[0001] La présente invention concerne un procédé de délignification de matières lignocellulosiques
en vue de la préparation de pâtes destinées à la fabrication du papier. Elle concerne
plus spécifiquement le domaine des pâtes chimiques obtenues par cuisson des matières
cellulosiques en présence de réactifs chimiques dotés de propriétés délignifiantes.
[0002] On a depuis longtemps cherché à accroître l'efficacité de la cuisson des matières
cellulosiques en soumettant ces dernières, préalablement à la cuisson, à une imprégnation
par une solution contenant un composé peroxydé.
[0003] Dans le brevet DE-B-873 649 (DEGUSSA), il est divulgué qu'un prétraitement de matières
cellulosiques au moyen d'une solution aqueuse d'un composé peroxydé, avant leur cuisson
par un procédé au sulfite ou au bisulfite améliore la blancheur de la pâte obtenue.
Ce prétraitement permet aussi, pour une blancheur de pâte équivalente, d'effectuer
la cuisson dans des conditions plus douces pour la cellulose, à savoir à température
réduite ou à durée plus faible (page 2, lignes 51 à 59).
[0004] Le brevet belge BE-A-678022 (DEGUSSA) concerne un procédé similaire dans lequel le
prétraitement des matières cellulosiques avec la solution aqueuse du composé peroxydé
se fait en milieu fortement alcalin. Dans ce brevet, on enseigne qu'en appliquant
cette technique, on facilite le processus de cuisson chimique ultérieur en préservant
le rendement pondéral en pâte (page 3, dernier paragraphe et page 4, lignes 1 à 13).
[0005] Dans PRZEGLAD PAPIERNICZY, Vol. 33, août 1977, W. MROZ et W. SUREWICZ "Modification
of the kraft pulping process aimed at improving the color of the pulp" (pages 277
à 280) on observe que, dans le cas d'une cuisson alcaline de type kraft, un prétraitement
des matières cellulosiques avec un composé peroxydé n'améliore que légèrement la blancheur
de la pâte, on y démontre que de meilleurs résultats sont obtenus avec un prétraitement
d'imprégnation au moyen d'agents réducteurs, en particulier l'hydrazine, plutôt qu'au
moyen d'agents oxydants.
[0006] Ces procédés connus présentent cependant tous le désavantage de produire des pâtes
plus dégradées, c'est-à-dire de viscosité plus faible et dont le rendement pondéral
est généralement inférieur, comparés aux viscosités et aux rendements des pâtes chimiques
classiques de taux de délignification équivalent.
[0007] L'invention remédie à ces inconvénients des procédés connus, en fournissant un procédé
nouveau de délignification de matières cellulosiques, qui permette d'atteindre des
taux de délignification élevés tout en préservant la qualité intrinsèque de la cellulose
et le rendement pondéral en pâte produite.
[0008] A cet effet, l'invention concerne un procédé pour la délignification de matières
cellulosiques selon lequel, dans une première étape, on traite des matières cellulosiques
avec un acide, dans une deuxième étape, on traite les matières cellulosiques de la
première étape avec du peroxyde d'hydrogène en milieu alcalin et, dans une troisième
étape, on soumet les matières cellulosiques de la deuxième étape à une cuisson en
présence d'au moins un réactif chimique sélectionné parmi les produits soufrés et
l'oxygène.
[0009] Selon l'invention, par le terme matières cellulosiques, on entend désigner des fragments
ligneux de végétaux utilisés comme matières premières dans l'industrie papetière.
Des exemples de telles matières sont des fragments de bois, de plantes annuelles herbacées
telles que l'alfa, de végétaux de la classe des monocotylédones tels que les pailles
de céréales, le bambou, l'esparto, les joncs et roseaux ainsi que la canne à sucre,
en particulier son résidu, la bagasse, après extraction du sucre. L'invention s'applique
tout particulièrement aux fragments de bois. Tous les types de bois de résineux ou
de feuillus utilisables en industrie papetière conviennent pour le procédé selon l'invention.
Les copeaux de bois de résineux et les déchets de scierie conviennent particulièrement
bien.
[0010] Dans le procédé selon l'invention, le traitement avec un acide a pour but de décontaminer
les matières cellulosiques des métaux qu'elles contiennent généralement. Tous les
acides inorganiques ou organiques utilisés en solution aqueuse, seuls ou en mélange
conviennent. Les acides forts inorganiques tels que l'acide sulfurique ou l'acide
chlorhydrique conviennent bien. Des mélanges de tels acides avec des acides organiques
de la classe des acides aminopolycarboxyliques ou aminopolyphosphoniques ou leurs
sels de métaux alcalins qui possèdent des propriétés séquestrantes vis-à-vis des ions
métalliques conviennent particulièrement bien. Des exemples d'acides aminopolycarboxyliques
adéquats sont l'acide diéthylènetriaminepentaacétique, l'acide éthylènediaminetétraacétique,
l'acide cyclohexanediaminetétraacétique et l'acide nitrilotriacétique. L'acide diéthylènetriaminepentaacétique
(DTPA) est préféré. Des exemples d'acides aminopolyphosphoniques sont l'acide diéthylènetriaminepentaméthylènephosphonique,
l'acide éthylènediaminetétra-(méthylènephosphonique) et l'acide nitrilotri(méthylènephospho-
nique). L'acide diéthylènetriaminepentaméthylènephosphonique (DTMPA) est préféré.
[0011] Les conditions opératoires de la première étape du procédé selon l'invention ne sont
pas critiques. Elles doivent être déterminées dans chaque cas particulier en fonction
du type des matières cellulosiques et de l'appareillage dans lequel s'effectue le
traitement. D'une manière générale, il convient de fixer le choix de l'acide et la
quantité mise en oeuvre pour imposer au milieu un pH inférieur à 7, par exemple compris
entre 0,5 et 6,5; des pH spécialement avantageux sont ceux compris entre 1,0 et 4,0.
[0012] La température et la pression ne sont pas critiques, la température ambiante et la
pression atmosphérique convenant généralement bien. La durée du traitement peut varier
dans de larges proportions selon le type d'équipement utilisé,le choix de l'acide,
la température et la pression, par exemple de 30 minutes à plusieurs heures si le
traitement est effectué par trempage des matières cellulosiques dans un cuvier, de
1 à 120 minutes s'il est effectué par percolation dans une colonne où les matières
cellulosiques à traiter sont empilées.
[0013] Dans une variante d'exécution du procédé selon l'invention, les matières cellulosiques
peuvent être soumises préalablement à la première étape, à un traitement par de la
vapeur d'eau. Ce traitement a pour but de faciliter les opérations d'imprégnation
qui vont suivre.
[0014] Le peroxyde d'hydrogène mis en oeuvre à la deuxième étape du procédé selon l'invention
a pour fonction d'accélérer la délignification des matières cellulosiques dans l'étape
de cuisson subséquente. La quantité optimum de peroxyde d'hydrogêne à mettre en oeuvre
dépend de l'origine des matières cellulosiques. En général, il est nécessaire de mettre
en oeuvre plus de 0,1 g de peroxyde d'hydrogène pour 100 g de matières cellulosiques
sèches. Des quantités de peroxyde d'hydrogène supérieures à 3 g/100 g de matières
cellulosiques sèches sont rarement nécessaires à l'obtention d'une délignification
rapide. Habituellement, on utilise des doses de peroxyde d'hydrogène comprises entre
0,5 et 2 g/100 g de matières sèches. Les doses de peroxyde comprises entre 0,7 et
1,5 g/100 g de matières sèches ont donné les meilleurs résultats.
[0015] Le peroxyde d'hydrogène mis en oeuvre peut être du peroxyde d'hydrogène anhydre ou,
de préférence, une solution aqueuse, par exemple une solution aqueuse commerciale
de peroxyde d'hydrogène dont la teneur en poids est comprise entre 25 et 90 g de peroxyde
d'hydrogène pur par 100 g de solution ou encore une solution aqueuse alcaline diluée
de peroxyde d'hydrogène produite par réduction électrochimique d'oxygène.
[0016] Dans le procédé selon l'invention, le traitement des matières cellulosiques avec
le peroxyde d'hydrogène alcalin peut être opéré en présence d'additifs tels que, par
exemple, des stabilisants et des inhibiteurs de la décomposition du peroxyde d'hydrogène.
De tels additifs sont par exemple des séquestrants d'ions métalliques inorganiques
ou organiques comme les sels de magnésium, les acides aminopolycarboxyliques ou le
silicate de sodium de la qualité verre soluble. D'autres additifs pouvant également
être mis en oeuvre sont des agents tensioactifs, des agents mouillants, des agents
capables de protéger les chaînes cellulosiques pour éviter leur dépolymérisation,
des agents activants ou des agents anti-corrosion. Généralement, la quantité d'additif
introduite n'est jamais supérieure à 1% du poids des matières cellulosiques. Elle
se situe le plus souvent entre 0 et 0,5% du poids de ces matières.
[0017] Dans la deuxième étape du procédé selon l'invention, le milieu alcalin est obtenu
par l'addition de matières solubles à caractère basique. L'ammoniac, les carbonates
et les hydroxydes inorganiques de métaux alcalins ou alcalino-terreux tels que le
carbonate de sodium, de potassium ou de calcium, l'hydroxyde de sodium, de potassium
ou de calcium sont généralement employés. Des oxydes ou des peroxydes de métaux alcalins
ou alcalino-terreux tels que Na
20, Na
20
2, Ca0 et Ca0
2, peuvent aussi convenir et dans le cas des peroxydes suppléer à l'apport d'une partie
du peroxyde d'hydrogène introduit dans la deuxième étape du procédé. L'hydroxyde de
sodium est habituellement préféré en raison de sa grande disponibilité et de son faible
coût. Les quantités de matière basique à mettre en oeuvre sont choisies de telle manière
à ajuster le pH de la solution de peroxyde entre 11 et 13,5 et de préférence entre
12 et 13.
[0018] Les conditions opératoires de la deuxième étape du procédé selon l'invention peuvent
aussi varier dans d'assez larges limites selon, notamment, le type de matières cellulosiques
et le type d'appareillage utilisés. La pression régnant durant la seconde étape peut
ainsi se situer dans la gamme allant de 2 kPa à 10 MPa et la température dans la gamme
de 290 K à 380 K. Le traitement au peroxyde d'hydrogène en milieu alcalin de la deuxième
étape est généralement effectué pendant un temps supérieur à 2 minutes et n'excédant
pas 180 minutes.
[0019] Dans un mode d'exécution particulier de l'invention on soumet les matières cellulosiques
à traiter à du peroxyde d'hydrogène alcalin dans un rapport pondéral liqueur sur bois
n'excédant pas 2,5:1, et, de préférence, allant de 1:1 à 2:1. Dans ce mode d'exécution
préféré, les matières cellulosiques provenant de la première étape sont imprégnées
dans un réacteur fermé avec la liqueur alcaline de peroxyde d'hydrogène préchauffée
après quoi l'excédent de liqueur n'ayant pas imprégné les matières cellulosiques est
drainé lors du réacteur qui est ensuite chauffé à la température de réaction.
[0020] Dans ce mode d'exécution préféré, le trempage des matières cellulosiques dans la
liqueur de peroxyde d'hydrogène, préalablement à la réaction, ne requiert généralement
pas plus de 5 minutes. Il ne peut cependant habituellement pas s'effectuer en moins
de 30 secondes. La température de la liqueur de peroxyde est le plus souvent choisie
de 5 à 20 K plus élevée que celle qui règne dans le réacteur et que l'on maintient
durant 15 à 120 minutes au moyen du manteau chauffant. Une température de réaction
comprise entre 310 et 360 K convient bien. Les meilleurs résultats ont été obtenus
avec une température de 323 K et pour une durée de réaction de 45 minutes.
[0021] La troisième étape du procédé selon l'invention consiste à soumettre les matières
cellulosiques provenant de la deuxième étape à une cuisson en présence d'au moins
un réactif chimique. Par réactifs chimiques, il faut entendre les produits soufrés
acides ou alcalins tels que ceux utilisés dans les cuissons bien connues dans l'industrie
de la pâte à papier sous les noms de cuisson au sulfite de sodium ou de magnésium,
au bisulfite de sodium, de magnésium ou de calcium, au sulfite acide de sodium, de
magnésium ou de calcium ainsi qu'au sulfate de sodium, ou cuisson kraft. Les cuissons
à l'oxygène sont également comprises dans la catégorie des cuissons au moyen de réactifs
chimiques.
[0022] Les conditions opératoires optima pour la troisième étape du procédé selon l'invention
dépendent de divers paramètres, notamment de l'origine des matières cellulosiques
et elles peuvent être déterminées aisément dans chaque cas particulier.
[0023] Dans une forme de réalisation préférée du procédé selon l'invention, on pratique
entre la deuxième et la troisième étape, un lavage à l'eau des matières cellulosiques.
Cette forme de réalisation est avantageuse lorsque la troisième étape est effectuée
à l'intervention de réactifs soufrés. Ce lavage a pour but d'éliminer des matières
cellulosiques, au moins une partie des produits hydrosolubles générés à la deuxième
étape et d'extraire les dernières traces de peroxyde d'hydrogène encore présentes,
pour éviter une oxydation inutile des réactifs soufrés mis en oeuvre à la troisième
étape de cuisson.
[0024] Le procédé selon l'invention permet d'accélérer notablement la délignification des
matières cellulosiques traitées, ce qui a pour effet de raccourcir la durée nécessaire
de la troisième étape de cuisson par les réactifs chimiques. Il en résulte l'avantage
important d'une diminution sensible de la taille des équipements de cuisson, ce qui
entraîne des économies d'espace et de coût d'investissement ou, de manière alternative,
une capacité accrue pour un équipement de cuisson donné.
[0025] L'invention permet aussi, à taux de délignification égale, une réduction sensible
de la quantité de réactifs chimiques à l'étape de cuisson. Il en découle une économie
substantielle en réactifs chimiques et une moindre pollution de l'environnement, notamment
par les rejets soufrés gazeux et liquides dans le cas où on met en oeuvre des réactifs
chimiques soufrés.
[0026] Enfin, l'invention produit aussi avec de meilleurs rendements pondéraux et partant
à moindre coût, des pâtes chimiques de solidité mécanique plus élevée que celles obtenues
par les procédés de l'art antérieur.
[0027] Les exemples de réalisation pratique qui suivent ont pour but d'illustrer l'invention
sans pour autant en limiter la portée.
Première série d'essais (essais 1 à 6R)
[0028] Les essais 1 à 6R dont la description va suivre, ont pour objectif de montrer l'avantage
apporté par l'invention sur les performances de la technique de cuisson chimique des
matières cellulosiques.
Essai 1 : (conforme à l'invention)
[0029] De la farine de bois de pinus taeda (fraction granulométrique passant au tamis de
40 mesh et refusée au tamis de 60 mesh de la norme TYLER) a été soumise à un traitement
par de l'acide chlorhydrique réalisé par trempage de la farine dans une solution 0,1
M HC1 pendant 4 heures à température ambiante. La solution aqueuse a été mise en oeuvre
en quantité pondérale égale à 40 fois le poids de la farine de bois traitée (Première
étape).
[0030] De la farine de bois provenant de la première étape en quantité équivalente à 10
g de matières sèches, a été introduite dans un réacteur de 200 ml garni intérieurement
d'un revêtement de polytétrafluoréthylène. Après préchauffage à 323 K du réacteur
dans un bain de polyéthylèneglycol, on a introduit dans le réacteur 150 g d'une solution
aqueuse de 0,04 M de peroxyde d'hydrogène et 0,5 M en hydroxyde de sodium. Le réacteur
a ensuite été chauffé à 353 K en 30 minutes, puis maintenu 15 minutes à cette dernière
température. Le réacteur a ensuite été refroidi et la farine de bois a été lavée (Deuxième
étape).
[0031] La farine de bois provenant de la deuxième étape a ensuite été soumise à une cuisson
kraft en présence d'une liqueur aqueuse de Na
2S et de NaOH dans un autoclave de laboratoire en acier inoxydable de 450 ml de capacité,
équipé d'un agitateur (troisième étape). Les conditions opératoires de cette cuisson
ont été les suivantes : Alcali actif de la liqueur : 20 g Na
20/litre de liqueur Sulfidité de la liqueur : 25X
Rapport pondéral liqueur/farine de bois sec : 40:1
Température et durée : 90 minutes de chauffage de l'ambiance jusqu'à 443 K et maintien
à 443 K pendant 52,5 minutes
Essai 2R (de référence)
[0032] Les conditions de cet essai de référence ont été identiques à celles de l'essai 1
excepté que l'on n'a pas effectué la première étape de traitement.
Essai 3R (de référence)
[0033] Identique à l'essai 1 excepté la seconde étape de traitement qui n'a pas été réalisée.
Essais 4R à 6R (de référence)
[0034] Il s'agit ici de cuissons kraft traditionnelles. Mises à part les étapes 1 et 2 qui
n'ont pas été réalisées, les conditions opératoires ont été les mêmes qu'à l'essai
1. Aux essais 5R et 6R cependant, la durée de la cuisson à 443 K a été portée à 60
et à 75 minutes respectivement.
[0035] A l'issue de l'étape de cuisson, les pâtes obtenues ont été analysées sous les trois
aspects : indice kappa, rendement pondéral total et viscosité. Les méthodes employées
pour ces analyses ont été les méthodes normalisées suivantes :
indice kappa : norme TAPPI T236
viscosité : norme TAPPI T230
[0036] Les résultats obtenus ont été portés au Tableau I.
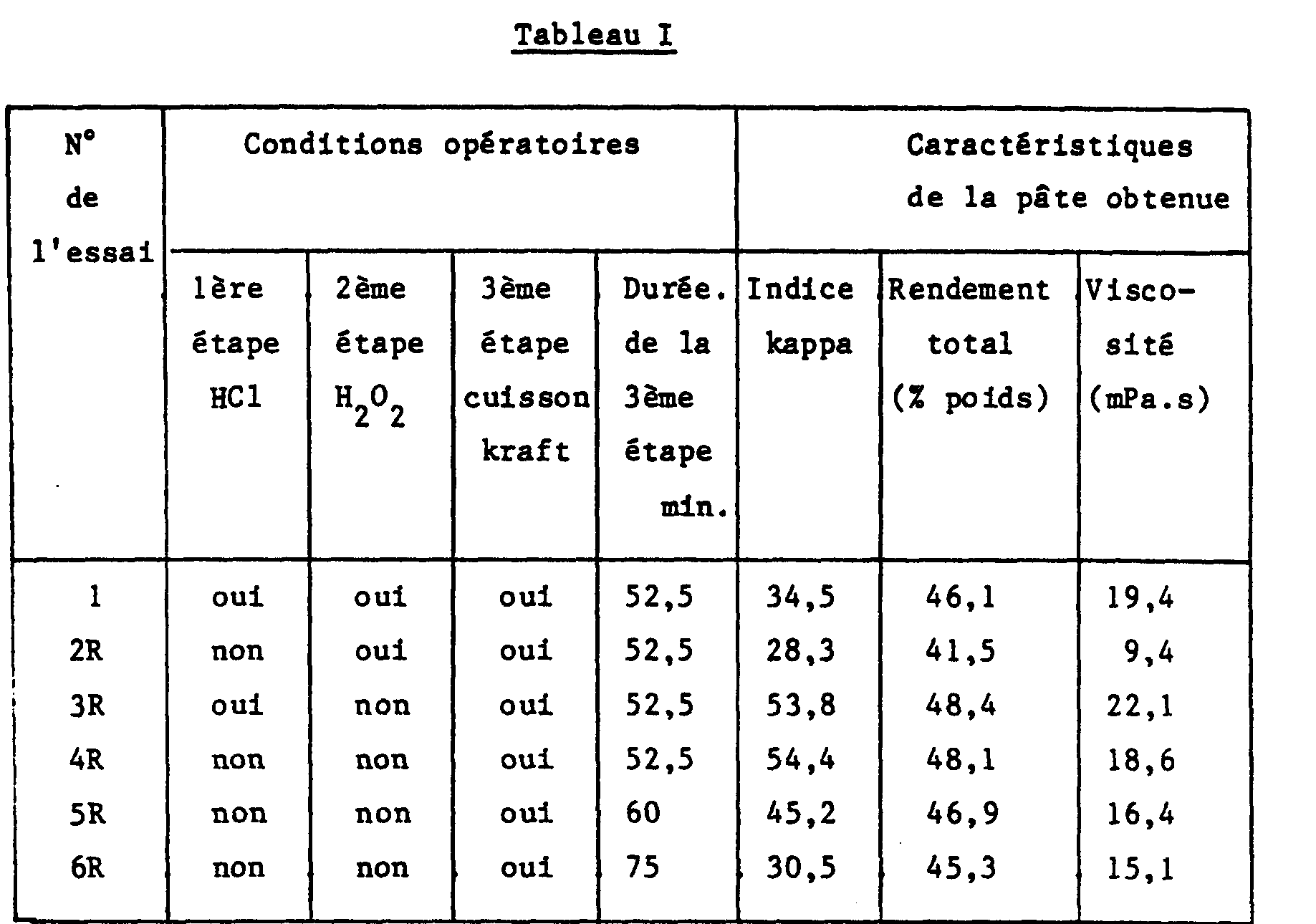
[0037] Une comparaison des résultats de l'essai 1 avec ceux des essais 2R, 3R et 4R montre
l'effet synergique inattendu de la mise en oeuvre combinée des première et deuxième
étapes de l'invention sur le taux de délignification à l'issue de l'étape de cuisson
subséquente. On remarque par ailleurs que l'application séquentielle des deux premières
étapes du procédé selon l'invention a aussi permis, de façon tout à fait surprenante
d'annihiler la chute de viscosité de la pâte due à l'action de l'oxydant : la comparaison
de l'essai 1 avec l'essai 4R montre même une amélioration de la viscosité de la pâte
obtenue selon le procédé de l'invention.
[0038] Les essais 5R et 6R ont été effectués à titre de référence afin d'évaluer le rendement
pondéral et la viscosité des pâtes délignifiées au moyen de la seule étape de cuisson
(conformément au procédé de l'art antérieur), pour un taux de délignification (mesuré
par l'indice kappa) équivalent à celui obtenu à l'essai 1. On voit directement l'avantage
apporté par l'invention pour ce qui concerne la durée de la cuisson chimique. Il apparaît
également que le procédé selon l'invention procure des pâtes de meilleure viscosité
et de rendement pondéral supérieur.
Deuxième série d'essais (essais 7 à 11R)
[0039] Les essais 7 à 11R, dont la description va suivre, ont également pour objectif de
montrer l'incidence de l'invention sur les performances de la technique de cuisson
chimique des matières cellulosiques.
Essai 7 : (conforme à l'invention)
[0040] Des copeaux de bois de pinus taeda ont été introduits à raison de 300 g de matières
sèches dans un réacteur doublé de verre et équipé d'un couvercle étanche. Le couvercle
était muni de deux orifices : le premier était connecté à une pompe à vide et le second
permettait l'introduction jusqu'au fond du réacteur d'une sonde tubulaire. Cette sonde
a été connectée au réservoir de réactifs qui communiquait lui-même avec l'atmosphère
ou avec une pompe à vide via une vanne à 3 voies. Dans le réacteur, les copeaux ont
été imprégnés, à température ambiante, avec une solution aqueuse 0,003 M de sel pentasodique
de l'acide diéthylènetriaminepentaacétique (Na
5DTPA) et 0,1 N en H
2SO
4 par aspiration de la solution dans le réacteur au moyen de la pression réduite réalisée
par la distribution de vide; la solution aqueuse a été mise en oeuvre en quantité
pondérale égale à 8 fois le poids de bois à l'état sec. Après 4 heures d'imprégnation,
les copeaux ont ensuite subi 3 cycles de lavage de 2 heures chacun avec une quantité
d'eau égale à 8 fois le poids de bois sec (Première étape).
[0041] Une solution aqueuse alcaline de peroxyde d'hydrogène contenant des ions Mg
++ (0,3 M H
20
21 0,5 M NaOH et 0,001 M Mg
++) a ensuite été introduite dans le réacteur. La solution a été mise en oeuvre en quantité
pondérale égale à 6 fois le poids de bois sec. Après deux minutes d'imprégnation la
liqueur en excès a été drainée hors du réacteur au moyen de la sonde tubulaire. On
a ensuite permis à la réaction de s'effectuer en phase vapeur pendant 45 minutes en
chauffant le réacteur par circulation d'eau thermostatisée à 323K dans la double enveloppe
(Deuxième étape).
[0042] On a ensuite soumis les copeaux provenant de la deuxième étape, à une cuisson kraft
conventionnelle en phase liquide dans un réacteur en acier inoxydable, l'apport de
calories étant opéré en plaçant le réacteur dans un milieu d'air chaud produit par
une étuve. Les conditions opératoires de la cuisson kraft ont été : Alcali actif total
de la liqueur : 20 X exprimé en Na 0 Sulfidité de la liqueur : 25%
Rapport pondéral liqueur/bois sec : 5:1
Température et durée : 90 minutes de chauffage jusqu'à 443 K suivies de 45 minutes
à 443 K.
Essai 8R : (de référence)
[0043] Conditions identiques à l'essai 7, excepté la première étape de traitement qui n'a
pas été réalisée.
Essai 9R : (de référence)
[0044] Identique à l'essai 7 excepté que l'on n'a pas effectué la deuxième étape de traitement
au peroxyde d'hydrogène.
Essais 10R et 11R : (de référence)
[0045] On n'a réalisé dans ces essais que la troisième étape de cuisson kraft traditionnelle
dans les mêmes conditions que la troisième étape de l'essai 7. Dans le cas de l'essai
11R, on a cependant accru la dose d'alcali actif jusqu'à 26X de Na
20.
[0046] La pâte obtenue à l'issue de l'étape de cuisson a été analysée sous les mêmes aspects
et suivant les mêmes méthodes qu'aux essais 1 à 6R excepté toutefois en ce qui concerne
la viscosité.
[0047] Les résultats ont été consignés au Tableau II.
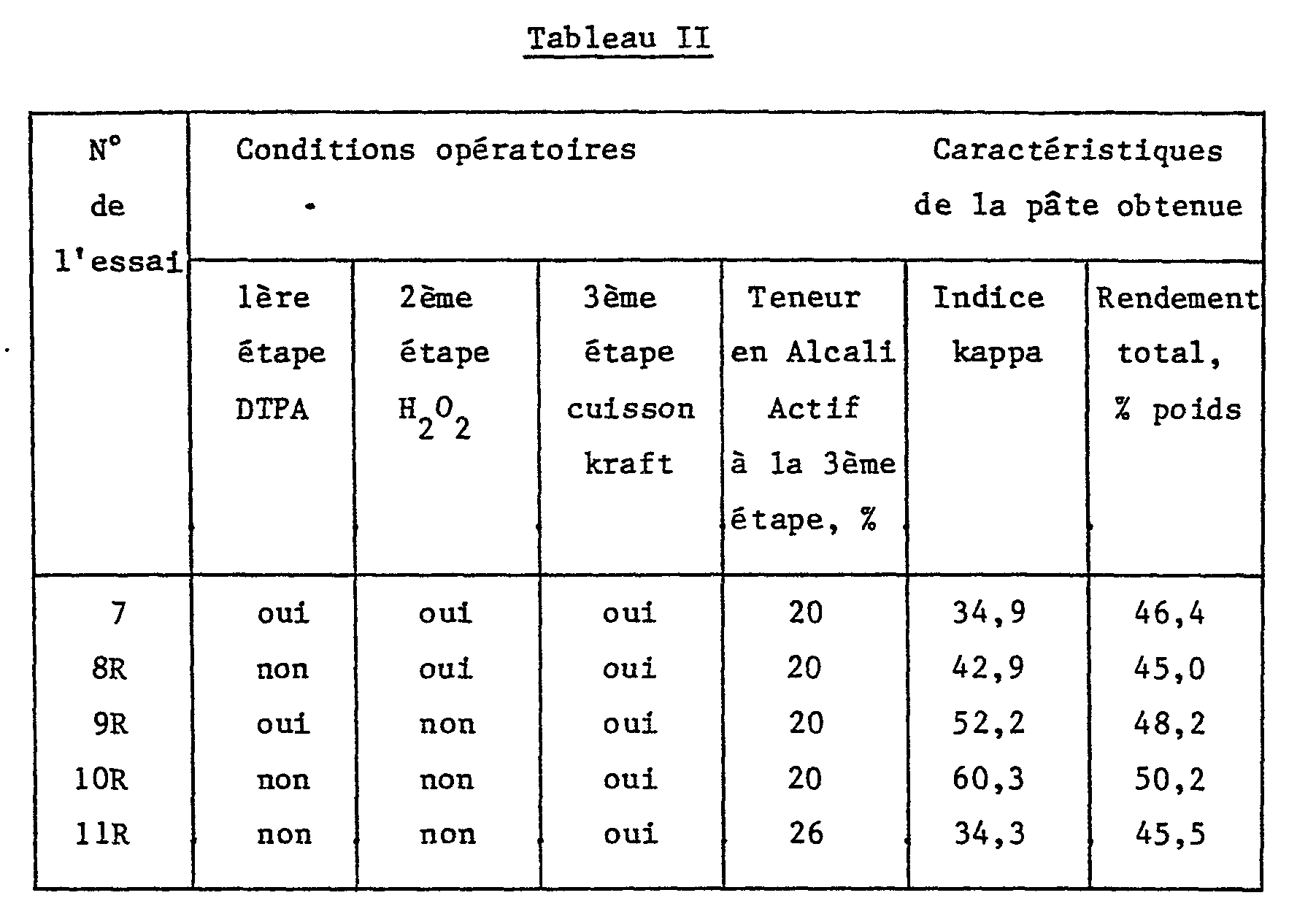
[0048] La comparaison des résultats de l'essai 7 effectué selon le procédé de l'invention
avec l'essai 11R montre qu'à taux de délignification équivalent, le procédé suivant
l'invention procure, après cuisson, une pâte kraft de rendement pondéral supérieur.
[0049] Les essais 7, 8R, 9R et 10R montrent également, comme à la première série d'essais,
que, dans le procédé selon l'invention, la combinaison des deux premières étapes réalise
un effet synergique inattendu.
Troisième série d'essais (essais 12 et 13)
[0050] Les essais 12 et 13, tous deux conformes à l'invention, ont pour objectif de montrer
l'avantage procuré par la forme de réalisation particulière de l'invention qui consiste
à intercaler, entre la deuxième et la troisième étape du procédé, un lavage à l'eau
des matières cellulosiques.
[0051] Les première et deuxième étapes du procédé ont été identiques à celles réalisées
dans la seconde série d'essais décrits ci-dessus.
[0052] Dans l'essai 12, on passe ensuite directement à la troisième étape du procédé tandis
que dans l'essai 13, on procède d'abord à 3 cycles de lavage à l'eau chaude, chacun
d'une durée de 2 heures, la quantité pondérale d'eau utilisés étant égale à 8 fois
le poids du bois sec.
[0053] Dans la troisième étape, on procède à l'imprégnation par la liqueur de cuisson kraft
de façon à réaliser les conditions opératoires suivantes :
Alcali actif : 20X exprimé en Na2O
Sulfidité : 25X
Rapport pondéral liqueur/bois sec : 5:1
Température et durée : 80 minutes de chauffage jusqu'à 443 K suivies de 30 minutes
de maintien à 443 K.
[0054] Après cuisson, la pâte obtenue a été analysée comme a la première série d'exemples.
Les résultats sont donnés au Tableau III.
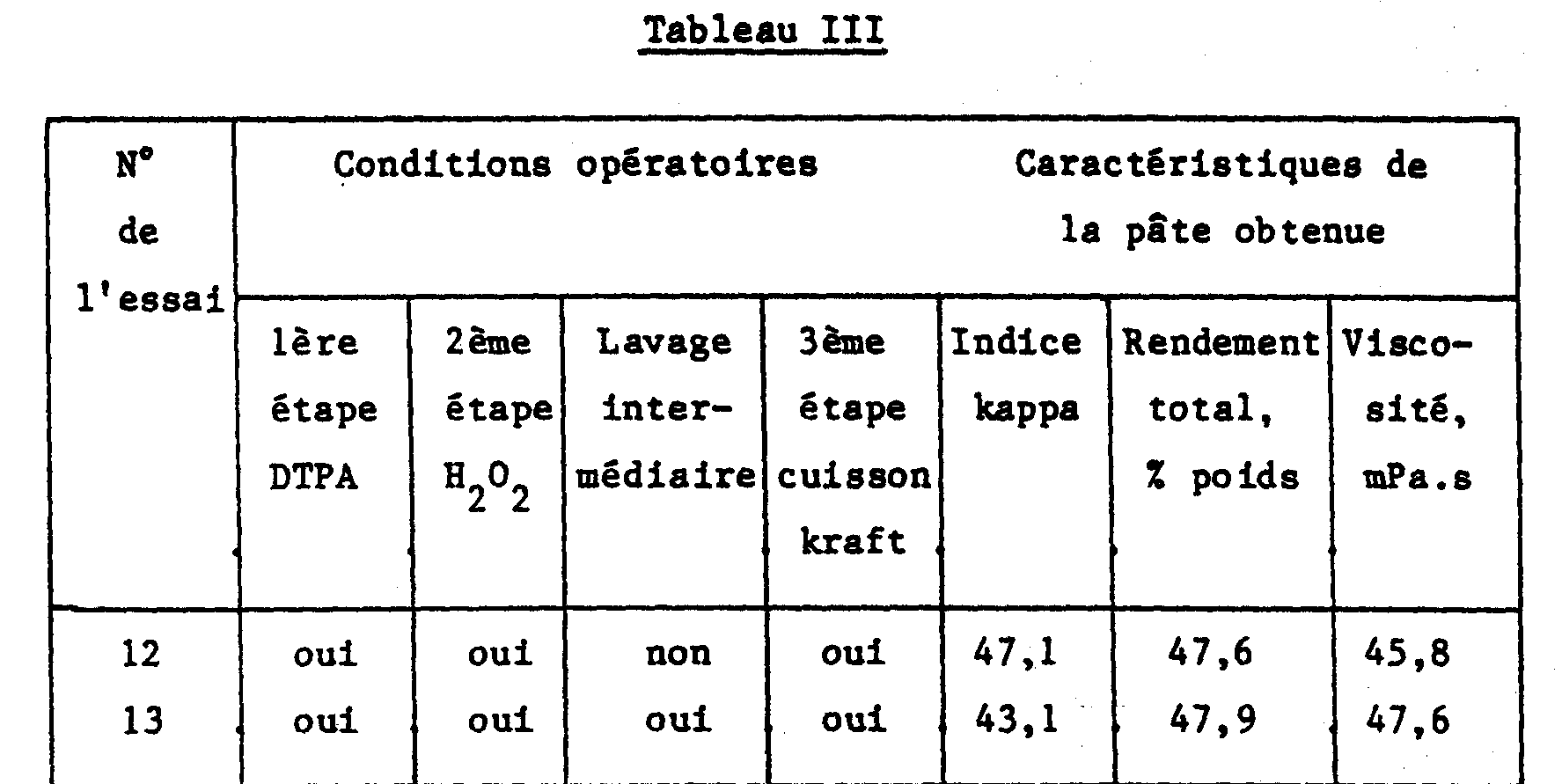
[0055] Ces résultats mettent en lumière l'avantage de l'opération de lavage intermédiaire
entre la deuxième et la troisième étape du procédé selon l'invention.
[0056] Ils illustrent son influence bénéfique sur l'accroissement du taux de délignification
tout en préservant plus efficacement le rendement pondéral et la viscosité de la pâte
produite.
Quatrième série d'essais (essais 14 à 16)
[0057] L'objet des essais 14 à 16 conformes à l'invention a été d'illustrer l'effet du pH
lors du traitement par le peroxyde

d'hydrogène à la deuxième étape du procédé selon l'invention. Ces essais ont été effectués
sur de la farine de bois de pinus taeda dans les mêmes conditions opératoires qu'à
la troisième série d'essais excepté les quantités de NaOH à la deuxième étape qui
ont été ajustées pour faire varier le pH de cette étape dans la plage allant de 10,1
à 12,9 en début de réaction.
[0058] Les résultats sont consignés au Tableau V.
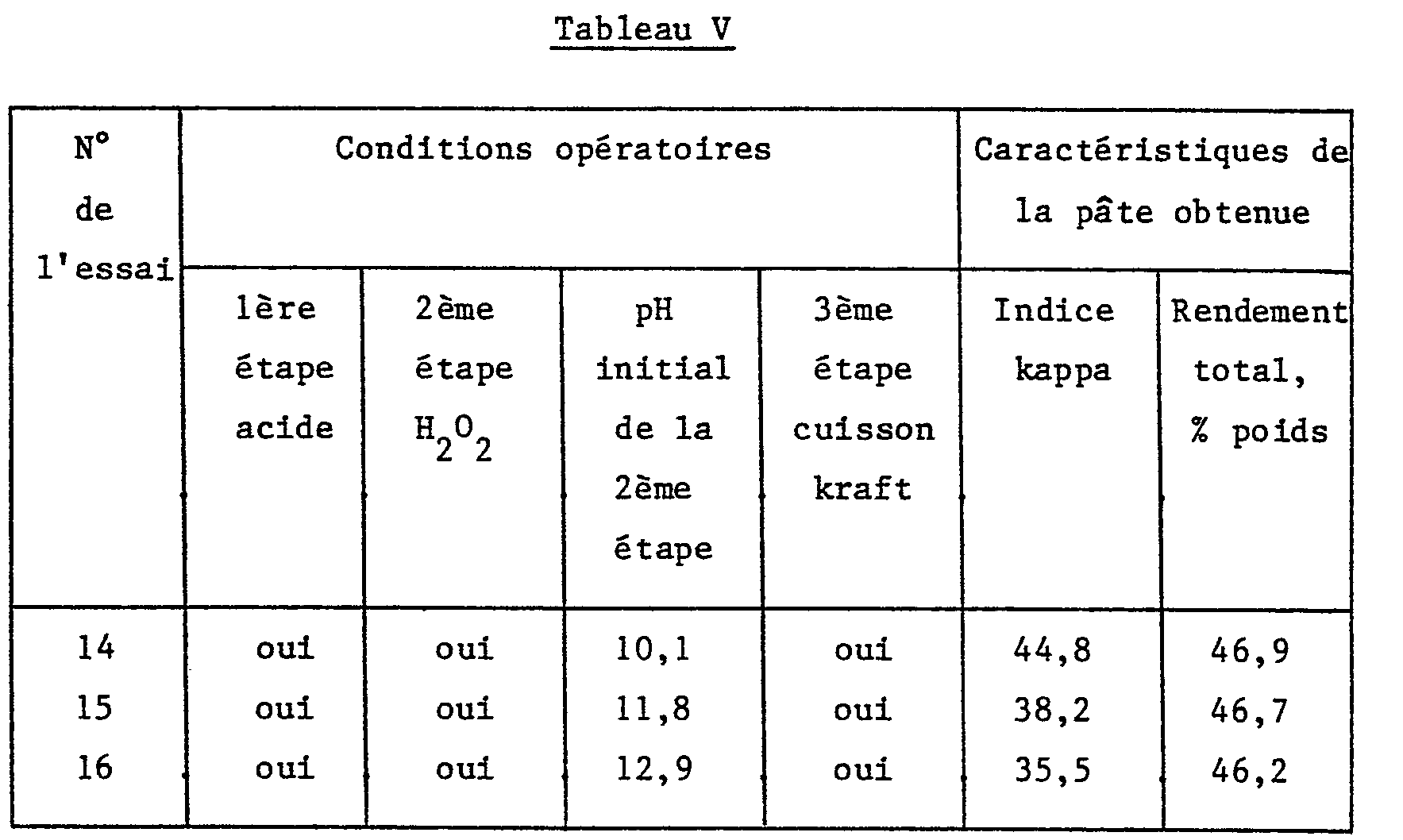
[0059] L'indice kappa le plus avantageux a été celui de l'essai 16 où le pH se situe entre
12 et 13 à la deuxième étape. L'accroissement du pH n'a pas d'effet marqué sur la
chute du rendement.
1 - Procédé pour la délignification de matières cellulosiques, caractérisé en ce que,
dans une première étape, on traite les matières cellulosiques avec un acide, dans
une deuxième étape, on traite les matières cellulosiques de la première étape avec
du peroxyde d'hydrogène en milieu alcalin et, dans une troisième étape, on soumet
les matières cellulosiques de la deuxième étape à une cuisson en présence d'au moins
un réactif chimique sélectionné parmi les produits soufrés et l'oxygène.
2 - Procédé selon la revendication 1, caractérisé en ce qu'on effectue la première
étape à un pH compris entre 1 et 4.
3 - Procédé selon l'une des revendications 1 ou 2, caractérisé en ce que la première
étape se fait en présence d'un acide inorganique.
4 - Procédé selon l'une quelconque des revendications 1 à 3, caractérisé en ce que
la première étape est effectuée en présence d'un complexant des ions métalliques.
5 - Procédé selon l'une quelconque des revendications 1 à 4, caractérisé en ce que
la troisième étape est une cuisson kraft.
6 - Procédé selon l'une quelconque des revendications 1 à 5, caractérisé en ce que
la deuxième étape se fait à un pH initial compris entre 12 et 13.
7 - Procédé selon l'une quelconque des revendications 1 à 6, caractérisé en ce que
la deuxième étape se fait à une température comprise entre 313 et 353K pendant 10
à 60 minutes.
8 - Procédé selon l'une quelconque des revendications 1 à 7, caractérisé en ce que
la deuxième étape est effectuée avec une quantité de peroxyde d'hydrogène comprise
entre 0,5 et 2 g/100 g de matières cellulosiques sèches et avec un rapport pondéral
liqueur sur bois compris entre 1:1 et 2:1.
9 - Procédé selon l'une quelconque des revendications 1 à 8 caractérisé en ce que
le peroxyde d'hydrogène de la deuxième étape est mis en oeuvre en solution aqueuse.
10 - Procédé selon l'une quelconque des revendications 1 à 9, caractérisé en ce que
les matières cellulosiques sont des copeaux de bois sélectionnés parmi la classe des
copeaux de bois résineux.