[0001] The present invention relates to antiperspirant compositions in the form of solid
applicators. The compositions herein comprise at least three phases, one of which
is an antiperspirant phase containing antiperspirant materials a second of which is
an alcohol gel phase which can contain deodorant materials and a third of which is
a barrier phase isolating and insulating the other two phases from each other.
[0002] Antiperspirant compositions in stick form are known in the art. Single phase antiperspirant
compositions have, for example, been disclosed in U.S. Patent 1,948,669 and British
Patent 1,433,695. Stick compositions of this type typically employ large amounts of
waxy materials as the vehicle which delivers the antiperspirant active to the skin.
The antiperspirant active materials often are present in the stick in particulate
form which is particularly effective. Such stick products are stable and are especially
effective for delivering large amounts of antiperspirant salts to the skin.
[0003] Attempt have been made to realize deodorant and antiperspirant sticks which deliver
active ingredients to the skin via a vehicle which glides easily over the skin surface
and which imparts a cooling sensation to the skin both during and after application.
Soap/alcohol gels can provide such cosmetic benefits. However, incorporation of conventional
astrigent antiperspirant salts into such gels tends to interfere with the gel structure
and render it less cosmetically desirable. To solve such compatibility problems, soap/alcohol
gel sticks have been formulated using special additives such as lactate salts. (See,
for example, U.S. Patent 2,732,327 and U.S. Patent 2,900,306. Some soap/alcohol gel
antiperspirant sticks have also been formulated in two phases with an inner core containing
gel-compatible antiperspirant salts and an outer shell containing deodorant materials
(See U.S. Patent 2,970,083).
[0004] Combinations of a conventional waxy antiperspirant composition with a soap/alcohol
gel to form a two-phase stick composition could enhance composition efficacy and improve
composition cosmetic benefits. Such combination is, however, not made without certain
difficulties. While each phase alone of such a stick composition is stable, contact
between the two phases can cause destructive interaction between the two phases. The
alcohol gel phase experiences syneresis which is a bleeding or leaking of the gelled
alcohol from the gel structure or matrix. Such leaked alcohol can interact with components
of the waxy phase and can thus consume or physically separate the phases, thereby
resulting in an unacceptable consumer product.
[0005] It is speculated herein that this problem of interfacial interaction is due to, or
at least exacerbated by, the presence of particulate materials in the antiperspirant
phase. Often, the particulate material present in the antiperspirant phase is the
antiperspirant active material itself. The particulate may be present, however, merely
as a filler or inert component. Interfacial interaction which affects gel pH is also
a factor in product stability.
[0006] Given the state of the antiperspirant art as described above, there is a continuing
need for new and useful antiperspirant compositions which are stable and which provide
both good antiperspirant efficacy as well as desirable application characteristics.
Accordingly, it is an object of the present invention to provide multi-phase antiperspirant
applicators with effective antiperspirancy performance and desirable application characteristics.
[0007] It is a further object of the present invention to provide such multi-phase antiperspirant
applicators which do not exhibit severe interfacial interaction.
[0008] It is a further preferred object of the present invention to provide multi-phase
antiperspirants which can deliver both antiperspirant and deodorant materials to the
skin simultaneously.
[0009] It has been surprisingly discovered that the above objectives can be realized and
superior multi-phase antiperspirants provided by formulating an applicator having
a thin waxy barrier of specific composition. This barrier phase prevents interfacial
interaction when present in the region interjacent to a solid shearable antiperspirant
phase which preferably utilizes particular amounts of certain types of waxes, emollients
and particulate antiperspirant actives and a gel phase formulated with particular
amounts of certain polyhydric alcohols and gel-forming agents.
Summary of the Invention
[0010] The present invention relates to antiperspirant compositions in the form of a multi-phase
applicator. Such compositions comprise from 35% to 65% by weight of a shearable solid
antiperspirant phase, from 35% to 65% by weight of a gel phase; and an interjacent
barrier phase contiguous to both the gel and the antiperspirant phase, which barrier
phase comprises from 1% to 10% by weight of the total antiperspirant composition.
[0011] The antiperspirant phase of the composition can be any solid, shearable material
which can deliver an astringent antiperspirant active. Preferably, the antiperspirant
phase contains from 2% to 15% by weight of the antiperspirant phase of a high melting
point wax, from 20% to 50% by weight of the antiperspirant phase of a water-insoluble,
liquid, organic emollient and from 15% to 60% by weight of the antiperspirant phase
of particulate astringent antiperspirant material on an anhydrous basis. The high
melting point wax utilized in the antiperspirant phase has a melting point from 65.5
°C to 102°C.
[0012] The gel phase of the compositions contains from 10% to 92% by weight of gel phase
of a polyhydric alcohol and from 5% to 15% by weight of gel phase of a gel forming
agent.
[0013] The polyhydric alcohol used in the gel phase can be a polyhydric aliphatic alcohol
having from 2 to 3 carbon atoms and 2 or 3 hydroxyl groups. The gel forming agent
can be either a sodium or potassium salt of a fatty acid having from 14 to 18 carbon
atoms.
[0014] The barrier phase of the compositions herein has a thickness of at least about 0.127
mm. This barrier phase comprises from 10% to 40% by weight of the barrier phase of
a water-insoluble, alcohol-insoluble, high melting point wax and from 20% to 90% of
a liquid organic emollient. The barrier phase contains no more than 0.01 % of particulate
materials having a particle size of greater than one micron and should not lower the
gel pH below about 9.5.
[0015] Preferred embodiments of the compositions herein provide the antiperspirant phase
in the form of a core, the barrier phase in the form of a tubular sleeve interjacent,
and with the gel phase surrounding the sleeve forming a shell. Preferred embodiments
also include three-phase sticks wherein the gel phase contains a mono-hydric alcohol
component to provide a skin cooling sensation and a deodorant material to provide
deodorant efficacy.
Brief Description of the Drawings
[0016]
Fig. 1 is a perspective view of the preferred embodiment of the present invention
with the cosmetic portion partially extended.
Fig. 2 is a cross-section taken on the line 2-2 of Fig. 2 with the thickness of the
barrier phase exaggerated for clarity of illustration.
Fig.3 is a fragmentary perspective view of another embodiment of the invention.
Fig.4 is a plan view of yet another embodiment of the invention.
Antiperspirant Phase
[0017] One essential component of the antiperspirant sticks herein is a solid, shearable
phase. This phase provides the vehicle for the antiperspirant-active ingredient. Such
an antiperspirant phase generally serves to deliver antiperspirant material(s) to
the skin via a medium which does not feel runny, cold, or sticky. The antiperspirant
phase component of the stick compositions herein comprises from 35% to 65%, preferably
from 45% to 55%, by weight of the total composition. The antiperspirant phase is solid
(i.e., able to retain a rigid form at 20°C) and is shearable (i.e., yields easily
when rubbed onto the skin in the normal manner of usage of cosmetic sticks).
[0018] Many solid antiperspirant compositions are known in the art which tend to interact
with soap/ alcohol gels if such antiperspirant compositions are formulated into stick
products along with such soap/alcohol gels. It has been discovered, however, that
such antiperspirant compositions can be combined with soap/alcohol gels in the three-phase
stick products of the present invention.
[0019] The skilled artisan can readily formulate a large number of solid compositions which
have antiperspirant effectiveness and have shearable cosmetics and which are thus
suitable for use as the antiperspirant phase of the stick compositions herein.
[0020] In an especially preferred embodiment, the antiperspirant phase is substantially
anhydrous, (i.e., comprises no more than about 1.0% by weight of the antiperspirant
phase of water in addition to water of hydration in the antiperspirant salt), provides
the antiperspirant active in an especially effective undissolved particulate form,
and comprises a water-insoluble wax, a liquid organic emollient and particulate antiperspirant-active
material.
Water-Insoluble Wax
[0021] A high melting point, water-insoluble wax is the principal component of the antiperspirant
phase in a preferred embodiment of the stick compositions herein. It is believed that
the high melting point wax provides a structure which can be sheared during application
to the skin, thereby depositing layers of wax and antiperspirant active particles
onto the skin.
[0022] The antiperspirant phase herein contains from 2% to 15%, preferably from 3% to 11%,
by weight of antiperspirant phase of the water-insoluble wax materials. Maintenance
of wax concentrations within these limits permits the realization of acceptable stick
cosmetic characteristics. Furthermore, exposure to normal temperature extremes, especially
during summer, might deform sticks without high melting point wax concentrations within
the limits indicated.
[0023] The waxes employed as an essential component of the preferred antiperspirant phase
of the sticks herein are essentially water-insoluble (soluble to an extent of less
than 0.5% by weight in water at 26.5°C). Such waxes have a melting point within the
range of from 65.5°C to 102°C, preferably within the range of from 76.5°C to 99°C.
Such waxes are referred to as high melting point waxes. Examples of suitable high
melting point waxes are beeswax, carnauba, bayberry, candelilla, monta, ozokerite,
ceresin, paraffin, synthetic waxes such as Fisher-Tropsch waxes, and microcrystalline
wax. Preferred high melting point waxes are ceresin, ozokerite, white beeswax and
synthetic waxes. Mixtures of such high melting point waxes are also useful.
Liquid Organic Emollient
[0024] A second essential component of the preferred antiperspirant phase is a liquid organic
emollient. This emollient component serves to improve the cosmetic acceptability of
the compositions herein by helping to impart a soft, supple character to the skin
treated with the instant stick compositions.
[0025] The emollients used herein can be any non-toxic, organic material or mixtures thereof
which is of low irritation potential, which is liquid at 20°C and which is substantially
water-insoluble (i.e. water solubility of from 0.5% to 1.0% by weight in water at
20°C). However, the liquid emollients of this invention are water-dispersible in the
presence of a surfactant, e.g., soap, which is desirable in that it permits the removal
of the composition during washing or bathing. The emollient component comprises from
20% to 50%°, preferably from 30% to 40%, by weight of the antiperspirant phase.
[0026] Suitable organic emollients include fatty acid and fatty alcohol esters and water
insoluble ethers. Examples of such emollients include isopropyl myristate, isopropyl
palmitate, cetyl acetate, cetyl propionate, di-n-butyl phthalate, diethyl sebacate,
diisopropyl adipate, ethyl carbomethyl phthalate, and the condensation product of
about 14 moles of propylene oxide with one mole of butyl alcohol (Fluid AP- Trade
Mark). Preferred organic liquid emollients include isopropyl myristate, isopropyl
palmitate, di-n-butyl phthalate, and Fluid A
pe. Especially preferred organic emollients include isopropyl myristate, isopropyl palmitate
and Fluid A
pe.
[0027] Suitable emollients for use herein also include both volatile and non-volatile polyorganosiloxane
materials, especially polydimethylsiloxanes having a viscosity of from 9 to 50 cs.
at 25°C. Examples of suitable organopolysiloxanes include DC-556 fluid, which is tris
(trimethylsiloxy) phenylsilane and DC-225 fluid, a polydimethylsiloxane having a viscosity
of 9.5 cs at 25°C, both marketed by Dow Corning Corporation. Preferred polysiloxane
emollients include SWS-03314 marketed by Stauffer Chemical company and UC-7158 or
UC-7207 each marketed by Union Carbide Corporation.
[0028] Emollients including the liquid emollients suitable for use herein are described
more fully in Balsam and Sagarin, Cosmetics Science and Technology, 2nd Ed., Vol.
1, Wiley-Interscience, 1972, Chapter 2, pp. 27-104 and in U.S. Patent 4,045,548, August
30,1977 to Luedders et al.
Particulate Antiperspirant Material
[0029] A third essential component of the preferred antiperspirant phase of the present
compositions comprises a particulate astringent antiperspirant material. Such antiperspirant
active material, of course, imparts antiperspirancy efficacy to the antiperspirant
stick compositions of the present invention.
[0030] Any aluminum astringent antiperspirant salt or aluminium and/or zirconium astringent
complex in particulate form can be employed herein. Such salts and complexes are well
known in the antiperspirant art. Useful as astringent antiperspirant salts or as components
of astringent complexes include aluminum halides, aluminum hydroxyhalides, zirconyl
oxyhalides, zirconyl hydroxyhalides and mixtures of these salt materials.
[0031] Aluminum salts of this type include aluminum chloride and the aluminum hydroxyhalides
having the general formula AI
2(OH)
XQ
y.XH
2O where Q is chlorine; bromine or iodine; where x is 2 to 5 and x+y = 6 and x and
y do not need to be integers; and where X is from 1 to 6.
[0032] Zirconium compounds which are useful in the present invention include both the zirconium
oxy salts and zirconium hydroxy salts, also referred to as the zirconyl salts and
zirconyl hydroxy salts. These compounds may be represented by the formula
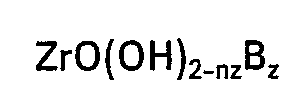
wherein z may vary from 0.9 to 2 and need not be an integer, n is the valence of B,
2-nz is greater than or equal to 0, and B may be selected from the group consisting
of halides, nitrate, sulfamate, sulfate and mixtures thereof. Although only zirconium
compounds are exemplified in this specification, it will be understood that other
group iV(b) metals, including hafnium could be used in the present invention. As with
the basic aluminum compounds, it will be understood that the above formula is greatly
simplified and is intended to represent and include compounds having coordinated and/or
bound water in various quantities, as well as polymers, mixtures and complexes of
the above. As will be seen from the above formula, the zirconium hydroxy salts actually
represent a range of compounds having various amounts of the hydroxyl group, varying
from 1.1 to only slightly greater than 0 groups per molecule.
[0033] Several types of antiperspirant complexes utilizing the above antiperspirant salts
are known in the art. For example, Luedders et al; U.S. Patent 3,792,068, issued February
12, 1974 discloses complexes of aluminum, zirconium and amino acids such as glycine.
Complexes such as those disclosed in this Luedders et al '068 patent and other similar
complexes are commonly known as ZAG. ZAG complexes are chemically analyzable for the
presence of aluminum, zirconium and chlorine. ZAG complexes useful herein are identified
by the specification of both the molar ratio of aluminum to zirconium (hereinafter
«AI:Zr» ratio) and the molar ratio of total metal to chlorine (hereinafter «MetaI:Cl»
ratio). ZAG complexes useful herein have an AI:Zr ratio of from 1.67 to 12.5 and a
Metal:Cl ratio of from 0.73 to 1.93.
Preferred ZAG complexes are formed by
[0034] (A) Co-dissolving in water
(1) one part Al2(OH)6-mQm, wherein Q is an anion selected from the group consisting of chloride, bromide and
iodide and m is a number from 0.8 to 2.0;
(2) parts Zr0(OH)2_aQa.nHzO where Q is chloride, bromide or iodide; where a is from 1 to 2; where n is from
1 to 8; and where x has a value of from 0.16 to 1.2;
(3) p parts neutral amino acid selected from the group consisting of glycine, dl-tryptophane,
dl-β-phenylalanine, dl-valine, dl-methionine and β-alanine, and where p has a value
of from 0.06 to 0.53;
(B) Co-drying the resultant mixture to a friable solid; and
(C) Reducing the resultant dried inorganic-organic antiperspirant complex to particulate
form.
[0035] The preferred aluminum compound for preparation of such ZAG type complexes is aluminum
chlorhydroxide of the empirical formula Al
2(OH)
5CL2H
20. The preferred zirconium compounds for preparation of such ZAG-type complexes are
zirconyl hydroxychloride having the empirical formula ZrO(OH)CI.3H
20 and the zirconyl hydroxyhalides of the empirical formula Zr0(OH)
2-aCI
a.nH
20 wherein a is from 1.5 to 1.87 and n is from 1 to 7. The preferred amino acid for
preparing such ZAG-type complexes is glycine of the formula CH
2(NH
2)COOH. (Salts of such amino acids can also be employed in such antiperspirant complexes.
See U.S. Patent 4,017,599 to A.M. Rubino).
[0036] A wide variety of other types of antiperspirant complexes are known in the art. For
example, Siegal; U.S. Patent 3,903,258, issued September 2,1975 discloses a zirconium
aluminum complex prepared by reacting zirconyl chloride with aluminum hydroxide and
aluminum chlorhydroxide. Rubino; U.S. Patent 3,979,510, issued September 7,1976 discloses
an antiperspirant complex formed from certain aluminum compounds, certain zirconium
compounds and certain complex aluminum buffers. Rubino; U.S. Patent 3,981,896, issued
September 21,1976 discloses an antiperspirant complex prepared from an aluminum polyol
compound, a zirconium compound and an organic buffer. Mecca; U.S. Patent 3,970,748,
issued July 20,1976 discloses an aluminum chlor- hydroxy glycinate complex of the
approximate general formula [Al
2(OH)
4CI][CH
2.NH
2.COOH]. Of all the above types of antiperspirant actives, preferred compounds include
the 5/6 basic aluminum salts of the empirical formula Al
2(OH)
5CL.2H
20; mixtures of AIC1
3.6H
20 and AI
2(OH)
5CL.2H
20 with aluminum chloride to aluminum hydroxychloride weight ratios of up to about
0.5; ZAG type complexes wherein the zirconium salt is ZrO(OH)CI.3H
20; the aluminum salt is Al
2(OH)
5CL.2H
20; and the amino acid is glycine and ZAG-type complexes wherein the zirconium salt
is Zr0(OH)
2-aCIa.nH
20 with a ranging from 1.5 to 1.87 and n ranging from 1 to 7; the aluminum salt is
A1
2(OH)
5CI.2H
20; and the amino acid is glycine.
[0037] The preferred embodiment of the antiperspirant phase of the present stick compositions
contains from 11% to 50%, preferably from 30% to 46%, by weight of the antiperspirant
phase of the particulate astringent antiperspirant material calculated on an anhydrous
metal salt (exclusive of glycine, glycine salts or other complexing agents). Such
particulate antiperspirant material is preferably impalpable, i.e. has particle sizes
ranging from 1 to 100 microns, more preferably from 1 to 50 microns. The antiperspirant
active material herein is preferably alcohol insoluble.
Optional Antiperspirant Phase Components
[0038] The antiperspirant phase of the instant stick compositions can contain a variety
of optional ingredients suitable for improving composition efficacy, stability, cosmetics
and/or aesthetics. Such optional antiperspirant phase components include low melting
point waxes to adjust stick cosmetics, inert filler material to improve composition
stability and cosmetics, perfumes, dyes, coloring agents, preservatives and the like.
[0039] A highly preferred optional component of the preferred antiperspirant phase is an
additional wax material having a melting point of from about 37.8°C up to 65.5°C.
Such optional waxes are referred to herein as low melting point waxes. The low melting
point wax component can be used as an adjunct to the high melting point wax to provide
improved emolliency and to enhance the structural integrity of the waxy antiperspirant
phase. The low melting point wax can also be used to adjust the feel of the stick
compositions herein. One skilled in the art will easily be able to make a product
which feels more brittle, soft, slippery, sticky, rough, etc., by blending various
suitable low melting point waxes with the essentially present high melting point waxes.
[0040] Examples of useful low melting point waxes include fatty acids containing from 12
to 20 carbon atoms, fatty alcohols containing from 12 to 20 carbon atoms, silicone
waxes and glycerol monostearate. Especially preferred materials of this type are the
C12tO C
20 fatty acids and C12tO C
20 fatty alcohols. The most preferred low melting point waxes are cetyl alcohol, stearyl
alcohol, myristyl alcohol, lauryl alcohol and glycerol monostearate.
[0041] If present, the low melting point wax or wax mixture component generally comprises
from 2% to 20%, more preferably from 5% to 15%, by weight of the antiperspirant phase.
[0042] Another preferred optional component for possible use in the antiperspirant phase
of the stick compositions herein is an inert filler material. Such filler materials
also serve to enhance the structural integrity of the antiperspirant phase herein
and serve to improve composition cosmetics.
[0043] Useful inert particulate filler materials include talc; colloidal silica, e.g., Cab-O-Sil
(Trade Mark - Cabot Corp.), a pyrogenic silica having an average particulate diameter
between 0.01 and 0.3 microns as disclosed in British patent 987,301 and British Patent
1,167,173, and finely divided hydrophobic clays such as the rection product of a clay
such as bentonite and dimethyldistearyl ammonium chloride, such treated clays being
marketed under the tradename «BENTONE» (Trade Mark) by NL Industries. Such clay materials
are described more fully in British Patent 1,167,173.
[0044] If present, the inert particulate filler material generally comprises from 0.5% to
5.0% by weight of the waxy antiperspirant phase of the present stick compositions.
[0045] The antiperspirant phase herein can also contain minor amounts i.e., from 0.1% to
1.5% by weight of antiperspirant phase, of conventional additives such as dyes, perfumes,
pigments, coloring agents, etc. In selecting such ingredients only small amounts of
hydrophilic materials shall be used in addition to the active material. Preferably,
less than about 5% of the antiperspirant phase, in addition to the antiperspirant
materials, is soluble in water.
Gel Phase
[0046] The second essential component of the antiperspirant sticks of this invention is
a gel phase formed from certrain polyhydric aliphatic alcohols and certain gel-forming
agents. This gel phase comprises from 3% to 65%, preferably from 45% to 55%, by weight
of the total antiperspirant stick compositions herein. The primary purpose of the
gel phase of the sticks herein is to improve the glidability and ease of application
of the instant stick compositions onto the skin. Optionally, the gel phase herein
can also act as a carrier for deodorant materials and for materials such as monohydric
alcohols which impart a desirable cooling, moist sensation to the skin upon application.
Po!yhydric Aliphatic Alcohol
[0047] One essential component of the gel phase of the present antiperspirant stick compositions
is a polyhydric aliphatic alcohol containing 2 or 3 carbon atoms and 2 or 3 hydroxyl
groups. This polyhydric alcohol or mixtures thereof is the medium which is "gelled"
to form the gel phase of the stick compositions herein. The polyhydric aliphatic alcohol
component of the gel phase comprises from 10% to 92%, preferably from 15% to 50%,
by weight of the gel phase.
[0048] Suitable polyhydric alcohols for use in the gel phase herein include ethylene glycol,
propylene glycol, trimethylene glycol, and glycerine. The most preferred polyol is
propylene glycol.
Gel Forming Agents
[0049] The second essential component of the gel phase of the antiperspirant stick compositions
herein is a gel forming agent which is added to the polyhydric aliphatic alcohol of
the gel phase to form the desired gel material. The gel forming agents used herein
are the sodium and potassium salts (i.e. soaps) of fatty acids containing from about
14 to 18 carbon atoms.
[0050] Gel forming agents generally comprise from 5% to 15% by weight of the gel phase herein,
preferably from 7% to 10% by weight of the gel phase. If the gel forming agent concentrations
lower than those specified are employed, the gels formed tend to be dimensionally
unstable and tend to deform at summertime temperatures. If concentrations of gel forming
agents above those specified are utilized, the gels formed tend to be too hard and
do not exhibit desirable glide and application characteristics. By utilizing gel-forming
agents of the particular type described and in the concentrations specified, gel phases
can be formulated which exhibit structural integrity and which exhibit cosmetically
desirable application properties.
[0051] The fatty acid portion of the soap gel forming agents should be essentially pure
saturated or unsaturated higher fatty acids having a C
14 to C
18 backbone. Suitable mixtures of such acids can be employed provided that such mixtures
are free from significant proportions of other fatty acids of higher or lower chain
length which substantially adversely affect or neutralize the desired gel forming
effects.
[0052] Examples of fatty acids useful in synthesizing the gel forming agents herein include
myristic, palmitic, stearic, oleic, linoleic, linolenic, behenic, margaric acids and
the mixtures of such acids. Naturally occurring sources of such fatty acids include
coconut oil, beef tallow, lanolin, fish oil, beeswax, palm oil, peanut oil, olive
oil, cottonseed oil, soybean oil, corn oil, rapeseed oil, rosin acids, and greases.
Conventional fractionation and/or hydrolysis techniques can be employed if necessary
to obtain the requisite types of fatty acids from such materials.
[0053] Preferred fatty acid soap type gel forming agents include sodium stearate, sodium
palmitate, potassium stearate, potassium palmitate and sodium myristate. The most
preferred gel forming agent is sodium stearate.
Optional Gel-Phase Components
[0054] The gel phase of the instant stick compositions can contain a variety of optional
ingredients suitable for improving composition efficacy, stability, cosmetics and/or
aesthetics. Such optional gel phase components include monohydric alcohols to improve
composition cosmetics, water in small amounts, deodorant materials, alcohol evaporation
retardants, and anti-syneresis agents, perfumes, dyes, pigments, and coloring agents.
[0055] A highly preferred optional component of the gel phase is a monohydric alcohol which
serves to impart a cosmetically desirable cooling sensation to the skin. Monohydric
alcohols of this type contain one to three carbon atoms. Examples of suitable monohydric
alcohols include methanol, ethanol, isopropanol, and n-propanol. Preferred monohydric
alcohols are ethanol and isopropanol.
[0056] While monohydric alcohols can provide a desirable cosmetic cooling benefit for the
antiperspirant stick compositions herein, inclusion of a monohydric alcohol component
can also lead to stick composition instability problems. Monohydric alcohols tend
to produce dimensional instability of the gel phase and tend to cause the gel phase
to evaporate and thereby become sticky as well as to deteriorate and assume a dried
and shriveled appearance.
[0057] It has been surprisingly discovered that such problems can be minimized and that
monohydric alcohols can be successfully incorporated into the gel phase of the stick
compositions herein provided certain concentrations limits for the essential gel phase
components are observed. When monohydric alcohols are employed, it has been found
that the weight ratio of polyhydric alcohol to gel forming agent must exceed about
2.45. When polyhydric aliphatic alcohols and gel forming agents are present in this
ratio, monohydric alcohols can be incorporated into the gel phase in amounts of from
10% to72%, preferably from 40% to 70%, by weight of the gel phase.
[0058] When monohydric alcohols are employed, another highly preferred optional component
of the gel phase is a material which helps retard alcohol evaporation and which acts
as an anti-syneresis agent. Especially preferred materials of this type are cellulose
derivatives such as hydroxyalkylcelluloses and carboxyalkylcelluloses. Especially
preferred materials of this type are hydroxypropylcellulose compounds having a molecular
weight in the range from 60,000 to 1,000,000. Such materials are sold under the name
of Klucel (Trade Mark) by Hercules Incorporated. If present, such alcohol evaporation
retarding agents and anti-syneresis agents comprise from 0.1% to 5.0% by weight of
the gel phase.
[0059] Another optional ingredient of the gel phase herein is a conventional deodorant material.
Suitable deodorants include bacteriostatic quaternary ammonium compounds such as cetyltrimethylammonium
bromide, cetyl pyridinium chloride, benzethonium chloride, diisobutyl phenoxy ethoxy
ethyl dimethyl benzyl ammonium chloride, N-alkylpyridinium chloride, N-cetyl pyridinium
bromide, sodium N-lauroyl sarcosine, sodium N-palmitoyl sarcosine, lauroyl sarcosine,
N-hyris- toyl glycine, potassium N-lauroyl sarcosine and stearyl trimethyl ammonium
chloride.
[0060] If present, deodorants generally comprise from 0.1 % to 1.0% by weight of the gel
phase.
[0061] Conventional optional ingredients such as perfumes, dyes, pigments, coloring agents
and the like can also be added to the gel phase. If present such minor additions comprise
from 0.1 % to 1.5% by weight of the gel phase.
[0062] Small amounts of water can be added to the gel phase. The amount of water added should,
however, be limited to less than about 10%. Water can be used as a solvent for an
optional dry material or for an optional deodorant material. Water in the gel phase
at concentrations exceeding 10% tends to produce a gel phase which is undesirably
soft.
Barrier Phase
[0063] The third essential component of the antiperspirant sticks of this invention is the
barrier phase. The barrier phase serves to segregate the gel phase from the antiperspirant
phase and thereby effectively eliminates the problem of destructive interfacial interaction.
The barrier phase comprises from 1% to 10%, preferably 2% to 4% by weight of the total
antiperspirant stick compositions herein. To insure that the barrier phase constitutes
a continuous layer of protection, the barrier phase should have a minimum thickness
of at least about 0.127 mm. Preferably, the barrier phase ranges in thickness from
0.25 mm to 1.02 mm.
[0064] It has been surprisingly discovered that a thin wax/emollient barrier in the region
interjacent to the gel phase and the antiperspirant phase effectively prevents this
interfacial interaction. Such a wax/emollient barrier must be substantially free (i.e.
present to an extent of less than 0.01% by weight of the barrier phase) of particulate
material (i.e. discrete solid material having a particle size of greater than about
one micron). It is speculated that by providing a region of waxy material which is
free of the diffusion pathways provided by particulate materials, the migration of
the alcohol into the antiperspirant phase is effectively prevented. Effectively isolated
by the interjacent, alcohol-impermeable barrier phase, the gel phase and antiperspirant
phase of the three-phase sticks exhibit negligible destructive interfacial interaction.
[0065] The barrier phase of the compositions herein should also be free of materials capable
of lowering the pH of the gel phase substantially. The barrier should not contain
materials which lower the gel pH in the area of the gel/barrier interface below about
9.5 (pH's below this value tend to deleteriously affect the integrity of the gel phase).
Gel pH can be determined at any time/temperature. Determination of deleterious gel
defects as a result of acidic material in the barrier can best be determined after
the product has been stored for one week at 49°C.
[0066] The barrier phase embodiments of the present invention provide the further advantage
of having shear rates roughly comparable to both the gel and the antiperspirant phases
herein. Thus, the barrier phase when applied to the skin wears away at approximately
the same rate as the gel phase and the antiperspirant phase. Undesirable phase protrusion
that would occur were one phase worn away more slowly is thereby avoided. Additionally,
the barrier phases of the present invention provide the additional cosmetic advantage
of being visually unnoticeable. The skilled artisan can easily formulate barrier phases
and antperspirant phases which have no readily apparent boundary.
[0067] The two essential components of barrier phases herein are alcohol-insoluble waxes
and liquid organic emollients.
Alcohol-Insoluble Waxes
[0068] An essential component of the barrier phase of the present antiperspirant stick compositions
is a high melting point, water-insoluble wax or wax mixture which is insoluble in
the polyhydric alcohol or mixtures thereof which are present in the gel phase (i.e.
alcohol solubility of less than 1% at 26.5°C). Such waxes are a subgroup of those
waxes suitable as the principal component of the preferred antiperspirant phase of
the stick compositions herein. Generally such waxes are non-polar compounds such as
hydrocarbon waxes. Suitable waxes have a melting point within the range of from 65.5°
to 102°C, preferably within the range of from 76.5 °C to 99°C. Examples of suitable
waxes are ozokerite, paraffin, and ceresin.
[0069] The barrier phase herein contains from 10% to 40%, preferably from 20% to 40%, by
weight of the barrier phase of the alcohol-insoluble wax. The skilled artisan will
recognize that barrier phases containing higher levels of the alcohol-insoluble wax
will have less desirable cosmetic characteristics. The skilled artisan may then wish
to adjust the maximum thickness of barrier phases having higher wax concentrations
so as to alleviate the perception of toughness.
Liquid Organic Emollient
[0070] A second essential component of the barrier phase is a liquid organic emolient. This
liquid emollient component serves to improve the cosmetic acceptability of the barrier
phase herein in the same manner as the emollient component of the antiperspirant phase.
The emollients suitable for use in the barrier phase herein are the same as are used
in the antiperspirant phase as described above. The emollient component comprises
from 20% to 90% by weight of the barrier phase.
Optional Barrier Phase Components
[0071] The barrier phase of the instant stick compositions can contain a variety of optional
ingredients suitable for improving composition stability, cosmetics or aesthetics
so long as the barrier phase is relatively free of discrete particulate material and
does not contain undesirable acidic materials. Such optional barrier phase components
include low melting point waxes to adjust stick cosmetics, perfumes, dyes, preservatives
and the like.
[0072] As noted, a highly preferred optional component of the barrier phase is an additional
low- melting wax material or mixtures thereof having a melting point of from 37.8°C
up to 65.5°C. Such optional waxes are referred to herein as low melting point waxes.
The low melting point wax component can be used as an adjunct to the high melting
point wax to provide improved emolliency and to enhance the structural integrity of
the barrier phase. The low melting point wax can be used to adjust the feel of the
stick compositions herein. One skilled in the art will easily be able to make a product
which feels more brittle, soft, slippery, sticky, rough, etc., by blending various
suitable low melting point waxes with the essentially present high melting point waxes.
[0073] Examples of useful low melting point waxes include fatty acids containing from 12
to 20 carbon atoms, fatty alcohols containing from 12 to 20 carbon atoms, silicone
waxes and glycerol monostearate. Especially preferred materials of this type are the
C
12 to C
20 fatty acids and the C
12 to C
20 fatty alcohols. The most preferred low melting point waxes are cetyl alcohol, stearyl
alcohol, myristyl alcohol, lauryl alcohol and glycerol monostearate.
[0074] If present, the low melting point wax component generally comprises from about 5%
to 50%, and preferably from 10% to 30% by weight of the barrier phase.
[0075] The barrier phase herein can also contain conventional additives such as dyes, perfumes,
preservatives, deodorants, etc. If present, such materials should constitute a minor
portion of the barrier phase, i.e., from 0.1% to 1.5% by weight of the barrier phase.
Composition Preparation
[0076] The antiperspirant, gel and barrier phases of the present stick compositions are
prepared separately. The preferred waxy antiperspirant phase of the present compositions
is generally prepared by heating the solid wax and liquid emollient in a suitable
container while gently stirring. When the wax or waxes are melted and mixed thoroughly
with the emollient, the antiperspirant-active ingredient is mixed and dispersed in
the melt. The optional ingredients can then be added or the melt can be cooled to
a temperature above the solidification point before adding additional ingredients.
The barrier phase of the present composition is generally prepared in the same manner
as the antiperspirant phase except that no particulate antiperspirant-active ingredient
is added. Case should be taken in preparing the preferred antiperspirant phases herein
and the barrier phase to avoid use of any materials or procedures which might introduce
free moisture into the composition above the substantially anhydrous level.
[0077] The gel phase of the present composition can be prepared by admixing the essential
and optional gel phase components together in such a manner as to produce a thickened,
stable gel. In a preferred mode of gel preparation, the polyhydric aliphatic alcohol
and the monohydric alcohol are mixed together in a reflux vessel with moderate agitation.
Upon heating the mixture to boiling, the gel-forming agents can be added under continuing
refluxing and agitation until the gel-form-, ing agent fully dissolves. Optional ingredients
such as dyes, deodorants and perfumes can then be added. Refluxing and moderate agitation
is continued until boiling reoccurs if there has been an appreciable temperature drop
due to the addition of the optional materials. The molten mixture can then be placed
in a mold device such that the mixture is allowed to gel into a dimensionally stable
mass of the desired geometric configuration.
[0078] Once prepared, the waxy antiperspirant, gel and barrier phases of the compositions
herein can be joined or combined by any suitable means or in any suitable device so
that a single antiperspirant stick is formed. In the stick product, the waxy antiperspirant
and gel phases should be separated and isolated from each other by the interjacent
barrier phase. The orientation of the phases should be such that all three phases
are exposed in a single application surface.
[0079] Referring now to the drawing, paticularly to Fig. 1 and 2 thereof, there is shown
a preferred geometrical embodiment of the present invention. The waxy antiperspirant
phase is formed as a core 12 of any suitable shape, the barrier phase is formed as
a sleeve 16 surrounding the waxy antiperspirant phase or core 12 and the gel phase
is formed as a shell 14 surrounding the barrier phase or sleeve 16. Most preferably,
the antiperspirant core 12, the barrier phase sleeve 16, and the gel phase shell 14
are in the form of concentric cylinders.
[0080] To prepare three-phase cylindrical antiperspirant stick compositions of this type,
the molten antiperspirant phase mixture is poured into a cylindrical mold and allowed
to set. After reaching room temperature (24°C) the antiperspirant phase core is removed
from the mold. Thereafter, the core is dipped momentarily into the molten barrier
phase mixture. Upon withdrawal from molten barrier phase mixture, the barrier coated
core piece is again allowed to reach room temperature. The piece is then centered
into another mold whose inner diameter is the desired stick diameter. The molten gel
phase which can contain colorants is then added to the annular space and allowed to
cool. Upon cooling, the three-phase sticks of the present invention are removed from
the mold.
[0081] Referring again to the drawing, particularly to Fig. 2, the prepared antiperspirant
stick 10 is carried by a moveable, inner piston 20 to define a stick/piston piece
19. The piston 20 is housed within the hollow cylinder 18. The tolerance between the
stick/piston piece 19 and the interior wall 21 of the cylinder 18 is such that the
stick/ piston piece 19 can be manually pressed upward by exerting force on the piston's
anterior face 22 to expose the distal end portion of antiperspirant stick 10 for use.
[0082] In other embodiments of the present invention, shown and illustrated in Fig. 3 and
4, multiple phases can be used. For example, with reference to Fig. 3, multiple planar
phases can be utilized, if desired. Hence, a generally rectangular stick can comprise
antiperspirant phases 12', gel phases 14', and barrier phases 16'. Additionally, for
example, with reference to Fig. 4, multiple concentric phases can be utilized, if
desired. Thus, a generally circular stick can comprise antiperspirant phases 12",
gel phases 14", and barrier phases 16".
[0083] The three-phase antiperspirant sticks of the present invention are illustrated by
the following examples:
Example I
[0084] A three-phase antiperspirant stick of the following composition is prepared.
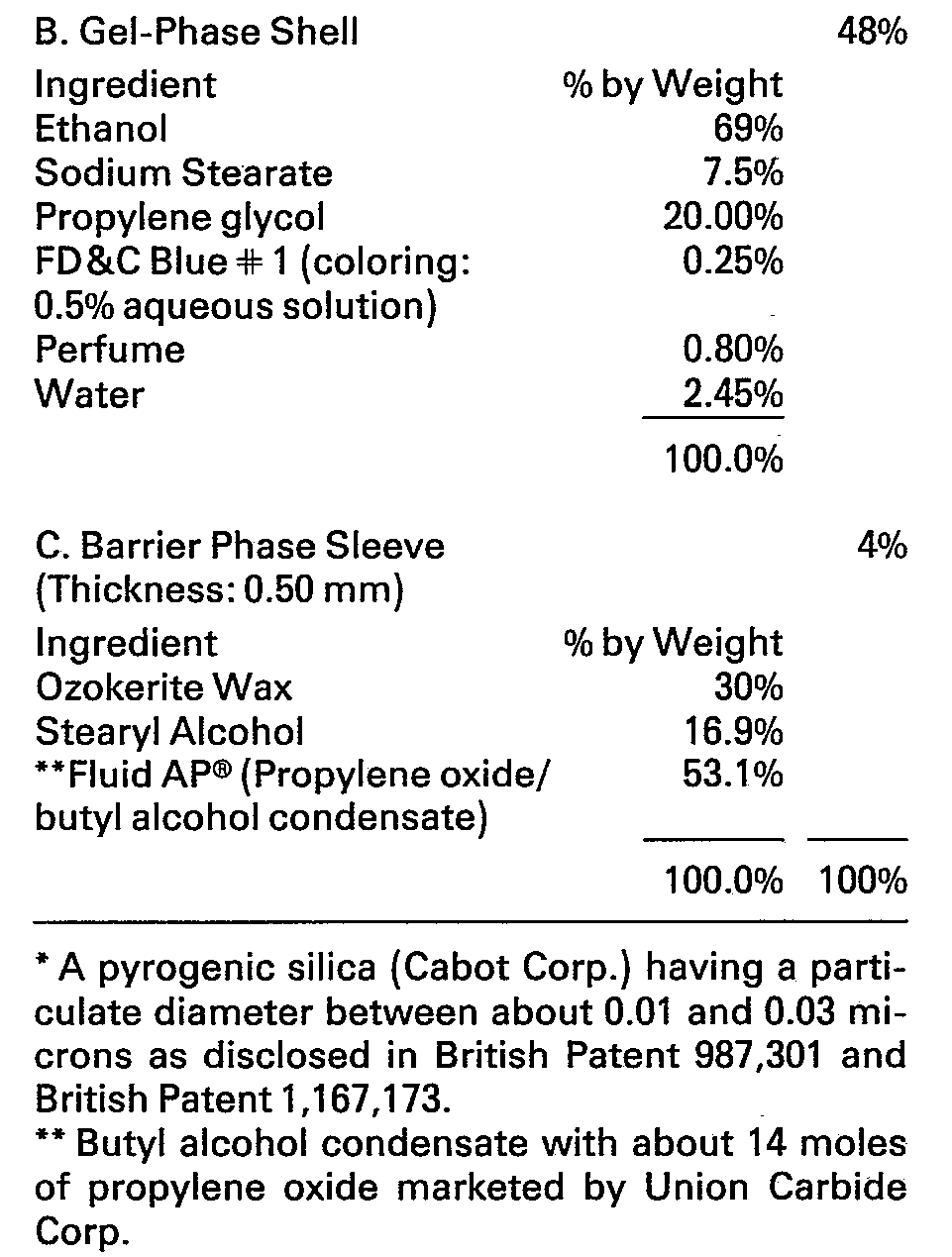
In Example I, the stick is prepared by first forming the antiperspirant core by charging
a steel vessel with the ozokerite wax, cetyl alcohol, and isopropyl myristate and
heating to approximately 93°C with the moderate agitation until these components are
well intermixed. Next, the cab-o-sil is stirred into the mixture and is dispersed
therein. Thereafter, the aluminum chlorhydroxide powder is likewise stirred into the
mixture and is dispersed therein. This mixture is then allowed to cool to just above
the solidification temperature at which point the perfume is stirred into the mixture.
The molten mixture is finally poured into the cylindrical mold; is allowed to solidify
by cooling to room temperature; and thereafter is removed from the mold to form the
antiperspirant cores of the present invention.
[0085] The barrier phase components of ozokerite wax, stearyl alcohol and Fluid AP
O of the specified proportions are charged to a second steel vessel and are heated
with moderate agitation until well intermixed. The antiperspirant cores prepared as
described above are dipped for about one second into the molten barrier phase mixture
and then are withdrawn. The antiperspirant core/barrier sleeve pieces are then allowed
to cool to room temperature.
[0086] The gel phase components are charged into a third steel vessel equipped with a reflux
condenser with the ethanol and the propylene glycol, and then are heated with moderate
agitation until the mixture begins to boil and reflux. Thereafter, sodium stearate
is added. The heating and agitation is continued until the sodium stearate is completely
dissolved. Next, the optional components comprising water, the FD&C Blue # 1, and
the perfume are added while maintaining the agitation and refluxing. The molten gel
material is then poured into the annular space of a suitable cylindrical mold into
which had been centered the previously prepared antiperspirant core/barrier phase
piece. The molten gel is allowed to solidify to form the shell of the three-phase
stick of the present invention.
[0087] The stick so produced is an effective antiperspirant composition in the form of a
three-phase stick. The stick exhibits minimal syneresis and interfacial interaction
and provides cosmetically desirable application characteristics when applied to the
skin.
[0088] Sticks of substantially similar physical/cosmetic character and antiperspirant effectiveness
are realized when in the Example I stick the isopropyl palmitate of the antiperspirant
core is replaced with an equivalent amount of isopropyl myristate, cetyl acetate,
cetyl propionate, di-n-butyl phthalate, diethyl sebacate, diisopropyl adipate, ethyl
carbomethyl phthalate, Fluid AP
O (Butyl alcohol condensed with about 14 moles of propylene oxide) or DCC-225 Fluid
(dimethyl siloxane polymer of viscosity 9.5 cs. at 25 °C marketed by Dow Corning Corp.).
[0089] Compositions of substantially similar physical/ cosmetic character and antiperspirant
effectiveness are realized when in the Example I stick the sodium stearate of the
gel phase shell is replaced with an equivalent amount of sodium palmitate, sodium
myristate, potassium palmitate or potassium stearate.
Example II
[0090] A three-phase antiperspirant stick of the following compositon is prepared:

Such a stick is prepared in a manner similar to that described in Example I. The stick
so produced is an effective antiperspirant composition in the form of a three-phase
stick. The composition exhibits minimal interfacial interaction and glides easily
onto the skin during application.
[0091] Stick compositions of substantially similar physical/cosmetic character and antiperspirant
effectiveness are realized when in the Example II stick composition the ceresin wax
of the antiperspirant core is replaced with an equivalent amount of ozokerite, white
beeswax or carnauba wax.
[0092] Compositions of substantially similar physical/ cosmetic character and antiperspirant
effectiveness are realized when in the Example II composition the propylene glycol
of the gel phase is replaced with an equal amount of glycerine, ethylene glycol, or
trimethylene glycol.
[0093] Compositions of substantially similar stability are realized when in the barrier
phase of the Example 11 composition the paraffin is replaced with an equal amount
of ceresin or ozokerite.
Example III
[0094] A three-phase antiperspirant stick of the following composition is prepared:

[0095] Such a stick is prepared in a manner similar to that described in Example I. The
stick so produced is an effective antiperspirant/deodorant composition in the form
of a three-phase stick. The composition exhibits minimal interfacial interaction and
provides a cooling sensation when applied to the skin.
[0096] Stick compositions of substantially similar physical/cosmetic character and antiperspirant/
deodorant effectiveness are realized when, in the Example III composition, the stearyl
alcohol of the antiperspirant core is replaced with an equivalent amount of cetyl
alcohol, myristyl alcohol, lauryl alcohol or glycerol monostearate.
[0097] Stick compositions of substantially similar physical/cosmetic character and antiperspirant/
deodorant effectiveness are realized when, in the Example III composition, the aluminum
chlorhy- droxide/aluminum chloride mixture is replaced with an equivalent amount of
a particulate antiperspirant active material selected from the group consisting of
ZAG complexes wherein the zirconium compound is Zr0(OH)
2-aCI
a.nH
zO with a = 1.5 to 1.87 and n = 1 to 7; the aluminum compound is A'2(OH)5
C'.2H20 and the amino acid compound is glycine: That is, the above represents any aluminum/zirconium/chlorhydroxide
salt having an AI:Zr molar ratio range of 1.67 to 12.5 and a Metal:Cl molar ratio
range of 0.73 to 1.93.
[0098] Stick compositions of substantially similar physical/cosmetic character and antiperspirant/
deodorant effectiveness are realized when in the Example III stick compositions the
ethanol of the gel phase is replaced by an equivalent amount of methanol, isopropanol,
or n-propanol.
Interfacial Interaction Evaluation
[0099] As noted above, a barrier phase of specified composition which is free of particulate
material and has a specified minimum thickness is essential to the realization of
antiperspirant sticks which are not subject to degradation by interfacial interaction.
The importance of such essential elements of the barrier phase can be demonstrated
by formulating stick compositions with barrier phases containing various types of
waxes and by formulating stick compositions with barrier phases containing various
particulate materials such as talc, particulate active, and kaolin, and then observing
such compositions after a one week storage at 49°C. Those compositions subject to
interfacial interaction can be identified by the presence of a liquid runoff present
in the bottom of the container holding the three-phase sticks and/or plasticization
of the antiperspirant core phase. Further visual evidence of interfacial interaction
is the shrinking of both the gel and the antiperspirant phases.
[0100] Storage at 49°C is a relatively harsh test condition. Even barrier-free sticks which
would remain stable under milder test conditions (e.g., room temperature) for as long
as two months might show appreciable interfacial interaction after only the one week
at the elevated 120°F storage temperature. Thus, sticks which do not exhibit interfacial
interaction after one week at the elevated temperature storage are very stable sticks.
Of course, it is realized that prolonged storage at elevated temperatures or storage
at even higher temperatures will induce degradation in even the barrier-containing
sticks of the present invention.
[0101] Several stick compositions are selected for such interfacial interaction evaluation
at 49°C for one week. The compositions tested are those described in Table I.
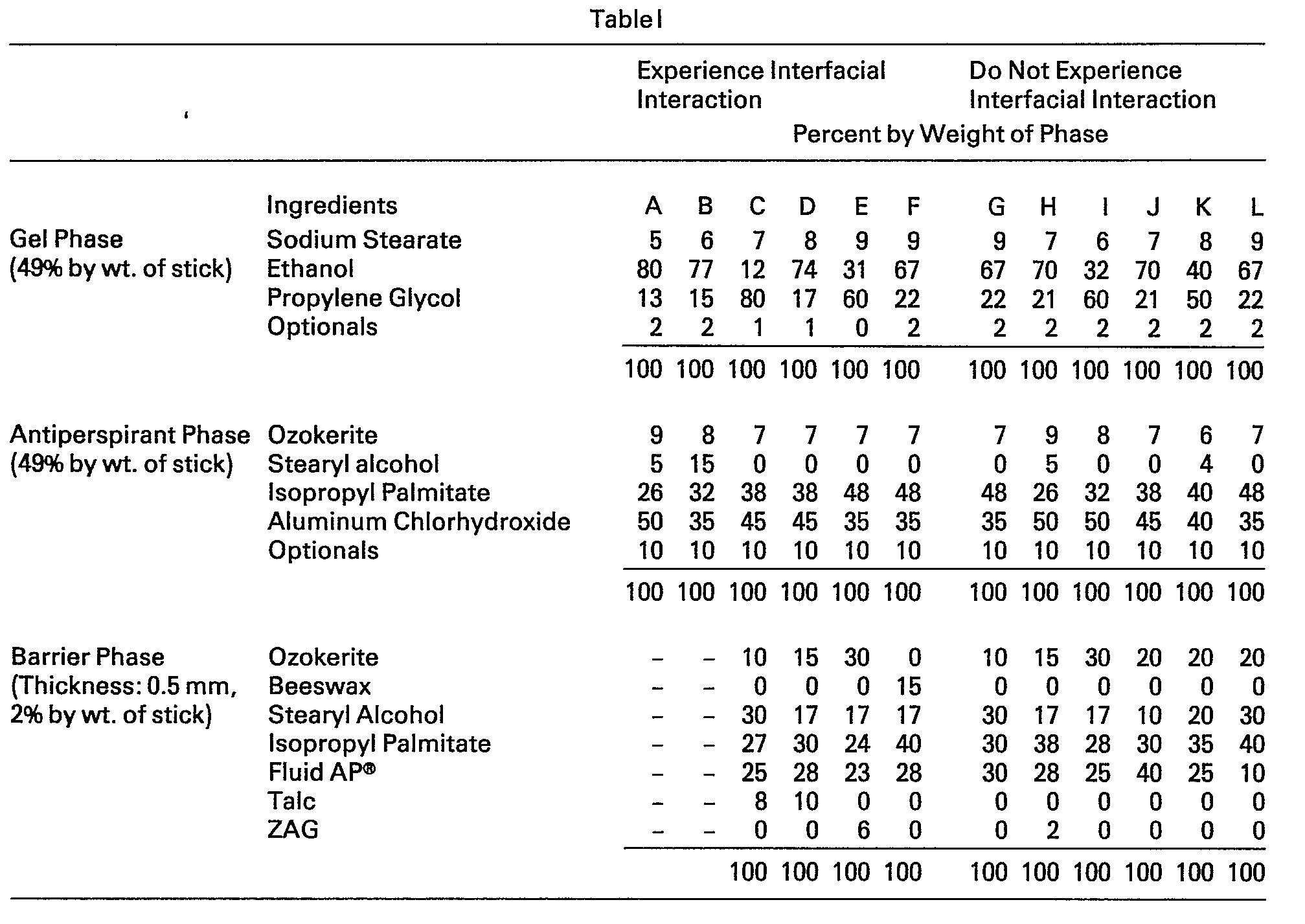
[0102] As can be seen from the above Table I, compositions A through F exhibit interfacial
interaction while compositions G through J do not exhibit such degradation: Compositions
G-J represent compositions of the present invention inasmuch as these compositions
contain a barrier phase of the requisite composition, minimum thickness and which
is relatively free of particulate materials. Compositions A-F either do not contain
a barrier phase or have a barrier phase either containing a high melting point wax
which is soluble in the gelling solution or containing significant amounts of particulate
materials. These compositions without barriers or with defective barriers are thus
subject to interfacial interaction.
1. An antiperspirant composition in the form of a multi-phase applicator including
an antiperspirant phase and a gel phase, characterised in that the composition comprises:
A) from 35% to 65% by weight of the composition of the antiperspirant phase which
comprises a solid, shearable vehicle containing an astrigent antiperspirant material;
B) from 35% to 65% by weight of the composition of the gel phase which comprises:
I. from 10% to 92% by weight of the gel phase of a polyhydric aliphatic alcohol containing
2 or 3 carbon atoms and 2 or 3 hydroxy groups; and Il. from 5% to 15% by weight of
the gel phase of a gel forming agent selected from sodium and potassium salts of fatty
acids containing from 14 to 18 carbon atoms; and
C) from 1% to 10% by weight of the composition of an interjacent barrier phase contiguous
to the gel phase and the antiperspirant phase, wherein the barrier phase has a thickness
of at least 0.127 mm and comprises:
I. from10% to 40% by weight of the barrier phase of a water-insoluble, alcohol-insoluble
high melting point wax or wax mixture having a melting point of from 65.6°C to 102°C;
and
II. from 20% to 90% by weight of the barrier phase of a water-insoluble, liquid organic
emollient, and wherein the barrier phase contains no more than 0.01 % of particulate
materials having a particle size of greater than one micron and does not reduce the
pH of the gel phase below pH 9.5 in the region of the gel/barrier interface.
2. An applicator according to Claim 1, characterized in that the antiperspirant phase
comprises:
I. from 2% to 15% by weight of the antiperspirant phase of a water-insoluble high
melting wax or wax mixture having a melting point of from 65.5°C to 102°C;
II. from 20% to 50% by weight of the antiperspirant phase of a water-insoluble liquid,
organic, emollient, and
III. from 11% to 50% by weight on an anhydrous basis of the antiperspirant phase of
a solid particulate astringent antiperspirant material;
and in that the gel phase additionally contains from 10% to 72% by weight of gel phase
of a monohydric alcohol selected from the group consisting of methanol, ethanol, isopropanol,
and n-propanol, and wherein the weight ratio of polyhydric alcohol to gel-forming
agent in the gel phase exceeds about 2.45.
3. An applicator according to Claim 2, characterised in that
(1) the high melting wax comprises from 3% to 11 % by weight of the antiperspirant
phase and is selected from the group consisting of beeswax, carnauba, bayberry, candelilla,
montan, ozokerite, ceresin, paraffin, Fisher-Trophsch waxes, microcrystalline waxes
and mixtures thereof;
(2) the organic emollient comprises from 30% to 40% by weight of the antiperspirant
phase and is selected from the group consisting of isopropyl myristate, isopropyl
palmitate, cetyl acetate, cetyl propionate, di-n-butyl phthalate, diethyl sebacate,
diisopropyl adipate, ethyl carbomethyl phthalate, the condensation product of about
14 moles of propylene oxide with one mole of butyl alcohol, and polydimethylsiloxanes
having a viscosity of from 9 to 50 cs. at 25 °C;
(3) the particulate antiperspirant material comprises from 30% to 46% by weight of
an anhydrous metal salt basis (exclusive of complexing agents) of the antiperspirant
phase and is selected from the group consisting of:
i) aluminum hydroxyhalides of the empirical formula AI2(OH)xQy.XH2O wherein Q is selected from the group consisting of chlorine, bromine and iodine,
wherein X is from 2 to 5 and x+y = 6 and wherein X is 1 to 6; and
ii) zirconium/aluminium/amino acid complexes which contain
a) one part of an aluminum compound of the formula A'2(OH)6-mQm.YH20 wherein Q is selected from the group consisting of chloride, bromide and iodide;
m is a number from 0.8 to 2.0 and Y is 1 to 6;
b) x parts of a zirconium compound of the formula Zr0(OH)2-aQa1.nH2O wherein Q is selected from the group consisting of chloride, bromide and iodide;
wherein a is from 1 to 2, wherein n is from 1 to 8 and wherein x is from 0.16 to 1.2;
and
c) p parts neutral amino acid selected from the group consisting of glycine, dl-tryptophane,
dl- phenylalanine, dl-valine, dl-methionine and -alanine, and wherein p has a value
of from 0.06 to 0.53;
(4) the polyhydric aliphatic alcohol comprises from 15% to 50% by weight of the gel
phase and is selected from the group consisting of ethylene glycol, propylene glycol,
trimethylene glycol, and glycerine;
(5) the monohydric alcohol comprises from 40% to 70% by weight of the gel phase and
is ethanol or isopropanol;
(6) the water-insoluble, alcohol-insoluble high melting point wax of the barrier phase
comprises from 20% to 40% by weight of the barrier phase and is selected from the
group consisting of paraffin, ozokerite and ceresin; and
(7) the barrier phase further comprises from 10% to 30% by weight of the barrier phase
of a low melting point wax or wax mixture having a melting point of from 37.8°C to
65.5°C.
4. An applicator according to Claim 3, characterised in that the low melting point
wax is selected from the group consisting of cetyl alcohol, stearyl alcohol, myristyl
alcohol, lauryl alcohol and glycerol monostearate.
5. An applicator according to any one of Claims 1-4, characterised in that the gel-forming
agent comprises from 7% to 10% by weight of the gel phase and is selected from the
group consisting of sodium stearate, sodium palmitate, sodium myristate, potassium
stearate and potassium palmitate.
6. An applicator according to any one of claims 1-5, characterised in that the antiperspirant
phase contains an additional component or components selected from
A) from 2% to 20% by weight of the antiperspirant phase of a low melting point wax
or wax mixture having a melting point of from 37.8°C to 65.5°C; and
B) from 0.5% to 5% by weight of the antiperspirant phase of an inert filler material.
7. An applicator according to any one of Claims 1-6, characterised in that the gel
phase contains an additional component or components selected from
A) from 0.1 % to 1.0% by weight of the gel phase of a deodorant material; and
B) from 0.1% to 5.0% by weight of the gel phase of an antisyneresis/evaporation retardant
selected from the group consisting of carboxyalkylcelluloses and hydroxyalkylcelluloses.
8. An applicator according to any one of Claims 1-7, characterised in that the antiperspirant
phase forms a core of a three-phase stick, the barrier phase forms a sleeve surrounding
the core and the gel phase forms a shell surrounding the barrier phase.
9. An applicator according to Claim 8, characterised in that the barrier phase has
a thickness of from 0.25 mm to 1.02 mm.
10. A rub-on antiperspirant applicator comprising a plurality of chemically dissimilar
active phases characterised in that a barrier phase is interposed between the chemically
dissimilar phases to preclude interaction of said active phases while contained within
the antiperspirant applicator, a transverse section across said active and barrier
phases defining an application surface to be rubbed across a skin surface to provide
antiperspirant protection thereto, and each of said active and barrier phases being
compounded and arranged to provide substantially equal shear rates so that they wear
at approximately the same rate during rubbing of the application surface across the
skin being treated, thereby reducing undesirable phase protrusion as the stick is
worn away inward of the application surface during use.
1. Composition anti-transpirante sous la forme d'un applicateur multi-phase comprenant
notamment une phase anti-transpirante et une phase gel, caractérisée en ce que la
composition est constituée de:
A) 35 à 65% en poids de la composition de la phase anti-transpirante qui comprend
un véhicule solide, cisaillable, contenant une substance anti-transpirante astringente;
B) 35 à 65% en poids de la composition de la phase gel qui comprend:
1. de 10 à 92% en poids de la phase gel d'un polyalcool aliphatique contenant 2 ou
3 atomes de carbone et 2 ou 3 groupes hydroxy; et
II. de 5 à 15% en poids de la phase gel d'un agent de formation de gel, choisi parmi
les sels de sodium et de potassium d'acides gras contenant de 14 à 18 atomes de carbone;
et
C) 1 à 10% en poids de la composition d'une phase barrière intermédiaire, contiguë
à la phase gel et à la phase anti-transpirante, où la phase barrière a une épaisseur
d'au moins 0,127 mm et comprend:
I. de 10 à 40% en poids de la phase barrière d'une cire ou d'un mélange de cires à
point de fusion élevé, insoluble dans les alcools, ayant un point de fusion compris
entre 65,6 et 102 °C; et I1. de 20 à 90% en poids de la phase barrière d'un émollient
organique liquide, insoluble dans l'eau, et où la phase barrière ne contient pas plus
de 0,01% de substances particulaires ayant une granulométrie supérieure à 1 micron
et ne réduit pas le pH de la phase gel en-dessous de 9,5 dans la région de l'interface
gel/barrière.
2. Applicateur selon la revendication 1, caractérisé en ce que la phase anti-transpirante
comprend:
I. de 2 à 15% en poids de la phase anti-transpirante d'une cire ou d'un mélange de
cires à point de fusion élevé, insoluble dans l'eau, ayant un point de fusion compris
entre 65,5 et 102°C;
II. de 20 à 50% en poids de la phase anti-transpirante d'un émollient organique liquide,
insoluble dans l'eau, et
III. de 11 à 50% en poids, par rapport à la phase anti-transpirante anhydre, d'une
substance anti-transpirante, astringente, solide, particulaire; et en ce que la phase
gel contient en outre de 10 à 72% en poids de la phase gel d'un monoalcool choisi
parmi le méthanol, l'éthanol, l'isopropanol, et le n-propanol et où le rapport pondéral
du polyalcool à l'agent de formation de gel dans la phase gel dépasse environ 2,45.
3. Applicateur selon la revendication 2, caractérisé en ce que:
(1) la cire à point de fusion élevé représente de 3 à 1% en poids de la phase anti-transpirante
et est choisie parmi la cire d'abeilles, la cire de carnauba, la cire du cirier, la
cire de candelilla, la cire de montan, l'ozokérite, la cérésine, la paraffine, les
cires de Fisher-Tropsch, les cires microcristallines et leurs mélanges:
(2) l'émollient organique représente de 30 à 40% en poids de la phase anti-transpirante
et est choisi parmi le myristate d'isopropyle, le palmitate d'isopropyle, l'acétate
de cétyle, le propionate de cétyle, le phtalate de di-n-butyle, le sébacate de diéthyle,
l'adipate de diisopropyle, le phtalate d'éthyl-carbométhyle, le produit de condensation
d'environ 14 moles d'oxyde de propylène avec une mole d'alcool butylique et les polydimé-
thylsiloxanes ayant une viscosité comprise entre 9 et 50 mPa.s à 25°C;
(3) la substance anti-transpirante particulaire représente de 30 à 46% en poids de
la phase anti-transpirante calculé par rapport à un sel métallique anhydre (à l'exclusion
des agents com- plexants) et est choisie parmi:
i) les hydroxyhalogénures d'aluminium de formule empirique Al2(OH)XOy.XH2O où Q est choisi parmi le chlore, le brome et l'iode, x est compris entre 2 et 5
et x+y = 6 et X est compris entre 1 et 6; et
ii) les complexes de zirconium/aluminium/amino acides qui contiennent:
a) une partie d'un composé d'aluminium de formule Al2(OH)6-mQm.Y H20 où Q est choisi parmi le chlore, le brome et l'iode; m est un nombre compris entre
0,8 et 2,0 et Y est compris entre 1 et 6;
b) x parties d'un composé de zirconium de formule ZrO (OH)2-aÛa.n H20 où Q est choisi parmi le chlore, le brome et l'iode, a est compris entre 1 et 2,
n est compris entre 1 et 8 et x est compris entre 0,16 et 1,2; et
c) p parties d'un amino-acide neutre choisi parmi la glycine, le dl-tryptophane, la
dl-phénylaline, la dl-valine, la dl-méthionine et l'alanine, et où p a une valeur
comprise entre 0,06 et 0,53;
(4) le polyalcool aliphatique représente de 15 à 50% en poids de la phase gel et est
choisi parmi l'éthylène glycol, le propylène glycol, le triméthy- lène glycol, et
la glycérine;
(5) le monoalcool représente de 40 à 70% en poids de la phase gel et est l'éthanol
ou l'isopropanol;
(6) la cire de la phase barrière, à point de fusion élevé, insoluble dans les alcools
et insoluble dans l'eau, représente de 20 à 40% en poids de la phase barrière et est
choisie parmi la paraffine, l'ozokérite et la cérésine; et
(7) la phase barrière comprend en outre de 10 à 30% en poids de la phase barrière
d'une cire ou d'un mélange de cires à bas point de fusion, ayant un point de fusion
compris entre 37,8 et 65,5°C.
4. Applicateur selon la revendication 3, caractérisé en ce que la cire à bas point
de fusion est choisie parmi l'alcool cétylique, l'alcool stéary- lique, l'alcool myristylique,
l'alcool laurylique et le monostéarate de glycérol.
5. Applicateur selon l'une quelconque des revendications 1 à 4, caractérisé en ce
que l'agent de formation de gel représente de 7 à 10% en poids de la phase gel et
est choisi parmi le stéarate de sodium, le palmitate de sodium, le myristate de sodium,
le stéarate de potassium et le palmitate de potassium.
6. Applicateur selon l'une quelconque des revendications 1 à 5, caractérisé en ce
que la phase anti-transpirante contient un ou des constituants supplémentaires choisis
parmi:
A) de 2 à 20% en poids de la phase anti-transpirante d'une cire ou d'un mélange de
cires à bas point de fusion, ayant un point de fusion compris entre 37,8 et 65,5 °C;
et
B) de 0,5 à 5% en poids de la phase anti-transpirante d'une charge inerte.
7. Applicateur selon l'une quelconque des revendications 1 à 6, caractérisé en ce
que la phase gel contient un ou des constituants supplémentaires choisis parmi:
A) de 0,1 à 1,0% en poids de la phase gel d'une substance désodorisante; et
B) de 0,1 à 5,0% en poids de la phase gel d'un retardateur d'antisynérèse/évaporation
choisi parmi les carboxyalkylcelluloses et les hydroxyalkylcelluloses.
8. Applicateur selon l'une quelconque des revendications 1 à 7, caractérisé en ce
que la phase anti-transpirante forme un noyau d'un baton à trois phases, la phase
barrière forme un manchon entourant le noyau et la forme gel forme une enveloppe entourant
la phase barrière.
9. Applicateur selon la revendication 8, caractérisé en ce que la phase barrière a
une épaisseur comprise entre 0,25 et 1,02 mm.
10. Applicateur anti-transpirant à utiliser par frottement, comprenant plusieurs phases
actives de composition chimique différente, caractérisé en ce qu'une phase barrière
est interposée entre les phases de composition chimique différente pour empêcher l'intéraction
desdites phases actives contenues dans l'applicateur anti-transpirant, une section
transversale des phases actives et barrière définissant une surface d'application
à frotter sur la surface de la peau pour fournir une protection contre la transpiration
sur ladite peau et chacune des phases actives et barrière étant composée et disposée
pour fournir des vitesses de cisaillement égales pour faire en sorte que leur usure
soit approximativement la même pendant le frottement de la surface d'application sur
la peau à traiter, d'où une diminution d'une saillie indésirable d'une des phases
au cours de l'usure du baton à l'intérieur de la surface d'application au cours de
l'utilisation.
1. Antiperspirationsmittel in Form eines Mehrphasen-Applikators mit einer Antiperspirationsphase
und einer Gelphase, dadurch gekennzeichnet, dass das Mittel enthält:
A) 35% bis 65% des Gewichts des Mittels an Antiperspirationsphase, die einen festen
scherfähigen Träger umfasst, der ein adstringierendes Antiperspirationsmittel enthält,
B) 35% bis 65% des Gewichts des Mittels an Gel- phase, die umfasst:
1. 10% bis 92% des Gewichts der Gelphase an mehrwertigem aliphatischem Alkohol, der
2 oder 3 Kohlenstoffatome und 2 oder 3 Hydroxylgruppen enthält;
II. 5% bis 15% des Gewichts der Gelphase an Gelbildungsmittel gewählt aus den Natrium-
und Kaliumsalzen von Fettsäuren, die 14 bis 18 Kohlenstoffatome enthalten; und
C) 1% bis 10% des Gewichts des Mittels an zwischenliegender Sperrphase angrenzend
an die Gelphase und an die Antiperspirationsphase, wobei die Sperrphase eine Dicke
von mindestens 0,127 mm hat und umfasst:
I. 10% bis 40% des Gewichts der Sperrphase an wasserunlöslichem, alkoholunlöslichem
hochschmelzendem Wachs oder Wachsgemisch mit einem Schmelzpunkt von 65,6°C bis 102°C,
und
11. 20% bis 90% des Gewichts der Sperrphase an einem wasserunlöslichen flüssigen organischen
Emolliens
und wobei die Sperrphase nicht mehr als 0,01% teilchenförmige Stoffe mit einer Teilchengrösse
von mehr als 1 Mikron enthält und das pH der Gelphase im Bereich der Gel/Sperre-Grenzfläche
nicht unter pH 9,5 vermindert.
2. Applikator nach Anspruch 1, dadurch gekennzeichnet, dass die Antiperspirationsphase
enthält:
I. 2% bis 15% des Gewichts der Antiperspirationsphase an wasserunlöslichem hochschmelzendem
Wachs oder Wachsgemisch mit einem Schmelzpunkt von 65,5°C bis 102°C;
1.20% bis 50% des Gewichts der Antiperspirationsphase an wasserunlöslichem flüssigem
organischem Emolliens, und
11.11% bis 50% des Gewichts der Antiperspirationsphase auf wasserfreier Basis an festem
teilchenförmigem adstringierendem Antiperspirationsmaterial
und dadurch, dass die Gelphase ausserdem 10% bis 72% des Gewichts der Gelphase an
einwertigem Alkohol gewählt aus der Gruppe bestehend aus Methanol, Ethanol, Isopropanol
und n-Propanol enthält, und wobei das Gewichtsverhältnis von mehrwertigem Alkohol
zu Gelbildungsmittel in der Gelphase grösser als etwa 2,45 ist.
3. Applikator nach Anspruch 2, dadurch gekennzeichnet, dass
(1) das hochschmelzende Wachs 3% bis 11% des Gewichts der Antiperspirationsphase ausmacht
und gewählt ist aus der Gruppe bestehend aus Bienenwachs, Carnaubawachs, Bayberrywachs,
Candellilawachs, Montanwachs, Ozokerit, Ceresin, Paraffin, Fisher-Trophsch-Wachse,
mikrokristalline Wachse und Mischungen hiervon;
(2) das organische Emolliens 30% bis 40% des Gewichts der Antiperspirationsphase ausmacht
und gewählt ist aus der Gruppe bestehend aus Isopropylmyristat, Isopropylpalmitat,
Cetylacetat, Cetylpropionat, Di-n-butylphthalat, Diethylsebacat, Diisopropyladipat,
Ethylcarbomethylphthalat, Kondensat aus etwa 14 Mol Propylenoxid mit 1 Mol Butylalkohol
und Polydimethylsiloxane mit einer Viskosität von 9 bis 50 cs. bei 25°C;
(3) das teilchenförmige Antiperspirationsmaterial 30% bis 46% des Gewichts der Antiperspirationsphase
an einer wasserfreien Metallsalzbasis (unter Ausschluss von Komplexierungsmitteln)
enthält, die gewählt ist aus der Gruppe bestehend aus:
i) Aluminiumhydroxyhalogeniden der Summenformel AI2(OH)xQy.XH20, worin Q gewählt ist aus der Gruppe bestehend aus Chlor, Brom und Jod, worin X 2
bis 5 und x+y = 6 ist und worin X 1 bis 6 ist; und
ii) Zirconium/Aluminium/Aminosäurekomplexen enthaltend
a) ein Teil einer Aluminiumverbindung der Formel Al2(OH)6-mQm.YH20, worin Q gewählt ist aus der Gruppe bestehend aus Chlorid, Bromid und Jodid; m ist
eine Zahl von 0,8 bis 2,0 und Y ist 1 bis 6;
b) x Teile einer Zirconiumverbindung der Formel Zr0(OH)2-aQa·nH2O, worin Q gewählt ist aus der Gruppe bestehend aus Chlorid, Bromid und Jodid; worin
a 1 bis 2 ist, worin n 1 bis 8 ist und worin x 0,16 bis 1,2 ist; und
c) p Teile neutrale Aminosäure gewählt aus der Gruppe bestehend aus Glycin, dl-Tryptophan,
dl-Phenylalanin, dl-Valin, dl-Methionin und Alanin, und worin p einen Wert von 0,06
bis 0,53 hat;
(4) der mehrwertige aliphatische Alkohol 15% bis 50% des Gewichts der Gelphase ausmacht
und gewählt ist aus der Gruppe bestehend aus Ethylenglycol, Propylenglycol, Trimethylenglycol
und Glycerin;
(5) der einwertige Alkohol 40% bis 70% des Gewichts der Gelphase ausmacht und Ethanol
oder Isopropanol ist;
(6) das wasserunlösliche, alkoholunlösliche, hochschmelzende Wachs der Sperrphase
20% bis 40% des Gewichts der Sperrphase ausmacht und gewählt ist aus der Gruppe bestehend
aus Paraffin, Ozokerit und Ceresin; und
(7) die Sperrphase weiterhin 10% bis 30% des Gewichts der Sperrphase an tiefschmelzendem
Wachs oder Wachsgemisch mit einem Schmelzpunkt von 37,8 °C bis 65,5 °C enthält.
4. Applikator nach Anspruch 3, dadurch gekennzeichnet, dass das tiefschmelzende Wachs
gewählt ist aus der Gruppe bestehend aus Cetylalkohol, Stearylalkohol, Myristylalkohol,
Laurylalkohol und Glycerinmonostearat.
5. Applikator nach einem der Ansprüche 1-4, dadurch gekennzeichnet, dass das Gelbildungsmittel
7% bis 10% des Gewichts der Gelphase ausmacht und gewählt ist aus der Gruppe bestehend
aus Natriumstearat, Natriumpalmitat, Natriummyristat, Kaliumstearat und Kaliumpalmitat.
6. Applikator nach einem der Ansprüche 1-5, dadurch gekennzeichnet, dass die Antiperspirationsphase
zusätzliche Komponente oder Komponenten enthält, die gewählt ist bzw. sind aus
A) 2% bis 20% des Gewichts der Antiperspirationsphase an einem tiefschmelzenden Wachs
oder Wachsgemisch mit einem Schmelzpunkt von 37,8°C bis 65,5°C, und
B) 0,5 bis 5% des Gewichts der Antiperspirationsphase an einem inerten Füllstoff.
7. Applikator nach einem der Ansprüche 1-6, dadurch gekennzeichnet, dass die Gelphase
zusätzliche Komponente oder Komponenten enthält, die gewählt ist bzw. sind aus:
A) 0,1% bis 1,0% des Gewichts der Gelphase an einem Deodoransstoff; und
B) 0,1% bis 5,0% des Gewichts der Gelphase an einem Antisynerese/Verdampfungsverzögerer
gewählt aus der Gruppe bestehend aus Carboxyalkylcellulosen und Hydroxyalkylcellulosen.
8. Applikator nach einem der Ansprüche 1-7, dadurch gekennzeichnet, dass die Antiperspirationsphase
einen Kern eines dreiphasigen Stiftes bildet, wobei die Sperrphase eine den Kern umgebende
Hülle und die Gelphase eine die Sperrphase umgebende Hülse bildet.
9. Applikator nach Anspruch 8, dadurch gekennzeichnet, dass die Sperrphase eine Dicke
von 0,25 mm bis 1,02 mm hat.
10. Aufreibe-Antiperspirationsapplikator mit einer Mehrzahl von chemisch unterschiedlichen
aktiven Phasen, dadurch gekennzeichnet, dass zwischen den chemisch unterschiedlichen
Phasen eine sperrende Phase liegt, um Wechselwirkungen zwischen den aktiven Phasen
auszuschliessen, während sich diese im Antiperspirationsapplikator befinden, wobei
ein Querschnitt durch die aktiven und sperrenden Phasen eine Applikationsoberfläche
zum Aufreiben auf die Haut definiert, um dieser einen Antiperspirationsschutz zu verleihen,
und wobei jede der aktiven und sperrenden Phasen zusammengesetzt und angeordnet ist,
um praktisch gleiche Scherraten zu bieten, so dass sie sich während des Reibens der
Applikationsoberfläche über die behandelte Haut mit annähernd gleicher Rate abnützen,
wodurch unerwünschtes Herausragen der Phasen bei Abnützung des Stiftes von der Applikationsoberfläche
nach innen während der Verwendung vermindert wird.