[0001] Die Erfindung betrifft ein Verfahren zur elektrolytischen Einfärbung von anodisierten
Oberflächen von Aluminium oder Aluminiumlegierungen unter Verwendung von Wechselstrom
oder wechselstromüberlagertem Gleichstrom, wobei die elektrolytische Färbung mit einem
kationische organische Farbstoffe enthaltenden Elektrolyt durchgeführt wird.
[0002] Zur Erhöhung des Korrosionswiderstandes und zur Erzielung dekorativer Wirkungen kann
die Oberfläche des Aluminiums und seiner Legierungen auf mechanischem Wege wesentlich
verändert oder mit metallischen oder nichtmetallischen überzügen versehen werden.
Große Bedeutung hat die Verstärkung des natürlichen schützenden Oxidfilms durch chemische
oder elektrische Verfahren.
[0003] Bei den Verfahren zur Einfärbung von Oberflächen von Aluminium oder Aluminiumlegierungen
unterscheidet man nach dem Stand der Technik, siehen Wernick, Pinner, Zurbrügg, Weiner
"Die Oberflächenbehandlung von Aluminium", Leuze Verlag, Sauigau/Württ. (1977), Seiten
354 bis 374 und 309 bis 312, die adsorptive Einfärbung, die Farbanodisierung und die
elektrolytische Einfärbung.
[0004] Bei der adsorptiven Einfärbung wird beispielsweise ein organischer Farbstoff in die
Öffnungen der Poren der Oxidschicht eingebracht, wobei dieser in der Oberflächenregion
der Oberfläche adsorbiert bleibt. Durch des genannte Verfahren kann das gesamte Farbspektrum
mit einer großen Gleichmäßigkeit und Reproduzierbarkeit erhalten werden. Die verschiedensten
Farbstoffe, die hierzu Verwendung finden können, sind käuflich erhältlich.
[0005] Ferner ist die sogenannte Farbanodisierung (Integralverfahren) seit Jahren in der
Anwendung. In einem integralgefärbten Film befinden sich die feinverteilten anorganischen
Farbpartikel nicht in den Poren der Oxidschicht, sondern bleiben als Legierungsbestandteil
in der Aluminiumoxidschicht zurück. Hierbei werden spezielle Aluminiumlegierungen
meistens unter Verwendung von Gleispannungen bis zu 150 V in nur einem Verfahrensschritt
sowohl eloxiert als auch eingefärbt, wobei als Elektrolyt geeignete organische Säuren,
z.B. Maleinsäure, Oxalsäure, Sulfosalicylsäure oder Sulfophthalsäure, eingesetzt werden.
Das Integralverfahren wird jedoch aus Kostengründen (hoher-Stromverbrauch, aufwendige
Kühleinrichtungen) in der Praxis immer weniger angewendet.
[0006] Bei der elektrolytischen Einfärbung mittels Metallsalzlösungen dagegen wird durch
anodische Oxidation unter Anwendung von Gleichstrom in wäßriger Schwefelsäure und/oder
anderen Elektrolytlösungen in einem ersten Verfahrensschritt zunächst eine farblose
transparente Oxidschicht erzeugt, deren Einfärbung anschließend in einem zweiten Verfahrensschritt
- im Unterschied zur adsorptiven Färbung - durch Abscheidung von Metallteilchen aus
Metallsalzlösungen am Grunde der Oxidschichtporen mittels Wechselstrom erfolgt. Die
Farbtöne reichen hierbei von hellbronze über dunkelbronze bis schwarz. Durch die Einlagerung
am Porengrund erhält man völlig lichtbeständige Färbungen (W. Sautter, Metalloberfläche,
32, 1978, Seite 450 bis 454).
[0007] Die elektrolytischen Einfärbeverfahren werden für die Einfärbung von Aluminium -
das im Architekturbereich Verwendung finden soll - aufgrund ihrer Vorteile, wie höhere
Lichtbeständigkeit und Wetterbeständigkeit, in überwiegendem Maße eingesetzt. Bei
den elektrolytischen Einfärbeverfahren überwiegen aufgrund niedrigerer Kosten und
damit höherer Wirtschaftlichkeit eindeutig - gegenüber der Integralfärbung - die elektrolytischen
Metallsalzeinfärbungen, wobei hierzu bevorzugt Sn(II)-, Co-, Ni- un Cu-haltige Elektrolytlösungen
verwendet werden.
[0008] Die DE-OS 28 50 136 beschreibt ein Verfahren zur elektrolytischen Metallsalzeinfärbung
von Aluminium, bei dem zuerst mittels Gleichstrom in saurer Lösung eine definierte
Oxidschicht erzeugt und diese anschließend mittels Wechselstrom unter Verwendung eines
Zinn(11)-Salze'enthaltenden sauren Elektrolyten eingefärbt wird, wobei der Elektrolyt
auch Stabilisatoren für die Zinn(II)-Salze enthält. Derartige, Metallsalze enthaltende
Färbeelektrolyten sind jedoch ungeeignet, um beliebige Buntheit und Helligkeit auf
den Aluminium- und Aluminiumlegierungsoberflächen zu erzeugen.
[0009] Die DE-PS 32 48 472 beschreibt ein Verfahren zum Einfärben von anodisch erzeugten
Oxidschichten auf Aluminium und Aluminiumlegierungen, bei dem ein Färbeelektrolyt
zum Einsatz kommt, mit dem Farben unterschied licher Buntheit und Helligkeit, insbesondere
zur Anwendung bei Profilen für Fenster, Türen, Fassadenelementen und dergleichen,
auf anodisierten Aluminiumoberflächen erzeugt werden können. Um derartige Einfärbungen
in wirtschaftlicher Weise auch bei unterschiedlichen Farbnuancen jederzeit farbgleich
reproduzierbar herstellen zu können, enthält der Färbeelektrolyt außer einem Metallsalz
eine organische Farbstoffkomponente. Als organische Farbstoffkomponente wird ein metallkomplexhaltiger
Azofarbstoff vorgeschlagen. Somit beschreibt die DE-OS 32 48 472 ein Verfahren zum
Einfärben von anodisch erzeugten Oxidschichten in einem Metallsalze enthaltenden Elektrolyten
unter gleichzeitiger adsorptiver Einfärbung mit einem metallkomplexhaltigen Azofarbstoff.
[0010] Die vorstehend beschriebenen Färbeverfahren befriedigen in anwendungstechnischer
Hinsicht jedoch nicht in vollem Umfange: Die elektrolytischen Farbeverfahren -sowohl
das Integralverfahren als auch die Metallsalzfärbung - erbringen keine bunten Farben,
sondern vielmehr nur graue bzw. bronzene bis - schwarze Farbtöne. Mittels Adsorptivverfahren
läßt sich zwar eine breite Palette bunter Farben erzielen; die Farbstoffe werden jedoch
hierbei nur im oberen Porenbereich adsorbiert. Solche Färbungen sind daher nicht abriebfest:
Bei mechanischen Belastungen wird die Oberfläche angegriffen, d.h. die Farbstoffe
werden abgetragen und die Färbung somit aufgehoben. Da solche Belastungen meist in
lokal unregelmäßiger weise erfolgen, sind die hierbei erzeugten Kratzer, Flecken,
Verfärbungen und dergleichen besonders auffällig. Die Gebrauchsfähigkeit derartig
eingefärbter Aluminiumteile ist daher in starkem Maße beeinträchtigt. Auch für Aluminiumfassa
den sind solche Oberflächeneinfärbungen ungeeignet, da Reinigungen derselben mit üblicherweise
Abrasivstoffen enthaltenden Mitteln zu einem Verblassen führen.
[0011] Der vorliegenden Erfindung liegt daher die Aufgabe zugrunde, ein verbessertes Verfahren
zur elektrolytischen Einfärbung anodischer Oberflächen von Aluminium oder Aluminiumlegierungen
unter Verwendung von Wechselstrom oder wechselstromüberlagertem Gleichstrom zur Verfügung
zu stellen, welches die vorstehenden Nachteile nicht aufweist.
[0012] Die Aufgabe der vorliegenden Erfindung wird dadurch gelöst, daß man die elektrolytische
Färbung unter Verwendung eines kationische organische Farbstoffe enthaltenden Elektrolyten
durchführt.
[0013] Gegenstand der vorliegenden Erfindung ist dementsprechend ein Verfahren zur elektrolytischen
Einfärbung anodisierter Oberflächen von Aluminium oder Aluminiumlegierungen unter
Verwendung von Wechselstrom oder wechselstromüberlagertem Gleichstrom, wobei die elektrolytische
Einfärbung mit einem kationische organische Farbstoffe enthaltenden wäßrigen Elektrolyten,
der gegebenenfalls noch zusätzlich Leitsalze enthält, durchgeführt wird.
[0014] Der Vorteil des erfindungsgemäßen Verfahrens zur elektrolytischen Einfärbung besteht
gegenüber adsorptiven Einfärbungen darin, daß die kationischen organischen Farbstoffe
bei der elektrolytischen Einfärbung bis auf den Grund der Poren der Oxidschicht vordringen,
wodurch ein besserer Schutz der Farbstoffe gegen Abrieb und Korrosion bewährleistet
ist. Infolge dieser tiefen Ablagerung im Grund der Poren gelingt es, in wirt schaftlicher
Weise außerordentlich abriebfeste bunte Farbtöne auf anodisiertem Aluminium zu erzeugen.
[0015] Durch die im Stand der Technik bekannte elektroadsorptive Einfärbung von organischen
Farbstoffen war es bisher lediglich möglich, sogenannte unbunte Farbtöne, wie beispielsweise
Grautöne, auf anodisiertem Aluminium zu erhalten. Demgegenüber ermöglicht das erfindungsgemäße
Verfahren die Erzeugung einer großen Farbvielfalt bei gleichzeitig hoher Eindringtiefe.
[0016] Prinzipiell können im Sinne des erfindungsgemäßen Verfahrens alle kationischen organischen
Farbstoffe Verwendung finden. Beispiele hierfür sind Farbstoffe aus den Gruppen der
Triphenylmethan-Farbstoffe, Cyanin-Farbstoffe, Xanthen-Farbstoffe (Xanthenfarbstoffe
der Rhodamingruppe), Acridin-Farbstoffe, Azin-Farbstoffe, Thiazinfarbstoffe oder der
Pyryliumfarbstoffe. Von diesen sind im Sinne des erfindungsgemäßen Verfahrens Farbstoffe
aus den Gruppen der Triphenylmethan-Farbstoffe, der Xanthen- Farbstoffe und der Azin-Farbstoffe
besonders bevorzugt. Als Beispiele für Vertreter aus diesen bevorzugten Gruppen der
kationischen Farbstoffe seien genannt: Kristallviolett, Malachitgrün, Methylviolett,
Rhodamin 6G, Methylenblau. Solche Farbstoffe können sowohl einzeln als auch in Form
von Gemischen in dem erfindungsgemäßen Verfahren verwendet werden.
[0017] Aufgrund der positiven Ladung der kationischen organischen Farbstoffe schlagen sich
diese während der negativen Halbwelle des Wechselstroms auf dem Porengrund nieder.
[0018] Im allgemeinen können die kationischen organischen Farbstoffe alle möglichen Anionen
aufweisen, sofern diese keinen störenden Einfluß auf die elektrolytische Abscheidung
der kationischen organischen Farbstoffe ausüben. In diesem Sinne ist bei der Auswahl
des Anions natürlich zu beachten, daß das Farbstoff-Salz in Wasser löslich ist. Prinzipiell
kommen als Anionen für die Farbstoff-Kationen die Anionen der Mineral- und Carbonsäuren
in Frage, beispielsweise Chlorid, Sulfat, Perchlorat, Acetat, Tetrafluorborat oder
Oxalat. Bevorzugte Anionen für die kationischen organischen Farbstoffe im Sinne der
Erfindung sind: Chloride, Perchlorate und/oder Oxalate. Derartige Farbstoffsalze sind
zum Teil käuflich erhältlich oder deren Herstellung ist dem Fachmann geläufig.
[0019] Das erfindungsgemäße Verfahren wird in den im Stand der Technik gebräuchlichen Spannungs-
und Stromdichtenbereichen durchgeführt, die für elektrolytische Metallsalzeinfärbungen
üblicherweise verwendet werden. In der Regel wird das erfindungsgemäße Verfahren bei
einer - vom Elektrodenabstand abhängigen - Spannung im Bereich von 8 bis 30 V und
den sich unter diesen Bedingungen einstellenden Stromdichten durchgeführt. Die Frequenz
des Wechselstroms beträgt üblicherweise 50 bis 60 Hz. Als Material für die Gegenelektrode
wird üblicherweise Edelstahl verwendet, jedoch können hierzu auch andere Materialien,
beispielsweise Graphit, eingesetzt werden.
[0020] Sofern im Zusammenhang mit dem erfindungsgemäßen Verfahren von wechselstromüberlagertem
Gleichstrom die Rede ist, so wird hierunter ein unsymmetrischer Wechselstrom verstanden,
dessen Amplitudenhöhen der positiven bzw. negativen Halbwellen unterschiedliche Werte
aufweisen. Entsprechende Schaltungen zur Erzeugung derartiger wechselstromüberlagerter
Gleichströme sind dem Fachmann aus dem einschlägigen Stand der Technik bekannt. In
diesem Zusammenhang sei jedoch auf die bislang unveröffentlichte deutsche Patentanmeldung
P 36 24 868.1 verwiesen.
[0021] Gemäß einer bevorzugten Ausführungsform der vorliegenden Erfindung wird das Verfahren
"bei einer Spannung von 10 bis 22 V und der hierbei resultierenden Stromdichte durchgeführt.
[0022] Erfindungsgemäße elektrolytische Einfärbungen werden in wäßrigen Lösungen durchgeführt.
Dementsprechend ist die obere Grenze der Konzentration des kationischen Farbstoffes
in der wäßrigen Elektrolytlösung durch die Löslichkeitsobergrenze des jeweiligen Farbstoffes
in Wasser vorgegeben. Hinsichtlich der unteren Konzentrationsgrenze des Farbstoffes
ist zu beachten, daß eine zu geringe Konzentration des Farbstoffes im Elektrolyten
eine wirtschaftliche Arbeitsweise im Sinne des erfindungsgemäßen Verfahrens nicht
zuläßt. Somit liegt die Konzentration der kationischen Farbstoffe in der Elektrolytlösung
erfindungsgemäß im Bereich von 0,01 g/I bis hin zur Löslichkeitsobergrenze des jeweiligen
Farbstoffes. Im allgemeinen enthalten die wäßrigen Elektrolytlösungen im Rahmen des
erfindungsgemäßen Verfahrens kationische Farbstoffe in Konzentrationen von 0,01 bis
10 g/I; vorzugsweise liegen die Konzentrationen im Bereich von 0,05 bis 5 g/i.
[0023] Die im Rahmen des erfindungsgemäßen Verfahrens verwendeten Elektrolytlösung können
- zusätzlich zu den kationischen organischen Farbstoffen - Leitsalze enthalten, um
die Leitfähigkeit der Lösungen zu steigern. Entsprechende Leitsalze sind dem Fachmann
aus dem ein schlägigen Stand der Technik bekannt; sie können beispielsweise ausgewählt
werden aus der Gruppe der wasserlöslichen Alkalimetall-, Ammonium- und/oder Erdalkalimetallsalze
derjenigen Säuren, die auch des Anion der kationischen Farbstoffe bilden. Im Sinne
der vorliegenden Erfindung werden als Leitsalze in der Regel Sulfate, bevorzugt Natriumsulfat
oder Magnesiumsulfat, verwendet. Die Konzentration der Leitsalze in den wäßrigen Elektrolytlösungen
liegt erfindungsgemäß im allgemeinen im Bereich von 1 bis 50 g/I; bevorzugt ist hierbei
ein Konzentrationsbereich von 5 bis 20 g/I. Ein Zusatz derartiger Leitsalze kann im
Einzelfall zu einer intensiveren Farbtönung der erzielten Färbung führen. Der Fachmann
wird mithin im Einzelfall - d.h. je nach verwendetem Farbstoff und nach Art und Intensität
der erwünschten Färbung - entscheiden, ob ein solcher Zusatz erwünscht ist.
[0024] Weitere - gleichfalls nicht kritische - Einflußgrößen des erfindungsgemäßen Verfahrens
sind der pH-Wert und die Temperatur der Elektrolytlösung sowie die Verweilzeit des
zu färbenden Gutes in derselben. Hinsichtlich des pH-Wertes der Elektrolytlösung gilt
im allgemeinen, daß für den jeweiligen Farbstoff derjenige pH-Wert optimal ist, der
sich beim Auflösen dieses Farbstoffes - im angegebenen Konzentrationsbereich - in
der wäßrigen Elektrolytlösung einstellt. Darüber hinaus kann jedoch prinzipiell auch
bei anderen pH-Werten der Elektrolytlösung gearbeitet werden. So liegt der pH-Wert
der Elektrolytlösungen im Rahmen des erfindungsgemäßen Verfahrens in der Regel im
Bereich von 1 bis 9; bevorzugt hierbei ist - im Hinblick auf das zuerst Gesagte -
der pH-Bereich von 2 bis 5. Sofern jedoch eine pH-Werte Einstellung der wäßrigen Elektrolytlösung
erwünscht ist, verwendet man hierzu Säuren bzw. Laugen, die keinen störenden Einfluß
auf die elektrolytische Abscheidung der kationischen Farbstoffe ausüben, beispielsweise
verdünnte wäßrige Schwefelsäure bzw. Natronlauge.
[0025] Hinsichtlich der Temperatur der Elektrolytlösung gilt, daß man vorzugsweise - alleine
im Hinblick auf die hiermit verbundene Energieersparnis - bei Raumtemperatur, d.h.
in einem Temperaturbereich von ca. 15 bis 25 C, arbeitet. Im Einzelfall, d.h. wiederum
in Abhängigkeit von den gewählten Farbstoff, kann es jedoch zweckmäßig sein, höhere
Temperaturen - beispielsweise bis ca. 60 C - zu wählen, um die Diffusion der Farbstoffmoleküle
zu unterstützen und somit eine gleichmäßigere Färbung zu erzielen.
[0026] Die Verweilzeit des zu färbenden Gutes in der Elektrolytlösung richtet sich vornehmlich
nach der erwünschten Farbtiefe der Färbung. Hierzu lassen sich keine allgemein gültigen,
verbindlichen Richtwerte angeben, vielmehr muß die optimale Verweilzeit von Fall zu
Fall ausprobiert werden. Beispielhaft seien hier jedoch Verweilzeiten von ca. 15 bis
hin zu 30 Minuten genannt.
[0027] Die zuletzt diskutierten Parameter Temperatur und Verweilzeit dienen insbesondere
einer Optimierung der erwünschten Färbung und bedürfen im Einzelfalle der Durchführung
einiger orientierender Vorversuche.
[0028] Gemäß einer bevorzugten Ausführungsform des erfindungsgemäßen Verfahrens wird das
zu färbende Gut; d.h. die anodisierten Werkstücke aus Aluminium oder Aluminiumlegierungen,
vor der eingentlichen Färbebehandlung unter Anwendung von Wechselstrom oder wechselstromüberlagertem
Gleichstrom zunächst - im gleichen Elektrolyten - einer Behandlung mit Gleichstrom
unterworfen. Hierbei wird das Werkstück bzw. die Werkstücke als Anode geschaltet.
Die Spannung des Gleichstromes liegt während dieser Behandlung im vorstehend erwähnten
Bereich; hinsichtlich der übrigen Parameter gilt gleichfalls das vorstehend Gesagte.
Während dieser Vorbehandlung erfolgt noch nicht der eigentliche Färbeprozeß; diese
Vorbehandlung bedingt vielmehr eine erhöhte Gleichmäßigkeit der nachfolgenden Färbung
sowie eine bessere Tiefenstreuung derselben. Nähere Einzelheiten zu einer solchen
Vorbehandlung mittels Gleichstrom sind in der DE-OS 26 09 146 beschrieben.
[0029] Durch die Anwendung mehrerer, aufeinander folgender Behandlungen nach dem erfindungsgemäßen
Verfahren lassen sich durch gezieltes Abstimmen der Einflußgrößen der einzelnen Behandlungen
die unterschiedlichsten Farbnuancen der Aluminiumoxidschichten erzielen.
[0030] Vor der erfindungsgemäßen elektrolytischen Einfärbung der anodisierten Oberflächen
werden die aus Aluminium bzw. dessen Legierungen hergestellten Gegenstände einer üblichen
Vorbehandlung zur Herstellung der oxidischen Oberflächenschicht unterzogen. Bei dieser
ersten Behandlungsstufe sind der Zustand der zu anodisierenden Halbzeuge, d.h. der
Glanz- bzw. Mattheitsgrad der Oberflächen, sowie die Elektrolytzusammensetzung und
die Arbeitsbedingungen während des Anodisiervorganges wichtige Einflußgrößen. Hier
gelten die dem Fachmann aus dem einschlägigen Stand der Technik, beispielsweise der
eingangs zitierten Monographie von Wernick, Pinner, Zurbrügg und Weiner, bekannten
Bedingungen.
[0031] Die nachfolgend genannten Ausführungsbeispiele dienen der Erläuterung der Erfindung,
ohne jedoch die vorliegende Erfindung auf die in den Ausführungsbeispielen genannten
Einzelheiten zu beschränken.
Beispiele
Vorbehandlung:
[0032] Für die nachstehenden Beispiele wurden Probebleche (Dimension 50 mm x 40 mm x 1 mm)
aus dem Werkstoff AI 99,5 (DIN-Werkstoff Nr. 3.0255) verwendet.
[0033] Vor dem Anodisieren wurden die Bleche nach herkömmlichen Verfahren entfettet, gebeizt
und dekapiert. Die Entfettung erfolgte mit einem alkalischen Reiniger, enthaltend
Borate, Carbonate, Phosphate und nichtionische Tenside (P3-almeco@ 18, Fa. Henkel
KGaA, Düsseldorf); Badkonzentration: 5 Gew.-%, Temperatur: 70 °C, Tauchzeit: 15 Minuten.
Zum Beizen wurde ein Gemisch (3:1) aus NaOH und einem Alkali, Alkohole und Salze anorganischer
Säuren enthaltendem Beizmittel (P3-almeco® 46, Fa. Henkel KGaA, Düsseldorf) verwendet;
Badkonzentration: 8 Gew.-%, Temperatur: 55
* C, Tauchzeit: 10 Minuten. Das Dekapieren erfolgte mit einem sauren, Salze anorganischer
-Säuren sowie anorganische Säuren enthaltendem Dekapiermittel (P3-almeco® 90, Fa.
Henkel KGaA, Düsseldorf), Badkonzentration: 15 Gew.-%, Temperatur 20 C, Tauchzeit:
10 Minuten. Nach jedem Verfahrensschritt-wurden die Bleche mit entionisiertem Wasser
gründlich gespült.
[0034] Die anschließende Anodisierung wurde nach dem Gleichstrom-Schwefelsäure-Verfahren
vorgenommen; Badzusammensetzung: 200 g/I H
2SO
4, 10 g/I Al; Lufteinblasung: 8 m
3im
2.h; Temperatur: 18 °C; Gleichspannung: 15 V. Die Anodisierzeiten betrugen etwa 3 Minuten
pro u.m Schichtaufbau; d.h. die Gesamtanodisierzeiten für die in den nachstehenden
Beispielen angegebenen Oxidschichtdicken von 15 bis 25 um lagen zwischen 45 und 75
Minuten.
[0035] Nach erneutem gründlichen Spülen mit entionisiertem Wasser erfolgte nun die erfindungsgemäße
elektrolytische Färbebehandlung (Einzelheiten nachstehend). Anschließend wurden die
Bleche wiederum gespült und sodann in heißem Wasser unter Zusatz eines Sealingbelagverhinderers
auf Basis von Salzen organischer Säuren und nichtionischer Tenside (P3-almecoseal®
SL, Fa. Henkel KGaA, Düsseldorf) verdichtet; Badtemperatur: 98 bis 100 C, Tauchzeit:
60 Minuten, Konzentration des Sealingbelagverhinderers: 0,2 Gew.-%.
Beispiele 1a bis 1f
[0036] In den nachstehenden Beispielen wurden die verwendeten kationischen Farbstoffe sowie
die Dicke der Oxidschichten variiert.
[0037] Die folgenden kationischen Farbstoffe wurden eingesetzt:
1a: Rhodamin 6G, als Perchlorat (Xanthenfarbstoff)
1b: Kristallviolett, als Chlorid (Triphenylmethanfarbstoff)
lc: Malachitgrün, als Oxalat (Triphenylmethanfarbstoff)
1 d + e: Methylviolett, als Chlorid (Triphenylmethanfarbstoff)
1f: Methylenblau, als Chlorid (Azinfarbstoff).
[0038] Die Farbstoffkonzentration im wäßrigen Elektrolyten betrug jeweils 5 gil, die Temperatur
des Elektrolyten 20 °C und die Behandlungsdauer (Färbezeit) je 15 Minuten. Die pH-Werte
des Elektrolyten ergaben sich jeweils durch Auflösen des genannten Farbstoffes in
der angegebenen Konzentration. Lediglich im Falle des Beispiels 1e wurde mittels H2S04
ein niederer pH-Wert eingestellt. Es wurde jeweils mit einer Wechselspannung von 15
V (50 Hz) - Gegenelektrode aus Edelstahl - gearbeitet.
[0039] Die Messung der Dicke der Oxidschicht erfolgte nach dem Wirbelstromprinzip gemäß
DIN 50984. Im Anschluß an die elektrolytische Einfärbung wurde die jeweilige Eindringtiefe
der Färbung durch Abreiben der Oxidschicht bis zur beginnenden Aufhellung mit einem
Abriebtestgerät nach ISO
/TC 79/SC 2 N420E und anschließender Messung der verbleibenden Schichtdicke wie vorstehend
angegeben bestimmt. Die ermittelten Werte sind in der nachstehenden Tabelle 1 zusammengefaßt:

[0040] Die vorstehenden Werte zeigen, daß es das erfindungsgemäße Verfahren ermöglicht,
unterschiedliche Färbungen der Oxidschicht bei gleichzeitig hohen Eindringtiefen in
dieselbe zu erzeugen. Beispiel 1e e verdeutlicht, daß durch Variation des pH-Wertes
die Eindringtiefe der Färbung beeinflußt bzw. gesteuert werden kann.
Beispiele 2a und 2i
[0041] Diese Beispiele wurden ausschließlich mit dem kationischen Farbstoffe Malachitgrün
(als Oxalat) - unter Variation-der-Farbstoffkonzentration, der Spannung und der Färbezeit
- durchgeführt. Die nachstehenden Parameter wurden bei allen Beispielen konstant gehalten:
Oxidschichtdicke: jeweils 22 u.m; pH-Wert des wäßrigen Elektrolyten: 2,3; Temperatur
des Elektrolyten: 20 ° C. In Beispiel 2i wurde dem Elektrolyten zusätzlich ein Leitsalz
- 10 g/l MgSO
4- zugefügt.
[0042] Die ermittelten Werde sind in Tabelle 2 zusammengefaßt:
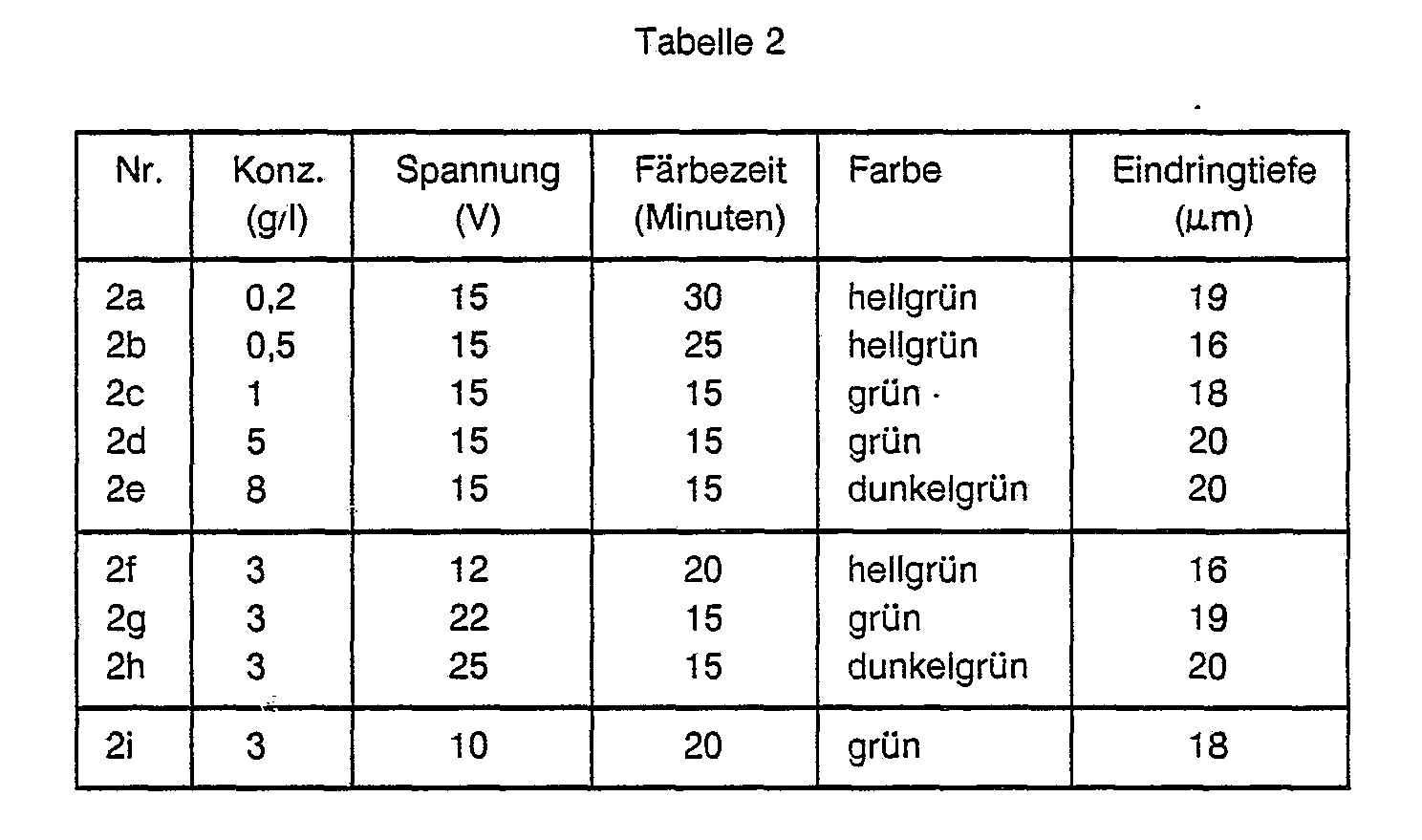
[0043] Die in den Beispielen 2a bis 2e ermittelten Werte zeigen, daß mit zunehmender Konzentration
des Farbstoffes intensivere Farbtönungen - bei etwa gleicher Eindringtiefe - resultieren.
Auch eine Erhöhung der Spannung -Beispiele 2f bis 2h - führt zu diesem Ergebnis. Der
Einfluß unterschiedlicher Färbezeiten ist demgegenüber weniger stark ausgeprägt.
[0044] Der Zusatz des Leitsalzes in Beispiel 2i führt - im Vergleich zu Beispiel 2f, bei
gleicher Färbezeit aber geringerer Spannung - gleichfalls zu einer intensiveren Farbtönung;
die Eindringtiefe wird hierdurch jedoch nicht nennenswert beeinflußt.
Vergleichsversuche 3a bis 3d
[0045] Zu dem Vergleichsversuchen wurden Probebleche eingesetzt, die in gleicher Weise wie
in den erfindungsgemäßen Beispielen vorbehandelt waren. Zur Färbung der Oxidschicht
wurden handelsübliche anionische Aluminium-Farbstoffe verwendet. Es wurde jeweils
einerseits im herkömmlichen Tauchverfahren sowie andererseite unter Anwendung von
Wechselstrom - 15 V, 50 Hz -gearbeitet. Die Temperaturen des wäßrigen Bades bzw. des
Elektrolyten betrugen jeweils 60 C; die Färbezeiten 15 Minuten. Der pH-Wert der Bäder
entsprach jeweils denjenigen Werten, die sich beim Auflösen des jeweiligen Farbstoffes
in Wasser ergaben. Farbstoff-Typ, -Konzentration und Dicke der Oxidschicht sowie die
hierbei erzielte Färbung und insbesondere die Eindringtiefen in die Oxidschicht -
ohne und mit Anwendung von Wechselstrom - sind aus Tabelle 3 ersichtlich.

[0046] Es zeigt sich, daß in allen Fällen eine nur unzureichende Eindringtiefe der Färbung
in die Oxidschicht erfolgt, wobei auch die Anwendung von Wechselstrom keine signifikanten
Änderungen - im Sinne von höheren Eindringtiefen - bedingt.
1. Verfahren zur elektrolytischen Einfärbung anodisierter Oberflächen von Aluminium
oder Aluminiumlegierungen unter Verwendung von Wechselstrom oder wechselstromüberlagertem
Gleichstrom, dadurch gekennzeichnet, daß die elektrolytische Einfärbung mit einem
kationische organische Farbstoffe enthaltenden wäßrigen Elektrolyten, der gegebenenfalls
noch zusätzlich Leitsalze enthält, durchgeführt wird.
2. Verfahren nach Anspruch 1, dadurch gekennzeichnet, daß die kationischen organischen
Farbstoffe ausgewählt sind aus den Gruppen der Triphenylmethan-, Xanthen-und/oder
Azinfarbstoffe.
3. Verfahren nach Anspruch 2, dadurch gekennzeichnet, daß die kationischen organischen
Farbstoffe in Form ihrer Chloride. Oxalate und/oder Perchlorate eingesetzt werden.
4. Verfahren nach den Ansprüchen 1 bis 3, dadurch gekennzeichnet, daß man bei der
elektrolytischen Einfärbung eine Wechselspannung oder eine wechselspannungsüberlagerte
Gleichspannung im Bereich von 8 bis 30 V anwendet.
5. Verfahren nach Anspruch 4, dadurch gekennzeichnet, daß man eine Spannung im Bereich
von 10 bis 22 V anwendet.
6. Verfahren nach Ansprüchen 1 bis 5, dadurch gekennzeichnet, daß die kationischen
organischen Farbstoffe in dem Elektrolyten in einer Konzentration von 0,01 g/I bis
zur Löslichkeitsobergrenze der Farbstoffe vorliegen.
7. Verfahren nach Anspruch 6, dadurch gekennzeichnet, daß die kationischen organischen
Farbstoffe in dem Elektrolyten in einer Konzentration im Bereich von 0,01 bis 10 g/I,
vorzugsweise von 0,05 bis 5 gil, vorliegen.
8. Verfahren nach Ansprüchen 1 bis 7, dadurch gekennzeichnet, daß der Elektrolyt als
Leitsalz Natriumsulfat und/oder Magnesiumsulfat in Konzentrationen von 1 bis 50 g/l,
vorzugsweise von 5 bis 20 g/l, enthält.
9. Verfahren nach Ansprüchen 1 bis 8, dadurch gekennzeichnet, daß man die anodisierten
Oberflächen von Aluminium oder Aluminiumlegierungen vor der elektrolytischen Einfärbung
unter Verwendung von Wechselstrom oder wechselstromüberlagertem Gleichstrom im gleichen
Elektrolyten einer Behandlung mit Gleichstrom unterwirft.