[0001] Die Erfindung betrifft eine Verbundelektrode aus elektrisch leitendem Grundkörper
und teilweise darin eingebetteten katalytischen Teilchen aus auf Träger- Teilchen
aufgebrachtem Katalysator, ein Verfahren zu ihrer Herstellung und ihre Anwendung.
[0002] Für unter anodischer Sauerstoff-Entwicklung ablaufende Elektrolyse-Verfahren, zum
Beispiel für die elektrolytische Metallgewinnung aus wässerigen Lösungen und für elektrochemische
Reduktionen von organischen Verbindungen, werden Anoden mit möglichst geringer Sauerstoff-Überspannung
benötigt.
[0003] Zur Zeit sind bei der elektrolytischen Kupfer- und Zink-Gewinnung Anoden aus Bleilegierungen
mit geringem Zusatz an Calcium, Kobalt oder Silber gebräuchlich. Blei-Anoden werden
auch bei organischen Elektrosynthesen verwendet. Sie sind verhältnismäßig preiswert
und können mehrere Jahre lang benutzt werden. Nachteilig sind die relativ hohe Sauerstoff-Überspannung,
die zu einer Verunreinigung der Elektrolyse-Produkte führende Korrosion des Bleis
und das die Handhabung erschwerende Gewicht der Anoden.
[0004] Seit mehreren Jahrzehnten sind mit Edelmetallen oder Edelmetalloxiden beschichtete
Metallelektroden bekannt, die besondere Vorteile bieten.
[0005] Solche aktivierten Elektroden mit niedrigeren Überspannungswerten können, wie in
der deutschen Patentschrift 1571 721 beschrieben, aus einem Kern aus filmbildendem
Metall oder Ventilmetall (Titan, Tantal, Zirkonium, Niob oder einer Legierung dieser
Metalle) und einer elektrochemisch aktiven Beschichtung aus Platingruppenmetalloxiden
und gegebenenfalls Unedelmetalloxiden bestehen. Dieser Elektroden-Typ hat als dimensionsstabile
Anode bei der Chlorerzeugung weite Verbreitung gefunden.
[0006] In der europäischen Patentschrift 46 448 wird zum Schutz des zum Beispiel aus Titan
bestehenden Elektrodensubstrats eine Schicht aus elektrisch leitendem unlöslichem
Polymernetzwerk zwischen dem Substrat und der äußeren Beschichtung vorgeschlagen.
Das Polymernetzwerk kann als feinverteiltes elektrisch leitendes Material einen Katalysator
aus einem oder mehreren Platingruppenmetallen, auch in Form der Oxide, enthalten und
wird in situ auf dem Elektrodensubstrat erzeugt.
[0007] Besonders für die elektrolytische Metallgewinnung aus sauren Lösungen geeignete dimensionsstabile
Anoden mit vergrößerter aktiver Oberfläche aus Blei oder einer Blei-Legierung mit
teilweise in die Oberfläche eingebetteten katalytischen Teilchen werden in der europäischen
Patentanmeldung 46 727 beschrieben. Die katalytischen Teilchen, deren Größe zwischen
75 und 850 µm liegt, bestehen aus Ventilmetall, zum Beispiel Titan, und darauf in
metallischer oder oxidischer Form durch thermische Zersetzung aufgebrachtem Platingruppenmetall
als Katalysator. Auch Unedelmetall-Katalysatoren, zum Beispiel aus Manganoxid, sind
möglich.
[0008] Aus der eurpäischen Patentanmeldung 62 951 sind Elektroden aus Blei-Platten und in
ihre Oberfläche eingepreßten Teilchen aus mit Platingruppenmetall(oxid) in feinster
Verteilung als Katalysator enthaltendem Kunststoff überzogenen Träger-Teilchen, zum
Beispiel aus Titan-Schwamm, bekannt.
[0009] Die in der europäischen Patentanmeldung 87 186 beschriebenen in saurer Lösung Sauerstoff
entwickelnden Anoden mit geringer Sauerstoff-Überspannung bestehen aus Blei oder Blei-Legierungen
und teilweise in ihre Oberfläche eingebetteten Teilchen aus Titan und/oder Titanoxid
(Rutil) und darauf aufgebrachtem Rutheniumoxid und gegebenfalls Manganoxid und Titanoxid.
[0010] Ebenfalls Metalle oder Metallverbindungen mit elektrokatalytischen Eigenschaften,
jedoch auf Graphit aufgebracht, enthalten die in der DDR-Patentschrift 150 764 beschriebenen
Elektroden. Die poröse Graphitunterlage dieser Elektroden enthält in ihren Poren die
elektrochemisch aktiven Metalle oder Metallverbindungen und einen elektrochemisch
inerten organischen Stoff, zum Beispiel Polystyrol, Polyäthylen, Polymethylmethacrylat,
Polyvinylchlorid oder Polyesteracrylat.
[0011] Anstelle von Titan-, Graphit- und Bleianoden für zahlreiche elektrolytische Verfahren
zu verwendende Anoden mit katalytischer Oberfläche sind aus der europäischen Patentanmeldung
90 381 bekannt. Sie bestehen aus einem elektrisch leitenden Verbundmaterial aus Kohlenstoff
oder Graphit und Kunststoff, besonders einem thermoplastischen fluorhaltigen Polymer,
dessen Oberfläche mit einer elektrokatalytischen Schicht aus chemisch inertem Kunststoff
und darin feinverteiltem aus Edel- oder Unedelmetall(oxid) bestehendem Katalysator
versehen ist. Die aktive Oberfläche dieser Anoden ist wesentlich kleiner als die der
in der europäischen Patentanmeldung 46 727 beschriebenen und soll durch mechanisches
Aufrauhen vergrößert werden. Auch sind relativ große Mengen an Katalysator erforderlich.
[0012] Es ist die Aufgabe der Erfindung, eine Verbundelektrode, die korrosionsbeständig
und leicht zu handhaben ist, eine lange Lebensdauer und - ähnlich wie die in der europäischen
Patentanmeldung 46 727 beschriebene - einen elektrisch leitenden Grundkörper mit großer
aktiver Oberfläche besitzt, zu finden. Die aktive Oberfläche soll aus katalytischen
Teilchen aus TrägerTeilchen mit darauf aufgebrachtem elektrochemisch aktivem Katalysator
bestehen.
[0013] Die die Lösung dieser Aufgabe darstellende Verbundelektrode ist erfindungsgemäß dadurch
gekennzeichnet, daß der Grundkörper aus elektrisch leitendem Kunststoff besteht.
[0014] Der elektrisch leitende Kunststoff besitzt vorzugsweise eine Dicke von mindestens
2 mm und enthält vorzugsweise feinteiligen Kohlenstoff als elektrisch leitendes Material.
[0015] Die Verbundelektrode gemäß der Erfindung weist folgende Vorteile auf:
relativ geringes Gewicht und leichte Handhabbarkeit durch den Grundkörper aus elektrisch
leitendem Kunststoff,
der den elektrischen Strom transportierende elektrisch leitende Kunststoff bleibt
elektrochemisch inaktiv und unterliegt keiner Korrosion und Dimensionsänderung, solange
die Katalysator-Teilchen aktiv sind,
geringer Katalysator-Gehalt,
große aktive Oberfläche,
niedrige Sauerstoff-Überspannung und
lange Lebensdauer.
[0016] Der elektrisch leitende Kunststoff mit einem elektrischen Widerstand kleiner als
103 0 mm besteht vorzugsweise aus einem geeigneten Kunststoff und darin gleichmäßig
verteiltem feinteiligem Kohlenstoff, zum Beispiel in Form von Ruß oder Graphit. Seine
äußere Form wird dem Zweck entsprechend gewählt. Platten mit einer Dicke von mindestens
2 mm haben sich besonders bewährt.
[0017] Als Kunststoff eignen sich besonders alle thermoplastischen Kunststoffe mit ausreichender
chemischer Beständigkeit. Beispiele dafür sind Polyäthylen, Polypropylen, Polystyrol,
Polymethacrylate, Polyesteracrylate, Polyamide, Polyacetale, Polycarbonate, Polytetrafluoräthylen,
Copolymere des Tetrafluoräthylens, wie Tetrafluoräthylen-Äthylen-und Tetrafluoräthylen-Perfluorpropylen-Copolymerisat,
Polytrifluorchloräthylen und Polyvinylchlorid.
[0018] Die Auswahl des Kunststoffes hängt von den Elektrolyse-Bedingungen, wie Elektrolyt-Zusammensetzung
und Stromdichte, ab. In 15%iger Schwefelsäure bei anodischen Stromdichten bis 1 kA/m
2 haben sich Polyäthylen, Polypropylen und Polytetrafluoräthylen besonders bewährt.
Vorzugsweise besteht dann der elektrisch leitende Kunststoff aus einem dieser Polymeren
und 5-80 Gewichts-% Graphit mit einer Teilchengröße unter 150 J,Lm oder 7,5 - 25 Gewichts-%
Ruß mit einer Teilchengröße unter 0,02 µm.
[0019] Der Kunststoff kann anstelle des feinteiligen Kohlenstoffs aber daneben auch andere
elektrisch leitende Materialien, wie Metalle oder Metalloxide, enthalten. Auch elektrisch
leitende Polymere können als elektrisch leitender Kunststoff eingesetzt werden.
[0020] Die Verbundelektrode gemäß der Erfindung enthält als elektrochemisch aktiven Katalysator
vorzugsweise die Platingruppenmetalle Ruthenium, lridium, Palladium, Platin und/oder
Rhodium als Metall und/oder Oxid.
[0021] Besonders bewährt haben sich Katalysatoren aus einem oder mehreren Platingruppenmetallen
und / oder Platingrupenmetalloxiden und einem oder mehreren der Unedelmetalle Titan,
Zirkonium Hafnium, Niob, Tantal, Mangan, Eisen, Kobalt, Nickel, Zinn, Blei, Antimon
und Wismut als Metall und/oder Oxid. Die mehrere Metalle enthaltenden oxidischen Katalysatoren
können Gemische der einzelnen Oxide und/ oder Mischoxide sein.
[0022] Als Träger werden Titan-Schwamm, besonders mit einer Teilchengröße zwischen 0,2 und
1,0 mm, und Titanoxide der allgemeinen Formel Ti0
2-
x mit 0< x < 1, besonders mit einer Teilchengröße zwischen 0,03 und 0,5 mm, bevorzugt.
Aber auch pulverförmiges Titan, Zirkonium, Niob oder Tantal kann verwendet werden.
[0023] Für die Verbundelektroden gemäß der Erfindung geeignete aus den Träger-Teilchen und
dem darauf aufgebrachten Katalysator bestehende katalytische Teilchen können nach
allen für diesen Zweck bekannten Methoden hergestellt werden (siehe zum Beispiel europäische
Patentanmeldung 46 727). Bewährt hat sich das Imprägnieren der Träger-Teilchen mit
Lösungen von thermisch zersetzbaren Verbindungen der Platingruppenmetalle und gegebenfalls
der Unedelmetalle und anschließendes Erhitzen sowie das galvanische Beschichten der
Träger-Teilchen mit den gewünschten Metallen, an das sich eine Oxidation anschließen
kann.
[0024] In bestimmten Fällen, zum Beispiel zur Verbesserung der mechanischen Stabilität,
hat es sich bewährt, die Verbundelektrode mit einem metallischen Stromverteiler, zum
Beispiel aus einem Streckmetall oder Metallnetz, zu versehen. Der Stromverteiler kann
zum Beispiel aus Kupfer, Eisen, Kobalt, Nickel, Legierungen dieser Metalle, Aluminium,
Blei, Titan, Zirkonium, Hafnium, Niob, Tantal, Molybdän oder Wolfram bestehen.
[0025] Ist ein Stromverteiler vorgesehen, so wird bei der Herstellung der Verbundelektrode
dieser vorteilhafterweise zunächst bei erhöhter Temperatur unter Druck mit dem elektrisch
leitenden Kunststoff verbunden; dann werden auf den Kunststoff die katalytischen Teilchen
aufgebracht.
[0026] Elektrisch leitender Kunststoff in Platten-oder Granulatform und Stromverteiler werden
durch 0,5-10 Minuten währendes Einpressen des Stromverteilers bei einer Temperatur
zwischen 140 und 380°C und unter einem Druck von 0,1-2 t/cm
2 dauerhaft und fest ineinander verankert. Dann werden die katalytischen Teilchen gleichmäßig
auf den Kunststoff aufgebracht und bei einer Temperatur zwischen 140 und 380°C und
unter einem Druck von 0,1-2 t/cm
2, vorzugsweise 0,5-10 Minuten lang, teilweise in die Oberfläche des Kunststoffs eingepreßt.
[0027] Die Figuren 1, 2 und 3 stellen Teilausschnitte von drei Ausführungsformen der erfindungsgemäßen
Verbundelektrode dar.
[0028] In der Figur 1 wird der Stromverteiler 1 auf einer Seite von dem elektrisch leitenden
Kunststoff 2 mit den in seine Oberfläche teilweise eingepreßten katalytischen Teilchen
3 bedeckt. Da bei dieser Ausführungsform der Stromverteiler mit dem Elektrolyten in
Berührung kommt, besteht hier der Stromverteiler aus chemisch beständigem Metall.
In wässerigen sauren Elektrolyten haben sich Stromverteiler aus Titanstreckmetall
besonders bewährt.
[0029] In der Figur 2 wird der Stromverteiler 1 auf beiden Seiten von dem elektrisch leitenden
Kunststoff 2 mit den in seine Oberflächen teilweise eingepreßten katalytischen Teilchen
3 bedeckt. Da hier der Kunststoff den Stromverteiler vor der korrodierenden Wirkung
des Elektrolyten schützt, können bei dieser Ausführungsform die Stromverteiler aus
anderen, zum Teil billigeren und den elektrischen Strom besser leitenden Metallen,
zum Beispiel Kupfer, bestehen.
[0030] Die Figur 3 zeigt eine der in Figur 2 dargestellten ähnliche Ausführungsform. Hierbei
ist jedoch nur eine Oberfläche der Verbundelektrode mit den katalytischen Teilchen
3 belegt.
[0031] Die erfindungsgemäße Verbundelekrode kann als Sauerstoffanode bei der Metallgewinnungselektrolyse,
in der Galvanotechnik, bei der elektrochemischen Reduktion organischer Verbindungen
und bei der Elektrotauchlackierung eingesetzt werden.
[0032] Zur näheren Erläuterung wird in den folgenden Beispielen die Herstellung von Verbundelektroden
gemäß der Erfindung beschrieben.
[0033] Zur Bestimmung der elektrochemischen Eigenschaften und des Langzeitverhaltens (Laufzeit)
werden die in den Beispielen 1 bis 5 beschriebenen Verbundelektroden als Sauerstoff-Anoden
in einer Elektrolysezelle mit schwefelsaurem Elektrolyten (150 g H
2S0
4/1; 50°C) und Platin-Kathode eingesetzt.
[0034] Die bei verschiedenen Stromdichten gegen die gesättigte Kalomelelektrode gemessenen
Halbzellenanodenpotentiale (SEP), die nach der Stromunterbrecher-Methode IR-korrigierten
Halbzellenanodenpotentiale (CISEP) und die bei einer Stromdichte von 0,3 kA/m
2 (Beispiel 4) oder 1 kA/m
2 bestimmte Laufzeit bis zum Ausfall der Anode, charakterisiert durch einen starken
Anstieg der Zellspannung, werden in der Tabelle angegeben.
SEP = single electrode potential
CISEP = current interruption single elecrode potential
IR = Ohmscher Spannungsabfall (ohmic drop)
Beispiel 1
[0035] Herstellung einer Verbundelektrode mit elektrochemisch aktivem Katalysator aus Ruthenium-Titan-Oxid
(Mol-Verhältnis Ruthenium:Titan = 30:70)
[0036] Stromverteiler; Durchmesser 33 mm:
Mit Korund gestrahltes und mit Salzsäure gebeiztes Titanstreckmetall (Maschenlänge
10 mm, Maschenbreite 5,7 mm und Stegdicke 1 mm) mit einer Stromzuleitung aus Titan-Draht
(Durchmesser 2 mm)
elektrisch leitender Kunststoff:
Scheibe (Durchmesser 36 mm, Dicke 6 mm) aus Novolen KR 1682 der Firma BASF AG, Ludwigshafen
(Polypropylen mit 80 Gewichts-% Graphit)
[0037] Träger-Teilchen:
Titan-Schwamm mit einer Korngröße von 0,4-0,85 mm, 30 Minuten lang mit90° C warmer
10prozentiger Oxalsäure behandelt, mit Wasser gewaschen und getrocknet
[0038] Imprägnierungslösung:
0,1 g RuCl3 · xH20 (38 Gewichts-% Ru)
0,3 g Tetrabutylorthotitanat
0,04 ml HCI, 37 prozentig
6 ml Isopropanol
[0039] Herstellung der katalytischen Teilchen durch lmprägnierung (Aktivierung) des Titan-Schwamms:
[0040] 2 g des Titan-Schwamms werden in einem Reagenzglas mit der Imprägnierungslösung durchmischt.
Dann wird die überstehende Flüssigkeit dekantiert und das zurückbleibende feuchte
Pulver langsam an der Luft getrocknet. Durch 30 Minuten lange Wärmebehandlung des
getrockneten Pulvers in einem geschlossenen Ofen bei 500°C wird auf dem Titan-Schwamm
durch thermische Zersetzung und Oxidation eine aktive Schicht aus Ruthenium-Titan-Oxid
erzeugt.
[0041] Das Behandeln mit der Imprägnierungslösung und die Wärmebehandlung werden wiederholt,
bis ein Ru-Gehalt von 31,3 mg/1 Titan-Schwamm erreicht ist.
Pressen:
[0042] In ein auf 185°C erhitztes Preßgesenk wird der Stromverteiler und darauf die Scheibe
aus Novolen KR 1682 gelegt. Nach 10 Minuten (Temperaturausgleich) werden Stromverteiler
und Scheibe durch 1 Minute dauerndes Pressen mit einem Druck von 0,1 t/cm2 miteinander
verbunden. Dann werden 0,8 g des aktivierten Titan-Schwamms (katalytische Teilchen)
gleichmäßig auf der Scheibe verteilt und bei 180°C mit einem Druck von 0,2 t/cm
2 1 Minute lang in die Oberfläche der Scheibe eingepreßt.
[0043] Die Menge der katalytischen Teilchen entspricht 800 g/m
2 Elektroden-Oberfläche mit einem Ru-Gehalt von 25 g.
Beispiel 2
[0044] Herstellung einer Verbundelektrode mit elektrochemisch aktivem Katalysator aus Ruthenium-Titan-Oxid
(Mol-Verhältnis Ruthenium:Titan = 30:70)
[0045] Stromverteiler; Durchmesser 33 mm:
Mit Korund gestrahltes und mit Salzsäure gebeiztes Titanstreckmetall (Maschenlänge
10 mm, Maschenbreite 5,7 mm und Stegdicke 1 mm) mit einer Stromzuleitung aus Titan-Draht
(Durchmesser 2 mm)
elektrisch leitender Kunststoff:
Scheibe (Durchmesser 36 mm, Dicke 2,5 mm) aus Lupolen 5261 Z der Firma BASF AG, Ludwigshafen
(Hochdruckpolyäthylen mit 7,5 Gewichts-% Ruß)
Träger-Teilchen:
[0046] Titan-Schwamm mit einer Korngröße von 0,4-0,85 mm, 30 Minuten lang mit 90° C warmer
10 prozentiger Oxalsäure gebeizt, mit Wasser gewaschen und getrocknet
lmprägnierungslösung:
0,1 g RuCl3 · xH20 (38 Gewichts-% Ru)
0,3 g Tetrabutylorthotitanat
0,04 ml HCI, 37 prozentig
6 ml Isopropanol
[0047] Herstellung der katalytischen Teilchen durch Imprägnierung (Aktivierung) des Titan-Schwamms:
[0048] 2 g des Titan-Schwamms werden in einem Reagenzglas mit der Imprägnierungslösung durchmischt.
Dann wird die überstehende Flüssigkeit dekantiert und das zurückbleibende feuchte
Pulver langsam an der Luft getrocknet. Durch 30 Minuten lange Wärmebehandlung des
getrockneten Pulvers in einem geschlossenen Ofen bei 500°C wird durch thermische Zersetzung
und Oxidation des RuCI
3 und des Titanats eine aktive Schicht aus Ruthenium-Titan-Oxid auf dem Titan-Schwamm
erzeugt.
[0049] Das Behandeln mit der Imprägnierungslösung und die Wärmebehandlung werden wiederholt,
bis ein Ru-Gehalt von 31,3 mg/1 g Titan-Schwamm erreicht ist.
Pressen:
[0050] In ein auf 150°C erhitztes Preßgesenk wird der Stromverteiler und darauf die Scheibe
aus Lupolen 5261 Z gelegt. Nach 10 Minuten (Temperaturausgleich) werden Stromverteiler
und Scheibe durch 1 Minute dauerndes Pressen mit einem Druck von 0,15 t/cm
2 miteinander verbunden. Dann werden 0,8 g des aktivierten Titan-Schwamms (katalytische
Teilchen) gleichmäßig auf der Scheibe verteilt und bei 140°C mit einem Druck von 0,2
t/cm
2 1 Minute lang in die Oberfläche der Scheibe eingepreßt.
[0051] Die Menge der katalytischen Teilchen entspricht 800 g/m
2 Elektroden-Oberfläche mit einem Ru-Gehalt von 25 g.
Beispiel 3
[0052] Herstellung einer Verbundelektrode mit elektrochemisch aktivem Katalysator aus Ruthenium-Titan-Oxid
(Mol-Verhältnis Ruthenium:Titan = 30:70)
[0053] Stromverteiler; Durchmesser 33 mm:
[0054] Mit Korund gestrahltes und mit Salzsäure gebeiztes Titanstreckmetall (Maschenlänge
10 mm, Maschenbreite 5,7 mm und Stegdicke 1 mm) mit einer Stromzuleitung aus Titan-Draht
(Durchmesser 2 mm)
elektrisch leitender Kunststoff:
Scheibe (Durchmesser 36 mm, Dicke 4 mm) aus Colcolor der Firma Degussa, Frankfurt
(Polypropylen mit 25 Gewichts-% Ruß)
Träger-Teilchen:
[0055] Titan-Schwamm mit einer Korngröße von 0,4-0,85 mm, 30 Minuten lang mit 90° C warmer
10 prozentiger Oxalsäure behandelt, mit Wasser gewaschen und getrocknet
[0056] Imprägnierungslösung:
0,1 g RuCl3 · xH20 (38 Gewichts-% Ru)
0,3 g Tetrabutylorthotitanat
0,04 ml HCI, 37 prozentig
6 ml lsopropanol
[0057] Herstellung der katalytischen Teilchen durch Imprägnierung (Aktivierung) des Titan-Schwamms:
[0058] 2 g des Titan-Schwamms werden in einem Reagenzglas mit der Imprägnierungslösung durchmischt.
Dann wird die überstehende Flüssigkeit dekantiert und das zurückbleibende feuchte
Pulver langsam an der Luft getrocknet. Durch 30 Minuten lange Wärmebehandlung des
getrockneten Pulvers in einem geschlossenen Ofen bei 500°C wird durch thermische Zersetzung
und Oxidation des RuC1
3 und des Titanats eine aktive Schicht aus Ruthenium-Titan-Oxid auf dem Titan-Schwamm
erzeugt.
[0059] Das Behandeln mit der Imprägnierungslösung und die Wärmebehandlung werden wiederholt,
bis ein Ru-Gehalt von 31,3 mg/1 g Titan-Schwamm erreicht ist.
Pressen:
[0060] In ein auf 180°C erhitztes Preßgesenk wird der Stromverteiler und darauf die Colcolor-Scheibe
gelegt. Nach 10 Minuten (Temperaturausgleich) werden Stromverteiler und Scheibe durch
1 Minute dauerndes Pressen mit einem Druck von 0,5 t/cm
2 miteinander verbunden. Dann werden 0,8 g des aktivierten Titan-Schwamms (katalytische
Teilchen) gleichmäßig auf der Scheibe verteilt und bei 180°C mit einem Druck von 0,5
t/cm
2 1 Minute lang in die Oberfläche der Scheibe eingepreßt.
[0061] Die Menge der katalytischen Teilchen entspricht 800 g/m
2 Elektroden-Oberfläche mit einem Ru-Gehalt von 25 g.
Beispiel 4
[0062] Herstellung einer Verbundelektrode mit elektrochemisch aktivem Katalysator aus Ruthenium-Titan-Oxid
(Mol-Verhältnis Ruthenium:Titan = 30:70)
[0063] Stromverteiler; Durchmesser 33 mm:
[0064] Mit Korund gestrahltes und mit Salzsäure gebeiztes Titanstreckmetall (Maschenlänge
10 mm, Maschenbreite 5,7 mm und Stegdicke 1 mm) mit einer Stromzuleitung aus Titan-Draht
(Durchmesser 2 mm)
elektrisch leitender Kunststoff:
[0065] Scheibe (Durchmesser 36 mm, Dicke 6 mm) aus Novolen KR 1682 der Firma BASF AG , Ludwigshafen
(Polypropylen mit 80 Gewichts-% Graphit)
Träger-Teilchen:
[0066] Ti-Oxid der Formel Ti0
2-
x (0< x < 1 ) mit einer Korngröße von 0,037 - 0,1 mm
[0067] Imprägnierungslösung:
0,1 g RuC13 - xH20 (38 Gewichts-% Ru)
0,3 g Tetrabutylorthotitanat
0,04 ml HCI, 37 prozentig
6 ml Isopropanol
[0068] Herstellung der katalytischen Teilchen durch Imprägnierung (Aktivierung) des Titanoxids:
[0069] 2 g des Titanoxids werden in einem Reagenzglas mit der Imprägnierungslösung durchmischt.
Dann wird die überstehende Flüssigkeit dekantiert und das zurückbleibende feuchte
Pulver langsam an der Luft getrocknet. Durch 30 Minuten lange Wärmebehandlung des
getrockneten Pulvers in einem geschlossenen Ofen bei 500°C wird durch thermische Zersetzung
und Oxidation des RuCl
3 und des Titanats eine aktive Schicht aus Ruthenium-Titan-Oxid auf dem Titanoxid erzeugt.
[0070] Das Behandeln mit der Imprägnierungslösung und die Wärmebehandlung werden wiederholt,
bis ein Ru-Gehalt von 31,3 mg/1g Titanoxid erreicht ist.
Pressen:
[0071] In ein auf 185°C erhitztes Preßgesenk wird der Stromverteiler und darauf die Scheibe
aus Novolen KR 1682 gelegt. Nach 10 Minuten (Temperaturausgleich) werden Stromverteiler
und Scheibe durch 1 Minute dauerndes Pressen mit einem Druck von 0,1 t/cm
2 miteinander verbunden. Dann werden 0,3 g des aktivierten Titanoxids (katalytische
Teilchen) gleichmäßig auf der Scheibe verteilt und bei 185°C mit einem Druck von 0,1
t/cm2 1 Minute lang in die Oberfläche der Scheibe eingepreßt.
[0072] Die Menge der katalytischen Teilchen entspricht 300 g/m
2 Elektroden-Oberfläche mit einem Ru-Gehalt von 15 g.
Beispiel 5
[0073] Herstellung einer Verbundetektrode mit elektrochemisch aktivem Katalysator aus Ruthenium-Titan-Oxid
(Mol-Verhältnis Ruthenium:Titan = 30:70)
[0074] Stromverteiler; Durchmesser 33 mm:
[0075] Mit Korund gestrahltes und mit Salzsäure gebeiztes Titanstreckmetall (Maschenlänge
10 mm, Maschenbreite 5,7 mm und Stegdicke 1 mm) mit einer Stromzuleitung aus Titan-Draht
(Durchmesser 2 mm)
[0076] elektrisch leitender Kunststoff:
[0077] Granulat aus Hostaflon TF 4215 der Firma Farbwerke Hoechst AG, Frankfurt (Polytetrafluoräthylen
mit mit 25 Gewichts-% Graphit)
Träger-Teilchen:
[0078] Titan-Schwamm mit einer Korngröße von 0,4-0,85 mm, 30 Minuten lang mit 90° C warmer
10 prozentiger Oxalsäure behandelt, mit Wasser gewaschen und getrocknet
[0079] Imprägnierungslösung:
0,1 g RuCl3 · xH20 (38 Gewichts-% Ru)
0,3 g Tetrabutylorthotitanat
0,04 ml HCI, 37 prozentig
6 ml Isopropanol
[0080] Herstellung der katalytischen Teilchen durch Imprägnierung (Aktivierung) des Titan-Schwamms:
[0081] 2 g des Titan-Schwamms werden in einem Reagenzglas mit der Imprägnierungslösung durchmischt.
Dann wird die überstehende Flüssigkeit dekantiert und das zurückbleibende feuchte
Pulver langsam an der Luft getrocknet. Durch 30 Minuten lange Wärmebehandlung des
getrockneten Pulvers in einem geschlossenen Ofen bei 500°C wird durch thermische Zersetzung
und Oxidation des RuCl
3 und des Titanats eine aktive Schicht aus Ruthenium-Titan-Oxid erzeugt.
[0082] Das Behandeln mit der Imprägnierungslösung und die Wärmebehandlung werden wiederholt,
bis ein Ru-Gehalt von 31,3 mg/ 1g Titan-Schwamm erreicht ist.
Pressen:
[0083] 2,5 g Granulat aus Hostaflon TF 4215 werden in ein Preßgesenk gefüllt, gleichmäßig
verteilt und durch 1 Minute dauerndes Pressen bei Raumtemperaturmiteinem Druck von
0,2 t/cm
2 zu einer Scheibe (Durchmesser 36 mm, Dicke 2 mm) verformt. Der Stromverteiler wird
dann auf die Scheibe gelegt, mit 2,5 g Granulat aus Hostaflon TF 4215 bedeckt und
durch 0,5 Minuten dauerndes Pressen bei Raumtemperatur mit einem Druck von 0,05 t/cm
2 auf beiden Seiten fest mit dem Hostaflon TF 4215 verbunden. In jede der beiden Kunststoff-Oberflächen
des erhaltenen Kunststoff/Stromverteiler/Kunststoff-Verbundes werden durch 1 Minute
langes Pressen bei Raumtemperatur mit einem Druck von 0,8 t/cm
2 0,8 g des aktivierten Titan-Schwamms (katalytische Teilchen) eingepreßt. Durch anschließendes
einstündiges Sintern bei 380°C wird dann die fertige Verbundelektrode erhalten.
[0084] Die Menge der katalytischen Teilchen entspricht 800 g/m
2 Elektroden-Oberfläche mit einem Ru-Gehalt von 25 g.
Beispiel 6
[0085] Herstellung einer Verbundelektrode mit elektrochemisch aktivem Katalysator aus einer
Platin-iridium-Legierung
Stromverteiler; Durchmesser 33 mm:
[0086] Mit Korund gestrahltes und mit Salzsäure gebeiztes Titanstreckmetall (Maschenlänge
10 mm, Maschenbreite 5,7 mm und Stegdicke 1 mm) mit einer Stromzuleitung aus Titan-Draht
(Durchmesser 2 mm)
[0087] elektrisch leitender Kunststoff:
[0088] Scheibe (Durchmesser 36 mm, Dicke 2,5 mm) aus Lupolen 5261 Z der Firma BASF AG, Ludwigshafen
(Hochdruckpolyäthylen mit 7,5 Gewichts-% Ruß)
Träger-Teilchen:
[0089] Titan-Schwamm mit einer Korngröße von 0,4-0,85 mm, 30 Minuten lang mit 90° C warmer
10 prozentiger Oxalsäure gebeizt, mit Wasser gewaschen und getrocknet
[0090] Imprägnierungslösung:
0,1 g H2[PtCl6]
0,5 g IrCl3 · xH20 (41 Gewichts-% Ir)
10 ml Isopropanol
10 ml Linalool
[0091] Herstellung der katalytischen Teilchen durch Imprägnierung (Aktivierung) des Titan-Schwamms:
[0092] 2 g des Titan-Schwamms werden in einem Reagenzglas mit der Imprägnierungslösung durchmischt.
Dann wird die überstehende Flüssigkeit dekantiert und das zurückbleibende feuchte
Pulver langsam bei 80° C an der Luft getrocknet. Durch 30 Minuten lange Wärmebehandlung
des getrockneten Pulvers in einem geschlossenen Ofen bei 480°C in reduzierender Ammoniak-Butan-Atmosphäre
wird auf dem Titan-Schwamm eine aktive Schicht aus 70 Gewichts-% Pt und 30 Gewichts-%
Iridium erzeugt.
[0093] Das Behandeln mit der Imprägnierungslösung und die Wärmebehandlung werden wiederholt,
bis ein (Pt+Ir)-Gehalt von 10 mg/lg Titan-Schwamm erreicht ist.
Pressen:
[0094] In ein auf 185°C erhitztes Preßgesenk wird der Stromverteiler und darauf die Scheibe
aus Nololen KR 1682 gelegt. Nach 10 Minuten (Temperaturausgleich) werden Stromverteiler
und Scheibe durch 1 Minute dauerndes Pressen mit einem Druck von 0,1 t/cm
2 miteinander verbunden. Dann werden 0,8 g des aktivierten Titan-Schwamms (katalytische
Teilchen) gleichmäßig auf der Scheibe verteilt und bei 180°C mit einem Druck von 0,2
t/cm
2 1 Minute lang in die Oberfläche der Scheibe eingepreßt.
[0095] Die Menge der katalytischen Teilchen entspricht 800 g/m
2 Elektroden-Oberfläche mit einem (Pt+ Ir)-Gehalt von 8 g.
Beispiel 7
[0096] Herstellung einer Verbundelektrode mit elektrochemisch aktivem Katalysator aus Ruthenium-Mangan-Oxid
(Mol-Verhältnis Ruthenium:Titan = 30:70)
Stromverteiler; Durchmesser 33 mm:
[0097] Mit Korund gestrahltes und mit Salzsäure gebeiztes Titanstreckmetall (Maschenlänge
10 mm, Maschenbreite 5,7 mm und Stegdicke 1 mm) mit einer Stromzuleitung aus Titan-Draht
(Durchmesser 2 mm)
[0098] elektrisch leitender Kunststoff:
[0099] Scheibe (Durchmesser 36 mm, Dicke 6 mm) aus Novolen KR 1682 der Firma BASF AG, Ludwigshafen
(Polypropylen mit 80 Gewichts-% Graphit)
Träger-Teilchen:
[0100] Titan-Schwamm mit einer Korngröße von 0,4-0,85 mm, 30 Minuten lang mit 90° C warmer
10 prozentiger Oxalsäure behandelt, mit Wasser gewaschen und getrocknet
[0101] Imprägnierungslösung:
0,57 g RuCl3 · xH20 (38 Gewichts-% Ru) und
1,33 g Mn(NO)2 · 4H20
werden in 4 ml Butanol gelöst. Zu der erhaltenen Lösung wird die sechsfache Menge
des Gewichts der Lösung an Butanol gegeben.
[0102] Herstellung der katalytischen Teilchen durch Imprägnierung (Aktivierung) des Titan-Schwamms:
[0103] 2 g des mit Trichloräthylen entfetteten und getrockneten Titan-Schwamms werden in
einem Reagenzglas mit der Imprägnierungslösung durchmischt. Dann wird die überstehende
Flüssigkeit dekantiert und das zurückbleibende feuchte Pulver etwa 1 Stunde lang bei
100°C getrocknet. Durch eine 10 Minuten lange Wärmebehandlung bei 200°C und eine darauf
folgende 12 Minuten lange bei 400°C in einem Luftstrom wird auf dem Titan-Schwamm
eine aktive Schicht aus Ruthenium-Mangan-Oxid erzeugt.
[0104] Das Behandeln mit der Imprägnierungslösung und die Wärmebehandlung werden wiederholt,
bis ein Ruthenium-Gehalt von 27,5 mg und ein Mangan-Gehalt von 34,9 mg pro 1 g Titan-Schwamm
erreicht ist.
Pressen:
[0105] In ein auf 185°C erhitztes Preßgesenk wird der Stromverteiler und darauf die Scheibe
aus Novolen KR 1682 gelegt. Nach 10 Minuten (Temperaturausgleich) werden Stromverteiler
und Scheibe durch 1 Minute dauerndes Pressen mit einem Druck von 0,1 t/cm
2 miteinander verbunden. Dann werden 0,8 g des aktivierten Titan-Schwamms (katalytische
Teilchen) gleichmäßig auf der Scheibe verteilt und bei 180°C mit einem Druck von 0,2
t/cm2 1 Minute lang in die Oberfläche der Scheibe eingepreßt.
[0106] Die Menge der katalytischen Teilchen entspricht 800 g/m
2 Elektroden-Oberfläche mit einem Ru-Gehalt von 22 g und einem Mn-Gehalt von 27,9 g.
Beispiel 8
[0107] Herstellung einer Verbundelektrode mit elektrochemisch aktivem Katalysator aus Ruthenium-Iridium-Oxid
Stromverteiler; Durchmesser 33 mm:
[0108] Mit verdünnter Salpetersäure gebeiztes Kupferstreckmetall (Maschenlänge 21 mm, Maschenbreite
9 mm und Stegdicke 0,8 mm) mit einer Stromzuleitung aus Titan-Draht (Durchmesser 2
mm)
[0109] elektrisch leitender Kunststoff:
[0110] Scheibe (Durchmesser 36 mm, Dicke 2,5 mm) aus Lupolen 5261 Z der Firma BASF AG, Ludwigshafen
(Hochdruckpolyäthylen mit 7,5 Gewichts-% Ruß)
Träger-Teilchen:
[0111] Titan-Schwamm mit einer Korngröße von 0,4-0,85 mm, 30 Minuten lang mit 90° C warmer
10 prozentiger Oxalsäure gebeizt, mit Wasser gewaschen und getrocknet
[0112] Imprägnierungslösung:
1,56 g IrCl3 · xH20 (41 Gewichts-% Ir)
3,4 g RuCl3 · xH20 (38 Gewichts-% Ru)
1,25 ml HCI, 37 prozentig
100 ml Isopropanol
[0113] Herstellung der katalytischen Teilchen durch Imprägnierung (Aktivierung) des Titan-Schwamms:
[0114] 2 g des Titan-Schwamms werden in einem Reagenzglas mit der Imprägnierungslösung durchmischt.
Dann wird die überstehende Flüssigkeit dekantiert und das zurückbleibende feuchte
Pulver 2 Stunden lang bei 120°C getrocknet. Durch 10 Minuten lange Wärmebehandlung
des getrockneten Pulvers in einem geschlossenen Ofen bei 250°C wird durch thermische
Zersetzung und Oxidation von IrCl
3 und RuC1
3 eine aktive Schicht aus Ruthenium-Iridium-Oxid erzeugt.
[0115] Das Behandeln mit der Imprägnierungslösung und die Wärmebehandlung werden wiederholt,
bis ein Ru-Gehalt von 20 mg/1 g Titan-Schwamm und ein Ir-Gehalt von 10 mg/1 g Titan-Schwamm
erreicht ist.
Pressen:
[0116] In ein auf 150°C erhitztes Preßgesenk wird der Stromverteiler und darauf die Scheibe
aus Lupolen 5261 Z gelegt. Nach 10 Minuten (Temperaturausgleich) werden Stromverteiler
und Scheibe durch 1 Minute dauerndes Pressen mit einem Druck von 0,15 t/cm
2 miteinander verbunden. Dann werden 0,8 g des aktivierten Titan-Schwamms (katalytische
Teilchen) gleichmäßig auf der Scheibe verteilt und bei 140°C mit einem Druck von 0,2
t/cm
2 1 Minute lang in die Oberfläche der Scheibe eingepreßt.
[0117] Die Menge der katalytischen Teilchen entspricht 800 g/m
2 Elektroden-Oberfläche mit einem Ir-Gehalt von 8 g und einem Ru-Gehalt von 16 g.
Beispiel 9
[0118] Herstellung einer Verbundelektrode mit elektrochemisch aktivem Katalysator aus Ruthenium-Palladium-Oxid
[0119] Stromverteiler; Durchmesser 33 mm:
[0120] Mit Korund gestrahltes und mit Salzsäure gebeiztes Titanstreckmetall (Maschenlänge
10 mm, Maschenbreite 5,7 mm und Stegdicke 1 mm) mit einer Stromzuleitung aus Titan-Draht
(Durchmesser 2 mm)
[0121] elektrisch leitender Kunststoff:
[0122] Scheibe (Durchmesser 36 mm, Dicke 4 mm) aus Colcolor der Firma Degussa, Frankfurt
(Polypropylen mit 25 Gewichts-% Ruß)
Träger-Teilchen:
[0123] Titan-Schwamm mit einer Korngröße von 0,4-0,85 mm, 30 Minuten lang mit 90° C warmer
10 prozentiger Oxalsäure behandelt, mit Wasser gewaschen und getrocknet
[0124] lmprägnierungslösung:

[0125] Herstellung der katalytischen Teilchen durch Imprägnierung (Aktivierung) des Titan-Schwamms:
[0126] 2 g des Titan-Schwamms werden in einem Reagenzglas mit der Imprägnierungslösung durchmischt.
Dann wird die überstehende Flüssigkeit dekantiert und das zurückbleibende feuchte
Pulver 20 Minuten lang bei 140°C getrocknet. Durch Wärmebehandlung des getrockneten
Pulvers in einem geschlossenen Ofen - zunächst 18 Minuten lang bei 250°C, dann 15
Minuten bei 450°C - wird auf dem Titan-Schwamm eine aktive Schicht aus Ruthenium-Palladium-Oxid
erzeugt.
[0127] Das Behandeln mit der Imprägnierungslösung und die Wärmebehandlung werden wiederholt,
bis ein Ru-Gehalt von 18,8 mg/1 g Titan-Schwamm und ein Pd-Gehalt von 6,9 mg/lg Titan-Schwamm
erreicht ist.
Pressen:
[0128] In ein auf 180°C erhitztes Preßgesenk wird der Stromverteiler und darauf die Colcolor-Scheibe
gelegt. Nach 10 Minuten (Temperaturausgleich) werden Stromverteiler und Scheibe durch
1 Minute dauerndes Pressen mit einem Druck von 0,5 t/cm
2 miteinanderverbunden. Dann werden 0,8 g des aktivierten Titan-Schwamms (katalytische
Teilchen) gleichmäßig auf der Scheibe verteilt und bei 180°C mit einem Druck von 0,5
t/cm
2 1 Minute lang in die Oberfläche der Scheibe eingepreßt.
[0129] Die Menge der katalytischen Teilchen entspricht 800 g/m
z Elektroden-Oberfläche mit einem Ru-Gehalt von 15 g und einem Fd-Gehalt von 5,5 g.
Beispiel 10
[0130] Herstellung einer Verbundelektrode mit elektrochemisch aktivem Katalysator aus Rutheniumoxid
[0131] Stromverteiler; Durchmesser 33 mm:
[0132] Mit Korund gestrahltes und mit Salzsäure gebeiztes Titanstreckmetall (Maschenlänge
10 mm, Maschenbreite 5,7 mm und Stegdicke 1 mm) mit einer Stromzuleitung aus Titan-Draht
(Durchmesser 2 mm)
[0133] elektrisch leitender Kunststoff:
[0134] Scheibe (Durchmesser 36 mm, Dicke 2,5 mm) aus Lupolen 5261 Z der Firma BASF AG, Ludwigshafen
(Hochdruckpolyäthylen mit 7,5 Gewichts-% Ruß)
Träger-Teilchen:
[0135] Titan-Schwamm mit einer Korngröße von 0,4-0,85 mm, 30 Minuten lang mit 90° C warmer
10 prozentiger Oxalsäure gebeizt, mit Wasser gewaschen und getrocknet
[0136] Imprägnierungslösung:
1,67 g RuCl3 · xH20 (38 Gewichts-% Ru)
6,7 ml HCI
100 ml Isopropanol
[0137] Herstellung der katalytischen Teilchen durch Imprägnierung (Aktivierung) des Titan-Schwamms:
[0138] 2 g des Titan-Schwamms werden in einem Reagenzglas mit der Imprägnierungslösung durchmischt.
Dann wird die überstehende Flüssigkeit dekantiert und das zurückbleibende feuchte
Pulver 1 Stunde lang bei 100°C getrocknet und anschließend 15 Minuten lang einer Temperatur
von 250° C ausgesetzt.
[0139] Das Behandeln mit der Imprägnierungslösung und die Wärmebehandlung werden wiederholt,
bis ein Ru-Gehalt von 15,6 mg/1g Titan-Schwamm erreicht ist.
[0140] Dann wird der Ru-haltige Titan-Schwamm in einem Ofen jeweils 10 Minuten lang einer
Temperatur von 300° C, 430° C und 400° C ausgesetzt.
Pressen:
[0141] In ein auf 150°C erhitztes Preßgesenk wird der Stromverteiler und darauf die Scheibe
aus Lupolen 5261 Z gelegt. Nach 10 Minuten (Temperaturausgleich) werden Stromverteiler
und Scheibe durch 1 Minute dauerndes Pressen mit einem Druck von 0,15 t/cm
2 miteinander verbunden. Dann werden 0,8 g des aktivierten Titan-Schwamms (katalytische
Teilchen) gleichmäßig auf der Scheibe verteilt und bei 140°C mit einem Druck von 0,2
t/cm
z 1 Minute lang in die Oberfläche der Scheibe eingepreßt.
[0142] Die Menge der katalytischen Teilchen entspricht 800 g/m
2 Elektroden-Oberfläche mit einem Ru-Gehalt von 12,5 g.
Beispiel 11
[0143] Herstellung einer Verbundelektrode mit elektrochemisch aktivem Katalysator aus Ruthenium-Mangan-Zinn-Oxid
elektrisch leitender Kunststoff:
Scheibe (Durchmesser 36 mm, Dicke 6 mm) aus Novolen KR 1682 der Firma BASF AG, Ludwigshafen
(Polypropylen mit 80 Gewichts-% Graphit)
Träger-Teilchen:
[0144] Titan-Schwamm mit einer Korngröße von 0,4-0,85 mm, 30 Minuten lang mit 90° C warmer
10 prozentiger Oxalsäure behandelt, mit Wasser gewaschen und getrocknet
[0145] Imprägnierungslösung:
0,44 g RuCl3 · xH20 (38 Gewichts-% Ru)
0,09 g SnCl2 · 2H20
0,52 g Mn(NO3)2 · 4H20
4 ml Butanol
[0146] Herstellung der katalytischen Teilchen durch Imprägnierung (Aktivierung) des Titan-Schwamms:
[0147] 2 g des Titan-Schwamms werden in einem Reagenzglas mit der Imprägnierungslösung durchmischt.
Die überstehende Flüssigkeit wird dekantiert und das zurückbleibende feuchte Pulver
15 Minuten lang bei 140° C getrocknet.
[0148] Durch Wärmebehandlung des getrockneten Pulvers zunächst bei 250° C, dann bei 420°
C für jeweils 10 Minuten wird durch thermische Zersetzung und Oxidation von RuC1
3, SnCl
2 und Mn(N0
3)
2 eine aktive Schicht aus Ruthenium-Mangan-Zinn-Oxid erzeugt.
[0149] Das Behandeln mit der Imprägnierungslösung und die Wärmebehandlung werden wiederholt,
bis ein Ru-Gehalt von 28,57 mg/1g Titan-Schwamm erreicht ist.
Pressen:
[0150] In ein auf 185°C erhitztes Preßgesenk wird die Scheibe aus Novolen KR 1682 gelegt.
Nach 10 Minuten (Temperaturausgleich) werden 0,7 g des aktivierten Titan-Schwamms
(katalytische Teilchen) gleichmäßig auf der Scheibe verteilt und bei 180° C mit einem
Druck von 0,2 t/cm
2 1 Minute lang in die Oberfläche der Scheibe eingepreßt.
[0151] Die Menge an katalytischen Teilchen entspricht 700 g/m
2 Elektroden-Oberfläche mit einem Ru-Gehalt von 20 g, einem Mn-Gehalt von 13,7 g und
einem Sn-Gehalt von 5,8 g.
Beispiel 12
[0152] Herstellung einer Verbundelektrode mit elektrochemisch aktivem Katalysator aus Platin
[0153] Stromverteiler; Durchmesser 33 mm:
[0154] Mit Korund gestrahltes und mit Salzsäure gebeiztes Titanstreckmetall (Maschenlänge
10 mm, Maschenbreite 5,7 mm und Stegdicke 1 mm) mit einer Stromzuleitung aus Titan-Draht
(Durchmesser 2 mm)
[0155] elektrisch leitender Kunststoff:
[0156] Scheibe (Durchmesser 36 mm, Dicke 4 mm) aus Colcolor der Firma Degussa, Frankfurt
(Polypropylen mit 25 Gewichts-% Ruß)
Träger-Teilchen:
[0157] Titan-Schwamm mit einer Korngröße von 0,4-0,85 mm, 30 Minuten lang mit 90° C warmer
10 prozentiger Oxalsäure behandelt, mit Wasser gewaschen und getrocknet.
[0158] Lösung für das galvanische Beschichten:
7,5 g KOH
10 g K2 lPt(OH)εI
500 ml Wasser
[0159] Herstellung der katalytischen Teilchen durch galvanisches Beschichten (Aktivierung)
des Titan-Schwamms:
[0160] Der Titan-Schwamm wird auf ein Blech gegeben und zusammen mit dem Blech als Kathode
in die 75° C warme Lösung für das galvanische Beschichten getan. Unter Verwendung
einer Anode aus platiniertem Titan werden bei einer kathodischen Stromdichte von 11
mA/cm2 innerhalb von 12 Minuten 100 mg Pt/1g Titan-Schwamm abgeschieden.
Pressen:
[0161] In ein auf 180°C erhitztes Preßgesenk wird der Stromverteiler und darauf die Colcolor-Scheibe
gelegt. Nach 10 Minuten (Temperaturausgleich) werden Stromverteiler und Scheibe durch
1 Minute dauerndes Pressen mit einem Druck von 0,5 t/cm
2 miteinander verbunden. Dann werden 0,2 g des aktivierten Titan-Schwamms (katalytische
Teilchen) gleichmäßig auf der Scheibe verteilt und bei 180°C mit einem Druck von 0,5
t/cm
2 1 Minute lang in die Oberfläche der Scheibe eingepreßt.
[0162] Die Menge der katalytischen Teilchen entspricht 800 g/m
2 Elektroden-Oberfläche mit einem Pt-Gehalt von 20 g.
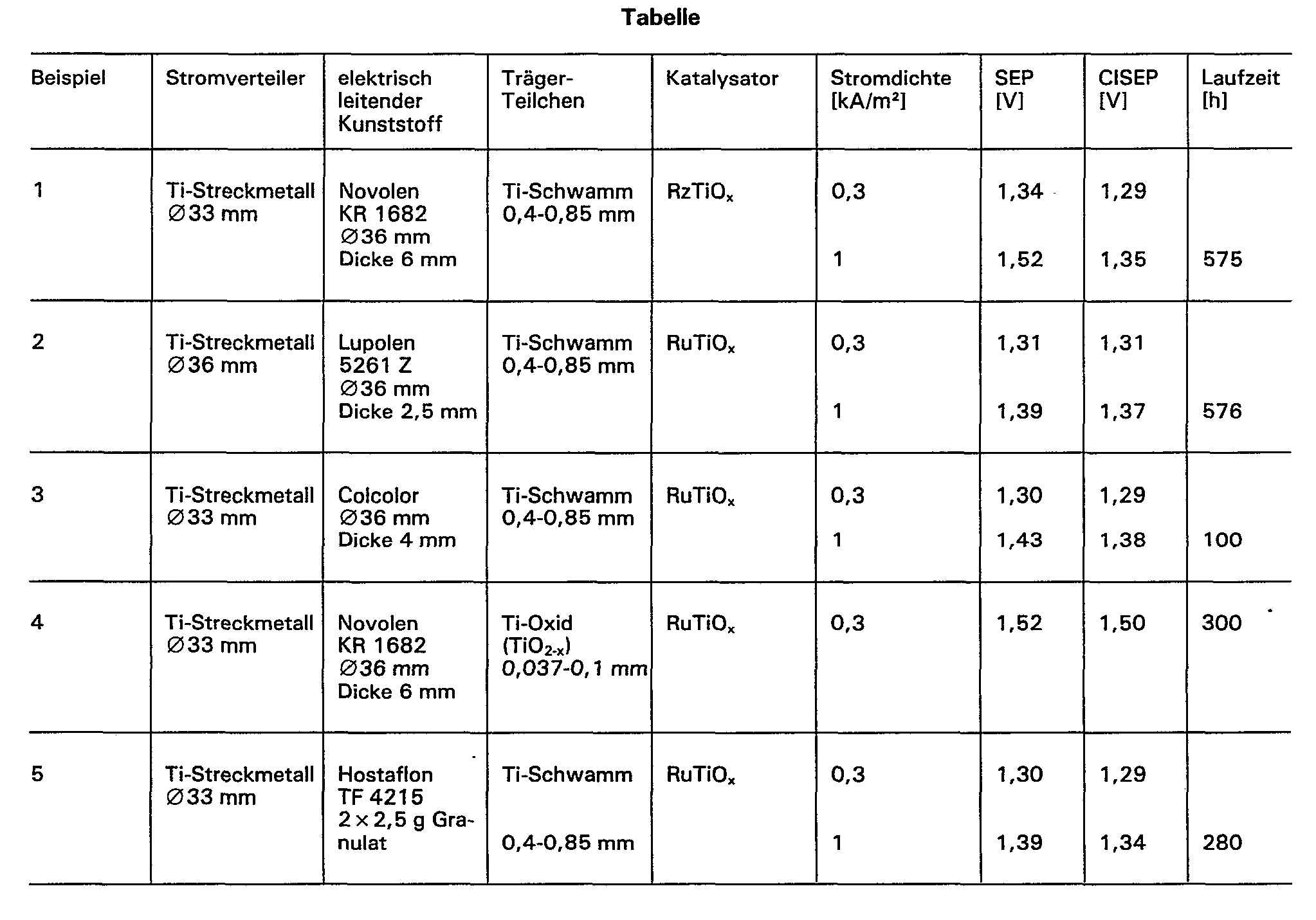
1. Sauerstoff-Verbundanode aus elektrisch leitendem, nichtporösem Grundkörper und
teilweise in seine Oberfläche eingebetteten katalytischen Teilchen aus auf Träger-Teilchen
aufgebrachtem Katalysator, dadurch gekennzeichnet, daß der Grundkörper aus elektrisch
leitendem Kunststoff besteht.
2. Sauerstoff-Verbundanode nach Anspruch 1, dadurch gekennzeichnet, daß der elektrisch
leitende Kunststoff mindestens eine Dicke von 2 mm besitzt.
3. Sauerstoff-Verbundanode nach Anspruch 1 oder 2, dadurch gekennzeichnet, daß der
elektrisch leitende Kunststoff feinteiligen Kohlenstoff als elektrisch leitendes Material
enthält.
4. Sauerstoff-Verbundanode nach Anspruch 3, dadurch gekennzeichnet, daß der elektrisch
leitende Kunststoff aus thermoplastischem Kunststoff und feinteiligem Kohlenstoff
besteht.
5. Sauerstoff-Verbundanode nach einem der Ansprüche 1 bis 4, dadurch gekennzeichnet,
daß der Katalysator ein oder mehrere der Platingruppenmetalle Ruthenium, Iridium,
Palladium, Platin und Rhodium als Metall und/oder Oxid enthält.
6. Sauerstoff-Verbundanode nach Anspruch 5, dadurch gekennzeichnet, daß der Katalysator
aus einem oder mehreren der Platingruppenmetalle als Metall und/oder Oxid und einem
oder mehreren Unedelmetallen als Metall und/oder Oxid besteht.
7. Sauerstoff-Verbundanode nach Anspruch 6, dadurch gekennzeichnet, daß das Unedelmetall
Titan, Zirkonium, Hafnium, Niob, Tantal, Mangan, Eisen, Kobalt, Nickel, Zinn, Blei,
Antimon und/oder Wismut ist.
8. Sauerstoff-Verbundanode nach Anspruch 6 oder 7, dadurch gekennzeichnet, daß der
Katalysator aus Ruthenium-Titan-Oxid besteht.
9. Sauerstoff-Verbundanode nach einem der Ansprüche 1 bis 8, dadurch gekennzeichnet,
daß die Träger-Teilchen aus Titan, Zirkonium, Niob der Tantal bestehen.
10. Sauerstoff-Verbundanode nach Anspruch 9, dadurch gekennzeichnet, daß die Träger-Teilchen
aus Titan-Schwamm bestehen.
11. Sauerstoff-Verbundanode nach Anspruch 10, dadurch gekennzeichnet, daß die Teilchengröße
des Titan-Schwamms zwischen 0,2 und 1,0 mm liegt.
12. Sauerstoff-Verbundanode nach einem der Ansprüche 1 bis 8, dadurch gekennzeichnet,
daß die Träger-Teilchen aus Titanoxid der allgemeinen Formel Ti02-x mit 0<x< 1 bestehen.
13. Sauerstoff-Verbundanode nach Anspruch 12, dadurch gekennzeichnet, daß die Größe
der Titanoxid-Teilchen zwischen 0,03 und 0,5 mm liegt.
14. Sauerstoff-Verbundanode nach einem der Ansprüche 1 bis 13, dadurch gekennzeichnet,
daß in den elektrisch leitenden Kunststoff ein metallischer Stromverteiler eingebettet
ist.
15. Sauerstoff-Verbundanode nach Anspruch 14, dadurch gekennzeichnet, daß der Stromverteiler
aus einem Streckmetall oder einem Metallnetz besteht.
16. Sauerstoff-Verbundanode nach Anspruch 14 oder 15, dadurch gekennzeichnet, daß
der Stromverteiler aus Titan besteht.
17. Sauerstoff-Verbundanode nach Anspruch 14 oder 15, dadurch gekennzeichnet, daß
der Stromverteiler aus Kupfer oder Aluminium besteht.
18. Verfahren zur Herstellung einer Sauerstoff-Verbundanode nach einem der Ansprüche
1 bis 17, dadurch gekennzeichnet, daß die katalytischen Teilchen gleichmäßig auf dem
elektrisch leitenden Kunststoff verteilt und bei erhöhter Temperatur unter Druck teilweise
in die Oberfläche des elektrisch leitenden Kunststoffs eingepreßt werden.
19. Verfahren zur Herstellung einer Sauerstoff-Verbundanode nach Anspruch 18, dadurch
gekennzeichnet, daß der elektrisch leitende Kunststoff mit einem metallischen Stromverteiler
bei erhöhter Temperatur unter Druck verpreßt wird.
20. Verwendung der Sauerstoff-Verbundanode nach einem der Ansprüche 1 bis 17 bei der
Metallgewinnungselektrolyse in sauren Lösungen mit einer anodischen Stromdichte von
0,3-1 kA/m2.
1. Composite oxygen anode having an electrically conductive, non-porous base member
and, partially embedded in its surface, catalytic particles of a catalyst coated onto
carrier particles, characterized in that the base member consists of electrically
conductive plastics.
2. Composite oxygen anode according to claim 1, characterized in that the electrically
conductive plastics has a thickness of at least 2 mm.
3. Composite oxygen anode according to claim 1 or 2, characterized in that the electrically
conductive plastics comprises finely divided carbon as an electrically conductive
material.
4. Composite oxygen anode according to claim 3, characterized in that the electrically
conductive plastics consists of thermoplastic resin and finely divided carbon.
5. Composite oxygen anode according to one of claims 1 to 4, characterized in that
the catalyst comprises one or more of the platinum group metals ruthenium, iridium,
palladium, platinum and rhodium as metal and/or as oxide.
6. Composite oxygen anode according to claim 5, characterized in that the catalyst
consists of one or more of the platinum group metals as metal and/or as oxide and
one or more base metals as metal and/or as oxide.
7. Composite oxygen anode according to claim 6, characterized in that the base metal
is titanium, zirconium, hafnium, niobium, tantalum, manganese, iron, cobalt, nickel,
tin, lead, antimony and/or bismuth.
8. Composite oxygen anode according to claim 6 or 7 characterized in that the catalyst
consists of ruthenium- titanium oxide.
9. Composite oxygen anode according to one of claims 1 to 8, characterized in that
the carrier particles consist of titanium, zirconium, niobium or tantalum.
10. Composite oxygen anode according to claim 9, characterized in that the carrier
particles consist of titanium sponge.
11. Composite oxygen anode according to claim 10, characterized in that the particle
size of the titan- tium sponge is between 0.2 and 1.0 mm.
12. Composite oxygen anode according to one of claims 1 to 8, characterized in that
the carrier particles consist of titanium oxide of the general formula Ti02-x with 0 is less than x is less than 1.
13. Composite oxygen anode according to claim 12, characterized in that the size of
the titanium oxide particles is between 0.03 and 0.5 mm.
14. Composite oxygen anode according to one of claims 1 to 13, characterized in that
a metallic current distributor is embedded in the electrically conductive plastics.
15. Composite oxygen anode according to claim 14, characterized in that the current
distributor consists of an expanded metal or a metallic lattice.
16. Composite oxygen anode according to claim 14 and 15, characterized in that the
current distributor consists of titanium.
17. Composite oxygen anode according to claim 14 or 15, characterized in that the
current distributor consists of copper or aluminium.
18. Process for manufacturing a composite oxygen anode according to one of claims
1 to 17, characterized in that the catalytic particles are uniformly distributed on
the electrically conductive plastics and partly pressed into to surface of the electically
conductive pastics at elevated temperature under pressure.
19. Process for the manufacturing of a composite oxygen anode according to claim 18,
characterized in that the electrically conductive plastics is impressed with a metallic
current distributor at elevated temperature under pressure.
20. Use of a composite oxygen anode according to one of claims 1 to 17, in metal recovery
electrolysis in acid solutions with an anodic current density of 0.3 to 1 kA/m2.
1. Anode composite à oxygène constituée d'un corps de base non poreux conducteur de
l'électricité et de particules catalytiques, partiellement enrobées dans sa surface,
d'un catalyseur déposé sur des particules de support, caractérisée en ce que le corps
de base consiste en une matière plastique conductrice de l'électricité.
2. Anode composite à oxygène selon la revendication 1, caractérisée en ce que la matière
plastique conductrice de l'électricité a une épaisseur d'au moins 2 mm.
3. Anode composite à oxygène selon la revendication 1 ou 2, caractérisée en ce que
la matière plastique conductrice de l'électricité contient comme matière conductrice
de l'électricité du carbon en fines paticules.
4. Anode composite à oxygène selon la revendication 3, caractérisée en ce que la matière
plastique conductrice de l'électricité consiste en une matière thermoplastique et
en du carbone en fines particules.
5. Anode composite à oxygène selon l'une des revendications 1 à 4, caractérisée en
ce que le catalyseur contient un ou plusierus des métaux du groupe du platine: ruthénium,
iridium, palladium, platine et rhodium, sous forme de métal et/ou d'oxyde.
6. Anode composite à oxygène selon la revendication 5, caractérisée en ce que le catalyseur
consiste en un ou plusieurs des métaux du groupe du platine à l'état de métal et/ou
d'oxyde et en un ou plusieurs métaux non nobles à l'état de métal et/ou d'oxyde.
7. Anode composite à oxygène selon la revendication 6, caractérisée en ce que le métal
non noble est le titane, le zirconium, le hafnium, le niobium, le tantale, le manganèse,
le fer, le cobalt, le nickel, l'étain, le plomb, l'antimoine et/ou le bismuth.
8. Anode composite à oxygène selon la revendication 6 ou 7, caractérisée en ce que
le catalyseur consiste en oxyde de ruthénium-titane.
9. Anode composite à oxygène selon l'une des revendications 1 à 8, caractérisée en
ce que les particules de support consistent en titane, zirconium, niobium ou tantale.
10. Anode composite à oxygène selon la revendication 9, caractérisée en ce que les
particules de support consistent en éponge de titane.
11. Anode composite à oxygène selon la revendication 10, caractérisée en ce que la
dimension des particules de l'éponge de titane est comprise entre 0,2 et 1,0 mm.
12. Anode composite à oxygène selon l'une des revendications 1 à 8, caractérisée en
ce que les particules de support consistent en oxyde de titane de formule générale
Ti02-x, dans laquelle 0<x< 1.
13. Anode composite à oxygène selon la revendication 12, caractérisée en ce que la
dimension des particules d'oxyde de titane est comprise entre 0,03 et 0,5 mm.
14. Anode composite à oxygène selon l'une des revendications 1 à 13, caractérisée
en ce qu'un répartiteur de courant métallique est noyé dans la matière plastique conductrice
de l'électricité.
15. Anode composite à oxygène selon la revendication 14, caractérisée en ce que le
répartiteur de courant consiste en un métal déployé ou en un treillis métallique.
16. Anode composite à oxygène selon la revendication 14 ou 15, caractérisée en ce
que le répartiteur de courant consiste en titane.
17. Anode composite à oxygène selon la revendication 14 ou 15, caractérisée en ce
que le répartiteur de courant consiste en cuivre ou en aluminium.
18. Procédé de fabrication d'une anode composite à oxygène selon l'une des revendications
1 à 17, caractérisée en ce que les particules catalytiques sont distribuées uniformément
sur la matière plastique conductrice de l'électricité et sont partiellement enfoncées
dans la surface de la matière plastique conductrice de l'électricité sous pression
à température élevée.
19. Procédé de fabrication d'une anode composite à oxygène selon la revendication
18, caractérisée en ce que la matière plastique conductrice de l'électricité est pressée
avec un répartiteur de courant métallique sons pression à température élevée.
20. Utilisation de l'anode composite à oxygène selon l'une des revendications 1 à
17 dans l'électrolyse de récupération des métaux dans des solutions acides avec une
densité de courant anodique de 0,3 - 1 kA/m2.