[0001] This invention relates to fire retardant composite fibres and a process for producing
them. More particularly it relates to polyolefin composite fibres comprising two kinds
of polyolefin polymers having - different melting points and having the same or different
fire retardants in the two components.
[0002] Polyolefin composite fibres have superior heat adhesive properties and also physical
and chemical properties and further are of light weight and cheap; hence they have
been used as a fibre material for non-woven fabrics in various applications fields.
For example, they are suitable as a material for thin products such as fabric bases,
hygienic materials, napkins, paper diapers, and for thick products such as quilting
goods, various felts, filters, fibre-shaped products, materials for public works,
etc. In general, fire retardant properties have been used indoors for fibre materials..
As a process for making polyolefin fibres fire retardant, there is first a process
of adding a fire retardant to raw material polymers, followed by spinning. However,
addition of fire retardants in a large amount raises various problems of reduction
in productivity and product quality, etc, such as obstacles at the time of spinning
and stretching eg fibre breakage, reduction in strength, rough fibre surface, reduction
in heat adhesive properties, etc. These problems are notable in the case of thin fibres
of 6 d/F or.less; and particularly in the case of composite fibres, they notably appear
on the side of lower melting component having a lower viscosity. Further, beside the
above-mentioned process, processes of coating fibres with a fire retardant or blending
fire retardant fibres have been known, but in the case of these processes, since shaped
fibres are treated by post-processing, the steps are complicated, the quality fluctuation
is large and the cost is high; hence these processes are not practical.
[0003] The present inventors have made various studies on such problems and found that when
the higher melting and lower melting components of composite fibres respectively contain
a fire retardant having a decomposition temperature higher than the melting points
of the respective components by 100°C or more and also having a particle size of 62
microns or less, it is possible to produce superior fire retardant and heat adhesive
composite fibres of a small denier having a relatively large amount of the fire retardant
blended also with the lower melting component, with a good spinnability.
[0004] One aspect of the present invention resides in:
fire retardant composite fibres comprising a fibre-formable polyolefin polymer as
a higher melting component and a polyolefin polymer having a melting point lower than
that of the higher melting component by 10°C or more, as a lower melting component,
and having a fire retardant contained in the respective components,
[0005] which composite fibres are characterized in that a fire retardant having a decomposition
temperature higher than the melting points of the respective components by 100°C or
more and also having a particle size of 62 microns or less, is contained in the respective
components in an amount of 3 to 15% by weight, and the total of the respective amounts
of the fire retardant contained in . the whole of the composite fibres is 5 to 10%
by weight.
[0006] Another aspect of the present invention resides in:
a process for producing fire retardant composite fibres by using a fibre-formable
polyolefin polymer having a melting point lower than that of the higher melting component
by 10°C or more, as a lower melting component, blending a fire retardant with the
respective components and subjecting the resulting components to melt-composite-spinning
followed by stretching,
which process is characterized by blending a fire retardant having a decomposition
temperature higher than the melting points of the respective components by 100°C or
more and also having a particle size of 62 microns or less, with the respective components,
so as to give an amount of the fire retardant of 3 to 15% by weight, and also so as
to give the total of the respective amounts of the fire retardant contained in the
whole of the composite fibres, of 5 to 10% by weight; melting the resulting components
at a temperature lower than the respective decomposition temperatures of the fire
retardant contained in the respective components to subject them to composite spinning.
[0007] In general, in the case of composite fibres, it is possible to impart various specific
features to their crimpability and adhesive properties, depending on the combination
manner of composite components, and it is also possible to use the fibres in application
fields corresponding thereto. Composite fibres of the present invention also have
various application fields, and it is particularly preferable for them to be a side
by side or a sheath and core type, so that the lower melting component can have a
percentage fibre-cross-sectional circumference of 50% or higher, thereby to provide
the composite fibres provided with heat adhesive properites by way of the lower melting
component. In this case, the composite ratio (higher melting component: lower melting
component) is preferably in the range of 5:5 to 3:7 in view of the thickness of the
lower melting component in the fibre section.
[0008] The higher melting component is preferably polypropylene or copolymers composed mainly
of propylene having a fibre formability. The lower melting component is preferably
polyethylene, ethylene-vinyl acetate copolymers, abbreviated to EVA, having a vinyl
acetate content of, eg 1 to 10% by weight, their saponified products., blends of polyethylene
with EVA or saponified EVA.
[0009] The respective contents of the fire retardant in the high melting component and the
lower melting component of the composite fibres are suitably in the range of 3 to
15% by weight, and the total content of the fire retardant in the whole of the composite
fibres is suitably in the range of 5 to 10% by weight. If the contents of the fire
retardant are lower than the above ranges, the fire retardant effectiveness is small,
and if.the contents exceed the above ranges, the spinnability of the fibres becomes
inferor thereby to make their production difficult and degrade their quality.
[0010] The fire retardant used in the present invention may be suitably selected from known
materials. Of these, organic halogen compounds are preferable, and concretely preferable
examples thereof are decabromodiphenyl oxide (decomposition temperature: 350°C; the
temperatures inside the following parentheses likewise indicating decomposition temperature),
perchloropentacyclododecane (650°C), ethylenediamine dihydrobromide (355°C), hexabromobenzene
(340°C), 2,2-bis[4-(2,3-dibromo- propoxy)-3,5-dibromophenyl]propane (270°C), tris(2,3-dibromopropyl)phosphate
(260°C), bis[3,5-dibrom-4-di- bromopropyloxyphenyl]sulfone (280°C), etc.
[0011] These fire retardants are also preferably used in admixture with Sb
20
3 in a ratio of retardant to Sb
20
3 in a ratio of 1.5:1 to 3:1.
[0012] The fire retardants used in the present invention have a particle size of 62 microns
or less. If the fire retardants contain particles larger than 62 microns, this causes
reduction in their productivity or quality, due to, eg, clogging of spinning nozzle,
fibre breakage at the time of stretching, forming of rough surface on fibres which
lowers their heat adhesive properties.
[0013] The fire retardants having a particle size of 62 microns or less may be obtained
by grading commercially available fire retardants by way of a known method such as
a precipitation method, cyclone method, etc, and as a simpler method, by grading them
through sieves indicated in JIS
Z8801 (nominal diameter 62 or 53 microns).
[0014] The fire retardant composite fibres of the present invention may be produced according
to a conventional melt-composite-spinning process and the apparatus employed may also
be a conventional apparatus. As an example, a powdery raw material polymer having
a fire retardant mixed is melted and extruded by a melt-extruder and the resulting
melt is passed through a temperature- controlled heating zone to heat it to a definite
temperature (hereinafter often referred to as spinning temperature). The melting and
temperature adjustment of the polymer are carried out in separate passages for each
of the commosite components, and the respective composite components each having a
definite temperature are fed in a composite ratio into spinning nozzles through the
holes of which they are composite-spun. In the present invention, for the respective
composite components, there is used a fire retardant having a decomposition temperature
higher than the melting piont of the components by 100°C or more, preferably higher
than the spinning temeratures by 40°C or more, thereby to prevent the decomposition
and consumption of the fire retardant at the time of spinning. Unstretched filaments
obtained by the composite spinning are stretched in an appropriately chosen ratio
depending on application fields. Usually the stretching is carried out very often
in a stretch ratio of 4 or more. As the stretching temperature, temperatures in the
range of from the softening point of the lower melting component up to a temperature
lower than the melting point by 10°C may be employed, but the effect of the extent
of the stretching temperature upon the fire retardant properties is little.
[0015] According to the process of the present invention, it is possible to produce composite
fibers containing a large amount of a fire retardant and having a small fineness,
with small frequencies of fiber breakage due to clogging of spinning nozzles and exchange
of spinning die, in a stabilized manner and over an extremely long term. Further,
the fire retardant composite fibers of the present invention are not only provided
with fire retardant properties, but also, in spite of a large amount of fire retardant
contained therein, have a smooth surface and superior heat adhesive properties.
[0016] The present invention will be further described by way of Examples and Comparative
examples. The terms and testing methods employed in these examples are as follows:
Particle size of fire retardant: this refers to the nominal dimension of meshes of
standard sieves (JIS Z8801) employed for the grading, and means the largest particle
size of the fire retardant.
[0017] Spinnability: this is classified by the number of fiber breakages per hour.
o: once or less, Δ: twice, x: three times or more. Life of spinning nozzle: this is
classified by the exchange interval of spinning nozzle.
o: 40 hours or longer, Δ: 20 to 39 hours,
x: shorter than 20 hours. Adhesive strength: relative value of the adhesive strength
of a sample non-woven fabric to its blank (a non-woven fabric prepared in the same
manner as in the case of the sample except that it does not contain any fire retardant).
o: more than 90%, A: 70 - 90%, x: less than 70%. Rough surface: the number of filaments
having a rough surface among 100 filaments as observed by a microscope.
o: 2 filaments or less, Δ: 3 - 9 filaments, x: 10 filaments or more
[0018] Content of fire retardant: Sb
20
3 is regarded as an additive other than fire retardants.
[0019] Fire retardant:
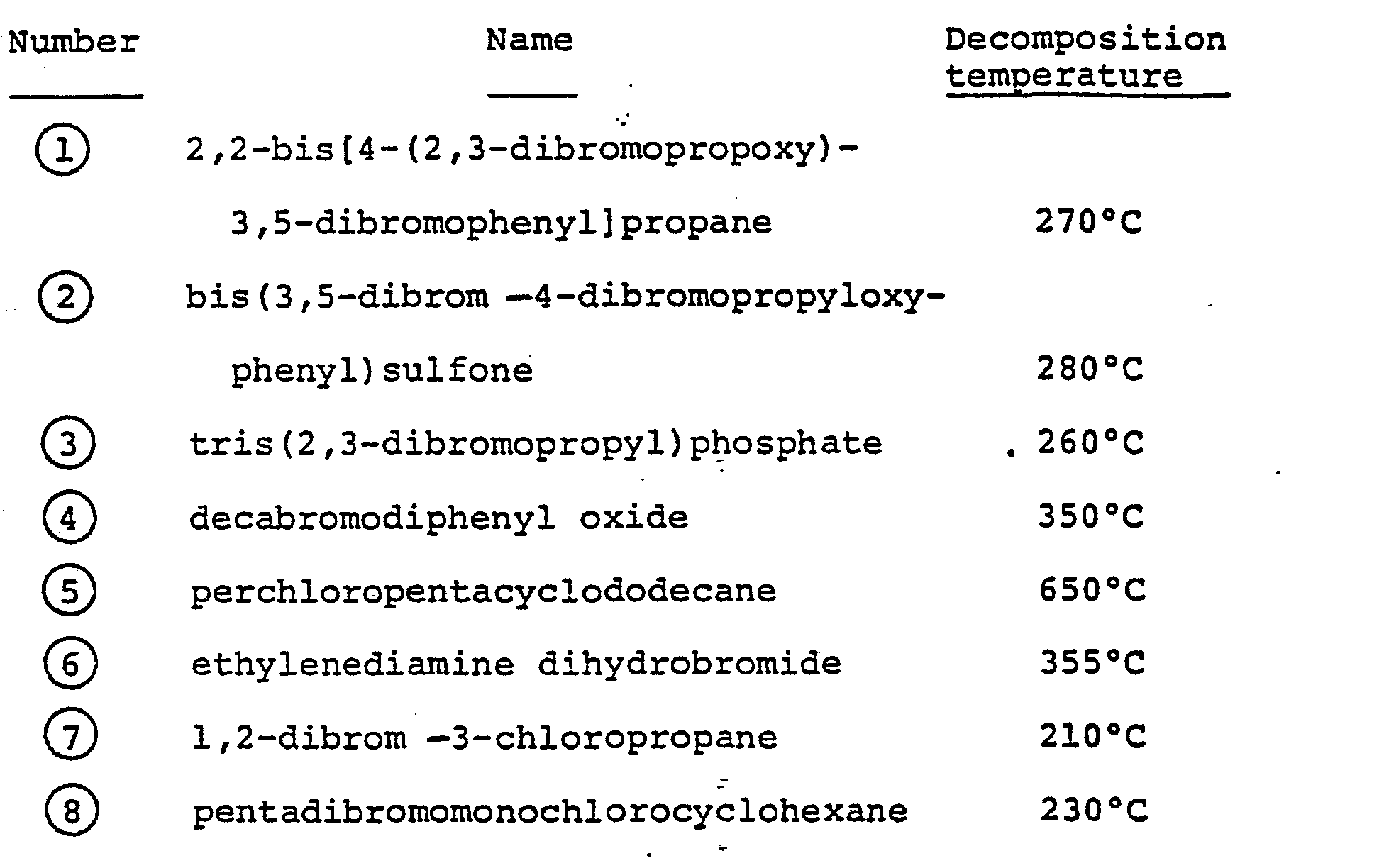
[0020] Combustion test (JIS method): method according to JIS L1091, Al (45° microburner).
[0021] Combustion test (match method):
A sheet of a non-woven fabric was cut into a test piece of 3 cm long and 20 cm wide
in the fiber direction. The resulting piece is then fixed so as to make an angle of
30° against the vertical surface and contacted with a flame of a match piece at the
lower end of the piece from therebelow; till the sample piece catches the flame, and
during the match piece is burnt, the lower end of the sample piece is burnt and the
flame rises and is driven upwards from the lower end; just after the test piece has
caught the fire, the match piece is drawn off, and the flame-remaining time is measured.
Thus a sheet having a time of 5 seconds or shorter was defined as having passed the
test, and that having a longer time was defined as failure.
Examples 1 - 3 and Comparative examples 1 - 4
[0022] As a lower melting component, a polyethylene (PE) having a melt flow rate (MFR) of
20 (according to JIS K7210, condition 4) and a melting point of 130°C, and as a higher
melting component, a polypropylene (PP) having a MFR of 4 (according to JIS K7210,
condition 14) and a melting point of 160°C, were used. A fire retardant (decabromodiphenyl
oxide) having passed through a definite sieve as indicated in the Table shown later,
in definite amounts relative to the PE and PP, respectively, as indicated in the Table,
and Sb
20
3 in
1/
2 of the respective amounts of the fire retardant were added to the PE and PP, separately.
Composite spinning was then carried out in a composite ratio of 1:1, at a spinning
temperature on the PE side of 230°C and at that on the PP side of 300°C to obtain
unstretched side-by-side composite filaments having percentages fiber-cross-sectional
circumference of the._PE component of 78 to 85%. These filaments were stretched to
4 times the original lengths and cut to obtain staple fibers of 18d/f (deniers per
filament)
x64 mm, which were then carded to prepare a web of 2
50 g
/m2.
[0023] This web was subjected to heat treatment at 140°C for 5 minutes to obtain a sheet
of non-woven fabric of 15 mm thick, partially adhered on the PE side. This sheet was
allowed to cool in a desicator for 3 - 4 hours, followed by carrying out combustion
test according to the above JIS method to measure flame-remaining time (seconds) and
carbonized area (cm
2). Further, the same sheet of non-woven fabric was subjected to the above combustion
test according to the match method. The results of blending of fire retardants, spinning
test and combustion tests are shown in the Table.
[0024] When Examples 1 and 2 are compared with Comparative examples 1 and 2,and Example
3 is compared with Comparative examples 3 and 4, even if the contents of a fire retardant
in the whole of the fibers are the same, if the fire retardant is contained only in
an amount less than 3% inside one of the composite components, the fire retardant
effectiveness is inferior, and this is remarkable particularly in the evaluation according
to the match method. Further, if the fire retardant is contained in an amount exceeding
15% inside one of the composite components, the spinning nozzle life becomes shorter
and also the frequency of fiber breakage increases; hence such amount is also undesirable.
Examples 4 and 5 and Comparative example 5 - 7
[0025] As a lower melting component, an ethylene-vinyl acetate copolymer (EVA) having a
melting point of 110°C, a content of vinyl acetate component of 5% and a MFR of 25
(according to JIS K7210, condition 2) was used, and as a higher melting component,
a polypropylene (PP) having a MFR of 4 was used. A blend of perchloropentacyclododecane
as a fire retardant to Sb
20
3 in a ratio of 2:1 was added in a definite amount to the PP and a blend of bis(3,5-dibrom
-4-dibromopropyloxyphenyl)sulfone to Sb
20
3 in a ratio of 1.5:1 was added in a definite amount to the EVA, as indicated in the
Table. Composite spinning was then carried out in a composite ratio of 1:1 at a temperature
of the lower melting component of 200°C and at that of the higher melting component
of 280°C to obtain unstretched filaments which were then stretched to 4 times the
original length and cut to prepare staple fibers (6d/f × 64 mm) of sheath and core
type composite fibers having a percentage fiber-cross-sectional circumference of the
lower melting component of 100%, from which a sheet of non-woven fabric was prepared,
followed by subjecting it to a combustion test as in Examples 1 and 2 to evaluate
its fire retardant properties. The results are shown in the Table.
[0026] When Examples 4 and 5 are compared with Comparative examples 5 and 6, it can be seen
that if the particle size of the fire retardant exceeds 62 microns, spinnability and
fiber quality become inferior, and if the spinning temperature is equal to its decomposition
temperature, spinnability and fiber quality also become inferior due to a generated
gas. Further it can be seen from Comparative example 7 that even if the contents of
a fire retardant in the whole of the fibers are the same, if the content of a fire
retardant contained in one of the composite components is less than 3%, the fire retardant
effectiveness is reduced.
Examples 6 and 7 and Comparative examples 8 - 11
[0027] As a lower melting component, a polyethylene (MFR: 10) (PE) was used and as a higher
melting component, a polypropylene (MFR: 8) (PP) was used-Blends of tris(2,3-dibromopropyl)phosphate,
1,2-dibrom -3-chloropropane or pentadibromomonochloro- cyclohexane as a fire retardant,
each in a definite amount, to Sb
20
3 in an amount in a ratio of the fire retardant to Sb
2O
3 of 3:1 were respectively added in a definite amount to PE, while a blend of ethylenediamine
dihydrobromide to Sb
20
3 in a ratio of 2:1 was added in a definite amount to PP, as indicated in the Table.
Composite spinning was then carried out at a temperature on the lower melting component
side of 210°C and at that on the higher melting component side of 300°C, in a composite
ratio of l:l to obtain unstretched filaments which were then stretched to 4 times
the original length and cut to obtain staple fibers of side by side composite fibers
(3d/f x64 mm) having a percentage fiber-cross-sectional circumference of the lower
melting component of 49 -50%. A sheet of non-woven fabric was prepared from the staple
fibers as in Examples 1 and 2 to evaluate the fire retardant properties. The results
are shown in the Table.
[0028] As apparent from these results, in the case where the fineness of fibers is small,
the particle size of fire retardant has a great influence upon spinnability (see Comparative
example 8 and 9); if a fire retardant is contained in the respective composite components
in an amount of 12% (less than 15%) (the content of the fire retardant in the whole
of the fibers being 12%), the spinnability and fiber quality are both inferior (see
Comparative example 11); and if a fire retardant having a decomposition temperature
equal to spinning temperature is used, spinning is impossible at all (see Comparative
example 10).
[0029]
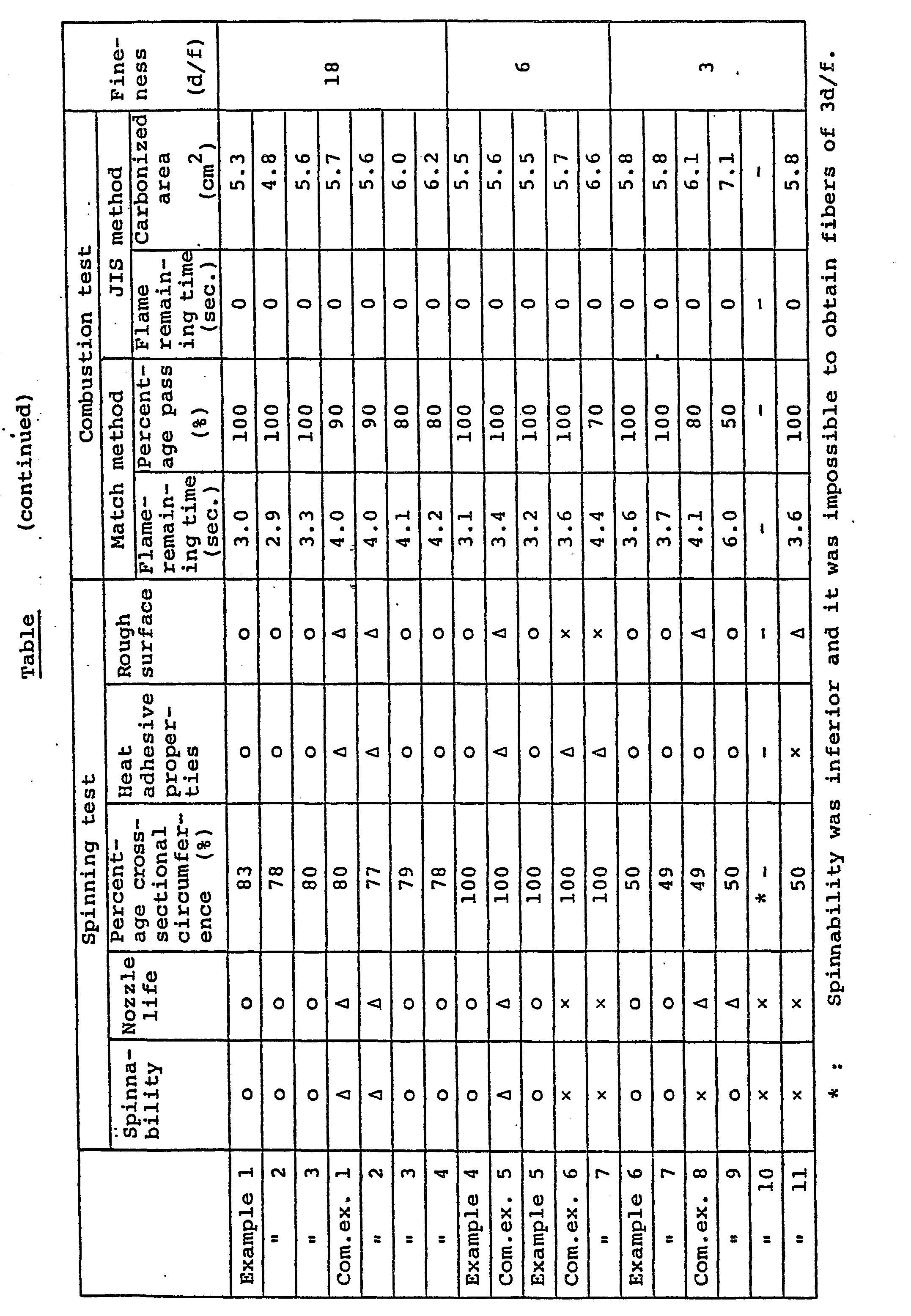