[0001] The present invention relates to a method of regenerating by crystallization on cooling
pickling bath solutions based on sulphuric acid and/or hydrochloric acid and used
for pickling iron, steel and other iron alloys.
[0002] Acid pickling processes are applied within the iron and steel industries and the
workshop industry for surface treating articles made of iron, steel and other iron
alloys. In the steel industry, acid pickling processes are primarily applied in order
to dissolve the scale and other oxide and hydroxide layers formed on the metal surfaces
of-workpieces during the various processes of their manufacture. These layers are
mainly the result of the thermal treatment processes to which the workpieces are subjected,
e.g. to annealing processes and subsequent rolling operations.
[0003] In the workshop industry, workpieces are pickled in acid baths in order to remove
rust and other contaminants from the surfaces of the workpieces. The rust is formed
during the transportation, storage and handling of the workshop raw materials, these
raw materials comprising, for example, finished goods from the steel industry or intermediate
products from other metal-processing industries, e.g. products obtained from different
subcontractors. The contaminants originate from the same sources, and may comprise
welding, soldering or brazing residues and handprints. They may also originate from
oil coatings and other coatings resulting from processing operations and from surface
treatment processes carried out in order to afford the steel surfaces of the workpieces
some protection against corrosion.
[0004] In the steel industry, sulphuric acid and hydrochloric acid pickling solutions are
primarily used to pickle non-alloyed steel or low-alloyed steel (commercial steel).
Those pickling baths used in the workshop industry are mainly sulphuric-acid solutions.
[0005] When scale-coated articles made of non-alloyed or low-alloyed steels are pickled
in acid pickling baths, the scale is first partially dissolved at the same time as
the major part of said scale is removed mechanically by the development of hydrogen
gas in pores and cavities in the scale. The thus exposed surfaces of the basic material
are then liable to attack by the acid, and if the pickling process is not stopped
at the correct point of time an unnecessarily large quantity of material is consumed,
without any advantage being gained thereby.
[0006] In normal cases the concentration of the solution and the temperature at which the
pickling process is carried out are those given in the following table:
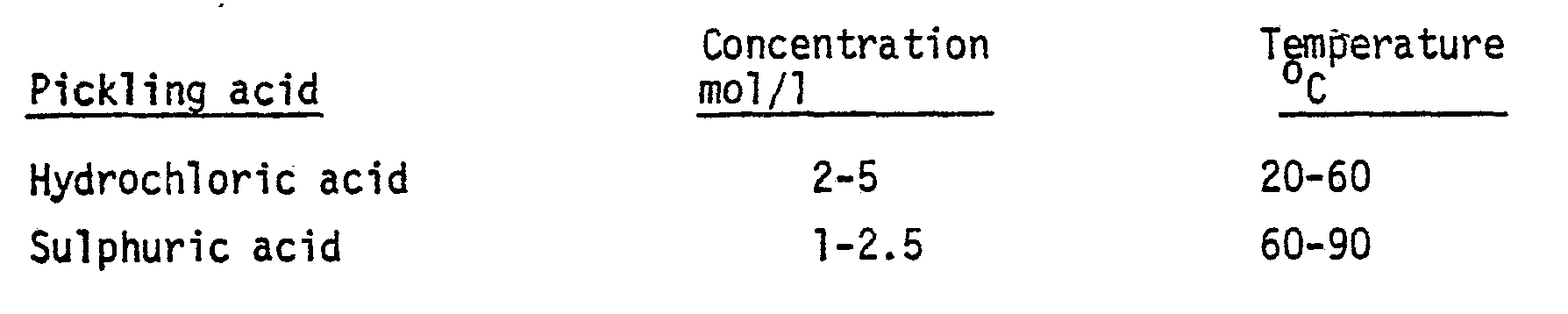
[0007] The pickling time for the complete removal of scale in a rolling mill is about 1
minute.
[0008] When pickling workpieces to remove rust therefrom, rust and other contaminants on
the surfaces of the workpiece are progressively dissolved, and the conditions are
somewhat different to those when pickling in order to remove scale. Normal concentrations
and temperatures are given in the following table:

[0009] The time required when pickling to remove rust is normally between 5 and 20 minutes.
[0010] One common feature of all pickling processes is that when the raw metal surface is
exposed it is readily attacked by the acid, resulting in an unnecessary loss of material
by dissolution of the metal. To avoid this it is normal to add an organic inhibitor,
sometimes referred to as a restrainer, whose purpose is to block the exposed, free
metal surface by adsorption thereon, thereby to protect said surface from acid attack.
[0011] Described in European Patent Application No. 80850166.2 is a method for acid-pickling
metallic material having > 80 % Fe while simultaneously inhibiting the exposed metal
surfaces against dissolution by acid attack. According to this method the material
are brought into contact with an aqueous solution containing phosphoric acid and one
or both of the mineral acids hydrochloric acid and sulphuric acid. The phosphoric
acid concentration is adjusted to at least about 0.01 M (i.e. mol/1) and at most about
1 M, while the total acid concentration is adjusted to the range between about 0.5
and 4 mole per litre.
[0012] Irrespective of the pickling acid used, the concentration of acid will decrease as
the process proceeds, while the concentration of dissolved iron (and possibly other
alloying metals) will increase at the same time. Ultimately the pickling effect will
be non-existent or will have decreased to such an extent as to render it no longer
possible to utilize the solution for pickling purposes.
[0013] Various methods of disposing of the consumed pickling solution are known to the art.
These methods are applied technically with differing degrees of success. The methods
are either concerned with the destruction of the solution or its regeneration for
re-use.
[0014] In those methods pertaining to the destruction of the solution, said solution is
neutralized by adding lime, sodium hydroxide or some other alkali thereto. At the
same time herewith, iron and other metals are precipitated in hydroxide form. Subsequent
to separating the precipitate, the water phase can be discharged to a recipient, while
observing those requirements appertaining to the care and protection of the environment.
Because of the low economic value of the precipitate, its metal content cannot be
utilized. It must therefore be dumped. The disadvantages with the destruction of pickling
bath solutions are many, and in a majority of cases obvious, although the costs of
the lime and the low economic value of the precipitate are among the most serious
of these disadvantages. Hydroxide precipitates are also difficult to handle and are
thus particularly difficult to separate from the water phase. Since the acid is neutralized,
it cannot be re-used or worked up. Thus, the regeneration of pickling bath solutions
is of much more interest in the present context. The different regenerating methods
which have been developed thus pertain to the re-use of either residual acid or dissolved
metals or, optionally, a combination thereof. The iron content of sulphuric - acid
pickling bath solutions can be recovered therefrom in the form of iron sulphates by
crystallization. This method, which is the one most used today for working-up pickling
bath solutions, requires the crystallization process to be effected either by strong
cooling of the solution or by evaporating the solution under a vacuum. Equipment for
such methods is commercially available. In one of the previously known methods according
to Keramchemie, the crystallization process is carried out in a vacuum crystallizer
at a temperature of about lO
oC. In another known crystallization method (The Otto-method) the crystallization of
iron sulphate is effected by strong indirect cooling without vacuum in one or more
interconnected crystallizers. In both of these methods iron sulphate -heptahydrate
is separated from the water phase by centrifugation. The mother liquor is returned
to the pickling bath, to which concentrated sulphuric acid is added so as to again
obtain suitable pickling conditions.
[0015] It is also since long known to regenerate sulphuric acid pickling solutions by first
increasing the sulphuric acid content of the pickling solution by supplying concentrated
sulphuric acid prior to a final cooling of the solution in order to crystallize iron
sulphate therefrom. Such processes, which for example are disclosed in DE-C-561514
(Sierp and Fränsemeier),DE-B-1124781 (Niedner) and US-A-1589610 (Marsh et al), show
much better regenerating efficiency than those using solely the cooling.
[0016] However, a common feature of the known crystallization methods is that large quantities
of energy are required, since both evaporation and the strong cooling of the bath
are unit processes requiring large quantities of heat.
[0017] The iron content of hydrochloric-acid pickling bath solutions can be recovered therefrom
in the form of iron chlorides or iron oxide.
[0018] In the so-called Ruthner-process, described in A Hake, österr. Chemiker Zeitung 68,
180/85 (1967), for example, a roasting process is applied, in which the spent pickling
bath solution is sprayed into a heated reactor space. The water in the solution evaporates
and hydrogen chlorine and iron oxide are formed from the metal chlorides and water
vapour present, said hydrogen chlorine and iron oxide being removed from the reaction
gases by cyclone separation. The hydrogen chlorine gas is absorbed in the water in
a column and the obtained hydrochloric acid can be re-used for pickling purposes.
[0019] A similar method is described in DE-A-1546164 and 1621615 (Metall- gesellschaft AG,
Frankfurt), in which the pickling bath solution, subsequent to a certain degree of
pre-vaporization, is charged to an oil-heated or gas-heated fluidized bed furnace
and there split up while recovering metal oxide and hydrogen chloride from the fumes,
by oxidation with an oxygen - containing fluidizing gas.
[0020] According to the Pori-process, described in detail in Burtch I W, Iron and Steel
Engineer, 50 (1973):4, 40-42 ferrous chloride in the pickling bath solution is oxidized
to ferric chloride, which is then hydrolyzed at high temperatures to iron oxide and
hydrochloric acid. Another known method described in NO-A-7302621 concerns the production
of iron sulphate from the spent pickling bath by adding sulphuric acid to the bath
and electrode-heating said bath to a temperature of 120°C.
[0021] It will be evident from the aforedescribed descriptions of the known processes for
regenerating pickling bath solutions based on sulphuric acid and hydrochloric acid
that present day techniques require very high energy inputs.
[0022] Thus, when crystallizing iron sulphate for the treatment of sulphuric acid baths
in which the iron is a high concentration and the acid in low.concentration, it is
necessary to subject the solution to a vacuum or to strong cooling (from about 60
0C to about 10°C) or a combination thereof. This requires complicated apparatus, and
the installation and operational costs are so high as to render the method unacceptable,
at least in the case of pickling installations of average size within the workshop
industry. In practice, it is only possible to recover sulphuric acid in those cases
when the consumed pickling bath solution is subjected to evaporation processes. In
other cases the acid concentration of the residual solution is too low.
[0023] The previously described methods available for recovering hydrochloric acid from
consumed hydrochloric acid bath solutions require even more energy, even though it
is possible by these methods to recover hydrochloric acid with a relatively high degree
of efficiency. The practical operation of the kind of apparatus required herefore,
is however, extremely complicated.
[0024] The object of the present invention is to eliminate the aforementioned disadvantages
encountered when regenerating pickling bath solutions based on sulphuric acid and
hydrochloric acid, and to provide a technically simple, energy-saving solution to
the problems encountered when working-up the pickling bath solution for re-use by
the normal user, for example within the workshop industry. Thus, a further object
of the present invention is to utilize the solubility of the iron salts at differing
acid concentrations and temperatures and in the presence of phosphoric acid in a manner
such as to eliminate such energy-consuming operations as high-temperature splitting,
or cooling to low temperatures, when regenerating spent pickling bath solutions. Another
object of the invention is to eliminate or reduce the necessity of destroying spent
or consumed pickling bath solutions, by using regenerating agents of suitable composition,
which, in comparison with previously known methods, provides a method which has a
less negative effect on the environment and which requires less energy.
[0025] Still another object of the invention is to eliminate the need of complicated and
expensive apparatus and to reduce the operational costs of regenerating pickling bath
solutions.
[0026] It is also an object of the present invention to permit operation of a continuous
pickling operation, in which substantially constant pickling conditions can be maintained.
According to another object of the invention it is also possible to utilize the iron
salts which are precipitated from the pickling solutions, for example as water purifying
agents.
[0027] It has now surprisingly been found that these objects easily can be realized in a
method where the solubility properties of the iron salts in question are utilized
in a suitably manner. The method is characterized in that sulphuric acid or hydrochloric
acid is added to the solution in a concentration higher than that of said solution
in a quantity sufficient to substantially decrease the solubility of the iron salt
corresponding to said acid at the temperature in question, in that a content of about
0.01 - 1 mole per litre of phosphoric acid is maintained in the solution,in that the
solution is then cooled to a given temperature to crystallize out the iron salt, said
temperature being so selected that the solubility of said iron salt at said temperature
is sufficiently low for the solution to again be used for pickling purposes and in
that the crystallized iron salt is removed from the solution.
[0028] In those acids or acid mixtures used when pickling iron, steel and other iron alloys
the solubility of corresponding iron salts is dependent on the acid concentration
and on the temperature. It has now further been found that presence of phosphoric
acid has an influence on the solubility of the iron salts in a favourable direction
in those concentration ranges being actual when regenerating the pickling solutions.
By adjusting the acid concentration and temperatures to suitable values it is thus
possible to precipitate iron salts from pickling solutions containing phosphoric acid
in a manner that.is favourable from an economic point of view and also from an energy
point of view.
[0029] The reason why a phosphoric acid content of the magnitude set forth in the claims,
that is up to 1 mole per litre, in this connection has such a favourable influence
on the solubility conditions for iron is not quite made clear, but probably a displacement
of the equilibria of the pickling solution will occur.
[0030] In accordance with the method of present invention, phosphoric acid containing pickling
bath solutions are thus treated in three stages, whereby excess of dissolved iron
is removed from the solution and the contents of acid and iron are re-set to values
which are suitable for re-use as a pickling solution.
[0031] In a first stage there is added to the consumed pickling bath solutions a concentrated
acid or an acid mixture containing one or both of these acids, whereat the composition
of the solution is displaced towards the saturation value of corresponding iron salts
at the temperature prevailing in the bath, which temperature, of course, can be slightly
increased by the heat of solution as the acid is added. If the spent pickling bath
solution does not contain any phosphoric acid also such acid is supplied to the solution
in this stage, suitably in the form of a mixture with sulphuric acid or hydrochloric
acid. If phosphoric acid already is present in the spent pickling bath solution a
minor amount phosphoric acid may be added to compensate for losses during the pickling.
If the solution has a high iron content, the saturation value is exceeded after only
a relatively small amount of acid is added, whereat precipitation of an anhydrous
or hydrous iron salt commences. When the iron- content of the solution is low, however,
the saturation value is not normally exceeded in this process stage. The amount of
acid added in this stage is suitably adapted so as to at least substantially obtain
the desired acid concentration in the pickling bath, and the desired maximum iron
content can be adjusted with the cooling capacity available. Thus, in the next stage
the pickling bath solution with the acid added thereto is cooled to a given temperature
above or in the proximity of the ambient temperature, using some conventional method
herefore. These methods, for example, may comprise conventional air cooling, water
cooling or self-cooling processes. If precipitation has already commenced in the first
process stage, it will continue during the cooling stage. Otherwise, the iron salts
begin to precipitate when the saturation value is exceeded in said cooling stage.
During the cooling stage, the iron content of the pickling bath decreases continuously
with decreasing temperature. Since iron is precipitated as hydrous salts, the acid
content of the solution increases indirectly during the cooling and iron-salt precipitation
processes. Cooling in the second stage is continued to a temperature at which acid
and iron contents of the pickling bath solution are suitable for re-use in pickling
processes.
[0032] In a third and last stage of the method, the crystallized iron salt is separated
from the bath solution. This separation can be effected by conventional methods, e.g.
filtration, sedimentation and centrifugation. The residual solution freed of crystals
is returned to the pickling operation. The acid in the solution is again con sumed
and iron is dissolved in said solution until said solution loses its pickling ability,
whereupon it is again considered a consumed or spent solution and the aforedescribed
regeneration stages are .e;eatet.
[0033] The regeneration method can be carried out batchwise, whereat a major portion of
a consumed pickling bath is removed and subjected to the aforedescribed stepwise treatment
process. The regneration process can also be carried out semi-continuously or continuously,
whereat minor portions of the bath or a continuous flow of bath solution are withdrawn
and processed in accordance with the above. In this way variations in concentration
during the pickling process are limited or completely eliminated.
[0034] By suitable selection of acid concentration and temperature, the described treatment
cycle can be repeated without changing the quantity of bath solution. The amount of
solution removed by crystallization.can be compensated by the quantity of acid added.
In practice, liquid is also lost by adhesion, vaporization and spillage. This loss
must also be replaced by suitable additions to the bath.
[0035] Since the crystallization process is carried out while increasing the concentration
in the bath, and displacing the equilibria by the presence of the phosphoric acid
the temperature difference required for the desired degree of crystallization is lower
than that required in known methods based on crystallization, and therefore the bath
need not be cooled to temperatures beneath ambient temperature or exposed to a vacuum.
The crystallization process can thus be carried out in a comparatively simpler apparatus
with less cooling requirements than for prior art crystallization processes. The cooling
therefore can readily be effected with air or available cooling water. The method
is energy saving, and incurs lower investment costs and operational costs than hitherto
known techniques.
[0036] By suitable selection of operating conditions, it is possible to control the actual
pickling operation in an optimal manner, since both the concentration of acid and
of iron in the pickling solution can be selected within reasonable limits already
during the regeneration process. Thus, the acid content can be set at a value preferably
within the range of 0.5-4 mol/1, whereat in the case of sulphuric-acid based solutions
there is suitably selected a content of 0.5-2.5 mol/l. The iron content, which in
the consumed solution can be permitted to reach to 100 g/1 or thereabove, can thus
be lowered to a value which normally lies beneath 50 g/l. As will be understood, even
lower contents can be obtained if desired, by a suitable combination of acid addition
and cooling.
[0037] By the aforementioned selection of iron content it is possible in practice to utilize
the well known phenomenom that a given content of iron in the pickling bath solution
provides better pickling conditions than the normal starting position for pickling,
when beginning with a freshly prepared acid solution which does not contain iron.
[0038] In practice suitable operating conditions are selected, such that both the iron concentration
and the acid concentration are allowed to vary within the optimum range. In a continuous
method, the concentrations of iron and acid may be selected so as to be practically
constant at suitably selected operational conditions.
[0039] During a pickling operation components other than iron are also taken up in the pickling
solution, e.g. alloying metals and oil. When practising the regenerating method according
to the present invention, these components will be accumulated in the bath solution
and may gradually build up to such concentrations as to disturb the pickling operation.
In such a case, the pickling bath solution must be replaced or subjected to special
purifying operations for removing these components.
[0040] The pickling and regenerating procedures are best illustrated on phase diagrams of
actual systems, such as FeSO
4- H
2SO
4- H
2O or FeCl
2- HC1 - H
20. One example of such a diagram is given in figure 1, in which the contents of FeS0
4 and H
2SO
4 present in aqueous solution in equilibrium with solid FeS0
4 are shown at different temperatures. Figure 2 shows a corresponding phase diagram
for the system FeCl
2 -HCl - H
20. Figure 3 illustrates on a phase diagram over the system FeSO
4-H
2SO
4- H
20 a regenerating procedure both with and without presence of phosphoric acid for a
sulphuric acid based pickling solution. Figure 4 illustrates in connection with a
flow sheet showing the process of the present invention a mass and energy balance
according to Example 3.
[0041] The invention will now further be illustrated by means of a number of non-limiting
examples, in which "%" means "% by weight".
EXAMPLE 1
[0042] When pickling iron in a sulphuric acid solution, the acid concentration is supposed
permitted to vary between about 16 and about 10 H
2S0
4. The pickling and regenerating procedure is illustrated by the diagram in Figure
3. Thus, the pickling starts at the point A in Figure 3, where the pickling solution
contains 16 % H
2SO
4 and about 13 % FeS0
4. During the pickling process acid is consumed and iron sulphate simultaneously formed.
When the acid concentration has fallen to about 10 % the pickling is broken off. The
iron sulphate content is now 21 %, which can be seen from point B in the diagram.
[0043] The regenerating process is commenced by an addition of a 95 % sulphuric acid, whereby
the H
2S0
4 content of the pickling solution increases, whereas the iron sulphate content decreases
due to dilution. The acid supply is interrupted at point C when the H
2S0
4 content has increased to a magnitude which is determined by the desired composition
of the pickling solution being regenerated. The solution contains then about 13 %
H
2S0
4 and 20 % FeSO
4.
[0044] Pickling with sulphuric acid is generally carried out at elevated temperatures, such
as about 70°C. When sulphuric acid is added to the spent pickling solution a further
temperature increase will occur. At the point C the solution in the example has a
temperature of about 77°C.
[0045] When the sulphuric acid supplied pickling solution is cooled, iron sulphate precipitation
will commence when the temperature reaches a value corresponding to the solubility
of the sulphate. In the present case sulphate will begin to precipitate in solid form
at about 37°C.
[0046] During the crystallization process the content of FeS0
4 in the solution will decrease whereas the content of H
2SO
4 will decrease due to the fact that FeSO
4 XH
2O is removed from the solution. Provided that the point C has been suitable chosen
the crystallization will be completed at the point. A
1, at which point the solution again has the composition which is suitable for pickling.
In this example the solution must be cooled to about 21°C to reach the desired composition.
EXAMPLE 2 -
[0047] The pickling procedure is performed following the same conditions as in Example 1,
but the pickling solution is supplied with phosphoric acid so as to reach a content
of 0.5 mol/l prior to the regenerating operation. The solubility of iron sulphate
is hereby lowered, so that the 21°C equilibrium curve (corresponding to the final
temperature in Example 1) lies about 5°C lower than in the system free from phosphoric
acid. See Figure 3. Precipitation of iron phosphate will not occur at prevailing conditions.
The pickling operation starts with a solution containing 17 % H
2S0
4 and 11.5 % FeS0
4 corresponding to point All. During the pickling operation the acid content decreases
to about 10 %, while the iron sulphate content will increase to about 21 %, point
B
11. Then sulphuric acid is supplied until point C11 is reached. At C
11 the acid content is about 13.5 % and the iron sulphate content about 20 %.
[0048] During the cooling operation iron sulphate is precipitated from the solution, which
will move the operation point from C
11 back to All, which point corresponds to the initial composition of the pickling solution.
Theoretically no phosphoric acid will be consumed during the pickling-regeneration
procedure irrespective of minor amounts which will adsorb on the pickling goods and
also of spill and other inevitable losses. The pickling bath may thus theoretically
be regenerated by addition of solely sulphuric acid, but, in practice, the solution
must be replenished with sulphuric acid containing a phosphoric acid content adjusted
to the circumstances.
EXAMPLE 3
Energy balances.
[0049] The benefit of utilizing a phosphoric acid containing pickling solution for the regenerating
operation is set forth of the energy balances composing the Examples 1 and 2, respectively.
In both cases 1000 m
2 steel sheet is pickled and the Fe0 scale removed corresponds to 4
0 g
/m2.
[0050] Provided that the process is performed using a heat exchange apparatus as indicated
of the flow sheet in Figure 4 mass and enerby balances can be calculated as shown
by the following table.

[0051] The presence of phosphoric acid will consequently result in a lowering of the amount
pickling acid in operation and thereby also a reduction of the energy demand with
almost 20 %, which is clearly shown of the figures corresponding to Example 2.
[0052] It will be evident that similar results as those obtained in the above examples may
also be achieved also for hydrochloric acid pickling baths. The lowering of the solubility
of FeCl
2 is here even more evident in this case and is furthermore dependent on the HC1 concentration
as is shown in the diagram of Figure 2 by the dotted line corresponding to a temperature
of 20°C.