Technical field
[0001] This invention relates to image generation. More particularly it relates to techniques
wherein a thermal printing means is employed to form latent images on a substrate.
The image is subsequently developed with a dry imaging powder and fixed by means of
pressure.
Background art
[0002] Image generation processes utilizing heat are known and are often referred to as
thermographic processes. They generally required image-wise exposure of a heat-sensitive
material to heat to either cause a chemical reaction of the heat-sensitive material
thereby producing a visible image, or, alternatively, to cause the heat-sensitive
material to become either tacky orfluid in exposed areas. In either event the image
may then be developed with an imaging powder.
[0003] Examples of thermographic recording processes are set forth in United States Patents
3,196,029; 3,260,612; 3,515,570; 3,941,596 and 3,902,062 and GB-A-1,106,199. Each
of these patents disclose processes wherein a substrate having a layer of a heat-sensitive
material is imaged by use of a master or an original document. The image may then
be toned with a powder or dye.
[0004] In U.S. 3,196,029 an original document is placed on the heat-sensitive layer and
then exposed to infra-red radiation. The image areas of the original absorb the radiant
energy and heat up causing the heat-sensitive layer to soften and produce a latent
image which is then made visible by contact with a powder. The powder may then be
fixed by either heating it or exposing it to solvent vapor. However, fixing is optional.
[0005] In U.S. 3,260,612 an image is formed by placing an original document on the heat-sensitive
layer of a substrate and exposing the original to infra-red radiation. The image is
made visible by contact with a powder or a dye.
[0006] In US-A-3 515 570 the heat-sensitive layer comprises a first material which shows
a stable super-cooling property and has a melting point of 45 to 120°C, and fine particles
of a second material which does not show the supercooling property and has a melting
point at least 10°C higher than the melting point of the first material. Images are
formed as described above.
[0007] In US-A-3 941 596 a heat-sensitive material of a mixture of a thermoplastic, amorphous,
organic polymer and a liquid plasticizer, is utilized. After image formation, the
image is made visible by either contact with a toner powder or by transfer of the
image to a receptor followed by contact with a toner powder.
[0008] US-A-3 902 062 discloses a thermographic copying method comprising the steps of bringing
a cut sheet of heat sensitive material into contact with an original bearing an image,
to form a sandwich; moving the sandwich in a first direction along a predetermined
path extending through a first station and a remotely spaced development station;
exposing said sandwich at said first station to radiation from a radiant source to
thermally impart said image to said sheet; separating said original from said sheet
at a point between said first station and said development station; passing said sheet
through said development station to at least partially develop said image while continuing
to move said sheet in said first direction along said path; moving said sheet in the
opposite direction along said path back through said development station and said
first station; and re-exposing said sheet at said first station to radiation from
said source to fix said image. Suitable heat sensitive sheets for use therein comprise
a support coated with a mixture of discrete particles of resin and discrete particles
of a crystalline plasticizer, e.g. diphenyl phthalate, bound together in a supporting
film by a binder.
[0009] GB-A-1 106 199 discloses a method of thermographic reproduction by use of a powder
developer comprising the steps of preparing a heat-sensitive sheet having solid fine
particles of a stable supercoolable material uniformly dispersed on a support, exposing
said heat-sensitive sheet and an original to heat in accordance with common heat exposure
practice to produce a latent image formed from the solid fine particles of the supercoolable
material kept at its supercooled state, and applying a powder developer to said latent
image to effect development thereof and wherein said solid fine particles include
particles of triphenyl phosphate.
[0010] Each of these processes requires the use of sophisticated equipment and, frequently,
the use of special coated or treated papers. Still further the heat generated during
some of these processes is great thereby necessitating the use of cooling equipment,
such as fans, in order to give acceptable machine life to the equipment. Additionally,
the heat liberated to the area surrounding the equipment can make these areas very
uncomfortable during periods of high usage.
[0011] The heat required to fix the images, such as in US-A-3 196 029, is disadvantageous
for other reasons. It limits the speed of the recording process and the substrates
that can be used. Still further, the heat requires a significant degree of power consumption
and, as noted above, liberates a significant amount of heat to the surrounding environment.
[0012] The present invention overcomes these disadvantages of the prior art. It provides
a simple, quiet, clean, cool and economical process for providing permanent images
on a substrate. It also provides an instant on system. Thus no warm-up time is needed
and no steady supply of heat must be provided between periods of use.
[0013] In accordance with one aspect of the present invention there is provided a method
for providing a permanent image upon a substrate, wherein, the image is made visible
by a fixed, dry imaging powder, and wherein fixing is achieved solely by the application
of pressure to the powder image.
[0014] According to the present invention there is provided a method of providing a permanent
image on a substrate bearing a coating of a normally solid, non-tacky material which
has a melting temperature at least 10°C above ambient and which forms a supercooled
melt when cooled to a temperature below its melting temperature, in which the permanent
image is formed by the successive steps of:
forming a latent liquid image pattern on said coating by image-wise contacting said
coating with a thermal printing means for a time sufficient to raise the temperature
of said non-tacky material to at least its melting temperature;
contacting said latent liquid image pattern with a dry imaging powder which attaches
to said latent liquid image pattern; characterised by the step of
applying sufficient pressure to said imaging powder to deform and embed it in said
latent liquid image pattern and form a substantially unified and visually continuous
mass thereon.
[0015] As it is used herein, the term "latent liquid image" means a fluid image that is
generally not readily perceptible to the naked eye. Such images are provided by image-wise
heating the coated surface of the substrate to a temperature sufficient to melt the
non-tacky material.
[0016] The latent liquid image areas need only be macroscopically (that is visually) continuous.
Thus, even though they appear to be continuous when examined by the naked eye, they
need not be. They may comprise halftone dots or other forms of discontinuous liquid
areas which generally make up the graphic character to be reproduced.
[0017] The process of the invention requires only the use of low pressures (e.g., as low
as about 4 kg/lineal cm) to secure adequate fixing of the toned image areas to plain
paper substrates as compared to pressures in the range of about 40 to 60 kg/lineal
cm typically required by prior art pressure-fixing processes.
[0018] These higher fixing pressures-have several disadvantages. For example, when plain
paper sheets are subjected to a fixing pressure of about 40 kg/lineal cm, they develop
a surface shine or glaze. As the pressure increases, the glaze increases. Glaze increases
the reflectance of incident light and is objectionable because it interferes with
visual contrast between image and background areas and renders such documents difficult
to read. These higher fixing pressures also densify plain paper giving it an objectionable
hand or feel. Still further, greater quantities of energy must be consumed in order
to achieve higher fixing pressures.
[0019] These disadvantages are overcome by the present invention. The lower fixing pressures
required means that the tendency to calender the substrate during fixing is substantially
eliminated. As a result, the final copy is easy to read and has the appearance and
feel of a plain-paper copy even though there is a coating or layer of particles thereon.
Additionally, the amount of energy required to achieve suitable fixing, and the amount
of heat generated during fixing are substantially reduced. This not only dramatically
reduces heat build-up in the machine and the area surrounding it, but also avoids
problems associated with heating and tackifying the entire sheet. Such total heating
and tackifying renders the background areas of the sheet susceptible smearing. Additionally,
it creates problems of image offsetting, image smearing, and fingerprinting until
the coating or particles on the sheet recrystallize.
[0020] The process of the present invention is also quiet. Consequently, it is not a distracting
influence to those working in the area of process. Additionally, the process does
not require the use of sophisticated machinery, such as electrophotographic imaging
equipment. Consequently it is simple and economical to employ.
Detailed description
[0021] The process of the present invention is easily carried out. It comprises the steps
of providing a defined substrate, forming a latent liquid image thereon, contacting
the liquid image with a dry toner powder, and then applying sufficient pressure to
the toned image areas to provide a unified, essentially permanent image on the substrate.
[0022] The substrate used in the invention may be selected from any dry, solid material
which is compatible with the coating of normally solid, non-tacky material. Examples
of such materials include polymeric films, metal foils, and paper. Most preferably
the substrate is paper.
[0023] The substrate preferably bears from 0.1 to 5 g/m
2 of the coating material attached to its surface. The coating material may be applied
to the surface of a substrate by a variety of techniques including solvent coating
and dry coating. For example, the selected normally solid, non-tacky material may
be dissolved or dispersed in an appropriate solvent (e.g., acetone, or water), the
solution or dispersion applied to a substrate, and the solvent allowed to evaporate.
The dissolved solid material is allowed to crystallize. Evaporation of the solvent
may be accelerated, if desired, by heating the coated substrate. However, care should
be taken to insure that the substrate does not curl or otherwise suffer adverse effects
as a result of the heating. Additionally, crystallization of the dissolved solid material
may be accelerated by seeding the coated substrate with undissolved solid material.
[0024] Thickening agents may be added to the coating solutions and dispersions, if desired,
to improve their handleability or coatability. Typically only a small amount of such
agents is required, e.g., 5% by weight or less of the coating solution. These materials
are known and include, for example, ethyl cellulose and styrene/acrylic acid/ethylacrylate
terpolymer.
[0025] Dry coating techniques may also be utilized. Thus, one may brush or rub the solid
form of the non-tacky material onto the substrate. Preferably the material, when applied
to the substrate, is either a powder or a form in which it may readily be converted
to a powder. This dry coating technique provides an efficient means for applying the
material to the substrate. Thus, materials applied by the dry coating technique do
not soak into the substrate as they do with solvent coating techniques. This has a
very surprising benefit since it reduces the amount of coating material applied to
the substrate while providing as good an image as the amount of coating material applied
by solvent coating. Still further, when a plain paper substrate is coated by the dry
coating technique, the resultant sheet appears indistinguishable from an uncoated
paper sheet and can be used immediately after coating.
[0026] The exact amount of the solid material applied to the substrate is not critical to
the invention provided that there is sufficient material to form a latent image and
not so much material that it fouls the thermal printing means, becomes too dielectric,
or gives a greasy feel or appearance to the substrate. Additionally, a sufficient
amount of the material must be used so that once the latent image has been formed,
there will be sufficient adhesion between it and the imaging powder to overcome both
the triboelectric and magnetic forces holding the imaging powder to the development
roll.
[0027] It has been found that a small quantity of the coating material is all that is needed
to provide these results. Thus, it has been found that from about 0.1 to 5 g/m
2 provide excellent results. When solvent coating is utilized to apply the coating
material to the substrate, the substrate preferably bears from about 2 to 5 g/m
2 of the coating. When dry coating is utilized, the substrate preferably bears from
0.1 to 2 g/m
2 of the material. More preferably from about 0.3 to 1.2 g/m
2, and most preferably from about 0.5 to 1.0 g/m
2 of the material. Surprisingly these small quantities of material are sufficient to
provide latent images that can be developed and essentially permanently fixed to the
substrate.
[0028] When dry coating techniques are employed, the particulate material is substantially
adsorbed onto the substrate surface. Thus, for example, when the substrate is paper,
the material becomes attached to the surface of the paper fibers.
[0029] The material utilized as the solid, non-tacky, material of the coating must have
a melting temperature about 10°C above ambient temperature. Ambient temperature, as
used herein, refers to the temperature utilized during the process. The coating must
also form a supercooled melt when cooled to a temperature below its melting temperature.
These materials may be said to exist, at least temporarily, as fluid metastable liquids
after being melted then cooled below their melt temperatures. When the latent image
has been formed, it should wet the surface of the substrate. Moreover, the image must
remain fluid and in place until it is contacted with (that is, developed by) the dry
imaging powder. Alternatively, it may be allowed to cool below its melting point to
form a supercooled melt before the image areas are developed. At this point the supercooled
liquid has not regained its solid crystalline state. Consequently, the material retains
sufficient memory in the imaged areas to be developed and fixed. Once the material
regains its crystalline state in the imaged areas, the latent image ceases to exist
as a distinct area.
[0030] The imaged area must also adhere the dry imaging powder. Thus, for example, the imaged
area may react with the imaging powder; it may form a solution with the powder; it
may wet the toner; or it may either absorb or be adsorbed by the powder. Whatever
the interaction between the powder and the imaged area is, the image must hold the
toner until the powder is fixed to the substrate.
[0031] A number of materials are useful as the coating in the invention. Representative
examples of these materials include dicyclohexyl phthalate, diphenyl phthalate, triphenyl
phosphate, dimethyl fumurate, benzotriazole, 2,4-dihydroxy benzophenone, tribenzylamine,
benzil, vanillin and phthalophenone. Another useful material of this type is "Santicizer
9", a mixture of ortho- and para-toluene sulfonamides obtained from the Monsanto Chemical
Company.
[0032] A variety of imaging powders are useful in the present invention. They must develop
the latent image and may be either pressure-fixable or heat-fusible even though only
pressure is used during fixing. In either event, the imaging powders comprise flowable,
dry powders which preferably are colored. The powders may contain magnetic particles
if desired, and typically comprise a thermoplastic organic binder and a colorant.
[0033] Binders suitable for use in the imaging powder preferably have a softening temperature
in the range of 45°C to 150°C and include thermoplastic organic resins and polymers,
and waxes. Representative examples of useful organic resins and polymers include polyamides,
polystyrenes, epoxy resins, acrylic resins, acrylic copolymers such as styrene/n-butylmethacrylate
copolymer, vinyl resins such as polyvinyl butyral, polyvinyl acetates, vinyl copolymers
such as vinyl chloride vinyl acetate, ethylene vinyl acetate copolymers, cellulose
esters such as cellulose acetate butyrate and cellulose acetate propionate, and cellulose
ethers. These resins may be used either individually or in combination with each other
in the binder.
[0034] Representative examples of useful waxes include natural and synthetic aliphatic waxes,
fatty acids and their metal salts, hydroxylated fatty acids and amides, low molecular
weight ethylene homopolymers, and mixtures thereof. Aromatic and polymeric wax-like
materials may also be used.
[0035] Specific examples of useful waxes include paraffin wax, microcrystalline wax, caranauba
wax, montan wax, ouricury wax, ceresin wax, candellila wax, s_qgar cane wax, stearic
acid, palmitic acid, behenic acid, aluminum stearate, lead stearate, barium stearate,
magnesium stearate, zinc stearate, lithium stearate, and zinc palmitate. Other useful
waxes include N(betahydroxyethyl)-ricinoleamide, N,N'ethylene-bis-ricinole- amide,
N(2-hydroxyethyl)-12-hydroxystearamide, and N,N'-ethylene-bis-1-hydroxystearamide.
[0036] Preferably a colorant is incorporated into the binder of the imaging powder. Suitable
colorants include pigments and dyes. Examples of useful pigments include carbon black,
Prussian blue, magnetic iron oxide (i.e. magnetite). Useful dyes include phthalocyanine
dyes.
[0037] The imaging powder may readily be prepared by known techniques. For example, the
binder may be heated until it forms a molten mass and the colorant or other desired
ingredients added thereto and mixed therewith until a relatively homogeneous mass
results. The molten mass may then be cooled until solid and the solid material crushed.
The resulting irregularly shaped chunks may be used as such or, alternatively, they
may be converted to spherical particles by passing them through a heated gas stream
as is described in U.S. Patent 3,639,245. In either event, the powder is preferably
classified to obtain the desired particle size.
[0038] Examples of useful imaging powders include those described in United States Patent
3,925,219; 3,965,022; 3,775,326; 3,829,314; 3,639,245; 3,377,286; 3,590,000, 3,577,345;
and 3,694,359, and British Patent No. 1,210,665, each of which are incorporated herein
by reference. Other useful imaging powders are Xerox 6500 magenta imaging powder and
Type 690 imaging powder obtained from Minnesota Mining and Manufacturing Company.
[0039] The foregoing list of useful imaging powders is illustrative only. Other such powders
are also useful in the invention.
[0040] The imaging powders may be used by themselves or in conjunction with a carrier material
while the latent image is being developed.
[0041] In the process of the invention a latent image pattern is first formed on the coated
substrate. Any thermal printing means, such as a hot stylus, a branding iron, a jet
of hot air, a thermal print head, or a laser may be used to provide the latent image.
[0042] In one embodiment of the invention the latent image comprises a series of melted
dot-like areas on the coating. These areas may be provided by any of the techniques
described above, although the following description refers to the use of a thermal
print head.
[0043] Thermal print heads are known. In the simplest sense they comprise at least one resistance
element between two conductors. The thermal print head may also comprise an array
of resistance elements. Thus, for example, there may be a 5 by 7 element array on
the print head. Additionally, the print head may be fixed or moveable with respect
to the surface to be imaged.
[0044] The latent image pattern is formed by contacting the resistance element to the coating
providing electric current to the element for a time sufficient to heat the element
and raise its temperature to a level sufficient to melt the coating in the area of
contact, discontinuing the electric current to the element, and relocating the element
on the coating. The steps of contacting, heating and relocating are repeated until
a sufficient number of melted dot-like areas have been provided to define the desired
latent liquid image.
[0045] When the print head has only a single element, the steps necessary to form the latent
image must be repeated frequently before an image has been defined. When the print
head comprises an array (or matrix) of elements, the steps necessary to form the latent
image formation need be repeated fewer times.
[0046] The print head may be positioned by mechanical means (such as keys) digital means,
or the like. Subsequently, the print head receives an electrical signal that is converted
to heat for an appropriate length of time and at the appropriate location on the substrate.
[0047] After formation of the latent im
gg
!2L the imaging powder may be applied thereto in a variety of ways. Preferably, however,
a magnetic development technique is utilized. This, of course, necessitates that the
powder contain magnetically responsive material such as iron or iron oxide. In this
technique, a rotating magnetic developer roll attracts the powder to its surface and
transports it to the image area where the powder is then attached to the image area
but not to the background area.
[0048] Other development techniques are also useful. Thus, one may employ a carrier material,
such as iron filings, and maintain the imaging powder in close proximity to the carrier
via triboelectric charging. The carrier and imaging powder may then be contacted with
the latent image by, for example, a magnetic brush technique.
[0049] Still further, the imaging powder may be applied to the latent image areas by merely
brushing it over the images by means of for example, a camel hair brush. The imaging
powder exhibits differential adhesion to the image and non-image areas after development
but prior to fixing. Thus the powder is removable from the non-image areas by vibration
while it remains adhered to the image areas.
[0050] After development by, for example, one of the foregoing techniques, the powder is
fixed, by means of pressure only, to provide a permanent image on the substrate. The
pressure required for fixing is surprisingly low. For example, it has been found that
as little as about 4 kg/lineal cm provides permanent images. Preferably, when prints
are made on office bond paper, pressure from about 15 to 25 kg/lineal cm can be used
to give permanent images without giving objectionable paper calendaring.
[0051] The permanency of the images produced by the invention may be demonstrated by means
of its "Crock" adhesion density (CAD) and its optical density. The "Crock" adhesion
density is determined from a mechanical rub test known as the Crockmeter test. In
this test, a 1.6 cm diameter rod having a flat circular rubbing surface is provided.
A weight of 219 g is loaded onto the rod. A white fabric (Crockmeter square from Test
Fabrics, Inc.) is placed over the rubbing surface of the rod. The pad is then cycled
over a solid image area in a back and forth manner so that it travels a distance of
63.5 cm. The optical density ("Crock" Adhesion Density) of the fabric surface is then
measured using a Mac Beth Quanta-Log Diffuse Reflection Densitometer, Model RD-100.
As the CAD value increases, the amount of toner powder removed from the fixed image
increases.
[0052] The process of the present invention preferably provides a CAD no greater than about
0.6. More preferably, the CAD is no greater than about 0.5 and most preferably no
greater than about 0.4. A CAD of 0.6 corresponds to that obtained from the image produced
by a #2 pencil while a CAD of 0.4 corresponds to that obtained from the image produced
by a #3 pencil. Both of such images are considered permanent.
[0053] The image density relates to the amount of toner covering the substrate in an image
area. Thus, higher image density values indicate that more toner powder is fixed thereto.
Image density is determined on an image which has not been subjected to the Crockmeter
test. A Mac Beth Quanta-Log as described above is utilized in the density determination.
[0054] Preferably the process of the present invention provides an image having a density
of at least about 0.5. More preferably, it provides an image having a density of at
least about 0.6, and most preferably an image having a density of at least about 0.7.
[0055] Both the Crockmeter test and the image-density test are run on black images as the
MacBeth Quanta-Log is designed for density determination of black images.
[0056] The substrate employed in the process of the invention may be chosen from a variety
of materials. Preferably it is thin and flexible and may be transparent or opaque.
Thus, the substrate may be selected from, for example, paper, polymeric films such
as polyesters, cellulose triacetate, polypropylene, etc., anodically oxidized aluminum
and foils of metals such as aluminum, copper, zinc, etc.
[0057] The present invention is illustrated by the following examples.
Example 1
[0058] A sheet of machine finished paper (37 lb. (16.8 kg), 3000 ft
2 (278.7 m
2) ream) was coated with a solution comprising 24% by weight dicyctohexytphthaiate
(DCHP), m.p. 63°C, 5% by weight ethyl cellulose (Hercules, Incorporated N-200) and
-71 % by weight acetone.
[0059] The coated paper was dried by allowing the acetone to evaporate for about 10 minutes
into a room at normal temperature and humidity to provide a dried coating weight of
2.7 g/m
2. The dried coated substrate was aged for one week to insure that the DCHP was in
a crystalline state. The crystallization process may be accelerated by seeding the
coated substrate with dry DCHP. The dried coated paper was then cut into 2 inch (5
cm) wide strips.
[0060] Latent image areas were provided on one strip of the dry coated paper by passing
it through an Olivetti Divisumma 33 electronic printing calculator. This calculator
heated the imaged areas of the paper to about 100°C. The latent image areas were then
contacted with a dry, pressure-fixable imaging powder described in United States Patent
3,925,219 and consisting essentially of
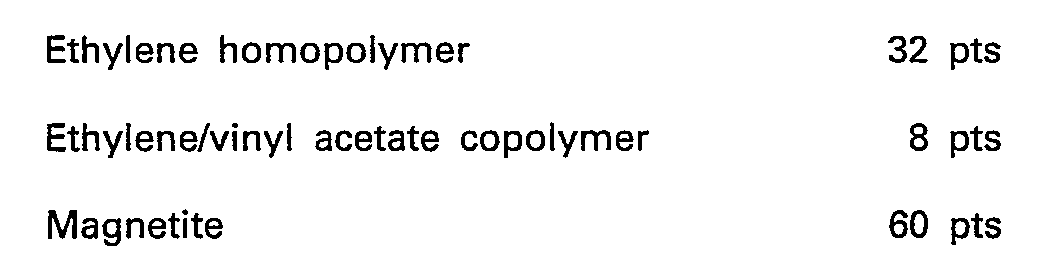
[0061] The imaging powder adhered to the image areas but did not adhere to the non-image
areas and was readily removed therefrom. The image areas of the strip were then permanently
fixed by passing them through the pressure fixing rolls of a Model 732 copier operating
at a fixing pressure of 24.5 kg/lineal cm and being available from the Minnesota Mining
and Manufacturing Company. Sharp, permanently bonded black images on white paper were
obtained. The images could not be removed by rubbing them with a finger.
[0062] Latent areas were then provided on other strips of the sheet of this Example by heating
the strips to a temperature slightly over 63°C using a hot plate. The latent areas
were then contacted with the pressure-fixable toner powder described above. Before
fixing, the toned areas of the strips could be easily smeared by rubbing the areas
with a finger. However, after fixing, the toned areas were permanently affixed.
[0063] The pressure used to fix the toned areas on the strips and the results of the Crock
adhesion density and image density tests are tabulated in Table 1.
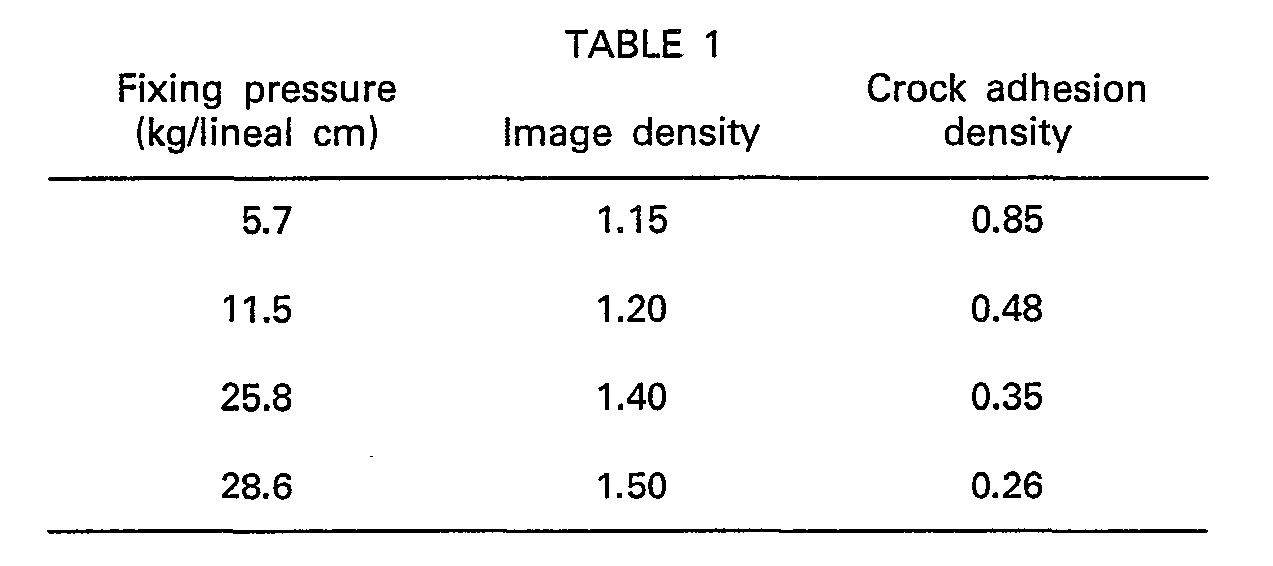
Example 2
[0064] A sheet of Substance 12 "Mirraform" paper manufactured by the Nekoosa Edwards Paper
Company was coated with a solution comprising 24% by weight diphenyl phthalate (DPP),
m.p. 75°C, 5% by weight ethyl cellulose (N-200 from Hercules, Incorporated) and 71
% by weight acetone. The coating was dried as described in Example 1 to provide a
dried coating weight of 2.7 g/m
2. The sheet was then aged for over one week to insure all the DPP was in the crystalline
state. The dried sheet was cut into individual strips.
[0065] One of the strips of the dry coated paper of this example was imaged, toned, and
fixed according to the procedures, and with the imaging powder, described in Example
1. Sharp, permanently bonded black images on white paper were obtained. The images
could not be removed by rubbing them with a finger.
[0066] Latent areas were provided on other strips of the sheet of this example by heating
the strips to a temperature over 75°C using a hot plate. The latent areas were then
contacted with the pressure-fixable imaging powder described in Example 1. The toned
area of the strips could be easily smeared by rubbing the area with a finger.
[0067] The toned areas of these strips were then fixed by subjecting them to different pressures.
They were then tested for crock adhesion density and image density. The results are
tabulated in Table 2.
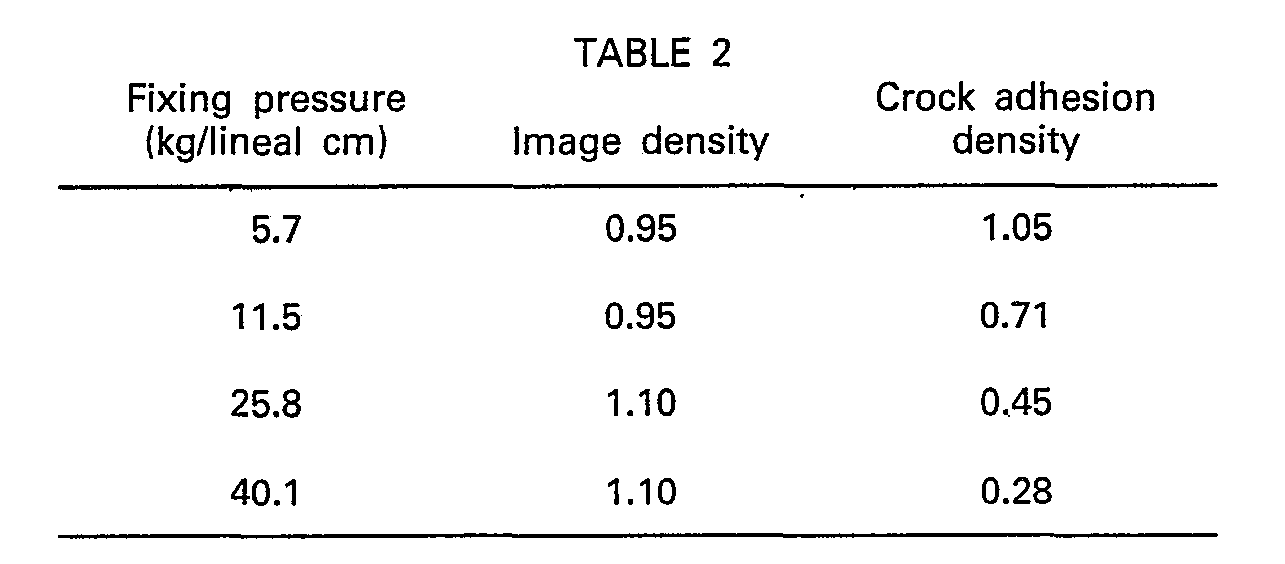
Example 3
[0068] - Substance 14 "Mirraform" paper manufactured by the Nekoosa Edwards Paper Company
was coated with a solution comprising 25% by weight triphenyl phosphate (TPP), m.p.
50°C, and 75% by weight acetone. The coating was dried as described in Example 1 to
provide a dried coating weight of 4.3 g/m
2. The resultant sheet was aged for about 3 hours and was then cut into individual strips.
[0069] One of the strips of the sheet of this example was imaged, toned and fixed according
to the procedures described in Example 1. The imaging powder employed to tone the
image areas was a heat fusible thermoplastic material of the type described in United
States Patent 3,639,245. Surprisingly, the powder was pressure-fixable when used in
conjunction with the TPP image. Sharp, permanently bonded black images on white paper
were obtained. The images could not be removed by rubbing them with a finger.
[0070] Latent image areas were provided on other strips of the sheet of this example by
heating the strips over a hotplate to slightly over 50°C. The latent image areas were
then contacted with the imaging powder employed previously in this example. The toned
areas of the strips could be easily smeared by rubbing the area with a finger.
[0071] The toned areas were then fixed by subjecting them to different pressures and tested
for crock adhesion density and image density. The results are tabulated in Table 3.
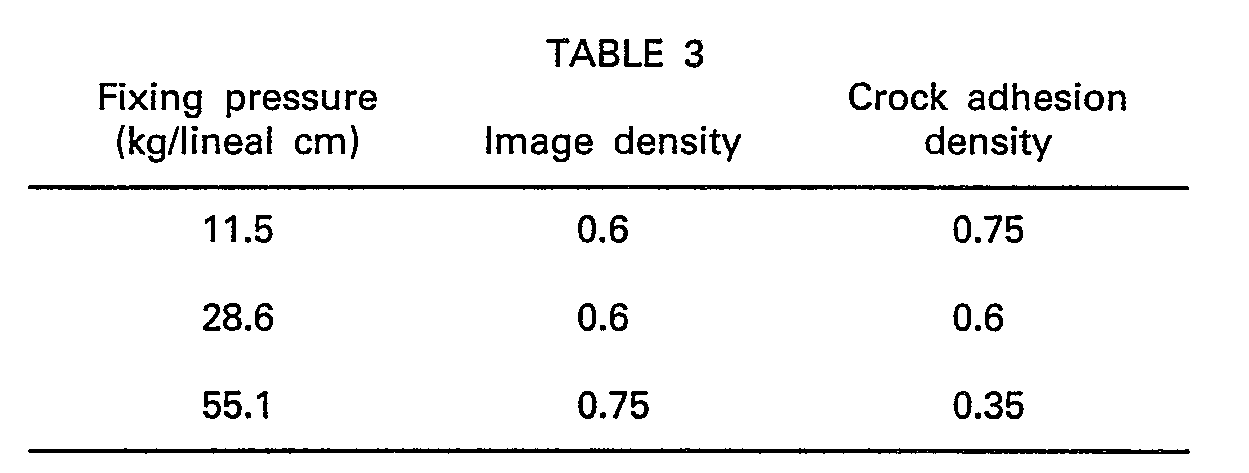
[0072] The words "Santicizer", "Xerox", "Crock" and "Mirraform" are believed to be Registered
Trade Names.
1. Verfahren zur Erzeugung eines bleibenden Bildes auf einem Substrat, das eine Beschichtung
aus einem normalerweise festen, nichtklebrigen Material trägt, das eine Schmelztemperatur
von mindestens 10°C über Raumtemperatur hat und das beim Abkühlen auf eine Temperatur
unter ihrer Schmelztemperatur eine unterkühlte Schmelze bildet, in der das bleibende
Bild durch die folgenden nacheinander durchgeführten Schritte erzeugt wird:
Ausbildung eines latenten flüssigen Bildmusters auf der genannten Beschichtung durch
bildhaftes Inberührungbringen der Beschichtung mit einer thermischen Druckeinrichtung
für ausreichende Zeit, um die Temperatur des genannten nichtklebrigen Materials mindestens
auf seine Schmelztemperatur zu erhöhen;
Inberührungbringen des latenten flüssigen Bildmusters mit einem trockenen bilderzeugenden
Pulver, das an dem latenten flüssigen Bildmuster haftet;
gekennzeichnet durch den Schritt:
Anlegen ausreichenden Druckes an das bildformende Pulver, um es zu verformen und in
das latente flüssige Bildmuster einzubetten und darauf eine praktisch gleichmäßige
und für das Auge kontinuierliche Masse zu erzeugen.
2. Verfahren nach Anspruch 1, dadurch gekennzeichnet, daß das nichtklebrige Material
Dicyclohexylphthalat, Diphenylphthalat, Triphenylphosphat, Dimethylfumarat, Benzotriazol,
2,4-Dihydroxybenzophenon, Tribenzylamin, Benzil, Vanillin, Phthalophenon oder ein
Gemisch von Ortho- und Paratoluolsulfonamiden ist.
3. Verfahren nach Anspruch 2, dadurch gekennzeichnet, daß das feste Material Dicyclohexylphthalat
ist.
4. Verfahren nach Anspruch 2, dadurch gekennzeichnet, daß das feste Material Triphenylphosphat
ist.
5. Verfahren nach Anspruch 2, dadurch gekennzeichnet, daß das feste Material eine
feste Lösung von Dicyclohexylphthalat und Diphenylphthalat ist.
6. Verfahren nach einem der vorangehenden Ansprüche, dadurch gekennzeichnet, daß die
thermische Druckeinrichtung einen thermischen Druckkopf mit mindestens einem Widerstandselement
zwischen zwei Konduktoren umfaßt und wobei das latente flüssige Bildmuster erzeugt
wird durch (a) Inberührungbringen des Widerstandselementes mit der Beschichtung, (b)
Zuführung von elektrischem Strom zu dem Widerstandselement für ausreichende Zeit,
um das Widerstandselement auf eine Temperatur zu erhitzen, bei der die Beschichtung
am Berührungspunkt schmilzt, (c) Unterbrechung der Stromzufuhr zu dem Widerstandselement,
(d) erneutes Anbringen des Widerstandselementes an die Beschichtung und (e) Wiederholung
der Schritte (a) bis (d) bis das latente flüssige Bildmuster erzeugt ist.
7. Verfahren nach einem der vorangehenden Ansprüche, dadurch gekennzeichnet, daß das
Substrat 0,1 bis 5 g/m2 der Beschichtung aufweist.
8. Verfahren nach Anspruch 7, dadurch gekennzeichnet, daß das Substrat etwa 0,1 bis
2 g/m2 der Beschichtung aufweist.
9. Verfahren nach einem der vorangehenden Ansprüche, dadurch gekennzeichnet, daß die
Beschichtung auf der Oberfläche des Substrats haftet.