[0001] Gegenstand der Erfindung ist ein Verfahren zur Herstellung von Hydroxylammoniumsalzen
durch katalytische Reduktion von Stickstoffmonoxid mit Wasserstoff in verdünnten wäßrigen
Lösungen von Mineralsäuren in Gegenwart von suspendierten Platinkatalysatoren bei
erhöhter Temperatur, wobei man das Reaktionsgemisch im Kreis führt.
[0002] Die Herstellung von Hydroxylammoniumsalzen durch Reduktion von Stickstoffmonoxid
mit Wasserstoff in verdünnten Mineralsäuren in Gegenwart von platinhaltigen Katalysatoren
wird, wie z.B. in der DE-AS 24 47 972 beschrieben wird, in Rührbehältern durchgeführt.
Hierbei erzielt man Raum-Zeit-Ausbeuten bis zu 0,43 Mol Stickstoffmonoxid pro Liter
flüssiges Reaktionsgemisch in der Reaktionszone und Stunde. Die Nachteile der Rührbehälter
sind technisch konstruktiv bedingt. Mit zunehmender Größe solcher Rührbehälter wird
die Abdichtung der Rührwellendurchführung durch den Behälter zunehmend schwieriger.
Die Behälter
= und Deckelkonstruktion muß wesentlich aufwendiger ausgeführt werden, um Lasten von
Rührergetriebe und Motor sowie die Rotationskräfte des Rührers aufnehmen zu können.
Darüber hinaus muß die Apparateaufhängung verstärkt werden, um die Schwingungen des
gesamten Systems abfangen zukönnen.
[0003] Dies führt zu technisch sehr aufwendigen Lösungen. Es wird deshalb angestrebt, eine
möglichst hohe Raum-Zeit-Ausbeute mit kleinem Reaktionsvolumen möglichst ohne Verwendung
von Rührvorrichtungen zu erzielen.
[0004] So ist aus der DE-AS 11 93 923 eine Arbeitsweise beschrieben, bei der die Umsetzung
in einer Siebbodenkolonne durchgeführt wird, wobei man die die Reaktionslösung fortlaufend
umpumpt. Nach dem aus den bekanntgemachten Unterlagen der NL-Patentanmeldung 69 08
934 bekannten Verfahren wird eine nach dem Mammutpumpenprinzip arbeitende Reaktionweise
angewandt. Ferner ist aus der DE-OS 15 42 219 auch schon eine Arbeitsweise bekannt,
bei der eine innige Gas-Flüssig-Feststoffvermischung durch Düsen bewirkt und die Dispersion
tangential in die Reaktionszone eingeführt wird. Die vorstehend aufgeführten Arbeitsweisen
sind hinsichtlich der erzielten Raum-Zeit-Ausbeuten noch verbesserungsbedürftig.
[0005] Es war deshalb die technische Aufgabe gestellt, bei der Synthese von Hydroxylammoniumsalzen
durch katalytische Reduktion von Stickstoffmonoxid mit Wasserstoff die Raum-Zeit-Ausbeute
bei den jeweils angewandten Drücken zu erhöhen und gleichzeitig die oben erwähnten
Nachteile zu vermeiden.
[0006] Diese technische Aufgabe wird gelöst in einem Verfahren zur Herstellung von Hydroxylammoniumsalzen
durch katalytische Reduktion von Stickstoffmonoxid mit Wasserstoff in verdünnten wäßrigen
Lösungen von Mineralsäuren in Gegenwart von suspendierten Platinkatalysatoren bei
erhöhter Temperatur unter Rückführung des Reaktionsgemisches, wobei man das im Gasraum
oberhalb der Reaktionszone befindliche Stickstoffmonoxid und Wasserstoff enthaltende
Gasgemisch durch mindestens einen von oben nach unten gerichteten, aus einer Düsenöffnung
austretenden Flüssigkeitsstrahl der im Kreis geführten Reaktionsmischung, in mindestens
eine sich in der Reaktionszone befindliche beidseitig offene Umlaufzone, die sich
in Richtung des eintretenden Flüssigkeitsstrahles erstreckt und
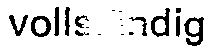
von der Reaktionslösung bedeckt ist,
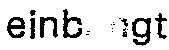
, das unten aus der Umlaufzone austretende nicht umgesetzte Gas enthaltende Reaktionsgemisch
umlenkt, in der die Umlaufzone außen umgebenden ringförmigen Zone nach oben leitet
und gleichzeitig aus einer unterhalb der Reaktionszone befindlichen Trennzone gasarmes
Reaktionsgemisch zurückführt.
[0007] Das neue Verfahren hat den Vorteil, daß unter den jeweils angewandten Drücken bessere
Raum-Zeit-Ausbeuten, bezogen auf Stickoxid erzielt werden. Dies beinhaltet, daß bei
Vorrichtungen vorhandener Größe höhere Durchsätze erzielt werden, oder bei einem vorgegebenen
Durchsatz kleinere Vorrichtungen gewählt werden können. Ferner hat das neue Verfahren
den Vorteil, daß es auf einfache Weise in einen größeren Maßstab übertragen werden
kann.
[0008] In der Regel hält man ein Molverhältnis von Wasserstoff : Stickstoffmonoxid von mehr
als 1, vorzugsweise von 1,5 : 1 bis 6 : 1 ein. Besonders gute Ergebnisse erhält man,
wenn man darauf achtet, daß in der Reaktionszone eine Molverhältnis von Wasserstoff
: Stickstoffmonoxid von 3,5 bis 5 : 1 aufrecht erhalten wird.
[0009] Im allgemeinen verwendet man starke Mineralsäuren, wie Chlorwasserstoffsäure, Salpetersäure,
Schwefelsäure oder Phosphorsäure. Geeignet sind auch deren saure Salze, wie Ammoniumbisulfat.
Besonders bevorzugt wird Schwefelsäure verwendet. In der Regel. geht man von 4 bis
6 normalen wäßrigen Säuren aus und läßt im Verlauf der Reaktion die Säurekonzentration
nicht unter 0,2 normal fallen.
[0010] Die Umsetzung führt man vorzugsweise bei Temperaturen von 30 bis 80°C durch. Besonders
bewarrt haben sich Temperaturen von 40 bis 60°C ie Umsetzung verläuft im allgemeinen
bei Atmosphärendruck. Es hat sich jedoch als vorteilhaft herausgestellt, die Umsetzung
unter erhöhtem Druck, z.B. bis zu 300 bar, durchzuführen.
[0011] Als Platinkatalysatoren werden vorteilhaft Trägerkatalysatoren verwendet; besonders
bewährt haben sich Kohleträgerstoffe. Besondere technische Bedeutung haben Platin-Graphit-Trägerkatalysatoren
erlangt. Vorteilhaft enthält ein solcher Katalysator 0,3 bis 5 Gew. % Platin. Die
Trägerkatalysatoren liegen in feiner Verteilung vor, so daß sie im Reaktionsmedium
suspendiert werden. Vorteilhaft enthalten die Katalysatoren zusätzlich ein oder mehrere
Elemente der 5. und/oder 6. Hauptgruppe des periodischen Systems mit einem Atomgewicht
>31, ferner Blei und/oder Quecksilber als vergiftende Mittel. Geeignete Katalysatoren
und deren Herstellung werden beispielsweise beschrieben in der DE-PS 1088037, DE-PS
920 963, 956 038, 945 752. Auf einen Liter wäßrige Mineralsäure wendet man in der
Regel 1 bis 400 g Platinträgerkatalysator an. Das im Gasraum oberhalb der Reaktionszone
befindliche Wasserstoff und Stickstoffmonoxid enthaltende Gasgemisch wird durch mindestens
einen, von oben nach unten gerichteten, aus einer Düsenöffnung austretenden Flüssigkeitsstrahl
der im Kreis geführten Reaktionsmischung, die im wesentlichen aus wäßrigen Mineralsäure,
Katalysator, gegebenenfalls aus bereits gebildeten Hydroxylammoniumsalzen und etwaigen
Nebenprodukten sowie gelösten und/oder feinzerteilten Gasen besteht, in mindestens
eine sich in der Reaktionszone befindliche, beidseitig offene Umlaufzone, die sich
in Richtung des eintretenden Flüssigkeitsstrahls erstreckt und vollständig von der
wäßrigen Reaktions-, mischung bedeckt ist, eingebracht. Das Gasgemisch kann neben
Wasserstoff und Stickstoffmonoxid auch als Nebenprodukte entstehende Gase wie N
zO sowie Inerte enthalten.
[0012] Es ist möglich, in eine Umlaufzone einen oder mehrere, z.B. drei Flüssigkeitsstrahlen
einzuführen. Andererseits ist es bei der Vergrößerung von Reaktionszonen vorteilhaft,
mehr als eine Umlaufzone zu benützen, z.B. eine zentraje Umlaufzone, die von sechs
weiteren Umlaufzonen umgeben ist. In jede der Umlaufzonen wird dann mindestens ein
Flüssigkeitsstrahl von oben nach unten gerichtet. Im einfachsten Fall ist die Umlaufzone
ein senkrecht zentral in die Reaktionszone eingebrachtes Rohr. Die Umlaufzone oder
Umlaufzonen sind beidseitig offen und erstrecken sich in Richtung des bzw. der eintretenden
Flüssigkeitsstrahlen. Die Umlaufzone ist auch völlig vom Reaktionsgemisch bedeckt.
Die Reaktionszone hat in der Regel ein Verhältnis von Höhe zu Durchmesser von 2 bis
30 : 1, vorzugsweise 5 bis 15 : 1. Das Durchmesserverhältnis von Umlaufzone zu Reaktionszone
beträgt in der Regel etwa 0,7 bis 0,1 und liegt bevorzugt um 0,5.
[0013] Die Geschwindigkeit des eingeleiteten Flüssigkeitsstrahls beträgt vorteilhaft von
5 bis 40 m/sec, vorzugsweise von 10 bis 30 m/sec. Die Menge an zurückgeführter Reaktionslösung
beträgt in der Regel von 10 bis 500, insbesondere 100 bis 400 m
3/m
3 der Reaktionszone und Stunde. Die Geschwindigkeit der Flüssigkeit in der Umlaufzone
soll vorteilhaft um den Faktor 1 bis 6, vorzugsweise 2 bis 4 mal so groß sein wie
in der die Umlaufzone umgebenden ringförmigen Zone. Auf diese Weise werden der Gasgehalt
in der Umlaufzone und in der ringförmigen Zone etwa gleich groß und die Dichtedifferenzen
klein.
[0014] Die Düsenöffnung hat vorteilhaft einen Abstand von dem oberen Ende der Umlaufzone,
der das 0,1- bis 3-, vorzugsweise 0,3- bis 0,9- fache des Durchmessers der Umlaufzone
beträgt.
[0015] Das unten aus der Umlaufzone austretende Reaktionsgemisch und das bis dorthin nicht
verbrauchte Gasgemisch werden umgelenkt. Die Umlenkung wird bewirkt durch eine unterhalb
der Umlaufzone quer angeordnete Umlenkplatte. Diese befindet sich vorteilhaft in einem
Abstand vom unteren Ende der Umlaufzone, der das 0,1- bis 1,0-fache, vorzugsweise
0,2- bis 0,7-fache des Durchmessers der Umlaufzone beträgt. Nicht verbrauchtes Gasgemisch
sowie ein Teil der Flüssigkeit steigen in der ringförmigen Zone, die die Umlaufzone
umgibt, nach oben. Durch den von oben eintretenden Flüssigkeitsstrahl wird das flüssige
Reaktionsgemisch wieder in der Umlaufzone nach unten bewegt und zugleich wird das
sich oberhalb des Flüssigkeitsspiegels befindliche Gasgemisch durch den nach unten
gerichteten Flüssigkeitsstrahl in die Umlaufzone eingebracht und fein verteilt.
[0016] Der Gaseintrag aus Gasphase oberhalb des Flüssigkeitsspiegels wird erfindungsgemäß
durch Eintauchen des Düsenmundes der Düsenöffnung in die Flüssigkeit selbsttatig geregelt,
d.h. wenn der Flüssigkeitsstand tiefer ist, wird mehr Gas eingetragen, bis der Flüssigkeitsstand
ansteigt und umgekehrt, wenn der Flüssigkeitsstand sich über dem Düsenmund befindet,
so wird weniger Gas eingetragen, so daß sich der Flüssigkeitsspiegel senkt. Auf diese
Weise läßt sich auf einfache Weise auch der Ge-, halt an feinverteilten Gasblasen
im Reaktionsgemisch regein. Dies geschieht zweckmäßig so, daß man nach Ingangsetzen
der Umwalzung die Flüssigkeitsmenge in der Reaktionszone durch Ablassen senkt. Es
wird dann so lange eingetragen, bis das Flüssigkeitsniveau die Düsenöffnung erreicht
hat.
[0017] Hierbei steigt das Flüssigkeitsniveau nicht durch vermehrte Zufuhr von flüssigem
Reaktionsgemisch, sondern durch vermehre Gasaufnahme, das in feiner Verteilung in
der Flüssigkeit vorliegt. Vorteilhaft hält man in dem flüssigen Reaktionsgemisch in
der Reaktionszone einen Gasgehalt (Gas-hold-up) von 5 bis 50%, bezogen auf das flüssige
Reaktionsgemisch, ein. 'Die Frisch-Gaszufuhr kann außer über die Gas- ,phase über
der Reaktionszone auch zusätzlich an der Stelle, wo das Reaktionsgemisch umgelenkt
wird, vorteilhaft unter der Umlenkplatte erfolgen. Darüber hinaus ist es auch möglich,
Gasgemisch in den die Umlaufzone umgebenden Ringraum einzuspeisen.
[0018] Es hat sich ferner als vorteilhaft erwiesen, wenn man in der Reaktionszone eine Leistungsdichte
von 1 bis 50, insbesondere 5 bis 30 kW/m
3 in der Reaktionszone befindliches flüssiges Reaktionsgemisch einhält. Die nötige
Leistungsdichte wird durch die Flüssigkeitsstrahlen in das Reaktionsgemisch eingebracht.
Sie ist eine Funktion der Umwälzmenge und des Druckabfalls an der Düsenöffnung.
[0019] Unmittelbar unterhalb der Reaktionszone schließt sich eine Trennzone an, in der sich
mitgerissene Gasblasen von flüssigem Reaktionsgemisch abscheiden. Die Gasblasen wandern
entgegen der Flüssigkeitsströmung nach oben, während das flüssige Reaktionsgemisch
abgezogen und wieder zu der Düsenöffnung oder den Düsenöffnungen zurückgeführt wird.
[0020] Bei dem beanspruchten Verfahren wird also ein Strahlantrieb benutzt, bei dem die.
Düse von oben nach unten arbeitet. Der Treibstrahl bringt Energie für den Umlauf im
Reaktor. Da die Düsenmündung an der Flüssigkeitsoberfläche liegt, trägt der Treibstrabl
Gas in die Flüssigkeit ein, das im Umlaufrohr sehr fein dispergiert wird. Dadurch
wird der Schlupf zwischen Flüssigkeit und Gas sehr klein und eine hohe Umlaufgeschwindigkeit
erzeugt.
[0021] Der größte Teil der in der ringförmigen Zone aufsteigenden Gasblasen wird von der
Flüssigkeitsströmung mit in die Umlaufzone gerissen. Im Gleichgewichtszustand trägt
der Treibstrahl deshalb nur so viel Gas ein, daß der Flüssigkeitsspiegel an die Düsenöffnung
reicht. Damit wird auch der Gasgehalt in der Flüssigkeit begrenzt und kann nie so
groß werden, daß der Umlauf der Gas-Flüssigkeits-Strömung im Reaktor in Gefahr kommen
kann, durch die Bildung von Großblasen zusammenzubrechen. Der Vorteil des erfindungsgemäßen
Verfahrens liegt demnach in der gleichmäßigen Verteilung von Gas und auch des suspendierten
Katalysators in der gesamten Reaktionszone. Beim Abstellen des Reaktors kann die Düsenöffnung
nicht durch abgesetzten Katalysator verstopfen.
[0022] Das Verfahren eignet sich für kontinuierliche und diskontinuierliche Arbeitsweisen.
Bei der kontinuierlichen Fahrweise wird die umzusetzende wäßrige Mineralsäure, gegebenenfalls
im Gemisch mit Hydroxylaminsalzen, in die Reaktionszone stetig eingeführt. Das Reaktionsprodukt
entnimmt man stetig dem äußeren Flüssigkeitsumlauf. Mit der Reaktionsflüssigkeit entnommene
Katalysatormengen werden durch entsprechende Katalysatorzugaben zum Flüssigkeitszulauf
ergänzt. Der gewünschte Gas-hold-up kann durch Variation des Flüssigkeitszulaufs oder
-ablaufs geregelt werden. Der Gas-hold-up kann z.B. durch Bestimmen der scheinbaren
Dichte des Flüssigkeits-Feststoff-Gasgemisches oder der Menge der Flüssigkeit im Reaktionsraum
gemessen werden.
[0023] Hydroxylammoniumsalze werden zur Herstellung von Cyclohexanonoxim, einem Vorprodukt
zur Herstellung von Caprolactam, verwendet.
[0024] Das Verfahren nach der Erfindung sei an folgenden Beispielen veranschaulicht.
Beispiele
[0025] In einer Tauchstrahlvorrichtung gemäß Figur 1, bestehend aus einem Reaktorgefäß (1)
mit Umlaufrohr (2) und Prallplatte (3) und einer außenliegenden Flüssigkeitsumwälzung
(4) mit Pumpe (5) und Wärmetauscher (6) zur Abführung der Reaktionswärme sowie Tauchstrahldüse
(7), Gaszuführung (8, 9) und Gasabführung (10), werden 4, 3 n Schwefelsäure und je
Liter eingesetzte Schwefelsäure 40 g eines Platin-Graphit-Katalysators mit einem Gehalt
von 0,5 Gew.% Pt vorgelegt. Nach Inbetriebnahme der Umwälzung entnimmt man dem Reaktor
soviel Reaktionsmedium, daß der gewünschte Gas-hotd-up erreicht wird. Die umgepumpte
Suspension wird über die Tauchstrahldüse in den Reaktor entspannt.
[0026] Nach Verdrängen der Luft mit H
2 führt man bei 40°C ein aus 36 Vol.% NO und 63 Vol.% H
2 (Rest lntergas) bestehendes Gasgemisch in den Reaktor ein. Das entweichende Abgas
wird gemessen und analysiert. Wenn die Schwefelsäure in der Reaktionslösung fast verbraucht
ist, beendet man die Reaktion, trennt die Hydroxyl-
'aminiösung vom Katalysator ab und bestimmt die gebildete Menge an Hydroxylamin.

1. Verfahren zur Herstellung von Hydroxylammoniumsalzen durch katalytische Reduktion
von Stickstoffmonoxid mit Wasserstoff in verdünnten wäßrigen Lösungen von Mineralsäuren
in Gegenwart von suspendierten Platinkatalysatoren bei erhöhter Temperatur, wobei
man das Reaktionsgemisch im Kreis führt, dadurch gekennzeichnet, daß man das im Gasraum
oberhalb der Reaktionszone befindliche Stickstoffmonoxid und Wasserstoff enthaltende
Gasgemisch durch mindestens einen von oben nach unten gerichteten aus einer Düsenöffnung
austretenden Flüssigkeitsstrahl der im Kreis geführten Reaktionsmischung in mindestens
eine sich in der Reaktionszone befindliche, beidseitig offene Umlaufzone, die sich
in Richtung des eintretenden Flüssigkeitsstrahles erstreckt und vollständig vom Reaktionsgemisch
bedeckt ist, einbringt, das unten aus der Umlaufzone austretende nicht umgesetzte
Gase enthaltende Reaktionsgemisch umlenkt, in der die Umlaufzone außen umgebenden
ringförmigen Zone nach oben leitet und gleichzeitig aus einer unter der Reaktionszone
befindlichen Trennzone gasarmes Reaktionsgemisch zurückführt.
2. Verfahren nach Anspruch 1, dadurch gekennzeichnet, daß man Stickstoffmonoxid und
Wasserstoff an der Düsenöffnung zuführt.
3. Verfahren nach Anspruch 1, dadurch gekennzeichnet, daß man Stickstoffmonoxid und
Wasserstoff dicht unterhalb der Stelle, an der das aus der Umlaufzone austretende
Reaktionsgemisch umgelenkt wird, zuführt.
4. Verfahren nach den Ansprüchen 1 bis 3, dadurch gekennzeichnet, daß die Reaktionsmischung
in der Reaktionszone einen GasGehalt von 5 bis 50 Vol.% hat.
5. Verfahren nach den Ansprüchen 1 bis 4, dadurch gekennzeichnet, daß man in der Reaktionszone
eine Leistungsdichte von 1 bis 50 kW/m3 flüssiges Reaktionsgemisch in der Reaktionszone einhält.
1. A process for the manufacture of hydroxylammonium salts by the catalytic reduction
of nitric oxide with hydrogen in a dilute aqueous solution of a mineral acid in the
presence of a suspended platinum catalyst at an elevated temperature, wherein the
reaction mixture is recycled, characterized in that the gas mixture, containing nitric
oxide and hydrogen, present in the gas space above the reaction zone is introduced,
by means of one or more downwardly directed jets of liquid, consisting of the recycled
reaction mixture and issuing from a nozzle orifice, into one or more circulation zones
which are present in the reaction zone, are open at both sides, extend in the direction
of the entering jet of liquid and are completely covered by the reaction mixture,
the reaction mixture leaving the bottom of the circulation zone and containing unconverted
gases is deflected, passed upwards in the annular zone externally surrounding the
circulation zone, and at the same time reaction mixture of low gas content is recycled
from a separation zone located under the reaction zone.
2. A process as claimed in claim 1, characterized in that nitric oxide and hydrogen
are fed to the nozzle orifice.
3. A process as claimed in claim 1, characterized in that nitric oxide and hydrogen.
are fed to a point just below the point at which the reaction mixture, issuing from
the circulation zone is deflected.
4. A process as claimed in claims 1 to 3, characterized in that the reaction mixture
in the reaction zone contains from 5 to 5096 by volume of gas.
5. A process as claimed in claims 1 to 4, characterized in that an energy density
of from 1 to 50 kW/m3 of liquid reaction mixture in the reaction zone is maintained in the said zone.
1. Procédé de préparation de sels d'hydroxylammonium par réduction catalysée de l'oxyde
azotique par l'hydrogène dans une solution aqueuse diluée d'un acide minéral à température
accrue et en présence d'un catalyseur au platine en suspension, le mélange réactionnel
circulant en circuit, caractérisé en ce que l'on fait passer le mélange gazeux, contenant
de l'oxyde azotique et de l'hydrogène, se trouvant dans la partie du réacteur surmontant
la zone de réaction et remplie de produits gazeux, à l'aide d'au moins un jet de la
solution réactionnelle circulant en circuit, injecté de haut en bas par une tuyère,
dans au moins une zone de circulation s'étendant dans la direction d'injection du
jet de liquide et ouverte des deux côtés, située dans la zone de réaction et entièrement
noyée dans le mélange réactionnel, tandis que le mélange réactionnel contenant les
produits gazeux n'ayant pas réagi, sortant de l'extrémité inférieure de la zone de
circulation, est dévié et ramené à travers une zone annulaire, entourant la zone de
circulation, dans la partie supérieure du réacteur avec recyclage simultané de mélange
réactionnel pauvre en produits gazeux, provenant d'une zone de séparation disposée
sous la zone de réaction.
2. Procédé suivant la revendication 1, caractérisé en ce que l'introduction de l'oxyde
azotique et de l'hydrogène s'effectue au niveau de l'embouchure de la tuyère d'injection.
3. Procédé suivant la revendication 1, caractérisé en ce que l'introduction de l'oxyde
azotique et de l'hydrogène s'effectue à un niveau disposé juste en dessous de l'endroit
de déviation du mélange réactionnel sortant de la zone de circulation.
4. Procédé suivant l'une quelconque des revendications 1 à 3, caractérisé en ce que,
dans la zone de réaction, le mélange réactionnel contient entre 5 et 5096 en volume
de produits gazeux.
5. Procédé suivant l'une quelconque des revendications 1 à 4, caractérisé en ce que,
dans la zone de réaction, la densité de puissance est maintenue entre 1 et 50 kilowatts
par m3 de mélange réactionnel liquide contenu dans cette zone de réaction.