[0001] Die Erfindung betrifft ein Verfahren zum Erzeugen von Phosphatüberzügen auf Oberflächen
von kaltgewalztem Stahl, ein- oder zweiseitig verzinktem Stahl im Tauchen mit einer
Zink, Phosphat, Nitrat and Fluorid enthaltenden Phosphatierungslösung.
[0002] Es ist seit langem bekannt, auf Metalloberflächen Phosphatüberzüge, die u.a. eine
gute Basis für anschließend aufgebrachten Lack bilden, aufzubringen. Hierbei spielen
insbesondere Zink-Phosphatüberzüge eine besondere Rolle. Derartige Überzüge können
aus Phosphatierungslösungen mit vergleichsweise hohem Zinkgehalt erzeugt werden (Normalzink-Technologie).
In den letzten Jahren haben jedoch Phosphatierverfahren, die Lösungen mit relativ
geringen Zingehalten einsetzen, zunehmend an Bedeutung gewonnen (Niedrigzink-Technologie).
Hierbei liegen die Zinkkonzentrationen im allgemeinen im Bereich von 0,9 bis 1,5 g/l.
Mit abnehmendem Zinkgehalt wird dabei das Verhältnis Phosphophyllit (P) (Zn₂Fe(PO₄)₂
. 4H₂O) zu Hopeit (H) (Zn₃(PO₄)₂ . 4H₂O) bzw. P/P+H höher, was sich auf eine sehr
hohe Lackfilmqualität auswirkt.
[0003] Bei der Erzeugung des Phosphatüberzuges ist die Behandlungstemperatur von wesentlichem
Einfluß. Im allgemeinen werden in Abhängigkeit von der zu behandelnden Oberfläche
und den Anforderungen an die Lackfilmqualität Temperaturen oberhalb 40°C angewendet.
Die Anwendung niedrigerer Temperaturen kann zu Schwierigkeiten bei der Erzeugung von
Phosphatüberzügen, die den gestellten Anforderungen gerecht werden sollen, führen.
Beispielsweise können Überzüge entstehen, die ein zu geringes Schichtgewicht besitzen,
nicht deckend sind, grobe Kristalle aufweisen und/oder zum Gelbrost tendieren.
[0004] Zwar lassen sich die bei niedrigen Phosphatiertemperaturen auftretenden Probleme
im gewissen Ausmaß durch Erhöhung des Zinkgehaltes kompensieren, jedoch werden dann
nicht die an sich angestrebten phosphophyllitreichen Phosphatüberzüge mit ihren günstigen
Auswirkungen auf die Lackfilmqualität erzielt.
[0005] Aufgabe der Erfindung ist es, ein Verfahren zur Erzeugung von Phosphatüberzügen auf
Oberflächen von kaltgewalztem Stahl, ein- oder zweiseitig verzinktem Stahl bereitzustellen,
das die Anwendung möglichst niedriger Arbeitstemperaturen gestattet und dennoch zu
Phosphatüberzügen von hoher Qualität, insbesondere hinsichtlich Aussehen des Phosphatüberzuges,
Schichtgewicht, Kristallgröße und Phosphophyllitanteil führen sowie - nach der Lackierung
- hohen Korrosionswiderstand und hohe Lackhaftung vermitteln. Die Phosphatüberzüge
sollen mithin im wesentlichen die gleiche Qualität aufweisen wie die, die bei höheren
Temperaturen erzeugt werden.
[0006] Die Aufgabe wird gelöst, indem das Verfahren der eingangs genannten Art entsprechend
der Erfindung derart ausgestattet wird, daß man die Oberflächen in eine Phosphatierungslösung
einer Temperatur im Bereich von 15 bis 39°C taucht, die
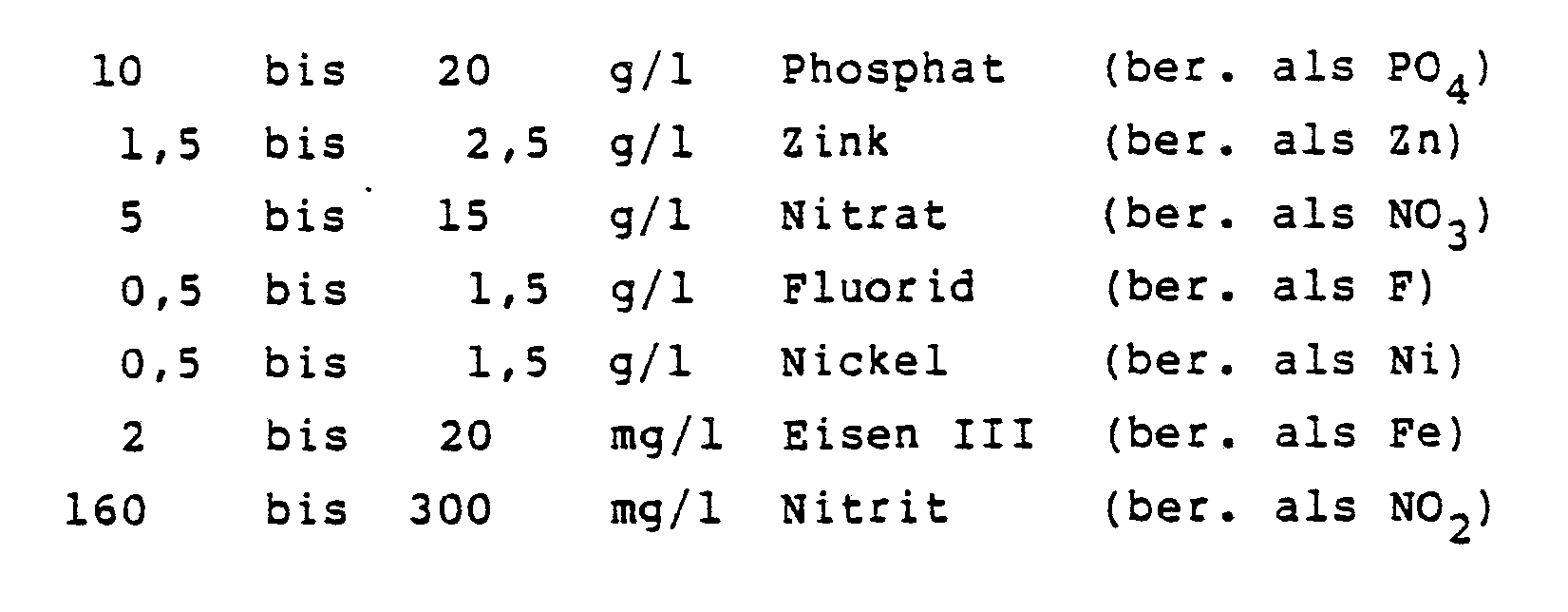
enthält und in der das Gewichtsverhältnis von Zn : PO₄ auf (0,08 bis 0,21) : 1 und
der Gehalt an freier Säure (FS) auf einen durch die untere Grenzkurve FS = 0,2 . Zn
- 0,4 und die obere Grenzkurve FS = 0,4 . Zn - 0,5 festgelegten Wert eingestellt ist.
[0007] Das durch die Grenzkurven und die zulässigen Zinkgehalte festgelegte Trapez ist in
der Figur wiedergegeben.
[0008] Bevor die Metalloberflächen dem erfindungsgemäßen Phosphatierverfahren unterworfen
werden, werden sie wie üblich gereinigt und aktiviert. Zur Aktivierung dienen wässrige
Phosphatlösungen, die eine kolloidale Titanverbindung enthalten.
[0009] Die Bedeutung der Konzentrationsgrenzen für die Bestandteile der Phosphatierungslösung
ergibt sich aus folgendem.
[0010] Unterschreitet die Phosphatkonzentration 10 g/l, werden die Phosphatüberzüge dünn
und ungleichmäßig. Bei Konzentrationen über 20 g/l wird die Überzugsqualität nicht
mehr verbessert, statt dessen der Chemikalienverbrauch
vergrößert.
[0011] Zinkkonzentrationen unter 1,5 g/l führen nicht zu Phosphatüberzügen mit dem erwünschten
Schichtgewicht, solche über 2,5 g/l lassen zu schwere Schichten entstehen. Darüber
hinaus wird der erwünscht hohe Phosphophyllitanteil nicht erhalten. Die Folge ist,
daß sich Lackhaftung und Korrosionswiderstand verschlechtern.
[0012] Falls das Gewichtsverhältnis Zn/PO₄ unter den Wert von 0,08 : 1 fällt, wird die Phosphatschichtausbildung
beeinträchtigt. Werte oberhalt 0,21 : 1 führen zu gröberen Kristallen.
[0013] Nitrat dient als Oxidationsmittel. Ein Gehalt unter 5 g/l ist mit einem Verlust des
Oxidationspotentials verbunden, ein solcher über 15 g/l bringt keine Verbesserung
der Wirkung. Er würde lediglich die Wirtschaftlichkeit des Verfahrens beeinträchtigen.
[0014] Fluorid ist sowohl für die gleichmäßige Anätzung der Stahloberfläche als auch für
die Ausbildung eines dichten Phosphatüberzuges verantwortlich. Außerdem wird die Schichtbildung
auf bestimmten Qualitäten von verzinktem Stahl, insbesondere schmelztauchverzinktem
Stahl mit Aluminiumgehalten, in der Zinkschicht verbessert. Als Quelle für Fluorid
können komplexe Fluoride, wie Fluorosilikat, Fluoroborat und Fluorozirkonat, aber
auch einfache Fluoride bzw. Mischung komplexer und einfacher Fluoride verwendet werden.
Bei einer Konzentration unter 0,5 g/l (ber. als F) ist die Ätzwirkung ungleichmäßig
und der Phosphatüberzug nicht ausreichend dicht. Bei Konzentrationen oberhalb 1,5
g/l wird der Phosphatüberzug zu dünn und die erwünschten Eigenschaften werden nicht
erzielt.
[0015] Auch der Nickelgehalt wirkt sich auf die Ausbildung eines dichten Phosphatüberzuges
aus, darüber hinaus verbessert er den Korrosionswiderstand und die Haftung des nachfolgend
aufgebrachten Lackes. Nickelkonzentrationen unter 0,5 g/l lassen die erwünschte Verdichtung
der Phosphatkristalle nicht entstehen, auch tritt die mögliche Verbesserung des Korrosionswiderstandes
der Lackhaftung nicht ein. Höhere Konzentrationen als 1,5 g/l bringen keine Verbesserung
der Wirkung.
[0016] Der Eisen III-Gehalt bewirkt die Aufrechterhaltung einer gewissen Übersättigung in
der Phosphatierungslösung, d.h. läßt eine Erhöhung des pH-Wertes, bei dem die Abscheidung
von Phosphat erfolgt, zu. Dadurch wird die Ausbildung des Phosphatüberzuges erleichtert.
Sofern die Eisen III-Konzentration unter 2 mg/l liegt, ist der Effekt noch nicht genügend
ausgeprägt. Bei Konzentrationen oberhalb 20 mg/l neigen die Phosphatierungslösungen
zur Schlammbildung und werden damit hinsichtlich ihrer Fähigkeit zur Ausbildung von
Phosphatüberzügen beeinträchtigt.
[0017] Der Nitritgehalt von 160 bis 300 mg/l, der wesentlich größer ist als der von Phosphatierungsbädern,
die bei höheren Temperaturen zum Einsatz kommen, ist maßgeblich für die Eisenauflösung
von der Stahloberfläche und die Abscheidung von Phosphophyllit verantwortlich. Nur
bei Einhaltung des angegebenen Bereiches ist Gewähr für den erwünscht hohen Phosphophyllitanteil
im Überzug und für die hohe Qualität des Überzuges gegeben. Außerdem verringert sich
bei niedrigerem Nitritgehalt die Bildungsgeschwindigkeit des Phosphatüberzuges. Bei
höherem Nitritgehalt besteht eine Tendenz zur Ausbildung von Eisen-Phosphatüberzügen.
[0018] Der Gehalt an Nitritpunkten wird in der Regel nach der Saccharometermethode bestimmt.
Hierzu werden 50 ml Badlösung mit 2 bis 5 g Sulfaminsäure versetzt. Die dabei gebildete
Gasmenge in ml ist gleich der Punktzahl. Ein Gas-Punkt entspricht einem Gehalt von
46 mg/l NO₂ in der Phosphatierungslösung.
[0019] Der Gehalt der Phosphatierungslösung an freier Säure hängt im wesentlichen von der
Zinkkonzentration ab. Je höher der Zinkgehalt ist, desto höher ist der Gehalt an freier
Säure einzustellen. Die exakte und bei Einsatz des erfindungsgemäßen Verfahrens einzustellende
freie Säure ergibt sich aus der Figur. Sofern ihr Gehalt unter der unteren Grenzlinie
liegt, wird die Phosphatierungslösung instabil und es beginn en sich Ablagerungen
zu bilden. Ist der Gehalt an freier Säure oberhalb der oberen Grenzlinie, ist die
Phosphatüberzugsausbildung verzögert und es ist schwierig, dichte Phosphatüberzüge
zu erhalten. Das schraffierte Feld veranschaulicht den zulässigen Gehalt an freier
Säure, bezogen auf die jeweilige Zinkkonzentration.
[0020] Zur Bestimmung der freien Säure wird eine 10 ml Badprobe gegen Bromphenolblau als
Indikator titriert. Falls bei Zugabe des Indikators die Lösung gelb bis gelbgrün ist,
wird mit 0,1 n Natronlauge bis zum Umschlag nach blau titriert. Ist die Badprobe nach
Indikatorzugabe blauviolett, erfolgt die Titration mit 0,1 n Schwefelsäure bis zum
Umschlag nach blau. In diesem Fall ist der erhaltene Wert für die freie Säure negativ.
Die Punktezahl an freier Säure ist gleich dem jeweiligen Verbrauch an Titrationslösung
in ml.
[0021] Gemäß einer bevorzugten Ausgestaltung der Erfindung taucht man die Metalloberflächen
in eine Phosphatierungslösung, die zusätzlich 0,2 bis 1 g/l Mangan (ber. als Mn) enthält.
Ein derartiger Mangangehalt wirkt sich insbesondere positiv auf die Lackhaftung bei
hoher Nässeeinwirkung aus, so daß Objekte, die insoweit beansprucht werden, gemäß
dieser bevorzugten Ausgestaltung behandelt werden sollten. Bei geringeren Konzentrationen
als 0,2 g/l ist die genannte Wirkung noch nicht hinreichend ausgeprägt. Konzentrationen
über 1 g/l führen insbesondere zu einer Verringerung der Ausbildungsgeschwindigkeit
des Phosphatüberzuges.
[0022] Eine weitere vorteilhafte Ausgestaltung der Erfindung besteht darin, die Oberflächen
in eine Phosphatierungslösung einer Temperatur im Bereich von 20 bis 30°C zu tauchen.
[0023] Die Einwirkungsdauer der Phosphatierungslösung sollte im allgemeinen 90 bis 180 sec.
bei der Behandlung von kaltgewalztem Stahl und 30 bis 180 sec. bei verzinktem Stahl
betragen. Sofern Werkstücke behandelt werden sollen, die Bereiche aus kaltgewalztem
Stahl und aus verzinktem Stahl (Verbundmetalle) aufweisen, empfiehlt sich die Anwendung
der Behandlungsdauer für kaltgewalzten Stahl.
[0024] Der besondere Vorzug des erfindungsgemäßen Verfahrens besteht darin, daß bei Temperaturen,
die praktisch Raumtemperatur sind, qualitativ hochwertige Phosphatüberzüge erhalten
werden, die die Eigenschaften eines nachträglich aufgebrachten Lackes vorteilhaft
beeinflussen. Die niedrigen Temperaturen ihrerseits haben den Vorteil, daß der apparative
Aufwand für die Beheizung der Phosphatierbäder und der Energieaufwand selbst erheblich
reduziert werden können. Darüber hinaus sind die zulässigen Toleranzen hinsichtlich
Temperatur und Zinkkonzentration vergleichsweise groß, so daß das Verfahren einfach
zu führen ist.
[0025] Die Erfindung wird anhand der folgenden Beispiele beispielsweise und näher erläutert.
Beispiele
[0026] Es wurden Stahlbleche der Qualität JIS-G-3141, SPCC (im folgenden mit SPC bezeichnet)
und beidseitig feuerverzinkte Stahlbleche (im folgenden mit "plated" bezeichnet) behandelt.
[0027] Die Bleche wurden mit einem konventionellen alkalischen Reiniger (pH-Wert 12, Punktezahl
19±1) bei 40±2°C im Tauchen 180 sec. behandelt, mit Leitungswasser von Raumtemperatur
20 sec. bespritzt, danach mit einer 1 g/l Titanphosphat enthaltenden Aktivierungslösung
von Raumtemperatur durch 30 sec. langes Tauchen konditioniert und anschließend 120
sec. im Tauchen phosphatiert (ausgenommen Vergleichsbeispiel 3, bei dem die Phospatierung
im Spritzen erfolgte). Die Zusammensetzung der jeweils verwendeten Phospatierungslösung
ist in den nachfolgenden Tabellen angegeben.
[0028] Im Anschluß an die Phosphatierung wurde zunächst mit Leitungswasser von Raumtemperatur
30 sec., dann mit vollentsalztem Wasser (elektrische Leitfähigkeit 0,2 µS x cm⁻¹)
für die Dauer von 20 sec. jeweils im Spritzen gespült und bei 100°C während einer
Dauer von 180 sec. getrocknet.
[0029] Der Lackaufbau erfolgt in drei Stufen. Zunächst wurde ein kationischer Elektrotauchlack
(Elecron 9400 der Fa. Kansai Paint Co., Ltd. )
aufgebracht.
[0030] Badtemperatur 28°C; Spannung 250 V
[0031] Behandlungsdauer 180 sec.
[0032] Die Schichtdicke betrug 20 µm.
[0033] Nach einer Spritzbehandlung zunächst mit Leitungswasser (20 sec.), dann mit vollentsalztem
Wasser der o.g. Beschaffenheit (5 sec.) wurde der Lackfilm bei 175°C für die Dauer
von 30 min. eingebrannt.
[0034] Die Zwischenschicht wurde mit einem Lack auf Basis Melamin/Alkydharz (Amilac N-2
Sealer der Fa. Kansai Paint Co., Ltd.) im Spritzverfahren mit Luft als Treibmittel
erzeugt. Der Film einer Dicke von 30 µm wurde nach einer Wartezeit von 10 bis 20 min.
bei 140°C während 30 min. eingebrannt.
[0035] Als Decklack diente ein Lack auf Melamin/Alkydharzbasis (Amilac White M3 der Fa.
Kansai Paint Co., Ltd.), der in der vorgenannten Weise, jedoch mit einer Filmdicke
von 40 µm aufgebracht wurde. Die Folgebehandlung geschah wie vorstehend erwähnt.
[0036] Die Bewertung des Phosphatüberzuges erfolgte unter den Gesichtspunkten Aussehen des
Überzuges, Schichtgewicht, Kristallgröße und Phosphophyllitanteil im Phosphatüberzug
(bei der Behandlung von Stahlblech).
[0037] Es bedeuten bei der Beurteilung des Aussehens des Phosphatüberzuges:
o es liegt ein dichter gleichmäßiger Überzug
x es liegt ein ungleichmäßiger Überzug mit Bildung von Gelbrost
vor.
[0038] Zur Ermittlung des Schichtgewichtes des Phosphatüberzuges wurde die Gewichtsdifferenz
zwischen phosphatierten und vom Phosphatüberzug befreiten Blechen ermittelt. Bei den
Stahlblechen (SPC) erfolgte die Ablösung des Phosphatüberzuges mit einer Chromsäurelösung
einer Konzentration von 50 g/l. Die feuerverzinkten Bleche (plated) wurden mit einer
Lösung, die durch Auffüllen von 20 g Ammoniumdichromat und 480 g konzentierter Ammoniaklöung
mit destilliertem Wasser auf 1 l erhalten worden war, vom Phosphatüberzug befreit.
Das Schichtgewicht ist in g/m² angegeben.
[0039] Die Messung der Größe der Phosphatkristalle geschah mit einem Elektronenmikroskop
durch zeilenweises Abtasten. Die Kristallgröße ist in µm aufgeführt.
[0040] Der Phosphophyllitanteil im Phosphatüberzug (bei Stahlblechen) wurde nach der Methode
der Röntgendiffractometrie über die Diffractionsintensitäten für die Fläche (100)
beim Phosphophyllit und (020) beim Hopeit ermittelt. Er ist als Verhältnis Phosphophyllit
zu Phosphophyllit + Hopeit (P/P+H) angegeben.
Prüfung des Lackfilmes
Salzsprühtest
[0041] Bleche, die lediglich mit dem kationischen Elektrotauchlack behandelt worden waren,
wurden mit einem Kreuzschnitt versehen und 1000 h dem Salzsprühtest mit einer 5 %igen
Kochsalzlösung gemäß JIS-Z-2371 ausgesetzt. Das Testergebnis ist als Lackunterwanderung
längs der Schnittlinien in mm angegeben.
Zyklischer Haftungstest
[0042] Mit dem kompletten Lackaufbau versehene Bleche wurden nach einer Wartezeit von 24
h 120 h in vollentsalztes Wasser von 40 ± 1°C derart getaucht, daß ein Kontakt der
Bleche miteinander unterblieb. Danach wurde 1 h an der Luft bei Raumtemperatur getrocknet.
[0043] Die Testbleche wurden anschließend unter einem Winkel von 45°C mit dem Lackfilm nach
oben fixiert und der Einwirkung von 100 Schraubenmuttern mit ca. 6 mm Durchmesser
ausgesetzt, die aus einer Höhe von 4,5 m - gerechnet vom Schnittpunkt der Schnittlinien
- durch ein Führungsrohr mit ca. 50 mm innerem Durchmesser fallengelassen wurden (Gesamtgewicht
der Schraubenmuttern 198 ± 0,5 g).
[0044] Anschließend wurden die Bleche dem Salzsprühtest gemäß JIS-Z-2371 für die Dauer von
72 h und dann 92 h lang einer Freiluftbewitterung ausgesetzt.
[0045] Die vorgenannte Behandlungsfolge wurde insgesamt viermal wiederholt, dann wurden
die Bleche nochmals für die Dauer von 72 h dem Salzsprühtest unterworfen. Abschließend
wurden die Testbleche mit einem metallischen Kratzer auf der lackierten Seite von
Korrosionsprodukten und abgelöstem Lack befreit und visuell bewertet. Es bedeuten:
A sehr wenig abgelöster Lack
B wenig abgelöster Lack
C merklich abgelöster Lack
D sehr viel abgelöster Lack
Naßhaftungstest
[0046] Mit dem kompletten Lackaufbau versehene Testbleche wurden 20 Tage in vollentsalztes
Wasser von 40°C getaucht und dann mit einem Gitterschnitt derart versehen, daß 100
Quadrate mit jeweils 2 mm Kantenlänge entstanden. Zur Ermittlung der Lackhaftung wurde
Klebeband auf die die Quadrate aufweisende Fläche aufgedrückt und wieder abgezogen.
Die Bewertung geschah durch Auszählen der auf dem Testblech verbliebenen Lackquadrate.
[0047] Die nachfolgende Tabelle 1 zeigt, daß bei exakter Einhaltung sämtlicher verfahrenswesentlicher
Parameter in jeder Hinsicht hervorragende Ergebnisse erzielt werden. Aus Tabelle 2
geht mit aller Deutlichkeit hervor, daß bereits die Veränderung nur eines Parameters,
selbst die Änderung der Applikationsweise der Phosphatierungslösung, mit erheblichen
Beeinträchtigungen der Qualität des Lackfilmes verbunden ist. Außerdem ergibt sich
aus einem Vergleich von Tabelle 1 mit Beispiel 1 aus Tabelle 2, daß mit dem erfindungsgemäßen
Verfahren trotz Anwendung erheblich niedrigerer Behandlungstemperaturen bei der Erzeugung
des Phosphatüberzuges mindestens ebenso gute Eigenschaften erzielbar sind als wenn
mit höheren Temperaturen entsprechend dem Stand der Technik gearbeitet wird.