[0001] La présente invention concerne un procédé de traitement thermique des alliages Fe-Co-Cr
destinés à la fabrication d'aimants permanents ainsi que les aimants réalisés par
ce procédé. Ces alliages ont pour composition (en poids):
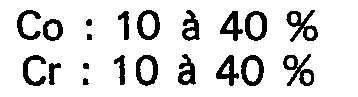
éventuellement un ou plusiers des éléments AI, Nb, Ta, W, Mo, V, Ti, Si, Cu en quantité
totale inférieure à 10 %, le reste étant du fer.
[0002] Le brevet français n°2.149.076 décrit certains alliages de ce type ainsi que leurs
traitements thermiques. On moule une première forme que l'on soumet à un traitement
d'homogénéisation à haute température entre 1200 et 1400°C pendant plus de 10 minutes,
suivi d'une trempe rapide jusqu'à la température ambiante. A ce stade, le corps moulé
peut subir, sans difficulté particulière, diverses opérations de mise en forme telles
que laminage, perçage, usinage, etc... pour l'amener à une forme proche de la forme
définitive.
[0003] Ensuite, le corps est soumis à un traitement isotherme de recuit dans un champ magnétique,
à une température comprise entre 580 et 650°C (de préférence 600 à 640°C) pendant
une période de 10 minutes à 2 heures, mais préférentiellement de l'ordre de 30 minutes.
Après retour à la température ambiante, la pièce est soumise à un ou plusieurs revenus
à des températures comprises entre 530 et 650°C pendant 1 à 9 h, ces revenus pouvant
se faire à des températures étagées décroissantes. On constate alors que ces différents
revenus ont tendance à diminuer la rectangularité du cycle d'hystérésis mesurée par
le rapport q entre l'énergie spécifique (BH) max et le produit Br Hc de l'induction
rémanente par le champ coercitif.
[0004] D'autre part, si l'on veut obtenir une énergie spécifique (BH) max supérieure à 40
kJ/m
3 (5.10
8 Gauss-Oersteds), il faut procéder, comme le montre l'exemple 12 du brevet francais
précité, à une opération de corroyage supplémentaire (laminage ou forgeage) entraînant
une réduction de la section transversale de la pièce. L'expérience montre que, dans
de nombreux cas, cette opération conduit à une fissuration ou une rupture de la pièce
due au fait qu'à ce stade, l'alliage est biphasé et fragile.
[0005] Le but de la présente invention est d'éviter ces inconvénients et de permettre la
fabrication d'aimants permanents anisotropes du type Fe-Cr-Co présentant un coefficient
il de rectangularité de la courbe d'hystérésis constant au cours des revenus et dont
l'énergie spécifique peut dépasser 40 kJ/m
3 (5.10
8 Gaus-Oersteds) sans opération de corroyage supplémentaire et, donc, sans risque de
rupture.
[0006] Elle peut permettre également la fabrication d'aimants permanents isotropes dont
la courbe d'hystérésis présente une rectangularité plus grande que celle obtenue aec
les traitements connus.
[0007] L'invention consiste à réaliser le traitement de recuit qui suit la trempe après
homogénéisation en deux étapes:
- une première étape à une température comprise entre 630 et 670°C, pendant une durée
comprise entre 5 et 30 minutes;
-une seconde étape immédiatement après, sans retour à basse température , à une température
inférieure de 40 à 70°C à la précédente pendant au moins 10 minutes.
[0008] La durée la première étape est suffisamment courte pour éviter la précipitation de
la phase u fragile dans l'alliage. La température de maintien pendant cette première
étape est comprise de préférence entre 640 et 660°C.
[0009] Le traitement de revenu se fait préférentiellement en trois étapes de durée croissante
à des températures étagées décroissantes d'environ 30°C. Ces étapes peuvent être enchaînées
ou séparées par des retours à la température ambiante.
[0010] Pour réaliser des aimants permanents anisotropes, on applique, pendant la première
étape du recuit, un champ magnétique dont la courbure des lignes de champ est appropriée
à l'application envisagée de l'aimant. La seconde étape du recuit peut se faire avec
ou sans action d'un champ magnétique.
[0011] Bien entendu, pour obtenir des aimants isotropes, le traitement de recuit ne comporte
aucune action d'un champ magnétique.
[0012] Les alliages mis en oeuvre dans le procédé selon l'invention peuvent être obtenus
de manières diverses, par exemple par fusion des éléments constitutifs à l'état pur
ou à l'état préallié, ou par frittage de mélanges pluvérulents des éléments constitutifs
ou d'alliages de ces éléments. On peut également appliquer le procédé à des alliages
auxquels on a conféré une structure cristalline priviligiée par des moyens connus
(gradient thermique, fusion de zone, etc...).
[0013] L'invention sera Illustrée par les exemples de réalisation suivants et par la figure
unique qui repre- sente un schéma du traitement thermique d'un alliage selon l'invention,
pour obtenir un aimant anisotrope, la partie hachurée de la courbe représentant la
zone de temps et de température où il est nécessaire d'appliquer un champ magnétique.
Exemple 1
[0014] On a coulé un alliage Fe-Co-Cr de composition suivante (en poids):
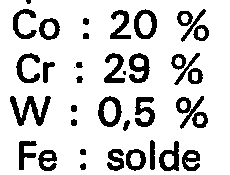
et on lui a fit subir le traitement thermique suivant, schématisé sur la figure:
1 ) homogénéisation à 1300°C suivie d'une trempe à l'eau jusqu'à température ambiante
2) chauffage jusqu'à 655°C et maintien, pendant 15 minutes, en présence d'un champ
magnétique de 159 kA/m (2000 Oersteds),
3) refroidissement en 5 minutes, en présence du champ magnétique ci-dessus jusqu'à
600°C,
4) maintien à 600°C, pendant 15 minutes, sans champ magnetique,
5) trempe à l'eau ou refroidissement à l'air jusqu'à la température ambiante,
6) revenus étages 1 h30 à 580°, puis 5 h à 550°C, puis 15 h à 520°C.
[0015] A titre de comparaison, on a réalisé le traitement de l'art antérieur dans lequel,
après les 15 minutes à 655°C, on est descendu en 15 minutes à 400°C. On a mesuré,
dans chaque cas, les caractéristiques magnétiques de l'aimant obtenu, et établi le
rapport:
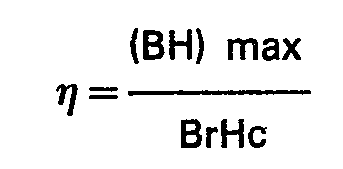
[0016] Les résultats ont été rassemblés dans le tableau I dans lequel on a désigné par:
-A et B deux résultats d'essais dans une même coulée pour laquelle le recuit a été
fait, selon l'invention, en deux étapes,
-C et D deux résultats issus de la même coulée que ci-dessus ayant subi le traitement
de comparaison,
-1, 2 et 3 les mesures faites respectivement après le recuit, après le deuxiéme revenu
et après le troisième revenu.
[0017] Ces résultats montrent clairement qu'avec le procédé selon l'invention, on obtient
des aimants anisotropes ayant une énergie spécifique supérieure à 40 kJ/m
3 et un coefficient η supérieur à 0,60, ce qui n'était pas possible avec le procédé
de l'art antérieur sans opération supplémentaire de corroyage. De plus, le durées
de traitement sont raisonables et n'élèvent pas le prix de revient.
Exemple 2
[0018] De même, on a appliqué un traitement identique selon l'invention, mais, cette fois,
en l'absence de champ magnétique pour réaliser des aimants isotropes et un traitement
de comparaison selon fart antérieur identique au cas précédent, mais sans champ magnétique.
[0020] On constate que le traitement A selon l'invention améliore notablement les propiétés
magnétiques d'un aimant isotrope, en particulier en ce qui concerne la recatangularité
de la courbe d'hystérésis.
Exemple 3
[0021] On a traité une composition constitutée (en poids) de 17 % Co, 26 Cr, 0,5 % W, le
reste étant essentiellement du fer, de la façon suivante:
- homogénéisation à 1320°C pendant 1h et trempe à l'eau,
- chauffage jusqu'à 655°C maintenu 15 minutes en présence d'un champ magnétique de
159 kA/m (2000 Oersteds),
-refroidissement en 5 minutes à 590°C en présence du champ magnétique,
-maintien à 590°C (sans champ) pendant 30 minutes et trempe à l'eau,
-trois revenus étagés 1h30 à 580°C, puis 5 h à 550°C, puis 15 h à 520°C.
[0022] Les résultats de deux essais effectués sur cette composition après recuit (1) après
le deuxième revenu (2) et après le troisième revenu (3), sont les suivants:
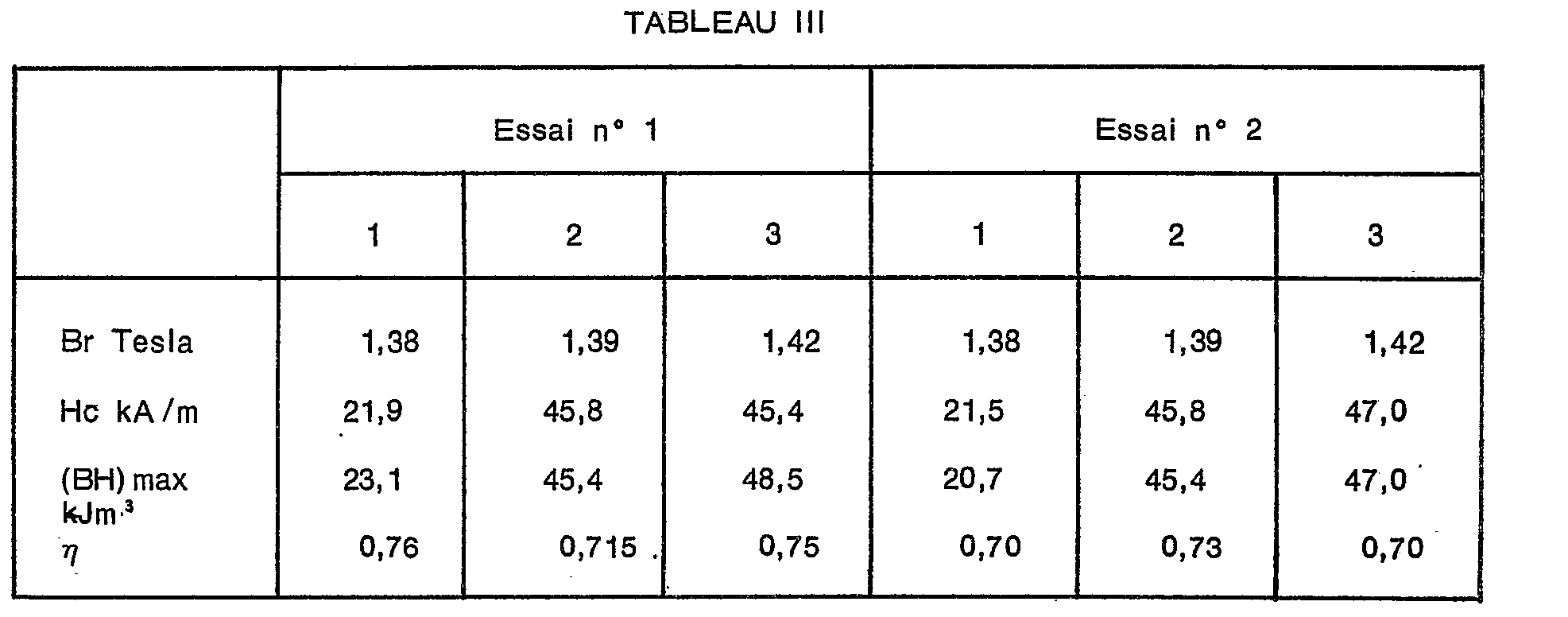
Exemple 4
[0023] On a traité une composition comprenant (en poids)15 % de Co, 24 % de Cr, 1 % W, le
solde étant essentiellement du fer, de la manière suivante:
- homogénéisation à 1250°C pendant 1 h, suivie d'une trempe à l'eau,
- chauffage à 670°C et maintien pendant 15 minutes en présence d'un champ magnétique
de 159 kA/m (2000 Oersteds),
-refroidissement en 5 minutes à 590°C (sous champ) et maintien pendant 30 minutes
(hors champ) suivi d'une trempe à l'eau (ou d'un refroidissement à l'air) jusqu'à
la température ambiante,
-triple revenu étagé de 1 h 30 à 580°C, puis 5 h à 550°C, puis 15 h à 520°C.
[0024] Les résultats obtenus sur deux échantillons sont reportés dans le tableau IV suivant
(avec les mêmes notations).
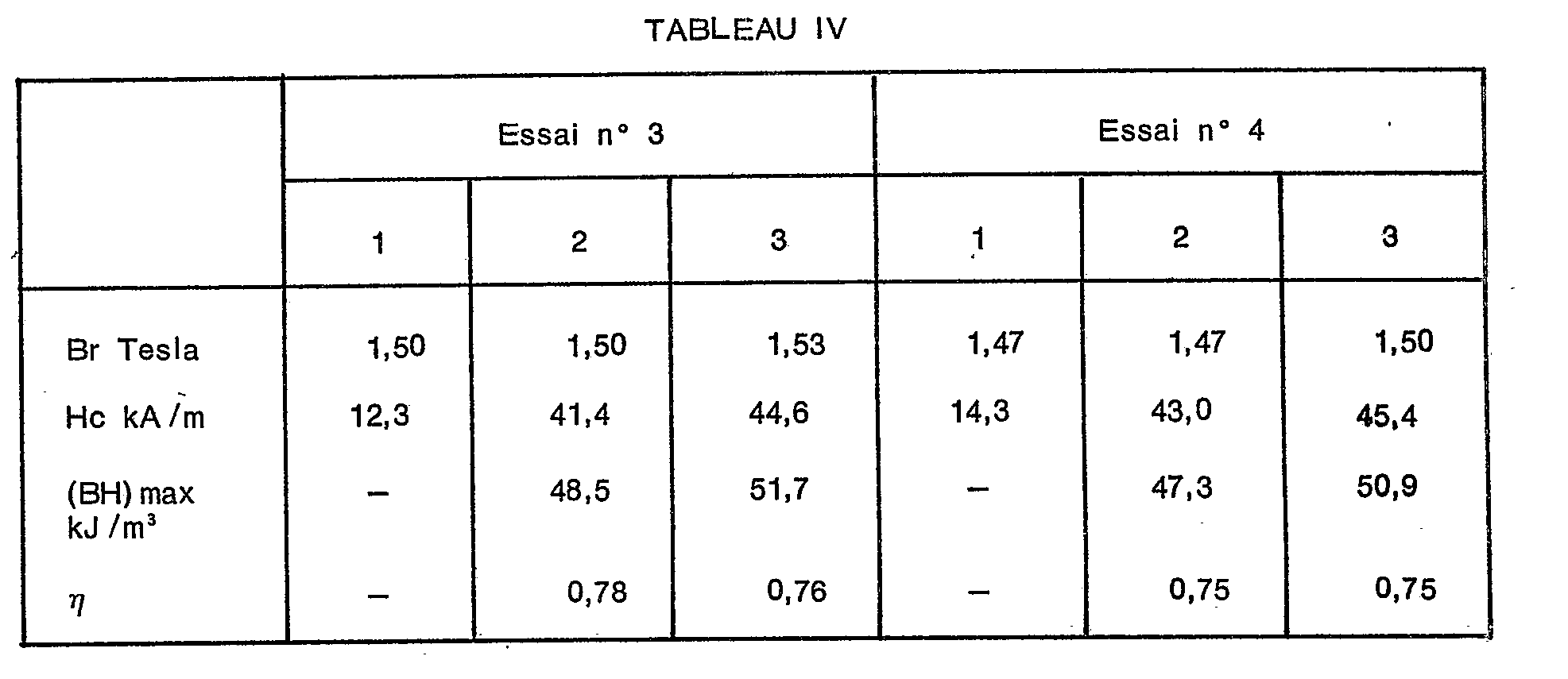
[0025] On peut constater que les compositions faiblement alliées (en Co et Cr) exemples
3 et 4, présentent des valeurs de BHmax et de η largement supérieures à celles obtenues
avec les alliages chargés (exemple 1 ) représentatifs de l'état de la technique, et
que le plus faiblement allié (exemple 4) offre lui- même des caractéristiques magnétiques
supérieures ou équivalentes à celles de l'alliage de composition intermédiaire (exemple
3).
1. Procédé de traitement thermique d'un alliage Fe-Co-Cr pour aimant permanent constitué
de 10 à 40 % de Co, 10 à 40 % de Cr, de 0 à 10 % d'un ou plusieurs des éléments du
groupe AI, Nb, Ta, W, Mo, V, Ti, Si et Cu, le reste étant du fer, comportant une homogénéisation
entre 1200 et 1400°C pendant au moins 10 minutes, suivie d'une trempe rapide un recuit
et un ou plusieurs revenus à des températures comprises entre 500 et 600°C, caractérisé
en ce que le recuit est réalisé en deux étapes:
- une première étape à une température comprise entre 630 et 670°C pendant une durée
comprise entre 5 et 30 minutes,
-une seconde étape suivant immédiatement la première sans retour à basse température
à une température inférieure de 40 à 70°C à la précédente pendant au moins 10 minutes.
2. Procédé selon la revendication 1, destiné à la fabrication d'un aimant permanent
anisotrope, caractérisé en ce qu'on applique un champ magnétique au moins dans la
première étape du recuit.
3. Procédé selon l'une des revendications 1 et 2, caractérisé en ce que la température
de la première étape du recuit est comprise entre 640 et 660°C.
4. Procédé selon l'une quelconque des revendications 1 à 3, caractérisé en ce que
le traitement de revenu est effectué en trois étapes de durées croissantes à des températures
étagées décroissantes d'environ 30°C l'une par rapport a l'autre.
5. Aimant permanent anisotrope réalisé par le procédé selon l'une quelconque des revendications
2 à 4, présentant une énergie spécifique BH max supérieure à 40 kJ/m3 (5.108 Gauss-Oersteds), caractérisé en ce que son coefficient il de reçtanqularité du cycle
d'hystérésis est supérieur ou égal à 0,60.
1. A process for the thermal treatment of a Fe-Co-Cr alloy for a permanent magnet
composed of 10 to 40% of Co, 10 to 40% of Cr; 0 to 10% of one or more of the following
elements Al, Nb, Ta, W, Mo, T, Si and Cu; Fe, remainder, comprising an homogenisation
at between 1200 and 1400°C for at least 10 minutes, followed by a rapid quenching,
an annealing treatment and one or several tempering at temperatures comprised between
500 and 600°C, characterised in that the annealing is conducted in two stages, wherein
the first stage is at a temperature of between 630 and 670°C for a period ofi between
5 and 30 minutes and the second stage which follows immediately after the first stage
without a return to low temperature and at a temperature of from 40 to 70°C below
the first stage and for at least 10 minutes.
2. A process as defined in claim 1, for the manufacture of anisotropic permanent magnet,
characterised in that the magnetic field is applied to the alloy at least during the
first annealing stage.
3. A process according to either claims 1 or 2 characterised in that the temperature
of the first annealing stage is between 640 and 660°C.
4. A process according to either of Claims 1, 2 or 3, and further characterised in
that the tempering treatment is conducted in three stages of increasing duration at
decreasng temperatures of approximately 30°C each other.
5. An anisotropic permanent magnet produced by the process according one of the claims
2 to 4, said magnet having a maximum specific energy BH max above 40 kJ/m3(5.106 Gauss-Oersteds), characterised in that its coefficient 11 of rectangularity of the hysteresis cycle is greater than, or egal to 0.60.
1. Verfahren zur Wärmebehandlung einer Fe-Co-Cr-legierung für Dauermagnet, die aus
10 bis 40 % Co, 10 bis 40 % Cr, 0 bis 10 % eines oder mehrerer der Elemente der Gruppe
Al, Nb, Ta, W, Mo, V, Ti, Si und Cu, Rest Fe zusammengesezt ist, das eine Homogenisierung
zwischen 1200 und 1400°C während wenigstens 10 Minuten mit anschließendem raschen
Abschrecken, ein Glühen une eine oder mehrere Anlaßbehandlungen bei Temperaturen zwischen
500 und 600°C umfaßt,
dadurch gekennzeichnet, daß das Glühen in zwei Stufen erfolgt:
-einer ersten Stufe bei einer Temperatur zwischen 630 und 670°C während einer Dauer
zwischen 5 und 30 Minuten,
- einer zweiten, unmittelbar nach der ersten ohne Rückkehr auf niedrige Temperatur
folgenden Stufe bei einer um 40 bis 70°C niedrigeren Temperatur als der vorangehenden
während wenigstens 10 Minuten.
2. Verfahren nach Anspruch 1, bestimmt zur Herstellung eines anisotropen Dauermagnets,
dadurch gekennzeichnet,
daß man wenigstens in der ersten Glühstufe ein Magnetfeld anlegt.
3. Verfahren nach Anspruch 1 oder 2,
dadurch gekennzeichnet,
daß die Temperatur der ersten Glühstufe zwischen 640 und 660°C liegt.
4. Verfahren nach einem der Ansprüche 1 bis 3,
dadurch gekennzeichnet,
daß die Anlaßbehandlung in drei Stufen wachsender Dauer bei abgestuften von einer
zur anderen um etwa 30°C abfallenden Temperaturen durchgeführt wird.
5. Anisotroper Dauermagnet, der nach dem Verfahren gemäß einem der Ansprüche 2 bis
4 hergestellt ist und eine spezifische Energie BHmax über 40 kJ/m3 (5.106 Gauss-Oersteds). aufweist, dadurch gekennzeichnet,
daß sein Rechteckigkeitskoeffizient η der Hystereseschleife über oder gleich 0,60
ist.