Technisches Gebiet
[0001] Die Erfindung bezieht sich auf ein Verfahren zum Einstellen der Mahlwalzenabstände
von Walzenstühlen mit jeweils nachgeschaltetem Siebsystem in einer Getreidemühlenanlage,
bei welchem in ausgewählten Schlüsselpassagen jeweils ein einen Istwert repräsentierendes
Meßsignal abgegriffen, einem Computer zugeführt, dort mit einem gespeicherten Sollwert
verglichen und bei Abweichung des Istwertes vom Sollwert ein Steuersignal erzeugt
wird.
[0002] Die Erfindung bezieht sich auch auf eine Getreidemühlenanlage mit einer Folge von
Walzenstühlen und nachgeschalteten Plansichtern, mit steuerbaren Antriebsmitteln zum
Einstellen der Walzenabstände, mit Meßeinrichtungen zur Istwertmessung von Betriebsparametern
und mit einem zentralen Computer mit Datenspeicher zur Überwachung der Istwerte ausgewählter
Schlüsselpassagen, zu deren Vergleich mit korrespondierenden, im Datenspeicher abgelegten
Sollwerten und zur Erzeugung von Steuersignalen bei Abweichungen zwischen Ist- und
Sollwerten.
Zugrundeliegender Stand der Technik
[0003] Für die Steuerung bzw. Regelung der Mahlwalzenabstände in einer Getreidemühlenanlage
liegen bis heute im wesentlichen vier Lösungsvorschläge vor. Der erste und älteste
Lösungsvorschlag besteht in der Regelung und Steuerung der Mahlwalzen durch die Bedienungsperson
(Obermüller) selbst. Um eine solche Steuerung "von Hand" überhaupt durchführen zu
können, ist jedoch eine vollständige Beherrschung des gesamten Produktionsablaufes
unbedingt erforderlich. Das Ergebnis der Steuerung ist dabei wesentlich abhängig von
dem jeweiligen fachlichen Können und der Erfahrung der Bedienungsperson, bei der es
sich in der Regel um den betreuenden Obermüller handelt. Muß weniger qualifiziertes
Personal für die Bedienung eingesetzt werden, z. B. während spezieller Zeiten (Ferien,
Nachtarbeit usw.), so kann sich unter Umständen eine Ergebnisschmälerung für die Mühle
einstellen, etwa durch eine geringere Ausbeute an heilen Mehlen o.ä.
[0004] Ein zweiter Vorschlag für die Steuerung ist in der Zeitschrift "Die Mühle und Mischfuttertechnik"
vom 3. September 1965 beschrieben. Wesentlich an diesem bekannten Vorschlag ist der
Einsatz einer Probesiebung. In der Produktion wird dabei nicht eine absolute Klassierung
in die einzelnen Kornfraktionen angestrebt, da dies eine zu lange Siebdauer benötigen
und auch Änderungen der Produktqualität ergeben würde. Wird z. B. Mahlgut zulange
einem Siebvorgang unterworfen, enthält der Siebdurchfall auch feine Schalenteile,
die normalerweise im Plansichterbetrieb oben auf dem Gut aufschwimmen und in den Abstoß
gelangen würden. Bei der theoretischen Behandlung der Vermahlung können solche Feinheiten
nicht berücksichtigt werden, da sie nicht zuletzt auch abhängig sind von der Art und
Weise des Betriebes der vorangehenden und nachfolgenden Verarbeitungsmaschinen, somit
nicht allein von der Vermahlung als solcher. Im Sinne einer vollständigen absoluten
Regelung der Mahlarbeit ist es somit folgerichtig, das Mahlgut einer gesonderten,
exakten Laborsiebung zu unterwerfen und bei Abweichungen entsprechende Korrekturen
vorzunehmen. Obwohl die vorgeschlagene Probesiebung sehr viel exakter ist, läßt sich
hierdurch jedoch immer noch kein repräsentatives Bild in der Praxis ableiten, da die
Arbeit des Plansichters, wie schon erwähnt, eine Kombination von Siebung und Sichtung
darstellt und etwa eine bestimmte Produktschicht über dem Siebgeflecht benötigt.
[0005] Eine andere Steuerungsmöglichkeit ist in der EP-A1-13 023 beschrieben. Dieser Vorschlag
geht davon aus, daß jede auf die Zukunft gerichtete Entwicklung im Bereich der Nahrungsmittelverarbeitung
nicht mehr grundsätzlich auf die Verdrängung des Menschen ausgerichtet sein darf.
Viele Vorgänge lassen sich vielmehr schneller und auch preisgünstiger durch den Menschen
direkt durchführen. Denn die immer stärker wachsende Erkenntnis von der fast vollständigen
Verflechtung aller Vorgänge ruft wieder vermehrt zur menschlichen Überwachung und
Führung bei Getreideverarbeitungsbetrieben. Es hat sich letztlich doch gezeigt, daß
es sich nicht lohnt, alle Vorgänge, die der Mensch mit seinen Sinnen überwachen, prüfen
und von Hand steuern kann, durch Apparate ausführen zu lassen.
[0006] Ein anderer bekannter theoretischer Vorschlag zur Steuerung einer Mühle (DE-C-2 413
956) stellt gerade darauf ab, die Bedienungsperson, insbesondere den Obermüller, durch
Computer und Regeleinrichtungen zu ersetzen. Dies läuft darauf hinaus, das Wissen
und die Erfahrung etwa des Obermüllers in Rechnerprogramme einzubringen und über selbständige
Regeleinrichtungen jeden Routineeingriff des Menschen überflüssig zu machen. Der bekannte
Vorschlag sieht vor, daß alle Mahlwalzen nach einem zuvor erarbeiteten Schema auf
ein bestimmtes Mahlergebnis eingeregelt werden, nämlich auf das Verhältnis von Siebdurchfall
zu Siebabstoß. Eine entsprechende Realisierung dieses Vorschlags in der Praxis ist
jedoch bislang nicht bekannt geworden.
Offenbarung der Erfindung
[0007] Ausgehend von dem letztgenannten Stand der Technik liegt der Erfindung nun die Aufgabe
zugrunde, ein Steuerungsverfahren der eingangs genannten Art so zu verbessern, daß
bei stark abgesenktem Aufwand ein nahezu vollautomatischer Betrieb bei voller Funktionstüchtigkeit
und ohne Gefahr einer Aufschaukelung ermöglicht wird, sowie eine Mühlenanlage zur
Durchführung eines solchen Verfahrens vorzuschlagen.
[0008] Erfindungsgemäß wird dies bei einem Verfahren der eingangs genannten Art dadurch
erreicht, daß als Ist- und Sollwerte der Abstoß oder der Durchfall der Siebsysteme
gewählt und das Steuersignal zur Vorgabe neuer Einstellwerte der Walzenabstände verwendet
wird.
[0009] Bei einer Getreidemühlenanlage der eingangs genannten-Art wird die Aufgabe dadurch
gelöst, daß die Meßeinrichtung ein den Piansichtern nachgeschaltetes Durchlauf-Gewichtsmeßsystem
zur kontinuierlichen Erfassung des Siebabstosses oder des Siebdurchfalles ist, und
der Steuerausgang des Computers mit einem Sollwertspeicher zur Vorgabe neuer Einstellwerte
an die Antriebsmittel verbunden ist
[0010] Die erfindungsgemäßen Maßnahmen erhöhen den Bedienungskomfort, wobei gleichzeitig
die eigentliche Führung der Gesamtsteuerung dem Obermüller belassen bleibt. Hierdurch
kann zunächst vermieden werden, daß der gesamte Mühlenlauf "ins Schwingen" kommt,
d.h. daß Aufschaukelvorgänge auftreten, was bei vielen Eingriffen eine relativ große
Gefahr darstellt. Die wirklich notwendigen Eingriffe können auf ein Minimum abgesenkt
und von einer erfahrenen Bedienungsperson ausgeführt werden. Eine oder mehrere Korrekturen
für die Steuervorgabe können gemäß der Erfindung nur im Rahmen einer Gesamtübersicht
durchgeführt werden, da zentral alle Ist-Werte, auch die der Schlüsselpassagen, jederzeit
dargestellt und ein Eingriff ganz gezielt ausgeführt werden kann, ohne daß irgend
ein vorgegebenes festes Korrekturprogramm ablaufen müßte. Tritt einmal tatsächlich
ein Fehler auf, so kann dabei der größte Fehler zuerst und anschließend die Folgefehler
unschwer beseitigt werden. In der Müllerei gibt es einen Erkenntnisstand, der besagt,
daß die Vermahlung als solche nicht durch komplizierte Regeleinrichtungen geführt
werden sollte. Bis heute ist es für das müllerische Mahlen auch noch nicht gelungen,
alle wirksamen Parameter in theoretisch bzw. mathematisch erfaßbare Formen zu bringen.
Dem Praktiker ist bekannt, daß dasselbe Ziel durchaus auf unterschiedliche Art und
Weise oftmals erreichbar ist. Es kommt dabei vielfach auf die besondere Erfahrung
des Obermüllers an und auf seine Kenntnisse anlagenspezifischer Daten. Darüberhinaus
ist die Vermahlung aber auch das Ergebnis des Einsatzes entsprechender Maschinengruppen.
Die Mahlarbeit wird zu einem nicht unwesentlichen Anteil vom Konstrukteur der Maschinen,
der Art des Betriebes und des Unterhaltes der Maschinen wie auch durch die spezifisch
eingesetzten Maschinen selbst, das Behandlungsdiagramm und die Anlagebesonderheiten
vorbestimmt, weshalb Einflußnahmen auf die Mahlarbeit in qualitativem Sinne durch
den Obermüller Grenzen gesetzt sind.
[0011] Ein weiterer Komplex, der bislang nur relativ wenig beachtet wurde, liegt in der
Frage der quantitativen Mahlarbeit. Es hat sich nämlich gezeigt, daß gerade die quantitative
Mahlarbeit ein ganz wichtiger Faktor insbesondere im Hinblick auf Automatisierungsbemühungen
ist. Für die qualitative Beurteilung ist der Mensch mit seinen Sinnen und der Möglichkeit,
intuitiv zu kombinieren, noch für lange Zeit gerade bei den Mühlenzwischenprodukten
Automatisierungstendenzen durch Maschineneinsatz überlegen. Dies gilt jedoch nicht
für den Fall der quantitativen Beurteilung. Die Bedienungsperson, etwa der Obermüller,
kann nicht gleichzeitig überall in der Mühle anwesend sein. Der Produktfluß dort wird
teilweise durch starre Vorgaben festgelegt, zu einem überwiegenden Teil finden die
einzelnen Produkte ihren Weg im Produktfluß selbst, während an einigen wichtigen Kreuzungen
der Mensch regelnd eingreift. Mit der erfindungsgemäß erarbeiteten Information über
ausgewählte Schlüsselpassagen ist jedoch das aktuelle wesentliche Bild über den gesamten
Verfahrensablauf jederzeit vorhanden, selbst nach Eingriffen z. B. durch den Obermüller.
Die Kenntnis der Verhältnisse an den Schlüsselpassagen ergibt zusammen mit der Gesamtausbeute
Rückschlüsse auf das Geschehen an der überwiegenden Mehrzahl der eingesetzten Maschinen,
die einen weniger hohen Überwachungsgrad erfordern. Die Erfindung stellt somit einen
glücklichen Griff im Hinblick auf den Einsatz sinnvoller Automatisierung unter Bewahrung
von Eingriffsmöglichkeiten durch den Obermüller dar. Erstmals macht das erfindungsgemäße
Verfahren von der überraschenden Erkenntnis Gebrauch, daß bei der Benutzung der Meßergebnisse
von nur einigen ausgewählten Schlüsselpassagen und deren Verarbeitung in einem nachgeschalteten
Rechner sich eine weitgehend automatisierte Steuerung der Mahlwalzenabstände in einer
Getreidemühlenanlage erreichen läßt, ohne daß eine außerordentlich große Vielzahl
weiterer Meßergebnisse durch entsprechend komplizierte Rechnerprogramme ausgewertet
werden müssen, weil bewußt eine verbleibende Eingriffsmöglichkeit des Obermüllers
mit eingeplant ist.
[0012] Bei der erfindungsgemäßen Getreidemühlenanlage lassen sich die mit der Meßeinrichtung
ermittelten Meßwerte ohne Auftreten einer Störgröße aus Produkteigenschaften, mit
der Genauigkeit von Waagen-Meßwerten ermitteln. Trotzdem ergeben sie den Vorteil eines
kontinuierlichen Meßverfahrens, ähnlich dem bei einer Bandwaage. Der wesentliche Unterschied
zur Bandwaage liegt jedoch gerade in dem sehr einfachen Aufbau und den entsprechend
geringen Herstellungskosten, wie dies andererseits auch bei den (allerdings störempfindlichen)
Pulsmeßgeräten der Fall ist. Tatsächlich weist die erfindungsgemäße Mühlenanlage für
den Erfindungszweck eine Kombination der Vorteile der Bandwaagen und der kontinuierlichen
Durchflußmesser auf, ohne daß deren Nachteile auftreten. Die Vorgabe neuer Einstellwerte
an die Antriebsmittel zum Einstellen der Walzenabstände dient ebenfalls dem eingangs
genannten Ziel, nämlich daß der gesamte Mühlenlauf nicht "ins Schwingen" kommt.
[0013] Die Erfindung erlaubt verschiedene sehr vorteilhafte Ausgestaltungsmöglichkeiten:
[0014] Bei den B-Passagen genügt z. B. die gleichzeitige Erfassung der Mühleneingangsleistung,
bei C-Passagen ist es vorteilhaft, wenn die Eingangsleistung jedes automatisch überwachten
Walzenstuhles gleichzeitig erfaßt wird. Bei sehr wenig Produktwechseln ist es völlig
ausreichend, wenn das Meßsignal von der Menge des Abstoßes des ersten Schrotes (B
1-Passage), bevorzugt in kurzen Zeitabständen, während des Mahlvorganges ermittelt
wird. Bei häufigen bzw. sehr häufigen Wechseln der Rohstoff- oder Endproduktqualität
wird vorzugsweise gleichermaßen das Meßsignal ebenfalls bei den Passagen B
2 und eventuell bei weiteren Passagen (B
3 ...) von der Menge des Siebabstoßes bzw. des Schrotes abgeleiter. Ganz besonders
vorzugsweise wird jedoch neben dem von der Menge des Siebabstoßes bzw. des Schrotes
abgeleiteten Meßsignal in den B-Passagen auch noch ein von der Menge des Siebdurchfalles
bzw. des Mehlanfalles abgeleitetes weiteres Meßsignal bei den Passagen C
1, wiederum vorzugsweise in kurzen Zeitabständen, während des Meßvorganges abgeleitet
und dem Rechner zugeführt. Bei den Ausmahlpassagen gilt aber ebenfalls, je nach Größe
und Komfortansprüchen, daß sowohl bei den C
2-Passagen und eventuell gezielt ausgewählten Mahlpassagen entsprechende Meßwertableitungen
vorgenommen werden können. Besonders vorzugsweise wird das Meßsignal aus der Menge
des Abstoßes bzw. Durchfalles folgender Passagenkombinationen abgeleitet:



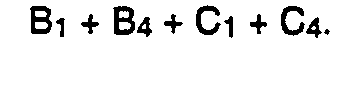
Der letztgenannten Kombination für die Ableitung des Meßwertes liegt der Gedanke zugrunde,
daß mit den Passagen Bi und Ci ein Regelvorgang sichergestellt wird, die Passagen
8
4 und C
4 hingegen nur zur Kontrolle dienen. Es sind hier lediglich besonders bevorzugte Kombinationen
für die Ableitung des Meßsignales an besonders wichtigen Meßstellen aufgeführt, die
jedoch vom Fachmann je nach spezifischer Mühlenanlage ausgewählt bzw. herangezogen
werden können.
[0015] In einer weiteren bevorzugten Ausgestaltung des erfindungsgemäßen Verfahrens ist
in dem Computer für jede Getreidemischung bzw. für jede Mahlaufgabe ein Vorgabe-Sollwert-Schema
gespeichert, in dem alle Werte für die automatische Steuerung der Mahlwalzenabstände,
insbesondere dem Mahlspalt entsprechende Vorgabe-Einstellwerte, sowie die für die
nachfolgend erfaßten Plansichter gültigen Minima- und Maxima-Werte für den Schrot-
bzw. Mehlanfall vorgegeben sind, innerhalb derer keine Sollwerte der Walzenstühle
verändert werden. Auf diese Weise läßt sich eine unerwünschte, zu häufige Korrektur
der Walzeneinstellungen vermeiden. Denn zumindest theoretisch hat eine einzige Mahlspaltkorrektur
beim ersten Schrot-Walzenstuhl bei einer größeren Mühlenanlage zur Folge, daß die
Verhältnisse bei allen folgenden zwanzig bis dreißig Walzenstühlen und Plansichtern
ebenfalls geändert werden. Bevorzugt wird daher dem Computer ein Korrekturprogramm
zugeordnet, das selbständig Korrekturbefehle durch Verändern der Arbeits-Sollwerte
in der Reihenfolge von der größten zur kleinsten Korrektur hin vornimmt. Wird also
z. B. bei der Auswahlpassage C
1 eine starke Abweichung festgestellt, so wird diese zuerst richtiggestellt, dann erst
z. B. eine notwendige Folgekorrektur etwa bei der Passage Bi usw.
[0016] Sehr vorteilhaft ist es weiterhin, wenn der Computer ein Grundprogramm enthält, das
auch nicht-automatisch erfaßte Parameter (wie etwa Mahldruck, Kraftaufnahme, effektive
Mahlspaltweite usw.), insbesondere auch solche der nicht-automatisch gesteuerten Maschinen
(d.h. nicht-automatisch einstell- bzw. regelbare Walzenstühle und abgeleitete Werte
bezüglich Siebarbeit) erfaßt und jederzeit abrufbar ist, so daß, gestützt auf ältere
Werte, Kontrollen und entsprechende Handeingriffe vorgenommen werden können. Bei dieser
Lösung kommt ganz besonders der Nutzen der automatischen Mittel für alle notwendigen
Kontrollen und Handeingaben zum Ausdruck. Gleichzeitig bringt dies aber auch den Vorteil,
daß der Müller bei jeder Schicht in einer Mühle die früheren Werte wieder verwenden
kann. Dies ermöglicht es auch, selbst bei wechselndem Personal eine relativ konstante
Betriebsführung der Mühlenanlage zu gewährleisten. In den meisten Fällen genügt es,
wenn nur bei einem Teil aller Walzwerke der Mahlspalt automatisch voreingestellt wird
und nur bei einem Teil dieser automatisch voreingestellten Walzwerke anschließend
der Siebabstoß und/oder der Siebdurchfall gemessen und hieraus das Meßsignal abgeleitet
wird. So wird vorzugsweise nur bei einem Teil aller Walzwerke der Mahlspalt automatisch
voreingestellt und nur bei einem Teil der automatisch voreinstellbaren Walzwerke anschließend
der Siebabstoß und/oder Siebdurchfall gemessen bzw. das Meßsignal hieraus abgeleitet,
wobei: wiederum vorzugsweise, bei weniger als der Hälfte aller Walzwerke der Mahlspalt
automatisch voreingestellt und bei zwei bis sechs nachfolgenden Plansichtern der Siebdurchfall
bzw. Siebabstoß gemessen und hieraus ein Meßsignal abgeleitet wird.
[0017] Eine besonders vorteilhafte Weiterbildung des erfindungsgemäßen Verfahrens besteht
darin, daß das Meßsignal aus Momentanwerten der Kraftanteile sowohl des Einströmimpulses
des Produktstroms wie auch dessen Gewichtes in einem Wägegefäß abgeleitet, der Siebdurchfall
und/oder der Siebabstoß bei kontinuierlichem Betrieb durch ein Erfassen dieser Momentanwerte
über einen kurzen Zeitraum hinweg festgestellt, hieraus eine Steuergröße abgeleitet
und für die automatische Überwachung und gegebenenfalls Steuerung der Walzenstühle
eingesetzt wird. Bemerkenswert ist, daß offensichtlich alle bisherigen Versuche, die
auf den direkt sich anbietenden kontinuierlich arbeitenden Impulsmeßsystemen basierten,
fehlschlugen. Bei diesen kontinuierlichen Wägesystemen wird aufgrund des Impulses
eines fallenden Produktstroms auf die Produktmenge geschlossen, was bei idealen Bedingungen
zu relativ guten Ergebnissen führt. Treten jedoch Störgrößen auf, beginnt z. B. das
Mehl an einer der Prallplatten zu kleben, so verfälscht sich sehr schnell der Meßwert
bis zur Unbrauchbarkeit. Bei dem erfindungsgemäßen Verfahren kann diesem Problem jedoch
unschwer Rechnung getragen werden, indem durch eine einfache Subtraktion zweier kurz
aufeinanderfolgender Messungen in einem Wägebehälter der Impulsanteil und damit jede
Störquelle durch Luftfeuchtigkeit, Produktankleben o.ä. in Wegfall kommt. Diese Impulsmessung
bedingt aber ein andauerndes Einströmen des Gutes in den Wägebehälter, so daß gleichzeitig
die Messung als kontinuierlich bezeichnet werden kann. Hat man das Ziel einer Verbesserung
der Gleichmäßigkeit des Produktflusses in der Mühlenanlage vor Augen, so erkennt man
den Wert einer Zwischenverwiegung, die im wesentlichen kontinuierlich ist, oft durchgeführt
wird, jedoch nur kurze Zeit in Anspruch nimmt. Die Verwendung eines Meßwertes (wie
bei üblichen Verfahren), der selbst eine Störgröße darstellt, die zu vermeiden gerade
das Ziel der eingesetzten Messung und Regelung war, ist zwecklos, was die Vergangenheit
deutlich gezeigt hat. In vorteilhafter Weiterentwicklung des erfindungsgemäßen Verfahrens
wird daher zur Ermittlung der Steuergröße die Gewichtszunahme im Wägegefäß ohne Unterbrechung
des Produktstromes pro Zeiteinheit erfaßt, der erfaßte Wert mit der gesamten Mühlenleistung
verglichen und sodann als Parameter für die Sichteinheit dem Computer mitgeteilt.
Bevorzugt wird dabei im Wägegefäß eine Verwiegung nach einem vorgegegebenen Zyklus
durchgeführt, vorzugsweise etwa alle 10 bis 30 Min., und sie dauert weniger als 10
Sekunden, vorzugsweise weniger als 5 Sekunden.
[0018] Bevorzugt werden die Mahlwalzen über den Computer aufgrund eines Ist-Sollwert-Vergleiches
zur Einstellung bzw. Regelung entsprechender über die Mahlwalzen einstellbarer Arbeitsparameter
(Mahlwalzendrehzahl und/oder Mahlspalt) ansteuerbar bzw. regelbar ausgeführt, wobei,
wiederum vorzugsweise, die Einstellvorrichtungen bzw. deren Antriebsmittel durch einen
zentralen Computer fernsteuerbar sind und eine mechanische oder elektrische Kupplung
zwischen Antriebsmitteln und Einstellkupplung vorgesehen ist. Diese Lösung wird bevorzugt
bei Ausmahl- passagen, also bei Glattwalzen angewendet. Bei Schrotpassagen bzw. bei
den Riffelwalzen sind hingegen bevorzugt die Einstellvorrichtung bzw. deren Antriebsmittel
über den Computer fernsteuerbar und zur Verhinderung schädlicher Einsteuerungen mit
einer Druck- oder Distanz- oder Kraftaufnahme-Begrenzungseinrichtung versehen.
Kurze Beschreibung der Zeichnungen
[0019] Die Erfindung wird nachfolgend anhand der Zeichnung im Prinzip beispielshalber noch
näher erläutert. Es zeigen:
Figur 1 die schematische Darstellung einer erfindungsgemäßen Vorrichtung für die automatische
Überwachung eines Mahlwalzenpaares;
Figur 2 eine stark vereinfachte, prinzipielle Darstellung des Ablaufs der Überwachung
der Mahl- und Sichtarbeit einer gesamten Mühlenanlage;
Figur 3 eine schematische Darstellung einiger Schrot- und Grießpassagen mit deren
Ausgangsprodukten, sowie
Figur 4 eine schematische Darstellung verschiedener Ausmahl-Passagen.
Ausführliche Beschreibung der Zeichnungen
[0020] Figur 1 zeigt einen Walzenstuhl 1, von dem aber nur eine Hälfte bzw. ein Mahlwalzenpaar
2, 2' dargestellt ist. Eine besondere Eigenart des Müllereiwalzenstuhles liegt darin,
daß, anders als bei Produkten wie Gesteinen oder Kohle, das Produkt nicht zerdrückt,
aber auch nicht nur rein gequetscht wird. Vielmehr wird ein eigentlicher Druck-Schervorgang
eingesetzt, was durch eine Erhöhung der Umlaufgeschwindigkeit einer Walze, etwa der
Walze 2', im Vergleich zur Umlaufgeschwindigkeit der anderen Walze, etwa der Walze
2 erreicht wird. Die Mahlwalzen 2, 2' dürfen deshalb nur bei Vorhandensein von Produkt
eingerückt werden, was über eine Produktfühleinrichtung 3 feststellbar bzw. steuerbar
ist. Über ein entsprechendes Signal wird ein Pneumatikkolben 4 und über diesen ein
Hebel 5 und damit die zugehörige Walze 2' in ihre ein- oder ausgerückte Stellung gebracht.
Der Mahlspalt selbst kann über ein Handrad 6 auf ein gewünschtes Maß voreingestellt
bzw. bei Bedarf nachträglich von der Bedienungsperson korrigiert werden. Unabhängig
von dieser Handeinstellung kann der Mahlspalt jedoch auch von einem Rechner 7 mit
Speichern 8, 8', 8" für Sollwerte, ferngesteuert werden. Der Mahlspalt kann nun z.
B. wie in der EP-B1-0 013 023 beschrieben, auf einen bestimmten, durch frühere Vermahlungen
gefundenen Optimalwert automatisch im Sinne einer Grobeinstellung über einen Verstellmotor
9 und eine Kette 10, die auf eine Welle 11 des Handrades 6 eingreift, eingestellt
werden. Ein jeweils analoger Wert zum Messen des Mahlspaltes wird über einen mit der
Kette 10 mitgeführten Positionsanzeiger 12 festgestellt und über eine Steuerleitung
13 dem Rechner 7 zurückgemeldet.
[0021] In der Figurendarstellung nach Figur 1 ist rechts oben schematisch ein Plansichter
14 dargestellt. Der Produktfluß ist als Eingangsleistung in den Walzenstuhl 1 mit
einem Pfeil 15 dargestellt, der Pfeil 16 zeigt die Produktüberführung vom Walzenstuhl
1 in den Plansichter 14, der Pfeil 17 bezeichnet den Siebabstoß und Pfeil 18 den Siebdurchfall.
Der Plansichter 14 ist mit einzelnen Siebrahmen 19, 20, 21 und 22 versehen, deren
Anzahl sich nach der Produktleistung und insbesondere nach der jeweiligen Produktqualität
richtet.
[0022] In Figur 1 ist die Erfassung des Produktdurchsatzes in Abhängigkeit vom Siebabstoß
(Pfeil 17) in einem Steuerkreis mit ausgezogenen Linien dargestellt. Ein Wiegegefäß
23 ist dabei über elastische Manschetten 27, 28 getrennt von den festen Anlageelementen
gelagert; ferner ist ein Einlauf 25 sowie ein Ablauf 26 vorgesehen. Das Wiegegefäß
23 ist auf elektronischen Waageelementen 24 abgestützt, welche die Gewichtssignale
als Meßsignale an eine Steuerung 29 weitergeben. Ein Umsetzer 30 gibt ein pneumatisches
Signal an einen Zylinder 31 ab, der einen Verschlußschieber 32 betätigt. Das Wiegesystem
ist in der EP-A1-140 213 näher beschrieben, worauf vollumfänglich Bezug genommen wird.
Mittels dieses Systems wird eine Gewichtszunahme pro Zeiteinheit gemessen, beispielsweise
während eines Bruchteiles einer Sekunde bis hin zu mehreren Sekunden, und ein abgeleitetes
Meßsignal für das Verhältnis Gewicht/Zeiteinheit an den Rechner 7 abgegeben. Entscheidend
ist bei diesem neuen Meßsystem, daß der Produktzufluß 17' in das Wiegegefäß 23 während,
vor und nach der Messung nicht unterbrochen wird. Für die Gewichtszunahme werden über
die elektronischen Waageelemente 24 in Zeitabständen Momentanwerte gemessen, z. B.
die Produktmenge A (nach einer gewissen Verzögerung nach Schließen des Verschlußschiebers
32) und die Produktmenge B im Wiegegefäß 23. Die Füllhöhendifferenz zwischen den Produktmengen
A und B entspricht dann genau der Produktmenge, die von einem entsprechenden der Produktmenge
B zugeordneten Zeitpunkt bis zu dem der Produktmenge A zugeordneten Zeitpunkt in den
Behälter eingeflossen ist, woraus somit ein entsprechendes Signal für den Produktdurchsatz
abgeleitet werden kann. Dem Rechner 7 werden ferner alle erforderlichen Daten (wie
etwa Eingangsleistung 15, Produktmischung sowie spezifische Mahlvorgaben) eingegeben
und in den entsprechenden Speichern 8, 8' bzw. 8" bereitgehalten. Ein weiteres Wiegesystem
ist in der gattungsgemäßen EP-A1-0 013 023 beschrieben.
[0023] Die Arbeitsweise der Anlage ist wie folgt:
[0024] In den Speichern 8, 8' und 8" werden entsprechend der gewünschten Mahlarbeit, die
ausgeführt werden soll, von einem zentralen Rechner 40 (Figur 2) über eine Steuerleitung
41 die entsprechenden Speicherstellen abgerufen und die Daten dem Rechner 7 zur Verfügung
gestellt. Wesentliche Daten sind dabei die Werte für die Getreidemischung und Feuchtigkeit,
für die Mahlarbeit und für die Eingangsleistung, insbesondere aber der zugehörige
Wert für den Walzenstuhl, der Mahlspalt, der Mahldruck oder die elektrische Stromaufnahme
des Antriebsmotors des Walzenstuhles. In Figur 1 sind nur symbolisch ein Druckmeßgerät
33 sowie ein Strommeßgerät 34 dargestellt. Der Mahlwalzenabstand kann direkt vom Meßwert
des Positionsanzeigers 12 abgeleitet oder aber, bei entsprechender Anzeige 6' des
Handrades 6, abgelesen werden. Der nächstwichtige Wert ist nun die Erfassung eines
entsprechend Meßwertes am Plansichter, im Beispiel der Figur 1 etwa die Gewichtsmenge
pro Zeiteinheit bezüglich des Siebabstoßes, der z. B. bei der ersten Schrotpassage
als bevorzugter Schlüsselpassage gewählt wird. Zur Vereinfachung der Darstellung ist
für das gezeigte Beispiel nun der Meßwert des Positionsanzeigers 12 (somit ein Wert
entsprechend dem Abstand der Mahlwalzen) als "Walzenabstand" bezeichnet. Weiterhin
wird die pro Zeiteinheit anfallende Produktmenge des ersten Siebabstoßes bzw. die
jeweils momentane oder gemittelte Leistung des zweiten Schrotes bzw. der Schrotanfall
B
2 gemessen und entsprechend verglichen. Der absolute Wert des Walzenabstandes interessiert
im Prinzip für die auszuführende Regelung nicht mehr, da ein entsprechender Zahlenwert
aus vorangegangenen Optimierungen ermittelt werden kann, hingegen der genaue Wert
des Schrotanfalles B
2 ist sehr wesentlich. Sind alle Verfahrensparameter als richtig befunden (Befeuchtung
des Getreides, Abstehzeit des Getreides, Mühleneingangsleistung usw.), so arbeitet
dennoch die Mühle erfahrungsgemäß nicht vollautomatisch mit konstanter Mahlarbeit
und konstanter Mahlqualität, da es sich bei dem zu vermahlenden Produkt (Getreide)
um einen "lebenden" Stoff handelt, der je nach Herkunftsort und klimatischen Bedingungen
oder in Abhängigkeit von seiner Wachstumsphase laufend irgendwelchen Einflüssen unterworfen
ist. Das Weizenkorn atmet, es verarbeitet Stärke, dabei verändert sich das Eiweiß,
wobei verschiedene sehr komplexe enzymatische und andere Vorgänge ablaufen. Durch
all dieses wird nicht nur die mechanische Bearbeitbarkeit, sondern auch das Wasseraufnahmeverhalten
und die Festigkeitseigenschaft der Schalenteile sowie des Mehlkornes beeinflußt. Letztlich
ist es das Ziel einer guten Vermahlung, eine hohe Ausbeute an hellen Mehlen mit optimaler
Qualität bei wirtschaftlich günstiger Ausnützung der Mühlenanlage zu erhalten. Wenngleich
der Obermüller letztlich die Mühle selbst steuern muß, so sind jedoch bei Großanlagen
(nur und gerade bei diesen) Kontrollmittel unerläßlich, damit eine Person tatsächlich
in die Lage versetzt wird, eine Mühlenanlage als Ganzes wirklich zu führen und dabei
den erforderlichen Überblick zu behalten, was das Hauptziel der vorliegenden Erfindung
ist.
[0025] Zum Steuern der Mahlarbeit werden dabei nun laufend die Werte aus einer oder mehreren
Schlüsselpassagen bzw. der gewählte Siebdurchfall oder Siebabstoß sowie ein oder mehrere
wichtige andere Meßwerte aus dem Produktionsablauf herausgegriffen und überwacht.
Liegt nun z. B. der Anteil des Siebabstoßes beim ersten Schrot bei 70 bis 75 % der
Mühleneingangsleistung, so ist dies für den Müller ein Indiz dafür, daß die Verarbeitung
bis zu der entsprechenden Stelle gut läuft. Die Steuerung kann nun so aufgebaut werden,
daß für den Siebwert ein enges Toleranzband für jede einzelne Mahlaufgabe und für
jede einzelne Mahlpassage gewählt wird, innerhalb dessen der Mahlablauf ausreichend
zufriedenstellend ist, was z. B. über eine entsprechende Kontrollampe angezeigt werden
kann. Darüberhinaus wird ein zweites, größeres Toleranzband vorgesehen, innerhalb
dessen vom Rechner eine Veränderung des Mahlspaltes direkt ausgelöst und nach entsprechender
Zeitverzögerung bei erfolgreicher Korrektur beibehalten wird. Wird jedoch ein Siebwert
gemessen, der noch außerhalb des breiteren Toleranzbandes liegt, dann kann z. B. Alarm
ausgelöst oder gegebenenfalls der Walzenstuhl ganz abgestellt werden.
[0026] Da jede Mühle spezifischen Anforderungen genügen muß und auch ein entsprechendes
besonderes Diagramm des Ablaufes aufweist, ist eine Vielzahl sinnvoller Anwendungsmöglichkeiten
gegeben. Als Grundschema hierfür sei Figur 2 herangezogen, wobei als Verarbeitungsmaschinen
nur jeweils einzelne Exemplare prinzipiell dargestellt sind, auch wenn jeweils eine
Vielzahl von solchen Maschinen anstelle des einzelnen dargestellten Exemplares in
der praktischen Mühlenarbeit eingesetzt sind.
[0027] Der zentrale Rechner 40 weist einen Speicher 42 für die Sollwertschemen auf und ist
gleichzeitig an andere Rechnereinheiten 43 anschließbar, etwa an einen Buchhaltungsrechner.
Entsprechend dem Ausbaugrad der Anlage kann der Rechner mit einem zentralen Bildschirm
44 sowie einem zentralen Eingabedrucker 45 ausgerüstet sein. In seiner vollen Ausbaustufe
werden bevorzugt ein oder mehrere transportable Bildschirme mit Eingabedrucker vorgesehen,
die für örtliche Eingriffe, z. B. bei einem Walzenstuhl usw., an der Arbeitsstelle
benützt werden können. Zur Vereinfachung sind in Figur 2 lediglich bei der ersten
Mahlpassage B
i die gleichen Bezugszeichen wie in Figur 1 gewählt worden, obwohl die entsprechenden
identischen Elemente an jeder beliebigen anderen Stelle in der Mühle, also etwa bei
B
2, B
3 bzw. Bx sowie Ci, C
2, C
3 ... Cx eingesetzt werden können. Dabei wird nur ein Teil der Passagen voll überwacht,
in Figur 2 sind dies die Passagen Bi und B
3 sowie C
i und Cs. Ferner weist ein weiterer Teil der Walzenstühle eine automatische Mahlspaltsteuereinrichtung
mit Rechner auf, jedoch ohne Wägesystem, in Figur 2 ist dies Passage B
x, und ferner ist bei einer Vielzahl der Passagen weder eine automatische Steuerung
der Walzenstühle noch eine Verwägung des Siebabstoßes bzw. Siebdurchfalles vorgenommen,
in Figur 2 mit Div 1 und C
x bezeichnet. Im Regelfall wird für die überwiegende Anzahl der Passagen keine mechanische
Überwachung im Sinne der Erfindung vorgenommen, hingegen ist es denkbar, daß bei allen
Antriebsmotoren der Walzenstühle die Stromaufnahme gemessen und überwacht wird.
[0028] Die Figuren 3 und 4 stellen lediglich vergrößerte Darstellungen aus Figur 2 dar,
wobei die diagramatischen Verknüpfungen ersichtlich sind. Die mit B bezeichneten Passagen
sind der Beginn der Vermahlung, mit S sind die Grießputzmaschinen bezeichnet und C
stellt die Ausmahl- passagen dar. Mit "Div 1" ist ein Diviseur bezeichnet.
[0029] Ferner ist nun wesentlich, daß in jedem Fall die Mühleneingangsleistung, d.h. die
Menge der zu verarbeitenden Rohfrucht, während der ganzen Vermahlung genau erfaßt
wird, etwa durch ein Wägesystem, das bei B
i mit 50 bezeichnet ist. Da die Ausmahlpassagen von verschiedenen Stellen-gespeist
werden, ist bei den C-Passagen eine Messung der Eingangsleistung zumindest bei C
1A durch eine Einrichtung 51 (nur prinzipiell dargestellt) sowie bei B
2, C
2 durch eine im Prinzip dargestellte Einrichtung 52 erforderlich.
1. Verfahren zum Einstellen der Mahlwalzenabstände von Walzenstühlen (1) mit jeweils
nachgeschaltetem Siebsystem (14) in einer Getreidemühlenanlage, bei welchem in ausgewählten
Schlüsselpassagen jeweils ein einen Istwert repräsentierendes Meßsignal abgegriffen,
einem Computer (40) zugeführt, dort mit einem gespeicherten Sollwert verglichen und
bei Abweichung des Istwertes vom Sollwert ein Steuersignal (41) erzeugt wird, dadurch
gekennzeichnet, daß als Ist- und Sollwerte der Abstoß (17) oder der Durchfall (18)
der Siebsysteme (14) gewählt und das Steuersignal (41) zur Vorgabe neuer Einstellwerte
der Walzenabstände verwendet wird.
2. Verfahren nach Anspruch 1, dadurch gekennzeichnet, daß das Meßsignal bei den Passagen
Bi oder Bi und B2 oder Bi, B2 und B3 von der Menge des Siebabstoßes bzw. des Schrotes abgeleitet wird.
3. Verfahren nach Anspruch 1 oder 2, dadurch gekennzeichnet, daß das Meßsignal bei
dem Passagen Ci oder Ci und C2 oder Ci und C2 und C3 von der Menge des Siebdurchfalles bzw. des Mehlanfalles abgeleitet wird.
4. Verfahren nach einem der Ansprüche 1 bis 3, dadurch gekennzeichnet, daß in den
Computer für jede Getreidemischung bzw. für jede Mahlaufgabe ein Vorgabe-Sollwert-Schema
gespeichert ist, in dem alle Werte für die automatische Steuerung der Mahlwalzenabstände,
insbesondere dem Mahlspalt entsprechende Vorgabe-Einstellwerte, sowie für den nachfolgend
erfaßten Plansichter gültige Minima- und Maxima-Werte für den Schrot- bzw. Mehlanfall
vorgegeben sind, innerhalb derer keine Sollwerte der Walzenstühle verändert werden.
5. Verfahren nach Anspruch 4, dadurch gekennzeichnet, daß dem Computer ein Korrekturprogramm
zugeordnet ist, das selbständig Korrekturbefehle durch Verändern der Arbeits-Sollwerte
in der Reihenfolge von der größten zur kleinsten Korrektur hin vornimmt.
6. Verfahren nach einem der Ansprüche 1 bis 5, dadurch gekennzeichnet, daß der Computer
ein Grundprogramm enthält, das auch nicht-automatisch erfaßte Parameter (wie Mahldruck,
Kraftaufnahme, effektive Mahlspaltweite usw.), insbesondere auch solche der nicht-automatisch
gesteuerten Maschinen (nicht-automatisch einstell- bzw. regelbare Walzenstühle und
abgeleitete Werte bezüglich Siebarbeit) erfaßt und jederzeit abrufbar ist, so daß
gestützt auf ältere Werte Kontrollen und entsprechende Handeingriffe vorgenommen werden
können.
7. Verfahren nach einem der Ansprüche 1 bis 6, dadurch gekennzeichnet, daß nur bei
einem Teil aller Walzwerke der Mahlspalt automatisch voreingestellt wird und nur bei
einem Teil der automatisch voreinstellbaren Walzwerke anschließend der Siebabstoß
und/oder Siebdurchfall gemessen wird.
8. Verfahren nach Anspruch 7, dadurch gekennzeichnet, daß bei weniger als der Hälfte
aller Walzwerke der Mahlspalt automatisch voreingestellt und bei zwei bis sechs nachfolgenden
Plansichtern der Siebdurchfall bzw. Siebabstoß gemessen wird.
9. Verfahren nach einem der Ansprüche 1 bis 8, dadurch gekennzeichnet, daß das Meßsignal
aus Momentanwerten der Kraftanteile sowohl des Einströmimpulses des Produktstromes
wie auch dessen Gewichtes in einem Wägegefäß abgeleitet, der Siebdurchfall und/oder
der Siebabstoß bei kontinuierlichem Betrieb durch ein Erfassen dieser Momentanwerte
über einen kurzen Zeitraum hinweg festgestellt, hieraus eine Steuergröße abgeleitet
und für die automatische Überwachung und gegebenenfalls Steuerung der Walzenstühle
eingesetzt wird.
10. Verfahren nach Anspruch 9, dadurch gekennzeichnet, daß zur Ermittlung der Steuergröße
die Gewichtszunahme im Wägegefäß ohne Unterbrechung des Produktstromes pro Zeiteinheit
erfaßt, der erfaßte Wert mit der Gesamtmühlenleistung verglichen und sodann als Parameter
für die Sichteinheit dem Computer eingegeben wird.
11. Verfahren nach Anspruch 9 oder 10, dadurch gekennzeichnet, daß im Wägegefäß eine
Verwiegung nach einem vorgegebenen Zyklus durchgeführt wird und weniger als 10 Sek.,
vorzugsweise weniger als 5 Sek. dauert.
12. Getreidenmühlenanlage mit,
a) einer Folge von Walzenstühlen (1) und nachgeschalteten Plansichtern (14),
b) steuerbaren Antriebsmitteln (4, 5, 9) zum Einstellen der Walzenabstände,
c) Meßeinrichtungen (23, 24) zur Istwertmessung von Betriebsparametern und
d) einem zentralen Computer (40) mit Datenspeicher (42) zur Überwachung der Istwerte
ausgewählter Schlüsselpassagen, zu deren Vergleich mit korrespondierenden, im Datenspeicher
(42) abgelegten Sollwerten und zur Erzeugung von Steuersignalen (41) bei Abweichungen
zwischen Ist- und Sollwerten, dadurch gekennzeichnet, daß
e) die Meßeinrichtung (23, 24) ein den Plansichtern (14) nachgeschaltetes Durchlauf-
Gewichtsmeßsystem zur kontinuierlichen Erfassung des Siebabstosses (17) oder des Siebdurchfalles
(18) ist und
f) der Steuerausgang (41) des Computers (40) mit einem Sollwertspeicher (8) zur Vorgabe
neuer Einstellwerte an die Antriebsmittel (4, 5, 9) verbunden ist.
13. Getreidemühlenanlage nach Anspruch 12, dadurch gekennzeichnet, daß die Mahlwalzen
über den Computer aufgrund eines Ist-Sollwert-Vergleiches zur Einstellung bzw. Regelung
entsprechender über die Mahlwalzen einstellbarer Arbeitsparameter (Mahlwalzendrehzahl
und/oder Mahlspalt) ansteuerbar bzw. regelbar sind.
14. Getreidemühlenanlage nach Anspruch 12 oder 13, dadurch gekennzeichnet, daß die
Einstellvorrichtungen bzw. deren Antriebsmittel durch einen zentralen Computer fernsteuerbar
sind und eine mechanische oder elektrische Kupplung zwischen Antriebsmitteln und Einstellvorrichtung
vorgesehen ist.
15. Getreidemühlenanlage nach Anspruch 12 oder 13, dadurch gekennzeichnet, daß die
Einstellvorrichtung bzw. deren Antriebsmittel über den Computer fernsteuerbar sind
und zur Verhinderung schädlicher Einsteuerungen mit einer Druck- oder Distanz- oder
KraftaufnahmeBegrenzungseinrichtung versehen sind.
1. Process for setting the distances between milling rollers of roller assemblies
(1) with screening system (14) connected downstream in each case, in a grain mill,
in which in selected key passages a measurement signal representing an actual value
in each case is accessed, fed to a computer (40), and compared there with a stored
desired value, and if the actual value deviates from the desired value a control signal
(41) is produced, characterized in that the actual and desired values selected are
the screen discharge (17) or the screenings (18) of the screening system (14), and
the control signal (41) is used to predetermine new settings of the distances between
rollers.
2. Process according to Claim 1, characterized in that the measurement signal in the
passages Bi or Bi and B2 or B1, B2 and B3 are derived from the quantity of screen discharge or of meal.
3. Process according to Claim 1 or 2, characterized in that the measurement signal
in the passages C1 or C1 and C2 or C1, C2 and Cs are derived from the quantity of screen discharge or of the meal obtained.
4. Process according to one of Claims 1 to 3, characterized in that stored in the
computer for each grain mixture or for each meal input is a preset desired value schedule
in which all values for automatic control of the distances between milling rollers,
in particular predetermined settings corresponding to the milling clearance, and for
the subsequently recorded sifter valid minimum and maximum values for the coarse millings
or meal obtained, within which no desired values of the roller assemblies are changed,
are predetermined.
5. Process according to Claim 4, characterized in that a correction program which
independently carries out correction commands by changing the working desired values
in an order going from the largest to the smallest correction is allocated to the
computer.
6. Process according to one of Claims 1 to 5, characterized in that the computer contains
a basic program which also records parameters not automatically recorded (such as
milling pressure, power consumption, effective milling clearance etc.), in particular
those of non-automatically controlled machines (non-automatically settable or controllable
roller assemblies and derived values as regards screening work) and can be called
up at any time, so that checks and appropriate manual interventions can be undertaken
based on older values.
7. Process according to claims 1 to 6, characterized in that the milling clearance
is automatically preset in only a part of all roller assemblies and the screen discharge
and/or screenings are measured subsequently in only a part of the automatically presettable
roller assemblies.
8. Process according to Claim 7, characterized in that the milling clearance is automatically
preset in fewer than half of all roller assemblies and the screenings or screen discharge
are measured in two to six sifters downstream.
9. Process according to one of Claims 1 to 8, characterized in that the measurement
signal is derived from current values of the power parts of both the inflow impulse
of the product flow and its weight in a weighing vessel, the screenings and/or the
screen discharge are established in continuous operation by ascertaining these current
values over a short period of time, and from this a control parameter is derived and
is used for the automatic monitoring and, if necessary, control of the roller assemblies.
10. Process according to Claim 9, characterized in that to ascertain the control parameter
the weight increase in the weighing vessel is ascertained without interrupting the
product flow per unit time, and the ascertained value is compared with the overall
mill output and is then entered in the computer as a parameter for the sifting unit.
11. Process according to Claim 9 or 10, characterized in that weighing according to
a predetermined cycle takes place in the weighing vessel and takes less than 10'sec., preferably less than 5 sec.
12. Grain milling unit with:
a) a sequence of roller assemblies (1) and sifters (14) connected downstream;
b) controllable drive means (4, 5, 9) for setting the distances between rollers;
c) measuring devices (23, 24) for actual value measurement of operating parameters;
and
d) a central computer (40) with data storage unit (42) for monitoring the actual values
of selected key passages, for their comparison with corresponding desired values stored
in the data storage unit (42), and for the production of control signals (41) in the
event of deviations between actual and desired values; characterized in that
e) the measuring device (23, 24) is a continuous weight measuring system connected
downstream of the sifters (14) for continuous recording of the screen discharge (17)
or of the screenings (17); and
f) the control output (41) of the computer (40) is connected to a desired value storage
unit (8) for feeding of new settings to the drive means (4, 5, 9).
13. Grain milling unit according to Claim 12, characterized in that the milling rollers
can be controlled or regulated by means of the computer on the basis of an actual
value/desired value comparison for setting or controlling relevant working parameters
which are settable by means of the milling rollers (milling roller speed and/or milling
clearance).
14. Grain milling unit according to claim 12 or 13, characterized in that the setting
devices or their drive means are remotely controllable by means of a central computer
and a mechanical or electrical coupling is provided between drive means and setting
device.
15. Grain milling unit according to claim 12 or 13, characterized in that the setting
devices or their drive means are remotely controllable by means of the computer and
are provided with a pressure or distance or power consumption limiting device to prevent
damaging control operations.
1. Procédé d'ajustement des écartements existant entre les cylindres broyeurs de moulins
à cylindres (1) comportant chacun un dispositif de blutage (14) monté en aval, ces
moulins à cylindres faisant partie d'une installation de mouture de céréales, procédé
selon lequel on relève, dans des passages-clés sélectionnés et dans chacun d'eux,
un signal de mesure représentant une valeur réelle, on l'envoie à un ordinateur (40),
on l'y compare à une valeur de consigne se trouvant en mémoire et, en cas d'écart
entre cette valeur réelle et cette valeur de consigne, on produit un signal de commande
(41 caractérisé en ce qu'on choisit, comme valeur réelle et valeur de consigne, le
rejet (17) ou le passé (18) du dispositif de blutage (14) et on utilise le signal
de commande (41) pour fixer de nouvelles valeurs d'ajustement pour les écartements
entre cylindres.
2. Procédé suivant la revendication 1, caractérisé en ce que, dans le cas des passages
Bi, ou Bi et B2, au Bi, B2 et B3, on déduit le signal de mesure de la quantité du rejet du blutage ou de celle du
gruau.
3. Procédé suivant la revendication 1 ou 2, caractérisé en ce que, dans le cas des
passages C1, ou Ci et C2, ou C1, C2 et C3, on déduit le signal de mesure de la quantité du passé du blutage ou de celle de
la farine produite.
4. Procédé suivant l'une des revendications 1 à 3, caractérisé en ce que, pour chaque
mélange de céréales ou pour chaque type de mouture prescrit, on met en mémoire dans
l'ordinateur un modèle de valeurs de consigne fixées, dans lequel sont indiquées toutes
les valeurs correspondant à la commande automatique des écartements entre cylindres
broyeurs, notamment les valeurs fixées d'ajustement correspondant à l'intervalle de
broyage, ainsi que, pour le gruau ou la farine produits, des valeurs minimales et
maximales, valables pour le plansichter intervenant suivant, à l'intérieur desquelles
aucune valeur de consigne des moulins à cylindres n'est modifiée.
5. Procédé suivant la revendication 4, caractérisée en ce qu'on associe à l'ordinateur
un programme de correction qui exécute automatiquement des ordres de correction, en
modifiant les valeurs de consigne de travail, dans l'ordre allant de la plus grande
correction à la plus faible.
6. Procédé suivant l'une des revendications 1 à 5, caractérisé en ce que l'ordinateur
contient un programme de base qui porte aussi sur des paramètres qui ne sont pas relevés
automatiquement (tels que la pression de broyage, la puissance consommée, la largeur
effective de l'intervalle de broyage, etc.), notamment aussi sur ceux des machines
qui ne sont pas commandées automatiquement (moulins à cylindres qui ne sont pas ajustables
et réglables automatiquement et valeurs déduites concernant le travail de blutage),
ce programme pouvant être interrogé à tout instant, de sorte que des contrôles et
des interventions manuelles appropriées peuvent être effectués en s'appuyant sur des
valeurs plus anciennes.
7. Procédé suivant l'une des revendications 1 à 6, caractérisé en ce qu'on procède
automatiquement à un préajustement de l'intervalle de broyage seulement sur une partie
de tous les broyeurs à cylindres et en ce qu'on mesure ensuite le rejet du blutage
et/ou le passé du blutage seulement sur une partie des broyeurs à cylindres pouvant
être préajustés automatiquement.
8. Procédé suivant la revendication 7, caractérisé en ce qu'on préajuste automatiquement
l'intervalle de broyage sur moins que la moitié de tous les broyeurs à cylindres et
on mesure le passé du blutage ou le rejet du blutage sur deux à six plansichters suivants.
9. Procédé suivant l'une des revendications 1 à 8, caractérisé en ce qu'on déduit
le signal de mesure à partir de valeurs instantanées des puissances partielles utilisées,
ainsi que de la quantité de mouvement d'entrée du courant de produit, ou de son poids
dans une enceinte à pesée, on détermine le passé du blutage et/ou le rejet du blutage
en fonctionnement continu en relevant ces valeurs instantanées sur un court intervalle
de temps, on en déduit une grandeur de commande et on l'utilise pour la surveillance
automatique et éventuellement la commande des moulins à cylindres.
10. Procédé suivant la revendication 9, caractérisé en ce que, pour déterminer la
grandeur de commande, on relève l'augmentation de poids par unité de temps dans l'enceinte
à pesée, sans interruption du courant de produit, on compare la valeur relevée à la
capacité globale des moulins et on l'introduit alors dans l'ordinateur en tant que
paramètre correspondant à l'unité de blutage.
11. Procédé suivant la revendication 9 ou 10, caractérisé en ce que, dans l'enceinte
à pesée et suivant un cycle fixé à l'avance, on exécute une pesée qui dure moins de
10 s, de préférence moins de 5 s.
12. Installation de mouture de céréales, comportant:
a) une série de moulins à cylindres (1) et de plansichters (14) disposés en aval de
ceux-ci,
b) des moyens d'entraînement (4, 5, 9) pouvant être commandés et servant à ajuster
les écartements entre cylindres,
c) des dispositifs de mesure (23, 24) servant à mesurer la valeur réelle de paramètres
de fonctionnement et
d) un ordinateur central (40) comportant une mémoire de données (42) et servant à
surveiller les valeurs réelles de passages-clés sélectionnés, à les comparer à des
valeurs correspondantes de consigne déposées dans la mémoire de données (42) et à
produire des signaux de commande (41) en cas d'écarts entre des valeurs réelles et
des valeurs de consigne, caractérisée en ce que:
e) le dispositif de mesure (23, 24) est un dispositif de mesure de poids en continu
disposé en aval des plansichters (14) et servant à relever en continu le rejet de
blutage (17) ou le passé de blutage (18) et
la sortie de commande (41) de l'ordinateur (40), qui comporte une mémoire de valeurs
de consigne (8), est reliée aux moyens d'entraînement (4, 5, 9) en vue de fixer de
nouvelles valeurs d'ajustement.
13. Installation de mouture de céréales suivant la revendication 12, caractérisé en
ce que les cylindres broyeurs peuvent être commandés ou être réglés à l'aide de l'ordinateur,
sur la base d'une comparaison de valeurs réelles et de valeurs de consigne, en vue
d'ajuster ou de régler des paramètres appropriés de travail (vitesse de rotation des
cylindres broyeurs et/ou intervalle de broyage) qui peuvent être ajustés à l'aide
des cylindres broyeurs.
14. Installation de mouture de céréales suivant la revendication 12 ou 13, caractérisée
en ce que les dispositifs d'ajustement ou leurs moyens d'entraînement peuvent être
télécommandés à l'aide d'un ordinateur central et en ce qu'il est prévu un accouplement
mécanique ou électrique entre les moyens d'entraînement et le dispositif d'ajustement.
15. Installation de mouture de céréales suivant la revendication 12 ou 13, caractérisée
en ce que le dispositif d'ajustement ou ses moyens d'entraînement peuvent être télécommandés
à l'aide de l'ordinateur et, afin d'empêcher des introductions perturbatrices, sont
pourvus d'un dispositif de limitation de pression, de distance ou de puissance consommée.