[0001] The present invention relates to an aluminium-based, dispersion-strengthened, mechanically
alloyed, alloy.
[0002] Considerable research efforts have been expended to develop high strength aluminium
alloys which would satisfy the demands of advanced design in aircraft, automotive
and electrical industries. There are well known alloys in the 2000 and 7000 series
which have high strength, but they do not exhibit the required combination of properties
for certain applications. For example, advanced aircraft material needs are for an
aluminium alloy exhibiting the strength of alloy 7075 in the T6 temper, but having
greater corrosion resistance. However thermal treatments which strengthen alloy 7075
to the T6 temper produce a susceptibility to stress-corrosion cracking. Al-Cu-Mg alloys
in the 2000 series have been developed which have good fatigue strength, but generally,
alloys in the 2000 series are weaker than 7000 series alloys and they are also less
resistant to stress corrosion. In other words, the improvement of a single property
by itself does not necessarily mean that an alloy will be useful. Rather groups of
properties must be considered. Thus, to improve the load carrying capabilitv of an
aircraft structural member, allowing reduction of load carrying area and in turn reducing
the weight of part, the properties of interest are tensile yield strength, notched
fatigue resistance, fracture toughness, fatigue crack growth rate, and resistance
to stress corrosion cracking.
[0003] Tensile yield strength (YS) is the primary design factor for determining the stress
loading for a structural member. Normally, maximum anticipated flight loads for a
member are specified as a percentage such as 40% or 60% of the YS. Thus the greater
the YS, the smaller the cross sectional area of the structural member may be. Tensile
ductility is another important material parameter. It is the practice of the aircraft
designers to specify an acceptable elongation, commonly 5% minimum. For conventional
aluminium alloys the tensile ductility decreases as the tensile yield strength increases
and this lack of ductility may limit the design potential in high strength areas.
Notched fatigue resistance is the alloy resistance to cyclic loading in the presence
of notches or cracks. Discontinuities in aircraft structures (e.g. rivet, holes, joints,
notches, filleted corners, etc.) act so as to magnify the applied load at the discontinuity.
Moreover the loads applied to aircrafts are not constant, but cyclic in nature, making
notched fatigue resistance to failure of a part at a discontinuity an important design
criterion. Notched fatigue resistance may decrease slightly with increased strength
in conventional alloys. Thus, an increase in tensile yield strengths in an alloy may
not be useful if the increased structural loading would exceed the cyclic stress level
which the structure can sustain without fatigue failure. Fracture toughness is a measure
of the ability of a material to resist catastrophic failure originating at an existing
crack. (Such cracks may originate in fatigue). The crack length and applied load control
the stress intensity at the crack tip. Higher toughness materials withstand greater
applied stress intensity and allow the growth of larger cracks before the structure
is in danger of catastrophic failure. In the design of an improved part from higher
tensile yield strength material, the toughness must be maintained at a level which
will allow the crack to grow to a detectable length (during intervals between aircraft
inspection) without risking catastrophic failure. Fatigue crack growth rate is an
important design characteristic. As the loading of a structural member increases,
the stress intensity at the tip of an active fatigue crack increases, and the growth
rate of a fatigue crack will increase with increasing stress intensity range. Thus,
if a higher strength part is exposed to a higher applied load, then fatigue cracks
will grow faster unless increased resistance to fatigue crack initiation and growth
is obtained along with increased YS. A faster growing crack necessitiates more frequent
aircraft inspection so that the crack does not reach the critical length for catastrophic
failure undetected. An additional property of major interest to designers is stress
corrosion cracking resistance (SCC). Most aluminium alloys are known to fail in tensile
loading at stresses well below their normal YS in the presence of a corroding medium.
(Normal operating conditions are corrosive to aircraft materials). Only some aluminium
alloys with very low YS do not show this phenomenon. The use of an alloy with high
YS may thus be prohibited because that alloy might fail in tension at a much lower
stress in actual service. It can be seen from the foregoing that advanced Al alloys
for the aerospace industry must exhibit a broad range of suitable properties to be
successfully applied.
[0004] The mechanical alloying process is broadly disclosed and claimed in UK Patent No.
1 265 343 and UK Patent No. 1 390 857 discloses a process for preparing mechanically-alloyed
dispersion-strengthened aluminium-based powders for consolidation to billet having
improved combinations of strength and ductility. The materials made by mechanically-alloying
are characterised by a fine grain structure which is stabilised by a dispersion of
oxide and carbide particles. European Patent Application No. 79 302 232.8 discloses
a dispersion-strengthened mechanically-alloyed aluminium-base alloy system having
high strength and good corrosion resistance and a method for controlling and/or optimising
strength and workability by variations in the thermomechanical processing. The aluminium-base
alloys contain up to 7% magnesium, up to 2.5% carbon and 0.3 to 4% oxygen. Among the
other additives which are disclosed for additional strength in the Al-Mg system are
Li, Cr, Si, Zn, Ni, Ti, Zr, Co, Cu and Mn.
[0005] The present invention is based on the discovery that in a mechanically-alloyed aluminium-base
alloy the addition of copper and magnesium in suitable amounts not only improves the
strength of the aluminium, but also unexpectedly, it can provide an Al-Cu-Mg alloy
system which has superior corrosion resistance properties. It is particularly surprising
that the alloy of this invention has a superior combination of strength and stress
corrosion cracking properties in view of the properties of conventional alloys of
the 2000 series, such as Alloy 2024.
[0006] According to the present invention a dispersion-strengthened mechanically-alloyed
aluminium-based alloy having improved resistance to stress corrosion cracking comprises
0.5 to 6% copper, 0.5 to 3% magnesium, 0.1% to 2.5% carbon, an effective amount up
to 3% oxygen, up to 1% manganese, up to 0.5% iron, balance apart from impurities and
incidental elements being aluminium, and containing oxide and carbide dispersoids
in an amount of 1% to 10% by volume. All percentages herein are by weight unless otherwise
specifically stated. Alloys of the invention have excellent resistance to stress corrosion
cracking and exhibit in the consolidated, forged and heat treated condition a fracture
toughness in the transverse direction of at least 33 MN/m
3/2 when the tensile yield strength in the transverse direction is about 551 MN/m
2 and a fracture toughness in the transverse direction of at least 49.5 MN/m 3/2 when
the tensile yield strength in the transverse direction is about 448 MN/m 2, and has
an elongation in short transverse direction of at least 5% and normally more than
10%. The stress corrosion cracking resistance has been found to be better than that
of the conventional aluminium alloy 2024 in the T4 temper by more than 50%, and in
some instances by more than 500%.
[0007] The alloy contains 1 to 10% by volume, preferably 2 to 7%, of finely divided,uniformly
distributed dispersoid materials consisting of oxides and carbides, and may include
other refractory dispersoids such as nitrides and borides.
[0008] The alloy powder is made by the mechanically alloying technique in the presence of
a process control agent and the powder is hot consolidated to a substantially dense
body, worked at an elevated temperature, such as 200 to 550°C, and subjected to a
solution treatment for a period of 1/4 to 10 hours at a temperature of 350 to 550°C,
preferably 480 to 510°C. However, it is possible to vary thermal solution and natural
and artificial aging treatments to produce various effects in the alloy.
[0009] Preferred alloys of the invention contain 2 to 5% copper, 0.5 to 2.5% magnesium,
oxygen in the range
0.4 to 1% and carbon 0.6 to 1.25%. More preferably the copper range is 3 to 4.5% and
magnesium 1 to 2.5%, or even 1.25 to 2%. Preferably the manganese content does not
exceed 0.4%, or more preferably 0.2%, and the iron content is preferably below 0.2%.
The alloy may also contain other minor amounts of other elements normally present
as trace elements in aluminium.
[0010] One embodiment of the invention consisting essentially of 4% copper, 1.5% magnesium,
0.8% oxygen, 1.1% carbon and by volume 5.5 to 7% of dispersed oxide and carbide refractory
phase, exhibits in the forged, heat-treated state a transverse yield strength of at
least 551 MN/m
2, a fracture toughness of at least
34.6 MN/m
3/2 normally 37.4 and elongation in the short transverse direction of 10% or more.
[0011] Alloys of the invention are produced and processed into consolidated form by the
processes disclosed in UK patent 1 390 857 and European Patent application 79 302
232.8. However the present alloys receive an additional solution treatment in order
to strengthen them and may further benefit from an age hardening treatment.
[0012] Some examples will now be described having reference to the accompanying drawings
in which:
Figure 1 shows a longeron end tie forging.
Figure 2 is a graph comparing fracture toughness vs. yield strength for various aluminium
alloys.
Figure 3 is a graph comparing fatigue crack growth rate in dry air of various aluminium
alloy forgings.
Figure 4 is a comparative bar graph showing load bearing capabilities of various aluminium-base
alloys in a stress corrosion cracking test.
Figure 5 is a transmission electronmicrograph at 51500X showing the fine grain structure
of an alloy of the present invention in the forged condition.
Example 1
[0013] In this example the properties of an alloy of the invention (Alloy C) are compared
with those of a commercial alloy known as 7075 alloy (Alloy A) and of an alloy as
disclosed in European patent application 79 302 232.8 (Alloy B). The compositions
of these alloys are summarised in Table I.
[0014]

Alloy A was purchased as a cast billet of 15.2 cm x 30.5 cm, and was prepared for
forging by extrusion to 4.45 cm diameter round bar at a temperature of about 316°C
and ram speed of 0.25 cm/sec. The extrusion was cut into 63.5 cm lengths, and each
length hot upset at one end to a length of 48.3 cm using a forging temperature of
371°C. The upset forging stock was then reheated to about 316°C and forged in a two
step combined die process to the longeron end tie configuration shown as (a) in Figure
1. Figure 1 shows schematically the various test specimen orientations which are considered.
The forging consists of web b, and flange c; tensile specimens d, and fatigue specimens
e, are shown together with fracture toughness specimen f, stress corrosion cracking
specimen g and fatigue crack propogation specimen h.
[0015] Alloys B and C were prepared by mechanically alloying in a 378.5 litre attritor.at
a 17:1 ball-to-powder weight ratio (B/P). The processing time was approximately 16
hours for Alloy B and approximately 14 hours for Alloy C, at approximately 87 rpm
with a ball charge of 0.95- cm diameter, 52100 steel balls. The process control agent
(PCA) was about 1.5% stearic acid, added incrementally throughout the run. The dynamic
process atmosphere was nitrogen. The powder batches were made from elemental powders
to produce compositions of Alloys B and C of Table I. The powders were heated at about
427°C under vacuum to remove the volatile elements of the stearic acid. The powders
were then loaded into cans, evacuated and maintained for about 6 hours at about 454°C
and 482°C under vacuum for Alloys B and C, respectively. Consolidation was effected
. at about 399°C in an extrusion press at a pressure of about 345 MN/m
2. After removal of the cans, the alloys were extruded to 4.4 cm diameter round bars
at approximately 260°C with a ram speed of 0.51 cm/min. The extrusion was cut into
63.5 cm lengths and forged by the same practice and temperature as used for Alloy
A. The forged products were heat treated under the conditions shown in Table I.
[0016] As both mechanical and corrosion properties were of interest, Alloy A, i.e. the 7075
alloy, was prepared in the T73 overaged temper while the mechanically alloyed Alloys
B and C were prepared in the F(as-forged) and T4 (naturally aged) tempers, respectively.
[0017] The results of room temperature tensile tests obtained from the three alloys in four
orientations are shown in Table II. Examination of these show that Alloy B is considerably
stronger than Alloy A; the yield strength values of Alloy B are significantly higher
than Alloy A while the ductilities are similar. In addition to higher strength, less
variation in strength with changing orientation is observed for Alloy B. It may be
noted that the transverse - tensile values of Alloy A are below "Handbook" value.
However, all three alloys were forged under substantially the same conditions, such
conditions not being optimised. However, still higher and more isotropic properties
were obtained from alloy C. Most significant is the retention of high ductility in
the short transverse (ST) direction. The closeness of % elongation and % RA, indicate
nearly uniform elongation of the Alloy C specimens over their length, while Alloys
A and B exhibit a tendency toward early localised necking.
[0018]
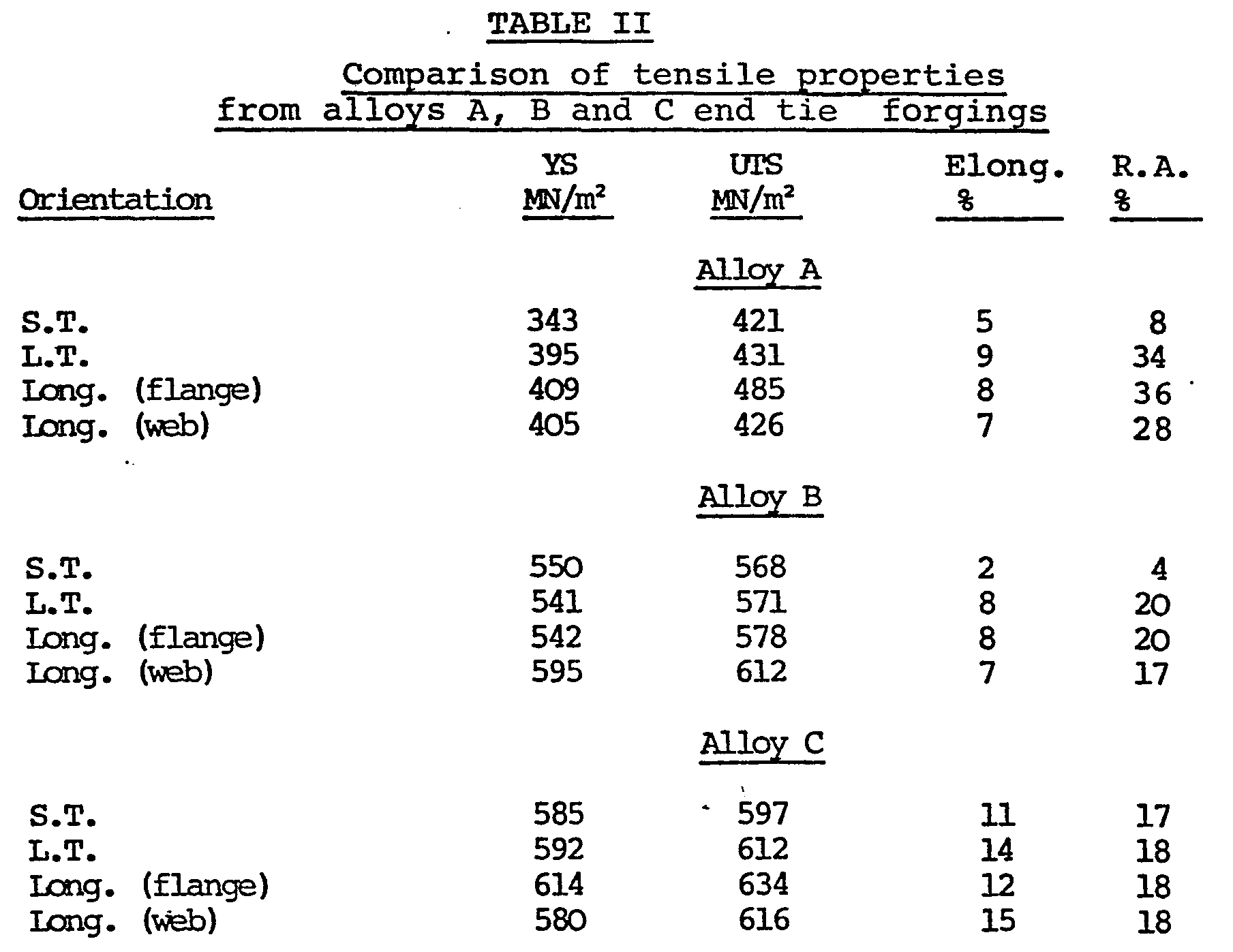
Notched fatigue strength evaluation of the alloys was carried out under severe conditions
using sheet specimens prepared with a stress concentration (K
t) of 5.0 tested in tension-tension loading with a minimum:maximum applied stress ratio
(R) of 0.1. This Alloy B has notched fatigue strength at 10
7 cycles comparable to Alloy A while Alloy C is 10% stronger. The fatigue strength
of Alloy C falls between 59 and 62 MN/m
2 while those of Alloy B and Alloy A fall between 52 and 59 MN/m2.
[0019] The fracture toughness of Alloys B and C was - determined using compact tension specimens
taken from the flange of the forgings and tested in the TL orientation. A value for
Alloy A reported by an independent source was used to compare toughness values of
the mechanically alloyed materials with the Alloy A. Typical test results for Alloys
B and C are given in Table III. These results show that Alloy B has slightly lower
toughness than the value reported for the Alloy A forging. However, the average fracture
toughness value exhibited by Alloy C shows an improvement over both the average values
for Alloy B and the value reported for the Alloy A forging. In fact, the combination
of toughness and strength for Alloy C forgings is believed to exceed that reported
for any other aluminium alloy. Figure 2, compares fracture toughness vs. yield strength
for various aluminium alloys in the forged condition, and gives a further comparison
with a 2000 series alloy designated Alloy X, the information for which was obtained
from Figure 1 of U.S. Patent No. 3,826,688. Projection of the Alloy C-T4 data into
the Alloy X line, clearly reveals the superiority of the alloy of this invention over
that of Alloy X. According to Figure 2, if Alloy X were brought to the same strength
as Alloy C-T4, the toughness of Alloy X would be ohly about 20.9 MN/m
3/2 compared to the value of about
37.
4 MN/m3/2 exhibited by Alloy C-T4. Similarly, if the Alloy X were brought to the same
toughness as Alloy C-T4, the strength of Alloy X would be only about 517
MN/m
2 compared to the 579 MN/m
2 of Alloy C-T4.
[0020]

The fatigue crack growth behaviour of the forged alloys of Table I was determined
from compact tension specimens in the LT orientation. Tests were conducted in dessicated
air at a frequency of 20 Hz and an R ratio of 0.1. Linear regression analysis was
used to reduce the data, as only steady state (stage II) crack growth was observed.
It was found, as shown in Figure 3, that the slowest rate of fatigue crack growth
(da/dn) is exhibited by Alloy C with the rate of crack growth increasing in order
with Alloy A followed by Alloy B.
[0021] The general corrosion resistance of each of alloys A, B and C was evaluated by testing
in an aqueous 3.5% NaCl solution (alternate immersion). Exfoliation resistance was
determined using both Asset and Exco tests. The Asset test was developed by the Navy
in 1972 to assess the exfoliation resistance of 5000 series alloys. The Exco test
(ASTM G34-79) is intended for the Cu-bearing 2000 and 7000 series alloys. The results,
summarised in Table IV, reveal immediately the vastly superior general corrosion resistance
of Alloy B followed by Alloy C which is also significantly better than the Alloy A.
The exfoliation test revealed that both Alloy C and Alloy B resisted exfoliation in
the Exco and Asset test environments, whereas Alloy A exhibited slight exfoliation
in the Exco test. Pitting was also observed in these environments in some cases, as
indicated in Table IV.

[0022] Another significant improvement in corrosion resistance was found by the results
of the short transverse stress corrosion cracking (SCC) tests shown in Figure 4. These
tests were run in accordance with ASTM G44-75 and involved a 10 minute immersion of
a fixed load specimen in an aqueous solution of 3.5% sodium chloride followed by 50
minutes out of the solution. The T73 temper, developed to improve the SCC resistance
of Alloy A, permits loading the alloy to 100% of its yield strength without failure
after 30 days exposure. However, the strength of Alloy A is quite low in this temper,
343 MN/m
2 in this case. The mechanically alloyed materials, on the other hand, are significantly
stronger. Despite their higher strength, these alloys have a dramatically improved
load bearing capability in the SCC environment. Alloy B, for example, resists stress
corrosion attack for at least 30 days when loaded to 440 MN/m', or 80% of its yield
strength. Even greater capability is shown by Alloy C, which survived at least 30
days in the stress corrosion environment when loaded to 585 MN/
M2 or 100% of its yield strength. The SCC resistance of Alloy C reveals a unique combination
of properties attainable only through mechanical alloying.
[0023] The contrast with the reported stress corrosion behaviour of chemically similar 2000
series alloys made by conventional ingot process is significant. For example, in the
T351 temper (a condition not too unlike the T4 temper) 2024 fails in less than 20
hours when loaded to 310 MN/m
2 which is 100% of the reported yield strength for this material.
[0024] Comparison of Young's modulus and density values obtained for each of the test materials
exhibits an additional benefit of the mechanically alloyed materials (Table V). Alloy
B shows a slight increase in elastic modulus and a significant (5.5%) decrease in
density compared to the Alloy A. Alloy C has a density nearly equal to that of Alloy
A, but has an elastic modulus value 5% higher than Alloy A.

[0025] Thus it will be observed that alloy C has an improved combination of properties over
alloy B, both of these having more attractive properties than Alloy A.
[0026] The good properties of the alloys of this invention result, in part, from the combination
of extremely fine grain size, dispersed refractory oxide and carbide particles, and
precipitated intermetallic compound phase. These features are revealed in Figure 5,
a TEM at 51500X. The extremely fine grain size is a consequence of the combination
of the severe mechanical working associated with mechanical alloying and the grain
growth retarding influence of the oxide and carbide particles. A further strengthening
increment is provided by the precipitated intermetallic compound phase.
[0027] A summary of properties of Alloys B and C relative to Alloy A (7075-T73) is given
in Table VI.
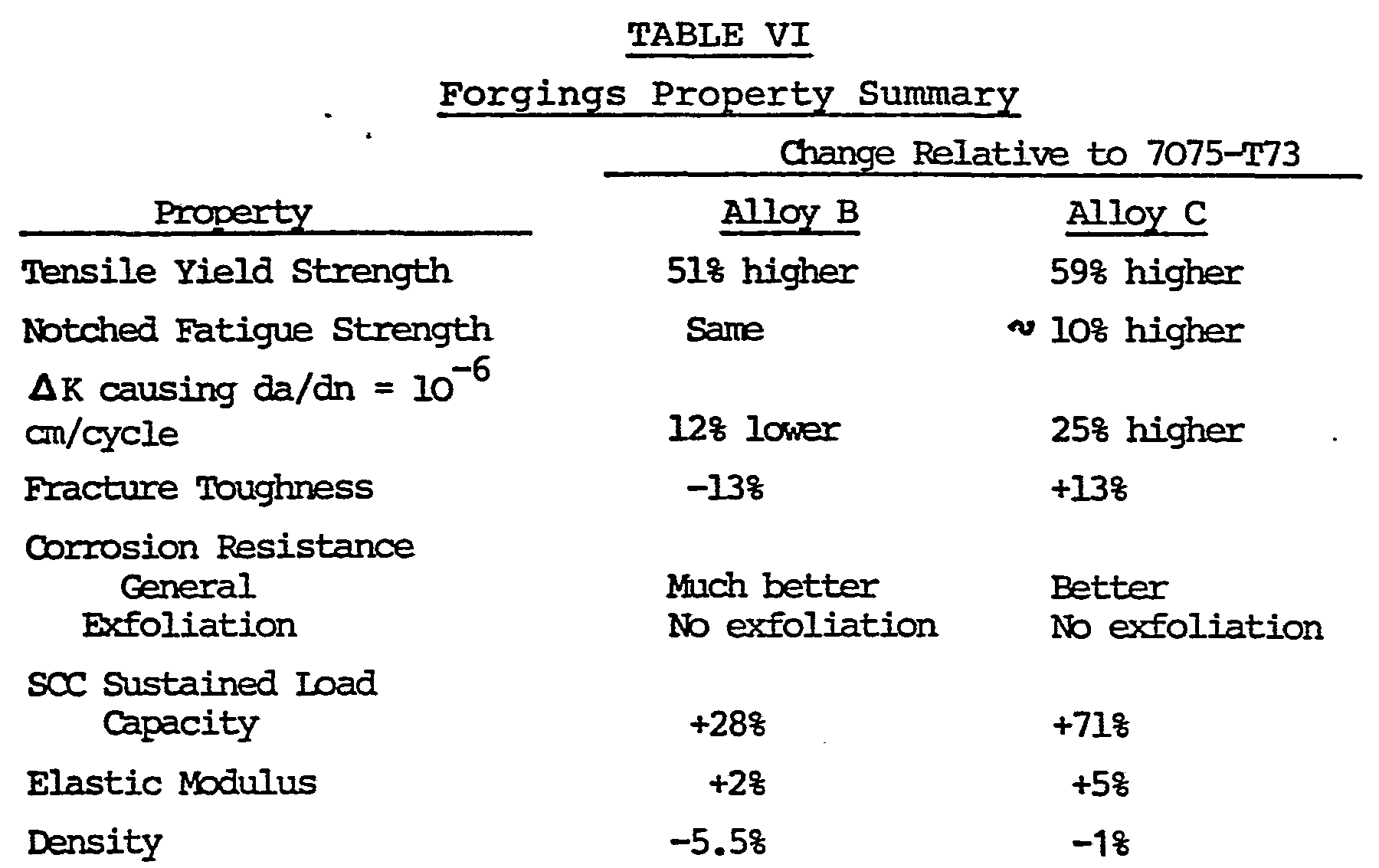
Example 2
[0028] Three alloys of the Al-Cu-Mg system of the invention and also one alloy of the Al-Cu
system were prepared in a 15.1 litre attritor at 20:1 ball-to-powder ratio. The processing
time was approximately 16 h. at approximately 280 rpm with a ball charge of 0.71 cm,
52100 steel balls. The process control agent (PCA) used was 1.5% stearic acid, all
of which was added at the start of the run. The dynamic process atmosphere was nitrogen.
These parameters were selected to to produce powders having comparable properties
of those in Example 1.
[0029] The chemical compositions of the four alloys are given in Table VII. The oxygen and
carbon levels are similar for the four heats. Assuming A1
20
3 and Al
4C
3 are the dispersed species, the volume % dispersoid ranges between 6.3 and 6.6%.
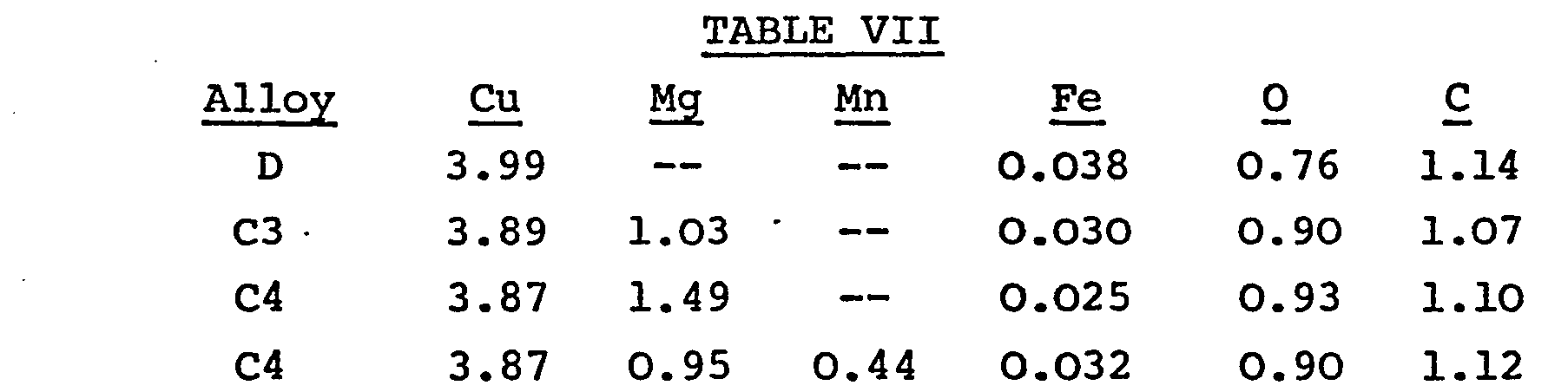
[0030] The mechanically alloyed powder was placed in mild steel cans which were subsequently
degassed. Vacuum degassing was performed in three stages: room temperature evacuation
followed by heating to 315°C for 4 hours under vacuum and finally evacuation for 2
hours. The steel cans were then sealed. Compaction was performed in the extrusion
press against a blank die after a soak of 2 hours at 427°C. The steel cans were then
stripped from the aluminium billets producing a 7.6 cm dia. billet. Extrusion was
performed at 343°C in a 8.9 cm dia. liner after 2.5 h. soak. A 1.6 cm diameter extruded
bar was produced using a 20% throttle setting. Extrusion ram speeds were typically
1.3 to 1.8 cm per sec. ,
[0031] The four alloys were heat treated using three sequence which can be described using
conventional aluminium alloy temper designations:

The heat treatment was not optimized for these studies.
[0032] Metallographic inspection of the attrited powder structures showed them to be quite
uniform. Microscopic analysis of the structures of the consolidated bar was carried
out using a 10% sodium hydroxide solution as etchant. This showed that significant
changes had occurred as a result of heat treatments. The F temper showed coarse aluminium-copper
intermetallic particles throughout the alloy structure. During heat treatment, the
coarse intermetallic particles were dissolved and a more uniform structure obtained.
The structure of the T6 temper was the same as that of the T4 temper. As expected
for the mechanically alloyed materials, grains were unresolvable at magnifications
typical in light microscopy. All four alloys exhibited similar structural changes
as a function of the various tempers. Only differences in the amount and size of the
intermetallic compounds were observed.
[0033] Tensile properties were determined at room temperature, 121°C, 204°C and-316°C.
[0034] The room temperature tensile properties are listed in Table VIII.
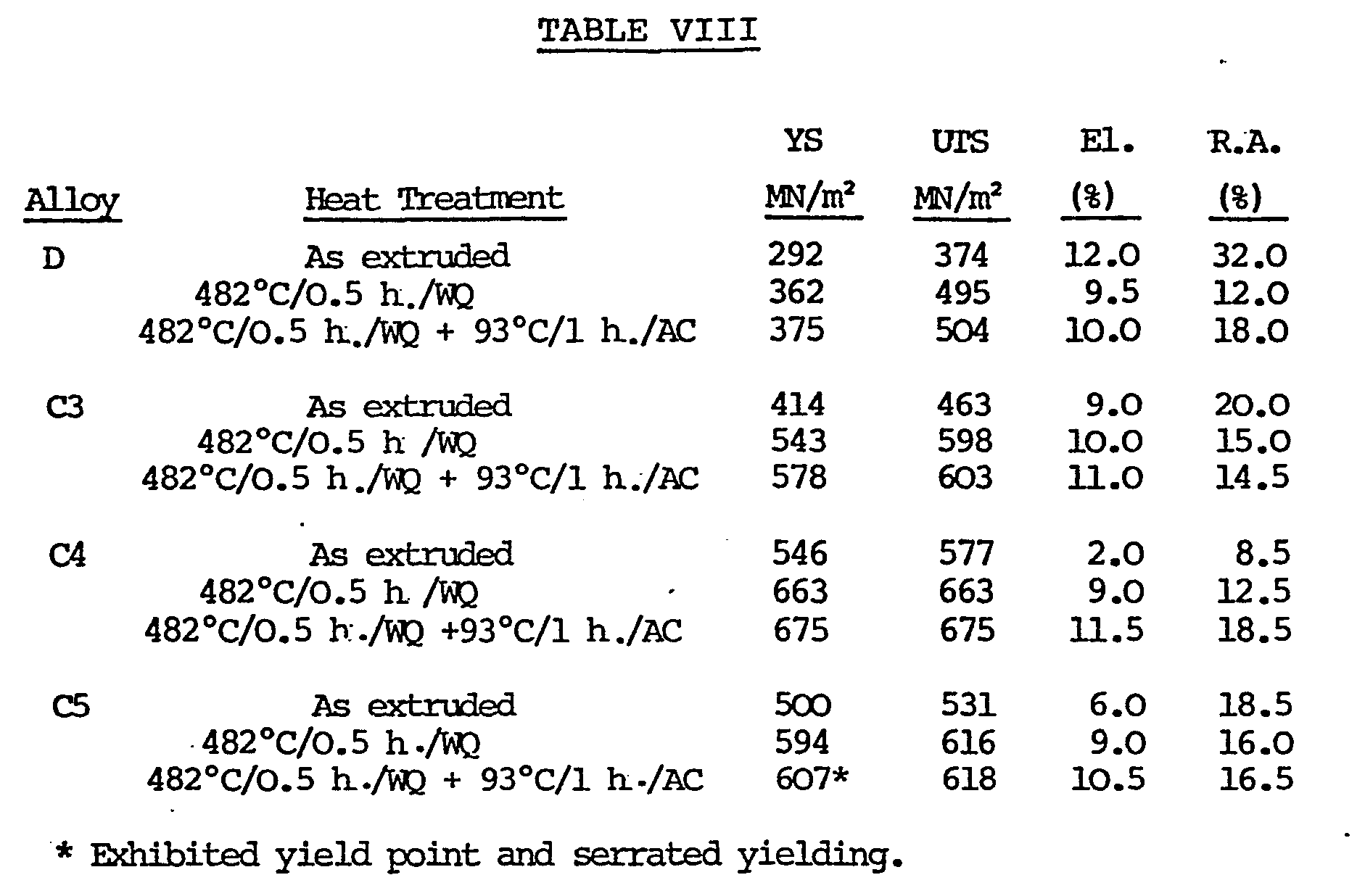
[0035] It will be observed that the effect of heat treatment was essentially the same for
all of the alloys of the invention. The F temper exhibits the lowest strength and
lowest elongation. The T4 temper shows an improvement in strength and elongation and
the T6 temper exhibits the highest strength and ductility. Additions of magnesium
to the Al-4Cu composition result in quite significant property changes. Strength is
significantly increased in all tempers as magnesium content increases from 0 to 1.5%,
while Mg additions .have only minimal effect on ductility in the T4 and T6 tempers.
The addition of 0.5% Mn to the Al-4Cu-lMg alloy provides little benefit to room temperature
properties except in the F temper.
[0036] Elevated temperature tensile properties for the T4 condition are listed in Table
IX..
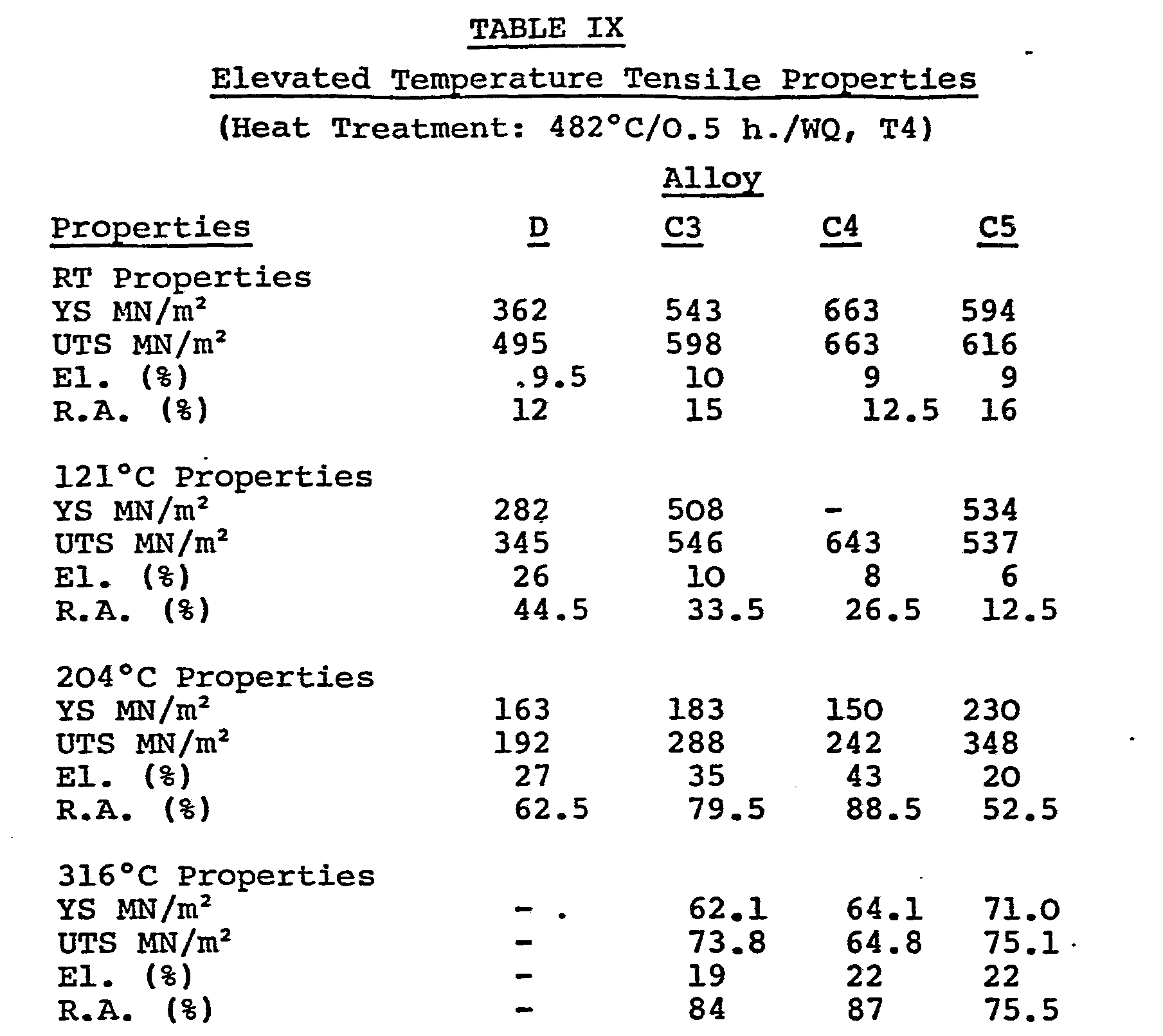
[0037] It will be observed that the benefits of magnesium and manganese additions on tensile
strength are retained up to about 204°C, and that at about 316°C all the alloys have
approximately the same strength. Magnesium additions increase strength at 121°C, thus
the C4 alloy containing nominally 1.5% Mg has a tensile strength of greater than 620
MN/m
2 at 121°C. However alloys C3 and C5, both having nominally 1% magnesium retain a greater
percentage of their room temperature strength at 204°C than C4. Alloy C5, containing
nominally 0.5% manganese, has higher tensile strength than alloy C3 at 204°C.
[0038] Stress rupture screening tests were carried out at 121°C using step loaded specimens
given stress increments of 13.79 MN/m
2 at 24 h intervals. Results are shown in Table X.
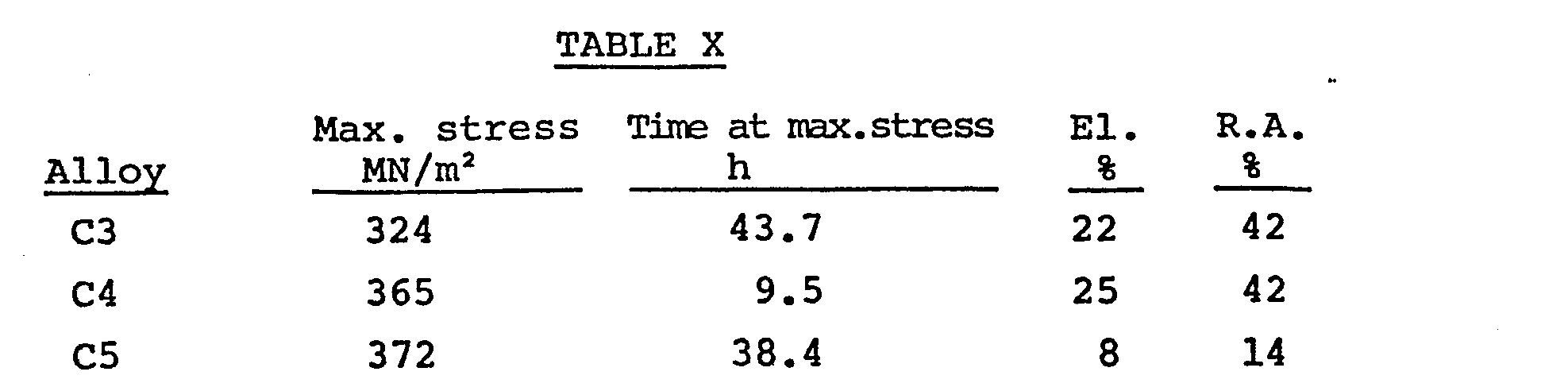
[0039] Although additions of magnesium and/or manganese improve stress rupture properties,
the addition of manganese in C5 however will be observed to be deleterious to ductility.
[0040] In Table XI, an alloy of the invention, C4, is compared with conventional alloys
2024 (Al-4.5 Cu - 1.5 Mg - 0.6 Mn) and 7075 (Al - 1.5 Cu - 2.5 Mg - 5.5 Zn - 0.3 Cr)
and also with a dispersion strengthened mechanically alloyed alloy having the nominal
composition Al-4 Mg.
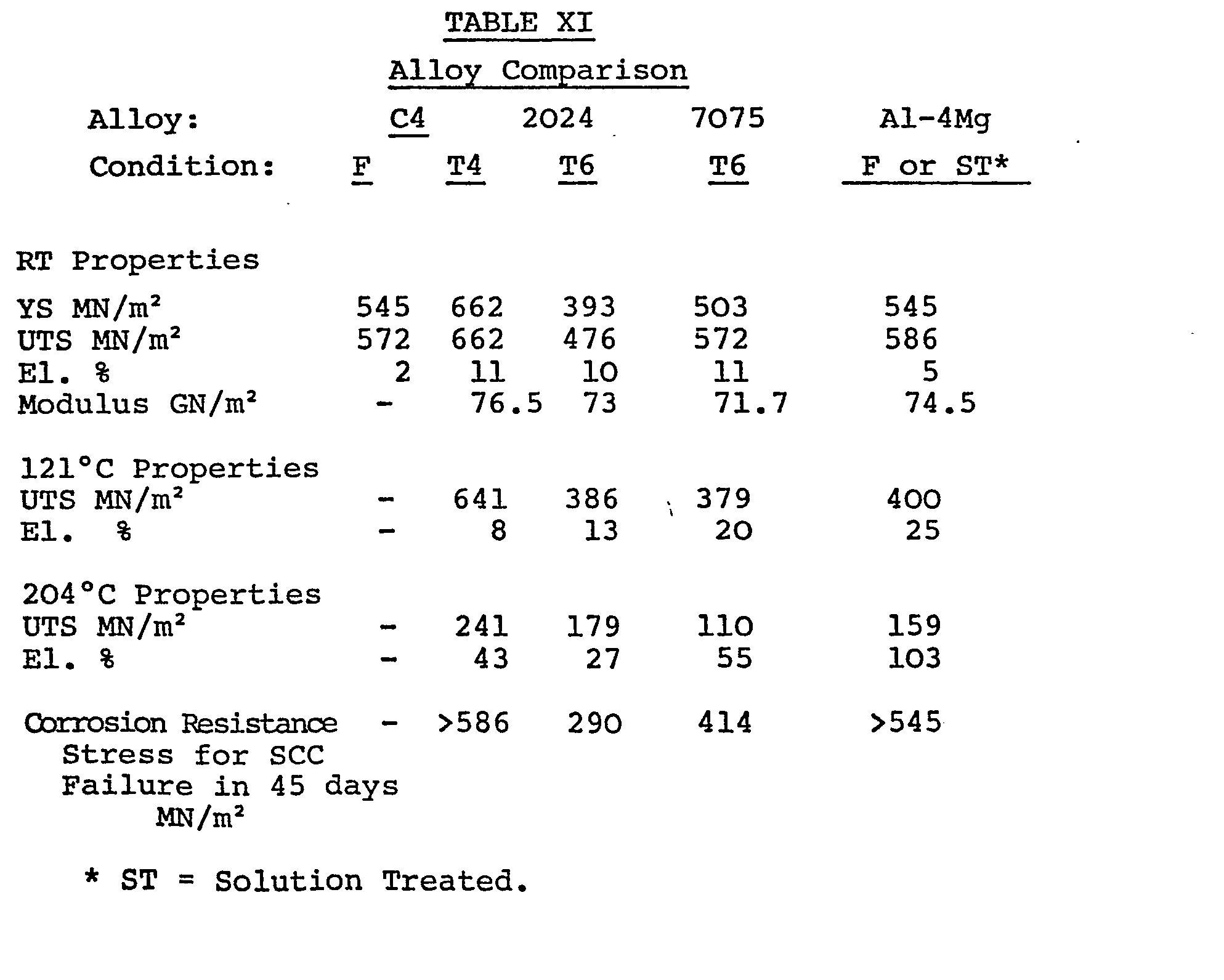
It will be seen that higher RT strength was achieved with alloy C4 at equivalent ductility
level than alloys 2024 and 7075. R.T. strength and ductility are both higher than
those of the Al-4Mg alloy. The strength superiority of alloys of the present invention
extends to temperatures of about 204°C.
Example 3
[0041] Fatigue crack propagation data for other aluminium based alloys, including powder
metallurgically produced alloys X7090 and X7091 has been tabulated from reported data
and is compared with experimentally obtained results on the mechanically alloyed materials
having nominal compositions Al4Cu - 1.5 Mg and Al-4Mg in Table XII.

1. A dispersion-strengthened mechanically-alloyed aluminium based alloy having improved
resistance to stress corrosion cracking comprising 0.5% to 6% copper, 0.5% to 3% magnesium,
0.1% to 2.5% carbon, an effective amount up to 3% of oxygen, up to 1% manganese, up
to 0.5% iron, the balance aluminium apart from impurities and incidental elements,
and containing oxide and carbide dispersoids in an amount of 1% to 10% by volume.
2. An alloy as claimed in claim 1 in which the copper content is in the range 2% to
5% and the magnesium content is in the range 0.5% to 2.5%.
3. An alloy as claimed in claim 1 or claim 2 in which the oxygen content is in the
range 0.4% to 1% and the carbon content is in the range 0.6% to 1.25%.
4. An alloy as claimed in any preceding claim in which the manganese content is up
to 0.4% and the iron content is less than 0.2%.
5. An alloy as claimed in any preceding claim in which the copper content is in the
range 3% to 4.5% and the magnesium content is in the range 1.25% to 2%.
6. An alloy as claimed in any preceding claim in which the total oxide and carbide
refractory dispersoids are present in an amount of from 2% to 7% by volume.
7. A method for the production of an aluminium-based alloy material comprising preparing
a mechanically alloyed alloy powder having a composition as claimed in any one of
claims 1 to 6, consolidating the powder at an elevated temperature to form a substantially
dense material, working the consolidated material at a temperature of 200 to 550°C
and subjecting the wrought product to a solution temperature of 350 to 550°C for from
1/4 to 10 hours.
8. An aluminium-based alloy material producec by a process as claimed in claim 7 and
characterised in the as forged condition by a fracture toughness in the transverse
direction of at least 33 MN/m3/2 when the tensile yield strength in the transverse direction is greater than 551 MN/m2 and a fracture toughness in the transverse direction of at least 49.5 MN/m3/2 when the tensile yield strength in the transverse direction is about 448 MN/m2, and has an elongation in the short transverse direction of at least 5%.