BACKGROUND OF THE INVENTION
FIELD OF THE INVENTION
[0001] The present invention relates to a novel Ni-base alloy member, particularly an Ni-base
alloy member suitable for use as material of springs and bolts used in nuclear reactors,
as well as a method of producing the same.
DESCRIPTION OF THE PRIOR ART
[0002] Hitherto, springs used in nuclear reactors have been produced by a process which
has the steps of forming the spring from a blank, subjecting the formed spring to
a solution heat treatment, effecting a cold rolling at a working ratio of 30% and
then subjecting the rolled spring to an aging treatment. In this process, sufficiently
high mechanical strength at high temperature and a superior spring property, both
of which are essential requisites for the springs used in nuclear reactors, are ensured
by the steps of cold working and subsequent aging treatment. Unfortunately, however,
no specific consideration has been made in this conventional process in regard to
the resistance against stress corrosion cracking (referred to as "SCC", hereinunder)
at crevice, which is a practical problem encountered when the springs are applied
to actual apparatus.
[0003] The springs, particularly springs for nuclear reactors such as expansion spring incorporated
in the control rod drives of a boiling water reactor (BWR), are often used in places
where crevices exist under application of high level of stress. The countermeasure
against SCC, therefore, is essential for such springs.
[0004] Currently, a material called "inconel x750" (commercial name) having a superior strength
and corrosion resistance is most broadly used as the material of springs intended
for use in nuclear reactors. In most cases, the spring blank formed from this material
is subjected to a cold working at working ratio of 30 to 40% after having been subjected
to a solution heat treatment, and then subjected to a direct aging treatment. The
cold working after the solution heat treatment is conducted for giving a final shape
to the spring. On the other hand, the aging treatment following the cold working contributes
to the improvement in the spring property and strength at high temperature essential
for the springs used in nuclear reactors. However, although the cold working at working
ratio of 30 to 40% is conducted between the solution heat treatment and the aging
treatment, no enough discussion has been made as to whether this cold working at working
ratio of 30 to 40% is effective for the improvement in the resistance to crevice SCC
which imposes a serious problem when the springs are put into practical use.
[0005] Japanese Patent Application Laid-Open No. 69517/79 mentions about the intergranular
corrosion in solid solution hardening alloy but does not mention at all about the
SCC resistance of precipitation hardening alloy. Unlike the solid solution hardening
alloy, the- precipitation hardening alloy does not exhibit any specific relationship
between the crevice SCC suscep- . tibility and the intergranular corrosion susceptibility.
SUMMARY OF THE INVENTION
OBJECT OF THE INVENTION
[0006] Accordingly, an object of the invention is to provide an Ni-base alloy member having
a superior SCC resistance, as well as a method of producing the same, thereby to overcome
the above-described problems of the prior art.
STATEMENT OF THE INVENTION
[0007] Under this circumstance, the present inventors have conducted extensive experiments
in which the working ratio of the cold working executed between the solution heat
treatment and the aging treatment was varied to investigate how the crevice SCC resistance
is influenced by the cold working ratio, approaching from two aspects: namely, a constant
strain test with crevice in pure water of high temperature and pressure and metallographic
observation of structure. At the same time, similar investigation was applied also
to the condition of aging treatment (direct aging and two-stepped aging). As a result,
the following facts were newly found by the inventors through the experiments.
[0008] (1) A cold plastic working at working ratio of 10 to 30%, executed between the solution
heat treatment and the direct aging treatment, exhibits a large crevice SCC susceptibility.
However, the crevice SCC resistance is increased when the cold plastic working is
conducted at a working ratio of 40%. It proved also that this alloy has precipitate
of discontinuous and granular Cr carbide in the grain boundary. In contrast, the conventional
process increases the SCC susceptibility due to continuous precipitate of Cr carbide
in the grain boundary. Therefore, the cold working ratio should be not smaller than
40% in terms of reduction of cross-sectional area.
[0009] (2) A cold plastic working executed at a working ratio of 10 to 20% between the solution
heat treatment and two-stepped aging treatment exhibits a remarkable crevice SCC susceptibility.
The crevice SCC susceptibility, however, is drastically decreased when the working
ratio of the cold plastic working is increased beyond 25%. In this case, the relationship
between the cold plastic working ratio and the crevice SCC susceptibility can easily
be judged through metallography. Namely, while an apparent primary recrystallization
is observed in the case of the cold plastic working at high working ratio (25% or
higher) in which the crevice SCC susceptibility is extremely small, no primary recrystallization
is found in the case of cold plastic working conducted at small working ratio (10
to 20%) in which the crevice SCC susceptibility is large. From this fact, it is assumed
that the mechanism of crevice SCC in high temperature water occurring in the material
subjected to two-stepped aging treatment is different from that of crevice SCC occurring
in the material subjected to a direct aging treatment. More specifically, it is understood
that the crevice SCC in high temperature water occurring in material treated by two-stepped
aging is closely related to the behaviour of the apparent primary recrystallization,
rather than to the depletion of Cr due to the precipitation of Cr carbide. The apparent
primary recrystallization is actually a decomposition of the matrix into a Widmanstatten
type or a dendritic type structure containing Eta phase (Ni
3Ti). Such a structure exhibits a high SCC resistance. In the structure obtained through
the conventional process, however, no primary recrystallization grains are observed,
and further the Eta phase is precipitated in columnar form along the grain boundary
and it is surrounded by precipitate free zone due to depletion of the elements consumed
for formation of Eta phase. The structure obtained through the conventional process,
therefore, exhibits a low SCC resistance.
[0010] The present invention has been accomplished on the basis of the newly found facts
as explained hereinabove.
[0011] According to one aspect of the invention, there is provided an Ni-base alloy member
superior in stress corrosion cracking resistance made of an alloy consisting essentially
of, by weight, 14 to 25% of Cr, not greater than 30% of Fe, 0.2 to 2% of Al, 0.5 to
3% of Ti, 0.7 to 4.5% of Nb and the balance substantially Ni, characterized in that
the alloy exhibits stress corrosion cracking depth of not greater than 200pm when
subjected to pure water of 288°C under a pressure of 86
Kg/cm
2 and having a dissolved oxygen content of 8 ppm, for 500 hours at a strain of 1%.
[0012] According to another aspect, there is provided an Ni-base alloy member made of an
alloy consisting essentially of, by weight, 14 to 25% of Cr, not greater than 30%
of Fe, 0.2 to 2% of Al, 0.5 to 3% of Ti, 0.7 to 4.5% of Nb and the balance substantially
Ni, wherein said alloy has a structure containing discontinuous granular precipitate
of Cr carbide along the grain boundary or an apparent primary recrystallization structure
which precipitates in Eta phase Widmanstätten form or in dendritic form.
[0013] Preferably, the Ni-base alloy member of the invention is made of an alloy consisting
seentially of, by weight, 14 to 20% of Cr, not greater than 10% of Fe, 0.4 to 1.0%
of Al, 2 to 3% of Ti, 0.7 to 1.5% of Nb and the balance substantially Ni, and having
a structure containing discontinuous granular precipitate of Cr carbide along the
grain boundary or an apparent primary recrystallization structure which precipitates
in Eta phase Widmanstatten form or in dendritic form.
[0014] The Ni-base alloy member of the invention is produced by a process having the steps
of subjecting the alloy of above-mentioned composition to a solution heat treatment,
effecting a cold plastic working on the alloy at a reduction of cross-sectional area
of not smaller than 40% and effecting a direct aging treatment on the alloy at a temperature
of between 650 and 750°C. Preferably, the cold plastic working ratio ranges between
60 and 70% in terms of reduction of cross-sectional area.
[0015] The Ni-base alloy member of the invention can be produced also through a process
having the steps of subjecting the alloy of the above-mentioned composition to a solution
heat treatment, effecting a cold plastic working on the alloy at a reduction of cross-sectional
area of not smaller than 25% and subjecting the alloy to « a two-stepped aging treatment
consisting of an aging at 800 to 950°C and another aging at 600 to 750°C. The cold
plastic working ratio preferably ranges between 40 and 70% in terms of reduction of
cross-sectional area. This process affords an advantage in that the working ratio
can be made smaller than that in the first- mentioned process.
[0016] Hereinunder, an explanation will be made as to the reasons of numerical restrictions
imposed on the contents of the components.
[0017] For attaining a sufficiently high SCC resistance, the Cr content should be 14% at
the smallest, but any Cr content exceeding 25% degrades the hot workability and, in
addition, a noxious phase known as TCP phase is formed to deteriorate the cold workability,
mechanical properties and corrosion resistance. From these points of view, the Cr
content preferably ranges between 14 and 25%, more preferably 14 and 20% and most
preferably 14 and 17%.
[0018] Fe is an element which is effective in stabilizing the structure of the matrix and
improving the corrosion resistance. A too large Fe content, however, permits the production
of noxious phase such as Laves phase and, therefore, the Fe content is preferably
not greater than 30%, more preferably not greater than 10% and most preferably 5 to
9%.
[0019] Al, Ti and Nb contribute to the precipitation hardening due to formation of intermetallic
compounds through reaction with Ni. In order to obtain an age hardenability, however,
at least a combination of not smaller than 0.2% of Al and not smaller than 0.5% of
Ti is essential. It is possible to obtain alloys of desired high strength by increasing
the Al and Ti contents while adding Nb thereto, but the property is degraded if the
Al, Ti and Nb contents are increased excessively. Therefore, Al, Ti and Nb contents
are preferably 0.2 to 2%, 0.5 to 3% and 0.7 to 4.5%, respectively. More preferably,
the Al, Ti and Nb contents are 0.4 to 1.0%, 2 to 3% and 0.7 to 1.5%, respectively.
[0020] Nb has greater effect on the precipitation hardening than Al and Ti and, therefore,
the addition of Nb is necessary for obtaining high hardenability required especially
for the material of aforesaid springs and bolts used in nuclear reactors. However,
a too large Nb content will undesirably deteriorate the mechanical properties and
reduce the workability due to formation of coarse carbide and intermetallic compounds.
Therefore, the Nb content preferably ranges between 0.5 and 1.5%.
[0021] In order to increase the strength at room temperature it is necessary to add C, but
the C content should not exceed 0.15% because C content exceeding 0.15% inconveniently
lowers the cold plastic workability. The C content preferably ranges between 0.02
and 0.08%.
[0022] Not greater than 1% of Si and not greater than 1.5% of Mn are added as deoxidizers
in the course of production of the alloy. Addition of more than 1% of Si and more
than 1.5% of Mn undesirably lowers the cold plastic workability of the alloy. Preferably,
the Si content and Mn content are selected to range between 0.02 and 0.5% and 0.1
and 1%, respectively.
[0023] In the Ni-base alloy member of the invention, the balance of the composition consists
substantially of Ni. The Ni content is preferably not smaller than 65%, and more preferably
not smaller than 70%.
[0024] The direct aging treatment is preferably conducted at a temperature ranging between
650 and 750°C. The two-stepped aging treatment is conducted preferably by heating
the material to and maintaining the same at 800 to 900°C for 1 to 30 hours, cooling
the material and then heating to and maintaining at 600 to 750°C for 1 to 30 hours.
It is also preferred that the solution heat treatment is conducted at a temperature
ranging between 950 and 1150°C.
BRIEF DESCRIPTION OF THE DRAWINGS
[0025]
Figs. la to lf are illustrations of various springs used in a nuclear reactor, as
embodiments of the Ni-base alloy member in accordance with the invention;
Figs. 2 (a) to (d) are microscopic photos of the structures of Ni-base alloy member
of the invention obtained through a direct aging treatment (magnification 400);
Figs. 3 (a) to (d) are microscopic photos of structures of Ni-base alloy member of
the invention obtained through two-stepped aging treatment (magnification 400); and
Fig. 4 shows microscopic photos at a large magnification of structures which are obtained
through direct aging treatment and two-stepped aging treatment, respectively.
DESCRIPTION OF THE PREFERRED EMBODIMENTS
[0026] The Ni-base alloy member of the invention is suitable for use particularly as springs
and bolts which are subjected to pure water of high pressure and tmpera- ture in nuclear
reactors.
[0027]
Figs. la to lf illustrate shapes of various springs and bolts used in nuclear reactors.
A description will be made hereinunder as to the natures of these springs and bolts,
as well as the method of producing these springs and bolts.
Figs. la and lb illustrate an expansion spring 12 which is used for securing graphite
seal segments 11 to the inner surface of an index tube 10. The expansion spring 12
has the form of a web-like ring cut at a portion thereof as at 13. The breadth or
axial height is 10 mm while the diameter is 60 mm. This expansion ring 12 is made
by a process having the steps of preparation of molten alloy material, solidification,
rolling, solution heat treatment, cold rolling at a working ratio of 25% or higher,
forimg and two-stepped aging treatment.
[0028] Figs. lc and ld illustrates a grater spring 22 for securing graphite seal segments
21 to a piston tube 20. The garter spring 22 is a coiled spring having a coil length
of 166 mm and formed from a wire of 0.36 mm dia. This garter spring is produced by
a process which has the steps of preparation of molten alloy material, solidification,
solution heat treatment, drawing, coiling at a working ratio of 25% or higher and
two-stepped aging treatment.
[0029] Fig. le shows a spring 32 which is interposed between a tie plate 30 and a channel
box 31, while Fig. lf shows a spring 41 associated with a cap screw 40. These springs
32 and 41 are produced by the same process as the expansion spring shown in Figs.
la and lb. In Fig. lf, a reference numeral 42 designates a guard. The cap screw 40
is produced by a process having the steps of forging or rolling, solution heat treatment,
and threading by thread rolling or machining. The aforementioned two-stepped aging
treatment is conducted following the threading.
Example:
[0030] Inconel x750 (commercial name) consisting essentially of, by weight, 72.92% of Ni,
15.48% of Cr, 6.91% of Fe, 0.57% of Al, 2.60% of Ti, 0.95% of Nb+Ta, 0.04% of C, 0.20%
of Si and 0.23% of Mn was used as the blank.
[0031] Table 1 shows the result of a crevice constant strain test conducted in pure water
of high temperature and pressure under the following condition.
[0032] test temperature: 288°C pressure: 86
Kg/cm
2 dissolved oxygen content: 8 ppm crevice forming material: graphite fiber wool strain:
about 1.0% test time: 500 hours
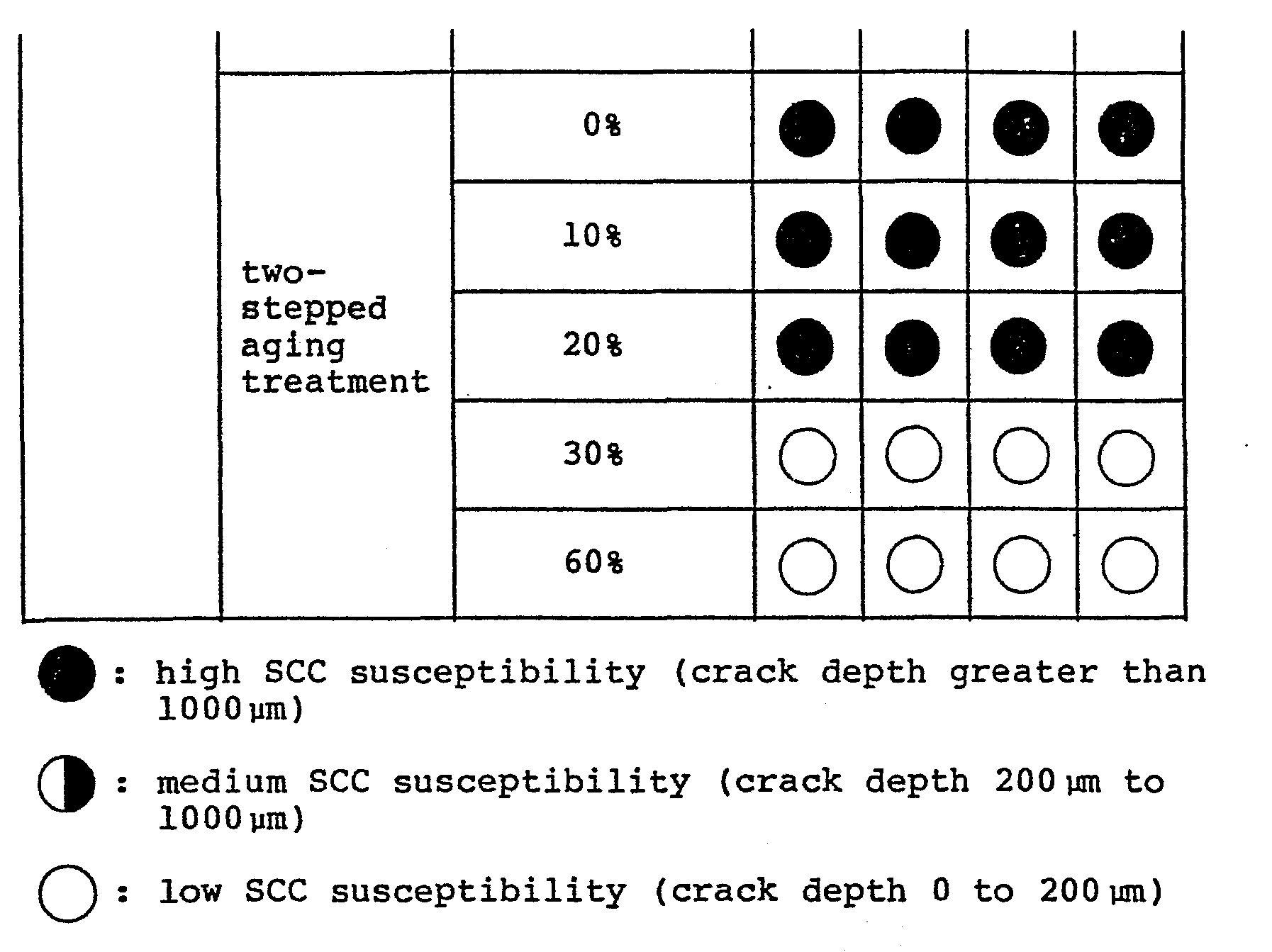
[0033] From Table 1, it will be understood that, when the inconel x750 is subjected to a
cold plastic working at a reduction of cross-sectional area of 10 to 60% after a solution
heat treatment (1066°C 1-hour heating followed by water cooling) and before a direct
aging treatment (704°C 4 to 20-hours heating followed by air cooling), the crevice
SCC susceptibility is varied according to the value of the reduction of cross-sectional
area. Namely, the crevice SCC susceptibility is impractically large when the cold
plastic working is conducted respectively at reduction of cross-sectional area of
10, 20 and 30%. This means that the cold plastic working at working ratio not greater
than 30% is detrimental to the crevice SCC resistance. The crevice SCC susceptibility
is remarkably decreased as the cold plastic working ratio is increased to 50% and
then to 60%. Such large cold plastic working ratio, however, is obtainable only through
a heavy cold plastic working.
[0034] In the case where the same cold plastic working is applied between a solution heat
treatment. (1066°C 1-hour heating followed by water cooling) and a two-stepped aging
treatment (843°C 24-hours heating followed by air cooling, and 704°C 4 to 20-hours
heating followed by air cooling), the crevice SCC resistance is remarkably improved
when the cold plastic working is conducted respectively at a working ratio of 30 and
60%, although the crevice SCC susceptibility is still high when the working ratio
is 10% and 20%.
[0035] In order to examine how the crevice SCC susceptibility of inconel x750 is affected
by the metallography, test pieces of this material were immersed in a mixed acid (92
ml Hcl + 3 ml HN0
3 + 5 ml H
2S0
4) and were observed by a microscope to obtain microscopic photos (magnification 400)
as shown in Figs. 2 (a) to (d) and Figs. 3 (a) to (d). More specifically, Figs. 2
(a) to (d) show the metallographies as obtained through a direct aging treatment when
the cold working ratio is 10%, 20%, 30% and 60%, respectively, while Figs. 3 (a) to
(d) shows those obtained through two-stepped aging treatment when the cold plastic
working is conducted at working ratio of 10%, 20%, 30% and 60%, respectively. When
the aging treatment is conducted throgh a direct aging, the grains become deformed
as the cold working ratio is increased. However, no specific relationship is observed
between the crevice SCC susceptibility and the metallography. On the other hand, when
the aging is conducted through a two-stepped aging treatment, the metallographies
exhibiting large crevice SCC susceptibility show only intergranular corrosion, whereas
the metallographies exhibiting small crevice SCC susceptibility show a comparatively
large number of apparent primary recrystallization grains, as well as intergranular
corrosion. This suggests that there is a certain relationship between the apparent
primary recrystallization behavior and the crevice SCC susceptibility in hot water,
when the aging is conducted through two-stepped aging treatment, and that the crevice
SCC resistance of the alloy of the invention can be improved effectively by finally
attaining a metallography of apparent primary recrystallization structure through
a suitable combination of the cold working ratio and heat treatment. The apparent
primary recrystallization is ruled by the cold working ratio and the condition of
the intermediate heat treatment. More specifically, the apparent primary recrystallization
is promoted to remarkably improve the crevice SCC resistance, as the cold working
ratio is increased.
[0036] Fig. 4 shows microscopic photos of metallographies of inconel x750 alloy subjected
to direct aging treatment and two-stepped aging treatment, after cold plastic working
at working ratio of 0%, 30% and 60%, respectively. In the alloy subjected to the direct
aging treatment, continuous precipitate of Cr carbide is observed along the grain
boundary when the cold plastic working ratio is 0% and 30%. It is, therefore, understood
that the low crevice SCC resistance in the alloy cold-worked at such low working ratio
is attributable to the continuous precipitate of Cr carbide in the grain boundary.
In contrast, in the alloy subjected to a plastic working at working ratio of 60% in
accordance with the invention, no continuous precipitate of Cr carbide is found along
the grain boundary, but the Cr carbide is precipitated in a granular form along the
grain boundary and within the grain.
[0037] On the other hand, in the alloy subjected to two-stepped aging treatment under the
cold plastic working ratio of 0%, columnar precipitate of Eta phase (Ni
3Ti intermetallic compound) is formed along the grain boundary and is surrounded by
Precipitate Free Zone. It is, therefore, understood that the low crevice SCC resistance
in the alloy having cold working ratio of 0
% is attributable to the columnar precipitate of the Eta phase and the presence of
the precipitate free zone around the Eta phase. Unlike the case of the cold working
ratio of 0%, the Eta phase is precipitated in Widmanstatten or dendritic form in the
alloy subjected to cold plastic working at ratio of 30% and 60% according to the invention.
The phase itself appearing as apparent primary recrystallization structure mentioned
before owes to this dendritic Eta phase.
[0038] From the facts described heretofore, it is understood that the cold working at a
working ratio not smaller than 40% is effective in the production of springs and bolts
having superior crevice SCC resistance suitable for use in nuclear reactors, when
the aging is conducted through a direct aging treatment, whereas, when the aging is
conducted through two-stepped aging treatment, the cold working at a working ratio
not smaller than 25% is effective. In this case, it is understood also that the crevice
SCC resistance can easily be evaluated through the observation of the metallography,
i.e. the state of precipitate of Cr carbide and the existence of the apparent primary
recrystallization structure.
[0039] Although the invention has been described through specific terms, it is to be noted
that the described embodiments are not exclusive and various changes and modifications
may be imparted thereto without departing from the scope of the invention which is
limited solely by the appended claims.
1. An Ni-base alloy memamber superior in stress corrosion cracking resistance made
of an alloy consisting essentially of, by weight, not greater than 0.15% of C, not
greater than 1% of Si, not greater than 1.5% of Mn, 14 to 25% of Cr, not greater than
30% of Fe, 0.2.to 2% of Al, 0.5 to 3% of Ti, 0.7 to 4.5% of Nb and the balance substantially
Ni, characterized in that said alloy exhibits stress corrosion cracking depth of not
greater than 200um when subjected to pure water of 288°C under a pressure of 86 Kg/cm2 and having a dissolved oxygen content of 8 ppm, for 500 hours at a strain of 1%.
2. An Ni-base alloy member according to claim 1, wherein said alloy has a structure
containing discontinuous granular precipitate of Cr carbide along the grain boundary
or a primary recrystallization structure.
3. An Ni-base alloy member superior in stress corrosion cracking resistance made of
an alloy consisting essentially of, by weight, 0.02 to 0.08% of C, 0.02 to 0.5% of
Si, 0.1 to 1% of Mn, 14 to 20% of Cr, not greater than 10% of Fe, 0.4 to 1.0% of Al,
2 to 3% of Ti, 0.7 to 1.5% of Nb and the balance substantially Ni, characterized in that
said alloy has a structure containing discontinuous granular precipitate of Cr carbide
along the grain boundary or an apparent primary recrystallization structure and exhibits
stess corrosion cracking length of not greater than 200um when subjected to pure water
of 288°C under a pressure of 86 Kg/cm2 and having a dissolved oxygen content of 8 ppm, for 500 hours at a strain of 1%.
4. An Ni-base alloy member according to claim 3, wherein said member is used as the
material for a spring or a bolt subjected to pure water of high temperatue and pressure
in a nuclear reactor.
5. An Ni-base alloy member superior in stress corrosion cracking resistance made of
an alloy consisting essentially of, by weight, 0.02 to 0.08% of C, 0.02 to 0.5% of
Si, 0.1 to 1% of Mn, 14 to 17% of Cr, 5 to 9% of Fe, 0,4 to 1.0% of Al, 2 to 3% of
Ti, 0.7 to 1.5% of Nb and the balance substantially Ni, characterized in that said
alloy has a structure containing discontinuous granular precipitate of Cr carbide
along the grain boundary or an apparent primary recrystallization structure and exhibits
stress corrosion cracking depth of not greater than 200pm when subjected to pure water
of 288°C under a pressure of 86 Kg/cm2 and having dissolved oxygen content of 8 ppm, for 500 hours at a strain of 1%. «
6. An Ni-base alloy member according to claim 5, wherein said member is used as the
material for a spring or a bolt subjected to pure water of high temperature and pressure
in a nuclear reactor.
7. A method of producing an Ni-base alloy member superior in stress corrosion cracking
resistance comprising the steps of: preparing an alloy consisting essentially of,
by weight, not greater than 0.15% of C, not greater than 1% of Si, not greater than
1.5% of Mn, 14 to 25% of Cr, not greater than 30% of Fe, 0.2 to 2% of Al, 0.5 to 3%
of Ti, 0.7 to 4.5% of•Nb and the balance substantially Ni; subjecting said alloy to
a solution heat treatment; effecting a cold plastic working on said alloy at a reduction
of cross-sectional area not smaller than 40%; and subjecting said alloy to an aging
treatment at a temperature of between 650 and 750°C.
8. A method according to claim 7, wherein said cold plastic working is effected at
a reduction of cross-sectional area of between 50 and 70%.
9. A method of producing an Ni-base alloy member superior in stress corrosion cracking
resistance comprising the steps of: preparing an alloy consisting essentially of,
by weight, 0.02 to 0.08% of C, 0.02 to 0.5% of Si, 0.1 to 1% of Mn, 14 to 20% of Cr,
not greater than 10% of Fe, 0.4 to 1% of Al, 2 to 3% of Ti, 0.7 to 1.5% of Nb and
the balance substantially Ni; subjecting said alloy to a solution heat treatment;
effecting a cold plastic working on said alloy at a reduction of cross-sectional area
not smaller than 40%; and subjecting said alloy to an aging treatment at a temperature
of between 650 and 750°C.
10. A method according to claim 9, wherein said cold plastic working is effected at
a reduction of cross-sectional area of between 50 and 70%.
ll. A method of producing an Ni-base alloy member superior in stress corrosion cracking
resistance comprising the steps of: preparing an alloy consisting essentially of,
by weight, not greater than 0.15% of C, not greater than 1% of Si, not greater than
1.5% of Mn, 14 to 25% of Cr, not greater than 30% of Fe, 0.2 to 2% of Al, 0.5 to 3%
of Ti, 0.7 to 4.5% of Nb and the balance substantially Ni; subjecting said alloy to
a solution heat treatment; effecting a cold plastic working on said alloy at a reduction
of cross-sectional area not smaller than 25%; subjecting said alloy to an aging treatment
at a temperature of between 800 and 950°C; and subjecting said alloy to another aging
treatment at a temperature of between 600 and 750°C.
12. A method according to claim 11, wherein said cold plastic working is effected
at a reduction of cross-sectional area of between 40 and 70%.
13. A method of producing an Ni-base alloy member superior in stress corrosion cracking
resistance comprising the steps of: preparing an alloy consisting essentially of,
by weight, 0.02 to 0.08% of C, 0.02 to 0.5% of Si, 0.1 toll% of Mn, 14 to 20% of Cr,
not greater than 10% of Fe, 0.4 to 1% of Al, 2 to 3% of Ti, 0.7 to 1.5% of Nb and
the balance substantially Ni; subjecting said alloy to a solution heat treatment;
effecting a cold plastic working on said alloy at a reduction of cross-sectional area
not smaller than 25%; sujecting said alloy to an aging treatment at a temperature
of between 800 and 950°C; and subjecting said alloy to another aging treatment at
a temperature of between 600 and 750°C.
14. A method according to claim 13, wherein said cold plastic working is effected
at a reduction of cross-sectional area of between 40 and 70%.