[0001] This invention relates to a photosensitive element comprising a nonplanar support
and a tabular grain silver halide emulsion.
[0002] High aspect ratio tabular grain silver halide emulsions, their preparation, and use
in photographic elements is the subject matter of Research Disclosure, Vol. 225, January
1983, Item 22534.
[0003] Photosensitive elements having supports providing a nonplanar surface pattern forming
an array have been disclosed by Whitmore U.S. Patents 4,362,806 and 4375,507, Gilmour
U.K. Specification 2,091,433A, Blazey et al U.S. Patent 4,307,105, Gilmour et al E.P.C.
Specification 50,474, Land E.P.C. Specification 58,568, Gerber U.S. Patents 4,356,257
and 4,359,525, and Walworth U.S. Patent 4,359,526.
[0004] According to the present invention there is provided a photosensitive element comprising
a support and radiation-sensitive imaging means capable of undergoing as a function
of at least one of photographic exposure and processing a change in the optical density
or mobility of said imaging means characterized in that said support provides a nonplanar
surface pattern forming an array and said imaging means includes a high aspect ratio
tabular grain silver halide emulsion comprised of a dispersing medium and silver halide
grains, wherein tabular silver halide grains having a thickness of less than 0.5 micron
and a diameter of at least 0.6 micron have an average aspect ratio of greater than
8:1 and account for at least 50 percent of the total projected area of the silver
halide grains.
Summary of the Drawings
[0005] The invention can be better appreciated by consideration of the detailed description
in conjunction with the drawings, in which
Figure 1A is a plan view of an element portion;
Figure 1B is a sectional view taken along section line 1B-1B in Figure lA;
Figures 2 through 5 are sectional views of alternative pixel (defined below) constructions;
Figure 6 through 8 are plan views of alternative element portions;
Figures 9 and 10 are sectional details of alternative element portions;
Figures 11A and 11D are plan views of alternative element portions;
Figure 11B is a sectional view taken along section line 11B-11B is Figure 11A;
Figures 11C and 12 through 14 are sectional views of photographic elements according
to this invention;
Figures 15, 16, and 17 are sectional details of image transfer film units;
Figure 18 is a schematic isometric view of a microcell filling arrangement;
Figures 19A through D are sectional details illustrating a sequence for filling microcells;
Figure 20 is a sectional detail of an element portion having microcells formed in
a photoconductive layer;
Figures 21A through D are sectional details illustrating a sequence for filling microcells;
Figure 22 is a plan view of an element showing a particular loading pattern of the
microcells;
Figure 23A is a plan view of an element portion;
Figure 23B is a sectional detail taken along section line 23B-23B in Figure 23A;
Figure 24 is a plan view of an alternative element portion;
Figure 25A is a plan view of an alternative element portion;
Figure 25B and 25C are sectional details taken along section line 25B-25B in Figure
25A showing differing stages of angled exposure;
Figures 26A and 26B show different angled exposure patterns of an element portion
shown in plan view;
Figures 27 and 28A are plan views of alternate element portions;
Figures 28B and 28C are sectional views at different stages of loading taken along
section line 28B-28B in Figure 28A;
Figure 29 is a sectional detail of an alternate element portion;
Figure 30A is a plan view of an alternate element portion;
Figures 30B and 30C are sectional views at different stages of loading taken along
section line 30B-30B in Figure 30A;
Figures 31, 32, and 33 are plan views of alternate element portions; and
Figure 34 is a sectional detail of an alternate element portion construction.
Description of the Preferred Embodiments
[0006] While subheadings are provided for convenience, to appreciate fully the elements
of the invention, it is intended that the disclosure be read and intrepreted as a
whole.
Illustrative Photographic Element Configurations
[0007] A preferred embodiment of a photographic element constructed according to the present
invention is a photographic element 100 schematically illustrated in Figures 1A and
1B. The element is comprised of a support 102 having substantially parallel first
and second major surfaces 104 and 106. The support defines a plurality of tiny cavities
or microcells (hereinafter termed microcells or reaction microcells) 108 which open
toward the second major surface of the support. The reaction microcells are defined
in the support by an interconnecting network of lateral walls 110 which are of lesser
width than the adjacent microcells they define. As a result, next adjacent microcells
are laterally spaced by less than their widths. The lateral walls are integrally joined
to an underlying portion 112 of the support so that the support acts as a barrier
between adjacent microcells. The underlying portion of the support defines the bottom
wall 114 of each reaction microcell. Within each reaction microcell is provided a
radiation-sensitive imaging material 116 which is capable of undergoing as a function
of photographic exposure and/or processing a change in its optical density or mobility
but which includes at least one component exhibiting the characteristic of visually
detectable lateral image spreading in translating an exposure pattern to a viewable
form when coated on a planar support surface as a continuous layer.
[0008] The dashed line 120 is a boundary of a pixel. The term "pixel" is employed herein
to indicate a single unit of the photographic element which is repeated to make up
the entire imaging area of the element. This is consistent with the general use of
the term in the imaging arts. The number of pixels is, of course, dependent on the
size of the individual pixels and the dimensions of the photographic element. Looking
at the pixels collectively, it is apparent that the imaging material in the reaction
microcells can be viewed as a segmented layer associated with the support.
[0009] The photographic elements of the present invention can be varied in their geometrical
configurations and structural makeup. For example, Figure 2 schematically illustrates
in section a single pixel of a photographic element 200. The support 202 is provided
for a first major surface 204 and a second, substantially parallel major surface 206.
A reaction microcell 208 opens toward the second major surface. Contained within the
reaction microcell is a radiation-sensitive material 216. The reaction microcells
are formed so that the support provides inwardly sloping walls which perform the functions
of both the lateral and bottom walls of the microcells 108. Such inwardly curving
wall structures are more conveniently formed by certain techniques of manufacture,
such as etching, and also can be better suited toward redirecting exposing radiation
toward the interior of the reaction microcells.
[0010] In Figure 3 a pixel of a photographic element 300 is shown. The element is comprised
of a first support element 302 having a first major surface 304 and a second, substantially
parallel major surface 306. Joined to the first support element is a second support
element 308 which is provided in each pixel with an aperture 310. The second support
element is provided with an outer major surface 312. The walls of the second support
element forming the aperture 310 and the second major surface of the first support
element together define a reaction microcell. A radiation-sensitive material 316 is
located in the reaction microcell. Additionally, a relatively thin extension 314 of
the radiation-sensitive material overlies the outer major surface of the upper support
element and forms a continuous layer joining adjacent pixels. The lateral extensions
of the radiation-sensitive material are sometimes a by-product of a specific technique
of coating the radiation-sensitive material. One coating technique which can leave
extensions of the radiation-sensitive material is doctor blade coating. It is generally
preferred that the lateral extensions be absent or of the least possible thickness.
[0011] In Figure 4 a pixel of a photographic element 400 is illustrated comprised of a support
402, which can be of extended depth. The support is provided with a first major surface
404 and a second, substantially parallel major surface 406. The support defines a
reaction microcell 408 which can be similar to reaction microcell 108, but is by comparison
of extended depth. Two components 416 and 418 together form a radiation-sensitive
imaging means which is capable of translating an imaging radiation pattern striking
it into a viewable image, but which exhibits the characteristic of permitting visually
detectable lateral image spreading to occur in translating the imaging radiation pattern
to a viewable form when coated on a planar surface as two continuous layers. The first
component 416, which in a continuous layer form would produce visually detectable
lateral image spreading, forms a column of extended depth, as compared with the material
116 in the reaction microcells 108. The second component 418 is in the form of a continuous
layer overlying the second major surface of the support. In an alternative form the
first component can be identical to the radiation-sensitive imaging material 116--that
is, itself form the entire radiation-sensitive imaging means--and the second component
418 can be a continuous layer which performs another function, such as those conventionally
performed by overcoat layers.
[0012] In Figure 5 a pixel of a photographic element 500 is illustrated comprised of a first
support element 502 having a first major surface 504 and a second, substantially parallel
major surface 506. Joined to the first support element is a transparent second support
element 508 which is provided with a network of lateral walls 510 integrally joined
to an underlying portion 512 of the second support element. In one preferred form
the first support element is a relatively nondeformable element while the second support
element is relatively deformable. An indentation 514 is formed in the second support
element in each pixel area. The surfaces of the second support element adjacent its
outer major surface, that is the outer surface of the lateral walls, as well as the
surfaces of the indentation, are overlaid with a thin layer 515, which performs one
or a combination of surface modifying functions. The portion of the coating lying
within the indentation defines the boundaries of a reaction microcell 517. A first
component 516 which lies within the reaction microcell and a second component 518
which overlies one entire major surface of the pixel can be similar to the first and
second components 416 and 418, respectively.
[0013] Each of the pixels shown in Figures 2 through 5 can be of a configuration and arranged
in relation to other pixels so that the photographic elements 200, 300, 400 and 500
(ignoring any continuous material layers overlying the viewed major surfaces of the
supports) appear identical in plan view to the photographic element 100. The pixels
120 shown in Figure 1 are hexagonal in plan view, but it is appreciated that a variety
of other pixel shapes and arrangements are possible. For example, in Figure 6 a photographic
element 600 is shown comprised of a support 602 provided with reaction microcells
608, which are circular in plan view, containing radiation-sensitive material 616.
Reaction microcells which are circular in plan are particularly suited to formation
by etching techniques, although they can be easily formed by other techniques, as
well. A disadvantage of the circular reaction microcells as compared with other configurations
shown is that the lateral walls 610 vary continuously in width. Providing lateral
walls of at least the minimum required width at their narrowest point inherently requires
the walls in some portions of the pattern to be larger than that required minimum
width. In Figure 7 a photographic element 700 is shown comprised of a support 702
provided with reaction microcells 708, which are square in plan view, containing radiation-sensitive
material 716. The lateral walls 710 are of uniform width.
[0014] Figure 8 illustrates an element 800 comprised of a support 802 having an interlaid
pattern of rectangular reaction microcells 808. Each of the microcells contains a
radiation-sensitive imaging material 816. The dashed line 820 identifies a single
pixel of the element.
[0015] In each of the elements 100 through 500, the surface of the support remote from the
reaction microcells is illustrated as being planar. This is convenient for many photographic
applications, but is not essential to the practice of this invention. Other element
configurations are contemplated, particularly where the support is transparent to
exposing radiation and/or when viewed.
[0016] For example, in Figure 9 a photographic element 900 is illustrated. The element is
comprised of a support 902 having substantially parallel first and second major surfaces
904 and 906. The support defines a plurality of reaction microcells 908A and 908B
which open toward the first and second major surfaces, respectively. In the preferred
form, the reaction microcells 908A are aligned with the reaction microcells 908B along
axes perpendicular to the major surfaces. The reaction microcells are defined in the
support by two interconnecting networks of lateral walls 910A and 910B which are integrally
joined by an underlying, preferably transparent, portion 912 of the support. Within
each reaction microcell is provided a radiation-sensitive material 916.
[0017] It can be seen that element 900 is essentially similar to element 100, except that
the former element contains reaction microcells along both major surfaces of the support.
Thus the microcells form two separate planar arrays, one along each major surface
of the support. As shown, the lateral walls 910A and 910B and the underlying portion
912 are proportioned so that next adjacent of the microcells forming the same planar
array are laterally spaced by less than the width of adjacent microcells opening toward
either of the first and second major surfaces. It is apparent that similar variants
of the photographic elements 200, 300, 400, 500, 600, 700 and 800 can be formed.
[0018] In Figure 10 a photographic element 1000 is illustrated. The element is comprised
of a support 1002 having a lenticular first major surface 1004 and a second major
surface 1006. Reaction microcells 1008 containing radiation-sensitive material 1016
and defined by lateral walls 1010 of the support open toward the second major surface.
The element is made up of a plurality of pixels indicated in one occurrence by dashed
line boundary 1020. Individual lenticules are coextensive with the pixel boundaries.
Although element 1000 is shown as a modification of element 100 to which the feature
of a lenticular surface has been added, it is appreciated that photographic elements
200, 300, 400, 500, 600, 700 and 800 can be similarly modified to provide lenticules.
[0019] The photographic elements and pixels thereof illustrated schematically in Figures
1 through 10 are merely exemplary of a wide variety of forms which the elements of
this invention can take. For ease of illustration the drawings show the pixels greatly
enlarged and with some deliberate distortions of relative proportions. For example,
as is well known in the photographic arts, support thicknesses often range from about
10 times the thickness of the radiation-sensitive layers coated thereon up to 50 or
even 100 times their thickness. Thus, in keeping with the usual practice in patent
drawings in this art, the relative thicknesses of the supports have been reduced.
This has permitted the reaction microcells to be drawn conveniently to a larger scale.
[0020] One function of the microcells provided in the photographic elements is to limit
or control lateral image spreading. The degree to which it is desirable to limit or
control lateral image spreading will depend upon the photographic application. For
most imaging applications the microcells are preferably sufficiently small in size
that the unaided eye does not detect discrete image areas (graininess) in viewing
images in the photographic element or images made from the photographic element. Where
the photographic image is to be viewed without enlargement and minimal visible graininess
is desired, microcells having widths within the range of from about 1 to 200 microns,
preferably from about 4 to 100 microns, are contemplated for use in the practice of
this invention. To the extent that visible graininess can be tolerated for the photographic
application, the microcells can be still larger in width. Where the photographic images
produced are intended for enlargement, microcell widths in the lower portion
I of the width ranges are preferred. It is accordingly preferred that the microcells
be about 20 microns or less in width where enlargements are to be made of the images
produced by the photographic elements of this invention.
[0021] The lower limit on the size of the reaction microcells is a function of the photographic
speed desired for the element. As the areal extent of the reaction microcell is decreased,
the probability of an imaging amount of radiation striking a particular reaction microcell
on exposure is reduced. Reaction microcell widths of at least about 7 microns, preferably
at least 8 microns, optimally at least 10 microns, are contemplated where the reaction
microcell contains radiation-sensitive material. At widths below 7 microns, silver
halide emulsions in the microcells can be expected to show a significant reduction
in speed.
[0022] The reaction microcells are of sufficient depth to contain at least a major portion
of the radiation-sensitive material. In one preferred form the reaction microcells
are of sufficient depth that the radiation-sensitive materials are entirely contained
therein when employed in conventional coating thicknesses, and the support element
which forms the lateral walls of the reaction microcells efficiently divides the radiation-sensitive
materials into discrete units or islands. In some forms the reaction microcells do
not contain all, but only a major portion, of the radiation-sensitive material, as
can occur, for example, by introducing the radiation-sensitive material into the reaction
microcells by doctor blade coating.
[0023] The minimum depth of the reaction microcells is that which allows the support element
to provide an effective lateral wall blockage of image spreading. In terms of actual
dimensions the minimum depth of the reaction microcells can vary as a function of
the radiation-sensitive material employed and the maximum density which is desired
to be produced. The depth of the reaction microcells can be less than, equal to or
greater than their width. The thickness of the imaging material or the component thereof
coated in the microcells is preferably at least equal to the thicknesses to which
the material is conventionally continuously coated on planar support surfaces. This
permits a maximum density to be achieved within the area subtended by the reaction
microcell which approximates the maximum density that can be achieved in imaging a
corresponding coating of the same radiation-sensitive material. It is recognized that
reflected radiation from the microcell walls during exposure and/or viewing can have
the effect of yielding a somewhat different density than obtained in an otherwise
comparable continuous coating of the radiation-sensitive material. For instance, where
the microcell walls are reflective and the radiation-sensitive material is negative-working,
a higher density can be obtained during exposure within the microcells than would
be obtained with a continuous coating of the same thickness of the radiation-sensitive
material.
[0024] Because the areas lying between adjacent reaction microcells are free of radiation-sensitive
material (or contain at most a relatively minor proportion of the radiation-sensitive
material), the visual effect of achieving a maximum density within the areas subtended
by the reaction microcells equal to the maximum density in a corresponding conventional
continuous coating of the radiation-sensitive material is that of a somewhat reduced
density. The exact amount of the reduction in density is a function of the thickness
of any material lying within the reaction microcells as well as the spacing between
adjacent reaction microcells. Where the continuous conventional coating produces a
density substantially less than the maximum density obtainable by increasing the thickness
of the coating and the reaction microcell area is a larger fraction of the pixel area
(e.g., 90 to 99 percent), the comparative loss of density attributable to the spacing
of reaction microcells can be at least partially offset by increasing the thickness
of the imaging material or component in the reaction microcell. This, of course, means
increasing the minimum depth of the reaction microcells. Where the photographic element
is not intended to be viewed directly, but is to be used as an intermediate for photographic
purposes, such as a negative which is used as a printing master to form positive images
in a reflection print photographic element, the effect of spacing between adjacent
reaction microcells can be eliminated in the reflection print by applying known printing
techniques, such as slightly displacing the reflection print with respect to the master
during the printing exposure, employing an optical filter, controlling a chemical
diffusion path, or controlling a scanning beam. Thus, in this instance, increase in
the depth of the reaction microcells is not necessary to achieve conventional maximum
density levels with conventional thicknesses of radiation-sensitive materials.
[0025] The maximum depth of the reaction microcells can be substantially greater than the
thickness of the radiation-sensitive matereal to be placed therein. For certain coating
techniques it is preferred that the maximum depth of the reaction microcells approximate
or substantially equal the thickness of the radiation-sensitive material to be employed.
In forming conventional continuous coatings of radiation-sensitive materials one factor
which limits the maximum thickness of the coating material is acceptable lateral image
spreading, since the thicker the coating, the greater is the tendency, in most instances,
toward loss of image definition. In the present invention lateral image spreading
is limited by the lateral walls of the support element defining the reaction microcells
and is independent of the thickness of the radiaon-sensitive material located in the
microcells. Thus, it is possible and specifically contemplated in the present invention
to employ reaction microcell depths and radiation-sensitive material thicknesses therein
which are far in excess of those thicknesses employed in conventional continuous coatings
of the same radiation-sensitive materials.
[0026] While the depth of the reaction microcells can vary widely, it is generally contemplated
that the depth of the reaction microcells will fall within the range of from about
1 to 1000 microns in depth or more. For exceptional radiation-sensitive materials,
such as vacuum vapor deposited silver halides, conventional coating thicknesses are
typically in the range from 40 to 200 nanometers, and very shallow microcells of a
depth of 0.5 micron or less can be employed. In one preferred form, the depth of the
reaction microcells is in the range of from about 5 to 20 microns. This is normally
sufficient to permit a maximum density to be generated within the area subtended by
the reaction microcell corresponding to the maximum density obtainable with continuously
coated radiation-sensitive materials of conventional thicknesses, such as silver halide
emulsions containing conventional addenda, including dye image-producing components.
These preferred depths of the reaction microcells are also well suited to applications
where the radiation-sensitive material is intended to fill the entire reaction microcells--e.g.,
to have a thickness corresponding to the depth of the reaction microcell.
[0027] The reaction microcells are located on the support element in a predetermined, controlled
relationship to each other. The microcells are relatively spaced in a predetermined,
ordered manner to form an array. It is usually desirable and most efficient to form
the microcells so that they are aligned along at least one axis in the plane of the
support surface. For example, microcells in the configuration of hexagons, preferred
for multicolor applications, are conveniently aligned along three support surface
axes which intersect at 120° angles. It is generally preferred that the reaction microcells
be positioned to form a regular pattern. However, it is recognized that adjacent reaction
microcells can be varied in spacing to permit alterations in visual effects. Generally
it is preferred that adjacent reaction microcells be closely spaced, since this aids
the eye in visually combining adjacent image areas and facilitates obtaining higher
overall maximum densities. The minimum spacing of adjacent reaction microcells is
limited only by the necessity of providing intervening lateral walls in the support
elements. Typical adjacent reaction microcells are laterally spaced a distance (corresponding
to lateral wall thickness) of from about 0.5 to 5 microns, although both greater and
lesser spacings are contemplated.
[0028] Spacing of adjacent reaction microcells can be approached in another way in terms
of the percentage of each pixel area subtended by the reaction microcell. This is
a function of the size and peripheral configuration of the reaction microcell and
the pixel in which it is contained. Generally the highest percentages of pixel area
subtended by reaction microcell area are achieved when the peripheral configuration
of the pixel and the reaction microcell are identical, such as a hexagonal reaction
microcell in a hexagonal pixel (as in Figure lA) or a square reaction microcell in
a square pixel (as in Figure 7). For closely spaced patterns it is preferred that
the subtended reaction microcell area account for from about 50 to 99 percent of the
pixel area, most preferably from 90 to 98 percent of the pixel area. Even with microcell
and pixel configurations which do not permit the closest and most efficient spacing
the subtended microcell area can readily account for 50 to 80 (preferally 90) percent
of the pixel area.
[0029] The photographic elements can be formed by one or a combination of support elements
which, alone or in combination, are capable of reducing lateral image spread and maintaining
spatial integrity of the pixels forming the elements. Where the photographic elements
are formed by a single support element, the support element performs both of these
functions. Where the photographic elements are formed by more than one support element,
as in Figures 3 and 5, for example, only one of the elements (preferably the first
support elements 302 and 502) need have the structural strength to retain the desired
spatial relationship of adjacent pixels. The second support elements can be formed
of relatively deformable materials. They can, but need not, contribute appreciably
to the ability of the photographic elements 300 and 500 to be handled as a unit without
permanent structural deformation.
Illustrative Support Materials
[0030] The support elements of the elements of this invention can be formed of the same
types of materials employed in forming conventional photographic supports. Exemplary
materials are described in Research Disclosure, Vol. 176, December, 1978, Item 17643,
Section XVII.
[0031] The second support elements which define the lateral walls of the reaction microcells
can be selected from a variety of materials lacking sufficient structural strength
to be employed alone as supports. It is specifically contemplated that the second
support elements can be formed using conventional photopolymerizable or photocrosslinkable
materials--e.g., photoresists. Exemplary conventional photoresists are disclosed by
Arcesi et al U.S. Patents 3,640,722 and 3,748,132, Reynolds et al U.S. Patents 3,696,072
and 3,748,131, Jenkins et al U.S. Patents 3,699,025 and '026, Borden U.S. Patent 3,737,319,
Noonan et al U.S. Patent 3,748,133, Wadsworth et al U.S. Patent 3,779,989, DeBoer
U.S. Patent 3,782,938, and Wilson U.S. Patent 4,052,367. Still other useful photopolymerizable
and photocrosslinkable materials are disclosed by Kosar, Light-Sensitive Systems:
Chemistry and Application of
Nonsilver Halide Photographic Processes, Chapters 4 and 5, John Wiley and Sons, 1965.
It is also contemplated that the second support elements can be formed using radiation-responsive
colloid compositions, such as dichromated colloids--e.g., dichromated gelatin, as
illustrated by Chapter 2, Kosar, cited above. The second support elements can also
be formed using silver halide emulsions and processing in the presence of transition
metal ion complexes, as illustrated by Bissonette U.S. Patent 3,856,524 and McGuckin
U.S. Patent 3,862,855. The advantage of using radiation-sensitive materials to form
the second support elements is that the lateral walls and reaction microcells can
be simultaneously defined by patterned exposure. Once formed the second support elements
are not themselves further responsive to exposing radiation.
[0032] Specific illustrations of photopolymers useful in forming the second support elements
(i.e., the lateral walls) include bichromate sensitized systems. Such systems include
a chromate such as (N
H4)
2C
r20
7 as the radiation-sensitive component and polymeric materials such as hydrophilic
colloids (e.g., gelatin or gelatin derivatives more specifically described below),
poly(vinyl alcohols (such as those commercially available under the trademarks Gelvatol
20/30 available from Shawiningen and Elvanol 50/42 or 72/30M available from Dupont),
polyamides (such as those commercially available under the trademarks Nylon 819 and
829 available from
Corticelli Ind. and
Elvamide 8061 commercially available from Dupont), poly(vinyl butyral) polymers (such
as those available under the trademarks Butvar B-90 and B-98 commercially available
from Monsanto). Hardeners, such as triethanolamine titanium chelate (Tyzor TE available
from DuPont), can be useful. Alternatively keto-coumarin sensitized systems can be
employed using polyesters. Polyesters formed from varied proportions of materials
such as 1,4-bis-(2-hydroxyethoxy)cyclohexane, diethyl succinate, diethyl 1,4-phenylene-
bis-(2-acrylate), a salt of dimethyl 5-(4-sulfo- phenoxy)isophthalate, a salt of dimethyl
5-(4-sulfo- cyclohexoxy)-1,3-cyclohexane dicarboxylate, and a salt of dimethyl nitridodisulfonylbis(3-benzoate)
are specifically preferred. Specifically preferred sensitizers are illustrated by
3-[(7-diethylamino-2-oxo-[1]benzopyran-3-yl)carbonyl-7-carboxy[I]benzopyran-2-one,
sodium salt and 1-methyl-3[(7,8,10,-11,12-pentahydro-2-oxo-2H,6H-[1]benzopyrano[6,7,8-y]quinolizin-3-yl)carbonyl]pyridinium
fluorosulfate.
[0033] It is contemplated that the second support elements can alternatively be formed of
materials commonly employed as vehicles and/or binders in radiation-sensitive materials.
The advantage of using vehicle or binder materials is their known compatibility with
the radiation-sensitive materials. The binders and/or vehicles can be polymerized
or hardened to a somewhat higher degree than when employed in radiation-sensitive
materials to insure dimensional integrity of the lateral walls which they form. Illustrative
of specific binder and vehicle materials are those described in Research Disclosure,
Item 17643, cited above, Section IX. Vehicle and binder magerials are particularly
useful in allowing controlled diffusion between adjacent microcells. Addenda known
to be useful in silver halide emulsion interlayers, such as scavengers, antifoggants,
inhibitors, etc., can be incorporated in the vehicle materials.
[0034] It is contemplated to employ photoconductive magnetics as second support elements
alone or in combination with the other lateral wall forming magnetics described above.
Specific photoconductive magnetics are discussed below.
[0035] The light transmission, absorption and reflection-qualities of the support elements
can be varied for different photographic applications. The support elements can be
substantially transparent or reflective, preferably white, as are the majority of
conventional photographic supports. The support elements can be reflective, such as
by mirroring the reaction microcell walls. The support elements can in some applications
contain dyes or pigments to render them substantially light impenetrable. Levels of
dye or pigment incorporation can be chosen to retain the light transmission characteristics
in the thinner regions of the support elements--e.g., in the microcell bottom wall
region--while rendering the support elements relatively less light penetrable in thicker
region--e.g., in the lateral wall regions between adjacent microcells. The support
elements can contain neutral colorant or colorant combinations. Alternatively, the
support elements can contain radiation absorbing materials which are selective to
a single region of the electromagnetic spectrum--e.g., blue dyes. The support elements
can contain materials which alter radiation transmission qualities, but are not visible,
such as ultraviolet absorbers. Where two support elements are employed in combination,
the light transmission, absorption and reflection qualities of the two support elements
can be the same or different. The unique advantages of varied forms of the support
elements can be better appreciated by reference to the illustrative embodiments described
below.
[0036] Where the support elements are formed of conventional photographic support materials
they can be provided with reflective and absorbing materials by techniques well known
by those skilled in the art, such techniques being adequately illustrated in the various
patents cited above in relation to support materials. In addition, reflective and
absorbing materials can be employed of varied types conventionally incorporated directly
in radiation-sensitive materials, particularly in second support elements formed of
vehicle and/or binder materials or using photoresists or dichromated gelatin. The
incorporation of relfective and absorbing materials in vehicle materials is illustrated,
for example, by Research Disclosure, Item 17643, cited above, Section VIII.
Illustrative Materials for Imaging portions of Elements
[0037] The radiation-sensitive portions of conventional silver halide photographic elements
are typically coated onto a planar support surface in the form of one or more continuous
layers of substantially uniform thickness. The radiation-sensitive portions of the
silver halide photographic elements of this invention can be selected from among such
conventional radiation-sensitive portions which, when coated as one or more layers
of substantially uniform thickness, exhibit the characteristics of undergoing (1)
an imagewise change in optical density or mobility in response to imagewise exposure
and/or photographic processing, and (2) visually detectable lateral image spreading
in translating an imaging exposure to a viewable form. Lateral image spreading has
been observed in a wide variety of conventional photographic elements. Lateral image
spread can be a product of optical phenomena, such as reflection or scattering of
exposing radiation; diffusion phenomena, such as lateral diffusion of radiation-sensitive
and/or imaging materials in the radiation-sensitive and/or imaging layers of the photographic
elements; or, most commonly, a combination of both. Lateral image spreading is particularly
common where the radiation-sensitive and/or other imaging materials are dispersed
in a vehicle or binder intended to be penetrated by exposing radiation and/or processing
fluids.
[0038] The radiation-sensitive silver halide containing imaging portions of the photographic
elements of this invention can be of a type which contain within a single component,
corresponding to a layer of a conventional silver halide photographic element, radiation-sensitive
silver halide capable of directly producing or being processed to produce a visible
image or a combination of radiation-sensitive silver halide and imaging materials
which together produce directly or upon processing a viewable image. The imaging portion
can be formed alternatively of two or more components, corresponding to two or more
layers of a conventional photographic element, which together contain radiation-sensitive
silver halide and imaging materials. Where two or more components are present, only
one of the components need contail radiation-sensitive silver halide and only one
of the components need be an imaging component. Further, either the radiation-sensitive
silver halide containing component or the imaging component of the imaging portion
of the element can be primarily responsible for lateral image spreading when conventionally
coated as a continuous, substantially uniform thickness layer. In one form the radiation-sensitive
silver halide containing portion can be of a type which permits a viewable image to
be formed directly therein. In another form the image produced is not directly viewable
in the element itself, but can be viewed in a separate element. For example, the image
can be of a type which is viewed as a transferred image in a separate receiver element.
[0039] The radiation-sensitive silver halide containing imaging portions of the photographic
elements are comprised of one or more high aspect ratio tabular grain silver halide
emulsions.
[0040] As herein defined "high aspect ratio tabular grain silver halide emulsions" are those
in which the tabular grains having a thickness of less than 0.5 micrometer (or micron)
and a diameter of at least 0.6 micrometer have an average aspect ratio of greater
than 8:1 and account for at least 50% of the total projected area of the silver halide
grains present in the emulsion.
[0041] The preferred high aspect ratio tabular grain silver halide emulsions of the present
invention are those wherein the silver halide grains having a thickness of less than
0.3 micron (optimally less than 0.2 micron) and a diameter of at least 0.6 micron
have an average aspect ratio of at least 12:1 and optimally at least 20:1. In a preferred
form of the invention these silver halide grains satisfying the above thickness and
diameter criteria account for at least 70 percent and optimally at least 90 percent
of the total projected area of the silver halide grains.
[0042] It is appreciated that the thinner the tabular grains accounting for a given percentage
of the projected area, the higher the average aspect ratio of the emulsion. Typically
the tabular grains have an average thickness of at least 0.03 micron, although even
thinner tabular grains can in principle be employed--e.g., as low as 0.01 micron,
depending on halide content. It is recognized that the tabular grains can be increased
in thickness to satisfy specialized applications. For example, this invention contemplates
the use of tabular grains having thicknesses up to 0.5 micron, in photographic applications
in which enlargement is not normally undertaken. Grain thicknesses of up to 0.5 micron
are also discussed below for recording blue light. (For such applications all references
to 0.3 micron in reference to aspect ratio determinations should be adjusted to 0.5
micron.) However, to achieve high aspect ratios without unduly increasing grain diameters,
it is normally contemplated that the tabular grains of the emulsions of this invention
will have an average thickness of less than 0.3 micron.
[0043] The grain characteristics described above of the silver halide emulsions of this
invention can be readily ascertained by procedures well known to those skilled in
the art. As employed herein the term "aspect ratio" refers to the ratio of the diameter
of the grain to its thickness. The "diameter" of the grain is in turn defined as the
diameter of a circle having an area equal to the projected area of the grain as viewed
in a photomicrograph or an electron micrograph of an emulsion sample. From shadowed
electron micrographs of emulsion samples it is possible to determine the thickness
and diameter of each grain and to identify those tabular grains having a thickness
of less than 0.3 micron and a diameter of at least 0.6 micron. From this the aspect
ratio of each such tabular grain can be calculated, and the aspect ratios of all the
tabular grains in the sample meeting the less than 0.3 micron thickness and at least
0.6 micron diameter criteria can be averaged to obtain their average aspect ratio.
By this definition the average aspect ratio is the average of individual tabular grain
aspect ratios. In practice it is usually simpler to obtain an average thickness and
an average diameter of the tabular grains having a thickness of less than 0.3 micron
and a diameter of at least 0.6 micron and to calculate the average aspect ratio as
the ratio of these two averages. Whether the averaged individual aspect ratios or
the averages of thickness and diameter are used to determine the average aspect ratio,
within the tolerances of grain measurements contemplated, the average aspect ratios
obtained do not significantly differ. The projected areas of the tabular silver halide
grains meeting the thickness and diameter criteria can be summed, the projected areas
of the remaining silver halide grains in the photomicrograph can be summed separately,
and from the two sums the percentage of the total projected area of the silver halide
grains provided by the tabular grains meeting the thickness and diameter critera can
be calculated.
[0044] In the above determinations a reference tabular grain thickness of less than 0.3
micron was chosen to distinguish the uniquely thin tabular grains herein contemplated
from thicker tabular grains which provide inferior photographic properties. A reference
grain diameter of 0.6 micron was chosen, since at lower diameters it is not always
possible to distinguish tabular and nontabular grains in micrographs. The term "projected
area" is used in the same sense as the terms "projection area" and "projective area"
commonly employed in the art; see, for example, James and Higgins, Fundamentals of
Photographic Theory, Morgan and Morgan, New York, p. 15.
[0045] In a preferred form offering a broad range of observed advantages the present invention
employs high aspect ratio silver bromoiodide emulsions. High aspect ratio tabular
grain silver bromoiodide emulsions can be prepared by introducing into a conventional
reaction microcell for silver halide precipitation equipped with an efficient stirring
mechanism dispersing medium. Typically the dispersing medium initially introduced
into the reaction microcell is at least about 10 percent by weight based on total
weight of the dispersing medium present in the silver bromoiodide emulsion at the
conclusion of grain precipitation. Since dispersing medium can be removed from the
reaction microcell by ultrafiltration during silver bromoiodide grain precipitation,
as taught by Mignot U.S. Patent 4,334,012, here incorporated by reference, it is appreciated
that the volume of dispersing medium initially present in the reaction microcell can
equal or even exceed the volume of the silver bromoiodide emulsion present in the
reaction microcell at the conclusion of grain precipitation. The dispersing medium
initially introduced into the reaction microcell is preferably water or a dispersion
of peptizer in water, optionally containing other ingredients, such as one or more
silver halide ripening agents and/or metal dopants, more specifically described below.
Additional dispersing medium is added to the reaction microcell with the silver and
halide salts and can also be introduced through a separate jet. It is common practice
to adjust the proportion of dispersing medium, particularly to increase the proportion
of peptizer, after the completion of the salt introductions.
[0046] A minor portion of the bromide salt employed in forming the silver bromoiodide grains
is initially present in the reaction microcell to adjust the bromide ion concentration
of the dispersing medium at the outset of silver bromoiodide precipitation. Also,
the dispersing medium in the reaction microcell is initially substantially free of
iodide ions. As employed herein, the term "substantially free of iodide ions" as applied
to the contents of the reaction microcell means that there are insufficient iodide
ions present as compared to bromide ions to precipitate as a separate silver iodide
phase. It is contemplated to maintain the pBr of the reaction microcell initially
in the range of from at or below 1.6 to at or above 0.6. In the absence or diminished
presence of a peptizer such as gelatin higher initial pBr levels can be employed.
(As herein employed, pBr is defined as the negative logarithm of bromide ion concentration.
pH, pCl, pI, and pAg are similarly defined for hydrogen, chloride, iodide, and silver
ion concentrations, respectively.)
[0047] During precipitation silver, bromide, and iodide salts are added to the reaction
microcell by techniques well known in the precipitation of silver bromoiodide grains.
Typically an aqueous silver salt solution of a soluble silver salt, such as silver
nitrate, is introduced into the reaction microcell concurrently with the introduction
of the bromide and iodide salts. The bromide and iodide salts are also typically introduced
as aqueous salt solutions, such as aqueous solutions of one or more soluble ammonium,
alkali metal (e.g., sodium or potassium), or alkaline earth metal (e.g., magnesium
or calcium) halide salts. The silver salt is at least initially introduced into the
reaction microcell separately from the iodide salt. The iodide and bromide salts can
be added to the reaction microcell separately or as a mixture.
[0048] It is possible to increase the permissible latitude of pBr during concurrent introduction
of silver, bromide, and iodide salts. Raising pBr values above 2.2 during tabular
grain growth results in thickening of the grains, but can be tolerated in many instances
while still realizing an average aspect ratio of greater than 8:1.
[0049] As an alternative to the introduction of silver, bromide, and iodide salts as aqueous
solutions, it is specifically contemplated to introduce the silver, bromide, and iodide
salts, initially or in the growth stage, in the form of fine silver halide grains
suspended in dispersing medium. The grains are sized so that they are readily Ostwald
ripened onto larger grain nuclei, if any are present, once introduced into the reaction
microcell. The maximum useful grain sizes will depend on the specific conditions within
the reaction microcell, such as temperature and the presence of solubilizing and ripening
agents. Silver bromide, silver iodide, and/or silver bromoiodide grains can be introduced.
(Since bromide and/or iodide are precipitated in preference to chloride, it is also
possible to employ silver chlorobromide and silver chlorobromoiodide grains.) The
silver halide grains are preferably very fine.
[0050] Subject to the pBr requirements set forth above, the concentrations and rates of
silver, bromide, and iodide salt introductions can take any convenient conventional
form. The silver and halide salts are preferably introduced in concentrations of from
0.1 to 5 moles per liter, although broader conventional concentration ranges, such
as from 0.01 mole per liter to saturation, for example, are contemplated. Specifically
preferred precipitation techniques are those which achieve shortened precipitation
times by increasing the rate of silver and halide salt introduction during the run.
The rate of silver and halide salt introduction can be increased either by increasing
the rate at which the dispersing medium and the silver and halide salts are introduced
or by increasing the concentrations of the silver and halide salts within the dispersing
medium being introduced. It is specifically preferred to increase the rate of silver
and halide salt introduction, but to maintain the rate of introduction below the threshhold
level at which the formation of new grain nuclei is favored--i.e., to avoid renucleation,
as taught by Irie U.S. Patent 3,650,757, Kurz U.S. Patent 3,672,900, Saito U.S. Patent
4,242,445, Wilgus German OLS 2,107,118, Teitscheid et al European Patent Application
80102242, and Wey "Growth Mechanism of AgBr Crystals in Gelatin Solution", Photographic
Science and Engineering, Vol. 21, No. 1, January/February 1977, p. 14, et. seq. By
avoiding the formation of additional grain nuclei after passing into the growth stage
of precipitation, relatively monodispersed tabular silver bromoiodide grain populations
can be obtained. Emulsions having coefficients of variation of less than about 30
percent can be prepared. (As employed herein the coefficient of variation is defined
as 100 times the standard deviation of the grain diameter divided by the average grain
diameter.) By intentionally favoring renucleation during the growth stage of precipitation,
it is, of course, possible to produce polydispersed emulsions of substantially higher
coefficients of variation. To reduce the coefficient of variation of tabular grains
it is preferred to increase pBr, either gradually or abruptly, such as by the gradual
or abrupt separate addition of dispersing medium early in the precipitation.
[0051] The concentration of iodide in the silver bromoiodide emulsions can be controlled
by the introduction of iodide salts. Any conventional iodide concentration can be
employed. Even very small amounts of iodide--e.g., as low as 0.05 mole percent--are
recognized in the art to be beneficial. In their preferred form the emulsions of the
present invention incorporate at least about 0.1 mole percent iodide. Silver iodide
can be incorporated into the tabular silver bromoiodide grains up to its solubility
limit in silver bromide at the temperature of grain formation. Thus, silver iodide
concentrations of up to about 40 mole percent in the tabular silver bromoiodide grains
can be achieved at precipitation temperatures of 90°C. In practice precipitation temperatures
can range down to near ambient room temperatures--e.g., about 30°C. It is generally
known in the art to optimize iodide concentrations for the specific photographic application.
[0052] The relative proportion of iodide and bromide salts introduced into the reaction
microcell during precipitation can be maintained in a fixed ratio to form a substantially
uniform iodide profile in the tabular silver bromoiodide grains or varied, as by increasing
the proportion of iodide in annular or otherwise laterally displaced regions of high
aspect ratio tabular grain silver bromoiodide emulsions as compared to central regions
of the tabular grains. In a variant form it is specifically contemplated to terminate
iodide or bromide and iodide salt addition to the reaction microcell prior to the
termination of silver salt addition so that excess halide reacts with the silver salt.
This results in a shell of silver bromide being formed on the tabular silver bromoiodide
grains. Thus, it is apparent that the tabular silver bromoiodide grains of the present
invention can exhibit substantially uniform or graded iodide concentration profiles
and that the gradation can be controlled, as desired, to favor higher iodide concentrations
internally or at or near the surfaces of the tabular silver bromoiodide grains.
[0053] High aspect ratio tabular grain silver bromide emulsions lacking iodide can be prepared
by the process described above modified to exclude iodide. High aspect ratio tabular
grain silver bromide emulsions can alternatively be prepared following procedures
previously taught in the art.
[0054] The tabular grain silver bromide and bromoiodide emulsions of this invention typically
contain (lll) crystal planes. Silver bromide tabular grains which appear square or
rectangular in projected area have been prepared by ripening seed grains in the substantial
absence of nonhalide silver ion complexing agents in the pAg range of from 5.0 to
8.0. Such tabular grains are believed to be bounded by {100} crystal faces. The tabular
grain silver bromide and silver bromoiodide emulsions of this invention can contain
tabular grains bounded by {100}, {110}, and {111} crystal faces, and the selection
of grain crystal faces can be controlled by selection of grain precipitation and growth
conditions.
[0055] Certain of the advantages achieved in the practice of this invention, are independent
of the halide content of the high aspect ratio tabular grain emulsions. A process
of preparing tabular silver chloride grains which are substantially internally free
of both silver bromide and silver iodide employs a double-jet precipitation process
wherein chloride and silver salts are concurrently introduced into a reaction microcell
containing dispersing medium in the presence of ammonia. During chloride salt introduction
the pAg within the dispersing medium is in the range of from 6.5 to 10 and the pH
in the range of from 8 to 10. The presence of ammonia at higher temperatures tends
to cause thick grains to form, therefore precipitation temperatures are limited. The
process can be optimized to produce high aspect ratio tabular grain silver chloride
emulsions.
[0056] A process of preparing tabular grains of at least 50 mole percent chloride having
opposed crystal faces lying in {111} crystal planes and, in one preferred form, at
least one peripheral edge lying parallel to a <211> crystallographic vector in the
plane of one of the major surfaces can be practiced by reacting aqueous silver and
chloride-containing halide salt solutions in the presence of a crystal habit modifying
amount of an amino-substituted azaindene and a peptizer having a thioether linkage.
[0057] Tabular grain emulsions wherein the silver halide grains contain chloride and bromide
in at least annular grain regions and preferably throughout are contemplated. The
tabular grain regions containing silver, chloride, and bromide are formed by maintaining
a molar ratio of chloride and bromide ions of from 1.6:1 to about 260:1 and the total
concentration of halide ions in the reaction microcell in the range of from 0.10 to
0.90 normal during introduction of silver, chloride, bromide, and, optionally, iodide
salts into the reaction microcell. The molar ratio of silver chloride to silver bromide
in the tabular grains can range from 1:99 to 2:3.
[0058] High aspect ratio tabular grain emulsions useful in the practice of this invention
can have extremely high average aspect ratios. Tabular grain average aspect ratios
can be increased by increasing average grain diameters. This can produce sharpness
advantages, but maximum average grain diameters are generally limited by granularity
requirements for a specific photographic application. Tabular grain average aspect
ratios can also or alternatively be increased by decreasing average grain thicknesses.
When silver coverages are held constant, decreasing the thickness of tabular grains
generally improves granularity as a direct function of increasing aspect ratio. Hence
the maximum average aspect ratios of the tabular grain emulsions of this invention
are a function of the maximum average grain diameters acceptable for the specific
photographic application and the minimum attainable tabular grain thicknesses which
can be produced. Maximum average aspect ratios have been observed to vary, depending
upon the precipitation technique employed and the tabular grain halide composition.
The highest observed average aspect ratios, 500:1, for tabular grains with photographically
useful average grain diameters, have been achieved by Ostwald ripening preparations
of silver bromide grains, with aspect ratios of 100:1, 200:1, or even higher being
obtainable by double-jet precipitation procedures. The presence of iodide generally
decreases the maximum average aspect ratios realized, but the preparation of silver
bromoiodide tabular grain emulsions having average aspect ratios of 100:1 or even
200:1 or more is feasible. Average aspect ratios as high as 50:1 or even 100:1 for
silver chloride tabular grains, optionally containing bromide and/or iodide, can be
prepared as taught above.
[0059] Modifying compounds can be present during tabular grain precipitation. Such compounds
can be initially in the reaction microcell or can be added along with one or more
of the salts according to conventional procedures. Modifying compounds, such as compounds
of copper, thallium, lead, bismuth, cadmium, zinc, middle chalcogens (i.e., sulfur,
selenium, and tellurium), gold, and Group VIII noble metals, can be present during
silver halide precipitation, as illustrated by Arnold et al U.S. Patent 1,195,432,
Hochstetter U.S. Patent 1,951,933, Trivelli et al U.S. Patent 2,448,060, Overman U.S.
Patent 2,628,167, Mueller et al U.S. Patent 2,950,972, Sidebotham U.S. Patent 3,488,709,
Rosecrants et al U.S. Patent 3,737,313, Berry et al U.S. Patent 3,772,031, Atwell
U.S. Patent No. 4,269,927, and Research Disclosure, Vol. 134, June 1975, Item 13452.
Research Disclosure and its predecessor, Product Licensing Index, are publications
of Industrial Opportunities Ltd.; Homewell, Havant; Hampshire, P09 lEF, United Kingdom.
The tabular grain emulsions can be internally reduction sensitized during precipitation,
as illustrated by Moisar et al, Journal of Photographic Science, Vol. 25, 1977, pp.
19-27.
[0060] Features of the high aspect ratio tabular grain emulsions not specifically described
above can take conventional forms. Conventional silver halide emulsion preparation,
washing, sensitization, and addenda features are described, for example, in Research
Disclosure, Item 17643, cited above, particularly Sections I through VII, IX, and
X.
[0061] The foregoing description of specific radiation-sensitive portions of the photographic
elements of this invention is recognized to be illustrative only of the varied known
photographic materials which can be employed. Similarly the uses and advantages of
the photographic elements according to this invention will be apparent and can be
generally appreciated from the following illustrative description directed to certain
preferred silver halide emulsion photographic elements and their use.
Silver Imaging With Silver Halides
[0062] The photographic elements can be imagewise exposed with various forms of energy,
which encompass the ultraviolet and visible (e.g., actinic) and infrared regions of
the electromagnetic spectrum as well as electron beam and beta radiation, gamma ray,
X-ray, alpha particle, neutron radiation and other forms of corpuscular and wave-like
radiant energy in either noncoherent (random phase) forms or coherent (in phase) forms,
as produced by lasers. Exposures can be monochromatic, orthochromatic or panchromatic.
Imagewise exposures at ambient, elevated or reduced temperatures and/or pressures,
including high or low intensity exposures, continuous or intermittent exposures, exposure
times ranging from minutes to relatively short durations in the millisecond to microsecond
range and solarizing exposures, can be employed within the useful response ranges
determined by conventional sensitometric techniques, as illustrated by T. H. James,
The Theory of the Photographic Process, 4th Ed. , Macmillan, 1977, Chapters 4, 6,
17, 18 and 23.
[0063] Referring to photographic element 100 in Figures 1A and 1B, in a simple, illustrative
form of this invention the support 102 is formed of a reflective material, preferably
and hereinafter referred to as a white reflective material, although colored reflective
materials are contemplated. The radiation-sensitive material 116 is a silver halide
emulsion of the type which is capable of producing a viewable image as a result solely
of exposure and, optionally, dry processing. Such silver halide emulsions can be of
the printout type--that is, they can produce a visible image by the direct action
of light with no subsequent action required--or of the direct-print type--that is,
they can form a latent image by high intensity imagewise exposure and produce a visible
image by subsequent low intensity light exposure. A heat stabilization step can be
interposed between the exposure steps. In still another form the silver halide emulsion
can be of a type which is designed for processing solely by heat.
[0064] The preferred printout emulsions are illustrated by Research Disclosure, Item 17643,
Section XXVI; the direct print emulsions by Section XVII, and the heat processing
emulsion by Section XXIV. Photothermographic silver halide systems that are useful
are also described in greater detail in Research Disclosure, Vol. 170, June 1978,
Item 17029.
[0065] It is recognized that silver halide photographic elements can exhibit lateral image
spreading solely as a result of lateral reflection of exposing radiation from beneath
an emulsion layer. Lateral image spreading of this type is referred to in the art
as halation, since the visual effect can be to produce a halo around a bright object,
such as an electric lamp, which is photographed. Other objects which are less bright
are not surrounded by halos, but their photographic definition is significantly reduced
by the reflected radiation. To overcome this difficulty conventional photographic
elements commonly are provided with layers, commonly referred to as antihalation layers,
of light absorbing materials on a support surface which would otherwise reflect radiation
to produce halation in an emulsion layer. Such antihalation layers are commonly recognized
to have the disadvantage that they must be entirely removed from the photographic
element prior to viewing in most practical applications. A more fundamental disadvantage
of antihalation layers which is not generally stated, since it is considered inescapable,
is that the radiation which is absorbed by the antihalation layer cannot be available
to expose the silver halide grains within the emulsion.
[0066] Another approach to reducing lateral image spreading attributable to light scatter
in silver halide emulsions is to incorporate intergrain absorbers. Dyes or pigments
similar to those described above for incorporation in the second support elements
are commonly employed for this purpose. The disadvantage of intergrain absorbers is
that they significantly reduce the photographic speed of silver halide emulsions.
They compete with the silver halide grains in absorbing photons, and many dyes have
a significant desensitizing effect on silver halide grains. Like the absorbing materials
in antihalation layers, it is also necessary that the intergrain absorbers be removed
from the silver halide emulsions for most practical applications, and this can also
be a significant disadvantage.
[0067] Another approach herein suggested is to coat a high aspect ratio tabular grain or
conventional silver halide emulsion on a support as one or more continuous layers.
The emulsion layer or layers can thereafter be exposed through a mask, thereby achieving
exposure in a pattern corresponding to a pattern of microcell walls. Development of
the exposed silver halide lying in areas corresponding to microcell walls results
in the development of silver which in turn increases the density of these microcell
wall forming regions. Upon subsequent imagewise exposure of the emulsion layer or
layers radiation that would otherwise be scattered laterally is intercepted by the
developed silver in the microcell wall forming regions. In this instance the microcell
walls are capable of intercepting laterally deflected exposing radiation, but remain
laterally permeable to the lateral migration of incorported addenda or processing
materials. Thus, migration of materials between developing and nondeveloping areas
can occur. Migration between developing and nondeveloping areas can achieve useful
photographic effects, such as edge effects, often employed to improve sharpness. In
the instance in which a dye image is formed, after imagewise exposure developed silver
forming increased density in a microcell wall pattern as well as silver developed
as a result of imagewise exposure can be removed by bleaching. By bleaching no microcell
wall pattern may be distinguishable in the finally processed element.
[0068] When light strikes the photographic element 100 so that it enters one of the microcells
108, a portion of the light can be absorbed immediately by the silver halide grains
of the emulsion 116 while the remaining light traverses the reaction microcell without
being absorbed. If a given photon penetrates the emulsion without being absorbed,
it will be redirected by the white bottom wall 114 of the support 102 so that the
photon again traverses at least a portion of the reaction microcell. This presents
an additional opportunity for the photon to strike and be absorbed by a silver halide
grain. Since it is recognized that the average photon strikes several silver halide
grains before being absorbed, at least some of the exposing photons will be laterally
deflected before they are absorbed by silver halide. The white lateral walls 110 of
the support act to redirect laterally deflected photons so that they again traverse
a portion of the silver halide emulsion within the same reaction microcell. This avoids
laterally directed photons being absorbed by silver halide in adjacent reaction microcells.
Whereas, in a conventional silver halide photographic element having a continuous
emulsion coating on a white support, redirection of photons back into the emulsion
by a white support is achieved only at the expense of significant lateral image spreading--e.g.,
halation, in the photographic element 100 the white support enhances the opportunity
for photon absorption by the emulsion contained within the reaction microcells while
at the same time achieving a visually acceptable predefined limit on lateral image
spread. The result can be seen photographically both in terms of improved photographic
speed and contrast as well as sharper image definition. Thus, the advantages which
can be gained by employing antihalation layers and intergrain absorbers in conventional
photographic elements are realized in the photographic elements of the present invention
without their use and with the additional surprising advantages of speed and contrast
increase. Further, none of the disadvantages of antihalation layers and intergrain
absorbers are encountered. For reasons which will become more apparent in discussing
other forms of this invention, it should be noted , however, that the photographic
elements of the present invention can employ antihalation layers and intergrain absorbers,
if desired, while retaining distinct advantages.
[0069] Most commonly silver halide photographic elements are intended to be processed using
aqueous alkaline liquid solutions. When the silver halide emulsion contained in the
reaction microcell 108 of the element 100 is of a developing out type rather than
a dry processed printout, direct-print or thermally processed type, as illustrated
above, all of the advantages described above are retained. In addition, having the
emulsion within reaction microcells offers protection against lateral image spreading
as a result of chemical reactions taking place during processing. For example, microscopic
inspection of silver produced by development reveals filaments of silver. The silver
image in emulsions of the developing out type can result from chemical (direct) development
in which image silver is provided by the silver halide grain at the site of silver
formation or from physical development in which silver is provided from adjacent silver
halide grains or silver or other metal is provided from other sources. Opportunity
for lateral image spreading in the absence of reaction microcells is particularly
great when physical developmen: is occurring. Even under chemical development conditions,
such as where development is occurring in the presence of a silver halide solvent,
extended silver filaments can be found. Frequently a combination of chemical and physical
development occurs during processing. Having the silver developed confined within
the reaction microcells circumscribes the areal extent of silver image spreading.
it is specifically contemplated to dedicate a portion of the microcells to developing
agent or other addenda, if desired. For example, by dedicating a few recurring microcells
in an array so that they contain developing agent, an activating solution can be used
for processing. Other uses of dedicated microcells are, of course, possible.
[0070] The light-sensitive silver halide contained in the photographic elements can be processed
following exposure to form a visible image by conventional means, as illustrated in
Research Disclosure, Item 17643, cited above, Sections XIX and XX.
[0071] In one specifically preferred form of the invention the photographic element is infectiously
developed. The term "infectious" is employed in the art to indicate that silver halide
development is not confined to the silver halide grain which provides the latent image
site. Rather, adjacent grains which lack latent image sites are also developed because
of their proximity to the initially developable silver halide grain.
[0072] Infectious development of continuously coated silver halide emulsion layers is practiced
in the art principally in producing high contrast photographic images for exposing
lithographic plates. However, care must be taken to avoid unacceptable lateral image
spreading because of the infectious development. In practicing the present invention
the reaction microcells provide boundaries limiting lateral image spread. Since the
microcells control lateral image spreading, the infectiousness or tendency of the
developer to laterally spread the image can be as great and is, preferably, greater
than in conventional infectious developers. In fact, one of the distinct advantages
of infectious development is that it can spread or integrate silver image development
over the entire area of the reaction microcell. This avoids silver image graininess
within the reaction microcell and permits the reaction microcell to be viewed externally
as a uniform density unit rather than a circumscribed area exhibiting an internal
range of point densities.
[0073] The combination of reaction microcells and infectious development permits unique
imaging results. For example, very high densities can be obtained in reaction microcells
in which development occurs, since the infectious nature of the development drives
the development reaction toward completion. At the same time, in other reaction microcells
where substantially no development is initiated, very low density levels can be maintained.
The result is a very high contrast photographic image. It is known in the art to read
out photographic images electronically by scanning a photographic element with a light
source and a photosensor. The density sensed at each scanning location on the element
can be recorded electronically and reproduced by conventional means, such as a cathode
ray tube, on demand. It is well known also that digital electronic computers employed
in recording and reproducing the information taken from the picture employ binary
logic. In electronically scanning the photographic element 100, each reaction microcell
can provide one scanning site. By using infectious development to produce high contrast,
the photographic image being scanned provides either a substantially uniform dark
area or a light area in each reaction microcell. In other words, the information taken
from the photographic element is already in a binary logic form, rather than an analog
form produced by continuous tone gradations. The photographic elements are then comparatively
simple to scan electronically and are very simple and convenient to record and reproduce
using digital electronic equipment.
[0074] Techniques for infectious development as well as specific compositions useful in
the practice of this invention are disclosed by James, The Theory of the Photographic
Process, 4th Ed., Macmillan, pp. 420 and 421 (1977); Stauffer et al, Journal Franklin
Institute, Vol. 238, p. 291 (1944); and Beels et al, Journal Photographic Science,
Vol. 23, p. 23 (1975). In a preferred form a hydrazine or hydra- zide is incorporated
in the reaction microcell and/or in a developer and the developer containing a developing
agent having a hydroxy group, such as a hydroquinone. Preferred developers of this
type are disclosed in Stauffer et al U.S. Patent 2,419,974, Trivelli et al U.S. Patent
2,419,975 and Takada et al Belgian Patent 855,453.
[0075] The foregoing discussion of the use and advantages of the photographic element 100
has been by reference to preferred forms in which the support 102 is a white, reflection
print. It can be used to form an image to be scanned electronically as has been described
above. The element in this form can be used also as a master for reflection printing.
[0076] It is also contemplated that the support 102 can be transparent. In one specifically
preferred form the underlying portion 112 of the support is transparent and colorless
while the integral lateral walls contain a colorant therein, such as a dye, so that
a substantial density is presented to light transmission through the lateral walls
between the major surfaces 104 and 106 and between adjacent reaction microcells. In
this form, the dyed walls perform the function of an intergrain absorber or antihalation
layer, as described above, while avoiding certain disadvantages which these present.
For example, since the dye is in the lateral walls and not in the emulsion, dye desensitization
of the silver halide emulsion is minimized, if not eliminated. At the same time, it
is unnecessary to decolorize or remove the dye, as is normally undertaken when an
antihalation layer is provided.
[0077] In addition, this form of the support element 102 has unique advantages in use that
have no direct counterpart in photographic elements having continuous silver halide
emulsion layers. The photographic element when formed with a transparent underlying
portion and dyed lateral walls is uniquely suited for use as a master in transmission
printing. That is, after processing to form a photographic image, the photographic
element can be used to control exposure of a photographic print element, such as a
photographic element according to this invention having a white support, as described
above, or a conventional photographic element, such as a photographic paper. In exposing
the print element through the image bearing photographic element 100 the density of
the lateral walls confines light transmission during exposure to the portions of the
support 102 underlying the reaction microcells. Where the reaction microcells are
relatively transparent--i.e., minimum density areas, the print exposure is higher
and in maximum density areas of the master, print exposure is lowest. The effect is
to give a print in which highly exposed areas of the print element are confined to
dots or spaced microareas. Upon subsequent processing to form a viewable print image
the eye can fuse adjacent dots or micro-areas to give the visual effect of a continuous
tone image. The effects of the nontransmission of exposing light through the lateral
walls has been adequately described further above in connection with the support elements
and the materials from which they can be formed. Since the eye is quite sensitive
to small differences in minimum density, it is generally preferred that the lateral
walls be substantially opaque. However, it is contemplated that some light can be
allowed to penetrate the lateral walls during printing. This can have the useful effect,
for instance, of bringing up the overall density in the print image. As mentioned
above, it is also contemplated to displace the print element with respect to the master
during printing so that a continuous print image is produced and any reduced density
effect due to reduced transmission through the lateral walls is entirely avoided.
Similarly, when the photographic element in this form is used to project an image,
the lateral spreading of light during projection will fuse adjacent microcell areas
so that the lateral walls are not seen.
[0078] To illustrate still another variant form of the invention, advantages can be realized
when the support element is entirely transparent and colorless. In applications where
the silver halide emulsion is a developing out emulsion and is intended to be scanned
pixel by pixel, as in the infectiously developed electron beam scanned application
described above, control of lateral image spreading during development is, of course,
independent of the transparency or coloration of the support element. However, even
when the lateral walls are transparent and colorless, the protection against light
scattering between adjacent microcells can still be realized in some instances, as
discussed below in connection with photographic element 200.
[0079] The photographic elements 200 through 1000 share structural similarities with photographic
elements 100 and are similar in terms of both uses and advantages. Accordingly, the
uses of these elements are discussed only by reference to differences which further
illustrate the invention.
[0080] The photographic element 200 differs from the element 100 in that the reaction microcells
208 have curved walls rather than separate bottom and side walls. This wall configuration
is more convenient to form by certain fabrication techniques. It also has the advantage
of being more efficient in redirecting exposing radiation back toward the center of
the reaction microcell. For example, when the photographic element 200 is exposed
from above (in the orientation shown), light striking the curved walls of the reaction
microcells can be reflected inwardly so that it again traverses the emulsion 216 contained
in the microcell. When the support is transparent and the element is exposed from
below, a higher refraction index for the emulsion as compared to the support can cause
light to bend inwardly. This directs the light toward the emulsion 216 within the
microcell and avoids scattering of light to adjacent microcells.
[0081] A second significant difference in the construction of the photographic element 200
as compared to the photographic element 100 is that the upper surface of the emulsion
216 lies substantially below the second major surface 206 of the support 202. The
recessed position of the emulsion within the support provides it with mechanical protection
against abrasion, kinking, pressure induced defects and matting. Although the emulsion
up to the second major surface 106, it also affords protection for the emulsion 116.
In all forms of the photographic elements of this invention, at least one component
of the radiation-sensitive portion of the element is contained within the reaction
microcells and additional protection is afforded against at least abrasion. It is
specifically contemplated that the lateral walls of the support can perform the function
of matting agents and that these agents can therefore be omitted without encountering
disadvantages to use, such as blocking. However, conventional matting agents, such
as illustrated by Research Disclosure, Item 17643, cited above, Section XVI, can be
employed, particularly in those forms of the photographic elements more specifically
discussed below containing at least one continuous hydrophilic colloid layer overlying
the support and the reaction microcells thereof.
[0082] The photographic element 300 differs from photographic element 100 in two principal
respects. First, relatively thin extensions 314 of emulsion can extend between and
connect adjacent pixels. Second, the support is made up of two separate support elements
302 and 306. The photographic element 300 can be employed identically as photographic
element 100. The imaging effect of the extensions 314 are in most instances negligible
and can be ignored in use. In the form of the element 300 in which the first support
element 302 is transparent and the second support element 308 is substantially light
impenetrable exposure of the element through the first support element avoids exposure
of the extensions 314. Where the emulsion is negative-working, this results in no
silver density being generated between adjacent reaction microcells. Where the extensions
are not of negligible thickness and no steps are taken to avoid their exposure, the
performance of the photographic element combines the features of a continuously coated
silver halide emulsion layer and an emulsion contained within a reaction microcell.
[0083] The photographic element 400 differs from photographic element 100 in two principal
respects. First, the reaction microcell 408 is of relatively extended depth as compared
with the reaction microcells 108, and, second, the radiation-sensitive portion of
the element is divided into two separate components 416 and 418. These two differences
can be separately employed. That is, the photographic element 100 could be modified
to provide a second component like 418 overlying the second major surface 106 of the
support, or the depth of the reaction microcells could be increased. These two differences
are shown and discussed together, since in certain preferred embodiments they are
particularly advantageous when employed in combination.
[0084] While silver halide absorbs light, many photons striking a silver halide emulsion
layer pass through without being absorbed. Where the exposing radiation is of a more
energetic form, such as X-rays, the efficiency of silver halide in absorbing the exposing
radiation is even lower. While increasing the thickness of a silver halide emulsion
layer increases its absorption efficiency, there is a practical limit to the thickness
of silver halide emulsion layers, since thicker layers cause more lateral scattering
of exposing radiation and generally result in greater lateral image spreading.
[0085] In a preferred form a radiation-sensitive silver halide emulsion forms the component
confined within the reaction microcell 408. Thus lateral spreading is controlled not
by the thickness of the silver halide or the depth of the microcell, but by the lateral
walls of the microcell. It is then possible to extend the depth of the microcell and
the thickness of the silver halide emulsion that is presented to the exposing radiation
as compared to the thickness of continuously coated silver halide emulsion layers
without encountering a penalty in terms of lateral image spreading. For example, the
depth of the reaction microcells and the thickness of the silver halide emulsion can
both be substantially greater than the width of the microcells. In the case of a radiographic
element intended to be exposed directly by X-rays it is then possible to provide relatively
deep reaction microcells and to improve the absorption efficiency--i.e., speed, of
the radiographic element. As discussed above, microcell depths and silver halide emulsion
thicknesses can be up to 1000 microns or more. Microcell depths of from about 20 to
100 microns preferred for this application are convenient to form by the same general
techniques employed in forming shallower microcells.
[0086] In one preferred form, the component 418 is an internally fogged silver halide emulsion.
In this form, the components 416 and 418 can correspond to the surface-sensitive and
internally fogged emulsions, respectively, disclosed by Luckey et al U.S. Patents
2,996,382, 3,397,987 and 3,705,858; Luckey U.S. Patent 3,695,881; Research Disclosure,
Vol. 134, June 1975, Item 13452; Millikan et al Defensive Publication T-0904017, April
1972 and Kurz Research Disclosure, Vol. 122, June 1974, Item 12233. In a preferred
form, the surface-sensitive silver halide emulsion contains at least 1 mole percent
iodide, typically from 1 to 10 mole percent iodide, based on total halide present
as silver halide. The surface-sensitive silver halide is preferably a silver bromoiodide
and the internally fogged silver halide is an internally fogged converted-halide which
is at least 50 mole percent bromide and up to 10 mole percent iodide (the remaining
halide being chloride) based on total halide. Upon exposure and development of the
iodide containing surface-sensitive emulsion forming the component 416 with a surface
developer, a developer substantially incapable of revealing an internal latent image
(quantitatively defined in the Luckey et al patents), iodide ions migrate to the component
418 and render the internally fogged silver halide grains developable by the surface
developer. In unexposed pixels surface-sensitive silver halide is not developed, therefore
does not release iodide ions, and the internally fogged silver halide emulsion component
in these pixels cannot be developed by the surface developer. The result is that the
silver image density produced by the radiation-sensitive emulsion component 416 is
enhanced by the additional density produced by the development of the internally fogged
silver halide grains without any significant effect on minimum density areas. It is,
of course, unnecessary that the component 416 be of extended thickness in order to
achieve an increase in density using the component 418, but when both features are
present in combination a particularly fast and efficient photographic element is provided
which is excellently suited to radiographic as well as other photographic applications.
In variant forms of the invention the surface-sensitive and internally fogged emulsions
can be blended rather than coated in separate layers. When blended, it is preferred
that the emulsions be located entirely within the reactive microcells.
[0087] In one preferred form of the photographic element 500, the first support element
502 is both transparent and colorless. The second support element 508 is relatively
deformable and contains a dye, such as a yellow dye. The components 516 and 518 can
correspond to the surface-sensitive and internally fogged silver halide emulsion components
416 and 418, respectively, described above. For this specific embodiment only, the
spectral sensitivity of the surface-sensitive emulsion is limited to the blue region
of the visible spectrum. The layer 515 can be one or a combination of transparent,
colorless conventional subbing layers. Conventional subbing layers and materials are
disclosed in the various patents cited above in connection with conventional photographic
support materials.
[0088] In one exemplary use the radiation-sensitive emulsion component 516 can be exposed
through the transparent first support element 502 and the underlying portion 512 of
the second support element 508. While the second support element contains a dye to
prevent lateral light scattering through the lateral walls 510, the thickness of the
underlying portion of the second support element is sufficiently thin that it offers
only negligible absorption of incident light. As another alternative the element in
this form can be exposed through the second emulsion component 518 instead of the
support, if desired.
[0089] In an alternative form of the photographic element 500 the emulsion component 516
can correspond to the emulsion component 418 and the emulsion component 518 can correspond
to the emulsion component 416. In this form the radiation-sensitive silver halide
emulsion is coated as a continuous layer while the internally fogged silver halide
emulsion is present in the microcell 514. Exposure through the support exposes only
the portion of the radiation-sensitive emulsion component 518 overlying the microcell,
since the dye in the lateral walls . 510 of the second support element effectively
absorbs light while the underlying portion 512 of the second support element is too
thin to absorb light effectively. Lateral image spreading in the continuous emulsion
component is controlled by limiting its exposure to the area subtended by the microcell.
Lateral image spreading by the internally fogged emulsion is limited by the walls
of the microcell.
[0090] In still another form of the photographic element 500 the first and second support
elements can be formed from any of the materials, including colorless transparent,
white and absorbing materials. The layer 515 can be chosen to provide a reflective
surface, such as a mirror surface. For example, the layer 515 can be a vacuum vapor
deposited layer of silver or another photographically compatible metal which is preferably
overcoated with a thin transparent layer, such as a hydrophilic colloid or a film-forming
polymer. The components 516 and 518 correspond to the components 416 and 418, respectively,
so that the only radiation-sensitive material is confined within the microcell 514.
[0091] In exposing the element in this form from the emulsion side the reflective surface
redirects light within the microcell so that light is either absorbed by the emulsion
component 516 on its first pass through the microcell or is redirected so that it
traverses the microcell one or more additional times, thereby increasing its chances
of absorption. Upon development image areas appear as dark areas on a reflective background.
If a dye image is produced, as discussed below, the developed silver and silver mirror
can be concurrently removed by bleaching so that a dye image on a typical white reflective
or colorless transparent support is produced.
[0092] A very high contrast photographic element can be achieved by employing as layer 515
a reactive material, such as a metal or metal compound capable of forming a high density
metal sulfide--e.g., silver oxide, thereby selectively converting the reflecting surface
within the reaction microcells to a light absorbing form. For instance, if a developer
inhibitor releasing (DIR) coupler of the type which releases an organic sulfide is
incorporated in the emulsion within the reaction microcells and development is undertaken
with a color developing agent, the color developing agent can react with exposed silver
halide to form silver and oxidized color developing agent. The oxidized color developing
agent can then couple with the DIR coupler to release an organic sulfide which is
capable of reacting with oxidized silver provided by the reactive material layer 515
in the microcells to convert silver oxide to a black silver sulfide. This increases
the maximum density obtainable in the microcells while leaving the reactive material
unaffected in minimum density areas. Thus, an increased contrast can be achieved by
this approach. Specific DIR couplers and color developing agents are described below
in connection with dye imaging. Metals and metal compounds other than silver oxide
which will react with the released organic sulfide to form a metal sulfide can be
alternatively employed.
[0093] In the foregoing discussion of elements 400 and 500 two component radiation-sensitive
means 416 and 418 or 516 and 518 are described in which the components work together
to increase the maximum density obtainable. In another form the components can be
chosen so that they work together to minimize the density obtained in areas where
silver halide is the radiation-sensitive component developed. For example, if one
of the components is a light-sensitive silver halide emulsion which contains a DIR
coupler and the-other component is a spontaneously developable silver halide emulsion
(e.g., a surface or internally fogged emulsion) imagewise exposure and processing
causes the light-sensitive emulsion to begin development as a function of light exposure.
As this emulsion is developed it produces oxidized developing agent which couples
with the DIR coupler, releasing development inhibitor. The inhibitor reduces further
development of adjacent portions of the otherwise spontaneously developable emulsion.
The spontaneously developable emulsion develops to a maximum density in areas where
development inhibitor is not released. By using a relatively low covering power light-sensitive
emulsion (e.g., a relatively coarse, high-speed emulsion) and a high covering power
spontaneously developable emulsion, it is possible to obtain images of increased contrast.
The DIR coupler can be advantageously coated in the microcells or as a continuous
layer overlying the microcells along with the radiation-sensitive emulsion, and the
spontaneously developable emulsion can be located in the alternate position. In this
arrangement the layer 515 is not one which is darkened by reaction with an inhibitor,
but can take the form, if present, of a subbing layer, if desired. The radiation-sensitive
emulsion can be either a direct-positive or negative-working emulsion. The developer
chosen is one which is a developer for both the radiation-sensitive and spontaneously
developable emulsions. Instead of being coated in a separate layer, the two emulsions
can be blended, if desired, and both coated in the reaction microcells.
[0094] It is conventional to form photographic elements with continuous emulsion coatings
on opposite surfaces of a planar transparent film support. For example, radiographic
elements are commonly prepared in this form. In a typical radiographic application
fluorescent screens are associated with the silver halide emulsion layers on opposite
surfaces of the support. Part of the X-rays incident during exposure are absorbed
by one of the fluorescent screens. This stimulates emission by the screen of light
capable of efficiently producing a latent image in the adjacent emulsion layer. A
portion of the incident X-rays pass through the element and are absorbed by the remaining
screen causing light exposure of the adjacent emulsion layer on the opposite surface
of the support. Thus two superimposed latent images are formed in the emulsion layers
on the opposite surfaces of the support. When light from a screen causes exposure
of the emulsion layer on the opposite surface of the support, this is referred to
in the art as crossover. Crossover is generally minimized since it results in loss
of image definition.
[0095] The photographic element 900 is well suited for applications employing silver halide
emulsion layers on opposite surfaces of a transparent film support. The alignment
of the reaction microcells 908A and 908B allows two superimposed photographic images
to be formed.
[0096] As an optional feature to reduce crossover, selective dying of the lateral walls
910A and 910B can be employed as described above. This can be relied upon to reduce
scattering of light from one reaction microcell to adjacent reaction microcells on
the same side of the support and adjacent, nonaligned reaction microcells on the opposite
side of the support. Another technique to reduce crossover is to color the entire
support 902 with a dye which can be bleached after exposure and/or processing to render
the support substantially transparent and colorless. Bleachable dyes suited to this
application are illustrated by Sturmer U.S. Patent 4,028,113 and Krueger U.S. Patent
4,111,699. A conventional approach in the radiographic art is to undercoat silver
halide emulsion layers to reduce crossover. For instance Stappen U.S. Patent 3,923,515
teaches to undercoat faster silver halide emulsion layers with slower silver halide
emulsion layers to reduce crossover. In applying such an approach to the present invention
a slower silver halide emulsion 916 can be provided in the reaction microcells. A
faster silver halide emulsion layer can be positioned in an overlying relationship
either in the reaction microcells or continuously coated over the reaction microcells
on each major surface 904 and 906 of the support. Instead of employing a slower silver
halide emulsion in the reaction microcells an internally fogged silver halide emulsion
can be placed in the reaction microcells as is more specifically described above.
The internally fogged silver halide emulsion is capable of absorbing crossover exposures
while not being affected in its photographic performance, since it is not responsive
to exposing radiation.
[0097] To illustrate a diverse photographic application, the photographic element 900 can
be formed so that the silver halide emulsion in the reaction microcells 908B as an
imaging emulsion while another silver halide emulsion can be incorporated in the reaction
microcells 908A. The two emulsions can be chosen to be oppositely working. That is,
if the emulsion in the microcells 908B is negative-working, then the emulsion in the
microcells 908A is positive-working. Using an entirely transparent support element
902, exposure of the element from above, in the orientation shown in Figure 9, results
in forming a primary photographic latent image in the emulsion contained in the microcells
908B. The emulsion contained in the microcells 908A is also exposed, but to some extent
the light exposing it will be scattered in passing through the overlying emulsion,
microcells and support portions. Thus, the emulsion in the microcells 908B in this
instance can be used to form an unsharp mask for the overlying emulsion. In one optional
form specifically contemplated an agent promoting infectious development can be incorporated
in the emulsion providing the unsharp mask. This allows image spreading within the
microcells, but the lateral walls of the microcells limits lateral image spreading.
Misalignment of the microcells 908A and 908B can also be relied upon to decrease sharpness
in the underlying emulsion. An additional approach is to size the microcells 908A
so that they are larger than the microcells 908B. Any combination of these three approaches
can, if desired, be used. Instead of employing oppositely working emulsions in the
microcells 908A and 908B, the emulsions can both be negatively working, for example.
The emulsion in the microcells 908A and
B differ in speed (or spectral sensitivity), however, so that the emulsion in microcells
908B is imagewise exposed and processed without producing an image in the microcells
908A. Thereafter exposure of the emulsion in microcells 908A through the image present
in the microcells 908B, followed by processing produces an unsharp mask in the microcells
908A. It is recognized in the art that unsharp masking can have the result of increasing
image sharpness, as discussed in Mees and James, The Theory of the Photographic Process,
3rd Ed., Macmillan, 1966, p. 495. Where the photographic element is used as a printing
master, any increase in minimum density attributable to masking can be eliminated
by adjustment of the printing exposure.
[0098] In the photographic element 1000 the lenticular surface 1004 can have the effect
of obscuring the lateral walls 1010 separating adjacent reaction microcells 1008.
Where the lateral walls are relatively thick, as where very small pixels are employed,
the lenticular surface can laterally spread light passing through the microcell portion
of each pixel so that the walls are either not seen or appear thinner than they actually
are. In this use the support 1002 is colorless and transparent, although the lateral
walls 1010 can be dyed, if desired. It is, of course, recognized that the use of lenticular
surfaces on supports of photographic elements having continuously coated radiation-sensitive
layers have been employed to obtain a variety of effects, such as increased speed,
color separation, restricted exposure and stereography, as illustrated by Cary U.S.
Patent 3,316,805, Brunson et al U.S. Patent 3,148,059, Schwan et al U.S. Patent 2,856,282,
Gretener U.S. Patent 2,794,739, Stevens U.S. Patent 2,543,073 and Winnek U.S. Patent
2,562,077. The photographic element 1000 can also provide such conventional effects
produced by lenticular surfaces, if desired.
[0099] The foregoing description of employing this invention to form silver images using
silver halide emulsions is believed adequate to suggest to those skilled in the art
variant element forms and imaging techniques which are too numerous to discuss individually.
Dye Imaging With Silver Halide
[0100] The photographic elements and the techniques described above for producing silver
images can be readily adapted to provide a colored image through the use of dyes.
In perhaps the simplest approach to obtaining a projectable color image a conventional
dye can be incorporated in the support of the photographic element, and silver image
formation undertaken as described above. In areas where a silver image is formed the
element is rendered substantially incapable of transmitting light therethrough, and
in the remaining areas light is transmitted corresponding in color to the color of
the support. In this way a colored image can be readily formed. The same effect can
also be achieved by using a separate dye filter layer or element with a transparent
support element. Where the support element or portion defining the lateral walls is
capable of absorbing light used for projection, an image pattern of a chosen color
can be formed by light transmitted through microcells in inverse proportion to the
silver present therein.
[0101] The silver halide photographic elements can be used to form dye images therein through
the selective destruction or formation of dyes. Conventional techniques are illustrated
by Research Disclosure, Item 17643, cited above, Section VII.
[0102] In the photographic elements described above the dye image supplements or replaces
the silver image by employing in combination with the photographic elements conventional
color photographic element components and/or processing steps. For example, dye images
can be produced in the microcells of the elements 100 through 1000 or in the imaging
components 418 and 518 by modifying the procedures for use described above in view
of current knowledge in the field of color photography. Accordingly, the following
detailed description of dye image formation is directed to certain unique, illustrative
combinations, particularly those in which the radiation-sensitive portion of the photographic
element is divided into two components.
[0103] In one highly advantageous form of the invention having unique properties the photographic
element 400 can be formed so that a radiation-sensitive silver halide emulsion component
416 is contained within the reaction microcell while a dye image providing component
418 overlies the reaction microcell. The dye image providing component is chosen from
among conventional components capable of forming or destroying a dye in proportion
to the amount of silver developed in the microcell. Preferably the dye image providing
component contains a bleachable dye useful in a silver-dye-bleach process or an incorporated
dye-forming coupler. In an alternative form the bleachable dye or dye-forming coupler
can be present in the emulsion component 416, and the separate imaging component 418
can be omitted.
[0104] When a photon is absorbed by a silver halide grain a hole-electron pair is created.
Both the electron and hole can migrate through the crystal lattice, but they are generally
precluded in an emulsion from migrating to an adjacent silver halide grain. While
holes are employed in surface fogged emulsions to provide direct-positive images,
in the more typical negative-working silver halide emulsions which are initially unfogged
the electrons generated by the absorbed photons are relied upon to produce an image.
The electrons provide the valence electrons given up by silver in the crystal lattice
to form metallic silver. It has been postulated that when four or more metallic silver
atoms are formed at one location within the crystal a developable latent image site
is created.
[0105] It is known in silver halide photography and is apparent from the mechanism of latent
image formation described above that the speed of silver halide emulsions generally
increases as a function of the average silver halide grain size. It is also known
that larger silver halide grains produce images exhibiting greater graininess. Ordinary
silver halide photographic elements employ silver halide grains whose size is chosen
to strike the desired balance between speed and graininess for the intended end use.
For example, in forming photographic images intended to be enlarged many times, graininess
must be low. On the other hand, radiographic elements generally employ coarse silver
halide grains in order to achieve the highest possible speeds consistent with necessary
image resolution. It is further known in the photographic arts that techniques which
increase the speed of a photographic element without increasing image graininess can
be used to decrease image graininess or can be traded off in element design to improve
some combination of speed and graininess. Conversely, techniques which improve image
graininess without decreasing photographic speed can be used to improve speed or to
improve a combination of speed and graininess.
[0106] It has been recognized and reported in the art that some photodetectors exhibit detective
quantum efficiencies which are superior to those of silver halide photographic elements.
A study of the basic properties of conventional silver halide photographic elements
shows that this is largely due to the binary, on-off nature of individual silver halide
grains, rather than their low quantum sensitivity. This is discussed, for example,
by Shaw, "Multilevel Grains and the Ideal Photographic Detector", Photographic Science
and Engineering, Vol. 16, No. 3, May/June 1972, pp. 192-200. What is meant by the
on-off nature of silver halide grains is that once a latent image site is formed on
a silver halide grain, it becomes entirely developable. Ordinarily development is
independent of the amount of light which has struck the grain above a threshold, latent
image forming amount. The silver halide grain produces exactly the same product upon
development whether it has absorbed many photons and formed several latent image sites
or absorbed only the minimum number of photons to produce a single latent image site.
[0107] The silver halide emulsion component 416 can employ very large, very high speed silver
halide grains. Upon exposure by light or X-rays, for instance, latent image sites
are formed in and on the silver halide grains. Some grains may have only one latent
image site, some many and some none. However, the number of latent image sites formed
within a single reaction microcell 408 is related to the amount of exposing radiation.
Because the silver halide grains are relatively coarse, their speed is relatively
high. Because the number of latent image sites within each microcell is directly related
to the amount of exposure that the microcell has received, the potential is present
for a high detective quantum efficiency, provided this information is not lost in
development.
[0108] In a preferred form each latent image site is then developed to increase its size
without completely developing the silver halide grains. This can be undertaken by
interrupting silver halide development at an earlier than usual stage, well before
optimum development for ordinary photographic applications has been achieved. Another
approach is to employ a DIR coupler and a color developing agent. The inhibitor released
upon coupling can be relied upon to prevent complete development of the silver halide
grains. In a preferred form of practicing this step selfinhibiting developers are
employed. A self-inhibiting developer is one which initiates development of silver
halide grains, but itself stops development before the silver halide grains have been
entirely developed. Preferred developers are self-inhibiting developers containing
p-phenylenediamines, such as disclosed by
Neuberger et al, "Anomalous Concentration Effect: An inverse Relationship Between the
Rate of Development and Developer Concentration of Some i-Phenylenediamines", Photographic
Science and Engineering, Vol. 19, No. 6, Nov-Dec 1975, pp. 327-332. Whereas with interrupted
development and development in the presence of DIR couplers silver halide grains having
a longer development induction period than adjacent developing grains can be entirely
precluded from development, the use of a self-inhibiting developer has the advantage
that development of an individual silver halide grain is not inhibited until after
some development of that, grain has occurred.
[0109] After development enhancement of the latent image sites, there is present in each
microcell a plurality of silver specks. These specks are proportional in size and
number to the degree of exposure of each microcell. The specks, however, present a
random pattern within each microcell and are further too small to provide a high density.
The next objective is to produce in each pixel a dye density which is substantially
uniform over the entire area of its microcell. Inasmuch as the preferred self-inhibiting
developers contain color developing agents, the oxidized developing agent produced
can be reacted with a dye-forming coupler to create the dye image. However, since
only a limited amount of silver halide is developed, the amount of dye which can be
formed in this way is also limited. An approach which removes any such limitation
on maximum dye density formation, but which retains the proportionality of dye density
in each pixel to the degree of exposure is to employ a silver catalyzed oxidation-reduction
reaction using a peroxide or transition metal ion complex as an oxidizing agent and
a dye-image-generating reducing agent, such as a color developing agent, as illustrated
by the patents cited above of Bissonette, Travis, Dunn et al, Matejec and Mowrey and
the accompanying publications. In these patents it is further disclosed that where
the silver halide grains form surface latent images the latent images can themselves
provide sufficient silver to catalyze a dye image amplification reaction. Accordingly,
the step of enhancing the latent image by development is not absolutely essential,
although it is preferred. In the preferred form any visible silver remaining in the
photographic element after forming the dye image is removed by bleaching, as is conventional
in color photography.
[0110] The resulting photographic image is a dye image in which each pixel in the array
exhibits a dye density which is internally uniform and proportional to the amount
of exposing radiation which has been supplied to the pixel. The regular arrangement
of the pixels serves to reduce the visual sensation of graininess. The pixels further
supply more information about the exposing radiation than can be obtained by completely
developing the silver halide grains containing latent image sites. The result is that
the detective quantum efficiency of the photographic element is quite high. Both high
photographic speeds and low graininess are readily obtainable. Where the dye is formed
in the microcells rather than in an overcoat, as shown, further protection against
lateral image spreading is obtained. All of the advantages described above in connection
with silver imaging are, of course, also obtained in dye imaging and need not be described
again in detail. Further, while this preferred process of dye imaging has been discussed
referring specifically to the photographic element 400, it is appreciated that it
can be practiced with any of the photographic elements shown and described above.
[0111] Referring to the photographic element 500, in one preferred form the component 518
can be a silver halide emulsion layer and the component 516 can be a dye image-forming
component. In conventional color photographic elements the radiation-sensitive portion
of the element is commonly formed of layer units, each comprised of a silver halide
emulsion layer and an adjacent hydrophilic colloid layer containing an incorporated
dye-forming coupler or bleachable dye. The components 518 and 516 in terms of composition
can be identical to these two conventional color photographic element layer unit coatings.
[0112] A significant difference between the photographic element 500 and a photographic
element having a continuously coated dye image component is that the reaction microcell
514 limits lateral image spreading of the imaging dye. That is, it can laterally limit
the chemical reaction which is forming the dye, where a coupler is employed, or bleaching
the dye, in the case of a silver-dye-bleach process. Since the silver image produced
by exposing and developing the element can be bleached from the element, it is less
important to image definition that silver development is not similarly laterally restrained.
Further, it is recognized by those skilled in the art that greater lateral spreading
typically occurs in dye imaging than when forming a silver image in a silver halide
photographic element. It is apparent that the advantages of this component relationship
is also applicable to photographic element 400.
Additive Multicolor Imaging
[0113] It has been recognized in the art that additive multicolor images can be formed using
a continuous, panchromatically sensitized silver halide emulsion layer which is exposed
and viewed through an array of additive primary (blue, green and red) filter areas.
Exposure through an additive primary filter array allows silver halide to be selectively
developed, depending upon the pattern of blue, green and red light passing through
the overlying filter areas. If a negative-working silver halide emulsion is employed,
the multicolor image obtained is a negative of the exposure image, and if a direct-positive
emulsion is employed, a positive of the exposure image is obtained. Additive primary
multicolor images can be reflection viewed, but are best suited for projection viewing,
since they require larger amounts of light than conventional subtractive primary multicolor
images to obtain comparable brightness.
[0114] Dufay U.S. Patent 1,003,720 teaches forming an additive multicolor filter by alternately
printing two-thirds of a filter element with a greasy material to leave uncovered
an array of areas. An additive primary dye is imbibed into the filter element in the
uncovered areas. By repeating the sequence three times the entire filter area is covered
by an interlaid pattern of additive primary filter areas. Rogers U.S. Patent 2,681,857
illustrates an improvement on the Dufay process of forming an additive primary multicolor
filter by printing. Rheinberg U.S. Patent 1,191,034 obtains essentially a similar
effect by using subtractive primary dyes (yellow, magenta and cyan) which are allowed
to laterally diffuse so that two subtractive primaries are fused in each area to produce
an additive primary dye filter array.
[0115] More recently, in connection with semiconductor sensors, additive primary multicolor
filter layers have been developed which are capable of defining an interlaid pattern
of areas of less than 100 microns on an edge and areas of less than 10-
4 cm
2. One approach is to form the filter layer so that it contains a dye mordant. In this
way when an interlaid pattern of additive primary dyes is introduced to complete the
filter, mordanting of the dyes reduces lateral dye spreading. Filter layers comprised
of mordanted dyes and processes for their preparation are
'disclosed by Whitmore U.S. Patents 4,312,806 and 4,375,507.
[0116] Another approach to forming an additive primary multicolor filter array is to incorporate
photobleachable dyes in a filter layer. By exposure of the element with an image pattern
corresponding to the filter areas to be formed dye can be selectively bleached in
exposed areas leaving an interlaid pattern of additive primary filter areas. The dyes
can thereafter be treated to avoid subsequent bleaching. Such an approach is disclosed
by Research Disclosure, Vol. 177, January 1979, Item 17735.
[0117] In addition to any one or combination of the various additive primary materials described
above, virtually any known additive primary dye or pigment can, if desired, be selected
for use in the multicolor filters. For example, the additive primary dyes and pigments
mentioned in the Colour Index, Volumes I and II, Second Edition, are generally useful
in the practice of at least one form of the present invention.
[0118] While it is recognized that conventional additive primary multicolor filter layers
can be employed in connection with the photographic elements 100 through 1000 to form
additive multicolor images in accordance with this invention, it is preferred to form
additive primary multicolor filters comprised of an interlaid pattern of additive
primary dyes or pigments in an array of microcells. The microcells offer the advantages
of providing a physical barrier between adjacent additive primary dye areas thus avoiding
lateral spreading, edge co-mingling of the dyes and similar disadvantages. The microcells
can be identical in size and configuration to those which have been described above.
[0119] In Figures 11A and 11B an exemplary filter element 1100 of this type is illustrated
which is similar to the photographic element 100 shown in Figures 1A and 1B, except
that instead of radiation-sensitive material being contained in the microcells 1108,
an interlaid pattern of green, blue and red dyes or pigments is provided, indicated
by the letters G, B and R, respectively. The dashed line 1120 surrounding an adjacent
triad of green, blue and red containing microcells defines a single pixel of the filter
element which is repeated to make up the interlaid pattern of the element. It can
be seen that each microcell of a single pixel is equidistant from the two remaining
microcells thereof. Looking at an area somewhat larger than a pixel, it can be seen
that each microcell containing one color is surrounded by microcells containing the
remaining two colors. Thus, it is easy for the eye to fuse the colors of the adjacent
microcells or, during projection, for light passing through adjacent microcells to
fuse. The underlying portion 1112 of the support 1102 must be transparent to permit
projection viewing. While the lateral walls 1110 of the support can be transparent
also, they are preferably opaque (e.g., dyed), particularly for projection viewing,
as has been discussed above in connection with element 100. Placing the red, green
and blue additive primary dyes in microcells offers a distinct advantage in achieving
the desired lateral relationship of individual filter areas. Although lateral dye
spreading can occur in an individual microcell which can be advantageous in providing
a uniform dye density within the microcell, gross dye spreading beyond the confines
of the microcell lateral walls is prevented.
[0120] An exemplary filter element has been illustrated as a variant of photographic element
100, but it is appreciated that corresponding filter element variants of photographic
elements 200 through 1000 are also contemplated. Figure 11D illustrates an alternative
form of filter element 1150. In section the element of Figure 11D can appear identical
to the section shown in Figure 11B. In this instance the microcells are diamond shaped
rather than being hexagonal. However, an interlaid pattern of red, green, and blue
filter segments is retained. The major axes of the diamond-shaped microcells are oriented
in three different directions which intersect at 60° angles. An equal number of each
of the blue, green, and red filter segments are oriented in each of the three major
axes directions. Thus, the elongation of individual microcells imparted by the diamond
shape, the filter retains an overall balance of red, green, and blue filter segments
in each major axis direction. The diamond-shaped microcells can, of course, compatible
with other microcell applications herein described as an alternative to use in forming
a filter element.
[0121] It is, of course, recognized that other interlaid patterns of microcells are possible.
For example, instead of being interlaid in the manner shown, the blue, green and red
filter areas can form separate rows of microcells. For instance, a row of filter areas
of one color can be interposed between two filter area rows, one of each of the two
remaining additive primary colors. Different interlaid patterns can also occur as
a result of devoting unequal numbers of microcells to the different filter colors.
For example, it is recognized that the human eye obtains most of its information from
the green portion of the spectrum. Less information is obtained from the red portion
of the spectrum, and the least amount of information is obtained from the blue portion
of the spectrum. Bayer
U.S. Patent 3,971,065 discloses an interlaid additive primary multicolor filter area
pattern in which the green areas occupy half of the total filter area, with red and
blue filter areas each occupying one half of the remaining area of the filter. Still
other filter area patterns can be employed, if desired.
[0122] In Figure 11C the use of filter element 1100 in combination with photographic element
100 is illustrated. The photographic element contains in the reaction microcells 108
a panchromatically responsive radiation-sensitive imaging means 116, such as a panchromatically
sensitized silver halide emulsion. The microcells 1108 of the filter element are aligned
(registered) with the microcells of the photographic element. Exposure of the photographic
element occurs through the blue, green and red filter areas of the aligned filter
element. The filter element and the photographic element can be separated for processing
and subsequently realigned for viewing or further use, as in forming a photographic
print. The second alignment can be readily accomplished by viewing the image during
the alignment procedure. It is possible to join the filter element and photographic
element by attachment along one or more edges so that, once positioned, the alignment
between the two elements is subsequently preserved. Where the filter and photographic
elements remain in alignment, processing fluid can be dispensed between the elements
in the same manner as in-camera image transfer processing. In order to render less
exacting the process of initial alignment of the filter and photographic element microcells,
the microcells of the filter element can be substantially larger in area than those
of the photographic element and can, if desired, overlie more than one of the microcells
of the photographic element. Complementary edge configurations, not shown, can be
provided on the photographic and filter elements to facilitate alignment. A variant
form which insures alignment of the silver halide and the additive primary filter
microcells is achieved by modifying element 900 so that silver halide remains in microcells
908A, but additive primary dyes or pigments are present in microcells 908B.
[0123] By combining the functions of the filter and photographic elements in a single element
any inconveniences of registering separate filter and photographic element microcells
can be entirely obviated. In perhaps the simplest approach, the filter element 1100
can be modified by incorporating in the blue, green, and red filter material containing
microcells blue, green, and red spectral senstizing dyes respectively. Blue spectral
sensitizing dye is not essential, since silver halides, particularly silver bromide
and silver bromoiodide, have significant levels of native blue sentivity. The sensitizing
dyes are chosen to be capable of wandering. Over the major surface of the element
1100 toward which the microcells open a silver halide emulsion is coated which is
not initially spectrally sensitized. The emulsion is coated to contact the contents
of the microcells. Following coating, spectral senstizing dye can wander from the
microcells into the emulsion. Absorption of sensitizing dye by the silver halide grains
immobilizes the dye on the grains lying adjacent the microcell. In this way, the emulsion
layer becomes selectively responsive to blue, green, and red light adjacent the microcells
containing blue, green, and red filter materials, respectively. This arrangement is
highly advantageous in that the microcells and differing senstivity regions of the
microcells are self-registering. Where the emulsion layer possesses limited native
blue sensitivity and a blue spectral sensitizing dye is employed, the emulsion layer
can be exposed either directly or through the filter materials contained in the microcells.
[0124] Photographic elements 1200, 1300 and 1400 illustrate forms of the invention in which
both radiation-sensitive imaging (hereinafter described by references to a preferred
imaging material, a silver halide emulsion) and filter materials are positioned in
the same element microcells. These elements appear in plan view identical to element
1100 in Figure 11A. The views of elements 1200, 1300 and 1400 shown in Figures 12,
13 and 14, respectively, are sections of these elements which correspond to the section
shown in Figure 11B of the element 1100.
[0125] The photographic element 1200 is provided with microcells 1208. In the bottom of
each microcell is provided a filter portion, indicated by the letters B, G and R.
A panchromatically sensitized silver halide emulsion 1216 is located in the microcells
so that it overlies the filter portion contained therein. Alternatively the emulsion
can be blue, green, and red sensitized by spectral sensitizing dye migration from
the filter materials as described above.
[0126] The photographic element 1300 is provided with microcells 1308. In the microcells
designated B a blue filter material is blended with a blue sensitized silver halide
emulsion. Similarly in the microcells designated G and R a green filter material is
blended with a green sensitized silver halide emulsion and a red filter material is
blended with a red sensitized silver halide emulsion, respectively. In this form the
silver halide emulsion is preferably chosen so that it has negligible native blue
sensitivity, since the blended green and red filter materials offer substantial, but
not complete, filter protection against exposure by blue light of the emulsions with
which they are associated. In a preferred form silver chloride emulsions are employed,
since they have little native sensitivity to the visible spectrum.
[0127] The photographic element 1400 is provided with a transparent first support element
1402 and a yellow second support element 1408. The microcells B extend from the outer
major surface 1412 of the second support element to the first support element. The
microcells G and R have their bottom walls spaced from the first support element.
The contents of the microcells can correspond to those of the photographic element
1300, except that,the silver halide emulsions need not be limited to those having
negligible blue sensitivity in order to avoid unwanted exposure of the G and R microcells.
For example, iodide containing silver halide emulsions, such as silver bromoiodides,
can be employed. The yellow color of the second support element allows blue light
to be filtered so that it does not reach the G and R microcells in objectionable amounts
when the photographic element is exposed through the support. The yellow color of
the support can be imparted and removed for viewing using materials and techniques
conventionally employed in connection with yellow filter layers, such as Carey Lea
silver and bleachable yellow filter dye layers, in multilayer multicolor photographic
elements. The yellow color of the support can also be incorporated by employing a
photobleachable dye. Photobleaching is substantially slower than imaging exposure
so that the yellow color remains present during imagewise exposure, but after processing
handling in roomlight or intentional uniform light exposure can be relied upon to
bleach the dye. Photobleachable dyes which can be incorporated into supports are disclosed,
for example, by Jenkins et al U.S. Reissue Patent 28,225 and the Sturmer and Kruegor
U.S. Patents cited above. The optimum approach for imparting and removing yellow color
varies, of course, with the specific support element material chosen.
[0128] Instead of relying on wandering sensitizing dye to sufficiently sensitize the emulsion
layer coated on element 1100 as described above, the filter element 1100 can be overcoated
with a panchromatically sensitized silver halide emulsion layer. In the photographic
elements 1200, 1300 and 1400 it is specifically contemplated that the radiation-sensitive
portion of the photographic element can be present as two components, one contained
in the microcells and one in the form of a layer overlying the microcells, as has
been specifically discussed above in connection with photographic elements 400 and
500. In the interest of succinctness element features are not discussed which are
identical or clearly analogous to features which have been previously discussed in
detail.
[0129] In one preferred additive primary multicolor imaging application one or a combination
of bleachable leuco dyes are incorporated in the silver halide emulsion or a contiguous
component. Suitable bleachable leuco dyes useful in silver-dye-bleach processes have
been identified above in connection with dye imaging. The leuco dye or combination
of leuco dyes are chosen to yield a substantially neutral density. In a specifically
preferred form the leuco dye or dyes are located in the reaction microcells. The silver
halide emulsion that is employed in combination with the leuco dyes is a negative-working
emulsion.
[0130] Upon exposure of the silver halide emulsion through the filter element silver halide
is rendered developable in areas where light penetrates the filter elements. The silver
halide emulsion can be developed to produce a silver image which can react with or
catalyze a separate reaction with the dye to destroy it using silver-dye-bleach processes,
described above.
' Upon contact with alkaline developer solution, the leuco dyes are converted to a
colored form uniformly within the element. The silver-dye-bleach step causes the colored
dyes to be bleached selectively in areas where exposed silver halide has been developed
to form silver. The developed silver which reacts with dye is reconverted into silver
halide and thereby removed. In every case subsequent silver bleaching can be undertaken,
if desired. The colored dye which is not bleached is of sufficient density to prevent
light from passing through the filter elements with which it is aligned.
[0131] When exposure and viewing occur through an additive primary filter array, the result
is a positive additive primary multicolor dye image. It is surprising and advantageous
that a direct-positive multicolor image is obtained with a single negative-working
silver halide emulsion. Having the dye in its leuco form during silver halide exposure
avoids any reduction of emulsion speed by reason of competing absorption by the dye.
Further, the use of a negative-working emulsion permits very high emulsion speeds
to be readily obtained. By placing both the imaging and filter dyes in the microcells
registration is assured and lateral image spreading is entirely avoided.
[0132] Another preferred approach to additive primary multicolor imaging is to use as a
redox catalyst an imagewise distribution of silver made available by silver halide
emulsion contained in the reaction microcells to catalyze a neutral dye image producing
redox reaction in the microcells. The formation of dye images by such techniques are
described above in connection with dye imaging. This approach has the advantage that
very low silver coverages are required to produce dye images. The silver catalyst
can be sufficiently low in concentration that it does not limit transmission through
the filter elements. An advantage of this approach is that the redox reactants can
be present in either the photographic element or the processing solutions or some
combination thereof. So long as redox catalyst is confined to lhe microcells lateral
image spreading can be controlled, even though the dye-forming reactants are coated
in a continuous layer overlying the microcells. In one form a blend of three different
subtractive primary dye-forming reactants are employed. However, only a single subtractive
primary dye need be formed in a microcell in order to limit light transmission through
the filter and microcell. For example, forming a cyan dye in a microcell aligned with
a red filter element is sufficient to limit light transmission.
[0133] To illustrate a specific application, in any one of the arrangements illustrated
in Figures 11C, 12, 13 and 14, the silver halide emulsion contained in the microcells
is exposed through the filter elements. Where the silver halide emulsion forms a surface
latent image, this can be enough silver to act as a redox catalyst. It is generally
preferred to develop the latent image to form additional catalytic silver. The silver,
acting as a redox catalyst, permits the selective reaction of a dye-image-generating
reducing agent and an oxidizing agent at its surface. If the emulsion or an adjacent
component contains a coupler, for example, reaction of a color developing agent, acting
as a dye-image-generating reducing agent, with an oxidizing agent, such as a peroxide
oxidizing agent (e.g., hydrogen peroxide) or transition metal ion complex (e.g., cobalt(III)
hexammine), at the silver surface can result in a dye-forming reaction occurring.
In this way a dye can be formed in the microcells. Dye image formation can occur during
and/or after silver halide development. The transition metal ion complexes can also
cause dye to be formed in the course of bleaching silver, if desired. In one form
the microcells each contain a yellow, magenta or cyan dye-image-generating reducing
agent and the blue, green and red filter areas are aligned with the microcells so
that subtractive and additive primary color pairs can be formed in alignment capable
of absorbing throughout the visible spectrum.
[0134] In the foregoing discussion additive primary multicolor imaging is accomplished by
employing blue, green and red filter dyes or pigments preferably contained in microcells.
It is also possible to produce additive multicolor images according to the present
invention by employing subtractive primary dyes or pigments in combination. For example,
it is known that if any two subtractive primary colors are mixed the result is an
additive primary color. In the present invention, if two microcells in transparent
supports are aligned, each containing a different subtractive primary, only light
of one additive primary color can pass through the aligned microcells. For example,
a filter which is the equivalent of filter 1100 can be formed by employing in the
microcells 908A and 908B of the element 900 subtractive primary dyes rather than silver
halide. Only two subtractive primary dyes need to be supplied to a side to provide
a multicolor filter capable of transmitting red, green and blue light in separate
areas. By modifying the elements 1100, 1200, 1300 and 1400 so that aligned microcells
are present on opposite surfaces of the support, it is possible to obtain additive
primary filter areas with combinations of subtractive primary colors.
Subtractive Multicolor Imaging
[0135] Multicolor images formed by laterally displaced green, red and blue additive primary
pixel areas can be viewed by reflection or, preferably, projection to reproduce natural
image colors. This is not possible using the subtractive primaries- yellow, magenta
and cyan. Multicolor subtractive primary dye images are most commonly formed by providing
superimposed silver halide emulsion layer units each capable of forming a subtractive
primary dye image.
[0136] Photographic elements according to the present invention capable of forming multicolor
images employing subtractive primary dyes can be in one form similar in structure
to corresponding conventional photographic elements, except that in place of at least
the image-forming layer unit nearest the support, at least one image-forming component
of the layer unit is located in the reaction microcells, as described above in connection
with dye imaging. The microcells can be overcoated with additional image-forming layer
units according to conventional techniques.
[0137] It is possible in practicing the present invention to form each of the three subtractive
dye images which together form the multicolor dye image in the reaction microcells.
By one preferred approach this can be achieved by employing three silver halide emulsions,
one sensitive to blue exposure, one sensitive to green exposure and one sensitive
to red exposure. Silver halide emulsions can be employed which have negligible native
sensitivity in the visible portion of the spectrum, such as silver chloride, and which
are separalely spectrally sensitized. It is also possible to employ silver halide
emulsions which have substantial native sensitivity in the blue region of the spectrum,
such as silver bromoiodide. Red and green spectral sensitizers can be employed which
substantially desensitize the emulsions in the blue region of the spectrum. The native
blue sensitivity can be relied upon to provide the desired blue response for the one
emulsion intended to respond to blue exposures or a blue sensitizer can be relied
upon. The blue, green and red responsive emulsions are blended, and the blended emulsion
introduced into the reaction microcells. The resulting photographic element can, in
one form, be identical to photographic element 100. The silver halide emulsion 116
can be a blend of three emulsions, each responsive to one third of the visible spectrum.
By employing spectral sensitizers which are absorbed to the silver halide grain surfaces
and therefore nonwan- dering any tendency of the blended emulsion to become panchromatically
sensitized is avoided.
[0138] Following imagewise exposure, the photographic element is black-and-white developed.
No dye is formed. Thereafter the photographic element is successively exposed uniformly
to blue, green and red light, in any desired order. Following monochromatic exposure
and before the succeeding exposure, the photographic element is processed in a developer
containing a color developig agent and a soluble coupler capable of forming with oxidized
color developing agent a yellow, magenta or cyan dye. Developed silver is removed
by bleaching. The result is that a multicolor image is formed by subtractive primary
dyes confined entirely to the microcells. Suitable processing solutions, including
soluble couplers, are illustrated by Mannes et al U.S. Patent 2,252,718, Schwan et
al U.S. Patent 2,950,970 and
pilato U.S. Patent 3,547,650, cited above. In the preferred form negative-working silver
halide emulsions are employed and positive multicolor dye images are obtained.
[0139] In another form of the invention mixed packet silver halide emulsions can be placed
in the reaction microcells to form subtractive primary dye multicolor images. In mixed
packet emulsions blue responsive silver halide is contained in a packet also containing
a yellow dye-forming coupler, green responsive silver halide in a packet containing
a magenta dye-forming coupler and red responsive silver halide in a packet containing
a cyan dye-forming coupler. Imaging exposure and processing with a black-and-white
developer is performed as described above with reference to the blended emulsions.
However, subsequent exposure and processing is comparatively simpler. The element
is uniformly exposed with a white light source or chemically fogged and then processed
with a color developer. In this way a single color developing step is required in
place of the three successive color developing steps employed with soluble couplers.
A suitable process is illustrated by the Ektachrome E4 and E6 and Agfa processes described
in British Journal of Photography Annual, 1977, pp. 194-197, and British Journal of
Photography, August 1974, pp. 668-669. Mixed packet silver halide emulsions which
can be employed in the practice of this invention are illustrated by
Godowsky U.S. Patents 2,698,974 and 2,843,488 and Godowsky et al U.S. Patent 3,152,907,
the disclosures of which are here incorporated by reference.
Silver Transfer Imaging
[0140] It is well recognized in the art that transferred silver images can be formed. This
is typically accomplished by developing an exposed silver halide photographic element
with a developer containing a silver halide solvent. The silver halide which is not
developed to silver is solubilized by the solvent. It can then diffuse to a receiver
bearing a uniform distribution of physical development nuclei or catalysts. Physical
development occurs in the receiver to form a transferred silver image. Conventional
silver image transfer elements and processes (including processing solutions) are
generally discussed in Chapter 12, "One Step Photography", Neblette's Handbook of
Photography and Reprography Materials, Processes and Systems, 7th Ed. (1977) and in
Chapter 16, "Diffusion Transfer and Monobaths", T. H. James, The Theory of the Photographic
Process, 4th Ed. (1977), the disclosures of which are here incorporated by reference.
[0141] The photographic elements 100 through 1000 described above in connection with silver
imaging can be readily employed for producing transferred silver images. Illustrative
of silver halide solvent containing processing solutions useful in providing a transferred
silver image in combination with these photographic elements are those disclosed by
Rott U.S. Patent 2,352,014, Land U.S. Patents 2,543,181 and 2,861,885, Yackel et al
U.S. Patent 3,020,155 and Stewart et al U.S. Patent 3,769,014. The receiver to which
the silver image is transferred is comprised of a conventional photographic support
(or cover sheet) onto which is coated a reception layer comprised of silver halide
physical developing nuclei or other silver precipitating agents. In a preferred form
the receiver and photographic element are initially related so that the emulsion and
silver image-forming surfaces of the photographic element and receiver, respectively,
are juxtaposed and the processing solution is contained in a rupturable pod to be
released between the photographic element and receiver after imagewise exposure of
the silver halide emulsion. The photographic element and receiver can be separate
elements or can be joined along one or more edges to form an integral element. In
a common preferred separate element or peel-apart form the photographic element support
is initially transparent and the receiver is comprised of a reflective (e.g., white)
support. In a common integral format both the receiver and photographic element supports
are transparent and a reflective (e.g., white) background for viewing the silver image
is provided by overcoating the silver image-forming reception layer of the receiver
with a reflective pigment layer or incorporating the pigment in the processing solution.
[0142] A wide variety of nuclei or silver precipitating agents can be utilized in the reception
layers used in silver halide solvent transfer processes. Such nuclei are incorporated
into conventional photographic organic hydrophilic colloid layers such as gelatin
and polyvinyl alcohol layers and include such physical nuclei or chemical precipitants
as (a) heavy metals, especially in colloidal form and salts of these metals, (b) salts,
the anions of which form silver salts less soluble than the silver halide of the photographic
emulsion to be processed, and (c) nondiffusible polymeric materials with functional
groups capable of combining with and insolubilizing silver ions.
[0143] Typical useful silver precipitating agents include sulfides, selenides, polysulfides,
poly- selenides, thiourea and its derivatives, mercaptans, stannous halides, silver,
gold, platinum, palladium, mercury, colloidal silver, aminoguanidine sulfate, aminoguanidine
carbonate, arsenous oxide, sodium stannite, substituted hydrazines, xanthates, and
the like. Poly(vinyl mercaptoacetate) is an example of a suitable nondiffusing polymeric
silver precipitant. Heavy metal sulfides such as lead, silver, zinc, aluminum, cadmium
and bismuth sulfides are useful, particularly the sulfides of lead and zinc alone
or in an admixture or complex salts of these with thioacetamide, dithiooxamide or
dithiobiuret. The heavy metals and the noble metals particularly in colloidal form
are especially effective. Other silver precipitating agents will occur to those skilled
in the present art.
[0144] Instead of forming the receiver with a hydrophilic colloid layer containing the silver
halide precipitating agent, it is specifically contemplated to form the receiver alternatively
with microcells. The microcells can be formed of the same size and configuration as
described above. For example, referring to Figure 11C, if instead of employing red,
green and blue filter areas in the microcells 1108, silver precipitating agent suspended
in a hydrophilic colloid is substituted, an arrangement useful in silver image transfer
results. The same alignment considerations discussed above in connection with Figure
11C also apply. In this form the support 1102 is preferably reflective (e.g., white)
rather than transparent as shown, although both types of supports are useful. By confining
silver image-forming physical development to the microcells protection against lateral
image spreading is afforded.
[0145] In another variation of the invention it is contemplated that a conventional photographic
element containing at least one continuous silver halide emulsion layer can be employed
in combination with a receiver as described above in which the silver precipitating
agent is confined within microcells. Where the silver precipitating agent is confined
in the microcells, their depth can be the same as or significantly less than the depth
of microcells which contain a silver halide emulsion, since the peptizers, binders
and other comparatively bulky components characteristic of silver halide emulsions
can be greatly reduced in amount or eliminated. Generally reaction microcell depths
as low as those contemplated for vacuum vapor deposited imaging materials, such as
silver halide, described above, can be usefully employed also to contain the silver
precipitating agents.
Dye Transfer Imaging
[0146] A variety of approaches are known in the art for obtaining transferred dye images.
The approaches can be generally categorized in terms of the initial mobility of the
dyes or dye precursors, hereinafter also referred to as dye image providing compounds.
(Initial mobility refers to the mobility of the dye image providing compounds when
they are contacted by the processing solution. Initially mobile dye image providing
compounds as coated do not migrate prior to contact with processing solution). Dye
image providing compounds are classified as either positive-working or negative-working.
Positive-working dye image providing compounds are those which product a positive
transferred dye image when employed in combination with a conventional, negative-working
silver halide emulsion. Negative-working dye image providing compounds are those which
produce a negative transferred dye image when employed in combination with conventional,
negative-working silver halide emulsions. Image transfer systems, which include both
the dye image providing compounds and the silver halide emulsions, are positive-working
when the transferred dye image is positive and negative-working when the transferred
dye image is negative. When a retained dye image is formed, it is opposite in sense
to the transferred dye image. (The foregoing definitions assume the absence of special
image reversing techniques, such as those referred to in Research Disclosure, Vol.
176, December 1978, Item 17643, paragraph XXIII-E).
[0147] A variety of dye image transfer systems have been developed and can be employed in
the practice of this invention, such as those described in Whitmore U.S. Patents 4,362,806
and 4,375,507.
[0148] Any one of the conventional systems for forming transferred dye images can be readily
employed in the practice of this invention. Photographic elements according to this
invention capable of forming transferred dye images are comprised of at least one
image-forming layer unit having at least one component located in the reacion microcells,
as described above in connection with dye imaging. The receiver can be in a conventional
form with a dye image providing layer coated continuously on a planar support surface,
or the dye image providing layer of the receiver can be segmented and located in microcells,
similarly as described in connection with silver image transfer. The dye not transferred
to the receiver can, of course, also be employed in most of the systems identified
to form a retained dye image, regardless of whether an image is formed by transfer.
For instance, once an imagewise distribution of mobile and immobile dye is formed
in the element, the mobile dye can be washed and/or transferred from the element to
leave a retained dye image. It is also specifically contemplated to form multiple
transferred dye images employing a single microcellular support containing an imagewise
distribution of mobile dye or dye precursor. The microcells can act as wells providing
more transferable image dye or dye precursor than is needed for a single transferred
image.
[0149] A preferred image transfer film unit capable of forming multicolor transferred dye
images according to the present invention is illustrated in Figure 15. The image transfer
film unit 1500 preferably is of the integral format type. A transparent support 1502
is provided which can be identical to transparent support 1102 described above. The
support is provided with reaction microcells 1508 separated by lateral walls 1510.
The lateral walls are preferably dyed or opaque for reasons which have been discussed
above. In each microcell there is provided a negative-working silver halide emulsion
containing a filter dye. The reaction microcells form an interlaid pattern, preferably
identical to that shown in Figure llA, of a first set of reaction microcells containing
redsensitized silver halide and a red filter dye, a second set of reaction microcells
containing green-sensitized silver halide and a green filter dye and a third set of
reaction microcells containing blue-sensitized or blue sensitive silver halide and
a blue filter dye. (In an alternative form, not shown, a panchromatically sensitized
silver halide emulsion can be coated over the microcells rather than incorporating
silver halide within the microcells.) In each of the emulsions there is also provided
an initially mobile subtractive primary dye precursor. In the red-sensitized emulsion
containing microcells R, the green-sensitized emulsion containing microcells G and
the blue-sensitized emulsion containing microcells B are provided mobile cyan, magenta
and yellow dye precursors, respectively. The support 1502 and emulsions together form
the image-generating portion of the image transfer film unit.
[0150] An image-receiving portion of the image transfer film unit is comprised of a transparent
support (or cover sheet) 1550 on which is coated a conventional dye immobilizing layer
1552. A reflection and spacing layer 1554, which is preferably white, is coated over
the immobilizing layer. A silver reception layer 1556, which can be identical to that
described in connection with silver image transfer, overlies the reflection and spacing
layer.
[0151] In the preferred integral construction of the image transfer film unit the image-generating
and image-receiving portions are joined along their edges and lie in face-to-face
relationship. After imagewise exposure a processing solution is released from a rupturable
pod, not shown, integrally joined to the image-generating and receiving portions along
one edge thereof. A space 1558 is indicated between the image-generating and receiving
portions to indicate the location of the processing solution when present after exposure.
The processing solution contains a silver halide solvent, as has been described above
in connection with silver image transfer. A silver halide developing agent is contained
in either the processing solution or a processing solution permeable layer which is
contacted by the processing solution upon its release from the rupturable pod, for
example. The developing agent or agents can be incorporated in the silver halide emulsions.
Incorporation of developing agents has been described above.
[0152] The image transfer film unit 1500 is preferably a positive-working image transfer
system in which dyes are not initially present (other than the filter dyes), but are
formed by reactions occurring in the image generating portion or receiver of the image
transfer film unit during processing following exposure, described above in connection
with Dye Image Transfer.
[0153] The image transfer film unit 1500 is imagewise exposed through the transparent support
1502. The red, green and blue filters do not interfere with imagewise exposure, since
they absorb in each instance primarily only outside that portion of the spectrum to
which the emulsion with which they are associated is sensitized. The filters can,
however, perform a useful function in protecting the emulsions from exposure outside
the intended portion of the spectrum. For instance, where the emulsions exhibit substantial
native blue sensitivity, the red and green filters can be relied upon to absorb light
so that the red- and green-sensitized emulsions are not imaged by blue light. Other
approaches which have been discussed above for minimizing blue sensitivity of silver
halide emulsions can also be employed, if desired.
[0154] Upon release of processing solution between the image-forming and receiving portions
of the element, silver halide development is initiated in the reaction microcells
containing exposed silver halide. Silver halide development within a reaction microcell
results in a selective immobilization of the initially mobile dye precursor present.
In a preferred form the dye precursor is both immobilized and converted to a subtractive
primary dye. The residual mobile imaging dye precursor, either in the form of a dye
or a precursor, migrates through the silver reception layer 1556 and the reflection
and spacing layer 1554 to the immobilizing layer 1552. In passing through the silver
reception and spacing layers the mobile subtractive primary dyes or precursors are
free to and do spread laterally. Referring to Figure 11A, it can be seen that each
reaction microcell containing a selected subtractive primary dye precursor is surrounded
by microcells containing precursors of the remaining two subtractive primary dyes.
It can thus be seen that lateral spreading results in overlapping transferred dye
areas in the immobilizing layer of the receiver when mobile dye or precursor is being
transferred from adjacent microcells. Where three subtractive primary dyes overlap
in the receiver, black image areas are formed, and where no dye is present, white
areas are viewed due to the reflection from the spacing layer. Where two of the subtractive
primary dyes overlap at the receiver an additive primary image area is produced. Thus,
it can be seen that a positive multicolor dye image can be formed which can be viewed
through the transparent support 1550. The positive multicolor transferred dye image
so viewed is rightreading.
[0155] The present invention offers a distinct advantage over conventional multicolor transfer
systems in terms of reduced diffusion times required to permit a transferred image
to be seen. The three color forming units forming the multicolor transferred image
are not superimposed, as in most color image transfer systems, and therefore permit
a shorter diffusion path for all mobile dyes or dye precursors.
[0156] It is recognized in forming multicolor dye images in conventional photographic elements
having superimposed color forming layer units that oxidized color developing agent
produced in one layer can, unless restrained, wander to an adjacent layer unit to
produce undesirable interimage effects. Accordingly, it is conventional practice to
incorporate oxidized developing agent scavengers in interlayers between adjacent color-forming
layer units. Such scavengers include ballasted or otherwise nondiffusing (immobile)
antioxidants, as illustrated by Weissberger et al U.S. Patent 2,336,327, Loria et
al U.S. Patent 2,728,659, Vittum et al U.S. Patent 2,360,290, Jelley et al U.S. Patent
2,403,721 and Thirtle et al U.S. Patent 2,701,197. To avoid autooxidation the scavengers
can be employed in combination with other antioxidants, as illustrated by Knechel
et al U.S. Patent 3,700,453.
[0157] In the multicolor image transfer film units according to this invention the risk
of unwanted wandering of oxidized developing agent is substantially reduced, since
the lateral walls of the support element prevent direct lateral migration between
adjacent reaction microcells. Nevertheless, the oxidized developing agent in some
systems can be mobile and can migrate with the mobile dye or dye precursor toward
the receiver. It is also possible for the oxidized developing agent to migrate back
to an adjacent microcell. To minimize unwanted dye or dye precursor immobilization
prior to its transfer to the immobilizing layer of the receiver, it is preferred to
incorporate in the silver reception layer 1556 a conventional oxidized developing
agent scavenger. Specific oxidized developing agent scavenger as well as appropriate
concentrations for use are set forth in the patents cited above as illustrating conventional
oxidized developing agent scavengers, the disclosures of which are here incorporated
by reference.
[0158] Since the processing solution contains silver halide solvent, the residual silver
halide not developed in the reaction microcells is solubilized and allowed to diffuse
to the adjacent silver reception layer. The dissolved silver is physically developed
in the silver reception layer. In addition to providing a useful transferred silver
image this performs an unexpected and useful function. Specifically, solubilization
and transfer of the silver halide from the reaction microcells operates to limit direct
or chemical development of silver halide occurring therein. It is well recognized
by those skilled in the art that extended contact between silver halide and a developing
agent under development conditions (e.g., at an alkaline pH) can result in an increase
in fog levels. By solubilizing and transferring the silver halide a mechanism is provided
for terminating silver halide development in the reaction microcells. In this way
production of oxidized developing agent is terminated and immobilization of dye in
the microcells is also terminated. Thus, a very simple mechanism is provided for terminating
silver halide development and dye immobilization.
[0159] It is, of course, recognized that other conventional silver halide development termination
techniques can be employed in lieu of or in combination with that described above.
For example, a conventional polymeric acid layer can be overcoated on the cover sheet
1550 and then overcoated with a timing layer prior to coating the dye immobilizing
layer 1552. Illustrative acid and timing layer arrangements are disclosed by Cole
U.S. Patent 3,635,707 and Abel et al U.S. Patent 3,930,684. In variant forms of this
invention it is contemplated that such conventional development termination layers
can be employed as the sole means of terminating silver halide development, if desired.
[0160] In addition to obtaining a viewable transferred multicolor positive dye image a useful
negative multicolor dye image is obtained. In reaction microcells where silver halide
development has occurred an immobilized subtractive primary dye is present. This immobilized
imaging dye together with the additive primary filter offers a substantial absorption
throughout the visible spectrum, thereby providing a high neutral density to these
reaction microcells. For example, where an immobilized cyan dye is formed in a microcell
also containing a red filter, it is apparent that the cyan dye absorbs red light while
the red filter absorbs in the blue and the green regions of the spectrum. The developed
silver present in the reaction microcell also increases the neutral density. In reaction
microcells in which silver halide development has not occurred, the mobile dye precursor,
either before or after conversion to a dye, has migrated to the receiver. The sole
color present then is that provided by the filter. It is a distinct advantage in reducing
minimum density to employ the silver reception layer 1556 to terminate silver halide
development as described above rather than to relie on other development termination
alternatives. If the image-generating portion of the image transfer film unit 1500
is separated from the image-receiving portion, it is apparent that the image-generating
portion forms in itself an additive primary multicolor negative of the exposure image.
The additive primary negative image can be used for either transmission or reflection
printing to form right-reading multicolor positive images, such as enlargements, prints
and transparencies, by conventional photographic techniques. By obtaining a useful
multicolor negative, the transferred multicolor image need not be of the usual large
size, since the negative is available to produce an enlarged print, if desired. Accordingly,
the format of the image transfer element can be small and less expensive, also permitting
a smaller, more compact camera to be employed than is needed when the transferred
print is the primary photographic product obtained.
[0161] It is apparent that transferred multicolor subtractive primary positive images and
retained multicolor additive primary negative images can also be obtained as described
above by employing direct-positive silver halide emulsions in combination with negative-working
dye image providing compounds. Dye precursors are initially present in the reaction
microcells, and dyes are formed by reactions occurring in the image-forming or image-receiving
portion following exposure, as described above in connection with dye image transfer.
[0162] As can be readily appreciated from the foregoing description, the image transfer
film unit 1500 possesses a number of unique and unexpected advantages. In comparing
the image-generating portion of the image transfer film unit to those of Land and
Rogers discussed above it can be seen that this portion of the image transfer film
unit is of a simple construction and thinner than the image-receiving portion of the
element, which is the opposite of conventional integral receiver multicolor image
transfer photographic elements. The emulsions contained in the microcells all lie
in a common plane and they do not present an uneven or nonplanar surface configuration
either to the support or the image-receiving portion of the element. The emulsions
are not wasted by being in overlapping arrangements, and they are protected against
lateral image spreading by being uniformly laterally confined. Further, the microcells
confining the emulsions can be of identical configuration so that any risk of dye
imbalances due to differing emulsion configurations are avoided. Whereas Land and
Rogers obtain a wrong-reading retained dye pattern which is at best of questionable
utility for reflection imaging, the image-generating portion of the image transfer
film unit of this invention provides a right-reading multicolor additive primary retained
image which can be conveniently used for either reflective or transmission photographic
applications.
[0163] Instead of incorporating subtractive primary dye precursors in the reaction microcells,
as described above, it is possible to use subtractive primary dyes directly. If the
dye is blended with the emulsion, a photographic speed reduction can be expected,
since the subtractive primary dye is competing with the silver halide grains in absorbing
red, green or blue light. This disadvantage can be obviated, however, by forming the
image-generating portion of the image transfer film unit so that the filter material
and silver halide emulsion are blended together and located in the lower portion of
the reaction microcells while the subtractive primary dye, preferably distributed
in a suitable vehicle, such as a hydrophilic colloid, is located in the reaction microcells
to overlie the silver halide emulsion. In this way when the image transfer film unit
is exposed through the support 1502, exposing radiation is received by the emulsion
and competitive absorption by the subractive primary dye of direct incident radiation
is not possible. It is also specifically contemplated that instead of mixing the filter
material with the emulsion the filter material can be placed in the reaction microcells
before the emulsion, as is illustrated in Figure 12. The advantages of such an arrangement
have been discussed in connection with photograhic element 1200. Finally, it is contemplated
that the reaction microcells can be filled in three distinct tiers, with the filter
dyes being first introduced, the emulsions next and the subtractive primary dyes overlying
the emulsions. It is recognized that preformed image dyes can in still another variant
form be shifted in hue so that they do not compete with silver halide in absorbing
light to which silver halide in the same microcell is responsive. The dyes can shift
back to their desired image hue upon contact with processing solution. It is thus
apparent that any of the conventional positive-working or negative-working image transfer
systems which employ preformed subtractive primary dyes, described above in connection
with dye image transfer, can be employed in the image transfer film unit 1500. If
the filter materials are omitted, no retained image is produced which can be directly
viewed.
[0164] Figure 16 illustrates a image transfer film unit 1600 which can be substantially
simpler in construction than the image transfer film unit 1500. The image-generating
portion of the image transfer film unit 1600 can be identical to the image-generating
portion of the image transfer film unit 1500. Reference numerals 1602, 1608 and 1610
identify structural features which correspond to those identified by reference numerals
1502, 1508 and 1510, respectively. In a simple preferred form the reaction microcells
1608 contain silver halide emulsions and filter materials as described in connection
with image transfer film unit 1500, but they do not contain an imaging dye or dye
precursor.
[0165] The image-receiving portion of the image transfer film unit 1600 is comprised of
a transparent support 1650 onto which is coated a silver reception layer 1656 which
can be identical to silver reception layer 1556. A reflective layer 1654 is provided
on the surface of the silver reception layer remote from the support 1650. The reflection
layer is preferably thinner than the imaging and spreading layer 1554, since it is
not called upon to perform an intentional spreading function. The reflection layer
is preferably white.
[0166] Upon exposure through the support 1602 negative-working silver halide is rendered
developable in the exposed microcells. Upon introducing a processing solution containing
a silver halide developing agent and a silver halide solvent in the space 1658 indicated
between the image-receiving and image-generating portions, silver halide development
is initiated in the exposed reaction microcells and silver halide solubilization is
initiated in the unexposed microcells. The solubilized silver halide is transferred
through the reflection layer 1654 and forms a silver image at the silver reception
layer 1656. In viewing the silver image in the silver reception layer through the
support 1650 against the background provided by the reflection layer a right-reading
positive silver image is provided. The photographer is thus able to judge the photographic
result obtained, although a multicolor positive image is not immediately viewable.
The image-generating portion of the image transfer film unit, however, contains a
multicolor additive primary negative image. This image can be used to provide multicolor
positive images by known photographic techniques when the image-generating portion
is separated from the image-receiving portion. The image transfer film unit 1600 offers
the user advantage of rapid information as to the photographic result obtained, but
avoids the complexities and costs inherent in multicolor dye image transfer.
[0167] As described above the image transfer film unit 1600 relies upon silver halide development
in the reaction microcells to provide the required increase in neutral density to
form a multicolor additive primary negative image in the image-generating portion
of the element. Since it is known that silver reception layers can produce silver
images of higher density than those provided by direct silver halide development,
it is possible that at lower silver halide coating coverages a satisfactory transferred
silver image can be obtained, but a less than desired silver density obtained in the
reaction microcells. The neutral density of the reaction microcells can be increased
by employing any one of a variety of techniques. For example redox processing of the
image-generating portion of the image transfer film unit after separation from the
image-receiving portion can be undertaken. In redox processing the silver developed
in the reaction microcells acts as a catalyst for dye formation which can increase
the neutral density of the microcells containing silver or can be employed as a catalyst
for physical development to enhance the neutral density of the silver containing microcells.
These techniques have been discussed above in greater detail in connection with multicolor
additive primary imaging.
[0168] In the foregoing discussion of the image transfer film unit 1500 silver halide emulsion
is positioned in the reaction microcells 1508 and silver precipitating agent is located
in the silver reception layers 1556. Unique and unexpected advantages can be achieved
by reversing this relationship. For example, the layer 1556 can be comprised of a
panchromatically sensitized silver halide emulsion while the microcells 1508 (or a
layer overlying the microcells, not shown) can contain a silver precipitating agent,
the remaining components of the microcells being unchanged.
[0169] Assuming for purposes of illustration a negative-working silver halide emulsion in
a positive-working image transfer system, upon imagewise exposure through the support
1502, silver halide is rendered developable in the lightstruck areas of the emulsion
layer. Upon release of the aqueous alkaline processing solution containing silver
halide solvent, unexposed silver halide is solubilized and migrates to the adjacent
microcells where silver precipitation occurs. In the image transfer film unit 1500
a projectable positive additive primary image is obtained in the support 1502 (which
is now an image-receiving rather than the image-generating portion of the element).
A portion of the imaging dye can be retained in the microcells to supplement the precipitated
silver in providing a neutral density in the unexposed microcells. The portion of
the imaging dye not retained in the microcells is, of course, immobilized by the layer
1552 and forms a multicolor subtractive primary positive transferred dye image. Oxidized
developing agent scavenger is preferably located in the microcells 1508 to reduce
dye stain and facilitate dye transfer. The emulsion layer 1556, the support 1502 and
the contents of the microcells together form the image-generating portion of the element.
[0170] One advantage of continuously coating the silver halide emulsion is that a single,
panchromatically sensitized silver halide emulsion can be employed since the emulsion
is entirely located behind the filter dyes during exposure. Another important advantage
is that the microcells in the support 1502 contain no light-sensitive materials in
this form. This allows the relatively more demanding steps of filling the microcells
to be performed in roomlight while the more conventional fabrication step of coating
the emulsion as a continuous layer is performed in the dark. It is also apparent that
the reaction microcells can be shallower when they do not contain silver halide emulsion,
although this is not essential.
[0171] Numerous additional structural modifications of the image transfer film units 1500
and 1600 are possible. For example, while the supports 1502 and 1602 have been shown,
it is appreciated that specific features of other support elements described above
containing microcells can also be employed in combination, particularly pixels of
the type shown in Figures 2, 3, 4 and 5, microcell arrangements as shown in Figures
6 and 7 and lenticular support surfaces, as shown in Figure 10. Instead of the image-receiving
portion disclosed in connection with element 1500 any convnetional image-receiving
portion can be substituted which contains a spacing layer to permit lateral diffusion
of mobile subtractive primary dyes, such as those of the Land and Rogers patents,
cited above. Instead of the image-receiving portion disclosed in connection with unit
1600 an image-receiving portion from any conventional silver image transfer photographic
element can be substituted. The dye immobilizing layer 1552 and the silver reception
layer 1656 can both be modified so that the materials thereof are located in microcells,
if desired. In one specific form the layers 1552 and 1554 can both be present in microcells
formed by the support 1550. These microcells can be sized to overlie a plurality of
the microcells 1508, thereby concurrently allowing limited lateral image spreading
while preventing uncontrolled lateral image spreading from occurring. For example
the microcells in the support 1550 can correspond to the configuration of pixels 1120.
The aqueous alkaline processing solution can be introduced at any desired location
between the supports 1502 and 1550 or 1602 and 1650, and one or more the layers associated
with support 1550 or 1650 can be associated with support 1502 or 1602 instead. Any
of the image transfer film units discussed above in connection with Dye Transfer Imaging
can be adapted to transfer multicolor dye images by overcoating the one image-forming
layer unit required and specifically described with one or, preferably, two additional
image-forming layer units each capable of transferring a different subtractive primary
dye. Any of the image transfer systems described above in connection with Dye Transfer
Imaging can be employed in Multicolor Transfer Imaging, as herein described. The patents
cited in connection with Dye Transfer Imaging generally describe Multicolor Transfer
Imaging as well. Finally, it is recognized that numerous specific features well known
in the photographic arts can be readily applied or adapted to the practice of this
invention and for this reason are not specifically redescribed.
[0172] The multicolor image transfers systems of this invention can be further illustrated
by reference to certain preferred dye image transfer systems. In one specific, illustrative
form the image transfer film unit 1500 can contain (1) in a first set of microcells
a blue filter dye or pigment and an initially colorless, mobile yellow dye-forming
coupler, (2) in a second, interlaid set of microcells a green filter dye or pigment
and an initially colorless, mobile magenta dye-forming coupler and (3) in a third,
interlaid set of microcells a red filter dye or pigment and an initially colorless,
mobile cyan dye-forming coupler. The filter dyes and pigments can be selected from
among any of those described above. The initially colorless, mobile dye-forming couplers
can be selected from those disclosed by Yutzy U.S. Patent 2,756,142, Greenhalgh et
al U.K. Patents 1,157,501-'506 and Land U.S. Patents 2,559,643, 2,647,049, 2,661,293,
2,698,244 and 2,698,798, cited above. In a preferred form a panchromatically sensitized
negative-working silver halide emulsion (not shown in Figure 15) is coated over the
microcells. The layer 1556 contains a silver precipitating agent and an oxidized developing
agent scavenger, the composition of which can take any of the forms described above.
The reflection and spacing layer 1554 can be a conventional titanium oxide pigment
containing layer. The dye immobilizing layer 1552 contains an immobile oxidizing agent
of the type described above.
[0173] The image transfer film unit 1500 so constituted is first exposed imagewise through
the transparent support 1502. Thereafter a processing composition containing a color
developing agent and a silver halide solvent is released and uniformly spread in the
space 1558. In exposed areas silver halide is developed producing oxidized color developing
agent which couples with the dye forming coupler present to form an immobile dye.
The filter dye or pigment, the immobile dye formed, and the developed silver thus
together increase the optical density of the microcells which are exposed.
[0174] In areas not exposed, the undeveloped silver halide is solubilized by the silver
halide solvent and migrates to the layer 1556 where it is reduced to silver. Any oxidized
developing agent produced in reducing the silver halide to silver immediately cross-oxidizes
with the scavenger which is present with the silver precipitating agent in the layer
1556.
[0175] At the same time mobile coupler is wandering from microcells which were not exposed.
The mobile coupler does not react with oxidized color developing agent in the layer
1556, since any oxidized color developing agent present preferentially reacts with
the scavenger. The coupler thus migrates through layer 1556 unaffected and enters
reflection and spreading layer 1554. Because of the thickness of this layer, the mobile
coupler is free to wander laterally to some extent. Upon reaching the immobilizing
layer 1552, the coupler reacts with oxidized color developing agent. The oxidized
color developing agent is produced uniformly in this layer by interaction of oxidizing
agent with the color developing agent. Due to lateral diffusion in the spreading layer,
superimposed immobile yellow, magenta and cyan dye images are formed in the immobilizing
layer and can be viewed as a multicolor image through the transparent support (or
cover sheet) 1550 with the layer 1554 providing a white reflective background. At
the same time, since only filter dye or pigment remains in the unexposed microcells,
a useable additive primary negative transparency is formed by the support 1502.
[0176] To illustrate a variant system, a image transfer film unit as described immediately
above can be modified by substituting for the initially colorless, mobile dye forming
couplers initially mobile dye developers. The dye developers are shifted in hue, so
that the dye developer present in the microcells containing red, green and blue filters
do not initially absorb light in the red, green and blue regions of the spectrum,
respectively. Suitable shifted dye developers can be selected from among those disclosed
by Rogers U.S. Patents 2,774,668 and 2,983,606, Idelson et al U.S. Patent 3,307,947,
Dershowitz et al U.S. Patent 3,230,085, Cieciuch et al U.S. Patent 3,579,334, Yutzy
U.S. Patent 2,756,142, Harison Defensive Publication T-889,017 and Bush et al U.S.
Patent 3,854,945, cited above. A dye mordant as well as an oxidant can be present
in the dye immobilizing layer 1552. Since the dye image forming material is itself
a silver halide developing agent, a conventional activator solution can be employed
(preferably containing an electron transfer agent). The remaining features can be
identical to those described in the preceding embodiment.
[0177] Upon imagewise exposure and release of the activator solution, dye developer reacts
with exposed silver halide to form an immobile subtractive primary dye which is a
complement of the additive primary filter material in the exposed microcell. Thus
the optical density of exposed microcells is increased, and a negative multicolor
additive primary image can be formed in the support 1502 by the filter materials.
Silver halide development is terminated by transfer of solubilized silver halide as
has already been described. In unexposed areas unoxidized dye developer migrates to
the immobilizing layer 1552 where it is immobilized to form a multicolor positive
image. During processing the dye developers shift in hue so that they form subtractive
primaries complementary in hue to the additive primary filter materials with which
they are initially associated in the microcells. That is, the red, green and blue
filter material containing microcells contain dye developers which ultimately form
cyan, magenta and yellow image dyes. Hue shifts can be brought about by the higher
pH of processing, mordanting or by associating the image dye in the receiver with
a chelating material.
[0178] Instead of using shifted dye developers as described above, initially mobile leuco
dyes can be employed in combination with electron transfer agents to produce essentially
similar results. Since the leuco dyes are initially colorless, hue shifting does not
have to be undertaken to avoid competing light absorption during imagewise exposure.
The leuco dyes are converted to subtractive primary imaging dyes upon oxidation in
the dye immobilizing layer. Mordant in the layer 1552 holds the dyes in place. Suitable
initially mobile leuco dyes can be selected from among those disclosed by Lestina
et al U.S. Patents 3,880,658, 3,935,262 and 3,935,263, Cohler et al U.S. Patent 2,892,719,
Corley et al U.S. Patent 2,992,105 and Rogers U.S. Patents 2,909,430 and 3,065,074,
cited above. The remaining features can be identical to those described in the preceding
embodiment.
[0179] Instead of employing initially mobile dyes or dye precursors as described above,
it is possible to employ initially immobile materials. In one specific preferred form
benzisoxazolone precursors of hydroxylamine dye-releasing compounds are employed of
the type disclosed by Hinshaw et al
U.K. Patent 1,464,104 and Research Disclosure, Vol. 144, April 1976, Item 14447. Upon
crossoxidation in the microcells with oxidized electron transfer agent produced by
development of exposed silver halide, release of mobile dye is prevented. In areas
in which silver halide is not exposed and no oxidized electron transfer agent is produced
mobile dye release occurs. The dye image providing compounds are preferably initially
shifted in hue to avoid competing absorption during imagewise exposure. Mordant immobilizes
the dyes in the layer 1552. No oxidant is required in this layer in this embodiment.
Except as indicated, this element and its function is similar to the illustrative
embodiments described above.
[0180] Each of the illustrative embodiments described above employ positive-working dye
image providing compounds. To illustrate a specific embodiment employing negative-working
dye image providing compounds, a first set of microcells 1508 can contain a blue filter
dye or pigment, a silver precipitating agent and a redox dye-releaser containing a
yellow dye which is shifted in hue to avoid absorption in the blue region of the spectrum
prior to processing. In like manner a second, interlaid set of microcells contain
a green filter dye or pigment, the silver precipitating agent and a redox dye-releaser
containing an analogously shifted magenta dye, and a third, interlaid set of microcells
containing a red filter dye or pigment, the silver precipitating agent and a redox
dye-releaser containing an analogously shifted cyan dye. The microcells are overcoated
with a panchromatically sensitized silver halide emulsion layer containing an oxidized
developing agent scavenger (not shown in Figure 15). The silver precipitating layer
1556 shown in Figure 15 is not present. The reflection and spreading layer is a white
titanium oxide pigment layer. The dye immobilizing layer 1552 contains a mordant.
In a preferred form the redox dye-releasers are compounds containing a dye linked
through an oxidizable sulfonamido group, such as those illustrated by Fleckenstein
U.S. Patents 3,928,312 and 4,053,312, Fleckenstein et al U.S. Patent 4,076,529, Melzer
et al U.S. Patent 4,100,113, Degauchi U.S. Patent 4,199,892, Koyama et al
U.S. Patent 4,055,428, Vetter et al U.S. Patent 4,198,235 and Kestner et al Research
Disclosure, Vol. 151, November 1976, Item 15157, cited above. Any of the techniques
described above for shifting the hue of the dye can be employed.
[0181] The image transfer film unit is imagewise exposed through the transparent support
1502. A processing solution containing an electron transfer agent and a silver halide
solvent is spread between the image generating and the image receiving portions of
the element. In a preferred form the pH of the processing solution causes the redox
dye-releasers to shift to their desired image-forming hues. In areas in which silver
halide is exposed oxidized electron transfer agent produced by development of exposed
silver halide immediately cross-oxidizes with the scavenger. Thus, in microcells corresponding
to exposed silver halide the redox dye-releasers remain in their initially immobile
form. In areas in which silver halide is not exposed, silver halide solvent present
in the processing solution solubilizes silver halide allowing it to wander into the
underlying microcells. In the microcells physical devlopment of solubilized silver
halide occurs producing silver and oxidized electron transfer agent. The oxidized
electron transfer agent interacts with the redox dye-releaser to release mobile dye
which is transferred to the layer 1552and immobilized by the mordant. A multicolor
positive transferred image is produced in the layer 1552 comprised of yellow, magenta
and cyan transferred dyes. A multicolor positive retained image can also be produced,
since (1) the silver density produced by chemical development in the emulsion layer
is small compared to the silver density produced by physical development in the microcells
and (2) with the image-generating portion separated from the image-receiving portion
the redox dye-releasers remaining in their initial condition in the microcells can
be uniformly reacted with an oxidizing agent to release mobile dye which can be removed
from the microcells by washing.
[0182] In presently commercially available color image transfer image transfer film units,
the image transfer film unit is ejected from the camera before formation of the color
image is completed. The image transfer film units 1500 and 1600 in the variant forms
disclosed above can be ejected from a camera before internal processing is complete
only if they are protected from room light. For example, the transparent supports
1502 and 1602 can have a black layer associated therewith to permit early room light
handling. The layers 1554 and 1654, which prevent light exposure from occurring through
the transparent cover sheets 1550 and 1650, can optionally be supplemented by a black
layer located behind the white reflecting layer. When so protected, the elements can
produce transferred multicolor images which are accessible in very short time periods,
since the dye diffusion paths are short as compared with conventional image transfer
element diffusion paths. The transferred image can in one form be viewed through a
window provided in a camera while protecting the support containing the microcells
from light exposure while processing is being completed.
[0183] Whereas presently commercially available color image transfer film units are of comparatively
large format, thereby requiring that the cameras be rather large and bulky, the present
image transfer film units, though useful in these large formats, are particularly
suited for smaller formats, such as the 110 and 135 film sizes. In employing the image
transfer film units of this invention in small formats, the retained image, which
is preferably a negative image, is the primary photographic image of interest. The
retained negative image can be readily employed to produce multicolor enlarged positive
prints. The small format transferred multicolor positive image can be employed primarily
to give the photographer instant assurance that he or she has obtained the desired
photographic image. Because of the small format, the added cost of providing transferred
multicolor image in addition to a useful negative multicolor image is relatively small.
[0184] The multicolor image transfer elements of this invention can be employed in either
peel apart or integral forms. In one specifically contemplated form, the image receiving
portion of each element can be peeled from the image generating portion in the camera.
The image generating portion is retained for later use and/or silver reclamation.
The image receiving portion can have the appearance of a conventional color print.
For instance, the receiving portion support can be white resin coated paper support
bearing a mordant or oxidant containing layer which provides the multicolor dye image.
The image generating portion will then contain any required silver reception layer
and any lateral image spreading layer as well as the support containing the microcell:
and any overcoated radiation-sensitive emulsion layer.
Intracell Multicolor Transfer Imaging
[0185] In Figures 15 and 16 image transfer film units are illustrated in which some, but
not all of the imaging components are present in microcells. There are advantages
to be realized by confining all of the components contributing to forming an image
within each pixel area within a separate microcell. Such an arrangement can be illustrated
in Figure 17 by image transfer film unit 1700. A support is shown formed of a planar
transparent first support element 1702 and a second support element 1704. The first
support element forms the bottom walls 1706 of a plurality of microcells 1708 while
the second support element forms the lateral walls 1710 of the microcells.
[0186] Within each microcell adjacent the bottom wall is located a mordant layer 1712. A
permeable reflecting layer 1714 overlies the mordant layer. Red, green, and blue recording
silver halide emulsion layer units 1716, 1718, and 1720, respectively, overlie the
reflecting layer. The red, green, and blue recording emulsion layer units are each
capable of releasing a corresponding cyan, magenta, or yellow dye as a function of
exposure. The emulsion layer units, including the dye associated therewith, can be
constructed similarly as in any conventional multicolor dye image transfer film unit.
At least one of the emulsion layer units and preferably all employ high aspect ratio
tabular grain silver halide emulsions.
[0187] In use the image transfer film unit can be imagewise exposed through the transparent
cover sheet 1750 or with the transparent cover sheet removed. Processing liquid is
then released between the cover sheet and the support elements. At this time the cover
sheet is pressed against the upper surface of the lateral walls 1710. In the form
shown the lateral walls extend sufficiently above the uppermost emulsion unit to form
a reservoir for the processing liquid. Depending upon the rate at which the processing
liquid is capable of penetrating the emulsion units, this may or may not be necessary.
By confining the processing liquid within each microcell lateral migration of mobile
dye or other materials between adjacent microcells is prevented, thereby contributing
to image sharpness. Mobile dye migrates from the emulsion units to the mordant layer
as a function of exposure and can be viewed through the transparent first support
element. Although not shown, timing layers to terminate development can also be included.
For example, a timing layers can be coated on the major face of the cover sheet adjacent
the support.
[0188] It can be seen that the image transfer film unit 1700 is in reality made up of a
large number of independent image transfer film units each corresponding to one microcell
or pixel of the total unit. The effect is to limit lateral spreading effects that
can interfere with image definition in units wherein imaging dyes migrate beyond individual
microcells. It is recognized that image transfer film unit 1700 is only illustrative
of a variety of variant units which can be constructed sharing at least some of the
advantages of unit 1700. Although unit 1700 is intended to form transferred dye images,
it is realized that a similar approach can be taken also in forming transferred silver
images.
[0189] While the foregoing is intended to point out certain illustrative embodiments of
the invention, it is appreciated that numerous additional variant forms of the invention
will readily occur to those skilled in the art.
Preparation Techniques
[0190] One preferred technique according to this invention for preparing microcell containing
supports is to expose a photographic element having a transparent support in an imagewise
pattern, such as illustrated in Figures lA, 6, 7 and 8. In a preferred form the photographic
element is negative-working and exposure corresponds to the areas intended to be subtended
by the microcell areas while the areas intended to be subtended by the lateral walls
are not exposed. By conventional photographic techniques a pattern is formed in the
element in which the areas to be subtended by the microcells are of a substantially
uniform maximum density while the areas intended to be subtended by the lateral walls
are of a substantially uniform minimum density.
[0191] The photographic element bearing the image pattern is next coated with a radiation-sensitive
composition capable of forming the lateral walls of the support element and thereby
defining the side walls of the microcells. In a preferred form the radiation-sensitive
coating is a negative-working photoresist or dichromated gelatin coating. The coating
can be on the surface of the photographic element bearing the image pattern or on
the opposite surface--e.g., for a silver halide photographic element, the photoresist
or dichromated gelatin can be coated on the support or emulsion side of the element.
The photoresist or dichromated gelatin coating is next exposed through the pattern
in the photographic element, so that the areas corresponding to the intended lateral
walls are exposed. This results in hardening to form the lateral wall structure and
allowing the unexposed material to be removed according to conventional procedures
well known to those skilled in the art. For instance, these procedures are fully described
in the patents cited above in connection with the description of photoresist and dichromated
gelatin support materials.
[0192] The image pattern is preferably removed before the element is subsequently put to
use. For example, where a silver halide photographic element is exposed and processed
to form a silver image pattern, the silver can be bleached by conventional photographic
techniques after the microcell structure is formed by the radiation-sensitive material.
[0193] If a positive-working photoresist is employed, it is initially in a hardened form,
but is rendered selectively removable in areas which receive exposure. Accordingly,
with a positive-working photoresist or other radiation-sensitive material either a
positive-working photographic element is employed or the sense of the exposure pattern
is reversed. If an exposure blocking pattern is present in or on the support corresponding
to the lateral walls forming the microcells, this pattern need not be removed for
many applications and can even take the place of increasing the optical density of
the lateral walls forming the microcells in many instances. Instead of coating the
radiation-sensitive material onto a support bearing an image pattern, such as an image-bearing
photographic element, the radiation-sensitive material can be coated onto any conventional
support and imagewise exposed directly rather than through an image pattern. It is,
of course, a simple matter to draw the desired pixel pattern on an enlarged or macro-scale
and then to photoreduce the pattern to the desired scale of the microcells for purposes
of exposing the photoresist.
[0194] Another technique which can be used to form the microcells in the support is to form
a plastic deformable material as a planar element or as a coating on a relatively
nondeformable support element and then to form the microcells in the relatively deformable
material by embossing. An embossing tool is employed which contains projections corresponding
to the desired shape of the microcells. The projections can be formed on an initially
plane surface by conventional techniques, such as coating the surface with a photoresist,
imagewise exposing in a desired pattern and removing the photoresist in the areas
corresponding to the spaces between the intended projections (which also correspond
to the configuration of the lateral walls to be formed in the support). The areas
of the embossing tool surface which are not protected by photoresist are then etched
to leave the projections. Upon removal of the photoresist overlying the projections
and any desired cleaning step, such as washing with a mild acid, base or other solvent,
the embossing tool is ready for use. In a preferred form the embossing tool is formed
of a metal, such as copper, and is given a metal coating, such as by vacuum vapor
depositing chromium or silver. The metal coating results in smoother walls being formed
during embossing.
[0195] Still another technique for preparing supports containing microcells is to form a
planar element, such as a sheet or film, of a material which can be locally etched
by radiation. The material can form the entire element, but is preferably present
as a continuous layer of a thickness corresponding to the desired depth of the microcells
to be formed, coated on a support element which is formed of a material which is not
prone to radiation etching. By irradiation etching the planar element surface in a
pattern corresponding to the microcell pattern, the unexposed material remaining between
adjacent microcell areas forms a pattern of interconnecting lateral walls. It is known
that many dielectric materials, such as glasses and plastics, can be radiation etched.
Cellulose nitrate and cellulose esters (e.g., cellulose acetate and cellulose acetate
butyrate) are illustrative of plastics which are particularly preferred for use. For
example, coatings of cellulose nitrate have been found to be virtually insensitive
to ultraviolet and visible light as well as infrared, beta, X-ray and gamma radiation,
but cellulose nitrate can be readily etched by alpha particles and similar fission
fragments. Techniques for forming cellulose coatings for radiation etching are known
in the art and disclosed, for example, by Sherwood U.S. Patent 3,501,636, here incorporated
by reference.
[0196] The foregoing techniques are well suited to forming transparent microcell containing
supports, a variety of transparent materials being available satisfying the requirements
for use. Where a white support is desired, white materials can be employed or the
transparent materials can be loaded with white pigment, such as titania, baryta and
the like. Any of the whitening materials employed in conjunction with conventional
reflective photographic supports can be employed. Pigments to impart colors other
than white to the support can, of course, also be employed, if desired. Pigments are
particularly well suited to forming opaque supports which are white or colored. Where
it is desired that the support be transparent, but tinted, dyes of a conventional
nature are preferably incorporated in the support forming materials. For example,
in one form of the support described above the support is preferably yellow to absorb
blue light while transmitting red and green.
[0197] In various forms of the supports described above the portion of the support forming
the bottom walls of at least one set of microcells, generally all of the microcells,
is transparent, and the portion of the support forming the lateral walls is either
opaque or dyed to intercept light transmission therethrough. As has been discussed
above, one technique for achieving this result is to employ different support materials
to form the bottom and lateral walls of the supports.
[0198] A preferred technique for achieving dyed lateral walls and transparent bottom walls
in a support formed of a single material is as follows: A transparent film is employed
which is initially unembossed and relatively nondeformable with an embossing tool.
Any of the transparent film-forming materials more specifically described above and
known to be useful in forming conventional photographic film supports, such as cellulose
nitrate or ester, polyethylene, polystyrene, poly(ethylene terephthalate) and similar
polymeric films, can be employed. One or a combination of dyes capable of imparting
the desired color to the lateral walls to be formed is dissolved in a solution capable
of softening the transparent film. The solution can be a conventional plasticizing
solution for the film. As the plasticizing solution migrates into the film from one
major surface, it carries the dye along with it, so that the film is both dyed and
softened along one major surface. Thereafter the film can be embossed on its softened
and therefore relatively deformable surface. This produces microcells in the film
support which have dyed lateral walls and transparent bottom walls.
[0199] Instead of solvent embossing as described above, thermal embossing can be undertaken.
According to this procedure a layer formed of a thermoplastic material, such as polymer,
is heated to its glass transition temperature and then embossed. The thermoplastic
material can contain a dye or pigment to impart the desired density to the lateral
walls of the microcells so formed. The layer of thermoplastic material can form the
entire support, being embossed to a depth less than its original thickness. Preferably
the thermoplastic material layer is coated over a separate bottom wall forming support
material layer. In a specifically preferred form the bottom wall forming support material
is a photoconductive material as exemplified below. In this case the thermoplastic
material is chosen to have a glass transition temperature in the range of from about
40 to 120°C. Optimization of thermal embossing for specific thermoplastic materials
and microcell sizes can be achieved by routine investigation.
[0200] In some forms of the invention described above it is desirable for the walls of the
microcells to be reflective. This can be achieved by coating the embossing tool with
reflective material. Upon embossing the reflective material transfers from the embossing
tools to the support. In a specific illustrative form, a silver amalgam, such as employed
in silvering mirrors, can be coated on the embossing tool and transferred to the walls
of the microcells.
[0201] Once the support with microcells therein is formed, material forming the radiation-sensitive
portion of the photographic element, or at least one component thereof, can be introduced
into the microcells by doctor blade coating, solvent casting or other conventional
coating techniques. Identical or analogous techniques can be used in forming receiver
or filter elements containing microcells. Other, continuous layers, if any, can be
coated over the microcells, the opposite support surface or other continuous layers,
employing conventional techniques, including immersion or dip coating, roller coating,
reverse roll coating, air knife coating, doctor blade coating, gravure coating, spray
coating, extrusion coating, bead coating, stretch-flow coating and curtain coating.
High speed coating using a pressure differential is illustrated by Beguin U.S. Patent
2,681,294. Controlled variation in the pressure differential to facilitate coating
starts is illustrated by Johnson U.S. Patent 3,220,877 and to minimize splicing disruptions
is illustrated by Fowble U.S. Patent 3,916,043. Coating at reduced pressures to accelerate
drying is illustrated by Beck U.S. Patent 2,815,307. Very high speed curtain coating
is illustrated by Greiller U.S. Patent 3,632,374. Two or more layers can be coated
simultaneously, as illustrated by Russell U.S. Patent 2,761,791, Wynn U.S. Patent
2,941,898, Miller et al U.S. Patent 3,206,323, Bacon et al U.S. Patent 3,425,857,
Hughes U.S. Patent 3,508,947, Herzhoff et al U.K. Patent 1,208,809, Herzhoff et al
U.S. Patent 3,645,773 and Dittman et al U.S. Patent 4,001,024. In simultaneous multilayer
coating varied coating hoppers can be used, as illustrated by Russell et al U.S. Patent
2,761,417, Russell U.S. Patents 2,761,418 and 3,474,758, Mercier et al U.S. Patent
2,761,419, Wright U.S. Patent 2,975,754, Padday U.S. Patent 3,005,440, Mercier U.S.
Patent 3,627,564, Timson U.S. Patents 3,749,053 and 3,958,532, Jackson
U.S. Patent 3,993,019 and Jackson et al U.S. Patent 3,996,885. Silver halide layers
can also be coated by vacuum evaporation, as illustrated by Lu Valle et al
U.S. Patents 3,219,444 and 3,219,451. Materials to facilitate coating and handling
can be employed in accordance with conventional techniques, as illustrated by Research
Disclosure, Vol. 176, December 1978, Item 17643, paragraphs XI and XII.
[0202] In some of the embodiments of the invention described above a multicolor photographic
element or filter element is to be formed which requires an interlaid pattern of microcells
which are filled to differ one from the other. Usually it is desired to form an interlaid
pattern of at least three different microcell confined materials. In order to fill
one microcell population with one type of material while filling another remaining
microcell population with another type of material at least two separate coating steps
are usually employed and some form o.f. masking is employed to avoid filling the remaining
microcell population with material intended for only the first microcell population.
[0203] One technique that has been proposed for filling three separate sets of microcells
each with a different material is to form the separate sets of microcells one at a
time and fill that set of microcells before forming another set. For example, a planar
support in which it is intended to form interlaid first, second, and third sets of
microcells containing first, second, and third imaging materials, respectively, is
first embossed to form only the first set of microcells. Thereafter the first set
of microcells is filled with the first imaging material. There is no risk of including
first imaging material in other microcells, since they are not yet formed. If desired,
the first set of microcells can be sealed after being loaded with the first imaging
material to assure that no migration of this material occurs. A thin hydrophilic colloid
coating can perform the sealing function.
[0204] The second set of microcells is then embossed in the support interlaid with but offset
from the first set of microcells. The second set of microcells is then loaded with
the second imaging material. Since only the second set of microcells is empty to receive
the second imaging material, there is no difficulty in directing this material to
this set of microcells. If desired, third or even additional sets of microcells can
be similarly formed and loaded. Care must, of course, be exercised to register second
and subsequent embossings with prior embossings so that they are properly laterally
related.
[0205] One preferred technique for selectively filling microcells to term an interlaid pattern
of two or more differing microcell populations is to fill the microcells on at least
one major surface of the support with a material which can be selectively removed
by localized exposure without disturbing the material contained in adjacent microcells.
A preferred material for this purpose is one which will undergo a phase change upon
exposure to light and/or heating, preferably a material which is readily sublimed
upon moderate heating to a temperature well below that at which any damage to the
support occurs. Sublimable organic materials, such as naphthalene, and para-dichlorobenzene
are well suited for this use. Certain epoxy resins are also recognized to be suitable.
However, it is not necessary that the material sublime. For example, the support microcells
can be initially filled with water which is frozen and selectively thawed. It is also
possible to fill the microcells with a positive-working photoresist which is selectively
softened by exposure. The softened photoresist can be washed out of the microcells
on development.
[0206] Another approach for selectively emptying one set of microcells to permit selective
loading involves the selective mechanical removal of an initially present material
from one set of microcells to be loaded. This can be accomplished by initially introducing
into all of the microcells a fluid material, such as a finely particulate or liquid
material, and thereafter fusing the material into a solid mass by radiation exposure
and/or heating. Selective removal of material from the microcells containing either
fused or unfused material can then be achieved by applying an adhesive cover sheet
to the major face of the support toward which the microcells open. By proper choice
of materials it is possible (1) to have the fused material adhere to the adhesive
cover sheet in preference to the microcell walls while the unfused material remains
in the microcells or (2) to have the unfused material adhere to the cover sheet while
the fused material adheres to the microcell walls. In the former instance repetition
of the process can be undertaken to remove fused material to fill second and third
sets of microcells in sequence. In the latter instance an alternative approach must
be employed for removing the fused material to permit loading of the microcells in
which it is contained and the microcells containing unfused material have been emptied
by stripping the cover sheet and selectively loaded with imaging material. Thus, a
wide range of materials which sublime, melt or exhibit a marked reduction in viscosity
upon exposure can be employed.
[0207] According to a preferred exposure technique a laser beam is sequentially aimed at
the microcells forming one population of the interlaid pattern. This is typically
done by known laser scanning techniques, such as illustrated by Marcy U.S. Patent
3,732,796, Dillon et al U.S. Patent 3,864,697 and Starkweather et al U.S. published
patent application B309,860. According to one specific, preferred technique two lasers
are employed. One of the lasers is of sufficient intensity to provide the desired
alteration with the microcells. The second laser is used only to position accurately
the first laser and can differ in wavelength and can be of lesser intensity. The first
and second laser beams are laterally displaced in the plane of the support by an accurately
determined distance. By employing a photodetector to receive light transmitted through
or reflected from the support from the second laser, it can be determined when a microcell
or a lateral wall is aligned with the second laser beam. In one preferred form, in
which the support bottom walls are substantially transparent and the lateral walls
are dyed, a substantial change in light intensity sensed by the photodetector will
occur as a function of the'relative position of the support and laser beam. In other
instances differences in reflection or refraction between the bottom and lateral walls
forming the microcells can be relied upon to provide information to the photodetector.
Once the position of the second laser with respect to a microcell is ascertained,
the position of the first laser with respect to a microcell can also be ascertained,
since the spacing between the lasers and the center-to-center widths of the microcells
are known. Depending upon the pattern and accuracy of exposure desired, indexing with
the second laser can be undertaken before exposing each microcell with the first laser,
only once at the beginning of exposure of one microcell population, or at selected
intermediate intervals, such as before each row of microcells of one population is
exposed.
[0208] When a first laser scan is completed, the support is left with one exposed microcell
population while the remaining microcells are substantially undisturbed. Instead of
sequentially laser exposing the microcells in the manner indicated, exposure through
a mask can be undertaken, as is well known. Laser scanning exposure offers the advantages
of eliminating any need for mask preparation and alignment with respect to the support
prior to exposure.
[0209] Where sublimable material is employed as an initial filler, the microcells are substantially
emptied during their exposure. Where the filler material is converted to a liquid
form, the exposed microcells can be emptied after exposure with a vacuum pickup. The
empty microcell population can be filled with imaging and/or filter materials using
conventional coating techniques, as have been described above. The above exposure
and emptying procedure is then repeated at least once, usually twice, on different
microcells. Each time the microcells emptied are filled with a different material.
The result is two, usually three, or more populations of microcells arranged in an
interlaid pattern of any desired configuration. An illustrative general technique,
applied to filling microcells in a gravure plate, is described in an article by D.
A. Lewis, "Laser Engraving of Gravure Cylinders", Technical Association of the Graphic
Arts, 1977, pp. 34-42, here incorporated by reference.
[0210] One alternative specifically preferred method of introducing imaging materials on
the supports at the desired locations is to move the support past a coating zone at
a substantially constant velocity. At the same time a stream (or jet) of substantially
equally sized and spaced drops of liquid containing imaging material is directed to
the support.
[0211] It is desirable, for stable drop formation break-up of the liquid jet, that photographic
liquids utilized in accordance with the present invention have a relatively high surface
tension characteristic and a relatively low viscosity characteristic. Thus aqueous
solutions or suspensions are one preferred form of photographic liquid for use in
the present invention. However other liquids, e.g. containing organic liquids can
be utilized if system parameters such as liquid surface tension, liquid density, liquid
viscosity and liquid jet diameter are properly adjusted. That is, higher liquid surface
tension and larger jet diameters facilitate the use of more viscous liquids. Temperature
of the photographic liquid also can be regulated to control liquid viscosities. It
is preferred that liquid viscosity be below about 5 centi- poise; however, high viscosity
liquids are useful in systems particularly designed to accommodate them. Also, in
embodiments of the invention employing electrically charged liquid drops, it is desirable
that the liquid have resistivity in the range of about 100 to 5000 ohm-cm. However,
other liquid resistivities are useful. Further background regarding useful parameters
of the kind described above can be found in the literature pertaining to inks for
ink jet printing.
[0212] Referring now to Fig. 18, next will be described preferred modes for depositing such
photographic liquids on such photographic supports in accordance with the present
invention. Figure 18 illustrates a web of support material 30 having many discrete
microcells, covering its upper surface (only three are shown). The support material
30 is moving in the direction indicated, from an upstream position to coating zones
that are located under liquid jet generator means, denoted generally 31, 32 and 33.
[0213] The jet generator means, in general, can be one of the many kinds now known in the
art of ink jet printing, which is currently in active development. Typically such
generator means fall in one of two broad classes, "on-demand" or "continuous." On-demand
generators can be of an electrostatically-gated type wherein a drop is formed at a
nozzle under low pressure (so that surface tension forces retain it) and released
by application of a high voltage between the drop meniscus and a gating electrode
(see e.g. U.S. Patent 2,600,129). On-demand generators also can be of the pressure-pulsed
type which utilize a transducer element, e.g. a piezoelectric crystal, that is selectively
energized to generate compressive force on a body of liquid to thus propel a drop
of the liquid through an orifice to a deposition zone. Exemplary pressure-pulsed generators
are disclosed e.g. in U.S. Patents 3,840,758 and 3,857,049. Although the on-demand
jet generators are useful in accordance with the present invention, the "continuous"
type jet generator is preferred and generator means 31, 32 and 33 shown in Fig. 18
are of this continuous type.
[0214] In general, continuous drop stream generators comprise a nozzle, or array of nozzles,
through which liquid is forced under pressure in a cylindrical jet. Such a cylindrical
jet is unstable and will break up into a series of drops. If the jet is subject to
a vibration of frequency near that corresponding to the fastest growing natural disturbance
within the jet (Rayleigh calculated this to be A = 4.51 x the jet diameter), the jet
can be broken up by this vibration. In this mode the jet forms a series of drops,
each of volume equal to a cylindrical section of the jet, which will be the length
of the impressed vibration wavelength.
[0215] Thus drop stream generators 31, 32 and 33 each respectively comprise a manifold and
nozzle array (35, 36 and 37), an electro-mechanical transducer (41, 42 and 43) for
impressing vibrations on the nozzle array and a supply (45, 46 and 47) of pressurized
photographic imaging liquid for coating on the support 30. Exemplary configurations
useful for such droplet generators are shown in more detail in U.S. Patents 3,373,437;
3,596,275; 3,586,907; 3,701,476; 3,701,998; 3,714,928; 3,739,393; 3,805,273 and 3,836,913.
[0216] In the usual ink jet generators, including those described in the previously cited
patents, an electrostatic charge is impressed on drops as they break from the stream,
and electrical deflection fields are provided along the drop stream path to guide
the charged drops to the desired destination. In the Fig. 18 embodiment, voltage sources
V
1, V
2 and V
3 provide potcntial to charge the drops, and lines L
1, L
2 and L
3 selectively energize deflector plates under the control of logic unit 40. Although
drop charging and field deflection are utilized in the subsequently described liquid
jet coating method, it will be understood that in other preferred embodiments according
to the present invention, drop deflection is not required.
[0217] Thus, support 30 is moved, as indicated in Fig. 18, at substantially constant velocity
past the coating stations beneath drop generators 31, 32 and 33, in the direction
D indicated in Figs. 1 and 3. As successive portions of the support move sequentially
past the coating stations, drop streams are directed onto predetermined sites of those
portions, i.e. into predetermined microcells within those portions. That is, the rate
of drop generation, the sequence of drop deflection and the velocity of movement of
the support past the coating zone are synchronized so that drops from generator 31
are deposited in a first set of microcells of the support, the drops from generator
32 are deposited in a second set of microcells of the support and the drops from generator
33 are deposited in a third set of microcells of the support.
[0218] More specifically, consider the drop stream from generator 31, which is supplied
with photographic coating liquid from supply 45. The orifices of the nozzle array
and liquid pressure (thus jet velocity) are chosen so that the drop size and rate
are compatible with the size and pitch P of the first set of microcells of the support
and the selected velocity of web movement. Logic unit 40 will therefore impress a
frequency on the array causing drop generation at a rate "r" that is equal to the
support velocity V divided by the intercell pitch of the microcells in the direction
of support movement D. Drop generators 32 and 33 function under control of logic unit
40 in a similar manner to deposit other photographic coating liquids in the remaining
microcell groups of the support 30.
[0219] To obtain proper synchronization of the transducers 41, 42 and 43 with the microcells
on the moving support 30 (and to maintain synchronization in the event of microcell
pitch variation or support velocity fluctuation), a control unit 50 is located upstream
from the coating zones. In its simplest form unit 50 can comprise a detector which
identifies microcell positions and signals of the logic unit 40 dynamically in accord
therewith. As illustrated in Fig. 18, the control unit 50 comprises a laser 51 whose
light beam is scanned by acoustooptic deflector 52 across the surface of a lens array
53 (e.g. fiber optics) adapted to direct light through the support to collector array
54. The collector array directs the scanned light to detector 55 which thus provides
logic unit 40 with the microcell line positions and indications of any deviation in
microcell position transversely across the support. If desired, selected logic corrections
can be applied to individual deflector plates of the generator arrays to correct for
transverse variations.
[0220] To further enhance the precision of drop deposit in the microcells, several additionally
preferred modes of operation can be utilized in cooperation with the method just described.
Thus, at a location upstream from the coating zones electrostatic charging station
60 can provide a charge (of the same polarity as the droplet charge) on the top surface
of the microcell walls. In the illustrated embodiment station 60 comprises conductive
rollers 61 and 62 and voltage source 63 for creating a potential of proper polarity
on roller 61. Thus e.g. a negative charge on cell wall tops will deflect the negatively
charged drops toward the center of the microcell. This electrostatic guidance is further
enhanced by creating a positive bias on the microcell bottoms which attracts the positively
charged drops. Positively biased rollers 65, 66, 67 provide this effect.
[0221] Another preferred droplet guidance enhancement procedure, useful in cooperation with
the present invention, is illustrated by pre-coating station 70. There a roller 71
applies to the top of the cell walls, from supply 72, a layer of material to which
the photographic coating liquids are hydrophobic. Thus, the photographic coating drops
seek the relatively hydrophilic microcell interiors in preference to the tops of cell
walls. One skilled in the art will appreciate that if the photographic coating liquid
"prefers" a hydrophobic surface, the microcells can be relatively hydrophobic.
[0222] To avoid unwanted disturbance of the droplet's flight, it is preferred in accordance
with the present invention to evacuate the atmosphere along the path from generators
31, 32 and 33 to the support. This can be accomplished by conventional means (not
shown).
[0223] One skilled in the art will appreciate that various modifications of the specifically
disclosed procedure are within the scope of the invention. For example, it would be
equivalent to move the drop generator instead of the support or to move both to provide
a predetermined relative velocity. Also it will be appreciated that the present invention
has utility in coating supports which do not have cell walls.
[0224] Another specifically preferred approach for loading one set of mircrocells or microcells
with one imaging material while loading a second set of microcells with another imaging
material is to place a physical closure over the microcells and thereafter selectively
remove the closure from one set of microcells so that it can be loaded. When the first
set of microcells is entirely filled by loading, the closure can be removed and the
remaining microcells loaded without any other step being required. Alternatively,
when the first set of microcells are not entirely filled or when three or more sets
of microcells are to be each filled with differing imaging materials, then the steps
of closing and selectively opening the microcells can be repeated.
[0225] Figures 19A through 19D illustrate the application of this method to the manufacture
of an element containing three interlaid sets of microcells each containing a different
material or combination of materials.
[0226] In Figure 19A the support 1902 is shown similar to supports described above. Adjacent
the first major surface 1904 of the support is a membrane 1906. The membrane overlies
and closes the microcells 1908 of the support. The membrane is comprised of or entirely
formed of a film-forming organic polymer and is thin as compared to the lateral walls
1910 of the support. The membrane is preferably of a thickness of from about 5 to
50 percent that of the lateral walls. The microcells preferably initially contain
a readily removable thermal insulator, such as air, although any readily removable
material could be initially present.
[0227] While any convenient conventional technique can be employed for forming the membrane
and locating it in the position shown in Figure 19A, in most instances the membrane
will be about 0.2 to 1 micron in thickness so that many approaches useful in forming
thicker membranes will not be useful in forming or positioning the membrane 1906.
In one specific preferred approach the membrane is formed by casting a film-forming
polymer in a volatile solvent on the surface of a liquid in which the polymer does
not readily dissolve, such as water, contained in a reservoir. The film is allowed
to at least partially set by solvent evaporation. To protect the film from disturbances
a floating frame can be laid on the film, if desired. By slowly raising the support
1902 from within the reservoir to the surface of the water, the membrane can be positioned
on the first major surface of the support in the desired position without endangering
the integrity of the membrane. Any water initially trapped in the microcells will
evaporate if the element is allowed to stand for a period of time. The minimal thickness
of the membrane allows both air and water vapor to diffuse therethrough, so that in
a period of time an element is produced as shown in Figure 19A having only air in
the microcells. It is appreciated that other volatile or highly thermally nonconductive
liquids can be substituted for water in providing a casting surface, if desired. Instead
of raising the support through the water, the support can be simply laid on the dry
upper surface of the membrane with the first major surface of the support contacting
the membrane.
[0228] The next step of the process is to selectively open the microcells intended to form
one of the interlaid sets. Any technique which allows one set of microcells to be
opened selectively can be employed. It is preferred to employ radiation striking the
membrane to open the set of microcells. Any of the various techniques disclosed by
Whitmore, such as the use of masks, can be employed. According to a preferred technique
a laser beam is sequentially aimed at the microcells forming one interlaid set. This
is typically done by known laser scanning techniques, such as illustrated by Marcy
U.S. Patent 3,732,796, Dillon et al U.S. Patent 3,864,697 and Starkweather et al U.S.
published patent application B309,860.
[0229] Following a specific, preferred technique two lasers are employed. One of the lasers
is of sufficient intensity to provide the desired alteration of the membrane overlying
the microcells. The second laser is used only to position accurately the first laser
and can differ in wavelength and can be of lesser intensity. The first and second
laser beams are laterally displaced in the plane of the membranes by an accurately
determined distance. By employing a photodetector to receive light transmitted through
or reflected from the support from the second laser, it can be determined when a microcell
or a lateral wall is aligned with the second laser beam. In the illustrated preferred
form, in which the support bottom walls are substantially transparent and the lateral
walls are dyed, a substantial change in light intensity sensed by the photodetector
will occur as a function of the relative position of the support and laser beam. In
other instances differences in reflection or refraction between the bottom and lateral
walls forming the microcells can be relied upon to provide information to the photodetector.
Once the position of the second laser with respect to a microcell is ascertained,
the position of the first laser with respect to a microcell can also be ascertained,
since the spacing between the lasers and the center-to-center spacings of the microcells
are known. Depending upon the pattern and accuracy of exposure desired, indexing with
the second laser can be undertaken before exposing each microcell with the first laser,
only once at the beginning of exposure of one microcell set, or at selected intermediate
intervals, such as before each row of microcells of one set is exposed.
[0230] When a first laser scan is completed, the support is left with one open microcell
set while the remaining interlaid microcell sets are substantially undisturbed. Instead
of sequentially laser exposing the microcells in the manner indicated, exposure through
a mask can be undertaken, as is well known. Laser scanning exposure offers the advantages
of eliminating any need for mask preparation and alignment with respect to the microcells
prior to opening one microcell set.
[0231] When radiant energy from a laser or other source impinges on the membrane in one
or more areas corresponding to one microcell or microcell set, the membrane is locally
heated. 'It is specifically preferred to impinge radiant energy selectively over that
portion of the membrane lying at or near the center of the underlying microcell. Since
the membrane is extremely thin, its heat capacity is low. That is, very little heat
energy is required to raise its temperature. Thus, a laser beam, for example, can
quickly raise the temperature of the organic membrane to its decomposition point in
a selected area overlying a microcell. Since the membrane is no more than half the
thickness of the lateral walls and usually of much less thickness, the lateral walls
do not rise in temperature to the same extent as the membrane, even when both the
membrane and support are formed of the same material. Being thicker, the lateral walls
have a higher heat capacity, slowing their increase in temperature. Second, if the
radiant energy is confined to the area near the center of the underlying microcell,
heat must be conducted laterally by the membrane to the lateral walls; but being very
thin, the membrane is an inefficient thermal conductor. Selective thermal destruction
of the membrane can be enhanced by forming the support of a more thermally stable
material, so that if the membrane and support should approach the same temperature,
the membrane will still be selectively destroyed.
[0232] It is specifically contemplated to employ a radiant energy source and membrane in
combination which allows the membrane to absorb efficiently the radiant energy. The
film-forming polymer composition can be modified by incorporating an ultraviolet absorber,
dye, or infrared absorber. Independently, an absorption promoting material can be
coated over the membrane once it is formed in place. For example, the membrane can
receive a deposit of lamp black by being passed over an open flame to increase its
absorption of radiant energy. In addition to increasing the radiant energy absorption
by the membrane, the support can be chosen so that it is relatively nonabsorbing in
the spectral region of the radiant energy.
[0233] From the foregoing it is apparent that, by selectively addressing areas of the membrane
overlying one set of microcells, it is possible to open selectively one set of microcells
without affecting adjacent sets of microcells and without damaging the support. Thereafter,
the opened set of microcells can be filled by any convenient conventional technique
without filling the remaining microcells. This is illustrated by reference to Figure
19B, in which the membrane 1906 has been modified by the introduction of apertures
1912 corresponding to one underlying set of microcells. For purposes of illustration,
the open set of microcells is shown to be filled with material forming the blue filter
segments B.
[0234] In filling the open set of microcells, a technique is preferably chosen which places
minimal physical stress on the membrane. For example, in the form illustrated, an
aqueous solution of blue dye or suspension of blue pigment can be introduced into
the open set of microcells while placing only minimal stress on the remaining membrane.
Upon evaporation of water, the blue dye or pigment is left in the open set of microcells.
Filling can be repeated, if desired, until the desired optical density of blue dye
or pigment is obtained in the open microcells. This approach can be practiced with
any material or combination of materials desired to be placed in the microcells and
any compatible volatile liquid. By proper choices of materials and liquids layering
can be achieved within the microcells, if desired. In an alternative form the filling
material can take the form of a fine particulate which is gently brushed into the
microcells. The particles, of course, have mean diameters substantially less than
the width of the microcells. The particles can, if desired, be fused in place. For
example, many particulate materials will fuse simply by standing under conditions
of high humidity. Fusion by mild heating is also contemplated.
[0235] In Figure 19C a second, interlaid set of microcells is shown opened and filled to
form green filter segments G. The techniques described above for opening and filling
the first set of microcells can be repeated unchanged, except for the substitution
of green filter material. When this stage of the process is reached, only discrete
segments 1914 of the original membrane remain overlying the third, interlaid set of
microcells.
[0236] To permit the third, interlaid set of microcells to be filled, the techniques described
above for opening the first and second sets of microcells can be repeated, except
that a red filter material is substituted. The product, as shown in Figure 19D, is
the multicolor filter element 1102. It will be apparent that the last set of microcells
can be filled by a broader selection of techniques than the first and any intermediate
sets of microcells. In opening the last set of microcells the techniques employed
for removing the membrane need not be areally selective. For example, in the specific
embodiment illustrated, since the membrane can be entirely destroyed in opening the
last set of microcells, it is not necessary to address the membrane segments 1914
selectively with radiant energy. Rather, the element as shown in Figure 19C can be
uniformly exposed to radiant energy to destroy the membrane segments 1914. Alternatively,
the membrane segments remaining can be removed by laminating it to a support to which
it adheres in preference to the first major surface 104 and then simply lifting the
membrane segments from the first major surface. Adhesion of the membrane segments
to another support can be accomplished by any one of a wide variety of conventional
laminant transfer techniques.
[0237] It is not even necessary to remove the membrane segments 1914 before filling. By
employing filling techniques which are in themselves capable of destroying the membrane
segments, the steps of opening and filling the last set of microcells-can be combined.
For example, by doctor blade coating the element as shown in Figure 19C with a red
filter material, the membrane segments can be collapsed into the underlying microcells
while leaving room for the red filter material to also enter the third set of microcells.
[0238] The foregoing microcell filling technique is particularly well suited to applications
in which the microcells of each set, except the last, are intended to be substantially
entirely filled. Thus, any material intended to be placed in a subsequent set of microcells
after the first set has been opened and filled cannot enter the first set of microcells,
since material filling these microcells prevents additional material from entering.
Any slight amount of material that may deposit above the first, filled set of microcells
in filling the second or subsequent sets can in many applications be ignored. Alternatively,
the additional surface material can be removed by gently abrading the first major
surface 104 of the support after all of the microcells have been filled. For example,
the major surface 1904 of the support can be swabbed or skived with a doctor blade
to remove any materials over and above those which are contained in the microcells.
[0239] In a variant approach, which is particularly applicable to only partially filling
the microcells or maintaining a high degree of separation of materials being placed
in separate sets of microcells, after the first set of microcells are opened and partially
filled to the extent desired, a second membrane is positioned over the first major
surface of the support. If desired, the first membrane can be entirely removed before
positioning the second membrane, as by using the laminant or destruction techniques
described above. Where the membranes are comparatively thin, so that the multiple
layers of membrane can still be thermally destroyed selectively without damaging the
support lateral walls, the second membrane can be positioned over the first, now apertured,
membrane. The first and second membranes are then selectively destroyed in areas overlying
the second set of microcells, so that these microcells can be at least partially filled
through the resulting apertures. Placement of the third membrane, if employed, follows
the same techniques and considerations as for the first and second membranes. It is
usually preferred that the last set of microcells be opened by the overlying membrane
or membranes being selectively addressed, thereby preserving the closure of the sets
of microcells previously at least partially filled. Depending upon the desired application,
any membrane(s) remaining after the last set of microcells have been selectively filled
to the extent desired can either be left in place, destroyed, or transferred to a
separate support, as has been described above.
[0240] In an alternative to the processes of differentially filling microcells in interlaid
sets described above, it is contemplated to place in all of the microcells prior to
closure by a membrane at least one material that permanently remains in at least one
interlaid set of microcells. The membrane closing the microcells is removed by any
of the specific techniques described above in all areas, except those corresponding
to the set of microcells in which initially present material is intended to remain.
Initially present material is then removed from the opened microcells. For example,
a soluble material can be removed merely by bringing the element into contact with
a solvent, as by spraying with or immersion in the solvent. Once at least one set
of microcells have been emptied, a second material or combination of materials is
placed in the emptied set of microcells.
[0241] The general procedure described above can be illustrated by reference to forming
the multicolor filter element 1102. A removable blue filter material, such as a blue
filter dye that can be solubilized is initially introduced into microcells 1908 of
the support 1902. The microcells are then closed with a membrane 1906 so that the
element appears similar to that of Figure 19A, but with the microcells each containing
blue filter material. Thereafter, the interlaid second and third sets of microcells
intended to contain green and red filter materials, respectively, are opened by using
any of the selective membrane removal techniques described above. Membrane segments
similar to 1914 now overlie only the microcells in which the filter material is to
be retained. The element can be contacted with a solvent for the blue filter material,
permitting it to be removed from the open second and third sets of microcells. The
second and third sets of microcells can be now at least partially filled with a green
filter material which can be solubilized, and the second and third sets of microcells
are closed with a second membrane. The segments of the first membrane can be first
removed or, preferably, left in place, since they do not affect the process. Using
an essentially repetitive procedure, the portions of the second membrane overlying
the third set of microcells is selectively removed, and the green filter material
is removed from the third set of microcells. The second membrane remains intact closing
the first and second sets of microcells, and the blue and green filter materials remain
in place in these microcells. Red filter material can now be introduced into the third
set of microcells.
[0242] It is to be noted that, since the membranes protect the microcells containing the
material desired to be retained, the green and blue microcells can be entirely or
only partially filled with material without any variation in the process. It is immaterial
whether the red filter material can be solubilized or whether the red filter material
entirely or partially fills the third set of microcells, since this has no effect
on the process steps. Once the third set of microcells are filled to the extent desired,
any portion of the membrane left in place can be removed, if desired, depending upon
the intended application for the element. Since air is an exceptionally good thermal
insulator, it is preferred that the microcells be only partially filled with the blue
and green filter materials to leave an air gap in the microcells separating the filter
materials from the membranes; however, if the filter materials are good thermal insulators,
the increase in laser energy required in addressing entirely filled microcells can
be tolerated.
[0243] The membranes positioned to close the microcells of the support are comprised of
any material which can be selectively destroyed or removed over an area corresponding
to that subtended by an underlying microcell (or, in some instances, an underlying
cluster of microcells). In general the membranes can be most conveniently formed of
organic film-forming polymers. The membranes can be identical in composition to conventional
photographic film supports. Typical film-forming polymers useful in forming membranes
are cellulose nitrate and cellulose esters, such as cellulose triacetate and diacetate,
polyamides, homo- and co-polymers of styrene, acrylates and methacrylates, vinyl chloride,
poly(vinyl acetal), and olefins, such as ethylene and propylene. Where the membranes
are intended to be thermally destroyed, as by impingement with a laser beam, the less
thermally stable film-forming polymers used in preparing photographic film supports
are preferred. Merely heating the membranes to their thermal decomposition temperature
is not, however, the only way of destroying the membranes. Cellulose coatings and
particularly cellulose nitrate can be selectively destroyed in exposed areas by alpha
particles and similar fusion fragments, as taught by Sherwood U.S. Patent 3,501,636,
here incorporated by reference. It is also specifically contemplated to employ electron
beams to destroy the membrane in selected areas.
[0244] Although the foregoing description is directed to certain preferred embodiments of
this invention, it is appreciated that a variety of modifications can be undertaken.
In one form of the membrane described above it is contemplated to incorporate a dye
in the membrane to increase its heat absorption characteristics. This offers the advantage
of rendering the membrane capable of adsorbing more energy upon laser addressing and
thereby making more efficient use of the laser beam employed for opening the microcells.
On the other hand, remnants of the membrane which are not thermally destroyed in opening
the microcells can impart coloration to the support which may be objectionable for
certain applications. Therefore it is specifically contemplated to incorporate in
the membrane a bleachable dye. For example, a heat and/or light bleachable dye can
be incorporated in the membrane. This will permit the membrane to more readily adsorb
light during laser addressing, but permits any remnants of the membrane remaining
in the completed product to be converted to a form exhibiting little or no coloration.
Both heat and light bleachable dyes are well known in the art, as illustrated by Sturmer
U.S. Patents 3,984,248, 3,988,154, and 3,988,156, Heseltine et al U.S. Reissue Patent
29,168, Krueger U.S. Patent 4,111,699, and Wise et al U.S. Patent 3,769,019.
[0245] When the membrane is located on the support, in most instances there is sufficient
adhesion to hold the membrane securely in position. Nevertheless, it is not necessary
to rely solely on adhesion to retain the position of the membrane. It is specifically
contemplated to place the membrane on the support in an atmosphere containing a gas
more membrane-permeable than air. For example, the unfilled microcells can be covered
by the membrane in a helium atmosphere. Upon standing in air the helium will slowly
diffuse through the membrane into the admosphere, but air, having a lower rate of
permeation of the membrane, will not diffuse through the membrane sufficiently to
replace the helium thus escaping. The result is that a pressure below atmospheric
will develop within the microcells. This pressure differential serves to hold the
membrane in position closing the microcells. Other techniques of holding the membrane
in position on the support can be employed also in combination with those techniques
described above or alone.
[0246] In most instances the membrane remains flexible as positioned on the support. If
desired, the membrane can be treated once positioned on the support to increase its
rigidity and strength. The exact treatment chosen will depend upon the specific composition
of the membrane, but, in general, the membranes are formed of polymeric materials
which can be increased in rigidity and strength by cross-linking. Effective cross-linking
agents can be chosen from among those generally known in the art, including photographic
hardeners, such as those disclosed in Research Disclosure, Vol. 176, December 1978,
Item 17643. For cellulose and cellulose derivative membranes preferred cross-linking
agents are epoxides, as illustrated by Allen et al U.S. Patent 3,047,394, Burness
U.S. Patent 3,189,459, and Birr German Patent 1,085,663. A particularly effective
epoxide cross-linking agent is 1,4-butanediol diglycidyl ether, available under the
trademark Acryldite.
[0247] In still an additional method of selectively introducing differing imaging materials
into interlaid sets of microcells both the composition of the support and the composition
of the imaging material is modified. The portion of the support forming at least the
bottom walls of the microcells is formed of a photoconductive material. The imaging
material is then prepared as an electrographic composition. By using xerographic imaging
techniques the electrographic imaging composition can be selectively placed in the
desired set of microcells. Such an approach to selectively loading the microcells
can best be appreciated by reference to an illustrative embodiment.
[0248] A specific preferred support 2000 is schematically illustrated in Figure 20. The
support is comprised of a photoconductive portion 2002 which has substantially parallel
first and second major surfaces 2004 and 2006. The photoconductive portion defines
a plurality of microcells (or microvessels) 2008, which open toward the first major
surface. The microcells are defined in the photoconductive portion by an interconnecting
network of dyed lateral walls 2010 which are integrally joined to a substantially
transparent underlying portion 2012 so that the photoconductive portion acts as a
barrier between adjacent microcells. The underlying portion defines the bottom wall
2014 of each microcell. The lateral walls need not be photoconductive. They can alternatively
be formed identically to the separate second support elements previously described.
[0249] In addition to the photoconductive portion, the support is formed by a thin, transparent
conductive layer 2016 and a transparent film base 2018. Along at least one lateral
edge of the support, not shown, the film base and the conductive layer can extend
laterally beyond the photoconductive portion to facilitate attachment of an external
conductor to the support. A charge control barrier layer, not shown, can be interposed
between the conductive layer and the photoconductive portion. Depending on the choice
of conductive materials employed, electrical biasing of a particular polarity can,
in some instances, result in charge injection from the conductive layer into the photoconductive
portion rendering it conductive. The function of the charge control barrier layer
is to intercept and trap injected charge--i.e., electrons or holes. Charge control
barrier layers are well known in the art, as illustrated by Dessauer et al U.S. Patent
2,901,348, Gramza et al U.S. Patent 3,554,742, Humphris et al U.S. Patent 3,640,708,
and Hodges German OLS 1,944,025, the disclosures of which are here incorporated by
reference.
[0250] Although the support is shown to be comprised of the photoconductive portion, the
conductive layer, and the film base, it is appreciated that it may be formed of only
the photoconductive portion. For instance, once the microcells are filled to the extent
desired, the conductive layer and/or film base can be stripped from the photoconductive
portion, leaving it as a separate element. Alternatively, the photoconductive portion
can form the entire support and be brought into contact, as required, with an electrode
which forms no part of the support. Although the support is shown to be transparent
with dyed lateral walls, it can be entirely transparent or entirely reflective--e.g.,
white. The photoconductive portion can be transparent, and the film base replaced
with a conventional photographic paper support. Other variant forms will be readily
apparent.
[0251] The electrostatic charge method of microcell loading of the present invention is
generally applicable to the formation of elements containing in a first set of microcells
a first imaging composition and in at least one other, interlaid set of microcells
a different imaging composition. Broadly, this method can be practiced with any microcellular
support in which the portion forming the microcells is sufficiently insulative to
permit an electrostatic charge to be selectively associated with one set of microcells.
For example, the remaining, interlaid microcells can be uncharged or bear an opposite
polarity electrostatic charge. The support with a charge pattern corresponding to
the distribution of the one set of microcells is brought into contact with a carrier
vehicle containing dispersed therein particles of an electrographic imaging composition.
As defined herein the term "electrographic" as applied to the imaging composition
means that it is capable of forming an image on a support exhibiting an electrostatic
charge pattern. By placing an electrostatic charge on the one set of microcells which
is opposite in polarity to the charge exhibited by the dispersed particles of the
electrographic imaging composition, the charged particles are selectively attracted
into the ' one set of microcells in preference to the remaining set of microcells.
One or more differing imaging compositions can be introduced into the remaining microcells
by repeating the procedures described above or by any other convenient conventional
technique.
[0252] A specific, preferred embodiment of the process of this invention is described by
reference to Figures 21A through 21D. In Figure 21A the support 200 is shown with
the photoconductive portion 2002 bearing on its outer surface a positive electrostatic
charge, applied in a nonimagewise manner to provide a substantially uniform charge
distribution. It is to be noted that the positive charge not only covers the bottom
walls 2014 of the microcells, but also covers the upper edges of the lateral walls
2010. As is well understood by those skilled in the art, the electrostatic charge
can be conveniently applied by passing the support through a corona discharge.
[0253] The next step of the process is to remove the electrostatic charge selectively from
the bottom walls of a first, interlaid set of microcells without disturbing the electrostatic
charge in other areas of the support. This is accomplished by rendering the photoconductive
portion 2002 of the support conductive in areas corresponding to the bottom walls
of the first set of microcells. By grounding or negatively biasing the conductive
layer 2016, electrostatic charge can be conducted through the conductive areas of
the photoconductive portion leaving the bottom walls of the first set of microcells
substantially discharged, as shown in Figure 21B.
[0254] The photoconductive portion can be rendered conductive in areas corresponding to
the first set of microcells by supplying radiant energy to which the photoconductive
portion is responsive to these areas. According to a preferred technique a laser beam
of a wavelength to which the photoconductive portion is sensitive is sequentially
aimed at the microcells forming the first set. This can be done by known laser scanning
techniques, such as illustrated by Marcy U.S. Patent 3,732,976, Dillon et al U.S.
Patent 3,864,697, and Starkweather et al U.S. published patent application B309,860.
The width of the laser beam can be adjusted to expose a plurality of adjacent microcells,
but it is preferably less than the width of a single microcell, so that the microcells
can be individually addressed.
[0255] Following a specific, preferred technique two lasers are employed. One of the lasers
is chosen to provide the desired alteration in conductivity. The second laser is used
only to position accurately the first laser . It is preferably of a wavelength to
which the photoconductive portion is less responsive and can be of lesser intensity.
The first and second laser beams are laterally displaced in the plane of the support
by an accurately determined distance. By employing a photodetector to receive light
transmitted through or reflected from the support from the second laser, it can be
determined when a microcell or a lateral wall is aligned with the first laser beam.
In the illustrated preferred form, in which the microcell bottom walls are substantially
transparent and the lateral walls are dyed, a substantial change in light intensity
sensed by the photodetector will occur as a function of the relative position of the
support and laser beam. In other instances differences in reflection or refraction
between the bottom and lateral walls forming the microcells can be relied upon to
provide information to the photodetector. Once the position of the second laser with
respect to a microcell can also be ascertained, the position of the first laser with
respect to a microcell can also be ascertained, since the spacing between the lasers
and the center-to-center spacings of the microcells are known. Depending upon the
pattern and accuracy of exposure desired, indexing with the second laser can be undertaken
before exposing each microcell with the first laser, only once at the beginning of
exposure of one microcell set, or at selected intermediate intervals, such as before
each row of microcells of one set is exposed.
[0256] When a first laser scan is completed, the support is left with one uncharged microcell
set while the remaining interlaid microcell set are substantially undisturbed. Instead
of sequentially laser exposing the microcells in the manner indicated, exposure through
a mask can be undertaken by well known techniques. Laser scanning exposure offers
the advantages of eliminating any need for mask preparation and alignment with respect
to the microcells.
[0257] To introduce a first imaging composition selectively into the first set of microcells,
a development procedure can be employed as illustrated in Figure 21C. A direct current
source 2102 is connected between a development electrode 2104 and the conductive layer
2016 of the support so that the development electrode is positively biased with respect
to the conductive layer 2016. An electrographic developer containing a carrier liquid
2106 and dispersed positively charged particles 2108 of an electrographic imaging
composition is interposed between the development electrode and the support 2000 so
that it can enter the microcells. The positive bias on the development electrode can
be viewed as induceing a negative electrostatic charge on the bottom walls of the
first set of microcells. (See Schaffert, Electrophotography, John Wiley Sons, New
York, p. 16.) The positively charged dispersed particles of electrographic imaging
composition are therefore selectively attracted into the first set of microcells while
being concurrently repelled from the remaining microcells, which contain a positive
electrostatic charge. Since it is preferred to attract the electrographic imaging
composition to the bottom walls of the microcells, it is appreciated that it is advantageous
to form the lateral walls 1020 of a nonphotoconductive material. This avoids having
the imaging material attracted to the lateral walls. In Figure 21D a first set of
microcells of the support 2000 are shown partially filled with a green electrographic
imaging composition.
[0258] To complete the preparation of an element containing green, red, and blue imaging
compositions in first, second, and third interlaid sets of microcells, the procedure
described above can be twice repeated, except that the second and third sets of microcells
are selectively laser addressed in second and third repetitions and a different electrographic
imaging composition is employed in each instance. Where the first and second sets
of microcells are substantially filled, the third set of microcells can be filled
by any of the techniques for filling microcells with a single imaging composition,
such as doctor blade coating, for example, since the third imaging composition cannot
enter the first and second sets of microcells in any significant quantity. The second
and third sets of microcells can be filled also by using any of the other filling
procedures disclosed.
[0259] It is an unexpected advantage of the present invention that when the procedure of
this invention described above is repeated second and subsequent electrographic imaging
compositions do not enter the set or sets of microcells which have already received
an electrographic imaging composition. Surprisingly, this is true even if the first
set of microcells is not entirely filled and even if the first set of microcells is
again exposed to radiation, either intentionally or inadvertently, in rendering the
photoconductive portion conductive in the areas of the second and subsequent sets
of microcells. This effect is hereinafter referred to as the exclusion effect. Hercock
et al U.S. Patent 3,748,125 reports exclusion effects for xerographic toners of specific
compositions applied to planar photoconductive surfaces. The exclusion effect observed
in the practice of this process does not appear related to any specific choice of
electrographic imaging compositions. Without wishing to be bound by any particular
theory to account for the exclusion effect observed, it may result from photoconductive
surface masking by the already deposited imaging compositions, field gradient or fringing
effects (influenced to a degree by the nonplanar configuration of the photoconductive
surface), or, most probably, some combination of these effects.
[0260] The exclusion effect facilitates the formation of interlaid patterns without introducing
more than one electrographic imaging composition into any one set of microcells. This
can be illustrated by reference to Figure 22. The multicolor filter 2200 can be formed
by introducing into a first set of microcells a green electrographic imaging composition,
as has been described above in connection with Figures 21A through 21D. It is to be
noted that the microcells labeled G, which each contain a green filter segment lie
in alternate rows of microcells. This offers the advantage of allowing uninterrupted
laser scanning of entire rows of microcells rather than addressing individual microcells,
as required for the pattern of Figure 2A, for example. After introducing the green
electrographic imaging composition, rotating the support 60°, and again nonimagewise
electrostatically charging the photoconductive portion of the support, the laser can
uninterruptedly scan alternate rows of microcells. During this second laser scan,
the laser beam crosses the microcells already containing the green electrographic
imaging composition. Because of the exclusion effect, however, during development
with a red electrographic imaging composition, only the microcells which are both
laser addressed and free of the first, green imaging composition receive the red electrographic
imaging composition. To introduce the third, blue imaging composition into the microcells
remaining forming the third set, the laser scanning procedure employed for the second
laser scan is repeated addressing now the alternate rows skipped during the second
scan. Following development with a blue electrographic imaging composition, the result
is the filter segment pattern shown in Figure 22. It is to be noted than an interlaid
pattern is obtained in which both red and blue filter segments are entirely surrounded
by filter segments of the remaining two sets. Yet this result is obtained with only
uninterrupted linear scanning by the laser, thereby significantly decreasing the amount
of laser indexing which would be required in the absence of the exclusion effect.
[0261] It is to be appreciated that the description of the process of this invention by
reference to Figures 21A through 21D and 22 is merely illustrative of certain preferred
embodiments. Numerous variations will readily occur to those skilled in the art of
electrophotography, once the invention is appreciated. For example, the polarity of
charge on the photoconductive portions, electrographic imaging composition particles,
and development electrode can be reversed without the exercise of invention. The use
of a development electrode is not required. Reversal development through field fringing
is known to be obtainable for small areas, such as line copy. Further, it is possible
to choose the polarity of the electrographic imaging composition particles so that
it is opposite that of the electrostatic charge on the photoconductive portion and
therefore attracted to the remaining charged microcells not exposed rather than the
microcells which are expu6ed. In such an alternative, initial laser scanning covers
the entire surface of the photoconductive portion, except the area represented by
the first set of microcells. Any conventional electrographic imaging composition particle
size capable of entering the individual microcells can be employed. It is preferred
to employ particle sizes of less than about 25 percent of the width of the microcells.
Although electrographic developers containing liquid carrier vehicles are preferred,
since smaller particle sizes compatible with the widths of the microcells are more
readily employed, any conventional electrographic development technique, such as the
use of aerosols and dry toners, can be employed. Liquid electrographic developers
are particularly preferred which require no separate fusing step to hold the electrographic
imaging composition particles in place in the microcells. A separate fusing step can
be employed where all of the components of the electrographic imaging composition
are intended to remain permanently in the microcells, as in a simple multicolor filter,
such as 2200, but it is preferred to avoid a separate fusing step intended to produce
a high degree of fusing where one or more materials are to be removed from the microcells.
Conventional biasing voltages are generally suitable for the practice of this process.
[0262] Preferred electrographic imaging compositions are comprised of a colorant portion,
which can include pigments, dyes, and/or dye precursors for producing filters or transferred
or retained dye images, as described above, and from 0.1 to 10 (preferably 0.3 to
3.0) parts by weight per part of the colorant portion of a resinous portion capable
of forming a particulate dispersion with the colorant portion in a liquid carrier
vehicle having a dielectric constant of less than 3.0 and a resistivity of at least
10
10 ohm-cm. At least one of the colorant and resinous portions is chosen to impart an
electrostatic charge of a selected polarity to the particulate dispersion in the liquid
carrier.
[0263] In one specific illustrative form the colorant portion of the preferred electrographic
imaging compositions is additionally comprised of at least one immobile additive primary
colorant or a combination of immobile colorants capable of collectively providing
a desired additive primary color further in combination with a positive or negative-working
dye image providing compound of the type used in producing a transferred dye image.
Unlike the subtractive primary dyes and dye precursors, the immobile additive colorants
which provide an additive primary color should remain immobile at all times and should
not wander from the microcells either before, during, or after a photographic image
is obtained. Suitable immobile colorants can be selected from among a variety of materials,
such as dyes and pigments, but are most preferably pigments, since these can be more
readily obtained in highly immobile forms. Useful immobile colorants can be selected
from the Color Index, 2nd Edition, 1956, Vols. I and II. Useful immobile polymeric
dyes are illustrated by Goldman et al U.S. Patent 3,743,503. Specific preferred immobile
pigments are disclosed in Research Disclosure, Vol. 109, May 1973, Item 10938, Paragraph
IX-C-2. Exemplary of preferred green, red, and blue immobile pigments are Monolite
Green GN, Red Violet MR® (Hoechst), Pyrazalone Red® (Harmon), Alkali Blue MG
* (Sherwin-Williams), and Monolite Blue
* (ICI). Exemplary of useful green, red, and blue substantially immobile dyes are Renazol
Brilliant Green 6B, Red Dye R3G (Drimarene Scarlet)® (Sandoz), and MX-G Procion Blue*
(ICI). The proportions of the subtractive primary dye or dye precursor to the immobile
additive primary colorant can be varied as desired to achieve an intended imaging
result without the exercise of invention. The proportions will vary, depending upon
the specific materials selected. For most materials ratios of subtractive primary
dye or dye precursor to immobile additive colorant in the range of from about 1:10
to 10:1, most commonly 1:2 to 2:1, are operative, although optimum color balancing
for a specific application requires individual adjustment by empirical procedures
well known to those skilled in the art.
[0264] The resinous portion which together with the colorant portion forms dispersed particles
in the liquid electrographic developer is preferably insoluble in the liquid carrier
vehicle or only slightly soluble therein. Resinous materials acting as binders appear
to form a coating around the colorants and thus facilitate dispersion in the liquid
carrier. Examples of useful resins are: alkyd resins as described in Australian Patent
254,001; acrylic resins described, for example,,in U.S. Patents 3,671,646 and 3,334,047;
alkylated polymers described, for example, in U.S. Patents 3,542,681 and '682; rosins
described, for example in U.S. Patent 3,399,140; polystyrene as described, for example
in Australian Patent 253,986 and U.S. Patent 3,296,140; addition polymers containing
a polar moiety as described, for example, in U.S. Patent 3,788,995; ethyl cellulose
described in U.S. Patent 3,703,400; cellulosic polymers as described, for example,
in U.S. Patent 3,293,183; polyamides, shellac as described, for example, in U.S. Patent
2,899,335; waxes or rubber-modified polystyrenes as described, for example, in U.S.
Patent 3,419,411; rosin-modified as described, for example, in U.S. Patent 3,220,830;
silica aerogels as described, for example, in U.S. Patent 2,877,133; halogenated polyethylenes
described, for example, in U.S. Patent 2,891,911; graft copolymers described, for
example, in U.S. Patent 3,623,986; cyclized rubbers described, for example, in U.S.
Patent 3,640,863; vinyl polymers described, for example, in
U.S. Patent 3,585,140 as well as coumaroneindene resins; ester gum resins; and polymerized
blends of certain soluble monomers, polar monomers and, if desired, insoluble monomers
as described in Belgian Patent 784,367.
[0265] In order to exhibit electrographic properties, the imaging composition must have
an electrostatic charge when dispersed as particles in a liquid carrier. The colorants
can themselves impart the desired electrostatic charge to the dispersed particles.
The colorants are selected to exhibit a single polarity of charge to insure the lowest
possible minimum densities. The electrostatic charge polarity of the dispersed particles
can be enhanced or controlled by the selection of resinous binder materials and/or
suitable charge control agents. Illustrative charge control agents are the polyoxyethylated
alkyl surfactants such as polyoxyethylated alkylamine, polyoxyethylene palmitate,
and polyoxyethylene stearate. Other useful materials are magnesium and heavier metal
soaps of fatty and aromatic acids as described in U.S. Patents 3,417,019, 3,032,432,
3,290,251, 3,554,946, 3,528,097, and 3,639,246. Useful metal soaps include cobalt
naphthenate magnesium naphthenate and manganese naphthenate, zinc resinate, calcium
naphthenate, zinc linoleate, aluminum resinate, isopropyltitanium stearate, aluminum
stearate, and others many of which are also described in Matkan U.S. Patent 3,259,581.
Typically, the amount of such materials used is less than about 2 percent by weight
based on the weight of the imaging composition. In certain instances, the resinous
binder materials per se can function as the charge control agent as disclosed, for
example, in U.S. Patent 3,788,995, cited above. A dispersing aid can also be added
as shown, for example in U.S. Patent 3,135,695. This patent shows an electrographic
liquid developer prepared by surrounding or dispersing electrographic-type pigment
particles with a suitable resinous binder envelope and treating the pigment-binder
combination with a small amount of an alkylaryl compound before suspending the combination
in a liquid aliphatic carrier. This type of liquid electrographic developer is especially
useful due to its relatively high stability. Other addenda may include: a phospholipid
charge stabilizing material, e.g., lecithin, as described in U.S. Patents 3,220,830,
3,301,677, 3,301,698, 3,241,957, 3,668,126, and 3,674,693, and U.K. Patent 1,337,325;
noble metal salts as described in French Patent 1,354,520, isocyanate compounds as
described in U.K. Patent 654,977, and U.S. Patent 3,383,316; magnetic particles as
described in U.S. Patent 3,155,531; conductive materials as described in U.S. Patents
3,300,410 and 3,409,358; fatty acid esters as described in U.S. Patent 3,692,520;
manganese salts as described in U.S. Patent 3,438,904; antistain agents as described
in U.S. Patent 3,681,243; and hydroxy-stearins as described in U.S. Patent 3,701,731.
[0266] Conventionally, the liquid carrier vehicle used in liquid electrographic developers
has a low dielectric constant less than about 3.0 and a resistivity of at least about
10° ohm-cm, preferably at least 10
10 ohm-cm. These requirements automatically eliminate water and most alcohols. However,
a number of liquids still are available to satisfy the above-noted requirements and
have been found to function as effective carrier vehicles for liquid developers. Among
the various useful liquid carrier vehicles are alkylaryl materials such as the xylenes,
benzene, alkylated benzenes and other alkylated aromatic hydrocarbons such as are
described in U.S. Patent 2,899,335. Other useful liquid carrier vehicles are various
hydrocarbons and halogenated hydrocarbons such a cyclohexane, cyclopentane, n-pentane,
n-hexane, carbon tetrachloride, fluorinated lower alkanes, such as trichloromono-
fluorane and trichlorotrifluorethane, typically having a boiling range of from about
2°C to about 55°C. Other useful hydrocarbon liquid carrier vehicles are the paraffinic
hydrocarbons, for example, the isoparaffinic hydrocarbon liquids having a boiling
point in the range of 145°C to 185°C (sold under the trademark Isopar by Exxon) as
well as alkylated aromatic hydrocarbons having a boiling point in the rage of from
157° to 177°C (sold under the trademark Solvesso 100 by Exxon). Various other petroleum
distillates and mixtures thereof may also be used as liquid carrier vehicles. Additional
carrier liquids which may be useful in certain situations include polysiloxane oils
such as dimethyl polysiloxane as described in U.S. Patents 3,053,688 and 3,150,976;
Freon carriers as described in Canadian Patent 701,875 and U.S. Patent 3,076,722;
mixtures of polar and nonpolar solvents as described in U.S. Patent 3,256,197; aqueous
conductive carriers such as described in U.S. Patent 3,486,922; nonflammable liquid
carriers such as described in U.S. Patent 3,058,914; polyhydric alcohols such as described
in U.S. Patent 3,578,593; and emulsified carriers such as described in U.S. Patents
3,068,115 and 3,507,794. Electrographic imaging composition can be dispersed in the
liquid carrier vehicle in any convenient conventional concentration, typically in
the range of from 0.01 to 10 percent by weight based on total weight. Conventional
techniques for dispersing the electrographic imaging composition can be employed,
as disclosed, for example, in Research Disclosure, Item 10938, cited above, Paragraph
IX-E and F.
[0267] Any conventional photoconductive material or combination of photoconductive materials
can be employed in the microcellular supports of this invention. Suitable photoconductive
materials are disclosed, for example, in Research Disclosure, Vol. 109, May 1973,
Item 10938, Paragraph IV. Photocon
- ductive materials which in themselves are capable of forming microcells can be employed
alone, as in the case of polymeric organic photoconductors which are plastically deformable.
The photoconductive material is preferably incorporated in a separate insulative binder
to form a microcellular structure, as disclosed by Wiegel, U.S. Patent 3,561,358.
Preferred photoconductive supports and support portions can be formed as taught by
Contois et al, Research Disclosure, Vol. 108, April 1979, Item 10823. Other suppport
portions, such as the conductive layers and base portions, can take any conventional
form, exemplary materials being disclosed in Research Disclosure, Item 10938, cited
above, Paragraphs II Supports and III Interlayers. When, as is preferred, the lateral
walls are formed of a nonphotoconductive material, the various second support element
materials described above can be employed. Poly(vinyl butyral), because of its adhesion
to the exemplified photoconductive materials is a preferred lateral wall forming material.
[0268] In a specific preferred form at least the photoconductive portion of each support
is substantially transparent. Where the photoconductive material forms a part of a
multicolor reflective photographic print, for instance, even a slight coloration is
apparent to the human eye and therefore objectionable. For such applications, preferred
photoconductive materials are those sensitive to the ultraviolet portion of the spectrum,
but not sensitized to the visible spectrum, to avoid imparting a visible minimum density.
Such photoconductive materials can be addressed with an ultraviolet laser beam.
[0269] In certain applications, as where radiation-sensitive materials are intended to be
located in the microcells, it is not practical to use ultraviolet radiation to address
the photoconductive portion, since many radiation-sensitive imaging materials exhibit
a native sensitivity in the ultraviolet region of the spectrum. For example, silver
halide possesses a native sensitivity in the near portion of the ultraviolet spectrum.
For introducing each of blue, green, and red-sensitized silver halide into separate
sets of microcells, the photoconductive portion is preferably sensitized to the red
or a longer wavelength region of the spectrum. The first and second sets of microcells
can be addressed with a red laser beam without fogging the blue and green-sensitized
silver halides introduced into the first and second sets of microcells. Even if a
third laser scan is employed, the red-sensitized silver halide introduced into the
third set of microcells is not fogged, since the red-sensitized silver halide is not
introduced until after the third laser scan is completed.
[0270] Sensitization of photoconductive materials to a selected portion of the spectrum
can be undertaken employing spectral sensitizing dyes well known in the electrographic
arts, such as those disclosed in Research Disclosure, Item 10838, cited above, Paragraph
IV-C. Any minimum density imparted by spectral sensitization need not be objectionable.
For example, if the photographic image to be produced is not intended to be viewed
directly, such as a multicolor negative image used for printing a multicolor positive
image, coloration due to spectral sensitization is not objectionable, since color
correction can be introduced in printing by procedures well known to those skilled
in the art.
[0271] In loading interlaid areas of the support surface with differing imaging materials
wherein the imaging materials are located as a function of a pattern of radiation
exposure, by exposing at an acute angle with respect to the plane of the support shadowing
can be relied upon to define exposed and unexposed support areas. Shadowed and unshadowed
areas can be controlled by varied lateral wall geoemetries forming the microcells.
The angle of exposure can also control exposures. A variety of specific illustrative
forms are described below.
[0272] An illustrative simple support 2300 is shown in Figures 23A and 23B. The support
has substantially parallel first and second major surfaces 2302 and 2304. The support
defines a plurality of parallel microgrooves 2306, which open toward the first major
surface of the support. The microgrooves are defined in the support by an array of
lateral walls 2308 which are integrally joined to an underlying portion 2310 of the
support.
[0273] In Figure 23B the arrows 2312 schematically designate radiation striking the support
at an acute angle b with respect to an axial plane 2314 along which the support is
areally extended. A portion of the radiation strikes the bottom walls 2316 of the
microgrooves in unshadowed microareas 2316A while another portion of the radiation
strikes the lateral walls 2308 and is thereby interrupted, so that microareas 2316B
of the microgrooves are shadowed and do not receive radiation, at least not to the
same extent, as the unshadowed microareas.
[0274] The lines 2318 define the boundary of an area unit containing a single microgroove.
The remaining depicted area of the support is formed by area units essentially identical
to that within the boundary. Each area unit forms a pixel. The term "pixel" is employed
herein to indicate an area which can be repeated to make up the support.
[0275] Certain features of the invention can be appreciated by reference to support 2300.
First, it should be noted that the lateral walls 2308 lie along half the boundaries
between adjacent micro- areas. Thus, if a material is contained in the microgrooves
which is capable of lateral spreading, it is restrained from spreading between microareas
over half of the boundaries therebetween. Similarly, radiation that might otherwise
be scattered between adjacent microareas is also restrained where the lateral walls
are present.
[0276] The acute angle b at which the radiation is directed toward the support can be varied
by repositioning either the radiation source and/or the support. As shown, the radiation
is directed parallel to the section line 23B-23B and perpendicular to the major axes
of the lateral walls 2308. In this orientation the minimum angle of 8 at which the
radiation can strike the bottom walls 2316 is determined by the relationship tan 8
= H/W, where H is the height of the lateral walls 2308 and W is the width of the bottom
walls 2316. It is therefore apparent that the proportion of the bottom walls that
are unshadowed can be controlled by varying any one or combination of b, H, or W.
Further, if the support is rotated 90° with respect to the radiation source so that
the radiation is introduced perpendicular to the section line 23B-23B, no shadows
are produced. It is therefore apparent that maximum shadowing for a given value of
⊖ is achieved when radiation is introduced perpendicularly to the major axes of the
lateral walls and that the degree of shadowing can be decreased by rotating the lateral
walls of the support toward alignment with the radiation.
[0277] Referring to Figure 23A, it can be appreciated that if the support 2300 is resolved
into two separate halves joined along the section line 23B-23B and one half is translated
with respect to the other along the axial plane 2314, the support continues to respond
to angled radiation exposure substantially as described above--that is, it continues
to satisfy the essential shadowing criteria described above. The plane represented
by the section line 23B-23B thus constitutes a glide plane--herein defined as a plane
separating two support portions which can be displaced relative to each other along
the axial plane of the support without dimininishing the shadowing utility of the
support. It is further observed that the support 2300 can be resolved not just into
halves, but into a large number of separate portions displaced along the axial plane
without substantially altering its shadowing utility. It is thus apparent that the
support 2300 provides only a simple example of a large family of lateral wall arrays
that provide roughly similar shadowing utility.
[0278] This is specifically illustrated in Figure 24 in which support 2400 is comprised
of identical support regions 2400A, 2400B, 2400C, and 2400D joined along parallel
glide planes 2402. In comparing supports 2300 and 2400, it can be seen that the two
supports are identical, except that the support regions 2400A and 2400C are laterally
displaced with respect to the support regions 2400B and 2400D. This has the result
of producing lateral walls 2408 and microareas 2416A and 2416B which are limited in
their maximum dimension in the form shown to the distance between glide planes 2402.
Thus, support 2400 is superior to support 2300 for applications in which the microareas
are preferably limited in their longest dimension. For example, by positioning the
glide planes between support regions at a spacing of 200 microns or less and the lateral
walls within each support region at a center-to-center spacing of 400 microns or less,
microareas limited in both length and width to 200 microns or less can be readily
obtained. As a result of the relative translation of adjacent support regions, the
support 2400 contains no grooves, but only upstanding lateral walls. This illustrates
that neither microgrooves nor any other type of areally limited depressions in the
support are required for the practice of this invention.
[0279] In further comparing the microarea patterns of supports 2300 and 2400, it can be
appreciated that the microareas 2416A and 2416B are interspersed to a greater degree
than the microareas 2316A and 2316B. The microareas 2416A and 2416B are interlaid
along two perpendicular axes, whereas the microareas 2316A and 2316B are interlaid
along only one axis. The higher degree of interlay can represent a distinct advantage
for specific applications requiring a high degree of interlay for desired optical
or chemical properties.
[0280] Still further comparing the supports 2300 and 2400, it can be seen that the lateral
walls 2408 separate the first and second microareas 2416A and 2416B over a boundary
approximately equal in length to that by which the lateral walls 2308 separate the
microareas 2316A and 2316B. However, in the support 2400, because the microareas 416A
and 416B are more highly interspersed, there is a larger boundary between adjacent
microareas where no lateral walls are present. This feature of the support 2400 can,
however, be readily modified in a manner which does not diminish the shadowing utility
of the support. If, for example, additional lateral walls are introduced along the
glide planes 2402 in Figure 24, it can be seen that the lateral walls now extend over
a much larger proportion of the boundaries between adjacent microareas. The result
is to limit significantly the boundary region available for lateral spreading between
adjacent microareas.
[0281] If additional lateral walls are provided for the support 2400 along the glide planes
2402, it is apparent that a predetermined, ordered array of microcells is created,
each containing two micro- areas. In the geometrical form described the microcells
produced on the modified support 2400 are approximately square, but it is apparent
that microcells of any geometric configuration can be employed. Thus, supports exhibiting
any of the microcell configurations disclosed above can be employed in the practice
of this invention. Polygonal (square, rectangular, and hexagonal), circular, and elliptical
microcell configurations have been explicitly disclosed, although any other predetermined
recurring microcell configuration (or combination of configurations, discussed below)
can be employed in the practice of this invention.
[0282] Any predetermined, ordered array of lateral walls capable of interrupting radiation,
whether or not microcells or microgrooves are formed by these walls, can be employed
in the practice of this invention to produce two or more laterally displaced contiguously
adjoining microareas (that is, micro- areas which over some boundary region are not
separated by lateral walls). Supports having uniformly spaced lateral wall arrays,
such as supports 2300 and 2400, or supports having a single repeated microcell configuration
are particularly suited for forming two or more laterally displaced contiguous sets
of microareas that are of uniform size in each individual occurrence.
[0283] Figures 23A, 23B, and 24 illustrate perhaps the simplest shadowing approach of this
invention wherein the bottom walls of the supports are shown divided into two separate
interlaid sets of uniform microareas of substantially equal area by a single exposure
of the support to radiation directed toward the axial plane of the support at an acute
angle. Where one composition is introduced into exposed microareas and a second composition
is introduced into unexposed or shadowed microareas, an interlaid array of two separate
compositions is produced. For some applications the microareas represented by the
lateral walls can also be utilized, so that three separate useful sets of microareas
are actually present.
[0284] Supports useful as described above can also be applied to applications requiring
more than two laterally displaced compositions. For example, in Figures 23A and 23B
it can be seen that by adjusting the angle of exposure
b, the size of the micro- areas 2316A exposed can be adjusted. If, for example, it
is desired to place three separate strips of equal size of three separate compositions
between adjacent pairs of lateral walls 2308, the angle b is adjusted so that the
radiation strikes only one third of the area of each bottom wall 2316. A first composition
can then be selectively positioned in the microareas corresponding to the exposed
portions of the bottom walls. The angle b is then increased so that on a second exposure
radiation strikes the area originally struck, now containing the first composition,
and a contiguous one third of each bottom wall 2316. A second composition is then
selectively positioned in the microareas corresponding to the exposed areas not occupied
by the first composition. The procedure can be repeated using radiation directed perpendicu-larly
to the axial plane 2314 to position a third composition in a third laterally displaced
set of microareas, or the third composition can in many instances be introduced by
a conventional technique for coating a single composition, such as doctor blade coating.
Although described by reference to three compositions and a specific support, it is
apparent that the procedure is generally useful with all of the supports containing
lateral wall arrays herein described and with more than three compositions.
[0285] The procedure described above for positioning three or more laterally displaced compositions,
while useful with all lateral wall array patterns, relies in part on the presence
of a previously positioned composition to define a microarea resulting from a later
exposure. Stated another way, the first and second exposures are in part areally overlapping.
This limits the shadowing procedure described above to use with materials which allow
the presence or absence of one composition to exclude a subsequent composition, as
is possible in certain preferred embodiments of this invention. Exclusion and exhaustion
effects are discussed more specifically below.
[0286] It is possible to address uniquely two or more areas of a support according to this
invention so that no materials dependent exclusion effect is relied upon. An approach
for uniquely addressing two separate sets of microareas with radiation while creating
a third set of microareas by shadowing is illustrated in Figures 25A, 25B, and 25C.
Except as otherwise noted below, the features bearing 2500 series reference numerals
are identical to those bearing the corresponding 2300 series reference numerals in
Figures 23A and 23B and are not redescribed in detail.
[0287] The support 2500 as illustrated differs from support 2300 solely in the use of an
optional transparent underlying portion 2510; however, the lateral walls 2508 remain
capable of interrupting radiation. In Figure 25B radiation 2512A is directed toward
the axial plane 2514 at an angle 0 chosen to permit impingement of radiation only
on the microareas 2516A. The remaining area of each bottom wall 2516 is shadowed by
the lateral walls 2508. Thus, exposure as shown in Figure 25B creates one set of microareas
2516A in an interlaid pattern with remaining support areas. A first composition can
be selectively positioned in the first set of microareas.
[0288] In Figure 25C the support is given a second exposure to radiation 2512B at an acute
angle b'. As shown, the radiation exposure patterns in Figures 25B and 25C are mirror
images, although the angles band
b' need not be equal, except when the microareas 2516A and 2516B are intended to be
equal. Instead of changing the direction of radiation between the first and second
exposures, the support could alternatively be rotated 180° in the axial plane.
[0289] Radiation impinges on the bottom walls 2516 only in the microareas 2516B, creating
a second set of radiation exposed microareas. A second composition can be selectively
positioned in the second set of microareas. A third set of microareas 2516C, not exposed
by either the first or second exposures, is created concurrently with the second set
of micro- areas. A third composition can be positioned in the third set of microareas,
if desired. It is to be noted that the first composition is laterally spaced from
the second microareas, and no exclusion property is required in order to position
the second composition. It is appreciated that the angles b and/or
b' can be increased to eliminate the microareas 2516C without in any way altering the
shadowing technique described above.
[0290] Using the support 2300, 2400, and 2500,only two interlaid sets of microareas can
be uniquely addressed by shadowing techniques. By the term "uniquely addressed" it
is meant that a set of microareas is exposed to only the single radiation exposure
which defines its boundaries and no other microarea defining radiation exposure. It
is possible, however, to produce three, four, five, six, or even more sets of uniquely
addressed micro- areas in a single support containing microcells. For this purpose
microcells of polygonal shape are preferred. Generally the number of sets of uniquely
addressed areas that can be produced by shadowing in a single polygonal microcell
is equal to its number of apices.
[0291] An illustration of the creation of micro- areas in a set of polygonal microcells
by shadowing techniques of the type described above is provided in Figures 26A and
26B, in which a detail of a support 2600 containing a predetermined, ordered array
of microcells 2602 of a regular hexagonal shape is shown. The support 2600 in section
can appear identical to the supports shown in Figures 23B or 25B. Referring first
to Figure 26A, exposure of the support 2600 in a direction parallel to arrow la at
an acute angle with the axial plane of the support exposes the bottom wall of each
microcell in only diamond-shaped area lb, the remainder of the wall of each microcell
being shadowed. By changing the direction of exposure, as indicated by arrows 2a,
3a, 4a, 5a, and 6a, but not the exposure angle, five more identical diamond-shaped
exposed micro- areas 2b, 3b, 4b, 5b, and 6b are produced. The six diamond-shaped microareas
provided in each microcell are of equal area, since each microcell is a regular hexagon
and the angle of exposure is unchanged. It is to be noted that none of the six microareas
impinges on any other of the six diamond-shaped microareas and therefore each is uniquely
addressed by shadowing exposures. Thus, it is possible to place up to six separate
compositions in each microcell 2602 without relying upon any exclusion property.
[0292] Exposure can be terminated after the sixth exposure and the central area of each
microcell can be left unexposed, if desired. In this instance the lateral spacing
in the center of each microcell between compositions introduced into the six separate
microareas can be relied upon to prevent or reduce boundary mixing of compositions.
In an alternative form in which the central region is desired to receive material,
one or more compositions can be employed capable of wandering from the diamond-shaped
areas to cover the central portion of each microcell.
[0293] By using a combination of the procedures described above and exclusion effects, it
is possible to produce additional microareas in each hexagonal microcell 2602. As
shown in Figure 26A, a microarea 7b equal in area to the diamond-shaped areas is produced
by exposing at the same acute angle in a direction indicated by arrow 7a. The radiation
overlaps both the microareas lb and 2b in exposing additional microarea 7b. By using
exclusion effects a seventh composition can be located in only the microarea 7b. Microareas
8b, 9b, 10b, llb, and 12b are sequentially similarly formed by shadowing exposures
along like numbered axes.
[0294] Thus far it can be seen that 12 microareas can be formed, six of which can be uniquely
addressed and six of which depend on exclusion effects. At this point the central
portion of each hexagonal microcell remains shadowed. If desired, the central portion
of the microcell can be left shadowed and unfilled. Alternately, the central, shadowed
portion of the microcell can be filled with a single composition. For example, if
the micro- areas lb, 2b, 3b, 4b, 5b, and 6b receive a first composition and the microareas
7b, 8b, 9b, lOb, llb, and 12b receive a second composition, a third composition can
be located in the central, shadowed portion of each microcell, and three compositions
will occupy roughly equal areas of each microcell bottom wall.
[0295] By increasing the acute angle of exposure and relying on exclusion effects, it is
possible to form additional microareas in the central, initially shadowed portion
of each microcell. By exposing again in the direction indicated by arrow 7a, but at
an increased acute angle, the microarea 13b can be formed, which is roughly equal
to the previously formed microareas. Similarly, by exposing in the direction indicated
by arrow 10a microarea 14b can be formed. By exposure in the direction indicated by
arrow 6a the microarea 15b can be formed, and by exposing in the direction indicated
by arrow 3a the microarea 16b can be formed. Microareas 13b, 14b, 15b, and 16b are
all formed at the same acute angle of exposure and are approximately equal. By increasing
the acute angle of exposure again, microareas 17b and 18b can be formed by exposing
in the direction indicated by arrows 6a and 3a, respectively. These microareas are
roughly equal to the previously formed microareas. Two triangular microareas 19b remain
unexposed which, together are roughly equal to the remaining microareas. By using
shadowed microareas 19b as one microarea, 19b laterally spaced compositions can be
placed on the bottom walls of each hexagonal microcell, each composition occupying
an approximately equal area. The shown pattern is, of course, only exemplary. Shadowing
exposures can produce microareas of differing configuration, size, and number.
[0296] The ability to uniquely address a plurality of sets of microareas so that the microareas
cover an entire surface of a support, except for the areas occupied by lateral walls,
is an obvious advantage in making maximum use of a support surface and in achieving
a high degree of interdigitation of compositions. Some lateral wall patterns offer
this capability and some do not. In referring to supports 2300, 2400, and 2500, it
can be seen that the lateral wall patterns permit the creation of uniquely addressed
microareas which cover the entire support surface not occupied by the lateral walls.
It is also apparent that microcells of square or rectangular configuration also offer
this capability, since it has already been pointed out above that any two contiguous
microareas in the same segment of the support 2400 can be enclosed in a microcell
without altering the shadowing capability of the support. Upon further reflection
it can be appreciated that square and rectangular microcells are but special cases
of lozenge (diamond-shaped) and parallelogram configuration microcells and that all
such microcells can be uniquely addressed over their entire bottom wall areas. As
shown in Figure 26A, the uniquely addressed areas lb through 6b of the hexagonal microcells
2602 do not occupy the entire bottom surface of the microcell; but, referring to Figure
26B, the identical support is uniquely addressed over the entire bottom walls of the
microcells by three exposures at an acute angle with respect to the axial plane. Area
ld is addressed by exposure in a direction lc, area 2d by exposure in a direction
2c, and area 3d by exposure in a direction 3c. This demonstrates that uniquely addressing
microcells over their entire bottom walls is a function not only of the shape of the
microcells, but also a function of the angle and direction of exposure. Many microcell
configurations, such as circular, elliptical, triangular, and trapezoidal microcells
cannot be uniquely addressed over their entire bottom wall areas by shadowing techniques,
regardless of the number or angle of shadowing exposures attempted.
[0297] While the present invention can employ supports containing any of the microcell arrangements,
it is additionally recognized that advantageous results can be obtained by using supports
containing identical microcells which by their orientation can be resolved into interlaid
sets that can be differentially addressed.
[0298] This is illustrated in Figure 27, in which a support 2700 is provided with a plurality
of identical microcells which appear triangular in plan. As can be readily appreciated,
however, the triangular microcells are not all similarly aligned. There are two interlaid
sets of microcells 2702A and 2702B. When the support is addressed by radiation at
an acute angle with respect to its axial plane, as indicated by arrow 2704, radiation
strikes the bottom walls of the microcells 2702A in microareas 2706A and strikes the
bottom walls of the microcells 2702B in microareas 2706B. It is to be noted that the
microareas are equal, but differ in their orientation similarly as the microcells
in which they occur. While the triangular microcells shown are each equilateral triangles,
triangles of any desired type, including isosceles and right triangles, can be employed
with similar results.
[0299] In each of the embodiments heretofore described at least two sets of microareas are
contiguously adjoining--that is, they are not separated by a lateral wall over some
portion of their boundary. Thus, the advantages which lateral walls have to offer
in preventing lateral spreading either of materials or radiation are partially, but
not entirely, realized. The preferred supports are those which offer the capability
of providing two or more interlaid sets of microareas by shadowing techniques, each
of the microareas being entirely separated from microareas of other sets by lateral
walls. Specifically preferred supports are those which allow three separate compositions
to be interlaid by shadowing techniques in separate sets of microareas each separated
from the other by lateral walls.
[0300] A simple support 2800 capable of providing three interlaid sets of microareas each
entirely separated from the other by lateral walls is illustrated in Figures 28A,
28B, and 28C. Except as otherwise noted, the features bearing 2800 series reference
numerals are identical to those bearing the corresponding 2300 series reference numerals
in Figures 23A and 23B and are not redescribed in detail.
[0301] The lateral walls 2808 of the support are arranged in parallel relationship, but
unlike the lateral walls in support 2300, are unequally spaced in a predetermined,
ordered manner. The widest spaced lateral wall pairs together with the connecting
portion 2810 form a first set of microgrooves 2806A each having a bottom wall 2816A.
The next widest spaced pairs of lateral walls similarly form a set of microgrooves
2806B each having a bottom wall 2816B. The closest spaced pairs of lateral walls form
a third set of microgrooves 2806C having a bottom wall 2816C.
[0302] When the support is exposed with radiation as indicated by arrows 2812A in Figure
28B, the acute angle b with respect to the axial plane 2814 is chosen so that the
radiation strikes only the bottom walls 2816A. The bottom walls 2816A are shadowed,
however, to some degree. The extent to which the bottom walls 2816A are shadowed can
be reduced significantly by performing a second exposure as described above in connection
with support 2500. For example, the support can be rotated 180° and given a second
exposure at the same angle. By properly positioning the lateral walls and choosing
the angle
b, it is possible to expose all of the bottom walls 2816A without exposing any portion
of the bottom walls 2816B and 2816C. Once the bottom walls 2816A have been selectively
exposed, a first composition can be selectively located in the first microgrooves
2806A.
[0303] With a first composition 2850 in place, as shown in Figure 28C, the support is given
a second exposure to radiation 2812B at an increased acute angle ϕ with respect to
the axial plane. Radiation strikes the first composition in the first microgrooves
and also the bottom walls 2816B of the second microgrooves 2806B, but is blocked by
the narrowness of the third microgrooves 2806C from striking the bottom walls 2816C.
Since a portion of the bottom walls 2816B remain shadowed, the support can be rotated
180° and exposed again to increase the exposure of the bottom walls 2816B as a function
of exposure. The second set of microgrooves 2816B can then be filled with a second
composition. A third composition can be introduced into the third microgrooves 2806C
similarly as in positioning a third composition in the microareas 2516C.
[0304] The area between the lines 2818 forms a single pixel of the support 2800. It is to
be noted that the microareas 2816A, 2816B, and 2816C of the pixel present unequal
areas. In applications where a more nearly equal distribution of microareas is preferred,
the support can be formed so that the number of occurrences of each microarea is varied
to more closely balance the total areas presented by the separate sets of microareas.
For example, a second microarea 2816C can be added to each pixel 2818, thereby doubling
the area of the third set of microareas without in any way altering the shadowing
capability of the support 2800 described above.
[0305] An alternative support which responds to shadowing exposures identically as the support
2800, described above, but which offers the further advantage of providing three interlaid
sets of microareas that present equal areas in each individual occurrence is shown
in Figure 29. The support 2900 is shown by reference to a single pixel 2918, which
contains three separate microgrooves 2906A, 2906B, and 2906C. The only difference
between the microgrooves is the depths of the bottom walls 2916A, 2916B, and 2916C,
which, as shown, are parallel to the axial plane 2914 of the support.
[0306] Shadowing exposure of the support 2900 can be appreciated by reference to the arrows
2912A, 2912B, and 2912C which strike the intersections of the bottom and lateral walls
of the microgrooves 2906A, 2906B, and 2906C, respectively. By reference to the arrows
it can be appreciated that an exposure to radiation at an angle greater than 0, but
less than ϕ, will strike the bottom walls of the microgrooves 2906A while leaving
the bottom walls of the microgrooves 2906B and 2906C entirely in shadow. After a first
composition is introduced into the microgrooves 2906A, a second exposure at an angle
with respect to the axial plane of greater than ϕ and less than a will permit the
bottom walls 2916B of the microgrooves 2906B to be exposed without exposing any portion
of the bottom walls 2916C of the microgrooves 2906C. After a second composition is
introduced into the second microgrooves, a third composition can be introduced into
the third microgrooves by any technique described herein for introducing a third composition.
[0307] It is apparent that the supports 2800 and 2900 can be resolved into separate segments
along glide planes similarly as the support 2300 is resolved along glide planes to
form the support 2400. Further, although described by reference to parallel lateral
walls only, it is apparent that the use of the sets of microcells differing in lateral
extent, in depth, or in any combination of both can be employed in the practice of
this invention. Although described above in terms of three separate sets of microareas,
it is appreciated that any one of the three sets of microareas in the supports 2800
and 2900 can be omitted to allow two compositions to be interlaid substantially as
described.
[0308] Figures 300A, 300B, and 300C illustrate a preferred support 3000 for use in the practice
of this invention which is (1) capable of entirely laterally separating three different
compositions similarly as supports 2800 and 2900, (2) capable of providing equal composition
microareas similarly as support 2900, (3) capable of additionally providing equal
microcell volumes of each composition within each pixel, (4) capable of being radiation
exposed by shadowing techniques over the entire bottom wall area of each of three
separate sets of microcells, and (5) capable of having two microcell sets uniquely
addressed.
[0309] The support 3000 is comprised of substantially parallel first and second major surfaces
3002 and 3004. The support defines a first set of rectangular microcells 3006A, a
second set of rectangular microcells 3006B, and a third set of square microcells 3006C.
The microcells are defined in the support by an array of lateral walls 3008 which
are integrally joined to an underlying portion 3030 of the support.
[0310] The microcells 3006A and 3006B as shown are identical in shape, but not in orientation.
The major axis of each microcell of the first and second set is aligned with or parallel
to the major axis of microcells of the same set and perpendicular to the major axis
of each microcell of the other set. The set of square microcells is positioned so
that an edge of each square is substantially parallel to an adjacent edge of a rectangular
microcell.
[0311] The dashed lines in Figure 30A separate the support into identical pixels 3018. Each
pixel contains one rectangular microcell from each of the first and second sets and
two square microcells of the third set.
[0312] By uniformly exposing the first major surface of the support in the direction indicated
by the arrows 3012A, it is possible to expose selectively the bottom walls of the
first set of microcells 3006A while the lateral walls prevent direct impingement of
the radiation on the bottom walls of the remaining two sets of microcells. If desired
to expose entirely the bottom walls of the first set of microcells, the support can
be rotated 180° and exposed again at the same angle or the support can be exposed
again at the same angle, but with the horizontal direction component of the radiation
as shown in Figure 30A reversed. After a first composition is positioned in the first
set of microcells as a function of exposure, the bottom walls of the second set of
microcells 3006B can be selectively exposed by uniformly exposing the first major
surface of the support in the direction indicated by the arrows 3012B, and in the
opposite horizontal direction at the same acute angle similarly as in exposing the
bottom walls of the first set of microcells. The bottom walls of the first and third
sets of microcells are not exposed. A second composition can then be selectively introduced
into the second set of microcells as a function of exposure. The bottom walls of the
third set of microcells can then be exposed by addressing the first major surface
of the support in a direction perpendicular to its axial plane 3014. A third composition
can then be introduced into the third set of microcells. It is to be noted that no
exclusion property is required to introduce selectively the first and second compositions
into the first and second sets of microcells, but that in using a third, perpendicular
exposure the first and second compositions must exclude the third composition from
the first and second sets of microcells, since the third set of microcells is not
uniquely addressed, but is addressed concurrently with all the other microcells.
[0313] In considering the sequence of exposures disclosed above, certain more general parameters
of the invention will become apparent. In exposing the microcells 3006A, it is apparent
that it is their length and the height of the lateral walls which controls exposure
of the bottom walls. Exposure is entirely independent of the width of the first set
of microcells. It is therefore apparent that the width of the first set of microcells
can be varied at will from very small to very large, depending upon the size of the
microareas and the amount of the first composition desired. The width of the microcells
of the first set in the direction of arrows 3012B can even be increased to a point
where it exceeds the length of these microcells in the direction of arrows 3012A.
The widths can, of course, be variable from one microcell to the next, if desired.
The microcells 3006B of the second set can be of any desired length, but to avoid
being exposed on their bottom walls while the first set of microcells are being addressed,
the width of the second set of microcells must be no greater than half the length
of the first set of microcells. Measured in a direction parallel to the major axes
of the first set of microcells, the microcells of the third set can be up to one half
the length of the microcells of the first set without being addressed on their bottom
walls during exposure of the bottom walls of the microcells of the first set. The
microcells of the third set similarly can be up to half the length of the microcells
of the second set measured in a direction parallel to the major axes of the second
set of microcells. In the preferred form shown the first and second sets of microcells
are of equal length and the microcells of the third set are each substantially one
half the length of both the first and second sets of microcells and thus square; however,
the third set of microcells can be rectangular whether or not the first and second
sets of microcells are of equal length. As suggested above, the rectangular microcells
of the first and second sets are only an example of a general class of microcells
of parallelogram configuration. The microcells of the third set, shown to be square,
can be of either lozenge or parallelogram configuration. Stated another way, adjacent
sides of the microcells need not be perpendicular, but to retain the functional capabilities
disclosed, opposite sides of the microcells should remain parallel. The above discussion
is limited to microcell dimensions that provide all the advantages of the support
3000 as shown. If less than the entire bottom wall of each microcell of the first
and second set is to be addressed by radiation, then the dimensions of the second
and third sets of microcells can be increased above the one half limits indicated.
[0314] A number of variations of the support 3000 and the shadowing technique for introducing
compositions will readily be apparent. For example, instead of giving the support
a third exposure to introduce the third composition, in many instances the third composition
can be introduced without reference to any exposure pattern, simply relying on the
first and second compositions to exclude the third composition from the first and
second sets of microcells, as has been mentioned in connection with previously discussed
supports. The support 3000 can be adapted to the use of two rather than three compositions
merely by omitting any one of the three sets of microcells without otherwise altering
the capabilties or shadowing techniques described above. It is to be noted that the
placement of the individual microcells in relation to each other is entirely a matter
of choice. For example, instead of placing pairs of square microcells side-by-side,
as shown, they can be separated by intervening rectangular microcells. Alternatively,
the square microcells can form columns and/or rows perpendicular to the columns which
are not interrupted by rectangular microcells.
[0315] In looking at the support 3000, it is apparent that it is only exemplary of a large
family of alternative support configurations capable of exhibiting some or all of
the advantages of this invention. For example, if the microcells 3006B are arranged
in an end-to-end pattern in parallel columns (this can be done by laterally displacing
the support along the horizontal dashed line in Figure 30A extending in the same direction
in the axial plane as the arrows 3012A); it is apparent that glide planes exist in
these columns. By laterally displacing the support on one side of a glide plane one-half
the length of the microcells 3006B, the second set of microcells 3006B are transformed
into a serpentine microgroove. The shadowing utility of the support is not affected,
however. In like manner, it can be appreciated that if the square microcells are arranged
in a row or column uninterrupted by rectangular microcells, glide planes exist in
these rows or columns. By translating one portion of the support on one side of a
glide plane with respect to the portion of the support on the other side, the square
microcells are converted into a serpentine microgroove, but the shadowing utility
of the support is not changed. If additional lateral walls are provided aligned with
the glide planes, the serpentine microgrooves, formed by displacing halves of the
first set of rectangular microcells, become rectangular microcells again, with two
rectangular microcells being present where only one existed prior to displacement
along the glide plane. In like manner, the serpentine microgroove formed by displacement
along a glide plane running through the square microcells is replaced by a series
of smaller rectangular microcells which are equal in length to the sides of the squares
initially present, but smaller in width. The variants of the support 3000 that can
be created by displacement along glide planes should be apparent by comparing supports
2300 and 2400 in light of the above description.
[0316] Figure 31 illustrates a preferred support 3100 for use in the practice of this invention
which is (1) capable of entirely separating three different compositions by intervening
lateral walls, similarly as supports 2800, 2900, and 30000 (2) capable of providing
equal microareas in each of three different sets, similarly as supports 2900 and 3000,
(3) capable of providing equal volumes in each of three separate microcell sets, similarly
as support 3000, (4) capable of being uniquely addressed in each of three separate
sets of microcells, a capability not shared by any of the supports previously discussed,
and (5) capable of providing a more symmetrical distribution of three compositions
than the support 3000.
[0317] The support 3100 can be resolved into a plurality of pixels 3118 each containing
three identical microcells 3106 which are diamond-shaped in plan view. Each microcell
within the pixel belongs to a separate set of microcells. A first set of the microcells
is positioned so that the longest dimension of each microcell is aligned with or parallel
to a first axis 3120. A second set of microcells is similarly positioned with respect
to a second axis 3122, which intersects the first axis at a 60° angle. In like manner
a third set of microcells is similarly positioned with respect to a third axis 3124,
which intersects each of the first and second axes at an angle of 60°. If the support
3100 is viewed in section along any one of the first, second, or third axes it would
appear similar to the sectioned support shown in Figure 23B (ignoring wall structures
outside of the section plane).
[0318] If the support 3100 is uniformly exposed at an acute angle with respect to its axial
plane similarly as the support 2300 in Figure 23B or the support 2500 in Figure 5B
in a direction indicated by the arrow 3126, which is parallel to the first axis, the
bottom wall of each microcell of the first set can be exposed to radiation in the
microarea 3128 while the bottom walls of the second and third sets of microcells remain
entirely shadowed. If a second exposure is given at the same acute angle, but in the
opposite direction, as indicated by arrow 3130, the bottom walls of the first set
of microcells are again exposed, this time in only the microareas 3132. Again the
bottom walls of the second and third sets of microcells remain entirely shadowed.
[0319] It can thus be seen that two uniquely addressed microareas can be formed by angled
exposure of the bottom walls of the first set of microcells. After the first angled
exposure, a first composition can, if desired, be introduced as a function of exposure
so that it is selectively positioned in only the microareas.3128. After the second
exposure a second composition can be similarly selectively positioned in only the
microareas 3132. Alternatively, both the first and second exposures can occur before
any composition is introduced, and a single composition can then be introduced so
that it is selectively positioned in the microareas 3128 and 3132 only.
[0320] By analogy it is apparent that if the procedure described above is twice repeated,
the second and third sets of microcells can be similarly uniquely addressed and up
to four additional compositions placed in uniquely addressed interlaid sets of microareas.
Uniform exposure in the direction indicated by arrow 3134, but otherwise identical
to the first uniform exposure uniquely addresses microareas 3136 while leaving the
remainder of the bottom walls in shadow. A reversed exposure in the direction indicated
by arrow 3138 uniquely addresses microareas 3140 while leaving the remainder of the
bottom walls in shadow. Uniform exposure in the direction indicated by arrow 3142
uniquely addresses microareas 3144 while a reversed exposure in the direction indicated
by arrow 3146 uniquely addresses microareas 3148. Thus, six separate uniquely addressed
microareas cnn be produced and six separate compositions can be introduced, each selectively
positioned in a separate microarea. It is generally preferred to position three compositions
in the microcells so that a different composition lies in each set of microareas.
[0321] In looking at the support 3110, it is apparent that it is merely representative of
a family of possible supports having generally similar capabilities. For example,
any one of the axes 3120, 3122, and 3124 shown in the drawings is merely one axis
arbitrarily selected for purposes of illustration from among a family of identical
parallel axes. Further, each family of axes constitutes a family of glide planes.
By relatively displacing portions of the support in the axial plane of the support
along one or up to the entire family of glide planes, essentially functionally identical
supports can be created which have differently shaped microcells, microgrooves, and/or
microareas. To avoid converting microcells into serpentine microgrooves by lateral
displacement additional lateral walls can be located along the glide planes.
[0322] To illustrate the effect of displacement along glide planes, in Figure 32 a support
3200 is shown differing from the support 3100 by lateral displacement of adjacent
portions of the support along glide planes 3220A and 3220B. This displacement converts
one set of microcells having major axes in the glide plane 3220A into serpentine microgrooves
which cross and recross this glide plane. Along the glide plane 3220B an additional
lateral wall 3208 is provided so that the one set of microcells having major axes
in the glide plane are converted by displacement and the lateral walls to triangular
microcells of approximately half the area, but twice the number, of the corresponding
diamond-shaped microcells in support 3100. The additional lateral walls 3208 can be
present along both glide planes 3220A and 3220B or omitted entirely. The first and
second sets of microcells are identical to those of support 3100. The shadowing utility
of the support 3200 is identical to that of the support 3100. Since the microcells
of the first, second, and third sets are identical and form a symmetrical pattern
in support 3100, it is apparent that identical patterns result from displacement along
glide planes aligned with the major axis of any one of the three sets of microcells.
In terms of capabilties and use the support 3200 is substantially the same as support
3100.
[0323] Referring again to support 3100, three axes 3152, 3154, and 3156 are present extending
through or parallel to the minor axes of the three sets of microcells. These three
axes intersect at 60° angles. Using any one of these axes as a glide plane and displacing
the portions of the support lying on either side of the glide plane in the axial plane
of the support, one set of microcells can be converted from diamond-shaped microcells
to triangular microcells of approximately half the area, but twice the number. When
this type of glide plane variation is undertaken, the result is a support that possesses
the capabilities of support 3100, except the capability of uniquely addressing the
triangular set of microareas produced by lateral displacement. The triangular microcells
can still be addressed similarly as the square microcells in the support 3000, however.
[0324] In Figure 33 an additional preferred support 3300 for use in the practice of this
invention is illustrated. The support is provided with first and second sets of diamond-shaped
microcells 3306A and 3306B. The microcells of each of the first and second sets have
major axes lying along parallel axes, while the axes of one set intersect those of
the other set at a 60° angle. A third set of microcells 3306C is rectangular in shape.
The major axes of the rectangular microcells are substantially parallel to each other
and intersect the axes of the first and second microcells at 60° angles. Thus, in
terms of microcell content the support 3300 differs from the support 3100 in substituting
for one set of diamond-shaped microcells a set of rectangular microcells. The first
and second sets of microcells can be uniquely addressed in microareas 3326, 3332,
3336, and 3340, which are identical to corresponding microareas in support 3100. The
rectangular microcells can be uniquely addressed in microareas 3344 and 3348, which
differ in shape from the corresponding uniquely addressed microareas in the support
3100. In terms of relative placement of microcells, it can be seen that the microcells
of each set form a separate column in the support 3300. Adjoining columns are shown
separated by glide planes 3320A, 3320B, and 3320C. It is apparent that any column
can be laterally displaced in the axial plane of the support without in any way affecting
the remaining columns or their function. For certain applications, such as linear
scanning, the columnar arrangement of the microcells in support 3300 is particularly
advantageous. Although the microcell pattern of support 3300 is less symmetrical than
that of support 3100, it otherwise offers all the capabilities of the support 3100.
[0325] Each of the supports 3100, 3200, and 3300 contain microareas within each microcell,
shown as shadowed areas, which cannot be uniquely addressed. These areas are shadowed
when the remaining bottom wall areas of each set of microareas is addressed with radiation
at an acute angle with respect to the axial plane of the support. In some applications
the shadowed areas can be left free of any composition. That is, one or two compositions
can be introduced into a microcell in only the uniquely exposed microareas thereof
without taking any further steps to introduce an additional composition in the remaining
microareas. If the compositions introduced in uniquely addressed microareas are not
capable of lateral spreading, the shadowed bottom wall portions remaining will have
no composition associated therewith. Where compositions capable of lateral spreading
are introduced into the uniquely addressed microareas, they can spread over the entire
bottom wall of each microcell in which they are contained. For example, if a mobile
cyan, magenta, or yellow dye is positioned in one uniquely addressed microarea of
a microcell and a different mobile subtractive primary dye is placed in the remaining
uniquely addressed microarea in the same microcell, one of three different additive
primary colors, depending on the combination of subtractive primaries chosen, can
be produced as the mobile dyes wander over the entire bottom wall of the microcell.
[0326] Where compositions are introduced into the uniquely addressed microareas of the supports
3100, 3200, or 3300 and it is desired to place a composition also in the shadowed
areas remaining, this can be undertaken using techniques similar to those described
above. For example, if the bottom walls of the support are transparent and colorants
are placed in the uniquely addressed areas, it may be undesirable to have transparent
microareas as well as colored microareas. It is possible to selectively position an
additional, high density or opaque composition in all of the shadowed microareas remaining
to eliminate transparent microareas in the support. Since the lateral walls are capable
of interrupting radiation, radiation cannot penetrate these areas of the support.
Where a technique is employed for positioning the additional composition that requires
the initially shadowed microareas to be exposed to radiation, the support can be exposed
in a direction substantially perpendicular to its axial plane and the exclusion properties
of the previously positioned materials employed can be relied upon to position selectively
the additional composition in the initially shadowed microareas. Where a technique
is employed for positioning the additional composition in initially shadowed areas
that allows a material to be selectively positioned in unexposed areas, the additional
composition can be selectively positioned without relying upon any exclusion capability
by any composition previously positioned and without exposing the initially shadowed
areas to radiation.
[0327] In various embodiments described above it is suggested to expose the support substantially
perpendicularly to its axial plane where shadowing is not desired. In some instances
this can be disadvantageous, since the radiation source is fixed at a particular acute
angle for shadowing exposures and it may be inconvenient to provide a second radiation
source or relocate the radiation source used for shadowing. An alternative is possible
when the lateral walls are capable of interrupting radiation, but are not entirely
opaque. For example, if transparent lateral walls are dyed to the extent necessary
to provide shadowing, they may still be penetrable by radiation of increased intensity.
In such instances it is contemplated to give the support a first uniform exposure
at an acute angle, choosing a level of radiation intensity which permits the lateral
walls to interrupt the radiation and provide shadowing as required. Thereafter, when
exposure of the shadowed areas is required, the same radiation source at the same
acute angle can be increased in intensity and used to reexpose the support. This time
sufficient radiation penetrates the lateral walls to allow exposure of the initially
shadowed areas. Instead of altering the intensity of radiation between exposures,
a change in the wavelength or even type of radiation can be relied upon to allow shadowing
in one instance, but not another. Transparent lateral walls containing an ultraviolet
absorber can interrupt ultraviolet radiation while permitting penetration of visible
light. Similarly lateral walls which are dyed to appear visibly opaque may nevertheless
absorb little ultraviolet radiation.
[0328] In the preferred embodiments of the invention, described in connection with supports
2800, 2900, 3000, 3100, 3200, and 3300, one set of micro- areas can be entirely separated
from all other sets of microareas by lateral walls. However, because of shadowing
by the lateral walls, the entire bottom wall surface between these boundary forming
lateral walls cannot be entirely exposed at one time. In some geometrical forms of
the support, such as support 3000, the entire bottom wall surface between boundary
forming lateral walls (e.g., the entire bottom wall of a microcell) can be addressed
by a combination of two exposures if the support is rotated 180° or the second radiation
source is changed in direction. In some instances, however, this still leaves bottom
wall surfaces shadowed that are not intended to be differentiated from exposed microareas
within the same lateral wall boundary. For example, the shadowed areas shown in the
supports 3100, 3200, and 3300 can represent a significant inconvenience and limitation
where it is desired to locate three compositions, each in a different set of microcells,
so that each composition entirely covers the bottom walls of its microcell set.
[0329] In those instances where it is desired for an entire bottom wall surface bounded
by lateral walls, such as the entire bottom wall surface of a microcell, to form a
single microarea, but exposure at an acute angle casts a shadow over at least a portion
of the microarea, it is specifically contemplated to modify the support to either
spread the radiation itself or to spread whatever modifying effect the radiation produces
over the entire microarea. The specific approach for accomplishing this objective
can be varied, depending upon the specific application the support is intended to
serve.
[0330] In another form, a removable cover, preferably bearing a semitransparent reflective
coating, can be laid over the first major surface of the support to aid in reflecting,
if desired. Exposure must, of course, occur through the cover. The lateral walls can
be relied upon to prevent radiation from scattering beyond the intended boundary of
the microarea.
[0331] Where the support or at least the bottom wall portion of the support is a photoconductor,
as described above, a conductive layer which is at least partially transparent can
be placed selectively on the the bottom wall surfaces. Without the conductive layer
present only the bottom wall portions actually exposed to radiation are increased
in conductivity, but with the conductive layer present, if any portion of a lateral
wall bounded bottom wall is struck by radiation to which the photoconductor is responsive,
the effect in terms of static charge retention is as though the entire bottom wall
had been radiation struck.
[0332] Another approach applicable to supports generally (i.e., not limited to reflective
or photoconductive supports, but also fully applicable to transparent and insulative
or conductive supports) is to locate a fluor on the bottom wall surfaces. Exposure
in one microarea stimulates emission of radiation by the fluor and causes the entire
bottom wall portion in the bounded area to be exposed to either direct or stimulated
radiation. Again, the lateral walls can be relied upon to prevent radiation scattering
beyond the intended boundary of the microarea.
[0333] In a very simple form of the invention the bottom walls of the supports can themselves
be relied upon to distribute radiation over a bottom wall surface. It is generally
recognized that even a polished transparent support will reflect some radiation. For
applications requiring very little radiation, the inherent light scattering property
of unmodified bottom walls can be sufficient to distribute a useful amount of radiation
over the entire bottom wall surface. Scattering of radiation by the bottom walls can
be significantly increased by roughening the bottom walls of the support.
[0334] In the foregoing exemplary embodiments the lateral walls of the microcells have been
shown to be perpendicular to the bottom walls. However, where the lateral walls are
reflective and particularly where the microcell walls have been mirrored, as discussed
above, this can result in reflection of radiation into areas of the microcells intended
to be shadowed. It is contemplated that unwanted reflection into microcell areas intended
to be shadowed can be avoided by providing lateral walls which slope with respect
to the bottom walls ofthe microcells.
[0335] Such an arrangement is shown in Figure 34. The support 3400 is shown provided with
lateral walls 3402 which are in section of a keystone or wedge shape. The lateral
walls form obtuse angles with the bottom walls. The slope of the lateral walls is
preferably chosen so that exposing radiation strikes the lateral walls at less than
a 90° angle and is reflected upwardly away from the bottom wall and out of the microcell.
If the slope of the lateral wall is increased so that incident radiation strikes the
lateral wall at greater than a 90° angle measure from the lateral wall surface, the
opposite effect, namely reflection down into the microcell, will occur.
[0336] Although the invention has been specifically described by reference to preferred
nonplanar supports, it is appreciated that still other nonplanar support structures
can be employed, such as those described by Land, Gerber, and Walworth, cited above.
Example 1
[0337] Sample reaction microcells were prepared in the following manner:
A. A pattern of hexagons 20 microns in width and approximately 10 microns high was
formed on a copper plate by etching. Using the etched plate having hexagon projections,
dichloromethane and ethanol (80:20 volume ratio) solvent containing 10 grams per 100
ml of Genacryl OrangeR, a yellow azo dye, was placed in contact with a cellulose acetate
photographic film support for six seconds. Hexagonal depressions were embossed in
the softened support, forming reaction microcells. The yellow dye was absorbed in
the cellulose acetate film support areas laterally surrounding, but not beneath, the
reaction microcells, giving a blue density.
B. Using an alternative technique, the desired hexagon pattern for the reaction microcells
was developed in a fine grain silver bromoiodide emulsion coated on a cellulose acetate
photographic film support. The pattern was spin overcoated first with a very thin
layer of a negative photoresist comprised of a cyclized polyisoprene solubilized in
2-ethoxyethanol and sensitized with diazobenzili- dene-4-methylcyclohexanone. The
pattern was then spin overcoated with an approximately 10 micron layer of a positive
photoresist comprised of a cresylformaldehyde resin esterified with 6-diazo-5,6-dihydro-5-oxo-l-naphthalene
sulfonyl chloride solubilized in 2-ethoxyacetate together with a copolymer of ethyl
acrylate and methacrylic acid, the resist being stabilized with glacial acetic acid.
The thin layer of negative photoresist provided a barrier between the incompatible
gelatin and positive photoresist layers. To prevent nitrogen bubble formation in the
negative photoresist, an overall exposure was given before the positive photoresist
layer was added. Exposure through the film pattern and development produced reaction
microcells in the positive photoresist.
C. Using still another method, an aqueous mixture of 12 1/2 by weight percent bone
gelatin plus 12 percent by weight of a 2 by weight percent aqueous solution of ammonium
dichromate (to which was added 1 1/2 ml conc. NH40H/100 ml of the aqueous mixture) was coated on a cellulose acetate photographic film
support with a 200 micron doctor coating blade. Exposure was made with a positive
hexagon pattern using a collimated ultraviolet arc source. Development was for 30
minutes with a hot (41°C) water spray. Reaction microcells with sharp, well defined
walls were obtained.
[0338] By each of the above techniques, reaction microcells were formed ranging from 10
to 20 micron in average diameter and from 7 to 10 microns in depth with 2 micron lateral
walls separating adjacent microcells.
Example 2
[0339] A fast, coarse grain gelatino-silver bromoiodide emulsion was doctor-coated onto
a sample of an embossed film support having reaction microcells prepared according
to Example 1A and dried at room temperature. A comparison coating sample was made
with the same blade on an unembossed film support. Identical test exposures of the
embossed and unembossed elements were processed for 3 minutes in a surface black-and-white
developer, as set forth in Table I.
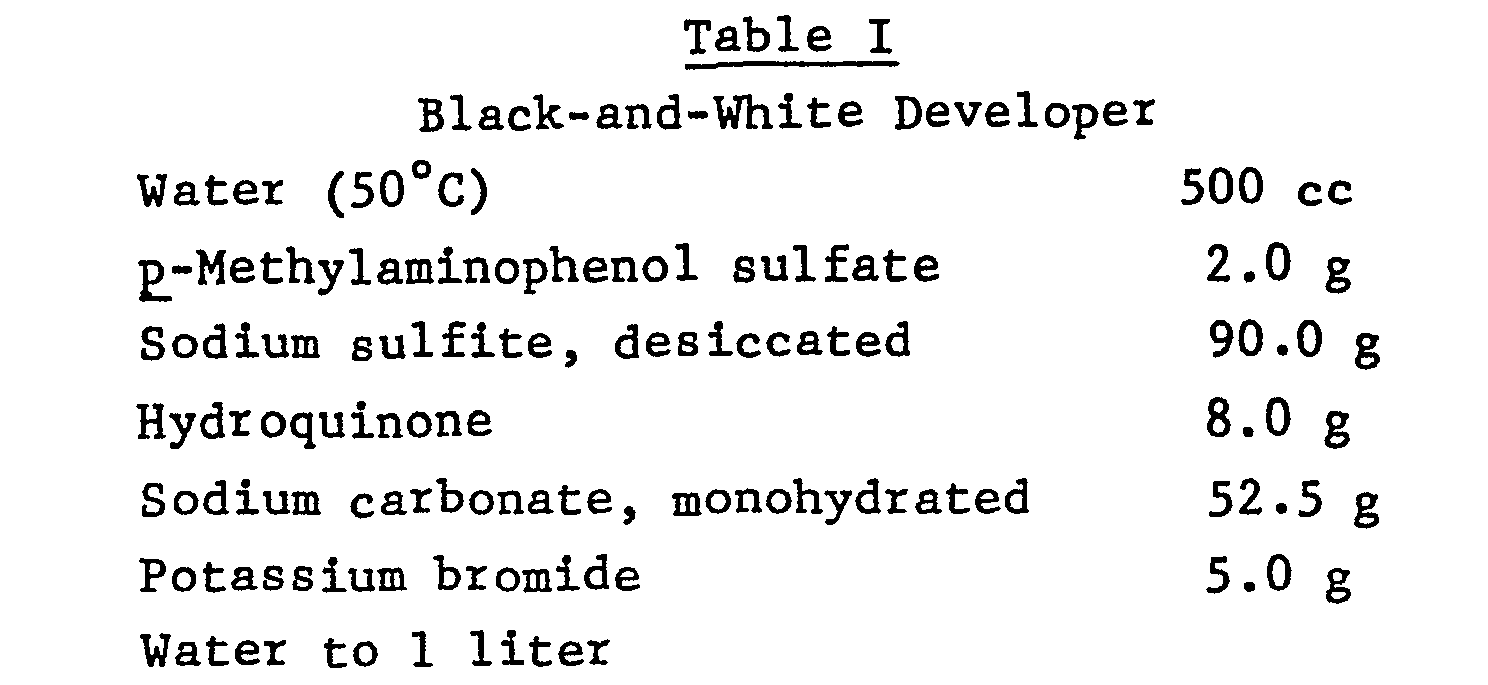
[0340] In a comparison of 7X enlarged prints made from the embossed and unembossed elements,
the image made from the embossed element was visibly sharper.
Example 3
[0341] A coarse grain gelatino-silver bromoiodide emulsion was doctor-coated onto a sample
of an embossed film support having reaction microcells prepared according to Example
lA. The silver bromoiodide emulsion was then overcoated with an emulsion of fine grain,
internally fogged converted halide silver bromide grains. Exposure and development
of the coarse grains released iodide which diffused to the fine grain emulsion, disrupting
the grains and making them imagewise developable in the surface developer.
Example 4
[0342] A coarse grain silver bromoiodide emulsion was doctor-coated onto a sample of an
embossed film support having reaction microcells prepared according to Example 1A
and dried at room temperature. After exposure the sample was developed in a lith-
type developer of the composition set forth in Table II in which parts A and
B were mixed in a volume ratio of 1:1 just prior to use. Extreme contrast was obtained
without loss of sharpness.
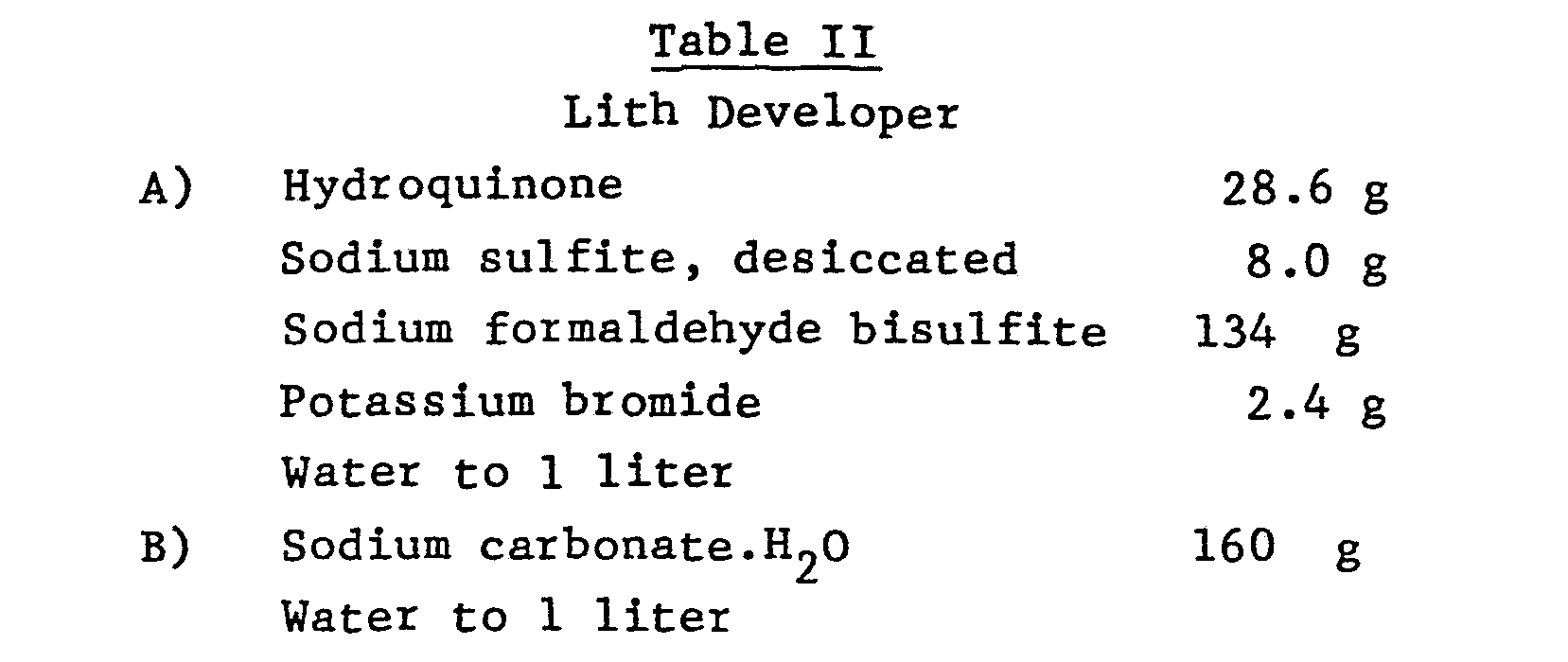
Example 5
[0343] A high speed, coarse grain gelatino-silver bromoiodide emulsion was doctor-coated
onto a sample of the film support having reaction microcells prepared according to
Example 1B. A first sample of the element was imagewise exposed and was then developed
in a black-and-white developer, as set forth in Table III.
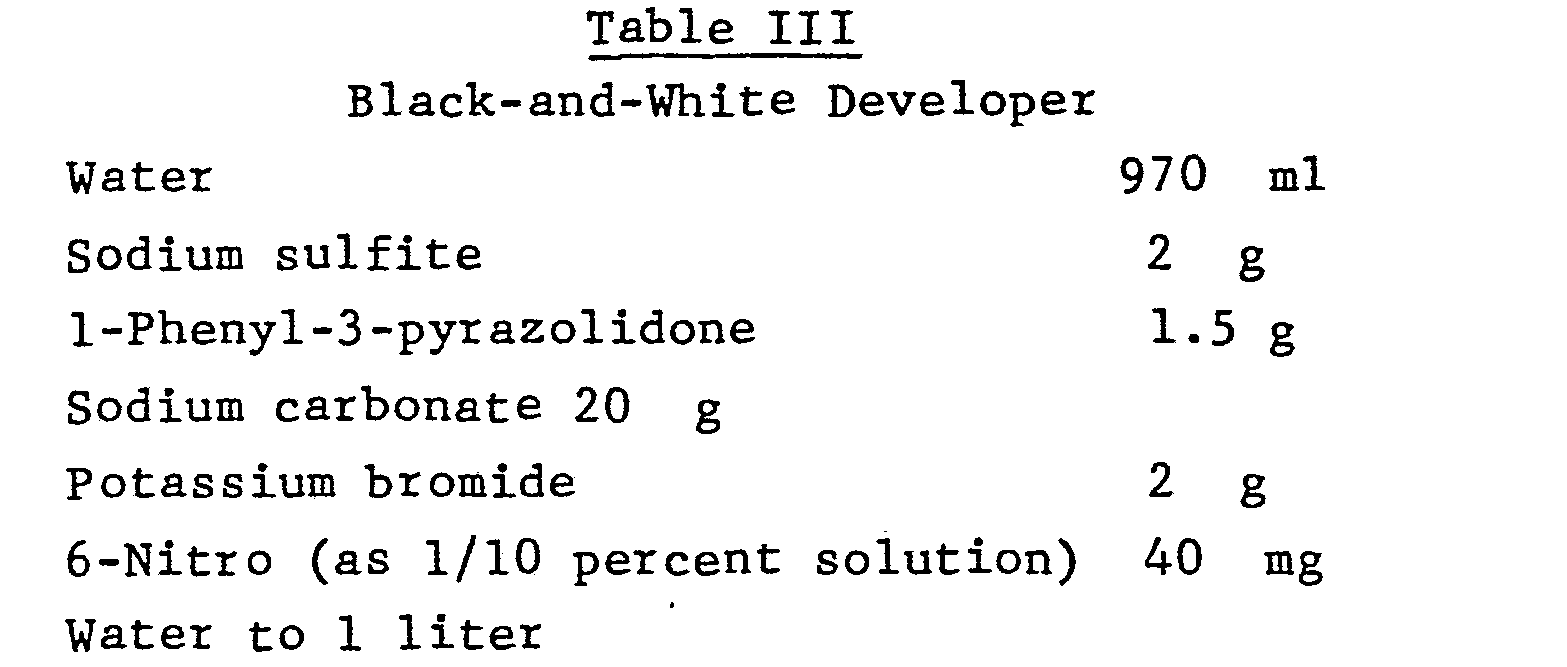
[0344] The first sample was washed in water and immersed in a fix bath of the composition
set forth in Table IV.
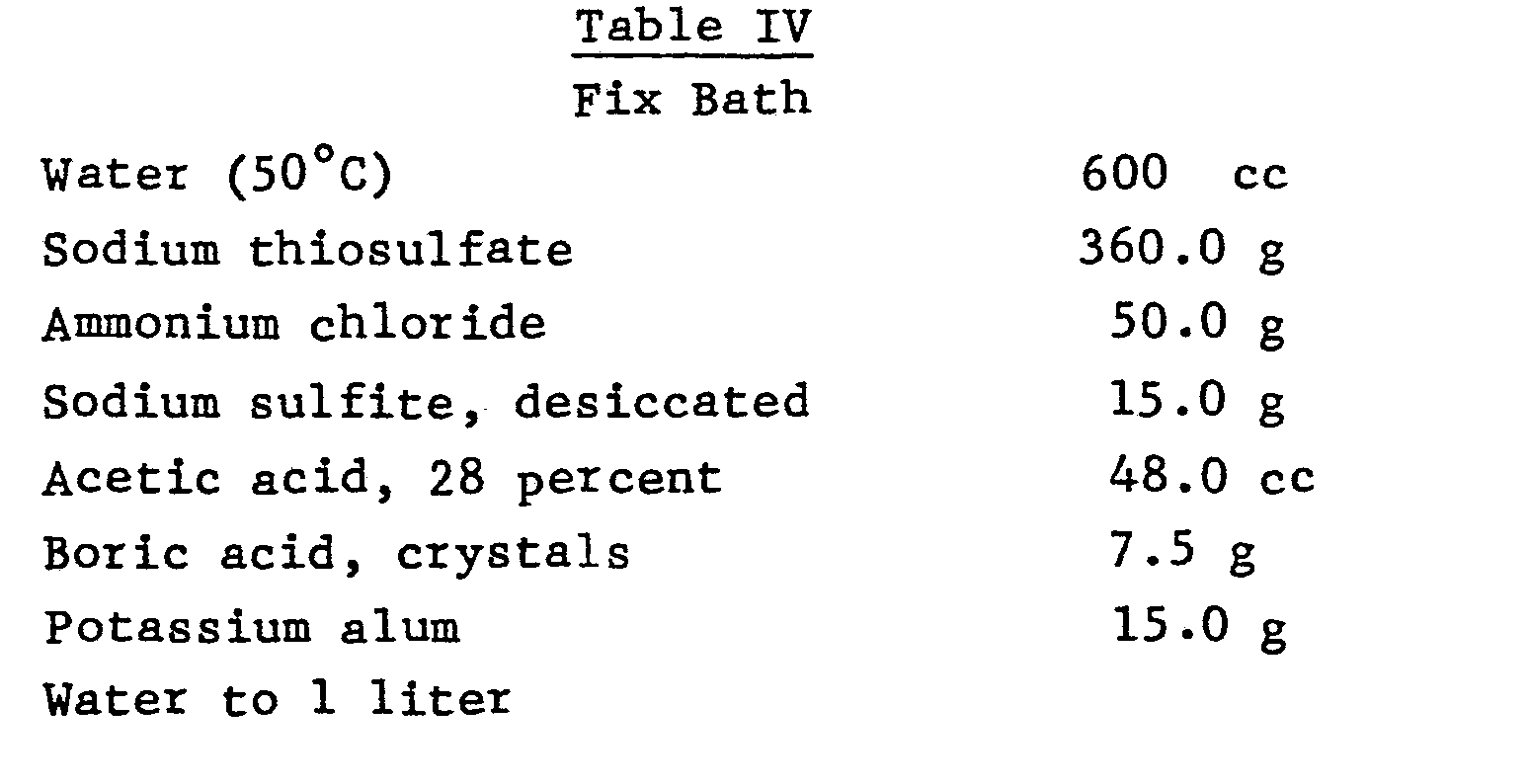
[0345] The first sample was washed in water and allowed to dry. The sample was then immersed
in a rehalogenizing bath of the composition set forth in Table V.
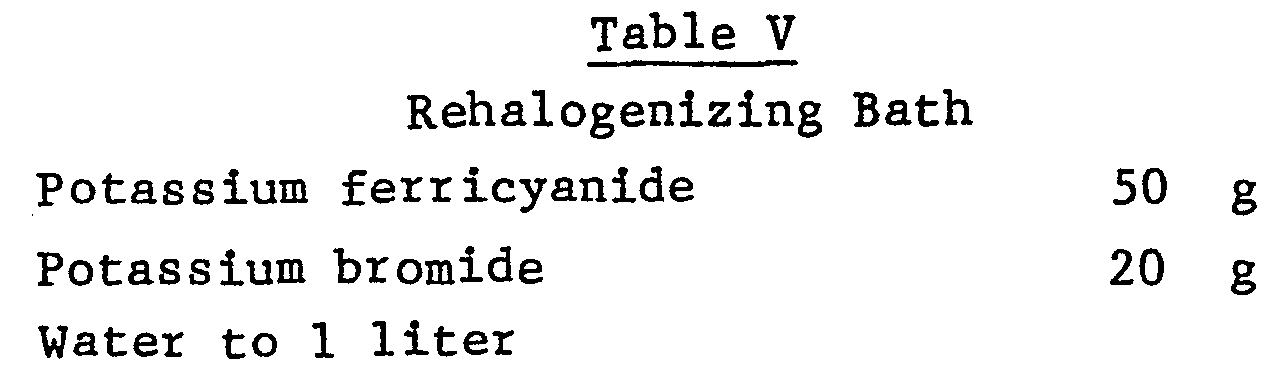
[0346] The first sample was washed in water and was then developed in the color developer
set forth in Table VI.
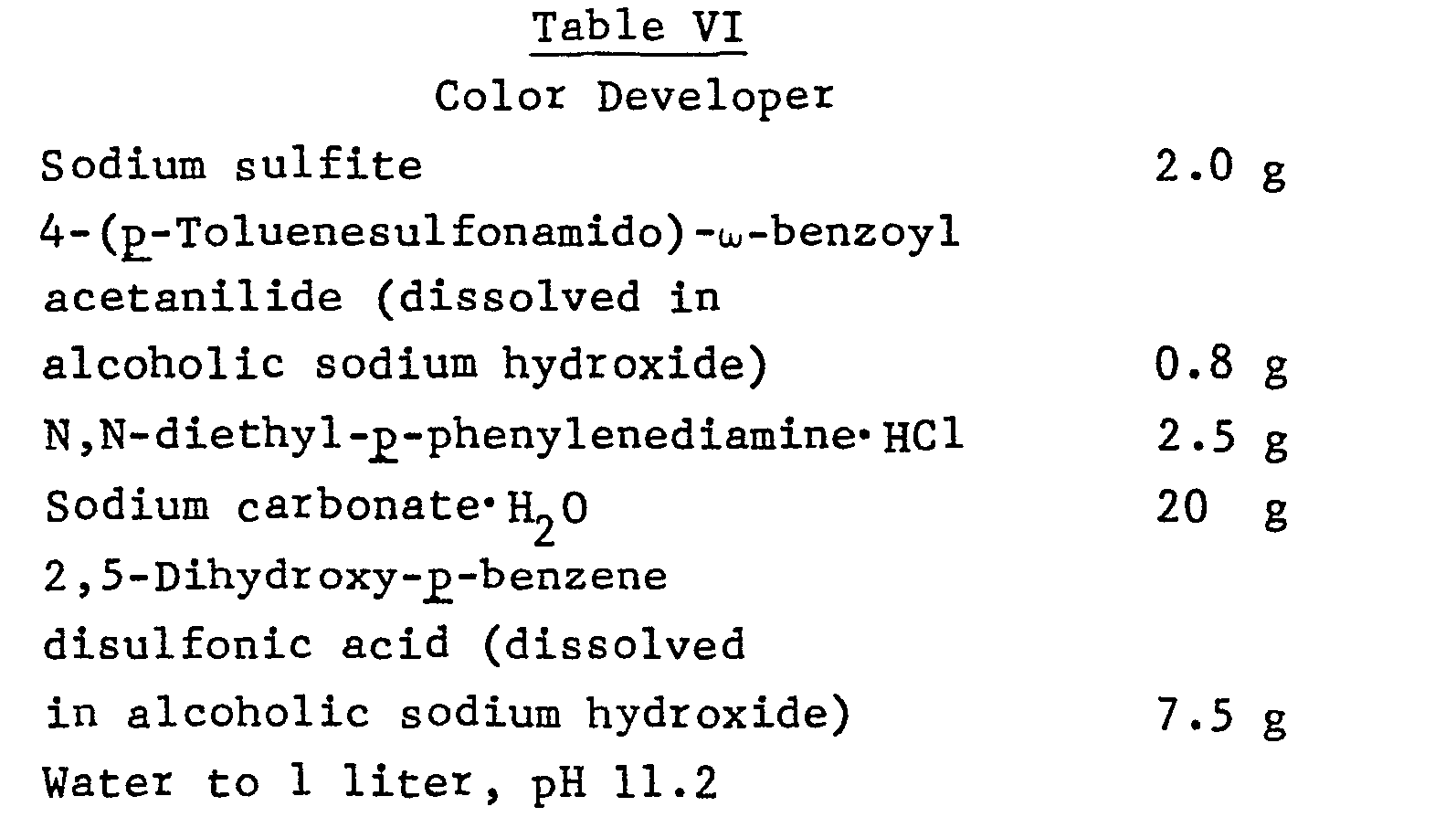
[0347] The first sample was washed in water and immersed in a bleach bath of the composition
set forth in Table VII.
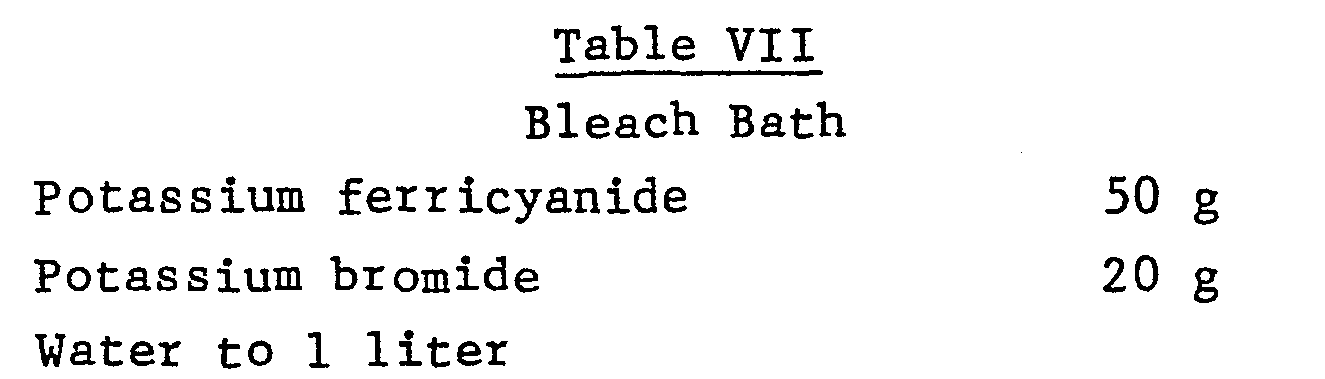
[0348] The first sample was immersed in a fix bath of the composition set forth above in
Table IV after which it was washed in water.
[0349] A second sample was similarly exposed and processed through the step of immersion
in the fix bath (first occurrence). The images obtained using the first and second
samples were enlarged 10X onto a light-sensitive commercial black-and-white photographic
paper. Graininess, due to the silver grain, was very apparent in the enlargement prepared
from the second sample but was not visible in the enlargement prepared from the first
sample. In the first sample, no grain was evident within the individual microcells.
Rather, a substantially uniform intramicrocell dye density was observed.
Example 6
[0350] Coatings were made as follows: A magenta coupler, 1-(2,4-dimethyl-6-chlorophenyl)-3-[(3-m-pentadecylphenoxy)butyramide]-5-pyrazolone,
was dispersed in tricresyl phosphate at a weight ratio of 1:1/2. This dispersion was
mixed with a fast gelatino-silver bromoiodide emulsion and doctor-coated onto a sample
of a film support having a pattern of 20 micron average diameter reaction microcells
prepared as discussed in Example lA. For comparison, a coating with the same mixture,
but without reaction microcells was made. Identical line test exposures on each coating
were processed in the following manner:
[0351] The coating was developed for 3 minutes in a black-and-white developer of the composition
set forth in Table VIII.

[0352] The coating was immersed in a fix bath of the composition set forth in Table IX.
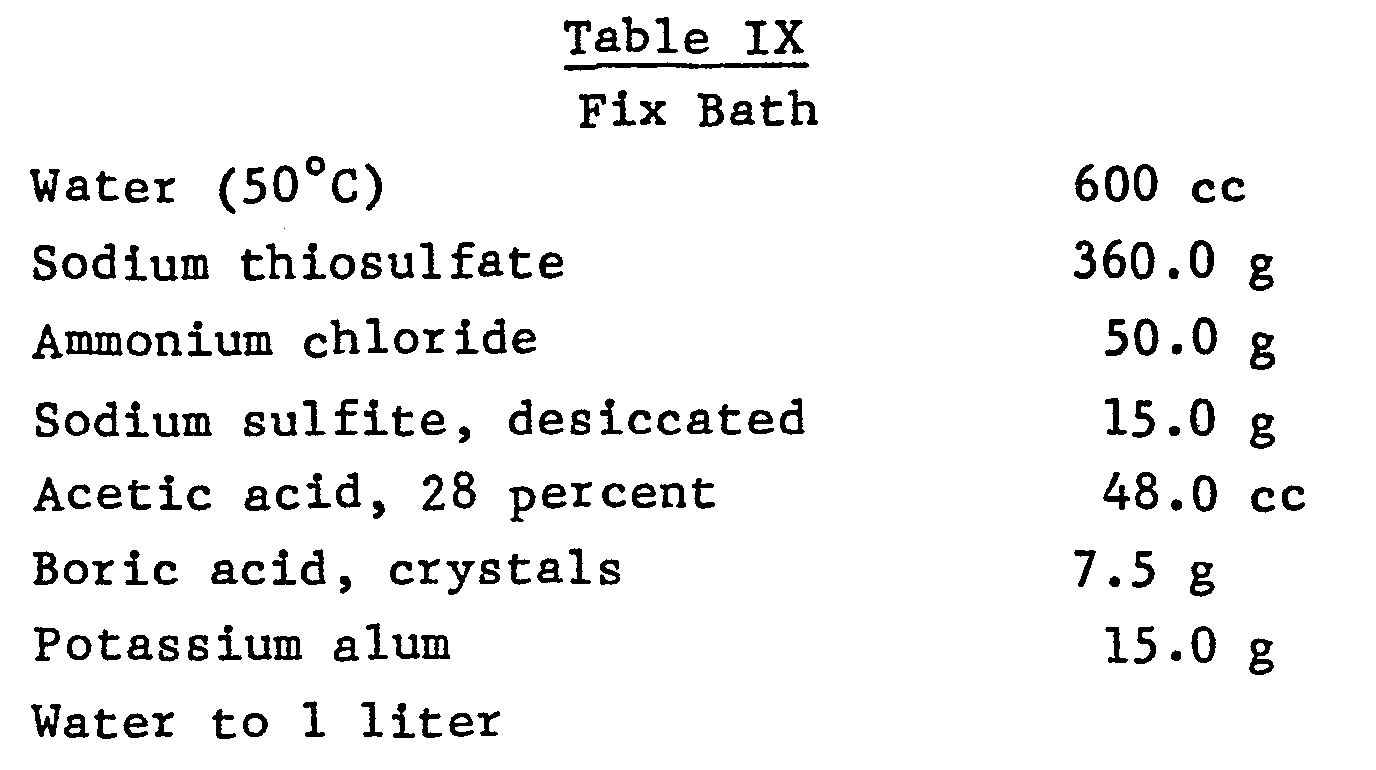
[0353] The coating was washed in water. It was then reactivated 15 minutes in 25 weight
percent aqueous potassium bromide and was washed for 10 minutes in running water,
followed by development for 3 minutes in a peroxide oxidizing agent containing color
developer of the composition set forth in Table X.
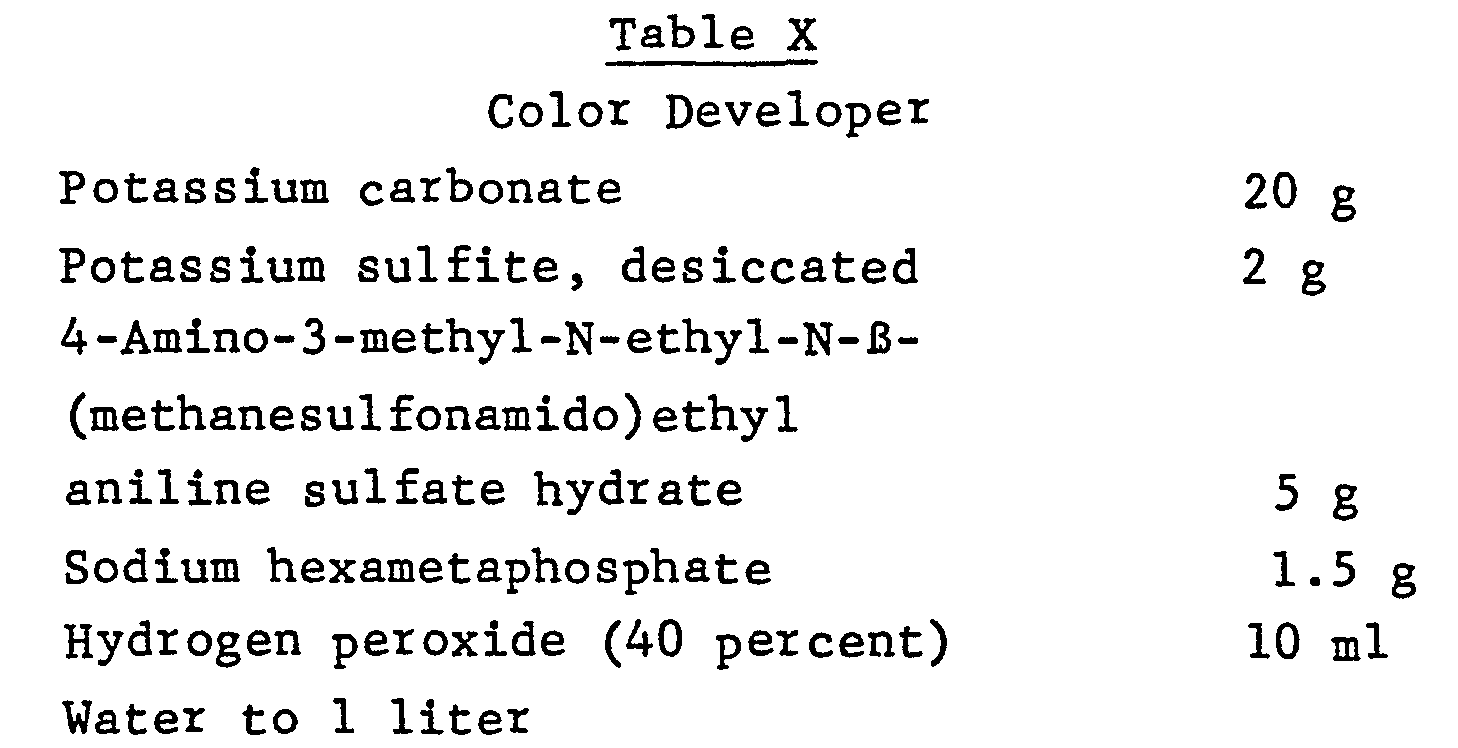
[0354] The coating was then washed in water.
[0355] Large amounts of dye were formed in both coatings. The comparison coating without
the reaction microcells showed gross spreading of dye and image degradation. The reaction
microcell coating spread was confined by the reaction microcells and showed no signs
of intercell spreading.
Example 7
[0356] A cellulose acetate photographic film support was embossed with a pattern of reaction
microcells approximately 20 microns in average diameter and 8 microns deep prepared
according to Example lA. A fast gelatino-silver bromoiodide emulsion was doctor-coated
onto the film support having reaction microcells and dried at room temperature. An
image of a line object was developed for two minutes in a black-and-white developer
of the composition set forth in Table XI.
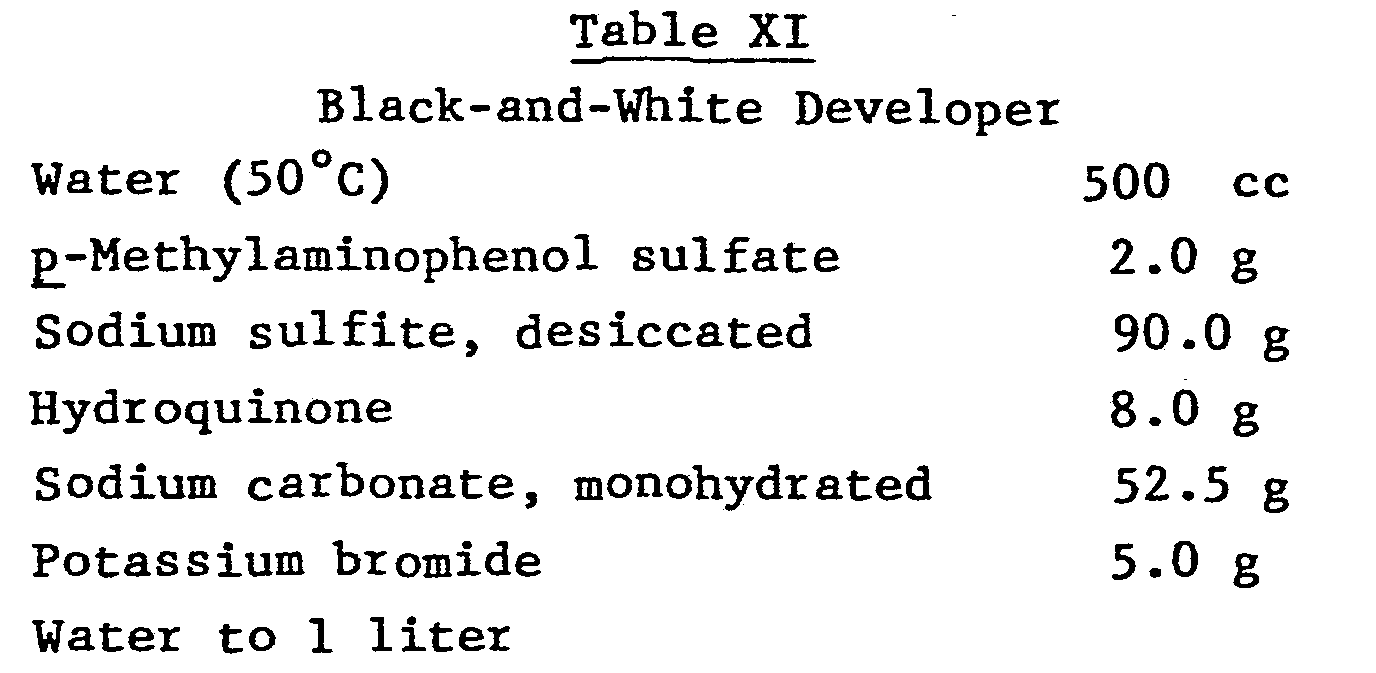
[0357] The sample was immersed in a fix bath of the composition set forth in Table XII.
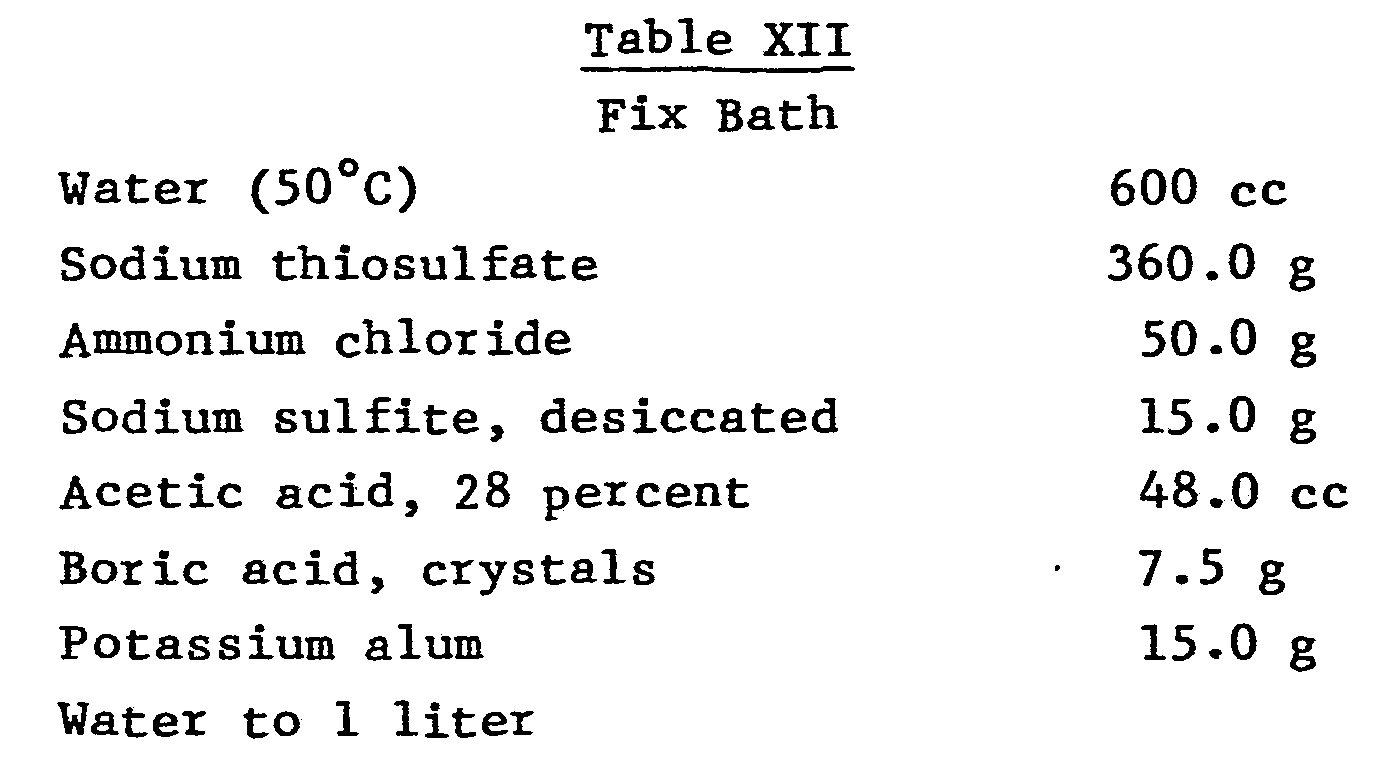
[0358] The sample was washed in water and dried. It was overcoated with a dispersion of
2-[a-(2,4-di-tert-amylphenoxy)butyramido]-4,6-dichloro-5-methylphenol, hardened for
two minutes in formalin hardener and was then washed in water. The sample was activated
for 15 minutes in 25 percent by weight aqueous solution of potassium bromide and was
washed for 10 minutes in water, followed by development for 5 minutes in a peroxide
color developer of the composition set forth in Table XIII.
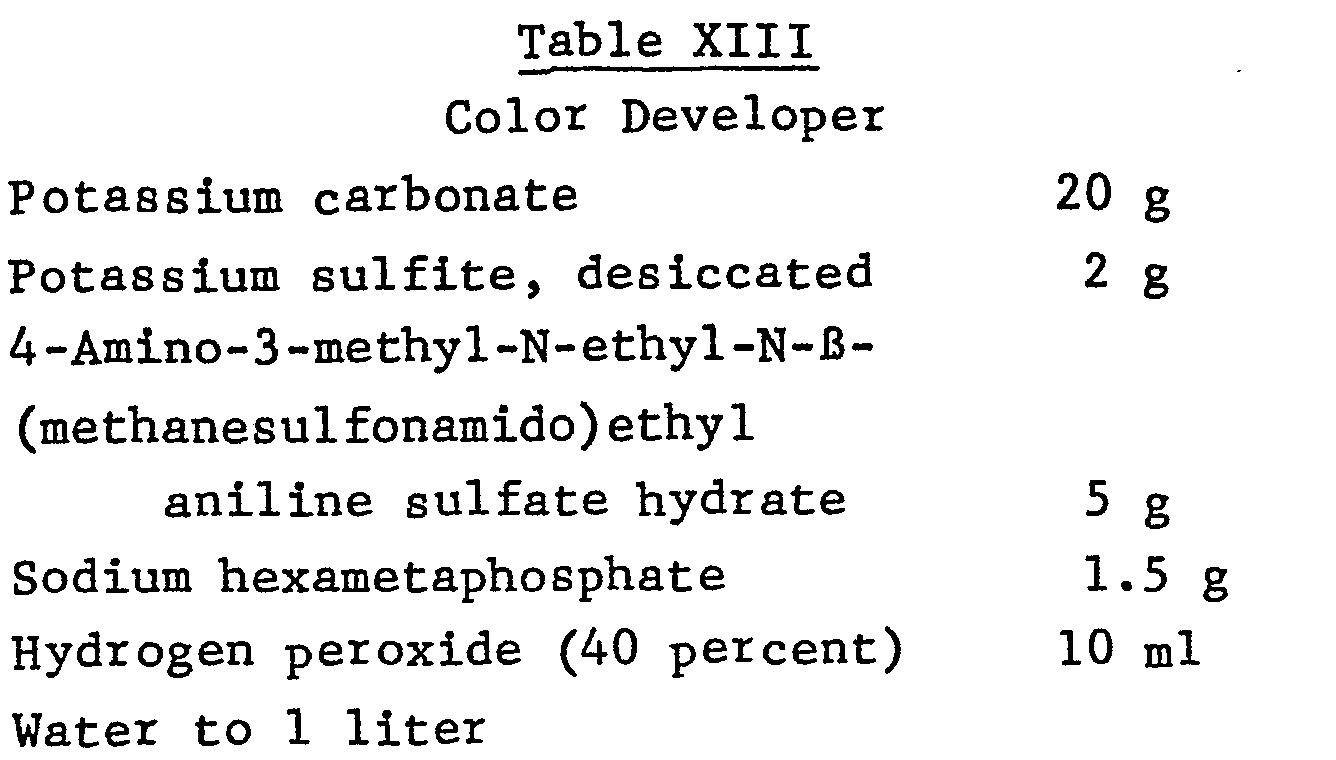
[0359] Within the exposed microcells a random pattern of silver specks were formed by development
in the black-and-white developer. Subsequent development in the color developer produced
a cyan dye within areas subtended by the microcells containing the silver specks.
The cyan dye was uniformly distributed within these microcell subtended areas and
produced greater optical density than the silver specks alone. The result was to convert
a random distribution of silver specks within the microcells into a uniform dye pattern.
Example 8
[0360] Two donor elements for image transfer were provided, each having an imagewise distribution
of an alkali diffusible cyan coupler, 2,6-dibromo-1,5-naphthalenediol on a film support.
[0361] A receiving element was prepared by coating a cellulose acetate film support embossed
according to Example 1, paragraph A, so that the microcells in the support were filled
with gelatin. To provide a control-receiving element, a second, planar cellulose acetate
film support was coated with the same gelatin to provide a continuous planar coating
having a thickness corresponding to that of the gelatin in the microcells.
[0362] Each of the receiving elements was immersed in the color developer of Table XIV and
then laminated to one of the donor sheets.
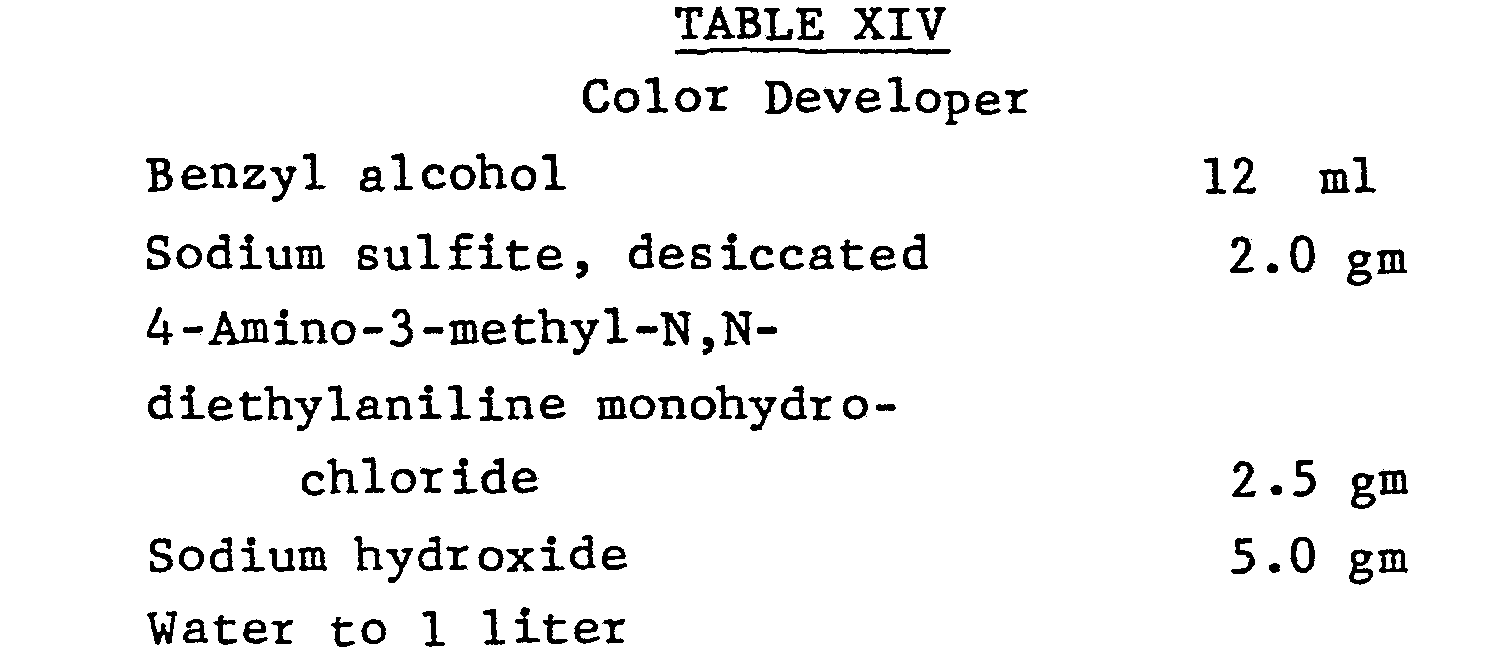
[0363] After diffusion of the cyan coupler to the receiving elements, the receiving and
donor elements were peeled apart. The receivers were then treated with a saturated
aqueous solution of potassium periodate to form the cyan dye.
[0364] The cyan dye image formed in the receiving element having the microcells was perceptably
sharper than the one formed in the control receiving element with the planar support
and continuous gelatin layer.
Example 9
[0365]
A. Nine grams of a finely divided immobile particulate green pigment, Monolite Green
GN, was mixed with 4.5 grams of a copolymer of tert-butylstyrene and lithium methacrylate
along with 85.5 grams of Solvesso 1001 (an isoparaffinic hydrocarbon liquid having a boiling point in the range of from
145 to 185°C, sold commercially by Exxon). The concentrate was ball-milled for two
weeks at room temperature.
B. Four grams of a finely divided immobile particulate red pigment, Red Violet MR"
(Hoechst), was mixed with 4.0 grams of a copolymer of tert- butylstyrene, lauryl methacrylate,
lithium methacrylate, and methacrylic acid in the weight ratio of 60:36:3.6:0.4 (hereinafter
designated TBS) and 36.0 grams of Solvesso 100®. The concentrate was ball-milled for
two weeks at room temperature.
C. Ten grams of a finely divided immobile particulate blue pigment, Monolite Blue.
(ICI), was mixed with 14.0 grams of TBS and 126.0 grams of Solvesso 100®. The concentrate
was ball-milled for two weeks at room temperature.
D. Four and one-half grams of a mobile magenta dye-forming coupler, 1-(2-benzothiazolyl)-3-amino-5-pyrazolone,
was mixed with 4.5 grams of TBS and 40.5 grams of Solvesso 100*. The concentrate was ball-milled for two weeks at room temperature.
E. The procedure of Paragraph D was repeated, except a mobile cyan dye-forming coupler,
2,6-di- bromo-1,5-naphthalenediol, was substituted for the magenta dye-forming coupler.
F. A mobile yellow dye-forming coupler, α-(4-carboxyphenoxy)-α-pivalyl-2,4- dichloro-
acetanilide, in the amount of 3.14 grams was mixed with 3.14 grams of TBS and 28.3
grams of Solvesso 100®. The concentrate was ball-milled for two weeks at room temperature.
G. The green pigment concentrate of Paragraph A and the magenta dye-forming coupler
concentrate of Paragraph D were mixed in equal weights of 3.85 grams each with 4.55
grams of a 10 percent by weight solution of a copolymer of ethyl acrylate, ethyl methacrylate,
lauryl methacrylate, and lithium sulfoethyl methylacrylate in Solvesso 100". To this
mixture was added Isopar G® (an isoparaffinic hydrocarbon liquid having a boiling
point in the range of 145 to 185°C commercially available from Exxon) at the rate
of 6 ml per minute for the first 50 ml and then at the rate of 15 ml per minute until
the volume of the developer reached 500 ml.
H. The procedure of Paragraph G was repeated, except the red pigment concentrate of
Paragraph B was substituted for the green pigment concentrate of Paragraph A and the
cyan dye-forming coupler concentrate of Paragraph E was substituted for the magenta
dye-forming coupler concentrate of Paragraph D.
I. The procedure of Paragraph G was repeated, except the blue pigment concentrate
of Paragraph C was substituted for the green pigment concentrate of Paragraph A and
the yellow dye-forming coupler concentrate of Paragraph F was substituted for the
magenta dye-forming coupler concentrate of Paragraph D.
J. A conventional planar photoconductive element consisting of a transparent 102 micron
thick poly(ethylene terephthalate) film base coated with a transparent 0.2 micron
cuprous iodide electrically conductive layer which was in turn overcoated with an
8 micron organic photoconductive layer was employed as a starting material. The photoconductive
element is commercially available as a recording film under the trademark Kodak Ektavolt
SO-101. The recording film and its characteristics are generally described in A Mini-Textbook--KODAK
Products for Electrophotography, Kodak Publication No. G-95, Standard Book Number 0-87985-233-X, Eastman Kodak Company,
1979. The conductive layer and film base extend laterally beyond the photoconductive
layer along one edge to allow convenient electrical contact with the conductive layer.
An array of hexagonal projections 20 microns in width and approximately 7 microns
high was formed on a copper plate by etching in generally the same manner described
in the Whitmore patent application cited above. An embossing solvent was placed on
the plate between one edge of the array of projections and a strip of pressure-sensitive
tape employed to restrain migration of the solvent away from the projections. A sheet
of the recording film was placed on the plate with the photoconductive layer adjacent
the projections, and the resulting sandwich was advanced beneath a roller with the
edge bearing the embossing solvent passing beneath the roller first. The pressure
exerted by the roller and the softening action of the embossing solvent being spread
laterally at the roller nip resulted in a hexagonal array of microcells being formed
on the photoconductive layer having lateral and bottom walls corresponding to the
walls of the hexagonal projections. The embossing solvent was a roughly equal volume
mixture of methanol and dichloromethane containing 0.51 parts by volume per 100 parts
of solvent Sundan Black B (Color Index No. 26150). As a result, the lateral walls
of the microcells were dyed black, since the dye entered the photoconductive layer
along with the embossing solvent. The bottom walls of the microcells remained transparent,
however. '
K. The embossed photoconductive portion of the support was given a charge of +500
volts by being passed through a corona discharge. The conductive electrode was attached
to ground. Except as stated the support was not intentionally exposed to light to
which the photoconductive portion was responsive. The positively charged support was
scanned with a laser having a wavelength of 482 nm. In one area of the support evry
third row of microcells was scanned. In another area all of the microcells were scanned.
For selected row scanning an indexing laser was employed in combination with the scanning
laser. The indexing laser was of a red wavelength to which the photoconductive portion
was not responsive. The indexing laser was employed in combination with a photosensor
to detect the position of the lateral walls of the microcells. Thus, three interruptions
of the indexing laser beam detected by the photosensor in advancing the support provided
a positive indication that the support had been advanced three rows of microcells.
The dyed lateral walls of the microcells facilitated indexing as well as obviating
light scatter to adjacent microcells.
After the laser scan was completed the support was electrophotographically developed
using the electrophotographic developer of Paragraph G using a development time of
10 seconds and a general development technique and apparatus of the type described
in Beyer et al U.S. Patent 3,407,786. A development electrode biased to +200 volts
was employed.
The procedure was twice repeated using the electrophotographic developers of Paragraphs
H and I. The result was an element having in one area interlaid rows of microcells
containing the electroscopic imaging compositions of Paragraphs G, H and I. Under
microscopic examination there was no evidence of any overlap of the imaging-compositions.
In three separate areas all of the microcells were filled with one of the three electroscopic
imaging compositions.
L. The element produced by Paragraph K was employed to form a multicolor screened
positive using additive primary pigments and a transferred multicolor negative using
subtractive primary dyes formed by the mobile couplers.
[0366] The filled microcells were overcoated with a mixed silver sulfide and silver iodide
silver precipitating agent dispersed in 2 percent by weight gelatin using a 50 micron
coating doctor blade spacing. A commercially available black-and-white photographic
paper having a panchromatically sensitized gelatino-silver chlorobromide emulsion
layer was attached along an edge to the support with the emulsion layer of the photographic
paper facing the microcell containing surface of the support. The photographic paper
was imagewise exposed through the support (and therefore through the filters formed
by the pigments in the microcells) with the elements in face-to-face contact. After
exposure, the elements were separated, but not detached, and immersed for 3 seconds
in the color developer of Table XV.

Water to 1 liter
[0367] Thereafter, the elements were restored to face-to-face contact for 1 minute to permit
development of the imagewise exposed silver halide and image transfer to occur. The
elements were then separated, and the silver image was bleached from the photographic
paper. A three-color negative image was formed by subtractive primary dyes in the
photographic paper while a three-color screened positive image was formed by the additive
primary filters and the transferred silver image on the support.
Example 10 Formation of Transferred Multicolor Positive
[0368] Example 9 was repeated, but with a silver halide emulsion layer coated over the filled
microcells and the silver nucleating agent layer being coated on a separate planar
film support. The emulsion layer was a high-speed panchromatically sensitized gelatino-silver
halide emulsion layer coated with a 150-micron coating doctor blade spacing. The color
developer was of the composition set forth in Table XVI.

[0369] Both elements were immersed in the color developer for 5 seconds and thereafter held
in face-to-face contact for 2 minutes. A screened three-color negative was obtained
on the support and a transferred positive silver and multicolor positive dye image
was obtained on the planar support.
[0370] Both elements were immersed in the color developer for 5 seconds and thereafter held
in face-to-face contact for 2 minutes. A screened three-color negative was obtained
on the microcellular support and a transferred positive silver and multicolor positive
dye image was obtained on the planar support.
Example 11 Use of Immobile Additive Primary Dye
[0371] Three grams of an immobile red dye,
Drimarene Scarlet, (Sandoz), were mixed with 3.0 grams of TBS and 27.0 grams of Solvesso
100® to form a red dye containing concentrate. The concentrate was ball-milled for
two weeks at room temperature.
Example 12 Green Imaging particles Produced By
[0372] Immobile Yellow and Cyan Dyes Twenty grams of l-(2,4,6-trichlorophenyl)-3-[3-(2,4-diamylphenoxy-acetamido)benzamido]-4-(p-methoxyphenylazo)-5-pyrazolone,
a yellow-colored ballasted coupler, here employed as a substantially immobile yellow
dye, and 40 grams of
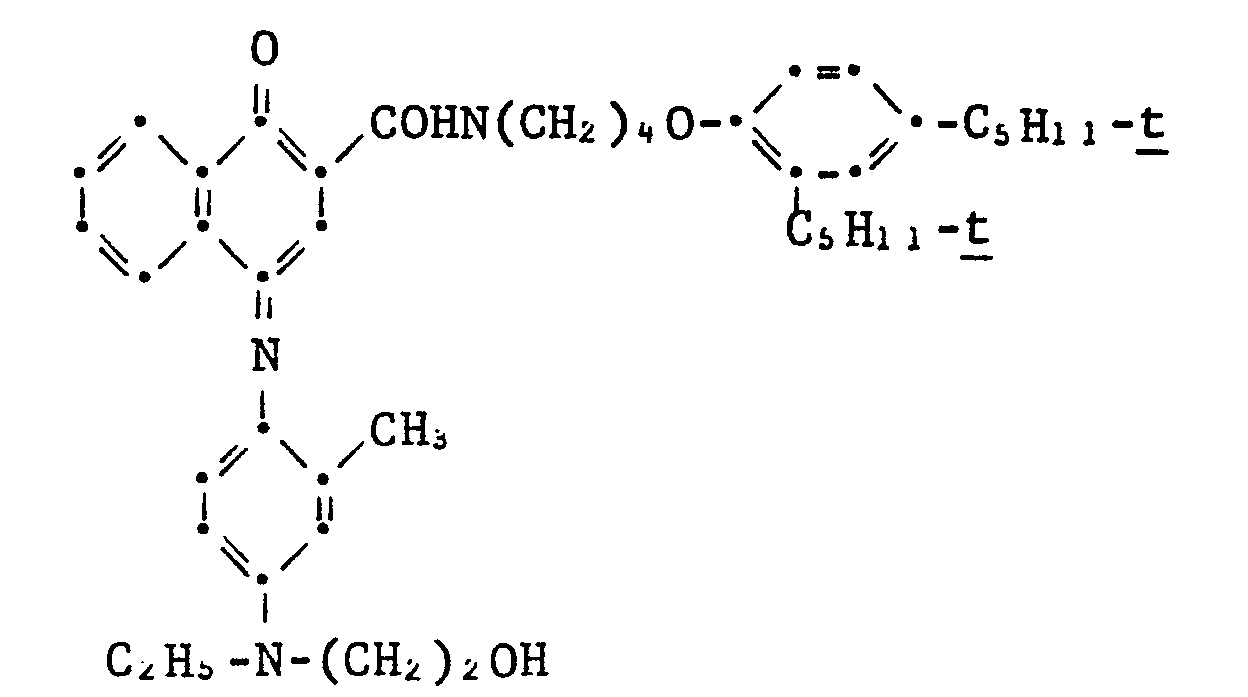
a substantially immobile cyan dye, were melted and diluted to a volume of 750 ml with
water to form an aqueous concentrate. To this concentrate were added 3.0 grams of
1-('2,4,6-trichlorophenyl)-3-(4-nitroanilino)-5-pyrazolone, a mobile magenta dye-forming
coupler. The magenta dye-forming coupler was dissolved in methanol and 5 percent by
weight sodium hydroxide.
[0373] The resulting concentrate was formed into a particulate dispersion by forming a mist
using a DeVilbus (Model 65)° ultrasonic nebulizer. The mist was passed through an
air drying column, and the neubulized solids were collected.
Example 13 Red Imaging Particles Produced by Immobile Yellow and Magenta Dyes
[0374] The procedure of Example 12 was repeated, except that 30 grams of
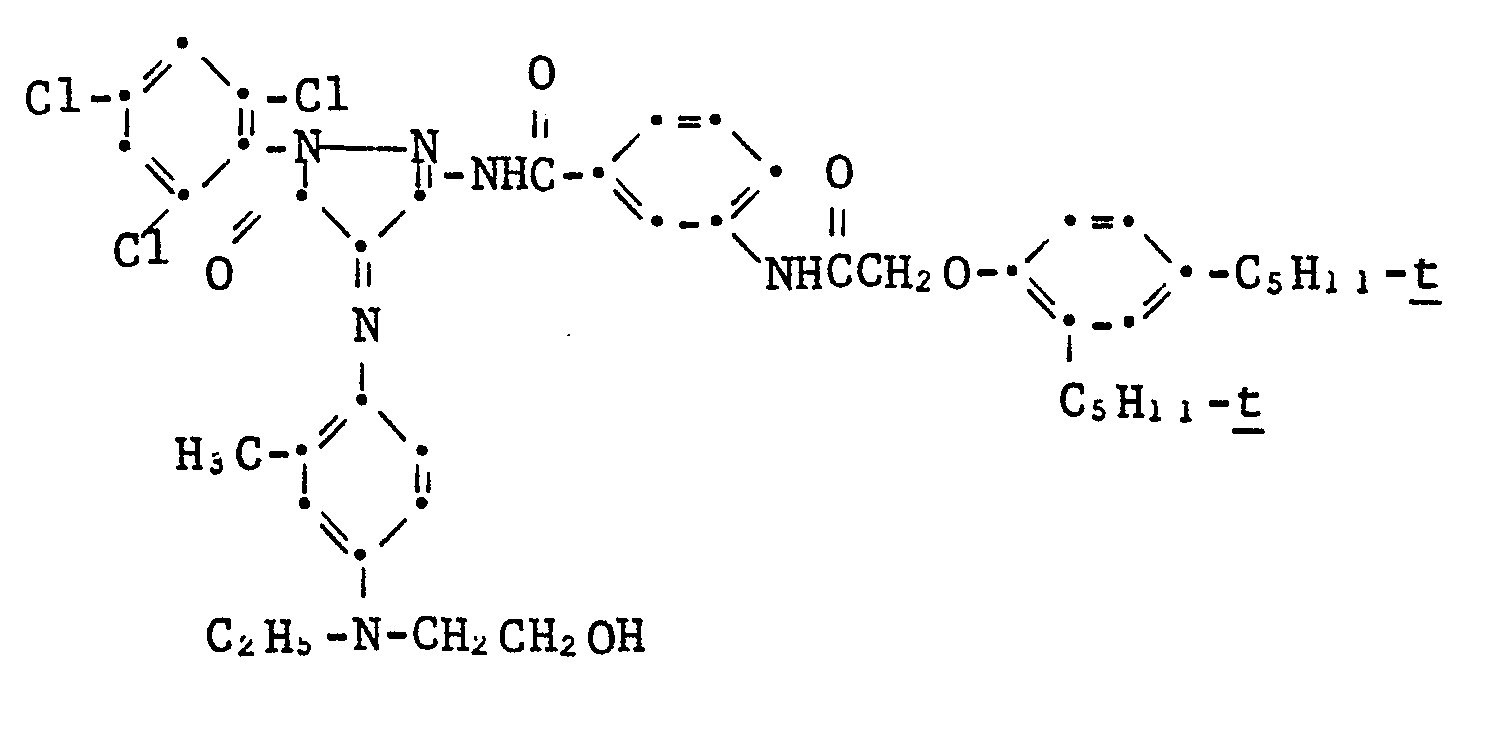
a substantially immobile ballasted magenta dye, was substituted for the substantially
immobile cyan dye and the mobile cyan coupler, 1-hydroxy-2-[β-(2'- aceatamido)phenethyl]naphthamide,
was substituted for the mobile magenta coupler.
Example 14 Blue Imaging Particles Produced by Immobile Cyan and Magenta Dyes
[0375] The procedure of Example 13 was repeated, except that 30 grams of the substantially
immobile cyan dye of Example 12 was substituted for the substantially immobile yellow
dye and a mobile yellow dye-forming coupler, a-(4- carboxy- phenoxy)-a-pivalyl-2,4-dichloroacetanilide,
was substituted for the mobile cyan coupler.
Example 15 Preparation of Green Electrographic Imaging Composition Containing Immobile
Subtractive Primary Dyes Dispersed in Carrier Vehicle to Form Electrographic Developer
and Use Thereof
[0376] The green imaging particles of Example 12 in the amount of 0.7 gram were mixed with
7.0 grams of a 10 percent by weight solution of TBS in Solvesso 100°. These materials
were placed in a container and tumbled for 24 hours to form a concentrate. The resulting
concentrate was mixed in the amount of 3.40 grams with 450 ml of
Isopar
G using ultrasonic agitation.
[0377] The resulting electrographic imaging composition was then employed substantially
as described in Example 9, paragraph K, except that only a single imaging composition
was employed.
Example 16 Preparation of Red Electrographic Imaging Composition Containing Immobile
Subtractive Primary Dyes Dispersed in Carrier Vehicle to Form Electrographic Developer
and Use Thereof
[0378] One gram of the red particles of Example 16 were mixed with 10 grams of a 10 percent
by weight solution of TBS in Isopar G. These materials were mixed on a roller mill
for 24 hours to form a concentrate. The resulting concentrate was mixed in the amount
of 5.0 grams with 450 ml of Isopar G using ultrasonic agitation. The electrographic
imaging composition particles in the resulting electrographic developer were about
5 microns in diameter.
[0379] The electrographic developer was employed substantially as described in Example 9,
paragraph K, except that only a single imaging composition was employed.
Example 17 Preparation of Blue Electrographic Imaging Composition Containing Immobile
Subtractive Primary Dyes Dispersed in Carrier Vehicle to Form Electrographic Developer
and Use Thereof
[0380] The procedure of Example 16 was repeated, but with the particles of Example 14 substituted
for those of Example 13. Instead of using ultrasonic agitation to form the electrographic
developer, a paint shaker was employed for agitation. The electrographic imaging composition
particles were plate-like having a maximum dimension of from 10 to 15 microns. The
resulting electrographic imaging composition was then employed substantially as described
in Example 11, except that only the imaging composition of this example was employed.
[0381] In comparing the electrographic imaging compositions of Examples 15 through 17 with
those of Examples 9, paragraphs G, H, and J, the former exhibited longer shelf life.
That is, the electrographic imaging composition particles settled at a slower rate.
The former also exhibited a higher charge to weight ratio and a higher extinction
coefficient. The higher extinction coefficient resulted in a higher maximum optical
density. It is attributed to a higher proportion of colorant, since materials such
as coupler solvent and gelatin were entirely eliminated in using pigment colorants.
Coupler mobility was initially observed to be higher using the compositions of Examples
15 through 17, but the mobility of couplers in pigment containing compositions was
found to be susceptible to increase by empirically selecting mobile couplers to be
employed.
Example 18
[0382] Following a procedure similar to that of Example 9, a microcellular array was thermally
embossed in the photoconductive layer of the support. The microcellular pattern was
similar to that shown in Figures 30A through 30C, except that pixels were displaced
along glide planes so that the second set of microcells 3006B were out of major axis
alignment by one-half of their width. That is, viewing Figure 30A, the microcells
appearing above the horizontal dashed line were all displaced to the right one width
of the microcells 3006B from the position shown. The microcells were 25 microns deep
from the wall widths between adjacent microcells being 15 microns. The inside width
of the square microcells of the third set 3006C was 125 microns. Thermal embossing
was conducted at a temperature of 82.2°C and at a pressure of 172 kPa applied to the
embossing master.
Example 19 Introduction of Imaging Compositions into Microcells of Support
[0383] The embossed photoconductive portion of the support was given a charge of +460 volts
by being passed through a corona discharge. The conductive electrode was attached
to ground. Except as stated, the support was exposed as shown in Figure 30B. A Xenon
arc lamp was employed controlled by an electronic shutter. Light was substantially
collimated and directed at an acute angle of 12° with respect to the axial plane 3014
of the support. After exposure the support was rotated 180° in the axial plane 3014
and exposed a second time. Each exposure was for 2 seconds, and the bottom walls of
the first set of microcells 3006A received during each exposure approximately 600
erts/cm
2 in the areas exposed. Direct light exposure of bottom wall areas were limited to
the bottom walls of the first set of microcells. The 15 microns width of the lateral
walls was sufficient to prevent light exposure of the remaining sets of microcells
through the lateral walls.
[0384] After angled exposure of the first set of microcells was completed, the microcellular
support was electrographically developed using an electrographic developer of the
type disclosed in Example 9, paragraph H, and a development time of 15 seconds. A
development electrode biased to +200 volts was employed.
[0385] The procedure described in the two preceding paragraphs was repeated, except that
an electrographic developer of the type disclosed in Example 9, paragraph I, was employed
and the exposure was as shown in Figure 30C rather than Figure 30B. That is, the second
set of microcells 3006B were selectively addressed and filled. Thereafter the support
was again recharged to +460 volts and exposed perpendicular to the axial plane 3014
at a distance of 15.24 cm to give an exposure of approximately 1,300 ergs/cm
2 using a UVL Mineralite. Development was repeated as described above, but using the
electrographic developer of the type disclosed in Example 9, paragraph G. After each
development step and prior to recharging a forced air dryer was employed to evaporate
developer solvent.
Example 20 Preparation of Photoconductive Support Having Hexagonal Microcells
[0386] A conventional planar photoconductive element similar to that described in Example
18 was solvent embossed using an embossing master having an array of hexagonal projections
20 microns in width and approximately 7 microns high. An embossing solvent was placed
on the plate between one edge of the array of projections and a strip of pressure-sensitive
tape employed to restrain migration of the solvent away from the projections. A sheet
of the recording film was placed on the plate with the photoconductive layer adjacent
the projections, and the resulting sandwich was advanced beneath a roller with the
edge bearing the embossing solvent passing beneath the roller first. The pressure
exerted by the roller and the softening action of the embossing solvent being spread
laterally at the roller nip resulted in a hexagonal array of microcells being formed
on the photoconductive layer having lateral bottom walls corresponding to the walls
of the hexagonal projections. The embossing solvent was a roughly equal volume mixture
of methanol and dichloromethane containing 0.2 gram per 10 ml of solvent Sudan Black
B (Color Index No. 26150). As a result, the lateral walls of the microcells were dyed
black, since the dye entered the photoconductive layer along with the embossing solvent.
The bottom walls of the microcells remained substantially transparent, however.
Example 21 Introduction of Imaging Compositions into Hexagonal Microcells of Support
[0387] The photoconductive portion of the support embossed with hexagonal microcells was
given a charge of +460 volts by being passed through a corona discharge. The conductive
electrode was attached to ground. Except as stated, the support was not identically
exposed to light to which the photoconductive portion was responsive. The positively
charged support was exposed as shown in Figure 26B. A Xenon arc lamp was employed
controlled by an electronic shutter. Light was substantially collimated and directed
at an acute angle of 26° with respect to the axial plane of the support. Exposure
was in the direction indicated by the arrow 1 in Figure 26B. The time of exposure
was 0.3 second. only the bottom wall areas 1 were exposed. The microcellular support
was electrographically developed using an electrographic developer of the type disclosed
in Example 9, paragraph I, and a development time of 10 seconds. A development electrode
biased to +200 volts was employed. The developer solvent was evaporated using heated
forced air. Material was selectively deposited in the microareas 1 of the support.
[0388] The support was rotated 120° in the axial plane with respect to the light source,
and the procedure described above was repeated, but with the substitution of an electrographic
developer of the type disclosed in Example 9, paragraph G, for the developer of Example
9, paragraph I. After the developer solvent was evaporated, the support was again
rotated 120° so that it occupied yet a third position with respect to the light source,
and the procedure described above was again repeated, but with the substitution of
the electrographic developer of Example 8. The result was the selective placement
of material in the microareas 1, 2, and 3 as shown in Figure 26B in each of the hexagonal
microcells.
Example 22
[0389] A pattern of hexagons 20 microns in width and approximately 10 microns high was formed
on a copper plate by etching. Using the etched plate having hexagon projections, dichloromethane
and ethanol (80:20 volume ratio) solvent containing 10 grams per 100 ml of Genacryl
Orange-R, a yellow azo dye, was placed in contact with a cellulose acetate photographic
film support for six seconds. Hexagonal microcells were embossed in the softened support
separated by 2 micron lateral walls, as measured at the surface of the support. The
yellow dye was absorbed in the cellulose acetate film support areas laterally surrounding,
but not beneath, the microcells, giving a density to blue light.
[0390] A membrane was prepared by placing four drops of a commercial casting solution (Microfilm
Solution', Sig Manufacturing Company, Montezuma, Iowa) onto the surface of water contained
in a 30 by 35 cm tray. The casting solution contained cellulose nitrate as a film-forming
polymer in an organic solvent comprised of aromatic hydrocarbon liquids (toluene and
xylene) forming a major component and, as minor components, a mixture of lower molecular
weight aliphatic alcohols, esters, and ketones (isopropyl alcohol, methyl ethyl ketone,
2-methyl propanol, isopropyl acetate, and methyl isobutyl ketone). The membrane was
estimated to be in the range of from 0.2 to 0.6 micron in thickness.
[0391] A balsa wood frame forming a square opening 16 cm on an edge was placed upon the
membrane to protect an area, and the membrane outside the frame was then collapsed
by crushing it against the frame. The microcellular film support was coated with this
membrane by immersing the film support in the water contained in the tray and then
withdrawing it through the membrane with the microcells on the upper surface of the
film support. The combined membrane and microcellular film support, with most microcells
now containing water, was then dried, so that no water remained as a liquid within
the microcells.
[0392] In order to increase the light absorbing capability of the membrane, the outer membrane
surface was passed rapidly through the incandescent portion of a candle flame. Under
microscopic examination, carbon could be seen on the outer surface of the membrane.
[0393] To open a first set of microcells, the microcellular film support with the membrane
present providing a lightly carbon-coated outer surface was subjected to irradiation
with a 647 nanometer laser beam in a pattern of laterally spaced lines. The beam power
was in the 12 to 28 milliwatts per square centimeter range, and the beam cross-section
was about 23 microns. Where the laser beam struck the membrane, the microcells were
uncovered in a single or double line, depending upon the power and placement of the
beam.
[0394] To form materials for selectively filling microcells, three subtractive primary filter
dye compositions were prepared as described below, identified as Yellow Dye Dispersion
A, Magenta Dye Dispersion B, and Cyan Dye Dispersion C. The filter dye was in each
instance chosen to be immobile, thereby avoiding transfer from the microcells once
introduced.
[0395] To form the compositions actually used to fill each of three separate sets of microcells,
two of the subtractive primary dye dispersions identified above were blended to form
an additive primary filter material. An initially mobile and colorless subtractive
dye-forming coupler was also blended with the two subtractive primary filter dyes.
(The mobile couplers were, of eourse, immobile in the microcells, since mobility refers
only to mobility upon contact with a photographic processing solution.)
Yellow Dye Dispersion A
[0396] A conventional aqueous-oil dispersion was prepared by homogenizing 40 grams yellow
dye 3-{3-[α-(2,4-di-t-pentylphenoxy)acetamido]-benzamido/-4-(4-methoxyphenylazo)-1-(2,4,6-trichlorophenyl)-2-pyrazolin-5-one,
120 grams auxiliary solvent 2-(2-butoxyethoxy)ethyl acetate and 27.2 grams gelatin
diluted to 454 grams with water. Following homogenization, the dispersion was chill-set
and noodle-washed to remove the auxiliary solvent.
Magenta Dye Dispersion B
[0397] A conventional aqueous-oil dispersion was prepared by homogenizing 40 grams magenta
dye 3-t3-[u-(2,4-di-t-pentylphenoxy)acetamidol- benzamido/-N-i4-[N-ethyl-N-(2-hydroxyethyl)-amino]-2-tolylimino/-l-(2,4,6-trichlorophenyl)-2-pyrazolin-5-one,
80 grams permanent solvent 1,4-cyclohexylenedimethylbis(2-ethylhexanoate), 80 grams
auxiliary solvent cyclohexanone, and 60 grams gelatin diluted to 1000 grams with water.
Following homogenization, the dispersion was chill-set and noodle washed to remove
the auxiliary solvent.
Cyan Dye Dispersion C
[0398] A conventional aqueous-oil dispersion was prepared by homogenizing 40 grams 2-[4-(2,4-di-t-pentylphenoxy)butylcarbamoyl]-N-t-4-[N-ethyl-N-(2-hydroxyethyl)amino]-2-tolyl/-1,4-naphthoquinone
4-monoimine, 80 grams permanent solvent 1,4-cyclo- hexylenedimethyl bis(2-ethylhexanoate),
80 grams auxiliary solvent cyclohexanone, and 60 grams gelatin diluted to 1000 grams
with water. Following homogenization, the dispersion was chill-set and noodle-washed
to remove the auxiliary solvent.
Dry Red Microsphere Dispersion Beads
[0399] First, 30 grams of yellow dye dispersion A and 30 grams of magenta dye dispersion
B were melted together and diluted to 750 ml with water. Next, 3.0 grams cyan dye-forming
coupler, l-hydroxy-N-[2-(2-acetamido)phenethyl]-2-naphthamide, were dissolved in a
minimum amount of ethyl alcohol and 5 percent sodium hydroxide and added to the solution
of dispersions.
[0400] The resultant mixture was passed through a DeVilbiss® (Model 65) ultrasonic nebulizer
and into a heat jacketed drying column where the water was evaporated. The resultant
dry red microsphere dispersion beads containing a cyan dye-forming coupler were collected
and examined microscopically. They were approximately three microns and smaller in
size.
Dry Green Microsphere Dispersion Beads
[0401] Yellow dye dispersion A, 20 grams, and cyan dispersion C, 40 grams, were melted together
and diluted to 750 ml with water. Magenta dye-forming coupler, 3-(4-nitroanilino)-1-(2,4,6-trichlorophenyl)-2-pyrazolin-5-one,
3.0 grams, dissolved in a minimum amount of ethyl alcohol and 5 percent sodium hydroxide
were added to the solution of dispersions. Following treatment in the nebulizer and
drying column, dry green microsphere dispersion beads containing a yellow dye-forming
coupler were obtained.
Dry Blue Microsphere Dispersion Beads
[0402] Magenta dye dispersion B, 30 grams, and cyan dye dispersion C, 30 grams, were melted
together and diluted to 750 ml with water. Yellow dye-forming coupler, α-(4-carboxyphenoxy)-α-pivaloyl-2,4-dichloroacetanilide,
3.0 grams, dissolved in a minimum amount of ethyl alcohol and 5 percent sodium hydroxide
were added to the solution of dispersions. Following treatment in the nebulizer and
drying column, dry blue microsphere dispersion beads containing a yellow dye-forming
coupler were obtained.
[0403] The microcellular film support with the membrane thereon destroyed in laterally spaced
lines to open a first interlaid set of microcells was covered with the green microsphere
dispersion beads. The dispersion beads were introduced into the opened microcells
with a flexible rubber blade with excess beads being removed by brushing. Microscopic
examination showed that microcells not struck by the laser beam still retained a membrane
cover.
[0404] The microcellular film support with the membrane thereon was again scanned with the
laser microbeam, but at an angle to the first linear scan. As before, the laser microbeam
removed membrane in areas contacted, leaving a second, interlaid set of microcells
uncovered. The newly uncovered microcells were filed with blue microsphere dispersion
beads by the same procedure described above for filling with the green microsphere
dispersion beads.
[0405] Thereafter, the remnants of the membrane were removed with an adhesive tape, opening
the third interlaid set of microcells. The newly opened microcells were filled with
the red microsphere dispersion beads. Excess fill material was then lifted from the
microcellular face of the film support using adhesive tape.
[0406] The resulting three color microcellular filter array was placed in a high relative
humidity environment overnight. The microcell contents became less scattering and
appeared to be partially fused.
Example 23
[0407] The procedure of Example 22 was repeated, except that the balsa wood frame was immersed
in the water beneath the membrane and lifted upwardly to raise the membrane from the
surface of the water. Thereafter the microcellular support element was gently laid
on the membrane so that the membrane closed the microcells. The support element with
the membrane in place was flexed so that the first major surface bearing the microcells
was convex. Final setting of the membrane occurred with the support in this configuration.
Example 24
[0408] The procedure of Example 22 was repeated, except that the composition of the casting
solution was varied. The casting solution employed to form the membrane consisted
of 8.5 grams of cellulose acetate and 42.0 grams of solvent. The solvent consisted
of 80 ml of dichloromethane and 20 ml of methanol containing 0.6 g of Genacryl Blue
dye to enhance the radiation adsorption of the membrane. No carbon was placed on the
surface of the membrane.
Example 25
[0409] The procedure of Example 22 was repeated, except that the composition of the casting
solution was modified to include 1 g of Sudan Black B, wet with 10 drops of dichloromethane
per 12 g of casting solution. No carbon was placed on the surface of the membrane.
[0410] In both Examples 24 and 25, the membranes adsorbed sufficient radiant energy from
the laser to permit their local destruction to open selected microcells.