[0001] A fabric softener is a dilute solution or dispersion of a quaternary ammonium derivative
used to treat fabrics in the final rinse of a laundering process in order to make
the fabrics feel softer. In addition to softness, fabric softeners are known to also
provide fluffiness control. Because of the affinity of quaternary ammonium compounds
for negatively charged surfaces, their single largest market has been as fabric softeners.
Commercial fabric softeners generally include about a four to eight percent dispersion
of quaternary ammonium compound which is added to the rinse cycle of the washing process.
The quaternary ammonium compound can also be applied to a nonwoven sheet or a polyurethane
foam which is added with wet clothes in a dryer. Such sheets contain a fatty acid
ester which allows the quaternary ammonium compound to transfer from the sheet to
the clothes in the dryer during the drying cycle. Recently, there have been devised
combined detergent and softener formulations which allow introduction of all additives
in the wash cycle.
[0002] Modern washing machines work automatically and the operator places the laundry in
the machine, pours in the detergent and sets the controls. One set of controls determines
whether the machine employs hot, warm, or cold water. Water enters the machine through
hoses connected to the hot and cold water pipes. The operator also sets controls in
order to select the length of washing and rinsing time and the amount of water that
enters the machine. The machine is powered by an electric motor and includes a filter
that removes lint and automatic dispensers for bleach and fabric softeners. A wash
cycle typically includes four stages. In the wash cycle, after water fills the wash
tub, an agitator reverses direction alternately and moves the laundry through the
water and detergent and forces water through the items of laundry. The washer is then
emptied of all of the wash liquor in the spin cycle and the clothes are spun to remove
excess water. In the rinse cycle, clean water is added along with the fabric softener
and the clothes are again agitated. The washer is emptied of rinse liquor and the
clothes are spun in a final spin cycle during which time excess water is removed and
pumped out of the machine through a drain hose. The clothing is then ready to be removed
from the machine and dried in a dryer or hung on a clothesline until dry.
[0003] Silicone polymers can be classified as being linear, branched or crosslinked. This
classification is commonly accepted and is used in the silicone industry. Branched
or crosslinked silicone polymers are prepared by the incorporation of an alkyl trisiloxy
unit into the siloxane polymer chain. Crosslinking results when two alkyl trisiloxy
units are connected by a segment of the polymer chain during the polymerization process.
The number of polymer branches which react with another polymer (or a different alkyl
trisiloxy unit on the same polymer) to form crosslinks is a function of the amount
of alkyl trisiloxy units present and the reaction conditions. It is generally accepted
in the industry that the inclusion of alkyl trisoloxy units will lead to branching
and crosslinking when polydiorganosiloxane is prepared via addition polymerization.
Because of the random nature of this polymerization, however, alkyl trisiloxy groups
will not be incorporated into all of the polymer chains; some linear polymers will
normally be present in such systems. Incorporation of a methyl trisiloxy unit into
a polydimethylsiloxane results in a branched and crosslinked siloxane and not a linear
siloxane. The use of the branched and crosslinked fluids in a rinse cycle fabric softener
is not taught in the prior art since the incorporation of a trisiloxy unit into the
linear siloxane polymer chain creates a branched and crosslinked siloxane that has
significantly different properties. For example, linear siloxanes are soluble in toluene
whereas branched and crosslinked siloxanes are not. Thus, a toluene solubility test
provides a simple method to distinguish between linear and nonlinear polydimethylsiloxanes.
In addition to differences in solubility, linear and nonlinear polydimethylsiloxanes
exhibit different physical properties. Linear polydimethylsiloxanes are liquids which
exhibit viscous flow, even at high molecular weights. Branched or crosslinked polydimethylsiloxanes
of comparable molecular weight are elastomers. The properties of the silicone polymer
in a water-based emulsion is conveniently determined by "breaking" the emulsion by
adding large amounts of salt or alcohol, or evaporating the water and examining the
residue. Since the two classes of siloxane polymers have such significant differences
in physical properties, it would not be obvious to substitute a branched and crosslinked
siloxane for a linear siloxane in fabric softener applications.
[0004] In accordance with the present invention, therefore, a branched and crosslinked silicone
emulsion is employed in contrast to the linear material of the prior art. More importantly,
it has been found that the use of an emulsion of nonlinear silicone provides certain
advantages neither taught nor previously appreciated. For example, softener treated
fabrics in accordance with the present invention possess enhanced rewettability or
improved water absorbency, in addition to softness. Thus, while there has been previously
observed a series of benefits resulting from the incorporation in the softener formulation
of a linear silicone material, the rewettability property of the present invention
was not one of the benefits discovered, nor the feature of branching or crosslinking
in general. In the present invention, therefore, water absorptivity or rewettability
of fabrics treated with hydrophobic softening agents is significantly improved, as
is softening by the use of branched and crosslinked silicone fluid emulsions. The
use of hydrophobic silicones as taught herein to improve water absorbency of treated
fabrics is unexpected since silicones are considered to provide water repellency properties
to fabrics rather than enhanced rewettability. Thus, the opposite result would be
expected. Accordingly, the present invention provides compositions and methods of
fabric treatment possessing significant advantages over prior art materials and processes.
[0005] This invention relates to a method of enhancing the rewettability of fabrics treated
in a laundering operation by contacting the fabrics with a mixture including a rinse
cycle fabric softening conditioning composition capable of producing on the fabrics
a hydrophobic surface and a hydrophobic cationic emulsion of a silicone polymer.
[0006] The invention also relates to a method of enhancing the rewettability or water absorbency
of fabrics treated in a laundering operation by contacting the fabrics with a hydrophobic
cationic emulsion of a silicone polymer, the silicone polymer including highly branched
and crosslinked polydimethylsiloxane fluids.
[0007] The invention further relates to a fabric softening composition for enhancing the
rewettability of fabrics treated in a laundering operation which is a mixture including
a rinse cycle conditioning composition capable of producing on the fabrics a hydrophobic
surface and a hydrophobic cationic emulsion of a branched and crosslinked silicone
polymer. In preferred embodiments, the rinse cycle conditioning composition includes
a cationic compound selected from the group consisting of quaternary ammonium salts
and organic based compounds having C₁₂ to C₁₈ hydrocarbon chain molecules of amines,
esters, acids or amine oxides. As noted above, the branched and crosslinked silicone
polymer is a highly branched and crosslinked polydimethylsiloxane and the branched
and crosslinked silicone polymer includes less than about forty percent of linear
silicone polymer as determined by extraction with toluene. The cationic compound of
the rinse cycle conditioning composition preferably constitutes from about four percent
to about eight percent by weight of the rinse cycle conditioning composition and the
mixture contains from about one-half of one percent to about six percent by weight
of the silicone polymer emulsion. The emulsion of the silicone polymer contains about
thirty-five percent by weight of active ingredient, and the cationic compound of the
rinse cycle conditioning composition is dihydrogenated-tallow dimethyl ammonium chloride
in a specific embodiment. The emulsion of the silicone polymer is preferably aqueous.
[0008] It is, therefore, the object of the present invention to not only treat fabrics such
as towels, for example, in order to make them feel softer and fluffier, but in addition,
to enhance the rewettability of the towel so that the towel will be capable of absorbing
more water at the conclusion of the treating and drying cycles normally encountered
in their routine daily usage.
[0009] These and other features, objects and advantages, of the herein described present
invention will become apparent when considered in conjunction with the following detailed
description of the present invention.
[0010] Ammonium compounds in which all of the hydrogen atoms have been substituted by alkyl
groups are called quaternary ammonium salts. These compounds may be represented in
a general sense by the formula:
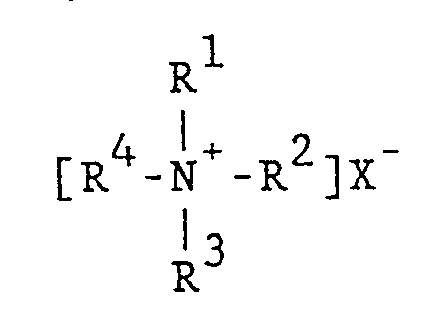
[0011] The nitrogen atom includes four covalently bonded substituents that provide a cationic
charge. The R groups can be any organic substituent that provides for a carbon and
nitrogen bond with similar and dissimilar R groups. The counterion X is typically
halogen. Use of quaternary ammonium compounds is based on the lipophilic portion of
the molecule which bears a positive charge. Since most surfaces are negatively charged,
solutions of these cationic surface active agents are readily adsorbed to the negatively
charged surface.
[0012] In accordance with the present invention, the hydrophobic softening agent can include
quaternary ammonium salts and specifically any of the cationic compounds described
in British Patent No. 1,549,180, such as quaternary mono-ammonium compounds having
either two C₁₂-C₂₀ alkyl chains or one C₁₈-C₂₄ alkyl chain; quaternary imidazolinium
textile softeners; polyammonium compounds; fabric softening polyamine salts; fully
substituted polyquaternary compounds; and polyalkylene imine salts. Particular quaternary
ammonium compounds suitable for use herein may include, for example, trimethyltallowammonium
chloride, trimethylsoyaammonium chloride, trimethylcocoammonium chloride, dimethyldicocoammonium
chloride, dimethyldi(hydrogenated tallow)ammonium chloride, trimethyldodecylammonium
chloride, trimethyloctadecylammonium chloride, trimethylhexadecylammonium chloride,
dimethylalkylbenzylammonium chloride, 1:1 mixture of trimethyltallowammonium chloride
and dimethyldicocoammonium chloride, N,N,N′,N′,N′-pentamethyl-N-tallow-1,3-propanediammonium
dichloride, methylbis(2-hydroxyethyl)cocoammonium chloride, methylpolyoxyethylene
cocoammonium chloride, methylbis(2-hydroxyethyl)oleylammonium chloride, methylpolyoxyethylene
oleyammonium chloride, methylbis(2-hydroxyethyl)oleylammonium chloride, methylbis(2-hydroxyethyl)octadecylammonium
chloride, methylpolyoxyethylene octadecylammonium chloride, n-dodecyl tetradecyl dimethylbenzylammonium
chloride, n-tetradecyl hexadecyl dimethylbenzylammonium chloride, n-dodecyl tetradecyl
dimethyldichlorobenzylammonium chloride, n-octadecyldimethylbenzylammonium chloride,
dialkylmethylbenzylammonium chloride, n-dodecyl tetradecyl hexadecyl dimethylbenzylammonium
chloride, n-dodecyl tetradecyl hexadecyl dimethylethylbenzylammonium chloride, methyl
sulfate quaternary of ethyoxylated tallow diethylenetriamine condensate, methyl sulfate
quaternary of propoxylated tallow diethylenetriamine condensate and 1-(tallow amidoethylene)-2-n(tallow
alkyl)2-imidazolinium, methyl sulfate quaternary.
[0013] The silicone compositions of the present invention that enhance the rewettability
of fabrics treated in a laundry operation are primarily highly branched and crosslinked
polydimethylsiloxanes and substituted derivatives, such as organofunctional silicones.
The resulting enhanced rewettability is independent of the siloxane molecular weight.
If the silicone polymer is substituted with organofunctional groups, the resulting
polymer must be hydrophobic to improve rewettability. The hydrophobic silicones are
delivered to the fabric as an emulsion. The silicone emulsions can be used alone or
formulated into a fabric conditioning composition, such as a rinse cycle fabric softener.
The quaternary ammonium salt based type of rinse cycle fabric softeners are preferred.
[0014] While the following examples are combinations of quaternary based softeners with
silicone emulsions, the silicone compositions will improve water absorbancy when used
in combination with any organic based fabric conditioning composition that produces
a hydrophobic surface, such as organic conditioning compositions comprised of long
hydrocarbon C₁₂-C₁₈ chain molecules of amines, esters, acids, amine oxides and derivatives
thereof.
[0015] The polydimethylsiloxanes used herein are high molecular weight branched and crosslinked
polymers having a molecular weight of at least 100,000 and a viscosity above 50,000
centistokes. The viscosity of such a polydimethylsiloxane is highly dependent on
the degree of branching and crosslinking present in the polymer. When the ratio of
alkyl trisiloxy units to dimethyl siloxy units exceeds about 1:100, the polymer can
no longer be considered a fluid with a measurable viscosity; it is an elastomer. The
siloxane polymers of the present invention are generally terminated by a hydroxyl
group. Endblocking species such as trimethyl siloxy units are not included in the
compositions of the present invention because this would prevent the polymer from
reaching the desired molecular weight. The polymers can be prepared by various techniques
such as the hydrolysis and subsequent condensation of dimethyldihalosilanes, or by
the cracking and subsequent condensation of dimethylcyclosiloxanes. The polymer can
be based on a branched and crosslinked silicone made by the addition of branching
units of methyl trimethoxysilane to polydimethylsiloxane by conventional techniques,
in a preferred mode.
Example I
[0016] Towels were prepared for treatment by removing the mill textile conditioners applied
at the mill during manufacture of the towels. The process was conducted at a commercial
laundromat. Bundles of 86:14 cotton polyester terry towels were washed three times
with a 9.8% phosphorous containing Tide® detergent followed by three washes with a
0.5% phosphorus containing Tide®. Tide® is an anionic detergent and a trademark of
the Procter & Gamble Company, Cincinnati, Ohio. The towels were subjected to a final
wash and rinse cycle from which detergent was omitted, in order to remove any residual
detergent. The treatments were conducted in a Whirlpool Imperial Seventy washing machine.
The Cycle Setting was Heavy/14 minutes. The Cloth to Liquor Ratio was 1:23. The Wash
Temperature was Warm (32°C.). The Rinse Temperature was Cold (11°C.). The Detergent
Concentration was 0.14% detergent by weight of wash liquor. The Dryer was a Whirlpool
model with a Dryer Setting of Permanent Press-High Drying, at a time of 55 minutes.
[0017] The test used to measure softness was a panel test in which ten people were asked
to rank several towels in order of softness, one being a control towel which had not
been treated with a softening agent. The towels were treated by the method described
above. Following treatment, the towels were placed in a constant temperature and humidity
room over night and tested the following day. Ten people were asked to evaluate the
towels by feeling the towels and choosing the harshest towel, the softest towel and
placing the remaining towels in order of increasing softness. The towels were assigned
a numerical ranking with the highest value corresponding to the softest towel. Since
the softness of a towel increases with repeated handling, a new surface of each towel
was exposed for each panel member and each towel was replaced after evaluation by
three people. The resulting rankings were averaged to provide a single integer for
each treatment.
[0018] The rewettability or water absorbency of the treated towels was determined by the
wicking method in which strips of fabric are suspended in a solution of water soluble
dye and the height of migration of the dye solution is measured over a specified time.
The greater height of migration of the dye solution up the fabric is indicative of
better rewet properties.
[0019] The height to which the dye solution had risen was measured after the strip had been
immersed for four minutes and the variability of the test method was +/- 6.9 mm.
[0020] Fabric softener formulations containing varying amounts of an emulsion of highly
branched and crosslinked silicone polymer were evaluated for softening and rewettability.
As noted above, terry towels of 86:14 cotton/polyester were treated with detergent
and softeners were added in the rinse cycle at a softener/fabric weight ratio of 1:30.
Each of the formulations employed included five percent dihydrogenated tallow dimethylammonium
chloride(DTDMAC), the active ingredient of a quaternary ammonium salt commercial fabric
softener dispersion, manufactured by Sherex Chemical Company, Dublin, Ohio, as ADOGEN®
442, a trademark of that company; together with varying amounts of the composition
of the present invention in amounts of one, two, four and six percent concentrations,
respectively. One control of DTDMAC without the composition of the present invention
was employed for comparative purposes. The five percent DTDMAC quaternary ammonium
salt softener was prepared by melting dihydrogenated tallow dimethylammonium chloride
and adding the molten material to hot water under agitation. The softener was stirred
until cool. Sodium chloride was included in order to lower the viscosity and ethanol
was added in order to assist in solubilizing the softener. The composition of the
present invention included therein was a thirty-five percent aqueous hydrophobic cationic
emulsion of a highly branched and crosslinked polydimethylsiloxane fluid including
less than about forty percent of linear silicone polymer. A series of five treatments
were conducted and evaluations were made following the first, third and fifth treatments.
Average softness rankings are set forth in Table I.
TABLE I
COMPOSITION |
TREATMENT |
% Softener* |
Silicone % |
No. I |
No. III |
No. V |
100 |
--- |
1.9 |
1.2 |
1.0 |
99 |
1.0 |
3.0 |
2.6 |
2.3 |
98 |
2.0 |
3.2 |
3.7 |
3.7 |
96 |
4.0 |
3.6 |
4.5 |
4.0 |
94 |
6.0 |
3.3 |
3.0 |
4.0 |
[0021] It should be apparent from Table I that the softener ingredient containing the higher
levels of the compositions of the present invention imparted the best softness. The
rewettability of each of the foregoing is set forth in Table II and it should be pointed
out, that the average rewettability imparted to each fabric was enhanced by the softeners
including the compositions of the present invention.
TABLE II
COMPOSITION |
REWETTABILITY mm/4 minutes |
% Softener* |
Silicone % |
|
100 |
--- |
42 |
99 |
1.0 |
53 |
98 |
2.0 |
55 |
96 |
4.0 |
57 |
94 |
6.0 |
58 |
Example II
[0022] Example I was repeated except that the softener DTDMAC was replaced by a commercial
grade rinse cycle fabric softening product. The product was an aqueous dispersion
of fabric softening agents including about five percent DTDMAC as the active softening
agent. The branched and crosslinked composition of the present invention employed
in Example I was again used in this example. The results are set forth in Table III.
TABLE III
COMPOSITION |
TREATMENT |
% Softener* |
Silicone % |
No. I |
No. III |
No. V |
100 |
--- |
3.3 |
2.6 |
4.1 |
99.5 |
0.5 |
3.9 |
2.4 |
1.8 |
99 |
1.0 |
2.3 |
3.5 |
3.6 |
98 |
2.0 |
2.9 |
4.7 |
4.8 |
96 |
4.0 |
5.1 |
4.7 |
3.0 |
* = Dispersion which contains 5% DTDMAC as the active softening agent. |
[0023] The rewettability of each of the foregoing is set forth in Table IV and it should
be pointed out, that the average rewettability imparted to each fabric was enhanced
by the softeners including the compositions of the present invention.
TABLE IV
COMPOSITION |
REWETTABILITY mm/4 minutes |
% Softener* |
Silicone % |
|
100 |
--- |
37 |
99.5 |
0.5 |
49 |
99 |
1.0 |
47 |
98 |
2.0 |
58 |
96 |
4.0 |
58 |
Example III
[0024] Example II was repeated again using the commercial grade rinse cycle fabric softening
product of Example II which was an aqueous dispersion of fabric softening agents including
five percent DTDMAC as the active softening agent. For purposes of comparison, there
was employed a series of emulsions of silicone compositions having varying amounts
of linear siloxane content. These emulsions were added to the commercial softener
at a level of two percent by weight. The silicone emulsions contained mixtures of
linear and nonlinear siloxanes with the percentage of linear polymers ranging from
about twelve percent to about thirty-five percent indicating a branched and crosslinked
siloxane content ranging from about sixty-five percent to as high as eighty-eight
percent. The linear polymer content for the emulsions was determined by toluene extraction
of dried samples of emulsion. The results are set forth in Tables V and VI.
TABLE V
COMPOSITION |
TREATMENT |
%Silicone |
%Softener* |
%Branching/Crosslinking |
No. I |
No. III |
No. V |
2 |
98 |
--- |
4.0 |
2.9 |
2.5 |
2 |
98 |
65 |
3.5 |
3.2 |
3.1 |
2 |
98 |
65 |
3.8 |
4.2 |
4.6 |
2 |
98 |
88 |
2.7 |
4.2 |
3.9 |
2 |
98 |
65 |
5.2 |
3.8 |
3.7 |
[0025] The rewettability of each of the foregoing is set forth in Table VI and it should
be pointed out, that the average rewettability imparted to each fabric was enhanced
by the softeners including the branched and crosslinked compositions of the present
invention.
TABLE VI
COMPOSITION |
REWETTABILITY |
%Silicone |
%Softener* |
%Branching/Crosslinking |
mm/4 minutes |
2 |
98 |
--- |
43 |
2 |
98 |
65 |
56 |
2 |
98 |
65 |
58 |
2 |
98 |
88 |
59 |
2 |
98 |
65 |
51 |
[0026] The branched and crosslinked silicone polymers employed herein and methods for their
preparation are described in more or less detail in U.S. Patent No. 2,891,920, issued
June 23, 1959. These materials can be any organosiloxane of the formula:
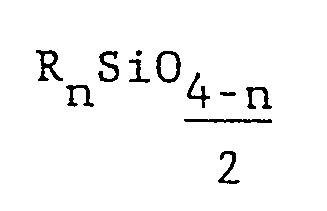
in which R is selected from the group consisting of monovalent hydrocarbon radicals,
halogenated monovalent hydrocarbon radicals and hydrogen atoms; and in which n is
an interger having an average value of from one to less than three. However, for purposes
of illustration, a procedure for the preparation of a representative branched and
crosslinked silicone polymer of the present invention is set forth in the following
examples.
Example IV
[0027] 88 grams of a 27% water solution of tallow trimethyl ammonium chloride was added
to 535 grams of water until a uniform mixture was obtained. To this mixture was added
350 grams of octamethylcyclotetrasiloxane and 6.5 grams of methyl trimethoxysilane
followed by vigorous stirring. The resulting emulsion was passed twice through a homogenizer
set at 7500 psig. The emulsion was then made alkaline by the addition of 1 gram of
a 50% sodium hydroxide solution. The emulsion was heated at 85°C. for 9 hours. After
cooling to 40°C., 1.5 grams of 85% phosphoric acid was added and stirred for 5 minutes
followed by the addition of MAKON® 10, a nonyl phenoxy-polyethylene oxide surfactant.
The emulsion was allowed to stir for 1 hour at 40°C. Upon cooling to room temperature,
0.5 grams of KATHON® CG/ICP, a preservative, was added.
[0028] Whereas Example IV is specific to methyl trimethoxysilane, branching may also be
obtained with materials such as (CH₃O)₃Si(CH₂)₃ NHCH₂CH₂NH₂ and (CH₃O)₃Si(CH₂)₃N
⊕(CH₃)₂(CH₂)₁₇CH₃Cl
⊖.
[0029] Compositions prepared in accordance with Example IV, when tested in accordance with
the procedures of Example II, yielded the following rewettability data.
TABLE VII
TREATMENTS |
REWETTABILITY mm/4 minutes |
1 |
62 |
2 |
42 |
3 |
56 |
4 |
58 |
5 |
58 |
6 |
62 |
[0030] Additional compositions prepared as in Example IV were further tested in accordance
with the procedure of Example II except that instead of employing the aqueous dispersion
of softening agents including 5% DTDMAC, there was used two commercial rinse cycle
fabric softening products marketed for home use. Both products are manufactured by
Lever Brothers Company, New York, New York and sold under the trademarks SNUGGLE®
and FINAL TOUCH®. Data from these tests are set forth hereinbelow.
TABLE VIII
COMPOSITION |
TREATMENT |
% Softener* |
Silicone % |
No. I |
No. III |
100 |
--- |
4.5 |
4.0 |
99.5 |
0.5 |
3.8 |
4.8 |
99 |
1.0 |
3.1 |
2.7 |
98 |
2.0 |
4.6 |
4.5 |
96 |
4.0 |
3.8 |
4.0 |
TABLE IX
COMPOSITION |
TREATMENT |
% Softener* |
Silicone % |
No. I |
No. III |
100 |
--- |
4.1 |
3.75 |
99.5 |
0.5 |
3.2 |
3.75 |
99 |
1.0 |
5.3 |
4.17 |
98 |
2.0 |
2.8 |
3.5 |
96 |
4.0 |
4.6 |
4.83 |
TABLE X
COMPOSITION |
REWETTABILITY mm/4 Minutes |
% Softener* |
Silicone % |
TREATMENT |
|
|
No. I |
No. III |
100 |
--- |
48 |
37 |
99.5 |
0.5 |
48.5 |
51 |
99 |
1.0 |
50 |
54 |
98 |
2.0 |
48 |
55 |
96 |
4.0 |
51 |
54.5 |
TABLE XI
COMPOSITION |
REWETTABILITY mm/4 Minutes |
% Softener* |
Silicone % |
TREATMENT |
|
|
No. I |
No. III |
100 |
--- |
31 |
31.5 |
99.5 |
0.5 |
40 |
44 |
99 |
1.0 |
47.5 |
51.5 |
98 |
2.0 |
48 |
51.5 |
96 |
4.0 |
50 |
52 |
[0031] A procedure for the preparation of another representative branched and crosslinked
silicone polymer of the present invention is set forth in the following examples.
Example V
[0032] 88 grams of a 27% water solution of tallow trimethyl ammonium chloride was added
to 535 grams of water until a uniform mixture was obtained. To this mixture was added
350 grams of octamethylcyclotetrasiloxane and 7.5 grams of methyl trimethoxysilane
followed by vigorous stirring. The resulting emulsion was passed twice through a homogenizer
set at 7500 psig. The emulsion was then made alkaline by the addition of 1 gram of
a 50% sodium hydroxide solution. The emulsion was heated at 85°C. for 9 hours. After
cooling to 40°C., 1.5 grams of 85% phosphoric acid was added and stirred for 5 minutes
followed by the addition of MAKON® 10, a nonyl phenoxy-polyethylene oxide surfactant.
The emulsion was allowed to stir for 1 hour at 40°C. Upon cooling to room temperature,
0.5 grams of KATHON® CG/ICP, a preservative, was added.
[0033] Compositions prepared in accordance with Example V, were tested in accordance with
the procedures of Example II, except that SNUGGLE® was again employed and such tests
yielded the following data.
TABLE XII
COMPOSITION |
TREATMENT |
% Softener* |
Silicone % |
No. I |
No. III |
100 |
--- |
3.55 |
3.0 |
98 |
2.0 |
3.82 |
3.8 |
TABLE XIII
COMPOSITION |
REWETTABILITY mm/4 Minutes |
% Softener* |
Silicone % |
TREATMENT |
|
|
No. I |
No. III |
100 |
--- |
35 |
40.5 |
98 |
2.0 |
53 |
51 |
[0034] A further procedure for the preparation of an additional representative branched
and crosslinked silicone polymer of the present invention is set forth in the following
examples.
Example VI
[0035] 88 grams of a 27% water solution of tallow trimethyl ammonium chloride was added
to 535 grams of water until a uniform mixture was obtained. To this mixture was added
350 grams of octamethylcyclotetrasiloxane and 35.0 grams of methyl trimethoxysilane
followed by vigorous stirring. The resulting emulsion was passed twice through a homogenizer
set at 7500 psig. The emulsion was then made alkaline by the addition of 1 gram of
a 50% sodium hydroxide solution. The emulsion was heated at 85°C. for 9 hours. After
cooling to 40°C., 1.5 grams of 85% phosphoric acid was added and stirred for 5 minutes
followed by the addition of MAKON® 10, a nonyl phenoxy-polyethylene oxide surfactant.
The emulsion was allowed to stir for 1 hour at 40°C. Upon cooling to room temperature,
0.5 grams of KATHON® CG/ICP, a preservative, was added.
[0036] Compositions prepared in accordance with Example VI, were tested in accordance with
the procedures of Example II, again using SNUGGLE® and yielded the following data.
TABLE XIV
COMPOSITION |
TREATMENT |
% Softener* |
Silicone % |
No. I |
No. III |
100 |
--- |
3.55 |
3.0 |
98 |
2.0 |
3.55 |
3.4 |
TABLE XV
COMPOSITION |
REWETTABILITY mm/4 Minutes |
% Softener* |
Silicone % |
TREATMENT |
|
|
No. I |
No. III |
100 |
--- |
35 |
40.5 |
98 |
2.0 |
48 |
54 |
[0037] Generically, the branched and crosslinked siloxanes set forth in the foregoing examples
are of the general formula:
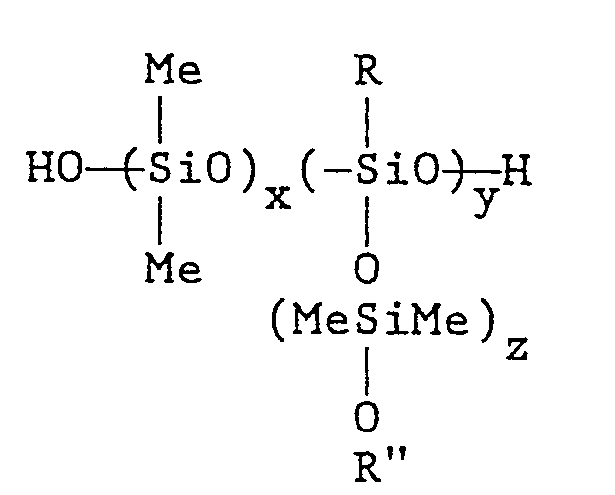
wherein:
Me is methyl;
x and z have values of 3 to 100,000;
y has a value of 1 to 10,000;
R is (CH₂)
nZ;
R˝ is hydrogen or
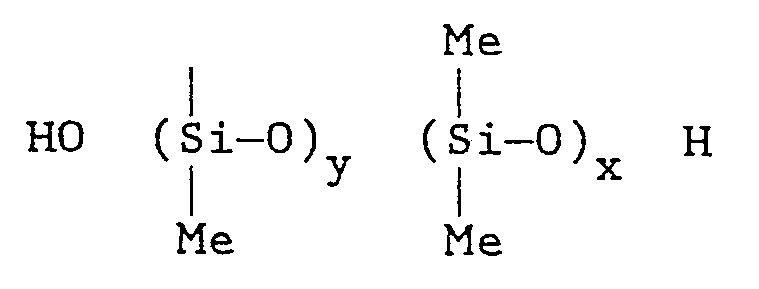
n has a value of 1 to 10;
Z is
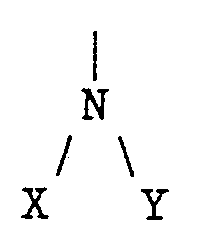
whereby X and Y are selected independently, -H; -C₁₋₃₀-alkyl; -C₆-aryl; -C₅₋₆-cycloalkyl;
-C₁₋₆-NH₂; -CO-R′; with the proviso that the nitrogen can be quaternized such as to
represent

whereby W can be selected from X or Y; or Z is
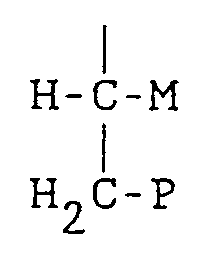
whereby P and M are -COOH; -CO-NR′₂; or C₁₋₂-alkyl; where R′=C₁₋₄ alkyl.
[0038] It will be apparent from the foregoing that many other variations and modifications
may be made in the structures, compounds, compositions and methods described herein
without departing substantially from the essential features and concepts of the present
invention. Accordingly, it should be clearly understood that the forms of the invention
described herein are exemplary only and are not intended as limitations on the scope
of the present invention.
1. The method of enhancing the rewettability of fabrics treated in a laundering operation
comprising contacting the fabrics with a mixture including a rinse cycle fabric softening
conditioning composition capable of producing a hydrophobic surface on the fabrics
and a hydrophobic cationic emulsion of a highly branched and crosslinked silicone
polymer, the polymer being an organosiloxane of the formula:
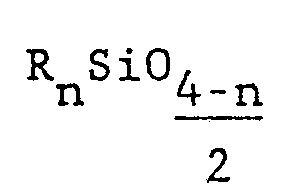
in which R is selected from the group consisting of monovalent hydrocarbon radicals,
halogenated monovalent hydrocarbon radicals and hydrogen atoms; and in which n is
an interger having an average value of from one to less than three, the branched and
crosslinked silicone polymer including less than about forty percent of linear silicone
polymer as determined by extraction with toluene.
2. The method of claim 1 in which the fabric softening conditioning composition includes
a cationic compound selected from the group consisting of quaternary ammonium salts
and organic based compounds having C₁₂ to C₁₈ hydrocarbon chain molecules of amines,
esters, acids or amine oxides.
3. The method of enhancing the rewettability of fabrics treated in a laundering operation
comprising contacting the fabrics with a hydrophobic cationic emulsion of a highly
branched and crosslinked silicone polymer, the polymer being an organosiloxane of
the formula:
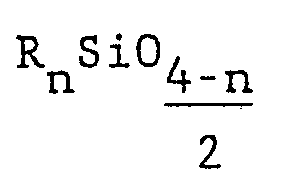
in which R is selected from the group consisting of monovalent hydrocarbon radicals,
halogenated monovalent hydrocarbon radicals and hydrogen atoms; and in which n is
an interger having an average value of from one to less than three, the branched and
crosslinked silicone polymer being essentially a polydimethylsiloxane, the branched
and crosslinked silicone polymer further including less than about forty percent of
linear silicone polymer as determined by extraction with toluene.
4. A fabric softening composition having rewet properties for enhancing the rewettability
of fabrics treated in a laundering operation comprising a mixture including a rinse
cycle conditioning composition capable of producing on the fabrics a hydrophobic surface
and a hydrophobic cationic emulsion of a highly branched and crosslinked silicone
polymer, the polymer being an organosiloxane of the formula:
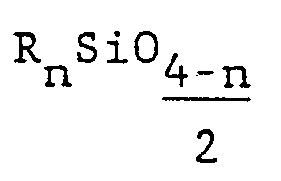
in which R is selected from the group consisting of monovalent hydrocarbon radicals,
halogenated monovalent hydrocarbon radicals and hydrogen atoms; and in which n is
an interger having an average value of from one to less than three, the branched and
crosslinked silicone polymer further including less than about forty percent of linear
silicone polymer as determined by extraction with toluene.
5. The composition of claim 4 in which the rinse cycle conditioning composition includes
a cationic compound selected from the group consisting of quaternary ammonium salts
and organic based compounds having C₁₂ to C₁₈ hydrocarbon chain molecules of amines,
esters, acids or amine oxides.
6. The method of enhancing the rewettability of fabrics treated in a laundering operation
comprising contacting the fabrics with a mixture including a rinse cycle fabric softening
conditioning composition capable of producing on the fabrics a hydrophobic surface
and a hydrophobic cationic emulsion of a silicone polymer having the general formula:
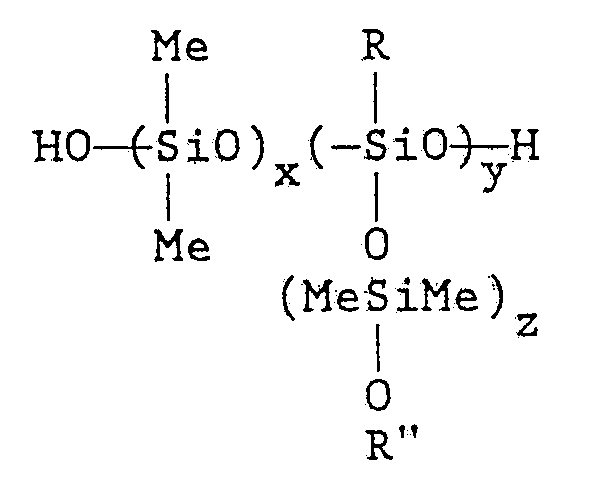
wherein:
Me is methyl;
x and z have values of 3 to 100,000;
y has a value of 1 to 10,000;
R is (CH₂)
nZ;
R˝ is hydrogen or
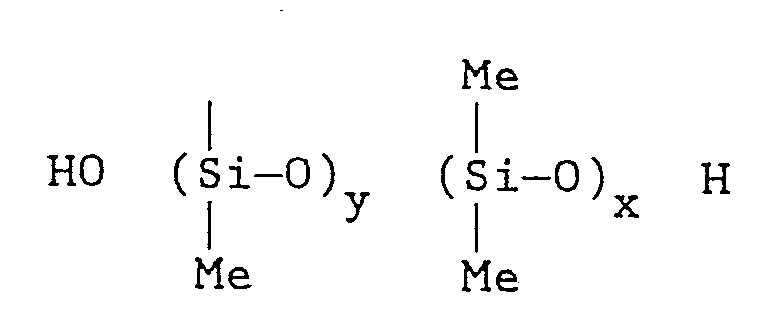
n has a value of 1 to 10;
Z is

whereby X and Y are selected independently, -H; -C₁₋₃₀-alkyl; -C₆-aryl; -C₅₋₆-cycloalkyl;
-C₁₋₆-NH₂; -CO-R′; with the proviso that the nitrogen can be quaternized such as to
represent
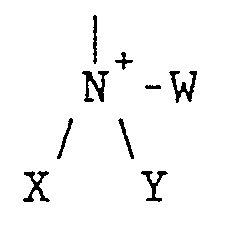
whereby W can be selected from X or Y; or Z is
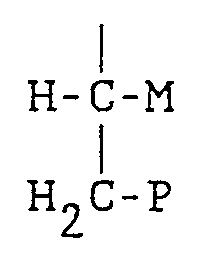
whereby P and M are -COOH; -CO-NR′₂; or C₁₋₂-alkyl; where R′=C₁₋₄ alkyl.
7. The method of enhancing the rewettability of fabrics treated in a laundering operation
comprising contacting the fabrics with a hydrophobic cationic emulsion of a silicone
polymer, the silicone polymer being a polydimethylsiloxane having the general formula:
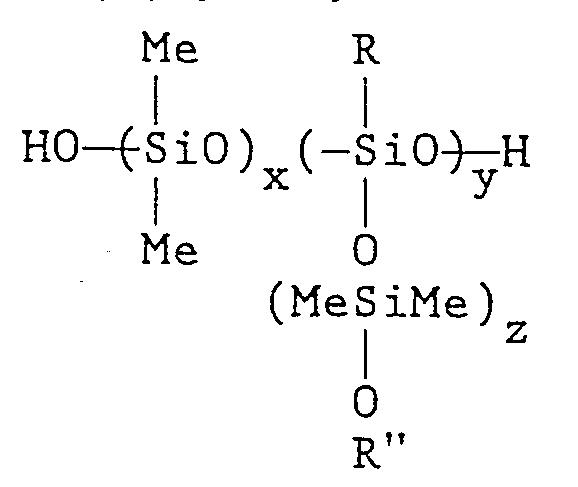
wherein:
Me is methyl;
x and z have values of 3 to 100,000;
y has a value of 1 to 10,000;
R is (CH₂)
nZ;
R˝ is hydrogen or
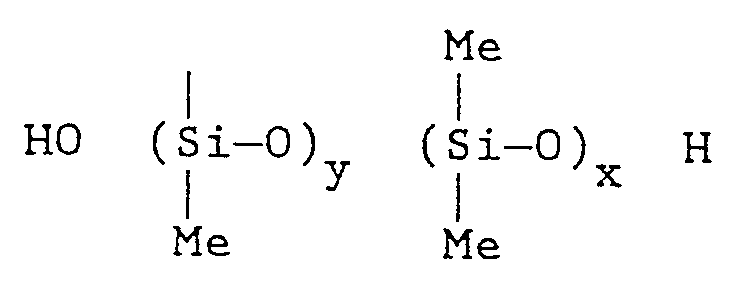
n has a value of 1 to 10;
Z is

whereby X and Y are selected independently, -H; -C₁₋₃₀-alkyl; -C₆-aryl; -C₅₋₆-cycloalkyl;
-C₁₋₆-NH₂; -CO-R′; with the proviso that the nitrogen can be quaternized such as to
represent
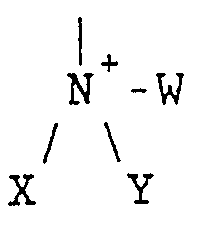
whereby W can be selected from X or Y; or Z is

whereby P and M are -COOH; -CO-NR′₂; or C₁₋₂-alkyl; where R′=C₁₋₄ alkyl.
8. A fabric softening composition having rewet properties for enhancing the rewettability
of fabrics treated in a laundering operation comprising a mixture including a rinse
cycle conditioning composition capable of producing on the fabrics a hydrophobic surface
and a hydrophobic cationic emulsion of a silicone polymer having the general formula:
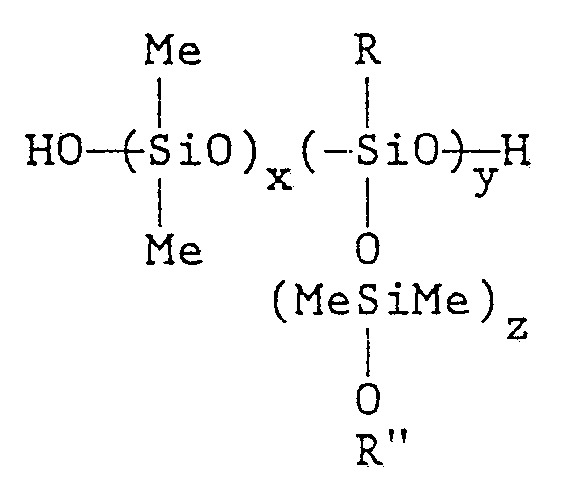
wherein:
Me is methyl;
x and z have values of 3 to 100,000;
y has a value of 1 to 10,000;
R is (CH₂)
nZ;
R˝ is hydrogen or
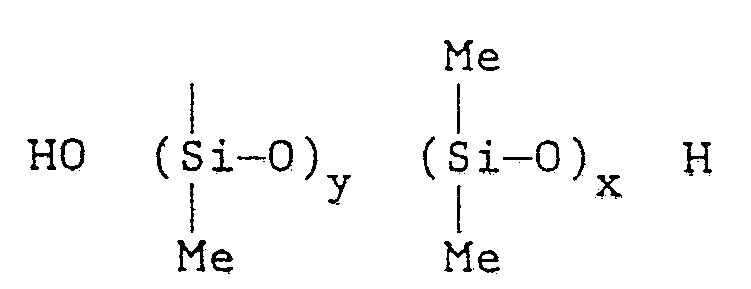
n has a value of 1 to 10;
z is
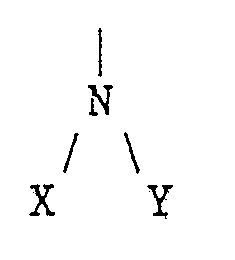
whereby X and Y are selected independently, -H; -C₁₋₃₀-alkyl; -C₆-aryl; -C₅₋₆-cycloalkyl;
-C₁₋₆-NH₂; -CO-R′; with the proviso that the nitrogen can be quaternized such as to
represent
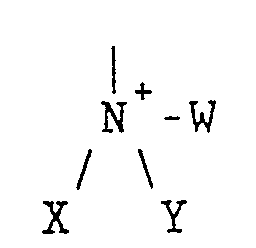
whereby W can be selected from X or Y; or Z is

whereby P and M are -COOH; -CO-NR′₂; or C₁₋₂-alkyl; where R′=C₁₋₄ alkyl.
9. The method of enhancing the rewettability of fabrics treated in a laundering operation
comprising contacting the fabrics with a mixture including a rinse cycle fabric softening
conditioning composition capable of producing a hydrophobic surface on the fabrics
and a hydrophobic cationic emulsion of a highly branched silicone polymer, the polymer
being an organosiloxane of the formula:
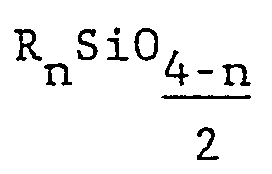
in which R is selected from the group consisting of monovalent hydrocarbon radicals,
halogenated monovalent hydrocarbon radicals and hydrogen atoms; and in which n is
an interger having an average value of from one to less than three.
10. The method of enhancing the rewettability of fabrics treated in a laundering operation
comprising contacting the fabrics with a hydrophobic cationic emulsion of a highly
branched silicone polymer, the polymer being an organosiloxane of the formula:
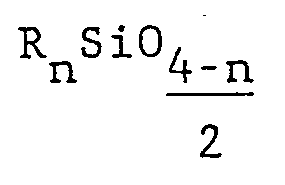
in which R is selected from the group consisting of monovalent hydrocarbon radicals,
halogenated monovalent hydrocarbon radicals and hydrogen atoms; and in which n is
an interger having an average value of from one to less than three, the branched and
crosslinked silicone polymer being essentially a polydimethylsiloxane.
11. A fabric softening composition having rewet properties for enhancing the rewettability
of fabrics treated in a laundering operation comprising a mixture including a rinse
cycle conditioning composition capable of producing on the fabrics a hydrophobic surface
and a hydrophobic cationic emulsion of a highly branched silicone polymer, the polymer
being an organosiloxane of the formula:
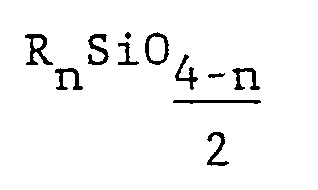
in which R is selected from the group consisting of monovalent hydrocarbon radicals,
halogenated monovalent hydrocarbon radicals and hydrogen atoms; and in which n is
an interger having an average value of from one to less than three.