[0001] La présente invention concerne essentiellement un procédé de traitement thermique
de l'acier, tel que le chauffage avant trempe, le recuit, la cémentation (carburation
ou carbonitruration), effectué dans un four en présence d'une atmosphère en écoulement
continu obtenue en mélangeant un gaz porteur incluant de l'azote et éventuellement
de l'hydrogène avec un gaz actif constitué par un hydrocarbure avec une proportion
en volume d'hydrocarbure comprise entre 0,2 et 30 % dudit mélange.
[0002] La mise en oeuvre de ce procédé connu peut présenter certaines difficultés, notamment
dans le cas de cémentation de pièces présentant des alésages profonds ou encore de
pièces de formes complexes. Il peut se produire, en effet, au fond de ces alésages
ou autres parties en creux difficilement accessibles, de légers dépôts de suies préjudiciables
à la qualité du produit fini.
[0003] Un but de la présente invention est d'éviter les difficultés sus-mentionnées et de
permettre une cémentation des pièces même réputées difficiles, qui soit homogène et
exempte de suies.
[0004] Les expériences faites pour la recherche de ce but ont permis de découvrir que le
rôle de l'oxyde de carbone est primordial dans le transfert des atomes de carbone
de l'atmosphère vers le métal. En effet, l'oxyde de carbone permet de réaliser une
cémentation à la surface de la pièce métallique par un effet de double couche. L'oxyde
de carbone est absorbé sous forme d'une liaison métallique carbone-métal permettant
de couvrir toute la surface, même dans les parties les moins accessibles, des pièces
réputées difficiles telles que les alésages profonds ou les creux des pièces de formes
complexes. L'hydrocarbure présent dans l'at- mosphèrc peut ensuite former une double
couche par une liaison avec les radicaux oxyde de carbone absorbés. Il s'ensuit un
passage continu des atomes de carbone ainsi pontés par la double couche, ce qui permet
une cémentation homogène sur toutes les parties des pièces traitées.
[0005] L'expérience a montré également qu'il importe d'exclure toute trace d'oxygène résiduel
dans l'atmosphère, ceci pour éviter une destabilisation de la double couche aus-mentionnée.
Les molécules d'oxygène entraînent un effet la domination, auteur d'elles de capture
d'hydrocarbures en phase gazeuse et empêchent de ce fait l'approvisionnement en hydrocarbure
de la double couche formée à la surface du métal, ce qui se traduit sur les pièces
par des zones insuffisamment riches en carbone, c'est-à-dire des hétérogénéités de
cémentation.
[0006] On sait par ailleurs que l'azote industriel ordinaire contient des quantités non
négligeables (pouvant atteindre 2 %) d'oxygène, de dioxyde de carbone et de vapeur
d'eau et l'expérience a montré encore que c'est cet oxygène apporté directement par
l'azote industriel ordinaire, ou provenant de la décomposition du dioxyde de carbone
ou de la vapeur d'eau qu'il véhicule, qui déstabilise la double couche décrite ci-dessus.
[0007] Le but sus-mentionné est atteint par le procédé selon la présente invention essentiellement
par le fait qu'on réalise ladite atmosphère en mélangeant au gaz porteur précité,
constitué par de l'azote ou contenant de l'azote ayant une teneur en O
2 < 10 ppm, une teneur en H
2O < 10 ppm et une teneur en CO
2 < 10 ppm, un hydrocarbure choisi parmi l'un des composés suivants : CH
4, C
4H
10, C
3H
8, C
2H
4, C
2H
2, C
2H
6 et de l'oxyde de carbone, la proportion d'oxyde de carbone dans le mélange total
étant comprise entre 0,1 et 30 % en volume et la température de l'acier étant comprise
entre 750 et 1150°C.
[0008] L'utilisation d'azote ayant une teneur en O
2 < 10 ppm, une teneur en C0
2-( 10 ppm et une teneur en H
20 < 10 ppm (qui correspond à un point de rosée de - 60°C environ), c'est-à-dire d'azote
ayant la pureté industrielle, assure l'obtention d'une atmosphère exempte d'oxygène
; l'oxyde de carbone que contient cette atmosphère peut jouer pleinement son rôle,
c'est-à-dire faciliter le passage dans le métal des atomes de carbone des hydrocarbures,
ce qui a pour conséquence une cémentation, plus précisément une carburation, homogène
et sans dépôts de suies, quelle que soit la configuration des pièces traitées.
[0009] La valeur du pourcentage en oxyde de carbone du mélange total, comprise dans la gamme
0,1 à 30 %, est choisie en fonction des caractéristiques de l'acier de la pièce traitée,
de la température du traitement, elle-même fonction, en partie au moins, des caractéristiques
de cet acier, et de la configuration de la pièce traitée, c'est-à-dire du rapport
entre l'aire de sa surface totale et son volume, le pourcentage de CO devant être,
pour ce dernier paramètre, d'autant plus important que ledit rapport est plus élevé.
[0010] Selon une autre caractéristique de l'invention l'oxyde de carbone peut être introduit
dans le mélange précité sous forme de gaz pur ou encore sous forme d'un mélange partiel
azote-oxyde de carbone à l'état gazeux ou liquide.
[0011] Selon encore une autre caractéristique de l'invention l'oxyde de carbone provient
de la décomposition à chaud du méthanol selon la réaction

ledit méthanol étant introduit dans le mélange précité.
[0012] La décomposition du méthanol selon la réaction précitée est celle qui se produit
pratiquement exclusivement dans la gamme des températures 700 - 1150°0 qui inclut
l'intervalle de température du traitement.
[0013] Dans le cas d'une carbonitruration, ladite atmosphère est réalisée en mélangeant
au gaz porteur, outre l'hydrocarbure et l'oxyde de carbone précités, de l'ammoniac
en proportion de 0,1 à 30 % en volume.
[0014] On obtient ainsi des pièces ayant une carbonitruration homogène et sans dépôts de
suies quelle que soit la configuration des pièces traitées.
[0015] La valeur du pourcentage en NH
3 est choisie en fonction de l'acier traité et du degré de nitruration désiré.
[0016] Il est à noter par ailleurs que le fait d'introduire dans le four une atmosphère
pratiquement exempte d'oxygène, de vapeur d'eau et de gaz carbonique, permet une réaction
molécules à molécules entre le gaz carbonique ou l'eau formés par la réaction de cémentation
et l'hydrocarbure selon les réactions suivantes (l'hydrocarbure étant supposé être
CHA) :

et

ce qui conduit à des contrôles très stricts en H
20, CO
2 et CH
4 en sortie du four qui caractérisent réellement et très exactement la situation de
carburation in situ.
[0017] L'invention vise également un procédé de contrôle du traitement thermique décrit
ci-dessus, c'est-à dire effectué dans un four en présence d'une atmosphère en écoulement
continu obtenue en mélangeant un gaz porteur incluant de l'azote et éventuellement
de l'hydrogène avec un gaz actif constitué par un hydrocarbure auquel on additionne
du 00.
[0018] Ce procédé de contrôle est caractérisé par le fait qu'on mesure la teneur résiduelle
en hydrocarbure, en vapeur d'eau et en gaz carbonique de l'atmosphère sortant du four,
on détermine, en utilisant des abaques préétablis qui donnent une relation entre les
teneurs résiduelles en hydrocarbure vapeur d'eau et gaz carbonique et les taux de
carbone de l'acier, la teneur en hydrocarbure de l'atmosphère entrant dans le four
qui est nécessaire pour l'obtention du taux de carbone désiré et on règle le débit
d'hydrocarbure entrant dans le four pour obtenir les teneurs précitées à la sortie
du four et par conséquent ledit taux de carbone désiré.
[0019] Un tel procédé de contrôle permet donc de piloter le traitement de façon à empêcher
que se forment, dans le four, du dioxyde de carbone et de la vapeur d'eau dont la
présence était soigneusement évitée dans l'atmosphère entrant dans le four ; il permet
par conséquent, d'obtenir un produit final ayant les caractéristiques désirées.
[0020] L'invention vise également les aciers obtenus par le procédé de traitement sus-mentionné.
[0021] Divers essais portant sur différents types de traitement (carburation, carbonitruration,
chauffage avant trempe) ont été effectues sur des aciers de compositions différentes,
les atmosphères entrant dans le four étaient formées d'une façon générale d'azote
industriellement pur, d'un au moins des hydrocarbures précités, éventuellement d'hydrogène,
composants auxquels était ajouté soit de l'oxyde de carbone, soit du méthanol. Dans
le cas d'une carbonitruration, l'atmospère contenait en outre de l'ammoniac.
[0022] En cc qui concerne les températures de traitement, comprises dans l'intervalle 750-1150°C
sus-mentionné, il a été observé que l'introduction de NH
3, entraînait un abaissement des températures préféren- tielles dans la partis basse
(750-1050°C) intervalle.
[0023] Dans choeur de ces essais, le traitement étant contrôlé en mesurant la teneur résiduelle
en hydrocarbure, CO
2 et H
2O de l'atmosphère sortant du four et en réglant le débit d'hydrocarbure introduit
dans l'atmosphère entrant dans le four pour l'obtention de l'activité carburante désirée,
c'est-à-dire en pilotant l'addition d'hydrocarbure à l'entrée du four. Pour permettre
ce contrôle, des abaques avaient été précédemment établis qui donnaient une relation
entre d'une part la teneur résiduelle en hydrocarbure, la teneur résiduelle en H
20, la teneur résiduelle en CO
2 à la sortie du four et d'autre part la quantité de carbone introduite dans l'acier.
La lecture de ces abaques permet le réglage du potentiel carbone comme indiqué ci-dessus.
[0024] On donnera ci-après quelques exemples des essais effectués dans chacun desquels seront
indiqués le traitement effectué, la matière de l'acier traité et la composition des
atmosphères d'entrée et de sortie du four.
Exemple 1 - (carburation)
[0025] Des pièces en acier 20NCD2 (Norme AFNOR) ont été traitées pendant 4 h 30 à 900°C
dans un four type batch dans lequel était introduite une atmosphère azote-hydrogène-méthane-oxyde
de carbone. Les compositions des atmosphères à l'entrée et à la sortie du four étaient
les suivantes :

[0026] La dureté de la couche carburée puis trempée à l'huile était de 60 Rockwell dans
l'échelle C. La profondeur carburée atteignait 0,7 mm avec un carbone en surface de
0,8 % sans austénite résiduelle ni carbures.
Exemple 2 - (carburation)
[0027] Des pièces en acier 16 CD4 (Norme AFNOR) ont été traitées pendant 2 heures à 900°C
dans un four type batch dans lequel était introduite une atmosphère d'azote-propane-méthanol
(ce dernier se décomposant en oxyde de carbone et hydrogène). La composition des atmosphères
d'entrée et de sortie était la suivante :

[0028] Des mesures de dureté faites sur des pièces trempées à l'huile après traitement ont
donné des valeurs de 87 Rockwell dans l'échelle A. La profondeur carburée atteignait
0,4 mm avec un carbone en surface de 0,8 %.
Exemple 3 - (carbonitruration)
[0029] Des pièces en acier 27CD4 (Norme AFNOR) ont été traitées pendant 4 heures à 870°C
dans un four batch dans lequel était introduite une atmosphère azote-hydrogène-méthane-oxyde
de carbone-ammoniac.
[0030] Les compositions des atmosphères d'entrée et de sortie du four étaient les suivantes
:
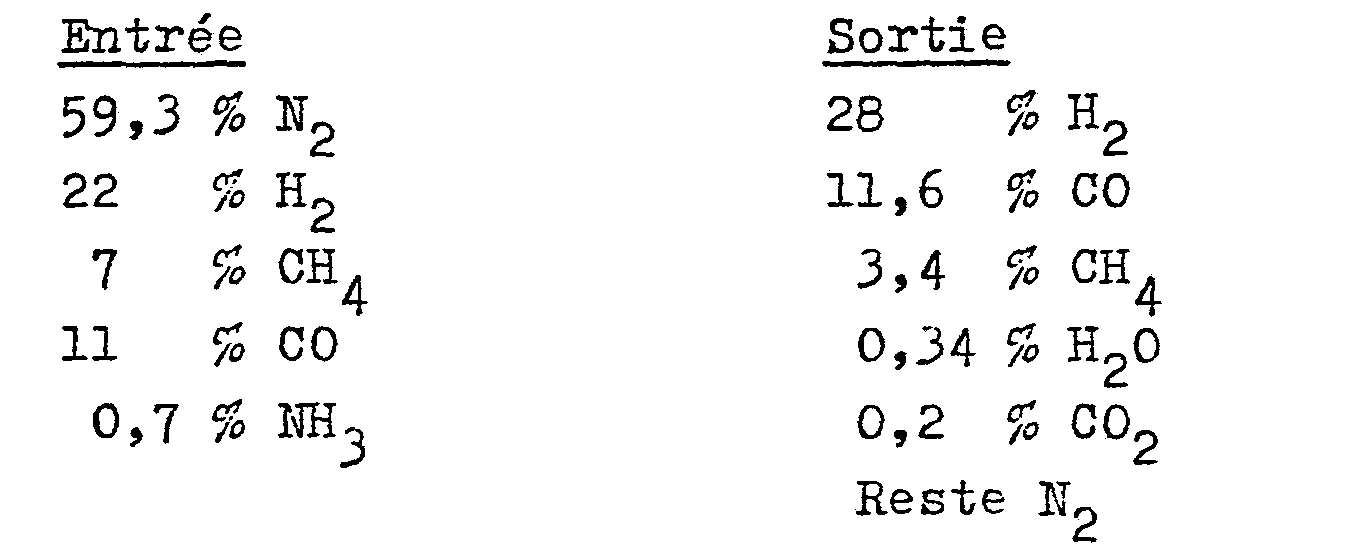
[0031] Des mesures de dureté faites sur des pièces trempées à l'huile ont donné des valeurs
de 857 Vickers en HV50g. La profondeur carbonitrurée atteignait 0,4 mm à 650 HVl kg.
Exemple 4 - (carbonitruration)
[0032] Des pièces en acier 38C2 (Norme AFNOR) ont été traitées pendant 3 heures et 15 minutes
à 890°C dans un four batch dans lequel était introduite une atmosphère azote-méthane-méthanol-ammoniac.
[0033] Les compositions des atmosphères d'entrée et de sortie du four étaient les suivantes
:
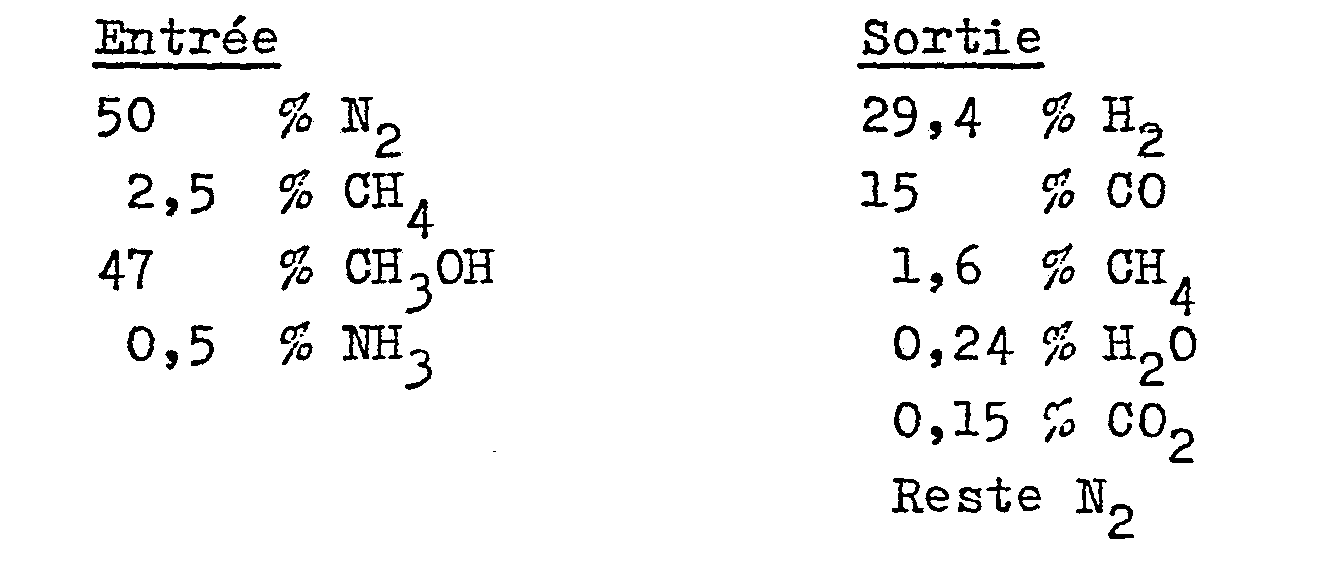
[0034] Des mesures de dureté faites sur des pièces trempées à l'huile après traitement ont
donné des valeurs de 62 Rockwell dans l'échelle C. La profondeur carbonitrurée atteignait
0,48 mm à 650 IIV 1 kg. La profondeur totale cémentée était de 0,70 mm.
Exemple 5 - (chauffage avant trempe)
[0035] Des pièces en acier 3OCD4 (Norme AFNOR) ont été traitées pendant 2 heures à 850°C
en four batch de trempe, en atmosphère azote-méthanol.
[0036] Les compositions des atmosphères d'entrée et de sortie du four étaient les suivantes
:
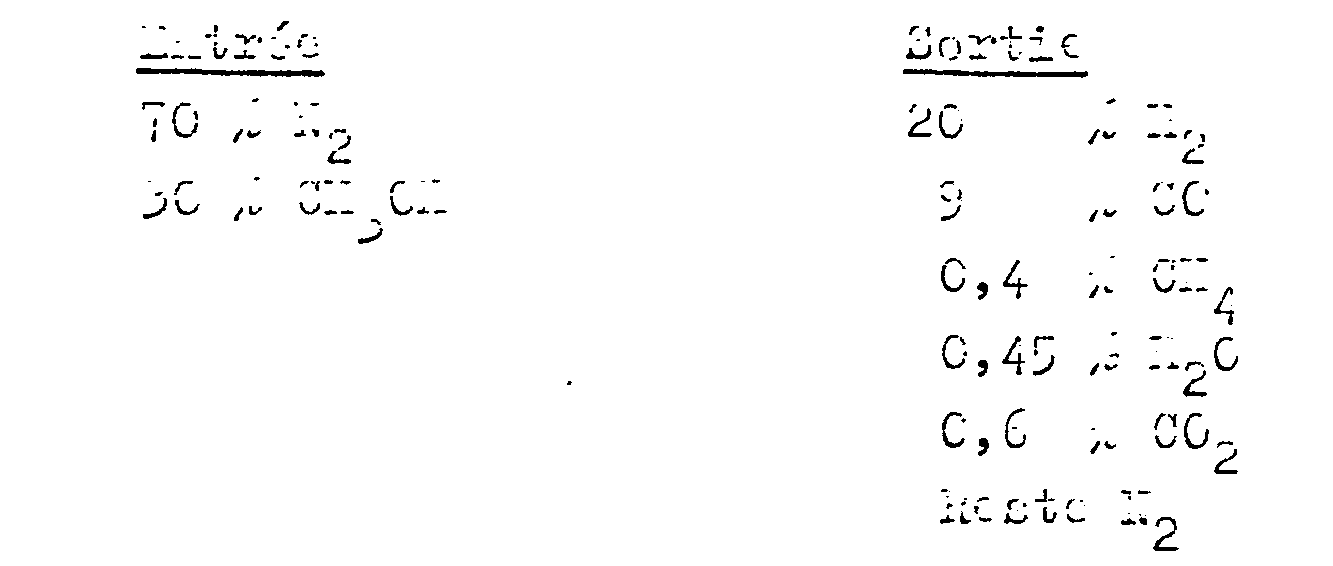
[0037] Les pièces trempées ne présentaient ni carburation ni décarburation. Le potentiel
carbone de l'at- nosphère mesurè par un clinquant était de 0,30 % C. Exemple 6 - (carburation
comparative)
[0038] Des essais ont été effectués d'autre part sur des pièces en acier 20NCD2 ; pendant
5 heures 30 minutes à 900°C avec deux atmosphères l'une du type décrit dans l'exemple
1, c'est-à-dire contenant 15 % de C0, l'autre identique mais sans C0. Ces pièces présentaient
des gorges ou alésages ayant une largeur de 3 mm environ, et une profondeur également
de 3 mm environ. Les résultats obtenus sont présentés dans le tableau suivant :
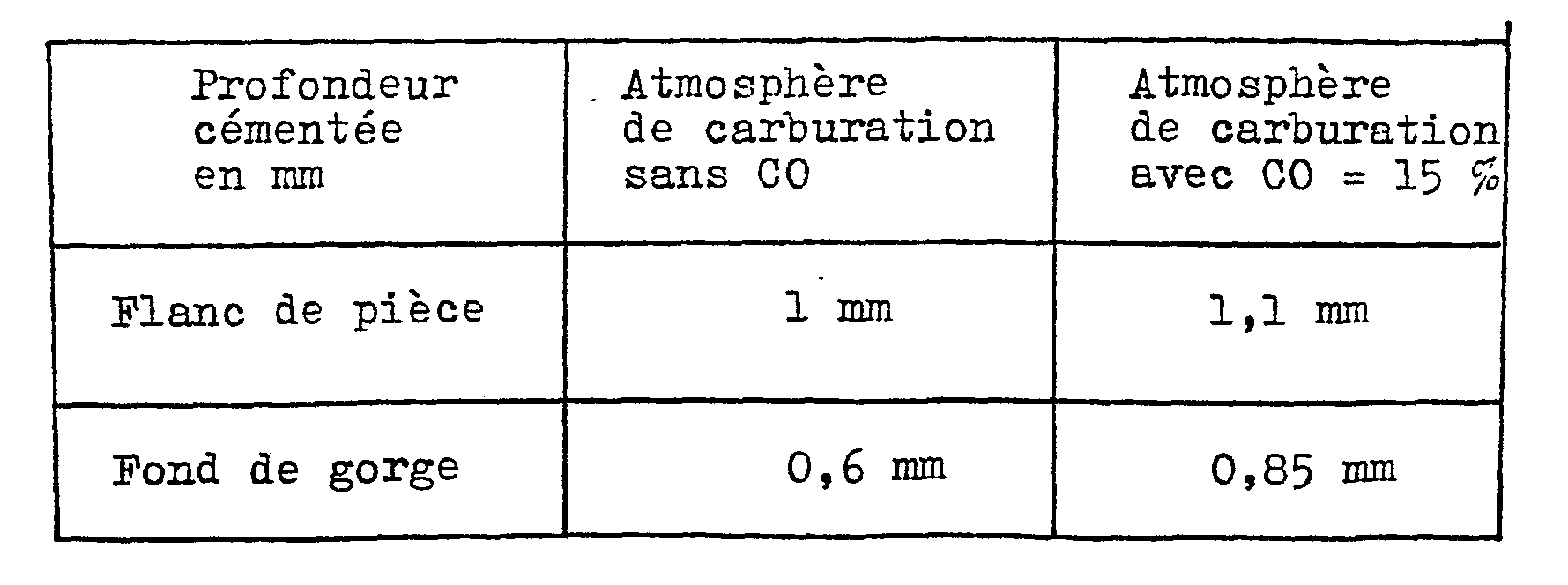
[0039] La profondeur carburée à flanc de pièce est augmentée ainsi que celle à fond de gorge.
De plus, l'homogénéité de traitement est meilleure avec un écart relatif beaucoup
plus satisfaisant.
[0040] L'invention n'est nullement limitée aux exemples décrits ci-dessus qui n'ont été
donnés qu'à titre illustratif mais non limitatif.
1. - Procédé de traitement thermique de l'acier tel que le chauffage avant trempe,
le recuit, la cémentation, effectué, dans un four en présence d'une atmosphère en
écoulement continu obtenue en mélangeant un gaz porteur incluant de l'azote et éventuellement
de l'hydrogène avec un gaz actif constitué par un hydrocarbure avec une proportion
en volume d'hydrocarbure comprise entre 0,2 et 30 % dudit mélange, caractérisé en
ce qu'on réalise ladite atmosphère en mélangeant au gaz porteur précité, constitué
par de l'azote ou contenant de l'azote ayant une teneur en O2 < 10 ppm, une teneur en H2O < 10 ppm et une teneur en CO2 < 10 ppm, un hydrocarbure choisi parmi l'un des composés suivants : CH4, C4H10, C3H8, C2H4, C2H2' c2H6 et de l'oxyde de carbone, la proportion d'oxyde de carbone dans le mélange total
étant comprise entre 0,1 et 30 % en volume et en ce qu'on porte l'acier à une température
comprise entre 750 et 1150°C.
2. - Procédé selon la revendication 1, caractérisé en ce que l'oxyde de carbone est
introduit dans le mélange précité sous forme de gaz pur.
3. - Procédé selon la revendication 1, caractérisé en ce que l'oxyde de carbone est
introduit dans le mélange précité sous forme d'un mélange partiel azote-oxyde de carbone
à l'état gazeux ou liquide.
4. - Procédé selon la revendication 1, caractérisé en ce que l'oxyde de carbone précité
provient de la décomposition à chaud du méthanol selon la réac-

ledit méthanol étant introduit dans le mélange précité.
5. - Procédé selon l'une des revendications 1 à 4, caractérisé en ce que, dans le
cas d'une carbonitruration, ladite atmosphère est réalisée par mélange outre du gaz
porteur, de l'hydrocarbure et de l'oxyde de carbone précités, d'ammoniac en proportion
de 0,1 à 30 % en volume.
6. - Procédé de contrôle du traitement ther. mique de l'acier effectué, selon l'une
des revendica- tions 1 à 5, dans un four en présence d'une atmosphère en écoulement
continu obtenue en mélangeant un gaz porteur incluant de l'azote et éventuellement
de l'hydrogène avec un gaz actif constitué par un hydrocarbure et par de l'oxyde de
carbone, caractérisé en ce qu' on mesure la teneur résiduelle en hydrocarbure, en
vapeur et eau et en gaz carbonique de l'atmosphère sortant du four, on détermine,
en utilisant des abaques préétablis qui donnent une relation entre les teneurs résiduelles
en hydrocarbure vapeur d'eau et gaz carbonique et les taux de carbone de l'acier,
la teneur en hydrocarbure de l'atmosphère entrant dans le four qui est nécessaire
pour l'obtention du taux de carbone désiré et on règle le débit d'hydrocarbure entrant
dans le four pour obtenir les teneurs précitées à la sortie du four et par conséquent
ledit taux de carbone désiré.
7. - Acier obtenu par le procédé selon l'une des revendications 1 à 5.