Technical field
[0001] The present invention relates to amorphous alloys and articles made of said alloys
and particularly to amorphous alloys containing iron group elements and zirconium
and articles made of said alloys.
Background art
[0002] Solid metals or alloys generally possess crystalline structures but if a molten metal
is quenched rapidly (the cooling rate is approximately 10
4-10
6°C/sec), a solid having a non-crystalline structure, which is similar to a liquid
structure and has no periodic atomic arrangement, is obtained. Such metals or alloys
are referred to as amorphous metals or amorphous alloys (both merely referred to as
"amorphous alloys" hereinafter). It has been well known that these amorphous alloys
are obtained through vapour deposition, sputtering process, electrodeposition or chemical
(electroless) plating, and the like as well as the above described rapidly quenching
of the molten metal (see Japanese Patent Laid-Open Specification No. 91,014/74). In
general, metals of this type are alloys consisting of two or more elements and can
be classified into two groups, generally referred to as metal-metalloid alloys and
inter-metal (metal-metal) alloys.
[0003] As the former embodiment, Fe-Ni-P-B (Japanese Patent Laid-Open Specification No.
91,014/74), Fe-Co-Si-B (Japanese Patent Laid-Open Specification No. 73,920-76), and
the like have been known.
[0004] As the latter embodiment, only U-Cr-V (Japanese Patent Laid-Open Specification No.
65,012/76) has been recently reported, except for Zr
60Cu
40, Zr
78Co
22, and the like, which were reported previously. Particularly, as amorphous alloys
of a combination of iron group elements and IVB, VB Group elements which contains
less than 50 atomic % of IVB or VB Group elements, only Nb
100-xNi
x (x: 33―78) and Zr
100-xNi
x (x: 40―60) have been known.
[0005] U.S. Patent No. 4 059 441 discloses metal-base glasses of the general formula R
rNi
sT
t, where R=Ta, Nb, and/or W, T=Ti and/or Zr, r=35 to 65 atomic%, s=25 to 65 atomic%,
and t=0 to 15 atomic%.
[0006] Already known amorphous alloys of combination of iron group elements and metalloid,
for example, Fe-P-C or Fe-Ni-P-B have excellent properties in view of strength, hardness,
magnetic properties, and the like; however, the structure of these alloys is unstable,
so that the properties are considerably varied during ageing and this is a great practical
drawback. In addition, it has been known concerning the heat resistance that embrittlement
occurs even at a lower temperature than the crystallization temperature as well as
at a higher temperature than the crystallization temperature.
[0007] On the other hand, in metal-metal amorphous alloys, it has been known that the content
of elements having a small atomic radius is not large, so that embrittlement at a
lower temperature than the crystallization temperature scarcely occurs. Even at a
higher temperature than the crystallization temperature, the extent of embrittlement
of these amorphous alloys is smaller than that of metal-metalloid amorphous alloys.
[0008] However, previously reported metal-metal amorphous alloys contain a large amount
of IVB and VB Group elements (Ti, Zr, V, Nb, Ta), so that the cost of raw material
is very high and the melting point of those alloys is high and the molten metal is
easily oxidized, therefore the production of these amorphous alloys is very difficult,
so there is a disadvantage with difficulties in production of ribbon, sheet and wire
in good shapes, which can be utilized for practical usages in industries. Furthermore,
a problem exists that the strong ferromagnetic property which is characteristic to
iron group elements, is lost.
[0009] An object of the present invention is to provide metal-metal amorphous alloys in
which the above described drawbacks and problems of already known metal-metalloid
amorphous alloys or metal-metal amorphous alloys are obviated and improved.
Disclosure of invention
[0010] The present invention can accomplish the above described object by providing amorphous
alloys containing iron group elements and zirconium as described hereinafter (1) and
(2) and articles made of said amorphous alloys.
(1) Amorphous alloys containing iron group elements and zirconium and having the composition
defined by the following formula
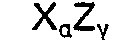
wherein X° shows that at least one element selected from the group consisting of Fe,
Co and Ni is contained in an amount of a atomic%, Zy shows that Zr is contained in
an amount of y atomic%, the sum of a and y is 100 and a is 80 to 92 and y is 8 to
20.
(2) Amorphous alloys containing iron group elements and zirconium and having the composition
defined by the following formula
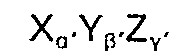
wherein XQ. shows that at least one element selected from Fe, Co and Ni is contained in an amount
of a' atomic%;
Yp. shows that at leat one element selected from Cr, Mo and W belonging to VIB Group,
Ti, V, Nb and Ta belonging to IVB or VB Group, Mn and Cu of transition metals, Be,
B, Al, Si, In, C, Ge, Sn, N, P, As, and Sb belonging to IIA, IIIA, IVA or VA Group
and lanthanum group elements is contained in an amount of (3' atomic%; and
Xγ, shows that Zr is contained in an amount of γ' atomic%, the sum of α', β' and γ'
being 100; and wherein
(A) Y is at least one element selected from the group consisting of Cr, Mo and W,
α' is 60 to 92, β' is not more than 20 and γ' is 5 to 20, provided that the sum of
β' and γ' is not less than 8, or
(B) Y is at least one element selected from the group consisting of Ti, V, Nb, Ta,
Cu and Mn, a' is 60 to 92, P' is not more than 20, γ' is 5 to 20, provided that the
sum of β' and γ' is not less than 8, or
(C) Y is at least one element selected from the group consisting of Be, B, AI and
Si, a' is from 67 to less than 90, β' is less than 13 and γ' is from more than 10
to 20, or
(D) Y is at least one element selected from the group consisting of C, N, P, Ge, In,
Sn, As and Sb, a' is from 70 to less than 90, β' is not more than 10 and γ' is from
more than 10 to 20, or
(E) Y is at least one element selected from lanthanum group elements, α' is 70 to
92, β' is not more than 10 and y' is 8 to 20, or
(F) Y is at least one element selected from the group consisting of Be, AI and Si,
α' is 77 to 92, β' is less than 13 and γ' is 3 to 10, provided that the sum of β'
and γ' is not less than 8, or
(G) Y is at least one element selected from the group consisting of N, Ge, In, Sn,
As and Sb, a' is 80 to 92, β' is not more than 10 and γ' is 5 to 10, provided that
the sum of β' and γ' is not less than 8, or
(H) Y is B, α' is 85 to 92, β' is not more than 5,γ' is 3 to 10, provided that the
sum of β' and γ' is not less than 8, or
(I) Y is at least one element selected from the group consisting of C and P, a' is
83 to 92, P' is less than 7 and y' is 5 to 10, provided that the sum of (3' and y'
is not less than 8, or
(J) Y consists of elements from at least two groups selected from the above described
groups combined, β' is within the range of β' value in each of the selected groups
and the total value of β' is not more than 20, α' is 60 to 92, γ' is 5 to 20 and the
sum of β' and γ' is not less than 8, but when γ' exceeds 10 and is not more than 20,
the Y elements are selected from the groups (A), (B), (C), (D) and (E), but the sum
of the Y elements selected from the groups (C) and (D) is always less than 13, and
when y' is 5 to 10, the Y elements are selected from the groups (A), (B), (E), (F),
(G), (H) and (I) but the sum of the Y elements selected from the groups (F) and (G)
is always less than 13, the sum of the Y elements selected from the groups (H) and
(I) is always less than 7 and the total sum of the Y elements selected from the group
(F) and/or (G) and the Y elements selected from the group (H) and/or (I) is always
less than 7.
[0011] The inventors have found novel amorphous alloys which contain a small amount of 8
to 20 atomic% of Zr as an element which contributes to formation of amorphous alloys
of iron group elements of Fe, Co and Ni, scarcely causes variation of properties during
ageing or embrittlement, have excellent properties of strength, hardness, corrosion
resistance and heat resistance and do not deteriorate magnetic properties which are
characteristic to iron group elements, and accomplished the present invention.
Brief description of the drawings
[0012]
Fig. 1 is a graph showing relation between ageing temperature and fracture strain
8f of amorphous alloys of the present invention and well known metalloid amorphous alloys;
Figs. 2(a) and (b) are schematic views of apparatuses for producing amorphous alloys;
Fig. 3 is a graph showing relation between an amount of VIB Group elements added and
the crystallization temperature.
Best mode of carrying out the invention
[0013] A major part of amorphous alloys of the present invention have practically very useful
characteristics that these alloys can maintain the ductility and toughness even at
temperature close to the crystallization temperature as shown in Fig. 1 and that even
at a higher temperature than the crystallization temperature, the extent of embrittlement
is lower than that of amorphous alloys containing a large amount of metalloid.
[0014] In general, the embrittlement of amorphous alloys has been estimated by the process
wherein an amorphous alloy ribbon is put between two parallel plates and the distance
L between the parallel plates is measured and a value L when the sample ribbon is
fractured by bending, is determined and the fracture strain is defined by the following
formula
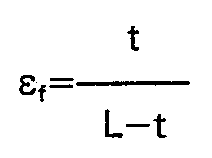
wherein t is the thickness of the ribbon. The inventors have measured the fracture
strain ε
f with respect to the samples maintained at each temperature for 100 minutes for comparison
of the amorphous alloys of the present invention with the metal-metalloid amorphous
alloys following to this method. The above described Fig. 1 shows that even though
the amorphous alloys of the present invention are lower in the crystallization temperature
Tx than (Co
94Fe
6)
0.7Si
15B
10 alloy which is relatively strong against the embrittlement among the metal-metalloid
amorphous alloys, the temperature at which the embrittlement starts, is 100°C higher
and this shows that the embrittlement is hardly caused. Such properties are very advantageous,
because the amorphous alloys of the present invention are not embrittled even by the
inevitable raised temperature in the heat treatment or production step, when the alloys
are used for tools, such as blades, saws, etc., for hard wires, such as tire cords,
wire ropes, etc., and for composite materials with vinyl, rubber, etc.
[0015] In general, it has been well known that the amorphous alloys are obtained by rapidly
quenching an alloy having the proper composition from the molten state or through
various techniques, such as vapour deposition, sputtering, plating, and the like and,
among them, sputtering can relax the limitation of the composition range of amorphous
alloys obtained by the process for quenching molten alloys. For example, the process
wherein a molten metal is continuously ejected on an outer circumferential surface
of a disc (Fig. 2(a)) rotating at a high speed or between two rolls (Fig. 2(b)) reversely
rotating with each other at a high speed to rapidly cool the molten metal on the surface
of the rotary disc or both rolls at a cooling rate of about 10
5 to 10
6°C/sec and to solidify the molten metal, has been publicly known. Furthermore, the
method and apparatus for directly producing a wide thin strip from a molten metal,
which have been developed by one of the inventors (Japanese Patent Laid-Open Application
No. 125,228/78, No. 125,229/78 may be used.
[0016] The amorphous alloys of the present invention can be similarly obtained by rapidly
quenching the molten metal and by the above described various processes wire-shaped
or sheet-shaped amorphous alloys of the present invention can be produced. Furthermore,
amorphous alloy powders from about several µm to 10 pm can be produced by blowing
the molten metal to a cooling copper plate using a high pressure gas (nitrogen, argon
gas and the like) to rapidly cool the molten metal in fine powder form, for example,
by an atomizing process. Accordingly, powders, wires or plates composed of amorphous
alloys of iron group elements of the present invention, which contain zirconium, can
be produced in commercial scale.
[0017] In the alloys of the present invention, even if a small amount, that is an extent
which is admixed from starting materials, of impurities for example, Hf, 0, S, etc.
is contained, the object of the present invention can be accomplished.
[0018] Particularly, Hf is generally contained in an amount of 1 to 3% in raw ore of Zr
to be used as one component of the alloys of the present invention and Hf is very
similar to Zr in the physical and chemical properties, so that it is very difficult
to separate both the components and refine Zr by usual refining process. In the present
invention, even if about 2% of Hf is contained, the object of the present invention
can be attained.
[0019] The composition of the first and second aspects of the present invention is shown
in the following Table 1 and the reason for limiting the component composition is
explained hereinafter.
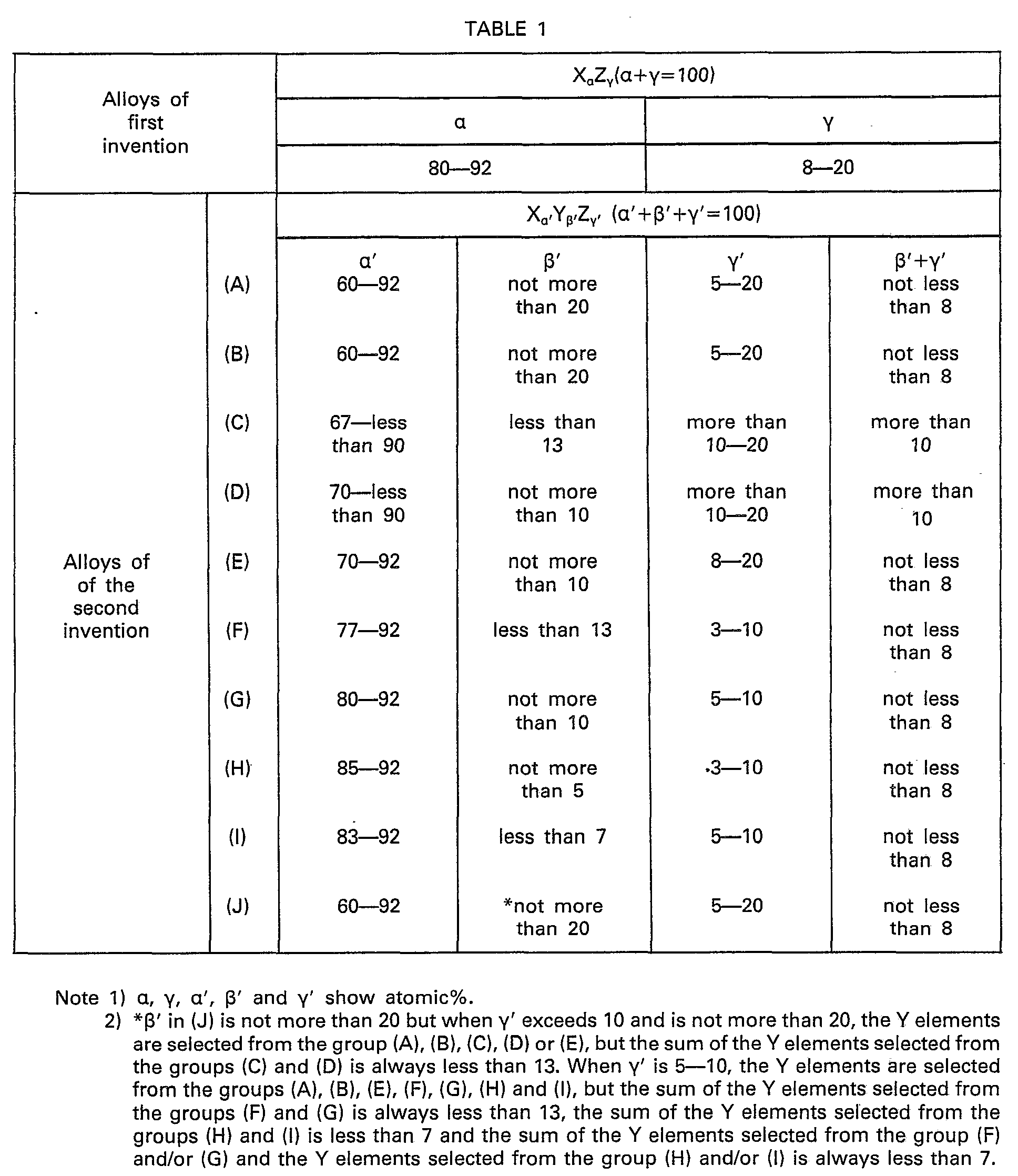
[0020] In the alloys of the first aspect of the present invention, Zr has the effect to
act as an amorphous forming element for iron group elements but in the alloys of the
first aspect of the present invention wherein only iron group elements and Zr are
combined, at. least 8 atomic% of Zr is necessary for amorphous formation and when
Zr is less than 8 atomic%, even if the molten metal is rapidly quenched and solidified,
for example in the composition of Co
95Zr
5 or Fe
94Zr
6, a complete crystalline state is formed and in the composition of Co
93Zr
7, the ratio of the amorphous structure is about 50% in the whole structure.
[0021] In the alloys containing more than 20 atomic% of Zr, production becomes difficult,
so that the amount of Zr added must be from 8 to 20 atomic%.
[0022] An explanation will be made with respect to the alloys of the second aspect of the
present invention.
[0023] (A) When Cr, Mo or W belonging to VIB Group is added as a third element, the crystallization
temperature is raised as shown in Fig. 3 and thermal stability is increased. Particularly,
this effect is noticeably high in W.
[0024] Cr and Mo have the effect of improving the corrosion resistance and increase the
strength, but when at least one element of Cr, Mo and W is added in a total amount
of more than 40 atomic%, embrittlement occurs and the production of alloys becomes
difficult.
[0025] Cr has particularly a large effect for improving the magnetic property but in any
case of Cr, Mo and W, when the amount of these elements exceeds 20 atomic%, the strong
ferromagnetic property is substantially lost or the magnetic induction is considerably
reduced, so that for improvement of the magnetic properties, not more than 20 atomic%
is preferable.
[0026] By the synergistic effect of Zr and the above described VIB Group elements, even
if the amount of Zr is less than 8 atomic% of the lower limit of Zr of the alloys
in the first aspect of the present invention, the amorphous formation cannot be attained,
so that Zr must be 5 to 20 atomic%, preferably 7 to 15 atomic%. Furthermore, when
the sum of the above described VIB Group elements and Zr is less than 8 atomic%, the
amorphous formation is difficult, so that said sum must be not less than 8 atomic%,
preferably not less than 12 atomic%.
[0027] In alloys having the composition shown by the formula (Fe,_
XCo
x)-γ-Zr, when x is more than 0.5, that is in the composition wherein Co is alone or
the number of Co atom is larger than the number of Fe atom, Mo has the large effect
for reducing the amount of Zr necessary for the amorphous formation, and when x is
less than 0.5, that is, in the composition wherein Fe is alone or the number of Fe
atom is larger than the number of Co atom, Cr has the large effect for reducing the
amount of Zr necessary for formation of the amorphous alloys.
[0028] (B) Ti, V, Nb, Ta, Cu and Mn are added in order to make the production of the alloys
more easy, increase the strength and improve the thermal stability and the magnetic
properties for magnetic materials. In particular, among Ti, V, Nb, Ta, Cu and Mn,
V has the noticeable effect for raising the crystallization temperature and making
the production of the alloys easy, Ti, Nb and Ta have the noticeable effect for raising
the crystallization temperature and improving the thermal stability, Cu and Mn have
the effect for making the production of the alloys easy and Cu is effective for improving
the corrosion resistance. However, the addition of more than 35 atomic% of any of
these elements makes the production of the alloys difficult. Concerning each element
of V, Nb and Ta belonging to VB Group, the addition of more than 20 atomic% increases
the embrittlement of the amorphous alloys, so that said amount must be not more than
20 atomic%.
[0029] Zr can form amorphous alloys of iron group elements by the synergistic effect with
the above described elements, even if the amount of Zr is less than 8 atomic% of the
lower limit of Zr in the alloys of the first aspect of the present invention. However,
if said amount is less than 5 atomic% or more than 20 atomic%, the amorphous formation
is infeasible, so that the amount of Zr must be 5 to 20 atomic%, preferably 7 to 15
atomic%. Furthermore, when the sum of Zr and at least one of V, Nb, Ta, Cu, Mn, and
Ti is less than 8 atomic%, the amorphous formation becomes difficult, so that said
sum be not less than 8 atomic%, preferably not less than 12 atomic%.
[0030] (C) At least one element of Be, B, AI and Si belonging to IIA, IIIA or IVA Group
aids the amorphous formation and not only makes the production of the alloys easy
but also improves the magnetic properties and the corrosion resistance.
[0031] However, when 13 or more atomic% is added, the magnetic induction is not only lowered
but also the thermal stability which is one great characteristic of the amorphous
alloys of the present invention is deteriorated so that the amount must be less than
13 atomic%, but in order to maintain the very high magnetic induction and thermal
stability, the amount is preferably to be less than 1 atomic%, and in order to obtain
a moderately high magnetic induction, thermal stability and easiness of formation
of amorphous alloys, the atomic% of the range from 1 to less than 7 is desirable and
in order to make the formation of amorphous alloys very easy, the atomc% of the range
from more than 10 to less than 13 is preferable.
[0032] When Zr exceeds 20 atomic%, the formation of the amorphous alloys is impossible,
so that the amount must be not more than 20 atomic%, preferably not more than 15 atomic%,
and the lower limit capable of forming the amorphous alloys can be lowered to 3 atomic%
which is lower than the lower limit of 8 atomic% of Zr in the alloys of the first
aspect of the present invention, owing to the synergistic effect with Be, B, AI or
Si, but since it is considered that the functional effect of each element of the above
described Be, B, AI and Si is different according to the concentration of Zr, which
is the main element for forming the amorphous alloys in the present invention, in
the item (C), Zr is the range of more than 10 atomic%, and concerning the range of
Zr of 3 to 10 atomic%, these elements are classified into a group of Be, AI and Si,
and B alone and then these groups will be explained in the items (F) and (H) respectively.
Accordingly, in this item (C), Zr is from more than 10 to not more than 20 atomic%.
[0033] (D) At least one element of C, N, P, Ge, In, Sn, As and Sb belonging to IIIA, IVA
or VA Group aids the formation of the amorphous alloys and makes the production of
the amorphous alloy easy and particularly P improves the corrosion resistance in coexistence
of Cr but when the amount exceeds 10 atomic%, the alloys are embrittled, so that said
amount must be not more than 10 atomic%, preferably not more than 7 atomic%. Furthermore,
when Zr exceeds 20 atomic%, the amorphous alloys cannot be formed, so that the amount
must be not more than 20 atomic%, preferably not more than 15 atomic% and the lower
limit capable of forming the amorphous alloys can be lowered to 5 atomic% which is
lower than 8 atomic% of Zr of the lower limit in the first aspect of the present invention
owing to the synergistic effect with the above described C, N, P, Ge, In, Sn, As and
Sb but it is considered that the functional effect of each element of the above described
C, N, P, Ge, In, Sn, As and Sb is different according to the concentration of Zr which
is the main element for forming the amorphous alloys in the present invention, but
in the item (D), Zr is defined to exceed 10 atomic% and concerning the range of Zr
of 5 to 10 atomic%, these elements are classified into a group of N, Ge, In, Sn, As
and Sb and a group of C and P and these groups will be explained in the items (G)
and (I) respectively. Accordingly, in this item D, Zr is within the range which exceeds
10 and is not more than 20 atomic%.
[0034] (E) The addition of lanthanum group elements facilitates the production of the amorphous
alloys but the addition of more than 10 atomic% of lanthanum group elements considerably
embrittles the alloys, so that the amount of addition must be not more than 10 atomic%.
When Zr is less than 8 atomic% or more than 20 atomic%, the amorphous formation is
impossible, so that Zr must be 8 to 20 atomic%. When the sum of the above described
lanthanum group elements and Zr is less than 8 atomic%, the amorphous formation becomes
difficult, so that said sum must be not less than 8 atomic%.
[0035] (F) As mentioned in the above item (C), at least one element selected from the group
consisting of Be, AI and Si aids the amorphous formation to facilitate the production
of the alloy and further improve noticeably the magnetic properties and the corrosion
resistance.
[0036] However, when 13 or more atomic% is added, the magnetic properties are not only lowered
but also the thermal stability, which is one of the great characteristics of the amorphous
alloys of the present invention, is deteriorated, so that the addition must be less
than 13 atomic%, preferably less than 7 atomic%, more preferably less than 10 atomic%.
Zr can produce amorphous alloys of iron group elements in an amount of less than 8
atomic% of the lower limit of Zr in the alloys of the first aspect of the present
invention. But, when the amount is less than 3 atomic%, the amorphous alloy cannot
be obtained, so that Zr is not less than 3 atomic%, preferably not less than 5 atomic%,
and the upper limit is not more than 10 atomic%.
[0037] Furthermore, when the sum of Zr and the above described elements Be, AI and Si is
less than 8 atomic%, the amorphous formation is difficult, so that this sum must be
8 or more atomic%, preferably 10 or more atomic%.
[0038] (G) As mentioned in the above described item (D), at least one element selected from
the group consisting of N, Ge, In, Sn, As and Sb aims the amorphous formation and
facilitates the production of the alloys. But when the amount exceeds 10 atomic%,
the. alloys are embrittled, so that the amount must be not more than 10 atomic%. Zr
can form the amorphous alloys of iron group elements even in the amount of less than
8 atomic% which is the lower limit of Zr in the alloys of the first aspect of the
present invention, due to the synergistic effect with N, Ge, In, Sn, As or Sb element.
However, when the amount is less than 5 atomic%, the amorphous formation is infeasible,
so that Zr is not less than 5 atomic%, preferably not less than 7 atomic%, the upper
limit is not more than 10 atomic%.
[0039] Furthermore, when the sum of Zr and the above described elements N, Ge, In, Sn, As
and Sb is less than 8 atomic%, the amorphous formation becomes difficult, so that
the above described sum must be not less than 8 atomic% and is preferred to be not
less than 10 atomic%.
[0040] (H) The metalloid element B, which is one of the elements described in the above
item (C) has been known as the element which can form the amorphous alloys of iron
group elements and it has been known that iron group element alloy containing not
less than 6 atomic% of B and not more than 10 atomic% of Zr can be made amorphous.
But the inventors have made further studies and found that Zr is the element which
can very easily form amorphous alloys of iron group elements, so that even the alloys
containing only not more than 5 atomic% of B can be made easily amorphous and discovered
amorphous alloys based on metal-metal system. Accordingly, it is preferred that B
is not more than 5 atomic%, more particularly less than 1 atomic% in orderj:o.-highiy
maintain the thermal stability which is one of the characteristics of the amorphous
alloy based on metal-metal system. Furthermore, in this item Zr is within the range
of 3 to 10 atomic%. When the sum of B and Zr is less than 8 atomic%, the amorphous
formation is difficult, so that the above described sum must be not less than 8 atomic%
and is preferred to be not less than 10 atomic%.
[0041] (I) P and C of the metalloid elements selected from the element group described in
the item (D) have been known as the elements by which iron group elements are readily
formed into amorphous alloys similarly to B and it has been known that iron group
element alloys containing not less than 7 atomic% of P or C and additionally not more
than 10 atomic% of Zr can provide amorphous alloys. But, the inventors have made further
studies and found that since Zr also is an element by which iron group elements can
be very easily formed into amorphous alloys, even in alloys containing only less than
7 atomic% of P or C, the amorphous alloys are easily obtained and discovered the amorphous
alloys based on metal-metal system. Accordingly, it is preferred that P or C is less
than 7 atomic%, more particularly less than 1 atomic% in order to highly maintain
the thermal stability which is one of the characteristics of the amorphous alloy based
on metal-metal system. Furthermore, in this item Zr is within the range of 5 to 10
atomic%. When the sum of Zr and the above described P or C is less than 8 atomic%
the amorphous formation is difficult, so that the above described sum must be not
less than 8 atomic%.
[0042] (J) When the total amount of the third element group as mentioned in the above items
(A)-(I) except for iron series elements and Zr is more than 20 atomic%, ferromagnetic
properties deteriorate, embrittlement occurs, or the production of the amorphous alloys
becomes difficult, so that said amount must be not more than 20 atomic%.
[0043] Zr can form the amorphous alloys of iron group elements by the synergistic effect
with the above described third elements, even if the amount is less than 8 atomic%
of the lower limit of Zr in the first aspect of the present invention. However, when
said amount is less than 5 atomic% or more than 20 atomic%, the amorphous formation
is impossible, so that Zr must be 5 to 20 atomic%, and when the sum of the above described
third element and Zr is less than 8 atomic%, the amorphous formation becomes difficult,
so that the above described sum must be not less than 8 atomic%.
[0044] However, when Zr exceeds 10 atomic% and is not more than 20 atomic%, the Y element
is selected from the group A, B, C, D or E and in this case, when the sum of the addition
of at least one element selected from each group of the groups C and D is 13 or more
atomic%, the thermal stability is deteriorated or the alloys are embrittled, so that
the sum must be less than 13 atomic%. When Zr is 5-10 atomic%, the Y element is selected
from the above described group A, B, E, F, G, H or I but when the sum of the Y elements
selected from the groups F and G is 13 or more atomic%, the thermal stability is deteriorated
or the alloys are embrittled, so that the sum must be less than 13 atomic%. The sum
of the Y elements selected from the groups H and I must be less than 7 atomic% in
order to maintain the higher thermal stability.
[0045] Furthermore, when the sum of the Y elements selected from the group F and/or the
group G and the Y elements selected from the group H and/or the group I is 7 or more
atomic%, the thermal stability is deteriorated or the alloys are embrittled, so that
the sum must be less than 7 atomic%.
[0046] Physical properties, magnetic properties and corrosion resistance of the amorphous
alloys of the present invention are shown in the following Examples.
Example 1
[0048] Then, the magnetic properties of the alloys of the present invention are shown in
the following Table 3.

[0049] In the alloys in Table 3 except for the alloys containing B, the magnetic induction
is high as 7,000 to 15,800 and the coercive force is relatively low, and the alloys
show the soft magnetic property.
[0050] The greatest characteristic of these alloys is that the magnetic properties are thermally
very stable.
[0051] In order to confirm the thermal stability of the magnetic properties of the alloys
of the present invention, the amorphous alloy having the composition of Fe
45Co
36Cr
9Zr
10 in Table 3 was heated at 465°C for 10 minutes to remove the strain, and then heated
at 100°C for 1,000 minutes. The coercive force was 0.03 Oe and no variation was found.
This shows that the alloy of the present invention is more magnetically stable than
a prior metal-metalloid amorphous alloy, for example, Fe
5Co
70Si
15B
10. When the alloy Fe
5Co
70Si
15B
10 was heated at 100°C for 1,000 minutes, the coercive force varied from 0.01 Oe to
0.06 Oe.
Example 2
[0052] Ribbon-formed samples of the alloys of the present invention were immersed in aqueous
solutions of 1 N-H
2S0
4, 1 N-HCI and 1 N-NaCI at 30°C for one week to carry out a corrosion test. The obtained
results are shown in the following Table 4 together with the results of stainless
steels.

[0053] This table shows that the amorphous alloys have corrosion resistance equal to or
higher than that of stainless steels. That is, the amorphous alloys consisting of
iron group elements and Zr, for example, Fe
54Co
36Zr
10 are inferior to 13% Cr steel in the corrosion resistance against H
2SO
4 and HCI but possess 40 times higher corrosion resistance against NaCI than 13% Cr
steel. Furthermore, when Mo is added, the alloy has more excellent properties than
304 steel and 316 L steel.
[0054] As mentioned above, the alloys of the present invention are completely novel amorphous
alloys, the composition range of which has been generally considered not to form amorphous
alloys, and which are completely different from the previously known metal-metalloid
amorphous alloys and also metal-metal amorphous alloys.
[0055] Among them, the alloys wherein Fe and/or Co is rich, are high in the magnetic induction
and relatively low in the coercive force and are very excellent in the thermal stability,
so that these alloys also have the characteristics that the magnetic and mechanical
properties are thermally stable.
[0056] By the addition of the third elements, such as Cr, Mo, etc., the crystallizing temperature
is raised, the thermal stability is improved and the corrosion resistance can be noticeably
improved.
Industrial applicability
[0057] The amorphous alloys of the present invention can greatly improve the thermal stability,
which has not been satisfied in the well known metal-metalloid amorphous alloys and
have the high strength and toughness which are the unique properties of amorphous
alloys. Accordingly, these alloys can be used for various applications which utilize
effectively these properties, for example, materials having a high strength, such
as composite materials, spring materials, and a part of the alloys can be used for
materials having a high magnetic permeability and materials having a high corrosion
resistance.
1. Amorphous alloys containing iron group elements and zirconium and having the composition
shown in the following formula

wherein X
a shows that at least one element selected from the group consisting of Fe, Co and
Ni is contained in an amount of α atomic%, Zγ shows that Zr is contained in an amount
of y atomic%, the sum of α and γ is 100 and a is 80 to 92 and y is 8 to 20.
2. Articles consisting of powder and its moldings, wires or plates made of the alloys
as claimed in claim 1.
3. Amorphous alloys containing iron group elements and zirconium and having the composition
shown in the following formula

wherein X
a, shows that at least one element selected from Fe, Co and Ni is contained in an amount
of a' atomic%;
Yβ, shows that at least one element selected from Cr, Mo, W, Ti, V, Nb, Ta, Mn, Cu,
Be, B, Al, Si, In, C, Ge, Sn, N, P, As, Sb and lanthanum group elements is contained
in an amount of β' atomic%; and
Zγ, shows that Zr is contained in an amount of γ' atomic%, the sum of α', β' and γ'
being 100; and wherein
(A) Y is at least one element selected from the group consisting of Cr, Mo and W,
α' is 60 to 92, β' is not more than 20 and γ' is 5 to 20, provided that the sum of
β' and γ' is not less than 8, or
(B) Y is at least one element selected from the group consisting of Ti, V, Nb, Ta,
Cu and Mn, a' is 60 to 92, β' is not more than 20, γ' is 5 to 20 provided that the
sum of β' and γ' is not less than 8, or
(C) Y is at least one element selected from the group consisting of Be, B, AI and
Si, α' is 67 to 90, β' is less than 13 and y' is more than 10 and not more than 20,
or
(D) Y is at least one element selected from the group consisting of C, N, P, Ge, In,
Sn, As and Sb, a' is 70 to less than 90, β' is not more than 10 and γ' is more than
10 and not more than 20, or
(E) Y is at least one element selected from lanthanum group elements, a' is 70 to
92, P' is not more than 10 and y' is 8 to 20, or
(F) Y is at least one element selected from the group consisting of Be, AI and Si,
α' is 77 to 92, β' is less than 13, γ' is 3 to 10, provided that the sum of β' and
γ' is not less than 8, or
(G) Y is at least one element selected from the group consisting of N, Ge, In, Sn,
As and Sb, a' is 80 to 92, β' is not more than 10 and γ' is 5 to 10, provided that
the sum of β' and γ' is not less than 8, or
(H) Y is B, α' is 85 to 92, β' is not more than 5 and γ' is 3 to 10 provided that
the sum of and γ' is not less than 8, or
(I) Y is at least one element selected from the group consisting of C and P, α' is
83 to 92, β' is less than 7 and γ' is 5 to 10, provided that the sum of β' and γ'
is not less than 8, or
(J) Y consists of elements from at least two groups selected from the above described
groups combined, β' is within the range of β' value in each of the selected groups
and the total value of β' is not more than 20, α' is 60 to 92, γ' is 5 to 20 and the
sum of β' and γ' is not less than 8, provided that when γ' is more than 10 and not
more than 20, the Y elements are combination of elements of at least two groups selected
from the groups (A), (B), (C), (D) and (E) but the sum of the Y elements selected
from the groups (C) and (D) is less than 13, and when y' is 5 to 10, the Y elements
are combination of elements of at least two groups selected from the groups (A), (B),
(E), (F), (G), (H) and (I), but the sum of the Y elements selected from the groups
(F) and (G) is less than 13, the sum of the Y elements selected from the group (H)
and (I) is less than 7, and the sum of the Y elements selected from the group (F)
and/or the group (G) and the Y elements selected from the group (H) and/or the group
(I) is less than 7.
4. Articles consisting of powder and its moldings, wires or plates made of the alloys
as claimed in claim 3.
1. Amorphe Legierungen, enthaltend Elemente der Eisengruppe und Zirkonium mit der
durch folgende Formel angegebene Zusammensetzung
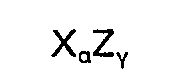
in der X
Q zeigt, daß zumindest ein Element aus der Gruppe bestehend aus Fe, Co und Ni in einer
Menge von a Atom-% enthalten ist, Z
" zeigt, daß Zr in einer Menge von y Atom-% enthalten ist, wobei die Summe von a und
y beträgt, und a 80 bis 92 und y 8 bis 20 ist.
2. Gegenstände, bestehend aus einem Pulver und dessen Formkörper, Drähte oder Platten
aus den in Anspruch 1 beanspruchten Legierungen.
3. Amorphe Legierungen, enthaltend Elemente der Eisengruppe und Zirkonium entsprechend
der in der folgenden Formel angegebenen Zusammensetzung
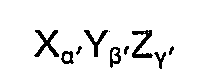
in der Xα, anzeigt, daß mindestens ein Element ausgewählt aus Fe, Co und Ni in einer
Menge von α' Atom-% vorhanden ist,
Yß, zeigt, daß zumindest ein Element ausgewählt aus Cr, Mo. W, Ti, V, Nb, Ta, Mn, Cu,
Be, B, Al, Si, In, C, Ge, Sn, N, P, As, Sb und Elementen der Lanthangruppe in einer
Menge von β' Atom-% vorhanden ist, und
Zγ, anzeigt, daß Zr in einer Menge von γ' Atom-% vorhanden ist, wobei die Summe von
α', β' und γ' 100 ist, und wobei
(A) Y mindestens ein Element aus der Gruppe, bestehend aus Cr, Mo und W ist, α' 60
bis 92, β' nicht mehr als 20 und γ' 5 bis 20 ist, mit der Maßgabe daß die Summe von
β' und γ' nicht weniger als 8 ist, oder
(B) Y mindestens ein Element aus der Gruppe, bestehend aus Ti, V, Nb, Ta, Cu und Mn
ist, a' 60 bis 92, β' nicht mehr als 20 und γ' 5 bis 20 ist, mit der Maßgabe, daß
die Summe von β' und γ' nicht weniger als 8 ist, oder
(C) Y mindestens ein Element aus der Gruppe, bestehend aus Be, B, AI und Si ist, α'
67 bis 90, β' weniger als 13 und y' mehr als 10 und nicht mehr als 20 ist, oder
(D) Y mindestens ein Element aus der Gruppe, bestehend aus C, N, P, Ge, In, Sn, As
und Sb ist, a' 70 bis weniger als 90, β' nicht mehr als 10 und γ' mehr als 10 und
nicht mehr als 20 ist, oder
(E) Y mindestens ein Element aus der Lanthangruppe ist, α' 70 bis 92, β' nicht mehr
als 10 und γ' 8 bis 20 ist, oder
(F) Y mindestens ein Element aus der Gruppe, bestehend aus Be, AI und Si ist, α' 77
bis 92, β' weniger als 13, γ' 3 bis 10 ist, mit der Maßgabe, daß die Summe von β'
und γ' nicht weniger als 8 ist, oder
(G) Y mindestens ein Element aus der Gruppe, bestehend aus N, Ge, In, Sn, As und Sb
ist, a' 80 bis 92, β' nicht mehr als 10 und γ' 5 bis 10 ist, mit der Maßgabe, daß
die Summe von β' und γ' nicht weniger als 8 ist, oder
(H) Y=B ist, α' 85 bis 92, β' nicht mehr als 5 und γ' 3 bis 10 ist, mit der Maßgabe,
daß die Summe von β' und y' nicht weniger als 8 ist, oder
(I) Y mindestens ein Element aus der Gruppe, bestehend aus C und P ist, α' 82 bis
92, β weniger als 7 und γ' 5 bis 10 ist, mit der Maßgabe, daß die Summe von β' und
γ' nicht weniger als 8 ist, oder
(J) Y aus Elementen aus mindestens 2 Gruppen, ausgewählt aus Kombinationen der oben
beschriebenen Gruppen, ist, β' in dem für β' in jeder der ausgewählten Gruppen angegebenen
Bereich liegt, und der Gesamtwert von β' nicht mehr als 20 ist, α' 60 bis 92, γ' 5
bis 20 und die Summe von β' und γ' nicht weniger als 8 ist, mit der Maßgabe, daß wenn
y' mehr als 10 und nicht mehr als 20 ist, die Elemente Y eine Kombination von Elementen
aus mindestens 2 Gruppen sind, ausgewählt aus den Gruppen (A), (B), (C), (D) und (E),
aber die Summe der Elemente Y aus den Gruppen (C) und (D) weniger als 13 ist, und
wenn y' 5 bis 10 ist, die Elemente Y eine Kombination sind von Elementen aus mindestens
zwei Gruppen, ausgewählt aus den Gruppen (A), (B), (E), (F), (G), (H) und (1), aber
die Summe der Elemente Y aus den Gruppen (F) und (G) weniger als 13 ist, die Summe
der Elemente Y aus den Gruppen (H) und (I) weniger als 7 ist, und die Summe der Elemente
Y aus der Gruppe (F) und/oder (G) und der Elemente Y aus der Gruppe (H) und/oder (I)
weniger als 7 ist.
4. Gegenstände, bestehend aus einem Pulver und dessen Formkörper, Drähte oder Platten
aus den in Anspruch 3 beschriebenen Legierungen.
1. Alliages amorphes contenant des éléments du groupe du fer et du zirconium et ayant
la composition représentée dans la formule suivante:
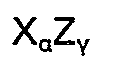
dans laquelle Xα indique qu'au moins élément choisi parmi Fe, Co et Ni est contenu
en quantité de α % en atome, Zy indique que Zr est contenu en une quantité de y %
en atome, la somme de a et y est égale à 100 et a va de 80 à 92 et y va de 8 à 20.
2. Articles consistant en poudre, moulages, fils ou tôles obtenus à partir des alliages
selon la revendication 1.
3. Alliages amorphes contenant des éléments du groupe du fer et du zirconium et ayant
la composition représentée dans la formule suivante:
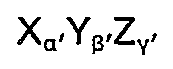
dans laquelle Xα. indique qu'au moins un élément choisi parmi Fe, Co et Ni est contenu
en quantité de α' % en atome,
Yβ. indique qu'au moins un élément choisi parmi Cr, Mo, W, Ti, V, Nb, Ta, Mn, Cu,
Be, B, AI, Si, In, C, Ge, Sn, N, P, As, Sb et les éléments du groupe du lanthane est
contenu en quantité de β' % en atome, .
Zγ, indique que Zr est contenu dans une quantité de γ' % en atome, la somme de γ',
β' et α' étant égale à 100; et dans laquelle
(A) Y est au moins un élément choisi parmi Cr, Mo et W, α' va de 60 à 92, β' n'est
par supérieur à 20 et γ' va de 5 à 20, pourvu que la somme de β' et γ' ne soit pas
inférieure à 8, ou
(B) Y est au moins un élément choisi parmi Ti, V, Nb, Ta, Cu et Mn, α' va de 60 à
92, β' n'est pas supérieur à 20, γ' va de 5 à 20, pourvu que la somme de β' et γ'
ne soit pas inférieure à 8, ou
(C) Y est au moins un élément choisi parmi Be, B, AI et Si, α' va de 67 à 90, β' est
inférieur à 13 et γ' est supérieur à 10 et inférieur à 20, ou
(D) Y est au moins un élément choisi parmi C, N, P, Ge, ln, Sn, As et Sb, α' va de
70 à moins de 90, β' n'est pas supérieur à 10 et y' est supérieur à 10 et n'est pas
supérieur à 20, ou
(E) Y est au moins un élément choisi parmi les éléments du groupe du lanthane, α'
va de 70 à 92, β' n'est pas supérieur à 10 et y' va de 8 à 20, ou
(F) Y est au moins un élément choisi parmi Be, AI et Si, α' va de 77 à 92, β' est
inférieur à 13, γ' va de 3 à 10, pourvu que la somme de β' et γ' ne soit pas inférieure
à 8, ou
(G) Y est au moins un élément choisi parmi N, Ge, In, Sn, As et Sb, α' va de 80 à
92, β' n'est pas supérieur à 10 et γ' va de 5 à 10, pourvu que la somme de β' et γ'
ne soit pas inférieure à 8, ou
(H) Y est B, α' va de 85 à 92, β' n'est pas supérieur à 5 et γ' va de 3 à 10, pourvu
que la somme de β' et γ' ne soit pas inférieure à 8, ou
(I) Y est au moins un élément choisi parmi C et P, α' va de 83 à 92, β' est inférieur
à 7 et γ' va de 5 à 10, pourvu que la somme de P' et y' ne soit pas inférieure à 8,
ou
(J) Y est constitué d'éléments d'au moins deux groupes choisis parmi les groupes ci-dessus
combinés, β' est situé dans l'intervalle des valeurs de β' dans chacun des groupes
choisis et la valeur totale de β' n'est pas supérieure à 20, α' va de 60 à 92, γ'
va de 5 à 20 et la somme de β' et γ' n'est pas inférieure à 8, pourvu que lorsque
y' est supérieur à 10 et n'est pas supérieur à 20 les éléments soient une combinaison
d'éléments d'au moins deux groupes choisis parmi les groupes A, B, C, D et E mais
que la somme des éléments dans les groupes C et D soit inférieure à 13 et que, lorsque
y' va de 5 à 10, les éléments soient une combinaison d'éléments d'au moins deux groupes
choisis parmi les groupes A, B, E, F, G, H et 1, mais que la somme des éléments choisis
dans les groupes F et G soit inférieure à 13, que la somme des éléments choisis dans
les groupes H et I soit inférieure à 7 et que la somme des éléments choisis dans le
groupe F et/ou le groupe G et des éléments choisis dans le groupe H et/ou dans le
groupe 1 soit inférieure à 7.
4. Articles consistant en poudre, moulages, fils ou tôles obtenus à partir des alliages
selon la revendication 3.