[0001] This invention relates to nonapertured, heavyweight nonwoven fabric made from hydraulically
entangled staple fibers of synthetic organic polymer. More particularly, the invention
concerns such a fabric having unusually strong tensile characteristics and high resistance
to disentanglement.
[0002] Nonwoven fabrics, in which hydraulically entangled staple fibers of synthetic organic
polymer form a stable, nonapertured fabric without the presence of resin binder of
fiber-to-fiber melt bonds are known in the art. Such fabrics have been manufactured
commercially with unit weights that are usually less than 4 oz/yd
2 [136 g/m
2]. Bunting et al, U.S. Patents 3,493,462, 3,508,308 and 3,560,326 disclose a wide
variety of such fabrics with unit weights as high as about 20 ozlyd
2 [680 g/m
2]. The commercially manufactured nonapertured fabrics of hydraulically entangled staple
fibers are strong and exhibit strip tensile strengths of as high as about 8.5 (Ib/in)/oz/yd
2) [0.44 (N/cm)/(g/m
2)]. However, the heavy-weight fabrics of this type which were disclosed by Bunting
et al were relatively weak. For example, such heavyweight fabrics had strip tensile
strengths of 4.39 (Ib/in)/(oz/yd) [0.226 (N/cm)/g/m
2)] at a weight of 6.7 oz/yd
2 [227 g/m
2] and 1.3 and 1.1 (lb/in)/(ozlyd
2) [0.067 and 0.059 (N/cm)/(glm
2)] for weights of 10 and 20 ozlyd
2 [339 and 678 g/m
2], respectively.
[0003] To strengthen these hydraulically entangled staple fiber nonwoven fabrics, arious
approaches have been made. These included incorporating in the fabrics very long (e.g.,
6 inch [15.24 cm]) fibers, fibers of special cross-section, substantially continuous
filaments, scrims, layers of continuous filament webs, or specially designed layers.
Process modifications intended to provide the increase in strength included treating
the staple fiber starting web with hydraulic jets first with the web moving in one
direction and then with the web moving in a direction perpendicular to the first direction,
adding special chemical agents to the hydraulic jets, utilizing special supports or
grills on which the webs were hydraulically treated, and starting with special yarns.
Generally, each of these strength increasing modifications were useful for lighter
weight fabrics. However, these modifications generally were not satisfactory for preparing
strong, heavy weight, nonapertured nonwoven fabrics, which consisted essentially of
hydraulically entangled staple fibers of synthetic organic polymer. Such strong, heavy-weight
fabrics are desired in uses such as heavy-duty gas filtration. The purpose of this
invention is to provide such a strong nonapertured, heavy- weight nonwoven fabric.
[0004] The present invention provides an improved heavy-weight, nonapertured nonwoven fabric
which consists essentially of hydraulically entangled staple fibers of synthetic organic
polymer. The improvement comprises the fabric having in combination a unit weight
in the range of 200 to 850 g/m
2 [6-25 oz/yd
2], a grab strength of at least 160 N/cm [91 Ib/in], a strip tensile strength of at
least 0.26 (N/cm)/(g/m
2) [5 (lb/in)/ (ozlyd
2)] and a resistance to disentanglement of at least 50 alternate extension cycles.
Preferably, the fabric combines a unit weight in the range of 240 to 510 g/m
2 [7-15 oz/yd
2], a grab strength in the range of 245 to 875 N/cm [140-500 Ib/in], a strip tensile
strength in the range of 0.36 to 0.77 (N/cm)/(g/m
2) [7-15 (lb/in)/oz/ yd 2) and a resistance to disentanglement of at least 90 alternate
extension cycles. Usually, the preferred fabrics have 3 to 10 jet tracks per centimeter
[7.5-25 per inch]. The preferred staple fibers are of 1 to 18 dtex [0.9-16 den] and
of 0.6 to 5 cm [1/4 to 2 inch] length. Preferred polymers for the staple fibers are
poly-(p-phenylene terephthalamide), poly(m-phenylene isophthalamide) or poly(ethylene
terephthalate).
[0005] The invention also provides a novel process for preparing heavy-weight, nonapertured,
nonwoven fabric by treating batts of staple fibers of synthetic organic polymer with
rows of fine columnar streams of water while the batts are supported on a foraminous
screen and are moving perpendicular to the rows of streams. The process is characterized
by, for stronger fabrics, preparing the fabric from batts having a unit weight of
200 to 850 g/m
2 and consisting essentially of staple fibers having a length in the range of 0.6 to
5 cm and a decitex in the range of 1 to 18, the batts being treated immediately after
preliminary consolidation and wetting by a row of streams which forces portions of
staple fibers from one surface of the batt through the thickness of the batt to the
opposite surface of the bat, said row of streams being spaced at a frequency in the
range of 3 to 10 per centimeter and being supplied from orifices having diameters
in the range of 0.13 to 0.22 mm, whereby an improved heavy-weight, nonapertured nonwoven
fabric as defined above is produced. In preferred embodiments of the process, the
batt unit weight is in the range of 240 to 510 g/m
2, the fiber length is in the range of 1.3 to 3.8 cm, the fiber decitex is in the range
of 1.4 to 2.5 dtex, the orifice frequency is in the range of 3 to 6 per cm, and the
streams are supplied at a pressure in the range of 6890 to 22740 kPa.
[0006] The invention will be understood more readily by reference to the drawing which is
a graph of strip tensile strength versus unit weight that compares the fabrics of
the present invention with those of the prior art.
[0007] As used herein, the term "heavy-weight" means a nonapertured nonwoven fabric of hydraulically
entangled staple fibers that has a unit weight in the range of 200 to 850 g/m
2 [6-25 ozlyd
2].
[0008] The key advantageous distinction of the products of the present invention is illustrated
in the graph of the attached drawing. The shaded area represents the nonapertured
nonwoven fabrics of hydraulically entangled staple fibers of the prior art. The individual
points shown on the graph represent the strip tensile data given in detail hereinafter
in the Examples. Note the extraordinarily higher tensile strengths of the heavy-weight
fabrics of the invention. These strong fabrics of the invention also possess excellent
grab strengths and resistance to disentanglement.
[0009] Generally the staple fibers which are suitable for use in the nonapertured nonwoven
fabric of the present invention are in the range of 1 to 18 dtex [0.9 to 16 denier]
and in the range of 0.6 to 5 cm [1/4-2 inches] long. Preferably, the dtex range is
1.4 to 2.5 dtex [1.25-2.25 denier] and the length range 1.3 to 3.8 cm [1/2-1-1/2 inches].
Fibers of circular cross-section are preferred.
[0010] The staple fibers may be of any synthetic organic polymer. Preferred polymers include
poly(p-phenylene terephthalamide), poly(m-phenylene isophthalamide) and poly(ethylene
terephthalate). Fabrics made of hydraulically entangled fibers of each of the polymers
are illustrated in the Examples.
[0011] The heavy-weight nonapertured nonwoven fabric of the present invention possesses
a unique advantageous combination of characteristics, which includes a grab strength
of at least, 160 N/cm [91 Ib/in], preferably in the range of 245 to 875 N/cm [140
to 500 lb/in], a strip tensile strength of at least 0.26 (N/cm)/(g/ m
2) [5 Ib/in)/(oz/yd
2)], preferably in the range of 0.36 to 0.77 (N/cm)/(g/m
2) [7-15 (lb/in)/ozlyd
2)] and the resistance to disentanglement is at least 50 alternate extension cycles,
preferably at least 90 cycles.
[0012] The preferred manner in which the hydraulic entanglement treatment is performed in
manufacturing the preferred fabrics of the present invention results in the nonapertured
fabrics having a repeating pattern of closely spaced lines of fiber entanglement,
called "jet tracks". The jet tracks are readily visible under low magnification. The
preferred fabrics of the invention have between 3 and 10 jet tracks per cm [7.5 to
25 per inch] and most preferably between 3 and 6 jet tracks per cm [7.5 to 15 per
inch].
[0013] In making the nonapertured nonwoven fabrics of the present invention, the staple
fibers are formed into starting batts of 200 to 850 g/m
2 [6 to 25 ozlyd
2] by known techniques which employ Rando-webbers or air-laydown equipment such as
that disclosed in Zafiroglu, U.S. Patent 3,797,074. A continuous hydraulic entanglement
treatment is then performed with the staple-fiber starting batt in place on a foraminous
support, such as a woven wire screen.
[0014] In the hydraulic entanglement treatment, the batt is exposed to a series of fine,
columnar streams of water supplied to one surface of the batt and then to the other
surface of the batt. The streams of water are supplied from a row of orifices located
a short distance, usually about 2.5 cm [1 inch] above the surface of the batt. Orifices
of the type disclosed in Dworjanyn, U.S. Patent 3,403,862, are employed. Preferred
orifices have a diameter in the range of 0.13 to 0.22 mm [0.005 to 0.009 inch]. In
the preferred process of the present invention the orifices are spaced to produce
at least 3 jet tracks per cm [7.5 per inch] and no more than 10 jet tracks per cm
[25 per inch], and most preferably no more than 5 jet tracks per cm [12.7 per inch].
[0015] In the preferred hydraulic treatment portions of the staple fibers initially located
at one surface of the batt are driven by the water jets through the thickness of the
batt to the opposite surface of the batt. This important rearrangement of the fibers
is performed immediately after an initial wetting and preliminary light consolidation
of the batt. If the starting batt has sufficient coherency as supplied to the entanglement
step, the very first row of water streams can perform this important rearrangement,
if supplied at sufficient pressure and if they impact the batt with sufficient force.
The use of such jets on wide spacings (i.e., no more than 10/cm) results in deeper
penetration of the streams into the batt with less interference from adjacent streams
than would be obtained with closer spaced jets. Furthermore, it is preferred that,
in contrast to the commonly used commercial practice of gradually increasing the supply
pressures of the streams in each successive row of jets, the highest pressures be
supplied to the first row of jets (or the first row after the initial wetting operation).
Preferably, the pressure to this first row of jets is in the range of 6890 kPa to
22740 kPa [1000-3300 psi]. This prevents the fibers at the surface of the batt from
immediately forming a dense, tightly entangled surface layer, which then resists water-jet
penetration and does not allow portions of fibers from one surface of the batt to
be forced through the thickness of the batt to the opposite surface. Once the initial
desired rearrangement has been performed, the remainder of the entanglement process
can be performed in the known manner. Even if closer spaced jets are used in the remaining
portion of the hydraulic entanglement procedure, the jet tracks produced by the initial
high impact jets are not erased or obscured. The preferred hydraulic-jet treatment
just described in comparison to the other methods illustrated herein is believed to
result in stronger, better entangled and more delamination-resistant heavy-weight
nonwoven fabrics.
[0016] Staple fiber blends of mixed lengths and/or mixed decitex usually are more readily
made into fabrics of the invention than fibers of substantially only one length and
decitex. Thus, blends of staple fibers may be formed into fabrics of the invention
with less total expenditure of energy per unit weight of fabric, with less total energy
impact product, and with lower maximum jet pressures. Heavier, longer and stiffer
fibers are more difficult to rearrange and entangle.
[0017] The following test procedures were used to measure the various characteristics and
properties reported herein. All measurements were made on dry fabrics or fiber.
[0018] Tensile properties are measured on an Instron tester at 70°F and 65% relative humidity.
[0019] Strip tensile strength is measured in general accordance with ASTM Method D-828-60
on a 1/2 inch [1.27 cm] wide by 4 inch [10.16 cm] long sample, using a 2 inch [5.08
cm] gauge length and an elongation rate of 50% per minute.
[0020] Grab strength is measured in general accordance with ASTM Method D-1682-64, on a
4 inch [10.16 cm] wide by 6 inch [15.24 cm] long sample, using a 3 inch [7.62 cm]
gauge length and an elongation rate of 25% per minute.
[0021] For each of the tensile measurements, samples were cut in the machine direction (MD)
and the cross-machine direction (XD) of the fabric. In the graph of the attached drawing,
only the averages of MD and XD values are plotted.
[0022] Disentanglement resistance of nonapertured nonwoven fabric was measured in cycles
by the Alternate Extension Test described by Johns & Auspos, "The Measurement of the
Resistance to Disentanglement of Spunlaced Fabrics," Symposium Papers, Technical Symposium,
Nonwovens Technology-Its Impact on the 80's, INDA, New Orleans, Louisiana, 158-162
(March 1979). The load applied to the test sample in the .machine direction of the
fabric (i.e., the vertical load on the tester) in grams was the unit weight in g/m
2 multiplied by 2.95. The load- applied in the cross-machine direction was one-half
that applied in the machine direction.
[0023] In the examples which follow batts of staple fibers are given a hydraulic jet treatment
to from strong, heavy-weight fabrics of the invention. Different sets of orifices
are employed to provide columnar streams of water to the batts, while the batts are
supported on screens, under which means are provided for removing the water. The orifices
are arranged in rows perpendicular to the direction of batt travel and are located
about 1 inch (2.5 cm) from the surface of the batt. Five sets of orifices and five
different screens are employed. These orifice sets are described as follows:
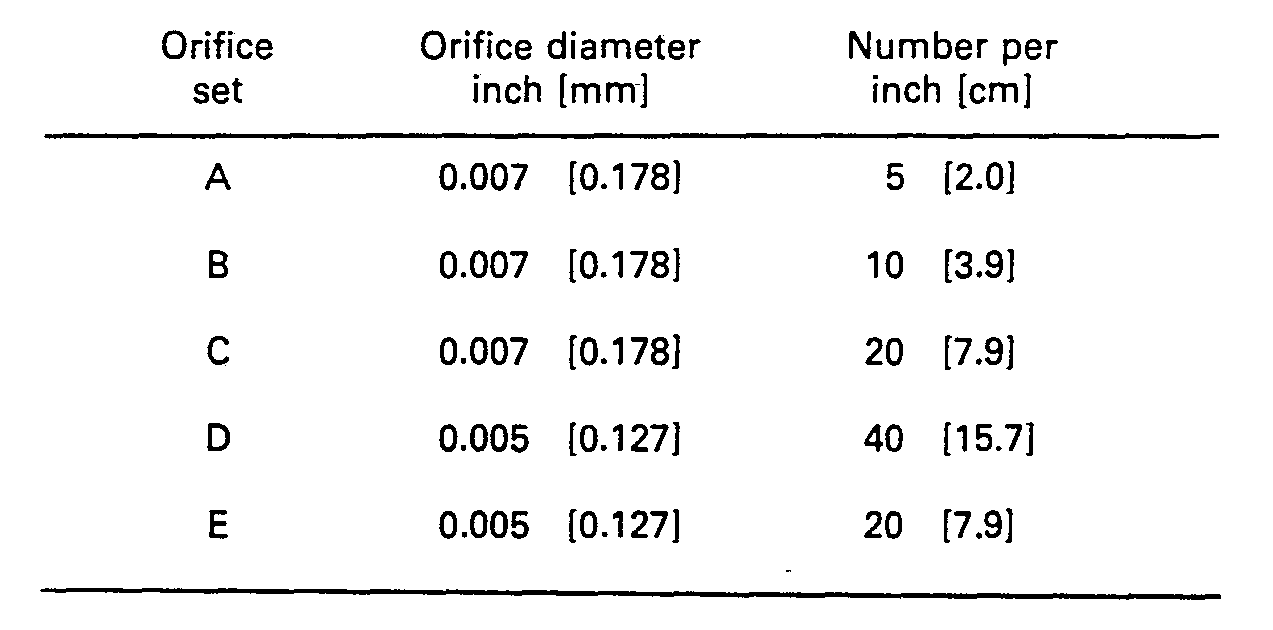
[0024] Note that in orifice set A, B, C and E, all the orifices are located in a single
row, but in set D the orifices are arranged in two staggered rows spaced 0.04 inch
[0.10 cm] apart with each row containing 20 orifices/ inch [7.9/cm].
[0025] The different wire mesh support screens that are employed in the examples are described
as follows:
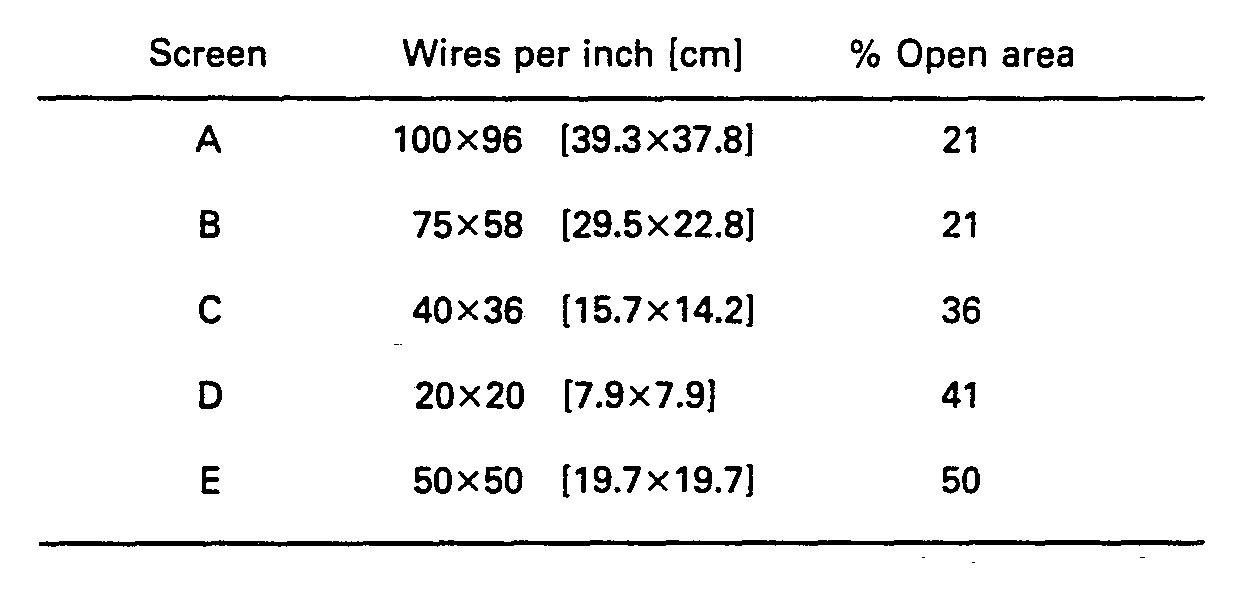
Example 1
[0026] This example illustrates the invention with heavy-weight, nonapertured, jet-tracks
nonwoven fabrics of hydraulically entangled staple fibers of poly(p-phenylene terephthalamide).
The fabrics have outstanding tensile characteristics.
[0027] Two batts of poly(p-phenylene terephthalamide) staple fibers were prepared. Each
batt consisted of three layers of webs that were formed on a Rando-webber air laydown
machine from 3/4 inch [1.9 cm] long and 1.5 denier [1.7 dtex] T-29 Kevlar® aramid
fibers. The fibers were commercially available from E.I. Du Pont de Nemours and Company.
Batt 1-a weighed 14.7 ozlyd
2 [498 g/m
2] and Batt 1-b weighed 16.4 oz/yd
2 [556 g/m
2]. Each batt was then placed on Screen C and forwarded at a speed of 10 yards per
minute [9.14 meters/min] under rows of columnar jets of water supplied for orifice
sets C. Supply pressure to successive rows of jets, was 500 psi [3450 kPa] to the
first row of jets followed by 3,300 psi [22,740 kPa] to each of the next three rows
of jets. The same sequence of jet treatments was then given through the opposite surface
of the batt.
[0028] Table I lists the total energy-impact product (Exl) and the total energy expended
in the hydraulic jet treatment along with properties of the resultant nonapertured
fabric. The average of the MD and XD strip tensile strengths of the fabrics are plotted
in the Figure and show the extraordinarily higher strip tensile strength of these
fabrics of the invention, as compared to the highest strip tensile strength exhibited
by same weight of prior art fabrics. The fabrics of this example have strip tensile
strengths that are about 7.7 to 9.2 times those of the prior art fabrics of comparable
weight.
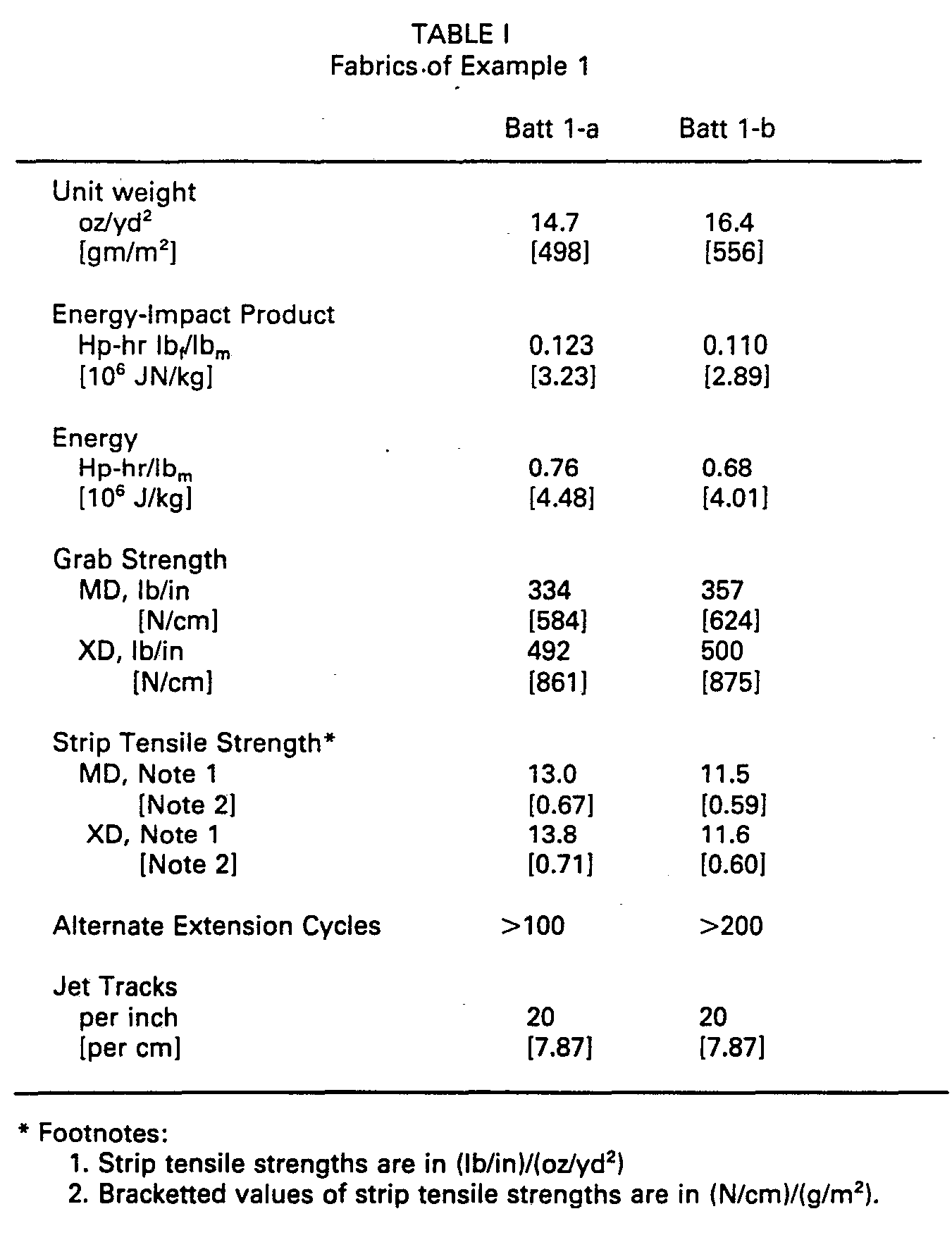
Example 2
[0029] This example further illustrates the invention with heavy-weight, nonapertured, jet-tracked
nonwoven fabrics of hydraulically entangled staple fibers of poly(m-phenylene isophthalamide):
[0030] Two batts of Nomex
s aramid staple fibers were prepared by an air-laydown process of the type described
in Zafiroglu, U.S. Patent 3,797,074. The Nomex® fibers were available commercially
from E.I. du Pont de Nemours and Company and are made from poly(m-phenylene isophthalamide)
polymer. Batt 2-a consisted essentially of a 67/33 blend of 1.5 inch [3.8 cm] long
and 1/4 inch [0.64 cm] long staple fibers of 2 denier [2.2 dtex]. Batt 2-b consisted
essentially of 1 inch [2.5 cm] long fibers of 2 denier [2.2 dtex]. Batts 2a and 2b
were treated with columnar hydraulic jets to form fabrics respectively weighing 7.0
and 8.6 oz/yd
2 [237 and 292 g/m
2]. Table II summarizes the sequence of jet treatments. The first five rows of jets
impact one face of the batt; the other rows, the other face.
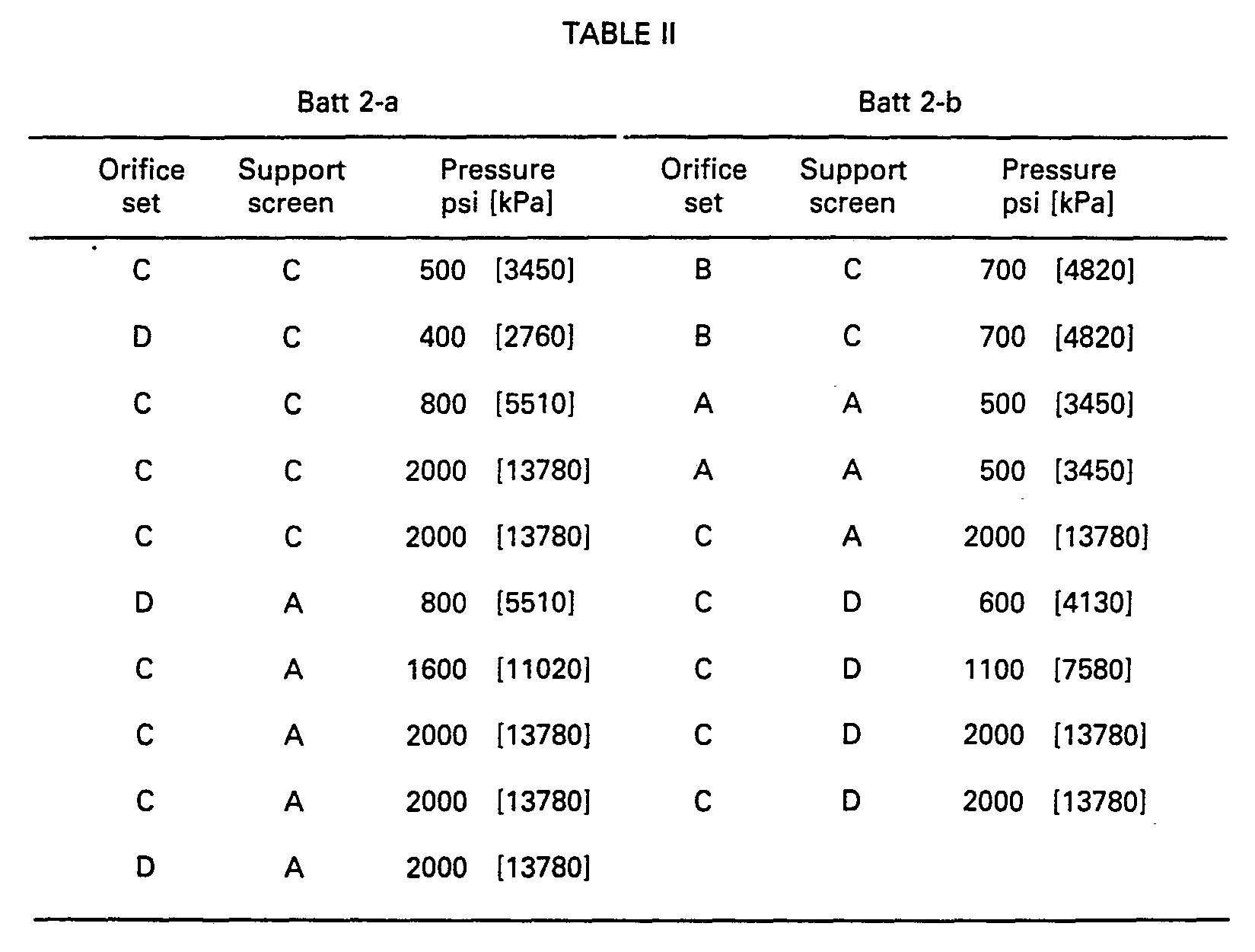
[0031] The total Exl product and energy expended in the treatment of Batts 2-a and 2-b are
summarized in Table III along with the characteristics of the resultant fabrics. The
average strip tensile strength of the batts is plotted in the Figure and again shows
the strength advantage of the fabrics of this example over similar prior art fabrics
of the same weight.
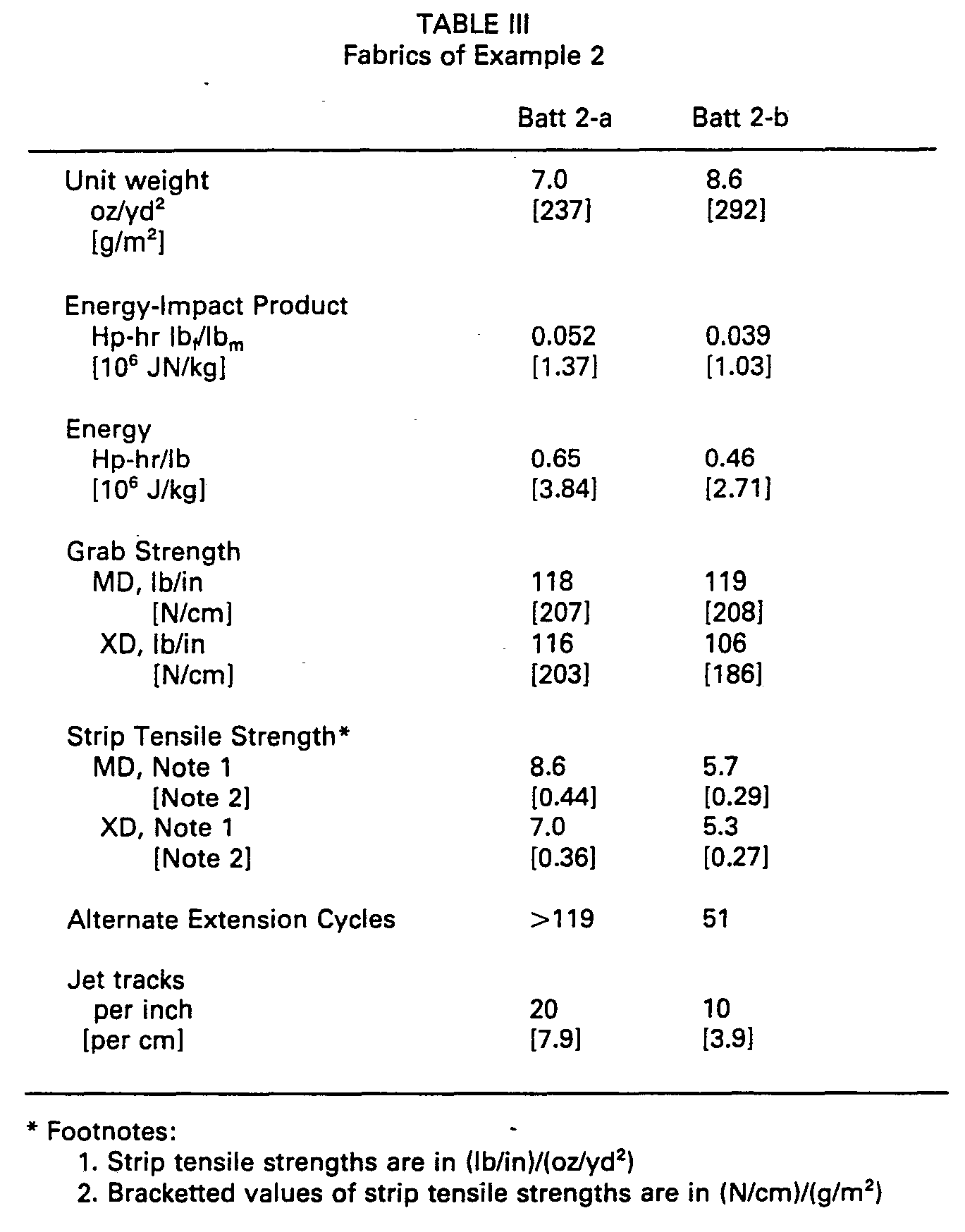
Example 3
[0032] This example illustrates the production of fabrics of the invention from poly(ethylene
terephthalate) staple fibers of 1.35 denier [1.5 dtex] and 3/4 inch [1.9 cm] length.
The fabrics exhibit excellent tensile characteristics and resistance to disentanglement.
The four fabrics were prepared as described in the following paragraphs.
[0033] Batt 3-a was prepared on Rando-webber equipment and then treated sequentially by
hydraulic jets from orifice set C while being forwarded at 10 yardslmin [9.14 m/min]
on screen support C. The batt was treated by seven rows of jets. The first four rows
of jets treated one side of the batt and the remaining three rows the other side of
the batt. The jet supply pressure was 200 psi [1380 kPa] for the first row of jets
and 2800 psi [19290 kPa] for the remaining rows of jets.
[0034] Batt 3-b was formed by means of an air-laydown apparatus of the type disclosed in
Zafiroglu, U.S. Patent 3,797,074 and then, while being forwarded at 10 yardslmin [9.14
m/min], was treated sequentially by seven rows of jets. The first four rows treat
one side of the batt; the last three rows treat the other side. While under the first
row of jets, the batt is on support screen C; on screen A while under the next three
rows; and on screen B while under the last three rows. The first row of jets was supplied
through orifice set C at a pressure of 1000 psi [6890] kPa. The next three rows were
supplied through orifice sets D respectively at pressures of 500, 1500 and 2000 psi
[3450, 10340 and 13780 kPa]. The final three rows were supplied through orifice sets
D respectively at pressures of 500, 1500 and 2000 psi [3450, 10340 and 13780 kPa].
[0035] Batts 3-c and 3-d were formed on a similar air laydown apparatus as used for Batt
3-b, but one that gave more MD direction strength to the batt. Batts 3-c and 3-d were
subjected to rows of hydraulic jets while being forwarded at 13.6 yards/min [12.4
m/min]. For Batt 3-c, one face of the batt was subjected in sequence to one row of
jets supplied through orifice set E at 1500 psi [10340 kPa] while on screen support
C, and then while on screen support B, to one row of jets supplied through orifice
set C at 500 psi [3450 kPa] and 4 rows of jets supplied through orifice set D at 2000
psi [13780 kPa]. Then, the other face of the batt was subjected while on screen support
B, to the same sequence of rows of jets as the first face except that the very first
row of jets was omitted. This treatment was repeated for Batt 3-d, except that the
first row of jets was replaced by two rows of jets (which treated only the first face
of the batt), the first being supplied at 1300 psi (8960 kPa) through orifice set
B and the second, through orifice E at 500 psi [3450 kPa].
[0036] The total Exl product and the energy expended in forming the four batts into fabrics
of the invention and the characteristics of the resultant fabrics are summarized in
Table IV. The average strip tensile strengths, which are plotted in the Figure, clearly
show the advantage of these heavy-weight fabrics of the nvention over the comparable
heavy-weight nonwoven fabrics of the prior art.
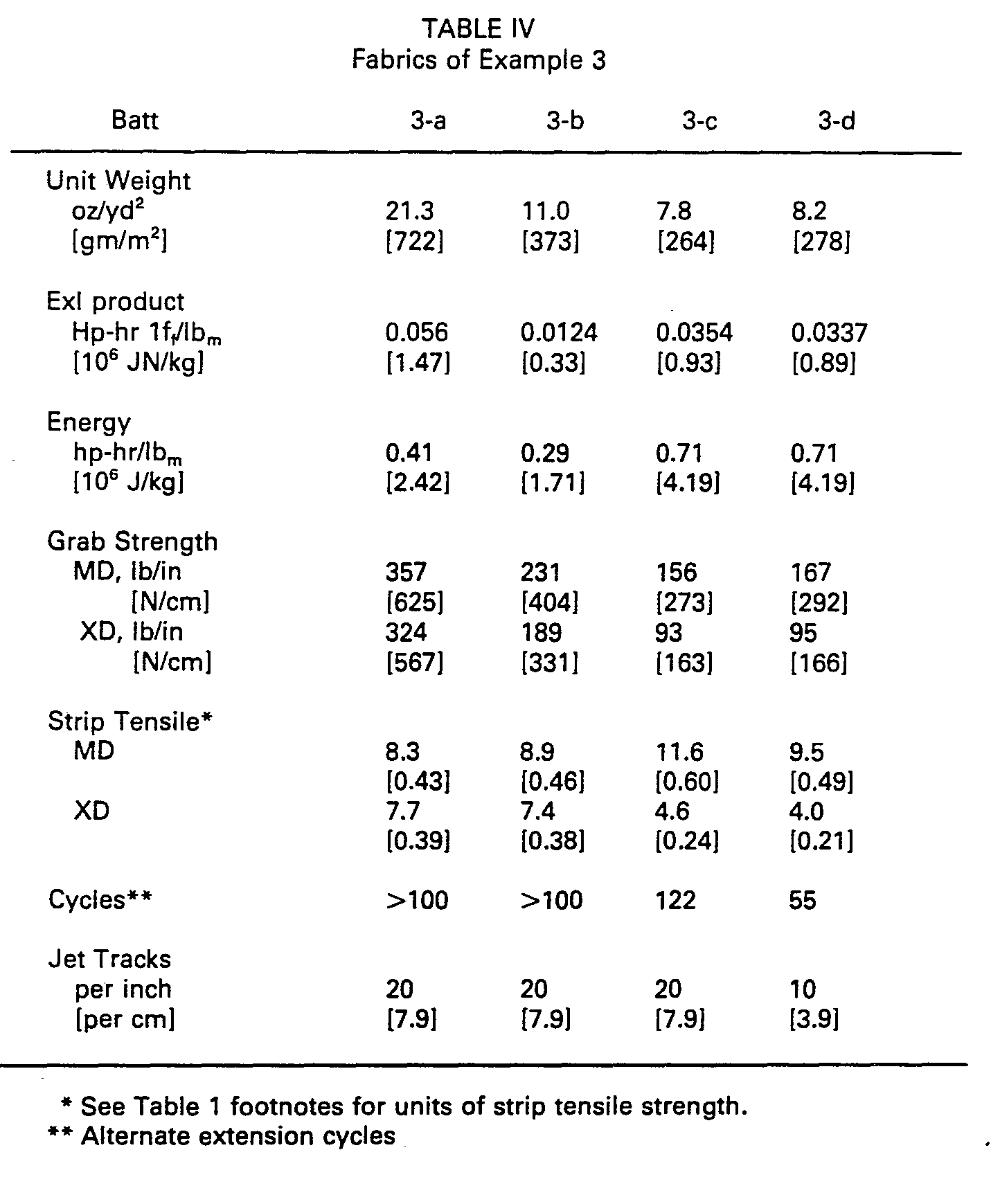
Example 4
[0037] In this example staple fibers of polyethylene terephthalate of different deniers
and of different lengths are blended together to form batts which are then treated
with columnar streams of water to obtain strong, nonapertured, heavy-weight nonwoven
fabrics of the present invention.
[0038] Three batts of blended polyester fibers were prepared by the same air-laydown process
as used in Example 2. Two of the batts labelled 4-a and 4-b were made with a 50/50
blend of 1-1/4-inch [3.2 cm] long, 6- denier [6.7-dtex] fibers with 1/4-inch [0.64-cm]
long, 1.35-denier [1.5-dtex] fibers. The third batt, 4-c, contained a 67/33 blend
respectively of these fibers. These batts were forwarded at 10 yards/min [9.14 m/
min] through columnar water jets, supplied through orifice sets D while supported
in sequence on Screens C, A and B. While on Screens C and A the jets entered through
one surface of the batt, and while on Screen B, the jets entered through the opposite
surface. The sequence of jet supply pressure was as given in Table V. The total Exl
product and the energy expended in treating the three batts are listed in Table VI
along with the characteristics of the resultant fabrics. The average strip tensile
strength of the fabrics are plotted in the Figure. The data clearly show the advantage
in tensile strength of these fabrics of the invention over similar prior art fabrics
of the same weight.
[0039]
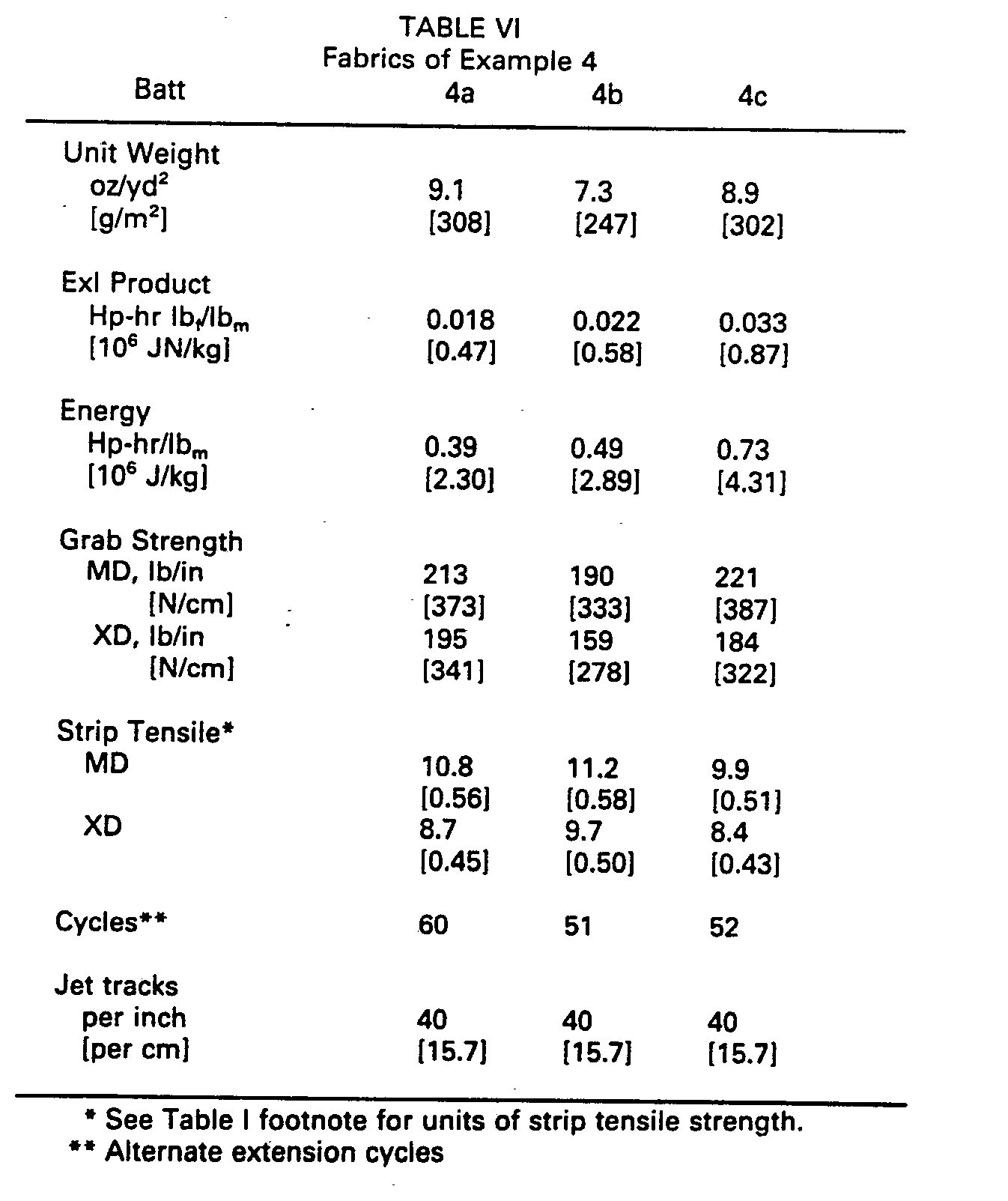
Example 5
[0040] This example illustrates the production of a nonwoven fabric of the invention from
a 50/50 blend of 1.5- inch [3.8-cm] long, 15-denier [16.7-dtex] with 1/4-inch [0.63-cm]
long, 1.8-den [2-dtex] staple fibers of 66 nylon. The fiber blend was formed into
a batt with an air laydown apparatus of the type disclosed in Zafiroglu, U.S. Patent
3,797,074. The batt was then forwarded at 8.0 yards/min [7.3 meters/min] through rows
of hydraulic jets, while supported on screens. The sequence of treatments was as follows:

[0041] While the batt was on screens C and B, the jets impinged on one surface of the batt
and then while the batt was on screen E, the jets impinged on the other surface of
the batt. As a result of the treatment of a strong, disentanglement resistant, heavy
weight, nonapertured nonwoven fabric was formed whose characteristics are summarized
in Table VII. As shown by the plot of average strip tensile versus unit weight, the
fabric is far superior in tensile strength to prior art.
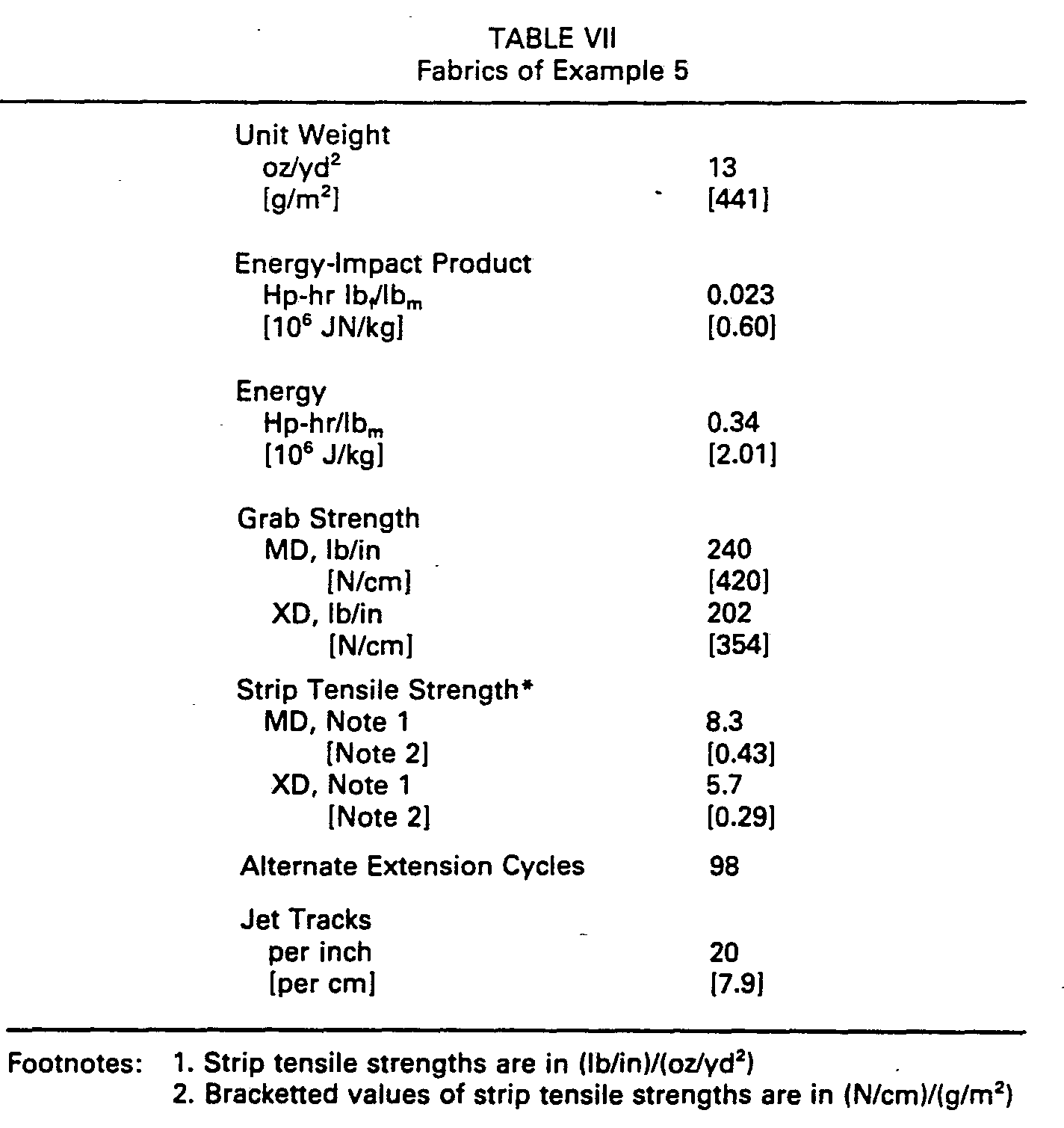
1. A heavy-weight, nonapertured, nonwoven fabric consisting essentially of hydraulically
entangled staple fibers of synthetic organic polymer, characterized by the fabric
having in combination a unit weight in the range of 200 to 850 g/m2, a grab strength of at least 160 N/cm, a strip tensile strength of at least 0.26
(N/cm)/(g/m2) and a resistance to disentanglement of at least 50 alternate extension cycles.
2. A nonwoven fabric according to Claim 1 characterized in that the unit weight is
in the range of 240 to 510 g/m2, the grab strength is in the range of 245 to 875 N/cm, the strip tensile strength
is in the range of 0.36 to 0.77 (N/cm)/(g/m2), the resistance to disentanglement is at least 90 alternate extension cycles and
the fabric has between 3 and 10 jet tracks per cm.
3. A nonwoven fabric according to Claim 1 or Claim 2 characterized in that the staple
fibers are of 1 to 18 dtex and of 0.6 to 5 cm length.
4. A nonwoven fabric according to any one of Claims 1 to 3 characterized in that the
polymer is poly(p-phenylene terephthalamide).
5. A nonwoven fabric according to any one of Claims 1 to 3 characterized in that the
polymer is poly(m-phenylene isophthalamide).
6. A nonwoven fabric according to any one of Claims 1 to 3 characterized in that the
polymer is poly(ethylene terephthalate).
7. A process for preparing heavy-weight, non-apertured, nonwoven fabric by treating
batts of staple fibers of synthetic organic polymer with rows of fine columnar streams
of water while the batts are supported on a foraminous screen and are moving perpendicular
to the rows of streams, characterized by for stronger fabrics, preparing the fabric
from batts having a unit weight of 200 to 850 g/m2 and consisting essentially of staple fibers having a length in the range of 0.6 to
5 cm and a decitex in the range of 1 to 18, the batts being treated immediately after
preliminary consolidation and wetting by a row of streams which forces portions of
staple fibers from one surface of the batt through the thickness of the batt to the
opposite surface of the batt, said row of streams being spaced at a frequency in the
range of 3 to 10 per centimeter and being supplied from orifices having diameters
in the range of 0.13 to 0.22 mm, whereby a fabric as defined in claim 1 is produced.
8. A process according to claim 7 characterized by the unit weight being in the range
of 240 to 510 g/m2, the fiber length being in the range of 1.3 to 3.8 cm, the fiber decitex being in
the range of 1.4 to 2.5 dtex, the orifice frequency being in the range of 3 to 6 per
cm, and the streams being supplied at a pressure in the range of 6890 to 22740 kPa.
1. Schwerer, nicht mit Öffnungen versehener Vliesstoff, welcher im wesentlichen aus
hydraulisch verwirrten Spinnfasern aus synthetischem, organischem Polymeren besteht,
dadurch gekennzeichnet, dass der Vliesstoff in Kombination ein Flächengewicht im Bereich
von 200 bis 850 g/m2, eine Grabfestigkeit von wenigstens 160 N/cm, eine Streifenzugfestigkeit von wenigstens
0,26 (N/cm)/(g/m2) und eine Entwirrungsbeständigkeit von wenigstens 50 alternierenden Streckzyklen
hat.
2. Vliesstoff nach Anspruch 1, dadurch gekennzeichnet, dass das Flächengewicht im
Bereich von 240 bis 510 g/m2, die Grabfestigkeit im Bereich von 245 bis 875 N/cm, die Streifenzugfestigkeit im
Bereich von 0,36 bis 0,77 (N/cm)/(g/m2) liegt und die Entwirrungsbeständigkeit wenigstens 90 alternierende Streckzyklen
umfasst und dass der Vliesstoff zwischen 3 und 10 Strahlspuren pro cm hat.
3. Vliesstoff nach Anspruch 1 oder Anspruch 2, dadurch gekennzeichnet, dass die Spinnfasern
1 bis 18 dtex und eine Länge von 0,6 bis 5 cm haben.
4. Vliesstoff nach einem der Ansprüche 1 bis 3, dadurch gekennzeichnet, dass das Polymer
Poly(p-phenylenterephthalamid) ist.
5. Vliesstoff nach einem der Ansprüche 1 bis 3, dadurch gekennzeichnet, dass das Polymer
Poly(m-phenylenisophthalamid) ist.
6. Vliesstoff nach einem der Ansprüche 1 bis 3, dadurch gekennzeichnet, dass das Polymer
Poly(ethylenterephthalat) ist.
7. Verfahren zum Herstellen eines schweren, nicht mit Öffnungen versehenen Vliesstoffes
durch Behandeln von Vliesen aus Spinnfasern aus synthetischem organischem Polymer
mit Reihen von feinen, säulenförmigen Wasserströmen während der Abstützung der Vliese
auf einem durchlochten Sieb und einer Bewegung senkrecht zu den Reihen der Ströme,
dadurch gekennzeichnet, dass für stärkere Gewebe das Gewebe aus Vliesen hergestellt
wird, die ein Flächengewicht von 200 bis 850 g/m2 haben und im wesentlichen aus Spinnfasern bestehen, die eine Länge im Bereich von
0,6 bis 5 cm und einen Decitexwert im Bereich von 1 bis 18 haben, die Vliese unmittelbar
nach einer vorläufigen Verfestigung und Benetzung mit einer Reihe von Strömen behandelt
werden, welche Teile der Spinnfasern von einer Oberfläche des Vlieses durch die Dicke
des Vlieses zu der gegenüberliegenden Oberfläche des Vlieses drücken, die Reihe der
Ströme in einem Abstand mit einer Wiederholrate im Bereich von 3 bis 10 pro cm vorgesehen
sind und über Öffnungen versorgt werden, die Durchmesser im Bereich von 0,13 bis 0,22
mm haben, wodurch man ein Gewebe nach Anspruch 1 herstellt.
8. Verfahren nach Anspruch 7, dadurch gekennzeichnet, dass das Flächengewicht im Bereich
von 240 bis 510 g/m2 liegt, die Faserlänge im Bereich von 1,3 bis 3,8 cm liegt, der Faserdecitexwert im
Bereich von 1,4 bis 2,5 dtex liegt, die Öffnungshäufigkeit im Bereich von 3 bis 6
pro cm liegt und die Ströme unter einem Druck im Bereich von 6890 bis 22 740 kPa eingeleitet
werden.
1. Un tissu non tissé lourd sans ouvertures, constitué essentiellement de fibres discontinues
de polymère organique synthétique enchevêtrées hydrauliquement, caractérisé en ce
que le tissu possède, en combinaison, un poids unitaire situé dans l'intervalle de
200 à 850 g/m2, une résistance à l'essai d'arrachement ("grab test") d'au moins 160 N/cm, une résistance
à la traction sur bande d'au moins 0,26 (N/cm)/(g/m2) et une résistance au désenchevêtrement d'au moins 50 cycles d'extensions alternées.
2. Un tissu non tissé selon la revendication 1, caractérisé en ce que le poids unitaire
se situe dans l'intervalle de 240 à 510 glm2, la résistance à l'essai d'arrachement se situe dans l'intervalle de 245 à 875 N/
cm, la résistance à la traction sur bande se situe dans l'intervalle de 0,36 à 0,77
(N/cm)/(g/m2), la résistance au désenchevêtrement est d'au moins 90 cycles d'extensions alternées
et le tissu présente entre 3 et 10 pistes de jet par cm.
3. Un tissu non tissé selon la revendication 1 ou la revendication 2, caractérisé
en ce que les fibres discontinues titrent 1 à 18 dtex et ont 0,6 à 5 cm de longueur.
4. Un tissu non tissé selon l'une quelconque des revendications 1 à 3, caractérisé
en ce que le polymère est du poly(p-phénylène-téréphtalamide).
5. Un tissu non tissé selon l'une quelconque des revendications 1 à 3, caractérisé
en ce que le polymère est du poly(m-phénylène-isophtalamide).
6. Un tissu non tissé selon l'une quelconque des revendications 1 à 3, caractérisé
en ce que le polymère est du poly(téréphtalate d'éthylène).
7. Un procédé pour fabriquer un tissu non tissé lourd sans ouvertures, en traitant
des nappes épaisses de fibres discontinues de polymère organique synthétique par des
rangées de minces jets d'eau en forme de colonne tandis que les nappes sont supportées
par un écran perforé et se déplacent perpendiculairement aux rangées de jets, caractérisé
en ce que, pour obtenir des tissus plus résistants, on fabrique te tissu à partir
de nappes ayant un poids unitaire de 200 à 850 g/m2 et constituées essentiellement de fibres discontinues ayant une longueur située dans
l'intervalle de 0,6 à 5 cm et un titre situé dans l'intervalle de 1 à 18 dtex, les
nappes étant traitées immédiatement après consolidation et mouillage préliminaires
par une rangée de jets qui contraint des portions de fibres discontinues à passer
à travers l'épaisseur de la nappe depuis une surface de la nappe jusqu'à la surface
opposée de la nappe, les jets de ladite rangée étant écartés à raison de 3 à 10 par
centimètre et étant délivrés par des orifices dont les diamètres se situent dans l'intervalle
de 0,13 à 0,22 mm, si bien que l'on obtient un tissu tel que défini dans la revendication
1.
8. Un procédé selon la revendication 7, caractérisé en ce que le poids unitaire se
situe dans l'intervalle de 240 à 510 g/m2, la longueur des fibres se situe dans l'intervalle de 1,3 à 3,8 cm, le titre des
fibres se situe dans l'intervalle de 1,4 à 2,5 dtex, les orifices sont écartés à raison
de 3 à 6 par cm et les jets sont délivrés à une pression située dans l'intervalle
de 6890 à 22 740 kPa.