[0001] Die Erfindung bezieht sich auf Verfahren zur anodischen Oxydation von Werkstücken
aus einer Aluminiumlegierung, insbesondere mit hohem Gehalt an Kupfer und/oder edleren
Metallen, wobei die Werkstücke in einem bewegten wässrigen Elektrolyten zusammen mit
einer oder mehreren Kathoden angeordnet werden und eine Spannung im wesentlichen periodisch
zum Erzeugen von kurz zeitigen Stromimpulsen mit hohem Stromfluss an die Werkstücke
und die Kathode(n) angelegt wird.
[0002] Es ist seit langem bekannt, Gegenstände aus Aluminium durch anodische Oxydation in
einem wässrigen Elektrolyten mit einer dicken (z B. 50
11m), harten und abriebfesten Oxidschicht zu versehen. Die so oxdierten Aluminiumwerkstücke
können überall dort eingesetzt werden, wo verschleißfeste Oberflächen notwendig sind.
[0003] Diese sogenannten Hartoxidschichten weisen Härtewerte auf, die dem 5- bis 10-fachen
der Harte des Grundmaterials entsprechen. Für die Hartanodisation wurden eine große
Anzahl von Elektrolyten entwickelt, mit denen es möglich ist, dicke, harte und abriebfeste
Oxidschichten zu bilden. Die bekanntesten dieser Elektrolyten basieren auf schwefelsäure,
wobei einerseits reine Schwefelsäure unterschiedlicher Konzentration und andererseits
Mischelektrolyte (z.B. Schwefelsäure und Oxalsäure) Anwendung gefunden haben.
[0004] Diese Elektrolyten weisen ein Rücklösevermögen der gebildeten Oxidschicht auf. Um
dieses Rücklösevermögen zu verringern und die geünschten dicken, harten und abriebfesten
Qxidschichten zu erreichen, wird der Elektrolyt gekühlt.
[0005] Bei der anodischen Oxydation bildet sich auf dem Aluminium eine poröse Oxidschicht,
deren Dicke mit der Oxydationszeit zunimmt. Bedingt durch dieses Wachsen der Oxidschicht
erhöht sich der elektrische Übergangswiderstans zwischen Elektrolyt und Werkstück.
An diesem Übergangswiderstand fällt in Abhängigkeit vom Anodisationsstrom eine Spannung
ab. Diese elektrische, vom Übergangswiderstans aufgenommene Leistung wird in Joule'sche
Wärme umgesetzt. Dies führt zu einer Temperaturerhöhung in der Oxidschicht.
[0006] Die freiwerdende Joule'sche Warme wird durch den Elektrolyten, der zur besseren Wärmeabfuhr
bewegt wird, und durch das Werkstück abgeführt. Insbesondere bei dünnen Werkstücken
und an Kanten mit kleinem Krümmungsradius ist die Wärmeabfuhr durch das Werkstück
selbst vernachlässigbar gering. Der Hauptanteil der Jouleschen Wärme wird daher durch
den Elektrolyten abgeführt. Dabei ist jedoch zu beachten, daß bei Zunahme der Schichtdicke
der Wärmefluss von der oxidierten Metallseite zum Elektrolyten zunehmend behindert
wird. Bei anodischer Oxydation mit Gleichstrom wird deshalb die Stromdichte begrenzt.
[0007] Im Anfangsstadium der Anodisation ist die Schichtdicke zunächst gering, so daß auch
nur ein geringer elektrischer Leistungsabfall auftritt. Die entstehende Joule'sche
Wärme kann durch den Vorbeiströmenden Elektrolyten an der Grenzfläche Aluminiumoxid/Elektrolyt
leicht abgeführt werden, so daß es zu keinem Wärmestau in der Oxidschicht kommen kann.
Bei größeren Schichtdicken wird auch der Leistungsabfall größer, so daß eine zunehmende
Erwärmung auftritt. Das Rücklösevermögen des Elektrolyten nimmt mit Erwärmung stark
zu, so daß die Bildung von dicken, harten Schichten behindert wird. Kein Schichtwachstum
erfolgt mehr, wenn die Auflösungsgeschwindigkeit des Oxids durh den Elektrolyten gleich
der Bildungsgeschwindigkeit des Oxids ist. Bei Werkstücken mit spitzen, scharfkantigen
Teilen oder unterschiedlichen Wandstärken treten aufgrund der hohen Auflösungsgeschwindigkeit
lokale Verbrennungen auf, da die entstandene Wärme durch das Metall nicht gleichmäßig
verteilt und abgeführt werden kann. Die Rücklösung kann mit bis zu einer Zerstörung
des Werkstücks führen.
[0008] Neben diesen thermischen Problemen, die auch bei reinem Aluminium auftreten, kommt
bei der anodischen Oxydation von Aluminiumlegierungen mit hohem Gehalt an elektrochemisch
edleren Legierungselementen, wie z.B. an Kupfer, noch folgendes Problem hinzu: Die
in die Aluminiummatrix eingebetteten elektrochemisch edleren Metalle oder Metallphasen
bilden Störstellen bei der Oxydation, da diese Metalle entweder eine höhere Auflösungsgeschwindigkeit
aufweisen als das Aluminium (wie z.B. die intermetallische Phase des Kupfers) oder
im Elektrolyten nicht löslich sind, wie z.B. Bleiausscheidungen, die gegenüber dem
gebildeten Oxid außerdem eine hohe Elektronenleitfähigkeit aufweisen. Diese Störstellen
verhindern eine homogene Ausbildung von Keimen, die das Primärwachstum der Oxidschicht
einleiten, auf der Aluminiummatrix. Bei intermetallischen Phasen, die, wie Kupfer,
bevorzugt in Lösung gehen, steigt der Stromfluss an den Störstellen sehr stark an,
so daß verstärkt Joule'sche Wärme auftritt, die wiederum zu einer erhöhten Rücklösung
führt.
[0009] Bei dem aus der US-PS-2 920 018 bekannten Verfahren der eingangs genannten Art wird
die Anodisierung mit pulsierendem Gleichstrom durchgeführt, dessen Frequenz der Netzfrequenz
entspricht. Mittels einer Phasenanschnittssteuerung werden aus den positiven (oder
negativen) Halbwellen Spannungsimpulse herausgeschnitten. Die Stromflusszeit, also
die Zeitdauer eines Einzelimpulses entspricht etwa einem Drittel der sich anschließenden
Ausschaltzeit. Während dieser Ausschaltzeit wird praktisch keine Joule'sche Wärme
mehr erzeugt, die Ausschaltzeit wird genutzt, um die während des vorangegangenen Spannungsimpulses
gebildete Joule'sche Wärme abzufuhren.
[0010] Die nach diesem bekannten Verfahren hergestellten Oxidschichten sind jedoch nicht
immer zufriedenstellend. In praktischen Versuchen hat sich vielmehr gezeigt, daß auch
bei relativ kurz zeitigen Spannungsimpulsen und dementsprechend zwangsläufig längere
Ruhepausen zwischen den einzelnen Spannungs impulsen ein gleichmäßiges Schichtwachstum
nicht immer erreicht wird. Die Wärmeabfuhr an den kritischen Stellen ist nicht ausreichend,
dementsprechend ist auch die Schichtbildung an kritischen Stellen und bei speziellen
Legierungen nicht zufriedenstellend.
[0011] Weiterhin ist aus der US-PS-3 857 766 ein Verfahren zur anodischen Oxydation vor
allem von kupferhaltigen Aluminiumlegierungen bekannt, bei dem einem Basisgleichstrom
niedriger Spannung ein pulsierender Gleichstrom, der mindestens 6 Spannungsimpulse
pro Sekunde hat, überlagert wird. Die Oxydation erfolgt dabei mit konstantem Strom.
Als Elektrolyt wird eine Mischung von Schwefelsäure und Oxalsäure verwendet. Auch
die nach diesem Verfahren hergestellten Hartanodisationsschichten sind, insbesondere
bei speziellen Aluminiumlegierungen, nicht immer zufriedenstellend, an kritischen
Stellen ist die Schichtbildung schlecht oder unvollständig.
[0012] Aufgabe der Erfindung ist es, die Nachteile der bekannten Verfahren zu vermeiden
und ein Verfahren der eingangs genannten Art zu schaffen, mit dem sich Hartoxidschichten
auch an dünnwandigen und spitzen, scharfkantigen Werkstücken herstellen lassen, die
ausreichende mechanische Eigenschaften, insbesondere hinsichtlich Abriebsfestigkeit
und Dicke aufweisen.
[0013] Diese Aufgabe wird dadurch gelöst, daß die Spannung jeweils solange eingeschaltet
bleibt, wie ein merklicher Aufbau der Oxidschicht erfolgt und anschließend solange
ausgeschaltet wird, bis die erzeugte Joule'sche Wärme im wesentlichen abgeführt ist.
[0014] Die Zeitdauer der Spannungsimpulse ist vorteilhafterweise größer als 1/lotel Sekunde,
sie liegt beispielsweise zwischen 0,1 und 1,5 Sekunden und ist damit relativ lang.
[0015] Das erfindungsgemäße Verfahren zeichnet sich dadurch aus, daß die Dauer der Einschaltzeit
und die Dauer der Ausschaltzeit der Anodisierspannung speziell an die chemischen und
physikalischen Vorgänge beim Aufbau einer Oxidschicht angepasst ist. Der Schichtbildungsmechanismus
wird dadurch entscheidend beeinflusst. Der Initialvorgang bei der Schichtbildung erfolgt
bekanntlich in den folgenden Stufen:
1. Ausbildung einer mit gelöstem Aluminium übersättigten Zone auf der Aluminiumoberfläche,
hervorgerufen durch die anodische Auflösung.
2. Ausbildung überkritischer Keime an aktiven Stellen.
3. Wachstum der Keime bei gleichzeitiger Neubildung von Keimen.
4. Ausbildung einer Primärstruktur, d.h. vollständige Bedeckung der Metalloberfläche
mit Keimen.
5. Zusammenwachsen der Keime zu einer homogenen Schicht.
[0016] Bei dem erfindungsgemäßen Verfahren wird eine relativ hohe Spannung während der angegebenen
Zeitdauer angelegt. Bei dem resultierenden hohen Stromfluss ist die Anodisationsgeschwindigkeit
von Anfang an hoch, so daß trotz der beschriebenen, bevorzugten hohen Auflösungsgeschwindigkeit
von intermetallischen Phasen (z.B. Kupfer) die Aluminiummatrix zur Bildung von Keimen
aktiviert und eine gleichmäßige Schichtbildung auch an kritischen Steilen erreicht
wird.
[0017] Während des elektrochemischen Prozesses der anodischen Oxydation verarmt der Elektrolyt
ander Grenzfläche Elektrolyt/Metalloberfläche an den zur Oxydation notwendigen lonen,
so daß eine starke Konzentrationspolarisation auftritt. In einem schwefelsauren Elektrolyten
erfolgt die Oxydation des Aluminiums über die Suifationen. Es laufen folgende Reaktionen
ab:

[0018] Aus den Reaktionsgleichungen wird deutlich, daß der Elektrolyt an der Grenzfläche
Elektrolyt/Metall an S0
42--lonen verarmt und sich lokal an S0
32--lonen anreichert.
[0019] Nach dem Abschalten des Stroms wird durch den bewegten Elektrolyten ein Konzentrationsausgleich
auftreten. Der Abbau des Konzentrationsgefälles läßt sich über das Abklingen der Konzentrationspolarisation
mittels eines Elektronenstrahloszillographen nachweisen. Dabei wurde festgestellt,
daß die Anodisationsspannung nach Abschalten des Stromes nicht sofort auf einen Wert
annähernd 0 absinkt, sondern daß der Abbau des Potentials von etwa 3 bis 5 Volt eine
Zeit von 0,1 bis 0,5 Sekunden benötigt.
[0020] Andererseits stellt sich jedoch erst 0,2 bis 0,8 Sekunden nach Einschalten des Stromes
eine annähernd konstante Spannung ein, wie sich ebenfalls mittels eines Elektronenstrahl
oszillographen nachweisen läßt.
[0021] Die angegebene, im Vergleich zum Stand der Technik große Zeitdauer, während der die
Spannungsimpulse anliegen, ist für den Aufbau einer Oxidschicht ausgesprochen günstig.
Die Unterbrechung der Spannung zwischen zwei Spannungsimpulsen sollte 0,1 bis 2 Sekunden
andauern, vorteilhafter Weise liegt diese Zeitdauer zwischen 0,1 und 1 Sekunden. Das
Verhältnis von Zeitdauer eines Spannungsimpulses zur Zeitdauer einer Ausschaltzeit
sollte 0,5 bis 5 betragen.
[0022] Bei diesen Verhältnissen wird eine optimale Anodisation bei sehr hoher Stromdichte
bei allen Aluminiumlegierungen, jedoch besonders vorteilhaft bei Legierungen mit hohen
elektrochemisch edleren Legierungszusätzen erreicht. Überraschend gute Oxidationsergebnisse
wurden bei Parallelschaltung mehrerer (mindestens fünf bis maximal einhundert) Proben
mit dem erfindungsgemäßen Verfahren erzielt.
[0023] Vorteilhafterweise wird die Temperatur des Elektrolyten oder des Werkstücks, insbesondere
an kritischen Stellen, gemessen Erst nachdem die so gemessene Temperatur wieder auf
einen vorgegebenen Wert zurückgefallen ist, wird ein erneuter Spannungsimpuls angelegt.
Je nach Notwendigkeit stellen sich die Ausschaltzeiten bei Beginn oder bei Ende der
Oxidation länger oder kürzer ein.
[0024] Die Hartanodisation nach dem erfindungsgemäßen Verfahren kann für Werkstücke aus
Guss- oder Knetlegierungen angewendet werden. Außerdem können besonders vorteilhaft
Werkstücke aus Sinteraluminium auch mit hohen Legierungsanteilen an elektrochemisch
edleren Elementen, wie Kupfer, nach dem erfindungsgemäßen Verfahren zufriedenstellend
beschichtet werden. Bedingt durch die hohe Bildungsgeschwindigkeit der Oxidschicht
und die verringerte Rücklösung gelingt es, auf dem porösen Sintermetallwerkstoff verhältnismäßig
homogene Schichten zu bilden.
[0025] Weitere Merkmale der Erfindung ergeben sich aus den übrigen Ansprüchen.
[0026] Ein Ausführungsbeispiel der Erfindung wird im folgenden näher erläutert und unter
Bezugnahme auf die Zeichnung beschrieben.
[0027] In dieser zeigen:
Figur 1 einen Längsschnitt durch eine Elektrolyt-Wanne zur Durchführung des erfindungsgemäßen
Verfahrens,
Figur 2 ein Zeitdiagramm der zwischen Kathode und Anode in einer Vorrichtung gemäß
Figur 1 angelegten Spannung,
Figur 3 eine graphische Darstellung des zeitlichen Verlaufs des durch den Elektrolyten
fließenden Stromes. Der Zeitmaßstab stimmt mit dem Zeitmaßstab in Figur 2 überein.
Figur 4 eine graphische Darstellung des zeitlichen Verlaufs der Schichtdicke, der
Zeitmaßstab stimmt mit den Figuren 2 und 3 überein, und
Figur 5 eine graphische Darstellung des zeitlichen Verlaufs der Temperaturänderung
im Elektrolyten bei gleichem Zeitmaßstab wie die Figuren 2 bis 4.
[0028] In Figur 1 ist die zur Durchführung des erfindungsgemäßen Verfahrens benutzte Vorrichtung
gezeigt. Dabei nimmt eine Elektrolytwanne 1 ein Elektrolytbad 2 mit 180 g/I Schwefelsäure
und 15 g/I Oxalsäure auf. In dieses Elektrolytbad 2 sind eine Anode 3 und eine Kathode
4 eingetaucht und über Zuleitungen 5 und 6 mit einem Spannungsversorgungsgerät 7 verbunden.
Die Anode 3 setzt sich zusammen aus einem Anodenhalter 8 und den zu behandelnden Werkstücken
9.
[0029] Über eine Rohrleitung 10, die zu einer Pumpe 11 führt, wird ständig Elektrolytflüssigkeit
aus dem Elektrolytbad 2 abgesaugt und über ein Elektrolytleitrohr 12 in das Elektrolytbad
2 zurückgefuhrt, wobei der zurückgeführte Strom auf das Werkstück 9 gerichtet ist.
[0030] Weiterhin ragt ein Kühler 13 (Wärmeaustauscher) eines Kühlaggregats 14 in das Elektrolytbad
2. Dieses Kühlaggregat 14 wird durch ein Kontaktthermometer 15 gesteuert, das ebenfalls
in das Elektrolytbad 2 hineinreicht.
[0031] Das Spannungsversorgungsgerät 7 liefert eine gleichgerichtete Ausgangsspannung über
eine zeit t
i-t
2, wie sie in Fig. 2 graphisch dargestellt ist. Diese Spannung kann, wie aus der Abb.
ersichtlich, rechteckförmig aussgebildet sein, oder eine Oberwelligkeit jeder beliebigen
technisch möglichen Spannungsform aufweisen. Diese Spannung U liegt über die Zuleitungen
5 und 6 an der Kathode 4 und der Anode 3 an und bewirkt einen Stromfluss durch den
Elektrolyten. Der zeitliche Verlauf dieses Stromflusses i ist in Figur 3 graphisch
dargestellt.
[0032] Wie Figur 2 zeigt, ist die vom Spannungsversorgungsgerät 7 gelieferte Spannung während
jedes einzelnen Spannungsimpulses konstant, sie bleibt zudem für die gesamte Anodisierungszeit
auf dem selben Wert. Das Stromversorgungsgerät 7 hat eine Strombegrenzung, die während
einer Zeit t, bis t
4 den Strom begrenzt, so daß auch die Stromimpulse annähernd rechteckförmig sind. Wird
ohne Strombegrenzung gearbeitet, so beginnt die Stromkurve direkt nach der Zeit t
4 abzusinken. Zweckmäßigerweise wird eine innerhalb des Spannungsversorgungsgeräts
7 erzeugte Gleichspannung zwischen 20 und 60 Volt durch einen Schalter so ein-und
ausgeschaltet, daß sich der in Figur 2 gezeigte Spannungsverlauf ergibt. Die Einschaltzeiten
t, bis t
2 liegen dabei erfindungsgemäß zwischen 0,1 und 3 Sekunden, die Pausenzeiten t
2 bis t
3 liegen zwischen 0,1 und 2 Sekunden. Dabei liegt das Verhältnis von Betriebs- zu Pausenzeiten
etwa im Bereich von 0,5 bis 5, im gezeigten Ausführungsbeispiel ist dieses Verhältnis
2.
[0033] Die ersten Stromimpulse sind bis zur Zeit t
4 wie bereits erläutert und durch die automatische Strombegrenzung bedingt, konstant.
Bedingt durch den Aufbau der Oxidschicht, wie er aus Figur 4 ersichtlich ist, und
der damit verbundenen Erhöhung des Durchgangswiderstandes dieser Oxidschicht nimmt
der Strom i beginnend mit der Zeit t
4 kontinuierlich ab, da die Spannung U entsprechend Figur 2 konstant ist. Dementsprechend
nimmt die Schichtdicke (Figur 4) während der Zeit t, bis t
4 annahernd konstant zu. Mit geringer werdendem Strom i wird die Schichtdickenzunahme
abnehmen.
[0034] Mit dem erfindungsgemäßen Verfahren kann, wie in Fig. 3 dargestellt, auch beispielsweise
in der Zeit t, bis t
4 über die gesamte Anodisationszeit mit Stromkonstanz der Stromimpulse oder mit Spannungskonstanz
beginnend mit der Zeit t
4 bis t
5 anodisiert werden.
[0035] In der Figur 5 ist die Temperaturerhöhung gegenuber dem Ausgangszustand dargestellt.
Die Temperaturerhöhung in der Schicht steigt während der Zeit t, bis t
4 an und schwankt dann um einen konstanten Wert.
[0036] Die in den Figuren 2 bis 5 wiedergegebenen Kurven sollen rein schematisch die erfindungsgemäße
Impulsstromtechnik verdeutlichen. Die Form der Spannung und des Stromes, insbesondere
die Rechteckform, entspricht nicht immer dem technisch Erreichbaren. Häufig erfolgen
die Spannungs- und Stromanstiege nicht linear von 0 auf den Nennwert, ebenfalls sind
die Abfälle am Ende des Impulses nicht immer so scharf, wie dargestellt. Bei vielen
Versuchen ergab sich, daß die Anstiegszeit und die Abfallszeit etwa bei 1/10 Sekunde
liegt. Die Kurvenform hat jedoch keinen Einfluss auf das Anodisationsergebnis.
[0037] Das erfindungsgemäße Verfahren ermöglicht es, trotz sehr hoher Impulßstromdichten
von maximal 80 A/dm
2 sehr dünnwandige Werkstücke wie solche mit scharfen Kanten und Ecken ohne Verbrennungserscheinungen
zu anodisieren. Das erfindungsgemäße Verfahren zeichnet sich dadurch aus, daß die
Anodisation direkt mit einer hohen Stromdichte begonnen wird. Der Strom kann jedoch
gegebenenfalls wie in Figur 3 gezeigtbegrenzt werden.
[0038] Um die Unterschiede und Vorteile des erfindungsgemäßen Verfahrens gegenüber dem bekannten
Verfahren zu ermitteln, wurden eine große Anzahl von vergleichenden Untersuchungen
durchgeführt Zielsetzung dieser Versuche war dabei, unter ansich konstanten, Anodisationsbedingungen
(wie Elektrolytart und zusammensetzung, Badabmessungen, Elektrolyttemperatur, Badbewegung
etc) den Einfluss des Anodisierstroms auf die Schichtbildung und Schichtqualität zu
untersuchen.
[0039] Als Anodisationsmaterial dienten technische Werkstoffe verschiedener Aluminiumlegierungen,
insbesondere von Aluminiumlegierungen mit höherem Kupfergehalt.
Beispiel 1
[0040] Für dieses Beispiel wurden unterschiedliche Werkstücke aus verschiedenen Stoffen
wie z.B.
1. AICuMg 2: Cu 4,3 % Mg 1,6 %
2. AICuMgPb: Cu 4,4 % Mg 1,4 % Pb 1,5 %
3. AICu4Ni2Mg: Cu 4,1 % Ni 2,0 % Mg 1.5 %
4. AICu5Ni1,5: Cu 5,3 % Ni 1,6 %
5. AISi17CuMg: Si 18,8 % Cu 1;4 % Mg 1,3 %
6. AlMgSi1: Si 1,1 % Mg 0,8 % untersucht.
[0041] Dabei wurden die folgenden vier Verfahren verwendet:
1. Gleichstrom-Verfahren. Die Versuche wurden mit reinem Gleichstrom bei einer Restwelligkeit
von etwa 3 % unter Stromkonstanz, durch automatische Nachregelung der Anodisationsspannung
durchgeführt.
2. Polarisierter pulsierender Gleichstrom. Die Stromimpuls dauer betrug bei einer
Frequenz von 50 Hz etwa 50 %. Die Stromkonstanz wurde durch Handregelung der Spannung
eingehalten. Dieses zweite Verfahren ist dem aus der US-PS-2 920 018 bekannten Verfahren
ähnlich.
3. Wechselstrom-überlagerter Gleichstrom. Die Versuche wurden mit Stromkonstanz durchgefuhrt.
Bei einer Frequenz von 50 Hz betrug die Restwelligkeit etwa 30 %. Dieses dritte Verfahren
entspricht im wesentlichen dem aus der US-PS-3 857 766 bekannten Verfahren.
4. Impulsstromverfahren nach der Erfindung. Diese Versuche wurden mit konstanter Spannung
durchgefuhrt, die jeweils manuell auf den gewunschten Sollwert eingestellt wurde.
Das Verhältnis der Einschalt- zu den Ausschaltzeiten betrug für alle Versuche 2,0.
Gemessen wurde der Effektivstrom.
[0042] In den folgenden drei Tabellen sind typische Messergebnisse zusammengefasst.
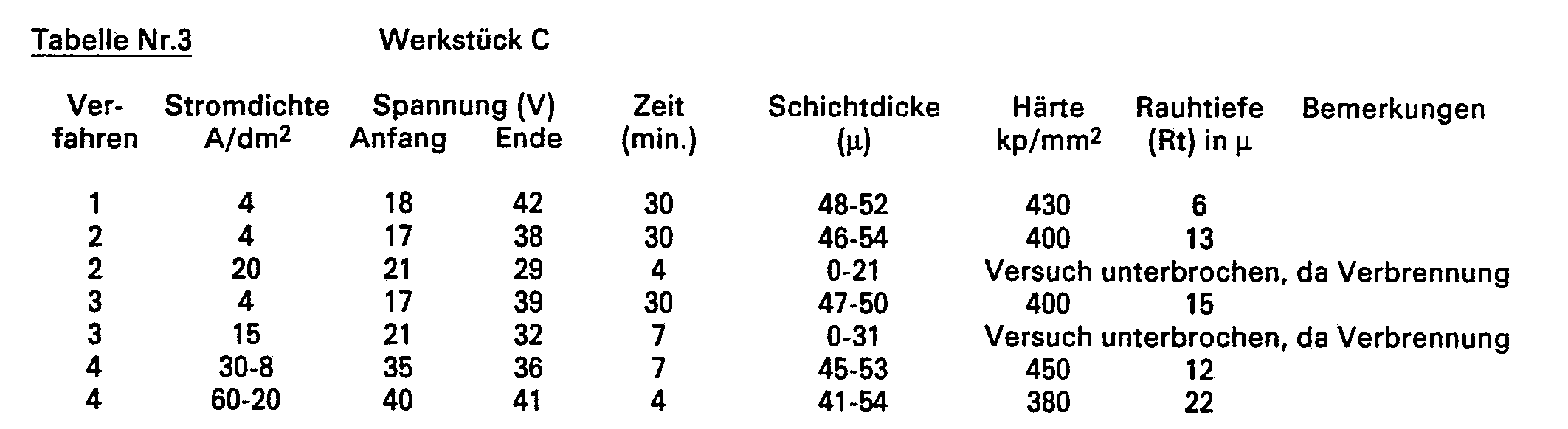
Die in den Tabellen 1 und 2 zusammengefaßten Versuchsergebnisse zeigen deutlich, daß
unter den gewählten Versuchsbedingungen eine Anodisation von Aluminiumlegierungen
mit hohen Gehalten an elektrochemisch edleren Metallen nicht möglich ist, wenn nach
dem ersten Verfahren, also mit Gleichstrom, gearbeitet wird.
[0043] Als besonders vorteilhaft zeigt sich das erfindungsgemäße Verfahren. Als einziges
Verfahren ermöglicht es, alle Werkstücke ohne Verbrennungserscheinungen bei hoher
Stromdichte und kurzen Anodisationszeiten zu oxydieren. Ferner zeigen die Tabellen,
daß mit dem erfindungsgemäßen Veifahren die Schichtqualitäten verbessert werden können,
auch solcher AI-Legierungen mit niedrigen Gehalten an elektrochemisch edleren Metallen,
wie dies die Tabelle 3 zeigt.
Beispiel 2
[0044] Neben dem beschriebenen Verfahren der diskontinuierlichen Anodisation in Bädern erweist
sich das erfindungsgemäße Verfahren als besonders vorteilhaft für die kontinuierliche
Anodisation. Unter der kontinuierlichen Anodisation ist die Anodisation von Bändern
oder Werkstücken zu verstehen, die kontinuierlich durch das Anodisationsbad und gegebenenfalls
durch Spül-oder Nachverdichtungsbäder gezogen werden.
[0045] Während bei der diskontinuierlichen Anodisation, wie beschrieben, mit dem Gleichstromverfahren
die Stromdichte durch Regelung der Spannung konstant gehalten wird, ist dies bei der
kontinuierlichen Anodisation nicht möglich. Bei der kontinuierlichen Anodisation besteht
nur die Möglichkeit, die Spannung konstant zu halten, während die Stromdichte bei
Entritt des bandes oder Werkstückes sehr hoch ist und durch den Aufbau einer Oxidschicht
mit der Verweilzeit stark abnimmt, so daß die Stromdichte kurz vor dem Austritt aus
dem Bad sehr gering ist. Die angelegte Spannung ist somit stark begrenzt von der Stromdichte
am Anfang des Eintritts des Bandes oder Werkstückes in das Bad, um Verbrennungen zu
vermeiden, die durch die Beschränkung des Abtransportes der Joule'schen Wärme mittels
des bewegten Elektrolyten gegeben ist.
[0046] Andererseits ist durch die Beschränkung der angelegten Spannung somit auch die maximal
erzielbare Schichtdicke begrenzt. Mit dem erfindungsgemäßen Verfahren konnte, wie
beschrieben, gezeigt werden, daß sehr hohe Spannungen und daraus resultierende sehr
hohe Stromdichten möglich sind.
[0047] Bei Eintritt des Bandes oder Werkstückes in das Bad ist die Stromdichte, bedingt
durch die hohe angelegte Spannung, sehr hoch und kann Werte bis zu 80 A/dm
2 aufweisen. In der darauf folgenden Strompause jedoch wird die Joule'sche Wärme durch
den bewegten Elektrolyten abtransportiert und außerdem werden, wie beschrieben, die
Polarisationsspannungen abgebaut.
[0048] Durch den Prozess des erfindungsgemäßen Impulsstromverfahrens ist es somit möglich,
die Anodisationszeit erheblich zu verringern, so daß bei bestehenden Bandanodisationsanlagen
der Durchsatz erheblich gesteigert werden kann, wenn die gleiche Schichtdicke erzielt
werden soll.
[0049] Ferner besteht die Möglichkeit, dicke Schichten von über 30 11m zu erreichen, wie
sie in den meisten Fällen für die Hartanodisation gewünscht werden.
[0050] Besonders vorteilhaft lassen sich mit dem erfindungsgemäßen Verfahren außerdem Aluminiumlegierungen
mit hohen Anteilen an elektrochemisch edleren Legierungselementen kontinuierlich beschichten.
[0051] Für den Versuch wurde eine Aluminiumfolie aus AIMg1 (Abmessung: Dicke 1,0 mm, Breite
300 mm, Länge 500 mm) in einen bewegten Elektrolyten mit einer Absenkgeschwindigkeit
von 0,2 m/min. eingebracht und nach voll ständigem Absenken der Folie im Elektrolyten
die Anodisation 2 Minuten fortgesetzt. Die angelegte Spannung betrug 35 Volt und die
Stromeinschaltzeit betrug 0,4 Sekunden, die Ausschaltzeit 0,2 Sekunden.
[0052] Die Probefolie zeigte trotz der hohen anfänglichen Stromdichte von etwa 90 A/dm
2 keine Verbrennungen. Die Schichtdicke betrug 40 bis 55 µm, wobei natürlich der Teil
der Folie mit der längsten Anodisationszeit die größte Schichtdicke aufwies.
1. Verfahren zur anodischen Oxydation von Werkstücken aus einer Aluminiumlegierung,
insbesondere mit hohem Gehalt an Kupfer und/oder edleren Metallen, wobei die Werkstücke
in einem bewegten wässrigen Elektrolyten zusammen mit einer oder mehreren Kathoden
angeordnet werden und eine Spannung im wesentlichen periodisch zum Erzeugen von kurzzeitigen
Stromimpulsen mit hohem Stromfluss an die Werkstücke und die Kathode (n) angelegt
wird, dadurch gekennzeichnet, dass die Spannung jeweils solange eingeschaltet bleibt,
wie ein merklicher Aufbau der Oxidschicht erfolgt und anschliessend solange ausgeschaltet
wird, bis die erzeugte Jouie'sche Wärme im wesentlichen abgeführt ist.
2. Verfahren nach Anspruch 1, dadurch gekennzeichnet, dass ein Spannungsimpuls von
10 bis 80 V, insbesondere 20 bis 60 V angelegt wird.
3. Verfahren nach Anspruch 1 oder 2, dadurch gekennzeichnet, dass die Zeitdauer der
Spannungsimpulse 0,1 bis 3 s, insbesondere 0,1 bis 1,5 s beträgt.
4. Verfahren nach einem der Ansprüche 1 bis 3, dadurch gekennzeichnet, dass die Dauer
der Ausschaltzeit zwischen zwei Spannungsimpulsen 0,1 bis 2 s, insbesondere 0,1 bis
1 s beträgt.
5.Verfahren nach einem der Ansprüche 1 bis 4, dadurch gekennzeichnet, daß das Verhältnis
von Zeitdauer eines Spannungsimpulses zur Zeitdauer einer Ausschaltzeit 0,5 bis 5
beträgt.
6. Verfahren nach einem der Ansprüche 1 bis 5, dadurch gekennzeichnet, daß die Stromdichte
während eines Spannungsimpulses konstant gehalten wird.
7. Verfahren nach einem der Ansprüche 1 bis 6, dadurch gekennzeichnet, daß die Stromdichte
während der Dauer der anodischen Oxydation konstant gehalten wird.
8. Verfahren nach einem der Ansprüche 1 bis 5, dadurch gekennzeichnet, daß die Spannung
während eines Spannungsimpulses und während der Dauer der anodischen Oxydation konstant
gehalten wird.
9. Verfahren nach einem der Ansprüche 1 bis 8, dadurch gekennzeichnet, daß zunächst
die Stromdichte und anschließend die Spannung während der Dauer der anodischen Oxydation
konstant gehalten wird.
10. Verfahren nach Anspruch 8, dadurch gekennzeichnet, daß man die Werkstücke, insbesondere
bandförmiges Material, durch das Elektrolytbad durchlaufen läßt.
11. Verfahren nach einem der Ansprüche 1 bis 10, dadurch gekennzeichnet, daß die Spannung
nach einem Spannungsimpuls solange ausgeschaltet bleibt, bis die vorzugsweise am Werkstück
gemessene Temperatur unterhalb eines Schwellwerts gesunken ist.
1. Process for anodic oxidation of workpieces made from an aluminium alloy, particularly
with high copper and/or nobler metal content, the workpieces being arranged in a moving
aqueous electrolyte together with one or more cathodes and a voltage being applied
mainly periodically to produce current pulses of short duration with high current
conduction to the workpieces and the cathode(s), characterised in that the voltage
remains switched on each time as long as a noticeable build-up of the oxide layer
results and then is switched off until the Joule effect produced is mainly eliminated.
2. Process according to Claim 1, characterised in that a voltage pulse of 10 to 80
V, particularly 20 to 60 V is applied.
3. Process according to Claim 1 or 2, characterised in that the duration of the voltage
pulse is 0.1 to 3 s, particularly 0,1 to 1,5 s.
4.Process according to one of Claims 1 to 3, characterised in that the duration of
the switch-off time between two voltage pulses is 0,1 to 2 s, particularly 0,1 to
1 s.
5. Process according to one of Claims 1 to 4, characterised in that the ratio of duration
of a voltage pulse to the duration of a switch-off time is 0,5 to 5.
6. Process according to one of Claims 1 to 5, characterised in that the current density
during a voltage pulse is kept constant.
7. Process according to one of Claims 1 to 6, characterised in that the current density
in the duration of the anodic oxidation is kept constant.
8. Process according to one of Claims 1 to 5, characterised in that the voltage during
a voltage pulse and in the duration of the anodic oxidation is kept constant.
9. Process according to one of Claims 1 to 8, characterised in that first the current
density and then the voltage is kept constant in the duration of the anodic oxidation
10. Process according to Claim 8, characterised in that the workpieces, particularly
material in strip form, are made to pass through the electrolytic bath.
11. Process according to one of Claims 1 to 10, characterised in that the voltage
after a voltage pulse remains switched off until the temperature, preferably measured
on the workpiece, has fallen below a threshold value.
1. Procédé d'oxydation anodique de pièces à usiner en un alliage d'aluminium, notamment
à haute teneur en cuivre et/ou en métaux plus nobles, dans lequel les pièces à usiner
sont disposées conjointement avec une ou plusieurs cathodes dans un électrolyte aqueux
en mouvement et une tension est appliquée aux pièces et à la cathode ou aux cathodes
de façon essentiellement périodique pour produire des impulsions de courant de courte
durée avec un flux de courant élevé, caractérisé en ce que la tension est maintenue
appliquée dans chaque cas aussi longtemps qu'une édification notable de la couche
d'oxyde s'effectue, puis elle cesse d'être appliquée jusqu'à ce que la chaleur produite
par effet Joule soit essentiellement dissipée.
2. Procédé suivant la revendication 1, caractérisé en ce qu'on applique une impulsion
de tension de 10 à 80 volts, notamment de 20 à 60 volts.
3. Procédé suivant la revendication 1 ou 2, caractérisé en ce que la durée des impulsions
de tension s'élève à une valeur de 0,1 à 3 secondes, notamment de 0,1 à 1,5 seconde.
4. Procédé suivant l'une des revendications 1 à 3, caractérisé en ce que la durée
de coupure entre deux impulsions de tension est de 0,1 à 2 secondes, notamment de
0,1 à 1 seconde.
5. Procédé suivant l'une des revendications 1 à 4, caractérisé en ce que le rapport
de la durée d'une maintenue constante pendant la durée de l'oxydation anodique.
6. Procédé suivant l'une des revendications 1 à 5, caractérisé en ce que la densité
de courant pendant une impulsion de tension est maintenue constante.
7. Procédé suivant l'une des revendications 1 à 6, caractérisé en ce que la densité
de courant est maintenue constante pendant la durée de l'oxydation anodique.
8. Procédé suivant l'une des revendications 1 à 5, caractérisé en ce que la tension
est maintenue constante pendant une impulsion de tension et pendant la durée de l'oxydation
anodique.
9 Procédé suivant l'une des revendications 1 à 8, caractérisé en ce que, tout d'abord
la densité de courant puis la tension pendant la durée de l'oxydation anodique sont
maintenues constantes.
10. Procédé suivant la revendication 8, caractérisé en ce qu'on fait défiler les pièces
usinées, notamment une matière en forme de bande, dans le bain électrolytique.
11. Procédé suivant l'une des revendications 1 à 10, caractérisé en ce que la tension
cesse d'être appliquéeaprès une impulsion de tension jusqu'à ce que la température
mesurée de préférence sur la pièce se soit abaissée au-dessous d'une valeur limite.