[0001] La présente invention concerne un four moufle pour traitements thermiques, en continu,
par défilement de produits dont le cycle de fabrication comporte un passage d'une
durée déterminée à température élevée. C'est le cas de certains réfractaires, de produits
carbonés, par exemple d'électrodes imprégnées, après une première cuisson, avec une
substance carbonée pyrolysable et cokéfiable, et aussi de métaux en vue de leur transformation,
et d'alliages métalliques, par exemple en vue de l'homogénéisation et de la mise en
solution solide des éléments d'alliage.
[0002] Dans tout ce qui suit, nous désignerons par "traitement thermique" toute opération
dans laquelle un des produits définis ci-dessus est porté à température élevée en
vue de lui conférer des propriétés particulières.
[0003] Ces traitements thermiques sont souvent effectués dans des fours statiques, soit
à chauffage électrique, soit à chauffage par flamme. C'est le cas, par exemple, des
fours de réchauffage de billettes métalliques (aciers ou alliages d'aluminium entre
autres) à contact direct avec les gaz de combustion ou des fours à chambre pour la
cuisson des électrodes de carbone, à des températures de l'ordre de 800 à 1200° C.
[0004] Il s'agit là, d'opérations discontinues avec tous les inconvénients inhérents à ces
procédés: difficulté de contrôler la température, ce qui conduit à des produits souvent
hétérogènes, immobilisation prolongée des fours, due à la lenteur des opérations d'enfournement
et de défournement, encombrement important des installations. En outre, dans certains
cas, le contact direct des produits à traiter avec les gaz de combustion présente
des inconvénients.
[0005] La présente invention permet de surmonter ces inconvénients. Elle a pour objet un
four moufle chauffé à la flamme pour le traitement thermique en continu, par défilement,
à une température qui peut atteindre 1100 à 1150° C environ, de produits tels que
réfractaires, métaux et alliages, produits carbonés, sans contact direct entre la
flamme ou les gaz de combustion et le produit à traiter.
[0006] Ce four comporte une zone d'entrée munie d'un moyen de préchauffage par circulation,
dans une double enveloppe disposée autour du moufle, de gaz de combustion recycles,
une zone de chauffage disposée à l'interieur d'une enceinte calorifugée, munie d'au
moins un moyen de mise en circulation des gaz de combustion autour de la zone de chauffe
du moufle et une zone de sortie munie d'au moins un moyen de contrôle de la vitesse
de refroidissement des produits.
[0007] Ce four est particulièrement adapté au traitement thermique de produits réfractaires
ou carbonés imprégnés d'une substance carbonée, telle que le brai, dont la pyrolyse
donne des vapeurs combustibles. Dans ce but et selon l'invention, la zone de chauffe
est divisée, au moyen d'une cloison supplémentaire en trois parties:
- une zone d'exsudation et de sortie des matières volatiles de la substance carbonée
d'imprégnation, dans laquelle le moufle comporte une ouverture débouchant sur un couloir
délimité par la cloison et la paroi externe, et dont la sortie est située à proximité
de la flamme du brûleur,
- une zone de pyrolyse et de cokéfaction de la substance carbonée d'imprégnation,
- une zone de cuisson finale dans laquelle est atteinte la température maximale nécessitée
par le traitement thermique, qui peut atteindre 1100 1150°C.
[0008] La figure 1 représente une réalisation d'un four moufle selon l'invention pour la
cuisson de produits carbonés imprégnés de brai, comportant un dispositif de récupération
des vapeurs de brai dont la combustion permet d'économiser jusqu'à 90 % du combustible
fourni au brûleur.
[0009] Le four comporte une zone d'entrée, constituée par un tunnel (1) muni d'un capot
amovible (2) dans lequel le produit à traiter thermiquement (3) est introduit par
des moyens de manutention habituels non représentés, par exemple, par une table à
rouleaux. Le four proprement dit est constitué par une enceinte réfractaire isolante
(4) sensiblement parallélépipédique qui forme la chambre de combustion (5).
[0010] L'entrée du four comporte une section de préchauffage (6) constituée par une double
enveloppe (7) dans laquelle circulent des gaz chauds récupérés dans la zone de combustion,
et mis en circulation par le ventilateur de recyclage (8).
[0011] Dans tout ce qui suit, nous désignerons par l'expression "gaz de combustion" aussi
bien les gaz de combustion en provenance directe du brûleur, que les gaz mis en circulation
dans les différents circuits du four, que ces gaz soient purs ou dilués par de l'âir
extérieur pour en abaisser la température.
[0012] Le moufle proprement dit est un tube cylindrique (10) disposé horizontalement dans
la partie supérieure du four. Il est en acier réfractaire, de préférence à haute teneur
en nickel, de façon à supporter des températures de service pouvant atteindre 1100
à 1150° C environ, sans que cette valeur constitue une limitation de l'invention.
[0013] La section intérieure du four est légèrement supérieure (de 5 à 20 % par exemple)
au diamètre extérieur maximal des produits à traiter ou, le cas échéant, du conteneur
rempli de produits à traiter. A l'intérieur du moufle (10), deux rails longitudinaux
assurent le guidage des produits pendant le défilement, qui se fait de droite à gauche
dans le cas représenté.
[0014] Le défilement des produits à traiter est généralement assuré par poussage, le mouvement
d'avance pouvant être continu ou pas à pas selon les exigences du traitement effectué.
[0015] Le chauffage du four est assuré par un brûleur (11) à combustible gazeux, liquide
ou solide pulvérisé, muni d'une arrivée d'air réglable avec un large excès éventuel,
pour une raison qui sera précisée plus loin, et que l'on peut également alimenter
en air préchauffé par un échangeur disposé dans le circuit des gaz de combustion ou
de refroidissement de la zone de sortie.
[0016] La mise en circulation des gaz de combustion est assurée par le ventilateur (12)
et la cloison (13). Les flèches indiquent, de façon approximative, le trajet des gaz
de combustion.
[0017] La cloison (13) détermine, avac la paroi externe (14), un couloir (15) qui débouche
sur le moufle, dans la zone de transition entre la zone de chauffe et la zone de sortie.
Les gaz de combustion circulent, autour du moufle, selon un trajet approximativement
schématisé par les flèches, ce qui assure une homogénéité de température remarquable
dans toute cette partie du moufle.
[0018] Dans le circuit d'évacuation des fumées par la cheminée (17), on prévoit, selon les
procédés habituels, un ou plusieurs dispositifs de recyclage des gaz de combustion,
et d'introduction éventuelle d'air extérieur, grâce aux volets (18), (19), (29), en
vue d'alimenter la double enveloppe (7) de la zone de préchauffe (6) en gaz chaud,
et, le cas échéant, le brûleur (11) en air préchauffé. La structure du circuit de
recyclage est donnée à titre indicatif, et ne constitue pas une caractéristique limitative
de l'invention.
[0019] Le four, objet de l'invention, est particulièrement adapté au cas particulier où
les produits à traiter thermiquement sont des produits réfractaires carbonés imprégnés
d'uns substance carbonée, telle que le brai, dont la pyrolyse donne des vapeurs combustibles.
On sait, en effet, que certains produits destinés à opérer dans des conditions mécaniques
sévères doivent subir une phase d'imprégnation par exemple avec du brai qui leur confère,
après cuisson, uhe plus graude résistance mécanique, une meilleure étanchéité, et,
dans le cas des produits carbonés une conductivité électrique plus forte. C'est le
cas notamment des électrodes de carbone ou de graphitedestinées à l'électrométallurgie:
après une première cuisson, les produits sont refroidis, imprégnés de brai sous pression
et à une température d'environ 200° C, puis soumis à une recuisson pour cokéfier le
brai retenu lors de l'imprégnation. C'est également le cas de certaines briques de
magnésie que l'on imprègne au brai puis que l'on soumet à une nouvelle cuisson.
[0020] Selon l'invention, la zone de chauffe est divisée, au moyen d'une cloison supplémentaire
(21) en trois parties:
- une zone d'exsudation et de sortie des matières volatiles de la substance carbonée
d'imprégnation (du brai) dans laquelle le moufle comporte une ouverture (22) débouchant
sur un couloir (23) délimité par la cloison (21) et la paroi externe (24) et dont
la sortie est située à proximité de la flamme du brûleur (11),
- une zone (25) de pyrolyse et de cokéfaction de la substance carbonée d'imprégnation
- une zone de cuisson finale (26) dans laquelle est atteinte la temperature maximale
nécessitée par le traitement thermique qui peut atteindre 1100° à 1150° C.
[0021] La possibilité de contrôler la température dans la zone de pyrolyse est une caractéristique
particulièrement avantageuse de l'invention. On sait, en effet, que, pour obtenir
le rendement maximal de cokéfaction du produit d'imprégnation, on doit déterminer
avec précision la vitesse de montée en température du produit imprégné et la durée
de maintien à une température prédéterminée, ce qui est aisément réalisable dans le
four à moufle, objet de l'invention.
[0022] Les matières volatiles qui se dégagent lors du début de pyrolyse de la substance
carbonée d'imprégnation ainsi que le brai qui exsude des électrodes (3), s'échappent
par l'ouverture (22) et le couloir (23) et atteignent la flamme du bruleur (11) où
ils sont brûlés grâce à l'apport d'un excès d'air (prechauffé ou non) dans le brûleur.
Comme on le verra dans l'exemple de mise en oeuvre, on peut ainsi économiser jusqu'à
90 % du combustible fourni au brûleur lorsque le four est en régime thermique. Le
recyclage des gaz de combustion et la récupération des calories qu'ils contiennent
sont assurés.
[0023] La zone de préchauffage (7) est alimentée par les gaz de combustion éventuellement
dilués avec de l'air extérieur. La zone (25) de pyrolyse et de cokéfaction comporte
une double enveloppe (27) dans laquelle circulent les gaz de combustion provenant
de la zone de cuisson finale, éventuellement dilués par de l'air extérieur et/ou des
gaz de combustion provenant de la zone de préchauffage.
[0024] L'évacuation des gaz de combustion s'effectue par la cheminée (17). Les volets tels
que (18) (19) permettent les réglages de débit nécessaires.
[0025] La zone de sortie comporte des moyens de refroidissement contrôlé, soit ralenti soit
accéléré, selon les exigences du produit traité et du cycle de traitement thermique
mis en oeuvre.
[0026] La partie du moufle (30) émergeant dans la zone de sortie peut être soit calorifugée,
soit exposée à l'air libre sur tout ou partie de sa longueur, ou soumise à un refroidissement
par ventilation forcée - et récupération éventuelle de l'air chaid pour alimenter
le brûleur - ou par aspiration ou pulvérisation d'un fluide tel que l'eau.
[0027] Au-delà, et jusqu'à la sortie du moufle, on peut prévoir différentes dispositions
de contrôle de refroidissement, telle qu'une double enveloppe (31) avec une circulation
d'un fluide liquide ou gazeux, ou, au contraire, un calorifugeage statique, par exemple
si l'on traite une billette de métal destinée à alimenter une presse à filer à chaud
ou encore une combinaison d'un calorifugeage à la sortie de la zone chaude, suivi
d'une zone de refroidissement accéléré.
[0028] La sortie peut également comporter, symétriquement avec l'entrée, un tunnel de sortie
(32) avec un capot amovible (33) pour extraire le produit traite.
[0029] Il est possible de créer, dans le moufle, une atmosphère contrôlée, par circulation
d'un gaz inerte, tel qu'argon ou azote, en prévoyant, le cas échéant, des moyens d'étanchéité,
même sommaires, à l'entrée et la sortie.
EXEMPLE DE MISE EN OEUVRE DE L'INVENTION
[0030] On a construit un four, conforme au dessin de la figure 1, destiné à la recuisson
d'électrodes, de barres à nipples et de tubes pour l'industrie chimique, imprégnés
au brai, ayant toutes 300 mm de diamètre externe. Le moufle a un diamètre interne
de 350mm. La vitesse de défilement des produits est réglable entre 0,2 et 2 mètres
par heure. Elle est ajustée en fonction de la température des différentes zones de
façon à obtenir une température à coeur du produit à traiter comprise entre:
200° et 300° C à la sortie de la zone de préchauffage
350° et 450° C à la sortie de la zone de pyrolyse
800° et 950° C à la sortie de la zone de cuisson finale
[0031] Lorsque le four est en régime, il fonctionne avec un apport de combustible extérieur
correspondant environ à 200 thermies (836 MJ) par tonne de produit à cuire alors que,
dans les fours statiques actuels, cette consommation est de l'ordre de 1800 thermies/tonne
environ (7524 MJ), - qui ne descend pas à moins de 600 thermies/ tonne dans le meilleur
cas, pour d'autres types de fours statiques - soit une économie de combustible proche
de 90 %. En outre la vitesse de montée en température, pour des électrodes de 300
mm de diamètre, peut attendre 150° C par heure alors qu' on ne dépasse guère 12 à
15°/heure dans les fours statiques et 40 à 50° C au plus dans des fours où les produits
sont au contact direct de la flamme.
[0032] Le moufle se prolonge à l'extérieur de l'enceinte (4) du four sur quelques mètres.
Dans une première zone le moufle se refroidit spontanément à l'air ambiant. Dans la
deuxième zone, le moufle est refroidi par une circulation d'eau froide dans la double
enveloppe (31). En sortie, les produits sont a une température inférieure à 400° C.
[0033] Les produits obtenus dans ce procédé après graphitation dans les conditions habituelles,
ont des caractéristiques tout à fait comparables et même un peu supérieures à celles
obtenues dans les fours à chambres classiques, du type "Riedhammer" par exemple ainsi
que le montrent les tableaux suivants.

[0034] En conclusion, l'nvention s'applique au traitement de certains produits réfractaires,
spéciaux tels que des briques ou pièces de forme en magnésie imprégnées au brai, des
produits carbonés crus, et de différents types de produits carbonés cylindriques,
tels qu'électrodes, barres à nipples, produits tubulaires pour l'industrie chimique
et aussi à des produits de plus petites dimensions, tels que les charbons pour piles
électriques, que l'on introduit à l'état cru, brut de filage, en paquets dans des
conteneurs ouverts en acier réfractaire, ce qui permet d'opérer dans le même moufle
cylindrique; on peut aussi, à l'évidence, adapter la forme et les dimensions du moufle
à celles des produits à traiter.
[0035] De même, le four permet la cuisson de tout produit, carboné ou réfractaire, imprégné
par une substance pyrolysable fournissant, comme les brais, des vapeurs combustibles:
c'est le cas notamment des résines à base de polymères organiques tels que les phénol-formol
et les polymétracrylates p
O'lr ne citer que les plus connus.
[0036] Dans ces divers cas, il permet de régler très précisément la pyrolyse et la cokéfaction
du produit d'imprégnation, d'obtenir des produits réfractaires parfaitement homogènes,
et d'économiser jusqu'à 90 % de l'énergie qui serait nécessaire dans la plupart des
fours statiques de mêmes performances.
[0037] Mais il est également possible d'utiliser ce four pour le traitement de produits
autres que des produits imprégnés de brai, tels que des barres et billettes en métaux
et alliages (à base d'aluminium, de cuivre, ou de fer pour ne citer que les plus courants).
[0038] Pour le traitement thermique des billettes ou plaques métalliques, la zone de chauffage
assure sur toute la longueur de chaque billette, une tempérrature de traitement constante
et homogène, qui permet d'effectuer dans des conditions idéales, des traitements d'homogénéisation
ou de mise en solution solide ou de revenu ou de chauffage avant filage, ou forgeage,
ou matriçage, ou même laminage, avec une précision de température de l'ordre du degré.
[0039] Bien entendu, dans ce cas, on ne bénéficie pas de l'apport énergétique dû à la combustion
des produits volatiles émis par les produits carbonés imprégnés de substances pyrolysables,
mais l'homogénéité de température et son contrôle rigoureux, et l'absence de contact
entre les produits à cuire et des gaz de combustion sont des caractéristiques très
attractives. A titre d'exemple, dans un four conforme au dessin de la figure 1, on
a traité des billettes de 300 mm de diamètre, en alliage à base d'aluminium, du type
7075, ayant la composition suivante:
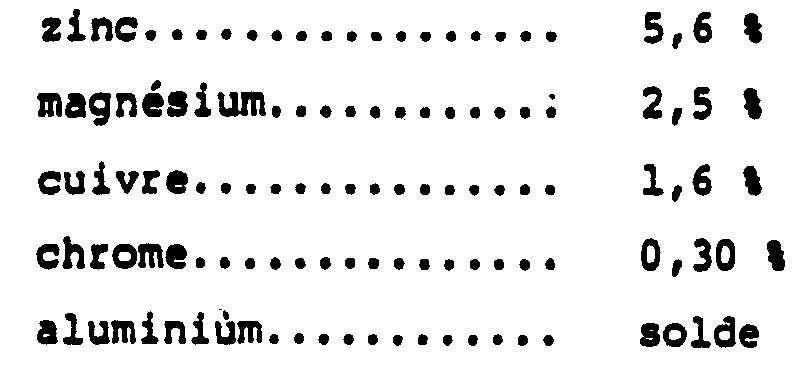
[0040] - Les billettes, brutes de coulée continue, ont été homogénéisées par chauffage à
485°C, puis, en sortie du four, dont la zone de sortie était calorifugée, directement
introduites dans le conteneur d'une presse à filer la température de la billette,
dans le conteneur, était de 455° C.
[0041] De la même façon, on a pu réchauffer, à 850°C, des billettes de cuivre, avec circulation
d'azote, en vue d'alimenter un laminoir-perceur destiné à la production d'ébauches
pour la fabrication, par laminage et étirage ultérieurs, de tubes de cuivre.
[0042] Enfin, bien que le four ait été décrit dans le cas particulier où le moufle est cylindrique,
il est évident que sa section peut être carrée ou rectangulaire si l'on prévoit de
traiter exclusivement des profilés de section autre que circulaire.
1°) Four moufle, pour traitements thermiques en continu, par défilement, de produits
réfractaires ou carbonés, imprégnés d'une substance carbonée telle que le brai dont
la pyrolyse donne des vapeurs combustibles, le cycle de fabrication de ces produits
comportant un passage d'une durée prédéterminée à une température pouvant atteindre
1100 à 1150 °C environ, ce four étant chauffé par un brûleur à flamme sans contact
direct entre les gaz de combustion et les produits à traiter, et comportant:
- une zone d'entrée munie d'un moyen de chauffage par circulation, dans une double
enveloppe (7) disposée autour du moufle (10), de gaz de combustion recyclés;
- une zone de chauffage, disposée à l'intérieur d'une enceinte calorifugée (4), munie
d'au moins un moyen (12) de mise en circulation des gaz de combustion, autour de la
zone de chauffe du moufle;
- une zone de sortie munie d'au moins un moyen de contrôle de la vitesse de refroidissement
des produits traités,
caractérisé en ce que la zone de chauffe est divisée, au moyen d'une cloison (21)
en trois parties:
a) une zone d'exsudation et de sortie des matières volatiles et de la substance carbonée
d'imprégnation (du brai) dans laquelle le moufle comporte une ouverture (22) débouchant
sur un couloir délimité par la cloison (21) et la paroi externe (24), et dont la sortie
est située à proximité de la flamme du brûleur (11);
b) une zone (25) de pyrolyse et de cokéfaction de la substance carbonée d'imprégnation;
c) une zone (26) de cuisson finale dans laquelle est atteinte la température maximale
nécessitée par le traitement thermique, qui peut atteindre 1100 à 1150° C.
2°) Four moufle, selon revendication 1, caractérisé en ce que le moyen de mise en
circulation des gaz de combustion recyclés est constitué par un ventilateur (12) et
une cloison de séparation (13) qui détermine, avec la paroi (14) du four, un couloir
(15) qui débouche sur le moufle (10) dans une zone de transition entre la zone de
chauffe et la zone de sortie.
3°) Four, selon revendication 1, caractérisé en ce que la zone (25) de pyrolyse et
de cokéfaction comporte une double enveloppe (27) dans laquelle circulent lez gaz
de combustion provenant de la zone de cuisson finale, éventuellement dilués par de
l'air extérieur et/ou des gaz de combustion provenant de la zone de préchauffage.
4°) Four, selon revendication 1, caractérisé en ce qu'il comporte un circuit de préchauffage
de l'air de combustion apporté au brûleur.
5°) Four, selon revendication 1, caractérisé en ce que le brûleur est muni d'un moyen
d'alimentation d'air additionnel - préchauffé ou non pour assurer la combustion des
vapeurs et de la substance carbonée d'imprégnation.
6°) Four, selon revendication 1, caractérisé en ce que le moyen de contrôle de la
vitesse de refroidissement des produits est constitué par un calorifugeage disposé
autour d'au moins une partie de la longueur de la zone de sortie.
7°) Four, selon revendication 1, caractérisé en ce que le moyen de contrôle de la
vitesse de refroidissement est une double enveloppe disposée autour d'au moins une
partie de la longueur de la zone de sortie, et dans laquelle circule un fluide liquide,
gazeux ou vaporisé.
8°) Four, selon revendication 1, caractérisé en ce que le moyen de contrôle de la
vitesse de refroidissement est constitué par un dispositif d'aspersion ou de pulvérisation
d'un fluide.
9°) Four, selon l'une quelconque des revendications 1 à 8, caractérisé en ce qu'il
comporte des moyens de poussage assurant l'avance des produits à traiter dans le moufle.
10°) Four, selon revendication 9, caractérisé en ce que les moyens de poussage agissent
de façon continue sur les produits à traiter.
11°) Four, selon revendication 9, caractérisé en ce que les moyens de poussage agissent
pas à pas sur les produits à traiter.
12°) Four, selon l'une quelconque des revendications 1 à 11, caractérisé en ce que
les produits à traiter sont disposés dans des conteneurs ouverts.
1. Muffelofen zur kontinuierlichen thermischen Behandlung durch Durchführen von feuerfesten
oder kohlenstoffhaltigen Produkten, die mit einer kohlenstoffhaltigen Substanz, wie
Pech, imprägniert sind, dessen Pyrolyse brennbare Dämpfe erzeugt,
wobei der Herstellungszyklus dieser Produkte einen Durchgang einer bestimmten Dauer
bei einer Temperatur von bis zu etwa 1100 bis 1150°C umfasst und der Ofen durch einen
Flammenbrenner ohne direkten Kontakt zwischen den Verbrennungsgasen und den zu behandelnden
Produkten geheizt wird, mit
- einer Eingangszone mit einer Heizvorrichtung durch Zirkulation der zurückgeführten
Verbrennungsgase in einem Doppelmantel (7) um die Muffel (10),
- einer Heizzone im Inneren eines wärmeisolierten Mantels (4) mit mindestens einer
Vorrichtung (12) zur Zirkulation der Verbrennungsgase um die Heizzone der Muffel,
- einer Ausgangszone mit mindestens einer Vorrichtung zur Kontrolle der Abkühlgeschwindigkeit
der behandelten Produkte,
dadurch gekennzeichnet, daß die Heizzone durch eine Trennwand (21) in drei Teile geteilt
ist:
a) eine Ausschwitz- und Ausgangszone für die flüchtigen Bestandteile und die kohlenstoffhaltige
Imprägniersubstanz (Pech), in der die Muffel eine Öffnung (22) auf einen durch die
Trennwand (21) und die Aussenwahd (24) begrenzten Gang hat, dessen Ausgang sich in
der Nähe des Flammenbrenners (11) befindet,
b) eine Zone (25) zur Pyrolyse und Verkokung der kohlenstoffhaltigen Imprägniersubstanz,
c) eine Endbrennzone (26), in der die für die thermische Behandlung notwendige Maximaltemperatur
von bis zu 1100 bis 1150° C erreicht wird.
2. Muffelofen nach Anspruch 1, dadurch gekennzeichnet, daß die Vorrichtung zur Zirkulation
der zurückgeführten Verbrennungsgase einen Ventilator (12) und eine Trennwand (13)
umfasst, die mit der Ofenwand (14) einen Gang (15) bestimmt, der in einer Übergangszone
zwischen der Heizzone und der Ausgangszone auf die Muffel (10) mündet.
3. Ofen nach Anspruch 1, dadurch gekennzeichnet, daß die Zone (25) zur Pyrolyse und
Verkokung einen Doppelmantel (27) umfasst, in dem die aus der Endbrennzone kommenden
Verbrennungsgase zirkulieren, die ggf. mit Aussenluft und/oder aus der Vorheizzone
stammenden Verbrennungsgasen verdünnt werden.
4. Ofen nach Anspruch 1, gekennzeichnet durch einen Vorheizkreis für die dem Brenner
zugeführte Verbrennungsluft.
5. Ofen nach Anspruch 1, dadurch gekennzeichnet, daß der Brenner mit einer Zufuhrvorrichtung
für zusätzliche Luft - vorgeheizt oder nicht - ausgerüstet ist, um die Verbrennung
der Dämpfe und der kohlenstoffhaltigen Imprägniersubstanz zu gewährleisten.
6. Ofen nach Anspruch 1, dadurch gekennzeichnet, daß die Vorrichtung zur Kontrolle
der Abkühlgeschwindigkeit der Produkte einen Wärmeschutz um mindestens einen Teil
der Länge der Ausgangszone umfasst.
7. Ofen nach Anspruch 1, dadurch gekennzeichnet, daß die Vorrichtung zur Kontrolle
der Abkühlgeschwindigkeit ein Doppelmantel um mindestens einen Teil de: Länge der
Ausgangszone ist, in dem eine Flüssigkeit, ein Gas oder Dampf zirkuliert.
8. Ofen nach Anspruch 1, dadurch gekennzeichnet, daß die Vorrichtung zur Kontrolle
der Abkühlgeschwindigkeit eine Vorrichtung zum Versprühen oder Pulverisieren einer
Flüssigkeit umfasst.
9. Ofen nach einem der Ansprüche 1 bis 8, gekennzeichnet durch Schubvorrichtungen,
die das Vorrücken der zu behandelnden Produkte im der Muffel gewährleisten.
10. Ofen nach Anspruch 9, dadurch gekennzeichnet, daß die Schubvorrichtungen kontinuierlich
auf die zu behandelnden Produkte wirken.
11. Ofen nach Anspruch 9, dadurch gekennzeichnet, daß die Schubvorrichtungen schrittweise
auf die zu behandelnden Produkte wirken.
12. Ofen nach einem der Ansprüche 1 bis 11, dadurch gekennzeichnet, daß die zu behandelnden
Produkte in offenen Behältern angeordnet werden.
1. A muffle furnace for continuous heat treatments, during passage of the material,
of refractory or carbon-containing products which are impregnated with a carbon-containing
material, such as pitch, the pyrolysis of which produces combustible vapours, the
production cycle of these products having a passage of predetermined duration at a
temperature which may be from 1100 to 1150°C, this furnace being heated by a flame
burner without the combustion gases directly contacting the products to be treated,
and comprising:
- an inlet zone provided with a heating means, by circulating recycled combustion
gases in a double casing (7) provided around the muffle (10);
- a heating zone, provided inside a heat-insulated chamber (4), provided with at least
one means (12) for circulating the combustion gases around the heating zone of the
muffle;
- an outlet zone provided with at least one means for controlling the cooling speed
of the treated products characterised in that the heating zone is divided into three
sections by a partition (21):
a) a zone for exuding and removing volatile materials from the carbon-containing impregnation
material (pitch) in which the muffle comprises an aperture (22) opening into a passage
delimited by the partition (21) and the outer wall (24) and the outlet of which is
situated in the vicinity of the flame of the burner (11);
b) a zone (25) for pyrolyzing and carbonizing the carbon-containing impregnation material;
c) a final firing zone (26) in which the maximum temperature required for the heat
treatment is reached, which can be from 1100 to 1150° C.
2. A muffle furnace according to claim 1, characterised in that the means for circulating
the recycled combustion gases comprises a ventilator (12) and a separating partition
(13) which delimits, with the wall (14) of the furnace, a passage (15) which opens
into the muffle (10) in a transition zone between the heating zone and the outlet
zone.
3. A furnace according to claim 1, characterised in that the pyrolyzing and carbonizing
zone (25) comprises a double casing (27) in which there circulate the combustion gases
originating in the final firing zone, optionally diluted by the surrounding air and/or
the combustion gases from the preheating zone.
4. A furnace according to claim 1, characterised in that it comprises a circuit for
preheating the combustion air supplied to the burner.
5. A furnace according to claim 1, characterised in that the burner is provided with
a means for supplying additional air - preheated or otherwise - for ensuring the combustion
of the vapours and the carbon-containing impregnation material.
6. A furnace according to claim 1, characterised in that the means for controlling
the cooling speed of the products consists of an insulation provided around at least
one section of the length of the outlet zone.
7. A furnace according to claim 1, characterised in that the means for controlling
the cooling speed is a double casing provided around at least one section of the length
of the outlet zone, and in which there circulates a liquid, gaseous or vapourized
fluid.
8. A furnace according to claim 1, characterised in that the means for controlling
the cooling speed consists of a device for drawing by section or spraying a fluid.
9. A furnace according to any one of claims 1 to 8, characterised in that it comprises
pushing means which ensure the forward movement of the products to be treated in the
muffle.
10. A furnace according to claim 9, characterised in that the pushing means act in
a continuous manner on the products to be treated.
11. A furnace according to claim 9, characterised in that the pushing means act stepwise
on the products to be treated.
12. A furnace according to any one of claims 1 to 11, characterised in that the products
to be treated are arranged in open containers.