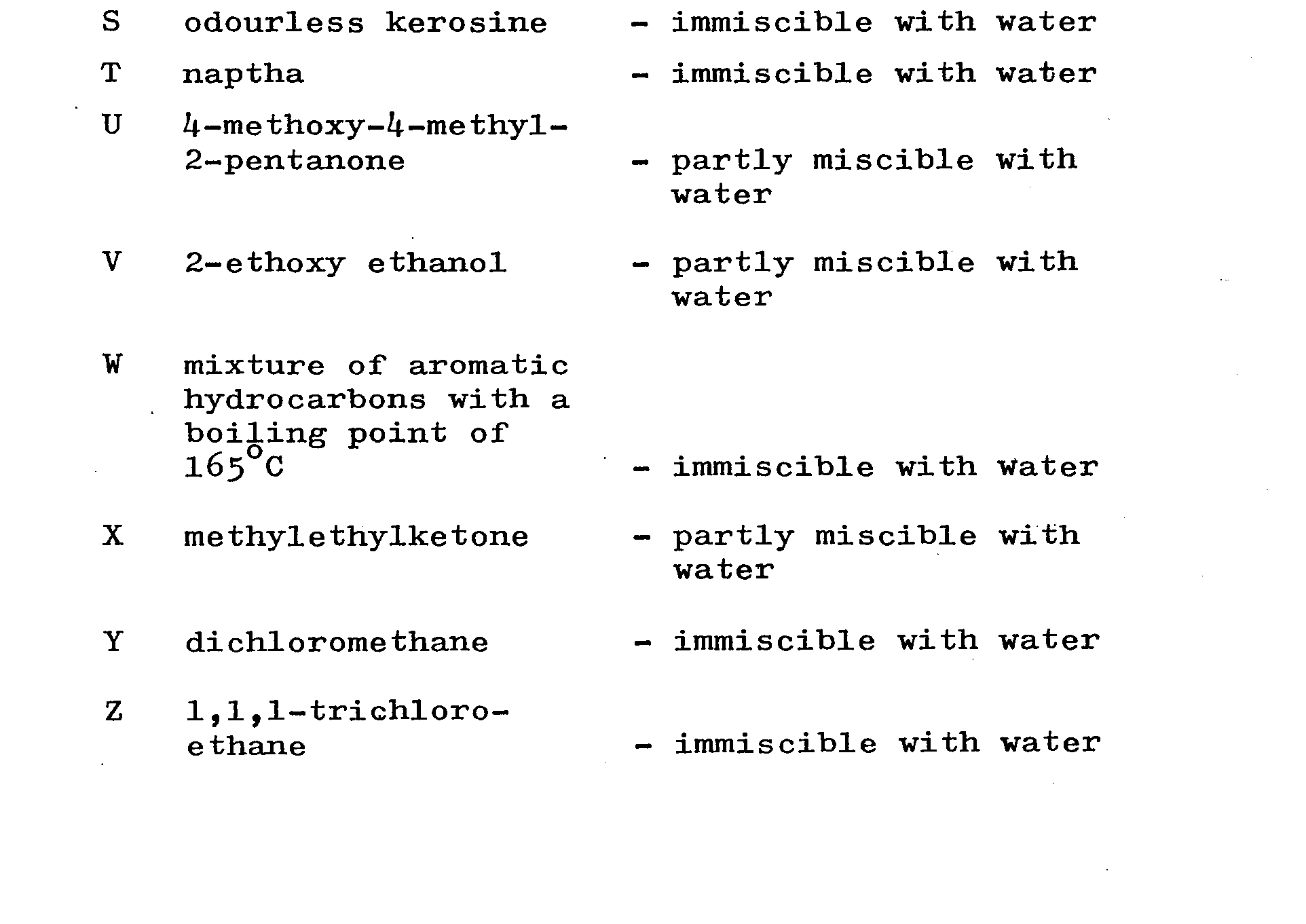
[0022] In Table I, anionic surfactants are designated by the letter A and a mixture of non-ionic
and anionic surfactant is designated by the letter M. Proportions of cationic surfactant
present in the compositions are shown separately. The letter N is used in Table I
to represent non-ionic surfactant.
[0024] Compositions 1 and 2 of Table II each comprise a single, different solvent. The other
constituents of compositions 1 and 2 are the same and are present in substantially
the same proportions. Composition 3 comprises two organic solvents andcan be formed
by mixing appropriate quantities of compositions 1 and 2. Except for the organic solvents,
the constituents of compositions 2 and 3 are present in the same proportions. It will
be noted that the total proportion of organic solvent in composition 3 is the same
as the proportion of organic solvent in composition 2 and that the solvent power of
composition 1 is less than that of composition 2. The solvent power of composition
3 exceeds the respective solvent powers of compositions 1 and 2.
[0025] This demonstrates the synergistic action of the two solvents. The synergistic effect
of different combinations of solvents can be shown by a comparison of compositions
4 and 5 with composition 6, of compositions 7 and 8 with composition 9 and of compositions
10 and 11 with composition 12.
[0026] Compositions comprising two solvents, especially solvents having respective kauri-butanol
numbers which differ considerably, can achieve a required solvent power at lower cost
than the same solvent power can be achieved by a composition comprising a single solvent
and provide the further advantages of relatively reduced inflammability and volatility
and a less harmful effect on the hands of users than is the case with compositions
comprising a single solvent and having the same solvent power.
[0027] All of the preferred compositions comprise a second surfactant which is cationic.
The first of the surfactants may be anionic but is preferably non-ionic. In a case
where the composition comprises three surfactants these are preferably non-ionic,
cationic and anionic respectively. The proportion of the cationic surfactant may be
less than the respective proportions of the non-ionic and anionic surfactants. In
a case where the composition comprises a non-ionic surfactant and a cationic surfactant
but no anionic surfactant, the weight of non-ionic surfactant preferably exceeds the
weight of the cationic surfactant, The ratio of the respective proportions of the
surfactants may be within the range 15:1 to 30:1.
[0028] The presence of a relatively small proportion of a cationic surfactant enables a
substantial reduction in the proportion of non-ionic and/or anionic surfactant, as
compared with the proportion necessary in the absence of any cationic surfactant.
This is illustrated by the examples of compositions listed in Table III. Each of these
compositions has a power of approximately 89 and comprises the same organic solvent,
a mixture of aromatic hydrocarbons, this mixture being the sole organic solvent in
the compositions of Table III.
[0029] In Table III, the proportions of the constituents in each example are indicated by
weight. From a comparison of examples 1, 2 and 3, it can be seen that the addition
of a relatively small proportion of cationic surfactant enables relatively larger
reductions to be made in the proportions of the non-ionic surfactants. Examples 4
and 5 show that where a mixture of anionic and non-ionic surfactant is used, the total
mount of surfactant necessary to provide a stable composition having a power of approximately
89 can be reduced by the inclusion of a relatively small proportion of cationic surfactant.
Furthermore, the composition according to example 4 is not stable at temperatures
below 20°C. Below this temperature, the composition separates into aqueous and non-aqueous
phases; whereas a composition according to example 5 is stable at temperatures below
20°C. Each of the examples listed in Table III contains just sufficient surfactant
to provide a stable emulsion when diluted by any selected amount of water.
[0030] Each of the compositions listed in Table I contains water in a proportion such that
the composition is suitable for dissolving or dispersing printing
ink. The water could be omitted when the composition is prepared for sale and added
to dilute the composition for use.
[0031] With the exception of compositions 1, 7, 8, 10, 13 and 14, each of the compositions
listed in Table I can be further diluted with any selected volume of water without
breakdown of the emulsion occurring. Once printing ink has been dissolved in a quantity
of the composition having the proportions set out in Table I, the dissolved ink can
be washed away with water. It will be noted that the compositions which cannot be
diluted with any selected volume of water without breakdown of the emulsion occurring
are compositions comprising a single organic solvent. All of the compositions which
contain more than one organic solvent can be diluted to any degree with water.
[0032] The compositions can be applied to a surface from which printing ink and/or other
matter is to be removed by spraying, brushing or wiping the composition onto the surface.
The composition, together with dissolved ink or other matter, can then be removed
by wiping or by rinsing with water. Wiping on of the composition is, of course effected
by means of a cloth or other absorbent medium impregnated with the composition. Wiping
off of the composition containing dissolved ink may be effected either by means of
a cloth or other absorbent medium impregnated with the composition or by means of
an aborbent medium impregnated with water. In either case, the printing ink or other
matter to be removed from the surface will tend to migrate into the absorbent medium
so that the surface of the absorbent medium will not become soiled to the same degree
as would occur if all of the matter wiped from the surface remains on the surface
of the absorbent medium.
[0033] In a case where a mixture of anionic, cationic and non-ionic surfactants is used,
the proportion by weight of cationic surfactant is preferably less than the respective
proportion by weight of the anionic and non-ionic surfactants. The cationic surfactant
may be a tertiary amine having two polyoxyethylene groups and a C12 to Cl8 alkyl group
attached to the nitrogen atom.
[0034] The plasticiser used in certain of the compositions of Table I is a plasticiser,
the use of which is known in coating compositions and which is the ester of an aliphatic
carboxylic acid. 2
f2,4- trimethyl 1,3-pentandiol diiobutyrate is a suitable plasticiser.
1. A cleaning composition comprising in admixture an organic solvent which is not
completely miscible with water and a surfactant capable of forming an emulsion of
the solvent in water.
2. A composition according to claim 1 wherein the solvent is immiscible with water.
3. A composition according to claim 1 or claim 2 further comprising a second organic
solvent, the second solvent being at least partly miscible with water.
4. A composition according to any preceding claim wherein the kauri-butanol number
of one of the solvents exceeds the kauri-butanol number of the other of the solvents
by at least 20.
5. A composition according to claim 1 further comprising a second organic solvent
and having a solvent power exceeding the weighted average of the respective solvent
powers of two sub-compositions which differ from each other only in respect of the
organic solvent content, which can be mixed to form the composition comprising two
organic solvents, one of which sub-compositions comprises the first organic solvent
but not the second organic solvent and the other of which sub-compositions comprises
the second organic solvent but not the first organic solvent.
6. A composition according to claim 4 wherein the proportion by weight of the solvent
with the lower kaui-butanol number exceeds the proportion by weight of the solvent
with the higher kauri-butanol number.
7. A composition according to any preceding claim further comprising a second surfactant
which is cationic, the first surfactant being anionic and/or non-ionic.
8. A composition according to claim 7 wherein the proportion by weight of the first
surfactant exceeds the proportion by weight of the second surfactant.
9. A method of removing printing ink from a surface wherein there is applied to the
surface a composition according to any one of claims 1 to 8 and the composition is
subsequently removed from the surface by rinsing the surface with water or wiping
the surface with an absorbent medium impregnated with water.