[0001] The present invention concerns a method of surface treating a workpiece, to provide
residual compressive stresses corresponding to a peening intensity of at least 0.1
mm N and a surface finish smoother than 40 AA by impacting the workpiece with spherical
shot particles having a hardness greater than the workpiece.
[0002] Shot peening is a manufacturing process wherein the surface of a workpiece is impacted
by particles or shot. An important use of peening is to generate a residual compressive
stress in surface of a metal workpiece, to improve fatigue resistance. Thus, localized
areas of tensile stress, phase transformations, machine and grinding marks, pits,
scratches, and the like, can be blended and effectively eliminated from acting as
stress concentration points.
[0003] Shot peening at low intensities, most often with glass beads, is used in the aircraft
gas turbine engine field to enhance the performance of disks, vanes, and blades which
are subject to high fatigue stresses. Characteristically, shot peening leaves a textured
surface owing to the slightly rounded depressions each particle impact produces.
[0004] Recently, it has been appreciated that the efficiency of gas turbines can be enhanced
by making the surface of peened compressor airfoils very smooth. Finishes of the order
of 15AA (Arithmetic Average; (10-
6 inch) 2.5 10-,
P mm, equal to Ra in ANSI B46-1-77) or better are desired. However, since airfoils
typically have contoured surfaces, they are difficult to easily polish without incurring
unacceptable change in dimension. Thus, abrasive polishing using a vibrating mass
media, following the peening step, has been preferred. But this, and any other surface
removal process, risks removal of too much of the necessary peened surface layer.
Also such processes tend to be time consuming. Therefore, there has been a need for
a simpler improved process.
[0005] In peening, shot size is usually chosen according to the size of the workpiece and
finish desired. There are many different choices, as indicated by the specification
SAE J444a (Society of Automotive Engineers). The nominal size of shot varies from
4.75 to 0.075 mm, and typically is cast steel or iron material. Glass beads in the
range of 1.4 to 0.038 mm nominal diameter are also commonly used. Commercial shot
is characterized by a relatively wide particle distribution about the mean or nominal
size. In addition, the shot tends to fragment during use, leading to the presence
of smaller jagged fragments. As a result, shot peening gives a textured surface finish
and the surface finish can vary over time with a given shot mass.
[0006] Large shot will tend to give a smoother surface finish than small shot, when obtaining
the same peening intensity. However, larger shot is undesirable because the time to
obtain a fully peened surface becomes considerably greater, and production rate is
lowered. Also, large shot has limited utility on many complex shaped parts where small
internal contours cannot be properly impacted. Thus, for production shot peening,
the smaller shot is preferred.
[0007] In addition to improved fatigue resistance, variations of peening processes have
been used in the past to provide various surface finishes on workpieces. For example,
US-A-937 180 discloses a method of obtaining a mottled effect on otherwise smooth
sheets. Hardened steel balls are dropped from a series of funnels onto an inclined
sheet workpiece placed below. US-A-3 705 511 describes a low penetration ball forming
process, for contouring aluminum sheet which is stretched across a convex die. Steel
balls in the range of 3-6 mm diameter fall by gravity from the edge of an inclined
surface, impacting the exposed convex surface of the sheet at about 5 m/sec. The workpiece
is translated under the shot stream for a time sufficient to permanently deform the
sheet (owing to the residual stresses) but insufficient to deform the sheet greater
than the die shape provides. When used for wing panels on aircraft, the contouring
process is followed by a conventional shot peening using smaller S230 (-0.7 mm) shot,
to obtain the requisite uniform residual stress for fatigue resistance.
[0008] The method of the present invention is characterized in that said impacting is carried
out with shot particles being infrangible, having a surface finish better than 30
AA and diameters lying in the range of 1-2.5 mm which are substantially uniform to
within at least ±0.5%.
[0009] An object of the invention is to produce parts having both a uniform residual surface
stress state and a smooth surface finish.
[0010] The method of the invention is based on the discovery of critical interdependencies
between shot size, energy, peening intensity, and surface finish. According to the
invention, a workpiece is simultaneously provided with compressive stresses corresponding
to a peening intensity of 0.1 mm N or greater, and a surface finish smoother than
40 AA by impacting it with spherical shot having substantially uniform diameter in
the range 1-2.5 mm, preferably 1.5-2 mm, traveling at a substantially uniform velocity.
The shot must be infrangible, so it maintains its sphericity in use, and have a surface
finish better than 30 AA. By substantially uniform diameter is meant that the shot
body will be comprised of particles having diameters within about ±0.05 mm, or uniform
within ±5%. This will provide unit masses uniform within about ±16%.
[0011] In the invention, the shot is impacted on the workpiece at a velocity less than 15
meter/sec, preferably in the range 1.4-12 m/s, more preferably in the range 2.5-7.8
m/s. The impact velocity will vary according to the desired peening intensity and
the diameter of the shot used, with higher velocities being associated with higher
intensity and smaller diameter. The impact velocity will be uniform within about ±4%
when the preferred method of acceleration, by force of gravity, is used. Resultant
unit impact energies will be uniform within about ±25%, in the range of 0.2x 10-
4 to 12x10-
4 J.
[0012] The final surface finish depends on the initial finish. If a titanium workpiece surface
has an initial finish of less than about 40 AA, the process is capable of producing
final finishes of 15 AA or better. When the workpiece is provided with a smoother
initial finish, final finishes down to 6 AA are attainable.
[0013] The workpiece finish is dependent on the peening intensity and diameter of shot.
For any given shot size, higher peening intensities are associated with poorer finishes.
However, at any given intensity a better finish is produced by a larger shot size.
As an example, to obtain better than 15 AA surface finish, the intensity of shot peening
must be less than about 0.30 mm N. Using 1.8 mm shot enables up to about 0.50 mm N.
As a corollary, at any given peening intensity the finish will be better for the larger
shot. As an example, for commonly encountered peening intensities in the range 0.20-0.30
mm N, shot significantly smaller than 1 mm will not be capable of producing a requisite
smooth surface of 15 AA, whereas shot greater than 2 mm gives a good finish, but without
advantage over 2 mm shot. Shot up to 2.5 mm is useful, nonetheless, when high peening
intensities are required. But associated with larger shot and especially that over
2.5 mm are long peening (saturation) times and low impact velocities which introduce
practical problems in controlling uniformity and obtaining good results on inside
radius contours.
[0014] When the shot is accelerated by gravity over drop height of 0.1-6 m, the uniform
velocities of the invention will be attained, together with shot which travels along
an essentially collimated path. Consequently a precision of shot peening and surface
finishing can be obtained which is economic and heretofore unknown.
[0015] The invention also improves the properties of overlay coatings, such as physical
vapor deposition (PVD) and plasma are sprayed coatings. For example, 0.13 mm thick
MCrAIY PVD and plasma coatings are peened with 1-2.5 mm shot to an intensity of 0.3-0.6
mm N and subsequently heat treated. Not only are leaders and voids in the coatings
healed to a degree greater than possible with the prior art air propelled glass bead
peening, but the coatings are substantially smoothed. PVD coatings of 60 AA finish
are improved to 25-35 AA while plasma coatings with 300 AA finish are improved to
finishes of less than 100 AA.
[0016] When the invention is applied to thin edged workpieces such as gas turbine airfoils,
the workpiece is manipulated with respect to the collimated shot stream in a manner
which avoids damage to the thin edges but at the same time produces the desired residual
compressive stress in the edge. The manipulating involves careful rotation of the
workpiece about an axis parallel to the edge so that only a portion of the edge is
presented to the collimated shot stream; direct impacts on the centerline of the edge
are avoided. For gas turbine blades, first one side and then the other side of the
airfoil is presented to the shot stream. When each side is presented the airfoil is
given an oscillatory rotation about its longitudinal axis to thereby finish both of
the opposing edges.
[0017] In order that the invention may be fully understood reference is made on the accompanying
drawings wherein:
Figure 1 graphically shows the relationship between saturation time and uniform shot
diameter.
Figure 2 graphically shows the relationship between peening intensity and saturation
time for different shot diameters.
Figure 3 graphically shows the relationship between the drop height and peening intensity
for different shot diameters.
Figure 4 graphically shows how shot peening energy transfer efficiency varies with
drop height and shot size.
Figure 5 graphically shows the drop height necessary to obtain a peening intensity
of 0.25 mm N, for different shot sizes.
Figure 6 graphically shows surface finishes which result from the use of different
size shot at different peening intensities, according to the starting finish.
Figure 7 graphically illustrates how surface finish varies with peening time for different
shot sizes.
Figure 8 graphically illustrates the interdependency of surface finish and peening
intensity for different sizes of shot.
Figure 9 graphically interrelates peening intensity, surface finish, and kinetic energy
of the shot, for different sizes of shot.
Figure 10 graphically shows the dependency of finish on shot size.
Figure 11 graphically shows the changing interrelationship between saturation time,
drop height, and surface finish, as a function of shot size.
Figure 12 shows a gas turbine blade positioned for shot peening while being rotationally
oscillated.
Figure 13 is an end view illustration of an airfoil section showing the degree of
rotation for each edge.
Figure 14 is a detail view of an edge of a workpiece, such as an edge of the workpieces
in Figures 12-13, showing the residual compressive stress achieved during peening.
[0018] The invention herein is described in terms of the finishing of a titanium alloy (Ti-6A1-4V
by weight) blade designed for use in the compressor section of a gas turbine engine.
The invention is also described in terms of attaining the following objectives: a
surface finish of better than 15 AA and a residual compressive stress intensity of
0.250.30 N, (in millimeters according to the Almen test). Both parameters are described
in more detail below. However, it will be understood that the invention will be useful
for finishing other workpieces and metals to other criteria; such as where the surface
finish may range up to 40 AA, and the intensity may range between 0.10-1.0 N.
[0019] In contrast to the shot peening as practiced in the prior art, the present invention
employs very uniform sized spherical shot, such as utilized in the construction of
ball bearings. The hardness of the shot should be greater than the hardness of the
metal being peened, to insure that the shot is not deformed during use. A preferred
material for peening Ti-6A1-4V (having a hardness of about Rc 40) is a carbon tool
steel, such as AISI C1013, which has been heat treated to a hardness in the range
of Rc 60. It is preferred that the shot be of a relatively high density material such
as steel. Other materials may be used, but such use will involve tradeoffs of increased
cost (for higher density hard materials) and less effectiveness (for lower cost and
lower density materials, such as ceramics). The shot material must be infrangible
to avoid generation of subsized particles during peening; the importance of this is
indicated below.
[0020] Most of the shot used in the prior art peening has been selected in accord with specification
SAE-J827 for iron or steel, and SAE-J1173 for glass beads and MIL-SPEC-S-13165B. Some
representative specification distributions of shot size are shown in Table 1 for the
SAE and MIL-SPEC materials. Also shown in the table are three types of shot, NL-10,
18, and 25, (nominally 1.0,.1.8 and 2.5 mm dia.) used in the present invention. Referring
now to the table, it will be seen that the prior art shot is characterized by relatively
wide distribution. For example, grade S550 contains diameters between 1.18 and 2 mm;
glass bead grade GB20 ranges in diameter between 0.125-0.300 mm. In contrast, the
shot of the present invention is seen to be uniform within a tolerance of a plus or
minus 0.05 mm. In the SAE and MIL-SPEC grades of shot it is expected that there is
a normal distribution which includes a certain number of fine shot particles. This
is evidenced by the lack of a screen specification for the 99-100% cumulative percentage.
In contrast, the grades of shot used in the invention, typified by the NL grades,
have 100 percent of the shot entirely within a specified narrow range.
[0021] In the practice of the invention, it is important that the shot be spherical. By
this is meant any characteristic shot particle should have a radius which does not
vary by more than about 2 percent. The sphericity requirements will be understood
within the context of the size uniformity requirements, elaborated upon further herein.
Irregular shaped shot can provide impacts which are of lower or greater intensity
than their spherical equivalent and may not provide the good results of the invention.
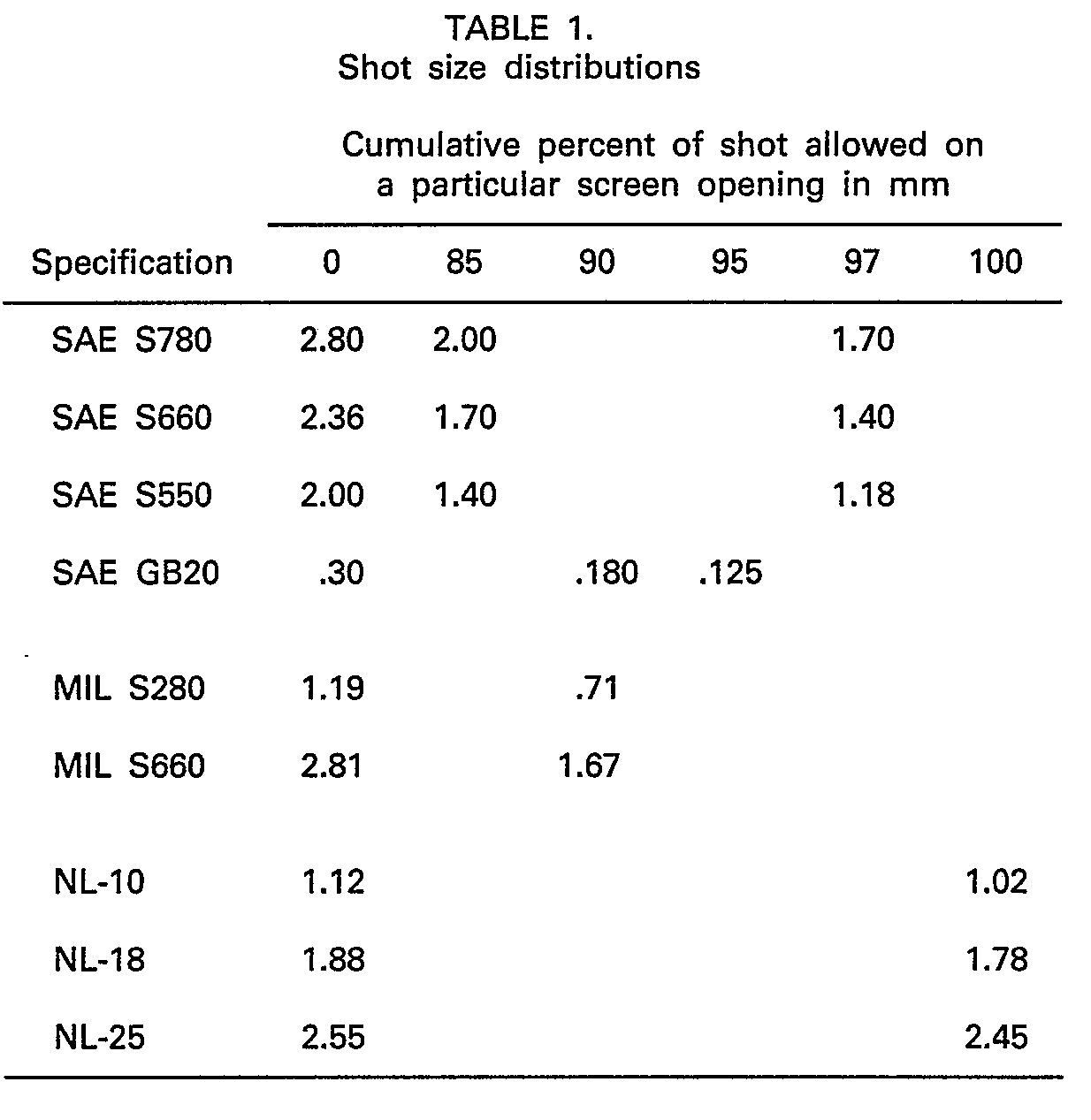
[0022] As indicated herein, the invention provides a smooth surface finish on the workpiece
being peened, better than 40 AA, and as low as 6 AA. To attain this, it is necessary
that the shot particles have at least a commensurate surface finish to that sought.
Preferably, the shot should have a finish of 6 AA or better. But, when less fine finish
is desired, somewhat poorer shot surface finishes may be usable, up to about 30 AA.
Heretofore there has been no particular requirement for shot surface finish in the
foregoing range. Somewhat irregular material, characteristic of atomized metal, has
been acceptable. The foregoing surface finish requirement in combination with the
sphericity requirement, precludes the use of shot containing fragments.
[0023] Shot particles must have substantially uniform energy when they impact the workpiece
surface. The preferred way to achieve this is to discharge the uniform sized shot
from a discharge gate (perforated plate) positioned above the workpiece, with a very
low uniform velocity. The shot is then allowed to fall by the force of gravity. This
will impart to all shot, regardless of size, a uniform acceleration and impact velocity.
The velocity at the time of impact will depend on the height of the gate above the
workpiece. The energy of a unit shot particle, E, will be determined by the relationship
E=0.5 mv
2 where m is the mass and v is the velocity at impact. As is well known the velocity
will be determined by the relationship v
2=2 gh, where h is the height, or the distance between the discharge gate and the workpiece
and g is the gravitational constant. Thus, the energy of a shot particle at the time
it hits the workpiece will be proportionate to h.
[0024] When a shot particle having sufficient velocity and mass impacts the workpiece, it
will cause plastic deformation and result in a residual compressive stress. The plastic
deformation will locally change the contour of the surface of the part. The effects
of shot peening insofar as residual compressive stresses are concerned are quantified
through intensity, I, measured with an Almen strip (SAE-J442 and AMS 2430). In this
method, a strip of SAE 1071 steel, productive of a reading in the Almen "N" range,
is subjected to shot peening while clamped in a flat holder. Upon removal from the
holder the residual compressive stresses imparted to the shot peened surface causes
the strip to curve. The Almen number is a measure of the height of a curvature of-the
strip; herein that number is referred to in millimeters.
[0025] To set forth the limits of the invention a multiplicity of tests were run using Almen
steel and AMS 4928 titanium (Ti-6A1-4V) test strips, and AMS 4928 titanium blades.
[0026] The intensity of shot peening, I, was measured using the aforementioned Almen steel
strip. The surface finish of the titaniums was measured using a standard surface finish
measuring system, such as a Bendix Model QEH Digital Profilometer and Amplimeter Peak
Counter (Bendix Automation & Measurement Division, Dayton, Ohio).
[0027] Saturation time, T, is a shot peening parameter which is a measure of the time at
which peening of the surface is deemed to be complete; it is determined with the use
of an Almen strip. Saturation time is defined as that time, which when doubled, causes
less than a 10% increase in measured intensity. Low saturation times are desired for
economic production.
[0028] Numerous experiments were conducted using gravity acceleration and different shot
sizes, the results of which are presented hereinafter. It will be seen that the data
variously suggest the preferred use of small and large shot sizes. However, when integrated,
a relatively narrow range of parameters is found to provide the desired unique combination
of surface finish and compressive stress.
Figure 1 shows the time to saturation at 0.025 N, for various diameter uniform size
shot flowing at equal mass rates. It is seen there is a considerable increase in time
with increasing shot sizes; e.g., a five-fold increase in diameter from 0.5 mm to
a 2.5 mm diameter increases the saturation time by eighteen-fold.
Figure 2 indicates the trend of saturation time with I, at constant mass flow. At
higher the time drops considerably. This can be attributed to the greater effectiveness
of higher energy or higher velocity shot in transferring energy to the workpiece.
Figure 3 indicates the relationship between drop height h, and the peening intensity
I. It is seen that as desired I increases, the necessary h increases greatly. Because
of its greater mass, a larger size shot will be preferred for higher intensity peening.
The Figure also indicates that disproportionately large increases in h are needed
with increasing I, suggesting a limiting situation insofar as residual stress effects
on the metal test strip are concerned.
[0029] In Figures 2 and 3 there is a lack of consistency in slopes for the three shot sizes.
The data for the 2.5 mm shot are limited, but believed valid. It is thought that the
changes in slopes reflect energy transfer phenomena and velocity effects which vary
in complex fashion as a function of I and shot diameter, and that there is a peaking
in the range between 1 and 2.5 mm.
[0030] Investigations were carried out on the energy transfer phenomena, and the results
illustrate significant differences between the shot sizes. The results will be seen
to be supported and correlated with the data in the paper "Residual Plastic Strains
Produced by Single and Repeated Spherical Impact", J. A. Pope and A. K. Mohamed, Journal
of Iron and Steel Institute, (1955) Vol. 180, pp. 285-297. The new data will be only
briefly touched on here.
[0031] Table 2 shows various parameters measured for three shot sizes. Among the data are
peening intensity, I(N); drop height, h; saturation time, T; total energy, E
t (the product of one-half the total mass flow per unit area, over time T, and the
square of the shot impact velocity); the efficiency, Eff, which is the ratio of the
impact energy, less the rebound energy, to the impact energy of a shot particle, and
it is a measure of the energy transferred to the workpiece by the shot; the energy
transferred, E
tr, which is the product of E
t and Eff; and the surface finish, SF.
[0032] Figure 4 shows the efficiency data from the table, plotted as a function of drop
height for different shot diameters.
[0033] Referring to the Table and Figure 4, it is seen that, (a) to achieve a particular
I, larger diameter shot requires higher E
t; (b) the larger diameter shot is more efficient in imparting its kinetic energy to
the workpiece; (c) efficiency falls off sharply when drop height falls below about
0.8 m for the 1-1.8 mm shot; (d) to obtain a certain peening intensity, there is need
for more energy to be transferred, E
tr, when using larger shot.
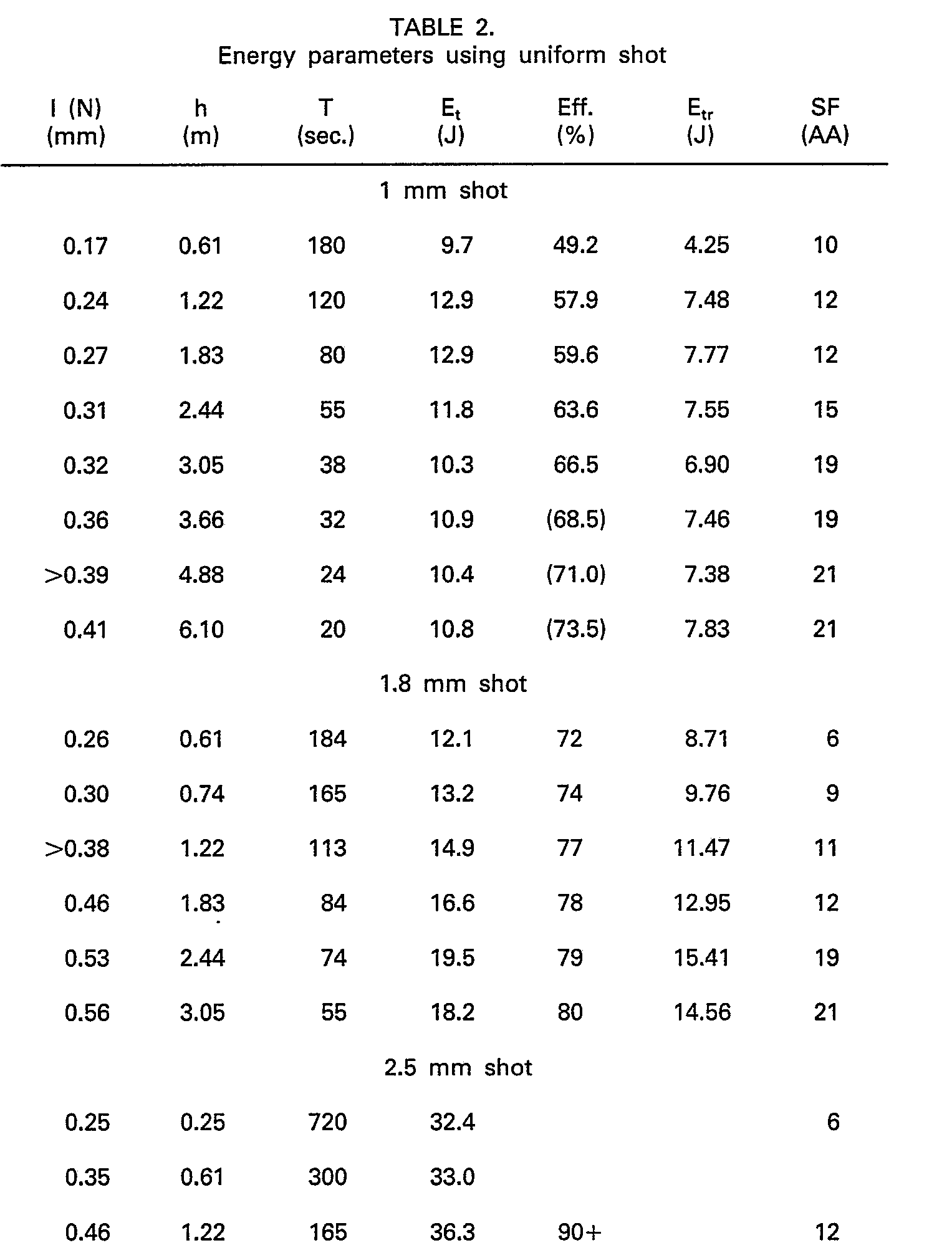
[0034] A full discussion of the hypotheses and ramifications relating to the foregoing observations
is beyond the present discussion. In summary, it can be concluded that (a) more energy
will be consumed when using large shot; and (b) low drop heights not only involve
the disadvantages mentioned elsewhere herein, but have associated with them low energy
transfer efficiencies. Both the foregoing suggest the desirability of using small
shot. û
[0035] Figure 5 illustrates the relationship between drop height and the shot size at I
of 0.25 N. The drop height decreases geometrically as shot diameter increases. From
Figure 5 it may be seen that when the shot diameter reaches 2.5-3 mm the permissabIe
h becomes small at about 0.25-0.40 m. Such small drop heights are to be avoided, since
associated with them are very low impact velocities, less than about 3 m/sec; these
make fluctuations in initial velocity more critical. Also, a contoured workpiece such
as an airfoil, and particularly one which is rotated or inclined with respect to the
shot streamline, may vary in height in space by as much as 50 mm. This will change
the effective drop height accordingly and cause unacceptable variations in the impact
velocity, with the result that I and finish will vary from point to point on the workpiece.
At the other extreme very small shot, such as is common in other shot peening, becomes
impractical from the standpoint of requiring infeasible vertical heights (and ultimately
encountering aerodynamic drag at high velocities). Substantial drop heights are impractical
simply because of the vertical height required in a building, and also because any
equipment in which is contemplated the use of different size shot must have the flexibility
to provide varying drop heights. When the usable range of drop height must be great,
equipment cost increases substantially.
[0036] Figure 6 illustrates the surface finish that is obtained at saturation time T, when
titanium alloy workpieces are subjected to different peening intensities with different
sized shot. For test pieces with initial finishes of 9 AA, it is seen that the larger
the diameter shot, the smoother the surface finish produced. For example, at 0.25
N a 1.8 mm shot will produce a surface finish of about 6 AA, whereas a 1 mm diameter
shot will produce a surface finish of about 12 AA. It is also seen from the Figure
that as the intensity is increased, the resultant roughness of the workpiece increases;
that is, there is poorer surface finish. See both and 1 and 1.8 mm data. This is understandable
because high intensities have associated with them greater forces and greater degrees
of surface deformations of the workpiece. Also shown in the Figure is the finish which
is produced by GB20 glass beads. At around 40 AA, it is considerably inferior to the
finish which can be obtained in the practice of the present invention. Figure 6 also
shows how 1 and 1.8 mm shot are effective in reducing the surface finish of a previously
rough surface. For example, a GB20 finished panel at 42 AA is provided with a surface
of about 15 AA using 1.8 mm shot at 0.25 N.
[0037] Figure 7 further illustrates the smoothing effect. Referring to curves A and B, there
is initially a roughening of initially smooth specimens, followed by smoothing at
T, and still further smoothing if peening is continued. For initially rough panels,
there is a progressive smoothing; at T, the preponderence of the smoothing which is
possible has been obtained, as curve C illustrates. Curve D illustrates the roughening
which the prior art glass bead peening provides, when saturation time is reached.
Curve D portrays the behavior of regular GB20 glass beads. Since within the typical
GB20 mass is a certain quantity of broken beads, continued peening time will produce
no change in finish. However, if specially selected (virgin, unused) glass beads are
used, there can be an improvement of surface finish to the range of 30 AA, if peening
is continued beyond saturation time.
[0038] While it is possible to improve the finish of parts, the final finish obtained will
be dependent on the initial workpiece finish. To obtain finishes of 15 AA or better,
with 1-2.5 mm dia shot, it is necessary for the initial workpiece finish to be less
than about 40 AA. In some workpieces there are considerable heavy machining marks,
waviness, and other gross effects which normally influence surface finish measurements.
Peening will not affect such gross defects. Therefore our surface finish statements
herein refer to surface roughness on a smaller scale, when the influences of the gross
defects have been subtracted out.
[0039] From the foregoing, it is indicated that peening with large size shot will only result
in smoothing to the desired degree if the peening is carried out for at least the
saturation time, T. Of course, there is an economic incentive to choose a shot which
gives the desired finish and I in the minimum time and the invention herein involves
the discovery of the critical parameters which provide these optimum parameters.
[0040] Figure 8 correlates the foregoing data, showing the important relation of finish
with peening intensity. It is seen that as I decreases, the surface finish improves.
It is seen that the S110 steel shot and the GB20 glass will not provide the desired
results. Only larger shot will produce a very smooth finish while simultaneously providing
significant I. The dashed box line on the Figure indicates the desired finish and
peening intensities for titanium airfoils. Shot in the range 1-2.5 mm dia. is usable.
But, it is seen that for a finish less than 15 AA, the 1 mm shot can only be used
up to an I of about 0.30 N. Although data was not obtained it appears evident that
shot substantially less than 1 mm, below 0.8 mm, will not be useful.
[0041] Figure 9 correlates the foregoing data with the input energy, E, which as pointed
out was proportionate to drop height, h. Using as an example goals of 0.30 N and less
than 15 AA, the Figure 9 curve is used by first entering at the desired intensity,
0.30 N. Moving to the right, the 1 mm curve is first intersected. Traveling from the
intersection vertically downward, the energy per unit shot particle needed to obtain
the desired I is indicated as 10-
4 J. (From this the height can be easily calculated). Traveling vertically upward,
another curve for 1 mm shot is intersected, and an ordinate location associated therewith
indicates a surface finish of about 15 AA will result from the E and shot diameter.
Treating the graph similarly for the same 0.30 N, but with 1.8 mm shot diameter shows
that higher unit shot energy level of 1.8×10* °J is required but that a better surface
finish of 8 AA will be obtained.
[0042] Figure 10 shows the relationship between shot size and surface finish, utilizing
the same data as in Figures 8 and 9. It is seen that when a shot size of greater than
about 2 mm is reached there is unexpectedly not a significant further increase in
surface finish.
[0043] Figure 11 is a summary of the prior data and graphically indicates the preferred
shot size. It is seen that between 2-2.5 mm diameter, surface finish does not improve,
while saturation time goes up substantially. The time disadvantage is more pronounced
for the lower I values and has associated with it low drop height. Thus, for I less
than 0.40 N, size should be less than 2 mm; for I above 0.40 N, shot size up to 2.5
mm may be used.
[0044] Small shot sizes, less than 1 mm, have associated with them, poor workpiece finishes
and in the case of high I, excessive drop heights. Thus, the shot size should be no
less than 1 mm, and preferably greater than 1.5 mm.
[0045] In summary it is seen that there is a range of shot size, of about 1.5-2 mm where
optimum results are obtained, and a range 1-2.5 mm which produces a superior combination
of surface finish and compressive stress, for particular intensities, compared to
the prior art.
[0046] Most of our concern herein has been with peening intensities of greater than 0.25
N, however, lesser intensities will be on occasion found useful, down to about 0.10
N. They may be provided in the practice of the invention as reference to the figures
and limited extrapolation will show. To achieve low intensities, shot diameters from
the smaller end of the range will be selected, since required velocities and drop
heights become undesirably small for shot in the larger diameter end of the range.
[0047] The 1-2.5 mm steel shot particles used in our experiments had a diameter tolerance
of ±0.05 mm and a specific gravity of about 7.8. Thus, the diameter was uniform within
±2.5%. The nominal particle mass ranged between 4-64 x 10-
3 gm; and the mass at a given diameter varied between ±6-15%, the smaller percentage
being associated with the larger shot size.
[0048] The range of velocity which is usable in the invention is dependent both on the size
of the shot (necessary to achieve the energy which produces the desired peening intensity)
and practical limits relating to how the shot is accelerated. While we conceive of
other means of accelerating shot, only gravity acceleration appears presently to have
both simplicity and consistency in providing uniform velocity. Therefore our practical
limits are related to the drop heights which are feasible. The drop height should
be more than 0.1 m, very preferably greater than 0.3 m, and most preferably in the
range 0.6-3 m. When the drop height becomes too low, variations in the placement or
controlled movement of the airfoil may significantly affect impact velocity, and thereby
the precision of peening required to achieve the objects of the invention. Heights
beyond 6 m are considered by us to be excessive and impractical, although they are
feasible. For the 0.1-6 m drop heights, impact velocity will range over 1.4-12 m/sec;
for 0.3-3 m drop; velocity will be 2.5-7.8 m/sec in gravity acceleration using the
apparatus described in the referenced applications, impact velocities were uniform
within ±4%.
[0049] When obtaining 0.1-0.6 N intensity, and smoother than 30 AA finish, and using 1-2.5
mm shot, Figure 9 shows the unit shot energy will range from approximately 0.2×10
-4 J to 12x10-
4J. For the use of the method in peening titanium airfoils to 0.25-0.30 N and less
than 15 AA finish, the unit energy range will be about 0.6x10-
4 to 3x10-
4J.
[0050] We have indicated the criticality of the peening parameters on the results obtained.
The mass and velocity, must be substantially uniform, within the context of the foregoing
tolerances. The mass and velocity tolerances are cumulative in their effect on energy
and peening intensity. The permissible tolerance for the energy level within a shot
stream depends on the relationship between the desired intensity and finish which
has been presented herein, and the requirements of the particular application. Generally,
in most applications it is preferred that the energy level be held within about 15
percent for best results and dependable saturation times; with the above presented
mass tolerances of ±6-15% and velocity tolerances of ±4% (meaning v
2 is ±16%), a statistical summation indicates energy tolerance is about ±25%, and this
has provided good results.
[0051] The foregoing tolerances should not be taken as absolute since they are approximations
based on the extensive but not entirely complete work which has been done. Obviously,
a closer tolerance in one parameter enables a lower tolerance in a related parameter.
Within the context of the prior art, the foregoing peening parameters tolerances given
may justly be characterized as substantially uniform. Reference to the specifications
for shot used in the prior art will show that the shot particle masses vary much more
than a hundred percent and with the mechanical and fluid acceleration, there are great
variations in velocity as well. Almost needless to say, the resultant energy varies
even more.
[0052] The practice of our invention calls for substantially uniform shot velocities. Uniform
velocities may be attained using gravity acceleration. However, any mode of propelling
the shot may be used, so long as the criteria of the invention are met. Also, the
best mode involves peening in dry air. In special circumstances, the invention may
be carried out as well in other environments, such as in liquids or vapors.
[0053] Since the invention provides for the use of substantially uniform size shot, it would
at first appear that the use of two or more different sizes of shot would not conform
with the invention. It is true that the preponderance of the shot must be substantially
uniform at the selected size to effectively practice the invention. And inclusion
of any significant quantity of shot which is substantially larger than-outside the
tolerance of-the selected size will not be in accord. However, the presence of some
smaller shot is contemplated as lying within the scope of the invention when such
inclusion may be desirable for secondary purposes or is without specific purpose.
The reasoning behind this is as follows.
[0054] The time to saturation is the measure of time upon which the desired residual stress
accumulates. This in turn is a direct function of the number of impacts and energy
of each impact which the surface receives. Therefore, decreasing the mass flow rate
will increase the saturation time in inverse proportion to the change. From the data
presented, it will be understood that using gravity accelerated shot, all the shot
in a mixed size mass will have the same velocity. The energy will be less for the
smaller shot particles and the intensity produced therefrom will be less. Accordingly,
it can be seen that if the shot size was mixed, for example if 1.8 and 1 mm shot were
mixed together, the time to saturation will be longer than the time for either of
the independent shot sizes. Saturation time and intensity will be controlled only
by the larger shot size, the mass flow of which would be effectively reduced.
[0055] Thus, the presence of smaller shot will merely serve to extend the saturation time.
Where the small shot hits, the I will be lower than that desired, which will be that
provided by the larger size shot. In a mixed size shot mass, at best the presence
of small shot will be benign. At worst, it will be impelled with unwanted excess energy,
as when a large shot drives a small shot against the workpiece, and locally causes
a poor surface finish and excess intensity.
[0056] Other shot material than the steel of our best embodiment may be used. The shot must
of a material harder than the workpiece, and elastic in its impacts with the workpiece
and apparatus. It must be substantially infrangible, that is, significant amounts
cannot fragment during impact with the workpiece or pieces of the apparatus. The good
results we obtained are based on the relationships between energy and diameter. Thus
it would appear that, for example, a low density material impelled at a given velocity
may produce the same results as a higher density material with the same energy and
a lower velocity. While this is true qualitatively, there is probably a velocity effect
which we cannot presently fully delineate, and low and high density particles of equal
energy may not produce comparable results. Evidently, absolute velocity level is influential.
This is suggested by the data in Table 2, when comparing 1 and 1.8 mm shot. When both
sizes are dropped from 1.22 m height, they yield essentially the same surface finish
of about 11-12 AA. Compare the data for 1 mm at 0.24 N and 1.8 mm at 6.38 N in Table
2. When the 1 mm shot is dropped from 4.88 m, it produces about the same intensity
as 1.8 mm shot for 1.22 mm. See Figure 3 and Table 2. However, the 1 mm shot under
such conditions produces a surface finish of 21 AA. Since lower density media by its
nature would have to be used at higher velocities, this data suggests that it may
have limited utility, and heavier materials with equal or greater density to steel
are preferred.
[0057] As indicated the bulk of our work was done with steel test specimens, and Ti-6A1-4V
titanium alloy workpieces and test specimens. The results herein reflect the materials
used, but we believe that analogous results will be obtained on other materials having
like properties. In this we include generally titanium alloys and ferrous alloys,
as well as nickel alloys, and other materials which have been peening by prior art
processes.
[0058] The invention is also useful in the finishing of various kinds of coatings and surface
depositions, as illustrated by an MCrAIY coating on a nickel super-alloy gas turbine
blade. Preferably the coating is deposited by physical vapor deposition (PVD) or plasma
spraying. MCrAIY coatings are described in U.S. Patents 3,542,530, 3,676,085, 3,918,139
and 3,928,026.
[0059] When PVD coatings are deposited, they frequently may have defects which are generally
characterized as leaders. These are voids which extend transverse to the surface of
the substrate, along the direction of the multiplicity of columnar grains which characterizes
the coating. A typical coating will be about 0.13 mm thick and it will have nominally
the same surface finish as the substrate. In accord with the invention the coating
is preferably peened using 1.8 mm diameter hardened spherical steel shot using substantially
the same practices as above. For an MCrAIY coating the shot velocity will lie in the
range of 4.7-6.3 meters per second and the shot peening intensity I will be in the
range of 0.47±0.5 mm N. The shot will impart plastic deformation to the coating and
thereby close the discontinuous leader regions in the coating. The coating will be
left with residual elastic mechanical stresses and the coating will be smooth. After
shot peening the coating is heated at a temperature of 1040±14°C in an inert atmosphere
such as a vacuum. After this the density will be found to be almost 100% of the solid
metal value and the surface finish will be of the order of 25-35 AA, compared to a
typical 50-60 AA of the coating before peening.
[0060] A coating prepared in the foregoing manner will be contrasted with one prepared according
to the techniques of the prior art. For example, if the coating is peened according
to the prior art with glass beads of SAE J1173 designation GB20 (about 0.2-0.3 mm
diameter) using conventional air propulsion, the peening intensity will be about 0.47
N. It will be found that the coating defects have been closed to a lesser depth than
with the invention and the surface finish of the coating will only be improved to
about 40-50 AA. This correlates with measurements of the residual compressive stress
of titanium alloy test panels using x-ray diffraction. The residual stress state for
the larger steel shot of the invention will extend deeper into the workpiece surface.
[0061] The invention may also be used with plasma spray coatings. Characteristically these
coatings have porosity defects more or less uniformly dispersed through the coating.
An MCrAIY coating will have a density of about 6.77 grams per cc, about 94% of the
theoretical density of the solid alloy. The finish of the coating typically is of
the order of 250-370 AA. When a coating is peened in the same manner as described
above, it will be found that there will be mechanical closure of many of the defects.
The surface of the coating will be significantly smoothed to a finish of about 60-80
AA. Heat treating at 1065-1093°C for four hours in hydrogen or vacuum will somewhat
further improve the density of the coating. Measurements show a density of about 7.14
grams per cc or 99% of theoretical is achievable. The result is contrasted with a
coating peened using the GB20 glass shot mentioned above. An inferior surface finish
of about 100-150 AA will be produced and the coating will not be as dense.
[0062] In applying the invention to MCrAIY coatings on nickel alloy turbine blades it is
found that chipping at the trailing edge is much less of a problem compared to that
which exists with the prior art glass bead peening. Because the shot is predictably
traveling uniformly along a collimated shot stream line, it is relatively easy to
position the airfoil so that direct impacts on the edge are avoided.
[0063] For the peening of overlay coatings on metal substrates, we have found that the shot
size should be of a diameter of 1 mm or greater, preferably between 1-2.5 mm and more
preferably between 1.5-2 mm. The shot should be uniform within ±0.05 mm. For the typical
0.13 mm thick coating used on gas turbine airfoils, the shot peening intensity should
be greater than 0.3 N. Up to 0.6 N will be useful. When gravity is used to accelerate
the shot, the drop heights should be greater than 0.3 m but less than 6 m, and preferably
between 0.5 and 2.0 m.
[0064] Special care has to be given in peening workpieces with thin edges, as exemplified
by gas turbine airfoils. A desired residual compressive stress layer is desired at
the edge, but there must not be gross deformation of the edge. As shown in Figure
12 a gas turbine blade 20 has a longitudinal axis 30 and a cross section normal to
the axis which has the characteristic cambered shape of an airfoil. The blade has
a leading edge 22 and a typically thinner trailing edge 24. To peen such a workpiece
it is mounted in a holder 32 adapted to rotate it about its longitudinal axis through
a prescribed arc M while the longitudinal axis is held nominally in a plane parallel
to the strain line 36 of the stream of shot 34. Shot impacts the surface 28. The workpiece
is rotated from a mean position to a certain maximum oblique angle to the shot stream
line for each edge as shown in Figure 13. Line 44 is the nominal chord of the airfoil
and its position normal to the shot streamline 36 is a reference position for rotation.
Lines 41a a and 40a are the center lines for the leading and trailing edges. Referring
to the leading edge 22 the airfoil is rotated through angle B from its reference position
to second reference position 71 where the center line 41 a is normal to the shot streamline.
From position 71 it is then moved through angle +C" to position 73 and then back to
position 71, repetitively to peen the upper half of the edge. To peen the other side
of the edge the airfoil is turned over on its holder and moved in analogous fashion.
Similarly, the trailing edge 24 is peened by first oscillating it through angle +C'
and then turning the part over and oscillating it through angle -C'. As should be
evident both the leading and trailing edge are peened when one side is presented to
the shot stream, as the workpiece is first rotated to position 73 and then rotated
to position 72.
[0065] As shown in Figure 14 shot traveling along lines 52, 54, 56 is thus caused to hit
the workpiece surface 26d at oblique angles P to the tangent 53 to the center line
41 d of an edge 22d but never hits normal to the tangent. Compressive stresses illustrated
by the shading 50d extends to a depth 58; these stresses are the cumulative effect
of the stress patterns 152, 154 created by individual shot impacts 52, 54, etc. The
angle C is always less than 90° and is selected so that the depth of peening D along
the center line is that desired. Generally the depth D will be sought to be 50-100
percent of the depth 58 of stressing achieved on the opposing airfoil sides 26d, 28d.
[0066] The approximate angle of rotation C for a particular workpiece edge is calculable
from the edge radius R, the depth of stressing D desired at the center line of the
edge, and the depth q of stressing which the 45° angle shot impacts produce in the
workpiece material at a reference location, such as at a point 54 in Figure 14. Namely,

[0067] As an example, for a part with an edge radius of 0.38 mm, steel shot of 1.8 mm diameter
produces a stress intensity concentration factor of 1.45. The peening intensity I
on the curved edge surface at 90° to the tangent is 0.36 N and the depth of stressing
is 0.18 mm. For a 45° impact the intensity will be about 0.25 N and the depth of the
stressing q will be 0.13 mm. Utilizing the formula above, the angle rotation C will
be found to be 33.5°. The preferred rate of oscillation in work thus far has been
20 cycles/minute where the peening time is 2-3 minutes.
1. Verfahren zur Oberflächenbehandlung eines Werkstückes, um Restdruckspannungen zu
schaffen, die einer Kugelstrahlintensität von wenigstens 0,1 mm N und einem Oberflächenfinish,
das glatter ist als ein arithmetischer Mittenrauhwert von 1,02 um (40 AA), entsprechen,
durch Beaufschlagen des Werkstückes mit kugelförmigen Schrotteilchen, welche eine
Härte haben, die größer als die des Werkstücks ist, dadurch gekennzeichnet, daß das
Beaufschlagen mit Schrotteilchen ausgeführt wird, die unzerbrechlich sind und ein
Oberflächenfinish, welches besser als ein artihmetischer Mittenrauhwert von 0,76 um
(30 AA) ist, und Durchmesser haben, welche in dem Bereich von 1-2,5 mm liegen, die
innerhalb von wenigstens ±0,5 % im wesentlichen gleichmäßig sind.
2. Verfahren nach Anspruch 1, dadurch gekennzeichnet, daß die Schrotteilchenmassen
innerhalb von ±16 % gleichmäßig sind.
3. Verfahren nach Anspruch 1, dadurch gekennzeichnet, daß die Schrotteilchen eine
Geschwindigkeit in dem Bereich von 1,4-12 Meter pro Sekunde haben, gleichmäßig innerhalb
von ±4 %.
4. Verfahren nach Anspruch 3, dadurch gekennzeichnet, daß die Geschwindigkeit in dem
Bereich von 2,5-7,8 m/s liegt.
5. Verfahren nach Anspruch 1, dadurch gekennzeichnet, daß die Schrotteilchendurchmesser
in dem Bereich 1,5-2 mm liegen.
6. Verfahren nach Anspruch 1, 2, 3, 4 oder 5, dadurch gekennzeichnet, daß die Kugelstrahlintensität
in dem Bereich 0,1-1,0 mm N liegt, gemessen nach der Almen-Methode.
7. Verfahren nach Anspruch 6, dadurch gekennzeichnet, daß die Schrotteilchen Einheitsenergien
in dem Bereich von 0,2×10-4 bis 12x10-4 J haben.
8. Verfahren nach Anspruch 6, dadurch gekennzeichnet, daß die Schrotteilchen durch
Schwerkraft auf einer Strecke von 0,3-6 m beschleunigt werden.
9. Verfahren nach Anspruch 5, dadurch gekennzeichnet, daß die Schrotteilchen eine
Kugelstrahlintensität in dem Bereich von 0,20-0,50 mm N und ein Oberflächenfinish,
das wenigstens einem arithmetischen Mittenrauhwert von 0,38 pm (15 AA) entspricht,
bei einem Titanlegierungswerkstück haben, wobei die mittlere Schroteinheitsenergie
in dem Bereich von 0,6×10-4 bis 3x10-4 J liegt.
10. Verfahren nach Anspruch 9, dadurch gekennzeichnet, daß das Schrot gehärteter Stahl
ist.
11. Verfahren nach Anspruch 1, gekennzeichnet durch Fertigbearbeiten des Werkstückes
bis zu einem Oberflächenfinish, das einem arithmetischen Mittenrauhwert von weniger
als 1,02 um (40 AA) entspricht, vor dem Kugelstrahlen, um ein Oberflächenfinish zu
schaffen, das nach dem Kugelstrahlen einem arithmetischen Mittenrauhwert von wenigstens
etwa 0,38 Ilm (15 AA) entspricht.
12. Verfahren nach Anspruch 1, dadurch gekennzeichnet, daß auf das Werkstück ein Decküberzug
aufgebracht worden ist, gekennzeichnet durch Beaufschlagen der Werkstücküberzugsoberfläche
mit Schrot, das eine Kugelstrahlintensität von 0,3-0,6 mm N hat.
13. Verfahren nach Anspruch 12, gekennzeichnet durch Wärmebehandeln des Überzugs im
Anschluß an den Schritt des Beaufschlagens der Oberfläche mit Schrotteilchen.
14. Verfahren nach Anspruch 13, dadurch gekennzeichnet, daß der Überzug vom MCrAIY-Typ
ist, gekennzeichnet durch Wärmebehandeln bei etwa 1040°C.
15. Verfahren nach Anspruch 1, dadurch gekennzeichnet, daß sich das Schrot auf einer
im wesentlichen kollimierten Bahn bewegt und daß das Werkstück einen dünnen abgerundeten
Rand hat, der parallel zu einer Werkstücklängsachse liegt, wobei der Rand eine Mittellinie
und eine dazu normale Oberflächentangente hat, gekennzeichnet durch Drehen des Werkstückes
um eine Längsachse um einen Winkel, der ausreicht, um einen Teil des Randes dem Schrotstrom
darzubieten, aber nicht ausreicht, um Aufschläge normal zu der Tangente hervorzurufen.
16. Verfahren nach Anspruch 15, wobei das Werkstück zwei entgegengesetzte Ränder hat,
gekennzeichnet durch Hin- und Herdrehen, um Teile jedes Randes der Schrotstromlinie
abwechselnd darzubieten.
1. Procédé de traitement de la surface d'une pièce; en vue de réaliser des contraintes
compressives résiduelles corréspondant à une intensité de grenaillage d'au moins 0,1
mm N et une finition de surface lisse supérieure à 40 AA par impacts sur la pièce
de particules de grenaille sphériques d'une durété supérieure à celle de la pièce,
caractérisé en ce que les impacts sont, obtenus à l'aide de particules de grenaille
infrangibles, présentant une finition de surface supérieure à 30 AA et des diamètres
se situant entre 1 et 2,5 mm qui sont sensiblement uniformes dans des limites d'au
moins+ou -0,5%.
2. Procédé selon la revendication 1, caractérisé en ce que les masses de particules
de grenaille sont uniformes dans des limites de + ou -16%.
3. Procédé selon la revendication 1, caractérisé en ce que les particules de grenaille
ont une vélocité se situant entre 1,4 et 12 mètres par second, vitesse qui est uniforme
dans des limites de + ou -4%.
4. Procédé selon la revendication 3, caractérisé en ce que la vitesse se situe entre
2,5 et 7,8 m/second.
5. Procédé selon la revendication 1, caractérisé en ce que les diamètres des particules
de grenaille se situent entre 1,5 et 2 mm.
6. Procédé selon la revendication 1,2,3,4, ou 5, caractérisé en ce que l'intensité
de grenaillage se situe entre 0,1 et 1,0 mm N, mesure effectué par la méthode d'Almen.
7. Procédé selon la revendication 6, caractérisé en ce que les particules de grenaille
présentent des énergies unitaires se situant entre 0,2x 10-4 et 12x10-4 J.
8. Procédé selon la revendication 6, caractérisé en ce que les particules de grenaille
sont accélérées par gravité sur une distance de 0,3―6 m.
9. Procédé selon la revendication 5, caractérisé en outre en ce que les particules
de grenaille ont une intensité de grenaillage se situant entre 0,20 et 0,50 mm N et
une finition de surface d'au moins 15 AA sur une pièce en alliage de titane, l'énergie
moyenne unitaire de la grenaille se situant entre 0,6×10-4 et 3x10-4 J.
10. Procédé selon la revendication 9, caractérisé en outre en ce que la grenaille
est en acier durci.
11. Procédé selon la revendication 1, caractérisé en outre en ce qu'il consiste à
finir la pièce avec une finition de surface inférieure à 40 AA avant grenaillage afin
d'obtenir une finition de surface d'au moins 15 AA environ après grenaillage.
12. Procédé selon la revendication 1, caractérisé en ce que la pièce comporte une
couche de recouvrement, caractérisée en ce que la surface de la couche de la pièce
est soumise à des impacts par des particules de grenaille d'une intensité de grenaillage
entre 0,3 et 0,6 mm N.
13. Procédé selon la revendication 13, caractérisé par un traitement thermique de
la couche après l'étape qui consiste à soumettre la surface des impacts de particules
de grenaille.
14. Procédé selon la revendication 13, caractérisé en ce que la couche est du type
MCrAIY caractérisée par un traitement thermique d'environ 1040°C.
15. Procédé selon la revendication 1, caractérisé en ce que les particules de grenaille
suivent un trajet sensiblement collimaté et en ce que la pièce présente un bord arrondi
s'étendant parallèlement à un axe longitudinal de la pièce, le bord ayant une ligne
médiane et une surface tangente normalement à celle-ci, caractérisé en ce qu'il consiste
à faire tourner la pièce autour de son axe longitudinal d'un angle suffisant pour
présenter une portion du bord au courant de particules de grenaille et insuffisant
pour provoquer des impacts normaux à ladite tangente.
16. Procédé selon la revendication 15, dans lequel la pièce présente deux bords opposés,
caractérisé par une rotation oscillatoire pour présenter des portions de chaque bord
en alternance à la ligne de courant de grenaille.