[0001] This invention relates to liquid detergent compositions and especially to so-called
light duty liquids intended primarily for dishwashing. More particularly the invention
concerns dishwashing liquid detergent compositions that have been formulated to secure
improved particulate soil removal ability without any loss in other performance areas
such as grease and oily soil removal and sudsing capability.
[0002] The greasy and/or oily nature of the majority of food residues has resulted in grease
and oily soil removal being the prime focus of dishwashing detergent performance,
together with the need to provide a satisfactory volume of suds over the duration
of the dishwashing task. This has been reflected in the composition of liquid detergent
products formulated primarily or exclusively for dishwashing, such products conventionally
comprising a combination of one or more surfactants and suds builders dissolved or
dispersed in a hydrotrope-water system.
[0003] Dishwasing liquid detergent formulations of this type include magnesium salts and
magnesium surfactants such as alkyl sulphates, alkyl ether sulphates and alkyl benzene
sulphonates and GB-A-1,524,441, 1,551,074, 2,010,893A and EP-A-0039110 are representative
disclosures of the state of the art. The art teaches that these formulations have
enhanced performance, particularly when used in water of low mineral hardness. Dishwashing
liquid detergent compositions containing alkane and alkene sulphonates are also known,
examples of such disclosures including those in GB-A-1,050,848,1,339,069, 1,382,295,
1,451,228, 1,551,074 and 1,567,421.
[0004] Formulations of this type employing total surfactant levels in excess of 25% by weight
cannot tolerate significant levels of inorganic detergent builder salts whilst retaining
a clear single phase solution form and additionally, the presence of inorganic salts
gives rise to aesthetically undesirable residues on the washed crockery or cutlery.
Consequently, these formulations are normally substantially completely free of detergent
builder salts, while metal chelating agents, if incorporated, are only employed in
trace amounts.
[0005] Nevertheless, particulate materials are also a significant component of food residues
and the low levels, or total absence, of detergent builder materials in conventional
dishwashing liquid detergents make these formulations less than optimum in terms both
of suds stability in the presence of particulate soil and of particulate soil suspension
during the washing process. It has now been found that, certain combinations of ingredients,
more particularly an alkali earth metal alkyl sulphate and an ethoxylated alcohol,
can provide an unexpected improvement in particulate soil handling capability without
any sacrifice of the grease and oily soil removal performance of a dishwashing liquid
formulation.
[0006] The employment of ethoxylated alcohols as components of dishwashing liquids is known
in the art, exemplified by GB-A-1,567,421 and GB-A-1,551,074. However, the benefit
asserted for their inclusion is principally in the area of suds boosting and, to a
lesser extent, greasy soil removal. Moreover the utilisation of ethoxylated alcohols
in dishwashing liquids is limited by the increase in chill point temperature which
they cause. For example, their incorporation into formulations such as are disclosed
in EP-A-0039110 results in products that show an insignificant performance benefit
together with totally unacceptable stability characteristics. Thus the finding that
the compositions of the invention have particulate soil removal efficacy together
with acceptable physical characteristics is the more unexpected.
[0007] According to the present invention therefore there is provided a clear homogeneous
magnesium containing liquid detergent composition having a chill point of not more
than 5°C comprising a surfactant mixture in a hydrotrope-water system, characterised
in that the surfactant mixture is formed by the combination of
a) a water soluble C13―C18 alkane or C12―C16 alkene sulphonate,
b) a water soluble alkyl polyethoxy sulphate wherein the alkyl group contains from
10 to 16 carbon atoms and the polyethoxy group contains an average of from 0.5―6 ethoxy
groups,
c) 2.0-5.0% by weight of the composition of an ethoxylated primary C8-Cl2 alcohol having an HLB in the range 7.5-12.0,
d) 6-18% by weight of the composition of a primary C10―C16 alkyl sulphate,
the composition comprising the magnesium ion in an amount corresponding to 0.40X-0.60X,
where X is the molar amount of said primary C
10―C
16 alkyl sulphate.
[0008] The present invention comprises a surfactant system containing paraffin or olefine
sulphonate, alkyl ether sulphate, alkyl sulphate and ethoxylated nonionic surfactant
components in a liquid vehicle composed of hydrotrope and water.
[0009] The alkyl sulphate surfactant component is a primary alkyl sulphate in which the
alkyl group contains 10-16 carbon atoms, more preferably an average of 12-15 carbon
atoms preferably in a linear chain. C
10―C
16 alcohols, derived from natural fats or Ziegler olefin build-up or oxo synthesis,
form suitable sources for the alkyl group. Examples of synthetically derived materials
include Dobanol 23 (RTM) sold by Shell Chemicals (UK) Ltd, Ethyl 24 sold by the Ethyl
Corporation, a blend of C
13―C
15 alcohols in the ratio 67% C,
3, 33% C,
5 sold under the trade name Lutensol by BASF GmbH and Synperonic (RTM) by ICI Ltd,
and Lial 125 (a highly branched C
12―C
15 primary alcohol) sold by Liquichimica Italiana. Examples of naturally occurring materials
from which the alcohols can be derived are coconut oil and palm kernel oil and the
corresponding fatty acids.
[0010] The alkyl sulphate component is present at a level of from 6% to 18% by weight of
the composition, more generally from 8% to 16% by weight.
[0011] For the purposes of the present invention the alkyl sulphate is associated with a
source of magnesium ions which, as will be described hereinafter, can either be introduced
as the oxide or hydroxide to neutralise the acid or can be added to the composition
as a water soluble salt. However, the addition of appreciable levels of magnesium
salts to the dishwashing compositions of the invention raises the temperature at which
inorganic salt crystals form in the compositions on cooling and is therefore less
preferable. The molar amount of magnesium ion in the compositions is controlled to
correspond to 0.40-0.60X preferably 0.45-0.55X where X is the number of moles of C
10―C
16 alkyl sulphate present. Most preferably the magnesium ion content is adjusted to
provide the stoichiometric equivalent of the alkyl sulphate present. In practice the
magnesium ion will be present at a level of from 0.15% to 0.70% by weight, preferably
from 0.35% to 0.60% by weight of the composition.
[0012] The paraffin sulphonate (s-alkane sulphonate), or a-olefine sulphonate (alkene sulphonate)
component comprises from 3% to 15%, more preferably from 4% to 12% by weight of the
formulation.
[0013] Secondary alkane sulphonates useful in the present invention preferably have from
13 to 18 carbon atoms per molecule, and most desirably from 14 to 17, and are characterised
by a high solubility in water compared to alkyl aryl sulphonates and other sulphuric
acid reaction products used for dishwashing detergent compositions. These sulphonates
are preferably prepared by subjecting a cut of paraffin, corresponding to the chain
lengths specified above, to the action of sulphur dioxide and oxygen in accordance
with the well-known sulphoxidation process. The product of this reaction is a secondary
sulphonic acid which is neutralized with a suitable base to provide a water-soluble
secondary alkyl sulphonate. Similar secondary alkyl sulphonates may be obtained by
other methods, e.g. by the sulpho- chlorination method in which chlorine and sulphur
dioxide are reacted with paraffins in the presence of actinic light, the resulting
sulphonyl chlorides being hydrolyzed and neutralized to form the secondary alkyl sulphonates.
Whatever technique is employed, it is normally desirable to produce the sulphonate
as the monosulphonate, having no unreacted starting hydrocarbon or having only a limited
proportion thereof present and with little or no inorganic salt by-product. Similarly,
the proportions of disulphonate or higher sulphonated material will be minimized but
some may be present. The monosulphonate may be terminally sulphonated or the sulphonate
group may be joined on the 2-carbon or other carbon of the linear chain. Similarly,
any accompanying disulphonate, usually produced when an excess of sulphonating agent
is present, may have the sulphonate groups distributed over different carbon atoms
of the paraffin base, and mixtures of the monosulphonates and disulphonates may be
present.
[0014] Mixtures of monoalkane sulphonates wherein the alkanes are of 14 and 15 carbon atoms
are particularly preferred wherein the sulphonates are present in the weight ratio
of C
14 to C
15 paraffins in the range from 1:3 to 3: 1, preferably 1:2 to 2: 1. Surprisingly, this
particular mixture produces detergents which clean dishes better and which suds longer,
especially in hard water, than other mixtures of paraffin sulphonates, e.g. those
of 13 to 17 carbon atoms. This is also true, to a lesser extent, of the individual
components of the C
14 and C,
5 mixture.
[0015] The term 'a-olefine sulphonates' or 'alkene sulphonates' is used herein to mean compounds
which can be produced by the sulphonation of alpha-olefines by means of uncomplexed
sulphur trioxide, followed by neutralization of the acid reaction mixture in conditions
such that any sultones which have been formed in the reaction are hydrolysed to give
the corresponding hydroxy-alkane sulphonates. The sulphur trioxide may be liquid or
gaseous, and is usually, but not necessarily, diluted by inert diluents, for example
by liquid S0
2, chlorinated hydrocarbons, etc., when used in the liquid form, or by air, nitrogen,
gaseous S0
2, etc., when used in the gaseous form.
[0016] The alpha-olefines from which the olefine sulphonates are derived are mono-olefines
having 12 to 16 carbon atoms, preferably 12 to 14 carbon atoms. Preferably, they are
straight chain olefines. Olefine sulphonates having more than 16 carbon atoms do not
give the desired high lathering performance in the mixtures according to the invention;
those with fewer than 12 carbon atoms have reduced detergent properties. In addition
to the true alkene sulphonates and a proportion of hydroxy-alkane sulphonates, the
olefine sulphonates may contain minor amounts of other materials, arising from impurities
in the original olefine stock and from side reactions during the sulphonation and
neutralisation processes.
[0017] The alkyl ether sulphate component comprises a primary alkyl ethoxy sulphate derived
from the condensation product of a C
lo-Cl, alcohol with an average of from 0.5 to 6 ethylene oxide groups. The C'O-C'6 alcohol
itself can be obtained from any of the sources previously described for the alkyl
sulphate component. It has, however, been found preferable to use alkyl sulphate and
alkyl ether sulphate in which the carbon chain length distributions are the same.
C
12―C
15 alkyl ether sulphates are preferred and the level of alkyl ethoxy sulphate in the
compositions lies between 0.5% and 20% by weight of the compositions, generally in
the range from 4% to 14% by weight.
[0018] The conventional average degree of ethoxylation is from 0.5 to 3 groups per mole
of alcohol, but as conventional ethoxylation processes result in a distribution of
individual ethoxylates ranging from 1 to 10 ethoxy groups per mole of alcohol, the
average can be obtained in a variety of ways. Blends can be made of material having
different degrees of ethoxylation and/or different ethoxylate distributions arising
from the specific ethoxylation techniques employed and subsequent processing steps
such as distillation. In fact, it has been found that equivalent sudsing and grease
removal performance to that given by a blend of alkyl sulphate and alkyl ethoxy ether
sulphate can be obtained by reducing the overall level of ethoxylation and using an
alkyl ether sulphate in which the ratio of ethoxylated to unethoxylated alkyl sulphate
is the same as would be obtained by mixing the separately prepared surfactants.
[0019] The cations, other than magnesium, that may be used in the neutralisation of the
anionic surfactants may be sodium, potassium, ammonium or alkanolammonium, but ammonium
is a preferred cation because of its depressive effect on the chill point temperature
of the compositions. Preferred compositions have chill points of less than 0°C.
[0020] The surfactant system also comprises an ethoxylated C
8―C
12 primary alcohol having an HLB (hydrophilic-lipophilic balance) in the range from
7.5 to 12.0, preferably from 8.0 to 9.5. The primary alcohol may be linear or branched
in structure and can be derived from sources such as those described in connection
with the alkyl sulphate component. Preferred materials are those in which the alcohol
is derived from a C
9―C
11 hydrocarbon fraction in which the hydrocarbon material contains up to 25% methyl
branching, and the level of ethoxylation provides an average of 2-3, more preferably
2.5 ethoxy groups per mole of alcohol.
[0021] Typical composition ranges for the surfactant combinations described above are
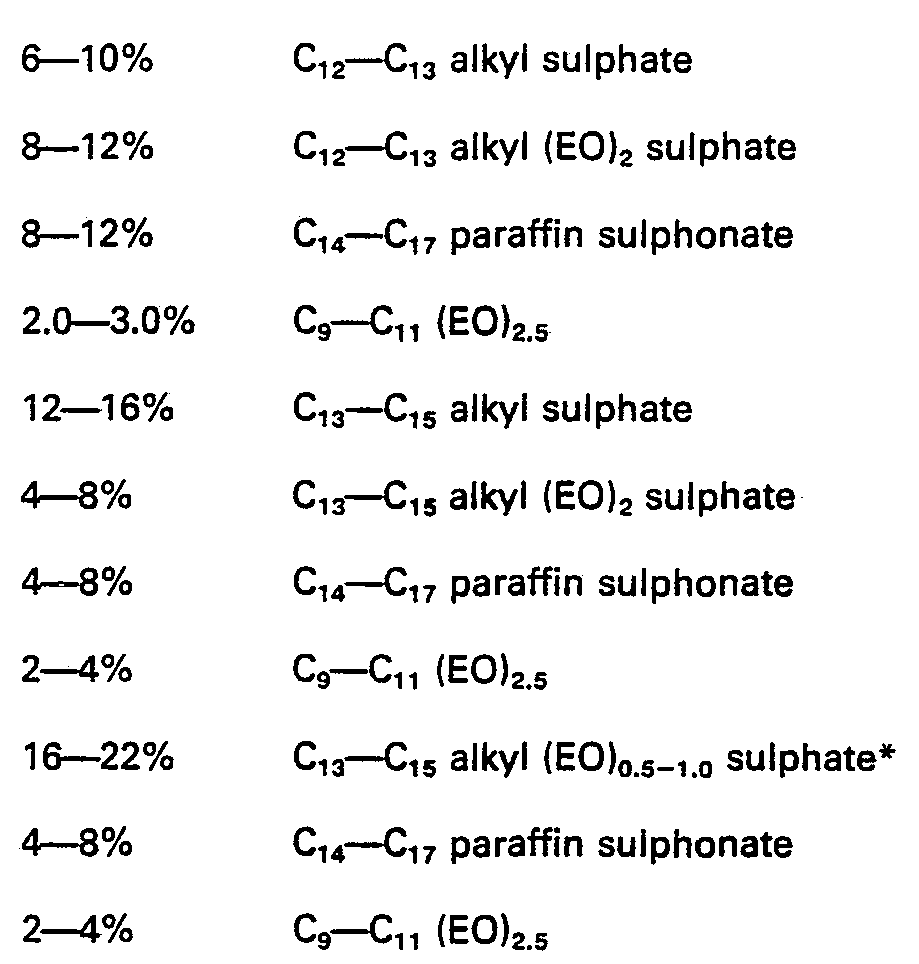
[0022] A desirable optional component of the invention is a suds boosting agent at a level
of up to 5%, preferably from 3% to 4% by weight.
[0023] The suds-promoting agent may be selected from C
12―C
14 mono- and di-C2--C3 alkanolamide, C
12―C
14 alkyl amides condensed with up to 15 moles of ethylene oxide per mole of amide and
tertiary amine oxides containing a C
8-C,
8 alkyl group.
[0024] Examples of the alkanolamides are coconut alkyl monoethanolamide, coconut alkyl diethanolamide
and coconut alkyl mono and di isopropanolamides.
[0025] Examples of the ethoxylated amides include coconut alkyl amide condensed with an
average of six moles of ethylene oxide, lauryl amide condensed with an average of
eight moles of ethylene oxide, myristyl amide condensed with an average of ten moles
of ethylene oxide and coconut amide condensed with an average of eight moles of ethylene
oxide. Amine oxides useful in the present invention have one alkyl or hydroxyalkyl
moiety of from 8 to 18 carbon atoms, preferably from 8 to 16 carbon atoms and two
moieties selected from alkyl groups and hydroxyalkyl groups containing 1 to 3 carbon
atoms. Examples of such amine oxides include dimethyl octylamine oxide, diethyldecylamine
oxide, bis-(2-hydroxyethyl)dodecylamine oxide, methylethyl hexadecylamine oxide, and
dimethyl
-2-hydroxyoctadecylamine oxide.
[0026] A highly preferred example of the tertiary amine oxide is a C
12-C
14 alkyl dimethyl amine oxide in which the C
12―C
14 alkyl group is derived from coconut oil.
[0027] The balance of the formula comprises a hydrotrope-water system in which the hydrotrope
may be urea, a C
l-C
3 alkanol, or a lower alkyl benzene sulphonate salt such as toluene, cumene or xylene
sulphonate. The preferred hydrotrope is ethanol which is employed at from 3% to 10%
by weight of the composition, preferably at from 4% to 8%.
[0028] Optional ingredients of the liquid detergent compositions of the invention include
thickeners such as guar gum, antibacterial agents such as glutaraldehyde and Bronopol
(RTM), antitarnish agents such as
* This corresponds to 12-16% alkyl sulphate and 4―6% of an ethoxylated C13―C15 alkyl sulphate having an average degree of ethoxylation of approximately 2.
benzoxytriazole, heavy metal chelating agents such as EDTA or EDTMP, perfumes and
dyes. The pH of the compositions may be anywhere within the range from 6 to 7.5 but
as manufactured the compositions normally have a pH in the range from 6.6 to 7.3,
preferably from 6.6 to 6.9 in order to maintain colour stability.
[0029] The technique of incorporation of the magnesium ions is not thought to be critical
and the compositions can be made in a number of ways.
[0030] The individual anionic surfactants can be made as aqueous solutions of alkali metal
or ammonium salts which are then mixed together with the hydrotrope, and the suds
booster, if this is included, following which the magnesium ion can be introduced
as a water soluble salt such as the chloride or acetate. Optional minor ingredients
are then added after which the pH and viscosity is adjusted. This method has the advantage
of utilising conventional techniques and equipment but results in the introduction
of additional chloride or acetate ions which can increase the chill point temperature
(the temperature at which inorganic salts precipitate as crystals in the liquid).
[0031] An alternative method of carrying out the invention is to mix the alcohol and alcohol
ethoxylate together and carry out a single sulphation and neutralisation. For this,
the alcohol and alcohol ethoxylate should be mixed in a weight ratio lying in the
range 45:1 to 1:5.5. Sulphation can take place by means of any of the conventional
sulphating agents such as e.g., sulphur trioxide or chlorosulphonic acid. Neutralisation
of the alkyl ether sulphuric acid and the alkyl sulphuric acid is carried out with
a magnesium oxide or hydroxide slurry which avoids the addition of chloride or sulphate
ions. Although not essential, it is convenient to use a mixture of these acids as
the magnesium salt of the alkyl ether sulphuric acid has relatively greater aqueous
solubility than the alkyl sulphuric acid component. The separately neutralised paraffin
sulphonate salt, and the neutralised alkyl and alkyl ether sulphate salts and the
hydrotrope are then added to the final mixing tank and the C
B-C,
2 alcohol ethoxylate and any optional ingredients added before the pH is adjusted as
above.
[0032] A further and preferred modification of the above technique involves the preparation
of a single alcohol ethoxylate feedstock whose composition is the same as, or closely
approximates that of, the alcohol and alcohol ethoxylate blend. For the purposes of
the present invention alcohol ethoxylates having an average degree of ethoxylation
in the range 0.5 to 1.0, more usually 0.75 to 0.95 are preferred.
[0033] Modifications of this latter technique can also be employed in which either the neutralised
paraffin sulphonate salt or the neutralised alkyl sulphate-alkyl ether sulphate mixture
are used as a 'heel' for the neutralisation of the acid form of the other, thereby
avoiding local overheating, formation of viscous phases etc.
[0034] The invention is illustrated in the following examples in which the percentage of
the components are by weight based on the finished composition.
Example I
[0035] The following composition was made up.
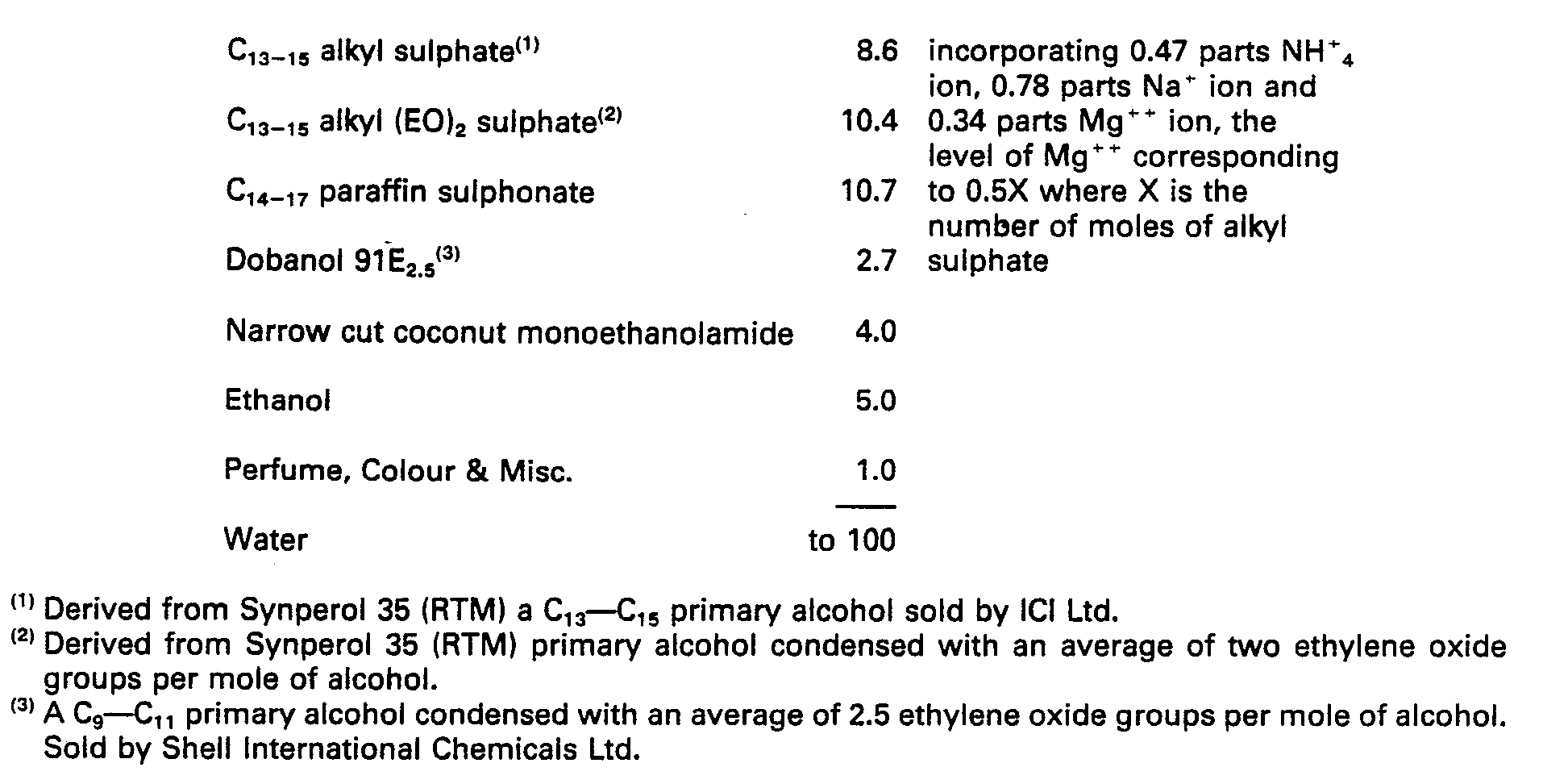
[0036] The paraffin sulphonate was performed by S0
2 sulphonation of C
14―C
17 n-alkanes and caustic soda neutralisation of the resultant sulphonic acid to give
an approximately 60% active paste starting material. This was diluted with water and
a little ethanol to form a 30% active solution in which the monoethanolamide was dispersed
with agitation to assist its solution. A blend of the alcohol and alcohol ether condensate
was sulphated using chlorosulphonic acid as the sulphating agent and the mixed sulphuric
acids were then neutralised with magnesium hydroxide and ammonia respectively. The
actual neutralisation (to pH 3.0) was carried out using a 'heel' formed by the diluted
paraffin sulphonate paste, in which the ammonia and magnesium hydroxide were dispersed
before addition of the mixed sulphuric acids. The pH was then trimmed to pH 6.6 with
ammonia before the ethoxylated nonionic and other minor ingredients (dye, perfume)
were added to form the final composition. The finished product had a viscosity of
0.23 Pa· s at 20°C and a chill point of -3°C.
Example II
[0037] The following composition is prepared using the same materials as in Example I.
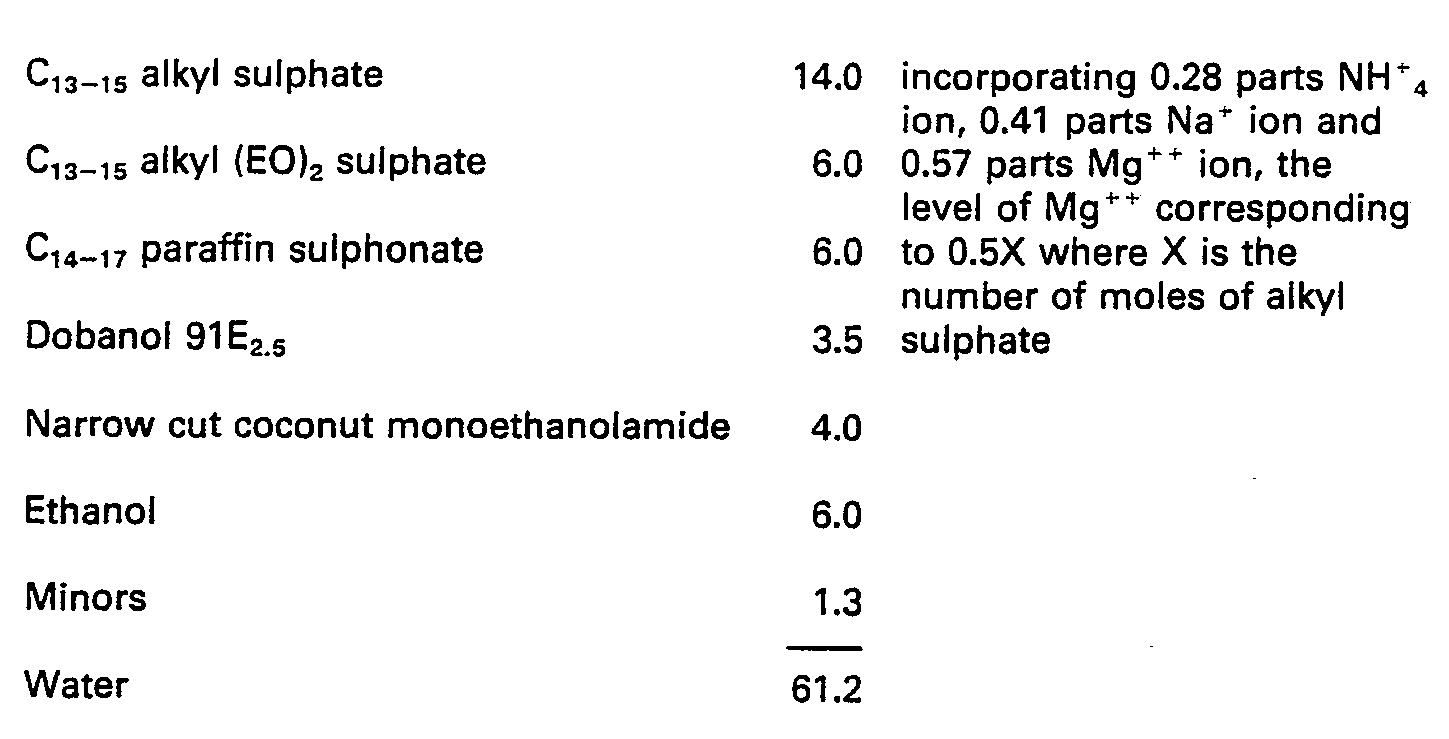
[0038] The n-paraffin is sulphonated and neutralised to produce the sodium paraffin sulphonate
as in Example I. The blend of C
12―C
13 alcohol and C
12―C
13 alcohol ethoxylate are sulphonated using gaseous S0
3 and are then neutralised by addition to an ethanol water mixture in which the ammonia
and magnesium hydroxide have been dispersed. Further ethanol, the amide and C
9―C
11 alcohol ethoxylate are added to this mixture together with paraffin sulphonate salt.
Perfume, colour and pH trimming acid forming the minor components are then added to
complete formation of the product which has a chill point of -3°C.
Example III
[0039] Four liquid detergent formulations were prepared having the following compositions.
Formulations A, B and C are commercially available liquid detergent products while
formulation D is in accordance with the invention.
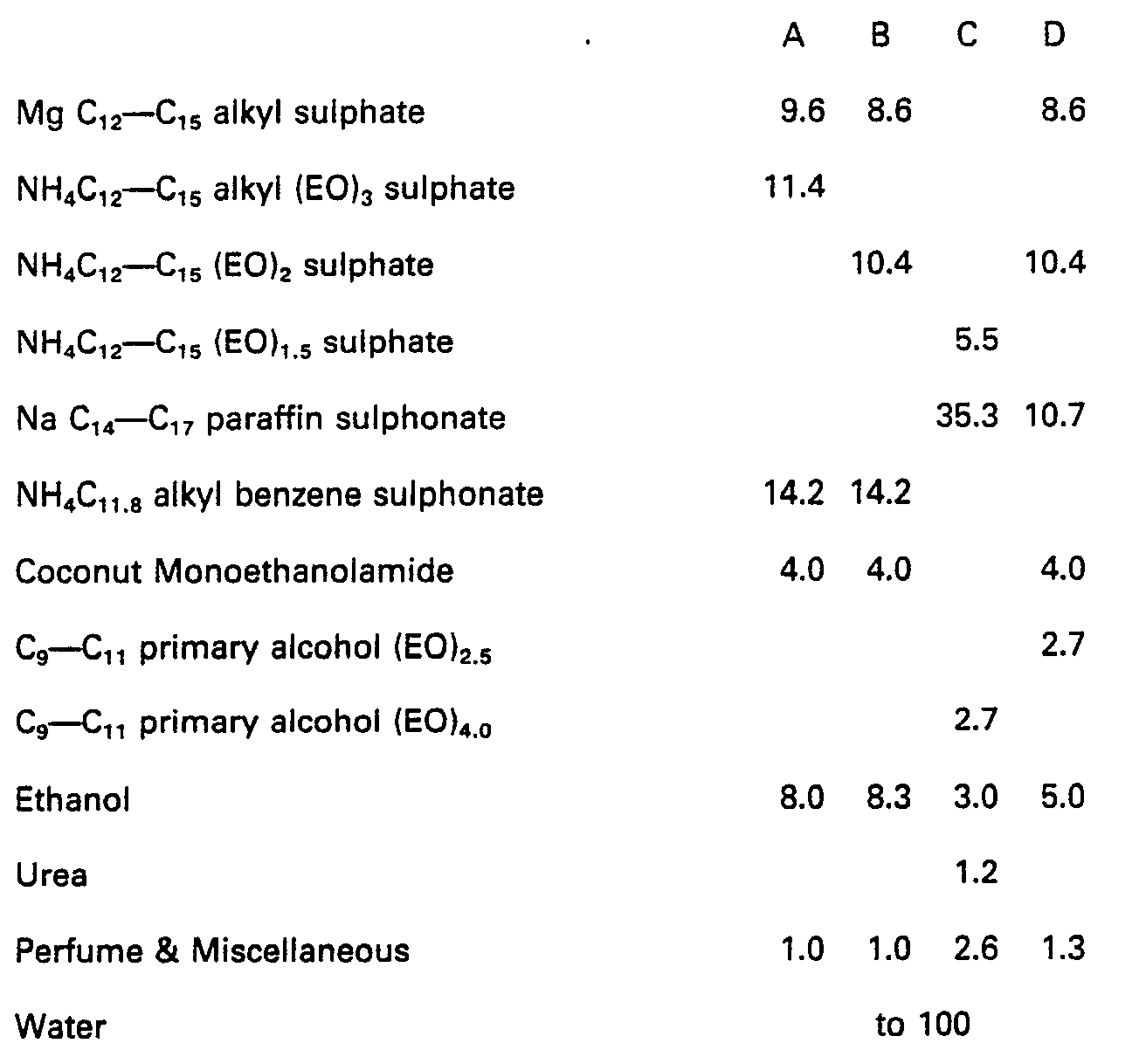
[0040] A series of comparative evaluations of the above formulations were run using the
mechanical sudsing test method described below.
[0041] This method uses 4 cylinders of length 30 cm and diameter 10 cm fixed side by side,
and rotatable at a speed of 24 rpm about a central axis. Each cylinder is charged
with 500 ml of product solution at a concentration of 0.12% and a temperature of 45°C.
The outer two cylinders are used for one of the products being compared and the inner
two for the other product.
[0042] The cylinders are rotated for 2 minutes, stopped, the initial suds are measured and
a soil load is then added. The grease soil comprises a mixture
* of fatty acids in a cooking oil base and 1 ml of this mixture (MFFA) is added to
each cylinder. Where particulate soil is included it is all added at this stage. After
1 minute the cylinders are restarted and allowed to rotate for 1 minute. The suds
height is noted and 1 ml of the 2% MFFA is added to each cylinder. After 1 minute
the cylinders are restarted. This process continues until the suds height in the cylinder
is lower than 0.5 cms.
* The grease soil comprised:
2 parts oleic acid
2 parts linoleic acid
1 part stearic acid
2.5 parts palmitic acid
367 parts pure corn oil to give a 2% Mixed Free Fatty Acid (MFFA) mixture
[0043] One product is designated as the control and suds and mileage figures are calculated
for the other product versus the 'control' product on the following basis.


[0044] Mileage figures of comparisons made using this test were as follows, the second-identified
product in each instance constituting the 'control'.
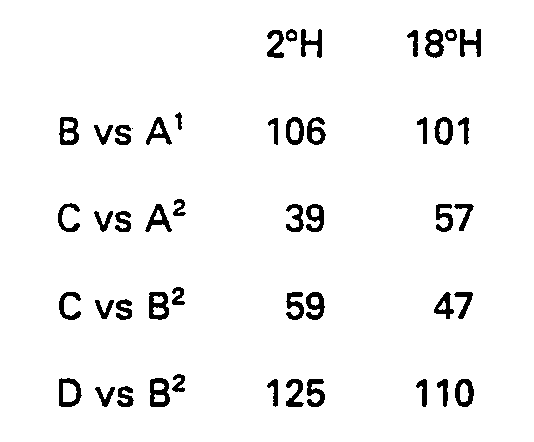
Suds figures of a comparison made between products D and B were as follows:
' The figures quoted are an average over a range of particulate - grease soil mixtures
including (i) 5 g cake mix (McDougalls Sponge Mix), 2% MFFA, (ii) 5 g gravy/flour,
2% MFFA, (iii) 5 g potato powder, 2% MFFA.
2 The figures quoted are for a 5 g cake mix, 2% MFFA soil mixture.
On the basis of the above tests it can be seen that the ranking of the formulations,
in terms of their mileage performance is
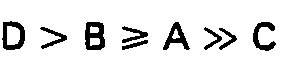
where D is a formulation in accordance with the invention. Moreover the above data
also shows that the sudsing performance of formulation D in the presence of particulate
soil is significantly better than that of formulation B.
[0045] In a further mileage evaluation, using soil (2) above, formulation B was compared
to formulation D and also to a formulation D' from which the ethoxylated primary alcohol
component was omitted.
[0046] The results are shown below, with formulation B serving as the 'control' and being
expressed as 100.
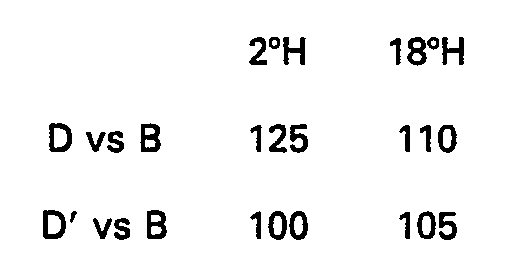
[0047] The benefit conferred by the incorporation of the nonionic component can be clearly
seen.
Example IV
[0048] Comparisons were made of the soil suspension performance of the formulations D &
B of Example III using the following test method.
[0049] Two 2 litre beakers were each charged with 1500 ml of soft water (2°H) at a temperature
of 40°C. A magnetic stirrer was placed in each beaker and activated, the stirring
mechanisms being adjusted so that both beakers were being stirred at the same rate.
20 g of cake mix, 15 ml of 2% MFFA and the desired weight of the detergent product
were weighed into each beaker, one product being the 'test' product and the other
forming the 'standard'. The solutions were then stirred for approximately 15 minutes
(to allow a homogeneous solution to be formed) after which the solutions were then
left to stand for 10 minutes during which time part of the solid soil separated out
on the bottom of the beakers, the remainder being maintained in suspension. The bulk
of the suspension was then decanted from each beaker so as to leave the same volume
of residual liquid in each and the water was then evaporated to give the cake mix
residue.
[0050] The beakers plus the residue were weighed, and the beakers were washed out and then
re-weighed to give the weight of residue. The test was then repeated reversing the
equipment for each product.
[0051] Deposition of soil was calculated on the following basis:

[0052] On this basis values > 100% indicate that the test product deposits more (i.e. is
worse) than the standard, while values < 100% indicate that the test product is superior
to the standard. The test is predictive of the ranking of products in terms of their
particulate soil suspension capability under normal usage conditions.
[0053] Using the above test with Product B forming the standard, Product D gave values of
92% at 0.4% product concentration and 80% at 0.25% product concentration thereby illustrating
the particulate soil suspension benefit provided by formulations in accordance with
the invention.
1. Eine klare, homogene, magnesiumhältige, flüssige Detergenszusammensetzung, die
einen Erstarrungspunkt von nicht mehr als 5°C aufweist, enthaltend ein Gemisch oberflächenaktiver
Mittel in einem Hydrotrop-Wasser-System, dadurch gekennzeichnet, daß das Gemisch oberflächenaktiver
Mittel durch die Kombination von
a) einem wasserlöslichen C,3-Cla-Alkan- oder C12―C16-Alkensulfonat,
b) einem wasserlöslichen Alkylpolyethoxysulfat, worin die Alkylgruppe 10 bis 16 Kohlenstoffatome
enthält, und die Polyethoxygruppe im Durchschnitt 0,5―6 Ethoxygruppen enthält,
c) 2,0-5,0 Gew.-% der Zusammensetzung eines ethoxylierten, primären C8―C12-Alkohols, der einen HLB-Wert im Bereich von 7,5-12,0 aufweist, und
d) 6-18 Gew.-% der Zusammensetzung eines primären C10―C16-Alkylsulfats gebildet ist,
wobei die Zusammensetzung das Magnesiumion in einer Menge entsprechend 0,40X-0,60X
enthält, worin X die molare Menge des genannten primären C
10―C
16-Alkylsulfats ist.
2. Eine flüssige Detergenszusammensetzung nach Anspruch 1, wobei der ethoxylierte
Alkohol einen HLB-Wert im Bereich von 8,0 bis 9,5 aufweist.
3. Eine flüssige Detergenszusammensetzung nach einem der Ansprüche 1 und 2, wobei
das Alkylsulfat im Durchschnitt 12 bis 15 Atome in der Alkylkette enthält und in einer
Menge von 8 Gew.-% bis 16 Gew.-% der Zusammensetzung vorliegt.
4. Eine flüssige Detergenszusammensetzung nach einem der Ansprüche 1 bis 3, welche
weiterhin einen Schaumverstärker enthält, der aus C12―C14-Mono- und Di-CZ-C3-Alkanolamiden, C12―C14-Aikyf- amiden, die mit bis zu 15 Mol Ethylenoxid je Mol Amid kondensiert sind, und
tertiären Aminoxiden, welche eine C8―C18-Alkylgruppe enthalten, ausgewählt ist.
5. Eine flüssige Detergenszusammensetzung nach einem der Ansprüche 3 und 4, enthaltend
8 Gew.-% bis 12 Gew.-% C14―C17-Alkansulfonat und 8 Gew.-% bis 12 Gew.-% C12―C13-Alkylpolyethoxysulfat mit im Durchschnitt zwei Ethoxygruppen je Mol, wobei das Gemisch
oberflächenaktiver Mittel auch 2,0 bis 3,0 Gew.-% eines C9―C11-primären Alkoholethoxylats enthält, welches im Durchschnitt 2 bis 3 Ethoxygruppen
je Mol Alkohol aufweist.
6. Eine flüssige Detergenszusammensetzung nach einem der Ansprüche 3 und 4, enthaltend
4 Gew.-% bis 8 Gew.-% C14―C17-Alkansulfonat und 4 Gew.-% bis 8 Gew.-% C13―C15-Alkylpolyethoxysulfat mit im Durchschnitt 2 Ethoxygruppen von Alkylethoxysulfat je
Mol, und 2 Gew.-% bis 4 Gew.-% eines C9-C"- primären Alkoholethoxylats, das im Durchschnitt 2 bis 3 Ethoxygruppen je Mol Alkohol
aufweist.
7. Eine flüssige Detergenszusammensetzung nach Anspruch 5 oder 6, wobei das Alkylsulfat
und das Alkylpolyethoxysulfat von einem einzigen Alkoholethoxylat abgeleitet sind,
das einen mittleren Ethoxylierungsgrad im Bereich von 0,5 bis 1,0 Mol je Mol Alkohol
aufweist.
1. Une composition détergente liquide, homogène, limpide contenant du magnésium ayant
un point de trouble non supérieur à 5°C comprenant un mélange tensioactif dans un
système hydrotrope-eau, caractérisée, en ce que le mélange tensioactif est formé par
la combinaison
a) d'un alcane C13―C18 ou alcène C12―C16 sulfonate soluble dans l'eau,
b) d'un alkyl polyéthoxysulfate soluble dans l'eau dans lequel le groupe alkyle contient
10 à 16 atomes de carbone et le groupe polyéthoxy contient en moyenne 0,5 à 6 groupes
éthoxy,
c) de 2,0 à 5,0% en poids, par rapport à la composition, d'un alcool primaire en Ca à C12 éthoxylé possédant une HLB comprise dans la gamme de 7,5 à 12,0,
d) de 6 à 18% en poids, par rapport à la composition, d'un alkyl C10―C16 sulfate primaire,
la composition renfermant l'ion magnésium en une quantité correspondant à 0,40X-0,60X
où X est la quantité molaire dudit alkyl C
10―C
16 sulfate primaire.
2. Composition détergente liquide selon la revendication 1, dans laquelle l'alcool
éthoxylé possède une HLB comprise dans la gamme de 8,0 à 9,5.
3. Composition détergente liquide selon l'une des revendications 1 et 2, dans laquelle
l'alkylsulfate contient une moyenne de 12 à 15 atomes dans la chaîne alkyle et est
présent à raison de 8% à 16% en poids de la composition.
4. Composition détergente liquide selon l'une quelconque des revendications 1 à 3,
contenant en outre un renforçateur de mousse choisi parmi des mono- alcanolamides
en C12 à C14 et des di- alcanolamides en C2 à C3, des alkyl C12―C14 amides condensés avec jusqu'à 15 moles d'oxyde d'éthylène par mole d'amide et des
oxydes d'amines tertiaires contenant un groupe alkyle en Ce à C18.
5. Composition détergente liquide selon l'une des revendications 3 et 4 renfermant
8% à 12% en poids d'un alcane C14―C17 sulfonate et 8% à 12% en poids d'un alkyl C12―C13 polyéthoxysulfate contenant en moyenne deux groupes éthoxy par mole, dans laquelle
le mélange tensioactif contient également 2,0 à 3,0% en poids d'un éthoxylat d'alcool
primaire en Cg à C11 renfermant en moyenne 2 à 3 groupes éthoxy par mole d'alcool.
6. Composition détergente liquide selon l'une des revendications 3 et 4 renfermant
4% à 8% en poids d'un alcane C14-C17 sulfonate, 4% à 8% en poids d'un alkyl C13―C15 polyéthoxysulfate contenant en moyenne deux groupes éthoxy d'alkyl éthoxysulfate
par mole et 2% à 4% en poids d'un éthoxylat d'alcool primaire en Cg à C11 renfermant en moyenne 2 à 3 groupes éthoxy par mole d'alcool.
7. Composition détergente liquide selon la revendication 5 ou 6, dans laquelle l'alkylsulfate
et l'alkyl polyéthoxysulfate dérivent d'un seul alcool éthoxylé avec un degré d'éthoxylation
moyen entre 0,5 et 1 mole par mole d'alcool.