Background of the invention
[0001] The present invention relates to microwave heating apparatus for processing material
enclosed in an evacuated chamber.
[0002] Heretofore, it is known to provide in industry a continuous process system for heating
and drying subject material moved on a conveyor through a microwave chamber that is
sealed and evacuated and into which microwave energy is fed. These systems are now
of large physical size and feed many kilowatts of continuous microwave power into
the chamber from a multitude of sources. A system of this sort is described in US-A-4,045,639.
The function of such apparatus is to feed microwave energy con-: tinuously into the
process material with as uniform distribution of the energy as can be achieved, while
the material is moved through the chamber on a conveyor. Large systems of this sort
may use six or more magnetrons, each operating continuously and producing many kilowatts
of power. Hence, the total microwave power fed into the chamber is large and may be
in the range of 50 to 100 kilowatts continuous power.
[0003] - Operating at such high power levels clearly requires the use of high power sources
in order to avoid having an excessively large number of sources. Magnetrons of such
high power have a narrow limitation on the allowable amount of power that may reenter
them, either as a reflection of the magnetrons' own output or as "cross-talk" from
other magnetrons in the system. It has been suggested by some to use circulators to
avoid this problem; however, circulators are relatively expensive and they do not
solve other problems that accompany high power delivery into a microwave chamber.
Also, where vacuum drying is carried out simultaneously with microwave heating, it
is very difficult to prevent ionization of gas in the chamber by the microwave electric
fields. Ionization permits arcing that wastes the microwave energy and, it can also
degrade the quality of the process material and is generally destructive of the apparatus.
[0004] It has been suggested to use arc detectors within the chamber that detect the occurrance
of an arc and quickly interrupt microwave power to minimize the harm that is done
by the arcing. However, frequent interruptions make the heating process very inefficient
and in the processing of some materials the interruptions are not at all acceptable.
[0005] Some of the objects of the present invention are to overcome these problems of non-uniform
high power, discontinuous heating, reflection into the magnetrons, as well as cross-talk.
Another object is to reduce ionization and arcing problems where microwaves are used
within an evacuated chamber.
Summary of the invention
[0006] The uniform distribution of continuous high microwave power into the process material
is accomplished by radiating, preferably at regular places along the inside of the
chamber, defined beams of circularly polarized microwave radiation, each beam being
directed to illuminate a prescribed portion of the process material or a prescribed
area through which the process material is moved. Microwave beams are weaker near
their edges than at the center and so they are overlapped to compensate for this and
provide illumination that is essentially uniform across the width of the path of the
process material. Overlapping may also be effective to compensate for non-uniform
distribution of the process material on the conveyor. Thus, the illumination does
not depend upon the use of mode stirrers or turntables or any other equipment designed
to reflect the microwave energy about the chamber and it does not depend particularly
upon the geometry of the chamber. It permits the chamber to be designed in view of
the pressure or vacuum conditions of operation: For example, it permits-a cylindrical
chamber which is the preferred shape for withstanding vacuum and still provide for
the spatially extended continuous processing of the subject materials on a conveyor
belt.
[0007] In the past where microwave heating has been accomplished in a cylindrical chamber,
the process material was not directly illuminated by microwave energy beamed into
the chambers. As a consequence, the tendancy was to concentrate the microwave energy
near the walls of the cylindrical chamber and there would be a deficiency of energy
along the cylinder axis (along the center of the conveyor). Thus, material carried
through the chamber on the conveyor would be heated more along the edges of the conveyor
than at the center. Where the process of microwave heating occurs while at the same
time vacuum drying occurs, the vacuum pressure produced in the chamber is often in
the range in which ionization by the microwave electric fields and arcing are very
difficult to prevent. In the present invention a structure is provided so that the
peak values of electric fields of the microwave energy at a window where the microwave
energy enters the chamber from the ambient pressure exterior are severely limited.
Experience as well as theory show that high intensity microwave electric fields are
produced at the "bottle neck" where the microwave is transmitted from the exterior
region through some sort of microwave transparent, pressure withstanding window, into
the evacuated interior of the chamber. Elsewhere, within the chamber, the intensity
of the electric fields is usually much lower and ionization problems are reduced.
[0008] In an embodiment of the present invention described herein, a cylindrical microwave
chamber is provided through which a conveyor belt moves the process material at about
the. center of the cylinder. Opposite the material along the walls of the chamber,
at regularly spaced places, separate sources radiate beams of microwave energy into
the chamber, directed toward the process material. Each beam illuminates a prescribed
area of the conveyor belt and the beams overlap particularly along the center of the
belt so as to produce a uniform or an intentionally "tailored" heating pattern. The
configuration of each beam is modified by a dielectric lens that redirects the microwave
energy just before it enters the chamber through the window and directs the beam toward
the conveyor.
[0009] In order to reduce arcing in the microwave chamber, it is necessary to minimize the
intensity of the microwave electric fields and, thereby minimize ionization within
the chamber, which occurs when the chamber is evacuated, as in a heating-drying operation.
This is done by radiating beams of microwave energy that are circularly polarized
and in the TE mode over substantially the whole area of the relatively large window
through which the microwave beam is radiated into the chamber.
[0010] In order to heat uniformally and avoid those problems in prior systems where heating
is excessive at the edges of the conveyor and deficient at the center, the radiation
is re-directed by the lens and radiated directly at the process material, impinging
upon the material at the "first pass". Another design feature that contributes to
uniform heating is to provide separate microwave power sources for the sources that
are not mutually coherent.
[0011] In the preferred embodiment, each of the individual beams is generated outside of
the chamber, re-directed by the lens and radiated into the chamber through a transparent
window at the chamber wall. Thus, there are a multitude of lenses and transparent
windows arranged along the chamber wall through each of which a formed beam of circularly
polarized microwave radiation is radiated directly toward the process material. The
window is a half wave length of the microwave in thickness to minimize reflections
from the window.
[0012] In order to minimize the likelihood of ionization around the window on the inside
of the chamber, the area of the window is made as large as practical, the beam radiated
through it is predominantly TE mode waves rather than TM mode waves and is essentially
a single mode beam rather than a mixture of modes and the single mode is circularly
polarized. One advantage of circular polarization is that twice as much power is transmitted
as for a plane polarized beam for a given peak value of the microwave electric field.
[0013] It is an advantage in some embodiments of the present invention to provide a dielectric
lens or prism near the dielectric window. This allows the source apparatus that produces
the circularly- polarized, single-mode TE beam spread over the entire area of the
relatively large window to be vertically oriented above the chamber (and above the
conveyor), with the source magnetron upright and not "tipped". Magnetron performance
and life is best when operated upright. Furthermore this orientation of the source
apparatus and the magnetron therein is often preferred from the standpoint of: total
floor area required for the heating apparatus; ease and convenience of maintenance;
and cost of manufacture.
[0014] Vertical orientation of the sources on top of the cylindrical chamber also facilitates
changing the direction of a beam so that the beam therefrom can be directed to one
side or the other of vertical and so pointed as needed at one region or another of
the conveyor. The vertical orientation of sources can be along the axial plane of
symmetry of the cylindrical chamber and conveyor therein; or the sources can be set
off to either side of that plane by the effect of a prism lens, and send skewed beams
toward the conveyor. The skewed beam does not define a figure of revolution and does
not illuminate the conveyor uniformally everywhere it strikes, but equal skewed beams
from opposite sides of that plane can balance each other and even provide combined
illumination that is uniform across the conveyor.
[0015] It is an object of the present invention to provide high power microwave apparatus
for continuously heating process material uniformly throughout, even when the material.
is spread over a relatively large surface.
[0016] It is a further object to provide microwave heating and drying apparatus wherein
problems of arcing are reduced or avoided.
[0017] It is another object to provide microwave heating and drying apparatus wherein the
problems of reflection into the source of microwave energy, cross-talk, uniform high
power continuous heating, ionization and arcing are reduced and/or avoided.
[0018] It is another object to provide a microwave lens for shaping and/or directing a pattern
of microwave energy radiated into microwave heating apparatus.
[0019] It is a further object to provide improved microwave heating apparatus.
Description of the drawings
[0020]
Figure 1 is a cross section of continuous process microwave heating and vacuum drying
apparatus for treating a process material;
Figure 2 shows the same apparatus in cross section taken longitudinally through the
apparatus;
Figures 3 and 4 show in detail the structure 6 for converting linearly polarized radiation
to circularly polarized radiation, and:
Figure 5 is a side cross section view of structure for providing a dielectric prism
lens adjacent to the outside of the chamber window for directing and/or shaping, the
circularly polarized microwave radiation as a skewed beam toward the conveyor.
Figure 6 is the top view of the dielectric prism lens structure 9;
Figure 7 is the top view of the layers of dielectric showing construction of the prism
lens; and
Figures 8 and 9 are a side cross section view and top view of the layers of dielectric
for another lens configuration for forming a controllably spread beam that is not
skewed as the beam formed by the lens shown by Figures 5, 6 and 7.
Description of an embodiment of the invention
[0021] Turning first to the Figures 1 and 2, there is shown a section of cylindrical microwave
chamber. The chamber is defined by the chamber wall 12 that is electrically conductive.
It is cylindrical in shape, because that shape is intrinsically strong and best able
to withstand the pressures produced on the chamber when it is evacuated as, for example,
in a microwave heating and vacuum drying process. Within the chamber is a conveyor
belt 21, a section of which is shown in the Figures, positioned substantially at the
center of the chamber and extending longitudinally therethrough. The conveyor belt
carries the process material 22 usually distributed evenly along and across the belt.
[0022] Only a section of the complete chamber is shown in these Figures. It is the section
where the process material is irradiated by the high power directional microwave beams
to heat the material. There are well known structures and techniques for vacuum sealing
the ends of such a cylindrical chamber, for mounting and powering a conveyor system
within the chamber and for feeding the process material on-to and off-of the conveyor
belt. Also, there are many known techniques for sealing the chamber against leakage
of microwave energy from the chamber that could be hazardous and/or wasteful. In as
much as none of those techniques are the particular subject of the present invention,
they are not described herein.
[0023] Along the section of the cylindrical chamber disclosed in the drawings, all on the
same side of the conveyor belt 21, six beams of microwave energy are radiated into
the chamber, each beam coming from a different source and directed to a specific area
of the belt (presuming the belt to be stationary for the moment). The spatial arrangement
of the beam is regular; they are uniformly spaced longitudinally along the belt in
pairs, each pair including the left beam and the right beam (as viewed in the direction
of the moving belt--Fig. 1). Thus, the arrangement of the beams along the chamber
is symmetrical about the plane defined by line 23 shown in Figure 1.
[0024] The microwave radiation contained within each beam is preferably of substantially
uniform intensity across the beam-prior to entering the cylindrical chamber-and is
circularly polarized. Furthermore, where the beams enter the cylindrical chamber,
defined by walls 12, through an opening 13 in the chamber, the beam substantially
completely fills that opening. As shown in Figures 1 and 2, the beams are defined
by broken lines and are denoted 24, 26 and 28 along the left side of the chamber,
and 25 along the right side of the chamber. Each beam preferably overlaps the adjacent
beams and so insures that along this microwave heating section of the chamber substantially
the whole area of the conveyor belt 21 is illuminated by the sources. Furthermore,
by overlapping the beams, the tendency is to compensate for the reduced intensity
of radiation at the edges of the beams.
[0025] The uniform arrangement of equal beams is preferred. If unequal beams are used and/or
the beam spacing is not regular, particular heating effect could be achieved; however
the problem becomes complicated. The particular embodiment described herein suggests
using equal beams all of the same intensity and size, uniformly spaced along the chamber
and overlapping where they illuminate the conveyor belt enough to insure adequate
illumination along and from side to side thereof in the microwave heating section
of the apparatus. Furthermore, each of the beams is from a different source wherein
the microwave energy is generated, converted to a linearly polarized TE mode, then
converted to circular polarization, spread, redirected and radiated into the chamber.
The separate sources, denoted 34, 36 and 38 .on the left side and 35, on the right
(one for each beam), may be constructed - su.bstantially identical to each other as
a matter of convenience..
[0026] The process material is carried through the microwave heating section shown in Figures
1 and 2 on the conveyor belt and heated by the direct radiation of the beams. Thus,
the process material is primarily heated by the first pass of microwave energy from
the microwave sources and there is no primary dependance upon reflections of the microwave
energy within the chamber to direct it to the process material. Hence, there is no
need of microwave mode stirrers within the chamber. In the preferred embodiment, each
beam is derived from a different source, and there is no phase coherence between the
beams; so, again, there is no need for mode stirrers within the chamber. In the preferred
embodiment there is no direct radiation from one source into another source, and since
the radiation is circularly polarized, a negligible amount of radiation from any source
that may reflect within the chamber will reenter the same or any - other source.
[0027] Thus, re-entrant, cross-talk, and moding problems, that have occurred with prior
systems, are avoided.
Sources
[0028] The beams 24, 26, 28 and 25 respectively are produced by sources 34, 36, 38 and 35
respectively. These sources may be constructed substantially all the same and so only
one of them, source 34, is described in detail herein below.
[0029] The source consists of a microwave power generator, a mode-forming launcher, a polarization
convertor, a conical expansion in diameter, and an assembly, which includes a sealed
transparent dielectric window in the chamber and a dielectric lens. The microwave
power generator is a,magnetron 1. The coaxial output section 2 from the magnetron
terminates in a probe 4 that feeds a standard waveguide section 3, also called a launcher,
that launches the microwave energy into the waveguide and thence into the polarizing
and beam-forming portions of the source.
[0030] The polarizing section of the source includes a quarter wavelength transformer section
5 between the launcher 3 and the polarization converter 6. The converter 6 consists
of a square waveguide and means, denoted 7, within the square waveguide for converting
linearly polarized radiation from the launcher into circularly polarized radiation.
Thus, the microwave radiation flowing out of the converter 6 is circularly polarized
and flows into the top end of conical wave guide coupling 8 that contains a dielectric
lens 9 at the wide circular bottom end thereof. The lens is immediately adjacent and
above the dielectric window 10 that is of minimally larger diameter than the lens,
in order to be captive in and sealed to holder 19 that, in turn, seals to cylindrical
chimney 11, connected directly to an opening 13 in the wall ofthe chamber 12. Suitable
flanges at 14,15,16,17 and 18 connect these various parts and sections together as
shown in the Figures. All of these flanges must provide contiguous conductive connections
between the parts to insure ideal operation without arcing or leakage of microwave
energy or mode transformation. In addition, flange 18 must seal against the vacuum
within the chamber when the equipment is used for vacuum drying and microwave heating
and, as mentioned above, the window must be sealed to its holder 19.
[0031] The curve 9a of the dielectric lens, the electrical thickness of the dielectric window
10 and the dimensions of the cylindrical chimney 11 are all designed to produce the
particular beam direction and shape that is desired. More particularly, it is generally
desired that the beam 24 from source 34 be directed to illuminate an area of the conveyor
21 that begins at the outside edge 21 a of the conveyor and extends across the conveyor
past the center at 21 b. Similarly, beacon 35 produces the beam 25 that illuminates
the conveyor from the opposite edge 21 c somewhat past the middle at 21 b; and so
at the middle, where the two beams 24 and 25 are weaker, they overlap to some wxtent.
This insures complete illumination from side 21 a to side 21 b of the conveyor.
[0032] Source 35 can be constructed identical to beacon 34, but would be a mirror image
of it, as viewed in Figure 1. Thus, these sources tend to produce beams directed radially
inward from the edge of the cylindrical chamber 12 toward the center of the chamber
and the subsequent pairs of sources 36 and 37 and 38 and 39 do the same. Clearly,
sources 34, 36 and 38 can be constructed identical to each other and sources 35, 37
and 39 can be constructed identical to each other and the even numbered sources are
mirror images of the odd numbered sources.
[0033] Figures 3 and 4 show details of construction of the polarization converter 6. It
consists of a square wave guide section 6a in which are mounted dielectric plates
7a and 7b contiguous to each other across a diagonal of the square. These plates are
longitudinally staggered along the length of the square wave guide. They are the same
length, (L1 plus L2) and one is staggered ahead of the other by the dimensions L2.
L1 is of such a length that:
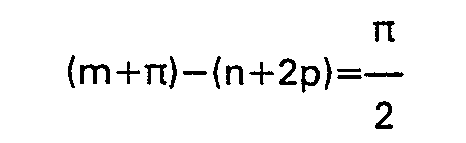
where

and m is greater than n.
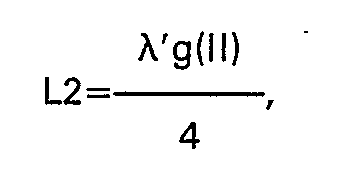
X'g is wavelength with only plate 7a or 7b. λ"g is with both plates 7a and 7b. Subscript
┴ is with electric field perpendicular to the plates. Subscript 11 is with electric
field parallel the plates.
[0034] The dielectric prism lens 9 may be constructed as illustrated by Figures 5, 6 and
7. The experimentally shaped curve 9a-of this lens is established by a stack of dielectric
plates 9a' to 9j, shown in the side cross section view by Figures 5 and a plan view
by Figures.7. The purpose of the dielectric lens in the source is to re-directthe
beam emerging from the conical wave guide 8, to be skewed toward the center of the
chamber.
[0035] This prism lens structure is clearly not a figure of revolution about the beacon
axis 30. It is symmetrical with respect to the plane through the beacon axis, perpendicular
to the chamber axis. The thickness of this lens varies around the edge or periphery
of the stack. Thus, it is generally prism- shaped. It is thicker at the inside edge
toward the chamber plane of symmetry 23, than at its edge away from plane 23. The
effect of this lens is to redirect the beam to one side of the beacon axis 30, toward
the center 21 b of the conveyor in the chamber.
[0036] The dielectric lens is immediately adjacent dielectric window 10. The -thickness
D of the window is one half wave length of the microwave radiation in the dielectric
material of which the window is made. Hence, D is expressed as follows:
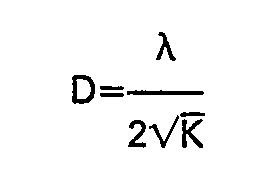
where K=relative dielectric permittivity of the material.
[0037] The conical wave guide connects to the dielectric window holder 19 by flange 17 and
the window holder connects to the cylindrical chimney 11 by flange 18. At flange 18
the window seals to the chimney by an 0-ring gasket vacuum seal 20 and so the interior
of the chamber is vacuum sealed from the exterior ambient and is also sealed from
the source structure.
[0038] Between the flanges 17 and 18, completely enclosing the dielectric window, the holder
19 provides electrical continuity between the wide end of the conical wave guide and
the cylindrical chimney 11. Thus, microwave currents conducted by the conical wave
guide 8, holder 19 and chimney 11 bound the propagating fields of the microwave energy
that flows into the cylindrical treatment chamber 12, and is radiated as the beam
24. By this construction, the beam of microwave radiation is substantially all in
a single TE mode, circularly polarized and fully blankets the dielectric window. As
a consequence of these conditions, the instantaneous peak value of the microwave electric
field at the dielectric window on the vacuum side (the chamber side) is maintained
low. It is maintained sufficiently low that it does not cause ionization of the gas
inside the chamber even at the low operating pressures desirable for vacuum drying.
[0039] Another dielectric lens structure is shown by Figures 8 and 9. This structure is
symmetrical with respect to all planes through the beacon axis 30. It defines a figure
of revolution about the axis 30 and so that axis of the pattern of radiation that
defines the beam issuing from this lens is a continuation of the axis 30. This lens
is spheroidal and has no prism. Using this. lens to direct the beam toward the center
of the conveyor may require that the source be located or oriented with its axis toward
the center of the conveyor and so the source axis would be substantially radial with
respect to the cylindrical chamber in which the center of the conveyor is at the center
of the chamber cylinder.
[0040] Beacons each with a lens constructed as in Figures 8 and 9 are preferably all in
line along the cylindrical chamber directly above the conveyor and so all such beacons
would have the beacon axis in the symmetrical plane 23 of the cylindrical chamber.
This lens is made up of a stack of dielectric plates 31 a, b, c each being ring-shaped.
The outer peripheries of these plates are all about the same and their inner peripheries
are successively larger and so the stack defines the dielectric lens curve 32 and
spreads the radiation into a wider directional beam directed along the source axis
30.
[0041] The embodiment of the invention described hereinabove includes and incorporates all
of the features of the invention and this embodiment is capable of microwave heating
of materials in a continuous process, while, at the same tjme, (or at least in the
same chamber), exposing the materials to a low pressure for vacuum drying. Thus, the
apparatus is suitable for microwave heating and vacuum drying and many of the features
of construction provide an advantage for both heating by microwaves and vacuum drying.
[0042] This apparatus is also usable in a discontinuous process.
1. Microwave heating apparatus for processing material enclosed in an evacuated chamber,
comprising at least one source of microwave energy mounted on the chamber and radiating
into it, characterized by a column comprising a microwave generator, followed by a
circular- polarizing section, followed itself by a conical waveguide section, containing
a dielectric divergent lens at the outlet window, which is designed in such a way
as.to spread the radiation, in order to homogenize the density of power at product
level and minimize the risk of arcing and corona effect.
2. Apparatus as in Claim 1, comprising a plurality of such sources.
3. Apparatus as in Claim 1, in which the product is on a moving conveyor, in order
to allow continuous microwave processing.
4. Apparatus as in Claim 1, in which the circular polarizer is a section of square
waveguide, containing diagonally-oriented dielectric material to differentially retard
the two space quadrature components of the entering wave and of that length in which
the cumulative differential retardation is π/2 radians, so that there is also time
quadrature of the two components, thereby . providing circular polarization.
5. Apparatus as in Claim 1, in which the outlet window is a dielectric of thickness
equal to half a wavelength inside the dielectric.
6. Apparatus as in Claim 1, in which the dielectric divergent lens is symmetric with
respect to the axis of the column.
7. Apparatus as in Claim 1, in which the dielectric divergent lens is asymmetric with
respect to the axis of the column, when irradiation is done by sources symmetrically
spaced above and across the conveyor's axis, so that the beams overlap, in order to
insure homogeneous irradiation of the subject material.
8. Apparatus as in any pair of claims 2, 3, 4, 5 and 6 or 7.
9. Apparatus as in a triplet of claims 2, 3, 4, 5 and 6 or 7.
10. Apparatus as in any quadruplet of claims 2, 3, 4, 5 and 6 or 7.
1. Mikrowellen-Heizvorrichtung zur Behandlung eines Produktes, welches sich innerhalb
eines Vakuumbehälters befindet, bestehend aus mindestens einer Mikrowellen-Energiequalle,
am Behälter angebracht und die in dessen Inneres einstrahlt, gekennzeichnet durch
eine Säule, bestehend aus einem Mikrowellengenerator, gefolgt von einer Sektion die
die Welle kreisförmig polarisiert, diese wiederum gefolgt von einer konusförmigen
Mikrowellen-leitenden Sektion, die am Ausgang eine dielektrisch-divergierende Linse
enthält, die so entworfen ist, dass sie die Ausstrahlung ausbreitet, um die Leistungsdichte
am Produktniveau zu homogenisieren, und um das Risiko von Lichtbüscheln und Ionisierung
zu vermindern.
2. Gerät wie in Anspruch 1 beschrieben, bestehend aus einer Vielzahl solcher Quellen.
3. Gerät wie in Anspruch 1 beschrieben, in dem sich das Produkt auf einem sich fortbewegenden
Transportband befindet,, um eine kontinuierliche Mikrowellenbehandlung zu ermöglichen.
4. Gerät wie in Anspruch 1 beschrieben, in dem der Kriespolarisator eine quadratische
Hohlleitersektion ist, die ein diagonalgerichtetes dielektrisches Material enthält,
um die beiden Volumenkomponente der einfallenden Welle differential zu verzögern,
und von derartiger Länge, dass die summierte differentiale Verzögerung rr/2 Radianten
beträgt, damit es auch zu einer Zeitquadratur der beiden Komponenten kommt, und dadurch
eine Kreispolarisierung entsteht.
5. Gerät wie in Anspruch 1 beschrieben, in dem das Ausgangsfenster ein Deilektrikum
ist, dessen Stärke die Hälfte der Wellenänge innerhalb dieses Dielektrikums gleicht.
6. Gerät wie in Anspruch 1 beschrieben, in dem die dielektrisch-divergierende Linse
achsensymmetrisch zur Säule ist.
7. Gerät wie in Anspruch 1 beschrieben, in dem die dielektrisch-divergierende Linse
achsenunsymmetrisch zur Säule ist, wenn die Bestrahlung durch Quellen in symmetrischen
Abständen über und quer durch die Achse des Transportbandes erfolgt, sodass sich die
Strahlenbündel überschneiden, um eine homogene Bestrahlung des zu behandelnden Gutes
zu sichern.
8. Gerät wie in irgendeinem Paar der Ansprüche 2, 3, 4, 5 und 6 oder 7.
9. Gerät wie in irgendeiner Dreiergruppe der Ansprüche 2, 3, 4, 5 und 6 oder 7.
10. Gerät wie in irgendeiner Vierergruppe der Ansprüche 2, 3, 4, 5 und 6 oder 7.
1. Appareil de chauffage à micro-ondes pour le traitement d'un produit se trouvant
à l'intérieur d'une enceinte sous vide, comprenant au moins une source d'énergie micro-ondes,
montée sur l'enceinte et émettant à l'intérieur de cette dernière, caractérisée par
une colonne comprenant un générateur micro-ondes, suivi par une section polarisant
l'onde circulairement, celle-ci suivie par une section de guide d'ondes en forme de
cône, comportant à la sortie une lentille diélectrique divergente, qui est conçue
de façon à étaler la radiation, afin de homogénéiser la densité de la puissance au
niveau du produit et de minimiser le risque d'aigrettage ou d'ionisation.
2. Appareil tel que décrit dans la Revendication 1, comprenant une pluralité de telles
sources.
3. Appareil tel que décrit dans la Revendication 1, dans lequel le produit se trouve
sur un tapis transporteur en mouvement, afin d'assurer un traitement "micro-ondes"
en continu.
4. Appareil tel que décrit dans la Revendication 1, dans lequel le polarisateur circulaire
est une section de guide d'ondes rectangulaire, comportant du matériel diélectrique
orienté diagonalement, afin de retarder différentiellement les deux composantes volumiques
de l'onde incidente et d'une longueur telle que le retardement différentiel cumulatif
est rr/2 radians, afin qu'il y ait également une quadrature du temps des deux composantes,
et causant ainsi une polarisation circulaire.
5. Appareil tel que décrit dans la Revendication 1, dans lequel la fenêtre de sortie
est un diélectrique d'épaisseur égale à la moitié de la longueur d'ondes à l'intérieur
de ce diélectrique.
6. Appareil tel que décrit dans la Revendication 1, dans lequel la lentille diélectrique
divergente est symétrique par rapport à l'axe de la colonne.
7. Appareil tel que décrit dans la Revendication 1, dans lequel la lentille diélectrique
divergente est asymétrique par rapport à l'axe de la colonne, quand l'irradiation
se fait par des sources symétriquement-espacées au-dessus et à travers l'axe du tapis
transporteur, de façon à ce que les faisceaux se recouvrent, afin d'assurer une irradiation
homogène du produit à traiter.
8. Appareil tel que décrit dans n'importe quelle paire des revendications 2, 3, 4,
5 et 6 ou 7.
9. Appareil tel que décrit dans n'importe quel triplet des revendications 2, 3, 4,
5 et 6 ou 7.
10. Appareil tel que décrit dans n'importe quel quadruplet des revendications 2, 3,
4, 5-et 6 ou 7.