[0001] The present invention relates to a process and apparatus for the calcining of raw
petroleum coke or coal.
[0002] During the refining of petroleum by the various processes of distillation, cracking,
reforming, polymerization, alkylation, and other well-known processes, eventually
a portion remains which is unusable in any other method than thermal cracking, distilling
off the overheads, with the dehydrogenated and polymerized residue precipitating as
petroleum coke. Raw petroleum coke is itself only useful as fuel, but further processed,
its value is increased by calcining to produce the various grades of calcined coke
useful for metals reduction or for further processing to industrial carbon and graphite.
[0003] Raw petroleum coke is an extremely complex mixture of medium to high molecular weight
hydrocarbons, organic sulfur compounds, and other organic derivatives, with a relatively
small proportion of ash.
[0004] Calcination of raw petroleum coke is essentially a process of heating the coke in
a controlled atmosphere with mechanical agitation at temperatures in the range of
1000°-1500°C. During calcination of petroleum coke, lower molecular weight components
are driven off and oxidized, while the higher molecular weight components are dehydrogenated
and molecularly rearranged to polymers of carbon with varying degrees of homogeneity
and crystallinityo
[0005] Calcining is most commonly done in a rotary kiln, which is essentially a steel cylinder,
lined with a refractory and inclined at a small angle from the horizontal. Raw coke
is fed in at the upper end and is gradually heated by a flame from a burner placed
at the lower end, or firing crown. Additional air may also be supplied either through
the firing crown or through tuyeres at the side as in U.S. Patent 4,053,365. Coke
passes from the upper to the lower ends by the tumbling action of the kiln while being
thus heated and calcined.
[0006] In normal operation it has been necessary to supply heat to the kiln from a separate
fuel supply, as the combustion of the volatiles released from the raw coke is incomplete
and the volatiles of insufficient concentration in the kiln atmosphere to support
sufficient combustion to carry out the calcination process.
[0007] The common practice has been for the supply of heat by a burner at the firing crown,
fired either by natural gas or fuel oil, with air, in addition to that mixed with
the fuel in the burner, supplied through the firing crown and tuyeres by blowers.
The air mixed with the fuel is designated primary air and that supplied through the
other blowers to the firing crown and the tuyeres is designated secondary air.
[0008] As the coke is fed into the upper end of the kiln, it starts tumbling and is heated
by the burning of the fuel gas and the volatiles released by coke being heated further
down the kiln. The initial stage of heating first drives off any water retained in
the coke from the cutting operation in the coker drum (in which it is loosened and
removed by high pressure jets) and the water remaining after outdoor storage.
[0009] At about 400°C., organic compounds first start to be distilled off, with molecular
rearrangement anddehydrogena- tion of the residue occurring up to about 900°C. Crystallization
of the coke into its final form then occurs during the last stage with the temperature
rising to 1500°C. These zones overlap as the reactions occurring are of great complexity,
with many variables, and it has not been possible to fully characterize them.
[0010] The normal calcining operation has, in the past, been based on the premise of cheap
raw materials and cheap fuel to operate the kiln. The inflation of oil prices and
of prices of the fuels derived from or competitive with petroleum has changed the
situation to the current one in which the most stringent economies are necessary.
[0011] In normal operation of rotary kilns, it has been necessary in order to maintain production
to supply fuel to the burner with the primary air in order to maintain the temperature
sufficiently high for calcination, while at the same time volatiles are escaping from
the upper end of the kiln and burning in the stack. This is both wasteful of fuel
and coke and a cause of excess air pollution, due to the large volumes of both primary
and secondary air used to oxidize the hydrocarbons driven off and to carry away the
unburned hydrocarbons and oxides formed.
[0012] The current concern over pollution of the environment has, therefore, dictated changes
in the operation and equipment necessary to meet the air quality standards. Past practices
resulted in the emission of large volumes of hydrocarbons, particulates, CO, and nitrogen
oxides. All of these must be limited in order to meet the current and proposed environmental
standards.
[0013] In accordance with the invention there is provided a process of calcining raw petroleum
coke or other carbonaceous material in which the calcining is carried out in air enriched
with a controlled amount of oxygen.
[0014] The invention also provides apparatus for the calcining of petroleum coke or other
carbonaceous material which comprises a rotary kiln equipped with a burner and air
blowers, and including means for injecting oxygen into the atmosphere in said kiln.
[0015] A conventional rotary kiln used for the calcination of petroleum coke or other carbonaceous
matter, such as coal, may be modified to accommodate enrichment of the atmosphere
with oxygen. This modification is preferably accomplished by the addition of an oxygen
injection port to the blower inlet leading to the burner in the firing crown, but
may also be done by adding pure oxygen in a separate injector inlet, or to the tuyere
air inlets.
[0016] The enrichment of the combustion atmosphere by oxygen has the effect that once burning
is established, the external supply of fuel may be cut off and the total heat needed
for combustion is supplied from the oxidation of the volatiles by the enriched atmosphere,
thus lowering the cost of fuel needed for the operation. It is also found that operation
in this manner allows better control of the temperature, more uniformity in the coke
bed temperature, and less total air pollution. Operation in this manner also aids
in desulfurizing the coke.
[0017] Air pollution is lowered by the effect of more nearly complete combustion of the
volatiles distilled off, lessening hydrocarbon emissions. The enrichment of the atmosphere
also reduces the need for air injection through the tuyeres, thus lowering the total
volume of gas emitted and the amounts of nitrogen oxides formed. The enriched atmosphere
also oxidizes the smaller particles, lessening particulate emissions.
[0018] The invention will be described with reference to the accompanying drawings in which:
Figure 1 is a shaking hearth calciner modified in accordance with the invention;
Figure 2 is a graph in which the effect of oxygen enrichment is illustrated in terms
of coke temperature vs. time at the calciner exit and six inches from the exit; and
Figure 3 is a graph showing gas temperature along the length of the kiln material
without oxygen injection.
[0019] The invention is illustrated by the following examples:
EXAMPLE 1
[0020] A test in a shaking hearth calciner 10, as shown in Fig. 1, was run using anthracite
coal with a volatile content of ca. 5%. The oxygen injection nozzle was placed near
the burner end of the calciner at 11. The burner 12 was at the lower exit end 15 of
the calciner, with feed at 13, and coal bed at 14. In this operation, stack dampers
16 and 17 were closed, with air 18 and oxygen 19 supplied through nozzle 11, and exhaust
at 20. The temperature was measured at points 21, 22, 23, 24, 25 and 27.
[0022] After oxygen enrichment was begun at 600 CFH, a rapid increase in gas temperature
in the calciner occurred, as shown in Fig. 3. The exit temperature of the coke product
increased only slightly, while the coke bed temperature further back in the kiln began
to increase rapidly, as shown in Fig. 2. At the same time, fuel consumption was decreasing
at a rate such that 2-1/4 hours after starting oxygen injection the fuel consumption
was about one-half of the original rate (Table lA, Time 1345). The coke bed temperature
had increased to a level greater than the coke exit temperature (Table 1B, Time 1345
and gas temperatures were still rising (Table lC, Time 1345).
[0023] The burner was then shut off (time 1350), and the remaining two hours were run without
external fuel. The product exit temperature decreased slightly, but the coke temperature
6 inches from the exit in the bed increased (Table 1C, Time 1445 and 1545). Fig. 2
shows the changes in coke temperatures at these two points. The hot zone has moved
back to the point of oxygen injection, with the coke cooling over the remainder of
the kiln length.
[0024] This test clearly indicated that oxygen injection could reduce external fuel and
total combustion volume requirements. Fuel free operation was attained, and in order
to reduce the temperature to the normal calcining level, it would have been necessary
to reduce the amount of oxygen enrichment.
[0025] The coke produced was analyzed with results shown in Table 2.
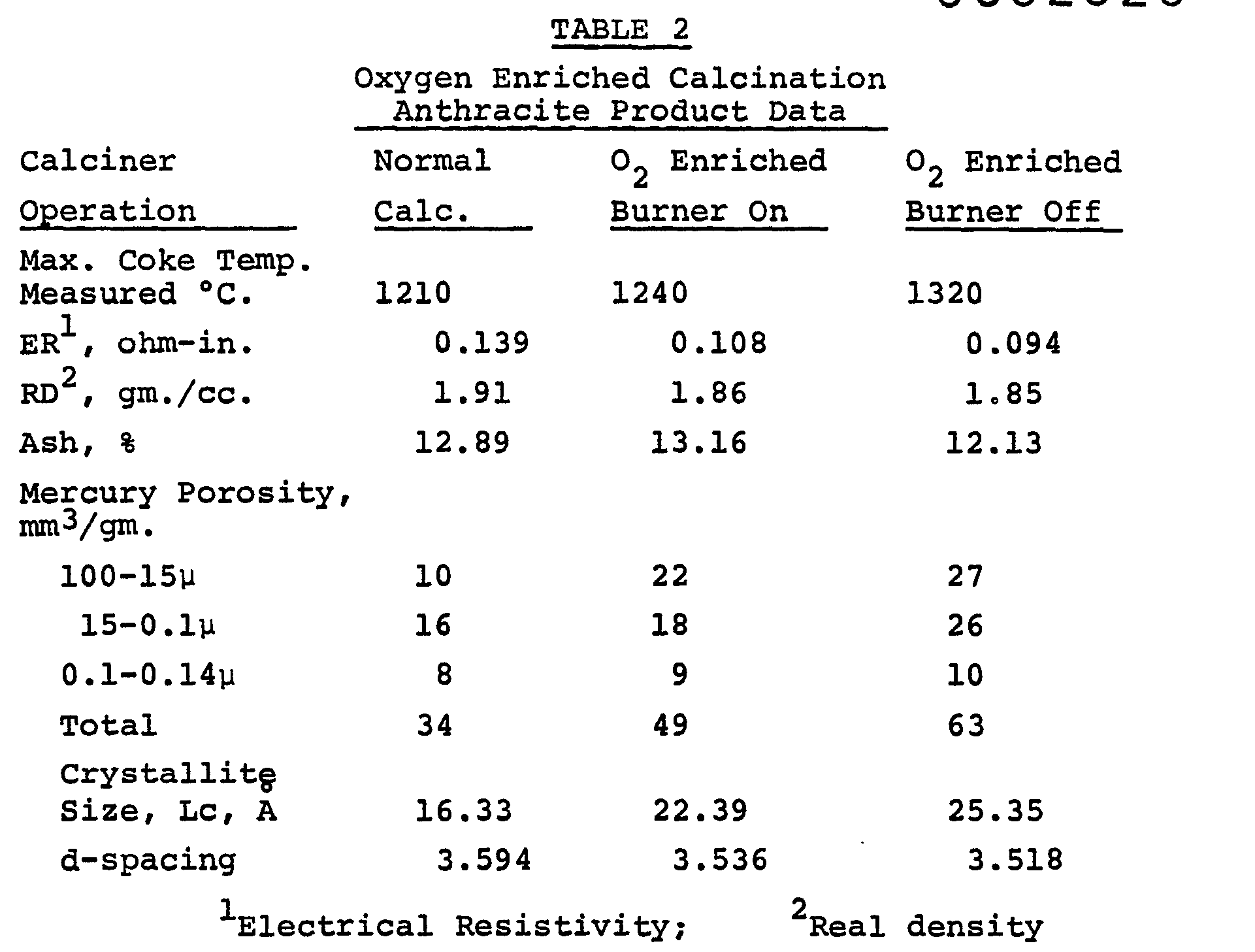
[0026] The decrease in resistivity verifies an increase in the temperature of the coal bed.
Based on comparisons with other coal data, a temperature of 1400°C. was probably reached
at some point in the calciner. This higher temperature is also indicated by the increase
in crystallite size and decrease in d-spacing. Mercury porosity increased, accompanied
by a decrease in density. The similar level of ash indicates that no more coal was
burnt during oxygen-enriched calcination than in normal practice.
EXAMPLE 2
[0027] A test during a normal calcining run was made in a large commercial rotary kiln calciner
using petroleum coke with a volatile content of ca. 11%. The feed rate at normal operating
conditions was ca. 25 tons per hour of coke with a product temperature of ca. 1370°-1400°C.,
with an E.R. of 0.040 ohm-in. and a density of 2.05 g./cc. Properties of this coke
are shown in the last column of Table 3.
[0028] An oxygen injection line was established, with a supply tank and regulator adjacent
to the kiln, leading to the combustion air line immediately downstream of the air
blower. This allowed for mixing of the gases prior to entering the kiln. Combustion
air flow was 4500 SCFM, and this rate was maintained throughout the run.
[0029] At 10:30 a.m., the burner was turned off and O
2 injection into the burner air started and gradually increased up to a rate of 705
C.F.M. at 11:10 a.m., raising the O
2 content of the burner combustion air to ca. 30%. The coke product temperature dropped
when the burner was shut off, but started to rise again when 0
2 injection started. At 11:30 a.m., the coke temperature was 1260°C., analysis confirming
by resistivity and density figures.
[0030] At 11:45 a.m., the injection rate was gradually increased further, reaching 950 C.F.M.
at 12:10 p.m., increasing the 0
2 content of the combustion to ca. 35%. Density and resistivity were unchanged, indicating
that a stable operation had not yet been reached at the higher temperature.
[0031] The product temperature increased to 1400°C., with readings of 1454°-1482° indicated
at a point 20 feet from the end of the kiln by optical pyrometer, although hindered
by flames at the bed surface. Resistivity and density of samples taken at 1:30 and
2:30 are consistent with higher calcining temperatures.
[0032] At 2:35 p.m., the coke feed rate was increased to 30 tons per hour, with the product
temperature lowering to 1370°C. at 3:30 p.m. Product resistivity and density data
do not reflect a temperature decrease, probably because of the lag in attaining stable
operation under the changed condition.
[0033] Analysis of the coke (Table 3) showed that bulk densities indicate no change; sulfur
analysis indicates some additional desulfurization; surface areas show no significant
change; microporosity showed little change; and macroporosity decreased, as a result
of the 0
2 enrichment of the process atmosphere.
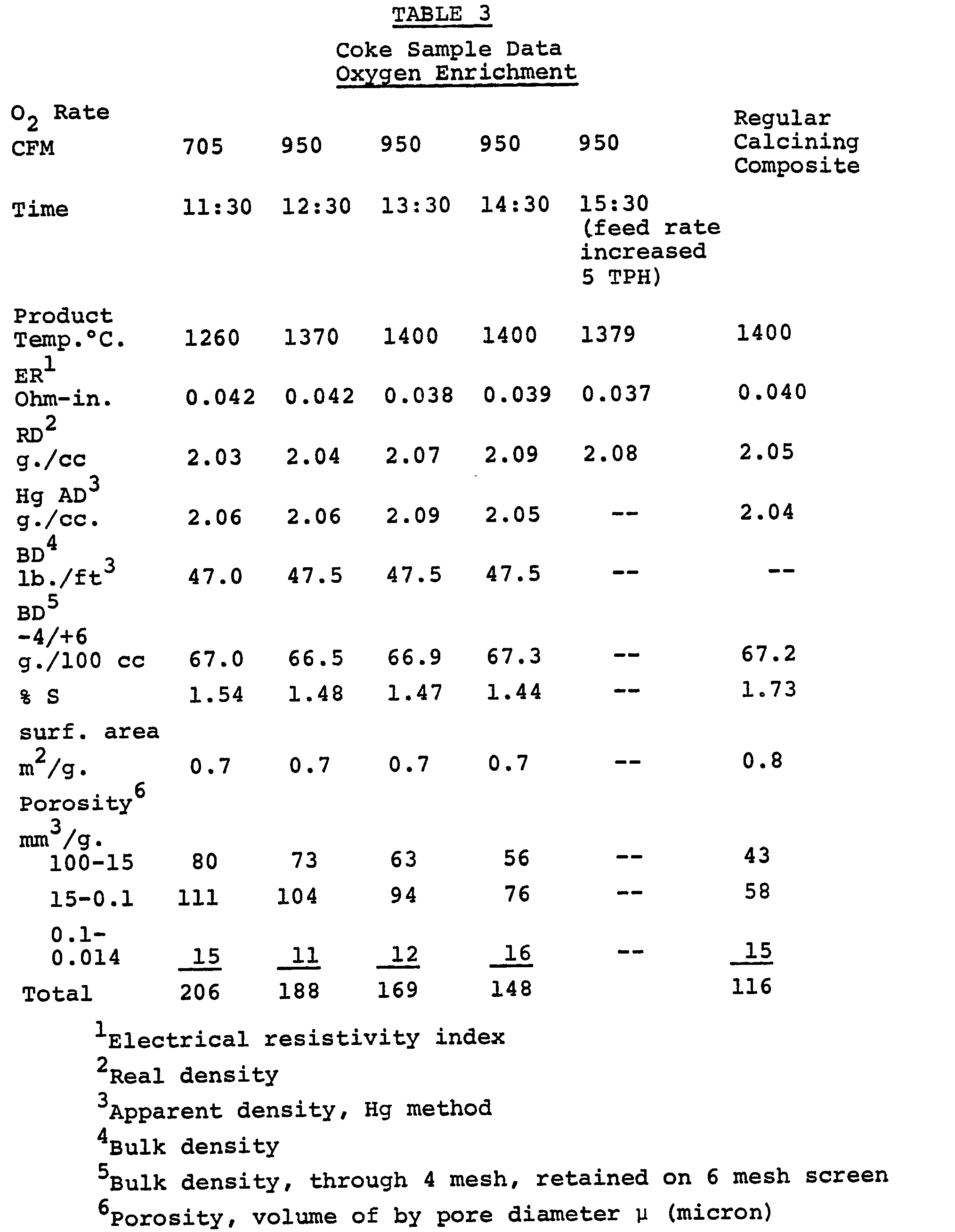
[0034] Based on this text, the use of 0
2 enrichment increased coke quality to a slight degree, principally by improved desulfurization.
[0035] Although the level of 0
2 as measured in the burner air was enriched to 35%, the precise level in the kiln atmosphere
was somewhat lower than this due to injection of un- metered air through tuyeres in
the wall of the kiln and by air leakage around the firing crown and the various seals.
Kiln draft was kept low in order to minimize leakage.
[0036] The increase of throughput of coke, equivalent to a reduction in combustion volume
of air, indicated a reduction in total air pollution.
1. A process of calcining raw petroleum coke or other carbonaceous material in which
the calcining is carried out in air enriched with a controlled amount of oxygen.
2. A process of calcining raw petroleum coke or other carbonaceous matter in which
the calcining is carried out in an atmosphere enriched with oxygen, the oxygen content
of the atmosphere being at least 20% by volume.
3. A process according to claim 2, in which the calcination atmosphere comprises up
to 35% by volume of total oxygen.
4. A process according to any one of the preceding claims, in which calcining is carried
out in a rotary kiln.
5. A process according to any one of the preceding claims, in which calcining is carried
out without the application of external heat after the initial charge is heated to
the operating temperature.
6. A process according to any one of the preceding claims, in which substantially
all of the heat necessary for calcination is derived from the combustion in an oxygen
enriched atmosphere of the volatile matter driven off during the calcination.
7. A process according to any one of the preceding claims, in which the calcining
is carried out in an atmosphere consisting of from 20-35% by volume of oxygen at a
temperature from 1000°-1500°C.
8. Apparatus for the calcining of petroleum coke or other carbonaceous material which
comprises a rotary kiln equipped with a burner and air blowers, and including means
for injecting oxygen into the atmosphere in said kiln.
9. Apparatus of claim 8, in which the oxygen injecting means are means for injecting
oxygen into the burner air stream.
10. Apparatus according to claim 8, in which the oxygen injecting means are means
for injecting oxygen into the blower air stream.