[0001] The present invention relates to an oxygenated, high-octane-number composition for
fuel, and to a method for its preparation.
[0002] It is known that methanol has interesting high-octane-rating characteristics, such
that the addition thereof to the gasolines is one of the suggested means to cope with
the lead-alkyls reductions. Such a use shows however a severe drawback in that methanol,
when admixed with hydrocarbons, if the resulting mixtures absorb even very minor amounts
of water (500-700 ppm), undergoes phase separations.
[0003] Because of its hydrophilic character, when two phases separate from each other, methanol
tends to concentrate in the aqueous phase, thus depriving gasoline of its antiknock-value
improving contribution. It is clear that such a behaviour jeopardizes the use of methanol
in the field of fuels.
[0004] An indirect way of adding methanol, with no problems, to a gasoline, consists in
reacting it with isobutene, or with other branched C₅-C₇ olefins, yielding high antiknock-rating
ethers which, once that they have been admixed with gasolines, do not show any longer
phenomena of instability in the presence of water. Such a procedure allows however
small methanol amounts, practically only the stoichiometric amount, to be added, which
means 57 parts by weight per each 100 parts of reacted isobutene, such parts decreasing
then to 46, if on the contrary a C₅ olefin, such as the isoamylenes, is used.
[0005] It is known that the presence of higher alcohols endows methanol/gasoline mixtures
with improved water stability, such that a preferred form of use of methanol in gasolines
is precisely that carried out in the presence of a higher alcohol - e.g., a mixture
containing equal parts by weight of methanol and tert-butyl alcohol (TBA). Inasmuch
as TBA can be obtained by isobutene hydration, it is logical to observe how by that
way introducing 132 parts of methanol per each 100 parts of reacted isobutene becomes
possible, which is more than the double of the amount which one succeeds in introducing
by the etherifying of a same amount of olefins.
[0006] However, the hydration reaction shows, relatively to the etherifying reaction, a
more unfavourable thermodynamics, so that, whilst it is possible to accomplish, in
the etherifying step, high (≧99%) isobutene conversions, reaching in the hydration
step a conversion of 80% is practically impossible, unless extremely complex process
schemes are used.
[0007] Obviously, such a fact lowers the yields and, by not completely removing isobutene
from the used olefinic fraction, it endangers the subsequent use thereof as the starting
material for the recovery of butene-1.
[0008] Another disadvantageous characteristic of the hydration is the mutual immiscibility
of the reactants (H₂O-olefins) with each other, which makes it necessary to use a
third component, acting as a solvent.
[0009] As regards this latter disadvantage, it should be observed that the third component
causes serious technical problems as for its separation and recycle, so that the production
of TBA is presently carried out on a commercial scale via the reduction of tert-butyl
hydro peroxide in propylene oxide syntheses.
[0010] It has been now surprisingly found a high-octane-rating composition for fuels having,
as its components, methanol, TBA and MTBE, wherein the components are comprised within
the following percent ranges:
methanol: 30-45%, preferably 43.1% by weight;
TBA : 30-45%, preferably 43.1% by weight;
MTBE : 5-20%, preferably 13.8% by weight;
and a method for preparing it has been surprisigly found, by which the drawbacks of
the prior art are overcome.
[0011] The high-octane-number composition for fuel according to the invention is such that
it contains, in its preferred fo rm, even
240 parts by weight of oxygen-contaning high-octane-number components per each 100
parts of reacted isobutene, as compared to the 155 parts which can be obtained by
means of the complete conversion of isobutene into MTBE.
[0012] The high-octane-number composition in accordance with the instant invention shows
considerable advantages of stability as compared to methanol alone, and also relatively
to methanol-TBA mixtures, as it shall be set forth in particular in Example 2.
[0013] The composition according to the invention is added to the gasolines in amounts comprised
within the range of from 3 to 30% by weight.
[0014] The method according to the present invention comprises submitting a butadiene-free
C₄ charge, containing a percentage of isobutene of from 10 to 55%, to one or more
sequential hydration treatment(s) with water, in the presence of an acidic cationic
resin, in particular based on sulphonated styrene-divinylbenzene of Amberlyst 15 type,
thus partly converting isobutene into TBA, separating TBA from the mixture of the
other components, containing the residual isobutene, submitting the residual isobutene
in said mixture to an etherifying treatment with an excess of methanol relatively
to the stoichiometric amount, to the purpose of converting it into MTBE in the presence
of an acidic cationic resin, in particular based on a sulphonated styrene-divinylbenzene
of Amberlyst 15 type, and is characterized in that the reaction mixture (isobutene
and water) is homogenised by means of a solvent selected from either pure or substantially
pure TBA, and mixtures of TBA and water (water is at a concentration comprised within
the range of from 0.1 to 18%), isobutene being converted into TBA at a temperature
comprised within the range of from 40 to 90°C, by a percentage of from 75 to 80%,
and the MTBE-containing mixture is submitted to fractionation, a mixture being separated
of MTBE and methanol with possible minor traces of TBA, which is admixed with pure
TBA up to the above-said concentrations.
[0015] The methanol excess is of from 8 to 15 times as the stoichiometric amount, as referred
to the residual isobutene after the hydration.
[0016] The method of the present invention can be carried out in particular as illustrated
in the following Example 1, which is not to be understood as being limitative of the
invention. In it, the reaction of TBA formation is carried out as a process of two
steps in series, and the solvent is constituted by a mixture of TBA and water, which
is obtained as an intermediate fraction from the TBA separation step.
[0017] It is clear that changes can be supplied to the process pattern, without going out
of the scope of the invention.
Example 1
[0018] To 100 parts by weight of an olefinic chargecontaining 50% by weight of isobutene
(stream 1, see herewith attached figure), added are 145.82 parts by weight of stream
6, which is a recycle stream, and is formed by 129.78 parts of TBA and 16.04 parts
of water. The resulting mixture is delivered, at an LHSV = 2, to reactor 10, containing
an ion-exchange resin in the acidic form (Amberlyst 15), operating at the temperature
of 60°C.
[0019] The ratios between water, hydrocarbons and TBA are so selected, that the mixture
is in single phase. In reactor 10, TBA is formed, from isobutene and water. The reaction
product (stream 2) has the following composition:
Inert butenes 50
Isobutene 20.70
TBA 168.48
H₂O 6.64
The isobutene conversion in 10 is of 58.6%.
[0020] To the stream 2, 13.03 parts of demineralized water, or anyway of water free from
cations or organic bases, are added; the resulting mixture (stream 3), which is perfectly
homogeneous, is passed at a space velocity = 1.6 over reactor 11 containing an ion-exchange
resin in the acidic form (Amberlyst 15), and operating at 60°C. The resulting product
(stream 4) has the following compositions:
Inert butenes 50
Isobutene 10.64
TBA 181.76
H₂O 16.44
[0021] The total conversion of isobutene is of 78.7%, with a nearly absolute selectivity
to TBA.
[0022] The stream 4 is sent to the fractionation column 12.
[0023] From column 12 three streams are collected:
- a overhead stream (stream 5), 61.04 parts, constituted by 50 parts of linear butenes,
10.64 parts of isobutene and 0.40 parts of H₂O. Water decants nearly totally as a
separated phase, so that the stream 5 contains, after the phase separation, only 0.06
parts thereof.
- a side stream (stream 6), which constitutes the recycle stream, to be admixed with
stream 1.
- a bottom stream, constituted by 51.98 parts of practically anhydrous TBA.
[0024] To the stream 5, after water being separated, 59.48 parts of methanol (16) are added,
and the resulting mixture is passed over reactor 13 at an LHSV = 5, and at a temperature
of 45°C.
[0025] The reaction product (stream 8) has the following composition:
Inert butenes 50
Isobutene 0.08
Methanol 53.46
MTBE 16.57
TBA 0.01
H₂O 0.05
[0026] The total isobutene conversion is thus higher than 99.8%.
[0027] The stream 8 is sent to the fractionation column 14, wherein a bottom fraction is
obtained, which is constituted by 16.57 parts of MTBE, 51.90 parts of methanol and
0.01 parts of TBA.
[0028] The remaining stream, constituted by C₄ hydrocarbons and azeotropic methanol is recovered
overhead in 14.
[0029] The stream 7 and stream 9 can be either used separately, or they can be combined
together, 120.46 parts being obtained of a mixture of high-octane-number oxygenated
compounds, which has the following composition:
Methanol 43.08%
TBA 43.16%
MTBE 13.76%
Example 2
[0030] A gasoline containing 25% of aromatic hydrocarbons is admixed with methanol, with
methanol and TBA and with such reaction product as obtained in Example 1. The ratios
are so adjusted, that methanol is always 5% of the mixture.
[0031] On the mixture, the highest water content is determined, which can be tolerated without
clouding appearing at the temperature of 20°C. The results are reported in the following
Table:
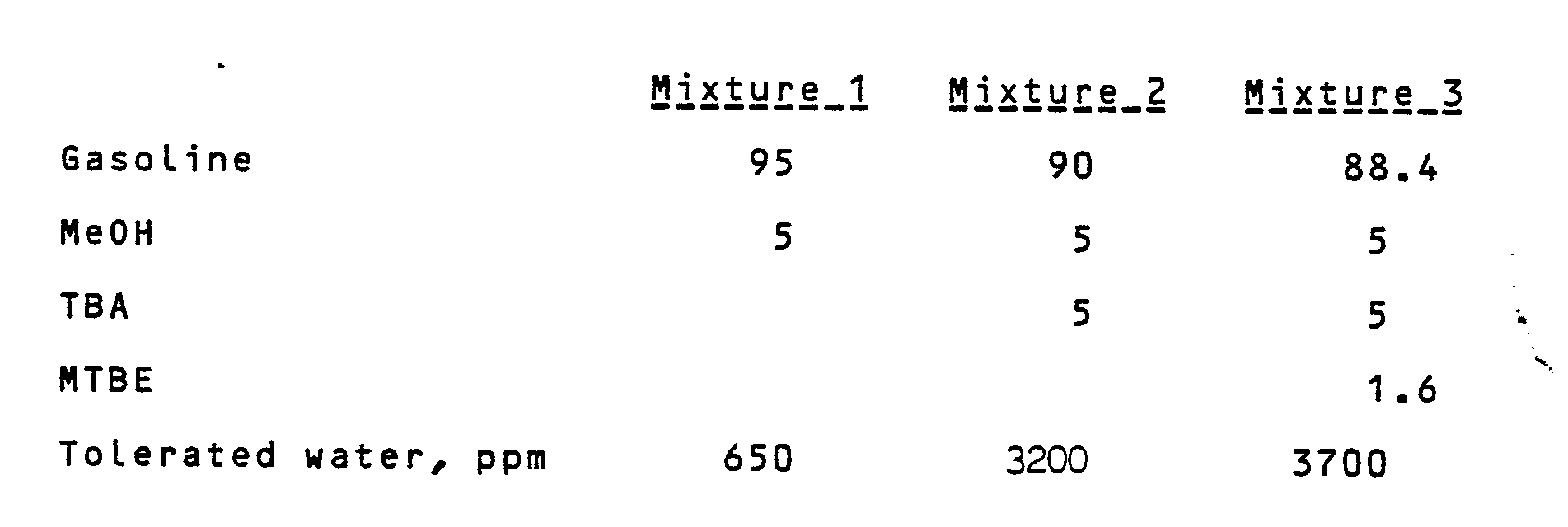
[0032] It can be observed that the stability of mixture 3 is higher not only than that of
only methanol-containing mixture, but also than the stability of the mixture con taining
methanol and TBA.
1. Oxygenated high-octane-number composition for fuels, comprising a mixture of methanol,
tert.butyl alcohol (TBA) and methyl-tert-butyl ether (MTBE), characterized in that
methanol, TBA and MTBE are comprised within the following percent ranges:
methanol: from 30 to 45% by weight;
TBA : from 30 to 45% by weight;
MTBE : from 5 to 20% by weight.
2. High-octane-number composition according to claim 1, characterized in that it is
constituted by 43.1% by weight by methanol, by 43.1% by weight by TBA, and by 13.8%
by weight by MTBE.
3. Method for the preparation of a high-octane-number composition for fuels according
to claims 1 or 2, comprising submitting a butadiene-free C₄ charge, containing isobutene
at a percentage, by weight, of from 10 to 55%, to one or more hydration treatment(s)
in series with water, in the presence of an acidic cationic resin, in particular based
on sulphonated styrene-divinylbenzene of Amberlyst 15 type, isobutene being thus partly
converted into TBA, separating TBA from the mixture of the other components, containing
the residual isobutene, submitting the residual isobutene in said mixture to an etherifying
treatment with an excess of methanol, as referred to the stoichiometric amount, to
the purpose of converting it into MTBE in the presence of an acidic cationic resin,
in particular based on sulphonated styrene-divinylbenzene of Amberlyst 15 type, characterized
in that the reaction mixtur e (isobutene and water) is homogenised
by a means of a solvent selected from either pure or substantially pure TBA, and mixtures
of TBA with water, isobutene being converted into TBA at a temperature comprised within
the range of from 40 to 90°C by a percentage comprised between 75 to 80%, and the
MTBE-containing mixture is submitted to fractionation, a mixture being separated of
MTBE and methanol, with possible minor traces of TBA, which is admixed with pure TBA
up to the concentrations according to claims 1 or 2.
4. Method according to claim 3, characterized in that the mixture of TBA and water,
used as the solvent, is obtained as an intermediate fraction in TBA separation step.