[0001] The invention relates to a thermoplastic elastomeric composition obtained by mixing
a powdered vulcanized rubber, a thermoplastic polymer and an additive.
[0002] Society is to a growing degree confronted with the desirability of recovering waste
products and converting them to a form suitable for reuse. The major reasons for this
are the increasingly heavy burden on the natural environment and the decreasing availability
of raw materials.
[0003] A particularly relevant example is the situation concerning waste vulcanized rubber
products, in particular used pneumatic tyres, which are turned out in great quantities
and cannot in general be rendered suitable for reuse without fairly intensive preliminary
treatment. For this reason, methods have long been sought in all quarters to utilize
these products in such a way that an optimum is obtained between as low as possible
processing costs on the one hand and a w technical application of the highest possible
quality on the other. A very suitable application for vulcanized rubber from waste
products is as a filler in polymers, particularly thermoplastic polymers, whereby
the cost price of the plastic is reduced and a modified property configuration is
obtained. For this purpose, little more has to be dbne than reduce the vulcanized
rubber to a state such that it can be mixed with the thermoplastic polymer, e.g. by
cutting or grinding.
[0004] A crucial problem in preparing mixtures based on a vulcanized rubber and a thermoplastic
polymer is the bonding between the two components, however. If there is insufficient
bonding between the rubber particles and the polymer phase, porosity and poor mechanical
properties result, which is for many applications very undesirable.
[0005] In U.S. Patent 4028288 a method is described for controlling the porosity of mixtures
of - comparatively coarse - vulcanized rubber particles and a thermoplastic polymer
by varying the relative quantity of rubber and the dimensions of the rubber particles.
A disadvantage of this method is that a very low degree of porosity cannot thus be
achieved at a somewhat higher rubber content, so that the properties of such mixtures
will not have much scope for variation and these mixtures will not be suitable for
a large number of applications.
[0006] The problem of proper bonding between vulcanized rubber particles and thermoplastic
phase is admitted in German Offenlegungsschrift 2408690, in which the preparation
is described of a thermoplastic material based on rubber particles and a minor quantity,
viz. less than 40 wt. %, preferably less than 30 wt. %, of a 'selected' thermoplastic
polymer as a binder. For this purpose, the two components are chosen such that they
differ, in terms of solubility parameter, by less than 1, preferably less than 0.5
units, from one another. A disadvantage of this method is that in many cases .the
solubility parameter must be determined for each charge of vulcanized rubber and thermoplastic
polymer and a restriction must be accepted as regards the possibilities for combining
the two basic constituents. As will be shown in a comparative example below, products
with inferior properties are obtained by the method according to the Offenlegungsschrift
mentioned.
[0007] In Netherlands Patent Specification 7806735 a method is revealed for the preparation
of products from recycled rubber and a thermoplastic or elastomeric polymer, characterized
in that an additive is supplied consisting of 0.1-10 wt.% of a plasticizing agent
and/or lubricant and 0.1-10 wt. % of a curing agent, both calculated relative to the
total mixture. As a plasticizing and/or lubricating agent (waste) oil is specifically
mentioned. A major advantage of this method is found to be its potential for regulating
the porosity of the final products; in particular, the manufacture is described of
porous drainage tubing using a mixture of 70-75 parts by wt. of rubber powder and
30-25 parts by wt. of polyethylene, in addition to 1 part by wt. of lubricant plus
sulphur. The vulcanization of the mixtures, which is inherent to the method, will
render the method more costly and more critical in its application , however.
[0008] It has now been found to be possible to prepare a thermoplastic elastomeric composition
from a vulcanized rubber and a thermoplastic polymer, which composition possesses
a very low level of porosity and improved mechanical characteristics, in particular
superior thoughness.
[0009] The thermoplastic elastomeric composition according to the invention, composed of
powdered vulcanized rubber, thermoplastic polymer and an additive is now characterized
in that it contains: a powdered adverse effect on their appearance. The powder can
be dried by treating with hot air for several hours, for example at a temperature
of 50-150 C for 1-12 hours. A particular advantage of the invention is that the use
of a non-ionic surfactant during the mixing of the components renders it easier to
remove any moisture still remaining.
[0010] The thermoplastic olefin or diolefin polymer may be constituted of ethylene, propylene,
butylene, butadiene or isoprene or of a mixture of these, or it may be a copolymer
of ethylene, propylene, butylene, optionally hydrogenated butadiene or isoprene with
less than 50 wt.% of one or more other monomers, such as other olefins or styrene.
Polyethylene is to be preferred, optionally mixed with minor quantities of one or
more other polymers. These thermoplastic polymers are also very suitable in the form
of waste material, such as is turned out in tneir normal processing.
[0011] In the composition according to the invention the powdered vulcanized rubber and
the thermoplastic polymer are present in a ratio of from 1 : 3 to 3 : 1 by weight.
At lower weight ratios not enough of an economic benefit can be attained and to rigid
a material is obtained for many applications. A higher ratio by weight reduces the
tensile strength of the composition excessively in relation to the tensile strength
the pure thermoplastic polymer will possess. If a non-ionic surfactant is used, it
is found that the toughness of the composition increases with an increasing quantity
of rubber powder, in contrast with the result obtained with application of ionic surfactants.
The composition according to the invention preferably contains the powdered vulcanized
rubber having a mean particle size of below 1.5 mm and the thermoplastic olefin or
diolefin polymer, in a weight ratio of from 1 : 2 to 2 : 1, more specifically of from
2 : 3 to 3 : 2.
[0012] The. thermoplastic composition according to the invention can be prepared by mixing
the powdered vulcanized rubber, the thermoplastic polymer and the non-ionic surfactant
under shearing forces in a conventional mixing device, e.g. in a Banbury kneader mixer
or on the rolls, until a homogeneous mixture is obtained. This is preferably carried
out a temperature above the processing temperature or melting point of the thermoplastic
polymer, for example at a temperature of from 100 °C to 250 °C, in particular from
130 °C to 200 °C. It is strongly recommended not to choose too high a temperature,
because at higher vulcanized rubber having a mean particle size of below 1.5 mm and
a thermoplastic olefin or diolefin polymer, the weight ratio of rubber and thermoplastic
polymer being from 1 : 3 to 3 : 1, and 0.1-5 wt.% calculated relative to the total
quantity of the other components, of a non-ionic surfactant.
[0013] The non-ionic surfactant is added in a quantity of 0.1-5 parts by wt. In a lower
quantity it is insufficiently active in the mixture, while at more than 5 parts by
wt. per 100 parts by wt. of the other components the sensitivity to water of the material
obtained rises sharply, rendering it less suitable for applications outside. The best
results are obtained at a quantity of 0.5-2.5 part by wt. of the non-ionic surfactant.
[0014] Very suitable non-ionic surfactants are the reaction products of a hydroxyl compound
with one or more units of an alkene oxide, in particular ethylene oxide and/or propylene
oxide, 1-500 alkene oxide units being present in the molecule, preferably 10-100 units.
Suitable hydroxyl compounds are alcohols for example, preferably alcohols with 4-18
carbon atoms per molecule, phenols or other compounds containing hydroxyl groups such
as fatty acids or partially hydrolyzed oils and fats. The phenols represent an important
group herein, preferably the mono- or polyalkyl-substituted phenols. The alkyl groups
preferably contain 1-12 carbon atoms per group. Examples of especially suitable non-ionic
surfactants are the reaction products of octyl or nonyl phenol and ethylene oxide.
Suitable non-ionic surfactants are the block copolymers of ethylene oxide and propylene
oxide with terminal OH groups, preferably those containing 60-90 wt. ethylene oxide.
A third group of suitable compcunds are polar vinyl polymers, e.g. polyvinyl pyridine,
polyvinyl pyrrolidone, polyvinyl alcohol and cellulose derivatives, e.g. carboxymethylcellulose
(CMC).
[0015] The powdered rubber preferably has a mean particle size of between 90 u m and 1200
µm and more particularly a median value of between 300 u m and 800 u m. The rubber
is, for instance, taken from pneumatic tyres, in particular from tyres of passenger
cars, and can be reduced to the above dimensions by grinding - preferably cryogenically.
For some applications it is advisable to use the tread material of the tyres, as this
contains relatively little canvas. The powder is preferably freed of ferrous constituents
and moisture. The moisture present in the powder increases the porosity of the products
formed and has, moreover, an temperatures a pronounced generation of odour and gas
may appear. Moreover, the products from compositions thus obtained will give off an
obnoxious smell during a long time after moulding. I is also possible to mix the powdered
rubber and the thermoplastic polymer in the method described above, the non-ionic
surfactant being added subsequently, to the mass, preferably in a molten form. The
whole mass is then blended without kneading for some time, for instance 5-50 min.,
in a rolling drum or paddle mixer. Provided the thermoplastic polymer is present in
an appropriate form, for example in particle form, simple mixing without kneading
all components may be sufficient for some purposes.
[0016] A variety of additives can be incorporated in the thermoplastic elastomeric composition
according to the invention, e.g. regenerated rubber, lubricants, carbon black, oil,
anti-oxidants, stabilizers, flame retardants, etc. Surprisingly, it has been found
that the composition is readily colourable, for instance by the addition of pigments,
despite the considerably quantity of carbon black generally present in the rubber
powder employed.
[0017] The thermoplastic elastomeric composition can be moulded by extrusion or injection
moulding or by another method to a variety of products with a wide range of applications.
Possible applications include extruded sealing profiles, roofing, floor coverings
for sheds, fencing posts, sleepers, pallets, etc., as well as shoe soles, saddle covers,
anti-skid ladder supports, mud flaps, solid tyres, sprinkling funnels, etc.
[0018] The invention is further elucidated with reference to the following examples and
comparative examples.
Examples I-III
[0019] In a heated 3anbury mixer homogeneous mixtures were prepared from high-density polyethylene
(STAMYLAN 8409) and rubber powder by kneading for 5 min. at a temperature varying
from 100 C to 175 °C. The rubber powder was obtained by grinding passenger-car tyres
and consisted substantially of SBR, butadiene rubber and a minor quantity of natural
rubber. The particle size was between 90 µm and 1200 µm, with a median value of 500
µm. The powder was dried for two hours at 80 °C after grinding and then rendered free
of iron with the aid of a magnet. Immediately after mixing in the Banbury mixer a
non-ionic surfactant of the polyethylene-oxide type (CARBOWAX 4000) in the molten
state was added to the hot mixtures. The whole mass was subsequently mixed in a drum
for 15 min.
[0020] Test specimens measuring 50 x 100 mm and 2 mm thickness were then moulded from the
compositions thus obtained in an injection- moulding machine, at a polymer temperature
of about 170 °C and a mould temperature of 50 C. Cycletime was approx. 25 sec.
[0021] The composition (in parts by weight) and the mechanical characteristics, combined
with those of the compounds as per comparative examples A-K, are given in the table
below. The compositions could be processed very well in an extruder. A good quality
tubing could thus be obtained.
Comparative examples A-K
[0022] By the same procedure as in Examples I-III, compositions were prepared in which CARBOWAX
4000 was replaced by an anionic (STRUKTOL W 33) or a cationic (ARQUAD 18) surfactant
or without addition of any surfactant.
[0023] To determine the mechanical characteristics, the test specimens, which were notched
5 mm on both longitudinal sides, were tensioned in a tensile strength tester and extended
to max. 45 % of their original length. During the whole test the tensile force applied
was measured as a function of the elongation.
[0024] The notch energy is defined by force x elongation (integrated over the whole elongation)
nett original cross-sectionel area of the test specimen and expressed in
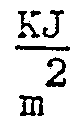
[0025] The specific strain is defined by

and expressed in %.
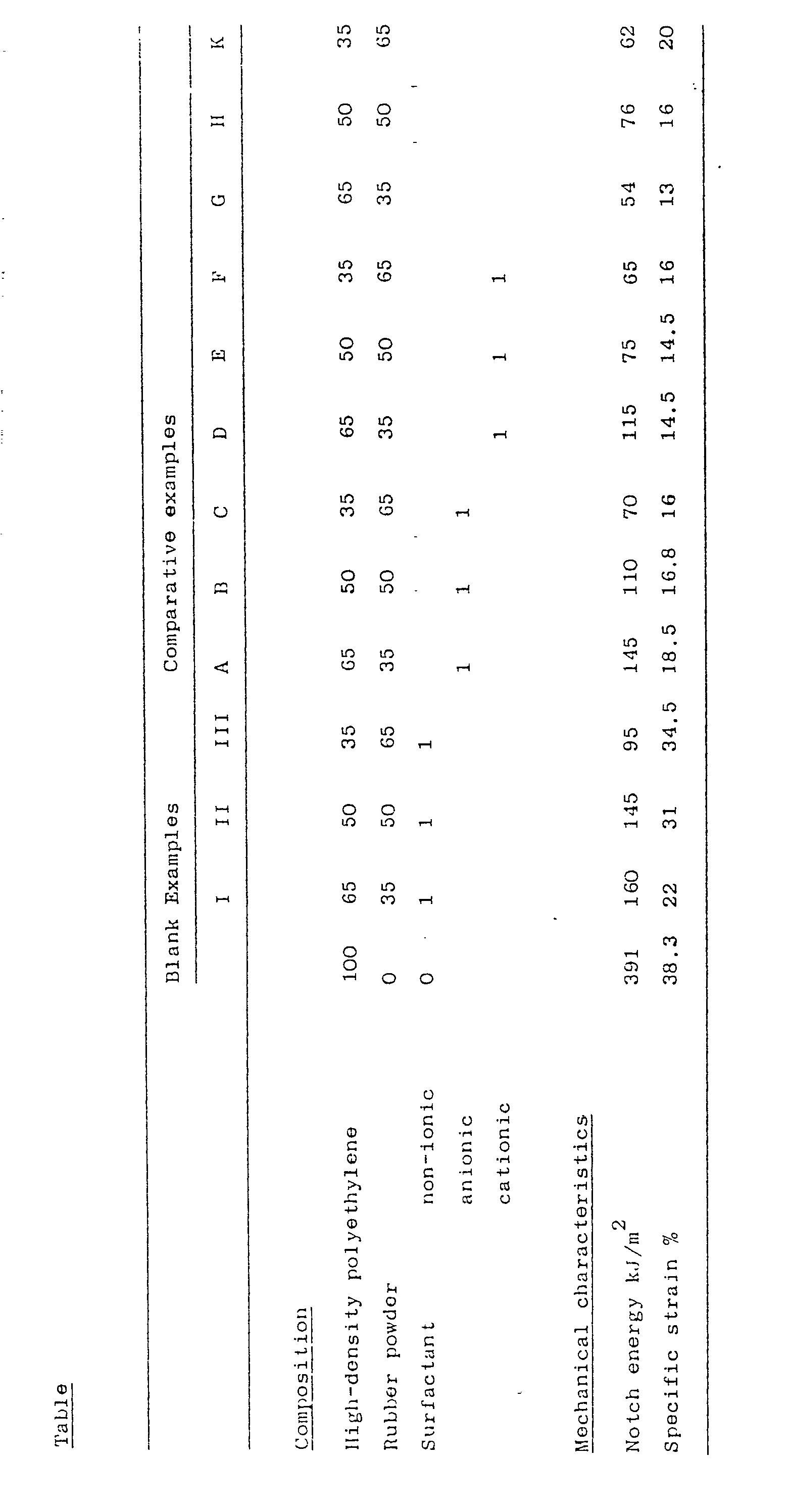
COMPARISON OF NOTCH ENERGY: kJ/m2
[0026] (100 % High density Polyethylene = 391)
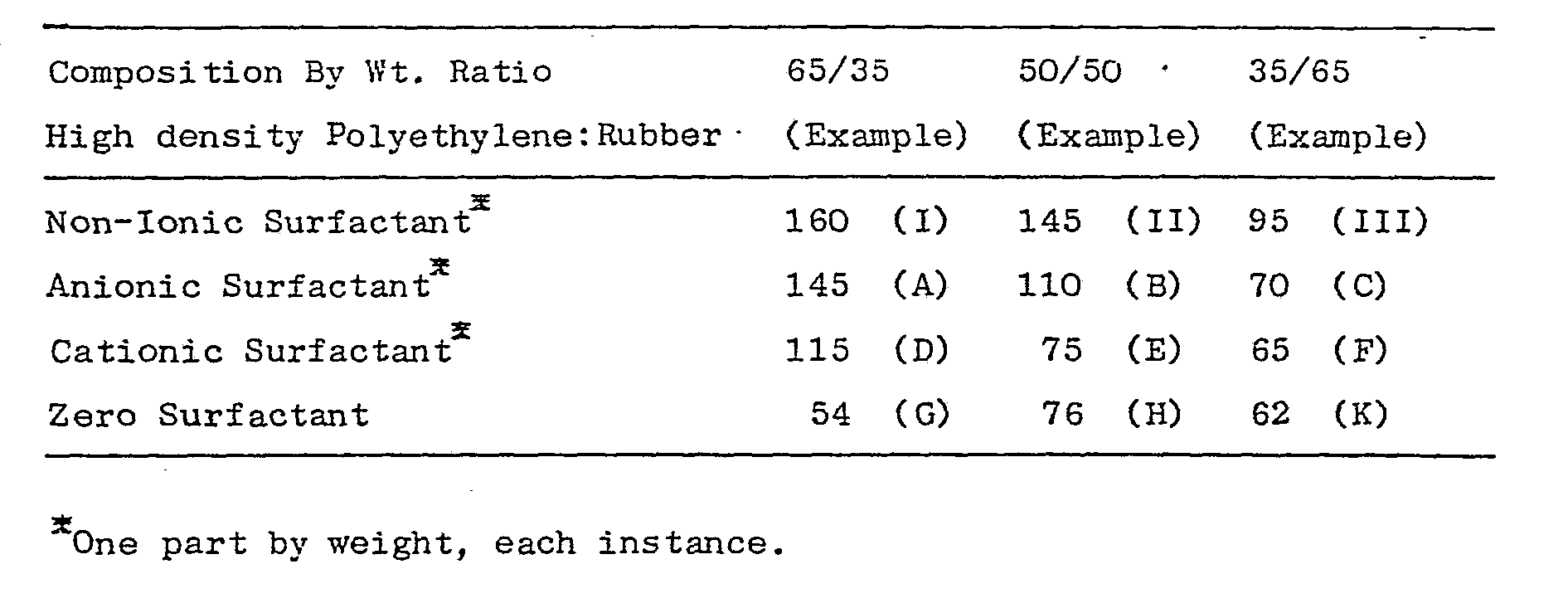
COMPARISON OF SPECIFIC STRAIN, PERCENT
[0027] (100 % High density Polyethvlene = 38.3 %)
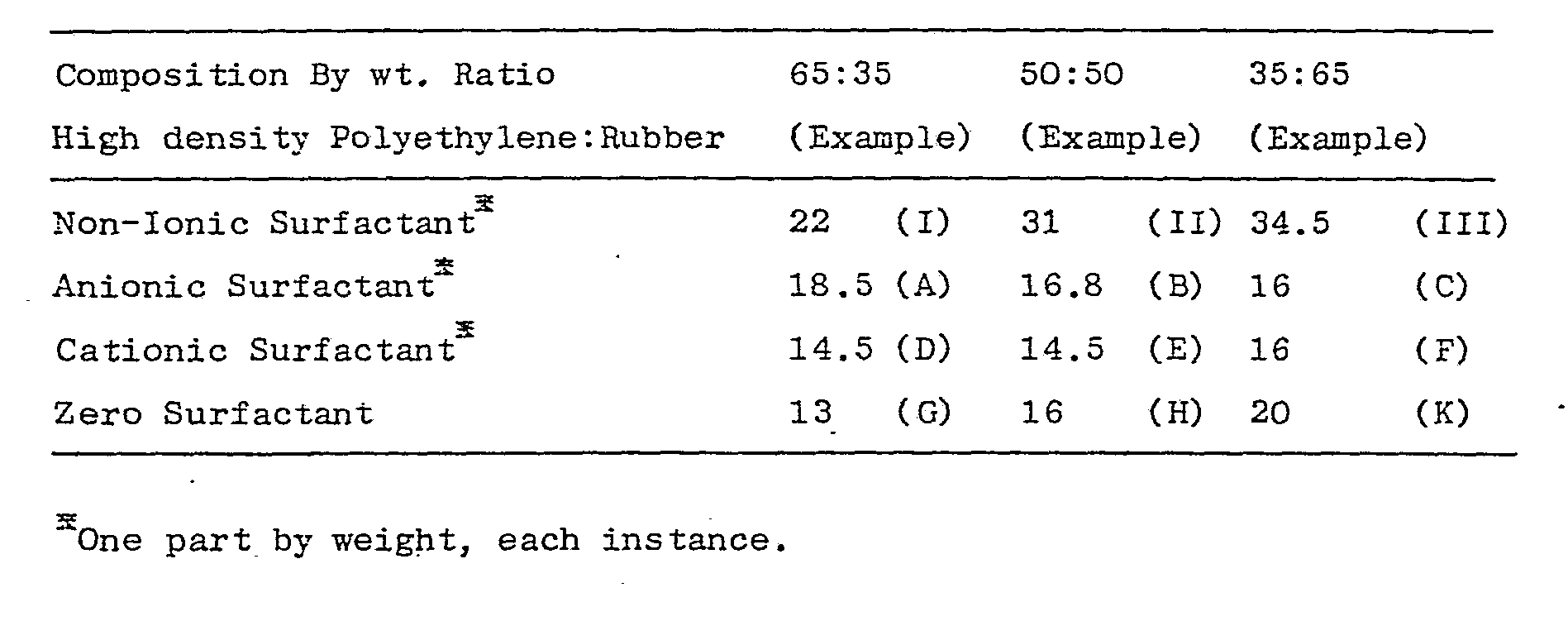
[0028] The results show that the toughness as represented by the specific strain values
is very much improved by the addition of 1 % non-ionic surfactants. The notch energy,
too, is considerably improved in this way.
[0029] In visual evaluation of the test specimens, a sharp decrease in the degree of porosity
is observed if 1 % non-ionic surfactant is added; this is observed less clearly if
the other two surfactants are added.
Example IV
[0030] By the same procedure as in Examples I-III compositions were prepared using thermoplastic
elastomers on a polyolefin basis as well as based on block copolymers of butadiene
and styrene (KELTAN TP 0300, KELTAN TP 0500 and CARIFLEX 4113, respectively), with
rubber powder contents of 50 to 70 wt.%. Here, too, a sharply decreased porosity was
observed if 1 % non-ionic surfactant was added.
Example V
[0031] Mixtures having the same composition as in Example IV were 0 prepared, but now by
mixing on heated rollers (at 140-160 C) instead of in a Banbury mixer. Very much improved
rolling behaviour was here observed when 1 wt. % non-ionic surfactant was added. A
coherent rolled sheet was more rapidly formed.
Comparative example L
[0032] A mixture of high-density polyethylene and undried rubber powder in a 1 : 1 weight
ratio was prepared in a Banbury mixer and then moulded to test specimens in accordance
with Example 1 of German Offenlegungsschrift 2408690. It was found that this mixture
gave off a considerable odour during processing and caused a white deposit on the
mould wall during injection moulding. The surface of the specimens was patchy.
Comparative example M
[0033] A mixture of polyvinyl chloride (PVC) and dried rubber powder in a 1 : 1 weight ratio
was prepared in a Banbury mixer. I was found to be impossible to extrude this mixture
to coherent tubing even at temperatures o to 200 C. The melt was too incoherent for
this purpose. The rubber particles were not well enclosed by the PVC, causing the
surface to remain rough ( the composition resembled coarse sandpaper). The pieces
of tubing possessed virtually no mechanical strength.
Examnles VI and VII
[0034] By the same procedure as in Example I-III compositions were prepared, however with
0.3 wt. % Carbowax 4000. The rubber particles were made from tread component material
of tires and had a low fiber and cord content. Articles with reduced porosity could
be injection moulded which were acceptable for certain applications such as mud flaps.
[0035] If these mixtures were made with 4.5 wt. % Carbowax 4000 no porosity could be observed.
However the surface was greasy and the yield on extruding was significantly lower.
Thermoplastic elastomeric composition prepared-from a powdered vulcanized rubber,
a thermoplastic polymer and_an additive, characterized in that the thermoplastic elastomeric
composition contains: a powdered vulcanized rubber having a mean particle size of
below 1.5 mm and a thermoplastic olefin or diolefin polymer, the weight ratio of rubber
and thermoplastic polymer being from 1 : 3 to 3 : 1, and 0.1-5 wt. %, calculated relative to the total quantity of the other
components, of a non-ionic surfactant.
Thermoplastic elastomeric composition according to Claim 1, characterized in that
the composition contains 0.5 - 2.5 wt. %, calculated relative to the total quantity
of the other components, of the non-ionic surfactant.
Thermoplastic elastomeric composition according to Claim 1 or 2, characterized in
that the reaction product of a hydroxyl compound with 1-500 units of an alkene oxide
is applied as a non-ionic surfactant.
Thermoplastic elastomeric composition according to Claim 3, characterized in that
the reaction product of a phenol with one or more alkyl groups having 1-12 carbon
atoms and 1-500 ethylene oxide units is applied as a non-ionic surfactant.
Thermoplastic elastomeric composition according to any of Claims 1-4, characterized
in that the weight ratio of rubber and thermoplastic polymer is from 1 : 2 to 2 : 1.
Thermoplastic elastomeric composition according to Claim 5, characterized in that
the weight ratio of rubber and thermoplastic polymer is from 2 : 3 to 3 : 2.
Thermoplastic elastomeric composition according to any of Claims 1-6, characterized
in that the powdered vulcanized rubber having a mean particle size of below 1.5 mm
is obtained by grinding pneumatic tyres, with subsequent removal of ferrous constituents
and drying.
Thermoplastic elastomeric composition according to any of Claims 1-7, characterized
in that the thermoplastic olefin or diolefin polymer is constituted of ethylene, propylene,
butylene, butadiene, isoprene, or mixtures of these, or it is a copolymer of ethylene,
propylene, butylene, optionally hydrogenated butadiene or isoprene with less than
50 wt. % of one or more other monomers, such as other olefins or styrene.
9. Thermoplastic elastomeric composition according to Claim 8, characterized in that
the thermoplastic olefin or diolefin polymer is polyethylene.
10. Thermoplastic elastomeric composition, as is substantially described in the description
and/or the examples.
11. Process for the manufacture of a thermoplastic elastomeric composition according
to any of Claims 1-10, characterized in that the powdered vulcanized rubber is mixed
with the other constituents of the composition at a temperature of below 250 °C.
12. Process according to Claim 11, characterized in that the powdered vulcanized rubber
is mixed with the other constituents of the composition at a temperature of below
200 °C.
13. Process for processing a thermoplastic elastomeric composition according to any
of Claims 1-10 to moulded products by a method known per se, characterized in that
the thermoplastic elastomeric composition is processed at a temperature of below 250
oC.
14. Process according to Claim 13, characterized in that the thermoplastic elastomeric
composition is processed at a temperature of below 200 °C.
15. Articles wholly or partially consisting of a thermoplastic elastomeric composition
according to any of Claims 1-10.