[0001] Tungsten is generally found in nature in scheelite type ores and wolframite type
ores. These two ores differ substantially in their chemical composition being a calcium
tungstate and an iron-manganese tungstate, respectively. Consequently, different processes
have generally been used to recover the tungsten values from each type of ore. In
the case of scheelite ores, the classical prior art process is to treat the ore with
hydrochloric acid to produce insoluble tungstic acid. The tungstic acid is taken up
in an ammonia solution to produce ultimately ammonium paratungstate (APT). Wolframite
on the other hand is usually decomposed by fusing the ore with sodium hydroxide/sodium
carbonate which extracts the tungsten as sodium tungstate. The cooled fused product
is leached with water to extract the soluble sodium tungstate. Similarly, this may
be treated with hydrochloric acid to precipitate tunstic acid which is taken up in
an ammonia solution to produce APT.
[0002] British patent specification No. 1,089,913 describes a process for recovering tunsten
values from both scheelite and wolframite type ores or concentrates. This process
comprises fusing powdered scheelite and/or wolframite type ores or concentrates with
a fluxing mixture of sodium carbonate, sodium chloride and sodium nitrate (which mixture
also contains, in the case of the starting material containing calcium, at least sufficient
siliceous material to form calcium silicate therewith), leaching the cooled, fused
material with water and separating a tungsten-bearing alkaline leach liquor from water-insoluble
impurities, acidifying the separated leach liquor and adding thereto sufficient of
a fluoride or hydrofluoric acid to form compounds which are substantially insoluble
in organic media, extracting the thus-treated material with an organic solution comprising
an organic amine capable of forming a water-insoluble organic amine tungsten complex
to transfer tungsten from the aqueous to the organic phase, separating the phases,
treating the separated organic phase, with aqueous ammonia to form a water-soluble
ammonium tungstate, and separating the aqueous phase containing ammonium tungstate
from the organic phase. This process involves, as an essential step, the fusion of
powdered scheelite and/or wolframite type ores or concentrates with a mixture of sodium
carbonate and sodium chloride. Indeed, it is stated in the specification that a fluid
melt should be produced. Typical temperatures at which the fusion take place are 698°C
to 825°C.
[0003] Fox U.S. Patent No. 3,800,025 describes a process of extracting tungsten values from
low grade tungsten ores which includes the steps of roasting a particulated tungsten-containing
ore in a water containing atmosphere in the presence of sodium chloride and at least
one of the reagents selected from sodium carbonate and sodium phosphate at a temperature
in the range of about 600°C to about 900°C for about 1 to 3 hours, water leaching
the resulting calcines to dissolve soluble tungsten values and filtering. This process
is restricted in application to low grade tungsten ores and requires a water containing
atmosphere for its operation. Moreover, relatively high roast temperatures and relatively
low amounts of sodium reactant are generally used.
[0004] French Patent Specification 992821 describes a process for extracting tungsten values
from low grade tungsten-containing slags in which a mixture of crushed slag and an
alkali metal salt is roasted at a temperature below the melting point and the roasted
product is leached in order to extract tungsten values.
[0005] We have now developed an improved method of recovering tungsten values from mixtures
of wolframite and scheelite.
[0006] According to the present invention, we provide a method of recovering tungsten values
from a tungsten-bearing ore or concentrate in which the ore or concentrate is roasted,
without fusion, in the presence of a reagent which is an alkali metal chloride or
carbonate or a mixture thereof and water-soluble tungsten values are extracted from
the roasted product, characterised in that the tungsten bearing ore or concentrate
is a high grade ore or concentrate which is a mixture of wolframite and scheelite
and that after extraction of the water-soluble values from the roasted product, the
latter is roasted again, without fusion, in the presence of the reagent and further
water-soluble tungsten values are extracted from the re-roasted product.
[0007] It is essential to the process that roasting takes place without general fusion,
that is the mix of ore or concentrate and reagent must not form a fluid melt during
roasting. The fact that a melt is not produced confers a much greater flexibility
in process design and can result in energy savings. The roasted product is an easily
handleable material.
[0008] The tungsten values in the roasted product will be in the form of water-soluble alkali
metal tungstate. This product may thereafter be treated in known manner to recover
the tungsten values as tungsten metal. For example, the tungsten values may be water
leached from the roasted mixture and the leach liquor then treated in the manner described
in British patent specification No. 1,089,913. These treatment steps are essentially
an application of chemistry known in the art.
[0009] The tungsten-bearing ore or concentrate is α
- high grade one, i.e. one containing at least 20 percent by weight tungsten as tungsten
oxide (W0
3). Such materials may contain up to 80.5 percent by weight tungsten as tungsten oxide.
[0010] The reagent is an alkali metal chloride, an alkali metal carbonate or a mixture thereof.
The alkali metal for both the chloride and the carbonate reagent is preferably sodium.
It is a particularly preferred feature of the process that the reactive composition
consists solely of an alkali metal carbonate, such as sodium carbonate. It has surprisingly
been found that excellent tungsten recoveries, at relatively mild temperatures can
be achieved using sodium carbonate alone.
[0011] The roasting temperature will vary according to the nature of the ore or concentrate
being treated and the type and quantity of reagent. The important point is that a
temperature must be chosen which will not result in fusion bf the mixture of ore or
concentrate and reagent taking place, but will yet be high enough for the desired
reaction to take place in a reasonable time. As a general rule temperatures in the
range 600° to 800°C will be used.
[0012] The step of re-roasting the extracted material in the presence of further reagent
and extracting tungsten values from the re-roasted material can be repeated until
as much of the tungsten as desired has been extracted from the ore.
[0013] The amount of reagent present during roasting will also vary according to the nature
of the ore or concentrate. There should be at least sufficient sodium present to combine
with all the tungsten to form sodium tungstate and it is generally preferred to use
a stoichiometric excess of sodium.
[0014] The roasting must take place for a sufficient time to convert as much as possible
of the tungsten to sodium tungstate. The roasting time is typically up to 120 minutes,
although for many ores no particular advantage has been found by heating for a period
of longer than 60 minutes.
[0015] Where necessary, depending on the ore composition and/or type of heating equipment
being used, the reagent may also contain a suitable oxidising agent, such as sodium
nitrate. It may be desirable in some cases to include finely divided silica in the
reactive composition. The silica reacts with the calcium to form tricalcium silicate
which is subsequently readily separable from the sodium tungstate.
[0016] The tungsten-bearing ore or concentrate and the reagent will generally both be provided
in finely divided state and will be intimately mixed prior to roasting. After roasting,
the product may be leached with water. It has been found experimentally that one leach
and a replacement wash under appropriate conditions are generally sufficient. The
fact that there is no fusion during roasting means that leaching may take place on
the roasted product as such without subjecting that product to a crushing or like
step. Moreover, leaching may take place while the roasted product is still hot.
[0017] After leaching, the leach liquor is treated by commonly known methods to remove impurities
such as aluminium, magnesium, phosphorous, silicon, antimony, arsenic and molybdenum.
[0018] After the first purification step, the filtrate may be further purified by treatment
with a fluoride or hydrofluoric acid. The adequately purified solution is then subjected
to a conventional solvent extraction procedure. The tungsten contained in the organic
phase may be extracted with ammonium hydroxide to provide an aqueous ammonium tungstate
solution.
[0019] Tungsten metal powder may be produced from the ammonium tungstate by known methods.
[0020] In order that the invention may be more fully understood, the following example is
given by way of illustration.
[0021] In this exampfe, the ore (or extracted residue) and reagent was in finely divided
or particulate form and was roasted as a mixture. After roasting, the sodium tungstate
was leached with water, the residue separated from the leach liquor by filtration
and washing and the leach liquor treated in the manner generally described above to
recover the tungsten values.
Example
[0022] A scheelite concentrate containing 74.8% of W0
3 and a wolframite concentrate containing 68.1% W03 were mixed 1:1 by weight and the
mixture was mixed with sodium carbonate in the proportion of 1 part of sodium carbonate
to four parts of the mixture. The specific quantities used were 300 g of scheelite,
300 g of wolframite and 150 g of sodium carbonate (the theoretical stoichiometric
amount of sodium carbonate was 98 g). The final mixture was roasted at 650°C for four
hours. After roasting, the material was leached with water as described above to give
a percentage extraction of tungsten of 58%.
[0023] The extracted residue was again mixed with sodium carbonate and roasted at 650°C
and two tests conducted with different amounts of sodium carbonate. The results are
given in Table I.
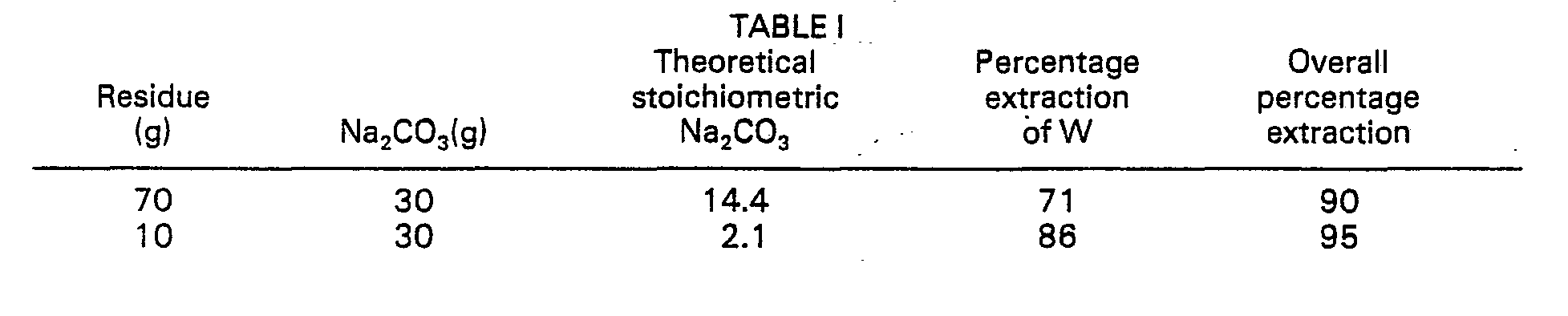
[0024] The overall tungsten extraction is 90 and 95 percent at residue: Na
2CO
3 ratios of 7:3 and 1:3. The particular ratio chosen will depend on the particular
economic circumstances under which-the process is, operated at any given time.
1. A method of recovering tungsten values from a tungsten-bearing ore or concentrate
in which the ore or concentrate is roasted, without fusion, in the presence of a reagent
which is an alkali metal chloride or carbonate or a mixture thereof and" water-soluble
tungsten values are extracted from the roasted product, characterised in that the
tungsten-bearing ore or concentrate is a high grade ore or concentrate which is a
mixture of wolframite.and scheelite and that after extraction of the water-soluble
values from the roasted product, the latter is roasted again, without fusion, in the
presence of the reagent and further water-soluble tungsten values are extracted from
the re-roasted product.
2. A method according to claim 1 characterised in that the roasted product is leached
with water while it is hot in order to extract tungsten values therefrom.
1. Procédé de récupération de sels de tungstène à partir d'un minerai ou d'un concentré
contenant du tungstène, selon lequel on grille le minerai ou le concentré, sans fusion,
en présence d'un réactif qui est un chlorure ou un carbonate d'un métal alcalin, ou
un mélange de ces corps, puis on extrait les sels de tungstène du produit grillé,
caractérisé en ce qu'on part d'un minerai ou d'un concentré contenant du tungstène
d'un grade élevé qui est un mélange de wolframite et de scheelite et que, après extraction
des sels de tungstène solubles dans l'eau du produit grillé on grille ce dernier à
nouveau sans fusion en présence du réactif et on extrait du produit regrillé des sels
de tungstène supplémentaires.
2. Procédé selon la revendication 1 caractérisé en ce qu'on traite le produit grillé
par lixiviation à l'aide d'eau pendant qu'il est chaud afin d'en extraire des sels
de tungstène.
1. Verfahren zum Gewinnen bzw. Wiedergewinnen von Wolfram aus einem wolframhältigen
Erz oder Konzentrat, wobei das Erz oder Konzentrat ohne zu schmelzen in Gegenwart
eines Reagens, das ein Alkalimetall-Chlorid oder -Karbonat oder eine Mischung davon
ist, geröstet und aus dem Röstprodukt wasserlösliche Wolframverbindungen extrahiert
werden, dadurch gekennzeichnet, daß ein hochwertiges wolframhältiges Erz oder Konzentrat
verwendet wird, das eine Mischung aus Wolframit und Scheelit darstellt, und daß nach
der Extraktion der wasserlöslichen Wolframverbindungen aus dem Röstprodukt dieses
letztere abermals ohne zu schmelzen in Gegenwart des Reagens geröstet wird und weitere
wasserlösliche wolframhältige Verbindungen aus dem wiedergerösteten Produkt extrahiert
werden.
2. Verfahren nach Anspruch 1, dadurch gekennzeichnet, daß das Röstprodukt noch in
heißem Zustand mit Wasser gelöscht wird, um die Wolframverbindungen zu extrahieren.