[0001] This invention relates to coal gasification and in particular to recycling tar and
other liquid by-products from the British Gas-Lurgi slagging gasifier such that they
are gasified.
[0002] The Lurgi dry-bottom gasifier and the British Gas-Lurgi slagging gasifier are well
known in the art of coal gasification. They are described, for example in 'The Chemistry
of Coal Utilization' 2nd Supplementary Volume, 1981, published by John Wiley & Son
Inc. In both gasifiers, coal is intermittently supplied at the top through lock-hoppers
to a distributor which spreads the coal continuously and uniformly on to a fixed bed'of
coal and coal-derived solids in a vertical shaft. As it moves downwardly through the
shaft, the coal is first heated, dried and partly de-volatilised in the presence of
hot gases moving upwards from the base of the reactor. In the lower regions of the
bed, the de-volatilised coal )i.e. char) is gasified by reaction with steam and oxygen.
Mineral matter contained in the coal passes through the gasifier and, in the conventional
Lurgi process, is removed as a dry ash at a comparatively low temperature maintained
by the use of excess steam. In contrast, mineral matter is fused to form a mobile
slag in the British Gas development of the process. This slag drains from the fuel
bed, is quenched with water and then discharged as a glassy frit.
[0003] The top part of the fixed bed, where drying and de-volatilisation take place, is
known as the 'de-volatilisation zone' and the lower part, where the coal char reacts
with steam and where other reactions occur, is known as the 'gasification zone'. In
the slagging gasifier, the steam and oxygen are injected through tuyeres and the fierce
reaction zone in front of the tuyeres is known as the 'raceway'. This is where char
oxidation predominates to give the temperatures high enough to fuse mineral matter
and form mobile slag.
[0004] The gasification of coal in either gasifier gives rise to a range of by-product organic
liquids including tar (hydrocarbons more dense than water), oil (hydrocarbons less
dense than water), naphtha (a low boiling-point oil fraction) and a phenolic concentrate.
Apart from the waste of material which would be more valuable converted into gas that
these by-products represent, the consequences of allowing them to accumulate in the
environment are an increasingly important consideration as the contemplated scale
of coal gasification projects enlarges. Thus it is highly desirable to route liquid
by-products back to the gasifier in such a way that they are completely gasified.
[0005] It is a common practice to recycle tars to the top of the bed in fixed bed gasifiers
to reduce dust carry-over. This it does very effectively, but the tar, which has already
survived passage through this part of the gasifier, is distilled from the top of the
bed with little or no decomposition so that the net yield of tar is not reduced.
[0006] Complete tar and oil gasification has been demonstrated by British Gas at its Westfield
Development Centre by injection of these materials via the tuyeres into the raceway
region of the slagging gasifier. Similar injection of naphthas and phenols is expected
to be perfectly practicable and to have the same effect of their being gasified to
extinction. In the raceway the temperatures are so high that the mineral content of
the coal is released as a molten slag which drains into the slag pool below. These
high temperatures also ensure that virtually all of the carbon in the coal undergoes
conversion, leaving no more than a trace in the slag. Recycled organic substances
do not survive here.
[0007] The very serious drawback of this approach, however, is that it significantly inereaes
the oxygen consumption of the gasifier on a basis both of thermal output and, more
evidently, of coal input. This is to be expected because the over-riding requirement
is to maintain temperatures that produce slag of appropriate viscosity to allow slag
tapping by proven techniques.
[0008] The invention seeks to mitigate the disadvantages of increased oxygn consumption
associated with the injection of tar, oils and phenols through the tuyeres of a slugging
gasifier. Accordingly, the invention provides a process for the gasification of coal
in a fixed bed-ash slagging gasifier wherein gasifying agents comprising steam and
oxygen are fed into the bed through tuyeres leading to a raceway located below the
bed and wherein condensible non-aqueous materials produced by the gasification of
coal are recycled to the coal bed characterised in that said materials are recycled
to the lower portion of the bed but above the raceway at a point where the bed temperature
is sufficient to gasify said materials.
[0009] Above the raceway, the turbulence and vigour of combustion give way to gasification
reactions in a more stable region (the gasification zone) composed of coal char particles
moving down the bed in a reasonably uniform and steady pattern in countercurrent flow
to hot gases. Much of the heat released in the combustion zone is carried into this
region as sensible heat by the upflowing gases to support the endothermic reactions:

[0010] The gases are cooled by these reactions and the bed temperature decreases from 1600-1800°C
to about 1000°C as they move upwards, leading to lower reaction rates. Eventually
the gas and char temperatures no longer suffice to support further endothermic reaction
and the gasification processes effectively stop, setting the upper boundary of the
gasification zone. Temperaturis at tie upper gasification zone boundary are significantly
higher in the slagging gasifier than in a dry-bottoom gasifier.
[0011] Drying and the de-volatilisation reations which occur in the top of the bed, causing
further cooling, are completed well above the upper boundary of the gasification zone.
There is, therefore, a substantial region vithin the fuel bed of a slagging gasifier
where temperatures are high enough to ensure that recycled tar, oils and phezols will
react rapidly. When these by-products are injeited into this reion they cannot cool
the raceway zone and do not interfere with slag formation; the need to significantly
increase oxygen consumption is this avoided.
[0012] The products from reaction of recycled by-products with the hot gases depend on the
chosen point of injection. Introduction into the gasification zone will result in
conversion mainly to carbon monoxide and hydrogen, where introduction further up the
bed, at lower temperature, will allow the survival of hydrocarbon gases such as methane.
Injection too far up the bed, however, results i= not all of the liquids being destroyed,
with the conseqtence that the gross liquid recycle rate is increased. Depending on
the precise conditions and the method of inject-on, some part of the liquid injected
is pyrolysed to form a solid carbonaceous deposit, which travels with the char into
the gasification zone to be gasified in the presence of steam.
[0013] It is advantageous to produce hydrocarbons such as methane from the recycled liquid
by-products, particularly in the manufacture of substitute natural gas (SNG), because
this is less endothermic than producing carbon monoxide and hydrogen. There is then
an increase in the gasifier outlet temprature and little or no effect on oxygen consumption.
EXAMPLES
[0014] The invention and the benefits which derive from it are exemplified by the gasification
of a British coal (Rossington) in the slagging gasifier at a gauge pressure of 31
bars and a molar steam/oxygen ratio of 1.3 using oxygen of 98% purity. The relevant
data are presented in Table 1. Comparable data are included for operation without
recirculation of liquid by-products, column (1), and for operation with injection
of these by-products into the raceway zone through the tuyeres, column (2).
[0015] Production of the gas shown in column (1) yields as by-product a mixture of tar,
oil and naphtha which, in total, amounts to 0.066 kg/kg when expressed in relation
to the coal feed on a dry, ash-free (d.a.f.) basis. When this mixture is injected
through the tuyeres, to be gasified in the raceway to give the gas of column (2),
it can be seen that the steam and oxygen comsumptions, in relation to the coal feed,
are increased by rather more than 10%.
[0016] There is an increase in gas yield, of course, but since gasification in the raceway
does not give rise to methane formation there is a slight fall in the product gas
calorific value. The extra oxygen consumption leads to a rise in outlet temperature
of over 50
0C.
Example 1
[0017] This example shows, see column (3), that when liquid by-products are recycled and
injected in accordance with the invention at a point about midway down the fixed bed,
the increase in oxygen consumption required is less than half that necessary when
injection is through the tuyeres. The product gas composition given is that obtained
at about 0.1 kg/kg recycle when the rate of gasification of by-products is 0.066 kg/kg.
That is to say when by-products are gasified at the same rate as they are produced
even though some fraction escapes gasification when it is first recycled.
[0018] As can be seen, the product gas calorific vsalue is raised, leading to greater efficiency
in the manufacture of SNG because less methane has to be made in subsequent methanation
stages. The benefit of making methane in the gasifier, as opposed to downstream, can
be seen as a reduction in downstream equipment and heat losses and in utility demands
associated with external methane formation. The ratio of methane made directly in
the gasifier to the total quantity that it is theoretically possible to make from
the product gas gives a first measure of this benefit. This ratio, for the product
gas shown in column (3) of Table 1, amounts to 31%. The comparable values without
recirculation and with injection through the tuyeres, columns (1) and (2), are 24%
and 23%.
Example 2.
[0019] In this second example, virtually complete gasification of recycled by-products in
one pass is achieved by moving the point of injection further down the bed so that
it is above but close to the upper gasification zone boundary. This gives a very low
oxygen consumption see column (4), both in relation to the coal gasified and more
significantly on a thermal output basis. The high methane content of the product gas,
amounting to 40% of what can theoretically be made, will lead to a lower methanation
duty and hence a high coal-to-SNG efficiency. A further improvement in efficiency
will result from the higher outlet temperature, which will increase steam production
in the gas cooling system.
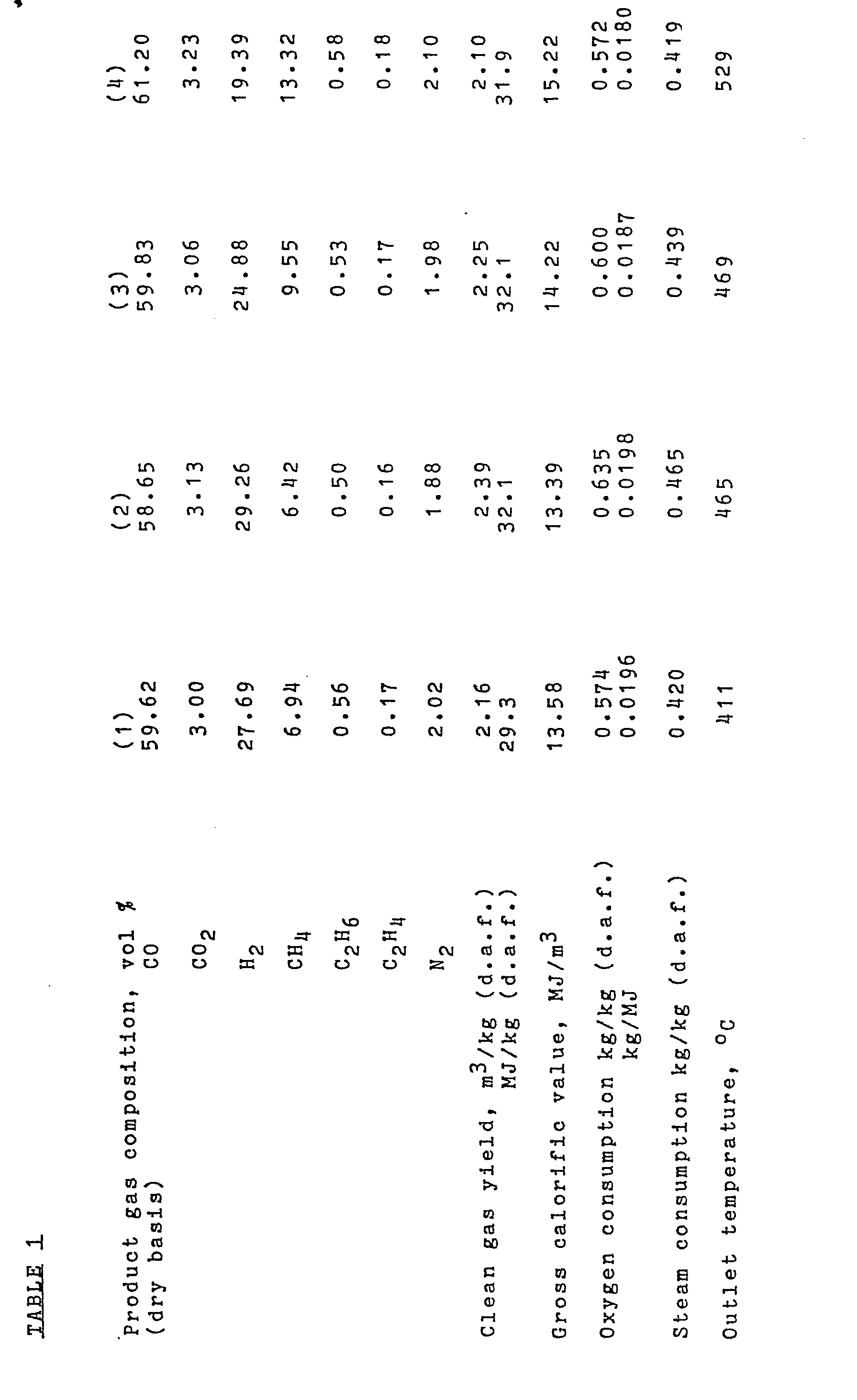