(19) |
 |
|
(11) |
EP 0 234 020 B1 |
(12) |
EUROPÄISCHE PATENTSCHRIFT |
(45) |
Hinweis auf die Patenterteilung: |
|
28.02.1990 Patentblatt 1990/09 |
(22) |
Anmeldetag: 10.12.1986 |
|
(51) |
Internationale Patentklassifikation (IPC)5: H01J 9/04 |
|
(54) |
Verfahren zum Herstellen eines porösen Presslings
Method of producing a porous compressed body
Procédé de fabrication d'un corps comprimé poreux
|
(84) |
Benannte Vertragsstaaten: |
|
DE FR GB |
(30) |
Priorität: |
10.01.1986 DE 3600480
|
(43) |
Veröffentlichungstag der Anmeldung: |
|
02.09.1987 Patentblatt 1987/36 |
(73) |
Patentinhaber: Licentia Patent-Verwaltungs-GmbH |
|
60596 Frankfurt (DE) |
|
(72) |
Erfinder: |
|
- Bossert, Frank, Dr.
D-7900 Ulm (DE)
- Hacker, Manfred
D-7901 Illerkirchberg 9 (DE)
|
(74) |
Vertreter: Amersbach, Werner, Dipl.-Ing. et al |
|
Licentia Patent-Verwaltungs-GmbH
Theodor-Stern-Kai 1 60596 Frankfurt 60596 Frankfurt (DE) |
(56) |
Entgegenhaltungen: :
DE-A- 3 133 754 US-A- 3 238 596 US-A- 4 215 457
|
US-A- 3 160 780 US-A- 3 623 198
|
|
|
|
|
|
|
|
|
Anmerkung: Innerhalb von neun Monaten nach der Bekanntmachung des Hinweises auf die
Erteilung des europäischen Patents kann jedermann beim Europäischen Patentamt gegen
das erteilte europäischen Patent Einspruch einlegen. Der Einspruch ist schriftlich
einzureichen und zu begründen. Er gilt erst als eingelegt, wenn die Einspruchsgebühr
entrichtet worden ist. (Art. 99(1) Europäisches Patentübereinkommen). |
[0001] Die vorliegende Erfindung betrifft ein Verfahren nach dem Oberbegriff des Patentanspruches
1.
[0002] Um schnell aufheizbare Kathoden für Wanderfeldröhren herstellen zu können, muß die
Kathodenmasse möglichst gering sein. Eine Reduzierung der Kathodenmasse ist aber bei
vorgegebener Stromdichte (Strom pro Emissionsfläche) nur über die Dicke der Kathodenpille.
möglich. Um elektronenoptischen Anforderungen zu genügen, muß die emittierende Oberfläche
kalottenförmig ausgebildet sein.
[0003] Eine weitere wichtige Anforderung ist die gleichmäßige Elektronenemission über die
gesamte Kathodenoberfläche, woraus sich die Forderung nach homogener Porosität des
Matrixkörpers ergibt.
[0004] Man versucht diesen Forderungen etwa dadurch gerecht zu werden, daß man Metallpulver
(in der Regel Wolfram oder Wolfram gemischt mit Os, Ir, Ru, Re) als zylindrische planparallele
Körper ausreichender Dicke in einen sog. Kathodenhalter preßt, bei hoher Temperatur
sintert und anschließend die Kalotte durch mechanische Bearbeitung erzeugt. Dieses
direkte Einpressen des Pulvers in dem Kathodenhalter hat gegenüber Verfahren, bei
denen Kathodenpillen ohne Kathodenhalter hergestellt werden, den Vorteil, daß das
für die Befestigung im Röhrensystem notwendige Halterungselement bereits nach dem
Sintern fest mit der Kathode verbunden ist und zusätzliche Prozesse, wie z. B. Löten
oder Schweißen nicht erforderlich sind. Durch das Pressen planparalleler Körper ist
ausreichend homogene Porositätsverteilung gewährleistet.
[0005] Beide Verfahren (mit oder ohne Kathodenhalter) haben aber die Nachteile, daß die
Herstellung der Kalotte aufwendig und teuer ist (insbesondere bei tiefen Kalotten)
und die Kathodenmasse wesentlich größer als notwendig wird, da ja im Grunde genommen
nur eine konkavkonvexe Scheibe konstanter Dicke benötigt wird.
[0006] Versucht man die konkave Kathodenoberfläche gleich beim Pressen herzustellen, indem
man den Oberstempel konvex ausbildet, so erzeugt man insbesondere bei tiefen Kalotten
durch inhomogene Verdichtung der Metallpulver inhomogene Porositätsverteilungen.
[0007] Versucht man außerdem die Kathodenmasse zu reduzieren, indem man den Kathodenhalterboden
mit einer Kalotte versieht, so wird die inhomogene Porositätsverteilung noch verstärkt.
[0008] Preßt man ohne Kathodenhalter, so hat man die äußerst schwierige und langwierige
beidseitige Bearbeitung der Kugelflächen durchzuführen, insbesondere wird dies kritisch,
wenn man berücksichtigt, daß poröse Pillen mit Dicken von 150 bis 300 µm wünschenswert
sind. Außerdem kommt das schwierige Problem der Befestigung der Kathodenpille und
die Unterdrückung von seitlicher und rückwärtiger Elektronenemission und Abdampfung
von Emissionsmaterial hinzu.
[0009] Der vorliegenden Erfindung liegt die Aufgabe zugrunde, ein Verfahren der eingangs
genannten Art so zu verbessern, daß leicht halterbare Preßlinge geringer Dicke und
hoher Gleichmäßigkeit der Porosität herstellbar sind, die bevorzugt als Vorratskörper
für Vorratskathoden von Elektronenstrahlröhren verwendbar sind.
[0010] Diese Aufgabe wird durch die im Kennzeichen des Patentanspruches 1 angegebenen Merkmale
gelöst. Beverzugte Ausführungsferner werden in den abhängigen Ansprüchen genannt.
[0011] Das beschriebene Verfahren ist geeignet pulvermetallurgische oder keramische Sinterkörper
mit konkav-konvexen Flächen mit homogener Porositätsverteilung herzustellen wobei
Masse des Körpers und Nachbearbeitungsaufwand minimiert sind. Solche Sinterteile können
z. B. als Strömungswiderstände, Filter, dauergeschmierte oder selbstschmierende Lagerteile
oder bevorzugt poröse Körper für Matrixkathoden in Elektronenstrahlröhren verwendet
werden.
[0012] Wesentliche Vorteile des erfindungsgemäßen Verfahrens zur Herstellung einer Vorratskathode
sind:
Es wird ein topfförmiges Halterungsteil mit planem Boden verwendet. Dieser Kathodenhalter
erhält erst beim Pressen seine endgültige Form. Durch den zunächst planen Boden des
Kathodenhalters ist über die gesamte Fläche homogene Verdichtung und damit homogene
Porosität möglich obwohl konkav und konvex geformte Preßstempel verwendet werden.
[0013] Durch die Verwendung eines dünnwandigen Kathodenhalters können extrem dünne Kathodenpillen
mit minimierter Masse ohne aufwendige und langwierige Nachbearbeitung hergestellt
werden.
[0014] Durch den beschriebenen Kathodenhalter und die lotfreie (gesinterte) Verbindung von
Kathodenpille und Halterungselement können auch extrem dünne Kathoden problemlos in
ein Röhrensystem integriert werden.
[0015] Bei großen Kathoden mit tiefen Kalotten sind bedeutende Material- und Bearbeitungszeiteinsparungen
möglich; dies ist vor allem von Bedeutung, wenn Platinmetalle zum Einsatz kommen,
wie bei sogenannten MM-Kathoden (MixedMetall-Kathoden).
[0016] Das beschriebene Verfahren ist bei relativ dicken Pillen auch ohne topfförmigen Kathodenhalter
durchführbar, wenn man statt des Topfes nur ein dünnes Metallplättchen einlegt. Bevorzugt
besteht der topf- oder plättchenförmige Kathodenhalter aus einem hochschmelzenden
Metall, insbesondere aus Molybdän oder Nickel. Anhand des in den Figuren 1 bis 6 beschriebenen
bevorzugten Ausführungsbeispiels wird die Erfindung nachfolgend näher erläutert.
[0017] Das Verfahren wird am Beispiel einer schnell aufheizbaren Matrixkathode für Wanderfeldröhren
erläutert. Bei dieser Anwendung ist das erfindungsgemäße Verfahren vor allem dann
von großem Vorteil, wenn relativ große Kathoden (o ≥ 3 mm) mit tiefen Kalotten gebraucht
werden.
[0018] Es wird ein dünnwandiger, z. B. 50 bis 200 11m dicker, topfförmiger Kathodenhalter
1 mit planem Boden 3 verwendet. Die Höhe dieses zylindrischen Topfes ist gleich oder
etwas größer als die sogenannte Schütthöhe des losen Pulvers 9 für entsprechende Pillendicke,
wie in Figur 1 dargestellt. Die genau bemessene Pulvermenge wird in diesem Topf 1
mit geringem Druck und planem Oberstempel 5 vorverdichtet, so daß eine parallele Schicht
2 mit mäßiger Dichte entsteht. In Figur 2 sind die weiteren Teile des Werkzeuges mit
4 und 6 bezeichnet. Die Figur 3 zeigt den Kathodenhalter 1 mit dem vorverdichteten
Preßling 2. Das Preßwerkzeug für den weiteren Verfahrensgang besteht aus einer Matrize
6 in die der Kathodenhalter 1 möglichst spielfrei paßt. Der Unterstempel 8 hat eine
kalottenförmige Stirnseite und paßt ebenfalls spielfrei in die Matrize 6.
[0019] Der Oberstempel 7 hat eine konvexe Stirnseite und paßt relativ leicht in den Kathodenhalter
1 (Figur 4).
[0020] Die Radien der beiden Stempel sind so bemessen, daß die gewünschte Form der emittierenen
Oberfläche der Kathode und gleichzeitig eine Scheibe konstanter Dicke entsteht.
[0021] Zum Pressen wird der Kathodenhalter 1 mit dem vorverdichteten Pulverpreßling 2 in
die Matrize 6 eingesetzt und mit dem notwendigen Druck die Kathodenpille 10 gepreßt.
Da die beiden Preßstempel 7 und 8 konvex und konkav ausgebildet sind und der plane
Boden 3 des Kahodenhalters i beim Preßvorgang mitverformt wird, erhält die Kathodenpille
die in den Figuren 5 und 6 gezeigte gewünschte Form als dünne konkav/konvexe Scheibe
10, ohne daß eine mechanische Nachbearbeitung erforderlich wäre. Lediglich der überstehende
Teil des Kathodenhalters 1 wird entfernt (Figur 6). Mit 11 ist die Emissionsfläche
bezeichnet.
[0022] Da die Schütthöhe im zunächst ebenen Kathodenhalter über die ganze Fläche gleich
war und die Gleitfähigkeit der einzelnen Pulverteilchen durch die Vorverdichtung drastisch
vermindert wurde, ist auch die Verdichtung und damit die Porositätsverteilung in der
konkav/konvexen Scheibe homogen.
[0023] Der Preßling wird dann in bekannter Weise noch durch Sintern bei erhöhter Temperatur
verfestigt. Dieser poröse Sinterkörper, z. B. aus überwiegend Wolfram, wird dann in
einer bekannten Weise mit einem Emissionsmaterial getränkt. Die Befestigung des Halters
3 erfolgt an einer Kathodenhülse, in deren Höhlung sich das Kathodenheizelement befindet.
[0024] Eine derart hergestellte Kathode zeigt ein außerordentlich günstiges Aufheizverhalten,
so daß sie in schnell aufheizbaren Elektronenstrahlröhren. aber auch in Langlebensdauer-Satellitenröhren
sowie in Hochleistungsröhren mit sehr großen Kathoden Anwendung findet.
1. Verfahren zum Herstellen eines porösen Preßlings mit konkav-konvexen Stirnflächen,
insbesondere eines mit einem Emissionsmaterial tränkbaren Vorratskörper für eine Matrixkathode
einer Elektronenstrahlröhre, bei dem mit einem Halterungsteil ein Pulver verpreßt
wird und die Form der Stirnflächen des Preßlings durch entsprechende Form der Stempel
eines Preßwerkzeuges erzeugt wird, dadurch gekennzeichnet daß zunächst ein vorverdichteter
Preßling (2) mit ebenen und zueinander parallelen Stirnflächen hergestellt wird und
dann dieser vorverdichtete Preßling (2) in einem weiteren Verfahrensschritt zum Preßling
(10) mit den konkav-konvexen Stirnflächen weiter verdichtet wird.
2. Verfahren nach Anspruch 1, dadurch gekennzeichnet, daß ein topfförmiges Halterungsteil
(1) mit planem Boden (3) verwendet wird, das beim Preßvorgang zusammen mit dem Pulver
entsprechend der Form der Preßstempel mitverformt wird.
3. Verfahren nach Anspruch 1 oder 2, dadurch gekennzeichnet, daß zunächst in einem
topfförmigen Halterungsteil mit planem Boden ein vorverdichteter Preßling (2) mit
ebenen und zueinander parallelen Stirnflächen hergestellt wird und dann dieser vorverdichtete
Preßling in einem weiteren Verfahrensschritt zusammen mit dem Halterungsteil zum Preßling
(10) mit den konkav-konvexen Stirnflächen weiterverdichtet wird.
4. Verfahren nach Anspruch 1, dadurch gekennzeichnet daß ein dünnes planparalleles
Plättchen als Halterungsteil verwendet wird, das dann zusammen mit dem Pulver beim
Preßvorgang entsprechend der Form der Preßstempel mitverformt wird.
5. Verfahren nach Anspruch 4, dadurch gekennzeichnet daß mit einem planparallelen
Plättchen als Halterungsteil zunächst ein vorverdichteter Preßling mit ebenen und
zueinander parallelen Flächen hergestellt wird, der dann zusammen mit dem Plättchen
beim Preßvorgang entsprechend der Form der Preßstempel mitverformt wird.
6. Verfahren nach einem der Ansprüche 1 bis 5, dadurch gekennzeichnet daß das topfförmige
Halterungsteil oder das planparallele Plättchen aus einem hochschmelzenden Metall,
insbesondere Molybdän oder Nickel, besteht.
7. Verfahren nach einem der Ansprüche 1 bis 6, dadurch gekennzeichnet, daß für das
Halterungsteil oder Plättchen ein Material verwendet wird, das vor oder während dem
Sintern des Pulverpreßlings thermisch zersetzt oder nach dem Sintern chemisch entfernt
werden kann.
8. Verfahren nach einem der Ansprüche 1 bis 7, dadurch gekennzeichnet, daß als Ausgangsmaterial
für den Preßling Metallpulver insbesondere hochschmelzender Metalle verwendet werden.
9. Verfahren nach einem der Ansprüche 1 bis 8, dadurch gekennzeichnet, daß Metallpulvermischungen
verwendet werden.
10. Verfahren nach einem der Ansprüche 1 bis 9, dadurch gekennzeichnet daß insbesondere
Wolframpulver gemischt mit Ir-, Os-, Re- oder Ru-Pulver wendet wird.
11. Verfahren nach einem der Ansprüche 1 bis 10, dadurch gekennzeichnet, daß Wolframpulver
gemischt mit 10 bis 50 Vol. % Iridium- oder Osmiumpulver verwendet wird.
12. Verfahren nach einem der Ansprüche 1 bis 11, dadurch gekennzeichnet, daß ein derart
hergestellter Preßling zusammen mit dem Halterungselement gesintert wird, in der Weise,
daß poröse Kathodenkörper hoher Festigkeit und gleichzeitig gute mechanische Verbindung
zwischen Kathodenkörper und Halterungselement erreicht wird.
13. Verfahren nach einem der Ansprüche 1 bis 12, dadurch gekennzeichnet, daß ein derart
hergestellter Kathodenkörper mit Halterungselement mit einem Emissionsmaterial getränkt
wird und als Kathode für Elektronenstrahlröhren verwendet wird.
14. Verfahren nach einem der Ansprüche 1 bis 7, dadurch gekennzeichnet, daß als Ausgangsmaterial
für den Preßling keramische Pulver verwendet werden.
1. Method for the production of a porous stamping with concaveconvex end faces, in
particular a storage body impregnable by an emissive material for a matrix cathode
of an electron beam tube, in which method a powder is compressed by a retaining part
and the shape of the end faces of the stamping is produced by corresponding shape
of the dies of a press tool, characterised thereby, that a preliminarily compacted
stamping (2) is produced initially with planar and mutually parallel end faces and
this preliminarily compacted stamping (2) is then in a further method step compacted
further into the stamping (10) with the concave-convex end faces.
2. Method according to claim 1, characterised thereby, that a pot-shaped retaining
part (1) with planar base (3) is used, which is deformed in correspondence with the
shape of the press dies together with the powder during the pressing operation.
3. Method according to claim 1 or 2, characterised thereby, that a preliminarily compacted
stamping (2) with planar and mutually parallel end faces is produced initially in
a pot-shaped retaining part with planar base and this preliminarily compacted stamping
is then in a further method step compacted further together with the retaining part
into the stamping (10) with the concave- convex end faces.
4. Method according to claim 1, characterised thereby, that a thin parallelly planar
platelet is used as retaining part which is then deformed in correspondence with the
shape of the press dies together with the powder during the pressing operation.
5. Method according to claim 4, characterised thereby, that a preliminarily compacted
stamping with planar and mutually parallel end faces is initially produced with a
thin parallelly planar platelet as retaining part and then deformed in correspondence
with the shape of the press dies together with the platelet during the pressing operation.
6. Method according to one of the claims 1 to 5, characterised thereby, that the pot-shaped
retaining part or the parallelly planar platelet consists of a metal of high melting
point, in particular molybdenum or nickel.
7. Method according to one of the claims 1 to 6, characterised thereby, that a material,
which decomposes thermally before or during the sintering of the powder stamping or
can be removed chemically after the sintering, is used for the retaining part or the
platelet.
8. Method according to one of the claims 1 to 7, characterised thereby, that metal
powders, in particular of metals of high melting point, are used as starting material
for the stamping.
9. Method according to one of the claims 1 to 8, characterised thereby, that metal
powder mixtures are used.
10. Method according to one of the claims 1 to 9, characterised thereby, that tungsten
powder mixed with Ir, Os, Re or Ru powder is used in particular.
11. Method according to one of the claims 1 to 10, characterised thereby, that tungsten
powder mixed with 10 to 50 % by volume of iridium or osmium powder is used.
12. Method according to one of the claims 1 to 11, characterised thereby, that a stamping
produced in such a manner is sintered together with the retaining element in the manner
that porous cathode bodies of great strength and a good mechanical connection between
the cathode bodies and the retaining element are achieved at the same time.
13. Method according to one of the claims 1 to 12, characterised thereby, that a cathode
body produced in such a manner with retaining element is impregnated with an emissive
material and used as cathode for electron beam tubes.
14. Method according to claims 1 to 7, characterised thereby, that ceramic powders
are used as starting material for the stamping.
1. Procédé de fabrication d'un corps comprimé poreux avec des surfaces frontales concaves-convexes,
en particulier d'un corps imprégné qui peut être imprégné par une matière émissive
pour une cathode concrétée d'un tube à faisceau électronique, dans lequel une poudre
est comprimée avec une pièce de fixation et la forme des surfaces frontales du corps
comprimé est obtenue par la forme correspondante du poinçon d'un outil de compression,
caractérisé en ce que l'on fabrique tout d'abord un corps comprimé (2) précomprimé
avec des surfaces frontales planes et parallèles l'une à l'autre et en ce que l'on
comprime ensuite encore ce corps comprimé précomprimé (2) dans une autre étape du
procédé en le corps comprimé (10) avec les surfaces frontales concaves-convexes.
2. Procédé selon la revendication 1, caractérisé en ce que l'on utilise une pièce
de fixation (1) en forme de pot à fond plan (3) qui est déformée lors du processus
de compression en même temps que la poudre de façon correspondant à la forme du poinçon
de compression.
3. Procédé selon la revendication 1 ou 2, caractérisé en ce que l'on fabrique d'abord
un corps comprimé précomprimé (2) avec des surfaces frontales planes et parallèles
l'une à l'autre dans une pièce de fixation en forme de pot à fond plan, puis en ce
que l'on comprime encore ce corps comprimé précomprimé dans une autre étape du procédé
en même temps que la pièce de fixation en le corps comprimé (10) avec les surfaces
frontales concaves-convexes.
4. Procédé selon la revendication 1, caractérisé en ce que l'on utilise comme pièce
de fixation une plaquette mince à faces planes et parallèles qui est ensuite déformée
en même temps que la poudre lors du processus de compression de façon correspondant
à la forme du poinçon de compression.
5. Procédé selon la revendication 4, caractérisé en ce que l'on fabrique tout d'abord,
avec une plaquette à faces planes et parallèles comme pièce de fixation, un corps
comprimé précomprimé à surfaces planes et parallèles entre elles, qui est ensuite
déformé en même temps que la plaquette lors du processus de compression de façon correspondant
à la forme du poinçon de compression.
6. Procédé selon l'une des revendications 1 à 5, caractérisé en ce que la pièce de
fixation en forme de pot ou la plaquette à faces planes et parallèles consiste en
un métal à haut point de fusion, en particulier en molybdène ou en nickel.
7. Procédé selon l'une des revendications 1 à 6, caractérisé en ce qu'on utilise pour
la pièce de fixation ou la plaquette un matériau qui peut être décomposé thermiquement
avant ou pendant le frittage du corps comprimé en poudre ou qui peut être éliminé
chimiquement après le frittage.
8. Procédé selon l'une des revendications 1 à 7, caractérisé en ce qu'on utilise comme
matériau de départ pour le corps comprimé une poudre métallique en particulier de
métaux à haut point de fusion.
9. Procédé selon l'une des revendications 1 à 8, caractérisé en ce que l'on utilise
des mélanges de poudres métalliques.
10. Procédé selon l'une des revendications 1 à 9, caractérisé en ce que l'on utilise
en particulier de la poudre de tungstène mélangée à de la poudre de Ir, Os, Re ou
Ru.
11. Procédé selon l'une des revendications 1 à 10, caractérisé en ce que l'on utilise
de la poudre de tungstène en mélange avec 10 à 50% en volume de poudre d'irridium
ou d'osmium.
12. Procédé selon l'une des revendications 1 à 11, caractérisé en ce que l'on fritte
un corps comprimé fabriqué de cette façon en même temps que l'élément de fixation
de façon à obtenir un corps de cathode poreux de grande résistance et en même temps
une bonne liaison mécanique entre le corps de cathode et l'élément de fixation.
13. Procédé selon l'une des revendications 1 à 12, caractérisé en ce que l'on imprègne
d'une matière émissive un corps de cathode fabriqué de cette façon avec l'élément
de fixation et en ce qu'on l'utilise comme cathode pour tubes à faisceau électronique.
14. Procédé selon l'une des revendications 1 à 7, caractérisé en ce que l'on utilise
comme matériaux de départ pour le corps comprimé des poudres céramiques.
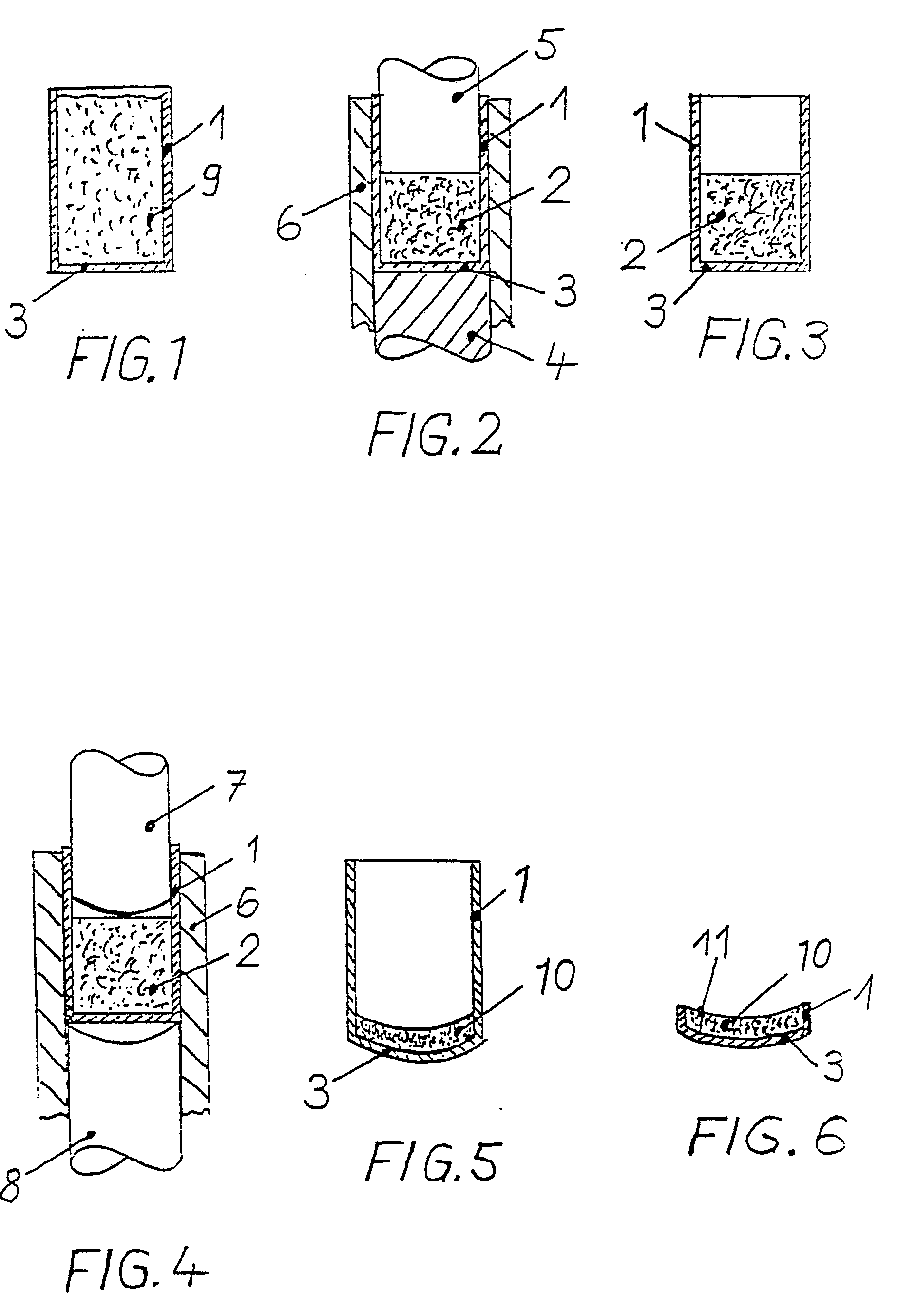