[0001] Die Erfindung bezieht sich auf ein Verfahren zum kontrollierten thermischen Nachverbrennen
von oxidierbare Bestandteile enthaltendem Prozeß-Abgas sowie auf eine Vorrichtung
zur Durchführung des Verfahrens gemäß der Oberbegriffe der Ansprüche 1 und 4.
[0002] Eine Vorrichtung zum thermischen Nachverbrennen brennbarer Substanzen in einem Prozeß-Abgas
wie z. B. Kohlenwasserstoffe ist der EP-B1-0 040 690 zu entnehmen. Hier wird das in
Wärmetauscherrohren vorgeheizte Prozeß-Abgas einem Brenner zugeführt, dessen Wärmeleistung
in jedem Moment auf die schwankende Menge der zu verbrennenden Bestandteile und die
unstete Menge des Prozeß-Luftstroms einzustellen ist.
[0003] Der US-A-2 905 523 ist ein Verfahren zum Behandeln von Abgas zu entnehmen, das dem
katalytischen Verbrennen von Ruß und brennbaren Stäuben zusammen mit gasförmigen Bestandteilen
dient. Dieses Verfahren benutzt zum Zweck der Temperatur-Anhebung des zu kalten Prozeßgases
die Rückführung und Einmischung eines Teils des verbrannten heißen Gases in das kalte
Gas ersatzweise für den sonst üblichen rekuperativen Wärmeaustausch und zum Kreislauf-Anfahren
des Systems. Diese Rückführung sichert so das Zündniveau, d.h. die Erhaltung der Mindest-Bettemperatur
im Katalysator. Darüberhinaus kennt das Verfahren die Einspeisung von Luft in den
Haupt- und einen By-pass-Strom des ungereinigten Abgases, zum Zwecke der Sauerstoff-Anreicherung
bei dessen Mangel, oder auch zum Zwecke der Verdünnung bei zu hoher Belastung mit
brennbarer Substanz. Das letztere dient dem Schutz des Katalysators, der nicht über
1600°F hinaus erhitzt werden soll. Beide Funktionen, Rückführung heißen Abgases und
Zugabe von Luft sind verfahrenstechnisch völlig getrennte Funktionen und erfüllen
verschiedene Zwecke. So dient die Rückführung heißer Luft allein der Aufrechterhaltung
des Prozesses. Im Falle der rekuperativen Vorheizung des Prozeß-Abgases entfällt die
Rückführung. In dem Fall, in dem die Einspeisung von Luft der Verdünnung und nicht
der 0
2-Beimengung dient, erfüllt sie nur den Zweck, den Katalysator vor einer Überhitzung
zu schützen. Durch die US-A-2 905 523 wird folglich ein Verfahren beschrieben, bei
dem sich der Brennraum mit Katalysator und nachgeschalteten Bauteilen im Temperaturbereich
zwischen 570
0F und 1600°F (573 K bis 1143 K) bewegen darf, ohne daß hierdurch eine Beeinflussung
des Verbrennens erfolgt.
[0004] Wünschenswert wäre, wenn die Brennkammer-Temperatur möglichst konstant gehalten würde,
da andernfalls eine zu hohe Material-Belastung und Ermüdung durch hohe Temperatur
Wechselgeschwindigkeiten erfolgen würde.
[0005] Es ist bekannte Praxis der thermischen Nachverbrennung, die Temperatur des Brennraums
bei Betrieb mit Minimum-Brennstoffverbrauch innerhalb eines 'Toleranz-Bereichs' bis
hin zu einem Wert schwanken zu lassen, der knapp unterhalb der gesetzten Sicherheitsabschaltgrenze
liegt, bis die prozeßbedingten Temperaturspitzen wieder abklingen. Gelegentlich sind
die Spitzen jedoch so hoch, daß die Abschalttemperatur erreicht wird und der normale
Betrieb unterbrochen werden muß. Man spricht dann von Übertemperatur-Abschaltungen.
Beides, die Überschwingungen und diese Unterbrechungen, wirken sich auf die Lebensdauer
der höher beanspruchten Teile negativ aus. Letzteres unterbricht bei der heutzutage
erforderlichen Vernetzung von Produktion und Abluftreinigung meist automatisch auch
den Produktionsprozeß und führt so zu hohen Produktionsverlusten.
[0006] Hinzu kommt noch, daß Temperaturfühler wie Thermoelemente in praxisgerechter Bauweise
in Schutzrohren stecken und somit Temperaturspitzen erst verspätet, reduziert oder
gar nicht registriert werden. Auch dieser Umstand fördert nicht die Lebensdauer von
Nachverbrennungsvorrichtungen. Kleinere Volumenstromschwankungen - wie sie prozeßbedingt
auftreten können - haben meist auch eine die Brennraumtemperatur negativ beeinflussende
Wirkung. In ihrer Auswirkung sind diese Schwankungen mit denen zu vergleichen, die
aus einem schwankenden Eintrag brennbarer Substanz resultieren.
[0007] Die bisher besprochenen Temperaturschwingungen sind beim Stand der Technik unvermeidbar,
wenn eine Verbrennungsanlage im Grenzbereich ihrer thermischen Kapazität und Störstoffkapazität
betrieben wird, und wenn nicht Maßnahmen zur Abfuhr von Überschußenergie getroffen
sind.
[0008] Nimmt aber der Eintrag an Wärmeenergie deutlich stärker zu als der Brenner der Nachverbrennungsanlage
Reserven hat zum Zurückregeln, dann muß unweigerlich die zwangsweise Abschaltung der
Anlage erfolgen (durch das Auslösen der Übertemperaturschaltung), wenn diese Anlage
nicht mit einem sekundären System zur Minderung der in die Brennkammer eingebrachten
gesamten Wärmemenge ausgerüstet ist.
[0009] Unter 'gesamter Wärmemenge' ist dabei die Enthalpie des zu reinigenden Prozeßgases
zu verstehen, inklusive der durch brennbare Substanz eingebrachten und in Minimumstellung
vom Brenner noch gelieferten Wärmemengen.
[0010] Da hohe Energiepreise heute zu hohem Vorheiz-Grad der Prozeßabluft zwingen, wird
die Enthalpie der im Wärmetauscher vorgewärmten Luft auch die limitierende Größe.
[0011] Diese wird - wie bereits gesagt - durch einen hohen Vorwärmegrad bestimmt, aber auch
schon durch die Temperatur der aus dem Produktionsprozeß herangeförderten Abluft.
Mit steigender Ablufttemperatur aus der Produktion steigt auch die Vorwärmtemperatur
weiter an, so daß die Aufnahmekapazität für brennbare Substanzen insgesamt sinkt.
[0012] Als Anteil der Auslegekapazität kann dieser durch erhöhte Abgastemperatur hervorgerufene
Kapazitätsschwund sogar sehr beträchtlich sein, ganz besonders aber dann, wenn nur
mit kleineren Teilvolumenströmen betrieben wird, bei weichem dann schon die Minimumleistung
des Brenners - sie ist ja eine konstante Größe - schon einen großen Teil der Kapazität
für brennbare Substanz aufzehrt.
[0013] Die herkömmliche Technik benutzt deshalb - um den Grad der Vorheizung der Abluft
zu senken - das Prinzip der einseitigen oder beidseitigen Umfahrung der meist rekuperativen
Wärmeaustauscher mit jeweils Teilmengen der Abluftvolumenströme, also die By-pass-Technik.
[0014] Dieses Teilumfahren des Wärmetauschers benötigt integrierte oder extern liegende
Kanäle oder Rohrleitungen, regelungs- und wärmetaugliche Ventil- und Klappentechnik,
Kompensationselemente für Wärmedehnungen und geeignete Mischtechniken für die Wiedereinmischung
mit den Hauptluftströmen nach Durchfahrung und Umfahrung des Wärmetauschers. Hinzu
kommt ein erhöhter Bedarf an Isolierungen.
[0015] Umfahrungs- oder By-pass-Techniken bei Nachverbrennungsvorrichtungen haben bei einseitiger
Umfahrung (heiße Seite oder kalte Seite) stets die Eigenschaft, daß die Masse des
Wärmetauschers - bedingt durch das Regeln des By-pass - immerwährend ein neues Wärmegleichgewicht
finden muß; mit anderen Worten: die Masse des Wärmetauschers wird in ihrem Temperatur-Niveau
hin- und hergefahren. Wird bei einem Wärmetauscher auf der Heißgasseite teilumfahren,
hat dies zur Konsequenz, daß die Veränderung der Vorheiztemperatur nur über die Veränderung
des Wärmegleichgewichts der gesamten Masse des Wärmetauschers vollzogen werden kann,
d.h., nur mittels eines sehr trägen Prozesses. Letzteres ist demnach als Spontan-Regelorgan
nicht geeignet und deshalb seltener.
[0016] Wird allein auf der Kaltgasseite teilumfahren, dann ist die Regelgeschwindigkeit
zwar spontan zu nennen, aber mit abnehmendem Volumenstrom im Wärmeaustauscher wird
die dort noch strömende verringerte Luftmenge höher vorgeheizt, und zwar umso höher,
je größer die By-pass-Entnahme ist. Diese Eigenschaft hat mitunter einen extremen
Vorabbrand der brennbaren Substanz im Wärmetauscher zur Folge. Sie macht diesen für
die Verbrennung der oxidierbaren Substanzen meist nicht geeigneten Wärmetauscher zu
einer Brennkammerstufe und dies verbunden mit allen negativen Auswirkungen.
[0017] Hinzu kommt noch der generelle Anstieg des Temperatur-Niveaus dieses Austauschers,
ein Prozeß, der aufgrund seiner meist großen Masse langsam abläuft.
[0018] Obwohl als Lösung der einseitigen Umfahrung des Wärmetauschers im Sinne der Praktikabil
ität nur die Kaltumfahrung in Frage kommt, so hat diese doch weitere wichtige Beschränkungen
und negative Folgen: sie zwingt zu einer sehr guten Einmischung des kalten, nicht
torgeheizten By-pass-Volumenstroms in und mit der vorgeheizten sehr heißen Luft. Dieser
Zwang ist dadurch begründet, daß Temperaturunterschiede in den Brennkammer-Strömungs-Querschnitten
von 15 K schon unzureichenden Ausbrand und hohe CO-Werte bedeuten können. Daraus resultiert,
der Zwang zum Anheben der Temperatur dieses Brennraumes um ebenso 15 K. Im gehobenen
Temperaturbereich moderner Anlagen mit kleiner Brenner-Grundlast und den sehr hohen
Endreinheitspflichten bedeuten aber weitere 15 K u.U. schon eine größere technologische
Pflicht.
[0019] Die hohen Anforderungen an den Ausbrand bei Vermeidung höherer Werte für CO und NOx
zwingen zu guter Mischtechnik und Brennraumtechnik. Die Forderung nach spontaner Anpassung
der Verbrennungstechnik an die immer schneller werdenden und schneller reagierenden
Produktionsprozesse, die Sicherheitsanforderungen und der Wunsch nach großer Verfügbarkeit
und Lebensdauer lassen bei herkömmlicher Technologie oft nur solche Energieregelungssysteme
zu, die aus der beidseitigen Umfahrung des Wärmeaustauschers bestehen. Im Vergleich
zur einseitigen (Kalt-)Umfahrung gleichen beidseitige By-pass-Systeme auch ungleich
größerer Unterschiede von Konzentrationen oxidierender Substanz aus. Wenn es also
um große Kapazitätsschwankungen und höhere Qualitätsanforderungen an die Verfahrenstechnik
geht, dann kommen bei solider Technik oft nur beidseitige Umfahrungen in Frage. Dies
hat besonders dort Gültigkeit, wo die brennbare Substanz eine niedrige Zündtemperatur
hat, z. B. bei den mineralischen Ölen und den Benzinen. Die allein aus einer Kaltumfahrung
resultierende zusätzliche Temperaturerhöhung des Wärmeaustauschers könnte unzulässige
Folgen für die CO-Generierung im Wärmeaustauscher haben und ebensolche Folgen auch
für die Stähle; denn es ist gemeinhin bekannt, daß CO ein Kohlenstofflieferant ist
und zur Versprödung der Stähle im höheren Temperaturbereich, aber auch zur rascheren
Abzunderung führen kann.
[0020] Eine hohe CO-Generierung ist tunlichst zu vermeiden. Hohe CO-Produktion ist aber
mit der By-pass-Technik geradezu verknüpft: Je höher die Konzentration der brennbaren
Substanz, je länger die Verweildauer im Wärmeaustauscher, desto höher die CO-Generierung.
Der By-pass-Betrieb ist dabei weiterer Verstärker dieser Zusammenhänge.
[0021] By,-pass-Techniken sind in aller Regel technisch aufwendig, teuer und verlangen ein
hohes Maß an Regelung und Überwachung. So müssen bei beidseitiger Umfahrung des Wärmeaustauschers
die Volumenströme in jedem Regelmoment möglichst gleichgroß sein und die Regelorgane
müssen stets parallel fahren.
[0022] Die By-pass-Systeme sind auch aufwendig in der Konstruktion, in der Detaiitechnik,
in der Montage und Inbetriebnahme. Im Betrieb benötigen sie einen erhöhten Serviceaufwand.
[0023] Aufgabe der vorliegenden Erfindung ist es, das Verfahren der eingangs beschriebenen
Art so auszubilden, daß eine fortwährende Einstellung der Wärmeleistung des Brenners
in Folge von Konzentrationsschwankungen der oxidierbaren Bestandteile im Prozeß-Abgas
nicht erfolgen muß, so daß insbesondere Temperaturspitzen vermieden werden, wobei
gleichzeitig sichergestellt sein soll, daß ein übliche Werte übersteigender Anstieg
der Störstoffkonzentration des der Verbrennungsvorrichtung zuzuleitenden Prozeß-Abgases
problemlos bewältigt werden kann, und daß insbesondere Material-Belastungen und Ermüdungen
durch hohe Temperaturwechselgeschwindigkeiten unterbleiben.
[0024] Diese Aufgabe wird gemäß der Erfindung verfahrensmäßig dadurch gelöst, daß die Konzentration
der in der Brennkammer oxidierbaren Bestandteile auf einem einstellbaren Wert gehalten
wird und daß die Eintrittstemperatur des der Nachverbrennungsvorrichtung zuzuführenden
aus zu reinigendem Prozeß-Abgas, gereinigtem Prozeß- Abgas und Frischluft bestehenden
Gasgemischs auf einem einstellbaren Wert gehalten wird. Mit anderen Worten wird bei
steigender Konzentration brennbarer Substanz ab jenem Moment, an dem der Brenner in
seinem Regelminimum (seiner Grundlast) angelangt ist, in geregeltem Umfang und in
der Menge zunehmend mit dem Anwachsen der Konzentration brennbarer Substanz, gereinigtes
Prozeßabgas zusammen mit Frischluft zugemischt. Die Zumischung erfolgt jederzeit in
eben dieser Menge, wie sie zur Aufrechterhaltung der Temperatur in der Brennkammer
gemäß deren Sollwert erforderlich wird. Der Brenner selbst bleibt während des Zumischbetriebs
im Regelminimum stehen, und greift nicht länger in das Geschehen ein. Die Herstellung
der Mischluft-Temperatur obliegt einen zweiten Regelkreis, durch welchen entschieden
wird, ob mehr oder weniger warmes gereinigtes Abgas oder kalte Frischluft beigemischt
werden. Das Maß für diese Regelaufgabe ist die jeweilige Abweichung der Abgas-Isttemperatur
von ihrer Solltemperatur. D.h. zusätzlich wird die Eintrittstemperatur des der Nachverbrennungsvorrichtung
zuzuführenden aus zu reinigendem Prozeß-Abgas, gereinigtem Prozeß-Abgas und Frischluft
bestehenden Gasgemischs auf einen einstellbaren Wert gehalten. Erfindungsgemäß wird
also vorgeschlagen, daß dem an brennbarer Substanz zu reichen Prozeß-Abgas vor Eintritt
in die Nachverbrennungsvorrichtung und vor deren Wärmeaustauscher eine angemessene
Menge Luftgemisch aus mehr oder weniger bereits gereinigter Abluft und weniger oder
mehr Frischluft beigemischt wird, und zwar in gerade derjenigen Menge, die nötig ist,
um bei Regelungs-Minimum des Brenner durch einen Verdünnungsbetrieb die Brennraumtemperatur
konstant zu halten. D.h., bei konstant im Minimum fahrendem Brenner wird so die Brennkammertemperatur
exakt konstant geregelt und gleichzeitig die Konzentration der brennbaren Substanz
im Abgas ebenfalls nahezu konstant gefahren.
[0025] Hierdurch ergeben sich u.a. Vorteile, die sich dadurch auszeichnen, daß die Brennraumtemperatur
stets auf der Sollhöhe ausgeregelt wird und unter gleichen Bedingungen auch nicht
überschwingen kann, daß der Wärmetauscher stets ein gleiches Temperatur-Niveau behält,
ungeachtet der Störstoffekonzentration und des Grades der Überflußenergieregelung,
daß die Verweildauer des aufzuheizenden Mediums im Wärmetauscher mit zunehmender Energie-Regelung
nicht zunimmt sondern abnimmt, daß die CO-Generierung dann nicht zunimmt, sondern
eher abnimmt, daß der Wärmeaustauscher nicht in verstärktem Umfang zur Vorverbrennzone
wird, sondern eher weniger, daß die Vorwärmtemperatur nicht fluktuiert, sondern konstant
bleibt, daß Temperaturgleichgewichte konstant bleiben, daß weitere Vorteile mit dieser
Technik verbunden seien, wie ein bei konstant warmer Temperatur ablaufender Stillstands-
oder Warmhaltebetrieb, ein verbilligtes Anfahren des gesamten Systems, ein kürzeres
Anfahren des gesamten Systems, ein Verlängern der Lebensdauer des Geräts durch Abbau
nahezu aller größeren Temperaturspitzen und -oberwellen, ein Abbau der Kohlenstoffdiffusion
in die Stähle durch Senken der CO-Pegel und damit der längere Erhalt der Eigenschaften
dieser Stähle, das Vermeiden von Umschaftschocks durch Schalten von Prozeßluft und
Kaftluft, superschnelles Reagieren auf prozessuale Veränderungen so wie es auch der
Brenner kann (oder gar schneller), ein niedrigeres CO-Niveau durch geringere Selbstgenerierung,
ein niedrigeres NOx-Niveau durch die Vermeidung einer angehobenen Brennraumtemperatur
sowie das Gegensteuern gegen eine zu hohe Ablufttemperatur, wenn die Konzentration
an brennbare Substanz ohnehin schon zu hoch ist für den Brennerregelbetrieb.
[0026] Erfindungsgemäß wird die Konzentration der oxiderbaren Bestandteile nach Erreichen
des Brennerminimums stets gleichbleibend so eingeregelt, daß die aus der Verbrennung
der oxidierbaren Bestandteile freiwerdende Wärmemenge die Brennraum-Temperatur exakt
auf Soll-Niveau hält, sie also nicht fallen oder steigen läßt.
[0027] Auch die folgende Eigenschaft ist mit der erfindungsgemäßen Lösung verbunden: die
Konstanz der Austrittstemperatur des gereinigten und wieder abgekühlten Abgases aus
der Nachverbrennungsvorrichtung. Während konventionelle By-pass-Anlagen Schwankungen
von bis zu 150 K (= 270°F) verursachen, läuft bei dem erfindungsgemäßen Verfahren
der Regelvorgang bei fast konstanter Temperatur ab. Diese Konstanz hat nicht nur die
bereits gemachten positiven Auswirkungen auf die Vorrichtung selbst, sondern auch
auf alle nachfolgende Gerätschaft: alle nachfolgende Technik ist allein für das niedrige
Standard-Temperatur-Niveau auszulegen und anzufertigen. Dies gilt bis hin zum Kamin.
[0028] Eine zukunftsweisende und wesentliche Eigenschaft des Systems ist seine gefahrlose
Eignung für den Einsatz höchstvorheizender Wärmeaustauscher. Wo konventionelle, By-pass
ausgestattet Anlagen mit der Vorheizung wegen des CO-Problems schon Schluß machen
müssen - genannt und in der Literatur nachweisbar sind max. 550°C (1022°F) - da ist
das erfindungsgemäße System lange noch nicht am Ende: die Vorheizung kann bis 650°C
(1202°F) betrieben werden, und erwähntermaßen fast schwankungsfrei.
[0029] Das Maß für die Zumischung von Luft zur ungereinigten Prozeßluft ist dann die Überschußmenge
an brennbarer Substanz oberhalb der bei Brennergrundlast maximal möglichen Kapazität.
[0030] Eine weitere Größe definiert im Zudosierbetrieb die Mischung aus mehr oder aus weniger
Warmluft und Kaltluft: die Höhe der Prozeßluft-Temperatur. Ist diese Temperatur auch
noch oberhalb der nominalen Größe, dann wird bei Anforderung von Mischluft zunächst
erst frische Luft und erst nach Erreichen der nominalen Temperatur auch Warmluft hinzufließen.
[0031] Ist jedoch die Temperatur unakzeptabel niedrig, so wird zunächst bei Bedarf auch
nur Warmluft fließen. D.h., das System erhält zu jeder Zeit und an jeder Stelle das
normale Temperatur-Niveau, a) für das Medium, b) für die Vorrichtung. Dahingegen sind
By-pass-Anlagen gewaltigen Schwankungen unterworfen. Bei dem erfindungsgemäßen Verfahren
entfällt folglich ein 'Hin- und Herzerren' der Bauelemente. Alles ist warm und bleibt
warm oder ist heiß und bleibt heiß. Der Betrieb nähert sich dem Idealbetrieb und erreicht
ihn: den völligen Konstantlauf aller Glieder über Lange Zeit.
[0032] Zum anderen wird ein Teil der oben spezifizierten Eigenschaften auch dadurch erreicht,
daß beim Ausfall des Prozeßluftstromes (prozeßbedingt und störungsbedingt) eine kleine
Menge ebenso gemischtes und auf die normale Prozeßluft-Temperatur geregelter Warmluft
den Betrieb in sparsamster Weise fortgesetzt, und dadurch die völlige Gleichheit der
Größenordnungen aller Temperaturen mit dem normalen Prozeß-Betrieb an einer jeden
Stelle der Anlage aufrechterhält und sie für den späteren Weiterbetrieb mit Prozeß-Abgas
sicherstellt.
[0033] Eine Vorrichtung nach dem Oberbegriff des Anspruchs 4 zeichnet sich dadurch aus,
daß zwischen der Vorrichtung und der Gaszuführung eine Verbindung besteht, über die
im gewünschten Umfang innerhalb der Vorrichtung gereinigtes Prozeß-Abgas im Kreislauf
führbar ist, daß die Regulierung der Temperatur des dem zu reinigenden Prozeß-Abgas
zuzumischenden gereinigten Prozeß-Abgases bzw. der Frischluft über Regelorgane wie
Klappen erfolgt, deren Regelgröße von der Temperatur bestimmbar ist, die das aus zu
reinigendem Abgas und gereinigtem Abgas und/oder Frischluft bestehende Gasgemisch
an der Druckseite des Gebläses aufweist, und daß die Wärmetauscherrohre an ihren kalten
Enden nach außen abgebogen und von gereinigtem Prozeß-Abgas umströmbar sind. Dabei
verläuft die Verbindung vorzugsweise zwischen dem Prozeß-Abgas-Auslaß und der Zuführung.
Hierdurch ist die Möglichkeit gegeben, mit konstruktiv einfachen Mitteln, ohne daß
diese innerhalb der Vorrichtung verlaufen und dort z. B. Klappenmechanismen aufweisen,
dem zu reinigenden Prozeß-Abgas im erforderlichen Umfang gereinigtes Prozeß-Abgas
und/oder Luft zuzuführen, um den Anteil der oxidierbaren Bestandteile auf einem konstanten
Wert zu hatten und das Prozeßgas in seiner Temperatur zu korrigieren.
[0034] Demnach werden Verbrennungs-Vorrichtungen so ausgebildet, daß zwischen dem Prozeß-Abgas-Auslaß
und der Prozeß-Abgäs-Zuführung eine Verbindung hergestellt wird, die es erlaubt, im
gewünschten Umfang gereinigtes Abgas im Kreislauf- oder Rückführbetrieb zu führen,
stets mit gleicher, mehr oder auch weniger Frischluft vermengt.
[0035] Die Zumischung der so erzeugten Mischluft mit dem Prozeß-Abgas erfolgt nahe der Saugseite
des Prozeß- Abgas-Gebläses.
[0036] Die Rückführung von Warmluft geschieht extern und mit konstruktiv einfachen Mitteln.
Die Dosierung der Warmluft und der Kaltluft übernehmen je ein selbständiges Regel-Organ,
d.h. Klappen oder Ventile.
[0037] Die Bestimmung der jeweiligen Warm- und Kaftluftmenge übernimmt ein Temperatur-Regler,
der die Temperatur der zur Nachverbrennungs-Vorrichtung geförderten Prozeß-Mischluft
überwacht.
[0038] Die Bestimmung der insgesamt zu fördernden Luftmenge bestimmt der Temperatur-Regler,
der für die Konstanz der Brennraumtemperatur verantwortlich ist.
[0039] Weitere Einzelheiten, Vorteile und Merkmale der Erfindung ergeben sich nicht nur
aus den Ansprüchen, den diesen zu entnehmenden Merkmalen - für sich und/oder in Kombination
-, sondern auch aus der nachfolgenden Beschreibung eines in der Zeichnung dargestellten
bevorzugten Ausführungsbeispiels. Es zeigen:
Fig. 1 eine Prinzipdarstellung eines Nachverbrennungs-Prozesses von Prozeß-Abgas enthaltend
oxidierbare Bestandteile mit 'By-pässen' zum Zwecke der Energieregelung,
Fig. 2 einen erfindungsgemäß ablaufenden Prozeß und
Fig. 3 eine den erfindungsgemäßen Prozeß realisierende Nachverbrennungs-Vorrichtung.
[0040] Anhand der Fig. 1 soll eine konventionelle Energieüberschußregelung verdeutlicht
werden wobei die wesentlichen Elemente der Nachverbrennungsvorrichtung (10) rein schematisch
dargestellt sind. Das zu reinigende Prozeßgas wird über ein Gebläse (12) und die Prozeßgas-
oder Prozeß-Abgas- oder Trägergas-Zuführung (14) zur Nachverbrennungsvorrichtung gebracht.
Sodann durchströmt das zu reinigende Prozeßgas einen Wärmetauscher (16), um in einen
Brennraum (18) zu gelangen, in dem die oxidierbaren Bestandteile verbrannt werden,
soweit sie nicht schon im Wärmetauscherteil verbrannt sind. Der Brennraum (18) kann
über ein nicht dargestelltes Hochgeschwindigkeitsrohr von einem Brenner (20) ausgehen,
dessen Brennstoffzufuhr über ein Regelventil (22) einstellbar ist. Vom Brennraum (18)
gelangt das gereingte Abgas erneut über den Wärmetauscher (16), um in diesem das noch
zu reinigende Prozeßgas rekupera- t
iv vorzuwärmen.
[0041] Anschließend wird das gereinigte Abgas über eine Leitung (24) abgeführt. Sofern größere
Schwankungen im Prozeßgas hinsichtlich der Konzentration der zu oxiderenden Bestandteile
- also in der Leitung (14) - auftreten, sind By-pässe (26) und (28) vorgesehen, die
dem Anstieg der Temperatur in der Brennkammer (18) so entgegenwirken, daß sie durch
teilweises Umfahren des Wärmetauschers (16) das Niveau der Vorheizung soweit absenken,
wie die Zunahme (Schwankung) der Konzentration brennbarer Substanz es erfordert. Der
Brenner (22) feuert dabei solange in seinem Regelungs-Minimum, als die übergroße Zufuhr
brennbarer Substanz anhält.
[0042] In diesem Prozeß ist die By-pass-Regelung (26) als eine Verbindung für Kaltgase und
die By-pass-Regelung (28) für Heißgase ausgelegt. Jede By-pass-Regelung (26) bzw.
(28) weist eine in/oder um die Vorrichtung (10) verlaufende Leitung (30) bzw. (32)
auf, die Regelmechanismen wie Ventile (34.1) bzw. (36.1) haben, um so im gewünschten
Umfang den By-pass modulierend zu fahren oder außer Betrieb zu setzen. Dabei stellt
die By-pass-Anordnung (26) zwischen dem in der Leitung (14) strömenden kalten Prozeßgas
und dem Brennervorraum - in der schematischen Darstellung mündet die Leitung in den
Brennraum 18) - her. Die By-pass-Anordnung (28) stellte eine Verbindung zwischen dem
Brennraum (18) und dem Abgasauslaß (24) her. Da ein By-pass nur solange seine Fördermenge
anheben kann, als die im Wärmetauscher fließende Restmenge größeren Fließwiderstand
erfährt als die im By-pass strömende Menge, ist die Regeffähigkeit schnell erschöpft,
wenn nicht ein zweites Regelorgan die Hauptseite abdrosselt und so die By-pass-Förderung
kontinuierlich steigert. Diese Organe sind mit (34.2) und (36.2) bezeichnet.
[0043] Die der Vorrichtung (10) nachgeschalteten Einrichtungen zur Verwertung von Restwärme
in der gereinigten Abluft sind in Fig. 1 in Form von einem Warmwasser-/Luft-Wärmetauscher
gezeigt. Die Einrichtung umfaßt einen Wärmetauscher (65), das durch Klappen (63.1)
und (63.2) dargestellte By-pass-Regelorgan zum Vergrößern oder Verringern der zu wechselnden
Wärme, der By-pass-Leitung (62) und der Wiedervereinigungs-Leitung (64), und aus dem
Wasser-Kreislauf (61) mit seinen Verbrauchern (67) und seiner Kreislaufpumpe (66).
[0044] Nach Verlassen des Wärmeaustauschers (65) oder teilweisen bis vollständigem Umfahren
desselben strömt die weiter abgekühlte Abluftmenge dem Raum (68) zu.
[0045] Alle Elemente der Vorrichtung (10) müssen wie auch die Abgas-Leitung (33) für die
maximale Temperatur ausgelegt sein, die erzeugt werden kann.
[0046] Das erfindungsgemäße Verfahren zum kontrollierten Nachverbrennen von oxidierbaren
Bestandteilen im Prozeß-Abgas (Abluft, Trägergas) ist der Fig. 2 zu entnehmen. Dabei
sind Elemente, die denen der Fig. 1 entsprechen, mit gleichen Bezugszeichen versehen.
[0047] Das zu reinigende Prozeßgas wird über eine Zuführleitung (14), in der ein Prozeßabgasgebläse
(38) mit Volumenstromregelung (hier als Drehzahl-Veränderung gezeigt) angeordnet ist,
dem Wärmetauscher (16) und anschließend dem Brennraum (18) zugeführt. Es wird das
zu reinigende Prozeßgas nach dessen Vorwärmung im Wärmetauscher (16) in den unmittelbaren
Bereich des Brenners (20) geleitet, um von dort über ein hier nicht dargestelltes
Hochgeschwindigkeitsrohr in den eigentlichen Hauptbrennraum (18) zu gelangen. Der
Brenner (20) wird mittels eines Regelventils (22) mit der in jedem Augenblick erforderlichen
Menge Brennstoffs versorgt. Nach dem Brennraum (18) gelangt das jetzt gereinigte Abgas
über die Heißgas-Seite des Wärmetauschers (16) zum Auslaß (24). Sollte die Konzentration
der zu reinigenden Abgase über das Regelvermögen des Brenners hinaus ansteigen, wird
erfindungsgemäß vorgeschlagen, daß durch Beimischung von bereits gereinigtem Abgas,
vermengt mit Frischluft, eine Korrektur der Konzentration so vorgenommen wird, daß
in die Vorrichtung (10) nur ein solches Abgas geführt wird, dessen Anteil an oxidierbarer
Substanz (wie z. B. Lösungsmitteln) gleichbleibend hoch ist. Hierdurch ist gewährleistet,
daß der Brenner (20) mit stets gleichbleibendem Regelungs-Minimum (-Grundlast) gefahren
werden kann. Da der spezifische Anteil der zu verbrennenden Substanz nun gleich bleibt,
ist die Konstanz der Temperaturen innerhalb der Vorrichtung (10) gewährleistet, wodurch
deren Bau-Elemente, insbesondere auch die Rohre des Wärmetauschers (16) keinen Dehnungsschwankungen
und Spannungsschwankungen unterworfen werden. Hierdurch wird die Lebensdauer des Wärmetauschers
verlängert.
[0048] Die Regelung erfolgt dabei erwähntermaßen in Abhängigkeit der über ein Thermoelement
(49) im Brennraum ermittelten Temperatur (Ist-Temperatur), die in einem Temperaturregler
(49.1) mit einer Solltemperatur verglichen wird. In Abhängigkeit von der Abweichung
zwischen Ist- und Solltemperatur wird zunächst über das Ventil (22) die Brennstoffzufuhr
so geregelt, daß der Brenner (20) auf Minimum-Last fährt. Dies wird durch einen Minimum-Schalter
(22.1) angezeigt. Anschließend erfolgt eine Beeinflussung von Stellorganen (46.1)
und (46.2) für das Beimischen von Frischluft und/oder gereinigtem Prozeß-Abgas zu
dem zu reinigenden in der Leitung (14) geführten Prozeß-Abgas, um die Temperatur im
Brennraum (18) auf dem Sollwert zu haften.
[0049] Der Abgriff der gereinigten und im Wärmeaustauscher (16) abgekühlten Abluft erfolgt
am Abgasauslaß (24) -verdeutlicht durch den Verbindungspunkt (42), von wo aus sie
in der Leitung (44) zur Vereinigungsstelle (47) fließt, welche Mischeigenschaften
haben kann. Die jeweils benötigte oder angeforderte Menge gereinigte Luft wird mittels
einer Regelklappe (46.1) bereitgestellt. Die adäquate Frischluftmenge fließt über
das Regelorgang wie Regelklappe (46.2) an die Mischstelle (47). Die Ansaugung beider
Mengen - jetzt als Mischluftmenge - geschieht durch Unterdruck in der Leitung (48).
Die Leitung (48) mündet in die Prozeß-Abluft-Leitung (14), in welcher dieser Unterdruck
oder Saugdruck konstant erhalten wird.
[0050] Das Gemisch aus Prozeßabluft und beigemengter Luft wird dann vom Gebläse (38) über
die Leitung (14.1) dem Wärmetauscher (16) zugefördert.
[0051] Die Vorheizung verändert sich nicht, auch nicht die Brennraumtemperatur. Der Brenner
brennt im Regelungs-Minimum, denn die Verantwortung für die völlige Konstanz hat sofort
mit Erreichen des Regelungs-Minimum des Brenners die hier beschriebene Regelung übernommen
und behält auch diese Verantwortung, bis die Menge brennbarer Substanz im Abgas wieder
soweit abfällt, daß der Zudosierbetrieb beendet und der Brenner die Regelungs-Aufgabe
wieder übernehmen kann.
[0052] Es ist nun ausreichend dargestellt worden, daß - und wie - überhöhte Konzentrationen
an brennbarer Substanz auf eine niedrigere spezifische Größe gedrückt werden, und
wie sie dort gehalten werden. Und es wurde erklärt, warum der Brenner dann mit Minimum-Flamme
brennt. Im folgenden soll noch erklärt werden, welche Rolle die Temperaturregelung
erfindungsgemäß spielt:
Die Praxis zeigt, daß meist gleichzeitig mit dem Eintreten höherer Konzentrationen
brennbarer Substanz auch die Temperatur der Prozeß-Abluft ansteigt. Oft ist die höhere
Prozeß-Temperatur die Voraussetzung für das Freiwerden der Substanzen, wie z. B. von
Lösemitteln aus Farben und Lacken.
[0053] Nun ist die Wirkung höherer Temperatur des Prozeß-Abgases auch die Anhebung der Vorheiztemperatur.
D. h., durch die höhere Vorheizung der Luft wird die Temperatur-Differenz zwischen
konstant hoher VerbrennungsTemperatur im Brennraum und der Vorheiztemperatur der Luft
kleiner. Da aber der Brenner - selbst wenn er sich auf sein Regelungs-Minimum zurückzieht
- davon einen bestimmten Anteil für sich beansprucht, bleibt für den thermischen Umsatz
der oxidierbaren Substanz der Prozeß-Abluft immer weniger übrig. Je höher also die
ProzeBluft-Temperatur ansteigt, umso höher wird die Vorheizung im Wärmeaustauscher,
und umso geringer wird die akzeptierbare Konzentration an oxidierbarer Substanz der
Ablauft (diese verhält sich wie eine zweite Brennstoffquelle, und ist auch eine solche).
[0054] Die erfindungsgemäße Vorrichtung wirkt mit ihrer Temperaturregelung diesem Verhalten
entgegen:
Erreicht eine Anlage ihre "erste Kapazitätsgrenze" durch die Brenner-Minimum-Stellung,
dann entscheidet die Regelung anhand der nach Gebläse (38) mittels Thermoelement (15)
gemessenen und mit einem Sollwert am Temperaturregler (15.1) verglichenen Wert, ob
zuerst mehr oder weniger kalte Luft zugegeben werden muß und ab wann Warmluft gleichlaufend
mit hinzugezogen wird. Auf diese Weise wird auch die Temperatur der Vorheizung auf
die Normalhöhe zurückgeführt und die Verarbeitungskapazität für die brennbare Substanz
wird erhöht. Die Gesamtanlage kehrt so auch in den Bereich ihrer spezifischen Parameter
zurück.
[0055] Geschieht aber der seltenere Fall, daß die Konzentration oxidierbarer Substanz zusammen
mit einer niedrigeren als der gewünschten Ablufttemperatur verbunden ist, dann korrigiert
das die Regelung selbsttätig durch die Anhebung der Abgastemperatur mittels vorzugsweisen
Zuführens von heißer Luft. Hierdurch wird auch Kondensatbildung in der Rohrleitung
und im Eintrittsbereich der Verbrennungsvorrichtung vermieden. D.h. dann, wenn die
Kondensatgefahr besonders hoch ist, nämlich bei hohen Konzentrationen kondensierfähiger
Anteile und bei niedriger Temperatur, reagiert die beschriebene Regelung gegen die
Tendenz der Kondensation.
[0056] Alle Betriebsfälle, die üblicherweise mit kalter Luft ablaufen, laufen erfindungsgemäß
im Warm-Betrieb ab. Gemeint sind das Warmhaften im Unterbrechungsfalle und das An-
oder Warmfahren der noch kalten Anlage.
[0057] Der zuerst genannte Fall stellt einen Sparbetrieb mit einem sehr kleinen Warmluft-Volumenstrom
dar. Die Warmlufttemperatur entspricht exakt der nominalen Prozeßgastemperatur. Der
Temperaturregler (15.1) stellt die Gemischtemperatur exakt her.
[0058] Infolge des warmen Unterbrechungsbetriebs halten alle Teile der Nachverbrennungsvorrichtung
ihr gewohntes Temperaturniveau. Der Anfahrbetrieb mittels warmer Luft erlaubt ein
schnelleres und sparsameres Anfahren als mit Kaftluft. Es werden außerdem die Bereiche
zwischen dem Gebläse (38) bis hin zum Wärmeaustauscher (16) sukzessiv auf höhere Temperaturen
gebracht, bis die Betriebsbereitschaft der Anlage auf einem Niveau erreicht ist, bei
dem bei Umschaltung auf Prozeßbedingungen die Kondensatgefahr in den gefährdeten Bereichen
ausgeschaltet ist.
[0059] Die großtechnische Erprobung des Verfahrens hat eine Reihe von weiteren Eigenschaften
gezeigt, die nicht vorhersehbar waren und deshalb besonders positiv überraschen. Im
einzelnen sind das:
a) Durch den warmen Unterbrechungsbetrieb herrschen auch bei kleinsten Volumenströmen
noch deutlich bessere thermodynamische Verhältnisse in der gesamten Nachverbrennungsvorrichtung,
so daß der zum Unterbrechungsbetrieb erforderliche Mindestluftstrom um bis zu 35 %
gesenkt werden konnte. Entsprechend konnten die Kosten für den Unterbrechungsbetrieb
gesenkt werden. Hinzu kommen die Kostensenkungen durch Warmluftbetrieb generell, die
dieser Betriebsweise innewohnen.
b) Das Verfahren regelt in Sekundenschnelle und ist somit der Brennerregelung mindestens
ebenbürtig, aber übertrifft die By-pass-Systeme bei weitem. Es gestattet jetzt auch
den Einsatz superschneller Thermoelemente.
c) Im Unterbrechungs- bzw. Warmhaftebetrieb bleibt jetzt die Temperatur auch am Austritt
der Nachverbrennungsvorrichtung konstant. Das hat nicht nur die bekannten positiven
Folgen für die nachfolgende Peripherie (wie für Warmwasser-Wärmetauscher), sondern
weitere: solche mit sog. 'kalten Flächen' fahrende Wärmeaustauscher werden bei Kaltluft-Betrieb
der Verbrennungsvorrichtung stark abgekühlt und gelangen so in die Kondensationszone.
Um dies zu vermeiden, darf die Wärmerückgewinnung nicht zu weit getrieben werden.
Erfindungsgemäß wird dies vermieden. Die Wärmerückgewinnung kann deutlich und ohne
Gefahr gesteigert werden. Der Gesamtprozeß wird wirtschaftlicher.
d) Druckschwankungen, hervorgerufen durch das Arbeiten von nachgeschalteter Verfahrenstechnik
wirken sich nicht auf die Menge der Warmluftrückführung aus, da die Temperaturregelung
Priorität hat.
e) Durch die Ausschaltung jeglicher Kondensatgefahr im Bereich des Eintritts der Nachverbrennungsvorrichtung
wird eine Brandgefahr grundsätzlich ausgeschaltet.
f) Neueste Produktionstechniken beinhalten heute auch schon Schnellreinigungs-Systeme,
wie z.B. der Rotations-Offsetdruck. In Sekundenschnelle und für kurze Zeit nur werden
hier große Mengen von Lösemitteln in den Abgasstrom eingebracht. Die Konzentration
brennbarer Substanz steigt dann plötzlich und stark an. Das erfindungsgemä-Be Verfahren
reagiert auf diese Spitzen sofort und schützt die Nachverbrennungs-Anlage vor Übertemperatur.
[0060] Die Fig. 3 zeigt in Prinzipdarstellung eine Nachverbrennungsvorrichtung, anhand der
die erfindungsgemäße Lehre realisierbar ist.
[0061] Die Nachverbrennungsvorrichtung (50), hier liegend dargestellt, umfaßt einen zylinderförmigen
Außenmantel
(52), der durch Stirnwände (54) und (56) begrenzt ist. Im Bereich der Stirnwand (56)
ist konzentrisch zur Achse
(58) des Mantels (52) ein Brenner (60) angeordnet, der in ein Hochgeschwindigkeitsmischrohr
(62) mündet, weiches wiederum zum Hauptbrennraum (64), der durch die äußere Stirnwand
(54) begrenzt wird, verbindet. Dabei ist es jedoch nicht notwendigerweise erforderlich,
daß - wie in der Zeichnung dargestellt - das Hochgeschwindigkeitsmischrohr (62) in
den Hauptbrennraum (64) hineinragt.
[0062] Konzentrisch zum Hochgeschwindigkeitsmischrohr (62) verläuft ein innenliegender Ringraum
(66), der in den Raum (68) übergeht, in welchen die Wärmetauscherrohre (70) konzentrisch
zur Längsachse (58) angeordnet sind. Die Wärmetauscherrohre (70) selbst münden in
einen äußeren an der Außenwandung (52) angrenzenden äußeren Ringraum (72), der in
den Einlaß (74) übergeht. Ferner ist eine Ringkammer (76) vorgesehen, die in den Auslaß
(78) übergeht.
[0063] Die Enden (80) der Wärmetauscher-Rohre (70) sind im Bereich zum Auslaß (78) nach
außen, also zur Wandung (52) hin umgebogen, um so nahezu senkrecht in die Wandung
(82) des äußeren Ringraums (72) zu münden. Die anderen Enden (84) der Wärmetauscherrohre
(70) münden in eine Rohrplatte (86), die einen den Brenner (60) umgebenden Vorbrennraum
(88) von dem Raum (68) trennt.
[0064] Der Brenner (60) ist mittels eines sich in Richtung des Hochgeschwindigkeitsrohres
(62) meist kegelförmig erweiternden Brennervorbaus (90) fortgesetzt, der auf der Umfangsfläche
Aussparungen wie Löcher (92) aufweist. Das Hochgeschwindigkeitsrohr (62) bildet an
seinem Anströmkonus (96) zusammen mit dem Brennervorbau (90) eine Coanda-Düse (im
Bereich (98) bis (94)). Diese bildet einen konzentrischen Ring um den Brenner herum
aus, wobei sie Teilarbeit bei der Ver- und Entsorgung des Brenners mit Luft leistet.
[0065] Ein Anschluß (100) oder der Auslaß (78) wird mit einer nicht dargestellten Mischvorrichtung
verbunden, die der in Fig. 2 gezeigten Mischvorrichtung (46) und (47) entspricht.
[0066] Das von der erfindungsgemäßen Vorrichtung nachzuverbrennende Prozeßgas wird über
den Einlaß (74) mit dem Ringraum (72) zugeleitet, um über die Wärmetauscherrohre (70),
den Brennervorbau (90), die Coanda-Düse (96), das Hochgeschwindigkeitsrohr (62) in
den Hauptbrennraum (64) geleitet zu werden. Sodann kann das gereinigte Abgas über
den Ringkanal (66) und den Raum (68), in dem die Wärmetauscherrohre (70) verlaufen,
an den Auslaß (78) abgegeben werden.
[0067] Damit der Brenner (60) im Regelungs-Minimum (Grundlast) arbeiten kann, obwohl die
Menge brennbarer Substanz ansteigt, wird über einen Anschluß (100) gereinigtes Abgas
an die in Fig. 2 mit (46) und (47) benannte Mischvorrichtung geführt, in welcher zum
Zweck der Erreichung einer gewünschten Mischtemperatur mehr oder weniger frische Luft
beigemengt wird. Das so entstehende Gemisch warmer Luft gelangt nach Fig. 2 über die
Leitung (48) zur Leitung (14), wo es mit dem ungereinigten Prozeßabgas steigender
oder gestiegener Störstoff-Konzentration zusammentrifft und mit diesem vermischt wird.
Mischluft wird in solchem Maße beigemischt, als es zur Konstanthaltung der Konzentration
brennbarer Substanz und zur Konstanthaltung der Brennkammer- temperatur erforderlich
ist, sowie auch zur Erreichung der erforderlichen oder gewünschten Temperatur vor
der Verbrennungsanlage.
[0068] Da nun die Konzentration gleichbleibend ist, erfolgen in den einzelnen Bereichen
der Anlage, insbesondere im Bereich der Wärmetauscherrohre (70) Temperaturschwankungen
grundsätzlich nicht mehr oder nur sehr gering, so daß auch größere kritische Dehnungsschwankungen
ausgeschlossen sind.
[0069] Auch alle negativen Einflüsse resultierend aus hohem Vorabbrand werden vermieden.
Da der Anschluß (100), dem gereinigtes Abgas zum Vermischen mit noch zu reinigendem
Prozeßgas entnommen wird, nicht innerhalb der Vorrichtung (10) liegt, ist demzufolge
die erfindungsgemäß vorgeschlagene Vermischung ohne konstruktiven Aufwand an der Vorrichtung
(10) möglich, um so die Konzentration der oxidierbaren Bestandteile auf Toleranzniveau
zu halten. Infolgedessen ist die erfindungsgemäße Vorrichtung (50) wartungsfreundlich
und sichert eine hohe Funktionszuvenässigkeit zu.
[0070] Anhand der nachstehenden Tabellen 1 bis 3 soll noch einmal verdeutlicht werden, daß
eine nach den erfindungsgemäßen Verfahren betriebene Nachverbrennungsvorrichtung selbstregulierend
optimale Bedingungen für die thermische Verbrennung und damit für die Vorrichtung
selbst schafft.
[0071] Die hier betrachtete thermische Nachverbrennungsanlage ist für maximal 15.000 m
3o/h ausgelegt und mit einem Wärmetauscherwirkungsgrad von 76 % ausgestattet. Die nominale
Abgastemperatur sei im Beispiel 160°C, effektiv weicht sie aber davon ab. Die Brennraumtemperatur
ist bei 760°C konstant zu fahren. Die vorgestellte Anlage ist mit einem Spezialbrenner
ausgerüstet, welcher seinen zur Verbrennung benötigten Sauerstoff aus dem Abgas entnimmt
(Sekundärluft-Brenner; Combustor-Brenner). Die Minimal-Leistung des Brenners (- unteres
Ende des Regelbereichs) beträgt 67,8 KWh/h.
[0072] Die Anlage wird aus verschiedenen Einzelquellen gespeist. Je nach Quelle und nach
Zahl der Quellen sind die Volumenströme unterschiedlich groß und es variieren die
Abgas-Temperatur und vor allem die Menge und Konzentration der brennbaren Substanzen
im Abgas. Die brennbaren Substanzen seien mineralische Öle. Drei verschiedene Betriebsbedingungen
werden untersucht. Die Ergebnisse sind tabellarisch dargestellt.
[0073] Abbildung 1:
Aufgabenstellung und Leistungsvermögen der Nachverbrennungs-Vorrichtung ohne Energieüberschuß-Regelung.
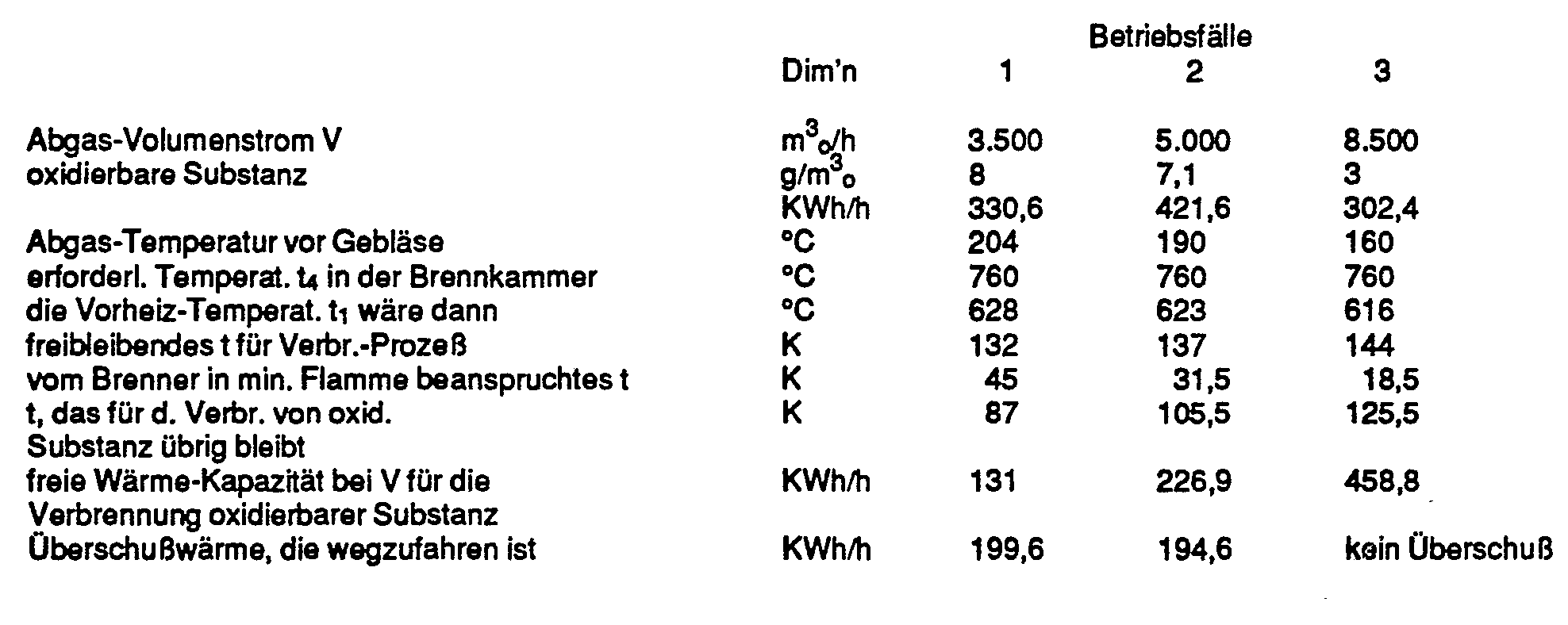
Kommentar: Bei den Betriebsfällen 1 und 2 besteht ein beträchtlicher Überschuß von
Wärme aus oxidierbarer Substanz, bezogen auf die obige Abgasmenge V. Das heißt, in
diesen beiden Fällen greift die erfindungsgemäße Regelung ein, nachdem der Brenner
am unteren Ende seines Regelbereichs (8O Regelungs-Minimum = Grundlast) angekommen
ist, und zwar bei dem Versuch, für die angewachsene Menge oxidierbarer Substanz Platz
zu machen. In beiden Fällen ist auch die nominale Abgastemperatur (hier 160°C) deutlich
überfahren, so daß das System korrigierend eingreift.
[0074] Beim Betriebsfall 3 ist die Konzentration der oxidierbaren Bestandteile im Abgas
geringer als es die Kapazität der Anlage mit diesem Volumenstrom zuließe. Deshalb
regelt der Brenner durch seinen modulierenden Durchsatz von Brennstoff die fehlende
Energiemenge exakt ein, ohne daß die erfindungsgemäße Regelung zum Einsatz kommen
muß.
[0075] Abbildung 2:
Bewältigung der Aufgabe durch das erfindungsgemäße System für die Betriebsfälle 1,
2 und 3 nach Abbildung 1.
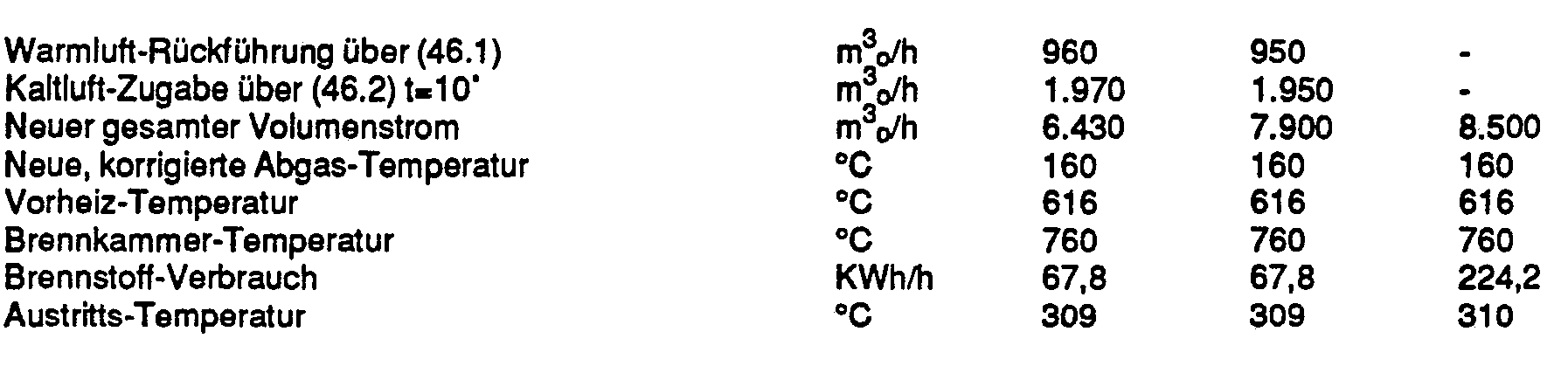
Würde die thermische Nachverbrennung mit einer aus dem Stand der Technik bekannten
By-pass-Anlage durchgeführt werden, so würden die Austrittstemperaturen für die Betriebsfälle
1, 2 und 3 442°C bzw. 399°C bzw. 310°C betragen.