[0001] Die Erfindung betrifft ein Verfahren zur Herstellung von SE-Metallen und SE-haltigen
Legierungen und ist dadurch gekennzeichnet, daß die Reduktion von SE-Halogeniden und/oder
SE-Oxiden einzeln oder als gemisch gegebenenfalls mit Legierungszusätzen aus der
Gruppe der Eisenmetalle und anderer Legierungselemente sowie gegebenenfalls mit Zusätzen
von Alkali- und/oder Erdalkalimetallsalzen mittels einem oder mehrerer Erdalkalimetalle
unter einer gegen SE-Metalle, SE-Verbindungen und Erdalkalimetalle weitgehend interten
Atmosphäre in einem elektrischen Lichtbogenofen erfolgt, wobei in diesem zur Erreichung
einer möglichst raschen und vollständigen Reduktion eine starke Rührwirkung in der
Schmelze durch elektromagnetische Kräfte erzeugt wird.
[0002] SE-Metalle und SE-Legierungen werden auf vielen Gebieten industriell eingestezt.
Das Cermischmetall beispielsweise , welches ein Gemisch aus Metallen der sogenannten
"leichten Seltenen Erden" oder Ceriterden ist und annähernd die in den natürlichen
Vorkommen (Bastnäsiten und Monaziten) aufscheinende Verteilung der Elemente La, Ce,
Pr, Nd, Sm und Eu aufweist, wird als metallurgischer Zusatz für Stähle, Gußeisen,
Magnesium usw. in hohem Maße eingesetzt. Im Stahl bindet Cermischmetall den restlichen
Schwefel bis zu sehr geringen Gehalten. Im Gußeisen fördert es die Kugelgrafitbildung.
Im Magnesium erhöht Cermischmetall die Festigkeit und Warmfestigkeit und setzt in
Gußstücken die Porosität herab. Die wohl älteste und vielleicht auch bekannteste
Anwendung von Cermischmetall ist die zur Herstellung von Zündlegierungen. Grundlage
derselben ist eine Legierung von Cermischmetall mit Eisen sowie diversen anderen
Metallen, die die Pyrophorität, Herstellbarkeit und Lagerfähigkeit verbessern. Legierungstypen
wie LaNi5, wobei La teilweise durch Ce. Pr sowie Nd und Ni durch Co, Cr, Cu, Fe ersetzt
sein kann, sind in der Lage, Wasserstoff unter Bildung von SE-Hydriden zu speichern.
Strnat fand in den 60er-Jahren an YCo5- und Y2Co17-Verbindungen, daß diese eine sehr
hohe einachsige magnetische Kristallanisotropie aufweisen und damit hartmagnetische
Eigenschaften besitzen. Basierend darauf kam es zur Ent wicklung einer Reihe von
SE-Legierungen mit 3d-Obergangselementen vom Typ SEA5 bzw. SE2A17, in dem als SE-Metall
die Ceriterden, besonders Sm und als 3d-Obergangsmetall Co und teilweise substituiert
mit Fe, Mn, Cr, aber auch Cu Verwendung fanden. Hervorragende hartmagnetische Eigenschaften,
nämlich hohe Energieprodukte, hohe Remanenz und hohe Koerzitivfeldstärken sind gemeinsames
Kennzeichen dieser Art von SE-Legierungen. Seit den 70er-Jahren werden Permanentmagnete
auf Basis von SmCo5 und Sm2Co17 industriell hergestellt.
[0003] Die Entdeckung von Strnat führte in den folgenden Jahren weltweit zu intensiven Forschungsaktivitäten,
zur Auffindung verbesserter, hartmagnetischer Werkstoffe auf Basis der SELTENEN ERDEN.
Den vorläufigen Höhepunkt stellen die nahezu gleichzeitig in den Laboratorien von
General Motors und Sumitomo Special Metals entwickelten hartmagnetischen Legierungen
auf Basis Neodym - Eisen - Bor dar. Europäische Patentanmeldungen von General Motors
(EU Anm. 0 108 474 A2, EU Anm. 0 125 752 A2) und von Sumitomo Special Metals (EU Anm.
0 101 552 A2, EU Anm. 0 106 948 A2, EU Anm. 0 125 347 A2, EU Anm. 0 126 179 A1, EU
Anm. 0 126 802 A1) beschreiben solche Legierunge, deren Herstellung und Verarbeitung
zu hartmagnetischen Werkstoffen. Faßt man die von den beiden Laboratorien eingebrachten
Anmeldungen zusammen, so überschneiden sich diese, was die Zusammensetzung der Legierung
betrifft. Ein wesentlicher Unterschied besteht in der Vorbereitung der Legierung
zur Herstellung der hartmagnetischen Werkstoffe. Nach dem Sumitomoverfahren werden
die Legierungen bevorzugt in einem Induktionsofen, aus den Einzelkomponenten aufbauend,
geschmolzen, zu Blöcken vergossen, anschließend zerkleinert und aus µm-Bereich vermahlen.
Das erhaltene Pulver wird darauf zur Erzielung anisotroper Magnete im Magnetfeld zu
Formen verpreßt, gesintert und die Sinterlinge einer entsprechenden Wärmebehandlung
unterzogen. Darauf erfolgt die endültige Magnetisierung.
[0004] Nach dem General-Motors-Verfahren wird die in üblicher Weise aus den Einzelkomponenten
aufgebaute Legierung geschmolzen und durch Guß auf eine rotierende Kupferwalze sehr
rasch abgekühlt (Melt Spinning). Sie erstarrt dabei extrem mikrokristallin bzw. amorph.
Das erhaltene, plättchenförmige Pulver wird anschließend nachvermahlen und mittels
Kunststoff- oder Metallbinder zu entsprechenden Magnetwerkstoffen verpreßt. Sieht
man von den speziellen, in den beiden Verfahrensvarianten angeführten Herstellungsschritten
ab, so werden für die Erzeugung der eigentlichen Legierungen bzw. deren Ausgangsstoffe
keine speziellen Verfahrenswege beschritten. Es werden übliche, in der Technik eingeführte
Verfahren angewandt, wobei als Ausgangsstoffe vorzugsweise reines oder mit Eisen vorlegiertes
Neodym, Eisen und Bor bzw. Ferrobor Verwendung finden. Für die Herstellung von Neodym
und der meisten anderen SE-Metalle und deren eisenhältige Vorlegierungen sind aus
der Literatur verschiedene Verfahren bekannt (Ullmann, Band 9 und 21). Die bekanntesten
und am häufigsten angewandten Verfahren sind die Schmelzflußelektrolyse und die metallothermische
Reduktion. Im Schmelzeflußelektrolyseverfahren setzt man als Rohstoff bevorzugt die
Halogenide der Seltenen Erden vielfach gemeinsam mit Alkali- oder Erdalkalihalogeniden
ein. Das an der Kathode abgeschiedene SE-Metall kann rein oder vorlegiert mit einem
Metall der Eisengruppe im Periodensystem oder einem anderen Legierungselement sein.
Nach einem von Bureau of Mines entwickelten Elektrolyseverfahren setzt man SE-Oxide
als Rohstoff ein. Der Elektrolyt ist ein Gemisch aus diversen SE-Alkali- und Erdalkalifluoriden.
Bei den metallothermischen Reduktionsverfahren werden als Rohstoff meist auch die
Halogenide der Seltenen Erden verwendet. Fallweise erfolgen Zusätze von Alkali- und
Erdalkalihalogeniden als Schlackenbildner oder Flußmittel. Als Reduktionsmittel dienen
die Alkali- und/oder Erdalkalimetalle, bevorzugt aber das Calcium. Die metallothermische
Reduktion wird in der Regel unter einer gegen das Reduktionsmittel und dem entstehenden
SE-Metall inerter Atmosphäre in einem geschlossenen Behälter durchgeführt.
[0005] Die elektrolytische Herstellung Verschiedener SE-Metalle bei Verwendung ihrer Halogenide,
insbesonders der Chloride verlangt, daß sie besonders frei von gebundenem Wasser und
möglicher Sauerstoffverbindungen (z.B. Oxychloride) sind. Außerdem gelingt es in
der Regel, nur solche SE-Metalle wirtschaftlich vertretbar herzustellen, deren Schmelz
punkt nicht wesentlich über 1000°C liegt. Das Zulegieren von beispielsweise Eisen
führt zwar zur Herabsetzung des Schmelzpunktes, es erschwert jedoch die Elektrolysebedingung
und schließt in der Regel die Verwendung von Refraktärmetallen als Zustellung aus.
Die EU Anm. 0 177 233 (Sumitomo) beschreibt die elektrolytische Herstellung eisenhältiger
Nd-Legierungen. Nicht möglich erscheint danach jedoch die gezielte Hertellung eisenreicherer
und borhältiger Legierungen, deren Zusammensetzung einer fertigen Magnetlegierung
entspricht (NdFeB). Außerdem bereitet der geringe mögliche Kathodenquerschnitt (Kathodenbelastung)
elektrolysetechnische Probleme.
[0006] Die metallothermischen Reduktionsverfahren unter Verwendung der SE-Halogenide oder
SE-Oxide als Rohstoff und beispielsweise Calcium als Reduktionsmittel beinhalten
ebenfalls eine ganze Reihe verfahrenstechnischer Probleme. Die meist relative langsam
und unvollständig ablaufende Reaktion verlangt die zusätzliche Zuführung von Energie
über das Reaktionsgefäß von außen. Die umgebende Atmosphäre muß gegen das Reduktionsmittel
und das Reaktionsprodukt inert sein. Hohe Ansprüche werden so an das Tiegeloder Zustellungsmaterial
der Reaktionsgefäße gestellt. Da sich bei Herstellung beispielsweise eisenhaltiger
Legierungen keine aus Tantal, Molybdän oder Wolfram bestehende Auskleidung eignet,
sind solche aus MgO, Al203 und/oder CaO erforderlich, die wiederum wenig Widerstand
gegen schmelzflüssige Chloride oder Fluoride entgegenbringen und gegen die Wärmezufuhr
isolierend wirken. Außerdem ist verfahrensbedingt meist nur ein diskontinuierlicher
Betrieb möglich, welcher hohe Kosten mit sich bringt. Die direkte Herstellung einer
fertigen SE-Co Magnetlegierung gelingt nur unter hohem apparativen Aufwand (AT PS
336 906, Th. Goldschmidt), wobei nur Legierungspulver erhalten werden, die über chemische
Reinigungsverfahren von anhaftender Schlacke bzw. Reaktionsprodukten gereinigt werden
müssen. Der Vorteil der metallothermischen Herstellung der SE-Metalle und Legierungen
gegenüber der Schmelzflußelektrolyse liegt in der relativ höheren Reaktionsgeschwindigkeit
und in gewissen Bereichen in der großen Variationsbreite in bezug auf die Temperatur.
Der Wasserund Sauerstoffgehalt in den eingesetzten Rohstoffen ist weniger kritisch.
[0007] Die vorliegende Erfindung hatte zum Ziel, die bekannten Vorteile metallothermischer
Reduktionsverfahren zu nützen und gleichzeitig entscheidende Verbesserungen im verfahrens-technischen
Ablauf der Reduktion zu bringen. Außerdem soll erfindungsgemäß erreicht werden, daß
sowohl die reinen SE-Metalle als auch deren verschiedene Legierungen, insbesondere
die Nd-Fe-B-Legierung nach ein- und demselben Verfahren herstellbar sind.
[0008] Dieses Ziel wird dadurch erreicht, daß nach dem erfindungsgamäßen Verfahren die Reduktion
der SE-Halogenide und/oder SE-Oxide einzeln oder als Gemisch, gegebenenfalls mit Legierungszusätzen
aus der Gruppe der Eisenmetalle und anderer Legierungszusätze sowie gegebenenfalls
mit Zusätzen von Alkali- und/oder Erdalkalimetallsalzen mittels eines oder mehrerer
Erdalkalimetalle, bevorzugt aber Calciummetall, unter einer gegen SE-Metalle, SE-Verbindungen
und Erdalkalimetalle inerten Atmosphäre in einem elektrischen Lichtbogenofen im zweiphasigen
Ofenbetrieb erfolgt, wobei in diesem zur Erreichung einer möglichst raschen und vollständigen
Reduktion eine starke Rührwirkung auf Grund des entsprechend gewählten Strom-Spannungsverhältnisses
in der Schmelze durch elektromagnetische Kräfte erzeugt wird.
Für die erfindungsgemäße Durchführung der Reduktion wurde der in Fig. 1 schematisch
dargestellte Lichtbogenofen entwickelt. Ober ein Vorratsgefäß 1 wird die aus den
jeweiligen Rohstoffen, dem Reduktionsmittel und gegebenenfalls weiteren Zusätzen bestehende
Mischung über eine Zahnradschleuse 2 in das Ofeninnere bzw. in die vorliegende Schmelze
3 befördert. Der Ofenkörper 5 besteht aus einem wassergekühlten Eisenmantel mit aufgesetzter,
ebenfalls wassergekühlter, Deckelkonstruktion. Vor dem eigentlichen Einbringen der
Mischung haben wir in der Regel auf dem mit MgO-Steinen ausgelegten Boden eine Mischung
bestehend aus Alkali- und/oder Erdalkalihalogeniden in einer Schichstärke von 2 -
3 cm vorgeschmolzen, in die dann der Möller eingetragen wurde. Zur Erzeugung einer
gegen die Reaktionspartner und das Reaktionsprodukt inerten Ofenatmosphäre strömte
über 7 Argon oder Stickstoff in den Ofenraum. Die Abgase konnten über die Abgasleitung
8 mit entsprechender Rückströmsicherung aus dem Ofenraum entweichen. Die Zufuhr elektrischer
Energie in die Schmelze erfolgte über die Elektroden 6. Die Stromstärke an den in
die Schmelze tauchenden Elektroden wählten wir so hoch, daß infolge der auftretenden
elektromagnetischen Kräfte eine so starke Rührwirkung auftrat, daß die neu eingetragene
Mischung sofort mitgerissen und mit der vorliegenden Schmelze innig vermischt wurde.
Die Folge war eine sehr rasche und vollständige Reduktion bei sehr geringen Abbrandverlusten.
Diese Abbrandverluste können durch unzureichend sauerstofffreie Ofenatmosphäre entstehen.
Das gebildete Metall oder die Legierung 4 schied sich am Boden des Ofens auf einer
dünnen, festen Schlackenschichte, die sich aus den Vorschmelzsalzen gebilden hatte
ab und konnte über eine Abstichrinne von Zeit zu Zeit aus dem Ofen abgelassen werden.
[0009] Die Wand des Ofengefäßes konnte bei der vorliegenden Ausführung der Ofenkonstruktion
ohne Schwierigkeiten aus gewöhnlichem Eisenblech gefertigt werden. Infolge der starken
Kühlung durch Wasser erstarrte an der Ofeninnenwand eine 5 - 10 mm starke Schichte
der jeweiligen Salzschlacke und bildete wie am Boden des Ofens eine Schutz- bzw. Zustellungsschichte
gegen das schmilzflüssige SE-Metall oder die SE-Legierung. Die Werkstoffauswahl für
die Elektroden mußte den Aufgaben entsprechend getroffen werden. Bei Herstellung reiner
SE-Metalle verwendeten wir bevorzugt Molybdän- oder Wolframelektroden, fallweise,
wenn höhere Kohlenstoffwerte im Metall erlaubt waren, auch Grafitelektroden. Auch
Elektroden aus Tantal sind möglich sowie wassergekühlte Kupferelektroden. Die Voraussetzungen
sind, daß sie nicht vom SE-Metall gelöst werden oder durch sonstigen Abtrag dieses
verunreinigen. Für die Hherstellung von SE-haltigen Legierungen, die eines oder mehrere
Metalle der Eisengruppe im Periodensystem und gegebenenfalls noch eines oder mehrerer
anderer Elemente enthalten, wurden neben Elektroden aus den Metallen der Eisengruppe
vorwiegend Wolframelektroden oder Grafitelektroden verwendet. Fallweise setzten wir
auch wassergekühlte Kupferelektroden ein. Da nach dem erfindungsgemäßen Verfahren
die Temperatur der Schmelze in weiten Grenzen variiert werden kann, sind sowohl an
die Art der eingesetzten Rohstoffe, der Reduktionsmittel, der Zuschlagstoffe und
letzlich auch an die der herzustellenden SE-Metalle und SE-Legierungen relativ wenig
Grenzen gesetzt. Die zur Herstellung einzelner SE-Metalle und SE-Legierungen verwendeten
Rohstoffe sollen aber bevorzugt als Halogenide der Seltenen Erden vorliegen. Bei
Verwendung der Chloride einzelner Seltener Erden sollte jedoch die Temperatur der
Schmelze nicht 1300°C übersteigen, da dabei schon erhebliche Verdampfunsverluste
auftreten können. Bei fallweise erforderlichen höheren Schmelztemperaturen, die durch
den Schmelzpunkt des SE-Metalls oder der SE-Legierung erforderlich sein können, hat
sich die Verwendung der entsprechenden SE-Fluoride als vorteilhaft herausgestellt.
Sowohl bei Einstatz der Chloride als auch der Fluoride sind den Wasser- und Oxychloridgehalten
Grenzen gesetzt. Diese können jedoch erheblich über den beispielsweise bei der Schmelzflußelektrolyse
erlaubten Werte liegen. Wassergehalte bis zu 2 % und Oxychloridgehalte bis zu 20 Gew.-%
sind fallweise tragbar. Zur Herabsetzung des Schmelzpunkte der Salzchlacke, insbesondere
bei Einsatz von SE-Fluoriden und Verwendung von Calcium als Reduktionsmittel, können
dem Rediktionsgemisch Alkali- und Erdalkalihalogenide, vorzugswiese NaCl, CaCl2 und
LiF in entsprechenden Mengen zugesetzt werden. Bei der Reduktion von insbesondere
SE-Fluoriden hat sich gezeigt, daß zumindest ein Teil der SE-Halogenide durch ein
meist billigeres, entsprechendes Oxid ersetzt werden kann. Die Menge hängt ausschließlich
von der bei der Reduktionstemperatur gegebenen Löslichkeit des Oxids in der Halogenidschmelze
ab. Als Reduktionsmittel hat sich bevorzuge körniges Calciummetall durchgesetzt. Aber
auch Magnesium und Mischungen von Calcium und Magnesium sind fallweise mit Erfolg
eingesetzt worden. Die Höhe des Reduktionsmittelzusatzes bzw. der Oberschuß gegenüber
dem stöchiometrischen Bedarf richtet sich nach der geforderten SE-Ausbringung, vor
allem aber nach den in den fertigen SE-Metallen und SE-Legierungen erlaubten Gehalten
an Erdalkalimetallen. Wird ein möglichst hohe SE-Ausbringung aus wirtschaftlichen
Oberlegungen angestrebt, so ist naturgemäß mit höheren Erdalkaligehalten in Metallen
und Legierungen zu rechnen. Es hat sich jedoch überraschenderweise gezeigt, daß nach
dem erfindungsgemäßen Verfahren das Verhältnis SE-Ausbringung zum Erdalkaligehalt
in Metallen und Legierungen wesentlich günstiger als bei den herkömmlichen Verfahren
ist. Bei beispielsweise einer SE-Ausbringung von 95 % lag der Calciumgehalt im SE-Metall
ca. um den Faktor 10 tiefer als bei herkömmlicher calciothermischer Reduktion in einer
Reduktionsbombe. Dadurch war es vielfach nicht erforderlich, die nach dem erfindungsgemäßen
Verfahren hergestellten SE-Metalle und Legierungen zur Entfernung zu hoher Erdalkaligehalte
zu raffinieren. Der Einsatz der zur zur Herstellung SE-haltiger Legierungen notwendingen
Legierungskomponenten aus der Gruppe der Eisenmetalle und anderer Legierungselemente
kann prinzipiell in beliebiger, dem Anlagenkonzept angepaßter Form, erfolgen. Als
vorteilhaft hat sich jedoch der Einsatz in metallischer, feinstückiger Form erweisen.
Eisen setzten wir beispielswiese als feinstückigen Eisenschrott oder Schwammeisen
und Bor als Ferrobor ein. Ein weiterer Vorteil des erfindungsgemäßen Verfahrens besteht
darin, daß mit der vorliegenden Ofenkonstruktion praktisch kontinuierlich gefahren
werden kann. Nach satzweisem Abstich der Metallschmelze wird die gebildete Salzschlacke
nur soweit in eine getrennte Vorlage mit abgelassen, daß für die nächste Charge noch
genügend Schmelze im Ofen verbleibt. Weiters ist es möglich, bei vollständigem Abguß
des Ofeninhalts Teile der noch flüssigen Schlacke in den Ofen, nach Abheben des Deckels,
rückzuführen.
[0010] Das erfindungsgemäße Verfahren soll durch einige Beispiele näher erläutert werden.
Vergleichsbeispiel
[0011] Ein Teil einer Mischung, bestehend aus 50 kg entwässertem Neodymchlorid (0,8 % Restwasser,
14 % Oxychlorid) und 13,3 kg granuliertem Calciummetall, wurde in einem aus Molybdän
gefertigten Behälter eingebracht, welcher über einen Eisentiegel induktiv von außen
beheizt werden konnte. Induktionsspule, Eisentiegel und Molybdänbehälter waren in
einer evakuierbaren Kammer untergebracht, die es ermölichte, die Reaktion unter Argon
im Normal-, Unter- und oberdruckbereich durchzuführen. Zur Einleitung der Reduktion
heizten wir die Vorlage auf ca. 1200°C auf. Nach Aufschmelzen derselben und Ablauf
der Reaktion trugen wir über ein Schleusensystem den Rest der Mischung während einer
Zeit von ca. 30 Minuten nach. Zur Vervollständigung der Reduktion wurde die Schmelze
noch weitere 30 Minuten auf Temperatur gehalten. Anschließend gossen wir Metall und
Salzschlacke weitgehend getrennt in gußeiserne Vorlagen ab. Das erhaltene Metall
behandelten wir zur Trennung von der CaCl2-Schlacke mit Wasser. Es wurden 26,1 kg
Neodym und 36,5 kg Salzschlacke mit 7,8 % Nd-Inhalt ausgebracht. Die gesamte Chargenzeit
ohne Abkühlen der Reaktionsprodukte dauerte 3 Stunden und 45 Minuten. (Siehe auch
Tab. 1)
Beispiel 1
[0012] In dem in Fig.1 dargestellten Lichtbogenofen wurden 15 kg einer Salzmischung , bestehend
aus ca. 70 Gew.-% CaCl2 und Ca. 30 Gew.-% CaF2, nach Zünden des Lichtbogens über eine
Kurzschlußbrücke, vorgeschmolzen. Die Ofenspannung betrug 90 Volt und der Strom zwischen
800 und 1000 Ampere. Gleichzeitig mit dem Einschmelzen der Salzmischung verdrängten
wir die Luft im Ofenraum durch Einblasen von Argon. Nachdem die Vorlageschmelze die
Temperatur von Ca. 1100°C erreicht hatte, begannen wir über die Zahnradschleuse mit
dem Eintragen der Reaktionsmischung, bestehend aus 50 kg entwässertem NdCl3 (0,8 %
Restwasser, 14 % Oxychlorid) und 13,0 kg granuliertem Calciummetall. Sobald sich in
der Salzschmelze ein leichter Metallnebel gebildet hatte, konnten wir die Ofenspannung
an den in die Schmelze tauchenden Wolframelektroden auf 50 Volt reduzieren, während
wir den Strom auf ca.2500 Ampere erhöhten. Die dadurch verursachten, starken elektromagnetischen
Kräfte bewirken eine ausgeprägte Bewegung der Schmelze, wodurch die eingetragenen
Möllerstoffe sehr rasch in die Schmelze eingezogen wurden. Bedingt dadurch konnte
die vorliegende Reaktionsmischung sehr rasch innerhalb von 35 Minuten eingeschmolzen
werden. Zirka 5 Minuten nach Beendigung des Eintragens verringerte sich die Leitfähigkeit
der Salzschlacke, bedingt durch das Abscheiden des Metallnebels, worauf der Abstich
von Metall und Schlacke weitgehend getrennt in gußeiserne Vorlagen erfolgte. Die Gesamtdauer
der Ofenreise betrug 1 Stunde und 25 Minuten. Das erhaltene Neodymmetall behandelten
wir zur Entfernung der Salzschlacke mit Wasser. Es wurden 27,8 kg Neodym und 49,3
kg Salzschlacke mit 1,4 Gew.-% Nd erhalten. (Siehe auch Tab.1)
Beispiel 2
[0013] Nach dem im Beispiel 1 beschriebenen Verfahren wurden 15 kg Salzschmelze bestehend
aus 50 Gew.-% CaCl2 und 50 Gew.-% CaF2, vorgeschmolzen. In diese Schmelze trugen
wir darauf bei einer Temperatur von ca. 1100°C wie im Beispiel 1 eine Mischung bestehend
aus 40 kg Neodymfluorid, 13 kg granuliertem Calciummetall und 23 kg wasserfreiem
CaCl2 ein. Nach einer Einschmelzzeit von 55 Minuten und Nachfahren von 5 Minuten
konnten wir 27,3 kg Neodymmetall und 62,5 kg Salzschlacke mit 2,4 Gew.-% Neodyminhalt
gewinnen. Die Gesamtchargenzeit betrug 1 Stunde und 45 Minuten. (Siehe auch Tab.1)
Beispiel 3
[0014] In gleicher Weise wie im Beispiel 1 haben wir 15 kg wasserfreies CaCl2 vorgeschmolzen.
Nach Erreichung einer Temperatur der Salzschlacke von 950 - 1000°C trugen wir, wie
im Beispiel 1 beschreiben, eine Mischung bestehend aus 50 kg wasserfreiem Lanthanchlorid
(0,5 % Restwasser, 7 % Oxychlorid) und 13,3 kg granuliertem Calciummetall in die durch
elektromagnetische Kräfte stark bewegte Salzschmelze ein. Die Einschmelzzeit betrug
32 Minuten. Nach einer Nachfahrzeit von wiederum 5 Minuten zogen wir Metall und Schlacke
weitgehend voneinander getrennt in Vorlagen ab. Wir erhielten 27,8 kg Lanthanmetall
und 50,3 kg Salzschlacke mit 1,4 % Lanthaninhalt. (Siehe auch Tab.1)
Beispiel 4
[0015] Nach Beispiel 1 wurden 15 kg wasserfreies CaCl2 vorgeschmolzen und in diese Schmelze
bei einer Temperatur von 900°C eine Mischung zusammengesetzt aus 50 kg wasserfreiem
Cerchlorid (0,8 % Restwasser, 8 % Oxychlorid), 9,3 kg granuliertem Calciummetall und
2,4 kg Magnesiumgrieß, eingetragen. Nach einer Einschmelzzeit von 35 Minuten und einer
Nachschmelzzeit von wieder 5 Minuten konnten wir 26,8 kg Cermetall und 49,3 kg Salzschlacke
mit 3,3 % Cerinhalt abgießen. (Siehe auch Tab.1)
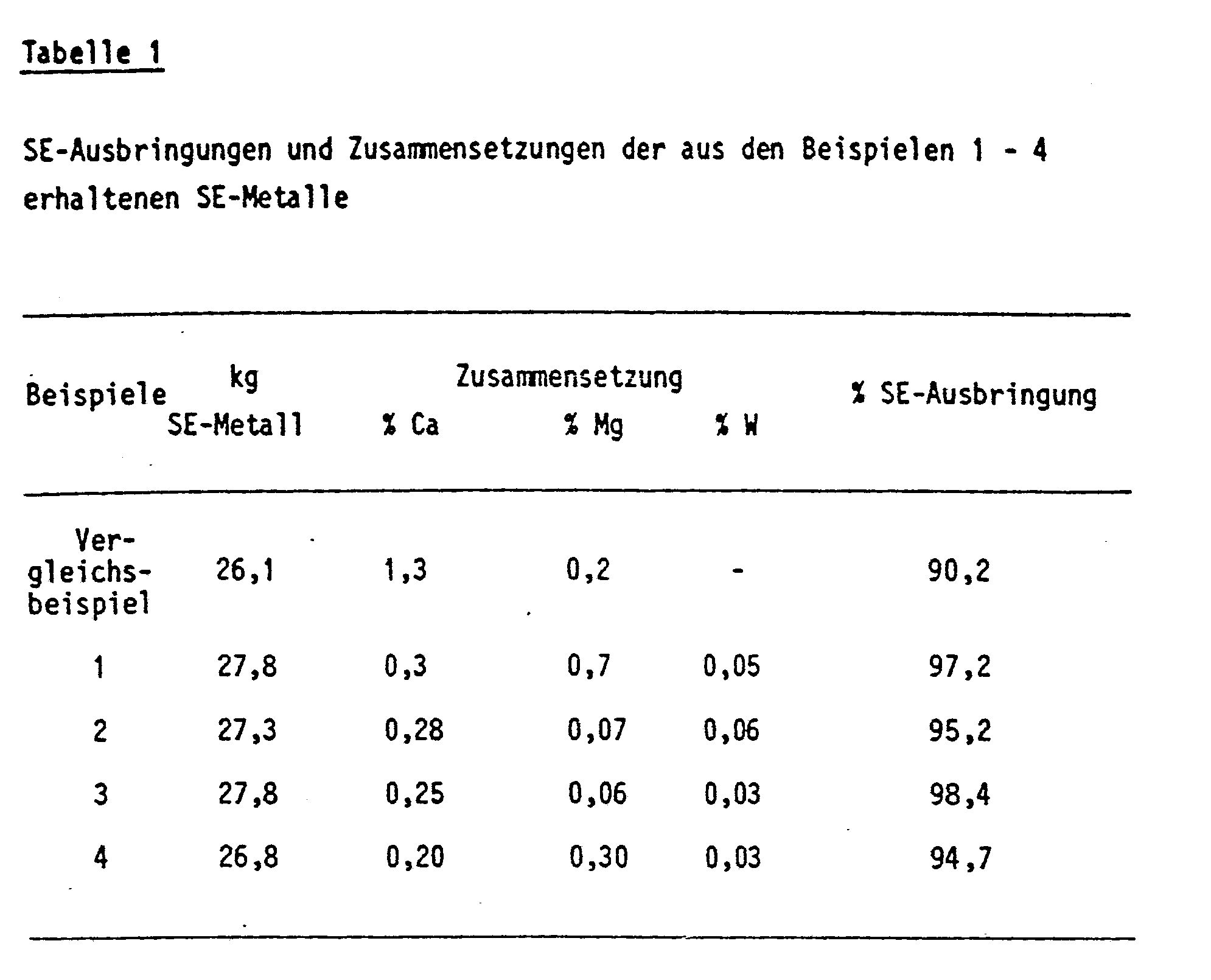
Beispiel 5
[0016] Wie im Beispiel 1 beschrieben worden ist, wurde in dem in Fig.1 dargestellten Lichtbogenofen
15 kg wasserfreies CaCl2 vorgeschmolzen. Die hier verwendeten Lichtbogenelektroden
waren aus einem unlegierten, kohlenstoffarmen Stahl gefertigt. Bei einer Temperatur
der Salzschmelze von 850 - 900°C trugen wir unter Ausnutzung der im Beispiel 1 beschriebenen,
starken Bewegung der Schmelze durch elektromagnetische Kräfte einer Mischung bestehend
aus 50 kg wasserfreiem Neodymchlorid (0,8% Restwasser, 14 % Oxychlorid), 13 kg granuliertem
Calciummetall und 2,3 kg Schwammeisen ein. Die Einschmelzzeit betrug 33 Minuten.
Nach einer Nacherhitzungszeit von 5 Minuten und einer Gesamtschmelzzeit von 1 Stunde
und 22 Minuten gossen wir den Ofeninhalt weitgehend getrennt in Legierungund Salzschlacke
in entsprechende Vorlagen ab. Wir erhielten 32,5 kg Legierung und 49,8 kg Salzschlacke
mit 1,3 % Neodyminhalt. (Siehe auch Tab.)
Beispiel 6
[0017] Nach Beispiel 1 wurden 15 kg wasserfreies CaCl2 vorgeschmolzen. Bei einer Temperatur
der Schmelze von 100 - 1050°C trugen wir eine Mischung, bestehend aus 40 kg Dysprosiumfluorid,
12 kg granuliertem Calciummetall, 3,7 kg Schwammeisen und 7 kg wasserfreiem CaCl2,
in diese ein. Nach einer Eintragszeit von 35 Minuten, einer Nachfahrzeit von 5 Minuten,
konnten wir 31,3 kg Legierung und 45,8 kg Salzschlacke mit 4,5 % Dysprosiuminhalt
ausbringen. Die Elektroden des Lichtbogenofens bestanden aus Wolfram. (Siehe auch
Tab.2)
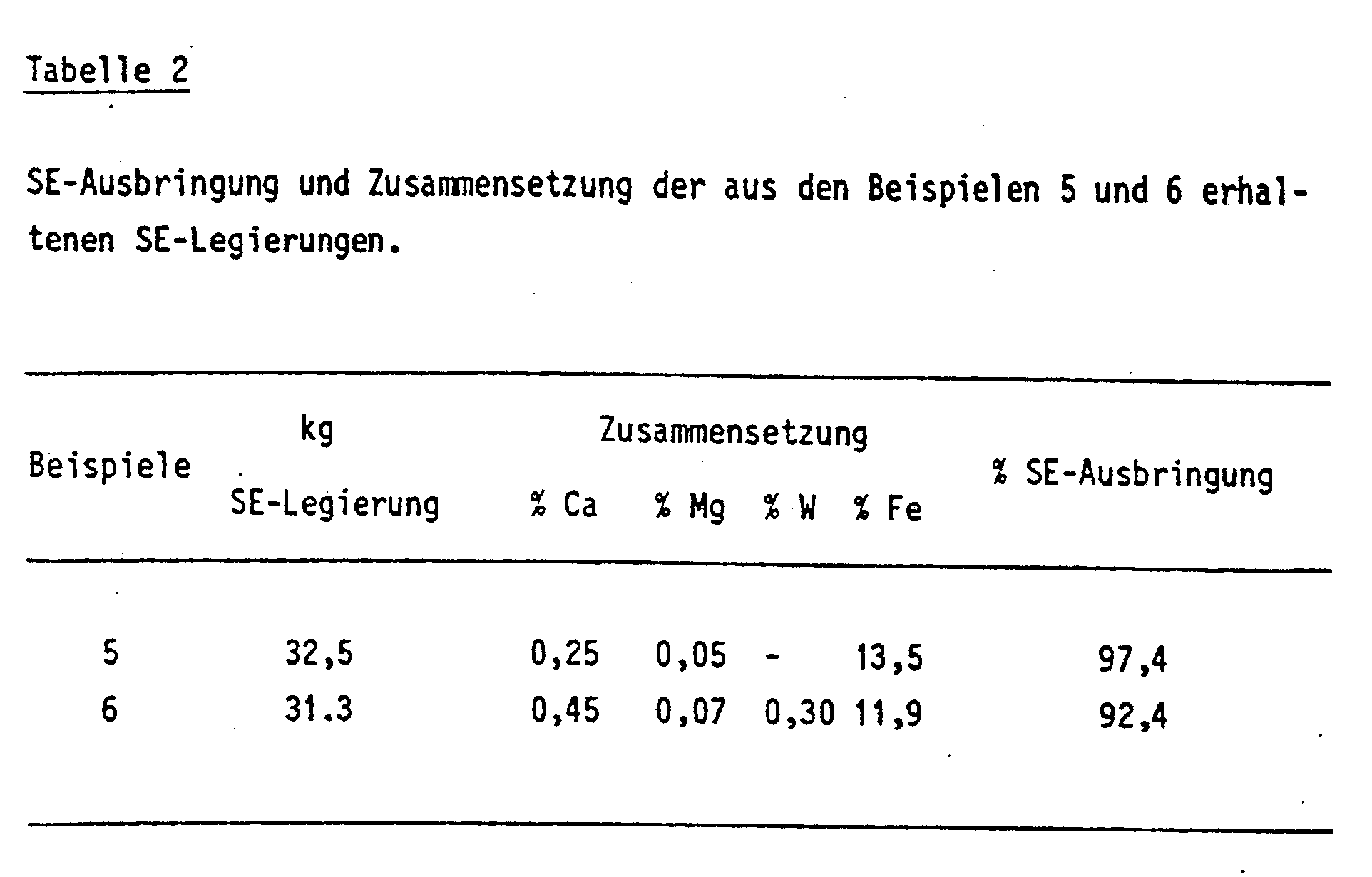
Beispiel 7
[0018] Entsprechend der Ausführungsform von Beispiel 1 wurden im Lichtbogenofen nach Fig.1,
der mit wassergekühlten Kupferelektroden ausgestattet war, 15 kg einer Salzmischung,
bestehend aus 60 Gew.-% CaF2 und 40 Gew.-% wasserfreiem CaCl2, vorgeschmolzen. Bei
einer Temperatur der Salzschmelze zwischen 1300 und 1350°C trugen wir eine Mischung,
zusammengesetzt aus 30 kg Neodymfluorid, 9,5 granuliertem Calciummetall, 3,9 kg Ferrobor
(19,6 % B), 10 kg Schwammeisen, 25,0 kg feinstückigem Reineisenschrott und11,0 kg
wasserfreiem CaCl2 in den Lichtbogenofen ein. Die Eintragszeit betrug 44 Minuten.
Nach einer Nachfahrzeit von ca. 5 Minuten wurde die Legierung in eine entsprechende
Kokille weitgehend frei von der Salzschlacke abgegossen. Die Schlacke floß in eine
getrennte Vorlage. Wir erhielten 58,6 kg Nd-Fe-B-Legierung und 44,2 kg Salzschlacke
mit4,3 % Neodyminhalt.
[0019] Die Legierung hatte folgende Zusammensetzung:
33,5 % SE
1,3 % B
0,07 % Al
0,08 % Si
0,05 % Ca
0,05 % Mg
[0020] Die SE-Ausbringung lag bei 91,3 % bewußt etwas tiefer, um den Calciumgehalt in der
Legierung zu begrenzen.
[0021] Aus den Ergebnissen der Beispiels 1 - 7 geht deutlich hervor, daß nach dem erfindungsgemäßen
Verfahren SE-Metalle und Legierung sehr rasch, mit hoher SE-Ausbringung und Wirtschaftlichkeit
hergestellt werden können. Hauptgrund dafür ist sicherlich, daß durch die starke Rührwirkung,
hervorgerufen durch elektromagnetische Kräfte, eine sehr rasche innige Vermischung
der flüssigen Reaktionspartner erforlgt.
1. Verfahren zur Herstellung von SE-Metallen und SE-haltigen Legierungen, dadurch
gekennzeichnet, daß die Reduktion von SE-Halogeniden und/oder SE-Oxiden einzeln oder
als Gemisch gegebenenfalls mit Legierungszusätzen aus der Gruppe der Eisenmetalle
und anderer Legierungselemente sowie gegebenenfalls mit Zusätzen von Alkali- und/oder
Erdalkalimetallsalzen mittels eines oder mehrer Erdalkalimetalle unter einer gegen
SE-Metalle, SE-Verbindungen und Erdalkalimetalle weitgehend inerten Atmosphäre in
einem elektrischen LBO im zweiphasigen Ofenbetrieb erfolgt, wobei in diesem zur Erreichung
einer möglichst raschen und vollständigen Reduktion auf Grund des entsprechend gewählten
Strom-Spannungsverhältnisses eine starke Rührwirkung in der Schmelze durch elektromagnetische
Kräfte erzeugt wird.
2. Verfahren nach Anspruch 1, dadurch gekennzeichnet, daß die Legierungssätze in
metallischer Form, als Oxid oder in Form ihrer Salze erfolgen.
3. Verfahren nach Anspruch 1, dadurch gekennzeichnet, daß als Erdalkalimetalle Ca
und/oder Mg verwendet werden.
4. Verfahren nach Anspruch 1, dadurch gekennzeichnet, daß die erhaltenen Legierungen
neben einem oder mehreren Elementen der SE-Gruppe noch Fe, Co und/oder Ni in einer
Menge von 5 - 80 Gew.-% enthalten.
5. Verfahren nach Anspruch 1, dadurch gekennzeichnet, daß die erhaltenen Legierungen
neben einem oder mehreren Elementen der SE-Gruppe noch ein oder mehrere Elemente der
3a in einer Menge von 0,02 bis 15 Gew.-% enthalten.
6. Verfahren nach Anspruch 1, dadurch gekennzeichnet, daß die erhaltenen Legierungen
neben einem oder mehreren Elementen der SE-Gruppe ein oder mehrere Elemente aus der
Gruppe Fe, Co, Ni in einer Menge von vorzugsweise 50 - 80 Gew.-% noch ein oder mehrere
Elemente aus der 3a-Gruppe in einer Menge von 0,02 - 5 Gew.-% enthalten.
7. Verfahren nach Anspruch 1, dadurch gekennzeichnet, daß als Elemente aus der 3a-Gruppe
B und/oder Al eingesetzt werden.
8. Verfahren nach Anspruch 1, dadurch gekennzeichnet, daß der in den SE-Metallen
oder jeweiligen Legierungen aus Rohstoffen, Zuschlägen und Reduktionsmitteln stammende
Gehalt als Verunreinigung zu betrachtender Elemente <5 Gew.-%, vorzugsweise <2 Gew.-%
beträgt.
9. Verfahren nach Anspruch 1, dadurch gekennzeichnet, daß als SE-Halogenide die Fluoride
und/oder Chloride eingesetzt werden.
10. Verfahren nach Anspruch 1, dadurch gekennzeichnet daß als Alkali- und/oder Erdalkalimetallsalze
vorzugsweise LiF, CaF₂, CaCl₂ einzeln oder als Mischung verwendet werden.
11. Verfahren nach Anspruch 1 bis 10, dadurch gekennzeichnet, daß der verwendete LBO
eine Deckelkonstruktion aufweist, die das Aufrechterhalten einer gegen SE-Metalle,
SE-Verbindungen und Erdalkalimetalle weitgehend inerten Atmosphäre gewährleistet
und über die neben den Elektroden die zur Herstellung von SE-Metallen oder Legierungen
vorgesehene Mischung weitgehend kontinuierlich in das Innere des LBO eingetragen
werden kann.
12. Verfahren nach Anspruch 1 oder 11, dadurch gekennzeichnet, daß Elektroden eingesetzt
werden, die gegen SE-Metalle weitgehend inert sind.
13. Verfahren nach Anspruch 1 oder 12, dadurch gekennzeichnet, daß Elektroden eingesetzt
werden, die aus Kohlenstoff, vorzugsweise Graphit, Wolfram, Kupfer, Molybdän oder
Tantal bestehen.
14. Verfahren nach Anspruch 1 oder 11, dadurch gekennzeichnet, daß zur Herstellung
von SE-Legierungen Elektroden eingesetzt werden, die gegen die SE-Legierung inert
sind oder aus einem Element, vorzugsweise der Eisengruppe bestehen.