(19) |
 |
|
(11) |
EP 0 040 306 B1 |
(12) |
EUROPEAN PATENT SPECIFICATION |
(45) |
Mention of the grant of the patent: |
|
25.07.1984 Bulletin 1984/30 |
(22) |
Date of filing: 24.03.1981 |
|
|
(54) |
Method for producing large grain semiconductor ribbons
Verfahren zur Herstellung grobkörniger Halbleiterbänder
Procédé de fabrication de rubans semi-conducteurs à gros grain
|
(84) |
Designated Contracting States: |
|
DE FR GB IT |
(30) |
Priority: |
15.05.1980 US 150257
|
(43) |
Date of publication of application: |
|
25.11.1981 Bulletin 1981/47 |
(71) |
Applicant: International Business Machines
Corporation |
|
Armonk, N.Y. 10504 (US) |
|
(72) |
Inventors: |
|
- Chaudhari, Praveen
Briarcliff Manor, NY 10510 (US)
- Mueller, René
CH-5442 Fislisbach (CH)
|
(74) |
Representative: Suringar, Willem Joachim |
|
Intellectual Property Department
IBM Nederland N.V.
Watsonweg 2 1423 ND Uithoorn 1423 ND Uithoorn (NL) |
|
|
|
Note: Within nine months from the publication of the mention of the grant of the European
patent, any person may give notice to the European Patent Office of opposition to
the European patent
granted. Notice of opposition shall be filed in a written reasoned statement. It shall
not be deemed to
have been filed until the opposition fee has been paid. (Art. 99(1) European Patent
Convention).
|
[0001] This invention relates to the manufacture of large grain semiconductor ribbons suitable
for solar cell applications.
[0002] In US-A-4,142,571 which has been used for the delimination of claim 1 is disclosed
a method for producing ribbons of amorphous alloy material, including a palladium-silicon
alloy, wherein the material in a molten state is discharged under controlled pressure
onto the surface of a rotating metal cylinder moving at a linear velocity of from
2 to 33 m/s, to form a solid ribbon by the cooling action of the metal surface on
the ejected melt. The cylinder diameter could be 40 cm, the rotational speed could
be 700 rpm and the ejection pressure could be 4.8 kPa (0.7 psig). The resulting alloy
strips were amorphous, i.e., the grain size, if any, had to be very small.
[0003] These small grains, in a semiconductor ribbon, would be substantially smaller than
those which should be employed to maintain a reasonable efficiency in any resulting
solar cell. In order to obtain an efficiency of approximately 10% it would be required
that the grain size be increased by an order of magnitude to approximately 10 to 30
pm.
[0004] It is an object of the invention to establish a method for producing a semiconductor
ribbon of suitable quality for solar cells.
[0005] Another object of the invention is to establish a method for production of semiconductor
ribbons with an average grain size of about 20 ,um and greater.
[0006] Still another object of this invention is to provide a method for producing semiconductor
ribbons with a coherent oxide.
[0007] Yet another object of the invention is to provide a method for the production of
substantial volumes of silicon ribbon.
[0008] The present invention provides a method for fabricating large grain semiconductor
ribbons as completely disclosed in claim 1, wherein a molten semiconductor material
is discharged under an ejection pressure between 27 and 104 kPa (4 to 15 psig) onto
a rotating cylindrical surface which is rotating with a rotational speed in the range
of from 2,000 to 9,000 rpm and a linear velocity from 8-36 m/s.
[0009] These and other objects, features and advantages of the invention will become apparent
from the following description, accompanying drawings, and appended claims in which
various novel features of the invention are more particuiarly set forth.
Fig. 1 is a schematic representation of a ribbon caster suitable for practicing the
invention.
Fig. 2 is a graphical depiction of the effect of wheel speed and injection pressure
on grain size.
[0010] A device suitable for the implementation of this invention is illustrated in Fig.
1. A tube 10 is employed for containing a molten semiconductor material 12. The semiconductor
material 12 is maintained molten by a furnace 14 which surrounds the tube 10. The
tube 10 has a nozzle 16 which is employed to direct a molten stream 18 of the semiconductor
material 12. Examples of such semiconductor materials are Si, Ge, and Ga-As. A gas
supply tube 20 feeds gas into the tube 10 via a regulating valve 22. The regulating
valve 22 controls pressure in the tube 10 above the molten semiconductor material
12. This pressure serves to discharge the molten semiconductor material 12 through
the nozzle 16 and forms the stream 18. The stream 18 impinges on a rotating wheel
24. Preferably the stream 18 impacts the wheel 24 at an angle 6 such that there is
a component of the stream direction which is in the direction of a tangent to the
rotating wheel 24 at the point of contact 25. This component should be in the direction
of the rotation. The wheel 24 is driven from a power drive 26 such as a motor. The
wheel 24 should be a conducting material. Stainless steel, as well as copper, have
been found to be satisfactory materials. During operation the stream 18 impinges on
the rotating cylindrical surface 28 thereby generating a semiconductor ribbon 30.
[0011] In carrying the invention into practice a gas is supplied to the gas supply tube
20 and pressure p in the tube 10 is maintained above the semiconductor material by
the regulating valve 22. This pressure p controls the discharge of the stream 18 from
the nozzle 16. The stream 18 impinges upon the wheel 24 which is rotating as illustrated
with an angular speed ω.
[0012] It has been found that when the ribbon is generated in air it is preferred to use
a copper wheel 24. When a copper wheel is used it is advisable to gold plate the cylindrical
surface 28 of the wheel to avoid oxidation of the copper during operation.
[0013] It has also been found that, when the injection pressure p in the insulating tube
is maintained at or above 8 psig (psig being defined as pounds per<square inch gauge
where reference pressure is the gas pressure at the wheel; 1 psi =6.9 kPa) and the
nozzle 18 has an opening of a nominal diameter of 1 mm, a satisfactory ribbon 30 can
be maintained when the linear velocity of the cylindrical surface 28 is in excess
of 8 m/s. It is furthermore preferred that the angle of incidence 0 of the stream
18 with respect to the cylindrical surface 28 be from about 9° to 15° when defined
with respect to an extended diameter passing through the point of contact 25.
[0014] In addition to the lower limits on the linear velocity of the cylindrical surface
28 which is required to maintain a semiconductor ribbon 30, the cylindrical surface
28 may not obtain velocities greater than 36 m/s without substantially reducing the
ultimate average grain size of the resulting semiconductor ribbon 30.
[0015] Fig. 2 offers a graphical representation of the effect of wheel speed on the average
grain size. For these curves semiconductor material ribbons were generated on a copper
wheel, having a diameter of 7.6 cm. Curves A, B and C are for silicon were the molten
silicon is heated to about 1500°C and the gas injection pressure p was maintained
at respectively 4 psig, 8 psig, and 15 psig for a nozzle having a nominal opening
1 mm in diameter. As the pressure is increased the ribbon becomes thinner and above
about 15 psig the ribbon becomes discontinuous and forms flakes. It is apparent that
as one increases the pressure there is an increase in the ultimate grain size which
can be obtained.
[0016] Wheel speed has a marked effect on the ultimate grain size. It can be seen that at
rpm (revolutions per minute) values of about 9000, i.e. a surface speed of about 36
m/s, the grain size has dropped to the neighborhood of slightly less than 10 µm and
as the velocity of the wheel is further increased the change in grain size is not
substantially affected. This decrease in grain size occurs for all pressures studied.
The drop is sharpest for curves B and C.
[0017] It is felt that one plausible explanation for the relatively large grain sizes produced
at the higher rotational speed of the wheel 24 when compared to the earlier reported
work of US-A4142571 is that in the present study a smaller wheel 24 was employed.
To obtain the same surface velocity with a smaller wheel requires a greater rotational
speed. Greater rotational speed will result in a greater centrifugal force acting
on the ribbon. The centrifugal force may act to reduce contact with the wheel and
thereby lessen the cooling effect of the wheel and thereby reduce the cooling rate
of the ribbon. A slower cooling rate may account for the larger grain size.
[0018] It is also apparent that, once the velocity has been slowed sufficiently to produce
a large grain size, further reduction in the wheel velocity does not substantially
change the grain size. The data used to generate these curves of Fig. 2 is contained
in Table I.
[0019] The velocity of the wheel is presented both in terms of rotational speed (rpm) and
the linear velocity (m/s) of the cylindrical surface 28. The pressures are given in
terms of the gas ejection pressure for the resulting semiconductor stream 18. It was
found that changing the orifice diameter from 0.5 to 1.5 mm did not noticeably affect
the grain size of the resulting ribbons. Furthermore, it should be appreciated that
the linear velocity of the surface of the wheel as well as ejection pressure are the
appropriate parameters for the control of relative grain size of the resulting ribbon.
These parameters can be maintained independent of the geometry of the equipment employed.
[0020] Curve D of Fig. 2 illustrates the effect of velocity on the grain size of germanium
semiconductor ribbons. These ribbons were generated from molten germanium which was
heated to about 1000°C and ejected at a pressure of 15 psig through a nozzle having
a nominal diameter of 1 mm. As can be seen by comparing curves C and D, the germanium
data as is the case for the silicon data show little dependence between grain size
and speed at low speeds. The tubular data used to generate curve D has been incorporated
into Table I.
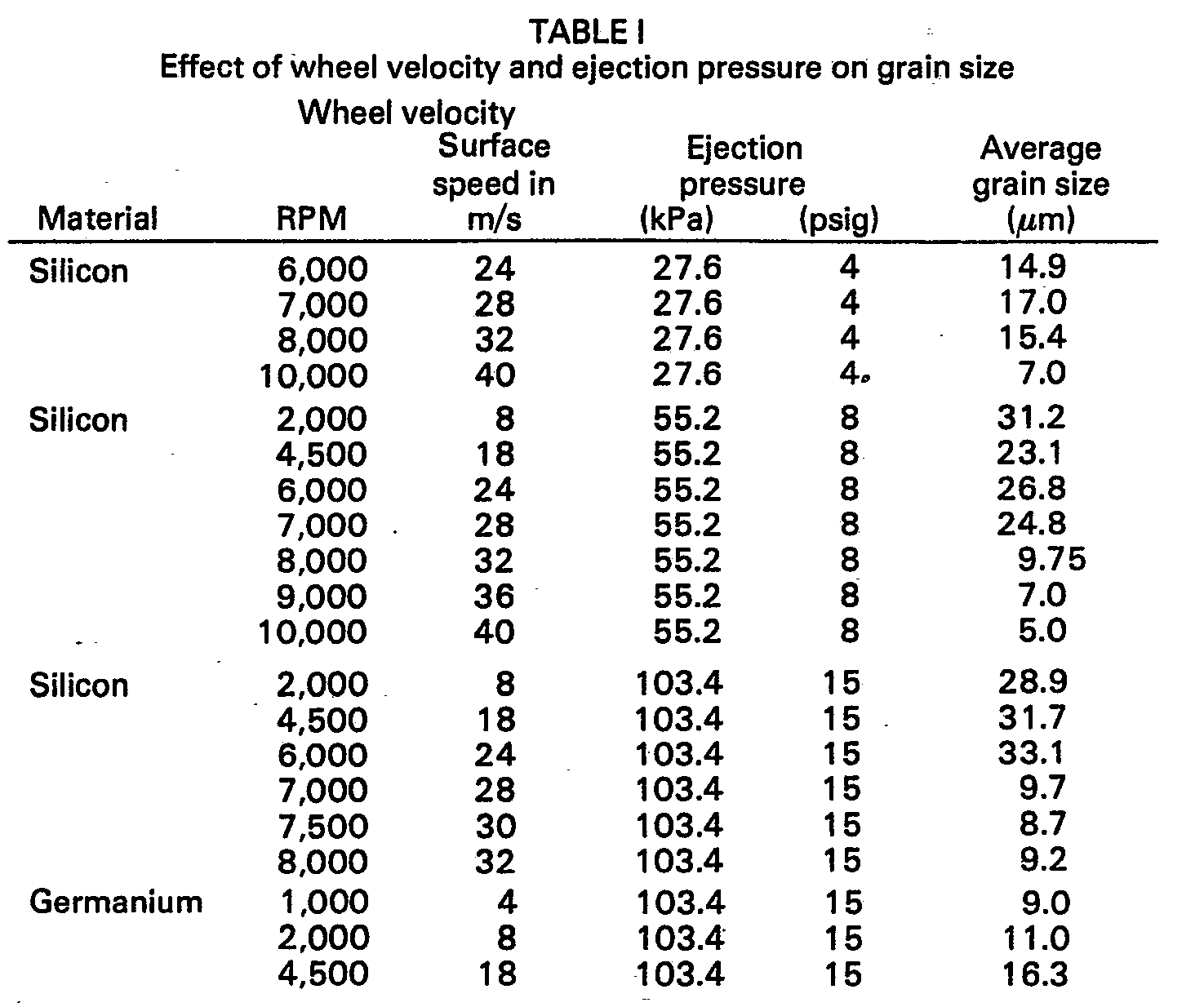
[0021] Both germanium and silicon form oxides on the surface of the resulting ribbons when
the ribbons are generated in an atmosphere of air. These oxides are sufficient to
provide an intermediate layer between the silicon and a metal deposited thereon. The
resulting metal silicon junctions form Schottky barriers.
[0022] The oxide may be prevented by generating the ribbon under a protective atmosphere.
Argon and helium have been found to be effective atmospheres in which to generate
the ribbons. In the event that a protective atmosphere is sought, the wheel 24 and
nozzle 16 should be placed in a chamber 32 as illustrated by the broken line in Fig.
1. This chamber will allow the atmosphere to be controlled.
[0023] The present invention will be of use in the semiconductor industry and in particular
in solar cell production.
[0024] While the present invention has been illustrated and described in terms of preferred
modes, it is to be understood that these modes are by way of illustration and not
limitation and the right is reserved to all changes and modifications coming within
the scope of the invention as defined in the appended claims.
1. A method of fabricating ribbons of semiconductor material, which material in a
molten state (12) is discharged (18) under controlled pressure onto the surface (28)
of a rotating metal cylinder (24) moving at a linear velocity of 8 m/s or more, to
form a solid ribbon (30) by the cooling action of the metal surface on the ejected
melt, characterized in that the ejection pressure of the melt is between 27 and 104
kPa (4 to 15 psig), the rotational speed of the metal cylinder (24) is in the range
of from 2,000 to 9,000 rpm, and the linear velocity of the cylinder surface is not
greater than 36 m/s, whereby a semiconductor ribbon (30), having a large grain size,
larger than 10,um is obtained.
2. A method according to claim 1, wherein the rotating metal cylinder has a diameter
in the order of 7.6 cm.
3. A method according to tlaim 1 or 2, wherein the semiconductor material is selected
from silicon and germanium.
4. A method according to a previous claim, carried out in air, whereby the semiconductor
ribbon is covered by a coherent oxide.
5. A method according to a previous claim, wherein the semiconductor is silicon, the
temperature of the molten silicon (12) to 1500°C, the ejection pressure is between
55 and 104 kPa (8 to 15 psig) and the rotational speed of said cylinder (24) is between
2,000 and 7,000 rpm, whereby a silicon ribbon having a grain size of 20 to 30 um is
obtained.
1. Une méthode de fabrication de rubans en matériau semiconducteur (12) matériau se
trouvant à l'état de fusion et étant éjecté (18) sous pression contrôlée sur la surface
(28) d'un cylindre métallique (24) en rotation se déplaçant à la vitesse linéaire
de 8 m/s ou davantage, pour former un ruban plein (30) sous l'action de refroidissement
de la surface métallique sur le matériau en fusion, caractérisée en ce que la pression
d'éjection du produit en fusion est comprise entre 27 et 104 kPa (4 à 15 psig), la
vitesse de rotation du cylindre métallique (24) se trouvant dans la gamme comprise
entre 2000 et 9000 tours/minute, et la vitesse linéaire de la surface du cylindre
n'étant pas supérieure à 36 m/s, ce qui permet d'obtenir un ruban semi-conducteur
(30) ayant un grain de grande dimension, supérieur à 10 jum.
2. Une méthode conforme à la revendication 1 dans laquelle le cylindre métallique
en rotation a un diamètre de l'ordre de 7,6 cm.
3. Une méthode conforme aux revendications 1 ou 2, dans laquelle le matériau semi-
conducteur est constitué par du silicium ou du germanium.
4. Une méthode conforme à une revendication précédente, mise en oeuvre dans l'air,
et grâce à laquelle le ruban semiconducteur est recouvert d'une couche d'oxyde cohérent.
5. Une méthode conforme à une revendication précédente, dans laquelle le semiconducteur
est du silicium, la température du silicium fondu (12) est de 1500°C, la pression
d'éjection est comprise entre 55 et 104 kPa (8 à 15 psig) et la vitesse de rotation
dudit cylindre (24) est comprise entre 2000 et 7000 tours/minute, ce qui permet d'obtenir
un ruban de silicium ayant des grains d'une dimension de 20 à 30 µm.
1. Verfahren zur Herstellung von Bändern aus Halbleitermaterial, welches in einem
geschmolzenen Zustand (12) unter gesteuertem Druck auf die Oberfläche (28) eines rotierenden
Metallzylinders (24), welcher sich mit einer Lineargeschwindigkeit von 8 m/s oder
mehr bewegt, abgegeben wird (18), zur Ausbildung eines festen Bandes (30) durch die
Kühlwirkung der Metalloberfläche auf die ausgestoßene Schmelze, dadurch gekennzeichnet,
daß der Ausstoßdruck der Schmelze zwischen 27 und 104 kPa (4 bis 15 psig) liegt, die
Drehgeschwindigkeit des Metallzylinders (24) im Bereich zwischen 2000 bis 9000 min-1
liegt, und die Lineargeschwindigkeit der Zylinderoberfläche nicht größer als 36 m/s
ist, wodurch ein Halbleiterband (30) mit grober Korngröße vom mehr als 10 µm gewonnen
wird.
2. Verfahren nach Anspruch 1, bei welchem der rotierende Metallzylinder einen Durchmesser
in der Größenordnung von 7,6 cm hat.
3. Verfahren nach Anspruch 1 oder 2, bei welchem das Halbleitermaterial aus Silizium
und Germanium ausgewählt wird.
4. Verfahren nach einem vorstehenden Anspruch, ausgeführt in Luft, wodurch das Halbleiterband
mit einem zusammenhängenden Oxid bedeckt wird.
5. Verfahren nach einem vorstehenden Anspruch, bei welchem der Halbleiter Silizium
ist, die Temperatur des geschmolzenen Siliziums (12) 1500°C beträgt, der Ausstoßdruck
zwischen 55 und 104 kPa (8 bis 15 psig) liegt und die Drehgeschwindigkeit des Zylinders
(24) zwischen 2000 und 7000 min-' liegt, wodurch ein Siliziumband mit einer Korngröße
von 20 bis 30 µm gewonnen wird.

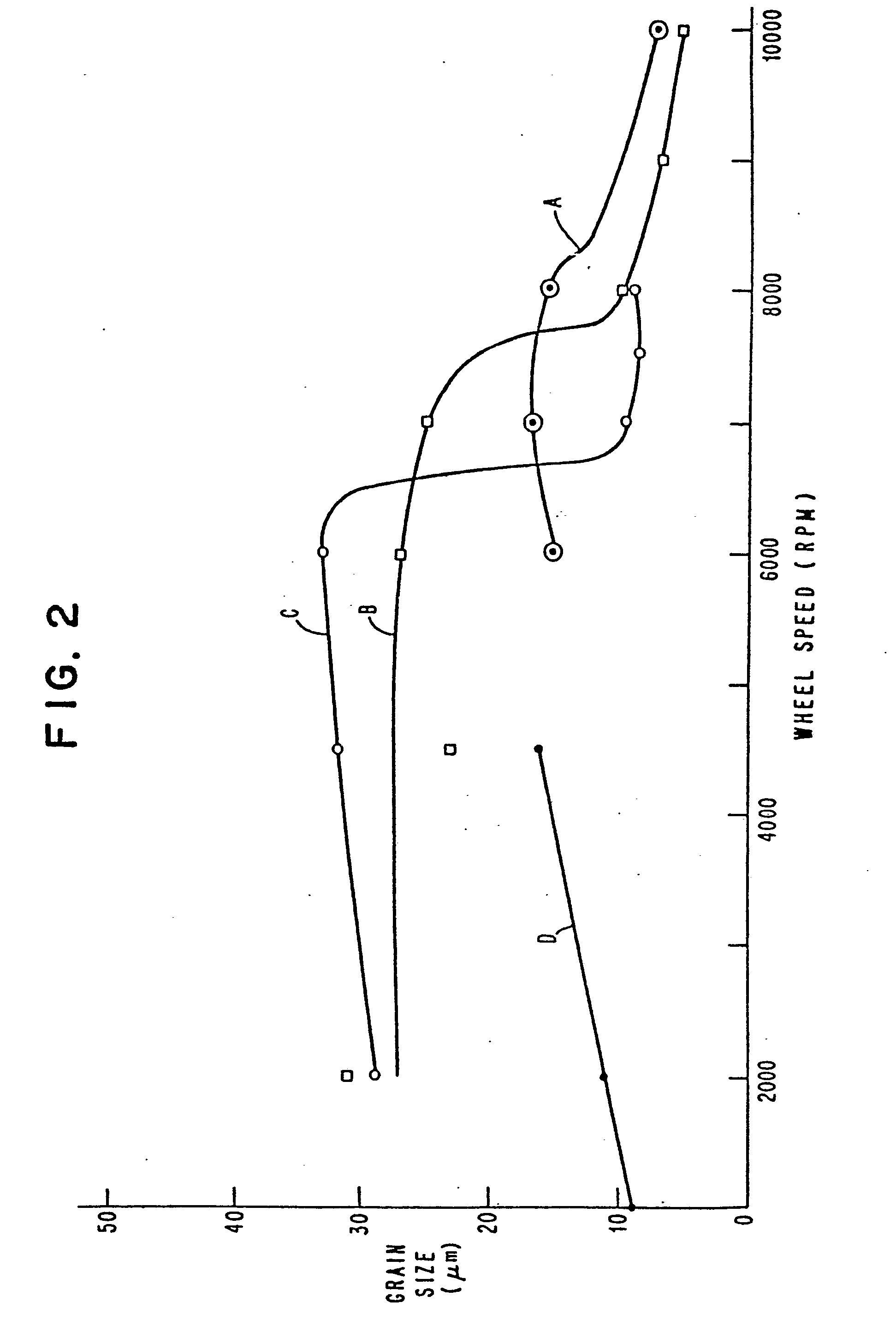