BACKGROUND OF THE INVENTION
[0001] This invention relates to a novel thermally conductive filler for insulating the
interior of a housing containing electrical components and to a method of filling
the housing and encapsulating the electrical components with the thermally conductive
medium.
[0002] It is well known that heat produced by electrical components contained within a housing
should be removed by conducting the heat to the exterior of the housing. When the
electrical components within the housing are relatively high voltage components and
the housing has a relatively small volume, it is not feasible to employ conventional
air cooling or liquid cooling systems. Moreover, it is frequently desirable that the
housing be filled with a medium which will encapsulate and protect the individual
components therein against relative movement due to shock forces and the like, and
against chemical attack or contamination by environment influences. Consequently,
electrical equipment including such assemblies as high voltage power supplies which
produce output voltages of the order of thousands of volts, are conventionally potted
by a potting material which is typically a polymerized resin.
[0003] These potting resins provide mechanical protection of the potted components but the
thermal conductivity of such resins is relatively poor. For example, the thermal conductivity
of typical potting material now used is of the order of 0.0005 cal. per second cm
°C. Therefore, heat generated by the electrical components within the housing is not
easily conducted to external surfaces of the housing.
[0004] It is known that thermally conductive particles can be added to polymerized potting
resins in order to increase the thermal conductivity of the potting meterial. These
thermally conductive particles are generally electrically insulative ceramics which
have good thermal conduction characteristics and typically may be beryllium oxide,
aluminium oxide, boron nitride or some types of silicon carbide. These thermally conductive
particles are normally stirred into the potting resin just before the resin is poured
into the interior of a housing.
[0005] It has been found that the volume of the insulation particles loaded in this way
can rarely exceed 50% of the total resin volume. Consequently, the thermal conductivity
of the insulation medium with the particles in pace is usually only about twice that
of the resin itself. Thus, while aluminium oxide, for example, has a bulk thermal
conductivity of 0.084 cal, per second cm °C. when particles of the ceramic consist
of about 50X of the total volume of a conventional polymerized potting resin, the
thermal conductivity of the ultimate material will be increased from about 0.0005
cal. per second cm' °C. to about 0.001 cal. per second cm °C.
BRIEF DESCRIPTION OF THE INVENTION
[0006] In accordance with the invention, the interior of an electrical housing filled with
heat-generating devices, such as transistors, transformers, resistors and the like,
having irregular volumes and shapes, is filled with an easily flowing slurry consisting
of a mixture of more than 50% by volume and preferably more than 70% by volume of
heat-conductive, electrically insulative particles, suspended in a dielectric fluid,
which preferably is a liquid such as silicone oil. The thermally conductive particles
typically may be aluminium oxide particles or the like having a particle size which
is preferably distributed about a mean diameter of about 150 microns. Beryllia can
also be used, but it is more expensive than alumium and is very toxic in powdered
form.
[0007] The slurry is first mixed at room temperature by pouring the particles into the dielectric
fluid and agitating this mixture. The slurry is then poured into a filler column which,
in turn, is connected to the open top of the electrical housing. The filler column
and housing are sealed to be air-tight so that the slurry cannot freely escape from
the interior of the housing. The slurry is then subjected to vacuum to remove trapped
air bubbles therefrom and the slurry is permitted to settle into the housing interior
under the force of gravity. During the settling period, the assembly is tilted in
different directions to eliminate Rankine slope effects. Oil appearing at the top
of the column is decanted and replaced by additional slurry during the settling process.
The volumetric packing density after settling for about 36 hours will often exceed
80% of particles by volume.
[0008] The slurry particles are then further compacted against one another to form a relatively
non-flowable paste. this further compacting can be carried ouy by a centrifugal process.
Thus, the entire housing is spun at moderate "g" force for about two hours in a suitable
fixture. The insulation particles, which are more dense than the suspending liquid,
tend to compact in one direction relative to the housing due to centripital force
effects to form a paste-like consistency in which silicone oil fills the interstices
between particles. The paste now forms an almost solid continuous body which encapsulates
the components and extends between the components and to the interior of the surrounding
walls of the housing. It has been found that the final highly compacted mass has a
thermal conductivity close to that of a solid block of the insulation material which
is employed.
[0009] The filler column is then removed and the paste, which extends above the top of the
open housing end, is sliced off to be flush with the housing top. A housing lid is
then sealed over the housing top to complete the enclosure.
[0010] Preferably, the housing is made of conductive material to act as a heat sink to heat
conducted from internal potted components through the encapsulant.
BRIEF DESCRIPTION OF THE DRAWINGS
[0011]
Figure 1 is a cross-section taken through a housing which has been filled with thermally
conductive insulation in accordance with the invention.
Figure 2 is a cross-section view of Figure 1 taken across the section line 2-2 in
Figure 1.
DETAILED DESCRIPTION OF THE DRAWINGS
[0012] Referring to the drawings, there is shown in generalized form a housing 10 which
may be of a good thermal conductor, preferably of aluminium, and which may have any
desired thickness. Housing 10 has a top lid 11 attached and sealed thereto in any
desired manner. The housing 10 can typically have dimensions of 2 inches by 4 inches
by 5 inches but it will be obvious that the invention can apply to any housing size
which contains any type of component.
[0013] Various heat-generating electrical components are mounted within the housing and
are schematically illustrated as the heat-generating components 12, 14, 16, 18, 20
and 22. These components can be of any desired nature. By way of example, component
12 could be a bridge-connected rectified circuit which might produce 4.8 watts during
its operation. Component 14 could be an inverter transformer which produces 25 watts
during its operation. Components 16 to 22 could be the elements of a bridge-connected
rectifier which produces 1.2 watts. Components 16 to 22 can be carried on a common
circuit board with other components, not shown. An electrical connector shown in the
form of a multi-conductor ribbon 24 carries suitable wires from the interior electrical
components of housing 10 to the exterior where the wires can be connected to other
circuits. A suitable insulation seal can enclose and seal ribbon 24 as it passes through
the wall of housing 10. Alternatively, a multi-pin connector can be formed in the
wall of housing 10 and individual wires from the components within housing 10 can
be connected to the multi-pin connector.
[0014] In order to prevent an excessive temperature rise of components 16 to 22 and their
connecting leads or wires during their operation without complicating the housing
design with metal heat sinks, and without having to enlarge the housing, the components
can be thermally connected to the exterior walls of housing 10 by the novel heat conductive
insulation of the invention which encapsulates the electrical components.
[0015] The housing 10 is provided with an open top (lid 11 is removed) and the electrical
components to be mounted therein are fixed in place. A filler column (not shown) which
has a volume larger than that of housing 10, is sealed to the open top of housing
10.
[0016] In accordance with the invention, an insulation medium is prepared as a relatively
non-viscous slurry of particles of a material having good thermal conductive properties
but which are electrically insulative, suspended in an insulation fluid. Typical particles
may be of aluminium oxide, beryllium oxide, boron nitride and certain types of known
silicon carbides. The particle size employed for these particles is not critical.
Good results have been obtained with particles distributed about a mean diameter of
less than about 300 microns which ensures uniform and homogeneous filling of the particles
within housing 10 and into very small irregular crevices or the like, in the interior
of housing 10.
[0017] The particles are loaded into a suitable dielectric fluid as silicone oil at room
temperature and stirred to ensure thorough mixing and uniform distribution of the
particles into the oil. There should be sufficient oil present in the mixture to ensure
that the slurry will flow easily into the interior of housing 10. Generally, the particles
should occupy more than one half by volume of the slurry.
[0018] In an illustrative embodiment of the invention, aluminium oxide particles have a
size distributed around a mean diameter of about 150 microns are stirred into a silicone
oil carrier. The powder and oil are in a ratio of about 70% to 30%, respectively,
by volume. The slurry is very easily flowable in this condition. Other stable dielectric
fluids can be used in place of silicone oil.
[0019] The slurry is then poured into the filler column connected to contained 10 of Figure
1 and 2, with the filler column and container under vacuum. The alumina containing
slurry is then permitted to settle into container 10 for a given settling period,
for example, 36 hours. During this settling period, the unit and column are tilted
to different orientations to eliminate Rankine slope effects. During the settling
period, oil at the top of the column is decanted and is replaced with the 70% to 30%
by volume slurry.
[0020] At the end of the settling period, the alumina particles will reach a packing density
in excess of 80% by volume of the slurry.
[0021] The assembly is then placed in a centrifugal apparatus and is rotated at a moderate
"g" force to cause the aluminium oxide particles to compact further. The compacted
particles now form an almost solid paste-like body which adheres to all exposed surfaces
within housing 10 and which encapsulates all components within the housing.
[0022] Thereafter, excess silicone fluid is drawn off from the top of the column and the
column is removed. The paste, which extends above the top of container 10, is sliced
through at the column to container joint.
[0023] A conductive lid 30 is then fastened to the top of housing 10. A compressible synthetic
rubber pad 31 is fixed to the interior of lid 31 to keep the paste under positive
pressure within housing 10.
[0024] Paste compacted in this way and employing aluminium oxide particles has a thermal
conductivity of the order of 0.07 cal. per second cm °C. as compared with a thermal
conductivity of 0.084 cal. per second cm °C, for the solid material.
[0025] After filling, small cavities may appear within the paste as a result of thermal
movement. These cavities are not important to thermal behavious, but they could be
significant in terms of formation of corona discharge. However, oil in and around
the alumina will fill these cavities as they form to prevent electrical breakdown
within the cavities.
[0026] If the interior of the volume contains large voids, a relatively large volume of
powder would be needed to fill the interior free volume. This interior volume can
be reduced by filling with solid filler blocks such as filler blocks 34 and 26 in
Figure 1. These blocks can have any desired shape and reduce the volume of compacted
particles needed to fill the housing interior. The filler blocks 34 and 36 may be
of the same ceramic material as the particles of the slurry and, in the preferred
example, are of aluminium oxide.
[0027] In a specific example of the invention, the electrical components 12 through 22 were
capable of having a working surface temperature of 220°C. The mean free path distances
from the surfaces of components 12 and 14 and of components 16, 18, 20 and 22 collectively
was 25mm (1 inch), 10mm (0.375 inch) and 25mm (1 inch) respecitvely, and their effective
areas were 13 square cm (2 square inches), 52 square cm (8 square inches) and 26 square
cm (4 square inches) respectively. The novel thermally paste of the invention encapsulated
and coupled these components to the surfaces of housing 10 so that the housing 10
had a temperature of about 210°C., indicating a temperature differential across the
thermally conductive insulating material of only 10°C.
[0028] In another example, a magnetic/rectifier module of a 550 watt inverter, working at
1 watt per cubic cm (16 watts per cubic inch) had an internal dissipation of the order
of 30 watts. The steady state temperature difference between the center of the module
and the outside walls was less than five centigrade degrees.
[0029] It is important to examine the variation of thermal conductivity for the encapsulating
material with the proportion of filler. This is tabulated in the following table for
two theoretical materials, one a thermally conductive powder and one a fluid. The
thermal conductivities are shown for three alternative thermal conductivity ratios
of the powder to fluid of 10:1, 100:1, 1000:1.
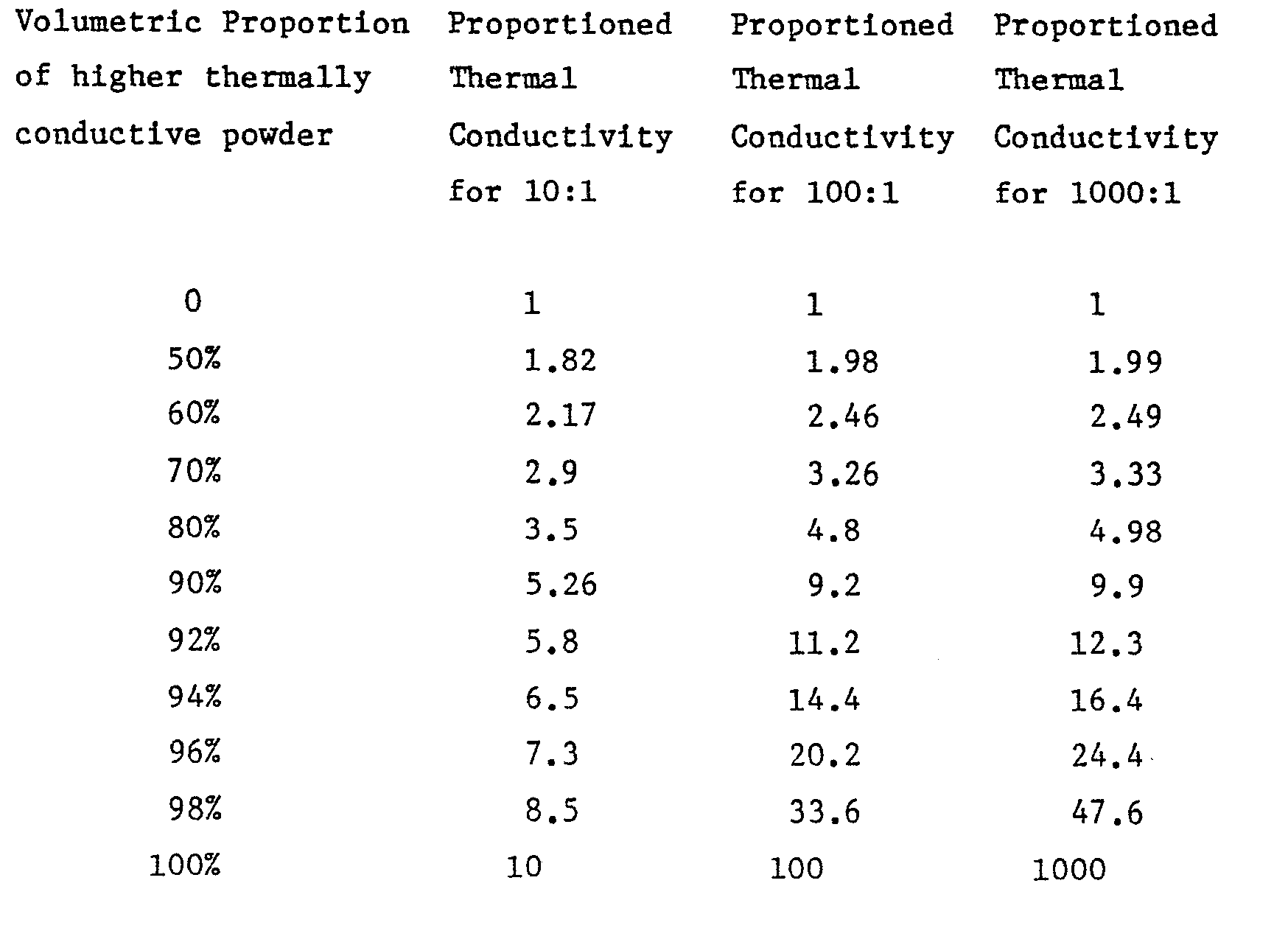
[0030] It is seen that for proportions of the higher thermal conductivity material, up to
about 70% by volume, there is no significant difference in the achieved thermal conductivity,
irrespective of whether the conductivity ratios are 10:1, 100:1 or 1000:1. This result
covers the range of proportions which can be obtained with loaded encapsulatinf resins
(due to limitations in pour and infill), and shows the restriction imposed by the
resin itself.
[0031] The table also shows that it would be valuable to achieve volumatic fill proportions
of the more conductive material of greater than about 80%, and specifically in the
range from 90% to 96%, and thereby obtain a significant proportion of the available
benefits of the material with a ratio of 100:1. The table also shows that the benefits
of a 1000:1 material cannot be obtained until a loading of virtually 100% hase been
achieved.
[0032] Although a preferred embodiment of this invention has been described, many variations
and modifications will now be apparent to those skilled in the art, and it is therefore
preferred that the instant invention be limited not be the specific disclosure herein,
but only by the appending claims.
1. A thermally-conducting filler for enclosing electrical components contained in
a housing, characterised by an easily-flowing slurry comprising at least 50% by volume
of thermally-conducting electrically-insulating particles suspended in a dielectric
fluid.
2. A filler as claimed in Claim 1 characterised in that said particles have a mean
diameter of 150 microns.
3. A filler as claimed in either of Claims 1 or 2 characterised in that the particles
are formed from a ceramic material.
4. A filler as claimed in Claim 3 characterised in that the ceramic material is selected
from the group comprising metal oxides, metal nitrides and metal carbides.
5. A filler as claimed in any one of Claims 1 to 4 characterised in that the dielectric
fluid is a silicone oil.
6. A method of filling a housing containing electrcal components characterised by
the steps of filling the interior of the housing with a filler as claimed in any one
of the preceding claims, and compacting the suspended particles to form a non-flowable
but deformable paste.
7. A method as claimed in Claim 6 characterised in that the filler material is initially
compacted by gravitational settling.
8. A method as claimed in Claim 7 characterised in that the filler is subsequently
compacted by being subjected to centrifugal force.
9. A method as claimed in Claim 8 characterised in that the non-flowable paste comprises
at least 80% by volume of said particles.
10. A method as claimed in any one of CLaims 6 to 9 characterised in that spaces within
the housing are partially filled with homogeneous solid blocks of thermally-conducting
electrically-insulating material prior to filling the remaining space with said filler.