[0001] Die Erfindung betrifft eine CuAlCo-Legierung hoher Verschleissfestigkeit und mit
feinem Gefüge, die als Komponenten - neben den üblichen Verunreinigungen - mindestens
Al, Fe, Co, Cr, Mn, Cu enthält.
[0002] Legierungen der genannten Art sind bekannt (US-PS 3,117,002); sie dienen vor allem
als Tiefziehwerkzeuge und Verschleissteile und werden als Sandguss oder Strangguss,
als Schmiede-oder extrudierte Werkstücke und/oder als Schweissmaterial, beispielsweise
zum Schweissplattieren, verwendet.
[0003] Für viele Anwendungen ist bei diesen Legierungen der Verschleiss, d.h. die Abnützung
bei Relativ-Bewegungen gegenüber anderen Materialien, beispielsweise Stahl, für heutige
Anforderungen zu hoch. Aufgabe der Erfindung ist es daher, die mechanischen Eigenschaften
und insbesondere das Verschleissverhalten der bekannten Legierungen zu verbessern.
[0004] Diese Aufgabe wird erfindungsgemäss durch Legierungen gelöst, deren Zusammensetzung
(in Gew. %) Al 14 - 16; Fe 4 - 6; Co 2,5 - 3,5; Mn 1 - 1,5; Cr 0,4 - 0,8; Zr 0,01
- 0,5; Rest Cu beträgt, wcbei die Summe von Fe und Co grösser als 7,5 ist, und deren
Gefüge im Gusszustand Korngrössen zwischen 20 bis 50 pm enthält.
[0005] Zwar sind nicht nur mehrere der genannten Komponenten, sondern auch ihre bei der
erfindungsgemässen Legierung verwendeten prozentualen Anteile aus der genannten US-PS
bekannt; die Erfindung unterscheidet sich von den bekannten Legierungen jedoch durch
einen geringeren Mn-Anteil, durch die Legierungskomponente Zr und durch engere Toleranzen
in den Cr-, Fe- und Co-Anteilen. Gerade diese Unterschiede sind nach Versuchen der
Anmelderin jedoch massgebend für die um den Faktor 5 bis 10 feineren Korngrössen,
die bei den bekannten Legierungen zwischen 100 bis 500 pm betragen, und damit für
die verbesserten Verschleisseigenschaften.
[0006] Die Giessbarkeit, d.h. vor allem die Fliessfähigkeit, der Legierungsschmelze lässt
sich verbessern, wenn sie bis zu 0,2 Be enthält; durch diesen Zusatz werden in erster
Linie die Bildung von A1
20
3 und die Gefahr von Oxid-Einschlüssen in der Schmelze herabgesetzt.
[0007] Ein Verfahren zur Herstellung der erfindungsgemässen Legierung ist dadurch gekennzeichnet,
dass mindestens ein Teil des Zr- und/oder Be-Gehaltes über Schmelzbehandlungen bei
Temperaturen zwischen 1150 und 1250° C innerhalb der letzten 30 Minuten vor dem Abguss
durch Zugaben von Mengen dieser Stoffe erreicht wird, die die genannten Endgehalte
gewährleisten. Die Schmelzbehandlung bewirkt vor allem die angestrebte, für das verbesserte
Verschleissverhalten notwendige Feinheit des Gefüges, die ein Charakteristikum der
vorliegenden Erfindung ist.
[0008] Die mechanischen Eigenschaften, die in gewissem Umfang durch Variationen der Zusammensetzung
innerhalb der angegebenen Bereiche beeinflusst werden können - so ist z. B. die erzielte
Härte abhängig vom Al-Gehalt -, ergeben beispielsweise für sandgegossene Werkstücke
im Gusszustand folgende Werte:
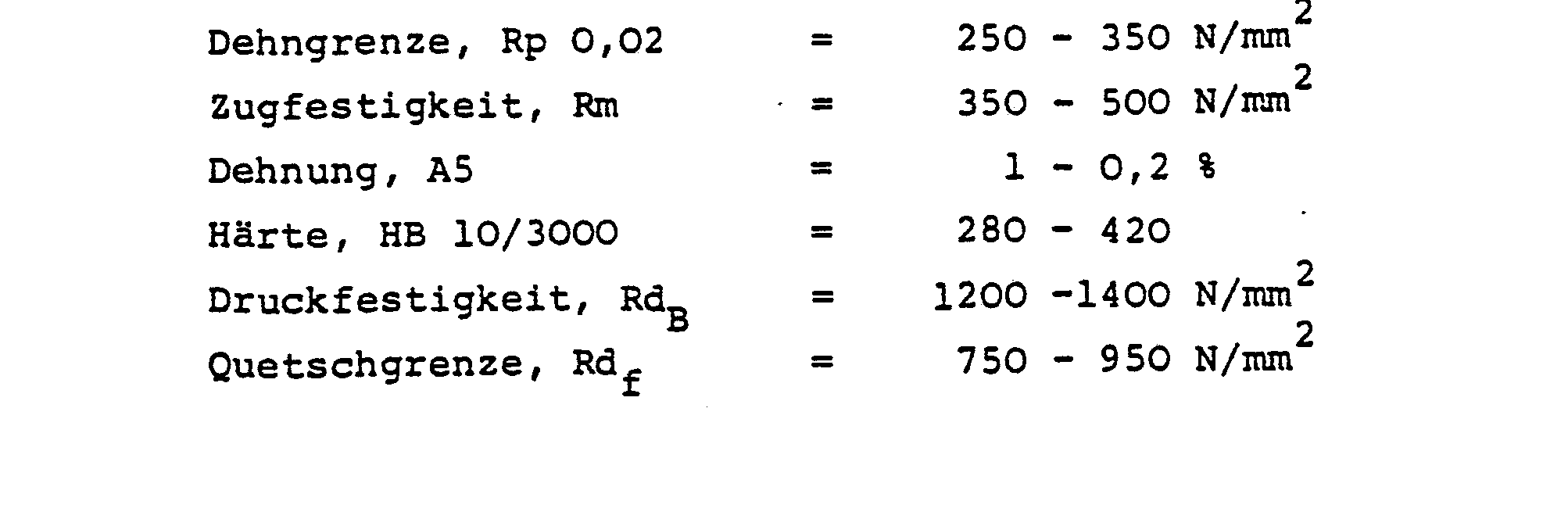
Diese Werte lassen sich weiter verbessern, wenn man das gegossene Werkstück bei Temperaturen
bis zu 1000
0 C einer Normalisierungsbehandlung unterzieht, bei der die Haltezeit mindestens 1
Stunde und zusätzlich pro 25 mm Wanddicke eine weitere Stunde beträgt und die Abkühlung
in ruhender Luft erfolgt, wobei bei der Aufheizung bis zum Erreichen von Temperaturen
um 600 C eine Erwärmungsgeschwindigkeit von höchstens 200° C pro Stunde einzuhalten
ist.
[0009] Im folgenden wird die Erfindung anhand eines Ausführungsbeispiels näher erläutert.
[0010] Es soll eine Schmelze von 100 kg einer erfindungsgemässen CuAlCo-Legierung hergestellt
werden, bei der das gegossene Werkstück eine Brinellhärte von 380 HB im Gusszustand
besitzen soll.
[0011] Als Einsatz werden 1/3 (33 kg) Rücklauf aus dem geforderten Material und 2/3 neues
Material verwendet, wobei das Einsatzmaterial möglichst rein sein soll. Neben den
33 kg Rücklaufmaterial werden dafür bereitgestellt:
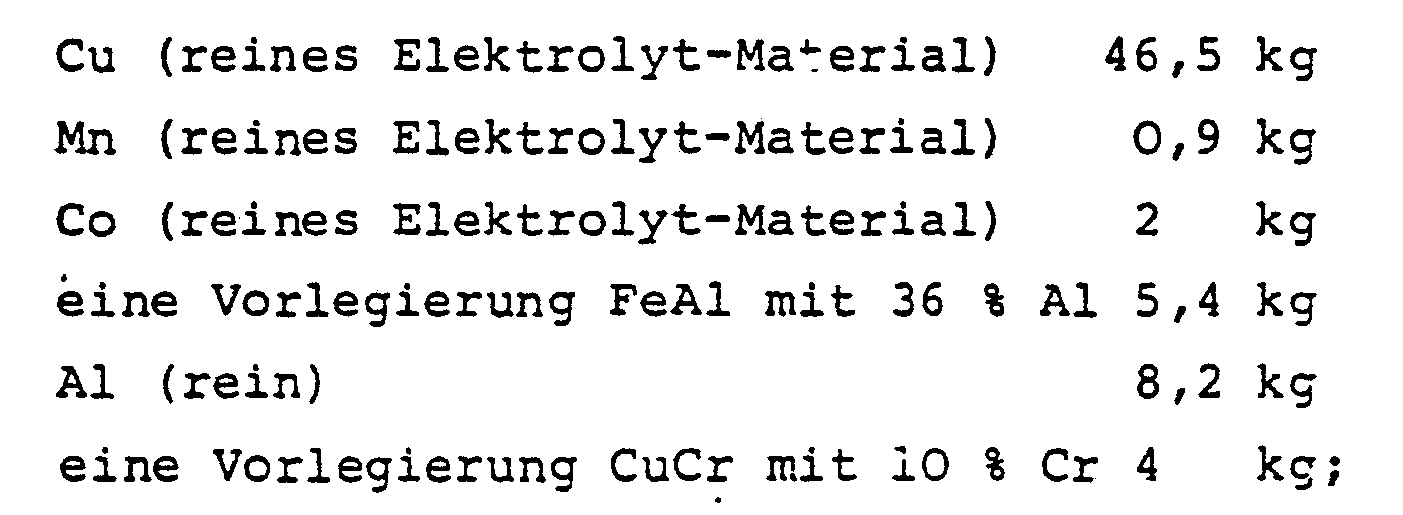
weiterhin muss zusätzlich zur Kompensation des Al-Abbrandes nochmals 500 g Al zur
Verfügung stehen.
[0012] Unter leicht oxidierenden, atmosphärischen Bedingungen werden in einem Mf-Induktionsofen,
der mit einem Graphit-Tiegel ausgerüstet ist, zunächst das Rücklaufmaterial, Mn, Cu,
Co und die Vorlegierung CuCr erschmolzen, wobei als Schlackenbilder
0,5 % Kryolith in die Schmelze zugegeben werden; anschliessend wird die Vorlegierung
FeAl eingefügt und danach das reine Aluminium in die Schmelze gebracht.
[0013] Etwa 10 bis 20 Minuten vor dem Abguss wird die Schmelze bei 1200° C mit Zirkon (Zr)
behandelt. Für diese Schmelzbehandlung wird eine Menge von 0,1 % Zirkon verwendet
in Form von einer Vorlegierung CuZr 50 (50 % Cu, 50 % Zr), die der Schmelze zugegeben
wird. Abschliessend wird die Legierung bei 1180°
C in Sandformen abgegossen.
[0014] Die chemische Analyse ergibt - neben den üblichen Verunreinigungen, die so tief wie
wirtschaftlich sinnvoll gehalten werden und im wesentlichen aus P (max 0,05); S (max.
0,1); Si (max. 0,1); Sn (max. 0,2); Zn (max. 0,2); Pb (max. 0,05) und Ni (max. 0,4)
bestehen - folgende zusammensetzung:

[0015] Das gegossene Werkstück wird anschliessend durch eine Wärmebehandlung zwischen 900
und 950
0 C normalisiert, wobei es mit einer Aufheizgeschwindigkeit von 150° C pro Stunde in
Luft bis auf etwa 600° C und anschliessend mit höherer Aufheizgeschwindigkeit auf
950
0 C aufgeheizt wird. Bei dieser Temperatur wird es dann 1 Stunde und zusätzlich je
25 mm Wanddicke nochmals 1 Stunde gehalten, ehe es an ruhender Luft abgekühlt wird.
[0016] Für die mechanischen Eigenschaften sind danach folgende Werte gemessen worden:
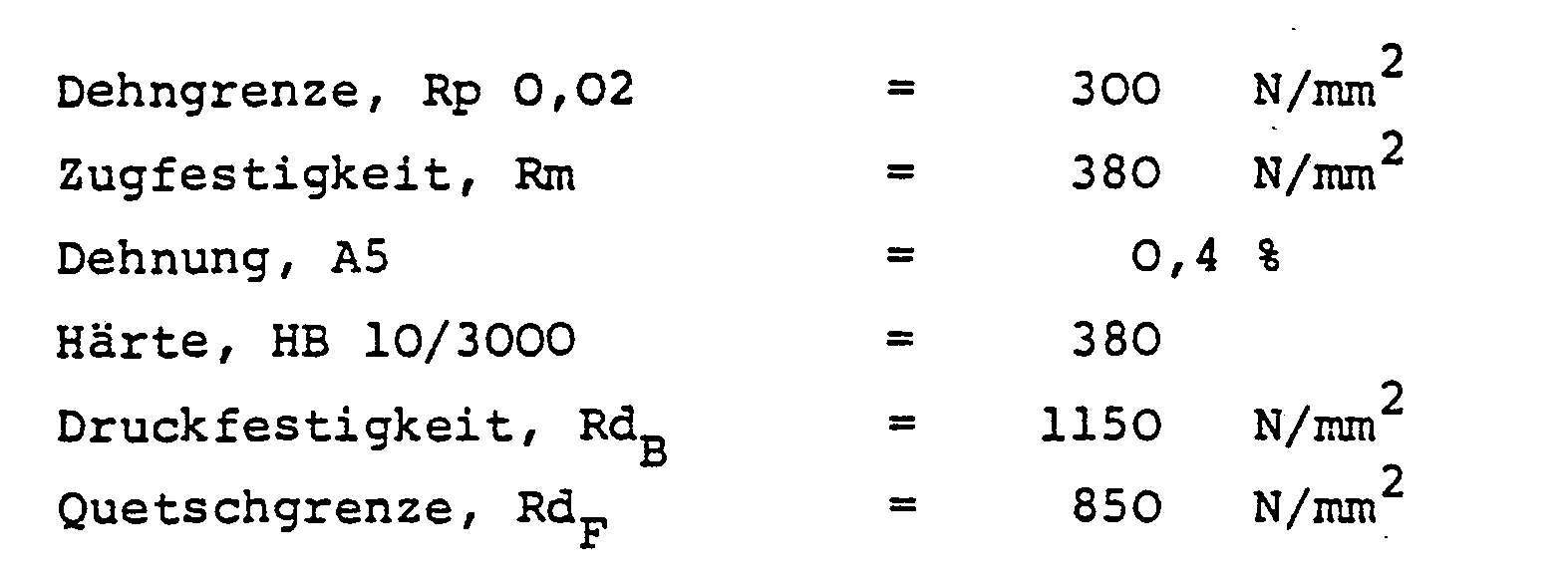
[0017] Die beigefügte graphische Darstellung der Fig. 1 verdeutlicht in einem Vergleich
die relativen Verschleissfestigkeiten einer bekannten Legierung der genannten Art
(Säule 1) und der erfindungsgemässen Legierung gemäss Beispiel 1 (Säule 2). Auf der
Ordinate der Darstellung ist in mg der durch Wägung ermittelte jeweilige Abrieb aufgetragen,
der sich bei einem Standard-Verschleissversuch ergibt. Bei diesem Versuch läuft ein
mit etwa 30 N belasteter Rollkörper aus rostfreiem 18/8-Cr/Ni-Stahl in einem Gleitkörper
aus der zu prüfenden Legierung ohne Schmiermittel eine festgelegte Zeitdauer, die
im vorliegenden Fall 20 Stunden beträgt. Der dabei entstehende Abrieb wird gesammelt
und gewogen.
[0018] Wie Fig. 1 zeigt, ergeben sich für die bekannte Legierung dabei - aus mehreren Messungen
gemittelt - Werte zwischen 550 und 800 mg/20 h - der Streubereich ist jeweils schraffiert
angegeben -, während bei der neuen Legierung Werte zwischen 250 und 550 mg pro 20
Stunden gemessen worden sind.
[0019] Fig. 2a und 2b stellen in 100-facher Vergrösserung metallographische Schliffbilder
dar, aus denen sofort die Unterschiede in den Korngrössen ersichtlich sind; in Fig.
2a ergeben sich für die bekannte Legierung, wie bereits erwähnt, Korngrössen von etwa
300 pm, während aus Fig. 2b für die erfindungsgemässe Legierung Korn
grössen von 40 um bestimmt werden können.
[0020] Wie bereits erwähnt, ist die Anwendung der neuen Legierung nicht auf Werkstücke aus
Sandguss beschränkt; so können daraus auch im Strangguss oder durch Extrudieren hergestellte
Elektroden für eine Auftragsschweissung, beispielsweise auf unlegiertem Stahl, hergestellt
werden. Durch Extrudieren bei Temperaturen zwischen 900 und 950° C lassen sich daraus
weiterhin Barren oder Drähte für die Produktion von Verschleissteilen gewinnen. Weiterhin
ist es möglich, die neue Legierung, ebenfalls bei Temperaturen zwischen 900 und 950
0 C, zu schmieden.
1. CuAlCo-Legierung hoher Verschleissfestigkeit und mit feinem Gefüge, die als Komponenten
- neben den üblichen Verunreinigungen - mindestens Al, Fe, Co, Cr, Mn, Cu enthält,
gekennzeichnet durch folgende Zusammensetzung (in Gew.%):
Al 14 - 16; Fe 4 - 6; Co 2,5 - 3,5; Mn 1 bis 1,5;
Cr 0,4 - 0,8; Zr 0,01 - 0,5; Rest Cu,
wobei die Summe von Fe und Co grösser 7,5 ist, ferner gekennzeichnet durch ein Gefüge
mit Korngrössen im Gusszustand zwischen 20 bis 50 µm.
2. Legierung nach Anspruch 1, dadurch gekennzeichnet, dass sie bis zu 0,2 % Be enthält.
3. Verfahren zur Herstellung einer Legierung nach Anspruch 1 oder 2, dadurch gekennzeichnet,
dass mindestens ein Teil des Zr- und/oder Be-Gehaltes über Schmelzbehandlungen bei
Temperaturen zwischen 1150 und 1250° C innerhalb der letzten 30 Minuten vor dem Abguss
durch Zugaben von Mengen dieser Stoffe erreicht wird, die die genannten Endgehalte
gewährleisten.
4. Verfahren nach Anspruch 3, für als Sandguss gegossene Werkstücke, dadurch gekennzeichnet,
dass das gegossene Werkstück bei Temperaturen bis zu 1000° C einer Normalisierungsbehandlung
unterzogen wird, bei der die Haltezeit mindestens 1 Stunde und zusätzlich pro 25 mm
Wanddicke eine weitere Stunde beträgt und die Abkühlung an ruhender Luft erfolgt,
wobei bei der Aufheizung bis zum Erreichen von Temperaturen um 600° C eine Erwärmungsgeschwindigkeit
von höchstens 200° C pro Stunde einzuhalten ist.