(19) |
 |
|
(11) |
EP 0 269 660 B1 |
(12) |
EUROPÄISCHE PATENTSCHRIFT |
(45) |
Hinweis auf die Patenterteilung: |
|
05.09.1990 Patentblatt 1990/36 |
(22) |
Anmeldetag: 09.06.1987 |
|
(51) |
Internationale Patentklassifikation (IPC)5: B22D 35/04 |
(86) |
Internationale Anmeldenummer: |
|
PCT/CH8700/066 |
(87) |
Internationale Veröffentlichungsnummer: |
|
WO 8707/856 (30.12.1987 Gazette 1987/29) |
|
(54) |
VERFAHREN ZUM GIESSEN VON METALLSCHMELZE
PROCESS FOR CASTING MOLTEN METAL
PROCEDE DE COULEE DE METAL
|
(84) |
Benannte Vertragsstaaten: |
|
AT BE CH DE FR GB IT LI NL SE |
(30) |
Priorität: |
17.06.1986 CH 2442/86
|
(43) |
Veröffentlichungstag der Anmeldung: |
|
08.06.1988 Patentblatt 1988/23 |
(73) |
Patentinhaber: |
|
- GEORG FISCHER AKTIENGESELLSCHAFT
CH-8201 Schaffhausen (CH)
- Eisenwerk Brühl GmbH
D-50321 Brühl (DE)
|
|
(72) |
Erfinder: |
|
- RIETHMANN, Max
CH-8272 Ermatingen (CH)
- SCHILLING, Herbert
D-5042 Erfstadt (DE)
|
(74) |
Vertreter: Sparing - Röhl - Henseler
Patentanwälte |
|
Postfach 14 04 43 40074 Düsseldorf 40074 Düsseldorf (DE) |
(56) |
Entgegenhaltungen: :
DE-A- 2 811 055 US-A- 3 256 571
|
US-A- 2 310 766
|
|
|
|
|
|
|
|
|
Anmerkung: Innerhalb von neun Monaten nach der Bekanntmachung des Hinweises auf die
Erteilung des europäischen Patents kann jedermann beim Europäischen Patentamt gegen
das erteilte europäischen Patent Einspruch einlegen. Der Einspruch ist schriftlich
einzureichen und zu begründen. Er gilt erst als eingelegt, wenn die Einspruchsgebühr
entrichtet worden ist. (Art. 99(1) Europäisches Patentübereinkommen). |
[0001] Die Erfindung betrifft ein Verfahren zum Gießen von Metallschmelze, mit der eine
Gießform mit in dieser enthaltenem Formstoff und einer im Formstoff ausgebildeten
Eingußöffnung aus einem mindestens einen eine Auslaufbohrung aufweisenden Ausgußstein
mit einem verschließbaren Bodenausguß aufweisenden Schmelzebehälter gefüllt wird,
wobei der Formstoff im Mündungsbereich der Eingußöffnung nachverdichtet wird und der
Ausgußstein eine gegenüber dem Schmelzebehälterboden vorstehende Unterseite aufweist,
die mit der Gießform beim Gießen in Eingriff steht.
[0002] Ein derartiges Verfahren ist aus der DE-A-2 811 055 bekannt, bei dem der Schmelzebehälter
mit seinem Ausgußstein unter Zwischenschaltung eines Trennkörpers auf die Gießform
bzw. den darin enthaltenen Formstoff aufgesetzt wird- .Der Trennkörper kann dabei
verschiedenartig, beispielsweise trichterförmig ausgebildet sein und auf dem Formstoff
in einer entsprechenden Vertiefung aufliegen, so daß er mit seinem unteren Trichterende
in den Eingußkanal der Gießform mündet. Der Trennkörper kann auch topfförmig oder
in anderer geeigneter Art ausgebildet sein und in einer entsprechenden Vertiefung
angeordnet werden. Der Trennkörper dient hierbei dem Zweck, eine Agglomeration von
Formstoffpartikeln an der Unterseite des Ausgußsteins zu vermeiden, die eine Abdichtung
beeinträchtigen und zu einem Herausquillen der Metallschmelze führen würden. Andererseits
stellt die Verwendung der Trennkörper einen beträchtlichen Aufwand dar.
[0003] Aufgabe der Erfindung ist es daher, ein Verfahren der eingangs genannten Art zu schaffen,
daß bei erhöhtem Ausbringen vereinfacht ist.
[0004] Diese Aufgabe wird dadurch gelöst, daß die Unterseite des Ausgußsteins unter einstellbarer
Anpreßkraft mit dem Formstoff im Bereich der Eingußöffnung in Flächenkontakt gebracht
und ferner die Gießform mit bis zum Gießzeitende sinkendem Flüssigkeitsniveau der
Metallschmelze im Schmelzenbehälter mit dieser gefüllt wird.
[0005] Hierbei ist es zweckmäßig, wenn das Verhältnis des Flüssigkeitsniveaus h1 der Metallschmelze
zu Beginn des Gießvorgangs zum Flüssigkeitsniveau h2 der Metallschmelze, das sich
nach erfolgtem Füllen der Gießform einstellt, in einem Bereich von 1:1 bis 1,8:1 liegt,
wobei sich h1 und h2 auf die Formteilung beziehen.
[0006] Die Erfindung wird nachstehend anhand der beigefügten Abbildungen näher erläutert.
[0007]
Fig. 1 zeigt einen Vertikalschnitt durch eine schematische dargestellte Einrichtung
zum Gießen in einer Position vor dem Füllen der Gießform.
Fig. 2 zeigt die Einrichtung von Fig. 1 nach beendetem Füllen der Gießform.
[0008] Der dargestellte Schmelzebehälter 1 weist am Boden einen Ausgußstein 2 mit einer
durch diesen sich hindurcherstreckenden Auslaufbohrung 3 auf, die mit einer durch
nicht dargestellte Antriebsmittel auf- und abbewegbaren Stopfenstange 4 einen verschließbaren
Bodenausguß 5 bildet. Der Ausgußstein 2 weist an seinem über den Schmelzebehälterboden
nach unten vorstehenden Ende eine ebene oder profilierte Unterseite 6 auf.
[0009] Um eine zu starke Belastung und eventuelles Abreißen des Formstoffs durch die Anpreßkräfte
zwischen Gießform 7 und Bodenausguß 5 in einem nachverdichteten Bereich 12 des Formstoffs
8 um die Eingußöffnung 10 an der Oberseite der Gießform 7 zu vermeiden, kann vorzugs
weise die Oberfläche 14 einer im Formstoff 8 im Bereich der Eingußöffnung 10 vorgesehene
Senke 13 zur Aufnahme des Ausgußstein 2 profiliert oder leicht nach außen ansteigend
ausgeführt werden.
[0010] Die Giessform 7 enthält Formstoff 8, in dem ein mit Metallschmelze zu füllender Formhohlraum
9 ausgebildet ist. Die Eingussöffnung 10 an der Oberseite der Giessform steht über
den Eingusskanal 11 mit dem Formhohlraum 9 in Verbindung. Der Formstoff 8 ist in einem
Bereich 12 rings um die Eingussöffnung 10 stärker verfestigt. Diese stärkere Verfestigung
ist vorzugsweise durch erhöhtes Verdichten des Formstoffes herbeigeführt. In diesem
höher verdichteten Bereich 12 ist dann eine Senke 13 ausgebildet, die vorzugsweise
durch Einfräsen oder Einformen hergestellt wird und die am Boden der Senke eine Oberfläche
14 aufweist, welche beim Giessen mit der Unterseite 6 des Ausgusssteines 2 in Flächenkontakt
gebracht wird. Der sauber bearbeitete oder geformte Boden dieser Senke 13 ermöglicht
eine einwandfreie Dichtung zwischen der Form 7, 8 und der Bodenfläche 6 des Ausgusssteines
2. Die Senke nimmt nach dem Trennen von Form und Schmelzebehälter die in der Auslaufbohrung
3 nach dem Schliessen des Stopfens 4 zurückbleibende Schmelze auf. Sie dient auch
zur Aufnahme des nachlaufenden Eisens. Der Querschnitt der Auslaufbohrung 3 ist grösser
als der Querschnitt des Eingusskanales 11, um das Vollaufen des gesamten Querschnittes
des Eingusskanales sicherzustellen und um zu gewährleisten, dass ein nicht ganz genaues
Anschliessen der Auslaufbohrung 3 an den Eingusskanal 11 mit zueinander fluchtenden
Achsen, d.h. eine geringe seitliche Verschiebung, keine nachteilige Wirkung in Bezug
auf den Füllvorgang hat.
[0011] Die Giessform 7 ist auf einer Unterlagsplatte 15 aufgesetzt, welche auf einer Rollenbahn
16 aufliegt. Für die Bewegung des Schmelzebehälters 1 in vertikaler Richtung dienen
in der Zeichnung nicht dargestellte Mittel, so dass dieser mit einstellbarer Kraft
gegen die Giessform 7 gedrückt werden kann. Natürlich kann auch umgekehrt nur die
Giessform 7 in vertikaler Richtung beweglich abgestützt sein und mit einem regelbaren
Druck gegen den Schmelzebehälter 1 angedrückt werden. Der Kontakt während des Füllvorganges
wird mit kontrollierter Kraft aufrechterhalten. Diese Kraft ist so bemessen, dass
die resultierende Flächenpressung geringer ist als die Formfestigkeit, damit die Form
nicht beschädigt wird. Aufgrund dieser kontrollierten Kraft sind die Unterseite 6
des Ausgusssteines 2 und die Oberfläche 14 der Senke 13 vollkommen dicht gegeneinander
gedrückt.
[0012] Beim Giessen wird die Giessform mit bis zum Giesszeitende sinkendem Flüssigkeitsdruck
der Metallschmelze mit dieser gefüllt. Das bedeutet, dass vor dem Giessen der Schmelzebehälter
1 mit mindestens der für die Giessformfüllung erforderlichen Metallschmelzemenge gefüllt
wird und mit dieser die Giessform mit auf Grund des Absenkens des Metallschmelzespiegels
sinkendem Druck gefüllt wird. Ein geregeltes Absenken des Metallschmelzespiegels lässt
sich mit Hilfe der Stopfenstange 4 herbeiführen. Mittels dieser wird der Bodenausguss
5 mindestens teilweise in einem Zeitpunkt geschlossen, kurz bevor der Formhohlraum
9 ganz gefüllt ist, um dadurch den Druckstoss durch die in Bewegung befindliche Metallschmelze
zu vermindern.
[0013] Das Volumen der Auslaufbohrung 3 im Ausgussstein 2 ist verhältnismässig gering und
das Füllen des Formhohlraumes 9 in der Giessform 7 lässt sich daher durch vollständiges
Schliessen des Bodenausgusses 5 derart durchführen, dass der Eingusskanal 11 und die
Senke 13, die nach dem Schliessen in der Auslaufbohrung 3 noch vorhandene Metallschmelzemenge
aufnehmen und das System wie ein Speiser wirkt, wobei die Metallschmelze aufgrund
der eintretenden Schrumpfung nachfliesst. Es lässt sich auf diese Weise erreichen,
dass oberhalb des Eingusskanales 11 keine Restmenge an Metallschmelze vorhanden ist,
was bedeutet, dass man beim Vergleich mit bisher bekannten Giessverfahren eine z.B.
mit Eingusstrichtern geringere Metallschmelzemenge benötigt, was sehr schnell zu grossen
Einsparungen führt.
1. Verfahren zum Gießen von Metallschmelze, mit der eine Gießform (7) mit in dieser
enthaltenem Formstoff (8) und einer im Formstoff (8) ausgebildeten Eingußöffnung (10)
aus einem mindestens einen eine Auslaufbohrung (3) aufweisenden Ausgußstein (2) mit
einem verschließbaren Bodenausguß (5) aufweisenden Schmelzebehälter (1) gefüllt wird,
wobei der Formstoff (8) im Mündungsbereich (12) der Eingußöffnung (10) nachverdichtet
wird und der Ausgußstein (2) eine gegenüber dem Schmelzebehälterboden vorstehende
Unterseite (6) aufweist, die mit der Gießform (7) beim Gießen in Eingriff steht, dadurch
gekennzeichnet, daß die Unterseite (6) des Ausgußsteins (2) unter einstellbarer Anpreßkraft
mit dem Formstoff (8) im Bereich der Eingußöffnung (10) in Flächenkontakt gebracht
und ferner die Gießform (7) mit bis zum Gießzeitende sinkendem Flüssigkeitsniveau
der Metallschmelze im Schmelzenbehälter (1) mit dieser gefüllt wird.
2. Verfahren nach Anspruch 1, dadurch gekennzeichnet, daß das Verhältnis des Flüssigkeitsniveaus
h1 der Metallschmelze zu Beginn des Gießvorgangs zum Flüssigkeitsniveau h2 der Metallschmelze,
das sich nach erfolgtem Füllen der Gießform (7) einstellt, in einem Bereich von 1:1
bis 1,8:1 liegt, wobei sich h1 und h2 auf die Formteilung beziehen.
3. Verfahren nach Anspruch 1 oder 2, dadurch gekennzeichnet, daß im nachverdichteten
Formstoffbereich (8, 12) eine die Eingußöffnung (10) enthaltende Senke (13) ausgebildet
wird, mit deren Oberfläche (14) die Unterseite (6) des Ausgußsteins (2) in Flächenkontakt
gebracht wird.
4. Verfahren nach einem der Ansprüche 1 bis 3, dadurch gekennzeichnet, daß die Unterseite
(6) des Ausgußsteins oder die Oberfläche (14) der Gießform (7) ein Profil aufweisen,
um den Anpreßdruck vom nachverdichteten Bereich (12) zu verlagern.
5. Verfahren nach einem der Ansprüche 1 bis 4, dadurch gekennzeichnet, daß die Änderung
des Niveaus im Schmelzebehälter (1) während des Gießvorgangs laufend überwacht und
der Bodenausguß (5) geschlossen wird, wenn keine Änderung des Niveaus mehr stattfindet.
6. Verfahren nach einem der Ansprüche 1 bis 5, dadurch gekennzeichnet, daß kurz vor
der vollständigen Füllung des Formhohlraums (9) in der Gießform (7) der Bodenausguß
(5) des Schmelzebehälters (1) mindestens teilweise zwecks Verminderung eines durch
die in Bewegung befindliche Metallschmelze in der Gießform (7) auftretendem Druckstoß
geschlossen wird.
7. Verfahren nach einem der Ansprüche 1 bis 6, dadurch gekennzeichnet, daß die Anpreßkraft
zwischen der Gießform (7) und dem Schmelzebehälter (1) durch Relativbewegung der in
vertikaler Richtung relativ zueinander beweglich abgestützten Gießform (7) und des
Schmelzebehälters (1) erzeugt wird.
1. Procédé pour couler un métal en fusion qui doit remplir un moule (7) comportant
un semi- produit moulé (8) contenu dans ledit moule et un orifice d'introduction (10)
pratiqué dans le semi- produit (8), à partir d'une poche de coulée comportant une
buse de coulée (2), présentant un canal d'évacuation (3) comportant un orifice (5)
pouvant être obturé, le semi-produit (8) étant recompacté dans la zone de l'orifice
d'introduction (10) et la buse de coulée (2) présentant une partie inférieure (6)
en saillie par rapport au fond de la poche de coulée, cette partie inférieure (6)
venant en contact avec le moule (7) lors de la coulée, caractérisé en ce que la partie
inférieure (6) de la buse de coulée (2) est amenée en contact avec le semiproduit
(8), au voisinage de l'orifice d'introduction (10), sous une pression réglable et
que, en outre, le moule (7) se remplit de métal en fusion à mesure que s'abaisse le
niveau liquide de celui-ci dans la poche de coulée.
2. Procédé selon la revendication 1, caractérisé en ce que le rapport entre le niveau
de liquide h1du métal en fusion au début de l'opération de coulée et le niveau de
liquide h2 du métal en fusion s'établissant après le remplissage du moule (7) se situe
entre 1:1 et 1,8:1, h1 et h2 se rapportant au joint de séparation du moule.
3. Procédé selon la revendication 1 ou 2, caractérisé en ce que dans la zone recompactée
du semi-produit (8,12) est pratiqué un évidement (13) dans lequel débouche l'orifice
d'insertion (10) et dont la surface (14) est amenée en contact superficiel avec la
face inférieure (6) de la buse de coulée (2).
4. Procédé selon l'une des revendications 1 à 3, caractérisé en ce que la face inférieure
(6) de la buse de coulée ou la surface (14) du moule (7) présente un profil conçu
pour écarter la pression d'application de la zone recompactée (12).
5. Procédé selon l'une des revendications 1 à 4, caractérisé en ce que le changement
du niveau à l'intérieur de la poche de coulée (1) est surveillé de manière continue
pendant toute l'opération de coulée et l'obturation de l'orifice de sortie (5) est
effectuée dès que ce niveau ne change plus.
6. Procédé selon l'une des revendications 1 à 5, caractérisé en ce que peu de temps
avant le remplissage complet de l'espace creux (9) à l'intérieur du moule (7), l'orifice
de sortie (5) de la poche de coulée (1) est obturé au moins partiellement afin de
diminuer l'impact de coups de bélier pouvant survenir à l'intérieur du moule (7) et
causés par le métal en fusion en mouvement.
7. Procédé selon l'une des revendications 1 à 6, caractérisé en ce que la force d'application
exercée entre le moule (7) et la poche de coulée (1) est générée par un déplacement
mutuel du moule (7) et de la poche de coulée (1) qui sont montés de manière à pouvoir
se déplacer dans le sens vertical l'un en direction de l'autre.
1. A method of pouring metal melt with which a mould (7) containing moulding material
(8) formed with an ingate (10) is filled from a melt container (1) having at least
one spout (2) formed with an outlet bore (3) and having a closable bottom outlet (5),
the moulding material (8) being further compressed in the inlet zone (12) of the ingate
(10), the spout having an underside (6) which projects from the base of the melt container
and which during pouring is in engagement with the mould (7), characterised in that
the underside (6) of the spout (2) is placed in surface contact at an adjustable pressure
with the moulding material (8) near the ingate (10) and the mould (7) is filled with
the metal melt in the melt container (1), the liquid level of such melt decreasing
towards the end of pouring.
2. A method according to claim 1, characterised in that the ratio of the liquid level
h1 of the metal melt at the start of pouring to the liquid level h2 of the metal melt
after filling of the mould (7) is in a range from 1:1 to 1.8 : 1, h1 and h2 relating
to the mould division.
3. A method according to claim 1 or 2, characterised in that a sink (13) in which
the ingate (10) is present is formed in the further compressed mould material zone
(8, 12) and the underside (6) of the spout (2) is brought into surface contact with
the surface (14) of the sink (13).
4. A method according to any of claims 1-3, characterised in that the underside (6)
of the spout or the surface (14) of the mould (7) have a cross-section such as to
displace the pressure of engagement away from the further compressed zone (12).
5. A method according to any of claims 1-4, characterised in that the alteration of
the level in the container (1) during pouring is supervised continuously and when
such level ceases to alter the bottom outlet (5) is closed.
6. A method according to any of claims 1-5, characterised in that shortly before complete
filling of the cavity (9) in the mould (7) the bottom outlet (5) of the melt container
(1) is closed at least to some extent in order to reduce a pressure surge caused by
the moving metal melt in the mould (7).
7. A method according to any of claims 1-6, characterised in that the engagement pressure
between the mould (7) and the melt container (1) is produced by relative movement
of the mould (7) and container (1), the same being borne so as to be movable relatively
to one another vertically.
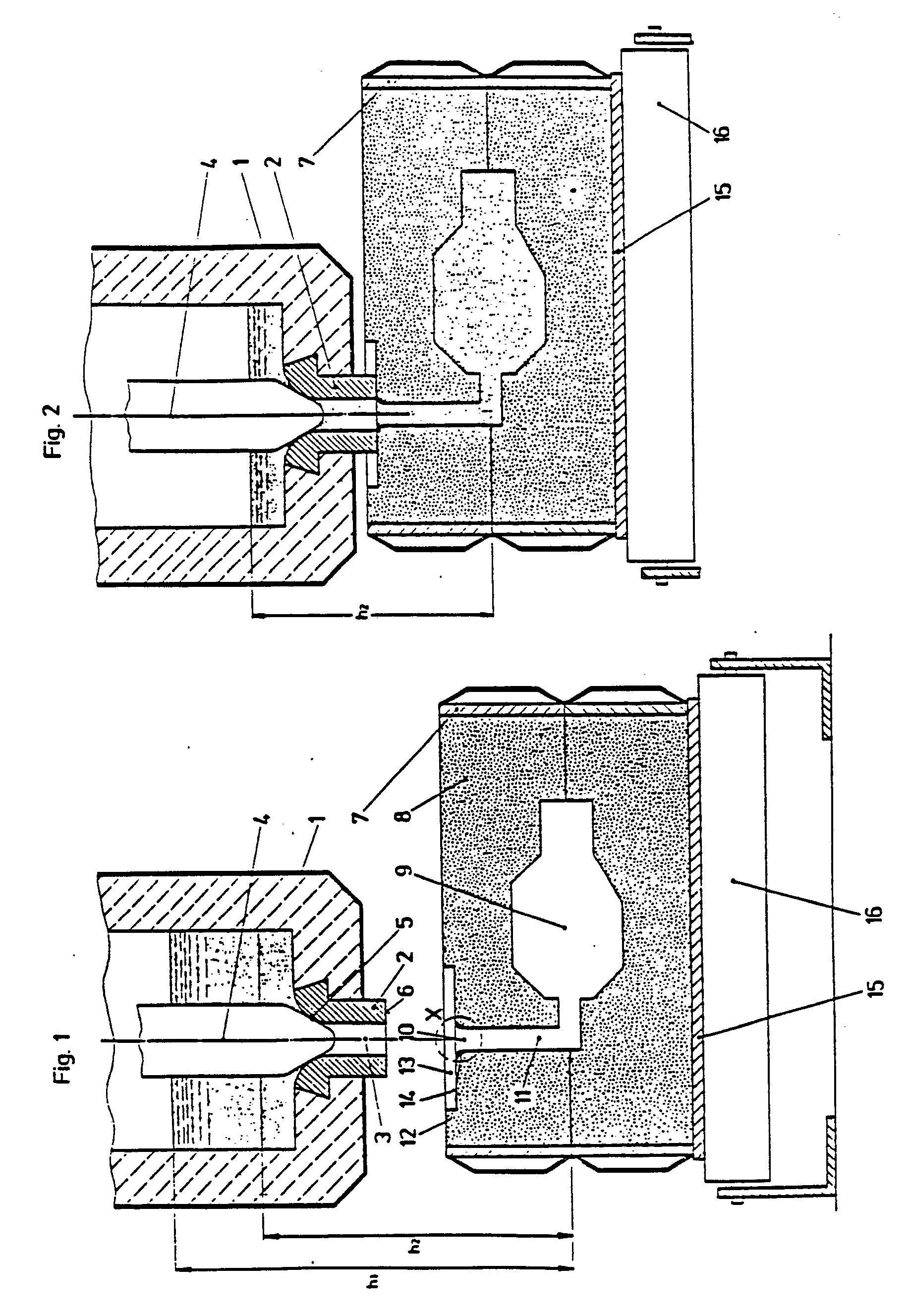