[0001] This invention relates to a method for improving the grinding of titaniferous ores
and increasing the amount of recovery of titanium dioxide from said ores.
[0002] The first step in the sulfuric acid process for recovery of titanium dioxide from
titaniferous ores, is to grind the ore to a desired particle size. Next the ore is
digested with sulfuric acid to yield a digestion cake which consists essentially of
water-soluble sulfates of titanium and iron, as well as minor impurities. After dissolution
of the digestion cake in either water or dilute sulfuric acid, the recovery of titanium
can be determined by comparing (a) the titanium assay and weight of the ore to (b)
the titanium assay and volume of the resulting solution.
[0003] The sulfuric acid process for preparing titanium dioxide from titaniferous ores is
conducted on a large scale and thus, even a small increase in the recovery of titanium
dioxide can be commercially important. For example, for a 25 ton batch of titaniferous
ore containing 64.6% titanium dioxide, a change in the titanium dioxide recovery from
84.5% to 89% represents a 29% decrease in unrecovered, or wasted titanium dioxide,
and 1400 pounds extra titanium dioxide actually recovered. So, any increase in the
efficiency of comminution of a titaniferous ore will result in a worth-while saving
even though the unit saving may appear small.
[0004] Canadian Patent No. 962,003 discloses the application of propane diol to pigmentary
titanium dioxide, following its preparation by either of the well known sulfuric acid
or chloride processes, to improve the dispersibility characteristics of the pigment,
particularly in paints; and U.S. Patent No. 3,076,719 describes a treatment of similarly
produced titanium dioxide pigment with a polyol of from 4 to 10 carbon atoms which
prevents clumping during storage.
[0005] U.S. Patent No. 2,822,241 discloses the addition of a glyceride, particularly a monoglyceride,
to a titaniferous ore containing organic flotation agents to improve the digestion
of the ore in sulfuric acid.
[0006] While the prior art discloses use of polyols to improve the qualities of recovered
titanium dioxide and the digestion of titaniferous ores, as hereinabove described,
the present invention provides as a major object a method whereby the comminution
of titaniferous ores may be conducted more efficiently, with the use of certain polyols,
so that the recovery of titanium dioxide from said ores upon digestion may be enhanced.
Further objects and advantages of the invention will become apparent from the description
of the invention which ensues.
[0007] In accordance with the objects of the present invention, it has been found that certain
polyols, when added to an unground titaniferous ore, can increase the efficiency of
comminution of the ore.
[0008] The polyols used in the method of the present invention have the formula:

wherein R is alkyl (C,-C
4), or hydroxyalkyl (C,-C
4) containing up to 3 hydroxy groups, and wherein R' is alkylene (C,-C
3). Preferably, R is alkyl (C,-C
3) and R' is methylene. Most preferably, R is ethyl and R' is methylene. The polyols
are preferably stable and wettable in concentrated sulfuric acid at ambient temperatures
(25°C, to 35°C.), but tend to be less stable at the digestion reaction temperature.
Suitable such compounds include trimethylolpropane, 1-hydroxy-2,2-dimethylolpropane;
1-hydroxy-2,2-dimethylol- pentane; 1-hydroxy-3,3-diethylolpentane; 1,3-dihydroxy-2,2-dimethylolbutane,
and pentaerythritol.
[0009] The polyol is added to the titaniferous ore in an amount effective to improve the
comminution thereof. Generally this amount will be from about 0.005% to about 2% by
weight of the ore, desirably from about 0.05% to about 1 %, and preferably from about
0.07% to about 0.5%. However, more of the polyol may be added if so desired.
[0010] By the introduction of the polyol to the ore either prior to or during comminution,
the comminution is rendered more efficient and the ultimate recovery of titanium dioxide
from the ore, upon digestion thereof in sulfuric acid, is enhanced. The polyol appears
to act as an anti-caking agent for the ore during comminution, resulting in a more
rapid reduction of ore particle size. The smaller particles, in turn, are believed
to be better wetted by the sulfuric acid, thereby yielding a higher recovery of titanium
dioxide.
[0011] In addition to enhancing the comminution of the titaniferous ore, the continued presence
of the polyol in the sulfuric acid digestion medium apparently further augments the
recovery of titanium dioxide from the ore.
[0012] The following examples are provided for illustrative purposes and may include particular
features of the invention. However, the examples should not be construed as limiting
the invention, many variations of which are possible without departing from the spirit
or scope thereof. All parts and percentages are by weight unless otherwise noted.
Example 1
[0013] In this example, the effectiveness of trimethylolpropane (TMP), corresponding to
the above polyol formula wherein R is ethyl and R' is methylene, as a grinding aid
in the size reduction of a Florida ore from a deposit in Green Cove Springs is shown.
[0014] A typical chemical assay of this Florida ore, which is weathered beach sand, reveals
hat the titanium dioxide content thereof is 64.6%.
[0015] A 1500 g. sample of the ore was first dried at 110°C. to less than 0.2% water and
then placed in a gallon ball jar containing 7500 g. of 2.54cm (1 inch) steel balls.
The ball jar was rotated at 53 rpm for the lengths of time shown in Table I below.
At the conclusion of the selected grind times, the ball jar was emptied and the ore
particle size determined on a 100 g. sample by sifting in a.Tyier Ro-Tap through a
bank of sieves ranging from 100 to 325 mesh (0.147 to 0.043 mm) (Tyler-U.S. Standard)
for 30 minutes.
[0016] Table 1 demonstrates that for grind times of 30 minutes and 360 minutes, more -325
mesh (0.043 mm) particles were produced when TMP in an amount of 0.1 % was added to
the ore. For this procedure, regular commercially used steel balls, which were not
polished, were employed..
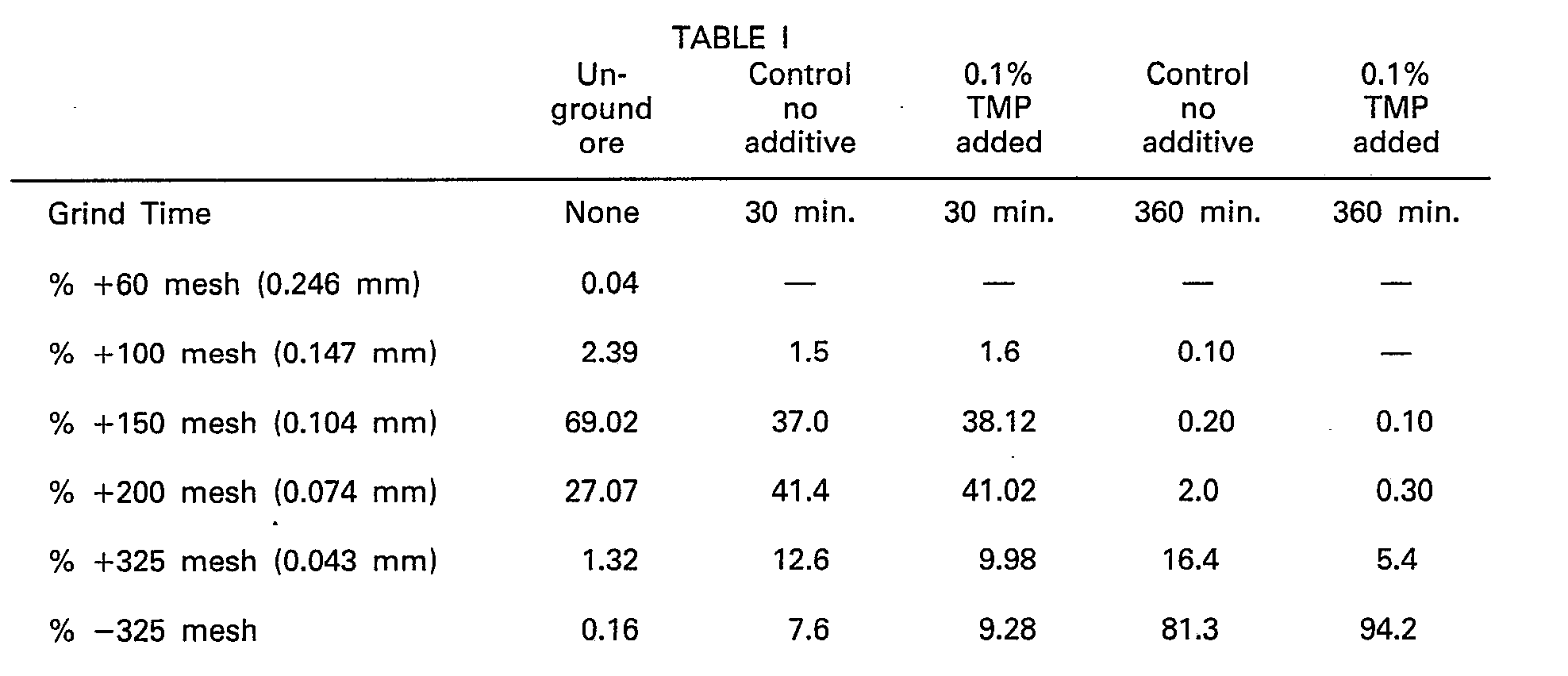
Example 2
[0017] This example shows the improvement in titanium dioxide recovery when a titaniferous
ore which was ground using a polyol as a grinding aid is digested with sulfuric acid.
[0018] The method used in this example closely approximates the industrial digestion process,
so the results received here are representative of results which would be expected
on an industrial scale.
[0019] Specifically, four separate 1000 g. samples of the titaniferous ore comminuted for
equal times as in Example 1, two samples with, and two samples without, the addition
of 0.1 % TMP, were wetted with 98% sulfuric acid for 30 minutes. Each mixture of ore
and sulfuric acid was then heated to 115°C. over periods ranging from 19 to 31 minutes,
while 60 ml. of water was added to simulate the dilution which occurs in the industrial
process when high pressure steam (2.76 bar) (40 psig) is introduced into the mixture.
End liquor, i.e., the mother liquor which remains after the titaniferous liquor is
hydrolyzed to yield titanium dioxide, was then added to achieve the desired ratio
of sulfuric acid to basic oxides in the ore. The end liquor contained about 20% sulfuric
acid, and a sufficient quantity was added so that after the valences of all other
recoverable sulfatable ore components had been satisfied, there remained enough sulfuric
acid to satisfy between 65 and 80% of the titanium valences with sulfate ions. The
samples were digested in the acid solution at temperatures of about 180―190°C. for
about 2 1/2 hours. Thereupon, the resulting digestion cakes were dissolved in water
to form a titaniferous liquor which was analyzed for titanium dioxide content, and
the results compared with the analysis of the original ore, to determine the titanium
dioxide recovery. The determination of recovery can be made using any well known method,
e.g., reduction of the titanium (IV) to titanium (III) with zinc amalgam and titration
of the reduced titanium with ferric ammonium sulfate to a thiocyanate end-point.
[0020] It was found upon analysis that the average recovery of titanium dioxide from the
two samples which had been comminuted with trimethylolpropane was 86.5%. For the two
samples comminuted without the use of trimethylolpropane, the average recovery was
only 80%.
Example 3
[0021] The procedure of Example 1 is repeated, except that the trimethylolpropane is replaced
by an equal weight amount of 1-hydroxy-2,2-dimethylolpropane; 1-hydroxy-2,2-dimethylolpentane;
1-hydroxy-3,3-di- ethylolpentane; 1,3-dihydroxy-2,2-dimethylolbutane, and pentaerythritol.
[0022] Similar improved comminution of the ore is observed.
Example 4
[0023] The procedure of Example 1 is repeated, except that trimethylolpropane in amounts
equal to 0.005%, 0.05%, 0.5%, 1% and 2% is added to the ore.
[0024] Similar improved comminution of the ore is observed.
1. A method for improving the comminution of a titaniferous ore which comprises adding
to said ore a polyol having the formula:

wherein R is alkyl (C
1―C
4) or hydroxyalkyl (C
1―C
4) containing up to three hydroxy groups and wherein R' is alkylene (C
1―C
3), in an amount effective to reduce the particle size of the ore as a result of the
comminution.
2. The method of Claim 1 wherein R of the formula R―C(̵R'OH)3 is alkyl (C1―C4) and R' of said formula is. methylene.
3. The method of Claim 1 wherein the polyol is trimethylolpropane.
4. The method of Claim 1 wherein the polyol is present in an amount equal to from
about 0.005% to about 2% by weight of the ore.
5. The method of Claim 1 wherein the polyol is present in an amount equal to from
about 0.05% to about 1% by weight of the ore.
1. Verfahren zur Verbesserung der Aufbereitung eines titanhaltigen Erzes, wobei man
dem Erz ein Polyol der Formel

zusetzt, wobei R für Alkyl (C
1-C
4) oder Hydroxyalkyl (C
1―C
4), enthaltend bis zu drei Hydroxygruppen, steht und wobei R' für Alkylen (C
1-C
3) steht, in einer Menge, die wirksam ist zur Verringerung derTeilchengröße des Erzes
als Ergebnis der Aufbereitung.
2. Verfahren nach Anspruch 1, wobei R in der Formel R―C(̵R'OH)3 für Alkyl (C1-C4) steht und R' in der Formel für Methylen steht.
3. Verfahren nach Anspruch 1, wobei das Polyol Trimethylolpropan ist.
4. Verfahren nach Anspruch 1, wobei das Polyol in einer Menge vorliegt, die etwa 0,005
bis etwa 2 Gew.-% des Erzes ausmacht.
5. Verfahren nach Anspruch 1, wobei das Polyol in einer Menge vorliegt, die etwa 0,05
bis etwa 1 Gew.-% des Erzes ausmacht.
1. Procédé visant à améliorer la pulvérisation d'un mineral titanifère, qui consiste
à ajouter audit mineral un polyol répondant à la formule:
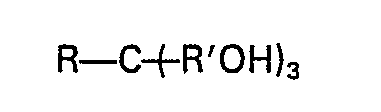
dans laquelle R est un groupe alkyle (C
1―C
4) ou hydroxyalkyle (C
1―C
4) contenant jusqu'à trois groupes hydroxy et dans laquelle R' est un groupe alkylène
(C
1―C
3), en une quantité efficace pour réduire la dimension particulaire du minerai conséquemment
à la pulvérisation.
2. Procédé selon la revendication 1, dans lequel R de la formule R-C+R'OH)3 est un groupe alkyle (C1―C4) et R' de ladite formule est le groupe méthylène.
3. Procédé selon la revendication 1, dans lequel le polyol est le triméthylolpropane.
4. Procédé selon la revendication 1, dans lequel le polyol est présent en une quantité
représentant d'environ 0,005% à environ 2% en poids du minerai.
5. Procédé selon la revendication 1, dans lequel le polyol est présent en une quantité
représentant d'environ 0,05% à environ 1% en poids du minerai.