[0001] Aus den DE-OS 24 59 765 und 26 20 010 sind Verfahren zur Herstellung von Carbamaten
und Carbamatgemischen durch Umsetzung von Alkoholen und Polyäthylenglykolen mit Harnstoff
in Gegenwart von Nickelionen enthaltenden Ionenaustauschern bekannt. Die so erhältlichen
Produkte sind zwar ausgezeichnete Textilausrüstungsmittel, jedoch bräunlich bis braun
verfärbt, was meist als störend empfunden wird.
[0002] Der vorliegenden Erfindung lag daher die Aufgabe zugrunde, ein auf technisch leicht
zugänglichen Ausgangsstoffen basierendes Verfahren zur Herstellung derartiger, jedoch
möglichst farbloser Textilausrüstungsmittel zu entwickeln, die gleichzeitig in der
Gesamtheit ihrer anwendungstechnischeh Eigenschaften noch weiter verbessert sind.
[0003] Die Lösung dieser Aufgabe wurde in dem Verfahren gemäß Anspruch 2 gefunden. Die so
erhältlichen Ausrüstungsmittel sind nicht nur farblos oder fast farblos, sondern weisen
darüber hinaus folgende sehr wesentlichen Eigenschaften auf: Lagerbeständigkeit der
neutralen Lösung und Badstabilität in saurer Lösung bei gleichzeitig guter Reaktivität;
auf dem ausgerüsteten Textilgut hohe Chlor- und Hydrolysebeständigkeit; gute Abriebfestigkeit;
angenehmer textiler Griff auch ohne Weichmacherzusatz; geringe Anschmutzbarkeit; geringe
Formaldehydabspaltung. Schließlich lassen sich die ausgerüsteten Textilien sehr gut
bedrucken. Die Kombination der Farblosigkeit mit allen diesen hervorragenden Eigenschaften,
denen praktisch keine Nachteile gegenüberstehen, macht das erfindungsgemäß erhältliche
Ausrüstungsmittel höchst wertvoll.
[0004] Zur Umsetzung in erster Stufe werden etwa äquimolare Mengen (ein evtl. Überschuß
der einen oder anderen Komponente kann in der zweiten Stufe ausgeglichen werden) Harnstoff
und Polyäthylenglykol III (dessen eines Kettenende mit Methyl-, Äthyl-, Propyl- oder
Butylalkohol veräthert sein kann; bevorzugt werden aber die freien, d.h. an beiden
Kettenenden unverätherten Polyäthylenglykole) vom Polymerisationsgrad 9 bis 100, vorzugsweise
9 bis 20, zweckmäßig in einem Inertgasstrom zwecks Luftausschluß und Abführung des
entstehenden Ammoniaks, ohne Katalysator unter Rühren einige (etwa 2 bis 7, vorzugsweise
3 bis 6) Stunden auf 130 bis 160, vorzugsweise 145 bis 155°C erhitzt. Die Reaktion
kann drucklos oder unter Druck kontinuierlich oder diskontinuierlich mit oder vorzugsweise
ohne Lösungsmittel durchgeführt werden. Als Lösungsmittel kommen unter den Reaktionsbedingungen
inerte, höher siedende organische Flüssigkeiten, z.B. aromatische oder araliphatische
Kohlenwasserstoffe in Betracht, beispielsweise Toluol, Xylol, Äthylbenzol, Isopropylbenzol
und deren Gemische. Das Lösungsmittel wird nach der Umsetzung abdestilliert.
[0005] Die Umsetzung erfolgt nach der Gleichung
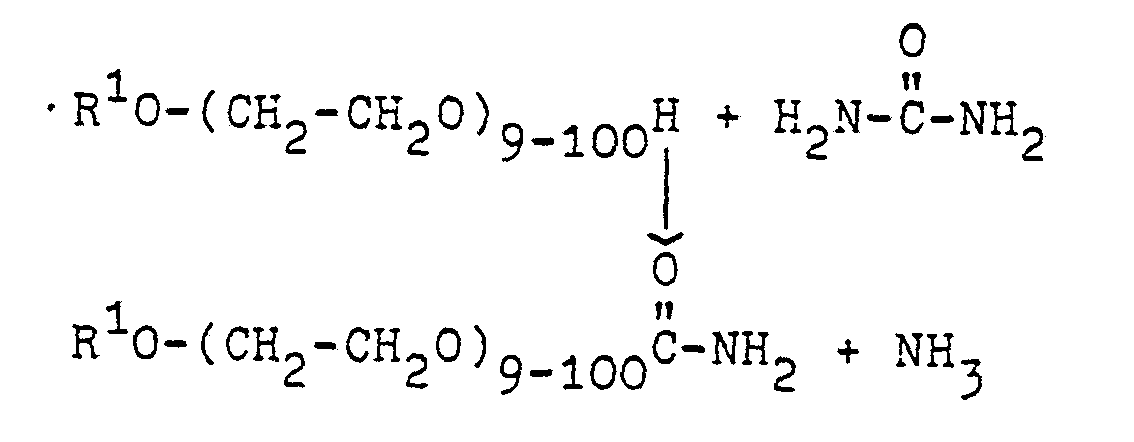
[0006] Bei R1 = H verläuft die Reaktion natürlich nicht vollständig nach dem obigen idealisierten
Schema, sondern es entstehen auch Dicarbamate durch Reaktion beider Hydroxyl--Endgruppen
des Polyäthylenglykols, während ein Teil des letztgenannten gar nicht reagiert. Für
die Zwecke der , vorliegenden Erfindung spielt das aber keine Rolle und bleibt daher
im folgenden außer Betracht, d.h. es wird vom "Monocarbamat" gesprochen, obwohl das
tatsächlich vorliegende Reaktionsgemisch gemeint ist.
[0007] Wenn diese Umsetzung zu mindestens 50, vorzugsweise mindestens 65, insbesondere mehr
als 80 % erfolgt ist (wobei im Falle von R
1 = H als 100 % die Umsetzung von im Mittel je einer der beiden Hydroxylgruppen des
Polyäthylenglykols anzusehen ist; der Umsetzungsgrad kann beispielsweise am Restharnstoffgehalt
erkannt werden) kann man mit der zweiten Stufe beginnen, bei der die analoge Umsetzung
erfolgt und die erste ggf. vervollständigt wird.
[0008] Dazu gibt man zu der Reaktionsmischung unter Rühren weiteren Harnstoff, das Alkylglykol
oder Glykol IV, vorzugsweise Methylglykol, und ggf. den Katalysator und erhitzt zweckmäßig
unter forgesetztem Druchleiten des Inertgasstromes oder im Vakuum 2 bis 40, vorzugsweise
5 bis 20 Stunden weiter, und zwar vorzugsweise mit Katalysator auf.130 bis 165, insbesondere
145 bis 155°C, oder ohne Katalysator auf 150 bis 200, insbesondere 160 bis 190°C,
wobei jeweils eine tiefere Temperatur selbstverständlich einer längeren Reaktionszeit
entspricht und umgekehrt. Die Reaktionstemperatur ist nur insoweit von Bedeutung,
als bei zu hohen Temperaturen mit Verfärbungen zu rechnen ist und bei zu tiefen Temperaturen
sich die Reaktionszeit übermäßig erhöht. Das Molverhältnis von Alkylglykol bzw. Glykol
IV zu dem für die 2. Stufe eingesetzten Harnstoff soll 1 : (0,5 bis 1), vorzugsweise
etwa 1 : 1 betragen. Beim Verhältnis 1 : ( 1) wird der Überschuß an IV anschließend
abdestilliert. Das Molverhältnis von Carbamat I zu Carbamat II liegt im Bereich von
12 : 1 bis 1 : 20, vorzugsweise von 1 : 1 bis 1 : 15, , insbesondere von 1 : 2,5 bis
1 : 12, wobei der Bereich von 12 : 1 bis etwa 1 : 1 nur für Polyester-Baumwoll--Mischware
in Betracht kommt.
[0009] Der in der 2. Stufe zweckmäßig eingesetzte Katalysator besteht aus Nickelionen enthaltenden,
in der Regel sauren Ionenaustauschern, vorzugsweise sauren Kunstharzaustauschern.
Solche Austauscher sind z.B. in Houben-Weyl, Methoden der Organischen Chemie, Band
1/1, Seite 528, Tabelle 3 beschrieben. Vorzugsweise verwendet man stark und mittelstark
saure Austauscher, z.B. Phenol- oder Polystyrolsulfonsäureharze, oder entsprechende
saure Harze enthaltende Austauscher, z.B. bifunktionelle Kondensationsharze. Man kann
auch Styrolphosphonsäure-, Styrolphosphinsäure-, Resorcinharze und aliphatische oder
aromatische Carbonsäureharze verwenden. Vorgenannte Kationenaustauscher sind im Handel
in zahlreichen Varianten erhältlich. Der Austauscher wird vor der Umsetzung nach den
üblichen Methoden mit Nickel beladen, zweckmäßig durch eine Behandlung mit Lösungen,
vorteilhaft wäßrigen Lösungen, von Nickelsalzen. Als Nickelsalz kommen zweckmäßig
Nickelchlorid, -acetat, -bromid, -nitrat oder vorzugsweise Nickelsulfat in Betracht.
Die Nickelverbindungen können auch als entsprechende Hydrate, z.B. Nickelchlorid-Hexahydrat,
vorliegen. Man kann aber auch z.B. Nickelphosphat, Nickelcarbonat, Nickelbicarbonat,
Nickelborat, Nickeloxalat, Nickelpropionat verwenden. Zweckmäßig aktiviert man den
Austauscher vor der Behandlung mit dem Nickelsalz mit Säure, vorzugsweise mit Schwefelsäure
oder der dem Anion des Nickelsalzes entsprechenden Säure. Vorteilhaft beläßt man den
Austauscher zuerst während 10 bis 30 Minuten unter bzw. in Wasser bei einer Temperatur
von 15 bis 40°C, aktiviert dann während 10 bis 60 Minuten mit Säure, zweckmäßig in
Gestalt , einer 2- bis 15-gewichtsprozentigen, wäßrigen Lösung, bei einer Temperatur
von 15 bis 40°C und wäscht den Austauscher mit Wasser bis zum Neutralpunkt. Die Behandlung
mit der Nickelsalzlösung wird zweckmäßig bei Temperaturen zwischen 10 und 50°C, vorteilhaft
zwischen 20 und 30°C, durchgeführt. Die Umsetzung kann drucklos oder unter Druck,
diskontinuierlich, z.B. nach einem Einrühr- oder Chargenverfahren, oder vorzugsweise
kontinuierlich, z.B. in Austauschersäulen, im Festbett, Fließbett, in der Wirbelfließschicht,
in Bodenkolonnen durchgeführt werden. Zweckmäßig verwendet man 5- bis 50-gewichtsprozentige
Nickelsalzlösungen und Behandlungszeiten von 10 bis 60 Minuten. Anschließend wird
vorteilhaft mit Wasser gespült, bis die aus der Austauschersäule austretende Waschflüssigkeit
neutral reagiert, und dann wird mit einem der vorgenannten inerten Lösungsmittel oder
einem Alkohol während 10 bis 60 Minuten bei 15 bis 40°C weitgehend wasserfrei gewaschen.
Zweckmäßig sind eine Beladung von 0,01 bis 0,2, vorzugsweise von 0,02 bis 0,1, insbesondere
0,02 bis 0,08 Gewichtsteilen Nickel je Gewichtsteil Austauscher und eine Menge von
0,01 bis 0,25 vorzugsweise von 0,02 bis 0,1 Gewichtsteilen Austauscher je Gewichtsteil
Harnstoff.
[0010] Prinzipiell sind zwar auch Nickelsalze anstelle der Nickelionen enthaltenden Ionenaustauscher
als Katalysator geeignet, doch lassen sich die Ionenaustauscher viel leichter als
die Salze (die als Hydroxid gefällt werden müßten) durch Filtration oder auch Sedimentation
vom Reaktionsprodukt abtrennen.
[0011] Für die Ausgangsprodukte genügt technische Reinheit.
[0012] Nach Abschluß der zweiten Stufe kann das Reaktionsgemisch auf etwa 70°C abgekühlt
und der Katalysator - zweckmäßig L durch Filtration - abgetrennt werden. Anschließend
destilliert man ggf. überschüssiges Methylglykol ab, ggf. im Unterdruck.
[0013] Das in der beschriebenen Weise erhaltene Carbamatgemisch wird dann zur Überführung
in das gewünschte Textilausrüstungsmittel in üblicher Weise methyloliert. Zu diesem
Zweck wird es mit überschüssiger wäßriger Formaldehydlösung bei pH 7,5 bis 11, vorzugsweise
8,5 bis 10 eine bis 10, vorzugsweise 2 bis 5 Stunden bei einer Temperatur' von 10
bis 80, vorzugsweise 30 bis 60°C behandelt. Anschließend wird die Lösung mit einer
beliebigen wasserlöslichen Säure, beispielsweise Schwefelsäure, neutralisiert und
ggf. mit Wasser auf die gewünschte Konzentration verdünnt. Falls erforderlich, kann
die Lösung, ggf. unter Zusatz von Filtrierhilfsmitteln, wie Aktivkohle, filtriert
werden.
[0014] Die so erhaltene völlig oder fast farblose, klare, wäßrige Lösung stellt das fertige
Textilausrüstungsmittel dar. Es kommt in Form konzentrierter (30 bis 70 gew.%iger)
Lösungen mit einem pH-Wert im Bereich von 5 bis 8, vorzugsweise 6 bis 7,5 in den Handel
und kann zur Anwendung beliebig verdünnt, angesäuert, mit Katalysatoren und sonstigen
Hilfsmitteln, anderen Ausrüstungsmitteln, Pigmenten, Weichmachern usw. versetzt werden.
Es dient zur Krumpf- und Knitterfest- und damit Pflege leicht ausrüstung von Textilien,
die Cellulose in nativer oder regenerierter From enthalten oder daraus bestehen.
[0015] Die in den Beispielen genannten Teile und Prozente beziehen sich auf das Gewicht,
sofern nicht anders vermerkt.
Beispiel 1
a) Herstellung des nickelhaltigen Katalysators
[0016] Eine Säule wird mit 1000 Teilen eins handelsüblichen Kationenaustauschers aus sulfoniertem
vernetztem Polystyrol gefüllt und unter Zugabe von 1000 Teilen Wasser 15 Minuten stehengelassen.
Man gibt danach 500 Teile 10-prozentige Salzsäure zu, läßt die Säule 20 Minuten stehen
und wäscht die Säule mit destilliertem Wasser neutral. Auf den so aktivierten Austauscher
werden 3400 Teile 10-prozentige Lösung von NiSO
4.7 H
20 gegeben. Tritt keine sauer reagie- ..rende Lösung am Säulenaustritt mehr aus, ist
die Aufnahme des Nickelsalzes beendet. Die Austauscherfüllung wird mit Wasser neutral
gewaschen und anschlie-3end mit Methanol wasserfrei gewaschen und getrocknet. Der
Austauscher ist gebrauchsfertig und enthält 8 - 8,5 Teile Nickel je 100 Teile Austauscher.
b) Herstellung eines Co-carbamates aus Polyäthylenätherdiol (= Polyäthylenglykol)
H(OCH2CH2)18OH, Methylglykol (= Äthylenglykolmonomethyläther) und Harnstoff
[0017] In einer Rührapparatur mit Rückflußkühlung und Gaseinleitungsrohr wird das Gemisch
aus 276 Teilen Poly- äthylenätherdiol mit einem Molekulargewicht von 810 (H(OCH
2)
180H) und 21 Teilen Harnstoff drei Stunden auf 145°C unter Rühren und gleichzeitigem
Durchleiten eines Stickstoffstroms erhitzt. Der Umsatz beträgt dann 65 % (gemessen
durch Bestimmung des Rest-Harnstoffgehaltes). Anschließend werden 472 Teile Methylglykol,
373 Teile Harnstoff und 31 Teile eines im Handel erhältlichen, wie oben unter 1a)
behandelten Kationenaustauschers hinzugefügt. Das Re- aktionsgemisch wird 15 Stunden
auf Rückflußtemperatur (maximal 150°C) unter Rühren und Durchleiten eines Stickstoffstroms
erhitzt. Danach wird die Reaktionslösung auf 120°C abgekühlt und der Austauscher abfiltriert.
Es werden 936 Teile eines Co- carbamates erhalten. Das entspricht einer Ausbeute von
91 % der Theorie. Der Restharnstoffgehalt liegt bei 0,4 %.
c) Umsetzung zum Methylolierungsgemisch
[0018] 785 Teile des nach Beispiel 1b) erhaltenen Co-carbamates werden in einer Rührapparatur
mit 634 Teilen ..einer 40%igen Formaldehyldlösung unter Zusatz von 17 Teilen einer
50%igen Natronlauge 3 Stunden auf 50°C erwärmt. Anschließend wird mit verdünnter Schwefelsäure
neutralisiert. Es werden 1450 Teile einer 63%igen Lösung erhalten. Der Gehalt an freiem
Formaldehyd beträgt 2,2 %. Durch Zusatz von 570 Teilen Wasser wird eine 50%ige Lösung
erhalten.
Beispiel 2
[0019] 300 Teile eines Polyäthylenätherdiols vom Molekulargewicht 600 werden in einer Rührapparatur
mit 300 Teilen Harnstoff drei Stunden unter Durchleiten eines Stickstoffstromes auf
150 - 155°C erhitzt. Der Umsetzungsgrad beträgt 90 %. Anschließend werden 68,4 Teile
Methylglykol, 54 Teile Harnstoff und 35 Teile eines nach Beispiel 1a) erhaltenen nickelhaltigen
Austauschers zugesetzt. Das Reaktionsgemisch wird 18 Stunden auf Rückflußtemperatur
(maximal 155°C) unter Rühren erhitzt. Nach Abkühlen auf 110 - 120°C wird der Austauscher
abfiltriert. Es werden 401 Teile des Co-carbamates mit einem Restharnstoffgehalt von
0,3 % erhalten. Das entspricht einer Ausbeute von 94 %.
[0020] Die Methylolierung erfolgt analog Beispiel 1.
Beispiel 3
[0021] In einer Rührapparatur werden 600 Teile eines Polyäthylenätherdiols mit einem Molekulargewicht
von 4000 und 9 Teile Harnstoff 3 Stunden auf 150 bis 155°C erhitzt. Es wird ein Umsetzungsgrad
von 90 % erreicht. Nach Hinzufügen von 31,8 Teilen Diäthylenglykol, 18 Teilen Harnstoff
und 4,5 Teilen eines ..nach Beispiel la) hergestellten nickelhaltigen Austauschers
wird das Reaktionsgemisch 15 Stunden auf 155
0C unter Durchleiten eines Stickstoffstromes erwärmt. Danach wird auf 110°C abgekühlt
und der Austauscher abfiltriert. Es werden 611 Teile (94 % d.Th.) des Co-carbamates
erhalten. Der Gehalt an Restharnstoff beträgt 0,25 %.
[0022] 611 Teile des so erhaltenen Co-carbamates werden in einer Rührapparatur mit 61 Teilen
einer 40%igen Formaldehydlösung nach Zusatz von 3 Teilen einer 50%igen Natronlauge
3 Stunden auf 50 bis 55°C erwärmt. Nach Zusatz von 400 Teilen Wasser und Neutralisation
mit verdünnter Schwefelsäure werden 1080 Teile einer 58%igen Lösung der Methylolverbindung
mit einem Gehalt von 1,7 % freien Formaldehyds erhalten.
Beispiel 4
[0023] In einer Rührapparatur werden 810 Teile des Polyäthylenätherdiols H(OCH
2)
18OH und 60 Teile Harnstoff 3 Stunden auf 150°C unter Durchleiten eines Stickstoffstromes
erwärmt. Es wird ein Umsetzungsgrad von 85 % erreicht. Anschließend werden 2158 Teile
Methylglykol, 1065 Teile Harnstoff und 94 Teile eines nach Beispiel 1a) hergestellten
nickelhaltigen Ionenaustauschers als Katalysator zugegeben. Das Reaktionsgemisch wird
auf Rückflußtemperatur unter Durchleiten eines Stickstoffstromes erwärmt. Bei 132
bis 134
0C wird die Rückflußtemperatur erreicht, die im Verlauf von 5 Stunden auf 150°C ansteigt.
Das Gemisch wird danach weitere 10 Stunden auf 150°C erwärmt. Nach dem Abkühlen auf
90°C wird der Katalysator durch Filtration abgetrennt. Bei ca. 100°C wird unter vermindertem
Druck das überschüssige Methylglykol abdestilliert. Es werden 2700 Teile eines Co-carbamates
aus 30 % Polyäthylenätherdiolmonocarbamat und 70 % Methoxyäthylcarbamat erhalten.
Das entspricht einer Ausbeute von 92 % d.Th. Der Gehalt an Restharnstoff liegt bei
0,2 %.
[0024] 2700 Teile des Co-carbamates werden in einer Rührapparatur mit
'2200 Teilen einer 40%igen Formaldehydlösung unter Zusatz von 30 Teilen einer 50%igen
Natronlauge 3 Stunden bei 50 bis 55°C erwärmt. Nach Neutralisation mit 25 Teilen einer
verdünnten Schwefelsäure werden 1780 Teile Wasser zugesetzt. Es werden 6735 Teile
einer 51%igen Lösung des Methylolierungsgemisches (im folgenden "Dimethylolcocarbamat"
genannt) mit einem Gehalt von 1,8 % freien Formaldehyds erhalten.
Beispiel 5
[0025] 8
10 Teile eines Polyäthylenätherdiols H(OCH
2CH
2)
180H und 60 Teile Harnstoff werden 6 Stunden auf 150°C unter Durchleiten eines starken
Stickstoffstromes erwärmt. Es wird eine Ausbeute von 845 Teilen des Monocarbamates
(bzw. des hier als solches bezeichneten Reaktionsgemisches) mit einem Restharnstoffgehalt
von nur 0,1 % erhalten. Das entspricht einer Ausbeute von 99' % d.Th. Anschließend
werden 4240 Teile Diäthylenglykol (HOH
2CH
2OCH
2CH
2OH) und 2400 Teilen Harnstoff zugemischt und das Ganze unter Durchleiten eines starken
Stickstoffstromes 5 Stunden ohne Katalysator auf 180°C unter Rühren erwärmt. Die Ausbeute
beträgt 5900 Teile Diäthylenglykolmonocarbamat (= 99 % d.Th.).
[0026] Die beiden Carbamate werden zusammen mit 4800 Teilen einer 40%igen Formaldehydlösung
unter Zusatz von 55 Teilen 50%iger Natronlauge 3 Stunden auf 50 bis 55°C erwärmt.
Nach Neutralisieren mit verdünnter Schwefelsäure werden 5700 Teile Wasser zugesetzt.
Es werden 17330 Teile einer 50%igen Lösung des Methylolierungsgemisches mit einem
Gehalt von 1,9 % freien Formaldehyds erhalten.
Beispiel 6
[0027] In einer Rührapparatur werden 590 Teile eines Polyäthylenätherdiols mit einem Molekulargewicht
von 590 (H(OCH
2CH
2)
130H) und 60 Teile Harnstoff 4 Stunden auf 150°C unter Durchleiten eines Stickstoffstromes
erwärmt. Hierbei wird ein Umsetzungsgrad von 91 % erreicht. Anschließend werden 1140
Teile Methylglykol, 900 Teile Harnstoff und 90 Teile des nach Beispiel la) hergestellten
nickelhaltigen Katalysators zugegeben. Das Reaktionsgemisch wird auf Rückflußtemperatur
aufgeheizt, die bei ca. 134 bis 135°C erreicht wird. Das Gemisch wird 15 Stunden erhitzt,
wobei die Temperatur 155°C nicht übersteigen soll. Nach Abfiltrieren des Katalysators
werden 2320 Teile eines Cocarbamatgemisches, bestehend aus 25 % Polyätherdiolmonocarbamat
H(OCH
2CH
2)
13OCONH
2 und 75 % Methoxyäthylcarbamat, erhalten. Dieses Gemisch wird mit 2160 Teilen einer
40%igen Formaldehydlösung unter Zusatz von 35 Teilen einer 50%igen Natronlauge bei
50 bis 60°C hydroxymethyliert und anschließend mit verdünnter Schwefelsäure neutralisiert.
Es werden 4550 Teile einer ca. 65%igen Lösung des Methylolierungsgemisches mit einem
Gehalt von 2,6 % freien Formaldehyds erhalten.
Beispiel 7
[0028] In einer Rührapparatur werden 810 Teile eines Polyäthy-
lenätherdiols vom Molekulargewicht 810 (H(OCH
2CH
2)
18OH) und 60 Teile Harnstoff 5 Stunden auf 150°C unter Durchleiten eines Stickstoffstromes
erwärmt. Der Umsetzungsgrad liegt nach dieser Zeit bei 92 %. Anschließend werden 2680
Teile Dipropylenglykol, 1200 Teile Harnstoff und 100 Teile des nach Beispiel 1a) hergestellten
nickelhaltigen Austauschers zugegeben. Das Reaktionsgemisch wird 16 Stunden unter
Durchleiten eines Stickstoffstromes auf 155°C erwärmt. Nach dem Abkühlen auf ca. 100°C
wird der Katalysator durch Filtration abgetrennt. Es werden 4350 Teile des Cocarbamat-Gemisches
erhalten, bestehend aus 24 % eines Polyäthylenätherdiolmonocarbamates H(OCH
2CH
2)
18OCONH
2 und 76 % Dipropylenglykolmonocarbamat.
[0029] Das Gemisch dieser Cocarbamate wird mit 2800 Teilen einer 40%igen Formaldehyldlösung
unter Zusatz von 40 Teilen einer 50%igen Natronlauge bei 50°C und einer Reaktionsdauer
von 3 Stunden hydroxymethyliert und anschließend mit verdünnter Schwefelsäure neutralisiert.
Es werden 7250 Teile einer 75%igen Lösung der methylolierten Cocarbamate erhalten.
Beispiel 8
[0030] 428 Teile eines Monomethylpolyäthylenätherdiols mit der Struktur CH
3-(OCH
2CH
2)
9OH werden mit 60 Teilen Harnstoff 3 Stunden auf 145 bis 150°C in einer Rührapparatur
unter Rühren und Durchleiten eines Stickstoffstromes erwärmt. Hierbei werden ca. 85
% zum Carbamat umgewandelt. Anschließend werden 2120 Teile Diäthylenglykol und 1200
Teile Harnstoff zugefügt. Das Reaktionsgemisch wird 6 Stunden ohne Katalysator auf
190°C unter Durchleiten eines Stickstoffstromes erwärmt. Hierbei wird der Harnstoff
bis auf einen Restgehalt von 0,2 % umgesetzt. Es werden 3420 Teile eines Cocarbamates
erhalten. Das entspricht einer Ausbeute von 99 % d.Th. Zu diesem Cocarbamatgemisch
werden 2550 Teile einer 40%igen Formaldehydlösung und 40 Teile einer 50%igen Natronlauge
zugefügt und das Gemisch 3 Stunden bei 50 bis 55°C gerührt. Nach Neutralisation mit
verdünnter Schwefelsäure werden 6070 Teile einer 73%igen Lösung des methylolierten
Cocarbamat-Gemisches erhalten.
Anwendungsbeispiele
[0031] Die Anwendungsbeispiele 9 bis 13 werden mit dem im Beispiel 4 beschriebenen Produkt
durchgeführt.
Beispiel 9
[0032] Es wird eine wäßrige Lösung hergestellt, die 7,5 % des Dimethylolcocarbamats (100
%) nach Beispiel 4 und 0,18 % basisches Aluminiumchlorid enthält. Eine Probe eines
Polyester/Baumwoll-Mischgewebes (50 : 50; Bettuchware), die lediglich gebleicht wurde,
wird mit dieser Lösung geklotzt, wobei die Flottenaufnahme 65 % beträgt. Die Proben
werden danach 20 Sekunden auf 205°C erhitzt.
[0033] Ein Teil der so behandelten Probe wird mit je einer Probe verglichen, die in analoger
Weise mit
a) Diemthylolmethylcarbamat
b) Dimethylolmethoxyäthylcarbamat
c) Dimethylol-4,5-dihydroxyäthylenharnstoff behandelt worden ist.
[0034] Methylolierte Polyäthylenoxidmonocarbamate allein, also nicht in Form der erfindungsgemäßen
Mischung, werden zum Vergleich erst gar nicht herangezogen, da sie bekanntlich wegen
zu geringer Vernetzungsmöglichkeiten mit den cellulosischen Hydroxylgruppen (infolge
ihres hohen Molekulargewichtes) einen zu geringen Ausrüstungseffekt ergeben (Durable-Press-Note
zu niedrig und Krumpfung zu hoch).
[0035] Die Bestimmung des Formaldehydgeruchs des ausgerüsteten Gewebes erfolgt in einem
zugeschmolzenen Gefäß nach dem Prüfverfahren 112 - 1975 der Association of Textile
Chemists an Colorists. Mit diesem Verfahren läßt sich analytisch die Formaldehydmenge
bestimmen, die unter Bedingungen, die denen der praktischen Lagerung ähnlich sind,
freigesetzt wird. Der Versuch wird jeweils zweimal durchgeführt; die Durchschnittswerte
sind im folgenden angegeben.

[0036] Aus diesen Werten ist zu ersehen, daß die Ausrüstung mit dem erfindungsgemäßen Mittel
zu geringerer Formaldehyd-Geruchsentwicklung führt als mit den anderen obengenannten
Ausrüstungsmitteln.
Beispiel 10
[0037] Aus folgenden Substanzen wird eine Klotzflotte hergestellt:

[0038] Diese Flotte wird auf Polyester/Baumwoll-Gewebe (65 : 35; Bettuchware) aufgeklotzt,
wobei die Flottenaufnahme 50 - 55 % beträgt. Nach dem Trocknen wird das Gewebe in
einem Spannrahmen 20 Sekunden lang auf 205°C erhitzt.
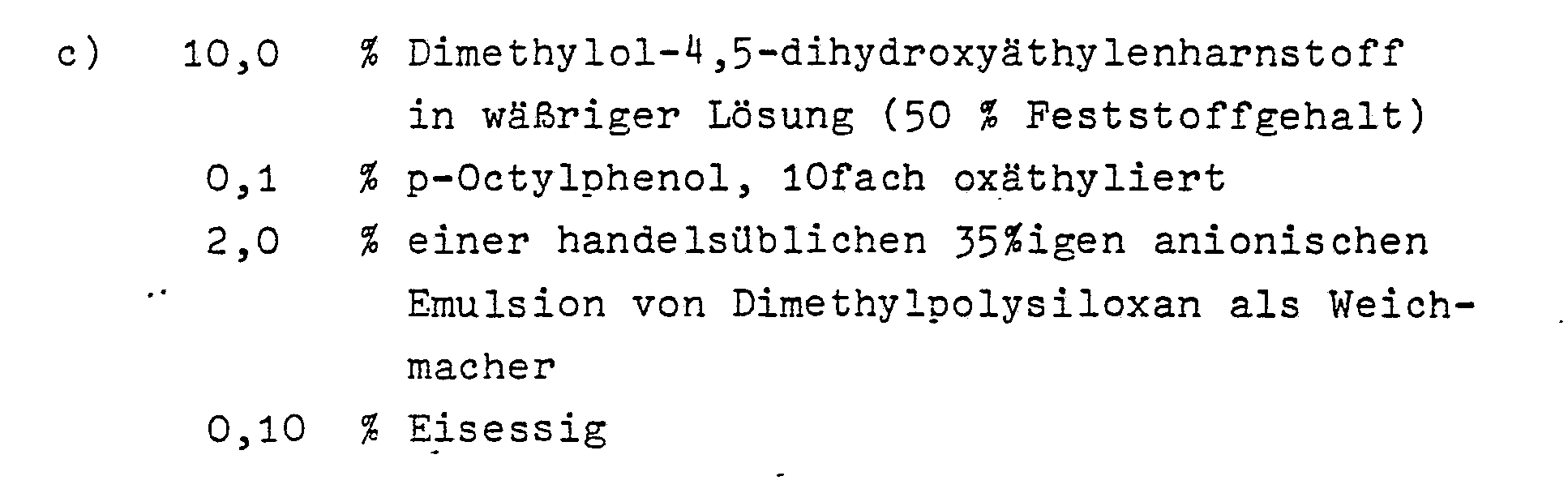
[0039] Der Rest ist in beiden Fällen Leitungswasser von Umgebungstemperatur. Die Unterschiede
in Art und Menge der Katalysatoren sind durch die unterschiedlichen Erfordernisse
zur. Erzielung optimaler Ergebnisse bedingt.
[0040] Sollen die Gewebe nach der Ausrüstung bedruckt werden, so kommt es auf ihr Absorptionsvermögen
an. Die Benetzbarkeit oder das Absorptionsvermögen der Gewebe wird nach dem AATCC-Prüfverfahren
79-1975 ermittelt. Je kürzer die durchschnittliche Benetzungszeit, desto saugfähiger
ist das Textilmaterial. Eine Zeit von weniger als 10 Sekunden entspricht einem für
den Textildruck guten Saugvermögen. Die Cocarbamat-Rezeptur (a) ergab eine hydrophile
Ausrüstung, wie aus der folgenden Tabelle zu ersehen ist:
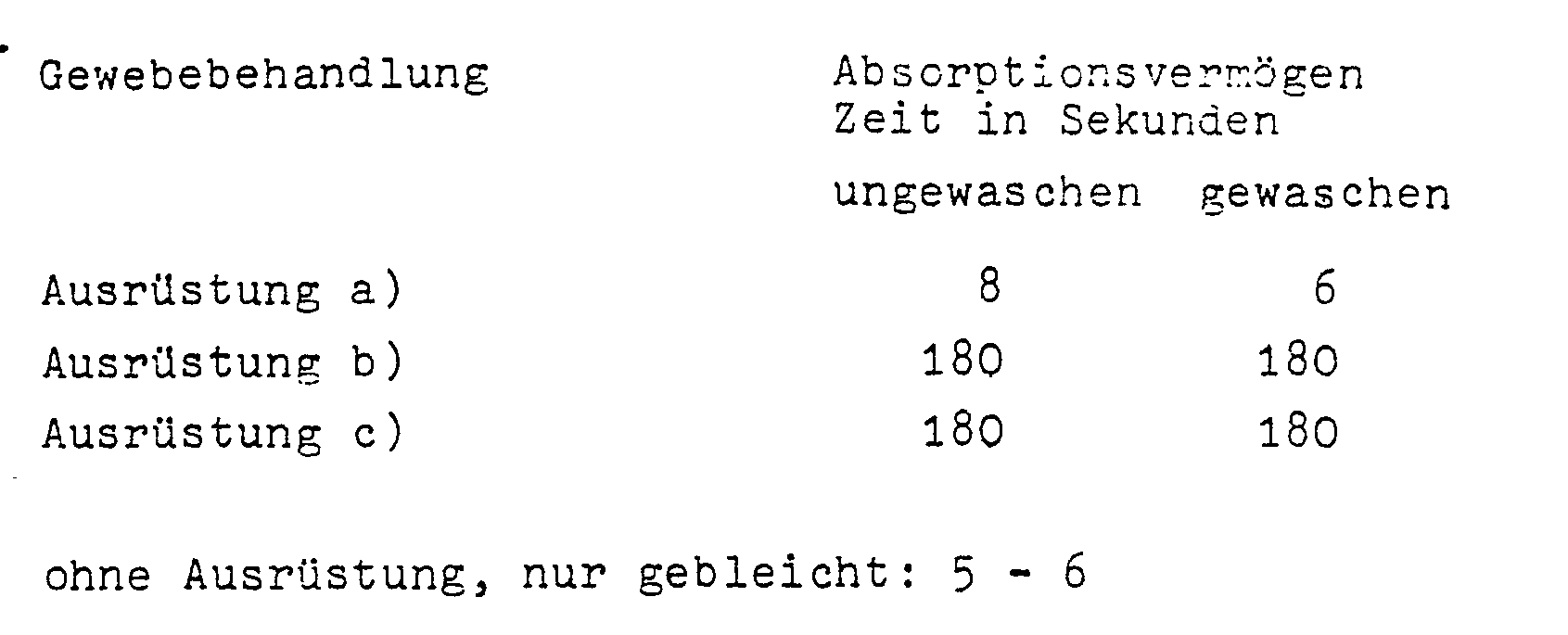
[0041] Daraus ist klar ersichtlich, daß die mit dem erfindungsgemäßen Ausrüstungsmittel
behandelten Gewebe ein günstiges Verhalten zeigen, verglichen mit den meisten Harzappreturen
für anschließendes Bedrucken.
Beispiel 11
[0042] Es werden wiederum die Rezepturen a), b) und c) von Beispiel 10 verwendet. Diese
Ausrüstungsmittel werden auf Polyester/Baumwoll-Gewebe (50:50; Bettuchware) aufgeklotzt.
Die Gewebe werden danach 20 Sekunden lang auf 205°C erhitzt.
[0043] Die so behandelten Gewebe, im folgenden mit A, B und C bezeichnet, werden nach dem
Filmdruckverfahren mit verschiedenen Mustern bedruckt, wobei man folgende Druckpaste
verwendet:
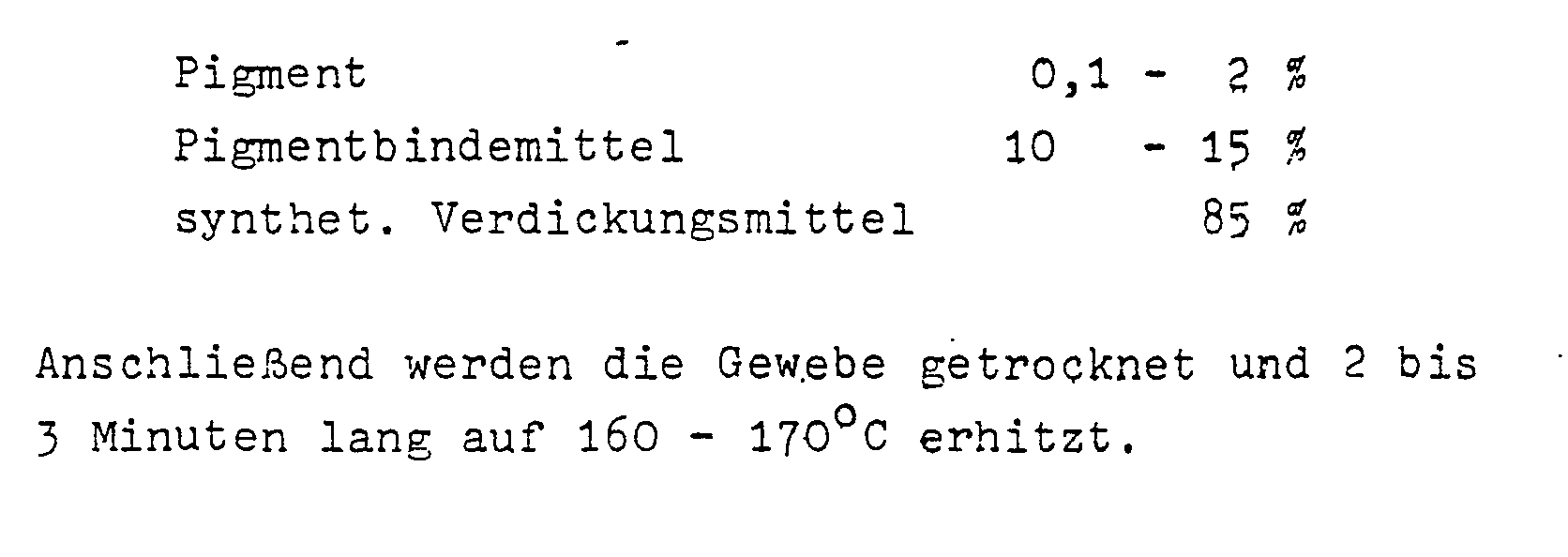
Ergebnisse
[0044]
1) Aussehen Probe A weist höhere Farbausbeute und Brillanz auf als Probe B, die etwas
"ausgewaschen" aussieht. Probe C zeigt eine ähnliche Farbausbeute wie Probe A.
2) Schärfe des Druckmusters Die auf Probe A hergestellten Drucke sind schärfer als
die auf den Proben B und C erzielten. Proben B und C wirken in zwei Farben (z.B. schwarz
und rot) etwas verschmiert. Bei Probe A liegt nur geringer oder kein Schmiereffekt
vor, so daß die Linien des "Drucks schärfer sind.
3) Griff des Gewebes nach dem Bedrucken Der Griff von Probe A ist voller und weicher
als der von Probe B. Probe C hat einen ebenso weichen Griff wie Probe A. Die Proben
werden von drei Personen unabhängig voneinander beurteilt.
4) Farbechtheiten Die Reibechtheit der Drucke wird nach dem AATCC-Prüfverfahren 8-1974
bestimmt. Erzielt werden die folgenden Ergebnisse:
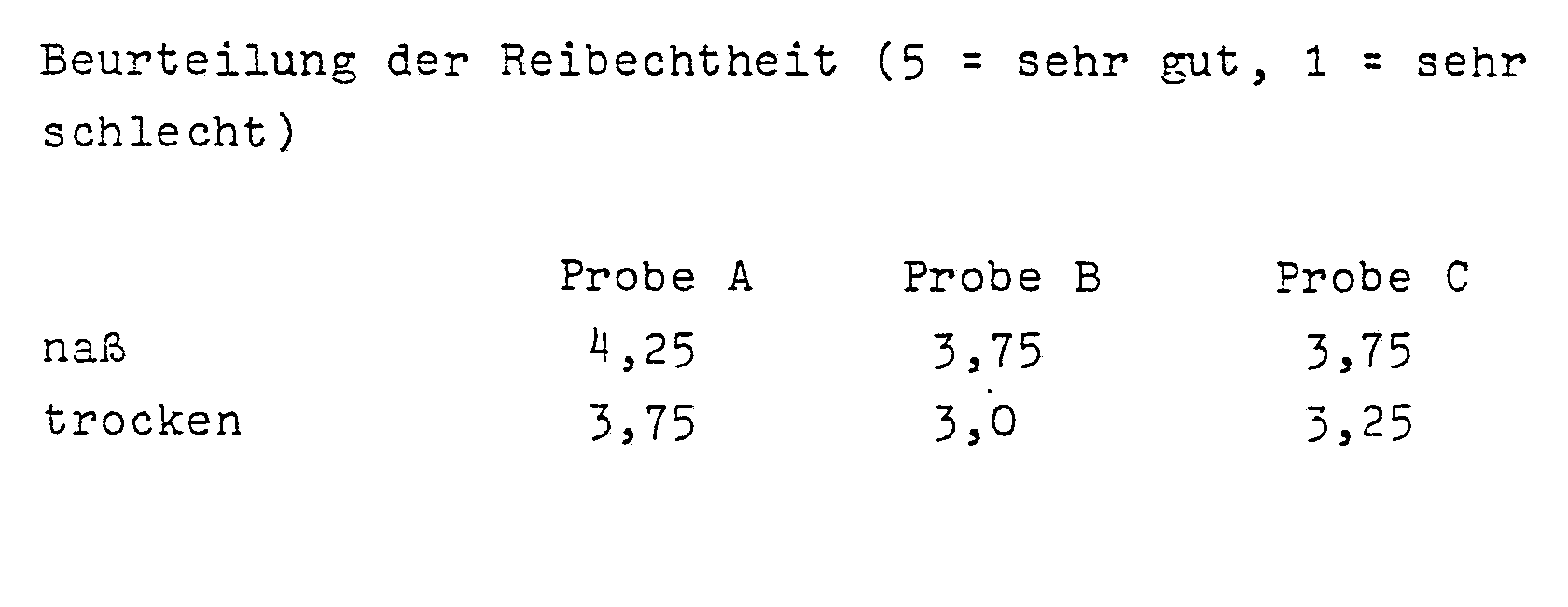
Beispiel 12
[0045] In diesem Beispiel wird die Tendenz der Proben zur Wiederanlagerung von öligen Substanzen
und von Schmutzstoffen, die in der Waschflüssigkeit gelöst oder dispergiert werden,
bestimmt. Die in Beispiel 10a, b und c beschriebenen Klotzflotten werden auf Polyester-Baumwoll-Gewebe
(50 : 50; Bettuchware) aufgeklotzt; die Gewebe werden dann 20 Sekunden lang auf 205°C
erhitzt. Die erhaltenen Proben werden mit A (Rezeptur 10a), B (Rezeptur lOb) und C
(Rezeptur 10c) bezeichnet und dem am Ende der Beschreibung erläuterten Celanese-Wiederanschmutzungstest
unterzogen. Die Schmutzaufnahme der Gewebe im Launder-Ometer wird bestimmt mit Hilfe
eines Hunter-Reflectometers, Typ D-40, hergestellt von Hunter Associates Laboratory,
Inc., 5421 Briar Ridge Road, Fairfax, Va., U.S.A.
[0046] Der Wert des Weißgrades (W) läßt sich aus diesen Werten nach folgender Formel errechnen:
W = Y + 4 (Z - Y) (%)
W = % Weißgrad
Y = Grün-Reflexionsgrad
Z = Blau-Reflexionsgrad
[0047] Zweck dieses Versuches ist die Messung der Weißgradretention des Polyester-Baumwoll-Gewebes
nach Durchführung der Waschverfahren. Die erhaltenen Werte sind in der folgenden Tabelle
aufgeführt:
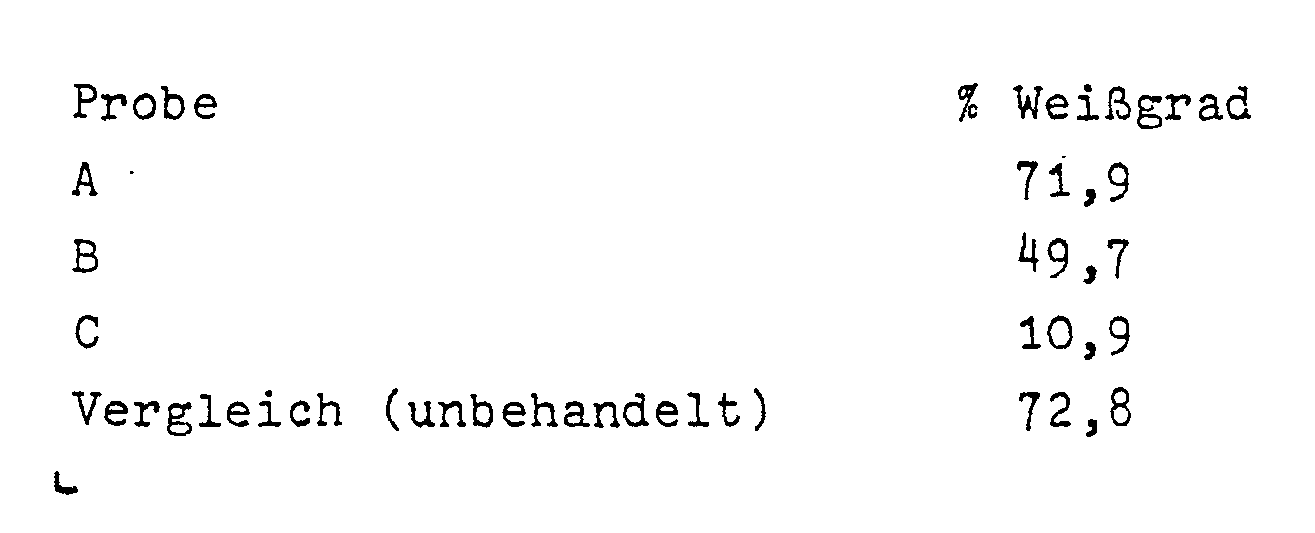
[0048] Aus der Tabelle ist ersichtlich, daß Gewebe B und C infolge des Waschens ihren Weißgrad
zum Teil oder größtenteils verloren haben. Dies zeigt, daß an Probe A wesentlich weniger
Schmutz aus der Waschlauge angelagert wird.
Beispiel 13
[0049] Das nach Beispiel 4 hergestellte und nach Beispiel 9 zubereitete Dimethylolcocarbamat
wird auf Polyester-Baumwoll-Gewebe (Bettuchware) aufgebracht und wie bei Beispiel
9 fixiert. Vergleichsproben desselben Gewebes werden in gleicher Weise mit einer entsprechenden
Zuberei- tun
g einer 45%igen N-Methylol-2-methoxyäthyl-carbamat-Lösung sowie mit den in Beispiel
10 beschriebenen Zubereitung b und c behandelt, in denen Dimethylol-4,5-dihydroxy-
äthylenharnsotff verwendet wird.
[0050] Die Proben werden 20 Sekunden auf 205°C erhitzt.
[0051] Sie weisen nach dem Scheuerfestigkeits-Test (Accelerotor--Methode; 1 Minute bei 3000
U/Min.) folgende Abriebwerte auf:
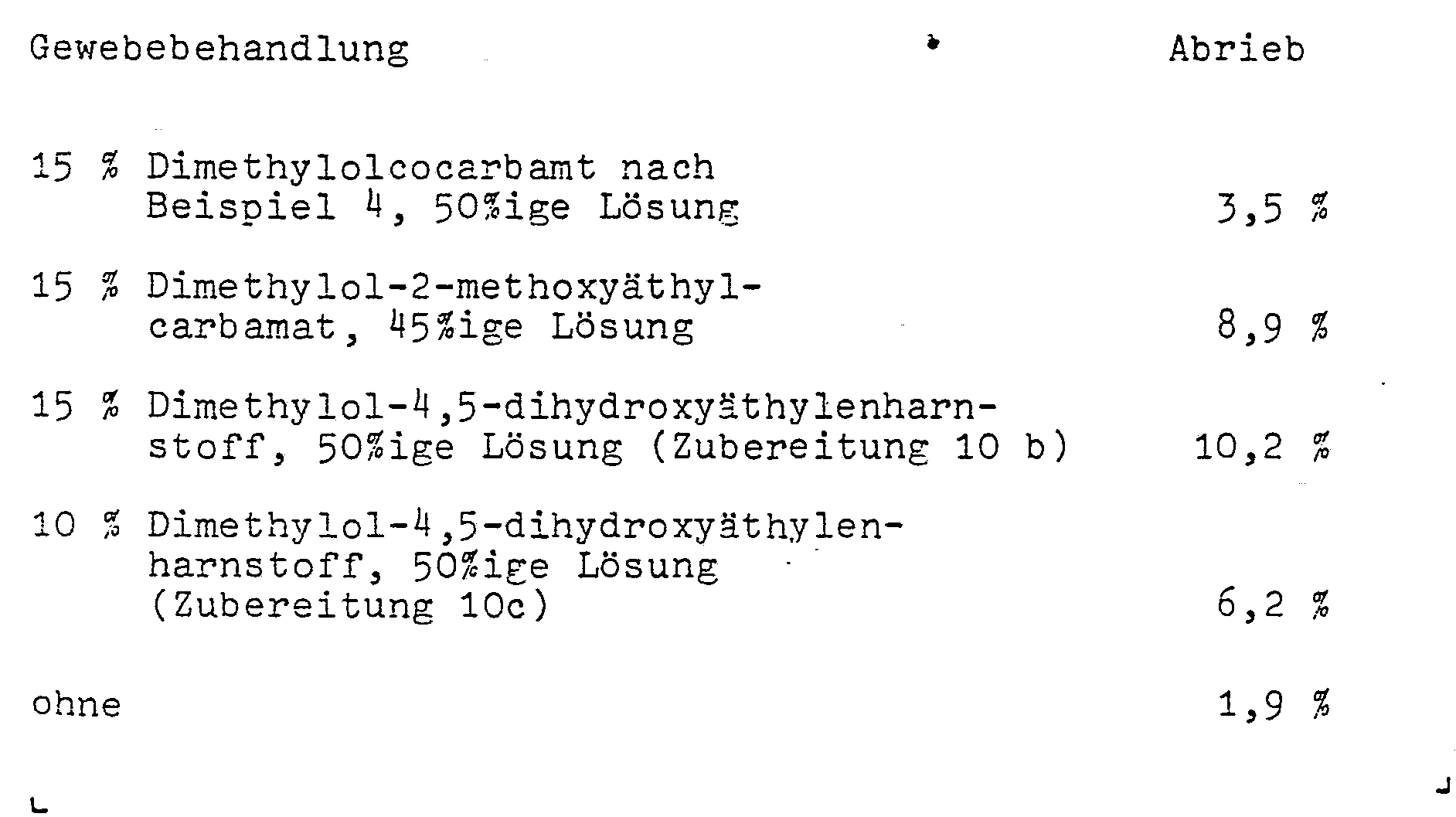
[0052] Es ist offensichtlich, daß das Dimethylolcocarbamat der Erfindung eine relativ geringe
Neigung zur Staubbildung besitzt (wichtig wegen der Staubentwicklung in Näh- und Gewebeverpackungsbetrieben).
Beispiel 14
[0053] Eine Klotzflotte aus
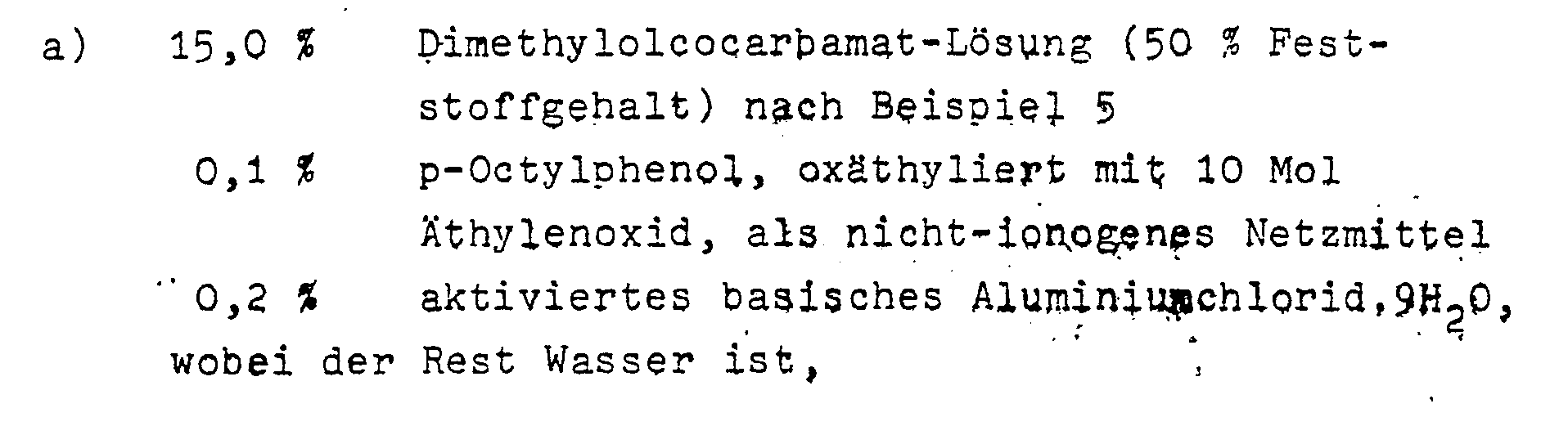
wird auf Polyester-Baumwoll-Gewebe (65/35) mit einem Gewicht von 120 g/m
2 aufgeklotzt, wobei die Flottenaufnahme 70 % beträgt. Nach dem Trocknen wird das Gewebe
in einem Spannrahmen 20 Sekunden auf 205°C erhitzt.
[0054] Zum Vergleich werden weitere Proben in ähnlicher Weise mit folgender Flotte geklotzt:
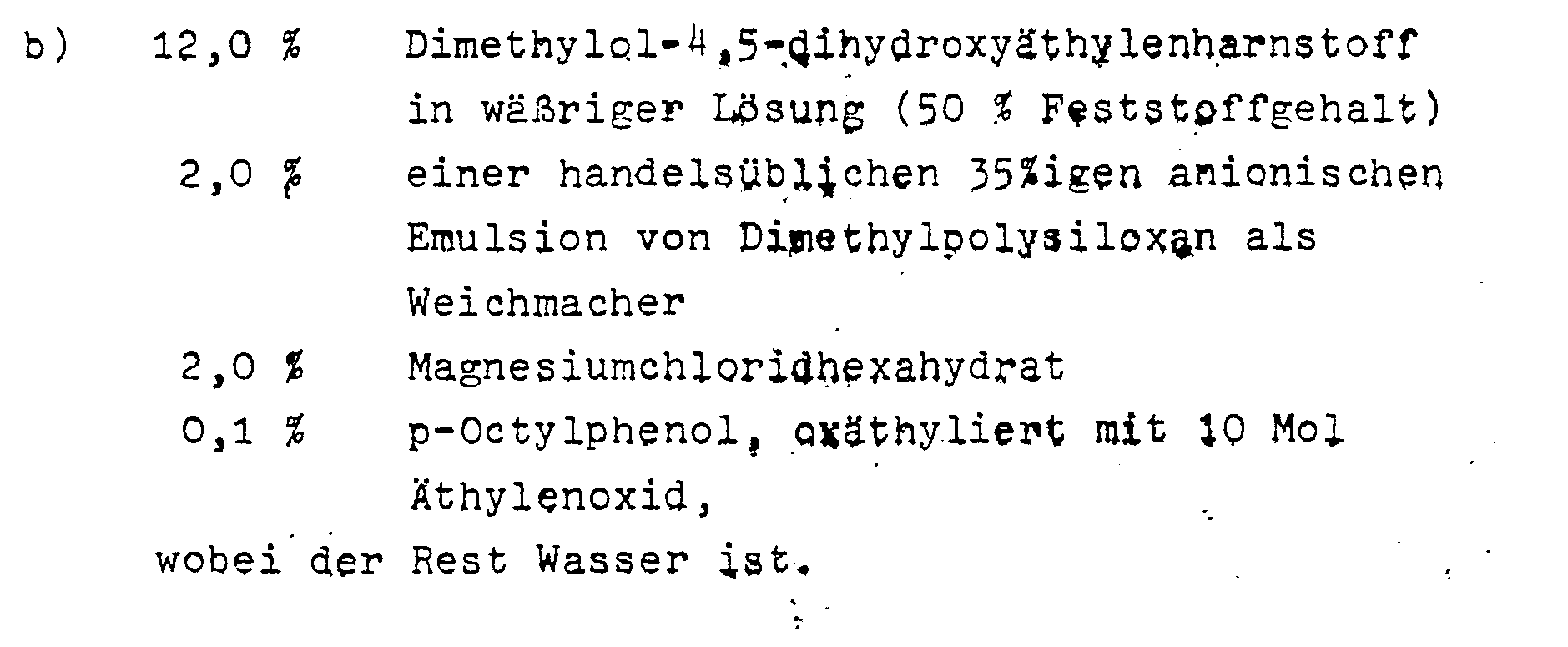
[0055] In beiden Fällen wurden die für die betreffende Ausrü- stung optimale Katalysatorart
und -menge gewählt.
[0056] Das Gewebe wird wie oben beschrieben getrocknet und erhitzt (20 Sekunden auf 205°C).
[0057] Die beiden Proben werden mit A (Rezeptur a) und B (Rezeptur b) bezeichnet und in
der im wesentlichen gleichen Weise wie oben beschrieben geprüft. Die folgende Tabelle
gibt eine Zusammenfassung der Ergebnisse:
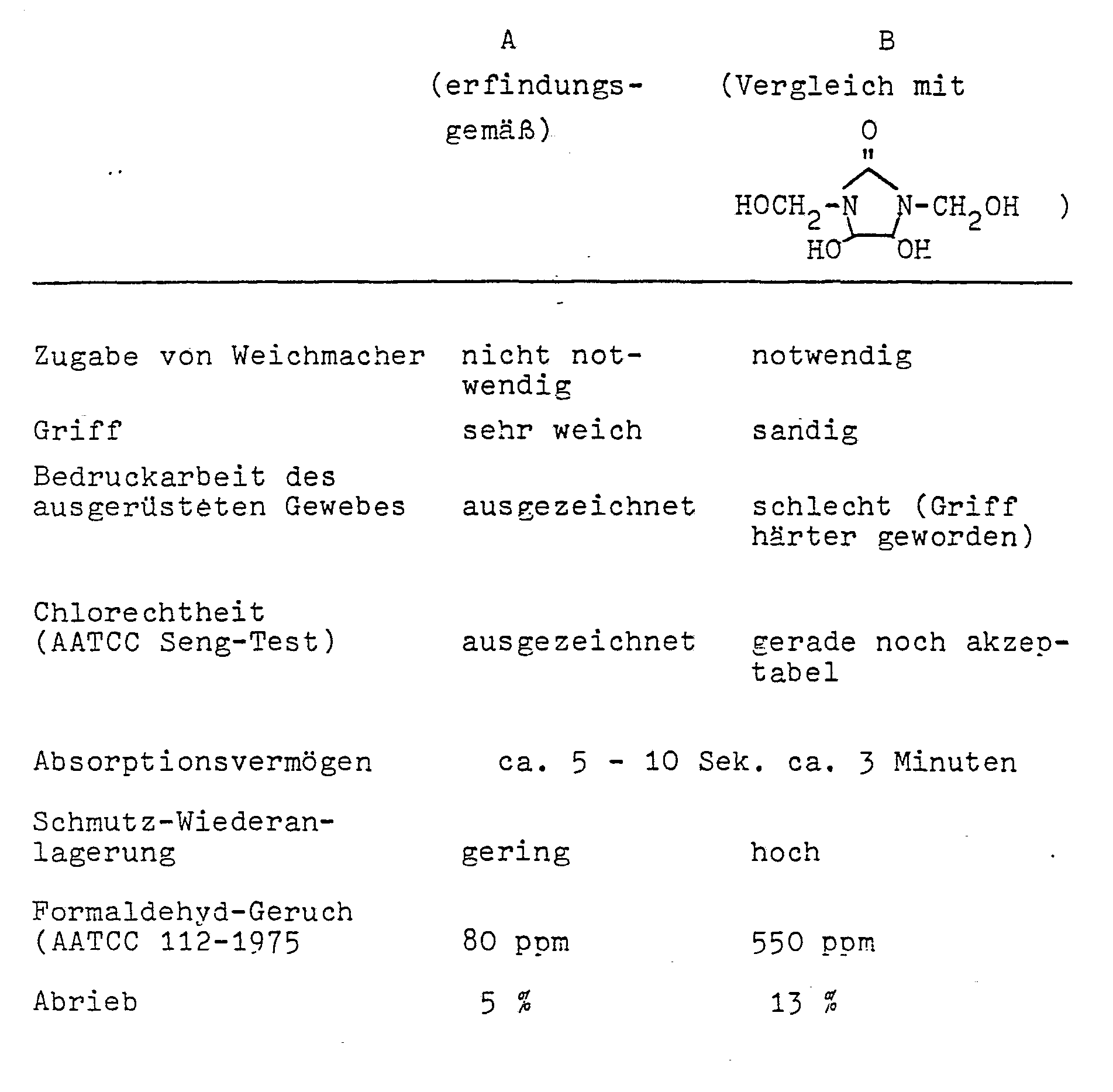
[0058] , Die Tabelle zeigt die Überlegenheit der erfindungsgemäßen Ausrüstung gegenüber
derjenigen des nächsten Standes der Technik. Trotz der Verwendung eines teuren Weichmachers
ist der Griff der Probe B weniger gut als der von Probe A, bei der kein Weichmacher
eingesetzt wurde. Krumpf- und Knitterfestigkeitseigenschaften sowie der Weißgrad sind
etwa gleich. Diese und verschiedene andere Ergebnisse sind deshalb in dieser Tabelle
nicht aufgeführt worden. Die erfindungsgemäße Ausrüstung scheint der bekannten in
keiner Eigenschaft unterlegen zu sein.
[0059] Die Vergleichsversuche der Beispiele 9 und 13 veranschaulichen die Überlegenheit
der erfindungsgemäßen Mischungen u.a. gegenüber einer Einzelkomppnente. Die andere
Komponente, Polyäthylenoxidmonocarbamat, ist, wie bei Beispiel 9 näher erläutert,
für sich allein unbrauchbar. Es ist überraschend, daß eine Mischung aus zwei Substanzen,
von denen jede für sich unbefriedigende Ergebnisse bringt, Resultate ergibt, die mindestens
befriedigend und in manchen Punkten sogar ausgezeichnet sind. Darüber hinaus zeigen
die Vergleichsversuche der Beispiele 9 bis 14 die Überlegenheit der erfindungsgemäßen
Mischung auch über einige der besten derzeit üblichen Ausrüstungsmittel.
Beispiele 15 und 16
[0060] Proben eines lediglich gebleichten Polyester-Baumwoll-Gewebes (50 : 50; Bettuchware,
108 g/m
2) werden geklotzt mit einer wäßrigen Lösung, die folgende Substanzen enthält:

[0061] Die Flottenaufnahme beträgt 65 %. Das Gewebe wird in einem Spannrahmen 20 Sekunden
auf 205°C erhitzt.
[0062] Ausrüstungsmittel A besteht aus einer 50%igen wäßrigen Lösung einer Mischung aus
9 Teilen Dimethylol-diäthylenglykolmonocarbamat und 1 Teil Dimethylolpolyäthylengly-
kol(800)-monocarbamat (N,N-Dimethylolmonocarbamat eines Polyäthylenglykols vom Molekulargewicht
800).
[0063] Ausrüstungsmittel B besteht aus einer 50%igen wäßrigen Lösung derselben Komponenten
im Gewichtsverhältnis 19 : 1 (95 % Dimethylol-diäthylenglykolmonocarbamat und 5 %
Dimethylolpolyäthylenglykol(800)-monocarbamat, bezogen auf das Gewicht der Carbamatmischung).
[0064] Die Prüfung der beiden Proben, die im wesentlichen wie oben beschrieben ausgeführt
wird, führt zu folgenden Ergebnissen:

Celanese-Wiederanschmutzungstes:
Apparatur: Launder-Ometer 60°C Celanese Standard-Schmutz (sollte einmal wöchentlich
60 Minuten lang gemischt werden).
[0065] Proben: 2 Proben mit den Maßen 15 x 15 cm.
[0066] Die Gewebe werden vor der Prüfung einer Maschinenwäsche unterzogen, und zwar dem
für die betreffende Gewebeart geltenden Normalprogramm.
1. Alle Wolle enthaltenden Gewebe: 40°C
2. Trikotwaren, Rundwirkwaren und bedrugke Waren 50°C
3. Alle gewebten Textilien: 60°C
[0067] Verfahren:
1. Schmutzlösung herstellen, 16 g/l.
2. 200 ml Schmutzlöser in den Behälter des Launder-Ometer einfüllen und 10 Stahlkugeln
zugeben.
3. Proben in Behälter einführen; Behälter verschließen und 30 Minuten drehen.
4. Proben entnehmen und in kaltem Leitungswasser spülen.
5. Proben in der Maschine mit 50 ccm eines haushaltüblichen Waschmittels was chen,
und zwar im Kaltwasch--Vorgang.
6. Im Wäschetrockner trocknen.