BACKGROUND OF THE INVENTION
[0001] The present invention relates to a method of coating a metal assembly including at
least one aluminum member and other metal members such as steel parts, particularly
to a method of coating assembled metal members for automobile bodies etc.
[0002] In the coating of automobile bodies constituted by different metal members such as
steel parts, zinc-plated steel parts, zinc alloy-plated steel parts, aluminum parts,
etc., since most parts are constituted by steel parts, only aluminum parts occupying
small areas are coated after stamping, degreasing and chemical treatment. The reasons
therefor are that since chemical coatings for steel parts constituting the automobile
bodies are formed by zinc phosphate chemicals, aluminum is dissolved away from the
aluminum parts by the chemicals, and accumulated in the treating solutions, and that
when an amount of aluminum accumulated in the chemical treating solutions exceeds
a certain level, the formation of chemical coatings on the steel surfaces is inhibited.
[0003] It was proposed by Japanese Patent Publication No. 45-16566 to remove the accumulated
aluminum by adding fluoric acid for precipitating the dissolved aluminum to the chemical
coating agents. However, it is difficult to control the exact amount of fluoric acid
necessary for precipitating aluminum, and the precipitated aluminum forms sludge such
as cryolite Na₃AlF₆, elpasolite NaK₂AlF₆, etc. The sludge should be removed from the
chemical treatment bath frequently, or the chemical treatment bath should be renewed
frequently.
[0004] Jitsumu Hyomen Gijutsu (Metal Finishing Practice) Vol. 35, No. 1, 1988 discloses
a method of coating assembled members consisting of aluminum parts and steel parts
in which the aluminum parts and the steel parts are treated separately in their exclusive
treatment lines and the treated aluminum parts and the steel parts are combined in
a final stage. However, in this method, the exclusive lines are necessary for both
of the aluminum parts and the steel parts, and the treated aluminum parts and the
steel parts should be handled very carefully in assembling. In addition, painted parts
may have slightly different finish colors.
[0005] In addition to the above problems, when aluminum parts are subjected to deep drawing
by stamping, a large amount of a lubricating oil having a high viscosity should be
used to impart good workability to the aluminum parts, thereby preventing cracks,
scratches, strains, etc. However, it is generally difficult to remove this lubricating
oil, requiring much time and labor. Therefore, aluminum parts which can be stamped
without using lubricating oils are desired.
OBJECT AND SUMMARY OF THE INVENTION
[0006] Accordingly, an object of the present invention is to provide a method of coating
a metal assembly including at least one aluminum member in which the aluminum member
and the other metal members such as steel parts can be treated simultaneously, thereby
effectively coating the aluminum member for automobile bodies, etc.
[0007] As a result of intense research in view of the above object, the inventors have found
that an aluminum member coated with a conductive primer is highly resistant to a treatment
chemical solution which is necessary for chemically treating steel members, and that
the aluminum member coated with a conductive primer can be easily stamped to provide
deep-drawn products, etc. without using lubricating oils. The present invention is
based on these findings.
[0008] Thus, the method of coating a metal assembly including at least one aluminum member
according to one embodiment of the present invention comprises the steps of applying
a conductive primer to the aluminum member; combining the aluminum member with other
metal members; and providing the resulting assembled members with chemical coatings
and electrodeposition coatings.
[0009] The method of coating a metal assembly including at least one aluminum member according
to another embodiment of the present invention comprises the steps of applying a conductive
primer to the aluminum member; stamping the aluminum member; combining the stamped
aluminum member with other metal member; and then providing the resulting assembled
members with an intermediate coat and/or a top coat.
[0010] The method of coating a metal assembly including at least one aluminum member according
to a further embodiment of the present invention comprises the steps of applying a
conductive primer to the aluminum member; combining the aluminum member with at least
one second aluminum member; and providing the resulting assembled members with chemical
coatings and electrodeposition coatings.
DETAILED DESCRIPTION OF THE INVENTION
[0011] The metal assembly to which the coating method of the present invention can be applied
may be constituted by at least one aluminum member and at least one other metal member.
A typical combination of aluminum members and other metal members are aluminum parts
and steel parts (including zinc-plated steel parts). Accordingly, the present invention
will be explained referring to aluminum parts and steel parts for simplicity. One
combination is at least one aluminum parts and at least one Steel parts, and another
combination is at least one first aluminum parts and at least one second aluminum
parts. In the case of different aluminum parts, the first aluminum parts is coated
with a conductive primer, while the second aluminum parts may not be coated with a
conductive primer. Specific combinations of metal members to be assembled are exemplified
as follows;
1. Aluminum parts coated with a conductive primer.
Steel parts (coated with or without a conductive primer).
[0012] A metal assembly of these plates are provided with chemical coatings and electrodeposition
coatings, optionally followed by the formation of an intermediate coat and/or a top
coat.
2. Aluminum parts coated with a conductive primer.
Steel parts which may be subjected to chemical coating.
[0013] After the aluminum parts is stamped, they are assembled together and then provided
with an intermediate coat and/or a top coat.
3. Aluminum parts coated with a conductive primer.
Steel parts.
[0014] After the aluminum parts is stamped, they are assembled together and then provided
with chemical coatings, etc.
4. First aluminum parts coated with a conductive primer.
Second aluminum parts which may not be coated with a conductive primer.
[0015] After the first aluminum parts is stamped, they are assembled together and then provided
with an intermediate coat and/or a top coat.
5. First aluminum parts.
Second aluminum parts.
[0016] They are assembled together, coated with a conductive primer and then provided with
chemical coatings, etc.
[0017] These assembled members are used for automobile bodies, electric appliances, etc.
In some applications, plastic members may be combined with aluminum parts and steel
parts.
[0018] The conductive primer which may be used in the present invention comprises:
(A) a bisphenol-type epoxy resin having a number average molecular weight of 300 to
100,000, in an amount of 30 weight % or more on a solid basis;
(B) at least one hardener selected from a polyisocyanate and a blocked polyisocyanate
in an amount of one-tenth to 2 times the weight of the above epoxy resin;
(C) fumed silica having an average particle size of 0.1 to 100 milli-µm, in an amount
of 5 to 50 weight % on a solid basis; and
(D) a ketone solvent in an amount of 40 weight % or more based on the total weight
of the primer.
[0019] The solid content of the conductive primer is 10 to 50 weight %, which makes it possible
to form a thin, uniform, conductive primer layer with excellent corrosion resistance,
high conductivity in electrodeposition coating, etc., improved formability, and excellent
adhesion to an electrodeposition coating layer., etc.
[0020] Usable as the binder resin (A) is a bisphenoltype epoxy resin soluble in an organic
solvent and having a number average molecular weight of 300 to 100,000, which is excellent
in water resistance, alkali resistance, and good adhesion to a substrate material
as well as a top coat. Examples are the epoxy resins represented by the formula:
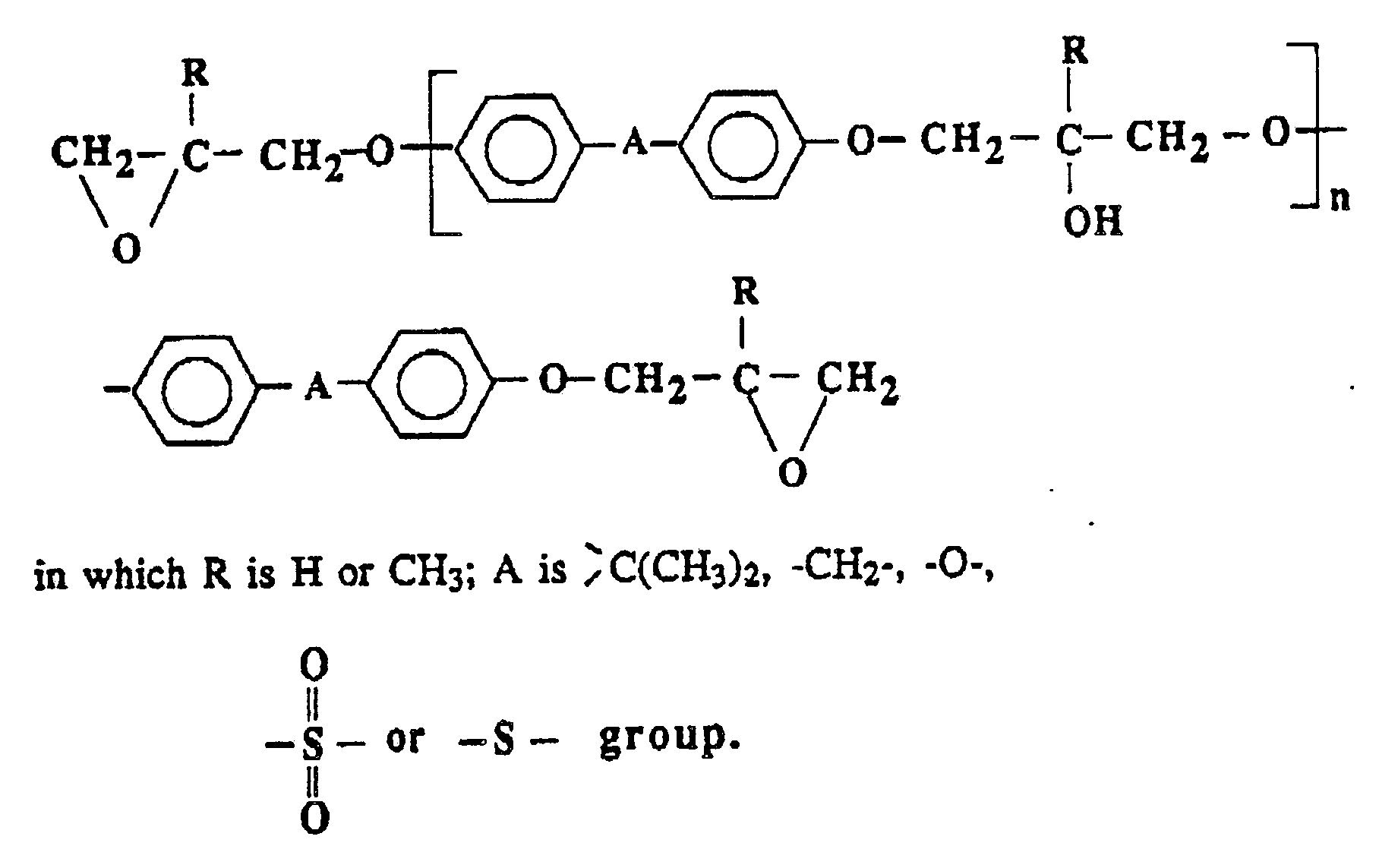
[0021] Particular preference is given to the epoxy resin wherein A is

C(CH₃)₂, having a number average molecular weight of 1,000 to 5,000, because of extremely
improved anti-corrosion properties.
[0022] If the number average molecular weight of the epoxy resin is less than 300, it is
unable to get a high polymer when reacted with a polyisocyanate, making the resulting
conductive primer layer deficient in anti-corrosive properties. On the other hand,
when it is more than 100,000, a cross-linking degree decreases, providing the resulting
conductive primer layer with poor anti-corrosive properties.
[0023] In the conductive primer layer used in the present invention, the above bisphenol-type
epoxy resin (A) should be 30 weight % or more on a solid basis of the conductive primer
layer, because, if otherwise, the resulting conductive primer layer is likely to be
brittle and have poor adhesion after stamping.
[0024] The hardener (B) used in the present invention is selected from the group consisting
of polyisocyanates and blocked polyisocyanates.
[0025] Examples of the polyisocyanates are aliphatic or alicyclic diisocyanates including
hexamethylene diisocyanate, isophorone diisocyanate, hydrogenated diphenyl methane
diisocyanate and the like; aromatic diisocyanates including tolylene diisocyanate,
diphenyl methane-4,4′-diisocyanate and the like; triisocyanates as adducts of 1 mol
of trimethylol propane and 3 mol of either one of the above-mentioned diisocyanates,
trimers of hexamethylene diisocyanate, trimers of tolylene diisocyanate and the like.
[0026] As the blocked polyisocyanates, any of the above-mentioned polyisocyanates blocked
with blocking agents may be used. Such blocking agents must be compounds capable of
reacting with an isocyanate group and forming addition products which are stable at
a room temperature but dissociated at a high temperature encountered at a baking stage,
thereby making the isocyanate group free.
Examples of the blocking agents are lactam blocking agents such as ε-caprolactam,
γ-butyrolactam and the like; oxime blocking agents such as methyl ethyl ketoxime,
cyclohexanone oxime and the like; alcohol blocking agents such as methanol, ethanol,
isobutyl alcohol and the like; phenol blocking agents such as phenol, p-t-butyl phenol,
cresol and the like; and β-diketone blocking agents as ethyl acetoacetate, methyl
acetoacetate, acetyl acetoacetate, dimethyl malonate, diethyl malonate and the like.
[0027] From the aspect of dissociation at a relatively low temperature, particular preference
is given to methyl ethyl ketoxime and β-diketones.
[0028] The above-mentioned hardener (B) is contained in the conductive primer in an amount
of one-tenth to 2 times the weight of the epoxy resin (A) on a solid basis.
[0029] The epoxy resin (A) and the hardener (B) react with each other at a relatively low
baking temperature in a short period of time, for example, at a maximum temperature
of about 100°C or more, preferably at 120°C to 200°C, in 5 to 60 seconds.
[0030] If the mixing ratio of (B)/(A) is less than 1/10, the cross-linking reaction is
insufficient, resulting in poor corrosion resistance of the conductive primer layer.
On the other hand, if the ratio (B)/(A) is more than 20/10, the conductive primer
layer are provided with poor water resistance, alkali resistance and adhesion to an
overlying coat. Particularly preferable mixing ratio of the hardener (B) to the epoxy
resin (A) is such that NCO equivalent of the hardener (B)/OH equivalent of the epoxy
resin (A) is within a range of 0.1/1 - 1.0/1. Under these conditions, excellent anti-corrosion
properties can be achieved.
[0031] The above-mentioned hardener (B) may be used together with a resol-type phenyl resin,
if desired. This is especially effective in accelerating the film-forming reaction
at a relatively low baking temperature, for example, at a maximum temperature of 100°C
to 130°C.
[0032] Particularly preferable resol-type phenol resins are the compounds of the formula:
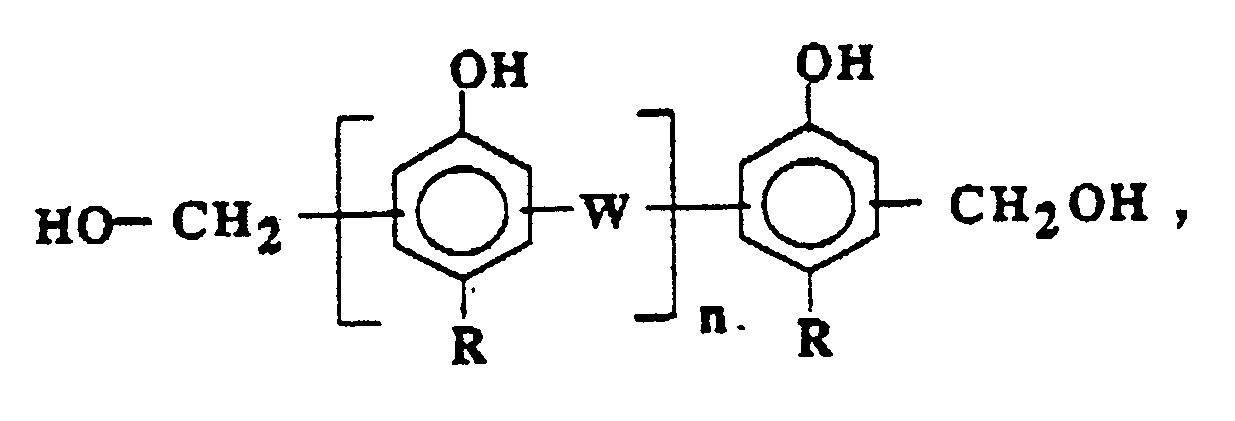
wherein n is an integer 0 to 4; W is -CH₂- or -CH₂-O-CH₂-; R is CH₃, H, or
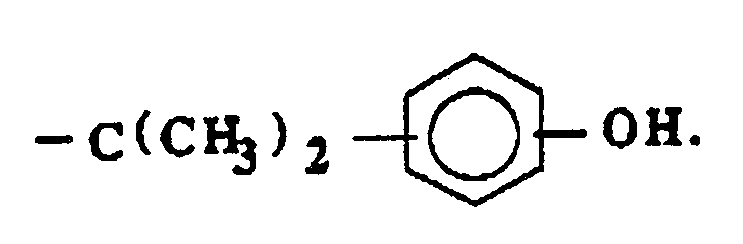
[0033] Such a resol-type phenol resin is preferably added in an amount up to 10 times the
weight of the hardener (B) on a solid basis. If the weight ratio of the phenol resin/hardener
(B) is more than 10/1, alkali resistance of the resulting conductive primer layer
is likely to be lowered.
[0034] In the present invention, fumed silica (C) having an average particle size of 0.1
to 100 milli-µm serves to provide the primer layer with electric conductivity, because
ions can pass through pores generated by the fumed silica in the primer layer in the
processes of chemical coating and electrodeposition coating. If the average particle
size of the silica is less than 0.1 milli-µm, the conductive primer layer is insufficient
not only in electric conductivity but also in adhesion to an overlying layer and alkali
resistance. On the other hand, when the average particle size of the fumed silica
exceeds 100 milli-µm, the corrosion resistance of the resulting conductive primer
layer is lowered.
[0035] The fumed silica (C) is 5 to 50 weight %, preferably 15 to 30 weight %, on a solid
basis of the conductive primer. Heretofore, such a large quantity of fumed silica
has not been used, because it makes the conductive primer highly viscous. However,
this problem has been solved by the use of particular ketone solvent (D).
[0036] When the fumed silica (C) is less than 5 weight % on a solid basis of the conductive
primer, the corrosion resistance of the resulting conductive primer layer becomes
poor. On the other hand, if it exceeds 50 weight %, adhesion properties of the conductive
primer layer after stamping tend to be undesirably decreased.
[0037] The epoxy resin (A), the hardener (B) and the fumed silica (C) are dissolved or dispersed
in a ketone solvent. The ketone solvent (D) should be 40 weight % or more to adjust
the solid content of the conductive primer to 10 to 50 weight %.
[0038] If the solid content of the conductive primer is less than 10 weight %, it is uneconomical
because too much solvent is consumed. On the other hand, if it exceeds 50 weight %,
it is hardly possible to form a thin, uniform conductive primer layer.
[0039] Preferred examples of the ketone solvents (D) are methyl isobutyl ketone, acetone,
cyclohexanone, isophorone and the like. If desired, additional solvents other than
the ketone solvent may be used together therewith. However, solvents reactive with
polyisocyanates, e.g. water, alcohol and the like, should be avoided.
[0040] From the viewpoint of formability of precoated aluminum parts, the conductive primer
may further contain 0.1 to 10 weight % based on the conductive primer, of such lubricants
as polyolefins, carboxylates, metal carboxylates, polyalkylene glycols, molybdenum
disulfide, silicone compounds, fluorinated compounds and the like. Particularly preferable
lubricants are polyethylene waxes having densities of 0.94 or more, molecular weights
of 1,000 to 10,000 and acid values of 15 KOH mg/g or less.
[0041] To enhance the electric conductivity of the conductive primer, conductive material
powder such as carbon black, graphite powder, zinc oxide powder, titanium oxide powder,
aluminum powder, copper powder, etc. may be added in proper proportions.
[0042] If desired, the conductive primer may further contain known anti-corrosive pigments
(e.g. chromate pigments, especially zinc chromate, lead chromate and barium chromate,
phosphate pigments, plumbate pigments and the like), extender pigments (e.g. carbonate
pigments, silicate pigments and the like), coloring pigments (e.g. titanium oxide,
carbon black and the like), anti-corrosive agents (e.g. amine compounds, phenolic
carboxylic acids and the like), dispersion stabilizers and the like.
[0043] The conductive primer used in the present invention forms an organic coating layer
which is electrically conductive for the purpose of the present invention. The term
"conductive" used herein means that the aluminum parts coated with the conductive
primer can be provided with chemical coatings and electrodeposition coatings, namely
meaning that electric conductivity can be achieved through the conductive primer in
the process of electrodeposition coating, etc. The reasons therefor may be considered
that since the conductive primer layer is thin and porous, electrodeposition coating
composition can be attracted to the aluminum parts via the conductive primer.
[0044] In addition, in a case where stamping such as deep drawing is conducted, the conductive
primer provides the aluminum parts with excellent workability, thereby making it unnecessary
to use lubricating oils. This is an outstanding advantage because the process of removing
lubricating oils from the stamped aluminum parts can be omitted. In addition, when
the aluminum parts is combined with a steel parts, it is preferable to use a conductive
primer for providing the same coating appearance to the aluminum parts and the Steel
parts.
[0045] To achieve the object of the present invention sufficiently, the aluminum parts is
coated with the conductive primer on one or both sides thereof, and then conveyed
to an automobile body manufacturing line, etc., where the aluminum parts is stamped
and combined with steel parts for subsequent treatments. However, in an alternative
method, after assembling the aluminum parts with the steel parts or the other aluminum
parts, the conductive primer may be applied to the assembled members by spraying,
etc. and then baked.
[0046] The conductive primer is usually applied to the aluminum parts in a dry film thickness
of 10 µm or less. When the dry film thickness exceeds 10 µm, the conductive primer
shows high insulation, making it difficult to provide it with chemical coatings and
electrodeposition coatings. Accordingly, the resulting coated aluminum parts has poor
corrosion resistance, impact resistance and workability. The preferred dry film thickness
of the conductive primer layer is 0.1-5 µm. When it is lower than 0.1 µm, the conductive
primer-coated aluminum parts is vulnerable to erosion in a zinc phosphate treatment
bath, permitting a large amount of aluminum to be dissolved into the zinc phosphate
treatment bath. In addition, in the case of stamping, the aluminum parts tends to
have cracks and strains. The more preferred dry film thickness of the conductive primer
layer is 0.5-3 µm.
[0047] The chemical coating can be conducted by using known coating chemicals. The preferred
coating chemicals for the purpose of the present invention are zinc phosphate chemicals
which contain zinc ion, phosphate ion, hydrochloric ion, nitrite ion, and, if necessary,
nickel ion, nitrate ion, chlorine ion, etc. in proper proportions. A typical example
of the coating chemicals consists essentially of about 0.4 to about 1 g/l of zinc,
about 5 to about 40 g/l of phosphate, about 0.01 to about 0.2 g/l of nitrite and about
2 to about 5 g/l of chlorate. Such coating chemicals suitable as primers for forming
electrodeposition coatings are exemplified in Japanese Patent Laid-Open No. 55-145180.
[0048] The coating chemicals may be applied to the aluminum parts and the Steel parts separately
or in combination. It should be noted that the coating chemicals are not necessarily
indispensable for the aluminum parts, but that the coating chemicals can provide the
aluminum parts with better corrosion resistance. When an assembly of the aluminum
parts coated with the conductive primer and steel parts for constituting automobile
bodies, etc. is immersed in a chemical treatment bath of zinc phosphate chemicals,
the precoated aluminum parts is not eroded by the chemical treatment bath so that
substantially no aluminum sludge is formed in the bath.
[0049] Next, the assembled members are provided with electrodeposition coatings. The electrodeposition
coating composition may be either one of a cation type and an anion type which are
known in the art. A uniform electrodeposition coating layer having a good appearance
can be formed on the precoated aluminum parts and the chemically treated steel parts.
[0050] If necessary, an intermediate coat and/or a top coat can be formed on the assembled
members thus treated. As an alternative method, without subjecting the aluminum parts
coated with the conductive primer to chemical coating with zinc phosphate chemicals,
electrodeposition coating can be conducted, optionally followed by the formation of
an intermediate coat and/or a top coat.
[0051] Incidentally, if oils, dusts, strains, etc. are attached to the conductive primer
layers, it is preferable that they are removed by solvents, etc. before subsequent
treatments.
[0052] Preferred examples of the coating process according to the present invention are
as follows:
(1) (a-1) Aluminum parts is degreased by a known method.
(a-2) Conductive primer is roll-coated and baked at a maximum temperature of 100-160°C
for 20 seconds.
(b-1) Assembling the aluminum parts with steel parts to provide automobile bodies,
etc.
(b-2) Forming chemical coatings.
(b-3) Forming electrodeposition coatings.
(b-4) Forming an intermediate coat and/or a top coat.
(2) (a-1) Aluminum parts is degreased by a known method,
(a-2) Conductive primer is roll-coated and baked at a maximum temperature of 100-160°C
for 20 seconds.
(b-1) Stamping.
(b-2) Assembling the aluminum parts with steel parts to provide automobile bodies,
etc.
(b-3) Forming electrodeposition coatings.
(b-4) Forming an intermediate coat/ a top coat.
(3) (a-1) One aluminum parts is degreased by a known method.
(a-2) Conductive primer is roll-coated on the above aluminum parts and baked at a
maximum temperature of 100°-160°C for 20 seconds.
(b-1) Stamping.
(b-2) Assembling of the stamped aluminum parts with another aluminum parts to provide
automobile bodies, etc.
(b-3) Forming an intermediate coat and/or a top coat.
In this aluminum-aluminum combination, the formation of chemical coatings and electroposition
coatings which are usually necessary for steel parts may be omitted.
4. (a-1) Aluminum parts is degreased by a known method.
(a-2) Conductive primer is roll-coated and baked at a maximum temperature of 100-160°C
for 20 seconds.
(b-1) Stamping
(b-2) Assembling the aluminum parts with steel parts to provide automobile bodies,
etc.
(b-3) Forming an undercoat by spraying.
(b-4) Forming an intermediate coat and/or a top coat.
[0053] In the above processes, the steps (a-1), (a-2) may be conducted in aluminum-working
lines, and the steps (b-1), (b-2) ... may be conducted in assembly lines of automobile
bodies, etc.
[0054] The present invention will be described in further detail by means of the following
Examples.
Example 1
[0055] The following coating process is conducted:
(a-1) Preparing aluminum parts (degreased by a known method).
(a-2) Applying an epoxy resin-type conductive primer (NIPPE) METALCOAT P19 CLEAR,
manufactured by Nippon Paint Co., Ltd.) to the aluminum parts in a dry film thickness
of 0.5 µm.
(a-3) Stamping the precoated aluminum parts (a-2).
(b-1) Assembling the stamped aluminum parts (a-3) and a stamped steel plate (cold-rolled
Steel parts) to provide an automobile body.
(b-2) Forming chemical coatings.
(i) Degreasing with alkali by immersing the automobile body in a 2-% RIDOLINE SD 400
(manufactured by Nippon Paint Co., Ltd.) solution at 60°C for 3 minutes.
(ii) Rinsing with water.
(iii) Surface adjusting by immersing the automobile body in a 0.1-% FIXODINE 5N-10
(manufactured by Nippon Paint Co., Ltd.) solution at 25°C for 30 minutes.
(iv) Forming coating chemicals by immersing the automobile body in zinc phosphate
chemicals (GRANODINE DP 3000, manufactured by Nippon Paint Co., Ltd.) solution having
a concentration:

at 50°C for 2 minutes.
(v) Rinsing with water.
(vi) Final rinsing if necessary) by spraying a 0.1-% DEOXYLITE 41 (manufactured by
Nippon Paint Co., Ltd.) solution at 20°C for 1 second.
(vii) Rinsing with pure water by spraying at 20°C for 1 second.
(viii) Drying at 150°C for 2 minutes.
(b-3) Forming electrodeposition coatings.
Cation electrodeposition paint: POWERTOP U-600, manufactured by Nippon Paint Co.,
Ltd.
Voltage applied: 200 V.
Applying time: 3 minutes.
Bath temperature: 30°C.
Baking: 185°C, 20 minutes.
Dry film thickness: 25 µm.
(b-4) Forming intermediate coat with ORGA P-41 GRAY, manufactured by Nippon Paint
Co., Ltd.
Baking: 140°C, 30 minutes.
Dry film thickness: 35 µm.
(b-5) Forming top coat with:
(1) SUPERLAC M-80 METALLIC, manufactured by Nippon Paint Co., Ltd., and
(2) SUPERLAC 0-50 CLEAR, manufactured by Nippon Paint Co., Ltd.
by a wet-on-wet coating process.
Baking: 140°C, 30 minutes.
Dry film thickness: 20/35 µm.
[0056] Various properties are evaluated, and the results are shown in Table 1.
Example 2
[0057] The same coating process as in Example 1 is conducted except for changing the dry
film thickness of NIPPE METALCOAT P19 CLEAR to 5 µm. Various properties are evaluated,
and the results are shown in Table 1.
Example 3
[0059] The following coating process is conducted:
(a-1) Preparing aluminum parts (degreased by a known method).
(b-1) Applying an epoxy resin-type conductive primer (NIPPE METALCOAT P19 CLEAR, manufactured
by Nippon Paint Co., Ltd.) to the aluminum parts in a dry film thickness of 1 µm.
(b-2) stamping the precoated aluminum parts.
(b-3) Assembling the stamped aluminum parts and a stamped steel plate (cold-rolled
Steel parts) to provide an automobile body.
[0060] The formation of coating chemicals, electrodeposition coatings, an intermediate coat
and a top coat are conducted in the same process as in Example 1. Various properties
are evaluated, and the results are shown in Table 1.
Example 4-1
[0061] The following coating process is conducted:
(a-1) Preparing two aluminum parts (degreased by a known method).
(a-2) Applying an epoxy resin-type conductive primer (NIPPE METALCOAT P19 CLEAR, manufactured
by Nippon Paint Co., Ltd.) to one aluminum parts in a dry film thickness of 3 µm.
(a- 3) Stamping the precoated aluminum parts.
(b- 1) Assembling the stamped aluminum parts and uncoated aluminum parts to provide
an automobile body.
[0062] The formation of coating chemicals, electrodeposition coatings, and an intermediate
coat and a top coat are conducted in the same process as in Example 1. Various properties
are evaluated, and the results are shown in Table 1.
Example 4-2
[0063] The same coating process is conducted as in Example 4-1 except for omitting the chemical
coating process. Various properties are evaluated, and the results are shown in Table
1.
Example 4-3
[0064] The same coating process is conducted as in Example 4-1 except for omitting the formation
of chemical coatings and the electrodeposition coatings. Various properties are evauated,
and the results are shown in Table 1.
Example 4-4
[0065] The same coating process is conducted as in Example 4-1 except for conducting the
electrodeposition coating process under the following conditions:
Undercoat
Applying an epoxy-resin type primer (ORGA SELECT 30 PRIMER, manufactured by Nippon
Paint Co., Ltd.) to the automobile body in a dry film thickness of 30 µm, and baking
it at 130°C for 30 minutes.
Various properties are evaluated, and the results are shown in Table 1.
Example 4-5
[0066] The same coating process is conducted as in Example 4-1 except for stamping one aluminum
parts, assembling it with another aluminum parts to provide an automobile body, and
then applying NIPPE METALCOAT P19 CLEAR in a dry film thickness of 3 µm.
Comparative Examples 1-4
[0067] An assembly of an aluminum parts and an Steel parts is coated as follows:
[1] Treatment of aluminum parts
[0068]
(1) Coating it with various amounts of lubricating oils.
(2) Stamping the aluminum parts at various stamping levels.
(3) Degreasing with alkali by immersing the stamped Aluminum parts in a 1-% RIDOLINE
53 (manufactured by Nippon Paint Co., Ltd.) solution at 60°C for 1 minute.
(4) Rinsing with water.
(5) Forming chemical coatings by immersing in 2-% chromate chemicals (ALODINE 1200,
manufactured by Nippon Paint Co., Ltd.) at 40°C for 30 seconds.
(6) Rinsing with water.
(7) Drying.
(8) Forming electrodeposition coatings in the same process as in Example 1.
[2] Treatment of Steel parts
(1) Coating chemical
[0069]
(i) Degreasing with alkali by immersing the steel parts in a 2-% RIDOLINE SD400 (manufactured
by Nippon Paint Co., Ltd.) solution at 60°C for 3 minutes.
(ii) Rinsing with water.
(iii) Surface adjusting by immersing the steel parts in a 0.1-% FIXODINE 5N-10 (manufactured
by Nippon Paint Co., Ltd.) solution at 25°C for 30 minutes.
(iv) Forming coating chemicals by immersing the Steel parts in a zinc phosphate chemicals
(GRANODINE DP 3000, manufactured by Nippon Paint Co., Ltd.) having a concentration:
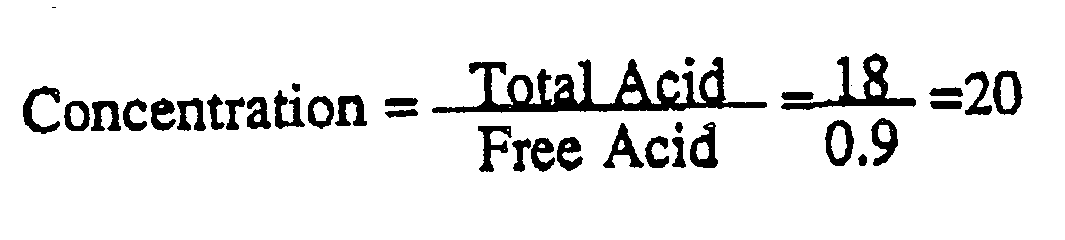
at 50°C for 2 minutes.
(v) Rinsing with water.
(vi) Final rinsing (if necessary) by spraying a 0.1-% DEOXYLITE 41 (manufactured by
Nippon Paint Co., Ltd.) solution at 20°C for 1 second.
(vii) Rinsing with pure water by spraying at 20°C for 1 second.
(viii)Drying at 150°C for 2 minutes.
(2) Forming electrodeposition coatings in the same process as in Example 1.
[3] Assembling the aluminum parts and the steel parts.
[4] Forming an intermediate coat/a top coat on the assembled plates.
[0071] As described above in detail, by the coating method of the present invention, a metal
assembly including at least one aluminum member and at least one other metal member
such as steel member can be provided with chemical coatings and electrodeposition
coatings without suffering from the erosion of the aluminum parts. In addition, the
aluminum parts coated with the conductive primer can be stamped to any shape, such
as a deep drawn shape without using a lubricating oil. This is greatly advantageous
in terms of productivity because the operation of removing a lubricating oil from
the stamped aluminum parts usually takes a lot of time and labor.