[0001] This invention relates to a spheroidal graphite cast iron which has a high resistance
of oxidation at high temperatures.
[0002] In many fields it is often desired to use a spheroidal graphite cast iron as a structural
material in an apparatus or device which is operated at high temperatures. In the
automobile industry, for example, the turbine housing of an exhaust gas turbocharger
is usually made of a spheroidal graphite cast iron. Sometimes a high silicon spheroidal
graphite cast iron having a ferrite matrix is employed as the material of the turbine
housing. For example, such a spheroidal graphite cast iron contains 3.0 to 3.4 wt%
of C, 3.65 to 4.10 wt% of Si, up to 0.6 wt% of Mn, up to 0.5 wt% of Ni, 0.5 to 0.7
wt% of Mo and up to 0.07 wt% of Cr. Spheroidal graphite cast irons of this class are
relatively low in price and are generally satisfactory in mechanical properties, but
have an unsatisfactorily low resistance to oxidation at high temperatures.
[0003] To meet the high temperature oxidation resistance requirement, it becomes necessary
to employ a high nickel-chromium spheroidal graphite cast iron commonly called niresist.
For example, a spheroidal graphite cast iron of this class contains up to 3.0 wt%
of C, 1.5 to 3.0 wt% of Si, 0.70 to 1.25 of Mn, 18.0 to 22.0 wt% of Ni and 1.75 to
2.75 wt% of Cr, and another cast iron of the. same class contains up to 2.4 wt% of
C, 1.0 to 2.8 wt% of Si, up to 1.0 wt% of Mn, 34.0 to 36.0 wt% of Ni and 2.0 to 3.0
wt% of Cr. However, cast irons of this class are very costly due to their Ni content,
and, further such cast irons are relatively low in strength (e.g. about 40 kgf/mm
2 in tensile strength and about 20 kgf/mm
2 in 0.2% proof stress) and also in toughness (e.g. below 10% in elongation).
[0004] It is an object of the present invention to provide a spheroidal graphite cast iron
which is satisfactory in both mechanical properties and resistance to oxidation at
high temperatures and is lower in production costs than the conventional high nickel
spheroidal graphite cast irons.
[0005] The present invention provides a heat-resistant spheroidal graphite cast iron which
consists of not more than 3.4 wt% of C, 3.5 to 5.5 wt% of Si, not more than 0.6 wt%
of Mn, 0.1 to 0.7 wt% of Cr, 0.3 to 0.9 wt% of Mo, not more than 0.1 wt% of a spheroidizing
agent and the balance of Fe plus impurities. The matrix of this cast iron is principally
ferrite.
[0006] Preferably the C content of the cast iron of the invention is not less than 1.7 wt%
and the Cr content is not less than 0.25 wt%.
[0007] A spheroidal graphite cast iron according to the invention is comparable to, and
sometimes better than conventional high silicon spheroidal graphite cast irons in
mechanical properties and distinctly superior in resistance to oxidation at high temperatures
such as 700-1000°C. The favourably balanced properties of the cast iron of the invention
are realized by correlatively specifying the contents of Si and Cr within the above
indicated ranges. Compared to conventional high nickel spheroidal graphite cast irons,
a spheroidal graphite cast iron of the invention is higher in strength and nearly
equivalent in the resistance to oxidation at relatively low temperatures and, as an
industrially important factor, can be prepared at a far lower cost.
[0008] In the following description reference will be made to the accompanying drawings
in which:
Figs. 1 and 2 are graphs showing the results of experiments to determine the dependence
of the oxidation resistance of a spheroidal graphite cast iron at high temperatures
with relation to the Si content of the cast iron;
Fig. 3 is a chart showing the ferritizing heat treatment conditions employed in the
preparation of a cast iron as an example of the invention;
Fig. 4 is a graph showing the result of experiments to determine the oxidation resistance
of spheroidal graphite cast irons prepared as examples of the invention at high temperatures
in comparison with examples of conventional spheroidal graphite cast irons; and
Fig. 5 is a photomicrograph showing the structure of a spheroidal graphite cast iron
prepared as an example of the invention.
[0009] A heat-resistant spheroidal graphite cast iron according to the invention has the
composition specified above. The effects of the respective alloying elements and the
reasons for the limitations on the amounts of the respective elements are as follows.
Throughout the following description, the amounts of the elements in the cast iron
are given in percentages by weight.
(1) Carbon
[0010] C is an alloying element indispensable to cast iron. In the cast irons of the present
invention the C content is limited to a maximum of 3.4 because the presence of more
than 3.4% of C tends to cause crystallization of an excessively large quantity of
graphite and a reduction in the strength and toughness of the cast iron. If the C
content is too low, the cast iron becomes inferior in its properties mainly because
of insufficiency in the crystallization of graphite and a reduction in the fluidity
of the molten metal. In most cases this tendency becomes significant if the C content
is less than about 1.7%. Therefore, it is preferred that a spheroidal graphite cast
iron according to the invention contains at least 1.7% of C.
(2) Silicon
[0011] In general Si is added to cast iron for the purpose of achieving graphitization.
In the cast irons of the present invention the Si content is specified to be higher
than in ordinary spheroidal cast irons with the additional purpose of enhancing the
oxidation resistance of the cast iron.
[0012] To examine the general relationship between the content of Si in spheroidal graphite
cast iron and the oxidation resistance of the cast iron at high temperatures, an experiment
was carried out using a conventional spheroidal graphite cast iron FCD 40 (according
to JIS G 5502) containing 2.90% of Si (together with about 3.4% of C, about 0.4% of
Mn, about 0.05% of Mg, about 0.02% of P and about 0.01 % of S) and by preparing modified
samples in which the content of Si was increased to 3.28%, 4.86% and 5.56%, respectively.
Test pieces of the four cast iron samples were kept heated in air at either 600°C
or 700°C for a total period of 500 hr, and the thickness of an oxidized scale layer
on each test piece was measured at suitable time intervals to estimate the oxidation
resistance of each cast iron sample on the basis of the maximum thickness of the scale
layer in each sample. The results of these experiments at 600°C and at 700°C are shown
in Figs. 1 and 2 of the drawings, respectively. From the curves in Figs. 1 and 2 it
is apparent that the oxidation resistance of the cast iron can be enhanced by increasing
the content of Si.
[0013] However, if the content of Si is increased too much the resultant spheroidal graphite
cast iron suffers from insufficient elongation and unfavourable brittleness at ambient
temperature. Considering such tendencies, the content of Si in the cast irons of the
present invention is limited within the range from 3.5% to 5.5%.
(3) Chromium
[0014] In a spheroidal graphite cast iron of the invention, Cr is an alloying element which
contributes to reinforcement of the oxidation resistance of the cast iron at high
temperatures. The minimum Cr content is set at 0.1 % because the expected effects
are insufficient if the Cr content is less than 0.1 %. Since the effect of reinforcing
the ferrite matrix augments as the Cr content is increased, it is preferred that the
Cr content of the cast irons of the present invention is at least 0.25%. However,
the content of Cr is limited to a maximum of 0.7% because the addition of more than
0.7.% of Cr is liable to deteriorate the workability and other mechanical properties
of the cast iron by reason of formation of free carbides.
(4) Molybdenum
[0015] Mo has the effect of reinforcing the ferrite matrix of the cast iron and thereby
enhancing the high temperature strength of the cast iron. The expected effect is insufficient
if the Mo content is below 0.3%. However the Mo content is limited to a maximum of
0.9% because the addition of more than 0.9% of Mo is liable to cause formation of
free carbides and to result in a deterioration of the mechanical properties of the
cast iron.
(5) Manganese
[0016] Mn is an alloying element having a desul- phurizing ability. The content of Mn is
limited to a maximum of 0.6% because the presence of an unnecessarily large amount
of Mn in the cast iron produces an unwanted effect of stabilizing pearlite in the
cast iron.
(6) Spheroidizing agent
[0017] In the cast irons of the present invention the spheroidizing agent may be freely
selected from known spheroidizing agents such as Mg, Ca and Ce for example. It is
undesirable to use an unnecessarily large amount of spheroidizing agent because of
its unfavourable side-effects. For example, the use of an unduly large amount of Mg,
which is a typical spheroidizing agent, has the unwanted effect of stabilizing cementite
in the cast iron. Therefore, the amount of the spheroidizing agent is limited to a
maximum of 0.1 %.
[0018] In practice, it is permissible that a spheroidal graphite cast iron of the invention
contains very small amounts of impurities besides the above described essential alloying
elements and Fe. Typical examples of such impurity elements are phosphorus and sulphur.
It is preferred that the P content is below 0.1 % because a higher P content is detrimental
to the workability, typified by ductility, of the cast iron. Also it is preferred
that the S content is below 0.1 % because a higher S content is obstructive to spheroidization
of graphite.
[0019] A spheroidal graphite cast iron of the invention can be prepared by a known method
of the preparation of a ferritic spheroidal graphite cast iron. In brief, a molten
metal of a suitable composition including a spheroidizing agent is allowed to solidify
in a mould, and the solidified casting is then subjected to a spheroidizing-ferritizing
heat treatment.
[0020] In order that the invention may be well understood the following Examples are given
by way of illustration only.
Example 1
[0021] A spheroidal graphite cast iron has the composition shown in Table 1 below was prepared
by a usual method, in which the solidified casting was subjected to a spheroidizing-ferritizing
annealing treatment under the conditions shown in Fig. 3 of the drawings. Besides
the elements listed in the Table, a small quantity of Mg was used as spheroidizing
agent so that the product contained 0.039% of Mg. As shown in Fig. 3, the annealing
treatment consisted of heating at 930°C for 2.5 hr, initial lowrate cooling from 930°C
to 300°C performed as furnace cooling and subsequent air cooling. Fig. 5 is a photomicrograph
(100xmagnification) showing the structure of the cast iron obtained in this way. The
structure of this cast iron may be expressed as being a ferrite matrix containing
spheroidal cementite and a very small portion of pearlite containing certain carbides
therein. That is, the cast iron was a ferritic spheroidal graphite cast iron.
Example 2
[0022] Another spheroidal graphite cast iron having the composition shown in Table 1 below
was prepared by the same method as described in Example 1. Besides the elements noted
in the Table, 0.045% of Mg was present in the product by reason of the use of Mg as
spheroidizing .agent. The structure of this cast iron was fundamentally similar to
that of the cast iron of Example 1. As can be seen in the Table, substantially the
sole difference of the cast iron of Example 2 from that of Example 1 was about a 45%
decrease in the Cr content accompanied by a slight decrease in the Mo content.
[0023] Test pieces cut out of the cast irons of Examples 1 and 2 were subjected to tensile
strength tests at ambient temperature and also to oxidation resistance tests at high
temperatures. For comparison, a conventional high nickel spheroidal graphite cast
iron (Reference 1) and a conventional ferric spheroidal graphite cast iron (Reference
2) were subjected to the same tests. The compositions of the cast irons of References
1 and 2 are shown in Table 1 below. In addition to the elements noted in the Table,
the cast irons of the References 1 and 2 contained 0.080% of Mg and 0.070% of Mg,
respectively.
[0024] Each test piece for the tensile strength test was 50 mm in gauge length, 70 mm in
the length of the straight portion and 7 mm in the diameter of the straight portion,
and the straining speed at the test was 20% min. The result of the test is presented
in Table 1.
[0025] The oxidation resistance test was carried out at 750°C, 850°C and 950°C. At each
temperature the test pieces were kept heated in air for 200 hr, and the oxidation
resistance of each sample was estimated from the maximum thickness of an oxidised
scale layer on each test piece. Fig. 4 shows the results of these tests.
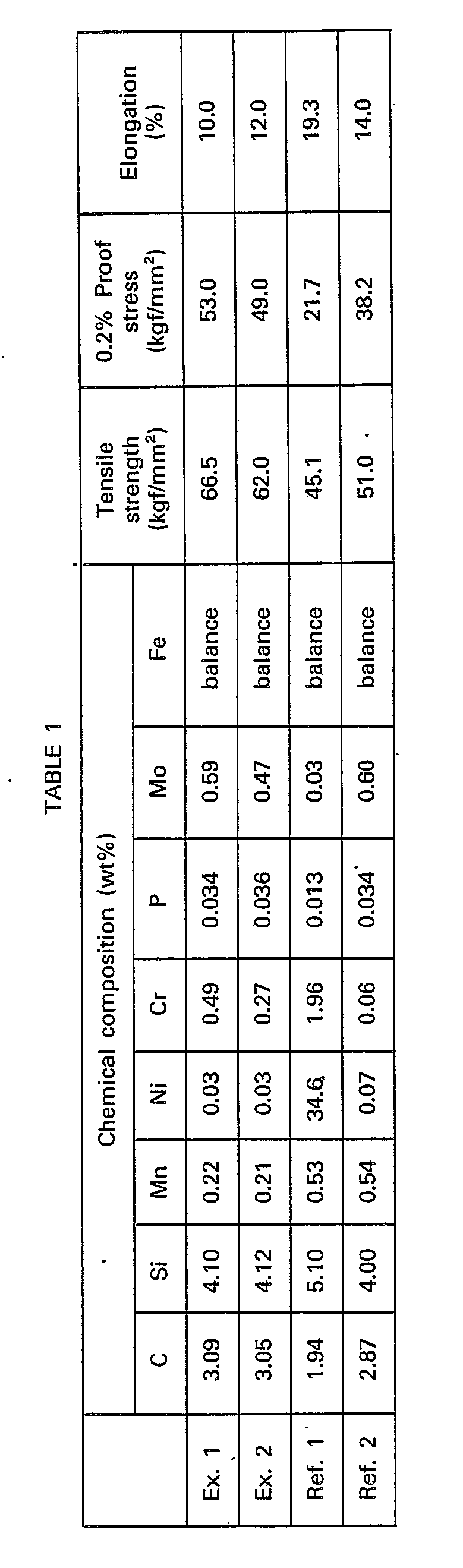
[0026] As can be seen from Table 1, the spheroidal graphite cast irons of Examples 1 and
2 were both superior in the tensile strength and proof stress to the conventional
spheroidal cast irons of References 1 and 2. Also it can be seen that the cast irons
of Examples 1 and 2 were inferior in the elongation to the cast irons of References
1 and 2. However, the 10% and 12% elongation values indicate that either of the cast
irons of Examples 1 and 2 is fully satisfactory as a material for turbine housing
of automotive exhaust gas turbochargers, for example.
[0027] As shown in Fig. 4, the spheroidal graphite cast irons of Examples 1 and 2 were higher
in resistance to oxidation than the conventional spheroidal graphite cast iron of
Reference 2 over the entire range of high temperatures in this test. At 750°C the
cast irons of Examples 1 and 2 were even comparable in oxidation resistance to the
high nickel spheroidal graphite cast iron of Reference 1. At higher temperatures the
oxidation resistance of the cast irons of Examples 1 and 2 became lower than that
of the cast irons of Reference 1, but this fact does not seriously affect the merit
of the invention firstly because the high nickel cast iron of Reference 1 is far more
costly that the cast irons according to the invention and secondly the oxidation resistance
values of the cast irons of Examples 1 and 2 at 850°C and 950°C can be taken as very
good values.
1. A heat-resistant ferritic spheroidal graphite cast iron, characterised in that
it consists of not more than 3.4 wt% of C, 3.5 wt% to 5.5 wt% of Si, not more than
0:6 wt% of Mn, 0.1 to 0.7 wt% of Cr, 0.3 to 0.9 wt% of Mo, not more than 0.1 wt% of
spheroidizing agent and the balance of Fe plus impurities.
2. A spheroidal graphite cast iron according to Claim 1, characterized in that it
contains at least 1.7 wt% of C.
3. A spheroidal graphite cast iron according to claim 1 or claim 2, characterized
in that it contains from 0.25 to 0.7 wt% of Cr.
4. A spheroidal graphite cast iron according to anyone' of the preceding claims characterized in that the principal component of the spheroidizing
agent is Mg, Ca or Ce.
5. A turbine housing of an automotive exhaust gas turbo charger made of an alloy as
claimed in any one of the preceding Claims.
1. Hitzebeständiges, ferritisches Gusseisen mit Kugelgraphit, dadurch gekennzeichnet,
daß es aus nicht mehr als 3,4 Gew.% C, 3,5 Gew.% bis 5,5 Gew.% Si, nicht mehr also
0,6 Gew.% Mn, 0,1 bis 0,7 Gew.% Cr, 0,3 bis 0,9 Gew.% Mo, nicht mehr als 0,1 Gew.%
Verkugelungs-Wirkstoff und im übrigen aus Eisen und Verunreinigungen besteht.
2. Gusseisen mit Kugelgraphit nach Anspruch 1, dadurch gekennzeichnet, daß es zumindest
1,7 Gew.% C enthält.
3. Gusseisen mit Kugelgraphit nach Anspruch 1 oder 2, dadurch gekennzeichnet, daß
es 0,25 bis 0,7 Gew.% Cr enthält.
4. Gusseisen mit Kugelgraphit nach einem der vorhergehenden Ansprüche, dadurch gekennzeichnet,
daß die Hauptkomponente des Verkugelungs-Wirkstoffes Mg, Ca oder Ce ist.
5. Turbinengehäuse- eines Kraftfahrzeug-Abgasturboladers, hergestellt aus einer Legierung
nach einem der vorhergehenden Ansprüche.
1. Fonte ferritique à graphite sphéroïdal, résistant à la chaleur, fonte caractérisée
en ce qu'elle consiste en pas plus de 3,4% en poids de C, 3,5% en poids à 5,5% en
poids de Si, pas plus de 0,6% en poids de Mn, 0,1 à 0,7% en poids de Cr, 0,3 à . 0,9%
en poids de Mo, pas plus de 0,1% en poids d'un agent d'obtention de graphite sphéroïdal,
le reste étant constitué par du fer plus des impuretés.
2. Fonte à graphite sphéroïdal selon la revendication 1, caractérisée en ce qu'elle
contient au moins 1,7% en poids de C.
3. Fonte à graphite sphéroïdal selon la revendication 1 ou la revendication 2, caractérisée
en ce qu'elle contient de 0,25 à 0,7% en poids de Cr.
4. Fonte à graphite sphéroïdal selon l'une quelconque des revendications précédentes,
caractérisée en ce que le principal constituant de l'agent d'obtention de graphite
sphéroïdal est Mg, Ca ou Ce.
5. Enveloppe de turbine d'un turbocompresseur à gaz d'échappement d'automobile, enveloppe
réalisée en un alliage tel que revendiqué dans l'une quelconque des revendication
précédentes.