[0001] As introduction to the following technical report on a device for the deposition
of metals on objects in suspension, it must be considered that whereas it is not admitted
that certain industrial processes can be made in a routine manner, this leads to new
situations and new layouts that prove valid, without this representing a great complication
in the process studied, and however, they adapt perfectly to the evolutive process
to which the industry is submitted.
[0002] There are quite a few cases that are known and which may be used as example of this
reflection and one of them is the case of paint. For centuries it has been thought
that a paint should have as its base an oil or a resin as filmogenous agent and to
obtain a better application, the paint concept has always been associated with the
concept of solvents or thinners. As the chemical industry began to develop and natural
products were analysed, artificial resins appeared and lastly a large number of products
were synthesized and proved better than the natural and artificial ones because they
were studied with a specific purpose in mind. A great change started in the Sixties
and the innovation, in this field, adopted two different directions: research on paint
that would use water as thinner and paint without thinner.
[0003] All this technological development furthermore purported improvements in quality,
and the possibility of automatically applying these new paints, for which automatic
pistols had to be developed and which concluded by becoming true robots.
[0004] Safety standards also played an important role, both from a point of view of hygiene
and safety, upon eliminating organic inflammable solvents.
[0005] The use of powder paints and varnishes could also be made by immersing the hot metal
parts in them, however the fluidized bed technique had to appear in order that the
part receive the same thickness.
[0006] In steel quenching, fused salts that are difficult to control in terms of their power
of oxidation, have been replaced by furnaces with controlled atmosphere. Recently,
at the ITEB, furnaces heated by propane have been used, because a sufficiently reducive
atmosphere can be obtained that can be used for this purpose, although the furnace
has been designed for ceramics. When a part is to be cooled, in a controlled way,
during quenching, fluidized beds are used with solid particles of high calorific capacity.
[0007] In other words, there is an immense technical capacity that opens the way to new
possibilities for using many products and furthermore, new products emerge to be used
with new techniques.
[0008] This short introduction which could have been extended to many other well known cases,
is simply a support and a justification, by introducing innovator ideas in the Imitation
Jewelry Sector, within the specific activities of the Research Association, which
is a Sector that is quite indifferent when it comes to studying improvements, but
which accepts them fast once their profitability has been proved.
[0009] When presenting the different steps that are involved in applying a layer of gold
to a metal object, we must not forget that in addition to attempting to rationalize
the process, we must consider the properties that the gold film should have, in order
to find a place on a market, as part of a finished product.
[0010] With this process, we have reviewed the possibilities that are offered by the world
market of gilt objects, field of immitation jewelry, and the factors that could help
obtain a good portion of it. The gilding process must be automatized better, and its
quality must be first class in fine layer, less than 1µm.
[0011] Within this conviction and consequent with it we are going to undertake the study
of these two targets, not in their entirety, but in specific acttions. We are
going to study how to eliminate a manual process that consumes a considerable amount
of manpower and at the same time, try to improve the quality of the deposited gold.
For greater clarity we shall recall some of the steps that are followed in gold-plating
pieces for imitation jewelry.
[0012] In the glavanic processes, each piece must be suspended in the bath, using a device
that permits electrical connection between this piece and the cathode. This is achieved
by placing the pieces in frames, called racks, with an insulant cover to eliminate
deposition of metal on them, except at the ends of their arms, bare metal.
[0013] The enormous variety of shapes and sizes of the pieces and other objects that are
to be protected, using metals deposited from their salts that form the galvanic baths,
has made it necessary to use two different processes.
[0014] Those pieces which have a difficult shape or size to be easily held by mechanical
means, are metallized introducing them in rotary platic drums, which have mesh walls
or perforated plate, so that once all the pieces are immersed in the bath, they are
all in contact with it. Inside the drumsk there are electric contacts, in connection
with the cathode, so that all the pieces that turn with the drums, have an electric
contact with one another but are constantly changing the points where the electric
current passes, obtaining a continuous and uniform metal deposition.
[0015] In this way, we can obtain various metallic layers of different metals, overlaid.
[0016] Certain geometric shapes are difficult to cover using this method because they maintain
a prolonged electric contact in one and the same zone and stick together, causing
irregularities and surface flaws. These pieces, along with other larger ones which
would need large size drums, are secured individually in the above-mentioned racks.
There are certain pieces that can be hung from the ends of the arms of the racks with
sufficient guarantee that they will not become detached from here, owing to the stirring
movement of the bath or simply their transfer movement, although the great majority
of these require that each piece be fixed to the rack with a conduction wire, which
is generally brass.
[0017] This process of fixing millions of pieces consumes a considerable amount of labour
which we should try and suppress. This is the basic target of this new Project and
invention which is based on the following facts:
a) The chemical baths and the autocatalytic ones do not require external current for
depositing a metal on another and they are consequently appropriate to be used in
our development.
By autocatalytic bath we mean the composition that the reductive agent has, in solution
and the metal on which we want the deposition to be made does not act as such. A gold
bath is autocatalytic when it deposits gold on a gold surface.
b) The study of the fall of solids in a static fluid and in a fluid in movement will
help to design and built an installation where our objective can be carried out.
THEORETIC BASIS OF THE PROJECT
Vertical free fall of an object in a fluid.
[0019] Let us establish the following hypothesis:
[0020] In a tube full of water (ρ₀=1) let us deposit on its surface a ball having a radius
r and density ρ=1. The ball, deposited at a velocity v=0 will remain in suspension
but will go towards the bottom more quickly if its density ρ is greater.
[0021] Mechanics of Fluids study these phenomena within the specific chapter on "Movement
of solids within a fluid" and in the analysis of the problem, solids that have regular
shapes such as in a sphere are taken, for greater simplicity. However, in the majority
of cases, solids that have irregular shapes are used, and consequently the theoretic
equations should be corrected if we want them to represent true facts. These correction
factors are diffic ult to find through mathematic calculus and largely
depend on the shape of the solid.
[0022] The more complicated is the geometry of the solid, in vertical fall, the greater
will be the resistance that the fluid presents, and consequently, the time of fall
to cover the same distance will also be greater.
[0023] In the simple case that is presented, the fall of flat solids will be experimented
where, generally, the surface/weight ratio is large and consequently it will be necessary
to adapt the laws that govern the fall to suit this fact.
[0024] The study is included in the vertical movement of solids in the interior of liquids
and we start by considering that there is no friction.
[0025] If a solid having density ρ is allowed to fall in a liquid having density ρ₀, such
that ρ₀<ρ, the forces that act are:
Weight = mg = Vµ g Thrust = V ρ g
[0026] The fundamental equation of the dynamic requires that:
F = ma = Vµ a = Weight - thrust
that is to say

that will be the acceleration with which the solid falls. In this case, the problem
is reduced to applying the equations of the uniformally accelerated movement.
[0027] In the case of vertical fall of a solid in a resistant medium, this is studied from
various angles depending on the fall velocity.
I Proportional resistance to the velocity.
II Proportional resistance to the square of the velocity.
III Proportional resistance to powers of velocity superior to 2.
[0028] This third case refers specially to movements of solids at high velocity, such as
projectiles in the air and which are ruled by a standard formula:
R = K v
n
where n = 5 for velocities like that of sound.
[0029] Not considering this possibility III and referring only to I and II.
[0030] In the case where the resistance is proportional to velocity, such as the case of
small velocities, the equation of the movement is:
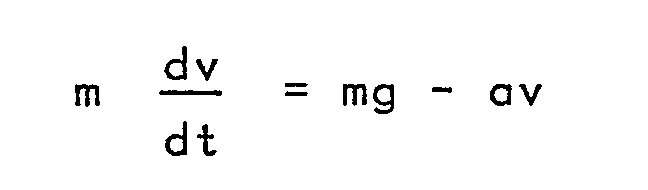
where a_ is a constant that may have the shape of a = mk
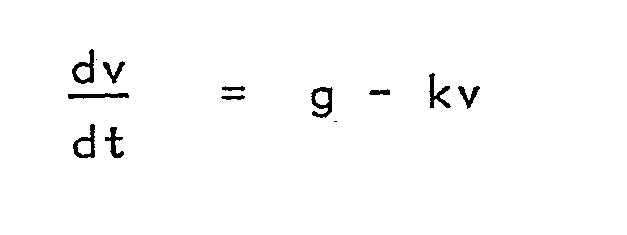
and the integration gives us:

where v
o is the velocity at the initial instant t = o
[0031] For a large value of t, we may say that the limit velocity V would have value:

the space covered by the body at the end of time t will be:

[0032] Returning to the sphere of radius
r. When it is moved with uniformal movement and with very small velocity
v in the interior of a fluid having viscosity coefficient η, resistance
Fthat this offers the movement may be calculated, quite approximately, through the
formula of Stokes.
F = 6πηrv (5)
[0033] Application of the formula requires that Re « 1.
[0034] If a sphere is left to fall in a fluid, the velocity will gradually increase until
it reaches a limit. Calculus of this velocity can be made considering that between
the weight of the sphere, the thrust and resistance
F there is the following relation:

where

[0035] The condition imposed on Reynolds' number for the field of validity of Stokes' formula
requires that the sphere be very small. With larger bodies, the resistance is no longer
proportional to the velocity, that is to say, Stokes' formula is no longer valid and
in accordance with Newton's law, it is admitted that resistance is proportional to
the square root of velocity, which corresponds to case II.
[0036] We can therefore draw the conclusion that we pass from a system of resistance proportional
to velocity to another where the resistance becomes proportional to the square root
of velocity, because it is considered that the radius of the sphere increases in va
, although with the same reasoning we can say that this might not occur, when the
density of the sphere decreases even though its diametre increases, when
v is maintained constant or with values that are valid for fulfilling Stokes' formula.
[0037] If we change the simile of the sphere, and substitute the spheres for disks for the
same diametre and material, they will fall in water at variable velocity, in accordance
with the area present at the time of fall, and their course will be represented by
a broken line.
[0038] Having established this premise, it is not essential to know which mathematical formula
governs the fall of metallic disks in water, but only what apparent velocity they
reach.
Vertical fall of solids in a fluid in movement.
[0039] Within the two likely possibilities, when a fluid is made to flow in the tube of
our project, only the direction contrary to the fall direction will be taken into
consideration, and we shall try and obtain an equilibrium velocity.
[0040] The immeidate objective of the system is based on the following facts:
1.- After a metallic disk has been deposited at the bottom of the tube, which it has
rached after a fall time t from height L, we can say that the average velocity has been
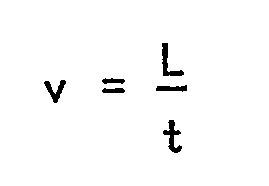
because the fall has not taken place according to a uniformally accelerated movement,
neither with rectilineal course.
If we produce a current of water in the tube at velocity below v, the disk will logically ascend and descend in a continuous movement and theoretically
for a specific velocity v, the disk will remain practically in suspension, without touching the bottom of the
tube, or emerging from the top.
2.- For a specific velocity V c, the upward current will make the disk emerge via the top of the tube.
[0041] It may be admitted that, in practice, length
L is not sufficient to keep the disk in suspension throughout its length. This means
that length L of the tube is not sufficient for the kind of test that is to be carried
out, that the velocity that was calculated is less than the limit velocity of that
disk in that fluid and that a value of more than L should be used.
[0042] Since the target is however to try and keep a disk in suspension within the smallest
possible space
L, there are other factors that should be considered which have not been taken into
account until now, one of the most important of these being to use a tube that has
a variable section in certain parts of it.
[0043] Knowing the laws that govern the fall of solids in fluids under very specific conditions,
experiments must be used as means of information when those specific conditions are
not fulfilled due to change in geometric shape, temperature, density and viscosity
of the fluid.
[0044] If the classification of the metals by their electrochemical activity is considered,
then a metal that is located at the top of this may be covered by another metal that
is situated under it.
[0045] An evident example of this is the deposition of copper on iron in an acidulated solution
of copper sulphate. The two reactions that take place, one being anodic and the other
cathodic, simultaneously, on the surface of the iron are:
Fe→Fe⁺⁺ + 2e (anodic) Eº = -0.44V
Cu⁺⁺ + 2e→Cu (cathodic) Eº = 0.337V
[0046] Once the iron has been completely covered by a layer of copper, the proces is stopped
and there is no later increase in thickness. The deposit is normally thin (<1.0µm)
and its adherence to the iron is not good.
[0047] Take a mechanical piece (M) that is joined to another piece (M₁) of a less noble
metal and both immersed in the deposition solution containing ions (M₂
n⁺) of a more noble metal M₂, dissolution of the less noble
tal M₁ (anodic) is produced, passing to the solution and the metal M₂ is deposited
on the mechanical piece.
M₁→M₁
n⁺ + n e
M₂
n⁺ + n e→M
[0048] In this case, netallization may continue whilst dissolution of the anode M₁ takes
place. There are gold solutions on the market than can provide thicknesses of 2.5µm,
on substrates of silver, copper, brass, nickel, and tin. The processes are, in principle,
similar to gilding by contact. The loss and gain of electrons is a basic part of the
above commented processes, as it is really in all water deposit processes.
[0049] To avoid confusions, it is essential to examine the term
deposition without current. Since the loss of an electron is essential, during the deposition we should base
our action on other methods that are neither chemical methods,
1. Displacement reaction.
2. Galvanic dissolution reaction.
nor electric methods, such as the well-used electrodeposition.
[0050] The following should be fulfilled in any process of deposition without current:
a) The solution must have a chemical reductive agent that acts as donor of electrons.
b) The process will continue to be catalysed by the deposited metal.
[0051] Thus, when the surface of the substrate becomes covered by the metallic deposit,
continuation of the process depends on the capacity of catalysis of the deposited
metal.
[0052] The term "autocatalytic" is applied to this type of process and has not undergone
the same confusion as the term "electroless".
[0053] Before a process of deposition of gold may be described as autocatalytic, that process
must necessarily be capable of depositing gold on a gold substrate.
[0054] Let us now discuss the specific case that we are concerned with, namely to learn
the possibilities that are offered by an autocatalytic formulation for the deposition
of gold. Unless a work piece is a non-conductive material or has a highly complex
geometry, it is best to use a conventional method of gilding.
[0055] The reasons that advise using standard electro-deposition methods are based on the
fact that autocataly tic baths present:
1 A smaller deposition velocity.
2 The conditions of electro-deposition must be carefully supervised.
3 Substrates must be very clean.
4 The baths have a more limited duration.
5 The distribution of thicknesses of the deposits depends largely on the stirring
conditions.
[0056] Before discussing in detail some of the formulations that may be used in this process,
it is best to understand the mechanism of the reactions involved. An introduction
into the kinetics of reactions is necessary, to help to choose the best viability
of a system, although we cannot eliminate the fact that experiments are necessary
in order to provide the pertinent proof.
[0057] In the autocatalytic deposition, a substrate is immersed in the deposition solution,
whereupon reactions commence immediately and the metal is deposited on the surface
of the substrate; this metal catalyses the reaction and provokes a continuation of
the deposition.
[0058] The two most essential components, in a bath of this type, are the ions M
n⁺ of the metal that is to be deposited, and the reductive agent (Red.) The deposition
reaction is:

[0059] The reduction-oxidation reaction takes place on the surface of the metallic or metallized
substrate, whilst the reductive, donating its electrons, is converted in its oxide
form (Ox). Thus, the reaction may be considered as two semi-reactions redcx:
M
n⁺ + n e →Mº
and
Red - n e →Ox
[0060] The equilibrium potentials of the electrodes of the metal E
m (M
n⁺ /M ) and of the reductive E
R (Red/ Ox) may be obtained used Nernst's equation and the potentials Eº of the tables
(oxidation-reduction standard potential).
[0061] Both potentials depend on the temperature of the solution and on the ionic concentrations,
and also on the nature of the compounds used. Thus, the value of E
R is strongly influenced by the pH of the solution.
[0062] The difference between Eº
m and Eº
R and, more correctly between E
m and E
R may help in a preliminary selection to determine the effectiveness of certain reductive
agents. If the difference is too small (or negative), the reduction of the metal may
not take place, whereas if it is too large, there may be a spontaneous decomposition
of the solution.
[0063] Since the oxidation-reduction reactions take place on the surface of the substrate,
the potential at which they take place drops in value between E
m and E
Rand is considered as mixed potential E
PM. The deposition velocity is obtained from change in potential (E
m→E
PM)
[0064] Two techniques may be used to determine the deposition velocity using the mixed theoretic
potential. These are:
a) The technique of extrapolation of Tafel's curve (or intersection) or
b) The technique of polarization resistance (sometimes called lineal polarization).
[0065] The first technique uses data obtained in anodic and/or cathodic polarization measurements.
Where the potential curve (anodic or cathodic) intercepts the mixed potential E
PM, the corresponding intensity i
dep is taken to determine the deposition velocity; the anodic and cathodic currents are
equal to the potential E
PM, in other words, the reduction velocity of the metallic ions to metal is equal to
the velocity of oxidation of the reductive.
[0066] In the second method, based on the technique of polarization resistance, it is based
on the fact, observed in the corrosion process, that the density of current applied
is approximately a lineal function of the potential of the electrode, so long as the
measurements are maintained at ± 10 mv of the mixed potential E
PM. Other kinetic parameters should however be obtained by some independent method,
especially the Tafels gradients, for anodic and cathodic reactions.
[0067] In order to understand all this better, and merely by way of example, which is by
no means restrictive, a sheet is appended hereto showing drawing where:
Fig. 1 - Represents the diagram of the functional installation.
[0068] In this figure, the following components are described:
1.- Suspension tube.
2.- Charging hole.
3.- Closing lid.
4.- Protecting screen.
5.- Drive equipment.
6.- Return pipe.
7.- PH fluid control.
8.- Rotameter with thermostat.
9.- Ion consumption control.
10.- Calefactor.
11.- Filter.
12.- Flow valve.
13.- Flow control with digital thermometer.
14.- Basket.
15.- Blowoff valve.
[0069] With reference to the above-mentioned illustrations that represent a diagrammtic
form of its industrial execution and are only included for informative pur poses,
and consequently are in no way restrictive in a practical study of solid elements
moving in fluids, the installation is presented and developed, where those solid elements
may become suspended, in terms of their shape, their weight and the velocity imparted
on the fluid, in a contrary direction to the vertical fall direction by action of
gravity.
[0070] Free fall of a piece inside a tube that is full of a chemical or autocatalytic bath
will constitute the most simple metallizing device when the time of fall,
with the bath at a suitable temperature, is sufficient for depositing the required
amount of metal.
[0071] Very simple reasons like recovery of the gold pieces, maintaining uniformity of the
bath composition and its temperature, as well as the length of the tube, mean that
it is almost impossible to use a device of this kind; however, the free fall of solid
elements may be used if this is combined with a fluid movement, that has the same
direction and in the opposite direction.
[0072] In the installation, that is represented in figure 1, solid elements may be metallized
by combining two principles that have previously been well studied.
[0073] Firstly, if the installation is filled with a suitable fluid which is made to circulate
with a centrifugal pump (5) towards the tube(1), a current of fluid is formed, whose
velocity will be in terms of the pump delivery and the section of the rest of the
installation. This velocity may be varied by using a flow valve (12). There is also
a possibility of adapting an electronic velocity variator to the pump motor, by means
of a rotameter (8), that is electronically connected to that velocity variator.
[0074] Once the movement of the fluid is established, in an upward direction along the tube
(1), the temper ature of the fluid may be modified by using a calefactor covered with
titanium (10). Temperature is controlled with a digital thermometer, the well of which
is located at (13).
[0075] Stabilization of the temperature of the fluid is obtained by combining (10) and (13)
using a thermostat.
[0076] Certain properties of the fluid such as pH, consumption of cerain ions, are determined
by electrodes installed on (7) and (9), on the return pipe (1) with the drive equipment
(5).
[0077] As safety elements, a protecting screen (4) is used to avoid solid elements from
dropping on (5), and a filter (11) to retain possible solid impurities circulating
in the equipment. Tube (1) has a closing lid (3) to avoid possible projections of
fluid and to prevent foreign objects from falling in the tube (1).
[0078] Up to now, we have got a fluid to circulate through the device of figure 1 at variable
velocity, so that if this is established appropriately, solid elements can be introduced
via hole (2) of tube (1), and which are maintained in suspension in the fluid at an
adequate velocity. The solid elements may also be introduced in tube (1) through hole
(2) with the fluid at a resting state, held up by the protecting screen (4).When an
appropriate velocity is given to the fluid, suspension is produced.
[0079] When the solid elements are introduced loose in tube (1), they may be taken out of
the tube increasing the velocity of the fluid above the suspension velocity and are
collected in the basket (14) that has been prepared for this purpose.
[0080] When the solid elements are introduced in the tube (1) in a perforated basket which
adapts well to its walls, suspension is produced inside the basket and this also helps
for emptying the pieces.
[0081] As already mentioned, a chemical or an autocatalytic bath has the property of depositing
a specific metal, on a surface that has been suitably prepared, in a quantity that
depends on the temperature and composition of the bath. When the device in figure
1 is filled with a chemical or autocatalytic bath and the appropriate velocity, pH
and temperature conditions are established, a solid element whose surface has been
appropriately treated may be metallized at the same time as it enters in suspension
in the fluid. Once the calculated time has elapsed, it is taken out in the manner
described above. On an industrial scale, a large number of pieces may be introduced,
and thanks to the constant movement obtained in the suspension, they are not permanently
in contact with one another to cause defects and irregularities on the layer of metal
deposited.
1.- DEVICE FOR DEPOSITING METALS ON OBJECTS IN SUSPENS
ION, characterized because a fluid flows inside a tube, which causes suspension by
counter-current, of the objects that are to be metallized.
2.- DEVICE FOR DEPOSITING METALS ON OBJECTS IN SUSPENSION, in accordance with claim
1, and furthermore characterized because the upper part of the tube has charging hole
with closing lid and a protecting screen at the bottom which communicates with the
fluid drive equipment so that the objects that are to be metallized which are introduced
in the charging hole, even though more dense than the fluid, are maintained in suspension
by virtue of the current of fluid which the drive equipment produces inside the tube
in an upward direction and contrary to the falling objects by gravitation.
3.- DEVICE FOR DEPOSITING METALS ON OBJECTS IN SUSPENSION, in accordance with the
above claims, and furthermore characterized because when the objects that are to be
metallized have less density than the fluid, the tube and direction of the current
of fluid is reversed in order to maintain the suspension by counter-current.
4.- DEVICE FOR DEPOSITING METALS ON OBJECTS IN SUSPENSION, in accordance with the
above claims, and furthermore characterized because the fluid used on each cycle provokes
deposition of the metal by chemical or autocatalitic reaction, without the use of
external electrical current being necessary to provoke an electro-chemical reaction.
5.- DEVICE FOR DEPOSITING METALS ON OBJECTS IN SUSPENSION, in accordance with the
above claims, and furthermore characterized because the drive equipment communicates
with a return conduit that shuts the flow circuit of the fluid because it communicates
at one end with the tube of claim one, and at the other end with the drive equipment
which, in turn, communicates at the top with that tube.
6.- DEVICE FOR DEPOSITING METALS ON OBJECTS IN SUSPENSION, in accordance with the
foregoing claims, and furthermore characterized because the objects that are to be
metallized are introduced via the charging hole of the tube in a perforated basket
which will also be used to take them out at the end of the metallization process.
If, however, through the drive equipment, the flow of fluid that must circulate through
the tube is increased to the maximum, the objects may be collected and separated from
the fluid in a recipient inserted in the return conduit, without having to use the
perforated basket.
7.- DEVICE FOR DEPOSITING METALS ON OBJECTS IN SUSPENSION, in accordance with the
foregoing claims, and furthermore characterized because the return conduit includes
control devices of fluid, Ph, selective ion, a flow valve which permits the flow of
the fluid in the circuit to be varied, and a heater unit to be able to work at suitable
temperature in each process and be able to vary the deposition velocity of the metals,
in addition to a filter to eliminate foreign elements in suspension in the circulating
fluid.
8.- DEVICE FOR DEPOSITING METALS ON OBJECTS IN SUSPENSION, in accordance with the
foregoing claims, and furthermore characterized because there is a temperature control
and a fluid flow control fitted between the drive equipment and pipe protecting screen.
9.- DEVICE FOR DEPOSITING METALS ON OBJECTS IN SUSPENSION, in accordance with the
foregoing claims, and furthermore characterized because at the bottom of the return
conduit and immediately before it enters the drive equipment, there is a pipe for
emptying fluid,fitted with a valve.
10.- DEVICE FOR DEPOSITING METALS ON OBJECTS IN SUSPENSION, in accordance with the
foregoing claims, and furthermore characterized because by making the fluid flow at
slow velocity, the metallization process is initiated, connection start-up of the
calefactor equipment to that of the drive equipment, setting the work temperature
which is automatically stabilized by the thermostat.
11.- DEVICE FOR DEPOSITING METALS ON OBJECTS IN SUSPENSION, in accordance with the
f oregoing claims, and furthermore characterized because by reducing the flow of the
fluid to a minimum velocity, the objects which are to be metallized are located inside
the tube by means of the perforated basket, or on the screen that is situated at the
bottom, gradually increasing the flow of fluid until the desired degree of suspension
is obtained, remaining in operation until a chronograph disconnects the current of
the drive element when the preset time has elapsed.
12.- DEVICE FOR DEPOSITING METALS ON OBJECTS IN SUSPENSION, in accordance with the
foregoing claims, and furthermore characterized because by increasing the velocity
of the fluid to the maximum, in accordance with claim six, the tube is emptied of
metallic objects, which will be collected from the recipient of the return conduit,
thus leaving the device in a condition to commence a new cycle of metallization or
deposition of a metal on new objects in suspension.