[0001] Aus der DE-PS 1 811 796 ist es bekannt, zum Färben und Bedrucken von Textilien aus
Cellulosefasern oder Gemischen aus Cellulosefasern und synthetischen Fasern mit Dispersionsfarbstoffen
in wäßrigem Medium zu arbeiten und die wasserunlöslichen Dispersionsfarbstoffe unter
Verwendung von wasserlöslichen Quell- und Farbstofflösungsmitteln in das Innere der
gequollenen Cellulosefasern zu bringen. Als wasserlösliche Quell- und Farbstofflösungsmittel
werden vor allem Polyäthylenglykole und deren Derivate verwendet. Bei der praktischen
Anwendung dieses Verfahrens tritt während des Fixierens der Farbstoffe eine starke
nebelbildung auf, die auf verdampftes Farbstofflösungsmittel zurückzuführen ist. In
Färbereibetrieben, in denen meist mit Geräten ohne spezielle Abluftführung (Spannrahmen,
Zylinderfixiermaschinen, Siebtrommelanlagen und Hotflue) gearbeitet wird, macht sich
die beim Fixieren auftretende Nebelbildung besonders störend bemerkbar.
[0002] Der Erfindung liegt daher die Aufgabe zugrunde, ein Verfahren zum Färben und Bedrucken
von Textilien aus Cellulosefasern oder Gemischen aus Cellulosefasern und synthetischen
Fasern mit Dispersionsfarbstoffen in wäßrigem Medium in Gegenwart von wasserlöslichen
Quell- und Farbstofflösungsmitteln und Fixieren der Farbstoffe durch Erhitzen der
gefärbten oder bedruckten Textilien auf Temperaturen bis zu 230°C zur Verfügung zu
stellen, bei dem die Nebelbildung während des Fixierens weitgehend zurückgedrängt
wird und das außerdem gute Färbungen ergibt.
[0003] Diese Aufgabe wird erfindungsgemäß dadurch gelöst, daß man als Quell- und Farbstofflösungsmittel
eine Mischung aus
(a) 99 bis 1 Gew.% mindestens eines Polyäthylenglykols oder eines Blockcopolymerisates
aus Äthylenoxid und Propylenoxid oder deren Äther-, Ester- oder Carbamat--Derivate
und
(b) 1 bis 99 Gew.% mindestens eines polyäthoxylierten Amins, dessen Äthoxylierungsgrad
mindestens 3 beträgt, einsetzt.
[0004] Die als Komponente (a) der Quell- und Farbstofflösungsmittel in Betracht kommenden
Polyäthylenglykole haben ein Molekulargewicht in dem Bereich von 300 bis 5 000, vorzugsweise
400 bis 1 000. Außerdem kommen Blockcopolymerisate aus Äthylenoxid und Propylenoxid
in Betracht, die 10 bis 100, vorzugsweise 20 bis 50 Propylenoxid-Einheiten und 8 bis
300, vorzugsweise 10 bis 200 Äthylenoxid-Einheiten enthalten. Diese Blockcopolymerisate
werden vorzugsweise dadurch hergestellt, daß man an Polypropylenglykol mit 10 bis
100 Propylenoxid-Einheiten 8 bis 300 Mol Äthylenoxid anlagert. Produkte dieser Art
können mit Hilfe der Formel

beschrieben werden, in der
n = 8 bis 300, vorzugsweise 10 bis 200 und
m = 10 bis 100, vorzugsweise 20 bis 50 bedeutet.
[0005] Außerdem eignen sich Mono- und Diäther von Polyäthylenglykolen oder Äthylenoxid-Propylenoxid-Blockcopolymerisaten
als Komponente (a) der Quell- und Farbstofflösungsmittelmischung. Diese Verbindungen
werden hergestellt, indem man ein- oder mehrwertige Alkohole oder Phenole mit Äthylenoxid
umsetzt. Geeignete Alkohole sind beispielsweise Methanol, Äthanol, Propanol, Butanol,
Hexanol, Decanol und Dodecanol, mehrwertige Alkohole, wie Äthylenglykol, Glycerin,
Trimethylolpropan, Pentaerythrit und Sorbit. Die Alkohole können auch mit einem Mischgas
aus Äthylenoxid und Propylenoxid umgesetzt werden. Dabei erhält man Monoäther von
Polyalkylenoxiden, in denen Äthylenoxid- und Propylenoxid-Einheiten statistisch verteilt
sind. Daneben kommen auch solche Derivate von Polyalkylenoxiden in Betracht, die Äthylenoxid-
und Propylenoxid-Blöcke enthalten. Außer den Alkoholen kommen zur Herstellung der
Äther auch Phenole in Betracht, die mit Äthylenoxid bzw. Äthylenoxid und Propylenoxid
umgesetzt werden. Geeignete Phenole sind beispielsweise das unsubstituierte Phenol,
die isomeren Methylphenole, Bisphenol-A, 2,5-Dimethylphenol, 2,4-Dimethylphenol, o-Phenylphenol
und p-Chlorphenol, Isooctylphenol, Isononylphenol, Isododecylphenol, p-tert. Butylphenol
und die entsprechenden Diisoalkylphenole.
[0006] Als Komponente (a) der Farbstofflösungsmittel eignen sich auch Carbonsäureester von
Polyäthylenglykolen und Blockcopolymerisaten der oben beschriebenen Art. Die Carbonsäurepolyglykolester
werden beispielsweise hergestellt, indem man z.B. einen Carbonsäureester einer C
2- bis C
20-Carbonsäure mit beispielsweise einem C
1- bis C
h-Alkohol einer Umesterungsreaktion mit einem Polyalkylenoxid unterwirft. Als Carbonsäuren
kommen sowohl gesättigte Carbonsäuren, wie Essigsäure, Propionsäure, Palmitinsäure
und Stearinsäure als auch ungesättigte Carbonsäuren, wie Acrylsäure, Methacrylsäure,
Maleinsäure und ölsäure in Betracht.
[0007] Geeignete Carbamate werden beispielsweise durch Umsetzung von Harnstoff mit Polyäthylenoxiden
oder Blockcopolymerisaten aus Äthylenoxid und Propylenoxid erhalten. Verbindungen
dieser Art können beispielsweise mit Hilfe der Formel

charakterisiert werden, in der
n = 8 bis 300 und
m = 0 bis 100 ist.
[0008] Neben diesen Monocarbamaten kommen die entsprechenden Biscarbamate in Betracht.
[0009] Außer Carbonsäureestern kommen auch Borsäureester in Betracht, die beispielsweise
durch Veresterung von Polyäthylenglykol oder Blockcopolymerisaten aus Äthylenoxid
und Propylenoxid mit Borsäure im Molverhältnis 0,5:1 bis 3:1 erhalten werden. Geeignete
Borsäureester erhält man auch, wenn man Monoäther von Polyäthylenglkyolen mit Borsäure
verestert. Hierzu kann man beispielsweise C
1- bis C
S-einwerti- 'ge Alkohole, C
2- bis C
8-Diole, Glycerin, Trimethylolpropan, Pentaerythrit und Sorbit mit Äthylenoxid umsetzen,
wobei man pro Hydroxylgruppe des Alkohols 1 bis 20 Äthylenoxid--Einheiten anlagert.
Zur Herstellung der Oxäthylierungsprodukte kann man auch von einem Mischgas aus Äthylenoxid
und Propylenoxid ausgehen, so daß man statistische Copolymerisate erhält. Man kann
jedoch auch Monoäther herstellen, in denen Propylenoxid- und Äthylenoxid-Einheiten
als Blöcke vorliegen. Diese Monoäther werden dann in bekannter Weise mit Borsäure
verestert.
[0010] Als Komponente (b) des Quell- und Farbstofflösungsmittelgemisches verwendet man polyalkoxylierte
Amine mit einem Alkoxylierungsgrad von mindestens 3. Verbindungen dieser Art sind
bekannt, sie werden beispielsweise hergestellt, indem man Amine mit Äthylenoxid bzw.
Propylenoxid umsetzt. Die Amine, die der Alkoxylierung unterworfen werden, enthalten
mindestens eine N-H-Gruppe oder funktionelle Gruppen, die der Alkoxylierungsreaktion
zugänglich sind, z.B. ein Hydroxyäthylgruppe wie Triäthanolamin. Die geeigneten Amine
enthalten mindestens ein C-Atom und mindestens ein basisches Stickstoffatom. Es kommen
sowohl Mono- als auch Di- und Polyamine in Betracht, z.B. Methylamin, Äthylamin, Propylamin,
Butylamin, Dimethylamin, Dibutylamin, Hexylamin, Äthanolamin, Diäthanolamin, Triäthanolamin,
Piperazin, 2-Äthylcyclohexylamin, Dioxadodecandiamin, Äthylendiamin, Propylendiamin,
Hexamethylendiamin, Neopentandiamin, Diäthylentriamin, Dipropylentriamin, Triäthylentetramin,
Tetraäthylenpentamin, PolyäthylenLmin, 'Anilin, N-Methylanilin, Naphthylamin, 3-Amino-1-cyclohexyl-
aminopropan, Diamino-dicyclohexylmethan, Diamino-diphenylmethan, Imidazol, Piperazin
und Polyäthylenimid.
[0011] Die in Betracht kommenden Amine werden entweder mit Äthylenoxid allein, und zwar
mit 3 bis 100, vorzugsweise 8 bis 50 Mol Äthylenoxid umgesetzt oder man lagert zunächst
3 bis 100 Mol Propylenoxid an und läßt dieses Reaktionsprodukt anschließend mit 3
bis 200 Mol Äthylenoxid reagieren. Man kann jedoch auch ein 3- bis 100-fach äthoxyliertes
Amin mit 4 bis 100 Mol Propylenoxid und daran anschließend mit 3 bis 100 Mol Äthylenoxid
umsetzen. Man erhält auf diese Weise Blockpolymerisate der Formeln A-B-A oder B-A-B,
bei denen A 3 bis 100 Äthylenoxid-Einheiten und B 3 bis 100 Propylenoxid-Einheiten
bedeuten. In allen Fällen liegen wasserlösliche Produkte vor, die ein Quellmittel
für die Cellulose und ein Farbstofflösungsmittel für den wasserunlöslichen Dispersionsfarbstoff
darstellen. Vorzugsweise werden bei dem erfindungsgemäßen Verfahren Quell- und Farbstofflösungsmittelmischungen
eingesetzt, die 95 bis 80 Gew.% einer oder mehrerer Verbindungen der Komponente (a)
und 5 bis 20 Gew.% einer oder mehrerer Verbindungen der Komponente (b) enthalten.
[0012] Nach dem erfindungsgemäßen Verfahren werden Cellulosefasern' oder Gemische aus Cellulosefasern
mit synthetischen Fasern gefärbt oder bedruckt. Die Cellulosefasern sind in Wasser
quellbar, beispielsweise eignen sich Baumwolle und Fasern aus Regeneratcellulose,
die für Wasser und das Lösungsmittelgemisch zugänglich sind. Im Falle von Fasermischungen
verwendet man als synthetische Fasern vor allem Fasern aus Polyester. Daneben eignen
sich als synthetische Fasern Cellulosetriacetat, Celluloseacetat und Polyamidfasern.
Der Anteil an synthetischen Fasern in der Fasermischung kann in einem weiten Bereich
schwanken, beispielsweise kann man Fasermischungen verwenden, die 80 bis 20 Gew.%
an synthetischen Fasern enthalten. Vorzugsweise werden erfindungsgemäß textile Materialien
aus Polyester und Baumwolle gefärbt oder bedruckt. Unter textilen Materialien sollen
Kammzüge, Faservliese, Garne, Fäden, Strickschläuche, Stückwaren, Gewebe und Teppiche
verstanden werden.
[0013] Cellulosefasern und synthetische Fasern werden erfindungsgemäß mit einer einzigen
Farbstoffklasse gefärbt oder bedruckt, nämlich mit Dispersionsfarbstoffen. Die Dispersionsfarbstoffe
können beispielsweise folgenden Farbstoffklassen angehören: Farbstoffe mit einer oder
mehreren Azobindungen, Anthrachinonfarbstoffen, indigoiden Farbstoffen und Phthalocyaninfarbstoffen.
Die Farbstoffe werden unter Zusatz anionischer oder nichtionogener Dispergiermittel
in eine fein verteilte Zubereitung überführt. Die Zubereitung kann als flüssige Einstellung
oder in Pulverform verwendet werden. Der Reinfarbstoffgehalt liegt meistens zwischen
10 und 90 %.
[0014] Von den Dispersionsfarbstoffen werden vor allem diejenigen bevorzugt, die in Wasser
bei einer Temperatur von 100°C und darunter unlöslich und im verwendeten Lösemittel
bei der Fixiertemperatur gut löslich sind. Die Färbung wird erfindungsgemäß in einem
wäßrigen Medium vorgenommen. Das textile Material wird dazu beispielsweise mit einer
Klotzflotte imprägniert, die pro 1 000 Gewichtsteile Flotte 30 bis 250 Gewichtsteile
der Quell- und Farbstofflösungsmittelmischung aus den Komponenten (a) und (b) sowie
1 bis 200 Gewichtsteile von 20 %-igen Zubereitungen der Dispersionsfarbstoffe enthält.
[0015] Für das Bedrucken werden Druckpasten eingesetzt, die sich von den Färbeflotten dadurch
unterscheiden, daß sie ein Verdickungsmittel in hoher Konzentration enthalten. Geeignete
Verdickungsmittel sind die üblicherweise verwendeten Stärkeäther, Alginate, Tragant
und Kernmehläther, sowie synthetische Verdickungsmittel auf Basis hochmolekularer
Polymerisate äthylenisch ungesättigter Carbonsäuren mit 3 bis 5 Kohlenstoffatomen.
Es handelt sich hierbei in erster Linie um Polymerisate der Acrylsäure, Methacrylsäure,
Maleinsäure, Maleinsäureanhydrid, Fumarsäure und Itaconsäure sowie um Copolymerisate
der genannten Carbonsäuren. Die genannten Carbonsäuren können auch mit anderen copolymerisierbaren
äthylenisch ungesättigten Monomeren, wie Äthylen, Vinylestern, Acrylsäureestern, Methacrylsäureestern,
Styrol, Vinyläther und Amiden von äthylenisch ungesättigten C
3- bis C
S-Carbonsäuren copolymerisiert werden. Diese Gruppe von Copolymerisaten enthält mindestens
40, vorzugsweise 75 bis 99,9 Gew.% an äthylenisch ungesättigten Carbonsäuren. Die
synthetischen Verdickungsmittel haben ein hohes Molekulargewicht. Besonders geeignete
synthetische Verdickungsmittel erhält man, wenn man die oben genannten äthylenisch
ungesättigten Carbonsäuren mit solchen Monomeren copolymerisiert, die zwei äthylenisch
ungesättigte Doppelbindungen enthalten, beispielsweise Butadien, Divinylbenzol, Butandioldiacrylat,
Divinyldioxan oder Diallylphthalat. Diese Monomeren sind zu etwa 0,05 bis 5 Gew.%
am Aufbau der hoch- molekularen Copolymerisate beteiligt. 1 000 Gewichtsteile ' der
Druckpaste enthalten im allgemeinen 10 bis 80 Gewichtsteile eines synthetischen oder
natürlichen Verdickungsmittels.
[0016] Gefärbt wird beispielsweise, indem man die Textilien mit einer Färbeflotte klotzt,
wobei die Flottenaufnahme in dem Bereich von 25 bis 120 % liegen kann. Nach dem Klotzen
erfolgt in der Regel ein Zwischentrocknen des Materials bei Temperaturen von 90 bis
120°C und daran anschließend das Fixieren bei Temperaturen von 180 bis 230, vorzugsweise
mit Heißluft bei 210 bis 220°C. Fixiert wird beispielsweise im Spannrahmen, auf der
Hotflue oder auf Siebtrommelanlagen. Für die Fixierung benötigt man etwa 15 bis 120,
vorzugsweise 45 bis 90 sec. Es kann auch Heißdampf bei 180 bis 190°C verwendet werden.
Dabei ist die Fixierzeit auf 5 bis 10 Minuten zu verlängern. Man erhält auch bei Fasermischungen
ein Ton-in-Ton gefärbtes textiles Material, das kalt und warm gespült und mit handelsüblichen
Waschmitteln gewaschen werden kann. Obwohl die Fixierung der Farbstoffe bei relativ
hohen Temperaturen erfolgt, wird überraschenderweise keine oder nur eine sehr geringfügige
Nebelbildung in Folge von verdampfendem Quell- und Farbstofflösungsmittel beobachtet.
Die Fixierausbeute ist sehr gut und es werden Färbungen mit guten Wasch- und Reibechtheiten
erhalten.
[0017] Die gleichen Vorteile werden auch beim Drucken erreicht. Die Klotzflotten und Druckpasten
können noch die üblichen Zusätze, wie pH-Regulatoren, Antimigrationsmittel, Antifrostingmittel,
Emulgatoren, Dispergiermittel, Egalisiermittel, Fixierbeschleuniger und Schaumdämpfer
enthalten. Im Anschluß an das Fixieren der Farbstoffe wird das gefärbte oder bedruckte
Gewebe gespült und einer Nachwäsche bei Kochtemperatur unterworfen, bei der übliche
Waschmittel verwendet werden können. L J
[0018] Die Erfindung wird anhand der folgenden Beispiele näher erläutert. Die in den Beispielen
angegebenen Teile sind Gewichtsteile, die Angaben in Prozent sind Gewichtsprozent.
Beispiel 1
[0019] Ein Gewebe aus 65 Teilen Polyester-Fasern und 35 Teilen mercerisierter Baumwolle
wurde mit einer Flotte imprägniert, die 5 g/1 einer 20 %-igen Zubereitung des braunen,
wasserunlöslichen Dispersionsfarbstoffes der Formel
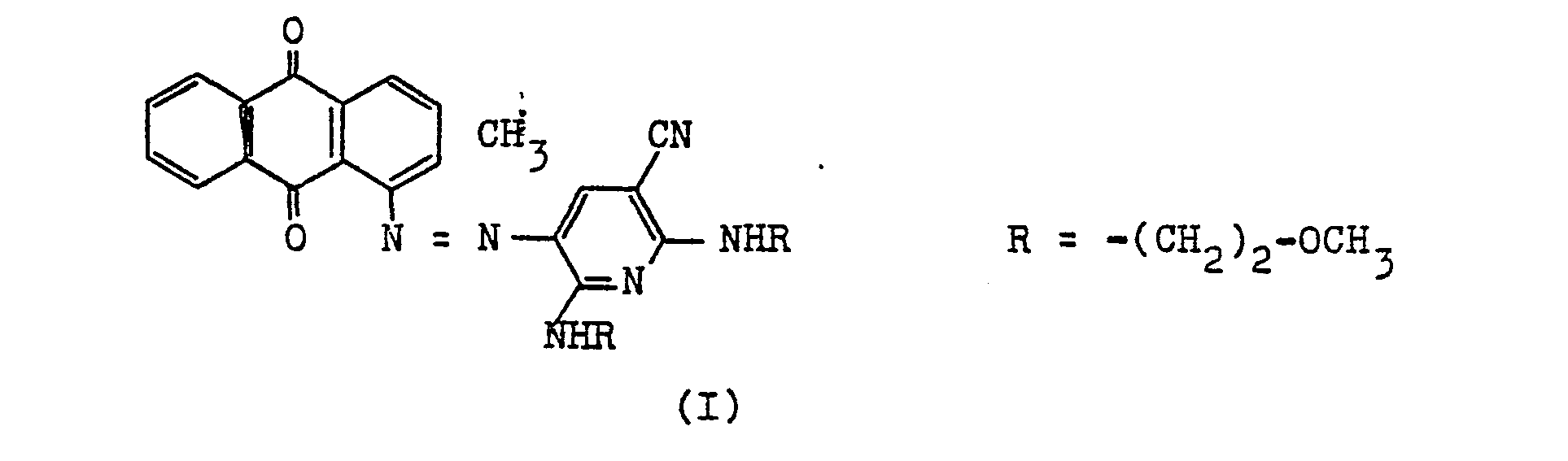
und 80 g/1 eines der nachstehend angegebenen Quell- und Farbstofflösungsmittel 1)
bis 14) oder deren Mischungen (vgl. Tabelle) enthalten.
[0020] Als Komponente (a) des Quell- und Farbstofflösungsmittels dienten folgende Verbindungen:
1) Polyäthylenglykol (Molekulargewicht 600)
2) Polyäthylenglykol (Molekulargewicht 1500)
3) 1 Mol Isooctylphenol umgesetzt mit 14 Mol Äthylenoxid
4) Umsetzungsprodukt aus Acrylsäuremethylester und Polyäthylenglykol (Molekulargewicht
400) im Molverhältnis 1 : 1
[0021] Als Komponente (b) des Quell- und Farbstoffläsungsmittels wurden folgende Verbindungen
eingesetzt:
5) Umsetzungsprodukt aus 1 Mol Butylamin und 14 Mol Äthylenoxid
6) Umsetzungsprodukt aus 1 Mol Neopentandiamin und 15,6 Mol Äthylenoxid
7) Umsetzungsprodukt aus 1 Mol Äthylendiamin und 35 Mol Äthylenoxid
8) Umsetzungsprodukt aus 1 Mol Äthylendiamin und 8 Mol Propylenoxid, das mit 8 Mol
Äthylenoxid zur Reaktion gebracht wurde
9) Umsetzungsprodukt aus 1 Mol Äthylendiamin und 16 Mol Propylenoxid, das anschließend
mit 16 Mol Äthylenoxid zur Reaktion gebracht wurde
10) Umsetzungsprodukt aus Hexamethylendiamin und 15 Mol Äthylenoxid
11) Umsetzungsprodukt aus 1 Mol Triäthanolamin und 14 Mol Äthylenoxid
12) Umsetzungsprodukt aus 1 Mol Anilin und 10 Mol Äthylenoxid
13) Umsetzungsprodukt aus 1 Mol Piperazin und 16 Mol Äthylenoxid
[0022] Der pH-Wert der Flotten wurde mit Glutarsäure auf 6 eingestellt. Die Flottenaufnahme
des Gewebes betrug 50 %. Die Gewebestücke wurden dann 60 Sekunden bei einer Temperatur
von 120°C getrocknet und danach 60 Sekunden bei 215°C in einem Labortrockner fixiert.
Danach wurde das Gewebe kalt und warm gespült und 5 Minuten bei 100°C in Gegenwart
eines handelsüblichen Waschmittels gewaschen.
[0023] Die Gewebestücke wurden in allen Fällen im klimatisierten Zustand vor dem Imprägnieren,
nach dem Zwischentrocknen und nach der Behandlung bei 215°C gewogen. Aus den gefundenen
Werten wurde derjenige prozentuale Anteil des aufgebrachten Lösemittels ermittelt,
der bei der Hitzebehandlung verdampft ist.
[0024] In der folgenden Tabelle sind die Flüchtigkeiten der Verbindungen 1) bis 13) sowie
von Mischungen im Gewichtsverhältnis 1 : 1 der Stoffe beim Einsatz als Quell- und
Farbstofflösungsmittel beim Färben zusammengestellt.
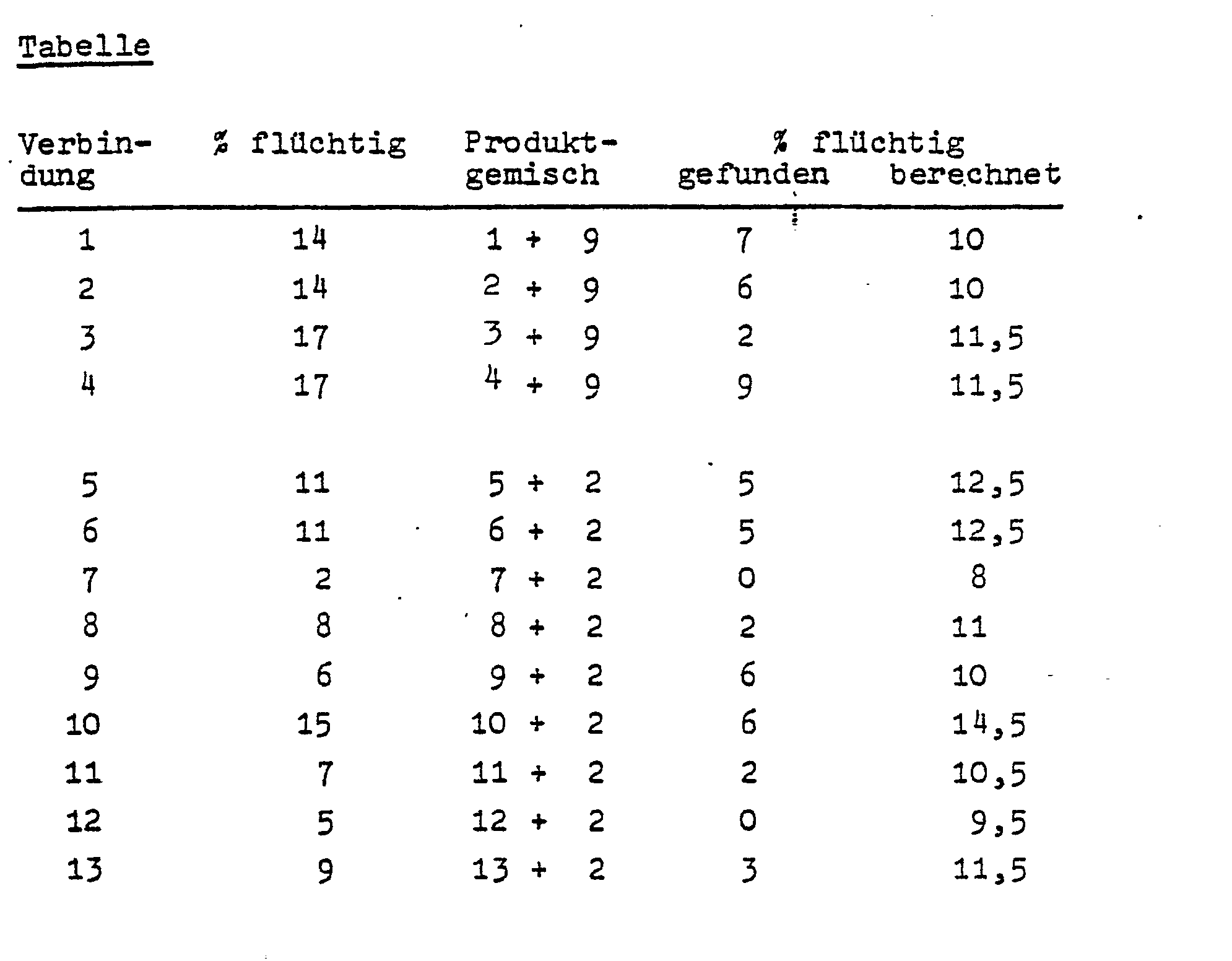
[0025] Die für die Mischungen berechneten Werte wurden aus dem arithmetischen Mittel der
flüchtigen Anteile der beiden Komponenten der Mischung erhalten.
[0026] Man erkennt, daß in allen Fällen das Gemisch weniger flüchtig ist, als zu erwarten
war.
[0027] In allen Fällen wurde mit den Mischungen eine hellbraune Färbung erhalten, die gute
Echtheiten aufwies.
Beispiel 2
[0028] Ein Gewebe aus 65 Teilen Polyester-Faser und 35 Teilen mercerisierter Baumwolle wird
mit einer Flotte imprägniert, die 10 g/1 einer 20 %-igen flüssigen Zubereitung des
roten wasserunlöslichen Dispersionsfarbstoffs der Formel
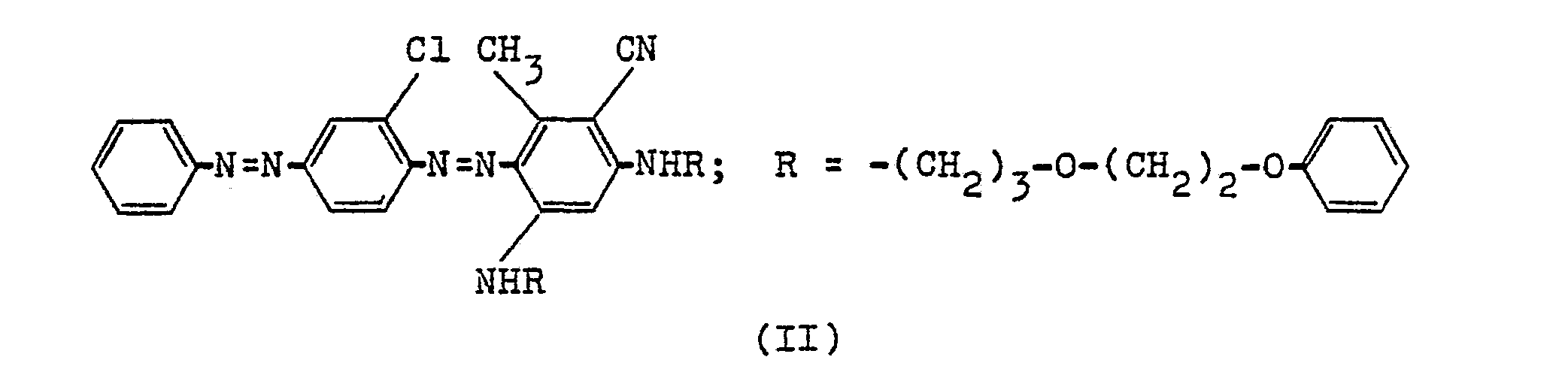
und 80 g/1 eines Quell- und Farbstofflösungsmittels aus einer Mischung aus 3 Teilen
Polyäthylenglykol mit einem Molekulargewicht von 1 500 und 1 Teil eines Umsetzungsprodukts
aus 1 Mol Neopentandiamin und 15,6 Mol Äthylenoxid enthält. Der pH-Wert der Klotzflotte
wird mit Glutarsäure auf 6 eingestellt. Das Gewebe wird mit der Klotzflotte imprägniert,
wobei die Flottenaufnahme 45 % beträgt. Das Gewebe wird dann 60 Sekunden bei einer
Temperatur von 120°C getrocknet und 90 Sekunden bei 225°C in einem kontinuierlich
arbeitenden Labortrockner fixiert. Danach wird es kalt und warm gespült und 5 Minuten
bei 100
0C in Gegenwart eines handelsüblichen Waschmittels gewaschen. Der Farbstoff ist fast
vollständig auf dem Gewebe fixiert. Man erhält eine rote Färbung mit guten Wasch-
und Reibechtheiten.
[0029] Bei der Fixierung des Farbstoffs sind, wie gravimetrisch bestimmt wurde, 3 % des
aufgebrachten Lösungsmittels verdampft. Beträgt das Verhältnis von Polyäthylenglykol
zu dem Umsetzungsprodukt aus Neopentandiamin und Äthylenoxid 15 : 1, so verdampfen
unter den angegebenen Fixierbedingungen 7 % des Quell- und Lösungsmittelgemisches.
[0030] Verwendet man dagegen als Quell- und Farbstofflösungsmittel allein das Polyäthylenglykol
eines Molekulargewichts von 1 500, so verdampfen unter den Fixierbedingungen 14 Gew.%.
Verwendet man das Umsetzungsprodukt von Neopentandiamin mit 15,6 Mol Äthylenoxid als
alleiniges Quell- und Farbstofflösungsmittel, so verdampfen unter den Fixierbedingungen
bei 225
0C 15 %.
Beispiel 3
[0031] Das im Beispiel 1 angegebene Textilmaterial wird mit einer Färbeflotte imprägniert,
die 20 g/1 einer 20 %-igen Zubereitung des Farbstoffs der Formel I (Beispiel 1) und
als Quell- und Farbstofflösungsmittel 60 g/1 einer Mischung aus 1 Teil eines Umsetzungsproduktes
aus 1 Mol i-Octylphenol und 14 Mol Äthylenoxid und 2 Teilen eines Umsetzungsproduktes
aus 1 Mol Piperazin und 16 Mol Äthylenoxid enthält. Der pH-Wert der Flotte wurde mit
Glutarsäure auf 6 eingestellt. Die Flottenaufnahme betrug 50 %. Das Gewebe wurde 60
Sekunden bei einer Temperatur von 120°C getrocknet und anschließend zur Fixierung
des Farbstoffs 30 Sekunden auf eine Temperatur von 225°C in einem kontinuierlich arbeitenden
Labortrockner erhitzt. Die Färbung wurde wie im Beispiel 2 beschrieben fertiggestellt.
Man erhielt eine helle Braun-färbung mit guten Echtheitseigenschaften. Der Auswaschverlust
war sehr gering. Der Gewichtsverlust der Gewebeprobe nach der Fixierung war nicht
höher als bei einem Vergleichsversuch, bei dem die Flotte wohl die Farbstoffpräparation
aber kein Quell- und Farbstofflösungsmittel enthielt.
Beispiel 4
[0032] Das im Beispiel 1 genannte Textilmaterial wurde mit einer Färbeflotte imprägniert,
die 100 g/1 einer 20 %-igen Zubereitung des blauen Farbstoffs der Formel
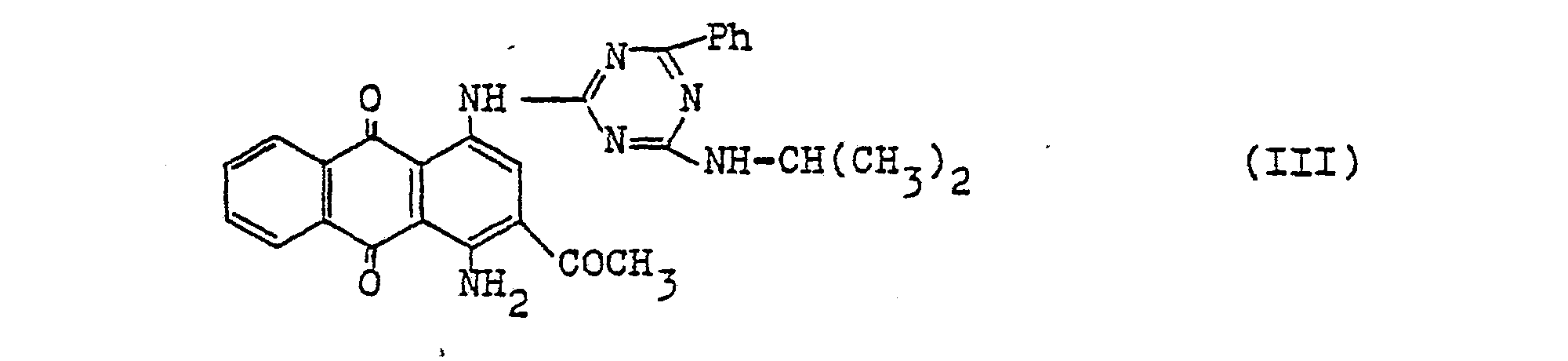
und als Quell- und Farbstofflösungsmittel 100 g/1 eines Gemisches aus 95 Teilen eines
Additionsproduktes aus 1 Mol Acrylsäuremethylester und 1 Mol Polyäthylenglykol vom
Molekulargewicht 400 (Alkoxy-propionsäurederivat) und 5 Teilen eines Umsetzungsproduktes
aus 1 Mol Anilin mit 10 Mol Äthylenoxid enthielt. Der pH-Wert der Flotte wurde mit
Zitronensäure auf 6 eingestellt. Die Flottenaufnahme betrug 50 %. Das Gewebe wurde
60 Sekunden bei einer Temperatur von 120°C getrocknet und anschließend zur Fixierung
des Farbstoffs 90 Sekunden auf 220°C in einem kontinuierlich arbeitenden Labortrockner
erhitzt. Der dabei verdampfte Lösemittelanteil war geringer als bei Verwendung des
Alkoxypropionsäurederivates allein, er betrug etwa 5 %. Die Färbung wird nach der
im Beispiel 2 angegeben Vorschrift fertiggestellt. Man erhält eine tiefe Blaufärbung
mit guten Licht- und Naßechtheiten. Der Auswaschverlust ist sehr gering.
Beispiel 5
[0033] Das im Beispiel 1 angegebene Textilmaterial wird mit einer Färbeflotte imprägniert,
die 80 g/1 des Farbstoffs I (vgl. Beispiel 1) und als Quell- und Farbstofflösungsmittel
80 g/1 einer Mischung aus,80 Teilen eines Polyäthylenglykols mit einem Molekulargewicht
von 1 500 und 20 Teilen eines Umsetzungsprodukts aus 1 Mol Hexamethylendiamin und
15 Mol Äthylenoxid enthält. Der pH-Wert der Flotte wurde mit Zitronensäure auf 5 eingestellt.
Die Flottenaufnahme betrug 50 %. Das Gewebe wurde 60 Sekunden bei einer Temperatur
von 120°C getrocknet und zur Fixierung des Farbstoffs 60 Sekunden bei einer Temperatur
von 215°C in einem Labortrockner erhitzt. Die Färbung wird wie im Beispiel 2 beschrieben
fertiggestellt. Man erhält bei geringerem Auswaschverlust eine dunkle rot-braun-Färbung
mit guten Wasch-, Licht- und Reibecht-
heiten. Beim Fixierprozeß verdampfte praktisch kein Lösemittel.
Beispiel 6
[0034] Ein Gewebe aus einer Fasermischung aus 50 Teilen Polyester-fasern und 50 Teilen Baumwolle
wird mit einer wäßrigen Flotte imprägniert, die 20 g/1 einer 20 %-igen Zubereitung
des Farbstoffs der Formel
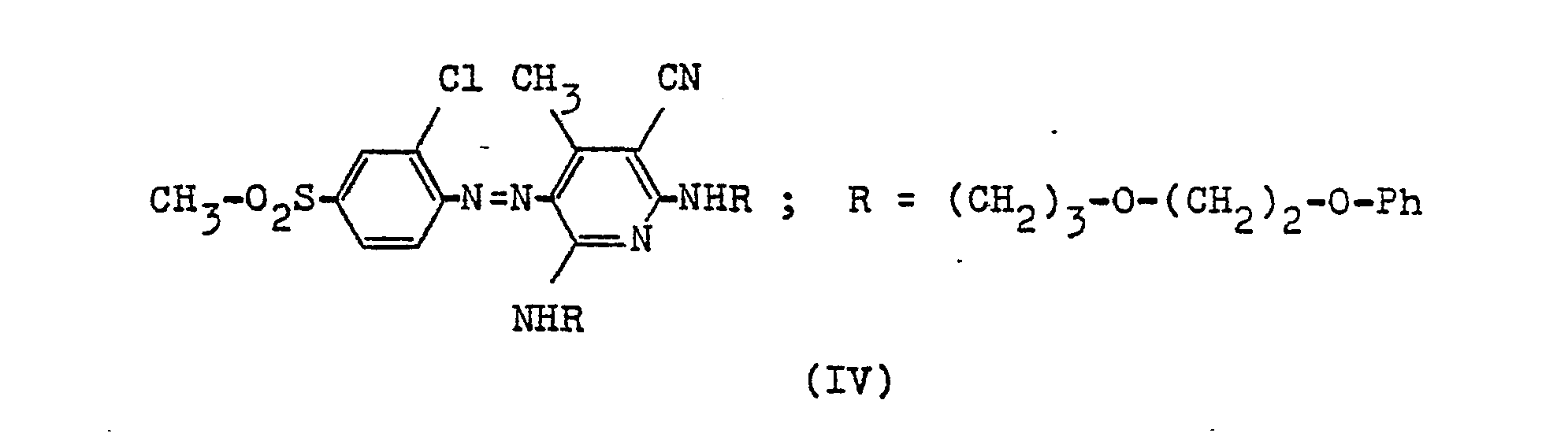
und als Quell- und Farbstofflösungsmittel 50 g/1 einer Mischung aus 80 Teilen eines
Polyäthylenglykols mit einem Molekulargewicht von 600 und 20 Teilen eines Umsetzungsproduktes
aus 1 Mol Triäthanolamin und 14 Mol Äthylenoxid enthält. Der pH-Wert der Flotte wurde
mit Glutarsäure auf 7 eingestellt. Die Flottenaufnahme betrug 52 %. Das Textilmaterial
wurde 60 Sekunden bei 120°C getrocknet und anschlie- Bend 90 sec bei 210°C in einem
Labortrocknungsaggregat erhitzt. Die Färbung wurde danach wie im Beispiel 2 angegeben
fertiggestellt. Man erhielt bei sehr geringem Auswaschverlust eine rotstichige Gelbfärbung
mit guten Licht-, Naß-und Reibechtheiten. Der Gewichtsverlust der Gewebeprobe nach
dem Fixierprozeß war nicht höher als bei einem Vergleichsversuch, bei dem das Gewebe
mit einer Flotte, die in diesem Fall nur den Farbstoff, aber kein Quell- und Farbstofflösungsmittel
enthält, geklotzt, getrocknet und unter gleichen Bedingungen fixiert wurde.
Beispiel 7
[0035] Ein mercerisierter Baumwoll-Köper wird mit einer Farbstoffflotte imprägniert, die
20 g/1 des wasserunlöslichen Farbstoffs der Formel II (vgl. Beispiel 2) und 120 g/1
Quell-und Farbstofflösungsmittelgemisch, das 90 Teile eines Umsetzungsprodukts aus
1 Mol Pentaerythrit und 7 Mol Äthylenoxid und 10 Teile eines Umsetzungsprodukts aus
1 Mol Butylamin und 14 Mol Äthylenoxid enthält. Der pH-Wert der Flotte wurde mit Glutarsäure
auf 6 eingestellt. Die Flottenaufnahme betrug 53 %. Das Gewebe wurde 60 Sekunden bei
einer Temperatur von 120°C getrocknet und zur Fixierung des Farbstoffes 60 Sekunden
bei einer Temperatur von 200
0C in einem Labortrockner erhitzt. Die Färbung wird nach der im Beispiel 2 angegebenen
Vorschrift fertiggestellt. Man erhält ohne bedeutende Auswaschverluste eine helle
Rotfärbung mit guten Naß- und Reibechtheiten. Beim Fixierprozeß verdampft praktisch
kein Lösemittel, wie ein Vergleichsversuch zeigt, der in Abwesenheit eines Quell-
und Farbstofflösungsmittels durchgeführt wurde.
r 1 Beispiel 8
[0036] Ein mercerisierter Baumwoll-Köper wurde mit einer wäßrigen Färbeflotte imprägniert,
die 80 g/1 Farbstoff (IV) (vgl. Beispiel 6) und 200 g einer Mischung aus 80 Teilen
eines Polyäthylenglykols mit einem Molgewicht von 800 und 20 Teilen eines Blockpolymeren
aus 1 Mol Äthylendiamin, 8 Mol Propylenoxid und 8 Mol Äthylenoxid enthielt. Der pH-Wert
der Flotte wurde mit Zitronensäure auf 6 gestellt. Die Flottenaufnahme betrug 52
[0037] Anschließend wurde das Gewebe wie üblich bei 120°C getrocknet und 30 Sekunden bei
215°C in einem Labortrockner fixiert. Beim Fixierprozeß verdampfte praktisch kein
Lösemittel. Nach dem Spülen und Waschen erhielt man bei sehr geringem Farbstoffverlust
eine brillante, intensive goldorange Färbung mit guten Echtheiten.
Beispiel 9
[0038] Ein Gewebe aus 67 Teilen Polyesterfaser und 33 Teilen Baumwolle (mercerisiert) wurde
mit einer Flotte imprägniert, die 100 g/1 einer Mischung aus 80 Teilen eines Borsäureesters
von Polyäthylenglykol (Molgewicht etwa 800) im Molverhältnis 1 : 3 und 20 Teilen Äthylendiamin,
umgesetzt mit 35 Mol Äthylenoxid, enthielt. Die Flottenaufnahme betrug 80 %. Anschließend
wurde 15 Minuten bei 60 bis 70°C getrocknet.
[0039] Auf das Substrat wurde folgende Druckpaste gedruckt:
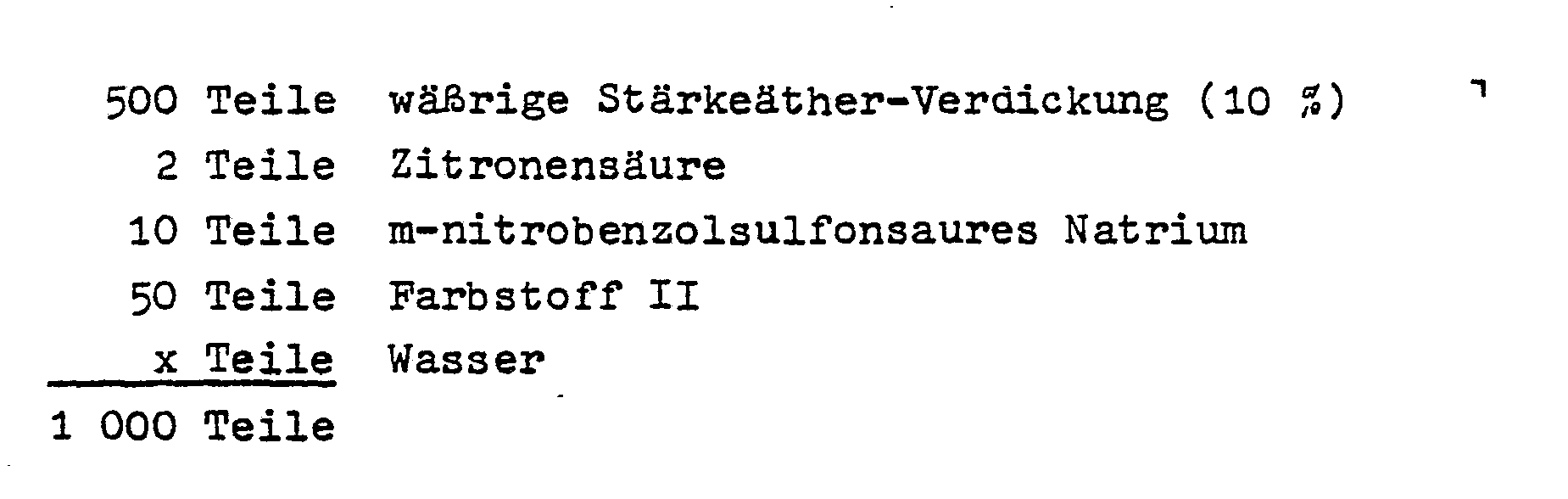
[0040] Nach dem Drucken wurde 2 Minuten bei 130°C getrocknet und 90 Sekunden bei 210°C mit
Heißluft behandelt, kalt und warm gespült, heiß geseift und kalt nachgespült. Bei
der Hitzebehandlung waren keine Lösemittelnebel festzustellen.
[0041] Man erhält einen leuchtend roten Druck auf weißem Fond.
[0042] Beispiel 9 wurde wiederholt, jedoch anstelle des Farbstoffes II mit 50 Teilen des
rotorangenen Farbstoffes
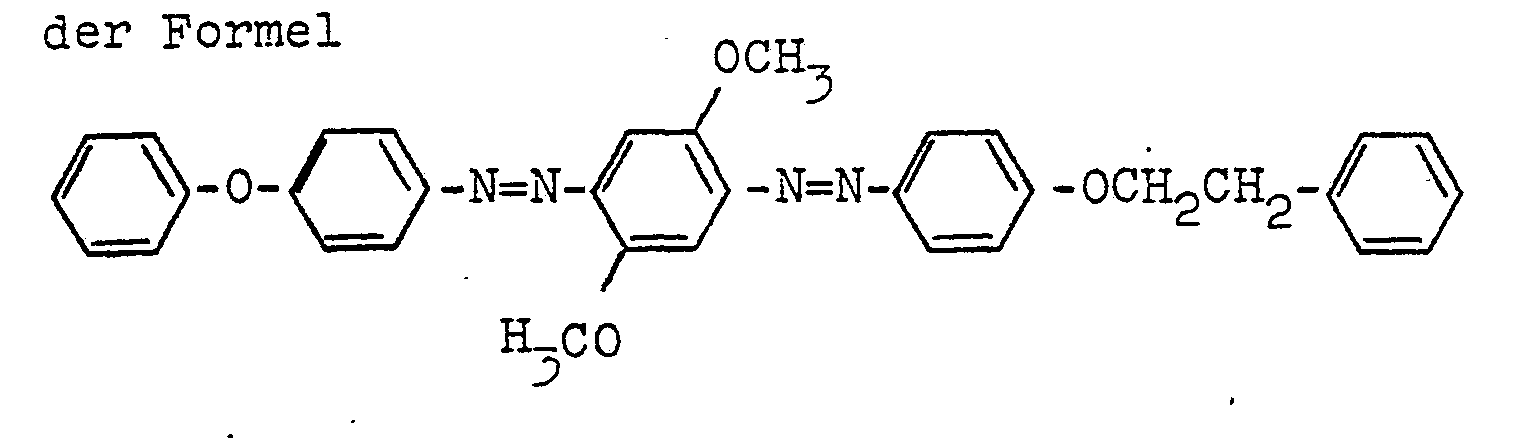
Man erhält eine gute Durchfärbung des Mischgewebes. Beim Fixieren trat keine Nebelbildung
auf.
Beispiel 10
[0043] Ein Gewebe aus Polyester/Baumwolle (im Gewichtsverhältnis 67 : 33) wird mit folgender
Druckpaste bedruckt:

Nach dem Drucken wird wie im Beispiel 9 beschrieben, getrocknet, 4 Minuten bei 190°C
mit Heißdampf behandelt, gespült, geseift und gespült.
[0044] Eine Nebelbildung bei der Hitzebehandlung konnte nicht festgestellt werden. Man erhält
einen klaren gelben Druck auf weißem Fond.
[0045] Die gleichen Ergebnisse erhält man, wenn anstelle des Farbstoffes IV 50 Teile des
gelben Farbstoffes der Formel
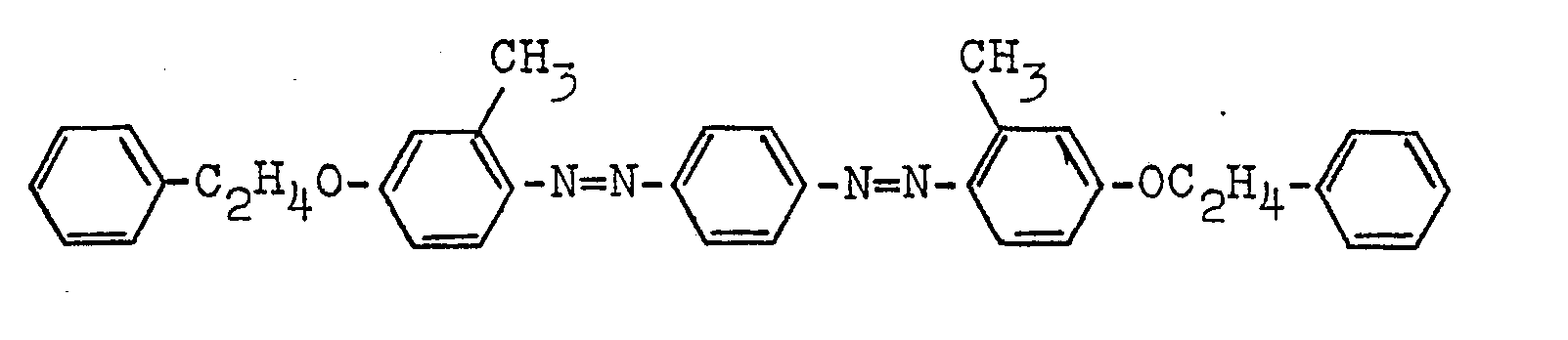
verwendet werden.
Beispiel 11 '
[0046] Beispiel 9 wurde wiederholt, jedoch anstelle des Farbstoffes II mit 50 Teilen des
rotorangenen Farbstoffes der Formel

Man erhält eine gute Durchfärbung des Mischgewebes. Beim Fixieren trat keine Nebelbildung
auf.
Beispiel 12
[0047] Beispiel 4 wurde wiederholt, jedoch mit der Ausnahme, daß anstelle des blauen Farbstoffes
der Formel III dieselbe Menge des braungelben Farbstoffes der Formel
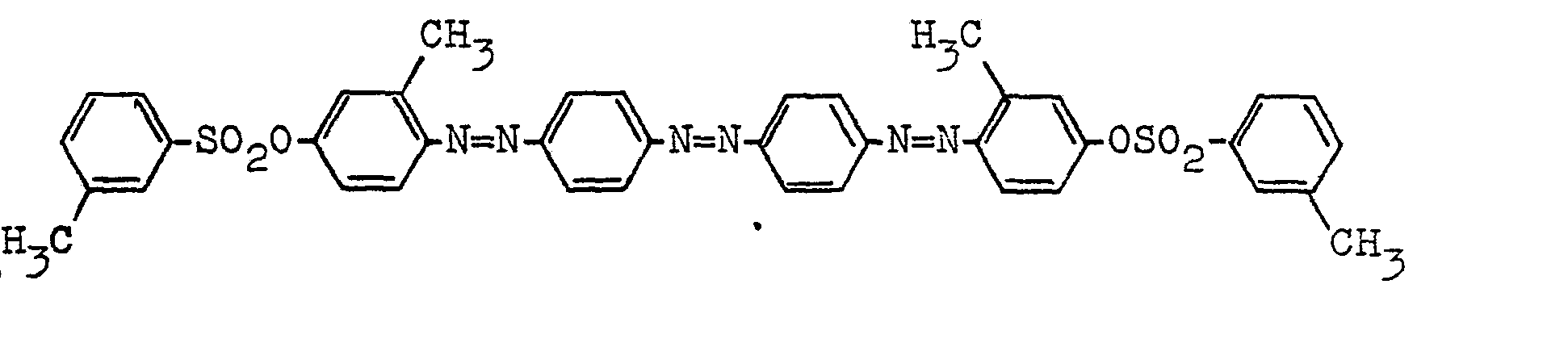
verwendet wurde. Auch in diesem Fall betrug der beim Fixieren verdampfte Anteil des
Quell- und Farbstofflösemittels ca. 5 %.