[0001] La présente invention concerne une cuve pour la production d'aluminium par électrolyse
d'alumine dissoute dans la cryolithe fondue, selon le procédé Hall-Héroult, dont la
cathode est constituée de blocs cathodiques carbonés modulaires, à faible chute de
tension.
Exposé de l'art antérieur
[0002] La cathode d'une cuve d'électrolyse Hall-Héroult est constituée par la juxtaposition
d'un ensemble de blocs carbonés, munis, à leur base inférieure, d'une (ou parfois
deux) rainure(s) ouverte(s) dans lesquelles sont scellées, généralement par coulée
de fonte, des barres d'acier de section carrée, rectangulaire ou circulaire, sur lesquelles
sont raccordés les conducteurs de liaison entre les cuves successives formant une
série. Ces blocs sont généralement jointoyés par une pâte carbonée dite pâte de brasque,
peu conductrice du courant, et dont l'épaisseur est de plusieurs centimètres.
[0003] Celle-ci doit être étanche à l'aluminium liquide qui se dépose par électrolyse au-dessus
des blocs carbonés. Le courant électrique traverse donc dans l'ordre une couche d'aluminium
liquide, une partie carbonée, les scellements barre-bloc, les barres en acier et passe
dans les conducteurs de liaison à la cuve suivante.
[0004] Chaque changement de matériau se traduit par une surtension de contact qui dépend
des conditions d'assemblage et des surfaces sollicitées. Ceci est particulièrement
vrai pour le contact carbone- scellement appelé contact de scellement.
[0005] La chute de tension totale peut donc se décomposer en trois éléments prépondérants
:
- la chute dans le carbone
- la chute au scellement
- la chute dans la barre en acier.
[0006] Pour réduire cette chute de tension, il est connu d'utiliser des blocs carbonés de
basse résistivité électrique.
[0007] A l'heure actuelle, la plupart des producteurs de blocs cathodiques proposent des
blocs dits « semi-graphite obtenus à partir d'une pâte carbonée dans laquelle les
grains d'anthracite ont été remplacés par des grains de graphite, et des blocs « semi-graphités
•, obtenus à partir d'une pâte carbonée classique, mais avec cuisson à température
élevée (> 2 000 °C) de façon à graphiter partiellement le bloc dans la masse. On augmente
ainsi sensiblement la conductivité électrique des blocs. Mais ce type de bloc présente
le défaut d'augmenter les distorsions de courant électrique dans la nappe d'aluminium
liquide supérieure par suite d'une plus grande inclinaison des lignes de courant dans
l'aluminium liquide, et de ce fait, d'augmenter les turbulences magnétiques de cette
nappe ce qui dégrade la stabilité hydrodynamique de l'électrolyseur.
[0008] On peut, pour corriger ce défaut, utiliser la technique des « blocs Sandwich , dont
une partie est constituée, par exemple, à partir de pâte carbonée avec grains d'anthracite,
et une autre partie de pâte carbonée semi-graphite ou semi-graphitée, de conductivité
électrique plus élevée.
[0009] On a également proposé, pour augmenter la surface active de la cathode de substituer
au jointoiement des blocs à la pâte de brasque (peu conductrice du courant), un collage
au moyen d'une colle conductrice à base de graphite et de résines thermodurcissables.
Cela a le quadruple avantage d'augmenter la surface totale conductrice, de permettre
des transferts électriques entre deux blocs adjacents, de réduire les émissions de
goudrons à la mise en place du jointoiement carboné et d'améliorer l'étanchéité.
[0010] Pour réduire la chute de tension totale, il est également connu d'augmenter la section
de la barre d'acier, au moins dans la zone scellée dans le carbone, tout en gardant
une section normale ou rétrécie à la traversée de la partie extérieure du calorifugeage
de la cuve, de façon à éviter des fuites thermiques trop importantes.
[0011] Cependant, une telle action est forcément limitée, car l'épaisseur de carbone des
ailes de la rainure doit être suffisante pour résister mécaniquement aux contraintes
dues à la dilatation thermique de la barre cathodique, et de son scellement, lors
de la mise en régime de la cuve. La forme de la section de la partie scellée peut
être indifféremment circulaire ou rectangulaire.
[0012] Pour réduire la chute de tension, on utilise également des blocs carbonés à deux
rainures étroites qui ont l'avantage de multiplier la surface de contact au scellement
sans trop fragiliser le bloc lorsqu'il est soumis aux contraintes thermiques de marche
de l'électrolyseur. On doit alors respecter un minimum de distance entre le bord du
bloc et la rainure la plus proche, ce qui limite la section possible des barres d'acier.
[0013] Quelle que soit la solution adoptée et quelles que soient la forme et la dimension
des blocs et des barres de fer qui sont scellées dans ces blocs, la construction de
la cathode est toujours effectuée en disposant les blocs parallèlement au petit côté
du caisson métallique, de telle sorte que les sorties cathodiques (extrémités des
barres de fer qui dépassent à l'extérieur du caisson, et sur lesquelles sont raccordés
les conducteurs de liaison entre cuves), se trouvent toujours sur le grand côté de
la cuve, que les cuves soient disposées en long ou en travers par rapport à l'axe
de la série.
[0014] A l'heure actuelle, les producteurs d'aluminium cherchent à accroître la puissance
unitaire des cuves d'électrolyse, en vue, notamment d'augmenter les rendements, de
diminuer les coûts d'investissement et de faciliter l'automatisation intégrale de
l'exploitation. Le niveau de 200 000 ampères est déjà largement dépassé, et il est
très probable que les 400 000 ampères seront atteints avant la fin des années 80.
[0015] Parallèlement, un effort important est fait pour diminuer les consommations énergétiques
de la cuve, en particulier en réduisant les chutes ohmiques dans la cathode.
[0016] La construction de cathodes à basse chute de tension pour des cuves de cette puissance
exige de nouvelles solutions qui ne peuvent pas être une simple extrapolation des
solutions actuelles. On sait en effet, que la durée de vie d'une cuve est étroitement
dépendante de la qualité de sa cathode car la plupart des mises hors-service prématurées
sont dues à des infiltrations de métal et d'électrolyte dans l'espace sous-cathodique.
Exposé de l'invention
[0017] La présente invention est basée sur une conception nouvelle des cathodes que l'on
peut qualifier de « modulaire •, car elle s'adapte, en jouant sur le nombre de modules,
à toutes dimensions de cuve qui soit un multiple entier des dimensions du module.
[0018] Elle a pour objet une cuve d'électrolyse pour la production d'aluminium selon le
procédé Hall-Héroult, cette cuve comportant un caisson métallique parallélépipédique
supportant une cathode sur laquelle se forme la nappe d'aluminium liquide, cette cathode
étant constituée par la juxtaposition de blocs carbonés parallélépipédiques, de forme
allongée, ayant un rapport longueur du grand axe sur largeur au moins égal à deux,
et dans lesquels est taillée au moins une rainure dans laquelle est scellée une barre
d'acier disposée parallèlement au petit côté du caisson et qui se raccorde à au moins
un collecteur cathodique, caractérisée en ce que les rainures de scellement sont taillées
dans le sens perpendiculaire au grand axe du bloc, qui est lui-même disposé parallèlement
au grand côté du caisson.
[0019] En associant, par collage sur une grande face latérale, un premier bloc cathodique,
à au moins un deuxième bloc, on constitue un demi-module cathodique dont la largeur
correspond à la demi-largeur de la cathode.
[0020] En associant deux demi-modules, par un moyen tel que le collage, on constitue un
module cathodique dont la largeur correspond à la largeur de la cathode.
[0021] D'autres modes de réalisation de l'invention ressortiront des revendications 4 à
10 et de la description des figures.
Description des figures
[0022] La figure 1 est un rappel de l'art antérieur.
[0023] Les figures 2 à 5 illustrent la mise en oeuvre de l'invention proprement dite.
[0024] La figure 1 représente schématiquement et partiellement en plan la cathode d'une
cuve d'électrolyse selon la technique actuelle. Les blocs cathodiques (1) sont disposés
parallèlement au petit côté (2) du caisson métallique qui supporte la cathode de la
cuve d'électrolyse. Ces blocs sont de forme parallélépipédique allongée de grand axe
AA', la hauteur h et la largeur I étant généralement de l'ordre de 300 à 700 mm, et
la longueur de l'ordre de 2 mètres et au-delà. Le rapport longueur sur largeur est,
dans la plupart des cas, supérieur à 2 et peut atteindre 4 à 8. La hauteur et la largeur
sont souvent dans un rapport peu différent de 1.
[0025] Dans le cas particulier représenté figure 1, chaque bloc (1) comporte deux barres
(3) souvent constituées chacune, en pratique, par deux demi-barres (3A) et (3B) qui
peuvent - ou non - être jointives dans leur partie centrale (4). A leur extrémité
(5), côté extérieur, les barres cathodiques sont raccordées à un ou plusieurs conducteurs
latéraux tels que (6) reliés au cadre anodique de la cuve suivante dans la série.
Les barres sont scellées, le plus souvent, à la fonte dans une ou deux rainures longitudinales
(7) du bloc (1).
[0026] Les blocs cathodiques successifs sont scellés par un joint de pâte de brasque (8),
damé à chaud, qui assure l'étanchéité de l'ensemble de la cathode vis-à-vis des infiltrations
d'aluminium liquide et de l'électrolyte fondu, étanchéité dont dépend étroitement
la durée de vie de la cuve.
[0027] Selon l'invention (figure 2 et suivantes), les blocs cathodiques (10) sont disposés
de façon que leur grand axe AA' soit parallèle au grand côté (11) du caisson et à
son grand axe XX'. Les barres cathodiques (3) et les sorties (5), ainsi que le collecteur
(6) conservent la même disposition, mais les rainures (12) sont maintenant taillées
en travers du bloc cathodique, parallèlement à son petit côté, donc perpendiculairement
à son grand axe AA'.
[0028] Chaque « demi-module cathodique est constitué par l'association de deux blocs (10A)
et (10B) préalablement assemblés par un moyen tel que le collage (9), la mise en place
et le scellement des barres cathodiques s'effectuant par les procédés habituels tel
que le scellement à la fonte ou, plus rarement, à la pâte carbonée. La juxtaposition
de deux demi-modules identiques, symétriquement par rapport au grand axe de la cuve,
constitue un premier module cathodique. Les deux demi-modules (10A-10B) et (10C-10D)
sont jointoyés de façon habituelle, par de la pâte de brasque (13), ou de préférence
par collage. Ce jointoiement peut être effectué avant ou après mise en place dans
le caisson. Ce premier module cathodique est ensuite complété par n modules identiques
jointoyés par de la pâte de brasque (8), selon le type de cuve. Une cathode pour cuve
à 180 000 ampères, par exemple, peut être constituée à partir de trois modules successifs.
Bien que l'on ait décrit des demi-modules constitués chacun de deux blocs, cet exemple
ne constitue pas une limitation de l'invention. On peut concevoir des demi-produits
constitués de deux blocs inégaux en largeur, ou de trois blocs égaux ou inégaux en
largeur, la hauteur et la longueur devant, par contre, être égales dans tous les cas.
[0029] A partir de ce principe de base, plusieurs modes de mise en oeuvre de l'invention
sont possibles. Chacun des deux blocs constituant un demi-module cathodique (10A)
et (10B) peut être de composition identique, c'est-à-dire obtenu à partir d'une même
pâte carbonée, ou de composition différente, de façon à conférer à l'un d'eux des
propriétés particulières, par exemple une conductivité thermique ou électrique différente.
[0030] Le bloc extérieur (10A) peut, par exemple, être du type classique (brai + grains
d'anthracite), ayant à 900 °C une résistivité électrique de l'ordre de 4,4 - 10
-3 Ω cm et une conductivité thermique À de l'ordre de 0,03 W/cm/°C, alors que le bloc
intérieur (10B) peut être du type « semi-graphite • , ayant à 900 °C, une résistivité
électrique de 2,8 · 10
-3 Ω cm et une conductivité thermique λ de 0,23 W/cm/°C.
[0031] Dans une variante représentée figure 3, le bloc extérieur (10A) peut lui-même être
constitué en deux parties, la partie externe (10E) étant en matériau à conductivité
thermique relativement faible, de façon à réduire le flux de chaleur drainé vers l'extérieur
par les blocs carbonés et à améliorer ainsi le bilan thermique de l'électrolyseur.
[0032] Enfin, les sections des rainures de scellement (12) peuvent être toutes de largeur
égale, ou certaines, notamment celles des extrémités, peuvent être différentes, par
exemple en vue d'avoir un écartement constant entre les trous prévus dans la paroi
latérale du caisson, par lesquels sortent les barres cathodiques.
[0033] Par ailleurs, on peut, sur une partie au moins de la surface des blocs cathodiques
constituant la cathode, incorporer une substance qui les rende mouillables par l'aluminium
liquide. Cette incorporation peut être superficielle ou intéresser tout ou partie
des blocs cathodiques.
[0034] Il est connu, notamment par la publication de K. Billehaug et H. A. Oye, « ALUMINIUM
56, 1980, pages 642 à 648 (avril 1980) et pages 713 à 718 (nov. 1980) que les composés
réfractaires dits « RHM (Refractory Hard Metals), et plus particulièrement le diborure
de titane TiB2, sont à la fois mouillés par l'aluminium liquide et relativement très
peu attaqués par ce métal à 930-960 °C.
[0035] On peut ainsi soit revêtir totalement ou partiellement la surface des blocs cathodiques,
de plaques ou autres éléments en TiB2 pur ou en composite titrant au moins 30 en TiB2,
soit effectuer, par tous moyens connus, un dépôt de TiB2, ou de composite à base de
TiB2, sur tout ou partie de la surface cathodique, soit introduire dans la pâte carbonée
constituant les blocs cathodiques, ou tout au moins la partie supérieure des blocs
cathodiques en contact avec l'aluminium liquide, du TiB2 et/ou un composé RHM, à une
teneur au moins égale à 30 %, qui est le minimum reconnu pour assurer l'effet de mouillabilité.
On peut ainsi stabiliser la nappe d'aluminium liquide et réduire sensiblement la distance
anode-cathode, donc la chute de tension dans le bain d'électrolyse, ce qui entraîne
une réduction corrélative de l'énergie spécifique en kilowatts heure par tonne d'aluminium
produit.
Avantages procurés par l'invention
[0036] La mise en oeuvre de l'invention procure de très nombreux avantages, que l'on peut
présenter de la façon suivante :
[0037] 1. La surface cathodique utile est augmentée du fait du remplacement des joints en
pâte de brasque de 30 à 40 mm de largeur - électriquement peu conducteurs - par des
joints collés de très faible épaisseur, de l'ordre du millimètre.
[0038] 2. On peut maintenant concilier une section d'acier importante avec une surface de
contact carbone- acier importante, ce qui n'était pas le cas selon l'art antérieur.
[0039] Sur la figure 5 qui représente, à échelle d'environ 1/20°, des sections verticales
de blocs cathodiques selon l'art antérieur (5A) et (5B), et selon l'invention (5C),
on constate que l'on passe, pour une coupe verticale donnée, de 36,8 dm de longueur
de contact de scellement et 17,16 dm2 de section acier et fonte pour le cas 5A, à
29,2 dm de longueur de contact et 26,4 dm2 de section pour le cas 5B, et à 41,6 dm
de longueur de contact et 25,08 dm
2 de section pour le cas 5C. Il en résulte une très forte réduction de la chute ohmique
de contact de scellement, combinée à une très basse chute ohmique dans l'acier. Il
est remarquable que ce gain global, qui a été trouvé égal à plusieurs dizaines de
millivolts, ait été obtenu sans fragiliser le bloc de carbone, les ailes (16) des
blocs c'est-à-dire les parties de carbone restant entre rainures ou entre rainure
et côté des blocs, ayant conservé les mêmes dimensions. L'homme de l'art sait qu'un
gain de 10 mV équivaut à une baisse de consommation de 30 à 35 kWh par tonne d'aluminium
produit.
[0040] 3. La disposition nouvelle des blocs cathodiques permet la réalisation de blocs mixtes
(ou « sandwiches ») de façon simple et économique. Selon l'art antérieur, il fallait
découper les blocs (1) puis assembler les deux parties (anthracite et semi-graphite,
par exemple) lors du montage des cathodes, alors que, selon l'invention, chaque bloc
mixte tel que 10A = 10B est obtenu par simple collage de deux blocs de dimensions
standards et mis en place tel quel.
[0041] 4. La mise en place requiert moins de main-d'oeuvre : on remplace la pose de quatre
blocs (figure 1) par celle de deux demi-modules (figure 2) ou d'un seul module préassemblé
par collage.
[0042] 5. Par rapport au collage classique de blocs (1) en travers poussés par des vérins
(14) à grande course (figure 4A), difficile à pratiquer, car cette disposition cumule
les erreurs de parallélisme, le montage par modules s'accommode d'imprécisions importantes
que l'on compense par le joint (8) de pâte de brasque entre modules adjacents (figure
2). Il suffit, en outre, de vérins (15) de faible course, disposés contre le grand
côté du caisson, pour assujettir les deux demi-modules (5C) en cours de collage pour
former chaque module cathodique.
[0043] 6. En remplaçant les joints en pâte de brasque par des joints collés, on améliore
l'étanchéité de la cathode aux infiltrations de métal et d'électrolyte fondus. L'importance
de cette étanchéité a été signalée précédemment.
[0044] 7. Enfin, l'invention est compatible avec l'utilisation de surfaces cathodiques mouillables
par l'aluminium liquide.
Exemple d'application
[0045] L'invention a été mise en oeuvre sur plusieurs cuves d'une série fonctionnant sous
180 000 ampères, en constituant la cathode à partir de demi-modules constitués de
deux blocs en « semi-graphite conformes au dessin de la figure 5C.
[0046] On a procédé sur les cuves classiques à blocs anthracitiques et sur les cuves modifiées
selon l'invention, à la mesure de la chute de potentiel dans le système cathodique,
au contact de scellement et dans la barre cathodique ; on a obtenu les résultats suivants
:
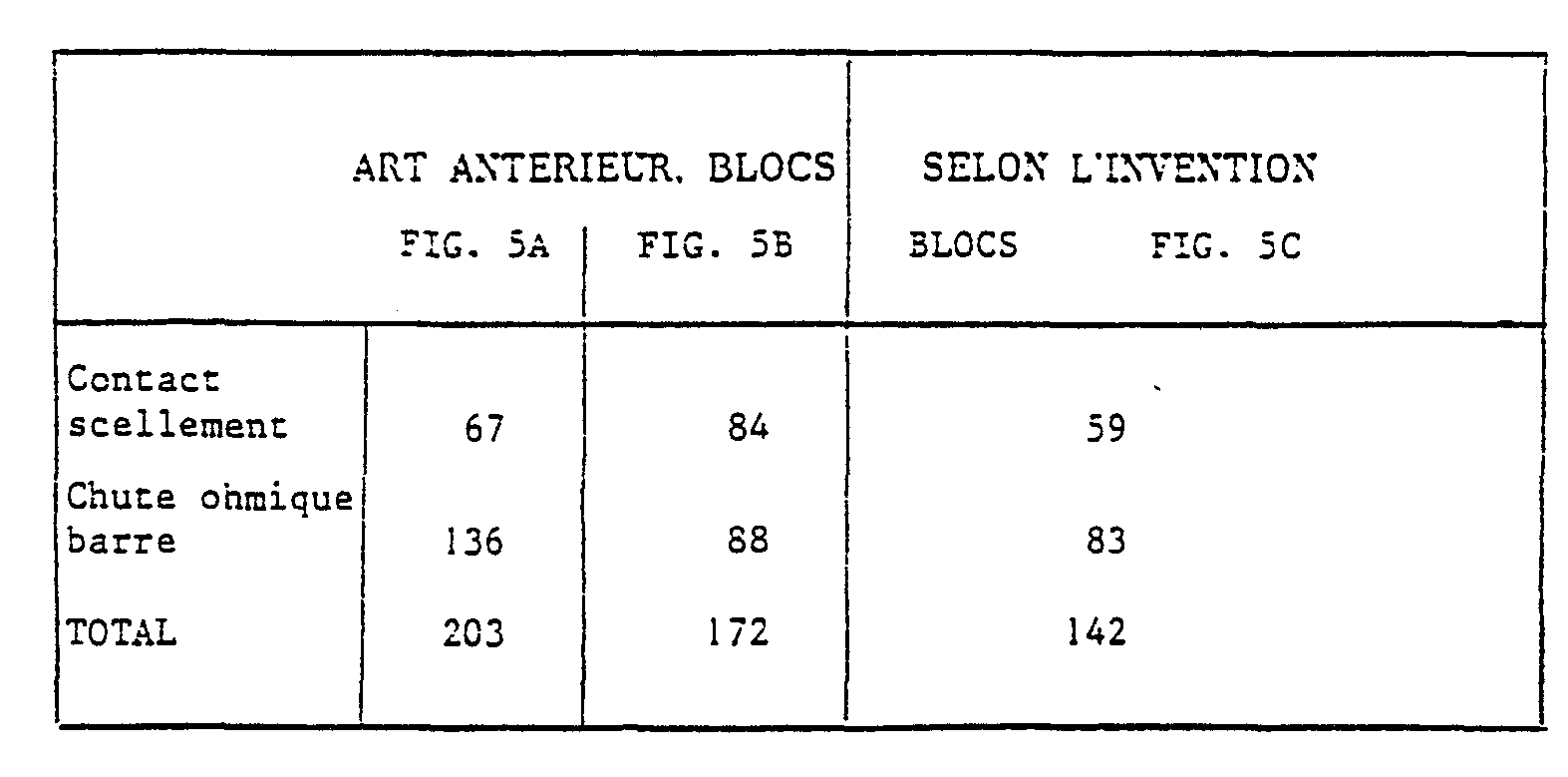
[0047] Le gain maximum obtenu est de 61 mV, ce qui correspond à près de 200 kWh en moins
par tonne d'aluminium produit. Ce gain a été obtenu pour moitié par l'utilisation
de blocs « semi-graphite à résistivité plus basse, et pour moitié par la mise en oeuvre
de l'invention de bloc cathodique modulaire.
1. Cuve d'électrolyse pour la production d'aluminium selon le procédé Hall-Héroult,
comportant des blocs cathodiques à faible chute de tension, cette cuve étant constituée
par un caisson métallique parallélépipédique supportant une cathode sur laquelle se
forme la nappe d'aluminium liquide, cette cathode étant constituée par la juxtaposition
de blocs carbonés parallélépipédiques, de forme allongée, ayant un rapport longueur
du grand axe sur largeur au moins égal à deux, et dans lesquels est taillée au moins
une rainure dans laquelle est scellée une barre d'acier disposée parallèlement au
petit côté du caisson, et dont l'extrémité sort sur le grand côté du caisson et se
raccorde à au moins un collecteur cathodique, caractérisée en ce que les rainures
de scellement (12) sont taillées dans le sens perpendiculaire au grand axe (AA') du
bloc (10), qui est lui-même disposé parallèlement au grand côté (11) du caisson.
2. Cuve d'électrolyse selon revendication 1, caractérisée en ce qu'un bloc (10) est
associé, par collage, sur une grande face latérale, à au moins un deuxième bloc pour
constituer un demi-module cathodique (10A 10B), dont la largeur correspond à la demi-largeur
de la cathode.
3. Cuve d'électrolyse, selon revendication 2, caractérisée en ce qu'elle comporte
au moins un module cathodique, dont la largeur correspond à la largeur de la cathode,
constitué par l'association de deux demi-modules (10A, 10B), (10C, 10D).
4. Cuve d'électrolyse, selon revendication 2, caractérisée en ce que chaque demi-module
(10A, 10B), est constitué par des blocs obtenus à partir d'une même pâte carbonée,
et présentant des propriétés thermiques et/ou électriques sensiblement égales.
5. Cuve d'électrolyse selon revendication 2, caractérisée en ce que chaque demi-module
(10A, 10B) est constitué par des blocs présentant entre eux des propriétés thermiques
et/ou électriques différentes.
6. Cuve d'électrolyse selon revendication 1, caractérisée en ce que toutes les rainures
de scellement 12, des blocs (10) ont une largeur égale.
7. Cuve d'électrolyse selon revendication 1, caractérisée en ce que certaines des
rainures de scellement (12) d'un même bloc (10) ont des largeurs différentes des autres.
8. Cuve d'électrolyse selon revendication 3, caractérisée en ce que sa cathode est
constituée par la juxtaposition, sur un même plan, d'au moins deux modules (10A, 10B,
10C, 10D).
9. Cuve d'électrolyse selon revendication 2 ou 3, caractérisée en ce que les demi-modules
(10A, 10B) et les modules (10A, 10B, 10C, 10D) sont assemblés par un moyen choisi
parmi le collage et le jointoyage avec de la pâte de brasque.
10. Cuve d'électrolyse selon l'une quelconque des revendications 1 à 9, caractérisée
en ce que chaque bloc cathodique (10) comporte un revêtement superficiel contenant
au moins 30 % de diborure de titane.
1. An electrolysis tank for producing aluminium according to the Hall-Heroult process,
comprising cathodic blocks having a low voltage drop, said tank comprising a parallelepipedic
metal casing supporting a cathode on which the layer of liquid aluminium is formed,
said cathode being formed by the juxtaposition of parallelepipedic carbonaceous blocks
of elongate shape, having a ratio of the length of the major axis to the width which
is at least equal to two, and in which there is cut at lest one groove into which
is sealed a steel bar disposed in parallel relationship to the short side of the casing
and the end of which issues at the long side of the casing and connects to at least
one cathodic collector, characterised in that the sealing grooves (12) are cut in
the direction which is perpendicular to the major axis AA' of the block which is itself
disposed in parallel relationship to the long side (11) of the casing.
2. An electrolysis tank according to claim 1 characterised in that a block 10 is associated
by glucing on a large side face with at least one second block thereby to form a cathodic
demi-module whose width corresponds to half the width of the cathode.
3. An electrolysis tank according to claim 2 characterised in that it comprises at
least one cathodic module whose width corresponds to the width of the cathode, formed
by the association of two demi-modules (10A, 10B), (10C, 10D).
4. An electrolysis tank according to claim 2 characterised in that each demi-module
is formed by blocks produced from the same carbonaceous paste and having substantially
identical thermal and/or electrical properties.
5. An electrolysis tank according to claim 2 characterised in that each demi-module
is formed by blocks having thermal and/or electrical properties which are different
from each other.
6. An electrolysis tank according to claim 1 characterised in that all the sealing
grooves (12) are of equal width.
7. An electrolysis tank according to claim 1 characterised in that some of the sealing
grooves (12) of a same block 10 are different in width from the others.
8. An electrolysis tank according to claim 3 characterised in that its cathode is
formed by the juxtaposition in the same plane of at least two modules (10A, 10B),
10C, 10D).
9. An electrolysis tank according to claim 2 or 3 characterised in that the demi-modules
(10A, 10B) and the modules (10A, 10B, 10C, 10D) are connected together by a means
choosen between glucing and joining by lining paste.
10. An electrolysis tank according to any of claims 1 to 9 characterised in that each
cathodic block (10) is provided with a surface coating comprising at least 30% of
titanium diboride.
1. Elektrolysewanne für die Erzeugung von Aluminium nach dem Hall-Héroult-Verfahren
mit Kathodenblöcken mit geringem Spannungsabfall, welche Wanne aus einem metallischen
parallelepipedischen Kasten gebildet ist, der eine Kathode trägt, auf der sich die
Aluminiumschmelzenschicht bildet, wobei diese Kathode durch die Nebeneinanderanordnung
von kohlenstoffhaltigen parallelepipedischen Blöcken länglicher Form mit einem Verhältnis
der Länge der großen Achse zur Breite von wenigstens zwei gebildet ist und in denen
wenigstens eine Nut eingeschnitten ist, in der eine parallel zur kleinen Seite des
Kastens parallel angeordnete Stahlstange eingesiegelt ist, deren Ende über die große
Seite des Kastens vorragt und mit wenigstens einem Kathodenkollektor verbunden ist,
dadurch gekennzeichnet, daß die Einsiegelungsnuten (12) in der zur großen Achse (AA')
des Blocks (10) senkrechten Richtung eingeschnitten sind, der selbst parallel zur
großen Seite (11) des Kastens angeordnet ist.
2. Elektrolysewanne nach Anspruch 1, dadurch gekennzeichnet, daß ein Block (10) an
einer großen Seitenfläche durch Kleben mit wenigstens einem zweiten Block zur Bildung
eines kathodischen Halbmoduls (10A, 10B) verbunden ist, dessen Breite der Halbbreite
der Kathode entspricht.
3. Elektrolysewanne nach Anspruch 2, dadurch gekennzeichnet, daß sie wenigstens einen
kathodischen Modul, dessen Breite der Breite der Kathode entspricht, aufweist, der
durch die Verbindung von zwei Halbmoduln (10A, 10B), (10C, 10D) gebildet ist.
4. Elektrolysewanne nach Anspruch 2, dadurch gekennzeichnet, daß jeder Halbmodul (10A,
10B) aus Blöcken gebildet ist, die aus derselben kohlenstoffhaltigen Paste erhalten
wurden und genaue gleiche thermische und/oder elektrische Eigenschaften aufweisen.
5. Elektrolysewanne nach Anspruch 2, dadurch gekennzeichnet, daß jeder Halbmodul (10A.
10B) aus Blöcken gebildet ist, die untereinander verschiedene thermische und/oder
elektrische Eigenschaften aufweisen.
6. Elektrolysewanne nach Anspruch 1, dadurch gekennzeichnet, daß alle Einsiegelungsnuten
(12) der Blöcke (10) eine gleiche Breite haben.
7. Elektrolysewanne nach Anspruch 1, dadurch gekennzeichnet, daß einige der Einsiegelungsnuten
(12) desselben Blocks (10) von den anderen verschiedene Breiten haben.
8. Elektrolysewanne nach Anspruch 3, dadurch gekennzeichnet, daß ihre Kathode durch
die Nebeneinanderanordnung von wenigstens zwei Moduln (10A, 10B, 10C, 10D) in derselben
Ebene gebildet ist.
9. Elektrolysewanne nach Anspruch 2 oder 3, dadurch gekennzeichnet, daß die Halbmoduln
(10A, 10B) und die Moduln (10A, 10B, 10C, 10D) durch ein Mittel verbunden sind, das
zwischen dem Kleben und dem Verfugen mit der Kohlenlöschepaste gewählt ist.
10. Elektrolysewanne nach irgendeinem der Ansprüche 1 bis 9, dadurch gekennzeichnet,
daß jeder Kathodenblock (10) einen Oberflächenüberzug aufweist, der wenigstens 30
% Titandiborid enthält.