(19) |
 |
|
(11) |
EP 0 212 469 B1 |
(12) |
EUROPÄISCHE PATENTSCHRIFT |
(45) |
Hinweis auf die Patenterteilung: |
|
07.02.1990 Patentblatt 1990/06 |
(22) |
Anmeldetag: 07.08.1986 |
|
|
(54) |
Hitzebeständiges Bauteil und Verfahren zu dessen Herstellung
Refractory component and method for producing the same
Elément de construction réfractaire et procédé pour sa fabrication
|
(84) |
Benannte Vertragsstaaten: |
|
DE FR GB IT SE |
(30) |
Priorität: |
29.08.1985 DE 3530924
|
(43) |
Veröffentlichungstag der Anmeldung: |
|
04.03.1987 Patentblatt 1987/10 |
(73) |
Patentinhaber: ALCAN DEUTSCHLAND GMBH |
|
D-37075 Göttingen (DE) |
|
(72) |
Erfinder: |
|
- Otte, Bernhard, Dr. Dipl.-Phys.
D-8502 Zirndorf (DE)
- Schwarz, Rudolf
D-8500 Nürnberg (DE)
|
(74) |
Vertreter: Hansen, Bernd, Dr. Dipl.-Chem. et al |
|
Hoffmann Eitle,
Patent- und Rechtsanwälte,
Postfach 81 04 20 81904 München 81904 München (DE) |
(56) |
Entgegenhaltungen: :
EP-A- 0 111 961 DE-C- 3 420 571 US-A- 4 404 262
|
DE-A- 3 328 435 US-A- 4 245 611
|
|
|
|
|
- PATENT ABSTRACTS OF JAPAN, Band 9, Nr. 100 (M-376)[1823], 2. Mai 1985; & JP - A -
59 225 871 (ISUZU JIDOSHA) 18.12.1984
|
|
|
|
Anmerkung: Innerhalb von neun Monaten nach der Bekanntmachung des Hinweises auf die
Erteilung des europäischen Patents kann jedermann beim Europäischen Patentamt gegen
das erteilte europäischen Patent Einspruch einlegen. Der Einspruch ist schriftlich
einzureichen und zu begründen. Er gilt erst als eingelegt, wenn die Einspruchsgebühr
entrichtet worden ist. (Art. 99(1) Europäisches Patentübereinkommen). |
[0001] Die Erfindung betrifft ein hitzebeständiges Bauteil, mit den Merkmalen des Oberbegriffs
der unabhängigen Ansprüche 1 und 10 sowie Verfahren zur Herstellung derartiger Bauteile
nach den Merkmalen der Ansprüche 17 und 18.
[0002] Hitzebeständige Bauteile, wie Brennraum-Bauteile, nämlich Kolben- und/oder Zylinderköpfe
sowie Ein- und Auslaßkanäle von Zylinderköpfen, enthalten örtlich Einsatzteile aus
einem fein-porösen, hitzebeständigen Werkstoff, insbesondere einem keramischen Werkstoff
oder einem Cermet, die in den Grundwerkstoff, z. B. Aluminium, der Gußteile zumindestens
teilweise eingegossen oder eingeschrumpft sind (vgl. z. B. DE-C-725 761 und DE-C-2
354 254).
[0003] Bei diesen Bauteilen erweist sich die fein-poröse Struktur des Werkstoffes der Einsatzteile
als nachteilig. Das in den Poren des Werkstoffes der Einsatzteile enthaltene Gasvolumen
dehnt sich nämlich beim Umgießen des Einsatzteiles mit Schmelze aufgrund der dabei
eintretenden Temperaturerhöhung aus und versucht, über die gesamte Oberfläche zu entweichen.
Die Oberflächenspannung der Schmelze, eventuell unterstützt durch die sich bildende
Oxidhaut, verhindert aber das Entweichen einzelner kleiner Bläschen.
[0004] Aufgrund dessen entsteht um das Einsatzteil ein geschlossener Gasschlauch, der sich
allenfalls an hochgelegenen Punkten des Einsatzteils in einzelnen, großen Blasen in
die Schmelze entleert. Bei leicht oxidierbarem Schmelzen kann es dadurch zu Materialtrennungen
in Form von Oxidschlieren kommen. Dadurch wird natürlich die Befestigung der Einsatzteile
im Grundwerkstoff der Gußteile beeinträchtigt. Die zur Rede stehenden Werkstoffe weisen
also zwar eine unvermeidliche Porosität auf, jedoch reicht die Porengröße in der Regel
nicht aus, um dem Gas über weitere Strecken innerhalb des Werkstoffes Wege zu bieten,
so daß es an gewünschten Stellen außerhalb des Metallumschlusses austreten oder im
Verlauf des Gießvorgangs abgesaugt werden könnte.
[0005] Aufgabe der Erfindung ist es, Bauteile der bezeichneten Art zu schaffen, bei denen
ein gasblasenfreier Umschluß des Einsatzteiles durch das Umgußmaterial gegeben ist,
sowie ein Verfahren zur Herstellung solcher Bauteile vorzuschlagen, durch das gewährleistet
wird, daß die beim Umgießen aus dem Einsatzteil austretenden Gase schadlos abgeleitet
werden können.
[0006] Diese Aufgabe wird in bezug auf die Bauteile als solche gemäß einem ersten Weg durch
die Merkmale des Anspruches 1 gelöst.
[0007] Der Erfindung liegt die Erkenntnis zugrunde, daß die Einsatzteile aus den genannten,
porösen, hitzebeständigen Werkstoffen aufgrund der thermischen Belastung während des
Umgießens Gase abgeben. Diese sammeln sich zumindestens teilweise in der Trennfuge
zwischen dem Einsatzteil und dem Gußteil und expandieren dort mit der Folge, daß sich
dadurch Gashohlräume im Umgußmaterial bilden. Diese Feststellung ist deshalb überraschend,
weil keramische Werkstoffe oder Cermet als inerte Materialien angesehen werden, bei
denen an sich ein Gasen auszuschließen ist, zumal die Einsatzteile vorher bereits
einer Wärmebehandlung, nämlich dem Sintern, unterworfen worden sind, so daß anzunehmen
wäre, daß bei diesem Vorgang bereits im wesentlichen die gasförmigen Stoffe ausgetrieben
worden sind.
[0008] Zwar wird in der schon erwähnten DE-C-2 354 254 vorgeschlagen, bei der Herstellung
eines einschlägigen Verbund-Bauteils das Einsatzteil vor dem Gießvorgang zumindestens
auf diejenige Temperatur zu erhitzen, die die Metallschmelze, mit der es umgossen
wird, aufweist. Bei dieser Maßnahme ist aber ersichtlich nicht daran gedacht, daß
damit vor dem Umgießvorgang die Gase aus dem Einsatzteil ausgetrieben werden sollen,
so daß dann beim Umgießen ein Gasen im wesentlichen nicht mehr auftritt. Bei der bekannten
Lösung soll nämlich die Oberfläche des Einsatzteils glatt sein und keine Öffnungen,
Poren oder Löcher aufweisen, in die die Metallschmelze eindringen kann. Die Möglichkeit
der Erhitzung des Einsatzteils scheidet ferner völlig aus, wenn es sich um Keramikeinsätze
mit Hohlräumen handelt, welche für den Umgießvorgang mit Kernsand ausgefüllt werden
müssen, oder wenn Kernsandpaßstücke (sog. Kernmarken) zur Lagefixierung in der Gießform
am Keramikteil befestigt sind (DE-C-2 354 254, Spalte 6, Zeile 6 ff. und DE-B-2 163
717. Spalte 2, Zeile 58 ff.).
[0009] Die ältere EP-A-0 163 241 der Patentinhaberin bezieht sich auf das Problem, bei einschlägigen
Bauteilen die sich bei Temperaturwechselbeanspruchung zwischen Einsatzteil und Umgußmetall
sammelnden Gase abzuführen. Diese Gase können nämlich bei Bauteilen, bei denen das
Einsatzteil im wesentlichen nur durch Schrumpfsitz kraftschlüssig im Gußteil verankert
ist, dazu führen, daß das derart eingegossene Einsatzteil allmählich aus dem es umklammernden
Umgußmaterial herauswändert, wodurch es zu einer Zerstörung des kompletten Bauteils
kommen kann. Die Lösung dieses Problems besteht darin, daß zur Entspannung des sich
zwischen dem Einsatzteil und dem Gußteil aufbauenden Gasdrucks im Gußteil mindestens
eine Gasdruck-Entlastungsbohrung vorgesehen ist, die von der Trennfuge zwischen Einsatzteil
und Gußteil zu einer freien Oberfläche des Gußteils führt. Demgegenüber beschäftigt
sich die erfindungsgemäße Lösung mit der schadlosen Abfuhr der beim Umgießen des Einsatzteils
freigesetzten Gase. Die durch die vorliegende Erfindung vorgeschlagenen Maßnahmen
können natürlich in speziellen Fällen auch dazu dienen, die im Betrieb aufgrund thermischer
Belastung des Bauteils noch freigesetzten Gase problemlos abzuführen.
[0010] Zur konkreten Lösung des Erfindungsvorschlags, nämlich das Einsatzteil derart auszubilden,
daß ein unbehindertes Abströmen der beim Umgießvorgang aus dem Eingießteil austretenden
Gase ermöglicht wird, greift die Erfindung zurück auf Vorschläge der Kerntechnologie
der Gießereitechnik, die ebenfalls darauf gerichtet sind, eine Ableitung der Gasabfuhr
aus den Form- und Kernwerkstoffen zu erreichen. Erst die Erkenntnis, daß die zur Rede
stehenden Einsatzteile trotz der dafür gewählten inerten Werkstoffe gasen, eröffnete
die Möglichkeit, die Kenntnisse aus der Kerntechnologie zur Lösung der angesprochenen
Probleme nutzbar zu machen. So ist z. B. in der DE-B-2 163 717 eine strikte Unterscheidung
getroffen zwischen den zur Rede stehenden Einsatzteilen, dort zwar Hohlkerne genannt,
wie auch in der DE-C-2 354 254, und den eigentlichen Kernen im Sinne eines konventionellen
Gießverfahrens (DE-B-2 163 717, Spalte 2, Zeilen 42 ff.). Eine Erklärung könnte darin
bestehen, daß der Fachmann einen deutlichen Unterschied macht zwischen Kernen, die
zur Erzeugung von Hohlräumen theoretisch nur bis zum Ende der Erstarrung des Gießmetalls
im Gußteil verbleiben müssen, und den hier angesprochenen Eingießteilen, die dazu
bestimmt sind, als dauernder funktionswichtiger Bestandteil des Gußteils für immer
in diesem verankert zu bleiben.
[0011] Um nun erfindungsgemäß das Einsatzteil derart auszubilden, daß ein unbehindertes
Abströmen der beim Umgießvorgang austretenden Gase ermöglicht wird, können sowohl
im Inneren des Einsatzteils als auch an dessen Oberfläche in bezug auf eine Oberfläche
offene Gasableit-Kanäle ausgebildet sein. Die Öffnungen der im Inneren des Einsatzteils
vorgesehenen Gasableit-Kanäle können in den an der Oberfläche vorgesehenen Gasableit-Kanälen
liegen, so daß letztere Sammelkanäle bilden, mittels denen die unter Expansion austretenden
Gase gesammelt und zu einer AbIeitstelle geführt werden können.
[0012] Die im Inneren des Einsatzteils geführten Kanälen können durch Schlitzungen, Perforationen
oder dergleichen ausgebildet sein. Die an der Oberfläche des Einsatzteils geführten
Gasableit-Kanäle können durch eine Oberflächenstruktur erzeugt sein, die offene Strömungswege
für das flächig austretende Gas bilden. Diese offenen Kanäle müssen so dimensioniert
sein, daß die Oberflächenspannung und die Oxidhaut der Schmelze ein Auffüllen der
Oberflächenstruktur verhindern. Über die gasführende Oberflächenstruktur kann das
austretende Gas zu einzelnen Absaugbohrungen gelangen. Die Struktur kann dabei die
Oberfläche des Eingießteils ganz oder nur teilweise abdecken.
[0013] Zwar ist es durch die DE-A-3 126 028 bekannt, in der Wandung eines Keramik-Einsatzteils
Schwalbenschwanznuten auszuführen, in die beim Gießen der Grundwerkstoff des Gußteils
eindringen kann. Jedoch soll bei dieser Lösung ausschließlich die Befestigung der
beiden Komponenten des Bauteils erhöht werden, während es erfindungsgemäß um das Ableiten
der aus dem Eingießteil austretenden Gase bei dem Umgießvorgang geht und folglich
die Kanäle gerade nicht vom flüssigen Metall aufgefüllt werden dürfen.
[0014] Natürlich müssen auch die Öffnungen der im Inneren des Einsatzteils geführten Gasabzugs-Kanäle
bezüglich des Querschnitts so ausgelegt sein, daß einerseits die Schmelze des Grundwerkstoffs
beim Umschmelzvorgang bei angelegtem Unterdruck nicht eindringen kann, andererseits
das Austreten und das Absaugen der Gase nicht behindert wird.
[0015] Es ist aber auch möglich, daß zumindest zwischen der Oberfläche des Einsatzteils,
an der ein Gasableit-Kanal endet bzw. vorgesehen ist, und dem aus dem Grundwerkstoff
bestehenden Gußteil eine gasdurchlässige und/oder-gasleitende Schicht angeordnet ist.
[0016] Diese Schicht trägt einerseits völlig oder teilweise dazu bei, daß die Schmelze beim
Umgießvorgang nicht in die Gasabzugs-Kanäle eintreten und daß andererseits das aus
dem Einsatzteil ausgetriebene Gas gut abgeleitet werden kann.
[0017] Diese Schicht kann durch Auflegen oder Umwickeln einer Folie auf oder um das Eingießteil
erzeugt werden, vorzugsweise einer Folie aus Metall. Sie wird vorzugsweise einen Schmelzpunkt
oberhalb der Gießtemperatur des Umgußmetalls haben. Ihr Aufschmelzen kann aber z.
B. aber auch allein dadurch verhindert werden, daß sie durch Kontakt mit kälteren
Körpern ausreichend intensiv gekühlt wird. Die gasführende Schicht wird gebildet durch
den Zwischenraum zwischen der Oberfläche des Einsatzteils und der Folie.
[0018] Die Schicht kann ferner aus einer Faser- bzw. Filzmatte bestehen, vorzugweise aus
Keramik oder Grafit. Die Matten können einseitig, und zwar bevorzugt zur Seite des
Umgußmetalls hin, gasundurchlässig beschichtet sein.
[0019] Zwar sind bereits einschlägige Bauteile bekannt, bei denen das Einsatzteil in bezug
auf das Gußteil mit einer Umhüllung aus Fasern aus anorganischen, u.U. keramische
Fasern umgeben ist (DE-A-3 309 699, US-A-4 245 611). Diese Faserumhüllungen dienen
allerdings einem anderen Zweck, bilden nämlich eine Art elastischen Puffer, um die
auf das Einsatzteil wirkenden Schrumpfspannungen sowohl beim Gießvorgang als auch
beim Betrieb des Bauteils zu erniedrigen.
[0020] Die zur Gasableitung bestimmte Schicht kann auch durch Aufspritzen oder Aufstreichen
geeigneter Massen erzeugt werden.
[0021] Es ist aber auch möglich, ausschließlich die Kanäle zumindestens in ihren oberflächenseitigen
Abschnitten mit einer gasdurchlässigen Füllung auszufüllen, um einerseits ein Eindringen
des Gußmetalls in die Kanäle zu verhindern und andererseits die Gasabfuhr aus den
Kanälen zu gewährleisten. Für den letztgenannten Zweck ist es empfehlenswert, die
Fasern weitgehend in Gasströmungsrichtung zu orientieren. Auch hier besteht die Füllung
zweckmäßigerweise aus einem Faser- bzw. Filzmaterial, vorzugsweise aus Keramik oder
Grafit.
[0022] Während die vorstehend beschriebenen Lösungsvarianten darauf hinauslaufen, Gasableit-Kanäle
durch entsprechende Formgebung des Einsatzteils zu erzeugen, besteht eine weitere
grundsätzliche Lösungsmöglichkeit der erfindungsgemäßigen Idee darin, partiell oder
insgesamt den Werkstoff des Einsatzteils so einzustellen, daß dieser einen Porendurchmesser
aufweist, der zur Ableitung der expandierenden Gase geeignet ist. Dies ist Gegenstand
des Anspruches 10.
[0023] Ein aus der EP-A-0 111 961 bekanntes hitzebeständiges Bauteil weist zwar ein Einsatzteil
aus einem Keramikwerkstoff auf, das eine offene Porosität besitzt. Diese offene Porosität
des Einsatzteils dient jedoch, daß während des Eingießvorgangs der Grundwerkstoff
in die Porenstruktur des Einsatzteils eindringt, um so die Festigkeit der Verbindung
der beiden Bauteile zu erhöhen. Nach Anspruch 10 sollen aber im Gegensatz dazu gerade
Maßnahmen getroffen werden, die ein Eindringen des flüssigen Grundwerkstoffs in die
offenporige Struktur des Einsatzteils verhindern. Nur dadurch kann nämlich gewährleistet
werden, daß die während des Eingießvorgangs erzeugten Gase tatsächlich aus dem Einsatzteil
abgeführt werden können.
[0024] Für eine partielle Erhöhung der Porosität des Werkstoffes des Einsatzteils bietet
sich in erster Linie an, an den gewünschten Stellen des Einsatzteils einen saugfähigen
Werkstoff als Art Einlage einzubringen. Der Porositätsgrad kann dann z. B. durch die
Wahl der Dichte oder durch die Saugfähigkeit dieses Werkstoffs, z. B. Schwamm, Fasern
usw., variiert werden. Falls es sich um Fasern, Fäden, Borsten oder dergleichen handelt,
kann die Entlüftbarkeit bzw. Absaugbarkeit durch die Ausrichtung dieser Fasern oder
dergleichen beeinflußt werden. Das saugfähige Material kann entweder im gesinterten
Einsatzteil verbleiben, z. B. wenn es sich um Fasern aus Keramik oder Grafit handelt,
oder aber beim Sintern durch Verbrennen, Verflüchtigen oder durch ein chemisches Verfahren
entfernt werden, z. B. beim Einsatz von Schaum, Grafit oder organischen Schwammstoffen.
[0025] Auch bei einer Erhöhung der Porosität des Werkstoffes des Einsatzteils über dessen
gesamtes Volumen kann so vorgegangen werden, wie oben im Zusammenhang mit der partiellen
Erhöhung der Porosität geschildert. In dem zur Rede stehenden Fall ist es aber auch
möglich, dem Werkstoff zur Herstellung der Einsatzteile Treibmittel oder Schaumbildner
als Zusätze hinzuzugeben. Dies bietet sich in erster Linie bei Keramik an, wo diese
Zusätze in den Keramik-schlicker eingebracht werden können.
[0026] Die erfindungsgemäße Lösung betrifft auch Verfahren zur Herstellung von Bauteilen
der beschriebenen Art mit den Merkmalen des Anspruches 17 für ein Bauteil nach Anspruch
1 und des Anspruches 18 für ein Bauteil nach Anspruch 10.
[0027] Die beschriebenen Gasabieit-Kanäie können in dem Einsatzteil in dessen Grünzustand
erzeugt werden. Dies kann z. B. beim Schlickern oder Pressen durch Einbringen von
nicht-saugfähigen Drähten, Stiften, Fäden usw. in die Herstellungsform erreicht werden.
Diese werden dadurch aus dem Grünling entfernt, daß sie fest mit der Form verbunden
sind und dadurch beim Öffnen der Form in dieser verbleiben. Es ist aber auch möglich,
diese Werkzeuge nach dem Entformen aus dem Grünling zu ziehen. Auch an eine chemische
oder thermische Entfernung, z. B. beim Sintern des Grünlings, kann gedacht werden.
[0028] Es ist aber auch grundsätzlich möglich, die Gasabzugs-Kanäle nach dem Sintern des
Einsatzteils durch Materialabtragung herzustellen. Hier ist z. B. an Ätzen, Bohren,
Ultraschall- oder Laserabtrag zu denken.
[0029] Bei der Lösungsvariante, bei der die Porosität des Einsatzteils generell durch entsprechende
Einstellung des Werkstoffs erhöht wird, können dem Werkstoff Zusätze von Treibmitteln
oder Schaumbildnern beigegeben werden.
[0030] Die an der Oberfläche des Einsatzteils vorgesehenen Gasableit-Kanäle können durch
Erzeugung einer Oberflächenstruktur auf dem Einsatzteil hergestellt werden. Dies kann
beim Schlickern oder Pressen durch entsprechend strukturierte Oberflächen der Herstellungsform
erfolgen. Die Oberflächenstruktur kann aber auch durch Materialabtrag erzeugt werden,
und zwar entweder im Grünzustand oder nach dem Sintern, z. B. durch Ätzen, Fräsen,
Sägen, Ultraschall- oder Laserabtrag. Es ist des weiteren denkbar, die Struktur durch
Einlegen von strukturbildenden Netzen, Geweben und ähnlichem in die Herstellungsform
zu erzeugen. Die Entfernung dieser strukturbildenden Elemente kann z. B. chemisch,
thermisch oder mechanisch erfolgen. Schließlich ist es möglich, auf das Einsatzteil
eine strukturierte poröse Oberflächenschicht, z. B. aus Keramik, Metall oder Metallkeramik,
auf das Einsatzteil aufzuspritzen.
[0031] Zur weiteren Unterstützung der Gasabfuhr in einem erfindungsgemäßen Bauteil mit einem
entsprechend ausgestalteten Einsatzteil kann nach einem weiteren Herstellungsverfahren
die Gasabfuhr während des Herstellungsvorgangs durch Fremd-Absaugung gefördert werden.
Dazu bieten sich lösungsmöglichkeiten an, die aus der Kerntechnologie bekannt sind
und an das erfindungsgemäße Verfahren entsprechend adaptiert werden können.
[0032] Ein Beispiel einer in der Kerntechnik bevorzugten Absauglösung, die auch auf das
erfindungsgemäße Verfahren anzuwenden ist, ergibt sich aus der DE-A-2 917 208.
[0033] Ausführungsbeispiele des erfindungsgemäßen Bauteils und Einzelheiten zur Durchführung
des Herstellungsverfahrens eines derartigen Bauteils ergeben sich anhand der Erläuterung
der Zeichnungen. In diesen zeigt in sehr schematischer Darstellung:
Fig. 1 einen Schnitt durch ein erfindungsgemäßes Bauteil,
Fig. 2 einen Schnitt durch ein weiteres Ausführungsbeispiel eines erfindungsgemäß
ausgebildeten Einsatzteils,
Fig. 3 einen Schnitt durch ein Bauteil in der Herstellungsphase, und
Fig. 4 einen Schnitt durch ein weiteres Ausführungsbeispiel des Bauteils.
In den Figuren sind vergleichbare Teile mit denselben Bezugszeichen versehen.
[0034] Gemäß Fig. 1 besteht das Verbund-Bauteil aus einem Gußteil 10, z. B. aus Aluminium.
In das Gußteil 10 ist zumindestens teilweise ein Einsatzteil 20 eingegossen. Dieses
Einsatzteil 20 besteht aus einem fein-porösen, hitzebeständigen Werkstoff, insbesondere
einem keramischen Werkstoff oder einem Cermet. Mit seiner Fläche 22 ist das Einsatzteil
20 der thermischen Belastung beim Umschließen durch das schmelzflüssige Metall ausgesetzt.
Ist das Bauteil 10, 20 z. B. ein Zylinderkopf, bildet die freie Fläche 21 des Einsatzteils
20 z. B. einen Teil der Brenngasauslaßkanäle.
[0035] In dem Einsatzteil 20 sind von der freien Fläche 21 zu der dem Gußteil 10 zugewandten
Fläche 22 verlaufende Schlitze bzw. Perforationen 23 eingebracht, die die schon im
Detail geschilderten Gasable
it-Kanäle bilden. Durch diese Gasableit-Kanäle 23 kann das beim Umgießvorgang expandierende
Gas an die Oberflächen 21, 22 des Eingußteils 20 getrieben und von dort abgeleitet
werden. Diese Ableitung erfolgt z. B. in bezug auf die Oberfläche 21 dadurch, daß
dort ein freies Abströmen ermöglicht oder ein entsprechender Unterdruck aufgebaut
wird. Um auch eine unmittelbare Gasableitung in bezug auf die dem Gußteil 10 zugewandte
Oberfläche 22 des Einsatzteils 20 zu ermöglichen bzw. zu fördern, ist zwischen dieser
Fläche 22 des Einsatzteils 20 und der zugehörigen Gegenfläche 11 des Gußteils 10 eine
Schicht 30, z. B. bestehend aus einer Fasermatte aus Keramik, eingebracht. Diese Schicht
30 ist dadurch im besonderen Maße gasleitend ausgebildet, daß die Fasern der Schicht
in Richtung der gewünschten Gasführung orientiert sind, d.h. im vorliegenden Fall
in etwa parallel zu den Flächen 11 und 22. Dadurch wird das in der Schicht 30 gesammelte
Gas leicht aufgrund des Gasdruckes in Randbereiche der Schicht 30 geleitet, von wo
aus es abgeführt werden kann. Diese Abführung kann z. B. dadurch erfolgen, daß durch
das Gußteil 10 ein Absaugstift 40 (Fig. 3) in den Bereich der Schicht 30 geführt ist,
in der das Gas sich sammeln soll und von wo aus es dann über den Absaugstift 40 abgesaugt
wird.
[0036] Gemäß Fig. 2, die einen Schnitt nur durch das Einsatzteil 20 zeigt, können in dem
Fall, in dem die Querschnitte der Gasabzugs-Kanäle 23 größer sein sollen als in Fig.
1, diese Gasabzugs-Kanäle 23 durch eine Füllung 31, z. B. aus keramischen Fasern,
aufgefüllt sein. Diese Füllung 31 verhindert einerseits ein Eindringen von Gußmetall
in die Gasableit-Kanäle 23 und fördert andererseits die Gasableitung aus den Gasableit-Kanälen
23, insbesondere dann, wenn die Fasern der Füllung 31 in Kanalrichtung orientiert
sind.
[0037] Gemäß Fig. 4 kann die Matte 30 aus insbesondere Keramik-Fasern nach Fig. 1 auch durch
eine Metallfolie 32 ersetzt sein, die ebenfalls das Ableiten des aus den Ableitkanälen
23 in diese Richtung sich bewegenden Gases zwischen sich selbst und der benachbarten
Fläche 22 des Einsatzteils fördert. Auf der von der Folie abgedeckten Fläche 22 des
Einsatzteils 20 sind ferner noch Oberflächen-Kanäle 24 vorgesehen, die zur Folie hin
offen sind und in die die im Inneren des Einsatzteils 20 geführten Gasableit-Kanäle
23 sich öffnen. Die Oberflächen-Kanäle 24 bilden also Sammelleitungen, in die eine
Mehrzahl von Gasableit-Kanälen 23 enden und in denen das aus dem Einsatzteil 20 ausgetriebene
Gas in einen Sammelbereich geführt wird, aus dem es dann z. B. durch Fremd-Absaugung
abgeleitet wird.
1. Hitzebeständiges Bauteil, bestehend aus einem Gußteil (10) und einem von dessen
Grundwerkstoff zumindest teilweise durch Eingießen umschlossenen Einsatzteil (20),
das aus einem fein-porösen, hitzebeständigen Werkstoff, insbesondere einem keramischen
Werkstoff oder einem Cermet, besteht, dadurch gekennzeichnet, daß das Einsatzteil
(20) durch gezielt angeordnete Strömungswege derart körperlich ausgebildet ist, daß
ein unbehindertes Abströmen der beim Eingießvorgang aus dem Einsatzteil freigesetzten
Gase ermöglicht ist, und daß Mittel vorgesehen sind, die ein Eindringen des flüssigen
Grundwerkstoffs in die Strömungswege verhindern.
2. Bauteil nach Anspruch 1 dadurch gekennzeichnet, daß in dem Einsatzteil (20) als
Strömungsweg mindestens ein Gasableit-Kanal (23, 24) ausgebildet ist, der in bezug
auf eine Oberfläche (21, 22) des Einsatzteils (20) offen ist.
3. Bauteil nach Anspruch 2, dadurch gekennzeichnet, daß der Gasableit-Kanal (23) sich
im Inneren des Einsatzteils (20) erstreckt und sich mindestens eines seiner Enden
an einer Oberfläche (21, 22) des Einsatzteils (20) öffnet.
4. Bauteil nach einem der vorhergehenden Ansprüche, dadurch gekennzeichnet, daß das
offene Ende oder die offenen Enden des Gasableit-Kanals (23, 24) in bezug auf den
Querschnitt so bemessen ist bzw. sind, daß ein Eindringen des schmelzflüssigen Grundwerkstoffs
in den Kanal beim Umschließen durch Eingießen weitgehend verhindert ist.
5. Bauteil nach einem der vorhergehenden Ansprüche, dadurch gekennzeichnet, daß an
einer Oberfläche (22) des Einsatzteils (20) mindestens ein offener Oberflächenkanal
(24) ausgebildet ist.
6. Bauteil nach einem der vorhergehenden Ansprüche, dadurch gekennzeichnet, daß mindestens
ein durch das Innere des Einsatzteils (20) verlaufender Gasableit-Kanal (23) mit seinem
Ende sich in einen Oberflächen-Kanal (24) öffnet.
7. Bauteil nach einem der vorhergehenden Ansprüche, dadurch gekennzeichnet, daß die
im Inneren des Einsatzteils (20) geführten Gasableit-Kanäle (23) durch Schlitzungen,
Perforationen oder dergleichen ausgebildet sind.
8. Bauteil nach einem der vorhergehenden Ansprüche, dadurch gekennzeichnet, daß die
Kanäle (23, 24) des Einsatzteils gleichmäßig angeordnet sind.
9. Bauteil nach einem der vorhergehenden Ansprüche 1 bis 7, dadurch gekennzeichnet,
daß die Kanäle des Einsatzteils örtlich konzentriert sind.
10. Hitzebeständiges Bauteil, bestehend aus einem Gußteil (10) und einem von dessen
Grundwerkstoff zumindest teilweise durch Eingießen umschlossenen Einsatzteil (20),
das aus einem sonst üblicherweise fein-porösen, hitzebeständigen Werkstoff, insbesondere
einem keramischen Werkstoff oder einem Cermet, besteht, dadurch gekennzeichnet, daß
der Werkstoff des Einsatzteils (20) aufgrund von Vorkehrungen bei der Herstellung
zumindest bereichsweise eine offenporige Struktur mit einem Poren-Durchmesser aufweist,
der einerseits zur Ableitung der beim Eingießvorgang aus dem Einsatzteil freigesetzten
Gase geeignet ist, und daß andererseits Mittel vorgesehen sind, die ein Eindringen
des flüssigen Grundwerkstoffs in die Struktur verhindern.
11. Bauteil nach einem der vorhergehenden Ansprüche, dadurch gekennzeichnet, daß zumindest
zwischen der Oberfläche (22) des Einsatzteils (20), an der ein Gasableit-Kanal (23,
24) endet bzw. vorgesehen ist, und dem aus dem Grundwerkstoff bestehenden Gußteil
(10) eine gasdurchlässige und/oder gasleitende Schicht (30, 32) angeordnet ist, die
eine Ableitung der Gase nach außen bewirkt.
12. Bauteil nach Anspruch 11, dadurch gekennzeichnet, daß die Schicht (32) als Zwischenraum
zwischen der Oberfläche des Einsatzteiles und einer darüber gelegten Folie - vorzugsweise
einer Metallfolie - ausgebildet ist.
13. Bauteil nach Anspruch 11, dadurch gekennzeichnet, daß die Schicht (30) aus einer
Faser- bzw. Filzmatte besteht, vorzugsweise aus Keramik oder Grafit.
14. Bauteil nach Anspruch 11, dadurch gekennzeichnet, daß die Schicht durch Spritzen
oder Streichen aufgetragen wird.
15. Bauteil nach einem der vorhergehenden Ansprüche, dadurch gekennzeichnet, daß die
Kanäle (23) zumindest in ihren oberflächenseitigen Abschnitten mit einer gasdurchlässigen
Füllung (31) ausgefüllt sind.
16. Bauteil nach Anspruch 15, dadurch gekennzeichnet, daß die Füllung (31) aus einem
Faser- bzw. Filzmaterial besteht, vorzugsweise aus Keramik oder Grafit.
17. Verfahren zur Herstellung eines Bauteils nach Anspruch 1 wobei ein Einsatzteil,
das aus einem fein-porösen, hitzebeständigen Werkstoff besteht, durch Eingießen von
dem Grundwerkstoff eines Gußteils zumindest teilweise umschlossen wird, dadurch gekennzeichnet,
daß vor dem Eingießvorgang in dem Einsatzteil gezielt angeordnete Strömungswege ausgebildet
werden, die ein unbehindertes Abströmen der beim Eingießvorgang aus dem Einsatzteil
freigesetzten Gase ermöglichen, daß ferner Maßnahmen getroffen werden, die ein Eindringen
des flüssigen Grundwerkstoffs in die Strömungswege verhindern, und daß während des
Eingießvorgangs die aus dem Einsatzteil freigesetzten Gase von einer Oberfläche des
Einsatzteils abgeleitet werden.
18. Verfahren zur Herstellung eines Bauteils nach Anspruch 10, wobei ein Einsatzteil
durch Eingießen von dem Grundwerkstoff eines Gußteils zumindest teilweise umschlossen
wird, dadurch gekennzeichnet, daß das Einsatzteil, das aus einem sonst üblicherweise
fein-porösen, hitzebeständigen Werkstoff besteht, mit einer zumindest bereichsweise
offenporigen Struktur erzeugt wird, die einen Poren-Durchmesser aufweist, der einerseits
zur Ableitung der beim Eingießvorgang aus dem Einsatzteil freigesetzten Gase geeignet
ist, daß andererseits Maßnahmen getroffen werden, die ein Eindringen des flüssigen
Grundwerkstoffs in die Struktur verhindern und daß während des Eingießvorgangs die
aus dem Einsatzteil freigesetzten Gase von einer Oberfläche des Einsatzteils abgeleitet
werden.
19. Verfahren nach Anspruch 17, dadurch gekennzeichnet, daß die als Strömungswege
dienenden Gasableit-Kanäle in dem Einsatzteil in dessen Grünzustand erzeugt werden.
20. Verfahren nach Anspruch 19, dadurch gekennzeichnet, daß die Gasableit-Kanäle durch
entsprechende Werkzeuge in der Herstellungsform für das Einsatzteil erzeugt werden.
21. Verfahren nach Anspruch 20, dadurch gekennzeichnet, daß die Werkzeuge thermisch
entfernt werden, z. B. beim Sintern des Einsatzteils.
22. Verfahren nach Anspruch 20, dadurch gekennzeichnet, daß die im Werkstück nach
dem Entformen verbleibenden Werkzeuge auf chemische Weise entfernt werden.
23. Verfahren nach Anspruch 17; dadurch gekennzeichnet, daß die Kanäle nach dem Sintern
des Einsatzteils durch Materialabtragung hergestellt werden.
24. Verfahren nach Anspruch 17, dadurch gekennzeichnet, daß die an der Oberfläche
des Einsatzteils vorgesehenen Gasableit-Kanäle durch Erzeugung einer Oberflächenstruktur
hergestellt werden.
25. Verfahren nach Anspruch 18, dadurch gekennzeichnet, daß die Porosität des Keramik-Einsatzteils
durch Zusätze von Treibmitteln oder Schaumbildnern zum Keramik-Schlicker erhöht wird.
26. Verfahren nach Anspruch 18, dadurch gekennzeichnet, daß die Porosität des Einsatzteils
(20) durch Einbringen eines porenbildenden Werkstoffs erhöht wird.
27. Verfahren nach Anspruch 26, dadurch gekennzeichnet, daß der porenbildende Werkstoff
durch hitzebeständige Fasern, wie Keramik, gebildet wird.
28. Verfahren nach Anspruch 26, dadurch gekennzeichnet, daß der porenbildende Werkstoff,
z. B. Schaumgrafit, durch Verbrennen, Verflüchtigen und/oder chemische Lösungsmittel
entfernt wird.
29. Verfahren nach Anspruch 17 bzw. 18, dadurch gekennzeichnet, daß die Gasabfuhr
während des Herstellungsvorgangs durch Absaugung unterstützt bzw. gefördert wird.
1. Composant réfractaire, constitué d'une partie moulée (10) et d'une partie formant
garniture (20) qui est au moins partiellement entourée par ce matériau de base lors
de la coulée et qui est constituée d'un matériau finement poreux, réfractaire, en
particulier d'un matériau céramique ou d'un composite métalcéramique "Cermet", caractérisé
en ce que la partie formant garniture (20) est, au moyen de chemins d'écoulement volontairement
disposés, conçue dans la masse de façon que soit possible une évacuation sans obstacle
des gaz libérés hors de la partie formant garniture lors du processus de coulée; et
en ce que sont prévus des moyens qui interdisent une pénétration du matériau de base
en fusion dans les chemins d'écoulement.
2. Composant selon la revendication 1, caractérisé en ce que dans la partie formant
garniture (20) est prévu comme chemin d'écoulement au moins un canal (23, 24) d'évacuation
des gaz qui est ouvert vis-à-vis d'une surface (21, 22) de la partie formant garniture
(20).
3. Composant selon la revendication 2, caractérisé en ce que le canal (23) d'évacuation
des gaz s'étend dans l'intérieur de la partie formant garniture (20) et qu'au moins
l'une de ses extrémités s'ouvre sur une surface (21, 22) de la partie formant garniture
(20).
4. Composant selon l'une des revendications précédentes, caractérisé en ce que l'extrémité
ouverte, ou les extrémités ouvertes, du canal (23, 24) d'évacuation des gaz présente
ou présentent une section de dimension telle qu'est largement interdite. une pénétration
du matériau de base en fusion dans le canal lorsque cette garniture est entourée par
la coulée.
5. Composant selon l'une des revendications précédentes, caractérisé en ce qu'au moins
un canal de surface ouvert (24) est prévu sur une surface (22) de la partie formant
garniture (20).
6. Composant selon l'une des revendications précédentes, caractérisé en ce qu'au moins
un canal (23) d'évacuation des gaz qui traverse l'intérieur de la partie formant garniture
(20) a son extrémité qui s'ouvre dans un canal de surface (24).
7. Composant selon l'une des revendications précédentes, caractérisé en ce que les
canaux (23) d'évacuation des gaz qui passent dans l'intérieur de la partie formant
garniture (20) sont formés par des fentes, des perforations et analogues.
8. Composant selon l'une des revendications précédentes, caractérisé en ce que les
canaux (23, 24) de la partie formant gamiture sont régulièrement disposés.
9. Composant selon l'une des revendications 1 à 7, caractérisé en ce que les canaux
de la partie formant garniture sont concentrés localement.
10. Composant réfractaire, constitué d'une partie moulée (10) et d'une partie formant
garniture (20) qui est au moins partiellement entourée par ce matériau de base lors
de la coulée et qui est constituée d'un matériau finement poreux habituel, réfractaire,
en particulier d'un matériau céramique ou d'un composite métal-céramique "Cermet",
caractérisé en ce que le matériau de la partie formant garniture (20), par suite de
dispositions prises lors de la fabrication, présente, au moins par zones, une structure
à pores ouverts avec un diamètre de pores qui d'une part convient pour l'évacuation
des gaz libérés hors de la partie formant garniture lors du processus de coulée; et
en ce que d'autre part sont prévus des moyens qui interdisent une pénétration du matériau
de base en fusion dans les chemins d'écoulement.
11. Composant selon l'une des revendications précédentes, caractérisé en ce qu'au
moins entre la surface (22) de la partie formant garniture (20) sur lequel un canal
(23, 24) d'évacuation des gaz se termine ou est prévu, et la partie moulée (10) constituée
du matériau de base, est disposée une couche (30, 32) perméable aux gaz et/ou conductrice
des gaz, qui opère une évacuation des gaz vers l'extérieur.
12. Composant selon la revendication 11, caractérisé en ce que la couche (32) est
conçue comme espace intermédiaire entre la surface de la partie formant garniture
et une feuille - de préférence une feuille métallique - placée pardessus.
13. Composant selon la revendication 11, caractérisé en ce que la couche (30) est
constituée d'un tapis de fibres ou de feutre, de préférence de céramique ou de graphite.
14. Composant selon la revendication 11, caractérisé en ce que l'on rapporte la couche
en la projetant ou en l'étendant.
15. Composant selon l'une des revendications précédentes, caractérisé en ce que les
canaux (23) sont remplis, au moins dans leurs tronçons côté surface, d'un remplissage
(31) perméable aux gaz.
16. Composant selon la revendication 15, caractérisé en ce que le remplissage (31)
est constitué d'un matériau du type fibres ou feutre, de préférence en céramique ou
en graphite.
17. Procédé de fabrication d'un composant selon la revendication 1, dans lequel on
entoure, au moins partiellement, une partie formant garniture, constituée d'un matériau
finement poreux, réfractaire, en coulant le matériau de base d'une pièce moulée, caractérisé
en ce qu'avant le processus de coulée, on forme des chemins d'écoulement qui sont
volontairement disposés dans la partie formant garniture et qui permettent une évacuation
sans obstacle des gaz libérés hors de la partie formant garniture lors du processus
de coulée; en ce qu'en outre sont prises des dispositions qui interdisent une pénétration
du matériau de base en fusion dans les chemins d'écoulement; et en ce que pendant
le processus de coulée, on évacue, par une surface de la partie formant garniture,
les gaz libérés de cette partie formant garniture.
18. Procédé de fabrication d'un composant selon la revendication 10, dans lequel on
entoure, au moins partiellement, une partie formant garniture en coulant le matériau
de base, caractérisé en ce que l'on produit la partie formant garniture, constituée
d'un matériau finement poreux, réfractaire, par ailleurs habituel, avec une structure
à pores ouverts ou moins par zones, qui présente un diamètre de pores qui d'une part
convient pour l'évacuation des gaz libérés hors de la partie formant garniture lors
du processus de coulée; et en ce que d'autre part sont prises des dispositions qui
interdisent une pénétration du matériau de base en fusion dans la structure; et en
ce que pendant le processus de coulée on évacue par une surface de la partie formant
garniture les gaz libérés hors de cette partie formant garniture.
19. Procédé selon la revendication 17, caractérisé en ce que l'on crée dans la partie
formant garniture, à l'état vert, les canaux d'évacuation des gaz servant de chemins
d'écoulement.
20. Procédé selon la revendication 19, caractérisé en ce que l'on crée les canaux
d'évacuation des gaz au moyen d'outils appropriés dans le moule de fabrication de
la partie formant garniture.
21. Procédé selon la revendication 20, caractérisé en ce que l'on élimine les outils
thermiquement, par exemple lors du frittage de la partie formant garniture.
22. Procédé selon la revendication 20, caractérisé en ce que l'on élimine par voie
chimique les outils restant dans la pièce après son démoulage.
23. Procédé selon la revendication 17, caractérisé en ce que l'on réalise des canaux
après le frittage de la partie formant garniture, par enlèvement de matière.
24. Procédé selon la revendication 17, caractérisé en ce que l'on réalise les canaux
d'évacuation des gaz prévus à la surface de la partie formant garniture par création
d'une structure de surface.
25. Procédé selon la revendication 18, caractérisé en ce que l'on augmente la porosité
de la partie formant garniture céramique en ajoutant à la barbotine de céramique des
agents moteurs ou des agents moussants.
26. Procédé selon la revendication 18, caractérisé en ce que l'on augmente la porosité
de la partie formant garniture (20) par apport d'un matériau formant des pores.
27. Procédé selon la revendication 26, caractérisé en ce que le matériau formant des
pores est formé de fibres réfractaires, comme des fibres céramiques.
28. Procédé selon la revendication 26, caractérisé en ce que l'on élimine le matériau
formant des pores, par exemple du graphite mousse, par combustion, volatilisation
et/ou au moyen d'un solvant chimique.
29. Procédé selon la revendication 17 ou 18, caractérisé en ce que l'on aide ou l'on
favorise l'évacuation des gaz par aspiration pendant le processus .de fabrication.
1. A refractory component comprising a casting (10) end an insert part (20) which
is at least partially surrounded by the base material of the casting by casting-in
and which comprises a fine- pore, refractory material, particularly a ceramic meterial
or a cermet, characterised in that the insert part (20) is formed physically by intentionally
arranged flow paths, in such a way that unhindered flowing-off of the gases released
from the insert part during the casting-in process is rendered possible, and that
means are provided which prevent the molten base -material from entering the flow
paths.
2. A component as claimed in claim 1, characterised in that at least one gas outlet
passage (23, 24) is formed as flow path in the insert part (20) and is open with respect
to a surface (21, 22) of the insert part (20).
3. A component as claimed in daim 2, characterised in that the gas outlet passage
(23) extends in the interior of the insert part (20) and at least one of its ends
opens at a surface (21, 22) of the insert part (20).
4. A component as claimed in one of the preceding claims, characterised in that the
open end or the open ends of the gas outlet passage (23, 24) is or are dimensioned
with respect to the cross section in such a way that the molten base material is largely
prevented from entering the passage during surrounding by casting-in.
5. A component as claimed in one of the preceding claims, characterised in that at
least one open surface passage (24) is formed in one surface (22) of the insert part
(20).
5. A component as claimed in one of the preceding claims, characterised in that the
end of at least one gas outlet passage (23) extending through the interior of the
insert part (20) opens into a surface passage (24).
7. A component as claimed in one of the preceding claims, characterised in that the
gas outlet passages (23) extending in the interior of the insert part (20) are formed
by slots, perforations or the like.
8. A component as claimed in one of the preceding claims, characterised in that the
passages (23, 24) of the insert part are disposed uniformly.
9. A component as claimed in one of the preceding claims 1 to 7; characterised in
that passages of the insert part are concentrated locally.
10. A refractory component comprising a casting (10) and an insert part (20) which
is at least partially surrounded by the base material of the casting by casting-in
and which comprises an otherwise conventional fine-pore, refractory material, particularly
a ceramic material or a cermet, characterised in that, by virtue of precautions taken
during manufacture, the material of the insert part (20) has, at least in regions
thereof, an open-pore structure having a pore diameter which, on the one hand, is
suitable for discharging the gases released from the insert part during the casting-in
process, and that, on the other hand, means are provided which prevent the molten
base material from entering the structure.
11. A component as claimed in one of the preceding claims, characterised in that a
gas-permeable and/or gas-conducting layer (30, 32) is disposed at least between that
surface (22) of the insert part (20) in which a gas outlet passage (23, 24) terminates
or is provided, and the casting (10) made from the base material, and effects discharge
of the gases outwardly.
12. A component as claimed in claim 11, characterised in that the layer (32) is formed
as a space between the surface of the insert part and a foil, preferably a metal foil,
placed thereabove.
13. A component as claimed in claim 11', characterised in that the leyer (30) comprises
a fibre or felt mat, preferably ceramic or graphite.
14. A component as claimed in claim 11, characterised that the layer is applied by
spraying or brushing.
15. A component as claimed in one of the preceding claims, characterised in that the
passages (23) are filled with a gas-permeable filling (31) at least at their ends
at the surface.
16. A component as claimed in claim 15, characterised in that the filling (31) comprises
a fibrous or felt material, preferably ceramic or graphite.
17. A method of producing a component as claimed in claim 1, wherein an insert part
made from a finepore, refractory material is at least partially surrounded by the
base material of a casting by casting-in, characterised in that intentionally disposed
flow paths are formed in the insert part before the casting-in process and facilitate
unhindered flowing-off of the gases released from the insert part during the casting-in
process, that measures are taken which prevent the molten base material from entering
the flow paths, and that the gases released from the insert part are discharged from
a surface of the insert part during the casting-in process.
18. A method of manufacturing a component as claimed in claim 10, wherein an insert
part is at least partially surrounded by the base material of a casting by casting-in,
characterised in that the insert part, which is made from an otherwise conventional,
fine-pore, refractory material, is produced, at least in regions thereof, with an
open-pore structure having a pore diameter which, on the one hand, is suitable for
discharging the gases released from the insert part during the casting-in process,
that, on the other hand, measures are taken which prevent the molten base material
from entering the structure, and that the gases released from the insert part are
discharged from a surface of the insert part during the casting-in process.
19. A method as claimed in claim 17, characterised in that the gas outlet passages
serving a flow paths are produced in the insert part when the latter is in its green
state.
20. A method as claimed in claim 19, characterised in that the gas outlet passages
are produced by corresponding tools in the mould for manufacturing the insert part.
21. A method as claimed in claim 20, characterised in that the tools are removed thermally,
for example during sintering of the insert part.
22. A method as claimed in claim 20, characterised in that the tools remaining in
the workpiece after the mould has been opened are removed chemically.
23. A method as claimed in claim 17, characterised in that the passages are produced
by removal of material after the insert part has been sintered.
24. A method as claimed in claim 17, characterised in that the gas outlet passages
provided in the surface of the insert part are produced by creating a surface structure.
25. A method as claimed in claim 18, characterised in that the porosity of the ceramic
insert part is increased by additives of propellants or frothing agents to the ceramic
slip.
26. A method as claimed in claim 18, characterised in that the porosity of the insert
part (29) is Increased by introducing a pore-forming material.
27. A method as claimed in claim 26, characterised in that the pore-forming material
is formed by refractory fibres such as ceramic.
28. A method as claimed in claim 26, characterised in that the pore-forming material,
such as foam graphite, is removed by burning, volatilization and/or chemical solvents.
29. A method as claimed in claim 17 or 18, characterised in that the the discharge
of gas is assisted or promoted by suction during the manufacturing process.
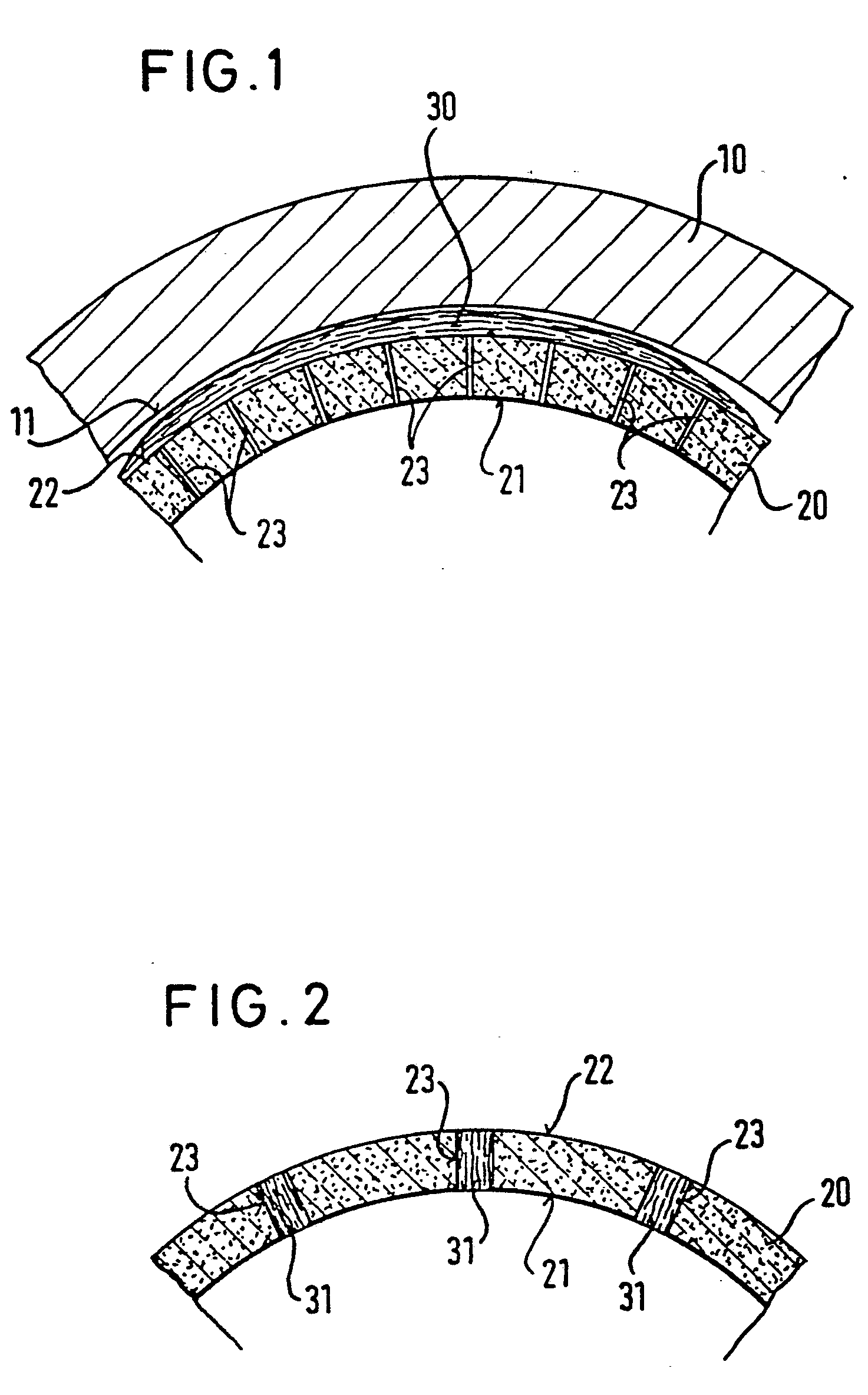
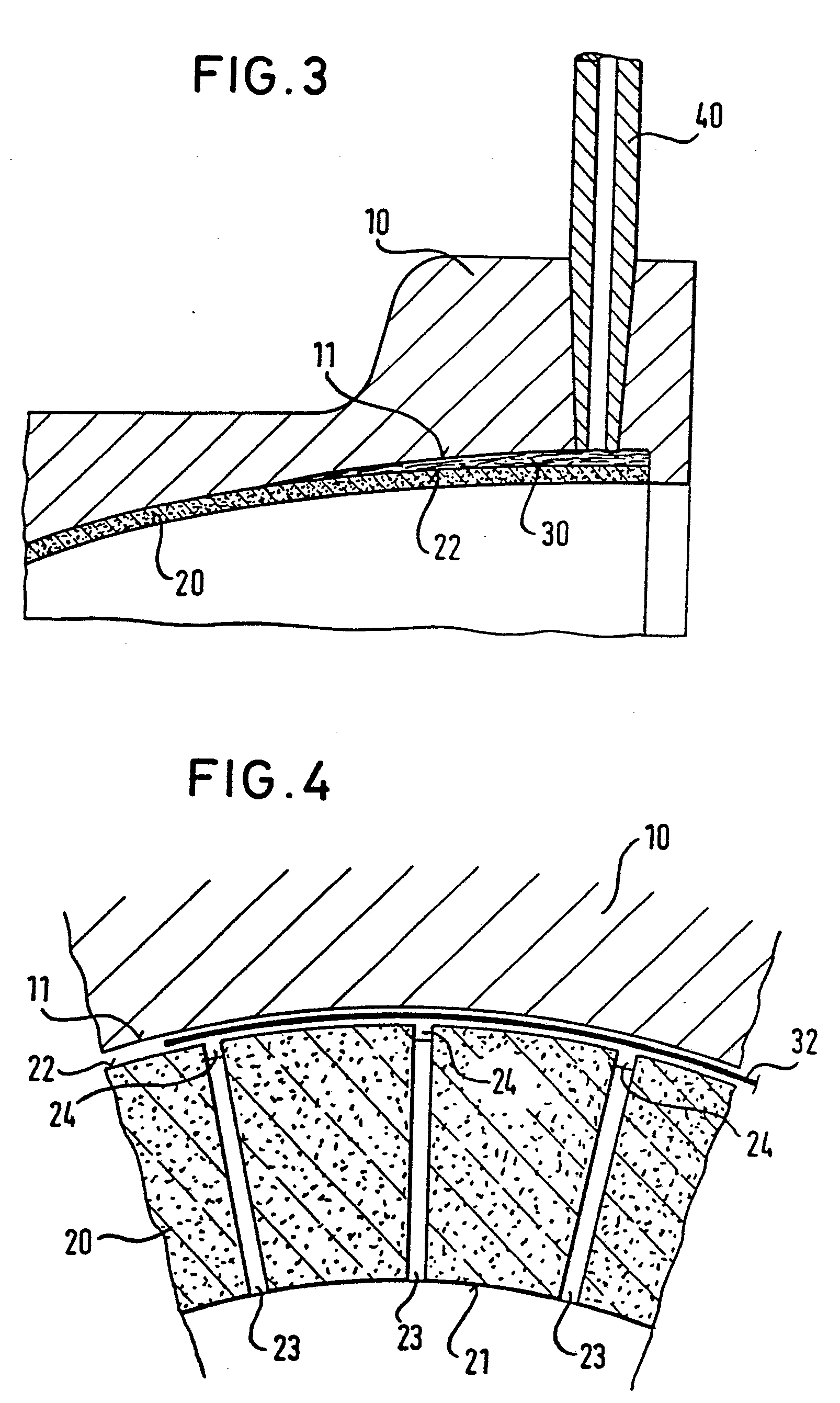