(57) In an installation for manufacturing mastic asphalt, bitumen from a hopper (10) is
kept warm so that it remains sufficiently fluid to enable it to be easily handled
and is supplied to a primary mixer (16). Powdered limestone filler from a hopper (14)
is heated by means of heaters (18) and is added, together with unheated grit from
a hopper (12), to the mixer (16), via a weighing hopper (20). The constituent materials
are mixed without further heat input and are then discharged into a secondary mixer
(24) where further mixing occurs. The mixer (24) incorporates passages for the circulation
of a heat exchange medium which contacts the asphalt to cool it to a temperature suitable
for moulding. The heat extracted from the asphalt is returned to the heaters (18)
and re-used for heating the filler for asphalt produced subsequently. Asphalt is discharged
from the secondary mixer (24) into a plurality of moulds (52) through a pneumatically-actuated
gate (34) (see Fig. 3). The gate (34) is operated by a control system incorporating
a micro- processor. Each mould (52) is weighed after filling and a signal indicative
of the weight of the mould is fed to the micro- processor. The time for which the
gate (34) is opened is varied by the microprocessor in response to the measured weight
of the mould so as to render the weight of the asphalt blocks produced as consistent
as possible. Consequently, the blocks produced are of substantially uniform size and
can be formed, after unmoulding, into a self-supporting stack. The filled moulds (52)
are conveyed through a cooling tower (50) in which they pass through an array of spray
nozzles arranged to spray water onto the moulds (52) so that at least some of the
water impinging on the moulds (52) initially forms steam and thereby cools the asphalt.
Inside the cooling tower (50) the moulds (52) are conveyed along a vertical zig-zag
path so as to fit.
|
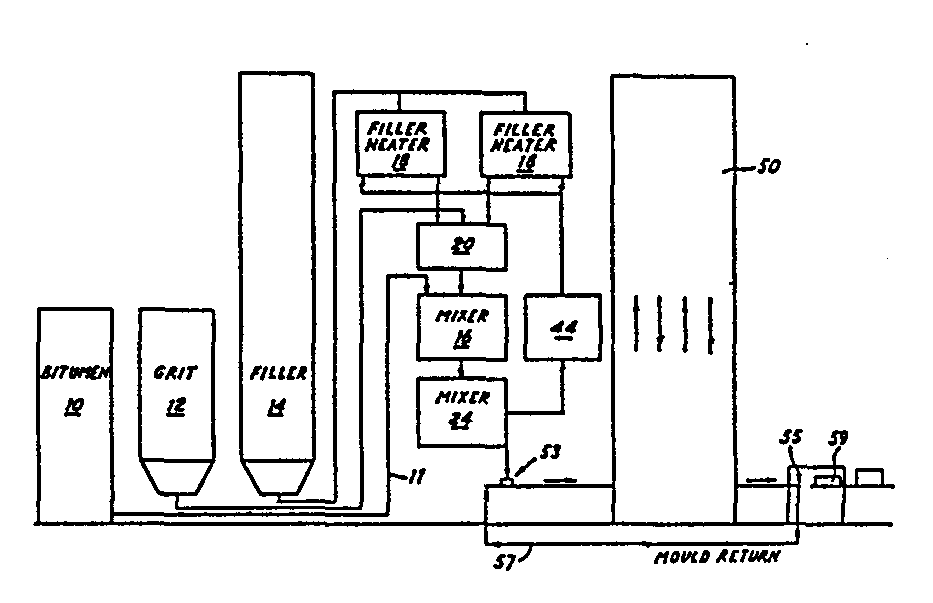
|