[0001] This invention relates to porous acrylic and modacrylic fibres, to a method of producing
such fibres and to post-treatment of the fibres in the formation of end-products.
[0002] Porous acrylic fibres are known and are described for example, in UK Patents 1,532,770
and 1,541,152 and in German Offenlegungsschrift 2,706,552. In each of these the porosity
of hydrophilicity of the fibres is achieved by including an additive such as glycerol
in the spinning solution and subsequently removing this additive after the fibres
have been spun. The use of an additive in the spinning solution has the disadvantage
that the properties of the fibre, such as tenacity, breaking load and extensibility,
are permanently altered.
[0003] We have now invented a process for producing acrylic and modacrylic fibres of a high
porosity, which process does not require the presence of such an additive in the spinning
solution.
[0004] Accordingly, the present invention provides a process for the production of porous
acrylic or modacrylic fibre which comprises:-
(i) contacting never-dried, standard wet-spun acrylic or modacrylic fibre with an
organic liquid which is a non-solvent for the fibre, is water-miscible and has a
boiling point at the operating pressure below the glass transition temperature (Tg)
of the fibre, so that substantially all the water contained in the never-dried fibre
is exchanged for the organic liquid; and
(ii) drying the fibre by exposing it to a temperature below the Tg of the fibre for
a period of time which is sufficient to remove substantially all the organic liquid
without causing substantially any collapse of the fibre, thereby to obtain dried,
porous fibre.
[0005] By "standard wet-spun acrylic or modacrylic fibre is meant fibre that has been spun,
using a wet spinning process, from a spinning solution which consists only of components
commonly used for spinning acrylic or modacrylic fibre. The polymer composition from
which the fibre is spun is preferably either a homopolymer or acrylonitrile or a copolymer
containing at least 85% by weight acrylonitrile, although modacrylic fibre can also
be used. Typical copolymers are methyl acrylate, methyl methacrylate and/or vinyl
acetate. Other comonomers, such as those that provide dye sites, may also be included.
Examples of these are itaconic acid (ITA), 2-acrylamidomethylpropianosulphonic acid
(AMPS) and sodium methylsulphonate (SMS). The polymer composition is dissolved in
a suitable spinning solvent such as aqueous sodium thiocyanate, aqueous zinc chloride,
dimethylformamide or dimethyl sulphoxide to form a spinning solution. Commonly used
additives for other purposes may be included in the spinning solution but no additives
which have the purpose of producing a porous fibre will be incorporated in the solution.
Examples of commonly used additives having other purposes are delustring agents such
as titanium dioxide, and optical brighteners such as fluorescent dye.
[0006] One example of a standard acrylic fibre according to the above definition is "Courtelle"
(registered Trade Mark - available from Courtaulds Fibres Ltd).
[0007] The effect of the abovementioned process according to the present invention is to
"freeze" the fibre into the structure that it has in the never-dried state.
[0008] Conventionally, fibre that is wet-spun into a spin bath contains interstices that
are filled with the spin bath liquid. This swollen fibre is washed, usually with water,
and the water replaces the spin bath liquid in the interstices. The fibre at this
stage is in the never-dried or gel state. Usually the fibre is then dried, typically
using air at a temperature of 140 - 160°C, to remove the water. During this drying
step the interstices in the fibre collapse and thus the resulting fibre is non-porous.
[0009] We have found that if, prior to drying, the water in the never-dried fibre is exchanged
for an organic liquid that has a boiling point below the Tg of the fibre, and if the
fibre is dried under drying conditions carefully controlled as to time and temperature,
both according to the abovementioned process of the present invention, then the open
structure of the never-dried fibre is substantially maintained and a dried, porous
fibre is obtained.
[0010] The Tg of acrylonitrile-based polymers is generally about 85 - 90°C, and accordingly
the maximum drying temperature is generally below 83°C. By "drying temperature" is
meant the temperature of the surface of the fibre during drying. As this is difficult
to measure, in practice it is ensured that the drying temperature is below the Tg
of the fibre by keeping the temperature of the drying medium surrounding the fibre,
for example heated air, below 85°C.
[0011] The fibre must be exposed to the drying temperature for a sufficient time to remove
the organic liquid, but this time must not be so long that the heat causes the pores
in the fibre to collapse. The actual drying time depends on the drying temperature,
the higher the temperature the shorter the time required. Preferably the fibre is
dried by a counter-current of heated air. In general, for drying air temperatures
of 60 - 80°C, the drying time is under 5 minutes, usually between 30 seconds and 2
minutes. For lower air temperatures of between ambient and less than about 45°C drying
times of up to 1 hour may be used.
[0012] Suitable organic liquids which may be used in the abovementioned process of the invention
are polar organic solvents, for example alcohols, ethers, aldehydes and acetone, which
have a boiling point at the operating pressure below 83°C. Alcohols, especially isopropyl
alcohol, are preferred.
[0013] The fibre produced by the abovementioned process according to the invention has the
advantage that its structure has not been irreversibly altered and thus the dried
fibre is capable of being collapsed to a non-porous fibre having properties, such
as tenacity, breaking load and extensibility, similar in value to an equivalent non-porous
fibre. By "an equivalent fibre" is meant fibre spun from the same spinning solution
composition as the fibre produced by the abovementioned process according to the invention
and using the same spinning conditions for spinning the non-porous fibre except that
the process is not adapted to obtain a porous fibre. The dried, porous fibre can be
collapsed by heating it above the Tg of the fibre.
[0014] By "porous fibre" is meant a fibre which, when dry, includes pores having a diameter
between 0.009 and 0.85 micrometer (µm).
[0015] By "non-porous fibre" is meant a fibre wherein substantially all the pores are less
than 0.009 µm in diameter.
[0016] The fibre produced by the abovementioned process of the invention has improved properties
over known, commercially available acrylic fibre. These properties may vary depending
upon the decitex of the fibre.
[0017] Thus, in another aspect the present invention provides:
(a) porous acrylic or modacrylic fibre having a decitex of greater than 2.5, a water
imbibition of at least 65%, a porosity of at least 0.3 cm³g⁻¹ and an internal surface
area of at least 50 m²g⁻1, the porosity and internal surface area being determined
from measurements on pores having a pore diameter between 0.009 and 0.85 micrometer;
and also
(b) porous acrylic or modacrylic fibre having a decitex of no more than 2.5, a water
imbibition of at least 55%, a porosity of at least 0.3 cm³g⁻¹ and an internal surface
area of at least 35 m²g⁻¹, the porosity and internal surface area being determined
from measurements on pores having a pore diameter of between 0.009 and 0.85 micrometer.
[0018] In both fibre (a) and fibre (b) the porosity is often at least 0.4 cm³g⁻¹ and can
be greater than 0.5 cm ³g⁻¹. In fibre (a) the internal surface area is often at least
60 m²g⁻¹, and in fibre (b) this area is often at least 45 m²g⁻¹.
[0019] Porosity, internal surface area and mean pore diameter were determined using mercury
porosity measurements on a Micromeritics Pore Sizer 9310 and were calculated from
the differences in cumulative intrusion volume (for porosity) and cumulative surface
area (for internal surface area) between pressures of 20,000 psi and 200 psi. This
pressure range measures pore volumes/surface areas of pores, which are assumed to
be cylindrical in shape, having a diameter of 0.009 to 0.85 µm respectively. Interstices
having a diameter greater than 0.85 µm are not considered to be pores and were not
measured as they cannot be separated from intra- or inter-filament voids. Mean pore
diameters were calculated from the change in volume of mercury intrusion for given
changes in the pressure level.
[0020] Water imbibition was determined by weighing a dry sample of the porous fibre, immersing
the sample in water to saturate the fibre, centrifuging the saturated fibre sample
and then weighing the resulting moist fibre.

where mmf is the mass of the moist fibre and mdf is the mass of the dry fibre.
[0021] In both fibre (a) and fibre (b) the proportion of pores having a diameter of between
0.009 and 0.50 µm expressed as a percentage of all pores in the fibre having a diameter
of between 0.009 and 0.85 µm is usually at least 95%, frequently at least 99%.
[0022] Using the same definition of the proportion, the proportion of pores having a diameter
between 0.009 and 0.35 µm is usually at least 94%, frequently at least 98%, and the
proportion of pores having a diameter between 0.009 and 0.20 µm is usually at least
92%. Thus the large majority of the pores have a pore size within the relatively
narrow band of 009 to 0.20 µm.
[0023] The fibre according to the invention can be impregnated with additives and it has
been found that this pore diameter of 0.009 to 0.20 µm, together with the high porosity
of at least 0.3 cm³g⁻¹, enables the fibre to be impregnated uniformly with a high
proportion of an additive.
[0024] The porous fibre according to the invention can be impregnated with a wide variety
of additives for a corresponding wide variety of end uses, or may be used additive-free,
for example to absorb water or other liquids.
[0025] Preferably, any additive is impregnated into the fibre in an aqueous or organic solution
of the additive, depending upon the relative solubility of the additive. The solvent
in which the additive is dissolved must be a non-solvent for the fibre.
[0026] By employing appropriate impregnating conditions the resulting dried, impregnated
fibre can be porous, partially collapsed or fully collapsed.
[0027] Accordingly, the present invention provides in one further aspect a process for impregnating
porous acrylic or modacrylic fibre with an additive, which process comprises:
(i) immersing the fibre in a solution or liquid dispersion of the additive so that
the fibre is swollen with the solution or liquid dispersion;
(ii) contacting the swollen fibre with an organic liquid that is a non-solvent for
the fibre, is miscible with the said solution or liquid dispersion and has a boiling
point at the operating pressure below the Tg of the fibre, so that substantially all
the solvent or liquid contained in the fibre is exchanged for the said organic liquid;
and
(iii) drying the fibre to remove substantially all the organic liquid.
[0028] In the above impregnation process the fibre is preferably immersed in an aqueous
solution of the additive, the additives being water-soluble. Organic solvents, which
can have a boiling point above, below or the same as the Tg of the fibre, may also
be used provided that they swell the fibre and the additive is soluble in them. Liquid
dispersions containing the additive dispersed in a dispersing medium which swells
the fibre may be used if desired.
[0029] Where the additive is soluble in an organic liquid of the type mentioned below, the
invention also provides a process for impregnating a porous acrylic or modacrylic
fibre with an organic liquid-soluble additive, which process comprises:
(i) immersing the fibre in a solution of the additive in an organic liquid, the liquid
having a boiling point at the operating pressure below the Tg of the fibre and being
a non-solvent for the fibre, so that the fibre is swollen with the solution; and
(ii) drying the fibre to remove substantially all the organic liquid.
[0030] The porous fibre impregnated according to the above process may be any porous fibre
capable of being impregnated with an additive. The term "porous fibre" includes both
substantially dry porous fibre and never-dried fibre containing pores which are filled
with liquid, usually water.
[0031] Where the fibre is a dry porous fibre it is preferably a fibre obtained by the process
for the production of porous acrylic or modacrylic fibre according to the invention.
[0032] Where the additive is impregnated into a never-dried fibre, impregnation can be achieved
by immersing the never-dried fibre in an aqueous solution of the additive, which
can be done either after or during washing of the never-dried fibre and prior to
the exchange with the organic liquid.
[0033] If the additive is soluble in an organic liquid which can be used in the process
for producing the porous fibre, then it can be dissolved in the liquid used for that
purpose and thus incorporated into the fibre when the water in the never-dried fibre
is exchanged for the organic liquid. Preferably, however, the never-dried fibre is
immersed in a subsequent bath, after the water has been changed for the organic liquid,
the subsequent bath containing the additive dissolved in an organic solvent.
[0034] In both types of impregnation process according to the present invention the drying
conditions used depend upon the degree of porosity desired for the resulting dried,
impregnated fibre.
[0035] Where it is desired to obtain a porous impregnated fibre, the drying is carried out
at a temperature less than the Tg of the fibre for a period of time that is sufficient
to remove substantially all the organic liquid without causing substantially any collapse
of the fibre, thereby to obtain a dried, impregnated fibre having a porosity which
is substantially the same as the porosity of the dried porous fibre prior to impregnation.
This method is analogous to the drying of the unimpregnated porous fibre described
above.
[0036] A fully porous impregnated fibre is desirable, for example, to obtain rapid release
of the additive contained in the fibre, such as is required in some medical applications.
The fibre is also useful for applications which require a maximum possible internal
surface area such as in absorption applications. The porous fibre may, for example,
be impregnated with a chemical additive that is capable of absorbing toxic gases or
capable of absorbing impurities in water.
[0037] Where a fully collapsed impregnated fibre is desired, the drying step is carried
out above the Tg of the fibre, usually between 110 and 160°c.
[0038] A fully collapsed fibre has uses where substantially no release of the additive is
required. However, with some additives, some release of the additive occurs over time,
and this has applications where a low-level, slow, sustained release of the additive,
usually for some months, is required. An example of this application is the replenishment
of soil nutrients. In this application the fibre is impregnated with a soil feed and
the fibre buried in the soil where it will release the soil feed at a continuous low
level for up to about six months.
[0039] The drying of the fibre can also be carried out under conditions such that a partially
collapsed fibre is obtained. This is particularly advantageous as the partial collapse
of the pores allows, in use, a certain release rate of the additive, the actual release
rate depending largely upon the degree of collapse of the fibre. This degree of collapse
can be obtained by selecting appropriate temperatures and times when drying the fibre.
Alternatively, the fibre can be dried into its porous state and then a post-drying
step carried out at a higher temperature to partially collapse the fibre.
[0040] Thus, the invention includes partially collapsed acrylic or modacrylic fibre that
has been impregnated with an additive while in a porous state and then the fibre pores
partially collapsed, the additive being releasable from the partially collapsed fibre
at a rate which is at least partly determined by the degree of collapse of the pores,
which rate is initially between the rates of release of equivalent uncollapsed and
fully collapsed fibres. By "equivalent fibre" is meant fibre spun from the same polymer
composition, using the same spinning conditions and incorporating the same additive
as the partially collapsed fibre, the only difference being that the drying step is
altered so as to obtain uncollapsed or fully collapsed fibre accordingly.
[0041] The partially collapsed fibre is obtained by drying the fibre at a temperature at
about or slightly above the Tg, for example between 80 and 110°C, for a period of
time that is sufficient to remove the organic liquid and to cause partial collapse
of the fibre pores without causing complete collapse of the pores. As mentioned above,
the actual temperature and time depend upon the required degree of collapse of the
pores. In general, however, the temperature is approximately 90°C and the drying time
is between 5 minutes and 1 hour, preferably between 10 and 30 minutes.
[0042] Examples of applications where controlled release of an additive is advantageous
are in the medical field, for example in wound dressings, the additive being a bactericide,
a transdermal drug or a soothing cream; and in agriculture, the additive being, for
example, a herbicide or a fungicide. Fibre impregnated with the fungicide may be formed
into a bandage which is wrapped around a tree or plant to prevent fungal growth. Fibre
impregnated with a herbicide may, for example, be formed into a non-woven sheet and
used as a cover to protect crops. In addition to the end uses listed below, other
examples of end uses for an impregnated fibre according to the invention include repellants,
air fresheners, growth accelerators and inhibitors, and filters.
[0043] The partially collapsed fibre, which may be impregnated or unimpregnated, can also
be used in applications which require an absorbent fibre for example absorbent wipes,
the degree of collapse determining the rate of absorption.
[0044] The following non-exhaustive list gives examples of additives with which the fibre
can be impregnated. The impregnated fibre may be fully porous or partially or completely
collapsed.
Bactericides - eg. chlorhexidine and salts thereof,
silver nitrate, polyvinylpyrrolidone-iodine
Herbicides - eg. chloral hydrate
Fungicides - eg. biphenyl and esters of p-hydroxybenzoic acid
Transdermal drugs - eg. Hydrocortisone
Non-adherents (for wound dressings) - eg. gelatins, sodium carboxymethyl cellulose
Soothing creams - eg. lanolin
Water purifiers - eg. silver nitrate, polyvinylpyrrolidone-iodine, polyvinylalcohol-iodine
Soil feeds - eg. metal salt trace elements
Acid gas absorbers - eg. alkali metal carbonates
Ammonia gas absorbers - eg. cobalt salts, zinc nitrate, citric acid
Water absorbers - eg. sodium silicate
Acidity indicators - eg. Methyl Red indicator, Universal indicator, Cresol Purple
indicator
Catalyst supports - eg. manganese dioxide
Corrosion preventers - eg. sodium benzoate, sodium nitrite
Metal oxide precursors - eg. Fehlings solution
Metal precursors - eg. Tollen's reagent
[0045] The amount of additive incorporated in the fibre depends on a variety of factors
including the amount of the particular additive the fibre is capable of containing,
the solubility of the additive in water or an organic solvent, and the desired amount
of additive for a given end-use. The amount of additive can vary but it is generally
present in an amount up to 50% wwf, often 5 to 30% wwf.
[0046] The impregnated or additive-free fibre may be used in loose or ground fibre form,
as a tow of continuous filaments, or may be formed into a fabric, for example a woven,
non-woven, or knitted fabric. The fabric may be used as a sheet, cloth or bandage
for example, or may be formed into shaped articles.
[0047] The invention will now be further described, by way of example only, by the following
Examples and with reference to the accompanying drawings in which:
Figure 1 shows a side view of a manufacturing line for producing dry, porous acrylic
fibre;
Figures 2 to 4 are bar charts plotting percentage incremental pore volume per gram
of fibres against pore diameter (d) in µm x 10⁻³ and showing respectively the degree
of porosity of a porous, partially collapsed and fully collapsed acrylic fibre.
Figure 5 is a graph plotting the hydrocortisone concentration (c) in g/l x 100 in
the wash water against the number of washes (liquor ratio 50:1, 5 minutes) for uncollapsed
(8i), partially collapsed (8ii) and fully collapsed (8iii) acrylic fibres; and
Figures 6 and 7 are graphs plotting the mass of dye in mg desorbed against the number
of washes (n) in high porosity (12i), medium porosity (12ii) and low porosity (12iii)
acrylic fibres, Figure 6 showing the cumulative amount (M) of dye desorbed after n
washes and Figure 7 showing the incremental amount (m) desorbed in the nth wash.
Example 1
[0048] Acrylic filaments having a decitex of 3.3 and a Tg above 80°C and containing 92.8%
acrylonitrile units, 6.0% methyl acrylate units and 1.2% 2-acrylamidomethylpropianosulphonic
acid (AMPS) units were spun from aqueous sodium thiocyanate solution. 0.45% by weight
based on the weight of the polymer composition of a titanium oxide additive was added
to the spinning solution. The filaments were spun into aqueous sodium thiocyanate,
the filaments being swollen by the solution. The swollen filaments were stretched
in steam and then washed with water at about 50°C for about 20 seconds. The resulting
never-dried filaments were formed into a 53.3 kilotex tow and the fibre collected
in a container.
[0049] Porous acrylic fibre was then obtained from this never-dried acrylic fibre using
the following method which is described with reference to Figure 1.
[0050] The never-dried fibre 1, having a water content of 120% wwf, passes through a series
of small guide bars 2 and into a trough 3. The trough consists of two portions 3′
and 3˝, each portion containing a pair of nip rollers 4′ and 4˝ followed by a series
of D-shaped baffles 5′ and 5˝. An organic liquid, isopropyl alcohol (IPA), is fed
into the trough at inlet 15 at a liquor to fibre ratio of 4.8:1. The isopropyl alcohol
flows down the trough 3′ and 3˝ and any waste together with any water removed from
the fibre exits at outlet 16.
[0051] On entering the trough portion 3′, the fibre 1 passes through the pair of nip rollers
4′ to squeeze out some of the water contained in the fibre, and then through the series
of baffles 5′. The fibre 1 is in contact with the isopropyl alcohol in the trough
portion 3′ and as the fibre passes through the series of baffles the water in the
fibre begins to exchange with the isopropyl alcohol. The fibre then enters the second
portion of the trough 3˝, is squeezed through the second pair of nip rollers 4˝ and
passed through the second series of baffles 5˝ in contact with the isopropyl alcohol
so that further exchange of isopropyl alcohol takes place. By the time the fibre leaves
the trough 3˝ substantially all the water in it has been exchanged for isopropyl alcohol.
Before passing into the dryer 6 the fibre goes through a series of rollers consisting
of two pairs of nip rollers 7′ and 7˝, between which is positioned a set of smaller
rollers 8. If a finish is used, this is applied to the fibre as it passes around this
set of rollers 8 and through nip rollers 7˝.
[0052] On entering the dryer 6 the fibre contains on average about 95% wwf isopropyl alcohol.
In the dryer the fibre is exposed to a counter-current of heated air which enters
the dryer at inlet 9 and exits at outlet 10. The air is heated to a temperature of
70°C by an air heater and flows through the dryer at a rate of 0.15 m³ per second,
passing a series of baffles 17 which interrupt the air flow and improve circulation
of the air in the dryer 6. The dryer 6 is 5 m long and the fibre is passed through
at a rate of 5 m per minute. Thus the fibre is exposed to the heated air for 1 minute.
[0053] The dried, porous fibre then passes over a roller 12 where any antistat used is applied
to the fibre, then through a final set of rollers 13, and is collected in a container
14.
[0054] The resulting, dried, porous acrylic fibre had the following properties:
Water imbibition 71.5%
Dye absorbency 58.1%
Internal surface area 71.9 m²g⁻¹
Porosity 0.54 cm³g⁻¹
Mean pore diameter ≦0.17 µm
[0055] The porosity, internal surface area and mean pore diameter were determined on a Micromeritics
Pore Sizer 9310 using pressures of 20,000 psi and 200 psi which measured all pores
having a diameter between 0.009 and 0.85 µm.
[0056] The porosity of the dried, porous fibre is shown graphically in Figure 2 in which
the percentage incremental pore volume per gram of fibre is plotted against pore diameter
(d) in µm x 10⁻³. The maximum incremental volume is 0.3438 cm³/g.
Example 1A
[0057] Acrylic fibre was produced as described in Example 1 except that the air in the dryer
6 was heated to 90°C and the fibre was exposed to the heated air for 5 minutes, in
order to produce a partially collapsed fibre.
[0058] The degree of porosity of the resulting dried partially collapsed fibre is shown
graphically in Figure 3 using the same parameters as in Figure 2. The maximum incremental
volume is 0.3248 cm³/g.
Example 2
[0059] A dried, porous acrylic fibre was produced as in Example 1 except that the following
parameters were used:
Tow speed 5.3 m min⁻¹
Liquor:fibre ratio 4.8:1
Rate of IPA supply 1.3 litres min⁻¹
Drying air temp (on entry into dryer) 67°C
Air flow 0.13 m³sec⁻¹
[0060] The resulting fibre had the following properties:
Water imbibition 48.5%
Dye absorbency 53.3%
Internal surface area 55.9 m²g⁻¹
Porosity 0.34 cm³g⁻¹
Mean pore diameter ≦0.12 µm
Example 3 (comparison)
[0061] A standard, non-porous acrylic fibre was spun using the same spinning solution and
spin bath composition and the same spinning conditions as in Example 1 with the exception
that the water in the gel-state fibre was not exchanged for IPA and the fibre was
dried using an air temperature of 140°C.
[0062] The resulting fibre had the following properties:
Water imbibition 7.0%
Dye absorbency 9.0-%
Internal surface area 4.36 m²g⁻¹
Porosity 0.02 cm³g⁻¹
Mean pore diameter ≦0.08 µm
[0063] When these results are compared with the fibre according to the invention produced
in Example 1, it can be seen that the improvement in water imbibition, surface area
and porosity of the fibre of Example 1 over the standard non-porous fibre is greater
than nine fold.
[0064] The degree of collapse of the resulting fibre is shown graphically in Figure 4 using
the same parameters as in Figures 1 and 2. The maximum incremental volume is 0.1310
cm³/g.
Example 4
[0065] A number of dried, porous acrylic fibres were produced using the process described
in Example 1 except that certain production parameters were varied. These parameters
together with the properties of the resulting fibres are given in Table 1.
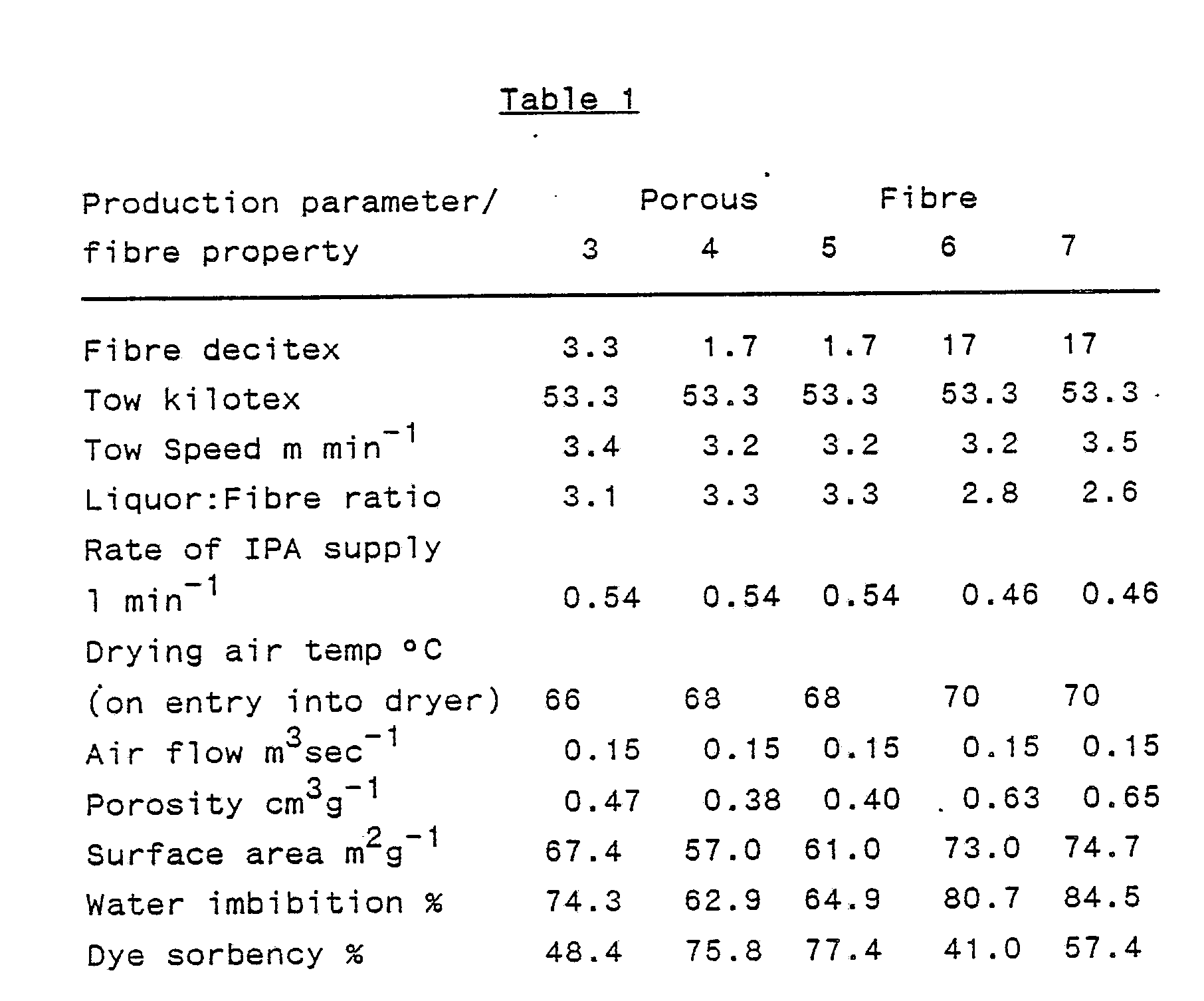
Example 5
[0066] 100 g of 3.3 decitex dry porous acrylic fibre tow produced by the process described
in Example 1 was impregnated with a soil replenishment additive, manganese (II) acetate
tetrahydrate, by immersing the fibre for 10 minutes in a 50% w/w aqueous solution
of the additive. The fibre was then mangled to an expression of about 200% and dried
in an oven at a temperature of 110°C for 30 minutes.
[0067] The resulting impregnated, dried fibre was fully collapsed and contained 31% wwf
of the manganese (II) acetate tetrahydrate additive, the additive level being determined
by the weight difference between the impregnated, dried fibre and the initial dry
porous fibre.
Example 6
[0068] 100 g of 3.3 decitex dry porous acrylic fibre tow as produced in Example 1 was impregnated
with the additive copper (II) chloride by immersing the fibre for 10 minutes in a
5% w/w solution of copper (II) chloride in isopropyl alcohol. Excess solution was
removed by mangling to an expression of about 200% and the remaining isopropyl alcohol
was removed by evaporation under compressed air at ambient temperature for 20 minutes.
[0069] The resulting impregnated, dried fibre was porous and contained 13% w/w of the copper
(II) chloride additive.
Example 7
[0070] 956 g of 3.3 decitex dry porous acrylic fibre tow as produced in example 1 was impregnated
with a bacteriostatic additive PVP-I. PVP-I is a complex of polyvinylpyrrolidone-iodine
containing about 10% by weight of available iodine and is obtainable from Aldrich
Chemical Company Ltd. The porous fibre was impregnated by immersing it in 9.56 litres
of 100 g/l PVP-I aqueous solution for 5 minutes at ambient temperature. The fibre
tow was then run through a mangle into a bath containing 10 litres of isopropyl alcohol.
Three further washes in isopropyl alcohol were carried out with intermediate mangling
to an expression of approximately 120%. A residence time of about 1 minute in each
bath was allowed. In the final wash 0.15% wwf of "Atlas G-1554", a finish available
from ICI Speciality Chemicals, was included. Following the final mangling the remaining
isopropyl alcohol was removed in a dryer using a counterflow of compressed air heated
to a temperature of about 45°C for about 1 hour.
[0071] The resulting impregnated, dried porous fibre contained 0.92% wwf PVP as determined
by aqueous soxhlet extraction and Kjeldahl nitrogen analysis. Assuming the same available
iodine ratio as is present in the free PVP-I complex (9.8% w/w), the iodine content
in the fibre was 0.1 wwf.
Example 8
[0072] This Example demonstrates the ability to control the release of the additive with
which acrylic fibre is impregnated by partially collapsing the porous fibre, the degree
of collapse determining the rate of release.
[0073] A 3.3 decitex dry porous acrylic fibre tow such as produced in Example 1 was impregnated
with the transdermal drug hydrocortisone (available from Sigma Chemicals) by immersing
the fibre in a solution of hydrocortisone in isopropyl alcohol. The fibre was then
mangled to remove excess isopropyl alcohol to an expression of about 200%. Three samples
of the fibre were dried in different ways to obtain an uncollapsed (i.e. fully porous),
partially collapsed and fully collapsed fibre respectively.
(a) Sample 8(i) was dried using compressed air at ambient temperature for 20 minutes
to obtain a dried, uncollapsed, impregnated fibre;
(b) Sample 8(ii) was dried as described in (a) and then further dried using compressed
air heated to 90°C for 20 minutes to obtain a dried, partially collapsed, impregnated
fibre; and
(c) Sample 8(iii) was dried as described in (a) and then further dried using compressed
air heated to 110°C for 1 hour to obtain a dried, fully collapsed impregnated fibre.
[0074] The rate of release of the hydrocortisone additive from each of the three samples
was tested by subjecting the samples to 5 successive aqueous washes, the additive
being released into the water. Each wash used a liquor to fibre ratio of 50:1 and
lasted for 5 minutes.
[0075] The results are given in graphical form in Figure 5, where the hydrocortisone concentration
(c), expressed in g/l x 100 in the wash water is plotted against the number of washes
(n). These results show that for the uncollapsed fibre most of the additive is released
in the first wash, and the amount released rapidly diminishes during successive washes,
with virtually no release from the fourth wash onwards. For the fully collapsed fibre
some additive is released during the first and second washes but this reduces to virtually
zero from the third wash onwards. For the partially collapsed fibre an amount of additive
is released on the first wash, this amount being approximately one-third the concentration
of additive released by the uncollapsed fibre on the first wash, but more than the
amount released by the fully collapsed fibre. The amount released reduces with successive
washes but this reduction is not as rapid as that of the uncollapsed fibre with the
result that from the third wash onwards more hydrocortisone is being released from
the partially collapsed fibre than from either uncollapsed or fully collapsed fibre.
Example 9
[0076] A 13 m length of 1.7 decitex never-dried acrylic fibre tow was produced by the process
for production of the never-dried tow as described in Example 1. The never-dried fibre
was impregnated with a bacteriostatic additive, chlorhexidine acetate, by immersing
the tow in 5 litres of an aqueous solution of 60 g/l chlorhexidine acetate for 5 minutes
at 60°C. The fibre was then run through a mangle into a bath containing 5 litres of
isopropyl alcohol to exchange the water in the fibre for the isopropyl alcohol. Three
further washes in isopropyl alcohol were carried out with intermediate mangling. A
residence time of about 1 minute was allowed in each bath. Following the final mangling
the remaining isopropyl alcohol was removed by evaporation under air flow at ambient
temperature for 2 hours.
[0077] The resulting dried, impregnated fibre was porous and contained at least 0.63% wwf
of the chlorhexidine acetate additive. The additive level was determined by immersing
a 1 g sample of the fibre in 100 ml water for 15 hours with agitation and then analysing
the solution using UV absorbance (chlorhexidine acetate λ max 233 mm, ε44 1g⁻¹cm⁻¹),
from which the concentration of chlorhexidine acetate extracted from the fibre into
the solution was found to be 6.32 x 10⁻² g/l. However the fibre sample still contained
some chlorhexidine acetate after extraction, as indicated by a deep red coloration
obtained on treatment with sodium hypochlorite, which shows that the amount of additive
present in the impregnated fibre is in excess of 0.63% wwf.
Example 10
[0078] Porous acrylic fibre was produced using the method and apparatus as described in
Example 1, except that the following parameters were used:
Tow speed 3.5 m min⁻¹
Liquor:fibre ratio 3.86:1
Rate of IPA supply 0.54 litres min⁻¹
Drying air temp (on entry into dryer) 72°C
Air flow 0.15 m³sec⁻¹
[0079] The fibre was impregnated in its never-dried state by introducing the additive in
the bath 8 in Figure 1 between nip rollers 7′ and 7˝.
[0080] The fibre finish was applied simultaneously. Solutions of both the finish and the
additive were metered directly into the bath to maintain a constant application level.
[0081] An antistatic fibre finish, Leomin AN (available from Hoechst), was applied by means
of the lick roller 12 subsequent to drying.
[0082] The 50 litre application bath was made up with a solution of 25 g/l polyvinylpyrrolidone-iodine
(PVP-I) and 20 g/l of the finish Atlas G-1554 (ICI Speciality Chemicals). Concentrate
solutions of 43.4 g/l PVP-I and 200 g/l finish were used to sustain the application
level during production. All solutions were isopropyl alcohol based. The application
of the fibre finish was targeted to give approximately 1.5% wwf.
[0083] On entering the application bath the fibre contained on average 95% wwf isopropyl
alcohol. On entering the dryer after nip 7˝ the fibre contained on average 95% wwf
of the application bath solution. On the basis of a no-loss system the average pick-up
of PVP-I finish can be estimated. Around 17 kg of fibre was produced at a rate of
3.5 m min⁻¹. PVP-I concentrate was supplied at 68 ml/min⁻¹. Finish concentrate was
supplied at 28 ml/min⁻¹. On the basis of a 40 g/metre tow the average loadings over
the whole run can be estimated to be 2.16% wwf PVP-I and 1.45% wwf finish.
Example 11
[0084] Never-dried acrylic fibre tow was produced according to the process for production
of the never-dried acrylic fibre tow described in Example 1. The fibre was then mangled
and washed with isopropyl alcohol in three consecutive baths with intermediate mangling.
In each bath the liquor to fibre ratio was 10:1 and the residence time about 15 seconds.
After a further mangle the fibre was fed into a bath containing a 5 g/l solution of
a non-substantive dye additive, Nylosan Yellow G-3R - available from Sandoz Limited
(Acid Orange 3), in isopropyl alcohol. The amount of dye additive present in the fibre
was analysed at 30.6 mg. The fibre was then mangled to remove excess isopropyl alcohol.
Three samples of the fibre were dried using compressed air for twenty minutes using
different temperatures in order to obtain an uncollapsed, partially collapsed and
fully collapsed fibre respectively. Sample 12(i) was dried at 80°C, Sample 12(ii)
at 95°C and Sample 12 (iii) at 110°C.
[0085] The rates of release of the dye additive from each of the three fibre samples were
tested by subjecting the samples to 10 successive aqueous washes at 50°C, the dye
being released into the water. Each wash used a liquor to fibre ratio of 50:1 and
lasted for five minutes.
[0086] The results are given in graphical form in Figures 6 and 7 in which the mass of dye
desorbed, measured in mg, is plotted against the number of washes (n). Figure 6 shows
the cumulative release of the dye additive and Figure 7 the incremental release after
each wash. Both graphs clearly show how the degree of collapse of the fibre affects
the rate of release of the additive, the medium porosity, partially collapsed sample
12(ii) having higher cumulative and incremental release after each wash than the low
porosity, fully collapsed sample 12(ii) but lower cumulative and incremental release
than the high porosity, uncollapsed sample 12(i).
1. A process for the production of porous acrylic or modacrylic fibre which comprises:
(i) contacting never-dried, standard wet-spun acrylic fibre with an organic liquid
which is a non-solvent for the fibre, is water-miscible and has a boiling point at
the operating pressure below the glass transition temperature (Tg) of the fibre, so
that substantially all the water contained in the never-dried fibre is exchanged for
the organic liquid; and
(ii) drying the fibre by exposing it to a temperature below the Tg of the fibre for
a period of time that is sufficient to remove substantially all the organic liquid
without causing substantially any collapse of the fibre, thereby to obtain dried,
porous fibre.
2. A process according to claim 1 wherein the organic liquid is an alcohol having
a boiling point at the operating pressure below the Tg of the fibre, or acetone, and
preferably is isopropyl alcohol.
3. Porous acrylic or modacrylic fibre having a decitex of greater than 2.5, a water
imbibition of at least 65%, a porosity of at least 0.3 cm³g⁻¹ and an internal surface
area of at least 50 m²g⁻¹, the porosity and internal surface area being determined
from measurements on pores having a pore diameter of between 0.009 and 0.85 micrometer.
4. Porous acrylic or modacrylic fibre having a decitex of no more than 2.5, a water
imbibition of at least 55%, a porosity of at least 0.3 cm³g⁻¹ and an internal surface
area of at least 35 m²g⁻¹, the porosity and internal surface area being determined
from measurements on pores having a pore diameter of between 0.009 and 0.85 micrometer.
5. A process for impregnating porous acrylic or modacrylic fibre with an additive,
which process comprises:
(i) immersing the fibre in a solution or liquid dispersion of the additive so that
the fibre is swollen with the solution or liquid dispersion;
(ii) contacting the swollen fibre with an organic liquid which is a non-solvent for
the fibre, is miscible with the said solution or liquid dispersion and has a boiling
point at the operating pressure below the glass transition temperature (Tg) of the
fibre, so that substantially all the solvent or liquid contained in the fibre is
exchanged for the said organic liquid; and
(iii) drying the fibre to remove substantially all the organic liquid.
6. A process according to claim 5 wherein in stage (i) the fibre is immersed in an
aqueous solution of the additive.
7. A process for impregnating porous acrylic or modacrylic fibre with an additive
soluble in an organic liquid, which process comprises:
(i) immersing the fibre in a solution of the additive in an organic liquid, the liquid
having a boiling point at the operating pressure below the glass transition temperature
(Tg) of the fibre and being a non-solvent for the fibre, so that the fibre is swollen
with the solution; and
(ii) drying the fibre to remove substantially all the organic liquid.
8. A process according to any of claims 5 to 7 wherein the porous fibre to be impregnated
is a substantially dry porous fibre.
9. A process according to any of claims 5 to 7 wherein the porous fibre to be impregnated
is a never-dried fibre.
10. A process according to any of claims 5 to 9 wherein the fibre is dried by exposing
it to a temperature less than the Tg of the fibre for a period of time sufficient
to remove substantially all the organic liquid without causing substantially any collapse
of the fibre, thereby to obtain a dried, impregnated porous acrylic or modacrylic
fibre.
11. A process according to any of claims 5 to 9 wherein the fibre is dried at a temperature
above the Tg of the fibre thereby to obtain a dried, impregnated, fully collapsed
acrylic or modacrylic fibre.
12. A process according to any of claims 5 to 9 wherein the fibre is dried by exposing
it to a temperature at about or slightly above th Tg of the fibre for a period of
time that is sufficient to remove substantially all the organic liquid and to cause
partial collapse of the fibre pores without causing complete collapse of the pores.
13. Partially collapsed acrylic or modacrylic fibre that has been impregnated with
an additive while in a porous state and the fibre pores partially collapsed, the additive
being releasable from the partially collapsed fibre at a rate which is at least partly
determined by the degree of collapse of the pores, which rate is initially between
the rates of release from equivalent uncollapsed and fully collapsed fibres.