[0001] La présente invention concerne des fils hybrides pour matériaux composites à matrice
thermoplastique, spécialement dans le cas où cette matrice est constituée de fibres
thermoplastiques ainsi que leur procédé d'obtention.
[0002] On sait que, dans les procédés actuels utilisés pour la fabrication de ces types
de matériaux composites, les fibres de renfort (carbone, aramide ou verre), qui se
trouvent généralement sous forme de multifilaments, sont tissées alternativement avec
des multifilaments de fibres matrices thermoplastiques.
[0003] Ces fibres matrices thermoplastiques appartiennent aux familles classiques : polyéther
éther éther cétone (PEEK), polysulfure de phénylène (PPS), polyétherimide (PEI), etc...
[0004] Cette technique de fabrication présente de multiples inconvénients parmi lesquels
on peut citer :
- une mauvaise mouillabilité,
- un taux de vide important,
- un délaminage des fibres de renfort.
[0005] Une autre technique consiste à entremêler le multifilament de fibres de renfort avec
le multifilament de fibre thermoplastique.
[0006] On constate alors une amélioration du résultat obtenu mais les problèmes exposés
ci-dessus ne sont pas complètement résolus. D'autre part, le coût de cette technique,
assez élevé, empêche pratiquement sa mise en oeuvre dans le cas de séries industrielles.
[0007] La présente invention s'est donné pour but de proposer des fils hybrides pour composites
à matrice thermoplastique permettant de maîtriser et de résoudre ces problèmes.
[0008] Les fils hybrides selon l'invention sont caractérisés en ce qu'ils sont constitués
d'un mélange intime de filés de fibres de renfort et de filés de fibres matrices thermoplastiques,
chacun des filés de fibres ayant été préalablement obtenu par craquage selon un étirage
lent et progressif de multifilaments.
[0009] Les filés de fibres de renfort sont choisis parmi les filés de fibres de carbone,
d'aramide ou de verre.
[0010] Les filés de fibres matrices thermoplastiques sont choisis parmi les filés de fibres
de polyéther éther cétone (PEEK), de polysulfure de phénylène (PPS), de polyéthersulfone
(PES), de polyétherimide (PEI), ainsi que parmi les autres filés de fibres connus
dans ce but, tels que les polyamides et les polyimides.
[0011] Selon un mode de réalisation préféré de l'invention, les proportions relatives des
fibres de renfort et des fibres matrices thermoplastiques, proportions qui peuvent,
bien entendu, varier en fonction des caractéristiques des fibres matrices et en particulier
de leur viscosité à chaud, se situent aux environs de 65 % pour les fibres de renfort
et de 35 % pour les fibres matrices thermoplastiques.
[0012] L'invention a également pour objet un procédé d'obtention des fils hybrides pour
matériaux composites selon l'invention.
[0013] Selon ce procédé, on soumet des multifilaments de fibres de renfort et des multifilaments
de fibres matrices thermoplastiques à un processus séparé de craquage par étirage
lent et progressif, puis on assemble les rubans de fibres discontinues ainsi obtenus
sur une machine d'étirage type intersecting, le ruban sortant de cette machine d'étirage
étant ensuite assemblé sur une seconde machine d'étirage avec d'autres rubans identiques,
cette opération étant répétée plusieurs fois de façon à réaliser le mélange le plus
intime possible, le ruban final obtenu étant ensuite soumis aux opérations classiques
de filature de fibres longues : passage sur banc à broches, filature proprement dite,
bobinage, assemblage et retordage.
[0014] Les filés ainsi obtenus sont aptes à être transformés par tissage, tricotage ou tressage
pour l'obtention de matériaux composites présentant de nombreux avantages par rapport
aux matériaux du même type obtenus selon les procédés de la technique antérieure.
[0015] Ces avantages sont les suivants :
- une très bonne mouillabilité des fibres de renfort,
- un très faible taux de vide,
- une drapabilité des surfaces textiles permettant le moulage des surfaces développables
ou non ;
- une très bonne isotropie du matériau dans la direction des fibres de renfort,
- une excellente résistance au délaminage. En fait, le matériau se présente comme
un solide monolithique qui a "oublié" sa structure initiale stratifiée.
[0016] Le composite obtenu présente, en outre, de très bonnes aptitutdes à l'estampage à
chaud.
[0017] Le procédé d'obtention des fils hybrides pour matériaux composites selon l'invention
va maintenant être décrit plus en détail en référence au dessin schématique annexé
qui l'illustre sans nullement le limiter. Dans ce dessin :
Figure 1 est un diagramme de longueurs des fibres ayant été soumises à l'opération
de craquage ;
Figure 2 est une vue très schématique de l'installation de craquage et,
Figure 3 est une vue très schématique de l'installation de mélange des fibres craquées
conduisant à l'obtention d'un ruban de filés de fibres hybrides selon l'invention.
[0018] Sur les figures, les fibres de renfort sont désignées de façon générale par
2 et les fibres de matrice thermoplastique par
3.
[0019] Sur l'installation de craquage représentée à la figure 2, les câbles de multifilaments
alimentés à partir des bobines
10 (qu'il s'agisse de multifilaments de fils de renfort ou de fils de matrice thermoplastique)
sont soumis à une opération de craquage par étirage et rupture contrôlée, les vitesses
des zones d'étirage
11,12 et des zones de craquage
13,14 augmentant progressivement de telle sorte que :
V₁₀ < V₁₂ < V₁₃ < V₁₄
ce qui permet d'obtenir à la sortie un ruban de fibres discontinues dont la longueur
moyenne est parfaitement maîtrisée.
[0020] Cette longueur est d'ailleurs illustrée par le diagramme de la figure
1 sur laquelle on a porté en ordonnées les longueurs de fibres en mm et en abscisses
la population des fibres exprimée en pourcentage du nombre de fibres de cette population.
[0021] Il est bien évident que l'on utilisera des installations de craquage différentes
pour obtenir, d'une part, des rubans de fibres discontinues de renfort
2 et, d'autre part, des rubans de fibres discontinues de matrice thermoplastique
3.
[0022] Les différents rubans
2 et
3 ainsi obtenus sont ensuite amenés, par tout moyen connu en soi, au dispositif de
mélange représenté à la figure 3.
[0023] Il s'agit d'une installation comportant une zone d'étirage
15, du type intersecting, qui permet d'obtenir, à la sortie un ruban non homogène
4 de fibres de renfort
2 et de fibres matrices
3 mélangées qui comporte des "traces" de chacun des composants.
[0024] Chaque ruban
4 ainsi obtenu sera, à la sortie de cette machine, assemblé sur une installation similaire
à celle représentée à la figure 3 avec dix autres rubans identiques ; cette opération
sera répétée environ quatre fois ce qui permettra d'obtenir les filés de fibres hybrides
selon l'invention dans les proportions finales désirées de fibres de renfort et de
fibres thermoplastiques, ces proportions, variant, bien évidemment, en fonction des
caractéristiques des fibres de matrices thermoplastiques et en particulier de leur
viscosité à chaud, se situant en général aux environs de 65 % de fibres de renfort
et aux environs de 35 % de fibres matrices thermoplastique. Ces filés de fibres sont
constitués d'un mélange intime de fibres de renfort et de fibres matrices thermoplastiques.
[0025] Ce ruban subit ensuite les opérations classiques de filature en technique fibres
longues :
- passage sur bancs à broches,
- filature,
- bobinage,
- assemblage,
- retordage,
ce qui permet d'obtenir le filé de fibres hybrides pour matériaux composites à matrice
thermoplastique selon l'invention, ce filé de fibres étant, bien entendu, susceptible
d'être transformé par la suite par tissage, tricotage ou tressage.
[0026] Ce filé ne possède pas de caractéristiques mécaniques particulières, car au moment
de la mise en forme, la fibre matrice thermoplastique fond en emprisonnant les fibres
de renfort. Les performances du composite ainsi obtenu ne sont donc fonction que des
caractéristiques des fibres élémentaires et de leur accrochage dans la matrice thermoplastique.
[0027] Le tableau I ci-après résume les propriétés de trois types de filés de fibres hybrides
selon l'invention dans lesquels on a fait varier tant les fibres de renfort que les
fibres matrices thermoplastiques.
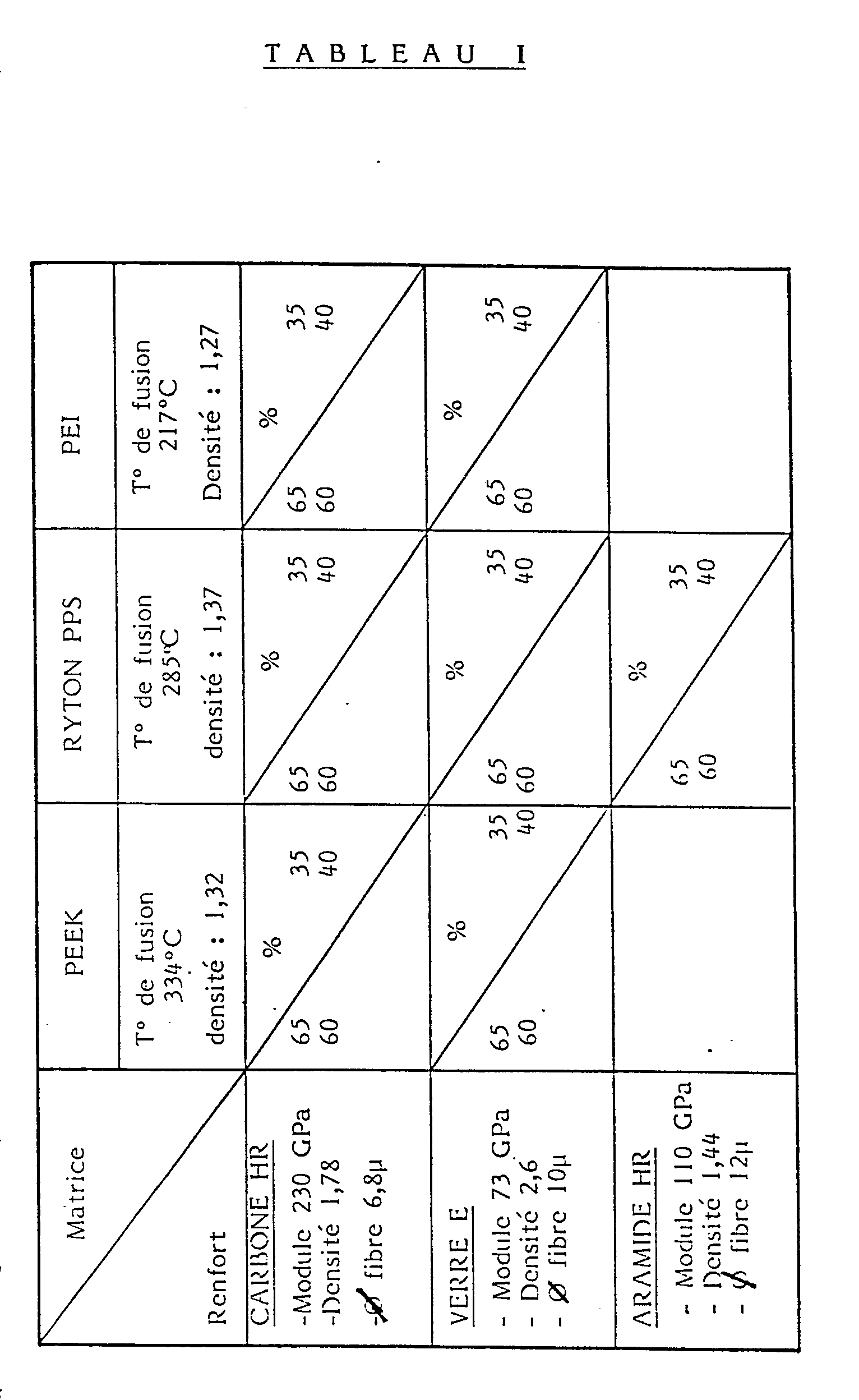
[0028] Le Tableau II compare les propriétés de différents matériaux composites réalisés
à partir de filés de fibres hybrides selon l'invention, comparativement à des composites
réalisés selon la technique antérieure et décrits dans la littérature.
TABLEAU II
Références échantillons |
Taux de fils en volume % |
Densité g/cm² |
Taux de vide % |
FLEXION |
CISAILLEMENT |
TRACTION |
|
|
|
|
Contrainte rupture (GPa) |
Module (GPa) |
Contrainte rupture (MPa) |
Contrainte rupture (GPa) |
Module (GPa) |
1 |
56 |
1,60 |
1,2 |
0,94 |
53,5 |
- |
- |
- |
2 |
56,7 |
1,60 |
0,9 |
0,86 |
65,4 |
- |
- |
- |
3 |
58,2 |
1,61 |
0,1 |
- |
- |
57,3 |
- |
- |
4 |
56 |
1,60 |
0,4 |
- |
- |
59,3 |
- |
- |
5 |
56,7 |
1.62 |
0,9 |
- |
- |
- |
0,96 |
44,7 |
6 |
58,9 |
1,62 |
0,9 |
- |
- |
- |
0,89 |
44,7 |
SAMPE, Jal Jan-Feb 88. p 8-10 * |
51 |
1,54 |
1,6 |
1,19 |
91,6 |
- |
1,43 |
120,6 |
53 |
1,58 |
0,5 |
1,34 |
99,9 |
- |
1,59 |
122,6 |
COmposite N°3-Mai-Juin 1986 - p121-128 ** |
56 |
- |
- |
1,4 |
126 |
- |
1,2 |
- |
* : Tableau IV page 10 |
** : Tableau N° II page 123 - dernière colonne. |
1- Fils hybrides pour composites à matrice thermoplastique, caractérisés en ce qu'ils
sont constitués d'un mélange intime de filés de fibres de renfort (2) et de filés
de fibres matrices thermoplastiques (3), chacun des filés de fibres ayant été préalablement
obtenu par craquage selon un étirage lent et progressif de multifilaments.
2- Fils hybrides selon la revendication 1, caractérisés en ce que les filés de fibres
de renfort sont choisis parmi les filés de fibres de carbone, d'aramide ou de verre.
3- Fils hybrides selon la revendication 1, caractérisés en ce que les filés de fibres
matrices thermoplastiques sont choisis parmi les filés de fibres de polyéther éther
cétone (PEEK), de polysulfure de phénylène (PPS), de polyéthersulfone (PES), de polyétherimide
(PEI), ainsi que parmi les autres filés de fibres connus dans ce but, tels que les
polyamides et les polyimides.
4- Fils hybrides selon l'une quelconque des revendications 1 à 3, caractérisés en ce
que les proportions relatives des fibres de renfort et des fibres matrices thermoplastiques,
se situent aux environs de 65 % pour les fibres de renfort et de 35 % pour les fibres
matrices thermoplastiques.
5- Procédé d'obtention des fils hybrides pour matériaux composites selon l'une quelconque
des revendications 1 à 4, caractérisé en ce que l'on soumet des multifilaments de
fibres de renfort (2) et des multifilaments de fibres matrices thermoplastiques (3)
à un processus séparé de craquage par étirage lent et progressif, puis en ce que l'on
assemble les rubans (2,3) de fibres discontinues ainsi obtenus sur une machine d'étirage
(15) intersecting, le ruban (4) sortant de cette machine d'étirage étant ensuite
assemblé sur une seconde machine d'étirage avec d'autres rubans identiques, cette
opération étant répétée plusieurs fois de façon à réaliser le mélange le plus intime
possible, le ruban final obtenu étant ensuite soumis aux opérations classiques de
filature de fibres longues : passage sur banc à broches, filature proprement dite,
bobinage, assemblage et retordage.