[0001] The present invention relates to copper sheeting for building purposes, and particularly,
although not exclusively, to copper sheeting for use as roofing material.
[0002] Copper sheeting used hitherto for building purposes, e.g. roofing material, has the
form of a rolled and annealed sheet product (Swedish Standard SS 14 50 13). The sheet
is rolled from electrolytically produced cathode copper, or from some other refined
copper product, which is first remelted and cast to form an ingot and then rolled,
in several stages, while in a hot state, at least initially, to the desired thickness,
normally 0.6-0.7 mm, whereafter the sheet is annealed, at least in the majority of
cases. By cathode copper or electrolytic copper, as designated according to Swedish
Standards, is meant here and in the following the refined copper product obtained
when raw copper, so-called anode copper, is refined by conventional electrolytic processes.
During this electrolytic refinement of the raw copper, the cathode copper is precipitated
on mother plates in the form of cathodes placed between anodes of the copper to be
refined in the electrolytic cell (anode copper).
[0003] The sheeting is not delivered to the building site in the large rolls into which
it is wound when leaving the rolls of the rolling mill, but more often in the form
of separate pieces having lengths/widths of 2 m x 1 m.
[0004] Copper is a highly useful building material, since it is impervious to water, has
practically unlimited durability and has an aesthetically pleasant surface colouring.
[0005] Of course, the use of copper for building purposes is restricted by its high price
compared with alternative products. The price of a product produced in the manner
described in the introduction is particularly high, the costs entailed therewith including
the cost of remelting and casting the raw copper to form ingots, heating the ingots
to rolling temperature, and rolling the ingots down to the fine sheet-dimensions required.
[0006] Various ideas as to how the costs entailed when using copper as a building material
can be reduced have been previously proposed in the art. One such proposal is found
in SE-C-71443 which instead of relatively thick sheets, or plates, recommends the
use of thin copper matting which can be glued or likewise bonded to the substratum
on which they are laid. According to the proposals set forth in this patent, the copper
matting is produced by rolling endless copper strip, or galvanically by precipitating
copper onto a drum or a belt, until the desired thickness is reached. These proposals,
however, have not resulted in commercial products, probably because the expense involved
by rolling the copper to such thin dimensions is excessive, and because of the difficult
technical problems encountered when applying the continuous galvanic method.
[0007] Thus, there is on the part of the building industry a desire for less expensive,
useful copper products, and on the part of the copper manufacturer a natural desire
to expand the market for copper.
[0008] It has now surprisingly been found possible to produce a copper product which solves
the aforesaid problems, at least to a substantial extent, since the product lends
itself to much lower manufacturing costs than present day commercial roofing material,
without departing from the quality requirements placed on building material of this
kind be the consumer and by the authorities.
[0009] To this end there is provided in accordance with the invention a copper product having
the characteristic features set forth in the following claims.
[0010] Thus, instead of a rolled and optionally annealed product, there is produced an electrolytically
formed product comprising a sheet of non-remelted cathode or electrolytic copper produced
in a limited dimension suitable for direct use. The sheet has a thickness of 0.5-1
mm, preferably 0.6-0.8 mm, and a length/width of about 1 m x 1 m.
[0011] The sheets are manufactured by conventional electrolytic copper refining techniques.
The electrolytic tanks used, however, have a depth which is roughly twice that of
conventional tanks, and the dimensions of the anodes and mother plates are adapted
accordingly. The cathodic copper product is preferably precipitated onto mother plates
made of titanium or stainless steel to the thickness desired, and then stripped therefrom
manually or mechanically in a conventional manner.
[0012] The mother plates preferably have a length/width of 200 cm x 100 cm and are suspended
"on end" in the electrolytic bath. The distance between the electrodes may be of the
same order of magnitude as that applied with conventional, smaller electrodes, since
longer electrodes tend to hang more vertically.
[0013] The deviations obtained at the bottom edge of the electrodes are thus comparable
with those obtained with conventional electrolysis.
[0014] The surfaces of the resultant cathodic copper sheet, or plate, are rougher than the
surface of rolled sheet, although this is more of an advantage than a disadvantage
in the case of roofing sheets, since rough copper sheeting obtains the desired green
patina much more quickly than rolled plate. When the consumer, or user, requires perfectly
flat and smooth sheets, the sheets may be cold-rolled in one or two cold-rolling stages,
therewith also increasing the mechanical strength properties of the sheeting at the
same time. The mechanical properties of the electrolytically formed sheeting are sufficiently
high, however, in the absence of such subsequent treatment, as illustrated hereinafter
in the following working example, in which the properties of electrolytically produced
sheeting are compared with industrial standards for copper-roof sheeting.
Example
[0015] Copper sheeting was produced electrolytically in dimensions of 1000 x 1000 x∼0.7
mm. Tensile tests, hardness tests, bending tests, and to-and-from bending tests (reverse
bending) were carried out in accordance with stan-dardized methods on samples taken
from the copper sheet, these samples comprising seven tensile-test rods (sheet sample
rods type F) according to SS 11 21 16 and 40 sample rods 100 x 20 x 0.7 mm for bending
and reverse bending tests. Prior to carrying out the tests, half of the sample rods
used were hardened at 200°C for two hours in an N₂ atmosphere.
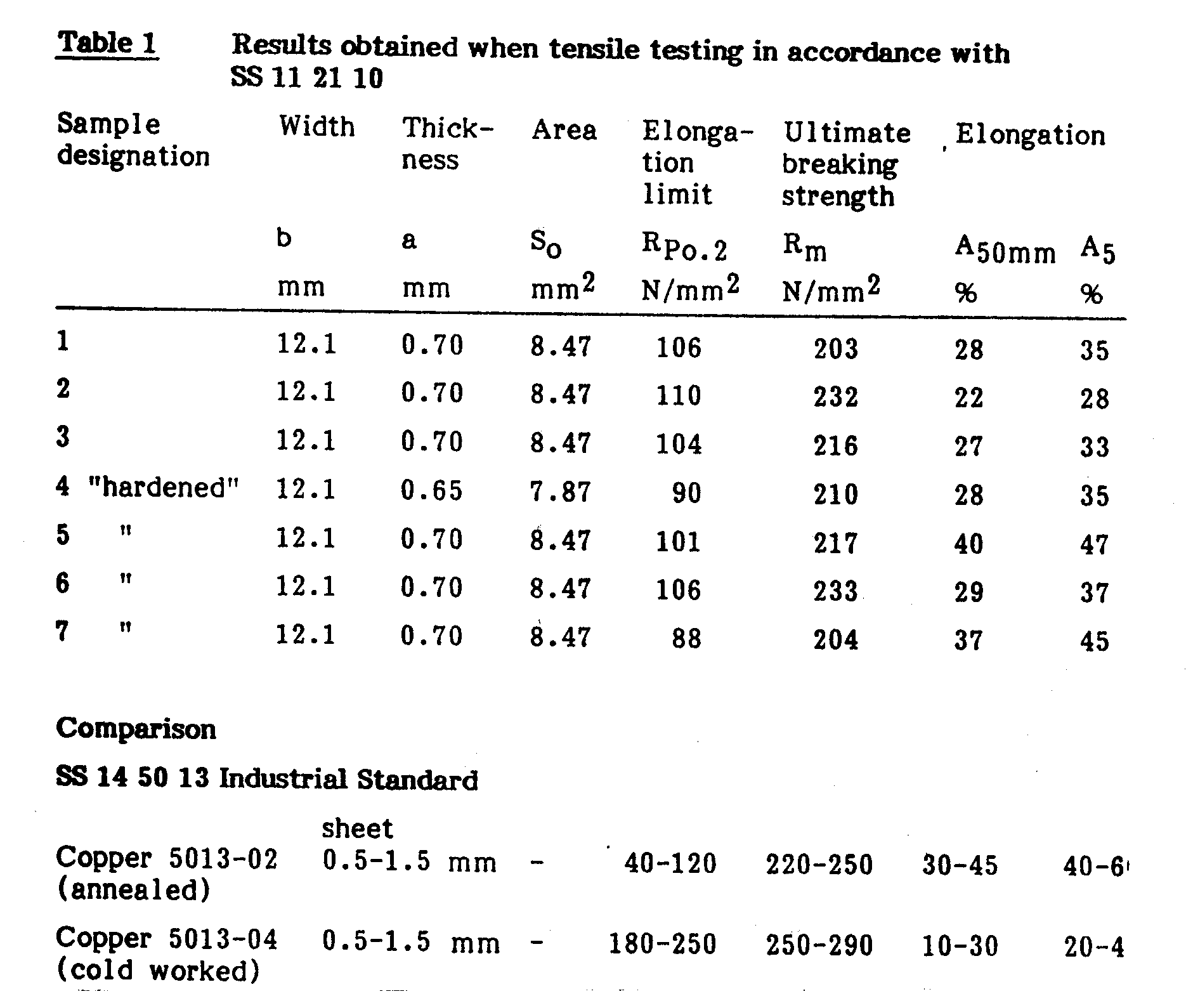
[0016] The hardness test was carried out in accordance with SS 11 25 17 (Vickers test HV
0.5), on the heads of the tensile rods subsequent to negligible polishing of the surfaces.
[0017] The word "bright" used in Table 2 signifies the surface facing the mother plate during
manufacture, whereas the word "dull" signifies the surface facing outwardly of the
electrolyte.
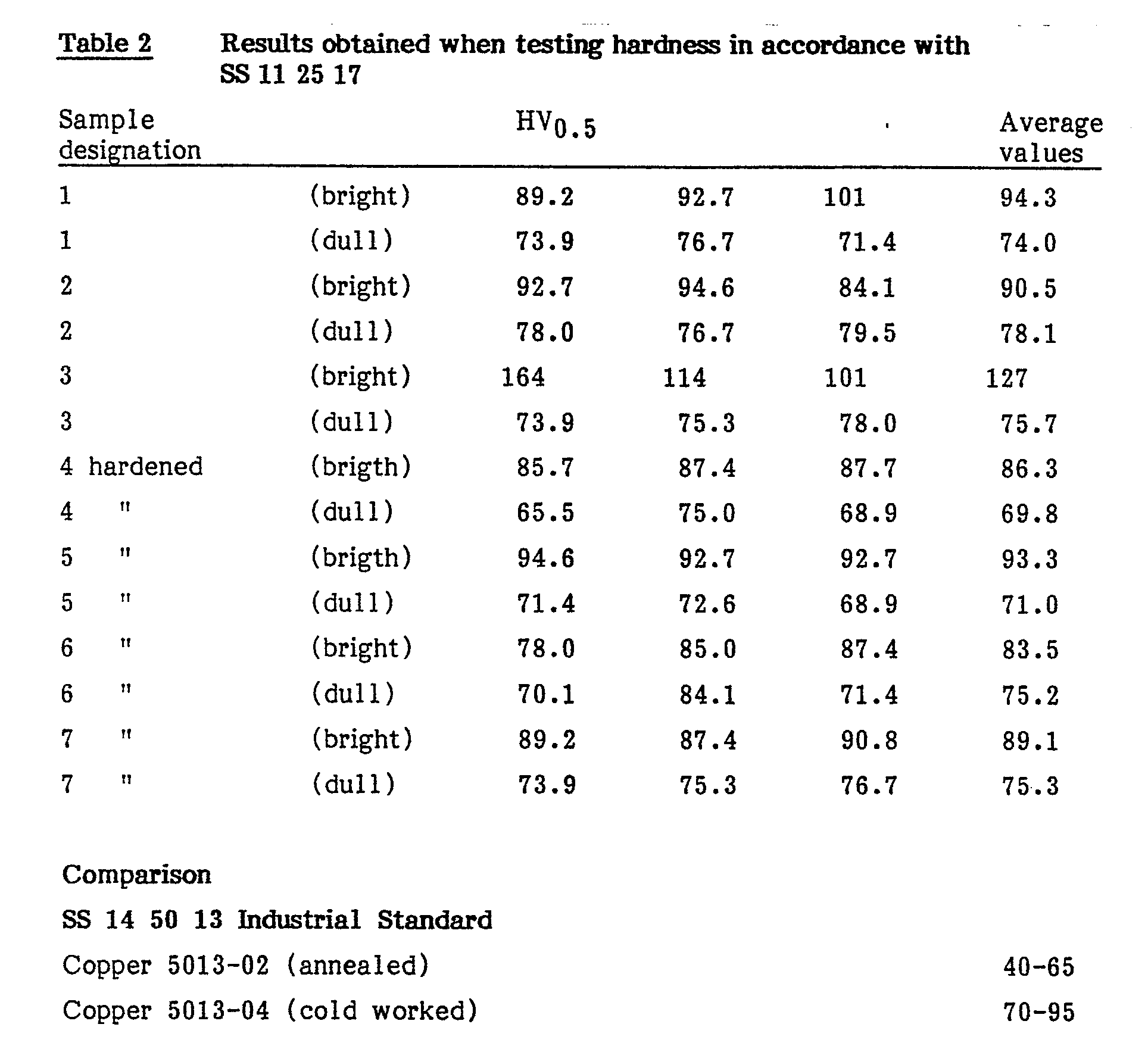
[0018] The samples were also bent in accordance with SS 11 26 26 and subjected to reverse
bending tests in accordance with SS 11 26 23 with no complaints regarding the properties
of the sheeting.
[0019] The example shows that the mechanical properties of copper sheeting, or plate, according
to the invention, which sheeting can be produced much more simply and therewith much
more cheaply than conventional copper roofing sheet, are well on a par with conventional
copper roofing sheet. The elongation limit and the ultimate tensile strength of the
inventive product are fully comparable with those of annealed, rolled copper sheet
or plate (5013-02), while the elongation values A
50mm and A₅ lie inbetween the annealed and cold-worked state (5013-04). The hardness HV
0.5 is comparable with that of 5013-04.
1. Copper sheeting for building purposes, particularly for roofing purposes, characterized
in that the sheeting comprises non-remelted cathode or electrolytic copper produced
in dimensions suitable for the purpose intended.
2. Copper sheeting according to claim 1, characterized in that is has a thickness
of 0.5-1 mm, preferably 0.6-0.8 mm.
3. Copper sheeting according to claim 1 or 2, characterized in that it has a length/width
of approximately 2 m x 1 m.
4. Copper sheeting according to any of claims 1-3, characterized in that the sheeting
has passed through at least one cold-rolling stage.